工业管道化学清洗施工工艺标准
管道化学清洗除垢技术

管道化学清洗除垢技术管道化学清洗除垢技术是一种采用化学药剂进行管道清洗和除垢的技术。
这种技术通常用于清洗工业管道,例如:石化、化工、炼油等工业领域中使用的管道。
管道内部积累的沉积物和垢会导致管道内部流量减小,导致管道堵塞、管道失效,从而影响生产效率和安全性。
因此,管道化学清洗除垢技术就显得尤为重要。
管道化学清洗除垢技术的步骤:第一步:管理人员要确定清洗的管道类型、长度、直径、材料和污染物类型等,并明确管道清洗的目的和要求。
第二步:根据管道类型和污染物类型选择适合的化学清洗药剂,比如说:碳酸钠、盐酸和氯酸等。
通常,在清除有机物和沉积物时,可以用醋酸和柠檬酸进行清洗。
第三步:将选好的清洗药剂用适量的水进行稀释,制成清洗药剂。
根据管道长度和直径的不同,使用不同的清洗方式,包括静置法、顺流法和逆流法等。
第四步:在清洗前,必须先将管道内部的水排干,并进行检查,确保管道内部没有残留的水和残留的污垢。
第五步:将清洗药剂从清洗入口注入管道内部,按照清洗计划进行清洗。
清洗时间的长短和清洗剂的使用量取决于管道长度和直径、污垢类型和管道材料等因素。
第六步:在清洗完成后,必须用水将管道内部清洗干净,并用空气或者其他方式将管道内壁吹干,防止水分留下。
管道化学清洗除垢技术的优势:1. 管道化学清洗除垢技术可以有效清除管道内部的各种污垢和沉积物,使得管道清晰、干净。
2. 管道化学清洗除垢技术可以提高管道的效率,减少由于管道堵塞造成的生产停顿时间。
3. 管道化学清洗除垢技术可以延长管道的使用寿命,减少管道故障和损坏。
4. 管道化学清洗除垢技术有时可以避免更加昂贵的替换管道的维修方式。
总的来说,管道化学清洗除垢技术是一种简单、快速、有效的管道清洗方法,使得管道清理更加轻松、安全,同时能够提高工业生产的效率和安全性。
管道清洗工程施工规范
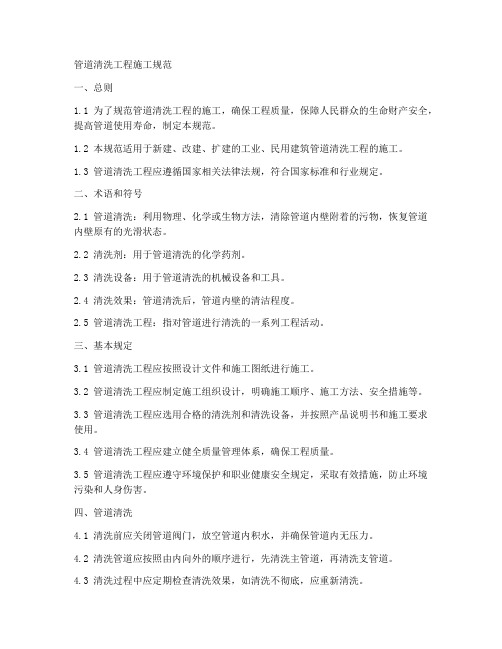
管道清洗工程施工规范一、总则1.1 为了规范管道清洗工程的施工,确保工程质量,保障人民群众的生命财产安全,提高管道使用寿命,制定本规范。
1.2 本规范适用于新建、改建、扩建的工业、民用建筑管道清洗工程的施工。
1.3 管道清洗工程应遵循国家相关法律法规,符合国家标准和行业规定。
二、术语和符号2.1 管道清洗:利用物理、化学或生物方法,清除管道内壁附着的污物,恢复管道内壁原有的光滑状态。
2.2 清洗剂:用于管道清洗的化学药剂。
2.3 清洗设备:用于管道清洗的机械设备和工具。
2.4 清洗效果:管道清洗后,管道内壁的清洁程度。
2.5 管道清洗工程:指对管道进行清洗的一系列工程活动。
三、基本规定3.1 管道清洗工程应按照设计文件和施工图纸进行施工。
3.2 管道清洗工程应制定施工组织设计,明确施工顺序、施工方法、安全措施等。
3.3 管道清洗工程应选用合格的清洗剂和清洗设备,并按照产品说明书和施工要求使用。
3.4 管道清洗工程应建立健全质量管理体系,确保工程质量。
3.5 管道清洗工程应遵守环境保护和职业健康安全规定,采取有效措施,防止环境污染和人身伤害。
四、管道清洗4.1 清洗前应关闭管道阀门,放空管道内积水,并确保管道内无压力。
4.2 清洗管道应按照由内向外的顺序进行,先清洗主管道,再清洗支管道。
4.3 清洗过程中应定期检查清洗效果,如清洗不彻底,应重新清洗。
4.4 清洗后的管道应进行吹扫,确保管道内无残留污物。
4.5 清洗后的管道应进行水质检测,符合设计要求后方可投入使用。
五、施工质量控制5.1 施工过程中应做好施工记录,记录清洗剂的使用量、清洗设备的工作时间等。
5.2 施工结束后应进行工程验收,验收内容包括管道清洗效果、清洗后的水质等。
5.3 验收不合格的管道清洗工程应重新施工,直至达到设计要求。
六、施工安全与环保6.1 施工过程中应严格遵守安全操作规程,防止发生事故。
6.2 施工过程中应做好个人防护,避免接触有害物质。
管道清洗标准
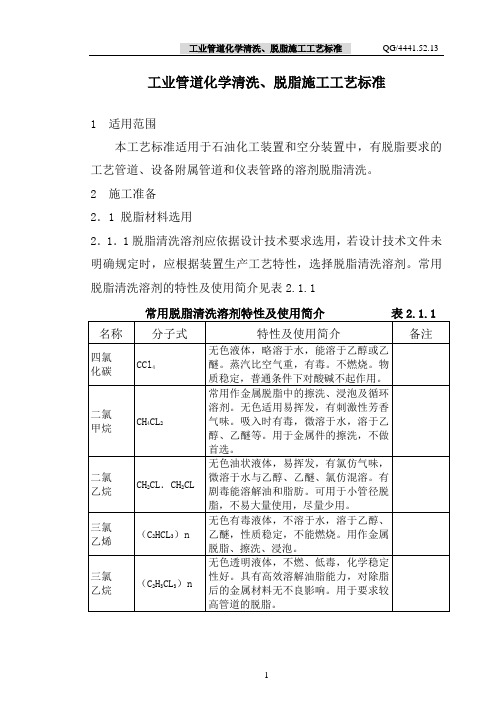
工业管道化学清洗、脱脂施工工艺标准1 适用范围本工艺标准适用于石油化工装置和空分装置中,有脱脂要求的工艺管道、设备附属管道和仪表管路的溶剂脱脂清洗。
2 施工准备2.1 脱脂材料选用2.1.1脱脂清洗溶剂应依据设计技术要求选用,若设计技术文件未明确规定时,应根据装置生产工艺特性,选择脱脂清洗溶剂。
常用脱脂清洗溶剂的特性及使用简介见表2.1.12.1.2 当设计文件未明确规定时,工艺管道的脱脂清洗应根据装置生产工艺特性、清洗工作量、清洗件规格等综合情况确定清洗方法和清洗溶剂种类。
清洗溶剂选用应遵循以下原则:a.选用擦洗方式进行脱脂时,应选用四氯化碳或三氯乙烯清洗剂;b.选用浸泡方式进行脱脂时,应选用四氯化碳或三氯乙烷清洗剂;c.选用循环清洗方式进行脱脂时,应选用用四氯化碳清洗剂。
2.1.3 对化验分析管和仪表导压、取样毛细管的清洗,宜选用挥发性较低、毒性较小且不易燃烧的三氯乙烷做清洗脱脂剂。
2.1.4 若配管、阀门、调节阀、管路附件油脂较重、内壁较脏时,应选用工业用金属清洗剂(5F386型金属清洗剂、水配比为3%~5%),在正式脱脂清洗前进行一次粗清洗。
2.2 机具设备2.2.1 循环清洗工作站一套(由一台耐蚀酸泵,一个溶剂罐及连接管路组成),非机动循环清洗装置二套(由一个溶剂罐及临时气源组成)。
2.2.2 其它工器具、塑料桶、白铁盘、毛刷、脱脂纱布及必备劳保用品等。
2.2.3 质量检查用黑光灯一套,YX—125携带式萤光探伤仪一台。
2.3 技术准备2.3.1 应根据设计文件要求或标准规范规定,对装置中需进行清洗脱脂的系统部位进行详细的统计,并根据其工艺介质特性和工艺流程特点,确定清洗方法,选择清洗溶剂,并编制详细的清洗脱脂施工技术方案,确定质量控制程序。
2.3.2 由工程技术人员负责向施工作业人员进行详细的施工技术交底。
使作业人员了解掌握清洗方法、步骤、范围和清洗脱脂的技术要求、质量标准、安全防护及产品保护等要求内容。
管道系统吹洗工艺标准
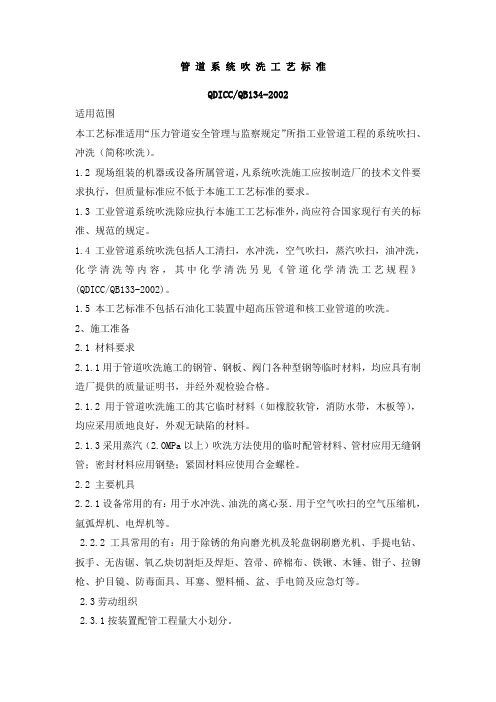
管道系统吹洗工艺标准QDICC/QB134-2002适用范围本工艺标准适用“压力管道安全管理与监察规定”所指工业管道工程的系统吹扫、冲洗(简称吹洗)。
1.2 现场组装的机器或设备所属管道,凡系统吹洗施工应按制造厂的技术文件要求执行,但质量标准应不低于本施工工艺标准的要求。
1.3 工业管道系统吹洗除应执行本施工工艺标准外,尚应符合国家现行有关的标准、规范的规定。
1.4 工业管道系统吹洗包括人工清扫,水冲洗,空气吹扫,蒸汽吹扫,油冲洗,化学清洗等内容,其中化学清洗另见《管道化学清洗工艺规程》(QDICC/QB133-2002)。
1.5 本工艺标准不包括石油化工装置中超高压管道和核工业管道的吹洗。
2、施工准备2.1 材料要求2.1.1用于管道吹洗施工的钢管、钢板、阀门各种型钢等临时材料,均应具有制造厂提供的质量证明书,并经外观检验合格。
2.1.2 用于管道吹洗施工的其它临时材料(如橡胶软管,消防水带,木板等),均应采用质地良好,外观无缺陷的材料。
2.1.3采用蒸汽(2.OMPa以上)吹洗方法使用的临时配管材料、管材应用无缝钢管;密封材料应用钢垫;紧固材料应使用合金螺栓。
2.2 主要机具2.2.1设备常用的有:用于水冲洗、油洗的离心泵.用于空气吹扫的空气压缩机,氩弧焊机、电焊机等。
2.2.2工具常用的有:用于除锈的角向磨光机及轮盘钢刷磨光机、手提电钻、扳手、无齿锯、氧乙炔切割炬及焊炬、笤帚、碎棉布、铁锹、木锤、钳子、拉铆枪、护目镜、防毒面具、耳塞、塑料桶、盆、手电筒及应急灯等。
2.3劳动组织2.3.1按装置配管工程量大小划分。
1)配管量在50Km以内,应有 12-16名管工, 2名电焊工和1名气焊工组成吹洗专业班组进行实施。
2)配管量在50Km-100Km之间,应有20-26名管工, 4名电焊工和2名气焊工组成两个吹洗作业班组,并配备适当辅助工。
2.3.2吹洗工作应按装置工艺系统划分,并以吹洗方法、类别分工组织,按工序计划有序实施。
管道清洗规范
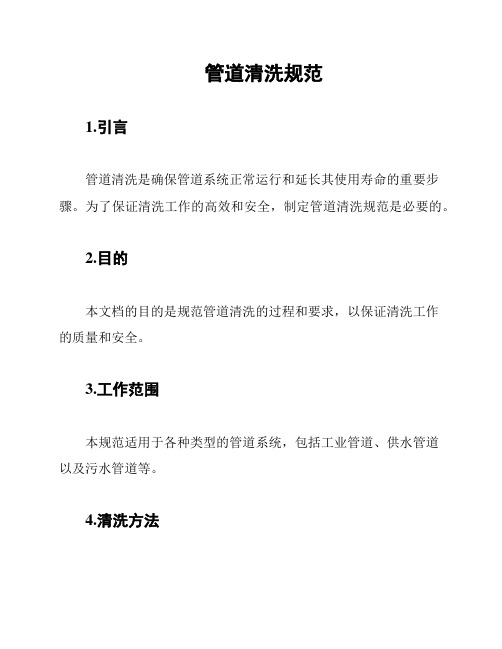
管道清洗规范1.引言管道清洗是确保管道系统正常运行和延长其使用寿命的重要步骤。
为了保证清洗工作的高效和安全,制定管道清洗规范是必要的。
2.目的本文档的目的是规范管道清洗的过程和要求,以保证清洗工作的质量和安全。
3.工作范围本规范适用于各种类型的管道系统,包括工业管道、供水管道以及污水管道等。
4.清洗方法根据管道系统的不同类型和材质,选择合适的清洗方法,包括但不限于以下几种:- 水冲洗:利用高压水流进行冲洗,去除管道内的污物和沉积物。
- 化学清洗:使用适当的清洗剂,对管道进行化学清洗,去除污物和污垢。
- 机械清洗:使用刷子、钢丝球等机械工具对管道进行清洗。
5.清洗步骤管道清洗的步骤如下:1. 确定清洗的目标和要求。
2. 准备清洗所需的设备和材料。
3. 关闭管道系统,并排除安全隐患。
4. 根据清洗方法选择合适的清洗工具和清洗剂。
5. 进行管道清洗,注意操作安全和清洗质量。
6. 排放清洗液和废弃物,确保环境保护和安全。
7. 检查清洗效果和系统的运行情况。
8. 如有需要,进行后续的维护和保养。
6.清洗安全在进行管道清洗时,应注意以下安全事项:- 戴上适当的个人防护用具,包括手套、护目镜和防护服等。
- 确保清洗设备和工具的正常工作和安全使用。
- 遵守操作规程,避免操作失误和事故发生。
- 注意防止清洗剂对环境和人体造成危害。
7.清洗记录对每次管道清洗进行记录,包括清洗时间、清洗方法、清洗剂使用情况以及清洗效果等信息。
清洗记录应妥善保留,以备查阅和追溯。
8.总结制定管道清洗规范对于确保管道系统的正常运行和延长使用寿命具有重要意义。
遵守本规范的要求,能够提高清洗工作的效率和安全性。
以上是对管道清洗规范的简要介绍,详细的规范内容和具体操作细节请参考相关文件和标准。
HGT2387-2007工业设备化学清洗质量标准

HGT2387-2007工业设备化学清洗质量标准工业设备化学清洗质量标准 HG/T2387-20071.范围本标准规定了工业设备化学清洗的技术要求、质量指标和试验方法。
适用于碳钢、不锈钢、紫铜及铜合金、铝及铝合金等材质的工业设备表面形成的水垢、锈垢、油垢及其它污垢的化学清洗。
物料垢化学清洗和其它材料制工业设备污垢的化学清洗可参照执行。
2.规范性引用文件本标准引用以下文件中的条款。
注日期的引用文件,其随后的修改单或修订版不适用于本标准,但鼓励使用最新版本。
不注日期的引用文件,其最新版本适用于本标准。
GB8978 污水综合排放标准GB8923 涂装前钢材表面锈蚀等级和除锈等级DL/T 794 火力发电厂锅炉化学清洗导则HG/T3523 冷却水化学处理标准腐蚀试片技术条件HG 脱脂工程施工及验收规范JB/T6074 腐蚀试样的制备、清洗和评定SH/T3517 石油化工钢制管道工程施工工艺标准3.术语和定义以下术语和定义只适用于本标准。
3.1 化学清洗采用化学药剂及其水溶液与被清洗设备或管线表面污垢发生化学反应而去除污垢的方法。
3.2 K—腐蚀率化学药剂及其水溶液与被清洗设备或管线的金属接触时金属被腐蚀的相对速率。
腐蚀率可用单位时间内单位面积上的金属腐蚀的质量表示:克每平方米每小时或 g/(m2?h)。
3.3 η—缓蚀率测定缓蚀剂缓蚀性能的参数。
η=3.4 A-腐蚀量化学清洗过程中,化学药剂及其水溶液与被清洗设备或管线的金属接触时金属单位面积上被腐蚀的质量。
腐蚀量单位为:克每平方米(g/m2)。
3.5 N—除垢率被洗除的垢量与清洗前原有垢量之比的百分数(%)。
3.6 B—洗净率清洗设备表面经化学清洗后除掉污垢的面积与清洗前原污垢覆盖面积之比的百分数(%)。
3.7 监视管管道内用于监视清洗液流量、压力、温度等参数的管道。
在化学清洗施工过程中,需要使用一段管子来监视清洗进度和测定除垢率。
这段管子应该从被清洗设备上割取,并且上面附着的污垢应该能代表该设备的结垢特点。
工业化工管道清洗方法

工业化工管道清洗方法随着工业化进程的不断发展,工业生产过程中产生的废水、废气和工业废料等对环境的污染情况日益严重。
工业管道清洗是一项重要的环境保护工作,对于保证生产过程的正常运行和保护环境具有重要意义。
下面将介绍一些常见的工业管道清洗方法。
1.水冲洗法水冲洗法是一种常见的清洗方法,适用于一般工业管道的清洗。
通过高压水流对管道内部进行冲洗,可以有效地清除管道内的污垢和残留物。
这种方法操作简单、成本低,不会对环境造成二次污染。
2.化学清洗法化学清洗法是利用化学试剂对管道进行清洗的方法。
根据管道内部的污垢性质和特点选择合适的化学试剂,通过化学反应溶解或氧化管道内的污垢和残留物,达到清洗的目的。
化学清洗法能够彻底清除管道内的污垢,但需要注意选择合适的化学试剂,以免对环境造成污染。
3.蒸汽清洗法蒸汽清洗法是利用高温蒸汽对管道进行清洗的方法。
蒸汽具有很强的杀菌和溶解力,可以快速清除管道内的污垢和残留物。
蒸汽清洗法能够达到较高的清洁效果,但需要注意控制蒸汽的温度和压力,以免对管道造成损坏。
4.其他清洗方法除了上述常见的清洗方法,还有一些其他的清洗方法值得一提。
例如,超声波清洗法利用超声波的震动力对管道进行清洗;机械刷洗法利用机械刷子对管道内壁进行刷洗。
这些方法在特定情况下可以起到很好的清洗效果,但需要根据具体情况选择合适的方法。
无论采用何种方法进行工业管道清洗,都需要注意以下几点:1.安全防护:清洗过程中需要做好相关的安全防护工作,避免工作人员受到污染物和清洗剂的伤害。
2.废物处理:清洗完成后,需将清洗过程中产生的废水、废气和废料进行合理的处理,以免对环境造成更大的污染。
3.定期清洗:工业管道应定期进行清洗,以防止污垢和残留物的积累,保证管道的正常运行。
总之,工业管道清洗对于保护环境和确保生产过程的正常进行具有重要意义。
在选择清洗方法时,需要根据管道的特点和清洗目的进行合理选择,并注意相关安全和环境保护措施的落实。
化学清洗施工方案模板
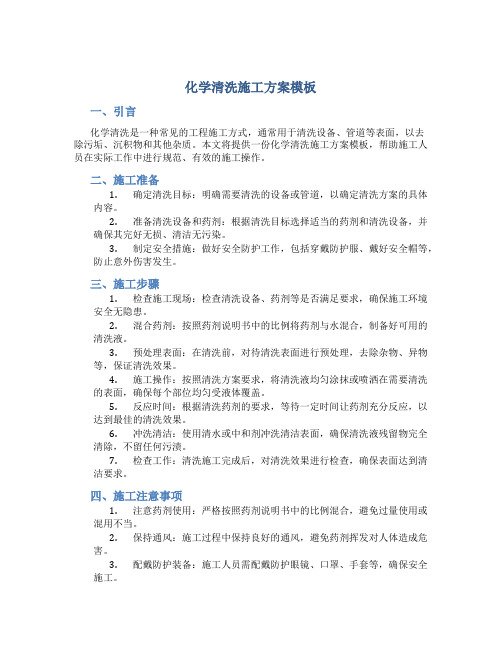
化学清洗施工方案模板一、引言化学清洗是一种常见的工程施工方式,通常用于清洗设备、管道等表面,以去除污垢、沉积物和其他杂质。
本文将提供一份化学清洗施工方案模板,帮助施工人员在实际工作中进行规范、有效的施工操作。
二、施工准备1.确定清洗目标:明确需要清洗的设备或管道,以确定清洗方案的具体内容。
2.准备清洗设备和药剂:根据清洗目标选择适当的药剂和清洗设备,并确保其完好无损、清洁无污染。
3.制定安全措施:做好安全防护工作,包括穿戴防护服、戴好安全帽等,防止意外伤害发生。
三、施工步骤1.检查施工现场:检查清洗设备、药剂等是否满足要求,确保施工环境安全无隐患。
2.混合药剂:按照药剂说明书中的比例将药剂与水混合,制备好可用的清洗液。
3.预处理表面:在清洗前,对待清洗表面进行预处理,去除杂物、异物等,保证清洗效果。
4.施工操作:按照清洗方案要求,将清洗液均匀涂抹或喷洒在需要清洗的表面,确保每个部位均匀受液体覆盖。
5.反应时间:根据清洗药剂的要求,等待一定时间让药剂充分反应,以达到最佳的清洗效果。
6.冲洗清洁:使用清水或中和剂冲洗清洁表面,确保清洗液残留物完全清除,不留任何污渍。
7.检查工作:清洗施工完成后,对清洗效果进行检查,确保表面达到清洁要求。
四、施工注意事项1.注意药剂使用:严格按照药剂说明书中的比例混合,避免过量使用或混用不当。
2.保持通风:施工过程中保持良好的通风,避免药剂挥发对人体造成危害。
3.配戴防护装备:施工人员需配戴防护眼镜、口罩、手套等,确保安全施工。
4.处理废物:清洗结束后,将废弃的药剂和污染物妥善处理,避免对环境造成污染。
五、施工总结化学清洗作为一种常见的施工方式,在工程领域具有广泛应用。
本文提供的化学清洗施工方案模板,可作为施工人员在实际操作中的参考,帮助他们规范、高效地完成清洗任务。
施工人员在进行化学清洗时应严格按照规范操作,做好安全防护,确保施工质量和人员安全。
管道清洗标准验收
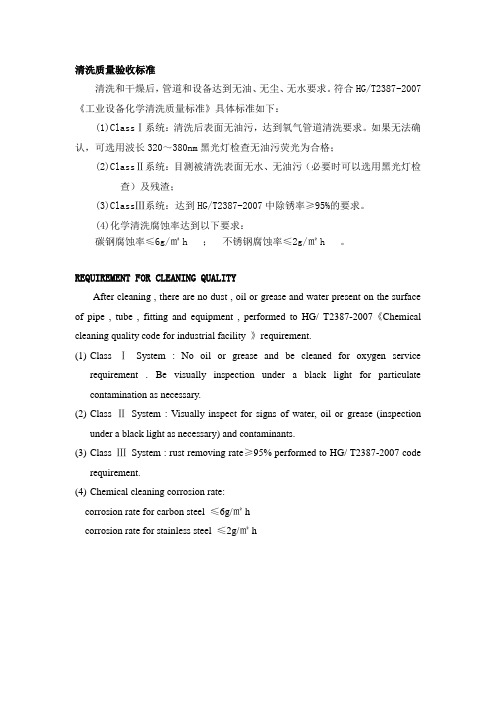
清洗质量验收标准清洗和干燥后,管道和设备达到无油、无尘、无水要求。
符合HG/T2387-2007《工业设备化学清洗质量标准》具体标准如下:(1)ClassⅠ系统:清洗后表面无油污,达到氧气管道清洗要求。
如果无法确认,可选用波长320~380nm黑光灯检查无油污荧光为合格;(2)ClassⅡ系统:目测被清洗表面无水、无油污(必要时可以选用黑光灯检查)及残渣;(3)ClassⅢ系统:达到HG/T2387-2007中除锈率≥95%的要求。
(4)化学清洗腐蚀率达到以下要求:碳钢腐蚀率≤6g/㎡h ;不锈钢腐蚀率≤2g/㎡h 。
REQUIREMENT FOR CLEANING QUALITYAfter cleaning , there are no dust , oil or grease and water present on the surface of pipe , tube , fitting and equipment , performed to HG/ T2387-2007《Chemical cleaning quality code for industrial facility 》requirement.(1)Class ⅠSystem : No oil or grease and be cleaned for oxygen servicerequirement . Be visually inspection under a black light for particulate contamination as necessary.(2)Class ⅡSystem : Visually inspect for signs of water, oil or grease (inspectionunder a black light as necessary) and contaminants.(3)Class ⅢSystem : rust removing rate≥95% performed to HG/ T2387-2007 coderequirement.(4)Chemical cleaning corrosion rate:corrosion rate for carbon steel ≤6g/㎡hcorrosion rate for stainless steel ≤2g/㎡h。
工业管道清洁施工方案
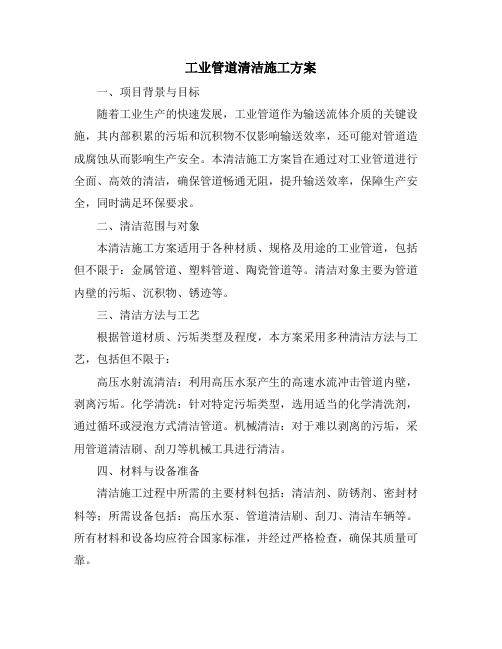
工业管道清洁施工方案一、项目背景与目标随着工业生产的快速发展,工业管道作为输送流体介质的关键设施,其内部积累的污垢和沉积物不仅影响输送效率,还可能对管道造成腐蚀从而影响生产安全。
本清洁施工方案旨在通过对工业管道进行全面、高效的清洁,确保管道畅通无阻,提升输送效率,保障生产安全,同时满足环保要求。
二、清洁范围与对象本清洁施工方案适用于各种材质、规格及用途的工业管道,包括但不限于:金属管道、塑料管道、陶瓷管道等。
清洁对象主要为管道内壁的污垢、沉积物、锈迹等。
三、清洁方法与工艺根据管道材质、污垢类型及程度,本方案采用多种清洁方法与工艺,包括但不限于:高压水射流清洁:利用高压水泵产生的高速水流冲击管道内壁,剥离污垢。
化学清洗:针对特定污垢类型,选用适当的化学清洗剂,通过循环或浸泡方式清洁管道。
机械清洁:对于难以剥离的污垢,采用管道清洁刷、刮刀等机械工具进行清洁。
四、材料与设备准备清洁施工过程中所需的主要材料包括:清洁剂、防锈剂、密封材料等;所需设备包括:高压水泵、管道清洁刷、刮刀、清洁车辆等。
所有材料和设备均应符合国家标准,并经过严格检查,确保其质量可靠。
五、安全防护措施为确保清洁施工过程中的安全,应采取以下防护措施:施工人员应佩戴防护眼镜、手套、口罩等个人防护用品。
清洁施工现场应设置警示标识,禁止非施工人员进入。
定期对清洁设备进行检查和维护,确保其安全性能。
六、清洁流程与时间表清洁流程主要包括:准备工作→管道检查→清洁方法选择→清洁施工→质量检查→清理现场→验收。
具体时间表应根据管道长度、污垢程度及施工条件等因素进行合理安排。
七、质量检测与验收清洁施工完成后,应对管道进行全面检查,确保管道内壁无残留污垢、光滑洁净。
同时,应对管道进行压力测试,确保其密封性和承压能力。
只有当管道通过质量检测和验收后,方可视为清洁施工完成。
八、环境影响评估清洁施工过程中应注意减少对环境的影响,如减少化学清洗剂的使用量、合理处理废水和废渣等。
管道清洗工程施工技术规程

管道清洗工程施工技术规程1. 总则管道清洗工程是为了确保管道系统畅通、安全、高效运行,提高管道设备的使用寿命,保障生产、生活用水质量,降低管道系统维修保养成本而进行的一项重要工作。
本规程适用于各类工业、民用建筑物中的给水排水管道、消防管道、空调水管道等清洗工程。
2. 术语2.1 管道清洗:采用物理、化学或生物方法,清除管道内壁附着物,恢复管道内壁光洁度的过程。
2.2 清洗剂:用于清洗管道的化学制剂,包括溶剂、酸碱剂、表面活性剂等。
2.3 清洗设备:用于管道清洗的机械设备,包括清洗车、清洗泵、清洗枪等。
3. 施工准备3.1 资料准备:收集相关管道的设计图纸、施工记录、维修记录等资料,了解管道系统的结构、功能和运行状况。
3.2 人员准备:根据工程规模和难度,配备足够数量的具备相关专业技能和经验的施工人员。
3.3 设备准备:根据工程需求,准备相应的清洗设备、防护设备、检测设备等。
3.4 材料准备:根据工程需求,准备相应的清洗剂、防护剂、堵漏材料等。
4. 清洗方法4.1 物理清洗:采用高压水射流、超声波、机械刮擦等物理方法清洗管道内壁。
4.2 化学清洗:采用酸碱剂、表面活性剂等化学制剂,通过浸泡、循环等方式清洗管道内壁。
4.3 生物清洗:采用生物酶等生物制剂,通过生物降解作用清洗管道内壁。
5. 清洗步骤5.1 管道冲洗:打开管道阀门,利用清水对管道进行冲洗,将管道内的杂物冲出。
5.2 管道检测:通过视频检测、人工检查等方式,了解管道内壁的清洗情况。
5.3 清洗剂配置:根据管道材质、污垢性质等因素,合理配置清洗剂。
5.4 清洗施工:将清洗剂倒入管道内,采用清洗设备进行清洗,确保清洗剂与管道内壁充分接触。
5.5 清洗效果评估:清洗完成后,对管道内壁进行检测,评估清洗效果。
6. 施工安全与环保6.1 施工过程中,应严格遵守国家和地方有关安全生产的法律、法规和规定,确保施工安全。
6.2 施工过程中,应采取有效措施,防止清洗剂、废水等对环境造成污染。
压力管道的管道清洗技术及其要求
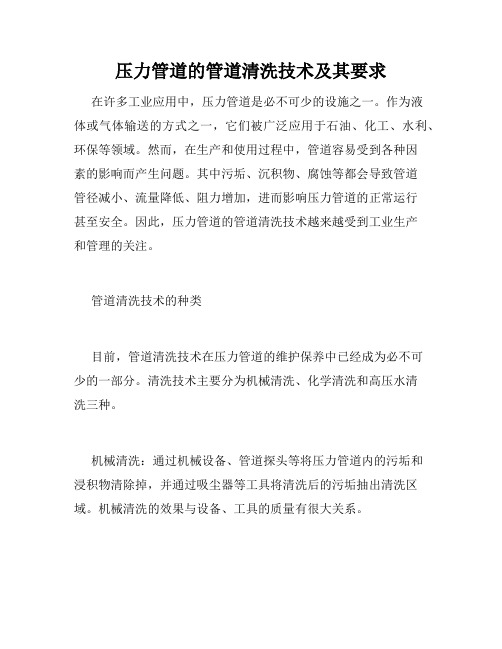
压力管道的管道清洗技术及其要求在许多工业应用中,压力管道是必不可少的设施之一。
作为液体或气体输送的方式之一,它们被广泛应用于石油、化工、水利、环保等领域。
然而,在生产和使用过程中,管道容易受到各种因素的影响而产生问题。
其中污垢、沉积物、腐蚀等都会导致管道管径减小、流量降低、阻力增加,进而影响压力管道的正常运行甚至安全。
因此,压力管道的管道清洗技术越来越受到工业生产和管理的关注。
管道清洗技术的种类目前,管道清洗技术在压力管道的维护保养中已经成为必不可少的一部分。
清洗技术主要分为机械清洗、化学清洗和高压水清洗三种。
机械清洗:通过机械设备、管道探头等将压力管道内的污垢和浸积物清除掉,并通过吸尘器等工具将清洗后的污垢抽出清洗区域。
机械清洗的效果与设备、工具的质量有很大关系。
化学清洗:用化学物质对管道内部的沉积物和腐蚀产物进行清洗的方法。
根据不同的清洗对象,可以选择不同的清洗剂和工艺。
化学清洗能够极大地提高清洗效率,但是也对环境造成一定的危害。
高压水清洗:利用高压水来清洗压力管道内部。
高压水清洗是一种高效、环保、经济的管道清洗技术。
通过比较试验,发现高压水清洗在清洗效率、清洗安全、操作便捷等方面具有优势,是压力管道清洗技术中的一种高效工艺。
管道清洗技术的要求管道清洗技术虽然有不同的分类,但无论是机械清洗、化学清洗还是高压水清洗都需要从以下几个方面考虑。
安全性要求:管道清洗是一项较为危险的作业,需要对操作人员进行专业的培训和防护措施。
同时需要对清洗区域进行规范化管理,避免安全事故的发生。
清洗效果:管道清洗的主要目的是将管道内的污垢和沉积物清除掉,保证管道的正常运行和使用寿命。
因此,要求清洗后的管道内壁平整、光滑、无残留,达到预期的清洗效果。
清洗耐用性:随着压力管道的使用,管道内表面可能会形成新的沉积物和污垢,这就要求清洗后的管道内壁能够长时间保持清洁状态,降低二次清洗的需求。
环保要求:管道清洗涉及到一定的化学品和废水产生,需要严格按照环保法规进行管理和处理,避免对环境造成不良影响。
管道化学清洗工艺规程
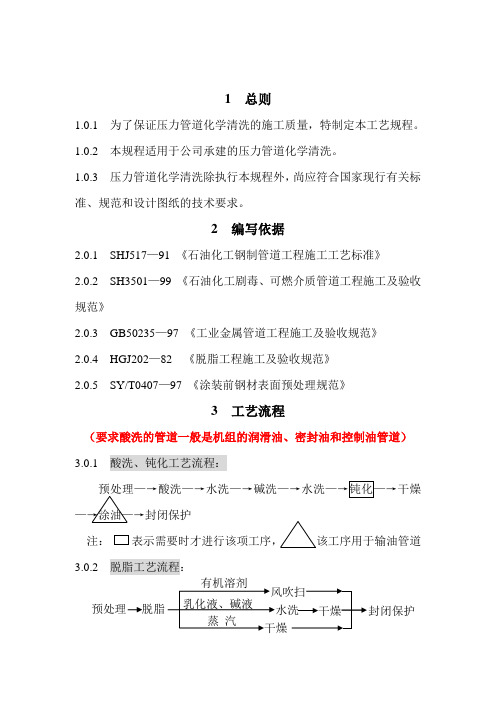
1 总则1.0.1 为了保证压力管道化学清洗的施工质量,特制定本工艺规程。
1.0.2 本规程适用于公司承建的压力管道化学清洗。
1.0.3 压力管道化学清洗除执行本规程外,尚应符合国家现行有关标准、规范和设计图纸的技术要求。
2 编写依据2.0.1 SHJ517—91 《石油化工钢制管道工程施工工艺标准》2.0.2 SH3501—99 《石油化工剧毒、可燃介质管道工程施工及验收规范》2.0.3 GB50235—97 《工业金属管道工程施工及验收规范》2.0.4 HGJ202—82 《脱脂工程施工及验收规范》2.0.5 SY/T0407—97 《涂装前钢材表面预处理规范》3 工艺流程(要求酸洗的管道一般是机组的润滑油、密封油和控制油管道)3.0.1 酸洗、钝化工艺流程:—→涂油—→封闭保护注:表示需要时才进行该项工序, 该工序用于输油管道 3.0.2 脱脂工艺流程:封闭保护4 化学清洗要求4.1一般规定4.1.1 需要化学清洗的管道,其范围和质量要求应符合设计文件的规定。
(一般是机组厂家的随机资料中要求的,要看厂家的随机资料)4.1.2 管道进行化学清洗时,必须与无关设备隔离。
(防止酸洗液进入无关系统造成事故)4.1.3 化学清洗液的配方必须经过鉴定,并曾在生产装置中使用过,经实践证明是有效和可靠的。
(配方)4.1.4 化学清洗时,操作人员应着专用防护服装,并应根据不同清洗液对人体的危害佩带护目镜、防毒面具等防护用具。
(安全要求)4.1.5 化学清洗合格的管道,当不能及时投入运行时,应进行封闭或充氮保护。
(封闭保护)4.1.6 化学清洗后的废液处理和排放应符合环境保护的规定。
(不得随意排放)4.2 酸洗钝化工艺要求4.2.1 管道内表面有特殊清洁要求的油管道或其它管道,一般在投产前可采用槽浸法或系统循环法进行酸洗。
4.2.2 当管道内表面有明显油斑时,酸洗前应进行必要的预除油处理,一般可用5%的碳酸钠溶液清除油污。
工业管道施工工艺标准

工业管道施工工艺标准酒店群工程部2014年3月目录一、不锈钢管道施工工艺标准 (4)1、施工准备 (4)2、操作工艺要求 (11)3、质量标准 (18)二、衬里工业管道施工工艺标准 (21)1、施工准备 (21)2、安装工艺流程图 (22)3、质量要求: (30)三、热力管道安装施工工艺标准 (32)1、施工准备 (32)2、工艺流程 (33)3、操作要求 (33)4、质量标准 (35)四、碳素钢管道施工工艺标 (37)1、施工准备 (37)2、操作要点 (38)3、质量要求 (58)4、安全要求 (60)五、燃气管道安装施工工艺标准 (62)1、施工准备 (62)2、工艺流程 (66)4、质量标准 (84)5、安全要求 (86)一、不锈钢管道施工工艺标准1、施工准备1.1常用材料1)不锈钢管分为三类。
按添加的金属元素不同分为:铬不锈钢、铬镍不锈钢和铬锰氮系列不锈钢。
按耐腐蚀性能分为:耐大气腐蚀、耐酸碱腐蚀和耐高温等不锈钢。
按不锈钢的金相组织分为:马氏体、铁素体、奥氏体加铁素体、奥氏体和沉淀硬化型钢。
2)不锈钢的牌号有:1Crl3,2Crl3,1Crl7,Cr25Ti,Cr28, 1Crl8Ni,1Crl8Ni9Ti,Crl8Nil2Mo2,Crl8Nil3Mo2Ti,1Cr21Ni5Ti, Cr23Nil8,Crl7Mn13Mo2N,Crl8Mn8Ni5N,Crl8Mn10Ni5Mo2N,00Crl8Nil0,0Cr18Ni10Ti, 00Crl7Nil3Mo2,Cr18Ni100Crl7Nil3Mo3。
3)不锈钢管具有较高的电极电位、表面致密的氧化膜和均匀的内部组织以及很高的耐腐蚀性能。
在常温下,不锈钢管能抗浓度在95%以下的硝酸、80%-100%的硫酸、10%的铬酸、70%以下的氢氧化钠等介质的腐蚀。
它被广泛地用于航空、原子能、化工、化肥、化纤、石油、医药等工业装置的工艺管道上。
1.2不锈钢管规格见GB2270—80、GB3090—82、GB3089-82。
(完整版)管道清洁施工方案(最新)

(完整版)管道清洁施工方案(最新)管道清洁施工方案(完整版)1. 方案背景管道清洁是确保工业设备和生活设施正常运行的重要步骤。
随着时间的推移,管道内部会积累沉积物,这可能导致流量减少、堵塞和污染等问题。
因此,有必要定期进行管道清洁施工,以保持管道系统的良好状态。
2. 方案目标本方案旨在提供一种有效的管道清洁施工方案,以确保管道系统的顺畅运行和安全性。
具体目标包括:- 清除管道内的沉积物和堵塞物,恢复管道的正常流量。
- 防止管道腐蚀和污染的发生。
- 提高管道系统的可靠性和工作效率。
3. 方案步骤3.1 管道评估在施工之前,需要对管道系统进行全面评估。
评估包括以下步骤:1. 管道检查:通过使用合适的工具和设备对管道进行内外部检查,以确定堵塞、破损或腐蚀的部位。
2. 流量测试:测量管道的流量和压力,以确定系统的性能问题。
3. 沉积物采样:采集管道内的沉积物样本进行实验室分析,以确定其成分和性质。
3.2 施工准备在施工之前,需要进行准备工作以确保施工的顺利进行。
准备工作包括以下步骤:1. 清除工作区域:清除周围的杂物和障碍物,以确保施工人员的安全。
2. 管道隔离:根据需要,通过关闭相应的阀门或使用临时封堵设备将管道隔离,以避免施工过程中的泄漏和交叉污染。
3. 工具和设备准备:准备所需的清洁工具、保护装备和施工设备。
3.3 清洁施工操作根据管道评估的结果,选择合适的清洁方法进行施工。
常见的清洁方法包括:1. 高压水冲洗:使用高压水流冲洗管道,以清除沉积物和堵塞物。
2. 化学清洗:使用合适的化学溶剂和清洗剂对管道进行清洗,以溶解沉积物和清除腐蚀。
3. 机械清洗:使用旋转刷、钢丝球等机械工具对管道进行刷洗,以彻底清除堵塞和污垢。
3.4 施工结束清洁施工完成后,需要进行以下工作:1. 清理工作区域:清理施工现场,排除临时设备和材料。
2. 管道检查:再次对管道进行检查,确保清洁施工达到预期效果。
3. 系统启动:重新启动管道系统,并进行流量和压力测试,以验证清洁施工的效果。
(全面版)最新管道清洁施工设计
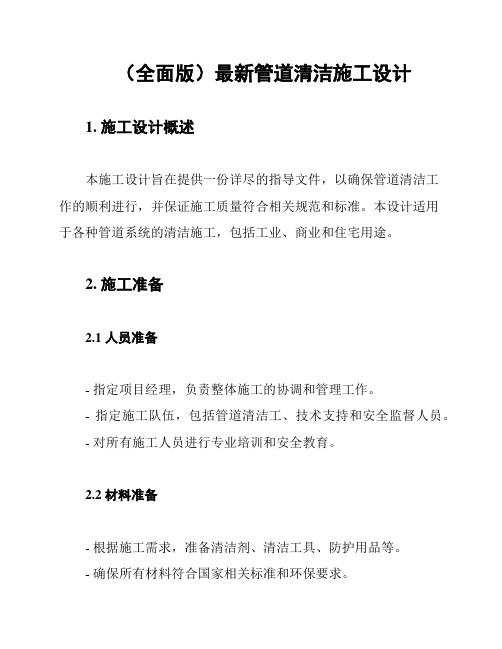
(全面版)最新管道清洁施工设计1. 施工设计概述本施工设计旨在提供一份详尽的指导文件,以确保管道清洁工作的顺利进行,并保证施工质量符合相关规范和标准。
本设计适用于各种管道系统的清洁施工,包括工业、商业和住宅用途。
2. 施工准备2.1 人员准备- 指定项目经理,负责整体施工的协调和管理工作。
- 指定施工队伍,包括管道清洁工、技术支持和安全监督人员。
- 对所有施工人员进行专业培训和安全教育。
2.2 材料准备- 根据施工需求,准备清洁剂、清洁工具、防护用品等。
- 确保所有材料符合国家相关标准和环保要求。
2.3 设备准备- 准备清洁设备,如高压水枪、吸尘器、管道机器人等。
- 确保设备性能良好,并经过安全检查。
2.4 现场准备- 与业主沟通,确定施工时间和入场日期。
- 准备施工所需的基础设施,如临时电源、水源等。
- 对施工区域进行安全围挡,确保施工安全。
3. 施工流程3.1 管道检查- 对管道系统进行全面检查,了解其结构、材质和污垢情况。
- 记录检查结果,为后续清洁工作提供依据。
3.2 管道预处理- 针对不同类型的污垢,选择合适的预处理方法,如化学清洗、物理研磨等。
- 预处理过程中,确保人员安全和环境保护。
3.3 清洁施工- 根据预处理结果,选择合适的清洁方法和设备。
- 执行清洁操作,确保清洁效果符合要求。
3.4 管道冲洗- 在清洁完成后,对管道进行冲洗,确保清洁残留物被彻底清除。
- 冲洗过程中,检查管道系统是否有损坏或漏水现象。
3.5 验收- 施工完成后,组织验收工作,确保施工质量符合规范和业主要求。
- 对验收结果进行记录,并为后续的维护提供参考。
4. 施工安全- 制定详细的安全计划,包括人员安全、环境保护、火灾预防等。
- 严格执行安全规定,确保施工过程中的安全。
5. 施工质量控制- 制定详细的质量控制计划,包括质量标准、检查方法和整改措施。
- 执行质量控制措施,确保施工质量符合要求。
6. 施工进度管理- 制定详细的施工进度计划,包括施工阶段、时间表和关键节点。
管道除垢清洗方案

管道除垢清洗方案一、清洗内容:循环水管道。
二、清洗时间:三天左右。
三、清洗验收标准:清洗结束后经双方验收符合《HG/T 2387—92 工业设备化学清洗质量标准》中的有关规定,除垢率:(1)、清洗以碳酸盐为主的水垢,除垢面积应达到原水垢覆盖面积的90%以上。
(2)、清洗硅酸盐或硫酸盐水垢,除垢面积应达到原水垢覆盖面积的60%以上。
(3)粘泥及藻类清除率80%以上。
四、清洗工艺流程:(一)、冷却水、冷媒水系统清洗工艺流程一、停机清洗水冲洗—杀菌灭藻清洗——使用“惠施通”WL102-2除垢剂清洗——清洗后冲洗——预膜——清洗后的清理。
1、水冲洗水冲洗的目的是用大流量的水尽可能冲洗掉管道中的灰尘、泥沙、脱落的藻类及腐蚀物等疏松的污垢,同时检查系统的泄漏情况。
冲洗水的流速以大于0.15m/s为宜,冲洗合格后排尽系统内的冲洗水。
2、杀菌灭藻粘泥剥离清洗杀菌灭藻清洗的目的是杀死系统内的微生物,并使管道表面附着的生物粘泥剥落脱离。
排掉冲洗水后将管道内加入杀菌灭藻剂进行清洗,当管道中的浊度趋于平衡时停止清洗。
3、“惠施通”WL102-2型除垢剂除垢清洗使用“惠施通”WL102-2型除垢剂清洗的目的是利用除垢剂把管道内的水垢、氧化物分解后溶于水冲洗掉。
先将除垢剂加入管道,用循环泵循环清洗。
清洗时应定时检测清洗液浓度、金属离子(Fe2+、Fe3+、Cu2+)浓度、温度、PH值等,当金属离子浓度、PH值趋于平缓时结束清洗。
4、清洗后的漂洗此次水冲洗是为了冲洗掉清洗时残留的清洗液以及清洗掉的杂质,冲洗时要不断开起导淋以使沉积在短管内的杂质、残液冲洗掉。
冲洗是不断测试PH值,浊度,当PH值、浊度趋于平缓时结束冲洗。
5、预膜预膜的目的是让清洗后处于活化状态下的金属表面或保护膜受到伤害的金属表面形成一层完整耐蚀的保护膜。
五、保养:清洗全部结束后,对管道循环水系统采取药剂保养。
管道内加入“惠施通”WL102-3型缓蚀阻垢剂,能与铁、铜、锌等多种金属离子形成稳定的络合物,阻止水中氧气及金属离子腐蚀。
管道冲洗规程标准

管道冲洗规程标准⼀、前⾔管道冲洗是⼯业⽣产和⽇常⽣活中不可或缺的重要环节,其⽬的是确保管道内部清洁,防⽌杂质、污垢等堵塞管道,保证流体顺畅流通。
本规程标准旨在规范管道冲洗作业,确保冲洗过程安全、有效,并达到预期的清洁效果。
⼆、适⽤范围本规程适⽤于各类材质、规格的管道冲洗作业,包括但不限于⽔管、油管、⽓管等。
在进⾏管道冲洗前,应详细了解管道的结构、材质、⽤途及流体特性,以确保冲洗作业的针对性和有效性。
三、冲洗前准备1.检查管道系统:确认管道系统完整,⽆破损、泄漏等问题。
如有必要,应进⾏修补或更换。
2.关闭阀⻔:关闭与冲洗管道相关的所有阀⻔,确保冲洗过程中流体不会外泄。
3.准备冲洗设备:根据管道规格和冲洗要求,选择合适的冲洗设备,如⾼压⽔枪、清洗球等。
4.安全防护:穿戴合适的防护服、⼿套、眼镜等,确保冲洗作业过程中的安全。
四、冲洗作业步骤1.注⼊冲洗介质:根据管道材质和流体特性,选择合适的冲洗介质(如⽔、清洗剂等),通过管道⼊⼝注⼊。
2.启动冲洗设备:启动冲洗设备,按照设备操作说明进⾏操作,确保冲洗过程中冲洗介质能够充分流动并冲刷管道内壁。
3.冲洗顺序:按照从上游到下游的顺序进⾏冲洗,确保冲洗介质能够依次流过各个管段,有效清除管道内部的污垢和杂质。
4.检查冲洗效果:冲洗过程中应定期检查冲洗效果,如观察冲洗介质的颜⾊、浑浊度等,确保管道内部清洁。
5.冲洗结束:当冲洗介质流出管道时清澈⽆杂质时,可认为冲洗结束。
关闭冲洗设备,停⽌注⼊冲洗介质。
五、冲洗后处理1.排放冲洗介质:将管道内的冲洗介质排放⾄指定地点,避免对环境造成污染。
2.检查管道:对管道进⾏再次检查,确认⽆残留污垢、杂质等。
如有必要,可进⾏⼆次冲洗。
3.恢复阀⻔:打开与冲洗管道相关的阀⻔,恢复管道系统的正常运⾏。
4.清洗设备:对冲洗设备进⾏清洗和保养,确保设备处于良好状态。
六、注意事项1.安全第⼀:在冲洗过程中应严格遵守安全操作规程,确保⼈员和设备的安全。
HG20202-2002-工业管道脱脂工艺

HG20202-2002-工业管道脱脂工艺1. 前言工业管道通常在使用前需要清洗和去除表面油污以保证其性能和使用寿命。
传统的脱脂方法包括机械清洗、酸洗、碱洗等,但这些方法不仅清洗效果有限,还容易导致金属表面的腐蚀和氢脆现象,严重影响管道的使用寿命。
HG20202-2002标准规定了一种工业管道脱脂工艺,具有清洗效果好、安全环保等优点,逐渐受到广泛应用。
2. 工艺流程工艺流程图(省略)2.1 去污首先,工业管道中的污垢需要被清洗干净。
可以使用溶液把管道内污垢化解,溶液的配方往往包括有机溶剂、表面活性剂等,不同的材质需要选择不同的配方,以保证去污效果和安全性。
2.2 水洗经过去污处理的工业管道需要用清水进行冲洗,把管道内的污渍彻底冲走。
2.3 酸洗管道表面常常有一层氧化层,酸性洗涤剂可以有效的去除管道表面的氧化层和其他污渍,同时也可以起到杀菌的作用。
2.4 中和酸洗之后,管道表面上仍有残留的酸洗涤剂。
如果残留的酸洗涤剂不被中和,会对后续加工和使用产生严重影响。
中和作为一个重要的环节,可以促进管道表面完全恢复到正常状态。
2.5 碱洗对于含铁、铜、锌等可腐蚀金属的管道,可以使用碱性洗涤剂对管道进行碱洗。
碱性洗涤剂可以除去管道表面的油脂、灰尘和一些化学物质,有助于保障管道的清洁度和使用寿命。
2.6 洗净使用碱性洗涤剂清洗后,需要用清水再次冲洗管道,使管道内部没有残留的碱性洗涤剂,以保证管道表面的纯净和不会腐蚀。
3. 工艺特点•利用化学方法清洗污垢,效果好、速度快;•脱脂过程安全,减少损耗;•环保节能,不会产生二次污染;•工艺步骤简单,可适用于不同材质的管道。
4. 注意事项•在使用工艺之前,需要先做好规范的安全措施,以防发生事故;•工艺所使用的溶液和洗涤剂需要根据管道材质的不同进行配方调整,以保证清洁效果和安全性;•加工过程中应避免管道表面被二次污染。
5. 总结HG20202-2002工业管道脱脂工艺是一种安全环保、高效快速的清洗方法。
- 1、下载文档前请自行甄别文档内容的完整性,平台不提供额外的编辑、内容补充、找答案等附加服务。
- 2、"仅部分预览"的文档,不可在线预览部分如存在完整性等问题,可反馈申请退款(可完整预览的文档不适用该条件!)。
- 3、如文档侵犯您的权益,请联系客服反馈,我们会尽快为您处理(人工客服工作时间:9:00-18:30)。
工业管道化学清洗通用工艺
1适用范围
1.1本通用工艺适用于工业金属管道工程中设计文件规定的需要进行化学清洗的管道施工。
1.2本通用工艺不适用于工业金属管道工程中用水冲洗和油清洗的施工。
2引用(依据)文件
2.1《工业金属管道工程施工及验收规范》 GB50235-97
2.2《石油化工钢制管道工程技术规程》 SHJ517-91
3施工准备
3.1材料准备
3.1.1所有用于工业管道化学清洗的化学清洗药品必须具有出厂质量合格证明书,其化学成分和特性必须符合有关标准的要求。
3.1.2用于现场临时接管的管子及其配件、材料宜采用不锈钢材料或塑料材料。
3.1.3用于现场盛接清洗化学药品的容器应采用不锈钢或塑料制品。
3.2设备机具
3.2.1设备:耐酸泵、不锈钢水槽、水泵、空压机、清洗质量检查用黑光灯、YX-125携带式萤光探伤仪(功率125W)等。
3.2.2用于浸泡法和擦洗法使用的工器具有塑料桶、盆、不锈钢刷、毛刷以及必备的劳动保护用品。
3.3作业条件
3.3.1试压已经结束,并办理工序交接。
4施工工艺
4.1施工程序见图4.1
图4.1化学清洗流程图
4.2.安装临时管线(需要循环酸洗时)
4.2.1临时配管口径,原则上主管直径不得小于100mm,支管直径与正式管径相同;
4.2.2布置好放空线和排疑线
4.2.3临时配管应根据实际需要加临时支架;
4.3 预清理
管道内表面有明显油斑时,不论采用何种酸洗方法,酸洗前应进行必要的预除油处理,一般采用5%的碳酸钠溶液清除油污或用四氯化碳(或三氯乙烯)进行脱脂处理。
同时检查焊缝质量,如有较大焊瘤及焊渣等,应加以处理。
4.4酸洗
4.4.1可采用槽浸法或系统循环法进行酸洗,酸洗液应按规定的配方按顺序进行配制,并应搅拌均匀。
酸洗液、中和液及纯化液的配方,当设计未规定时可按表4.4.1-1和表4.4.1-2的规定配制使用。
表4.4.1-1 碳素钢及低合金钢管道酸洗液和钝化液配方
4.4.2系统循环法即用酸泵向管内边灌酸液,边排空气,排净空气后再进行循环,酸洗的操作温度和持续时间,应根据锈斑去除情况而定,一般情况持续6-8小时,酸洗液温度为70℃左右。
4.4.3酸洗过程中,应定期分析酸洗液的成分并及时补充新液,当除锈效果明显下降时,应予以更换。
4.5中和清洗:
酸洗排净后,接上中和液胶管,用泵动态进行管内残存酸液的中和。
在排放口用PH试纸检查,当溶液呈中性或弱碱性时,即停止中和。
4.6钝化
酸洗、中和合格后,接上钝化液胶管,启动泵向管内。
灌送钝化液,边灌边排空气,使钝化液在管内循环半小时后,再静态2小时后排放干净
4.7水冲洗
钝化后,开启水泵用洁净水冲洗循环系统。
4.8干燥:水冲洗后,立即用干燥气吹扫循环系统,直至管道内残液全部排净。
4.8.1水冲洗合格后,用干燥无油空气或氮气彻底吹干管内壁。
碳钢管内壁呈银灰色认为合格。
4.8.2在完成系统吹扫干燥后,应在短时间内拆除临时管线,并将拆除的管道附件恢复。
如果距试、开车时间较长,待管道系统恢复后,在系统内充0.07MPa 的氮气对管道系统进行氮封保护。
4.9对于小型管段,管件等可采用浸泡法清洗,清洗时将管段、管件直接放入各溶液槽中,其步骤与循环清洗一样,经酸洗,中和、钝化、水洗、干燥后组装,根据需要进行充氮保护。
5质量标准
5.1管内表面或清洗件表面无铁锈和氧化斑迹,无杂质、水垢并呈金属光泽。
5.2 酸洗后的管道以目测检查法以管道内壁呈金属光泽为合格。
5.3中和后,溶液的PH值应为9-9.5。
5.4钝化的质量以兰点检验法检查钝化膜致密性。
用检验液一滴点于钝化表面,15min内出现的兰点,少于8点为合格。
兰点检验液的配方,见表5.4
表5.4兰点检验液配方
6施工注意事项
6.1为获得良好的清洗质量,使化学清洗溶液在一定流速下对管内壁产生冲蚀最佳效果,应选用大扬程大流量耐蚀泵使溶液在一定压力下对整个回路管道进行循环清洗。
其清洗简易流程见附图1。
6.2酸洗时,管内排空很重要,一定要使管内不产生气囊,否则该处铁锈洗不到,会严重影响酸洗质量。
6.3酸洗液和钝化液要经常检查其浓度,应始终保持规定的浓度,否测影响处理效果。
6.4应严禁酸液与中和液、钝化液相混合,尤其钝化液,否测将产生有毒的二氧化氮气体,影响操作人员身体健康。
6.5酸洗完成后应随即进行钝化,钝化完毕随即密封,中途不能停顿,以免管内再次氧化。
7成品保护
7.1所有清洗合格的管道及其附件不得损坏,如不能及时进行管道系统复位,必须用塑料布进行包封。
7.2复位后,要求氮封时,应及时在系统内充氮气,并将系统内空气置换完,每系统应设置两块以上的压力表监视氮封压力。
为保证氮封效果,应设立专人进行定时检查,当系统内氮气压力低于0.05MP a时,应及时补充氮气,并保证氮气压力在0.07~0.1 MP a。
8质量记录
工序交接记录
管道吹洗(脱脂)记录
附图1:循环清洗简易流程
更多内容:河北美德钢管制造有限公司。