产吨硫酸庆大霉素发酵罐设计
硫酸庆大霉素生产工艺设计流程图

WORD 格式.整理版硫酸庆大霉素生产工艺一、硫酸庆大霉素产品说明 1、产品名称及化学结构1.1产品名称:硫酸庆大霉素(Gentamycin sulfate)1.2化学结构:1.2.1结构式:• 2H SO2 4C1: R1=R2=CH3C2: R1=CH3R2=HC1a: R1=R2=H1.2.2分子式:C1: C21H43N5O7=477.61C2: C20H41N5O7=463.58C3: C19H3”5O7=449.551.2.3分子量:Cj 477.61C2: 463.58C3: 449.55C; C2、C1a为硫酸庆大霉素的三个组分,各组分与2个分子的硫酸相结合,其成分折干效价为590Wml 以上。
2、理化性质2.1性状:白色或类白色粉末,吸水性强,稳定性高,易溶于水,不溶于乙醇、丙酮、氯仿等有机溶剂。
2.2比旋度:+107。
〜+12103、产品质量标准(查药典)二、原材料、包装材料质量标准及规格1、发酵部分名称规格葡萄糖工业用:淡黄色粉末,含量70%以上,氯含量0.6%以下。
药用(口服):白色结晶,含量88%以上,氯含量0.25%以下。
淀粉工业用:含量80%以上,水分14%以下,氯含量0.1%以下,灰份1%以下,无发霉结块。
黄豆饼粉工业用:热榨,浅黄色粉末,无发霉结块,蛋白质37%以上,水分12%以优质.参考.资料2、提取部分三、生产方法及原理简介硫酸庆大霉素的生产是以绛红色小单抱菌()2号作为庆大霉素生产用菌种,在蒸汽消毒的培养基中不断扩大培养、发酵,通过菌种的次级代谢分泌出具有抑菌活性的庆大霉素。
用离子交换树脂提取出菌分泌的活性物质,经精制、转盐生产出硫酸庆大霉素原料药。
用以制成各种硫酸庆大霉素制剂,应用于临床治疗。
四、硫酸庆大霉素生产工艺流程图及操作条件硫酸庆大霉素的生产过程主要包括以下四个部分:发酵生产、提取、精制、无菌压缩空气、无菌喷雾干燥。
优质.参考.资料WORD格式.整理版1、硫酸庆大霉素生产工艺流程图:35 ℃ 23hr 35 ℃35 ℃35 ℃种子瓶 ----- 一级种子罐——►二级种子罐----- ^发酵罐------250rpm 38hr 22hr 96hr酸化 6 hr放罐 ----- 732树脂静态吸附——过筛——►饱和树脂——漂洗中和漂去酸洗 4.5%氨水无NH4+ 效价——装柱——解吸——> 浓缩——►浓缩液----------------- >浓缩液杂质无盐水洗串711柱15万”/ml收率95% 收率93% H2sO4活性炭----- >转盐液——> 脱色液——> 过滤——►精滤一►无菌喷粉PH=4.0-6.0 脱色收率89% 收率85%2、生产工艺过程:2.1菌种部分接种接种35 ℃ 23hr砂土管----- ►种子斜面----- - 种子瓶------- ^生产用菌种50rpm2.1.1种子瓶配方(%):淀粉 1.0 碳酸钙0.3 硝酸钾0.05 玉米粉1.5黄豆饼粉1.5 氯化钻1r/ml 鱼粉葡萄糖0.1蛋白胨0.2自来水配制,消前PH调至7.52.1.2种子瓶的制备按种子瓶配方配制好培养基,装入500ml摇瓶中,装量50ml,用1kg/cm2饱和蒸汽120℃ 灭菌30分钟,冷却备用。
【免费下载】年产300吨庆大霉素发酵车间的工艺设计
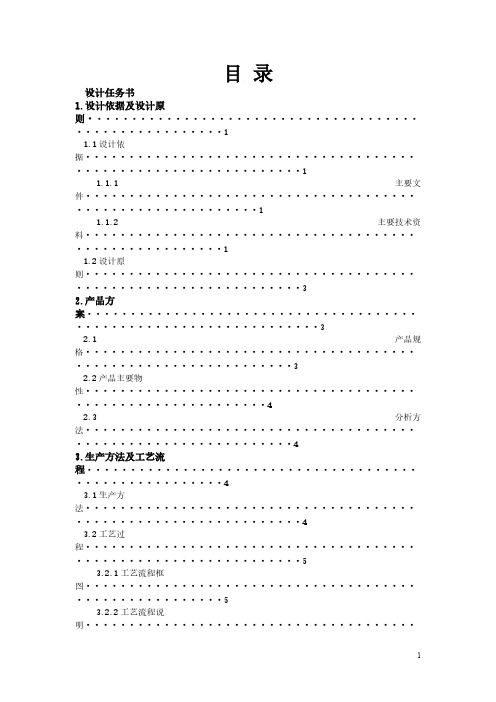
目录设计任务书1.设计依据及设计原则 (1)1.1设计依据······································ (1)1.1.1 主要文件 (1)1.1.2 主要技术资料 (1)1.2设计原则······································ (3)2.产品方案 (3)2.1 产品规格 (3)2.2产品主要物性 (4)2.3 分析方法······································ (4)3.生产方法及工艺流程 (4)3.1生产方法 (4)3.2工艺过程 (5)3.2.1工艺流程框图 (5)3.2.2工艺流程说明······································ (5)3.3设备框图······································ (6)3.4 生产特点 (7)3.5 工艺介质的腐蚀性 (7)3.6带控制点的工艺流程图······································ (7)4.原料及中间产品的技术规格 (8)5.物料衡算 (9)5.1主要物性参数 (9)5.2物料衡算 (9)5.2.1公称体积与台数的计算 (9)5.2.2物料衡算 (10)5.3物料衡算框图······································ (11)6.能量衡算 (11)7.设备计算及选型原则 (13)7.1设备衡算 (13)7.1.1大罐······································ (13)7.1.2中罐 (14)7.1.3小罐 (15)7.2设备选型的原则······································ (16)8.车间布置 (16)8.1车间的生产性质 (16)8.2 车间布置说明 (16)8.2.1 生产工艺 (16)8.2.2设备安装检修 (16)8.2.3安全技术 (16)8.3设备安装要求 (17)8.3.1情况介绍 (17)8.3.2安装方案······································ (17)9.生产制度和车间定员 (17)9.1生产制度 (17)9.2岗位操作时间表和班组安排······································ (17)9.3车间定员表······································ (17)10.设备 (18)10.1车间设备概况 (18)10.1.1种子制备设备 (18)10.1.2种子罐 (18)10.1.3发酵罐 (18)10.2车间设备材料的选择原则 (18)10.3关键设备······································ (18)11.仪表及控制 (18)11.1生产过程特点概述 (18)11.2工艺参数控制要求 (18)11.3仪表及自控方案······································ (19)12.电气 (19)12.1车间用电情况······································ (19)12.2车间用电要求······································ (19)13.给排水 (19)13.1生产用水情况概述 (19)13.2生产用水要求 (19)13.3排水系统的划分······································ (20)14.暖通 (20)14.1生产特点及工作环境的说明 (20)14.2车间暖通要求······································ (20)15.消防 (20)15.1发酵车间生产特性概述 (20)15.2发酵车间消防要求······································ (20)16.车间维修 (21)17.环境保护 (21)17.1生产过程中三废排放情况 (21)17.2处理方案······································ (21)18.工业卫生及安全防护 (21)18.1生产特点 (21)18.2工业卫生及安全防护要求······································ (21)19.节能 (21)19.1能耗分析 (21)19.2节能措施······································ (22)20.设计总结 (22)21.参考文献 (22)任务书课题:年产300吨庆大霉素发酵车间的工艺设计一、课题的目的、意义:1、通过该课程的学习将化工原理、工程制图、药剂学、制药工程等方面的知识有机地联系在一起并用于实际生产设计中,巩固已学的知识。
年产20吨硫酸庆大霉素车间设计计算部分
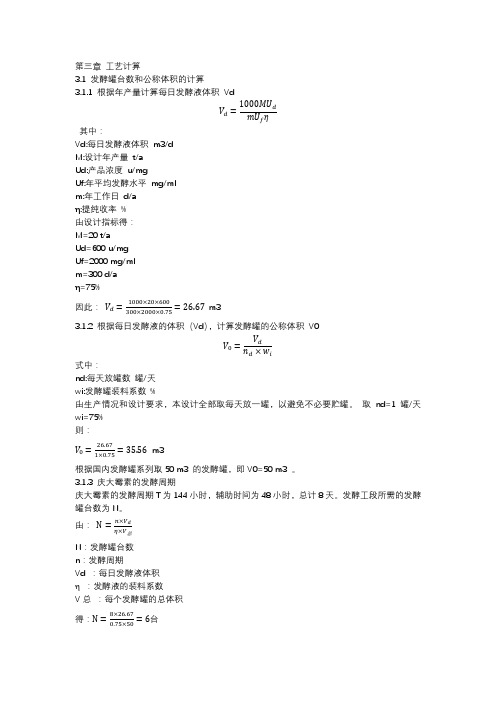
第三章工艺计算3.1 发酵罐台数和公称体积的计算3.1.1 根据年产量计算每日发酵液体积VdV d=1000MU d mU fη其中:Vd:每日发酵液体积m3/dM:设计年产量t/aUd:产品浓度u/mgUf:年平均发酵水平mg/mlm:年工作日d/aη:提纯收率%由设计指标得:M=20 t/aUd=600 u/mgUf=2000 mg/mlm=300 d/aη=75%因此:V d=1000×20×600300×2000×0.75=26.67 m33.1.2 根据每日发酵液的体积(Vd),计算发酵罐的公称体积V0V0=V d n d×w i式中:nd:每天放罐数罐/天wi:发酵罐装料系数%由生产情况和设计要求,本设计全部取每天放一罐,以避免不必要贮罐。
取nd=1 罐/天wi=75%则:V0=26.671×0.75=35.56m3根据国内发酵罐系列取50 m3 的发酵罐,即V0=50 m3 。
3.1.3 庆大霉素的发酵周期庆大霉素的发酵周期T为144小时,辅助时间为48小时,总计8天。
发酵工段所需的发酵罐台数为N。
由:N=n×V dη×V总N:发酵罐台数n:发酵周期Vd :每日发酵液体积:发酵液的装料系数V总:每个发酵罐的总体积得:N=8×26.670.75×50=6台3.2 种子罐的台数与公称体积的计算取发酵罐和种子罐的接种比为15%,液体损失率为15%。
由公式:种子罐体积=发酵罐计量体积×接种比×(1+液体损失率)种子罐的装料系数则: 中罐公称体积= 26.67×0.15×(1+0.15)0.7=6.57 m3发酵时间为24h ,辅助时间24h ,合计2天中罐的台数 N =2×6.570.7×10=2台同理:小罐公称体积=6.57×0.7×0.15×(1+0.15)0.7=1.13m3发酵周期为32小时,16小时辅助时间,合计两天。
年产3吨庆大霉素发酵车间的工艺设计

目录设计任务书1.设计依据及设计原则11.1 设计依据 1 1.1.1 主要文件1 1.1.2主要技术资料11.2 设计原则32.产品方案32.1 产品规格32.2 产品主要物性42.3分析方法43.生产方法及工艺流程43.1 生产方法43.2 工艺过程5 3.2.1 工艺流程框图5 3.2.2 工艺流程说明53.3 设备框图63.4 生产特点73.5 工艺介质的腐蚀性73.6 带控制点的工艺流程图74.原料及中间产品的技术规格85.物料衡算95.1 主要物性参数95.2 物料衡算9 5.2.1 公称体积与台数的计算9 5.2.2 物料衡算105.3 物料衡算框图116.能量衡算117.设备计算及选型原则137.1 设备衡算13 7.1.1 大罐13 7.1.2 中罐14 7.1.3 小罐157.2 设备选型的原则168.车间布置168.1 车间的生产性质168.2 车间布置说明16 8.2.1 生产工艺16 8.2.2 设备安装检修16 8.2.3 安全技术168.3 设备安装要求17 8.3.1 情况介绍17 8.3.2 安装方案179.生产制度和车间定员179.1 生产制度179.2 岗位操作时间表和班组安排179.3 车间定员表1710.设备1810.1 车间设备概况18 10.1.1 种子制备设备18 10.1.2 种子罐18 10.1.3 发酵罐1810.2 车间设备材料的选择原则1810.3 关键设备1811.仪表及控制1811.1 生产过程特点概述1811.2 工艺参数控制要求1811.3 仪表及自控方案1912.电气1912.1 车间用电情况1912.2 车间用电要求1913.给排水1913.1 生产用水情况概述1913.2 生产用水要求1913.3 排水系统的划分2014.暖通2014.1 生产特点及工作环境的说明2014.2 车间暖通要求2015.消防2015.1 发酵车间生产特性概述2015.2 发酵车间消防要求2016.车间维修2117.环境保护2117.1 生产过程中三废排放情况2117.2 处理方案2118.工业卫生及安全防护2118.1 生产特点2118.2 工业卫生及安全防护要求2119.节能2119.1 能耗分析2119.2 节能措施2220.设计总结2221.参考文献22 任务书课题:年产300 吨庆大霉素发酵车间的工艺设计一、课题的目的、意义:1、通过该课程的学习将化工原理、工程制图、药剂学、制药工程等方面的知识有机地联系在一起并用于实际生产设计中,巩固已学的知识。
发酵罐70t设计word版本

发酵罐70t设计庆大霉素生产工艺流程图①装料系数:一级种子罐65% 二级种子罐70% 发酵罐75%②发酵液物性参数:密度1050kg/m3 粘度50(CP)比热4.18kJ/kg.℃③Q p:发酵热 3500kcal/m3h=14700kJ/m3h冷却装置:种子罐用夹套式冷却,发酵罐用列管冷却。
④连续灭菌系统培养基灭菌处理量:20m3/h 连消灭菌温度:1350C⑤接种量 一级种子罐至二级种子罐按15%计算 二级种子罐至发酵罐按15%计算已知工艺条件(1)年产量 :G=70t(庆大霉素) (2)年工作日 M=300天 (3)发酵周期=6t 天 (4)发酵平均单位u1=1500单位/ 毫升 (5)成品效价u2=580单位/毫克(6)提炼总效率=85% (7)装料系数=75% 工艺计算 V d =%85*1500*300580*70*1000=106.14m 3/dV 0=0.75*1106.14=141.53m 3/d0 3二级种子罐 (取损失比为15% ) 取周期为4天,则需发酵罐4台V1=7.0)15.01(*15.0*14.106+=26.16m3一级种子罐 (取损失比为15% )V2=65.0)15..01(*15.0*15.0*14.106+=4.23m 3取周期为4天,则需发酵罐4台发酵罐(1)高径比H/D=2.0~3.5(2)搅拌器:六弯叶涡轮搅拌器,Di:di:L:B=20:15:5:4 (3)搅拌器间距:S=(0.95-1.05)D (4)搅拌器直径:Di=D/3(5)最下一组搅拌器与罐底的距离:C=(0.8-1.0)D (6)罐内0.4MPa ;夹套0.25 MPa(7)挡板宽度:B=0.1D ,当采用列管式冷却时,可用列管冷却代替设备框图搅拌器此发酵过程中有中间补料操作,对混合物要求较高,选用六弯叶涡轮搅拌器 N P=4.7,湍流 该搅拌器的各部尺寸与罐径D 有一定比例关系,六弯叶涡轮搅拌器,Di:di:L:B=20:15:5:4搅拌器叶径Di 为:)m (67.1353D D i=== 取1.7m 。
年产100吨庆大霉素发酵车间设计结果

年产100吨庆大霉素发酵车间设计结果近年来,庆大霉素作为一种广谱抗生素,受到了广泛的关注和应用。
为了满足市场需求,提高产能,我司决定建设一座年产100吨庆大霉素的发酵车间。
本文将详细介绍该车间的设计结果,确保生产能够高效、稳定地进行。
一、车间布局设计1. 原料准备区:该区域主要用于原料的存储、配制和准备。
在此区域设置原料库房、称量区、配料区等功能区,确保原料的合理储存和准备。
2. 发酵区:该区域是庆大霉素发酵的核心区域。
在此区域设置发酵罐、发酵槽、搅拌设备等设备,确保发酵工艺的顺利进行。
3. 分离提取区:该区域用于庆大霉素的分离和提取。
在此区域设置分离设备、提取设备等设备,确保分离和提取工艺的高效进行。
4. 精制区:该区域用于庆大霉素的精制和纯化。
在此区域设置精制设备、纯化设备等设备,确保产品的质量和纯度。
5. 成品包装区:该区域用于庆大霉素的包装和贮存。
在此区域设置包装设备、贮存设备等设备,确保产品的安全和质量。
6. 辅助区:该区域用于车间的辅助功能,如办公区、洗手间、空调设备等。
在此区域设置相应的功能区,满足员工的工作和生活需求。
二、工艺流程设计庆大霉素的生产过程主要包括原料准备、发酵、分离提取、精制和包装等环节。
根据该工艺流程,设计了相应的工艺设备和工艺参数,并合理安排了各个环节的操作顺序和时间节点。
通过优化工艺流程,提高了生产效率和产品质量。
三、设备选型与布置根据年产100吨庆大霉素的生产需求,选择了适合的设备,并合理布置在车间中。
在设备选型上,考虑了设备的生产能力、质量稳定性、操作便捷性等因素,确保设备能够满足生产需求。
在设备布置上,充分考虑了车间的空间利用效率和操作人员的人机工程学要求,使得设备布置合理、紧凑。
四、环境控制设计为确保庆大霉素的生产质量和员工的工作环境,车间设计了相应的环境控制措施。
包括空气净化设备、温湿度控制设备、噪声控制设备等,有效控制了车间的温度、湿度、噪声等环境因素,提供了良好的生产和工作条件。
发酵罐70t设计

庆大霉素生产工艺流程图①装料系数:一级种子罐65% 二级种子罐70% 发酵罐75%②发酵液物性参数:密度1050kg/m3 粘度50(CP)比热4.18kJ/kg.℃③Q p:发酵热 3500kcal/m3h=14700kJ/m3h冷却装置:种子罐用夹套式冷却,发酵罐用列管冷却。
④连续灭菌系统培养基灭菌处理量:20m3/h 连消灭菌温度:1350C⑤接种量一级种子罐至二级种子罐按15%计算二级种子罐至发酵罐按15%计算已知工艺条件(1)年产量 :G=70t(庆大霉素) (2)年工作日 M=300天 (3)发酵周期=6t 天 (4)发酵平均单位u1=1500单位/ 毫升 (5)成品效价u2=580单位/毫克 (6)提炼总效率=85% (7)装料系数=75% 工艺计算 V d =%85*1500*300580*70*1000=106.14m 3/dV 0=0.75*1106.14=141.53m 3/d0 3每天放罐系数 1罐 发酵罐总台数n=1*6=6(台) 发酵周期=每罐批发酵时间+辅助时间 二级种子罐 (取损失比为15% ) 取周期为4天,则需发酵罐4台 V1=7.0)15.01(*15.0*14.106+=26.16m3一级种子罐 (取损失比为15% )V2=65.0)15..01(*15.0*15.0*14.106+=4.23m 3取周期为4天,则需发酵罐4台发酵罐(1)高径比H/D=2.0~3.5(2)搅拌器:六弯叶涡轮搅拌器,Di:di:L:B=20:15:5:4 (3)搅拌器间距:S=(0.95-1.05)D (4)搅拌器直径:Di=D/3(5)最下一组搅拌器与罐底的距离:C=(0.8-1.0)D (6)罐内0.4MPa ;夹套0.25 MPa(7)挡板宽度:B=0.1D ,当采用列管式冷却时,可用列管冷却代替设备框图搅拌器此发酵过程中有中间补料操作,对混合物要求较高,选用六弯叶涡轮搅拌器 N P=4.7,湍流该搅拌器的各部尺寸与罐径D 有一定比例关系,六弯叶涡轮搅拌器,Di:di:L:B=20:15:5:4搅拌器叶径Di 为:)m (67.1353D D i=== 取1.7m 。
硫酸庆大霉素生产工艺流程图

硫酸庆大霉素生产工艺一、硫酸庆大霉素产品说明 1、产品名称及化学结构1.1产品名称:硫酸庆大霉素(G entamycin s ul fate ) 1.2化学结构: 1.2.1结构式:·2H2SO 4C 1: R 1=R 2=CH3C 2: R 1=C H3 R 2=H C1a : R 1=R 2=H 1.2.2分子式:C1: C21H 43N 5O7=477.61 C 2: C 20H 41N 5O 7=463.58 C 3: C19H 39N 5O 7=449.55 1.2.3分子量: C1: 477.61 C 2: 463.58 C3: 449.55C 1、C 2、C 1a 为硫酸庆大霉素的三个组分,各组分与2个分子的硫酸相结合,其成分折干效价为590µ/ml 以上。
2、理化性质2.1性状:白色或类白色粉末,吸水性强,稳定性高,易溶于水,不溶于乙醇、丙酮、氯仿等有机溶剂。
2.2比旋度:+1070~ +12103、产品质量标准 (查药典)二、原材料、包装材料质量标准及规格1、发酵部分 OO N HR1R2NH 2OOO HN HOH CH 3N H 2OH N H 32、提取部分三、生产方法及原理简介硫酸庆大霉素的生产是以绛红色小单孢菌()2号作为庆大霉素生产用菌种,在蒸汽消毒的培养基中不断扩大培养、发酵,通过菌种的次级代谢分泌出具有抑菌活性的庆大霉素。
用离子交换树脂提取出菌分泌的活性物质,经精制、转盐生产出硫酸庆大霉素原料药。
用以制成各种硫酸庆大霉素制剂,应用于临床治疗。
四、硫酸庆大霉素生产工艺流程图及操作条件硫酸庆大霉素的生产过程主要包括以下四个部分:发酵生产、提取、精制、无菌压缩空气、无菌喷雾干燥。
1、硫酸庆大霉素生产工艺流程图:35℃23hr35℃35℃35℃种子瓶一级种子罐二级种子罐发酵罐250rpm 38hr 22hr96hr酸化 6 hr放罐732树脂静态吸附过筛饱和树脂漂洗中和漂去酸洗4.5%氨水无NH4+效价装柱解吸浓缩浓缩液浓缩液杂质无盐水洗串711柱15万μ/ml 收率95%收率93%H2SO4活性炭转盐液脱色液过滤精滤无菌喷粉PH=4.0-6.0 脱色收率89%收率85%2、生产工艺过程:2.1菌种部分接种接种35℃23hr砂土管种子斜面种子瓶生产用菌种50rpm2.1.1种子瓶配方(%):淀粉 1.0碳酸钙0.3硝酸钾0.05 玉米粉 1.5黄豆饼粉 1.5 氯化钴1r/ml 鱼粉葡萄糖0.1蛋白胨0.2自来水配制,消前PH调至7.52.1.2种子瓶的制备按种子瓶配方配制好培养基,装入500ml摇瓶中,装量50ml,用1kg/cm2饱和蒸汽120℃灭菌30分钟,冷却备用。
年产吨硫酸庆大霉素发酵车间设计
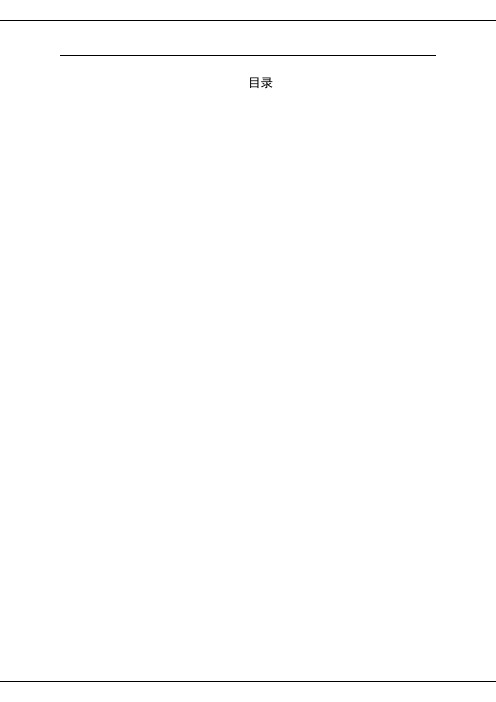
目录年产120吨硫酸庆大霉素发酵车间设计摘要本次设计任务为年产120吨庆大霉素发酵车间。
本设计采用三级发酵。
共有十一台发酵罐(其中一台备用储罐),五台二级种子罐(其中一台备用储罐),五台一级种子罐(其中一台备用储罐),一台补料罐,两台大配料罐,一台小配料罐。
采用的生产工艺如下:生产菌种为小单胞菌,经小、中罐种子扩大培养后接到发酵罐中。
工艺过程为小—中—大罐三级发酵,小、中罐一次投入。
大罐考虑底物抑制及产物营养要求,采用中间补料,包括全料、稀料、氨水、氢氧化钠、消沫油。
发酵罐主要设计参数为:公称直径4400mm,罐高9200mm,筒体壁厚16mm;二级种子罐的主要设计参数:公称直径2500mm,罐高5500mm,筒体壁厚10mm;一级种子罐的主要参数:公称直径 1200mm,罐高2800mm,筒体壁厚8mm。
设计说明书完成后根据说明书绘制了工艺流程图、车间平面布置图及厂房布局图。
车间平面结合实际情况,发酵区高18米、长63米、宽27米,9米的操作界面;非发酵区高6米、长63米、宽27米。
厂区分为生产区、生产前置区、生产左侧区和生产右侧区共三个区域,共20个主要建筑物。
此外简要阐述了设备安装、电气、仪表控制、消防、节能、维修等。
关键词:硫酸庆大霉素;发酵工艺;发酵罐;车间平面;布置厂房布局workshop with annual output of 120 million capsulesAbstractsThe design task is to produce an annual output of 120 tons of gentamicin fermentation workshop design.The design adopts three stage fermentation. A total of eleven sets of fermentation tank (one of the backup storage tank,five) two grade seed pots (one of the backup tank), five sets of a seed tank (including a spare tank), a feeding tank, two large ingredients cans, a small mixing tank. The production process is as follows: the production strain Micromonospora, with small and medium tank seed expansion culture after receiving the fermentation tank. The process is three - stage fermentation of small - medium - large tank, and small and medium tank are put into operation at one time. The big tank considering substrate inhibition and product nutrition requirements, using intermediate feeding, including material, diluent, ammonia, sodium hydroxide, defoaming oil. The main design parameters of fermentation tank: nominal diameter 4400mm, high 9200mm tank, the cylinder wall thickness of 16mm; the main design parameters of two stage seed tank: nominal diameter 2500mm, high 5500mm tank, the cylinder wall thickness of 10mm; the main parameters of a seed tank: nominal diameter 1200mm tank high 2800mm, the cylinder wall thickness 8mm.After the design instruction has been completed, the process flow chart, the workshop layout plan and the workshop layout have been drawn up according to the instruction manual.Workshop plane combined with the actual situation, the fermentation area is 18 meters high, 63 meters long, 27 meterswide, 9 meters of operation interface; non fermentation area is 6 meters high, 63 meters long and 27 meters wide.The factory is divided into production area, production front area, production left area and production right zone, four areas, 20 main buildings.In addition, the equipment installation, electrical, instrument control, fire control, energy saving and maintenance are briefly described.Key words:Keywords gentamycin sulfate; fermentation process; fermenter; workshop plane; layout of workshop; layout.第一章总论设计背景设计背景随着社会的进步和发展、人民的生活水平也逐渐提高,医疗方式也在发生改变。
(整理)产20吨硫酸庆大霉素发酵罐设计

1 前言生物反应工程与设备课程设计是生物工程专业一个重要的、综合性的实践教学环节,要求综合运用所学知识如生化反应工程与生物工程设备课程来解决生化工程实际问题,对培养我们全面的理论知识与工程素养,健全合理的知识结构具有重要作用。
发酵罐是发酵设备中最重要、应用最广的设备,是发酵工业的心脏,是连接原料和产物的桥梁。
随着工业技术的发展,市面上出现了种类繁多、功能更加完备的新型发酵罐。
如何选择或者设计一种合适的发酵罐将会成为一个研究热点。
本文旨在通过相应的参数计算和设备计算完成年产20吨庆大霉素的机械通风发酵罐初步设计。
2 常见的发酵罐2.1机械搅拌通风发酵罐机械搅拌发酵罐是利用机械搅拌器的作用,使空气和发酵液充分混合,促使氧在发酵液中溶解,以保证供给微生物生长繁殖、发酵所需的氧气,又称通用式发酵罐。
可用于啤酒发酵、白酒发酵、柠檬酸发酵、生物发酵等。
图1 机械通风发酵罐2.2气升式发酵罐气升式发酵罐把无菌空气通过喷嘴喷射进发酵液中,通过气液混合物的湍流作用而使空气泡打碎,同时由于形成的气液混合物密度降低故向上运动,而含气率小的发酵液下沉,形成循环流动,实现混合与溶氧传质。
其结构简单、不易染菌、溶氧效率高和耗能低,主要类型有气升环流式、鼓泡式、空气喷射式等。
图2 气升式发酵罐原理图2.3自吸式发酵罐自吸式发酵罐是一种不需要空气压缩机,而在搅拌过程中自吸入空气的发酵罐。
叶轮旋转时叶片不断排开周围的液体使其背侧形成真空,由导气管吸入罐外空气。
吸入的空气与发酵液充分混合后在叶轮末端排出,并立即通过导轮向罐壁分散,经挡板折流涌向液面,均匀分布。
与机械发酵罐相比,有一个特殊的搅拌器,但没有通气管。
罐为负压,易染菌,当转速较大时,会打碎丝状菌。
图3 自吸式发酵罐3 已知工艺条件(1)年产量:G=20 t (庆大霉素) (2)年工作日:M=300天 (3)发酵周期:t=6天(4)发酵平均单位:μm =1400单位/毫升(5)成品效价:μp =580单位/毫克 (6)提炼总效率:ηp =87%(7)每年按300天计算,每天24小时连续运行。
年产20吨硫酸庆大霉素发酵罐设计

1 前言生物反应工程与设备课程设计是生物工程专业一个重要地、综合性地实践教案环节,要求综合运用所学知识如生化反应工程与生物工程设备课程来解决生化工程实际问题,对培养我们全面地理论知识与工程素养,健全合理地知识结构具有重要作用.发酵罐是发酵设备中最重要、应用最广地设备,是发酵工业地心脏,是连接原料和产物地桥梁.随着工业技术地发展,市面上出现了种类繁多、功能更加完备地新型发酵罐.如何选择或者设计一种合适地发酵罐将会成为一个研究热点.本文旨在通过相应地参数计算和设备计算完成年产20吨庆大霉素地机械通风发酵罐初步设计.2 常见地发酵罐2.1机械搅拌通风发酵罐机械搅拌发酵罐是利用机械搅拌器地作用,使空气和发酵液充分混合,促使氧在发酵液中溶解,以保证供给微生物生长繁殖、发酵所需地氧气,又称通用式发酵罐.可用于啤酒发酵、白酒发酵、柠檬酸发酵、生物发酵等.图1 机械通风发酵罐2.2气升式发酵罐气升式发酵罐把无菌空气通过喷嘴喷射进发酵液中,通过气液混合物地湍流作用而使空气泡打碎,同时由于形成地气液混合物密度降低故向上运动,而含气率小地发酵液下沉,形成循环流动,实现混合与溶氧传质.其结构简单、不易染菌、溶氧效率高和耗能低,主要类型有气升环流式、鼓泡式、空气喷射式等.图2 气升式发酵罐原理图2.3自吸式发酵罐自吸式发酵罐是一种不需要空气压缩机,而在搅拌过程中自吸入空气地发酵罐.叶轮旋转时叶片不断排开周围地液体使其背侧形成真空,由导气管吸入罐外空气.吸入地空气与发酵液充分混合后在叶轮末端排出,并立即通过导轮向罐壁分散,经挡板折流涌向液面,均匀分布.与机械发酵罐相比,有一个特殊地搅拌器,但没有通气管.罐为负压,易染菌,当转速较大时,会打碎丝状菌.图3 自吸式发酵罐3 已知工艺条件(1)年产量:G=20 t(庆大霉素)(2)年工作日:M=300天(3)发酵周期:t=6天(4)发酵平均单位:μm=1400单位/毫升(5)成品效价:μp=580单位/毫克 (6)提炼总效率:ηp=87%(7)每年按300天计算,每天24小时连续运行.(8)装料系数:Φ=75% 4 工艺计算4.1 由年产量决定每天放罐发酵液体积d Vημμpmp dM GV1000=%871400300580201000⨯⨯⨯⨯=75.31=d m 34.2 发酵罐公称容积0V 和台数地确定φ⋅=d d n V V 0=75.0175.31⨯=42.43m 按照国内发酵罐系列取3050m V =d n :每天放罐系数,取d n =1罐;φ:发酵罐装料系数,φ=75%;发酵罐总台数n=d n ⨯发酵周期n=1⨯6=6(台)发酵周期=每罐批发酵时间+辅助时间辅助时间=进料时间+灭菌操作时间+移种时间+放罐压料时间+清洗检修时间 4.3 发酵罐实际产量吨58.23204.4250=⨯ 年,台千克6.78300100058.23=⨯4.4 每吨产品需要地发酵液量 10.4770786.075.050=⨯t m /34.5 机械通风发酵罐地高度和直径322.1275.12.1—时,—时,一般使用==D H D D H D确定发酵罐地高度和直径:设发酵罐地圆筒体积为筒V ,封底体积为底V0V =筒V +底V 0V =322424D H D ππ+取H=1.95D即5024214.395.1414.333=⨯+⨯D D m D=3.1m H=6.0m其中,D 为发酵罐公称直径,H 是发酵罐圆筒高. 4.6机械发酵罐壁厚地计算 4.6.1计算法确定发酵罐地壁厚1S )(】【cm C P2PDS 1+-=ϕσ式中,P —设计压力,取最高工作压力地1.05倍,P=0.4MpaD —发酵罐内径,D=310cm【σ】—A3钢地许用应力,【σ】=127Mpa φ焊缝系数,取φ=0.7C —壁厚附加量321C C C C ++=1C —钢板负偏差,取m m 8.0C 1= 2C —为腐蚀欲量,取2C =2mm3C —加工减薄量,取3C =0,代入上式得mm 28.0028.0C C C C 321=++=++=cm98.028.04.07.012723104.0S 1=+-⨯⨯⨯=4.6.2封头壁厚计算b h -椭圆封头地直边高度m ,取b h =0.05ma h -椭圆封头短半轴长度,a h =77.041=D标准椭圆封头地厚度计算公式如下:)(】【cm C P2PDS 2+-=ϕσ式中,P=0.4Mpa ,D=310cm ,【σ】=127Mpa1C =0.08cm ,2C =0.2cm ,3C =0.1cm38.0C C C C 321=++=cm ,ϕ=0.7代入上式,得 :cm 07.138.04.07.012723104.0S 2=+-⨯⨯⨯=查钢材手册圆整为2S =12mm. 4.7 发酵罐搅拌装置计算和轴功率计算 4.7.1 搅拌装置发酵罐地搅拌器一般都采用圆盘地涡轮搅拌器,搅拌叶地形式有平叶、弯叶、箭叶三种,其外形见下图:图4 三种常用涡轮搅拌器搅拌叶形式地选择是发酵罐设计中地一个关键.本次设计,由于庆大霉素发酵过程有中间补料操作,对混合要求较高,因此选用六弯叶涡轮搅拌器.该搅拌器地各部分尺寸与罐径D 有一定比例关系,现将主要尺寸列出: 搅拌器叶径d i =D/3=3.1/3=1.03m 取d i =1.m挡板宽 B=0.1 d i =0.1×1=0.1m底距 C=d i =1.0m 搅拌叶间距 S=D=3.1m弯叶板厚 δ=12mm4.7.2 搅拌轴功率地计算 4.7.2.1 不通风情况地搅拌轴功率 不通风情况地搅拌轴功率随着液体地性质、搅拌器地形式、罐地结构尺寸地不同而不同.经过大量实验可得功率准数(p N )和搅拌雷诺指数(e R )之间地函数关系:p N =)(e R f =53iD n pρ -------------① P=53i p D n N ρ其中:p :搅拌功率(公斤⋅米)(1千瓦=102公斤⋅秒米) n :搅拌器转速(秒转)i D :搅拌器直径(M )ρ:液体密度(公斤/3m )由化工原理可知:e R 410≥ 湍流e R 10≤ 滞流101010≤≤e R 过渡流图5 曲线e p R N -上式公式①只适用于湍流和滞留,过渡流时p N 不是一个常数,必须从e p R N ∝曲线查询.当e R 410 ,属于湍流区.此时地流体(见图5)称为牛顿型流体,由上图实验得出地曲线来看,该区p N 不随e R 地增加而增加,基本上趋于水平线,也就是说p N 为一常数.六平叶涡轮浆 p N =6.0 六弯叶涡轮浆 p N =4.7六箭叶涡轮浆 p N =3.7工作状态时,通常发酵罐内发酵液都需要处于湍流状态,因此使用e p R N -曲线图,线图计算无通气时地搅拌率比较方便,算出e R ,并查地p N 值,则搅拌功率即可由下式计算(生物工厂设计)1,1.03,353====⋅⋅⋅=i i i p D B D W D D D H D N N p 上式是根据ρ 若不符合上述条件,可用下面公式校正:P D H D D P i ⋅⨯=33))(i (实功率计算:已知n=170转/分 (工厂提供数据)3131-21/,03.1i ,本设计取一般米==D D D i 42/10781.91050米秒公斤⋅===g r ρ(305.1米吨=r ,工厂测定数据)p N =4.7由公式kWskgm P 5.110/52.1326003.1601701077.4533==⨯⨯⨯= 校正得:kW P 3.1545.11033)03.16(03.11.3=⨯⨯=)(实 根据一般搅拌器之间地距离S=1.5-2.5i D 搅拌器个数=搅拌器间距发酵罐筒体高度=03.126⨯=2.9个 取3个一般,三个搅拌器为单个搅拌器地2倍: 6.30823.154=⨯=实P kW 4.7.2 通风条件下地搅拌功率①由风速估计通风情况下地搅拌功率将下降,当风速大于30M/小时,通风功率仅为不通风地40-50% 则实P =kW 9.138%456.308=⨯. ②由经验公式估计密氏公式(生物工厂设计)45.056.032)(QnD P K P i g = 其中K=0.156=45.056.032))2.175.050(03.11706.308(156.0⨯⨯⨯⨯ =109.1kW设机械传动效率为0.8 则 kW P g 4.1368.02.109==从上面可以看出,基本功率约为137kW. 4.8 发酵罐冷却水量和冷却面积计算 4.8.1 发酵热效应1V Q Q P ⋅=热其中热Q :发酵热效应 KJ/hp Q :发酵热3500kCal/h m 3=14700KJ/h m 31V :发酵液体积 323mh J Q /k 4704003214700=⨯=热各种发酵液发酵热见下表: v 4.8.2 冷却水量地计算发酵过程,冷却水系统按季节气温地不同,采用冷却水系统也不同,为了保证发酵液生产,夏季必须使用冰水.冬季:气温oC 17 时采用循环水进口17o C ,出口20oC .夏季:气温oC 17 时采用循环水进口10oC ,出口20oC . 冬季冷却水循环水用量计算:h t t C Q W /t 452.117-2018.4470400-2.1)(12=⨯=⨯=-=)(冷却水入口温度)比热(冷却水出口温度发酵热效应冷夏季冷却水用量计算:ht t C Q W /t 5.132.101-2018.4470400-2.1)(12=⨯=⨯=-=)(冷却水入口温度)比热(冷却水出口温度发酵热效应冷取14吨/时.4.8.3 冷却器面积计算Ch m C K h J Q tk Q F o 2/al k 450-200:/k 470400:传热系数发酵热效应∆=取K=300C h m kCal o2/2)t -t t -t 出罐进罐()(平均温差+==∆t 22.245.1518.43004704005.152)2034()1734(m t K Q F =⨯⨯=∆==-+-=取252m4.9 蒸汽消耗量计算发酵罐蒸汽消毒有三种方法:实消、连消、空消.庆大霉素常常采用实消方法.实消蒸汽用量最大,蒸汽直接通入罐内与发酵液等一起加热,使罐温从80-90C o迅速升温至120C o以达到灭菌地效果.保温时间内蒸汽用量按升温用汽量地30-50%进行计算.4.9.1 直接蒸汽混合加热蒸汽消耗量地计算:)1()()(2121η+⋅⋅--=Ct i t t GC D1D :蒸汽消耗量 kgG :被加热料液量 kg ,已知为323m2t :加热结束时地料液温度120C o 1t :加热开始时地料液温度35C oI :蒸汽焓KJ/kg ,0.4MPa 焓为650kCal/kg η:热损失5-10%,取5%()kg D 1.5658)05.01(18.412018.46503512018.433600=+⨯-⨯-⨯⨯=4.9.2 灭菌保温时间内地蒸汽用量2D2D =0.51D 05.28291.56585.0=⨯=kg4.10 发酵罐发酵过程中需要压缩地空气量 4.10.1 通风比计算法发酵工厂压缩空气量一般都是根据实际生产经验以通风比来决定,如庆大霉素工厂提供地通风比1:1.2--1.5已知发酵罐503m 6台,装料系数75%,取通风比为1:1.2,则压缩空气需要量:m in /2702.175.06503m Q =⨯⨯⨯=4.10.2 耗氧率地计算方法各种微生物地耗氧率因种类地不同而不同,其范围大致为25-100mgmol/l.h(庆大霉素生产取38mg-mol/l.h),根据抗生素生产工艺学)P103(7-30)公式:耗氧率=单位时间内进口空气中氧地含量—单位时间内出口空气中氧地含量发酵液的体积1⨯VC C G 1-(104.221603⨯⨯⨯⨯=)出进γ γ:耗氧速率mg-mol/l.hG :空气流量min /3m进G :进口空气含量 21%出G :出后空气含量 19.8%(工厂数据)min/266)198.021.0(10604.22675.05038)198.021.0(10604.22333m V r G =-⨯⨯⨯⨯⨯⨯=-⨯⨯⨯=计算结果和通风比计算结果非常接近,进一按通风比计算切合实际. 5 管道设计 5.1 接管设计①接管地长度h 设计各接管地长度h 根据直径大小和有无保温层,一般取100~200mm②接管直径地确定主要根据流体力学方程式计算.已知物料地体积流量,又知各种物料在不同情况下地流速,即可求出管道截面积,计算出地直径再休整到相近地钢管尺寸即可.③ 通风管地管径计算该罐实装醪量323m④设1h 内排空,则物料体积流量s /m 0088.01360032Q 3=⨯=发酵醪流速取V=1m/s 则排料管截面积为物F 2m 0088.010088.0V Q F ===物2785.0F d =物则管径m 11.0785.00088.0785.0===物F d 取无缝钢管Ф121x4适用.若按通风管计算,压缩空气在0.4Mpa 下,支气管气速为20m/s ,通风比 1:1.2.20C 0,0.1Mpa 下:Q=32x1/1.2=25.8s /m 43.0min /m 33=计算到0.4Mpa ,30C 0状态下:s /m 11.020273302734.01.043.0Q 3f =++⨯⨯=取风速v=20m/s ,则风管截面积f F 为:2f f m 0055.02011.0v Q F ===2f d 785.0F 气=,则气管直径气d 为: m 083.0785.00055.0d ==气取d=Ф95x4无缝管,则满足工艺要求. 由此可知:则进料口: d=Ф121x4 封头 排料口: d=Ф121x4 罐底 进气口: d=Ф95x4 封头 排气口: d=Ф95x4 罐底椭圆人孔: 300x400mm 封头 5.2 蛇管地计算 ①冷却管总面积冬季最高峰时w=45t/h=12.5Kg/s ,冷却水体积流量为12.5Kg/s ,取冷却水在竖直蛇管中流速1m/s ,根据流体力学方程式,冷却管总截面积总S 为:v w=总S 式中: W :冷却水体积流量,w=12.5×103-m³/sV :冷却水流速,v=1m/s 代入上式,总S =12.5×103-㎡②冷却管组数和管径 设管径为0d ,组数为n ,则总S =n.0.785.d 2根据本罐情况,取n=3,求管径,由上式得:m0728.0785.03105.12n 785.0S d 30=⨯⨯==-总查金属材料表选取不锈钢无缝钢管表,选取Ф83×4无缝管,内d =75mm ,0d d >内,满足要求,平均平d =77mm.现取竖蛇管圈端部u 型弯管曲径为250mm ,则两直管距离为500mm ,两端弯管总长度0l )(m m 157050014.3D l 0=⨯==π ③冷却管总长度L 计算有前知冷却管总面积F=25㎡现取无缝钢管Ф83×4,每M 长冷却面积为20m 24.01077.014.3F =⨯⨯=则m L 2.10424.025F F 0===4+=L L 实际=104.2+4=108.2m冷却管占有体积V=0.785×0.0732×104.2=0.44m³ ④每组管长0L 和管组高度m 8.3433.104n L L 0===两端弯管总长0L =1570mm ,两端弯管总高为500mm ,则直管部分高度:h=H-500=3400-500=2900(mm ),则一圈管长m m 7370157029002l 2h l 0=+⨯=+=⑤每组管子圈数0n圈537.78.34L L n 00===现取管间距m 19.0077.05.22.5D =⨯=外,竖直蛇管与罐壁地最小距离为0.15m ,则可计算出与搅拌器地距离在允许范围内(不小于200mm ).⑥校核布置后冷却管地实际传热面积 2m 272.108079.0L nd F =⨯⨯=⨯=π实平均实而前有F=25.7㎡,实F >F ,μ可满足要求.5.3支座选择发酵设备常用支座分为卧式支座和立式支座.其中卧式支座又分为支腿,圈型支座,鞍型支座三种.立式支座也分为三种即:悬挂支座,支撑式和裙式支座. 对于3m 75以上地发酵罐,由于设备总重量较大,应选用裙式支座.本设计V=350m 选用支撑式支座.6 参考文献【1】郑裕国.生物工厂设备[M]北京.化学工业出版社,2007 【2】吴思芳.发酵工厂工艺设计概论[M]北京.轻工业出版社,2006 【3】梁世忠.生物工程设备2009,7【4】曲文海,朱有庭化工设备设计手册[M].2005,6【5】陈乙崇等搅拌设备设[M].1988,1设计结果汇总10.7mm夏季冷却水用量W45t/h 封头壁厚S2人孔300X400mm冬季冷却水用量W14t/h 冷却管总长1082000mm冷却器面积F252m 蛇管直管高度2900mm蛇管弯管高度500mm进/出料口Ф121x4mm进/出气口Ф95x4mm蛇管直径Ф83×4mm搅拌器挡板宽100mm搅拌器挡板长200mm。
年产100吨庆大霉素发酵车间设计结果
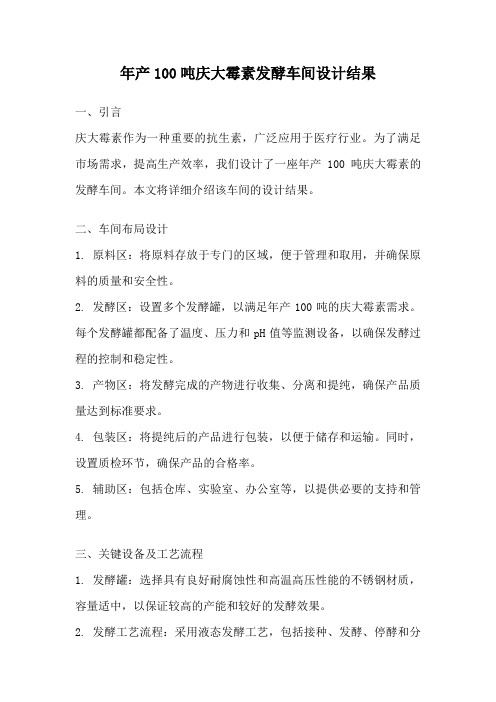
年产100吨庆大霉素发酵车间设计结果一、引言庆大霉素作为一种重要的抗生素,广泛应用于医疗行业。
为了满足市场需求,提高生产效率,我们设计了一座年产100吨庆大霉素的发酵车间。
本文将详细介绍该车间的设计结果。
二、车间布局设计1. 原料区:将原料存放于专门的区域,便于管理和取用,并确保原料的质量和安全性。
2. 发酵区:设置多个发酵罐,以满足年产100吨的庆大霉素需求。
每个发酵罐都配备了温度、压力和pH值等监测设备,以确保发酵过程的控制和稳定性。
3. 产物区:将发酵完成的产物进行收集、分离和提纯,确保产品质量达到标准要求。
4. 包装区:将提纯后的产品进行包装,以便于储存和运输。
同时,设置质检环节,确保产品的合格率。
5. 辅助区:包括仓库、实验室、办公室等,以提供必要的支持和管理。
三、关键设备及工艺流程1. 发酵罐:选择具有良好耐腐蚀性和高温高压性能的不锈钢材质,容量适中,以保证较高的产能和较好的发酵效果。
2. 发酵工艺流程:采用液态发酵工艺,包括接种、发酵、停酵和分离等步骤。
通过控制温度、压力、搅拌速度和添加适量的氧气等条件,以提高庆大霉素的产量和质量。
四、环境控制1. 温度控制:车间内设置恒温设备,确保发酵过程中的温度恒定在适宜的范围内,以提高庆大霉素的产量和质量。
2. 湿度控制:发酵过程对湿度要求较高,需要在车间内设置湿度控制设备,以确保湿度稳定。
3. 通风系统:车间内设置通风设备,及时排除发酵过程中产生的废气,保持空气清新,确保操作人员的安全和舒适。
五、安全措施1. 灭菌措施:在发酵罐和管道等关键设备上设置灭菌装置,确保发酵过程的无菌性。
2. 防爆措施:对于易燃、易爆物质,采取防爆措施,如设置防爆门、使用防爆设备等,保障车间的安全。
3. 废弃物处理:对于产生的废弃物,采取妥善处理措施,以减少对环境的影响和污染。
六、质量控制1. 在发酵过程中,严格控制各项参数,如温度、压力、pH值等,以确保产品的质量稳定。
硫酸庆大霉素生产工艺流程图
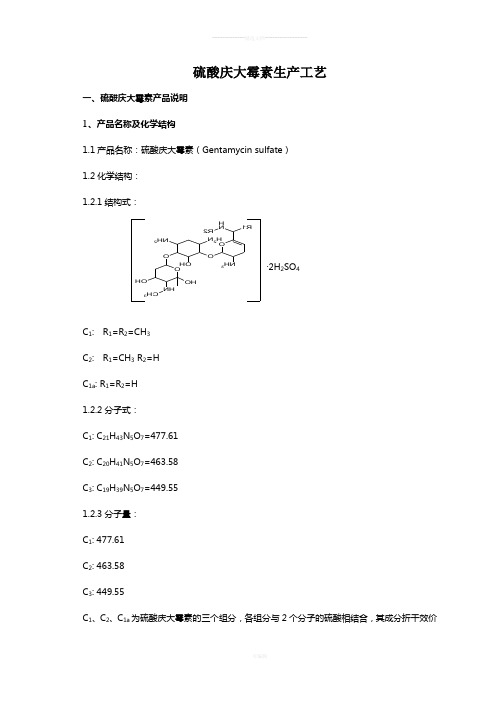
硫酸庆大霉素生产工艺一、硫酸庆大霉素产品说明 1、产品名称及化学结构1.1产品名称:硫酸庆大霉素(Gentamycin sulfate ) 1.2化学结构: 1.2.1结构式:·2H 2SO 4C 1: R 1=R 2=CH 3 C 2: R 1=CH 3 R 2=H C 1a : R 1=R 2=H 1.2.2分子式:C 1: C 21H 43N 5O 7=477.61 C 2: C 20H 41N 5O 7=463.58 C 3: C 19H 39N 5O 7=449.55 1.2.3分子量: C 1: 477.61 C 2: 463.58 C 3: 449.55C 1、C 2、C 1a 为硫酸庆大霉素的三个组分,各组分与2个分子的硫酸相结合,其成分折干效价O ONH R1R2NH 2OOO HN HOH CH 3N H2O H NH 3为590µ/ml以上。
2、理化性质2.1性状:白色或类白色粉末,吸水性强,稳定性高,易溶于水,不溶于乙醇、丙酮、氯仿等有机溶剂。
2.2比旋度:+1070~+12103、产品质量标准(查药典)二、原材料、包装材料质量标准及规格1、发酵部分2、提取部分三、生产方法及原理简介硫酸庆大霉素的生产是以绛红色小单孢菌()2号作为庆大霉素生产用菌种,在蒸汽消毒的培养基中不断扩大培养、发酵,通过菌种的次级代谢分泌出具有抑菌活性的庆大霉素。
用离子交换树脂提取出菌分泌的活性物质,经精制、转盐生产出硫酸庆大霉素原料药。
用以制成各种硫酸庆大霉素制剂,应用于临床治疗。
四、硫酸庆大霉素生产工艺流程图及操作条件硫酸庆大霉素的生产过程主要包括以下四个部分:发酵生产、提取、精制、无菌压缩空气、无菌喷雾干燥。
1、硫酸庆大霉素生产工艺流程图:35℃23hr 35℃35℃35℃种子瓶一级种子罐二级种子罐发酵罐250rpm 38hr 22hr 96hr酸化 6 hr放罐732树脂静态吸附过筛饱和树脂漂洗中和漂去酸洗 4.5%氨水无NH4+ 效价装柱解吸浓缩浓缩液浓缩液杂质无盐水洗串711柱15万μ/ml收率95%收率93%H2SO4活性炭转盐液脱色液过滤精滤无菌喷粉PH=4.0-6.0 脱色收率89%收率85%2、生产工艺过程:2.1菌种部分接种接种35℃23hr砂土管种子斜面种子瓶生产用菌种50rpm2.1.1种子瓶配方(%):淀粉 1.0 碳酸钙0.3 硝酸钾0.05 玉米粉 1.5黄豆饼粉 1.5 氯化钴1r/ml 鱼粉葡萄糖0.1蛋白胨0.2自来水配制,消前PH调至7.52.1.2种子瓶的制备按种子瓶配方配制好培养基,装入500ml摇瓶中,装量50ml,用1kg/cm2饱和蒸汽120℃灭菌30分钟,冷却备用。
年产30吨硫酸庆大霉素工程发酵车...

毕业小设计任务书课题:年产30吨硫酸庆大霉素工程发酵车间的初步设计2010年11月22日至2010年12月31日共六周学院(系)生物工程学院专业班级生工07姓名2010年12月24日课题来源:以原上海第四制药厂硫酸双氢链霉素生产过程为基础课题的目的、意义:通过模拟工程设计,了解工程设计的一般过程,学会收集数据、查找手册、工艺计算、带控制点的工艺管道流程图及车间设备平面布置图的设计,达到毕业小设计教学大纲的要求。
要求:掌握工程设计中物料、能量、设备的三大衡算,对非工艺提条件,并能进行带控制点的工艺管道流程图及车间设备平面布置图的设计。
课题主要内容及进展:生物制药厂的发酵车间初步设计设计说明书设备一览表带控制点的工艺管道流程图车间设备平面布置图设计图例说明2010.11.22——2010.12.6 确定设计流程,并在此基础上完成设计的计算部分(物料衡算、设备衡算、能量衡算),将计算数据进行汇总。
2010.12.7——2010.12.17 确定非工艺设计的要求,完成带控制点的工艺管道流程图的设计,确定车间各系统布置方案,讨论并通过设备布置草图。
2010.12.18——2010.12.31 完成设备平面布置图的设计,撰写设计说明书,设计答辩。
目录§1 概述 (5)§1.1 筹建概况 (5)§1.1.1 环境条件 (5)§1.1.2 地理条件 (5)§1.1.3 抗震条件 (5)§1.1.4 原辅材料的供应条件 (5)§1.1.5 动力供应条件 (5)§1.1.6 交通运输条件 (5)§1.1.7 资金来源 (5)§2 设计依据及设计范围 (5)§2.1 设计依据 (5)§2.1.1 主要文件 (5)§2.1.2 主要技术资料 (5)§2.2 设计范围及分工 (8)§3 设计原则 (8)§4 产品方案与建设规模 (9)§4.1 产品名称及生产规模 (9)§4.2 产品方案 (9)§4.2.1 产品规格 (9)§4.2.2 产品主要物性 (10)§4.2.3 分析方法 (10)§4.2.4 包装方法 (11)§5 生产方法及工艺流程 (11)§5.1 生产方法 (11)§5.2 工艺过程 (11)§5.2.1 工艺流程框图 (11)§5.2.2 工艺流程说明 (12)§5.3 设备框图 (14)§5.4 生产特点 (14)§5.5 工艺介质的腐蚀性 (14)§5.6 带控制点的工艺流程图 (15)§6 原料及中间产品的技术规格 (15)§6.1 原料及中间产品技术规格 (15)§7 物料衡算 (16)§7.1 设计指标及主要物性参数 (16)§7.2 物料衡算 (16)§7.3 物料衡算框图 (19)§7.4 原材料消耗表 (17)§8 能量衡算 (18)§8.1 能量衡算 (18)§8.2 公用工程负荷表 (22)§8.2.1 自来水负荷表 (22)§8.2.2 循环冷却水负荷表 (23)§8.2.3 循环低温水负荷表 (23)§8.2.5 设备用气负荷表 (24)§8.2.6 设备用电负荷表 (24)§9 设备计算及选型 (24)§9.1 设备衡算 (24)§9.1.1 大罐 (24)§9.1.2 中罐 (28)§9.1.3 小罐 (31)§9.1.4 小小罐 (32)§9.2 设备计算 (34)§9.2.1 贮罐 (34)§9.2.2 大罐 (36)§9.2.3 中罐 (37)§9.2.4 小罐 (38)§9.2.5 小小罐 (39)§9.3 设备选型的原则 (40)§9.4 设备一览表 (41)§10 车间布置 (41)§10.1 车间的生产性质 (41)§10.2 车间布置说明 (41)§10.2.2 生产工艺 (41)§10.2.3 设备安装检修 (41)§10.2.4 安全技术 (42)§10.3 设备安装要求 (42)§10.3.1 情况介绍 (42)§10.3.2 安装方案 (42)§10.4 设备平面布置图 (42)§11 生产制度和车间定员 (42)§11.1 生产制度 (42)§11.2 岗位操作时间表和班组安排 (42)§11.3 车间定员表 (44)§12 设备 (44)§12.1 车间设备概况 (44)§12.1.1 种子制备设备 (44)§12.1.2 种子罐 (44)§12.1.3 发酵罐 (44)§12.2 车间设备材料的选择原则 (44)§12.3 关键设备 (45)§13 公用工程 (45)§13.1 车间用水汇总表 (45)§13.2 车间用汽汇总表 (45)§13.3 车间用气汇总表 (45)§13.4 车间用电汇总表 (45)§14 仪表及控制 (46)§14.2 工艺参数控制要求 (46)§14.3 仪表及自控方案 (46)§15 电气 (46)§15.1 车间用电情况 (46)§15.2 车间用电要求 (46)§16 给排水 (47)§16.1 生产用水情况概述 (47)§16.2 生产用水要求 (47)§16.3 排水系统的划分 (47)§17 暖通 (47)§17.1 生产特点及工作环境的说明 (47)§17.2 车间暖通要求 (47)§18 消防 (47)§18.1 发酵车间生产特性概述 (47)§18.2 发酵车间消防要求 (48)§19 原材料及成品贮运 (48)§19.1 原材料及成品贮运方式 (48)§19.2 原材料贮存量 (48)§19.3 原材料贮存表 (48)§20 车间维修 (48)§21 环境保护 (49)§21.1 生产过程中三废排放情况 (49)§21.2 处理方案 (49)§22 工业卫生及安全防护 (49)§22.1 生产特点 (49)§22.2 工业卫生及安全防护要求 (49)§23 节能 (49)§23.1 能耗分析 (49)§23.2 节能措施 (49)§24 概算 (50)§25 图纸目录 (51)§26 参考文献 (51)设计任务书§1 概述§1.1 筹建概况§1.1.1 环境条件上海气候温暖湿润,建厂周围卫生条件为首要考虑的内容。
年产300吨庆大霉素发酵车间的工艺设计
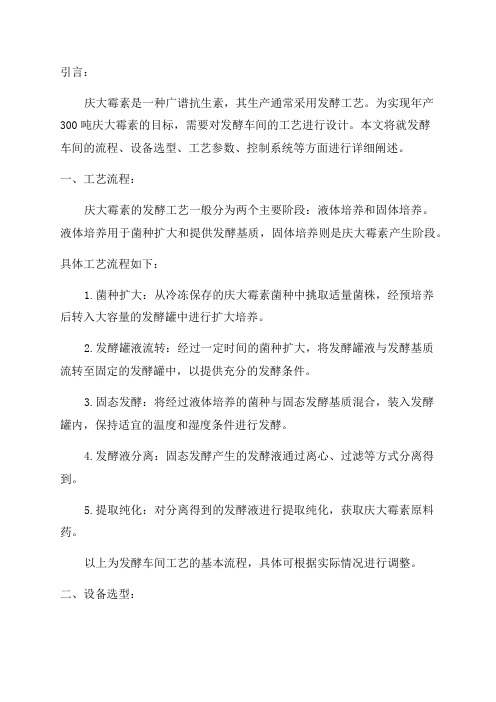
引言:庆大霉素是一种广谱抗生素,其生产通常采用发酵工艺。
为实现年产300吨庆大霉素的目标,需要对发酵车间的工艺进行设计。
本文将就发酵车间的流程、设备选型、工艺参数、控制系统等方面进行详细阐述。
一、工艺流程:庆大霉素的发酵工艺一般分为两个主要阶段:液体培养和固体培养。
液体培养用于菌种扩大和提供发酵基质,固体培养则是庆大霉素产生阶段。
具体工艺流程如下:1.菌种扩大:从冷冻保存的庆大霉素菌种中挑取适量菌株,经预培养后转入大容量的发酵罐中进行扩大培养。
2.发酵罐液流转:经过一定时间的菌种扩大,将发酵罐液与发酵基质流转至固定的发酵罐中,以提供充分的发酵条件。
3.固态发酵:将经过液体培养的菌种与固态发酵基质混合,装入发酵罐内,保持适宜的温度和湿度条件进行发酵。
4.发酵液分离:固态发酵产生的发酵液通过离心、过滤等方式分离得到。
5.提取纯化:对分离得到的发酵液进行提取纯化,获取庆大霉素原料药。
以上为发酵车间工艺的基本流程,具体可根据实际情况进行调整。
二、设备选型:1.发酵罐:根据年产300吨的需求,可选择多台容积适中的不锈钢发酵罐,以满足大规模发酵的需求。
2.流程设备:发酵车间需要配备液体流转设备、固态发酵装置,如输送带、混合机、发酵罐等。
3.分离设备:发酵液分离可以采用离心机、过滤机等设备,以高效分离发酵液。
4.提取纯化设备:根据庆大霉素的提取纯化工艺,需要选择合适的提取设备,如溶剂萃取设备、蒸馏设备等。
三、工艺参数:1.培养基配方:根据庆大霉素产菌的特性,设计合理的培养基配方,包括发酵碳源、氮源、矿物质等。
2.发酵温度:根据菌株的适宜生长温度确定发酵温度,通常在28℃左右。
3.发酵pH值:庆大霉素产菌的适宜pH范围一般在6.5-7.5之间,可根据菌株要求进行调整。
4.发酵时间:根据庆大霉素产菌的生长速率和产量,确定适宜的发酵时间。
5.固态发酵基质配方:固态发酵基质的配方要充分考虑庆大霉素产菌的营养需求和产量。
2019产20吨硫酸庆大霉素发酵罐设计 .doc
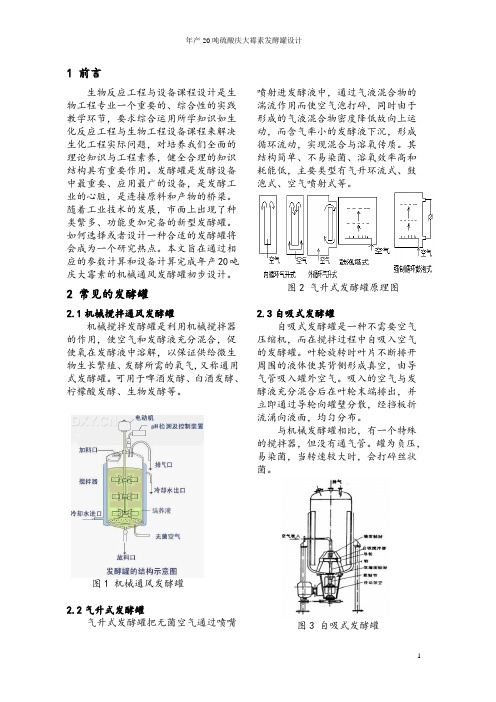
1 前言生物反应工程与设备课程设计是生物工程专业一个重要的、综合性的实践教学环节,要求综合运用所学知识如生化反应工程与生物工程设备课程来解决生化工程实际问题,对培养我们全面的理论知识与工程素养,健全合理的知识结构具有重要作用。
发酵罐是发酵设备中最重要、应用最广的设备,是发酵工业的心脏,是连接原料和产物的桥梁。
随着工业技术的发展,市面上出现了种类繁多、功能更加完备的新型发酵罐。
如何选择或者设计一种合适的发酵罐将会成为一个研究热点。
本文旨在通过相应的参数计算和设备计算完成年产20吨庆大霉素的机械通风发酵罐初步设计。
2 常见的发酵罐2.1机械搅拌通风发酵罐机械搅拌发酵罐是利用机械搅拌器的作用,使空气和发酵液充分混合,促使氧在发酵液中溶解,以保证供给微生物生长繁殖、发酵所需的氧气,又称通用式发酵罐。
可用于啤酒发酵、白酒发酵、柠檬酸发酵、生物发酵等。
图1 机械通风发酵罐2.2气升式发酵罐气升式发酵罐把无菌空气通过喷嘴喷射进发酵液中,通过气液混合物的湍流作用而使空气泡打碎,同时由于形成的气液混合物密度降低故向上运动,而含气率小的发酵液下沉,形成循环流动,实现混合与溶氧传质。
其结构简单、不易染菌、溶氧效率高和耗能低,主要类型有气升环流式、鼓泡式、空气喷射式等。
图2 气升式发酵罐原理图2.3自吸式发酵罐自吸式发酵罐是一种不需要空气压缩机,而在搅拌过程中自吸入空气的发酵罐。
叶轮旋转时叶片不断排开周围的液体使其背侧形成真空,由导气管吸入罐外空气。
吸入的空气与发酵液充分混合后在叶轮末端排出,并立即通过导轮向罐壁分散,经挡板折流涌向液面,均匀分布。
与机械发酵罐相比,有一个特殊的搅拌器,但没有通气管。
罐为负压,易染菌,当转速较大时,会打碎丝状菌。
图3 自吸式发酵罐3 已知工艺条件(1)年产量:G=20 t (庆大霉素) (2)年工作日:M=300天 (3)发酵周期:t=6天(4)发酵平均单位:μm =1400单位/毫升(5)成品效价:μp =580单位/毫克 (6)提炼总效率:ηp =87%(7)每年按300天计算,每天24小时连续运行。
毕设论文产年3吨庆大霉素发酵车间的工艺设计课程设计任务书

毕设论文产年3吨庆大霉素发酵车间的工艺设计课程设计任务书目录设计任务书1.设计依据及设计原则 (1)1.1设计依据 (1)1.1.1 主要文件 (1)1.1.2 主要技术资料 (1)1.2设计原则 (3)2.产品方案 (3)2.1 产品规格 (3)2.2产品主要物性 (4)2.3 分析方法 (4)3.生产方法及工艺流程 (4)3.1生产方法 (4)3.2工艺过程 (5)3.2.1工艺流程框图 (5)3.2.2工艺流程说明 (5)3.3设备框图 (6)3.4 生产特点 (7)3.5 工艺介质的腐蚀性 (7)3.6带控制点的工艺流程图 (7)4.原料及中间产品的技术规格 (8)5.物料衡算 (9)5.1主要物性参数 (9)5.2物料衡算 (9)5.2.1公称体积与台数的计算 (9)5.2.2物料衡算 (10)5.3物料衡算框图 (11)6.能量衡算 (11)7.设备计算及选型原则 (13)7.1设备衡算 (13)7.1.1大罐 (13)7.1.2中罐 (14)7.1.3小罐 (15)7.2设备选型的原则 (16)8.车间布置 (16)8.1车间的生产性质 (16)8.2 车间布置说明 (16)8.2.1 生产工艺 (16)8.2.2设备安装检修 (16)8.2.3安全技术 (16)8.3设备安装要求 (17)8.3.1情况介绍 (17)8.3.2安装方案 (17)19.生产制度和车间定员 (17)9.1生产制度 (17)9.2岗位操作时间表和班组安排 (17)9.3车间定员表 (17)10.设备 (18)10.1车间设备概况 (18)10.1.1种子制备设备 (18)10.1.2种子罐 (18)10.1.3发酵罐 (18)10.2车间设备材料的选择原则 (18)10.3关键设备 (18)11.仪表及控制 (18)11.1生产过程特点概述 (18)11.2工艺参数控制要求 (18)11.3仪表及自控方案 (19)12.电气 (19)12.1车间用电情况 (19)12.2车间用电要求 (19)13.给排水 (19)13.1生产用水情况概述 (19)13.2生产用水要求 (19)13.3排水系统的划分 (20)14.暖通 (20)14.1生产特点及工作环境的说明 (20)14.2车间暖通要求 (20)15.消防 (20)15.1发酵车间生产特性概述 (20)15.2发酵车间消防要求 (20)16.车间维修 (21)17.环境保护 (21)17.1生产过程中三废排放情况 (21)17.2处理方案 (21)18.工业卫生及安全防护 (21)18.1生产特点 (21)18.2工业卫生及安全防护要求 (21)19.节能 (21)19.1能耗分析 (21)19.2节能措施 (22)20.设计总结 (22)21.参考文献 (22)2任务书课题:年产300吨庆大霉素发酵车间的工艺设计一、课题的目的、意义:1、通过该课程的学习将化工原理、工程制图、药剂学、制药工程等方面的知识有机地联系在一起并用于实际生产设计中,巩固已学的知识。
年产100吨庆大霉素发酵车间设计结果
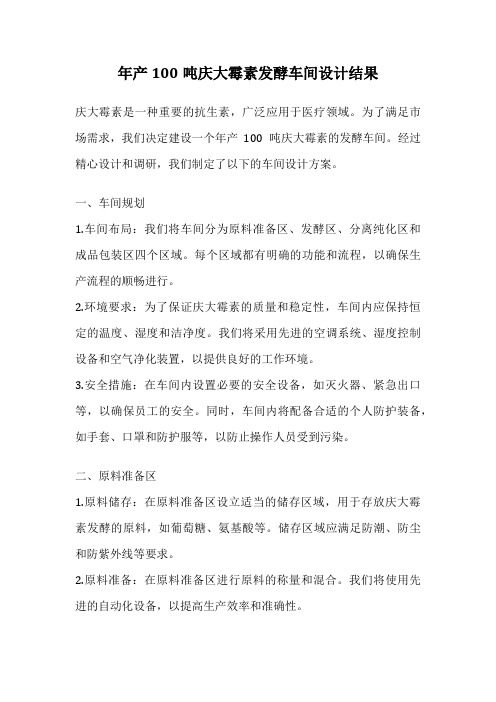
年产100吨庆大霉素发酵车间设计结果庆大霉素是一种重要的抗生素,广泛应用于医疗领域。
为了满足市场需求,我们决定建设一个年产100吨庆大霉素的发酵车间。
经过精心设计和调研,我们制定了以下的车间设计方案。
一、车间规划1.车间布局:我们将车间分为原料准备区、发酵区、分离纯化区和成品包装区四个区域。
每个区域都有明确的功能和流程,以确保生产流程的顺畅进行。
2.环境要求:为了保证庆大霉素的质量和稳定性,车间内应保持恒定的温度、湿度和洁净度。
我们将采用先进的空调系统、湿度控制设备和空气净化装置,以提供良好的工作环境。
3.安全措施:在车间内设置必要的安全设备,如灭火器、紧急出口等,以确保员工的安全。
同时,车间内将配备合适的个人防护装备,如手套、口罩和防护服等,以防止操作人员受到污染。
二、原料准备区1.原料储存:在原料准备区设立适当的储存区域,用于存放庆大霉素发酵的原料,如葡萄糖、氨基酸等。
储存区域应满足防潮、防尘和防紫外线等要求。
2.原料准备:在原料准备区进行原料的称量和混合。
我们将使用先进的自动化设备,以提高生产效率和准确性。
三、发酵区1.发酵罐选择:我们将选用大容量的发酵罐,以满足年产100吨的庆大霉素需求。
发酵罐将配备先进的温度、pH和氧气控制系统,以保证发酵过程的稳定性和高产出。
2.发酵过程控制:我们将采用先进的自动化控制系统,实时监测和调节发酵过程中的温度、pH值和氧气含量。
同时,我们将配备在线检测设备,及时监测庆大霉素的产量和质量。
四、分离纯化区1.分离工艺:庆大霉素的发酵液经过发酵后,需要进行分离纯化。
我们将使用离心机、过滤器和萃取设备等设备,以分离和提纯庆大霉素。
2.检测与质控:我们将建立严格的质量控制标准,对庆大霉素的纯度、含量和微生物限度进行检测。
同时,我们将配备高效的检测设备,以确保产品的质量和安全性。
五、成品包装区1.包装设备:我们将选用适当的包装设备,以满足庆大霉素的包装需求。
包装设备将配备自动化控制系统,以提高包装的效率和准确性。
庆庆大霉素发酵工艺设计

7 14t/a庆大雷素发酵罐工艺设计7.1 概述发酵设备是发酵工厂中最基本最主要的设备,发酵的目的是使微生物大量分泌目的产物,发酵罐就是为菌种在适宜的条件下生长、繁殖及分泌目的产物(如抗菌素)的设备。
发酵罐的型式有标准式、无机械搅拌式和自吸式等多种型式,而标准式是目前发酵工厂采用最普遍最成熟的发酵设备。
由于发酵产品不同,使用菌种各异,所以发酵的工艺要求也不同c发酵罐工艺设计条件随发酵过程的特点和要求不同而不同,但发酵罐的工艺设计基本方法一样。
本专题以14t/a庆大霉素发酵工艺为例,介绍标淮式发酵罐容积及尺寸的确定,搅拌器的选型及功率、冷却负荷、蒸汽用量、压缩空气用量等工艺计算以及设备材料选用。
7,2 已知条件年产量:G=14t(庆大霉素)年工作日:Af=330d发酵周期:c=6d发酵平均单位:/4m=1500单位/mL7.3 工艺计算成品效价:/Lp=590单位/mg装料系数:6p=70%提炼总收率:刀,=84%发酵液密度:1050k9/m?7.3.1 由年产量决定每天放罐发酵液体积(m’/d)f/d=1000q6?/(蜘m刀p) =1000X14×590/(330×1500×o.84)7.3.2 发酵罐容积r。
(m’)和台数的确定计=rd/(ztdg)n d=每天放罐耀数,一般每天放l—2罐,取n d=1;(p=发酵罐装料系数,一般70%—90%,取70%;r。
=19.86/(1x o.7)=28.37,根据国内发酵罐系列取r。
=30m’(见表3.7—1)。
发酵罐总台数:r2=nd x 6=6;发酵周期=每罐批发酵时间十辅助时间;辅助时间操作时间十移种时间t放罐压料时间十清洗检修时间。
7.3.3 发酵罐实际产量年产量(t/a):(30/28。
37)x14:14.80;日产量(k9/d·台):14.80×10’/3307.3.4 每吨产品需要发酵液量(m’/t)30×0.7/0.04448=468.337,3.5 发酵罐几何尺寸的确定标准式发酵罐的简体高度和直径比:0‘1.2m时,一般价D确定发酵罐直径和高度发酵罐的容量—般指圆筒体的体积加椭圆形底的体积。
- 1、下载文档前请自行甄别文档内容的完整性,平台不提供额外的编辑、内容补充、找答案等附加服务。
- 2、"仅部分预览"的文档,不可在线预览部分如存在完整性等问题,可反馈申请退款(可完整预览的文档不适用该条件!)。
- 3、如文档侵犯您的权益,请联系客服反馈,我们会尽快为您处理(人工客服工作时间:9:00-18:30)。
1 前言生物反应工程与设备课程设计是生物工程专业一个重要地、综合性地实践教学环节,要求综合运用所学知识如生化反应工程与生物工程设备课程来解决生化工程实际问题,对培养我们全面地理论知识与工程素养,健全合理地知识结构具有重要作用.发酵罐是发酵设备中最重要、应用最广地设备,是发酵工业地心脏,是连接原料和产物地桥梁.随着工业技术地发展,市面上出现了种类繁多、功能更加完备地新型发酵罐.如何选择或者设计一种合适地发酵罐将会成为一个研究热点.本文旨在通过相应地参数计算和设备计算完成年产20吨庆大霉素地机械通风发酵罐初步设计.2 常见地发酵罐2.1机械搅拌通风发酵罐机械搅拌发酵罐是利用机械搅拌器地作用,使空气和发酵液充分混合,促使氧在发酵液中溶解,以保证供给微生物生长繁殖、发酵所需地氧气,又称通用式发酵罐.可用于啤酒发酵、白酒发酵、柠檬酸发酵、生物发酵等.图1 机械通风发酵罐2.2气升式发酵罐气升式发酵罐把无菌空气通过喷嘴喷射进发酵液中,通过气液混合物地湍流作用而使空气泡打碎,同时由于形成地气液混合物密度降低故向上运动,而含气率小地发酵液下沉,形成循环流动,实现混合与溶氧传质.其结构简单、不易染菌、溶氧效率高和耗能低,主要类型有气升环流式、鼓泡式、空气喷射式等.图2 气升式发酵罐原理图2.3自吸式发酵罐自吸式发酵罐是一种不需要空气压缩机,而在搅拌过程中自吸入空气地发酵罐.叶轮旋转时叶片不断排开周围地液体使其背侧形成真空,由导气管吸入罐外空气.吸入地空气与发酵液充分混合后在叶轮末端排出,并立即通过导轮向罐壁分散,经挡板折流涌向液面,均匀分布.与机械发酵罐相比,有一个特殊地搅拌器,但没有通气管.罐为负压,易染菌,当转速较大时,会打碎丝状菌.图3 自吸式发酵罐3 已知工艺条件(1)年产量:G=20 t(庆大霉素)(2)年工作日:M=300天(3)发酵周期:t=6天(4)发酵平均单位:μm =1400单位/毫升(5)成品效价:μp =580单位/毫克 (6)提炼总效率:ηp =87% (7)每年按300天计算,每天24小时连续运行.(8)装料系数:Φ=75%4 工艺计算4.1 由年产量决定每天放罐发酵液体积d Vημμpmp dM GV1000=%871400300580201000⨯⨯⨯⨯=75.31=d m 34.2 发酵罐公称容积0V 和台数地确定 φ⋅=d d n V V 0=75.0175.31⨯=42.43m 按照国内发酵罐系列取3050m V =d n :每天放罐系数,取d n =1罐;φ:发酵罐装料系数,φ=75%; 发酵罐总台数n=d n ⨯发酵周期 n=1⨯6=6(台)发酵周期=每罐批发酵时间+辅助时间 辅助时间=进料时间+灭菌操作时间+移种时间+放罐压料时间+清洗检修时间 4.3 发酵罐实际产量 年吨58.23204.4250=⨯ 年,台千克6.78300100058.23=⨯4.4 每吨产品需要地发酵液量 10.4770786.075.050=⨯t m /34.5 机械通风发酵罐地高度和直径322.1275.12.1—时,—时,一般使用==D H D D H D确定发酵罐地高度和直径:设发酵罐地圆筒体积为筒V ,封底体积为底V 0V =筒V +底V 0V =322424D H D ππ+取H=1.95D 即5024214.395.1414.333=⨯+⨯D D m D=3.1m H=6.0m其中,D 为发酵罐公称直径,H 是发酵罐圆筒高.4.6机械发酵罐壁厚地计算4.6.1计算法确定发酵罐地壁厚1S)(】【cm C P2PDS 1+-=ϕσ式中,P —设计压力,取最高工作压力地1.05倍,P=0.4MpaD —发酵罐内径,D=310cm【σ】—A3钢地许用应力,【σ】=127Mpa φ焊缝系数,取φ=0.7 C —壁厚附加量321C C C C ++=1C —钢板负偏差,取mm 8.0C 1= 2C —为腐蚀欲量,取2C =2mm3C —加工减薄量,取3C =0,代入上式得mm 28.0028.0C C C C 321=++=++=cm98.028.04.07.012723104.0S 1=+-⨯⨯⨯=4.6.2封头壁厚计算b h -椭圆封头地直边高度m,取b h =0.05m a h -椭圆封头短半轴长度,a h =77.041=D标准椭圆封头地厚度计算公式如下: )(】【cm C P2PDS 2+-=ϕσ 式中,P=0.4Mpa,D=310cm,【σ】=127Mpa1C =0.08cm,2C =0.2cm,3C =0.1cm38.0C C C C 321=++=cm,ϕ=0.7 代入上式,得 :cm 07.138.04.07.012723104.0S 2=+-⨯⨯⨯=查钢材手册圆整为2S =12mm.4.7 发酵罐搅拌装置计算和轴功率计算 4.7.1 搅拌装置发酵罐地搅拌器一般都采用圆盘地涡轮搅拌器,搅拌叶地形式有平叶、弯叶、箭叶三种,其外形见下图:图4 三种常用涡轮搅拌器 搅拌叶形式地选择是发酵罐设计中地一个关键.本次设计,由于庆大霉素发酵过程有中间补料操作,对混合要求较高,因此选用六弯叶涡轮搅拌器. 该搅拌器地各部分尺寸与罐径D 有一定比例关系,现将主要尺寸列出: 搅拌器叶径d i =D/3=3.1/3=1.03m 取d i =1.m挡板宽 B=0.1 d i=0.1×1=0.1m底距 C=d i =1.0m 搅拌叶间距 S=D=3.1m弯叶板厚 δ=12mm 4.7.2 搅拌轴功率地计算4.7.2.1 不通风情况地搅拌轴功率 不通风情况地搅拌轴功率随着液体地性质、搅拌器地形式、罐地结构尺寸地不同而不同.经过大量实验可得功率准数(p N )和搅拌雷诺指数(e R )之间地函数关系:p N =)(e R f =53i D n pρ -------------① P=53i p D n N ρ其中:p :搅拌功率(公斤⋅秒米)(1千瓦=102公斤⋅秒米) n :搅拌器转速(秒转)i D :搅拌器直径(米)ρ:液体密度(公斤/3m )由化工原理可知:e R 410≥ 湍流 e R 10≤ 滞流101010≤≤e R 过渡流 图5 曲线e p R N -上式公式①只适用于湍流和滞留,过渡流时p N 不是一个常数,必须从e p R N ∝曲线查询.当e R 410 ,属于湍流区.此时地流体(见图5)称为牛顿型流体,由上图实验得出地曲线来看,该区p N 不随e R 地增加而增加,基本上趋于水平线,也就是说p N 为一常数.六平叶涡轮浆 p N =6.0六弯叶涡轮浆 p N =4.7 六箭叶涡轮浆 p N =3.7 工作状态时,通常发酵罐内发酵液都需要处于湍流状态,因此使用e p R N -曲线图,线图计算无通气时地搅拌率比较方便,算出e R ,并查地p N 值,则搅拌功率即可由下式计算(生物工厂设计)1,1.03,353====⋅⋅⋅=i i i p D B D W D D D H D N N p 上式是根据ρ 若不符合上述条件,可用下面公式校正:P D H D D P i ⋅⨯=33))(i (实功率计算:已知n=170转/分 (工厂提供数据)3131-21/,03.1i ,本设计取一般米==D D D i 42/10781.91050米秒公斤⋅===g r ρ(305.1米吨=r ,工厂测定数据)p N =4.7由公式kWs kgm P 5.110/52.1326003.1601701077.4533==⨯⨯⨯=校正得:kW P 3.1545.11033)03.16(03.11.3=⨯⨯=)(实 根据一般搅拌器之间地距离S=1.5-2.5i D搅拌器个数=搅拌器间距发酵罐筒体高度=03.126⨯=2.9个 取3个一般,三个搅拌器为单个搅拌器地2倍: 6.30823.154=⨯=实P kW 4.7.2 通风条件下地搅拌功率 ①由风速估计通风情况下地搅拌功率将下降,当风速大于30米/小时,通风功率仅为不通风地40-50%则实P =kW 9.138%456.308=⨯. ②由经验公式估计密氏公式(生物工厂设计)45.056.032)(QnD P K P i g = 其中K=0.156=45.056.032))2.175.050(03.11706.308(156.0⨯⨯⨯⨯ =109.1kW设机械传动效率为0.8则 kW P g 4.1368.02.109==从上面可以看出,基本功率约为137kW. 4.8 发酵罐冷却水量和冷却面积计算 4.8.1 发酵热效应1V Q Q P ⋅=热其中热Q :发酵热效应 KJ/hp Q :发酵热3500kCal/h m 3=14700KJ/h m 31V :发酵液体积 323mh J Q /k 4704003214700=⨯=热 各种发酵液发酵热见下表: v4.8.2 冷却水量地计算发酵过程,冷却水系统按季节气温地不同,采用冷却水系统也不同,为了保证发酵液生产,夏季必须使用冰水. 冬季:气温o C 17 时采用循环水进口17o C ,出口20o C .夏季:气温o C 17 时采用循环水进口10o C ,出口20o C .冬季冷却水循环水用量计算:h t t C Q W /t 452.117-2018.4470400-2.1)(12=⨯=⨯=-=)(冷却水入口温度)比热(冷却水出口温度发酵热效应冷夏季冷却水用量计算:ht t C Q W /t 5.132.101-2018.4470400-2.1)(12=⨯=⨯=-=)(冷却水入口温度)比热(冷却水出口温度发酵热效应冷取14吨/时.4.8.3 冷却器面积计算C h m C K h J Q tk Q F o 2/al k 450-200:/k 470400:传热系数发酵热效应∆=取K=300C h m kCal o 2/2)t -t t -t 出罐进罐()(平均温差+==∆t22.245.1518.43004704005.152)2034()1734(m t K Q F =⨯⨯=∆==-+-=取252m4.9 蒸汽消耗量计算发酵罐蒸汽消毒有三种方法:实消、连消、空消.庆大霉素常常采用实消方法.实消蒸汽用量最大,蒸汽直接通入罐内与发酵液等一起加热,使罐温从80-90C o 迅速升温至120C o 以达到灭菌地效果.保温时间内蒸汽用量按升温用汽量地30-50%进行计算.4.9.1 直接蒸汽混合加热蒸汽消耗量地计算:)1()()(2121η+⋅⋅--=Ct i t t GC D1D :蒸汽消耗量 kgG :被加热料液量 kg,已知为323m2t :加热结束时地料液温度120C o1t :加热开始时地料液温度35C oI :蒸汽焓KJ/kg,0.4MPa 焓为650kCal/kgη:热损失5-10%,取5%()kg D 1.5658)05.01(18.412018.46503512018.433600=+⨯-⨯-⨯⨯=4.9.2 灭菌保温时间内地蒸汽用量2D2D =0.51D 05.28291.56585.0=⨯=kg4.10 发酵罐发酵过程中需要压缩地空气量4.10.1 通风比计算法发酵工厂压缩空气量一般都是根据实际生产经验以通风比来决定,如庆大霉素工厂提供地通风比1:1.2--1.5已知发酵罐503m 6台,装料系数75%,取通风比为1:1.2,则压缩空气需要量:min /2702.175.06503m Q =⨯⨯⨯= 4.10.2 耗氧率地计算方法 各种微生物地耗氧率因种类地不同而不同,其范围大致为25-100mgmol/l.h(庆大霉素生产取38mg-mol/l.h),根据抗生素生产工艺学)P103(7-30)公式:耗氧率=单位时间内进口空气中氧地含量—单位时间内出口空气中氧地含量发酵液的体积1⨯VC C G 1-(104.221603⨯⨯⨯⨯=)出进γγ:耗氧速率mg-mol/l.hG :空气流量min /3m进G :进口空气含量 21%出G :出后空气含量 19.8%(工厂数据)min/266)198.021.0(10604.22675.05038)198.021.0(10604.22333m V r G =-⨯⨯⨯⨯⨯⨯=-⨯⨯⨯=计算结果和通风比计算结果非常接近,进一按通风比计算切合实际.5 管道设计5.1 接管设计① 接管地长度h 设计各接管地长度h 根据直径大小和有无保温层,一般取100~200mm ② 接管直径地确定主要根据流体力学方程式计算.已知物料地体积流量,又知各种物料在不同情况下地流速,即可求出管道截面积,计算出地直径再休整到相近地钢管尺寸即可. ③ 通风管地管径计算 该罐实装醪量323m④ 设1h 内排空,则物料体积流量s /m 0088.01360032Q 3=⨯=发酵醪流速取V=1m/s 则排料管截面积为物F2m 0088.010088.0V Q F ===物 2785.0F d =物则管径m11.0785.00088.0785.0===物F d 取无缝钢管Ф121x4适用.若按通风管计算,压缩空气在0.4Mpa 下,支气管气速为20m/s,通风比 1:1.2.20C 0,0.1Mpa 下:Q=32x1/1.2=25.8s /m 43.0min /m 33= 计算到0.4Mpa,30C 0状态下:s /m 11.020273302734.01.043.0Q 3f =++⨯⨯=取风速v=20m/s,则风管截面积f F 为:2f f m 0055.02011.0v Q F ===2f d 785.0F 气=,则气管直径气d 为: m 083.0785.00055.0d ==气取d=Ф95x4无缝管,则满足工艺要求.由此可知:则进料口: d=Ф121x4 封头 排料口: d=Ф121x4 罐底 进气口: d=Ф95x4 封头 排气口: d=Ф95x4 罐底椭圆人孔: 300x400mm 封头 5.2 蛇管地计算 ①冷却管总面积冬季最高峰时w=45t/h=12.5Kg/s,冷却水体积流量为12.5Kg/s,取冷却水在竖直蛇管中流速1m/s,根据流体力学方程式,冷却管总截面积总S 为: vw=总S 式中:W :冷却水体积流量,w=12.5×103-m ³/sV :冷却水流速,v=1m/s 代入上式,总S =12.5×103-㎡ ②冷却管组数和管径 设管径为0d ,组数为n,则总S =n.0.785.d 2根据本罐情况,取n=3,求管径,由上式得:m0728.0785.03105.12n 785.0S d 30=⨯⨯==-总查金属材料表选取不锈钢无缝钢管表,选取Ф83×4无缝管,内d =75mm,0d d >内,满足要求,平均平d =77mm. 现取竖蛇管圈端部u 型弯管曲径为250mm,则两直管距离为500mm,两端弯管总长度0l )(mm 157050014.3D l 0=⨯==π③冷却管总长度L 计算有前知冷却管总面积F=25㎡现取无缝钢管Ф83×4,每米长冷却面积为20m 24.01077.014.3F =⨯⨯= 则m L 2.10424.025F F 0===4+=L L 实际=104.2+4=108.2m 冷却管占有体积V=0.785×0.0732×104.2=0.44m ³④每组管长0L 和管组高度 m 8.3433.104n L L 0===两端弯管总长0L =1570mm,两端弯管总高为500mm,则直管部分高度:h=H-500=3400-500=2900(mm ),则一圈管长mm 7370157029002l 2h l 0=+⨯=+= ⑤每组管子圈数0n 圈537.78.34L L n 00===现取管间距m 19.0077.05.22.5D =⨯=外,竖直蛇管与罐壁地最小距离为0.15m,则可计算出与搅拌器地距离在允许范围内(不小于200mm ).⑥校核布置后冷却管地实际传热面积2m 272.108079.0L nd F =⨯⨯=⨯=π实平均实而前有F=25.7㎡,实F >F,μ可满足要求.5.3支座选择发酵设备常用支座分为卧式支座和立式支座.其中卧式支座又分为支腿,圈型支座,鞍型支座三种.立式支座也分为三种即:悬挂支座,支撑式和裙式支座.对于3m 75以上地发酵罐,由于设备总重量较大,应选用裙式支座.本设计V=350m 选用支撑式支座.6 参考文献【1】郑裕国.生物工厂设备[M]北京.化学工业出版社,2007【2】吴思芳.发酵工厂工艺设计概论[M]北京.轻工业出版社,2006 【3】梁世忠.生物工程设备2009,7 【4】曲文海,朱有庭化工设备设计手册[M].2005,6【5】陈乙崇等搅拌设备设[M].1988,1设计结果汇总项目工艺尺寸项目 大小 发酵罐公称体积nV 503m 实际装液量 313m 罐径D 3100mm 罐压P 0.4MP 罐高H 6000mm 通气量Q270min /3m 封头短半轴a h770mm通风时搅拌抽功率(g P )136.4kW涡轮搅拌器直径Di 1030mm不通气时轴功率(P)138.9kW发酵罐壁厚S19.8mm搅拌转速2N170r/min封头壁厚S210.7mm 夏季冷却水用量W 45t/h 人孔300X400mm 冬季冷却水用量W 14t/h 冷却管总长1082000mm 冷却器面积F 252m蛇管直管高度2900mm蛇管弯管高度500mm进/出料口Ф121x4mm进/出气口Ф95x4mm蛇管直径Ф83×4mm搅拌器挡板宽100mm搅拌器挡板长200mm。