基于正交试验的铣削振动影响因素分析
铣削振动的分析和解决方案 PPT

如果镗刀的刀尖产生160公斤的切削力,直径32毫米的
14
镗刀杆悬伸320毫米时产生的刀杆前端弹变为1.6毫米
提高刀杆的静态刚性(StaticToughness)
这样的刀片在镗削或铣削中的切削
pos. 楔入角最小,切削当然轻快。在车 削与镗削中,7度和11度后角是最
常见的刀片,刀片为螺钉夹持的最
neg..
多;在20mm以下的孔镗削中,即便
不存在振动问题,也通常选择11度
后角的刀片,例如山特维克可乐满
的TPMT,DPMT,VCEX的刀片(V型刀
片后角为7度或11度)。后角以7或
11
2、如何应对系统刚性差—— 薄壁工件的铣削用90度主偏角的刀具。
薄壁工件铣削发生振动的原因完全来自于工件,这种工件 一般是箱式或者碗式零件。
改善工件夹持。如:增加合适的辅助支撑点,在夹具和机 床工作台面之间加装一层木板,用粗大的橡皮条或者弹簧 勒在壳体的外面,在箱体内部充满湿沙子等等,奇思妙想 不一而足。
铣削
通用的 HRC40 以上的合金钢刀杆,刀杆从主轴端部向外悬深 与刀杆直径比大于 3 到 4; 模块化刀杆的模块接口磨损影响定位或者接口类型不适合铣削 加工; 刀杆的模块化接口之间拉紧力不够。
3
切削振动的三个分类
似起皱的丝绸
小直径细长刀杆或者薄壁工件 进行高转速切削
被定义为细长轴的零件外圆车削,通常由尾部顶尖支撑但是没 有跟刀架
内孔车、镗削
通用的 HRC40 以上的合金钢刀杆,刀杆夹持悬深与刀杆直径 比大于 4; 同时刀杆夹紧采用螺拴侧压,定位采用 V 型铁或孔柱间隙配 合; 刀尖偏离孔中心线 0.1mm 以上。
2
机夹刀片车镗刀与铣刀的切削振动条件
铣削加工振动影响因素分析

经 过 多年 的 工 作 实践 总结 得 出, 高速 铣 削 加 工 的 过程 中一 旦 出现 振 动 , 必然 会 影 响到 工件 表 面 的精 度 和 工件 整 体 质 量 ,甚 至 是 缩 短 刀 具 乃 至 整个
机床 的使用寿命、 降低机床的使用性 能。有研究表 明, 这种振动的大小会髓 着切 削参数的变化而不断 的变动. 因此在对铣削加工时振动产生的研 究中, 首先要做好切削参数与振动关系之间的研究, 只有科 学的处理好振动 饲题 , 才能更好的为企业生产和社会发展做贡献。 1铣 削振 动 的研 究现 状 目前, 随着工业化生产道路的不断加速, 社会对制造 业产品的性能要求 日益严格 , 使得各种工件的更换速度不断加快 。在这种时代背景 下, 如何提 高制造业产品的性能、 质量 , 缩短产品的生产周期成为制造业发展的关键问 题 。切 削系 统 作为 制造 业 生产 的 核心 环 节 , 如 何 保证 生 产 产 品的 高 效 、 稳定 、 可靠已成为业界追求的主要目标 。众所周知, 铣削加工是一个高速发展的环 节, 它在工件加工中有着诸多的优越性 , 能满 足各种 不同工件 的加工需要 。 但是铣削加工本 身是一个高速运转和无振动要求加工环节,但是它又是一 个复杂、 多元 的综 合 性 设 备 . 这 类 设 备 在 运行 中必 然 会 因 为各 种 因素 而 产 生 振动, 这些振动包含共振、 受迫振动以及系统内部的再生振动等 因此。 要想 确保铣削加工工件的质量、 精度, 就必须要提 前做好各种振动 因素的预防和 控制措施。在 目前的铣削加工中, 常见的振动控制方法主要采取 降低铣削量 的方式, 这种做法虽然一定程度上保证 了机床的稳 定性, 延长 了机床使 用寿 命, 但是很大程度 上却造成生产效率的降低, 给 企业经济效益带来极大 的影 响。同时 。 由于铣床在加工中结构和受力复杂多变 的原因, 这种方 法对于一 些特殊原因引发的振动仍然是束手无策。尤其在近几年, 随着数控机床的应 用和 机 床 刀 具 运 转速 度 的不 断 加 快 , 系 统 动 态 性 能 引发 的 振 动越 来 越 突 出 , 其各 种 变 量也 表 现 的更 加 复 杂 , 这 也 给 我 国铣 削加 工 产 业 的发 展 造 成 制约 。 2铣 削加工振动影响因素分析 经 过对 数 控 机 床 铣 削振 动 所 引发 的 原 因进 行 分 析 ,它 的 出现 主 要 包 含 了受迫式振动和 自激 式振动两种。受迫式振动主要指 的是机床在铣削加工 当中因为机械传动不平衡 、冲击力复杂以及结构构件松弛而引发的一种振
基于正交试验的铣削参数和刀具磨损对表面粗糙度的影响研究

Vo 1 . 2 6, No . 2
Ma r . . 201 3
文 章 编 号 :1 0 0 2 — 6 6 7 3( 2 0 1 3 )0 2 — 1 3 3 - 0 3
基于正交试验的铣削参数和刀具磨损对表面粗糙度的影响研究
朱红 波 ,王 迪 ,王 笑
( 1 . 克 拉 玛 依 职 业 技 术 学 院 ,新 疆 独 山 子 8 3 3 6 0 0 ;2 . 新 疆 机 电 职 业 技 术 学 院 ,新疆 乌 鲁 木 齐 8 3 0 0 1 1 )
摘
要 :切 削加 工表 面粗糙 度 对 零件 的使 用 性能 有 重要 影响 ,而加 工过程 中的 工艺条 件 又是 影响表 面粗糙 度
的 主要 因素 。利 用 正交 试验 方 法安排 铣 削试 验 ,通过 方 差分 析等 方 法进 一步 分析 切 削参 数和 刀具磨
损 对 表 面 粗 糙 度 的 影 响 规 律 .确 定 影 响 表 面 粗 糙 度 的 主 要 因 素 , 为 合 理 选 择 切 削 加 工 工 艺务 件 提 供
of t h e c ut in t g pa r a me t e s r a nd t o o l we r a o n s ur fa c e r o u 【 g hn e s s i nv e s t i g a t e d t h r ou g h me t ho d s s u c h a s a n a l y s i s o f va r i a nc e ,de t e r mi n e t h e e fe c t s o f t he s u fa r c e r o u g hn e s s o f t h e ma i n f a c t o r s , p r ov i d e a t he o r e i t c l a b si a s f o r t he r e a s o n a b l e c ho i c e of c ut t i n g p r oc e s s c on d i t i o ns . Ke y wo r ds :o r t h og o n l a t e s t ;c u t i t ng p a r a me t e r s ;t o o l we r ;s a ur fa c e r o u g h ne s s ;a na ly s i s o f v a r i a nc e
铣削加工振动影响因素分析

(p a d a i tn i es 口) a e eniet e e h i cosh t f c e ut g i ain I a) n da c t g hc s (c hv e ni dt b ema f tr ta eth tn b t .n r lu i t k n b d f o t i na a t c i vr o
第 3 卷第 6 0 期
Vo _ 0 l 3 No 6 .
辽宁工程技术大学学报 ( 自然科学版 )
J u n l f a nn e h ia ie s y ( tr l ce c o r a o igT c n c l v ri Nau a in e) o Li Un t S
(. 1东北大学 机械工程与 自动化学院,辽宁 沈阳 100 ;2沈 阳理工大学 10 4 . 摘 应用 技术 学院,辽宁 沈 阳 13 2 ) 1 12 要 :为了解决铣削振动的影响因素难 以确定的问题 ,建立 了铣 削系统二 自由度模型,利用切削厚度分析的方
法进行 了切削力分析 ;利用动力学方程 ,根据方程 中的各参量 ,确定 了主轴 转速 、轴 向切削深度 、进给速度和径 向切 削深度 四个切削参数是影响铣削振动 的主要 因素 。 通过正交切 削实验 , 确定了各切 削参数对铣削振动的权 重 排序 ,得 出切削速度是铣削振动的最 主要 的影 响因素 的结论 。为研究铣削加工振动稳定性研究奠定了理论基础 , 同时也为利用变参数切削振动控制确 定了首选控制参量 。 关键 词:切削振动 ;切削力 ;正交实验;影响因素 ;动力学方程;变参数切削 ;振动稳定性;影响因素 中图分类号:T 3 B5 3 文献标 志码 :A
2Po)e h i c o l h n a gLio gUnv ri 1 1 21 . 1tc ncS h o S e y n g n ie st 1 3 2 Of y
基于正交试验法的高速铣削工艺参数优化设计

摘 要 : 章 使 用硬 质 合 金 刀 具 对 铝 合 金 ( A 0 叶 轮 进 行 高 速 铣 削 试 验 研 究分 析 了不 同 的切 削 参 数 的 选 文 27)
,
择 对 叶轮 叶片加 工 的表 面粗糙 度 影响 、首 先采 用 多因 素 的a 交试 验 分析 了各 因素 对 高速铣 削过程 中 四 Y - - 个 目标 值 的影 响 ; 然后 利 用极 差分 析 方 法分 析 试验 结果 , 出各 个 因素 对 表 面粗糙 度 影 响 的主 次顺 序 指
.
v s ia e e tg t d.Fis sn rh g n lar y f rm ut-a t ra ays st e ef c fe c a t ri ih-pe d mi i r tu ig o t o o a ra o lif c o n l e h fe to a h fc o n h g s e lng l t n a ptn her n e a aytc lm eho o a ayz h ra e uls a d po n u he prm a y a d s c nd r he do i g t a g n l ia t d t n l e t e til s t r n i to tt i r n e o av
,
.
e pe i e t l r s ls s o x rm n a e u t h w h t be t s r a e r u hn s a b ane e e tn h ppr pra e c t i g pa t a s u f c o g e s c n be o t i d by s lc i g t e a o i t u tn . r m e e s f r t e a u i m lo mpe l r v ne Th x rm e t lr s ls a s h w ha h r s a d fnie s g a t r o h l m nu a l y i l a e e e p e i n a e u t l o s o t t t e e i e i t i.
基于正交实验的p20钢高速铣削研究

基于正交实验的p20钢高速铣削研究近年来,随着工业的迅速发展,机械制造的性能要求也越来越高,高速铣削成为目前机械加工技术的重要组成部分。
P20钢是一种常用的工具钢,因其易于加工和造型,被广泛应用于机械零件的加工。
今天,我们将探索如何基于正交实验,来研究P20钢高速铣削的加工效果。
首先,建立正交实验的方案。
针对P20钢的高速铣削,实验因素包括接触磨头的道数、主轴转速、进给速率以及润滑等四个因素,每组因素分别取5个不同的水平值。
由此,总共可以得到25个实验组合,进而建立5因4水平的正交实验方案。
其次,在实验中我们确定了以下参数:接触磨头的道数为3道、4道、5道; 主轴转速分别为8000rpm、10000rpm、12000rpm;给速率为0.1mm/s、0.2mm/s、0.3mm/s;滑方式分为冷却剂和脂类润滑。
最后,利用正交实验设计方案,进行P20钢的高速铣削实验。
我们在实验中,以加工表面粗糙度、切削温度和切屑形态为主要测试指标,并观察分析不同实验条件下的高速铣削效果。
实验结果显示,3道接觑磨头的条件下,主轴转速12000rpm和进给速率0.3mm/s的实验条件,P20钢的加工表面粗糙度和切削温度最优,切屑形态呈现一定的线性,润滑条件下,冷却剂的铣削效果优于脂类。
从结果看出,正交实验设计对P20钢高速铣削的研究有着重要的作用,能够为后续进行优化设计和进行工艺控制提供参考,有助于P20钢高速铣削的技术实现。
总而言之,在正交实验的设计和实施过程中,我们针对P20钢高速铣削的加工效果做出了初步的探讨,得出了有效的结论,为后期进行更多实验研究及技术应用提供了可靠的依据。
近年来,机械加工工艺的发展以及工业需求的不断增长,产品加工性能也越来越受到重视。
基于正交实验的高速铣削研究,能够准确体现P20钢高速铣削的加工效果,有助于技术指导的准确性,以及钢材的高效加工。
未来,还可以更深入地研究P20钢高速铣削及其他金属材料的加工性能,进一步提高机械加工技术的水平。
影响叶轮铣削加工质量的因素分析
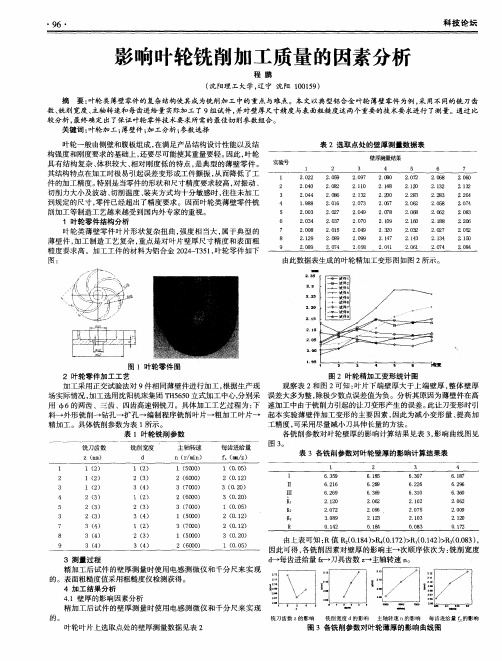
铣刀齿数 z的影响 铣削宽度 d的影响 主轴转速 n 的影响 每齿进给量 f 』的影响
【 4 】 罗跃. 难加 工材料薄壁零件的振动切 削技术研 究【 D 】 . 成都 : 四川 大
学, 2 0 0 4 .
图 4 各铣削参数 对叶轮表面粗糙度 的影响 曲线图
1 9 7 6, 1 2 : 2 0 - 9 0.
[ 2 】 孔金星. 低 刚度 薄壁 零件 的精 密加 工【 J 】 . 中国物理 工程研 究院机械
制造工艺研究所 , 2 0 0 3 : 2 0 — 2 2 .
[ 3 】 任 家平. 影 响 高速加 工的 几个 主要 因素[ J 】 . 高速加 工专题 综述 ,
家 已设计好 仅= 4 5 。时 , 行程 正好达到标准 , 但 如遇特殊情况必须进 行程开关位置等 。 行调整。( 2 ) 在地刀水平连杆 紧固之前, 三相地刀动触杆处于合位 , 经 3 . 3排除故障的操作顺序 验上应使其合足程度 自主动相到从动相 由低到高 ( 略微 ) 。这样做有 ( 1 )手摇刀闸至 中间位置,以防止试验时电机反转损伤机械部 利于保证在地刀同期度合格的前提下 , 其合 闸后剩余间隙一致 。( 3 ) 分。( 2 ) 根据故障类型判断故障点大概位置、 所属 回路 , 一般程序是先 机械联锁 间隙的调整需要在主刀分 、 合位置分别调整 3  ̄ 8 mm。 控制 回路后电机回路 。( 3 ) 用万用表对所判 断的故障回路测量分析 , 3 电动回路的故障处理( 以 CJ 5电动机构为例 ) 以回路末端为测量起点 ,以接线端子或桩头为单位向回路起点逐一 3 . 1电动回路原理 测量排查 , 直至找到故障点。 如图 3所示 , 其动作逻辑并不复杂( 这里不再讲述 ) , 关键是调试 3 . 4排除故障过程中关键点分析 人员应充分熟悉 图纸和实际接线 , 回路分为两个部分 : 电机部分和控 ( 1 ) 调试人员在排 除故 障过程 中, 思路要清晰 , 判断 回路 的好坏 制 部分 。 以万用表量值为唯一依据 , 切不能盲 目拉扯线头 , 走冤枉路 。( 2 ) 若按 下分合闸按钮 , K MI ( 合) 、 K M 2 ( 分) 均不动作 , 说明在操作回路上的分 合公共部分有故障 ; 若K M1 动作 , K M 2不动作, 说明操作回路 中的合 茸 毯t 闸部分有故障 ; 反之则是分 闸部分有故障。( 3 ) 对控制 回路 的故障排 除, 带电使用万用表交 流电压档测量较为方便 。( 4 ) 对于电机缺相运 ^勺^ 2 K T 行, 可仔 细观察接触器 主触头灭 弧情况 , 并迅速判断没有电弧 的一相 即为故障相 , 再用表逐一排查。若 电机相序表现为分合 闸均反 , 可将 主电源两相互调 ; 若分 闸反 , 可将 K M2的 1 、 3 、 5 端子连 线之中的两 个互调 ; 若合 闸反 , 则将 K M1 的1 、 3 , 5 端子连线( 双线同时 ) 互调。 4 结 论 在 国网变电检修技能比赛 中, 我们教练组和队员共 同努力 , 反复 试验 、探 索出一套行之有效 的调试 规范 ,事后本人进行了总结和细 化,望上述这些经验总结 能与广大同行们分享 ,能有助于大家提高 G W4刀闸调试水平 。 参考文献 【 1 ] 蒋巧林 , 刘燕. G W4 、 G W5系列 隔离开关运行 分析及 改造措施【 J 1 . 江 西电力职业技术学院学报 , 2 0 o 5 , 1 8 ( 3 ) : 4 5 - 4 6 . 图 3 电动 机构 控 制 回 路 [ 2 ] 陈宏伟 , 王光临. G W4 — 1 2 6型户外隔离开关的常见 ( 下转 1 0 5页 )
机械加工过程中机械振动的原因及对策分析

机械加工过程中机械振动的原因及对策分析机械加工过程中出现机械振动的原因较多,主要包括以下几个方面:1.切削力的不平衡:机械加工过程中,切削力的大小和方向会不断变化,如果切削力不平衡,就会引发机械振动。
这主要是由于工件材料的异质性、表面瑕疵等原因导致的切削力不均匀分布。
2.进给速度过大:如果在机械加工过程中进给速度过大,刀具与工件之间会发生剧烈的冲击,从而产生振动。
进给速度过大还会引起切屑的断裂不良、刀具严重磨损等问题。
3.机床刚度不足:机床的刚度不足也是引起机械振动的重要原因。
刚度不足会导致机械系统的固有频率过低,与工件切削频率接近,从而引起共振现象。
4.切削液不当:切削液在机械加工过程中起到冷却润滑的作用,如果切削液的流量、温度、质量不合适,则会导致切削液无法有效冷却刀具和工件,增加切削力并引起振动。
针对上述问题,可以采取以下对策来降低机械振动:1.切削力平衡:选择合适的刀具和进给方式,确保切削力均匀分布。
在加工过程中可以采用动态平衡的方法动态调整刀具和工件的重心位置,提高切削力的平衡性。
2.控制进给速度:根据加工材料的性质和切削条件,合理控制进给速度,避免过大的进给速度引起振动。
如果需要加工高硬度材料,可以采用高速切削技术来提高加工效率,减少机械振动。
3.提高机床刚度:加强机床的刚度和稳定性可以有效抑制机械振动。
可以采用增加机床结构重量、增大导轨尺寸、优化机械系统刚度等措施来提高机床刚度。
4.优化切削液:选择合适的切削液,并设置合理的流量、温度和质量控制,确保切削液能够有效冷却刀具和工件,降低切削力。
还可以通过合理的刀具设计、提高工件材料的均匀性、改善切削过程中的冷却条件等方法来减少机械振动的发生,提高加工质量和效率。
对于特殊要求的加工任务,可以采用振动缓冲系统、动态平衡系统等技术手段来抑制机械振动,实现稳定加工。
立铣削过程中的颤振稳定性分析与研究

http :M ZZ HD.chinaj ou rna.l n et .cn E-m ai:l ZZHD @chai n aj ou rna.l n et .cn 5机械制造与自动化6作者简介:鲁杰(1979) ),男,江西九江人,硕士研究生,研究方向为航空宇航制造工程。
立铣削过程中的颤振稳定性分析与研究鲁杰(南京航空航天大学机电学院,江苏南京210016)摘 要:铣削过程中的颤振会导致刀具磨损、工件表面粗糙、产量下降等问题。
分析和比较了一维动态铣削数学模型,结合已获得的试验数据,根据一维理论开发出动态铣削仿真软件。
该软件预测了在特定铣削条件和模态参数下的稳定性曲线。
研究表明,动态铣削仿真软件的开发对于数控铣床铣削参数的给定具有重要意义,仿真计算对铣削过程中稳定性判别是一种有效的方法。
关键词:铣削;颤振;稳定性中图分类号:TG 54 文献标识码:B 文章编号:1671-5276(2009)02-0084-03Analysis of V ibration Stability inM illing ProcessLU Jie(Co ll e ge o fM echan ica l and E lectr ica,l Nanjing Un ive rsity o f Ae ronau tics and A stronau tics ,Nan jing 210016,Ch ina)Abstrac t :V i b ration in m illing pr ocess can result in cutt er abras i o n ,roughness o f fi n i s h surface ;out putdecrease and so on .T his pa -per ana l y zes and co mpares m at hematic model o f one dm i ens ion dyna m ic m illing process and developes dyna m ic m illing sm i ul a ti o n soft ware according t o dm i ens ion t heory and i n co mb i n a tion w ith the t esti n g da t a .This soft ware can pred i c t stabilit y curve i n given m illing condition and mode paramet er .According t o t he s t udy it is shown that t he deve l o p mento fdyna m ic m illi n g s m i ulation soft ware is o f gr eat m i port ance t o m illing paramet er identification o f nu mera l control m illing m achine .Sm i ulati o n ca l c ulati o n is a good met hod f or s t ability identifi c ati o n i n m illi n g process .K ey word s :m illing ;v ibration ;s t ab ility0 前言铣削颤振产生源于刀具和工件之间的相互振动,它会导致切屑厚度会随着时间变化而变化。
高速铣削下的刀具振动分析与控制策略
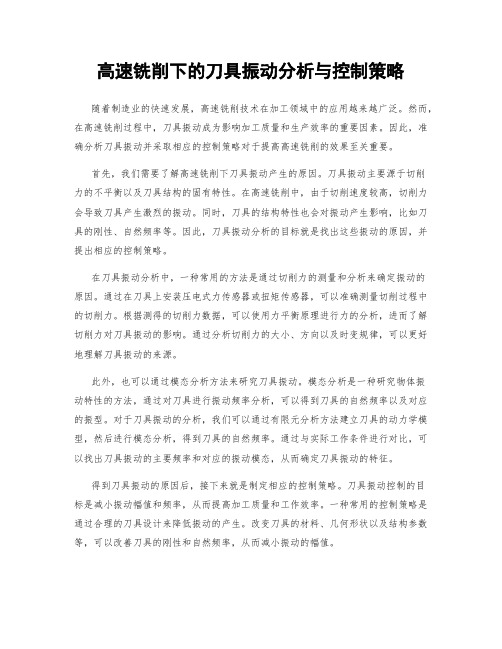
高速铣削下的刀具振动分析与控制策略随着制造业的快速发展,高速铣削技术在加工领域中的应用越来越广泛。
然而,在高速铣削过程中,刀具振动成为影响加工质量和生产效率的重要因素。
因此,准确分析刀具振动并采取相应的控制策略对于提高高速铣削的效果至关重要。
首先,我们需要了解高速铣削下刀具振动产生的原因。
刀具振动主要源于切削力的不平衡以及刀具结构的固有特性。
在高速铣削中,由于切削速度较高,切削力会导致刀具产生激烈的振动。
同时,刀具的结构特性也会对振动产生影响,比如刀具的刚性、自然频率等。
因此,刀具振动分析的目标就是找出这些振动的原因,并提出相应的控制策略。
在刀具振动分析中,一种常用的方法是通过切削力的测量和分析来确定振动的原因。
通过在刀具上安装压电式力传感器或扭矩传感器,可以准确测量切削过程中的切削力。
根据测得的切削力数据,可以使用力平衡原理进行力的分析,进而了解切削力对刀具振动的影响。
通过分析切削力的大小、方向以及时变规律,可以更好地理解刀具振动的来源。
此外,也可以通过模态分析方法来研究刀具振动。
模态分析是一种研究物体振动特性的方法,通过对刀具进行振动频率分析,可以得到刀具的自然频率以及对应的振型。
对于刀具振动的分析,我们可以通过有限元分析方法建立刀具的动力学模型,然后进行模态分析,得到刀具的自然频率。
通过与实际工作条件进行对比,可以找出刀具振动的主要频率和对应的振动模态,从而确定刀具振动的特征。
得到刀具振动的原因后,接下来就是制定相应的控制策略。
刀具振动控制的目标是减小振动幅值和频率,从而提高加工质量和工作效率。
一种常用的控制策略是通过合理的刀具设计来降低振动的产生。
改变刀具的材料、几何形状以及结构参数等,可以改善刀具的刚性和自然频率,从而减小振动的幅值。
此外,也可以通过刀具切削参数的优化来减小振动。
切削参数包括切削速度、进给量、切削深度等。
调整这些参数的值可以有效地控制切削力的大小和方向,从而减小振动的产生。
工业机器人铣削加工振动研究
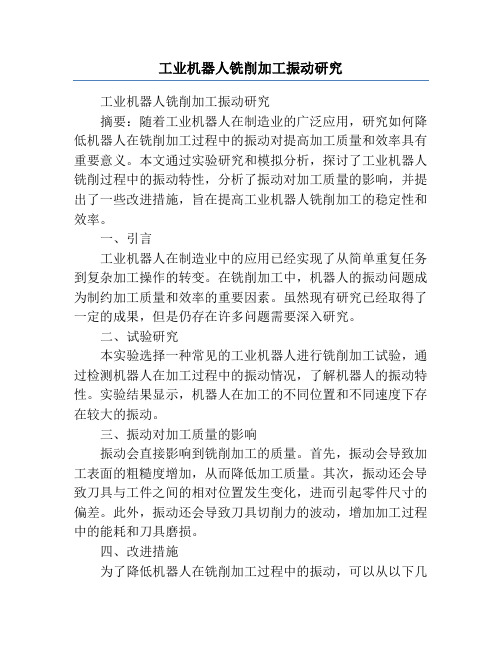
工业机器人铣削加工振动研究工业机器人铣削加工振动研究摘要:随着工业机器人在制造业的广泛应用,研究如何降低机器人在铣削加工过程中的振动对提高加工质量和效率具有重要意义。
本文通过实验研究和模拟分析,探讨了工业机器人铣削过程中的振动特性,分析了振动对加工质量的影响,并提出了一些改进措施,旨在提高工业机器人铣削加工的稳定性和效率。
一、引言工业机器人在制造业中的应用已经实现了从简单重复任务到复杂加工操作的转变。
在铣削加工中,机器人的振动问题成为制约加工质量和效率的重要因素。
虽然现有研究已经取得了一定的成果,但是仍存在许多问题需要深入研究。
二、试验研究本实验选择一种常见的工业机器人进行铣削加工试验,通过检测机器人在加工过程中的振动情况,了解机器人的振动特性。
实验结果显示,机器人在加工的不同位置和不同速度下存在较大的振动。
三、振动对加工质量的影响振动会直接影响到铣削加工的质量。
首先,振动会导致加工表面的粗糙度增加,从而降低加工质量。
其次,振动还会导致刀具与工件之间的相对位置发生变化,进而引起零件尺寸的偏差。
此外,振动还会导致刀具切削力的波动,增加加工过程中的能耗和刀具磨损。
四、改进措施为了降低机器人在铣削加工过程中的振动,可以从以下几个方面进行改进:1. 优化机器人的姿态控制:通过优化机器人的运动轨迹和加工参数,减小机器人的加速度和转动惯量,降低振动的产生。
2. 选择合适的铣削刀具:选择合适的刀具材料和几何结构,提高切削性能,减小切削力波动对振动的影响。
3. 加强机器人的结构刚度:通过优化机器人的结构设计和材料选择,提高机器人的刚度和抗振能力。
4. 应用主动振动控制技术:利用主动振动控制技术对机器人进行振动补偿和控制,降低振动对加工质量的影响。
五、结论通过实验研究和分析,我们对工业机器人在铣削加工中的振动特性进行了研究。
实验结果表明,机器人的振动对加工质量有着直接影响。
为了降低振动对加工质量的影响,我们提出了一些改进措施,包括优化机器人的姿态控制、选择合适的切削工具、加强机器人的结构刚度和应用主动振动控制技术等。
机械加工过程中机械振动的成因及解决措施探讨

机械加工过程中机械振动的成因及解决措施探讨【摘要】机械加工中的振动问题是一项常见而重要的挑战,振动不仅会影响加工质量和工件精度,还会降低生产效率和延长加工周期。
本文首先分析了机械振动的成因,包括切削力、刀具不平衡和机床结构等问题。
然后探讨了解决振动问题的措施,如使用平衡刀具、提高机床刚度、优化切削参数和使用减振设备等方法。
最后总结了振动问题的解决方法,展望了振动控制技术的发展前景,并强调了振动控制对机械加工的重要性。
通过本文的学习,读者将更深入地了解机械振动问题及其解决方法,提高加工质量和效率。
【关键词】机械加工,机械振动,切削力,刀具平衡,机床结构,振动问题解决,刚度,减震性能,控制切削参数,优化加工工艺,减振设备,隔振装置,振动控制技术,发展前景,重要性。
1. 引言1.1 介绍机械加工中的振动问题在机械加工中,振动是一个普遍存在的问题,它直接影响着加工质量和工件精度。
振动会导致切削力不稳定,进而影响刀具的切削性能,造成加工表面粗糙度增大、形状偏差加大,甚至使工件破裂。
振动还会加速刀具的磨损,降低加工效率,增加生产成本。
振动问题的严重性不容忽视,需要引起机械加工行业的高度重视和关注。
解决振动问题不仅可以提高加工质量和工件精度,减少损耗和成本,还可以提升机械加工的稳定性和可靠性,提高生产效率。
探讨机械振动问题的成因及解决措施,对于提升机械加工的水平和质量具有重要意义。
通过深入分析振动问题的根源,寻找针对性的解决方法,不仅可以改善加工质量,提高工件精度,还可以推动振动控制技术的进步,促进机械加工行业的发展。
1.2 阐述振动对加工质量和工件精度的影响振动是机械加工过程中常见的问题,它直接影响着加工质量和工件精度。
振动会导致切削过程不稳定,使得工件表面出现凹凸不平的情况,从而影响加工表面的光洁度和精度。
在高速加工过程中,振动还会导致刀具磨损加剧,加工精度降低,甚至加速机床的磨损,降低机床的使用寿命。
振动还会影响加工中切屑的形成和排除。
铣削振动的分析与解决方案共24页文档共26页PPT

21、要知道对好事的称颂过于夸大,也会招来人们的反感轻蔑和嫉妒。——培根 22、业精于勤,荒于嬉;行成于思,毁于随。——韩愈
23、一切节省,归根到底都归结为时间的节省。——马克思 24、意志命运往往背道而驰,决心到最后会全部推倒。——莎士比亚
25、学习是劳动,是充满思想的劳动。——乌申斯基
谢谢!
铣削振动的分析与解决 方案共24页文档
6、纪律是自由的第一条件。——黑格 尔 7、纪律是集体的面貌,集体的声音, 集体的 动作, 集体的 表情, 集体的 信念。 ——马 卡连柯
8、我们现在必须完全保持党的纪律, 否则一 切都会 陷入污 泥中。 ——马 克思 9、学校没有纪律便如磨坊没有水。— —夸美 纽斯
铣削颤振稳定性影响因素分析

铣削颤振稳定性影响因素分析发布时间:2022-11-24T00:34:06.229Z 来源:《中国科技信息》2022年第15期作者:孟德强[导读] 目前高速铣削加工广泛的应用在汽车行业、模具行业、航天航空等多种行业之内,孟德强陆军装甲兵学院士官学校摘要:目前高速铣削加工广泛的应用在汽车行业、模具行业、航天航空等多种行业之内,为了更准确的对高速铣削进行颤振稳定性预测,本文对铣削加工过程中的颤振产生机理进行建模,然后对不同的铣削模态参数对铣削颤振稳定性预测的影响进行研究。
关键词:颤振稳定性预测参数影响装备制造业是一个国家的经济建设和国防建设的基础行业,并且装备制造也是衡量一个国家的综合实力的重要标。
而铣削加工作为制造业中的重要一部分。
在切削加工过程中,颤振是加工系统本身特性所激起的一种剧烈振动,当颤振发生时,会在被加工工件表面留下明显的振纹,并严重影响被加工工件表面质量,严重时甚至会损坏刀具和机床加工设备。
因此,本文对铣削颤振产生的机理进行了阐述,最后研究不同模态参数对颤振稳定性预测的影响。
为后续的铣削加工应用研究提供借鉴意义。
1 稳定性叶瓣图基本概念稳定性叶瓣图(Lobe)的概念是Tobias[1]于1965年提出的,它是用轴向极限切削深度随主轴转速的变化关系来描述切削过程中的稳定切削区域和不稳定切削区域。
在稳定性叶瓣图中可以将整个区域分为三个不同的稳定性区域即:不稳定区、绝对稳定区和有条件稳定区。
且在不发生颤振的条件下,获得最大的去材料除率。
而稳定性叶瓣图也是现阶段进行加工过程颤振稳定性预测的最常见的方法。
2 铣削再生颤振产生机理根据颤振发生的机理不同,一般可以分为:摩擦型颤振、耦合型颤振和再生型颤振三种[2],而在铣削加工过程中,再生型颤振是最为常见的。
再生型颤振的产生主要是由于一些外部的扰动或者工件表面不平整引起刀具的振动,从而在被加工工件表面留下波纹状的切削振纹。
当外界发生扰动时会使刀具发生振动,从而刀具在工件Y方向上的切削厚度发生变化,且在工件表面上留下明显的振纹,若本次留下的切削振纹为y(t),上一次留下的振纹为y(t-T),T为主轴旋转的周期,则有瞬时切削厚度为:式中,[y(t)-y(t-T)]为动态切削厚度,在此只考虑切削厚度对切削力的影响,可得到切削力与瞬时切削厚度的关系为:式中, Ff(t)为进给方向上的切削力,a为轴向切削深度,Kf为进给方向上的切削力系数。
机械加工过程中机械振动的原因及对策分析
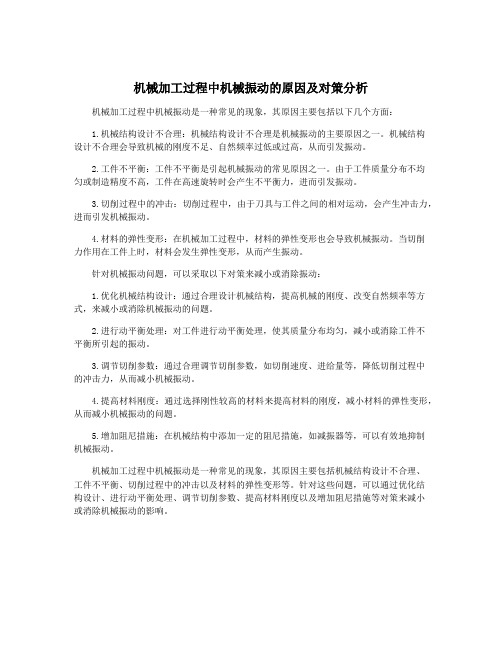
机械加工过程中机械振动的原因及对策分析机械加工过程中机械振动是一种常见的现象,其原因主要包括以下几个方面:1.机械结构设计不合理:机械结构设计不合理是机械振动的主要原因之一。
机械结构设计不合理会导致机械的刚度不足、自然频率过低或过高,从而引发振动。
2.工件不平衡:工件不平衡是引起机械振动的常见原因之一。
由于工件质量分布不均匀或制造精度不高,工件在高速旋转时会产生不平衡力,进而引发振动。
3.切削过程中的冲击:切削过程中,由于刀具与工件之间的相对运动,会产生冲击力,进而引发机械振动。
4.材料的弹性变形:在机械加工过程中,材料的弹性变形也会导致机械振动。
当切削力作用在工件上时,材料会发生弹性变形,从而产生振动。
针对机械振动问题,可以采取以下对策来减小或消除振动:1.优化机械结构设计:通过合理设计机械结构,提高机械的刚度、改变自然频率等方式,来减小或消除机械振动的问题。
2.进行动平衡处理:对工件进行动平衡处理,使其质量分布均匀,减小或消除工件不平衡所引起的振动。
3.调节切削参数:通过合理调节切削参数,如切削速度、进给量等,降低切削过程中的冲击力,从而减小机械振动。
4.提高材料刚度:通过选择刚性较高的材料来提高材料的刚度,减小材料的弹性变形,从而减小机械振动的问题。
5.增加阻尼措施:在机械结构中添加一定的阻尼措施,如减振器等,可以有效地抑制机械振动。
机械加工过程中机械振动是一种常见的现象,其原因主要包括机械结构设计不合理、工件不平衡、切削过程中的冲击以及材料的弹性变形等。
针对这些问题,可以通过优化结构设计、进行动平衡处理、调节切削参数、提高材料刚度以及增加阻尼措施等对策来减小或消除机械振动的影响。
- 1、下载文档前请自行甄别文档内容的完整性,平台不提供额外的编辑、内容补充、找答案等附加服务。
- 2、"仅部分预览"的文档,不可在线预览部分如存在完整性等问题,可反馈申请退款(可完整预览的文档不适用该条件!)。
- 3、如文档侵犯您的权益,请联系客服反馈,我们会尽快为您处理(人工客服工作时间:9:00-18:30)。
图1 所示 。
零件精度 降低、 刀具磨损加剧、 机床的极限加工能力 受 到限制 以及 工 作 环境 受 到噪 音污 染 等 问题 ,对 零 件 的加 工 质 量 和加 工 效 率 产 生 重要 影 响 【 1 】 。一 般 来 说 ,受 迫振 动 和 自激振 动 是机 械加 工 过程 中产生 的 主要振动形式。其中, 受迫振动一般容易识别也容易 解决 , 而 自激振动( 又称颤振 ) 的发生 、 发展规律与机 械加工过程联 系紧密 , 影响因素多 , 一般较难识别 , 也不容 易解 决翻 。 为 了进 一 步分 析 切削 加 工过 程 中各 种 工 艺 因素 对 切 削振 动 的影 响规 律 ,采 用 正交 试验 法 对 不 同工 艺条件 下铣削振动 信号 的变化 情况进行分 析和研 究 。正交试 验设计 是 利用 正交表合 理 安排试 验 , 以尽 可能少的试验次数确定主要影响因素及各 因素对试 验 指标 的影 响规律p 】 。利用 正交表 安排 试验 首先要 明 确试验 目的、 确定试验指标 ; 其次根据试验指标 的特 征确定影响因素及各 因素水平 ;最后根据试验 因素 及水平选择合适 的正交表安排试验计划 。
Eq u i p me n t Ma n u f a c t u r i n g T e c h n o l o g y No . 6, 2 0 1 4
基 于正交试验 的铣削振 动影响因素分析
朱红波
( 克拉玛依职业技术学院 , 新疆 独 山子 8 3 3 6 0 0 )
摘 要: 切 削振动对零件加 工表 面质 量影 响较 大, 为 了控制切 削振 动 , 提 高加 工表 面质量 , 利 用正交试验进行 不同工艺
8 0 o
1 . 2
O. 3
l 4 o
1 o o
O. 5 2
O_ 3 7
2 . 9 0 3 3 7
2 . 1 8 4 6 1
1 试验条件
1 . 1 振 动信 号采集 与分 析 系统
结合试验所使用的机床及实际加工所选用的切 削参数 ,选择 I N V 9 8 1 8 压 电式加速度传感器作为数 据采集用传感器 , 电荷灵敏度 1 8 9 . 1 p c / m s 一 2, 可用频 率范围 1 k H z ~1 0 0 k H z 。传感器的安装位置如 图 2
条件 下的铣 削试验 , 采集振动信 号并提 取信号特征值 , 通过方差分析等方 法研 究铣 削参数和 刀具磨损对铣 削振动 的影 响规律 , 确定影响铣 削振动的显著因素 , 为切 削振动控制研 究及铣 削工艺参数 的合理选择提供理 论参考 。
关键词 : 切 削振动 ; 正交试验 ; 切 削参数 ; 刀具磨损
收 稿 日期 : 2 0 1 4 - 0 3 — 0 7
一
图 2传 感器 的 安装
作者简介 : 朱红波 ( 1 9 8 2 一) , 男, 辽宁抚顺 人 , 硕士 , 讲师 , 研究方向为机械制造 质量 控制。
2 7 O
《 装备制造技术) ) 2 0 1 4年第 6 期
表 2试 验 计 划 及 试验 结果
2 试 验指标及 因素水平 的确定
从传感器检测到的原始信号包含了很 多与试验
样 本 主 A 轴 ( 转 n ) 速
序号 ( r / a r i n )
1 6 0 o
进 给 c ∽ 速 度 刀 具 D ( 磨 口 损 ) 量 信 善 方
( n l n 1 )
1 o o
1 2 O
O. 2
0. 3 7
1 . 9信号 的强 弱 , 因而 以铣削振 动信号
的均方根值作为试验指标 。切削加工过程中影响切 削振动的因素很多 , 包括机床的精度 、 刀具材料与几
4
5
6 o o
中图分类号 : T H1 6 1 . 6 文献标识码 : A 文章编号 : 1 6 7 2 — 5 4 5 X ( 2 0 1 4) 0 6 - 0 2 7 0 - 0 3
机械 加工 过 程 中常 常会 产 生振 动 ,使工 艺 系统 的正常 切 削过 程受 到 干扰 和破 坏 。发 生 在金 属切 削 过 程 中 的振 动 常 常会 带 来 已加 工 表 面 粗 糙 度增 加 、
O. 3
( m m/ m i n )
7 0
( m m)
O. 0 5
根值
1 . 8 1 8 3 3
因素无关 的信息 , 所 以必须对这些信号进行处理 , 提
取与试验 因素关 系紧密的信号特征 。由于均方根能
2
3
6 0 o
6 0 o
O. 6
O. 9
图1 铣 削振 动 测试 系统
1 . 2 试 验 机床
试 验 所 用 机 床 为武 汉华 中数 控 生 产 的 D M4 6 0 0 立 式 镗铣 加 工 中心 , 主 轴最 高 转 速 6 0 0 0 d mi n , 分辨 率0 . 0 0 1 r f l l n 。 1 . 3 试 验 刀具及 试件 材料 试验刀具为高速钢三齿直立铣刀 ( H S S , 1 0m m) , 试件材料为 4 5 # 钢, 尺寸为 1 2 0 mm ×1 0 0 m m ×2 0 m m。 1 . 4传 感器
所示 。
试验所用铣削过程振动信号采集与分析系统是 利用加速度传感器对铣削工艺系统进行切削振动信 号的测量 ,通过传感器采集到电荷信号后将 电荷信 号送入滤波放 大器进行信号 转换与放 大 ,然后 由 C o i n v D A S P V 1 0 信号采集处理分析仪采集后 , 使 用 C o i n v D A S P V 1 0软件所配置 的频谱分析功能模块对 振动信号进行特征提取分析。铣削振动测试系统如