实验十八 运料小车控制模拟
运料小车的模拟控制(西门子)
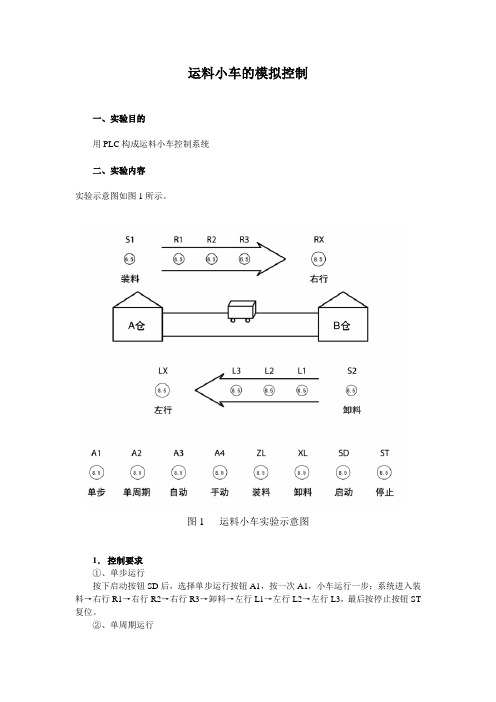
运料小车的模拟控制一、实验目的用PLC构成运料小车控制系统二、实验内容实验示意图如图1所示。
图1 运料小车实验示意图1.控制要求①、单步运行按下启动按钮SD后,选择单步运行按钮A1,按一次A1,小车运行一步;系统进入装料→右行R1→右行R2→右行R3→卸料→左行L1→左行L2→左行L3,最后按停止按钮ST 复位。
②、单周期运行按下启动按钮SD后,选择单周期运行按钮A2,小车来回运行一次后停止,最后按停止按钮ST复位。
③、自动运行按下启动按钮SD后,选择自动运行按钮A3,系统进入装料→右行→卸料→左行→装料循环,最后按停止按钮ST复位。
④、手动运行按下启动按钮SD后,选择手动运行按钮A4,系统通过ZL、XL、RX、ZX四个按钮的状态来决定小车的运行方式。
按下装料开关ZL,系统进入装料状态,灯S1亮,S1灭,按下右行按钮RX,灯R1、R2、R3依次点亮,模拟小车右行,按下卸料按钮XL系统进入卸料状态,灯S2亮,S1灭,按下左行按钮XL,灯L1、L2、L3依次点亮,模拟小车左行。
最后按停止按钮ST复位。
2.I/O分配输入输出起动SD:I0.0 装料S1:Q0.0停止ST:I0.1 卸料S2:Q0.1装料ZL:I0.2 右行R1:Q0.2卸料XL:I0.3 右行R2:Q0.3右行RX:I0.4 右行R3:Q0.4左行XL:I0.5 左行L1:Q0.5单步A1:I0.6 左行L2:Q0.6单周期A2:I0.7 左行L3:Q0.7自动A3:I1.0手动A4:I1.13.按图所示的梯形图输入程序。
4.调试并运行程序。
机械手动作的模拟 运料小车控制模拟

机电一体化专业综合实训报告实训题目:机械手动作的模拟运料小车控制模拟指导老师:王晓光韩伟娜班级:姓名:学号:摘要1、深入了解具有多种工作方式系统顺序功能图的编程方法。
2、操作模式1)回初始模式在开始进入单周期、连续和单步工作方式之前系统必须处于初始位置。
如果不满足这一条件,则必须将开关拨到“初始”模式下使系统自动返回初始位置状态下。
2)手动模式在手动模式下每个执行器的动作必须按下相应的动作按钮才能实现。
在手动编程中,运用经验法就可以实现其功能,但在程序中必须加入连锁功能。
如限位开关对运动的极限位置的限制。
上行与下行、左行与右行之间的互锁。
在转换到其他工作模式时,所有的操作必须复位。
3)自动模式在自动模式下,程序自动循环,前提条件是各部件位置在其初始位置上。
在自动模式下有单周期、单步和连续三种工作方式。
这三种工作方式可用“连续”标志和“转换允许”标志来区分,这些标志以常开接点的方式串联在程序中。
其中“连续”标志区分单周期方式和连续工作方式; “转换允许”标志区分单步运行方式和连续自动运行方式。
这三种运行方式的编程按照同一个顺序功能图来实现。
3、进一步加强PLC的工业应用目录摘要 (1)引言 (3)机械手动作的模拟 (4)一、实训目的 (4)二、实训设备介绍 (4)三、工作步骤 (4)四、I/O分配表 (5)五、外部硬件接线图 (5)六、调试程序(梯形图及注释) (5)七、调试结果 (7)运料小车控制模拟 (8)一、实训目的 (8)二、运料小车实验面板图 (8)三、控制要求 (8)四、调试程序(梯形图及注释) (9)五、调试结果 (14)总结 (15)附录 (17)参考资料 (17)引言可编程控制器是一种专为在工业环境下应用而设计的数字运算操作的电子系统。
它采用一类可编程序的存储器,用于其内部存储程序,执行逻辑运算、顺序控制、定时、计数与算术运算等操作的面向用户的指令,并通过数字式或模拟式输入/输出控制各类型的机械设备或生产过程。
运料小车控制设计设计报告

(3)选择合适P要求等来进行PLC的选择。选择包括机型、存储器容量、输入/输出模块、电源模块和智能模块等。
3、监控参数、精度要求以满足实际需要为准。
二、主要收获
懂得了一般PLC控制系统的设计步骤,具体操作如下:
(1)控制要求分析
在设计PLC控制系统之前,必须对工艺过程进行细致的分析,详细了解控制对象和控制要求,这样才能真正明白自己所要完成的任务,并更好地完成任务,设计出令人满意的控制系统。
(2)确定输入/输出设备
青岛理工大学琴岛学院
课程设计报告
课题名称:
学院:
专业班级:
学号:
学生:
指导老师:
青岛理工大学琴岛学院教务处
2011年12月22日
学生
指导老师
课题名称
运料小车控制
设计时间
2011年12月12日-2011年12月21日
设计地点
实验楼415
设计目的
通过实训掌握S7-200小型控制系统的设计和调试,联系实际,将理论知识转化为实际编程,加深对PLC系统的认识。
四、解决措施
随着经济的不断发展,运料小车的应用也不断扩大到各个领域,从手动到自动,逐渐形成了机械化、自动化。但是,传统的继电器接触器控制在工作中已经暴露出种种弊端,因此,新的控制设计已成为社会发展的必然趋势。本设计运用的可编程控制器实现的自动运料小车控制器,避开了以往继电器接触不良、开关易损坏等缺点,可靠性和稳定性都有所提高。在检测小车是否到装料、卸料点的时候,运用了行程开关使小车的停靠位置更加准确。同时,由于输入输出很明显,不需要好多额外的外接电路,让设计更简洁。这也是采用了成熟的可编程控制器带来的好处。即使在出现故障、紧急停止等环节中都能快捷操作。
运料小车模拟控制技能竞赛方案
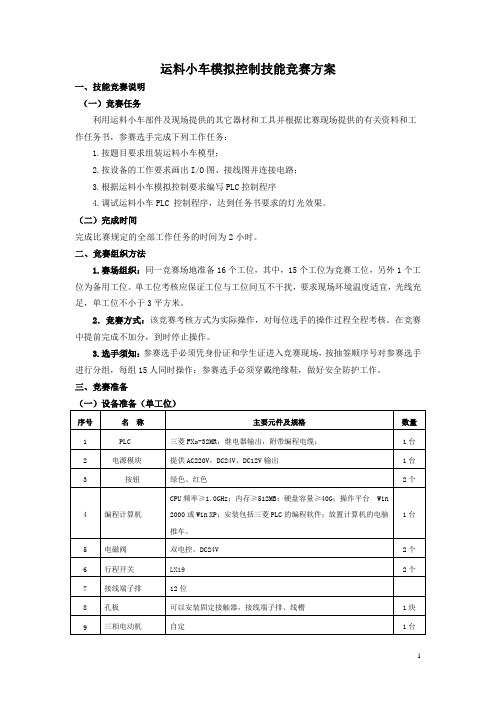
运料小车模拟控制技能竞赛方案一、技能竞赛说明(一)竞赛任务利用运料小车部件及现场提供的其它器材和工具并根据比赛现场提供的有关资料和工作任务书,参赛选手完成下列工作任务:1.按题目要求组装运料小车模型;2.按设备的工作要求画出I/O图、接线图并连接电路;3.根据运料小车模拟控制要求编写PLC控制程序4.调试运料小车PLC 控制程序,达到任务书要求的灯光效果。
(二)完成时间完成比赛规定的全部工作任务的时间为2小时。
二、竞赛组织方法1.赛场组织:同一竞赛场地准备16个工位,其中,15个工位为竞赛工位,另外1个工位为备用工位。
单工位考核应保证工位与工位间互不干扰,要求现场环境温度适宜,光线充足,单工位不小于3平方米。
2.竞赛方式:该竞赛考核方式为实际操作,对每位选手的操作过程全程考核。
在竞赛中提前完成不加分,到时停止操作。
3.选手须知:参赛选手必须凭身份证和学生证进入竞赛现场,按抽签顺序号对参赛选手进行分组,每组15人同时操作;参赛选手必须穿戴绝缘鞋,做好安全防护工作。
三、竞赛准备(二)器材准备(单工位)(三)工具准备1.连接电路的工具:螺丝刀(不允许用电动螺丝刀)、剥线钳、电工钳、尖咀钳等;2.电路和元件检查工具:万用表;3.圆珠笔或签字笔(禁止使用红色圆珠笔和签字笔)、HB和B型铅笔、三角尺(禁止带丁字尺)等。
四、评分标准根据在规定的时间内完成工作任务的情况,结合维修电工国家职业标准高级工的技能要五、选手名次排列按竞赛成绩从高到低排列参赛选手的名次。
竞赛成绩相同,完成工作任务所用时间少的名次在前;竞赛成绩和完成工作任务用时相同,控制程序步数少的名次在前。
竞赛成绩、完成工作任务用时相同、控制程序步数相同,名次并列。
六、奖项设置设置奖项为三个等级,其中一等奖占参赛总人数的5%,二等奖占参赛总人数的10%,三等奖占参赛总人数的20%,总的获奖比例为35%。
七、竞赛纪律1. 选手实际操作的出场顺序、工位由抽签确定,不得擅自变更、调整。
运料小车控制——实训指导书
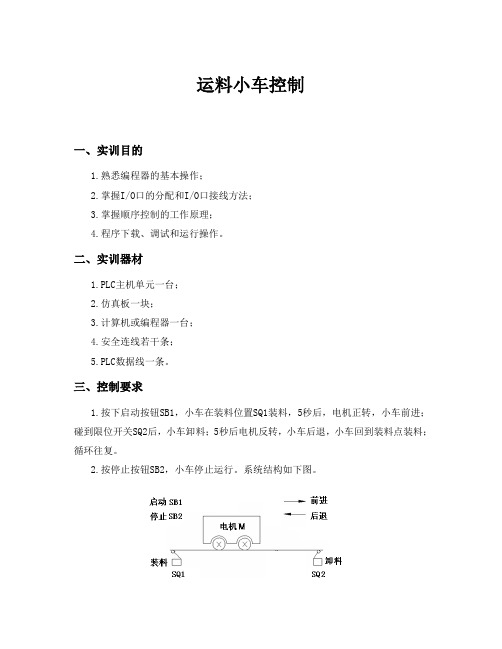
运料小车控制
一、实训目的
1.熟悉编程器的基本操作;
2.掌握I/O口的分配和I/O口接线方法;
3.掌握顺序控制的工作原理;
4.程序下载、调试和运行操作。
二、实训器材
1.PLC主机单元一台;
2.仿真板一块;
3.计算机或编程器一台;
4.安全连线若干条;
5.PLC数据线一条。
三、控制要求
1.按下启动按钮SB1,小车在装料位置SQ1装料,5秒后,电机正转,小车前进;碰到限位开关SQ2后,小车卸料;5秒后电机反转,小车后退,小车回到装料点装料;循环往复。
2.按停止按钮SB2,小车停止运行。
系统结构如下图。
四、I/O分配表
五、I/O接线图
输入输出
地址作用符号地址作用符号X0 启动SB1 Y0 前进KM1 X1 停止SB2 Y1 后退KM2 X2 装料限位SQ1 Y2 装车KM3 X3 卸料限位SQ2 Y3 卸车KM4
六、参考程序
七、操作步骤
1.先将PLC主机的电源开关拨到关状态,严格按图接线,注意5V和24V电源的正负不要短接;
2.在电脑中输入程序;
3.给PLC主机上电,将程序下载到PLC;
4.打开仿真软件,选择“运料小车”;
5.按下“启动”按钮,系统运行,循环往复;
6.按下停止按钮,系统停止。
八.思考题
1.如何将卸料时间改为3秒?
2.如果系统有两个卸料点SQ2和SQ3,分别卸料3秒、4秒,如何设计硬件和软件?。
基于组态软件仿真的运料小车的模拟控制

基于组态软件仿真的运料小车的模拟控制(沈阳理工大学 信息科学与工程学院,沈阳)摘要:本文介绍了运料小车模拟控制的设计过程,该控制系统,根据实际要求利用PLC 的实时控制和顺序处理功能,完成系统控制,并完成了组态王上位机界面的设计。
同时进行了上位机和下位机之间的联机调试。
将组态软件应用到PLC 实验中,在计算机上虚拟仿真PLC 的控制对象,解决了可缟程序控制器实验无控制对象、不直观、难以理解等问题。
针对目前常用可编程控制器监控方法的不足,提出了以组态软件为开发平台,实现可编程控制器工作状态计算机图形监控的方法。
应用实例表明,该方法有利于及时确定并排除故障;且简单便利,能在保证系统性能的前提下,缩短开发周期。
关键词 组态软件;可编程序控制器;通信Simulation control of haulling car based on the configuration software simulation Yangjie(Shenyang Ligong University Information Science and Engineering Institute ,Shenyang 0903010234) Abstract :This control system , based on the request of practice adopt the PLC’s merits to finish the control of system.To apply Configuration software to the experiment of PLC. With the control object ofPLC simulated on computer,problems which often arise in the experiment of PLC such as having no control object,process and results unperceivable,hard to comprehend etc are avoided. Considering the shortcoming of PLC monitor method commonly used at present, the computer diagram PLC monitor method for working condition is proposed, which is based on MCGS configuration software as development platform. The application example shows that the method proposed is facilitate to determinate and remove troubles in time. In addition, the method is easy to use and can shorten the period of development with the guarantee of the system performance.KeywordsConfiguration software; Programmable controller ; communication目录1组态王的概述 (1)1.1 组态王的简述 (1)1.2 组态王的主要功能 (1)2 运料小车模拟控制组态界面设计 (3)2.1 建立组态王新工程 (3)2.2 创建组态画面 (4)2.3 定义IO设备 (6)2.4 构造数据库 (7)3 S7-200的自动化通信网络 (9)3.1网络产品的层次 (9)3.2 S7—-200的通信方式与通信参数的设置 (9)3.3 S7-200通信的硬件选择 (9)3.4网络部件 (10)3.4.1通信口 (10)3.4.2网络连接器 (11)3.5使用PC/PPI电缆通信 (11)3.6 S7-200的网络通信协议 (11)3.6.1点对点接口协议(PPI) (11)3.6.2多点接口协议(MPI) (11)4 组态王与PLC的联机 (12)4.1 进入组态运料小车运行画面 (12)4.2 进入PLC界面 (13)5 结束语 (14)6 参考文献 (15)1组态王的概述1.1组态王的简述组态王.52是一个具有丰富功能的HMI/SCADA软件。
实训16 运料小车的模拟控制

PLC实训指导书垦利职专09级电工电子班
一.实验目的
用PLC构成运料小车控制系统,掌握多种方式控制的编程。
二.控制要求
系统启动后,选择手动方式(按下微动按钮A4),通过ZL,XL,RX,LX四个开关状态决定小车的运行方式。
装料开关ZL为ON,系统进入装料状态,灯S1亮,ZL为OFF,右行开关RX为ON,灯R1,R2,R3依次点亮,模拟小车右行,卸料开关XL为OFF,左行开关LX为ON,灯L1,L2,L3依次点亮,模拟小车左行。
拨动停止按钮后,再触动微动按钮A3,系统进入自动模式,即“装料——右行——卸料——装料——左行——卸料——装料”循环。
再次拨动停止按钮后,选择单周期方式(按下微动按钮A2),小车来回运行一次。
同理,选择单步方式(选择A1按钮),每按动一下A1,小车相应的运行一步。
三,运料小车实验面板图
实训十六运料小车的模拟控制 1。
装卸料小车多方式运行的PLC控制2
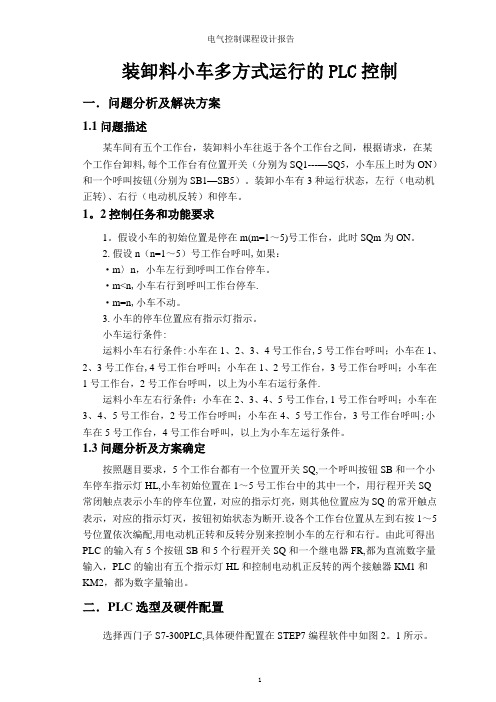
装卸料小车多方式运行的PLC控制一.问题分析及解决方案1.1问题描述某车间有五个工作台,装卸料小车往返于各个工作台之间,根据请求,在某个工作台卸料,每个工作台有位置开关(分别为SQ1---—SQ5,小车压上时为ON)和一个呼叫按钮(分别为SB1—SB5)。
装卸小车有3种运行状态,左行(电动机正转)、右行(电动机反转)和停车。
1。
2控制任务和功能要求1。
假设小车的初始位置是停在m(m=1~5)号工作台,此时SQm为ON。
2.假设n(n=1~5)号工作台呼叫,如果:·m〉n,小车左行到呼叫工作台停车。
·m<n,小车右行到呼叫工作台停车.·m=n,小车不动。
3.小车的停车位置应有指示灯指示。
小车运行条件:运料小车右行条件:小车在1、2、3、4号工作台,5号工作台呼叫;小车在1、2、3号工作台,4号工作台呼叫;小车在1、2号工作台,3号工作台呼叫;小车在1号工作台,2号工作台呼叫,以上为小车右运行条件.运料小车左右行条件:小车在2、3、4、5号工作台,1号工作台呼叫;小车在3、4、5号工作台,2号工作台呼叫;小车在4、5号工作台,3号工作台呼叫;小车在5号工作台,4号工作台呼叫,以上为小车左运行条件。
1.3问题分析及方案确定按照题目要求,5个工作台都有一个位置开关SQ,一个呼叫按钮SB和一个小车停车指示灯HL,小车初始位置在1~5号工作台中的其中一个,用行程开关SQ 常闭触点表示小车的停车位置,对应的指示灯亮,则其他位置应为SQ的常开触点表示,对应的指示灯灭,按钮初始状态为断开.设各个工作台位置从左到右按1~5号位置依次编配,用电动机正转和反转分别来控制小车的左行和右行。
由此可得出PLC的输入有5个按钮SB和5个行程开关SQ和一个继电器FR,都为直流数字量输入,PLC的输出有五个指示灯HL和控制电动机正反转的两个接触器KM1和KM2,都为数字量输出。
二.PLC选型及硬件配置选择西门子S7-300PLC,具体硬件配置在STEP7编程软件中如图2。
运料小车监控系统设计

运料小车监控系统设计一、控制要求系统启动后,选择手动方式(按下微动按钮A4),通过ZL、XL、RX、LX四个开关的状态决定小车的运行方式。
装料开关ZL为ON,系统进入装料状态,灯S1亮,ZL为OFF,右行开关RX为ON,途经相关位置(SQ1、SQ2、SQ3)灯R1、R2、R3依次点亮,卸料开关XL为ON,小车进入卸料,XL为OFF,左行开关LX为ON,途经相关位置(SQ3、SQ2、SQ1)灯L1、L2、L3依次点亮。
在A点与B点时,SQA、SQB行程开关分别接通。
拨动停止按钮(ST)后,再触动微动按钮A3,系统进入自动模式,即“装料->右行->卸料->装料->左行->卸料->装料”循环,每完成一次循环让外部LED与监控见面显示值加1.再次拨动停止按钮后,选择单周期方式(按下微动按钮A2),小车运行来回一次。
同理,拨动停止按钮后,选择单步方式(选择A1按钮),每按动一次A1,小车运行一步。
二、监控界面组态要求组态界面如上图,具体要求如下:XL、ZL、ST、SD:模拟按钮信号,鼠标点击相关图形送PLC相关控制按钮信号。
A1、A2、A3、A4:模拟开关信号,鼠标点击相关图形送PLC相关控制信号,点下后一直接通并点亮该图形,点击其他图形会让先前的灭,而后点击的亮。
如:先点击A1,A1亮并送PLC一持续接通信号,再点击A2,则A1灭而A2亮,送PLC 的A1信号为0,而A2为1。
SQA、SQB、R1、R2、R3、L1、L2、L3:当小车运行至相关位置时分别送PLC 相关位置信号并点亮该灯。
(SQA、SQB上图没有,另加)LX、RX:接受PLC左右行信号,以亮灭表示。
小车:由A仓右行经过R1、R2、R3时速度递增,在右B仓返回经过L1、L2、L3时速度递减。
LED显示(另加):接受连续循环工作时的PLC计数值显示循环次数。
三、监控系统设计分析1.设计思路:运料小车监控系统要求实时监控小车的运行状态,且通过WINCC控制界面来控制小车运行,则需建立相应的“二进制”过程变量,实现控制PLC信号及监控。
自动控制实训题4_运料小车PLC控制和交流变频调速控制系统

电气自动控制模块实训题4――运料小车PLC控制变频凋速系统1.操作条件(1)、安川电机Varispeed G7交流变频调速实训装置:(2)、三相交流异步电动机:YSJ7124P N=370W,U N=380V, I N=1.12A, n N=1400r/min ,f N=50HZ,COSφN=0.72,ηN=0.70(3)FX2N系列的PLC实训装置(配备装有三菱编程软件SWOPC-FXGP/WIN-C的电脑)2.操作内容(1)工艺流程及控制要求:1)系统工作概况:运料小车系统工艺流程示意图如下图所示。
运料小车由三相交流电动机驱动。
注:SQ1-X11,SQ2-X12, ,SQ4-X14,SQ5-X15,KM1-Y5,KM2-Y6,KM3-Y7,KM4-Y4 KM5-Y1,KM6-Y2。
本运料小车电气系统具有自动工作方式与手动点动工作方式,具体由自动工作与手动点动工作转换开关选择。
在自动工作方式时,运料小车处于原点即限位开关SQ1压合,卸料门关闭,按启动按钮后,运料小车到乙料斗进行装料,装好料到卸料处卸料,卸完料到清洗处清洗,然后再返回乙料斗装料,卸料,清洗,如此不断自动循环工作。
按停止按钮后,运料小车在本次装料、卸料、清洗完成后,快速回到原点停止。
按急停按钮后,运料小车立即仃在原处,由手动点动工作方式进行处理。
在手动点动工作时,运料小车可通过正向点动按钮和反向点动按钮进行正向点动和反向点动以便对设备进行调整、检修和故障处理。
运料小车电气自动控制系统采用PLC控制,运料小车电动机采用交流变频调速系统, 运料小车电动机交流变频调速系统亦由PLC控制。
2)自动工作方式时装料、卸料及清洗运行控制要求:①在原位时按下启动按钮时,运料小车电动机先以1200 (1300)(1000) r/min速度运行15(14)(10)秒钟,然后减速至500 (600)(600) r/min速度运行,当运料小车到达行程开关SQ4时停车装料。
运料小车基于PLC控制系统的设计

目录1 绪论 (1)1.1运料小车控制发展的概述 (1)1.2课题背景 (1)2 PLC的发展与控制原理 (3)2.1 PLC的定义与发展趋势 (3)2.2 国内主流PLC的应用比较 (4)2.3 PLC的硬件结构及工作原理 (5)2.3.1 PLC控制系统组成 (6)2.3.2 PLC的工作过程 (6)3 运料小车控制系统的方案论证 (8)3.1利用可编程控制器控制 (8)3.2 方案比较论证 (8)4 PLC控制系统的设计 (8)4.1 I/O点数的估算和PC机型的选择 (8)4.2 运料小车控制系统构成图 (11)4.3系统I/0点的分配 (11)4.3.1 输入地址计算及分配 (11)4.3.2 输出地址计算及分配 .................................................错误!未定义书签。
4.4 内部辅助继电器的分配 .................................................错误!未定义书签。
5 运料小车控制系统程序设计 ..................................................错误!未定义书签。
5.1 小车启动/停止 ...............................................................错误!未定义书签。
5.2 小车行程开关 .................................................................错误!未定义书签。
5.3 小车呼叫开关 .................................................................错误!未定义书签。
5.4 编码比较 .........................................................................错误!未定义书签。
运料小车控制(组态软件)

组态软件与网络通讯课程设计说明书题目:运料小车控制姓名:窦晓彤学号:09220331指导老师:冯小林班级:控制工程1班日期:2012年12月23日内容摘要运料小车控制的设计其目的是运用各种软件如力控、VB、Wincc、PLC等多种软件分别实现对运料小车的智能控制,并能通过多种通讯方式实现多种软件之间的通讯,本设计主要以组态软件为主设计了运料小车的控制过程,对过程中各个部件如小车、传送带等进行了定义,并对整体的布局和工作过程进行了控制,通过对动作脚本的编程及其调试过程最终实现了运料小车的控制过程,可以通过开始、停止、手动前进、手动后退、指示标志等多个按键选择实现对运料小车整个运行过程的智能控制,本设计还设计了从组态力控到VB的dbcon通讯,和从VB到力控组态的DDE通讯,实现了各种软件之间的联系与应用,有很重要的意义。
关键词:运料小车、组态力控、VB、控制过程、通讯、联系目录1 设计任务和要求 (1)1.1设计任务 (2)1.2设计要求 (2)2 系统设计 (2)2.1系统要求 (2)2.2方案设计 (2)2.3系统工作原理 (3)3 单元设计与系统设计 (3)3.1 系统各单元界面的设计 (3)3.1.1开发系统界面的创建 (3)3.1.2开机界面的创建 (4)3.1.3主界面的创建 (5)3.2 系统总体设计 (6)3.2.1 IO设备组态 (6)3.2.2 数据库组态 (7)3.2.3单元部件的属性设置及脚本编辑............................................... (8)3.2.4控制系统的属性设置及脚本编辑............................................................ .123.2.5初始启动窗口的选择.............................................................................. (14)4. 系统调试、仿真与结果分析.......................................................... . (14)4.1仿真预期结果............................................................................. . (14)4.2仿真过程及其调试过程............................................................... . (15)4.3仿真结果及其分析 (15)5 . 组态力控与VB之间的通讯 (17)5.1从组态力控到VB之间的通讯 (17)5 .1.1力控中工程项目的创建 (17)5.1.2力控中主界面的创建 (18)5.1.3 IO设备组态 (19)5.1.4 数据库组态 (19)5.1.5 各单元部件的属性设置及脚本编辑............................................ (20)5.1.6 数据库VB中工程项目的创建 (21)5.1.7 从力控到VB的通讯过程 (24)5.2 从组态力控到VB 的通讯 (25)5.2.1 力控中工程项目的创建 (25)5.2.2 数据库VB中工程项目的创建 (28)5.2.3 VB到力控的通讯过程 (29)6 VB与数据采集卡之间的通讯 (30)6.1 VB 从数据采集卡中采集信息 (31)6.1.1 VB主界面的创建及其属性设置 (31)6.2 VB 从数据采集卡采集信息的过程 (32)6.3VB 从数据采集卡采集信息的结果及其分析 (32)7 总结体会 (33)8 参考文献 (33)9 附录 (34)1设计任务和要求1.1设计任务设计一个运料小车,通过组态力控软件的设计,使其可实现通过开始、停止、手动前进、手动后退等按键实现运料小车的智能控制。
PLC课程设计---运料小车控制模拟

1 概述PLC的基本概念在PLC的发展过程中,美国电器制造商协会(NEMA)经过四年的调查,于1980年把这种新型的控制器正式命名为可编程控制器(Programmable Controller),英文缩写为PC,并且作如下定义:“可编程控制器是一种数字运算操作的是的电子系统,专为在工业环境下应用而设计。
它使用可编程序的存储器来存储指令,用来在其内部存储执行逻辑运算,顺序控制,计数,计时和算术运算等操作的指令。
并且通过数字式和模拟式的输入和输出,控制各种类型的机械或生产过程。
PLC及其有关外部设备,都应按易于与工业系统联成一个整体,易于扩充其功能的原则设计。
”定义强调了PLC应直接应用于工业环境,它必须有很强的抗干扰能力,广泛的适应能力和应用范围。
这是区别于一般微机控制系统的一个重要特征。
PLC的发展PLC自问世以来,经过40多年的发展,在美,德,日等工业发达的国家已成为重要的产业之一。
世界总销售额不断上升,生产厂家不断涌现,品种不断翻新,产量产值大幅度上升而价格不断下降。
(目前,世界上有200多个厂家,较有名的公司有美国:AB通用电气,莫迪康公司;日本:三菱,富士,欧姆龙,松下电工等:德国:西门子公司;法国:TE施耐德公司;韩国:三星,LG公司等。
PLC的发展趋势(一)大型化为适应大规模控制系统的要求,大型PLC向着大存储容量,高速度,高性能,增加I|O点数的发展方向。
主要表现在以下几个方面:1.增强网络通信功能:;2.发展智能模块;3.外部故障诊断功能;。
4.编程语言、编程工具标准化、高级化5.实现软件、硬件标准化6.编程组态软件发展迅速(二)小型化发展小型PLC,其目的是为了占领广大的、分散的、中小型的工业控制场合,使PLC不仅成为继电器控制柜的替代物,而且超过继电器控制系统的功能。
小型PLC朝着简易化、体积小、功能强、价格低的方向发展。
PLC的主要功能1.、2.开关量逻辑控制;3.模拟量控制;4.闭环过程控制;5.定时控制;6.计数控制;7.顺序(步进)控制;8.数据处理;9.通信和联网。
运料小车的控制运行

第三章控制系统设计3.1控制系统工作原理运料小车在自动化生产线上运动的控制要求如下:(1)按下启动按钮,系统开始工作,按下停止按钮,系统停止工作;(2)当小车当前所处停靠站的编码小于呼叫按扭HJ的编码时,小车向右运行运行到按钮HJ所对应的停靠站时停止;(3)当小车当前所处停靠站的编码大于呼叫按扭HJ的编码时,小车向左运行,运行到按钮HJ所对应的停靠站时停止;(4)当小车当前所处停靠站的编码等于呼叫按扭HJ的编码时,小车保持不动;呼叫按钮开关HJ1--HJ5应具有互锁功能,先按下者优先。
3.2小车运动分析小车在呼叫按钮之间的运动如图3-2所示,图3-2小车在呼叫按钮之间的运动根据生产工艺要求设计出小车在运料过程中的速度变化情况如图3-3所示,图3-3小车在两呼叫按钮之间运料过程中速度变化情况根据料车运料过程中速度曲线图"确定变频器的频率变化情况如图3-4所示,图3-4变频器的频率变化情况根据系统控制要求,分析出如下系统控制流程图,图3-5控制系统流程图3.3运料小车控制系统的PLC选型和资源配置3.3.1控制系统图控制系统如图3-5所示3.5系统资源分配3.5.1I\O地址分配由于CPU模块有14点数字量输入,10点数字量输出,所以不再需要输入\输出模块。
采用I\O自动分配方式,模块上的输入端子对应的输入地址是X000—X015,输出端子对应的输出地址是Y000—Y011。
3.5.2数字量输入部分这个控制系统的输入有启动按钮开关、停止按钮开关、5个呼叫按钮开关、5个行程3.5.3数字量输出部分这个控制系统需要控制的外部设备只有控制小车运动的三相电动机。
但是电机有正转和反转两种状态,分别对应正转继电器和反转继电器,所以输出点有2个。
具体的输出表3-2输出地址分配3.5.4内部继电器部分3.6系统硬件设计系统硬件接线图如图3-7、3-8所示,按下启动按钮和呼叫按钮后,开始对行程开关数据寄存器D0和呼叫按钮数据寄存器D1中的数据进行比较。
步进指令综合实训8.运料小车模拟控制
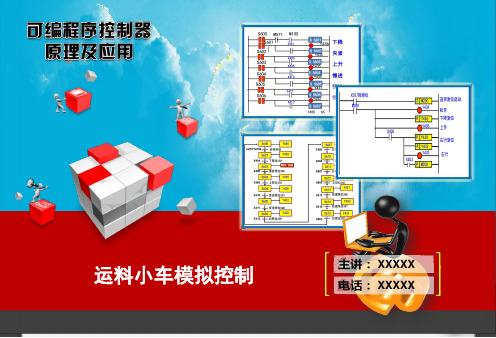
表6-2-8 输入输出I/O分配
输入
输入元件 SB1 功能作用 启动按钮 输入继电器 X000 输出元件 KM1
输出
控制对象 电机正转 输出继电器 Y000
SB2
SQ1 SQ2
停止按钮
前限位 后限位
X001
X002 X003
KM2
运料小车模拟控制
XXXXX XXXXX
任务描述
如图6-2-36所示为运料小车的模拟控制示意图:
图6-2-36
运料小车的模拟控制示意图
任务描述
请根据图6-2-37所示的电路图进行操作,完成下列控制任务:
图6-2-37(a)
小车驱动电机的主电路
任务描述
请根据图6-2-37所示的电路图进行操作,完成下列控制任务:
图6-2-37(b)
运料小车的模拟系统控制电路图
控制要求
SB1为运料小车启动按钮,SB2为停止按钮。按下启
1
动按钮后,运料小车开始运行,按下停止按钮后,
运料小车必须完成当前正在搬运的物料,并返回初
始位置后才能停止工作。
运料小车初始位置要求:运料小车卸料完毕后向左
2
前进2S的位置为运料小车的初始位置。
控制要求
运料小车运行过程:控制系统启动后,运料小车从初始位
置出发,向左前进到限位开关SQ1处停止,料斗的料阀YV1 打开,小车开始装料,5S后小车装料完成,料斗的料阀 YV1自动关闭,小车向右后退到卸料口处的后限位开关SQ2 处停止,小车底门放料阀YV2打开,开始卸料,5S后卸料 完成,小车底门放料阀自动关闭,小车向左前行2S回到初 始位置。如果在此过程中没有按下停止按钮,则运料小车
实训五 装卸料小车的模拟控制

实训五装卸料小车的模拟控制
一、实训目的
1.用FX2N系列PLC按工艺流程写出梯形图、语句表。
2.用模拟设置控制装料小车的自动控制系统。
3.按基本指令编制的程序,进行程序输入并完成系统、调试。
二、实训说明
1. 启动按钮S01用来开启运料小车,停止按钮S02用来立即停止运料小车。
2. 工作流程:
(1)按S01启动按钮,小车装料10秒后,第一次由1号仓送料到2号仓后,停留5秒卸料,然后空车返回到1号仓停留10秒装料;
(2)小车第二次由1号仓送料到3号仓后,停留8秒卸料,然后空车返回1号仓停留10秒装料;
(3)然后在重新工作上述工作过程。
(4)按下S02小车立即停止。
三、实训面板图
四、实训步骤
输入输出端口配置
输入设备输入端口编号
所有的COM端均短接,24V+接V+。
五、设计电路图
六、程序设计。
实验十 运料小车的自动控制实验

实验十运料小车的自动控制实验
专业:08电子信息工程姓名:张磊学号:0828024047 一、实验目的
1.学会用PLC 解决一个实际问题的思路。
2.熟悉PLC 指令的功能。
3.掌握程序设计中起保停电路、自锁电路和互锁电路的设计方法。
二、实验器材
1.FX 系列PLC 一台
2.FX-10P-E 或FX-20P-E 手持编程器一台
3.模拟开关板一块
4.编程电缆
5.连接导线
三、实验原理
运料小车的自动控制可由 PLC 完成。
小车可在甲、乙两地分别启动。
且在甲、乙两地停留时间均为1min。
在甲地起动时小车停车等待装料,然后自动驶向乙地,到达乙地后停车1min 等待卸料,然后返回甲地。
小车从乙地起动时,小车等待1min 等待卸料,然后自
动驶向甲地,在甲地停车1min 等待装料,然后驶向乙地,循环往复。
在运行过程中,小车可在任意位置手动停车,再次起动后,小车重复原来的运动。
此外,在小车前进、后退过程中,分别有指示灯指示其行进方向。
根据实验要求,PLC 的I/O 分配如下表所示
本实验的的梯形图和指令表如下图所示
四、实验步骤和内容 1.按图28 输入程序。
2.检查程序是否正确。
3.运行程序,观察结果是否与要求相符合。
- 1、下载文档前请自行甄别文档内容的完整性,平台不提供额外的编辑、内容补充、找答案等附加服务。
- 2、"仅部分预览"的文档,不可在线预览部分如存在完整性等问题,可反馈申请退款(可完整预览的文档不适用该条件!)。
- 3、如文档侵犯您的权益,请联系客服反馈,我们会尽快为您处理(人工客服工作时间:9:00-18:30)。
实验十八运料小车控制模拟
在运料小车控制模拟实验区完成本实验(THSMS实验扩展箱)
一、实验目的
用PLC构成运料小车控制系统,掌握多种方式控制的编程。
二、运料小车实验面板图图6-18-1所示
运料小车控制模拟控制面板
输入:
启动SD I0.0 停止ST I0.1 装料ZL I0.2
卸料XL I0.3 右行RX I0.4 左行LX I0.5
单步A1 I0.6 单周期A2 I0.7 自动A3 I1.0
手动A4 I1.1
输出:
装料 Q0.0 卸料 Q0.1 右行R1 Q0.2
右行R2 Q0.3 右行R3 Q0.4 左行L1 Q0.5
左行L2 Q0.6 左行L3 Q0.7
三、控制要求
系统启动后,选择手动方式(按下微动按钮A4),通过ZL、XL、RX、LX四个开关的状态决定小车的运行方式。
装料开关ZL为ON,系统进入装料状态,灯S1亮,ZL为OFF,右行开关RX为ON,灯R1、R2、R3依次点亮,模拟小车右行,卸料开关XL为ON,小车进入卸
料,XL为OFF,左行开关LX为ON,灯L1、L2、L3依次点亮,模拟小车左行。
选择自动方式(按下微动按钮A3),系统进入装料->右行->卸料->装料->左行->卸料->装料循环。
选择单周期方式(按下微动按钮A2),小车运行来回一次。
选择单步方式,按一次微动按钮A1一次,小车运行一步。
一、编制梯形图并编写程序
实验参考程序表6-18-1所示
参考梯形图如下所示:
图6-18-2
五、实验设备
1、THSMS-A型、THSMS-B型实验装置或THSMS-1型、THSMS-2型实验箱一台
2、安装了STEP7-Micro/WIN32编程软件的计算机一台
3、PC/PPI编程电缆一根
4、锁紧导线若干
5、THSMS扩展实验箱一台
六、预习要求
阅读实验指导书,复习教材中有关的内容。
七、报告要求
整理出运行和监视程序时出现的现象。