汽车踏板强度模拟方法
奇瑞汽车踏板组碰撞建模指南V

编号:版本: 1.0 密级:秘密踏板组碰撞建模指南编制/日期:王鹏翔校对/日期:审核/日期:批准/日期:奇瑞汽车有限公司汽车工程研究院整车安全部2007年04月5日目录1 前言踏板组是车辆被动安全的重要组成部分之一,在整车前部碰撞过程中直接影响到驾驶员脚部、小腿、膝盖处的伤害值。
世界上主要的几个法规、标准的前碰部分都制订了相应的踏板位移量指标。
踏板组数值模拟涉及材料动态本构关系以及材料动态破坏规律等众多理论课题,如何准确的模拟碰撞过程中踏板的动态响应,对踏板组的碰撞建模提出了较高的要求。
本建模指南结合奇瑞CAE工程师的经验和当前的工程应用背景,旨在规范踏板组建模的一般要求和准则,确保不同团队、不同平台在踏板组建模时的一致性和规范性,提高碰撞建模效率。
建模时以HyperMesh7.0为前处理器。
2 踏板组模型介绍踏板组作为汽车重要操纵机构,是人完成操控汽车的主要工具,通常由离和、制动、加速三踏板,踏板转动枢轴,踏板支架,限位装置,复位弹簧,真空助力器等基本部分组成。
图2.1是Chery-Q21踏板组结构示意图。
图2.1 Chery-Q21踏板组结构示意图3 数据需求●踏板组在整车坐标系中的3维CAD数据(CATIA或UG格式);●踏板组零件所用材料的牌号,材料的本构关系曲线,零件厚度;●踏板力、踏板行程、复位弹簧劲度系数;●踏板组总质量。
4几何清理及网格划分首先,将三维CAD数模转化为HyperMesh可识别的Model、Igs或Step格式的文件。
将几何文件单个或使用加装补丁后HyperMesh7.0的HyperMesh用户界面的Multi-import命令成批导入HyperMesh。
使用geom cleanup命令对导入HyperMesh的几何进行修补,删除重复面。
直径较小的孔或小的加强筋可以去除。
真空助力器在前部碰撞过程中,通常和发动机舱内部构件发生接触,因此针对不同发动机舱空间布置,不同的真空助力器形状,建模前预测碰撞过程中可能与发舱件发生接触的部位,将这些部位的几何形状准确保留。
汽车踏板强度模拟方法
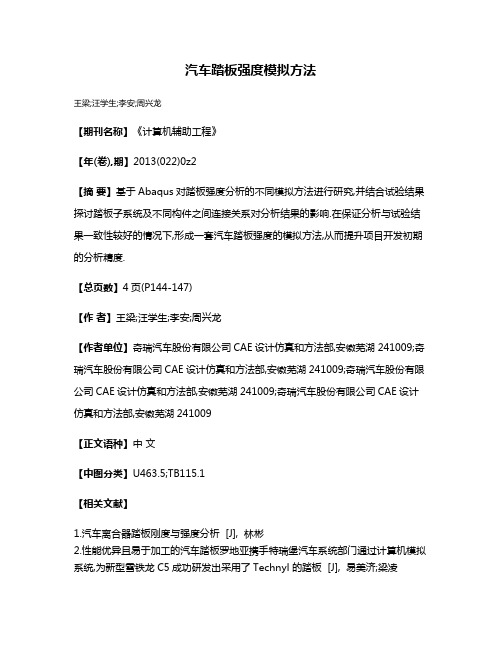
汽车踏板强度模拟方法
王梁;汪学生;李安;周兴龙
【期刊名称】《计算机辅助工程》
【年(卷),期】2013(022)0z2
【摘要】基于Abaqus对踏板强度分析的不同模拟方法进行研究,并结合试验结果探讨踏板子系统及不同构件之间连接关系对分析结果的影响.在保证分析与试验结果一致性较好的情况下,形成一套汽车踏板强度的模拟方法,从而提升项目开发初期的分析精度.
【总页数】4页(P144-147)
【作者】王梁;汪学生;李安;周兴龙
【作者单位】奇瑞汽车股份有限公司CAE设计仿真和方法部,安徽芜湖241009;奇瑞汽车股份有限公司CAE设计仿真和方法部,安徽芜湖241009;奇瑞汽车股份有限公司CAE设计仿真和方法部,安徽芜湖241009;奇瑞汽车股份有限公司CAE设计仿真和方法部,安徽芜湖241009
【正文语种】中文
【中图分类】U463.5;TB115.1
【相关文献】
1.汽车离合器踏板刚度与强度分析 [J], 林彬
2.性能优异且易于加工的汽车踏板罗地亚携手特瑞堡汽车系统部门通过计算机模拟系统,为新型雪铁龙C5成功研发出采用了Technyl 的踏板 [J], 易美济;梁凌
3.电动汽车再生制动过程制动踏板位移与制动意图及制动强度之间的关系 [J], 刘剑开;张向文
4.基于多尺度联合仿真的汽车加速踏板强度分析 [J], 唐俊琦;吴奕东;孙涛;余家皓;李明;赵勇
5.依维柯汽车使用与维修案例分析与探讨七题轮胎打补丁引起制动踏板反弹——记排除依维柯汽车制动踏板反弹故障的前后 [J], 桂健生;陆卫华
因版权原因,仅展示原文概要,查看原文内容请购买。
汽车模拟驾驶操作方法

汽车模拟驾驶操作方法1. 上车准备首先,打开车门,调整座位和方向盘的位置。
接下来,系好安全带,调整后视镜和侧视镜,确认车内配件齐全(如空调、收音机等),调节座椅高低和倾斜度,并将脚放在刹车和油门踏板上。
2. 接通点火插入钥匙,拧转至‘on(开)’位置。
等待车辆系统自检完成,确认仪表盘上的所有指示灯都正常亮起。
3. 启动引擎按下离合器踏板(手动档车辆)或刹车踏板(自动档车辆),同时把钥匙拧到‘start (发动)’位置,待引擎启动后,松开钥匙。
如果发动机未成功启动,可以再试一次或保持离合/刹车踏板踩下状态。
4. 操作离合器和换挡当车辆处于空挡状态时,离合器应完全松开,以便引擎能够正常运转;在车辆启动和加速时,离合器应缓慢踩下,使车辆缓慢前进。
在手动挡车辆中,平稳地踩下油门踏板,同时迅速踩下离合器,高低挡位之间切换时,必须完全松开油门踏板,以避免过度加速。
5. 方向控制使用方向盘控制车辆的方向,左转方向盘使车辆向左转,右转方向盘使车辆向右转;当车辆在急转弯时,需要减速,以避免侧滑或翻车。
6. 制动控制当需要停车时,首先要踩下刹车踏板,从而减缓车辆的速度。
在停车时,手动档车辆必须同时踩下刹车和离合器,以免熄火或冲出空挡。
7. 定速巡航控制(适用于部分车型)当车辆开上高速公路时,可以使用定速巡航控制功能,以保持匀速行驶,同时减轻司机的疲劳感。
启动定速巡航后,加速或刹车都不会影响车速,只有手动断开系统或者踩刹车后重新启动才能解除定速巡航模式。
8. 停车熄火在停车熄火前,需要先换至空档(手动挡)或者P挡(自动挡),踩下紧急刹车并拉上手刹,松开刹车踏板和离合器踏板,通过钥匙拧至‘off(关)’位置熄火,最后才能离开车辆。
以上是汽车模拟驾驶操作方法,新手记得多练习,对于不熟悉的操作可请教老司机或者关注交通安全知识,切勿以身试法,保持安全驾驶。
踏板车车架静强度分析(1)
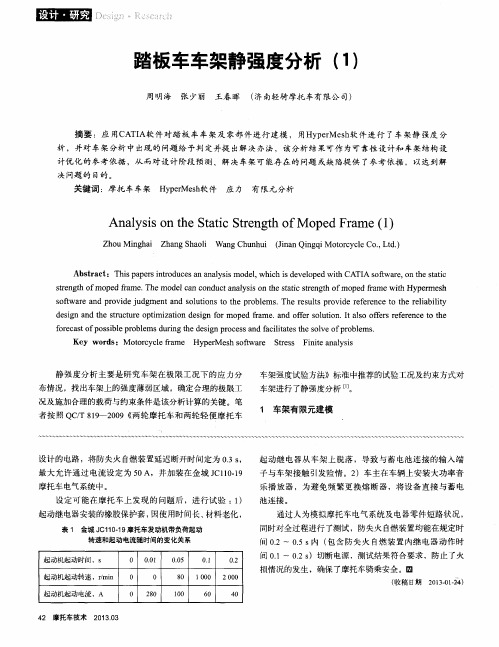
通过人为模拟摩托车电气系统及 电器零件短路状况,
同时对 全过 程进 行 了测试 ,防 失火 自燃 装 置均能 在规 定时 间0 . 2~ 0 . 5 S 内 ( 包 含 防 失 火 自燃 装 置 内 继 电 器 动 作时 间0 . 1~ 0 . 2 S )切断 电源 ,测 试结 果符 合要 求 ,防止 了火 损情 况的发 生 ,确保 了摩 托车 骑乘安 全 。皿
囵口团
} 。 l l l 。 _
踏板车车架静强度分析 ( 1 )
周明海 பைடு நூலகம்少丽 王春 晖 ( 济南轻骑摩托车有限公 司)
摘要 :应 9 1C A T I A软件 对踏 板 车车架及 零部件 进行建模 ,用Hy p e r Me s h  ̄ / : 件进行 了车 架静 强度 分
析 ,并对车架分析 中出现 的问题给 予判定并提 出解决 办法,该 分析 结果可作 为可靠性设 计和 车架结构设 计优 化的参考依据 ,从 而对设 计阶段预 测、解决车架可 能存在 的问题 或缺 陷提 供 了参考依据 ,以达 到解
决 问题 的 目的 。
关键词 :摩托车车架 H y p e r Me s h  ̄件 应 力 有限元 分析
s o f t wa r e a n d p r o v i d e j u d g me n t a n d s o l u t i o n s t o t h e p r o b l e ms . T h e r e s u l t s p r o v i d e r e f e r e n c e t o t h e r e l i a b i l i t y
Ke y wo r d s :Mo t o r c y c l e la f me Hy pe r Me s h s o f t wa r e St r e s s Fi n i t e a n a l ys i s
踏板模拟器的原理

踏板模拟器的原理踏板模拟器是一种用于模拟踏板操作的设备,常用于汽车驾驶模拟器、游戏等领域。
它的原理是通过传感器感知踏板的运动,并将其转化为电信号,再通过连线连接至相应设备,实现对踏板操作的模拟。
踏板模拟器的工作原理主要包括传感器、信号转换和模拟输出三个部分。
传感器是踏板模拟器的重要组成部分,常用的传感器包括压力传感器、位移传感器等。
压力传感器通过感知踏板上压力的大小来确定踏板的踩踏程度,位移传感器则通过感知踏板的位移来确定踏板的移动程度。
这些传感器将踏板的运动转化为电信号。
接下来,信号转换是将传感器输出的电信号转化为计算机或游戏设备能够识别的信号。
传感器输出的电信号通常是模拟信号,而计算机或游戏设备一般是通过数字信号进行操作的。
因此,需要通过模拟-数字转换器或信号处理器将模拟信号转化为数字信号。
模拟-数字转换器可以将模拟信号转化为与输入信号相对应的数字信号,信号处理器可以对模拟信号进行滤波和放大等处理,以保证信号的准确性和稳定性。
模拟输出是将转化后的数字信号通过连线连接至相应设备,实现对踏板操作的模拟。
通过模拟输出,踏板模拟器可以将踏板的运动转化为游戏角色的行走、汽车的加速或刹车等操作。
这样,玩家或驾驶员就可以通过踏板模拟器来模拟真实的踩踏操作,提升游戏或驾驶模拟的真实感和沉浸感。
踏板模拟器是一种通过传感器感知踏板运动并转化为电信号,再通过信号转换和模拟输出实现对踏板操作的模拟的设备。
它的工作原理包括传感器、信号转换和模拟输出三个部分。
传感器用于感知踏板的运动,信号转换将模拟信号转化为数字信号,模拟输出将数字信号连接至相应设备实现模拟操作。
踏板模拟器的应用领域广泛,可以提升游戏和驾驶模拟的真实感,给用户带来更好的体验。
踏板集中载荷试验方法

踏板集中载荷试验方法
踏板集中载荷试验方法是一种评估踏板结构强度和耐久性的测试方法。
该方法通过在踏板上施加集中载荷来模拟实际使用中可能出现的局部高压力情况,以评估踏板的承载能力和变形情况。
以下是踏板集中载荷试验的一般步骤:
1. 准备试验设备:准备一台能够施加集中载荷的试验设备,例如压力机或万能试验机等。
2. 安装踏板:将待测试的踏板安装到试验设备上,并确保踏板与试验设备之间的连接牢固可靠。
3. 施加载荷:根据试验要求,在踏板上施加集中载荷。
载荷的大小和施加位置应根据实际情况进行选择和调整。
4. 记录数据:在施加载荷的过程中,记录载荷大小、踏板变形量、破坏情况等数据。
可以使用位移计、应变计等测量工具来测量踏板变形量和应变情况。
5. 分析结果:根据记录的数据,分析踏板的承载能力和变形情况。
可以通过对比不同载荷下的变形量和应变情况,评估踏板的强度和耐久性。
需要注意的是,踏板集中载荷试验方法的具体步骤和要求可能因不同的踏板类型和试验标准而有所差异。
因此,在进行踏板集中载荷试验时,应参考相关的标准和规范,确保试验结果的准确性和可靠性。
某车型踏板感模拟器设计及验证

52. 7 50.0 57. 980 N 45.0 165.350 N 40. 6 259.836 N 335. 685 MPa 660. 000 MPa 25. 8 640.9 6. 178
图4弹簧2设计参数
于试验台架上,设备输入推杆与台架的试验输出端连 接,输入力传感器和输入位移传感器安装在台架的试 验输出端;以2±0.2 mm/s的加载速度推动模拟器推 杆,直至输入力达到450 N。
踏板总行程 L1二 踏板比 — 21.2 mm
L2 ——1 — 28.2 mm 2&
式中:L为弹簧1自有高度;L1为工作行程;L2为预紧 压缩行程;厶3为压并高度+剩余可压缩行程。
通过拟合计算得出弹簧1的参数见图3。
弹簧类型 弹簧材料 切变模量 材料直径 弹簧中径 有效圈数 总圈数 节距 旋绕 比
10咼径比 11曲度系数 12刚度
为兼顾能量回收及制动踏板感,制动踏板模拟器 适时出现。现在行业内主要有两种形式:制动踏板机
械解耦形式和制动主缸液压解耦形式⑷。笔者依托 机械解耦方案,基于某车型的踏板感需求,设计一款 新型的模拟器方案,通过不同刚度弹簧并联组合设 计,满足制动过程中的踏板感需求,不仅很好解决了 踏板感问题,而且简单的结构对模拟器的产业化及成 本控制意义重大。
此设计方案利用弹簧特性来匹配制动踏板感:① A-B,通过弹簧1在安装时的预紧力实现,在位移不 变的条件下,力从0 N突变至62 N;②通过弹簧1的 压缩形变来实现B-C的变化,通过计算力-位移的对 应关系,设计弹簧1刚度等相关参数;③通过弹簧1 与弹簧2并联后的压缩形变来实现C-D的变化,通 过计算力-位移的对应关系,设计弹簧2刚度等相关 参数。模拟器结构如图2所示。
-机械研究与应用 -2021年第3期(第34卷,总第173期)
汽车制动踏板行程及踏板力的评定
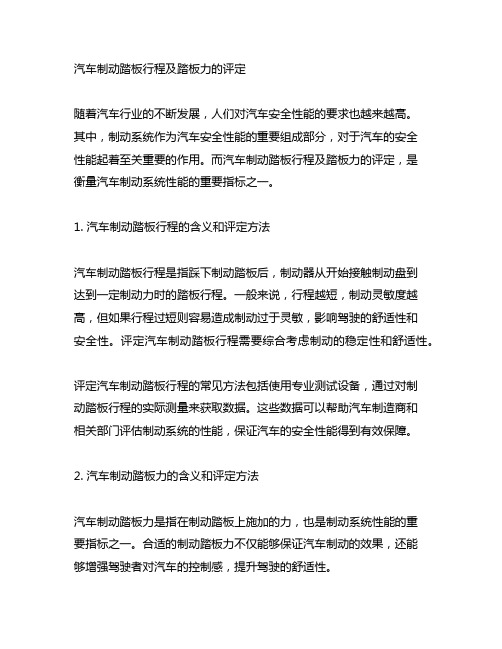
汽车制动踏板行程及踏板力的评定随着汽车行业的不断发展,人们对汽车安全性能的要求也越来越高。
其中,制动系统作为汽车安全性能的重要组成部分,对于汽车的安全性能起着至关重要的作用。
而汽车制动踏板行程及踏板力的评定,是衡量汽车制动系统性能的重要指标之一。
1. 汽车制动踏板行程的含义和评定方法汽车制动踏板行程是指踩下制动踏板后,制动器从开始接触制动盘到达到一定制动力时的踏板行程。
一般来说,行程越短,制动灵敏度越高,但如果行程过短则容易造成制动过于灵敏,影响驾驶的舒适性和安全性。
评定汽车制动踏板行程需要综合考虑制动的稳定性和舒适性。
评定汽车制动踏板行程的常见方法包括使用专业测试设备,通过对制动踏板行程的实际测量来获取数据。
这些数据可以帮助汽车制造商和相关部门评估制动系统的性能,保证汽车的安全性能得到有效保障。
2. 汽车制动踏板力的含义和评定方法汽车制动踏板力是指在制动踏板上施加的力,也是制动系统性能的重要指标之一。
合适的制动踏板力不仅能够保证汽车制动的效果,还能够增强驾驶者对汽车的控制感,提升驾驶的舒适性。
评定汽车制动踏板力的方法主要包括使用专业测试设备进行实际测量和计算。
通过对制动踏板力的评定,可以帮助汽车制造商和相关部门了解汽车制动系统的性能,保证汽车在制动过程中能够提供稳定而舒适的驾驶体验。
3. 如何提高汽车制动踏板行程和踏板力的性能为了提高汽车制动踏板行程和踏板力的性能,汽车制造商和相关部门可以从以下几个方面着手:- 通过改进设计和工艺,优化制动踏板机构,减小踏板行程,提高制动灵敏度。
- 选择高品质的材料和制造工艺,提高制动系统的稳定性和可靠性。
- 采用先进的制动系统技术,如电子制动系统和自动制动辅助系统,提升汽车的制动性能和安全性能。
通过不断的技术创新和产品改进,可以有效提高汽车制动踏板行程和踏板力的性能,为汽车的安全性能提供更加有效的保障。
4. 结语汽车制动踏板行程和踏板力的评定,对于保障汽车的安全性能起着至关重要的作用。
机动车制动器的工作过程仿真分析
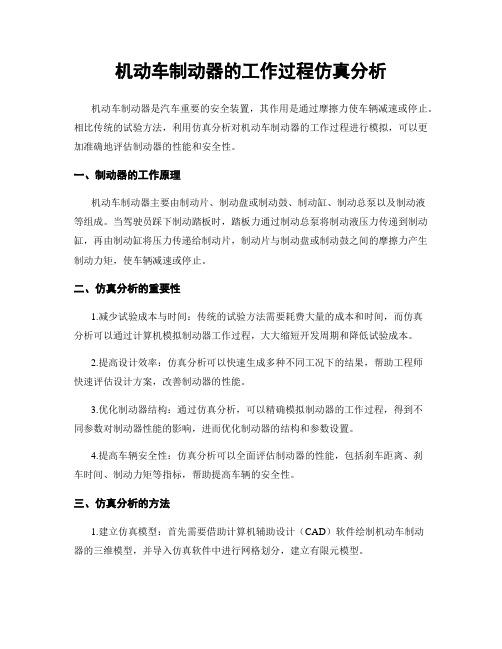
机动车制动器的工作过程仿真分析机动车制动器是汽车重要的安全装置,其作用是通过摩擦力使车辆减速或停止。
相比传统的试验方法,利用仿真分析对机动车制动器的工作过程进行模拟,可以更加准确地评估制动器的性能和安全性。
一、制动器的工作原理机动车制动器主要由制动片、制动盘或制动鼓、制动缸、制动总泵以及制动液等组成。
当驾驶员踩下制动踏板时,踏板力通过制动总泵将制动液压力传递到制动缸,再由制动缸将压力传递给制动片,制动片与制动盘或制动鼓之间的摩擦力产生制动力矩,使车辆减速或停止。
二、仿真分析的重要性1.减少试验成本与时间:传统的试验方法需要耗费大量的成本和时间,而仿真分析可以通过计算机模拟制动器工作过程,大大缩短开发周期和降低试验成本。
2.提高设计效率:仿真分析可以快速生成多种不同工况下的结果,帮助工程师快速评估设计方案,改善制动器的性能。
3.优化制动器结构:通过仿真分析,可以精确模拟制动器的工作过程,得到不同参数对制动器性能的影响,进而优化制动器的结构和参数设置。
4.提高车辆安全性:仿真分析可以全面评估制动器的性能,包括刹车距离、刹车时间、制动力矩等指标,帮助提高车辆的安全性。
三、仿真分析的方法1.建立仿真模型:首先需要借助计算机辅助设计(CAD)软件绘制机动车制动器的三维模型,并导入仿真软件中进行网格划分,建立有限元模型。
2.确定工况:根据实际使用情况,确定不同工况下的制动器工作条件,包括车速、踏板力、制动时间等参数。
3.制动片材料模型定义:选择合适的摩擦材料模型,包括弹性模量、泊松比、摩擦因数等参数,根据试验数据或资料进行模型定义。
4.加载边界条件:根据制动器受力分析,确定制动片与制动盘(或制动鼓)之间的接触载荷模型,包括径向力和切向力。
5.进行仿真计算:基于建立的有限元模型和设定的工况,进行仿真计算,计算制动器在不同工况下的受力情况和变形情况。
6.分析结果:根据仿真计算得到的结果,包括接触面的压力分布、接触面的滑移速度、接触面的温度分布等进行分析和评估。
汽车踏板强度模拟方法

汽车踏板强度模拟方法作者:王梁汪学生李安周兴龙来源:《计算机辅助工程》2013年第05期摘要:基于Abaqus对踏板强度分析的不同模拟方法进行研究,并结合试验结果探讨踏板子系统及不同构件之间连接关系对分析结果的影响.在保证分析与试验结果一致性较好的情况下,形成一套汽车踏板强度的模拟方法,从而提升项目开发初期的分析精度.关键词:汽车;踏板总成;模拟方法;试验结果中图分类号: U463.5;TB115.1文献标志码: B引言汽车踏板系统是汽车用户日常驾驶中最重要的交互系统之一.踏板系统强度不足,会影响行车安全;刹车时的“软”、“硬”关系到顾客操纵踏板时身体感官的综合感觉.[1]因此考察汽车踏板系统的强度是否满足目标要求,具有十分重要的意义.依据行业标准及试验方法,对一系列踏板系统进行强度分析,探讨影响踏板强度分析精度的因素,以保证分析与试验结果的一致性,提升CAE在汽车踏板开发初期的分析精度.1汽车踏板性能要求和试验方法汽车行业标准QC/T 788—2007对汽车踏板的强度要求[2]如下:踏板装置在纵向力作用下,踏板表面的永久变形量≤5 mm,且无裂纹或损坏等缺陷.试验加载方法是按实车状态固定踏板机构总成,将踏板机构输出端与负载机构连接,并将踏板臂在工作行程的中间位置固定.在踏板几何中心点,施加所规定的垂直于踏板表面的纵向力并保持5 s,测量加载点的纵向位移(变形)量.2汽车踏板系统模拟2.1汽车踏板系统简介典型的汽车踏板系统总成由支撑支架、踏板臂、套筒、销轴和尼龙衬套等组成.研究发现,各子系统模拟方法不同,会对汽车踏板强度的分析结果产生一定影响.以一款比较复杂的可变杠杆比汽车踏板为例,结合试验结果,探讨汽车踏板强度的模拟方法,该踏板系统结构见图1.图 1某车型踏板系统2.2分析工况介绍踏板液压系统原理示意见图2,可知,根据踏板杠杆比原理,驾驶员在操纵汽车踏板系统装置时,垂直施加在踏板面的载荷Fp放大为施加在助力装置上的驱动力F1,然后通过液压系统得到执行装置上的载荷F2,最终得到汽车踏板液压系统的管道压力.该压力直接关系到车辆的制动距离或离合系统的行程大小.踏板液压系统遵循帕斯卡定律[3],其工作原理见图2.3.1汽车踏板模拟方法探讨通常情况下,在操纵汽车踏板过程中,支撑支架会产生微小变形,但如果踏板结构设计的不合理,在纵向加载工况容易造成套筒和销轴部分结构屈服严重,导致支撑踏板臂端部的结构产生较大的变形.根据前文分析工况所描述的杠杆比原理,最终造成踏板臂加载点位移过大.踏板臂及助力装置连接臂与套筒之间采用烧焊连接.从受力角度看,套筒同时承受弯曲与扭转组合载荷的作用,见图3.因此,在建立踏板模型时,所建立的烧焊区域大小,会对套筒或销轴产生的屈服程度和扭转变形大小造成直接影响.如果套筒或销轴本身屈服严重,同样会造成踏板加载点位移过大.图 3踏板套筒及销轴受力示意图为避免金属结构件之间相互接触造成磨损,减小噪音,便于装配和增大接触摩擦力,在设计过程中,套筒与销轴之间会存在一定的间隙,用于布置开口的尼龙衬套,尼龙衬套模型见图4.踏板臂在绕销轴旋转过程中,尼龙衬套承受扭转载荷,在开口位置发生变形.2.3.2汽车踏板不同模拟方案描述及分析使用Abaqus软件对汽车踏板强度进行模拟,其中踏板支架采用壳单元模拟,焊点采用rod 单元模拟,踏板臂采用实体单元模拟,模型中考虑材料非线性[4].通过几种不同建模方法,将得到的仿真结果与试验结果对比,探讨适合该类踏板且分析精度较高的模拟方法.在模型细节方面,主要考虑销轴及套筒、焊接区域和踏板臂转轴处尼龙衬套等的模拟方法以及是否考虑接触等,具体为:从各模拟方法的分析结果来看,对于该类踏板结构,销轴及套筒采用柔性体、尼龙衬套,并且采用接触方法模拟连接,对踏板强度分析影响最大.3分析与试验的对比3.1试验设备及测试模型试验测试所用的设备为MTS系统公司提供的模拟试验系统.汽车踏板机构按实车状态固定安装在专用试验台上,考虑到踏板不同构件之间的安装间隙,试验前先对踏板机构进行预加载,然后按照试验流程进行汽车踏板的强度试验,踏板试验模型见图7.图 7踏板试验模型3.2分析与试验结果对比以上各方案的对比结果见图8,可知采用CASE4探讨的模拟方法所建立的分析模型,强度分析与试验测试的载荷位移曲线具有较好的一致性,踏板加载点最大位移相差很小,误差仅为1.88%(见图9);而常规分析所采用的模拟方法与试验结果差异较大,不能很好地反映实车情况.4结束语采用试验与分析相结合的手段,利用Abaqus有限元软件,对汽车踏板模型的模拟方法进行探讨.结果认为,在保证分析结果与试验数据一致性较好、分析结果准确性的同时,可以在项目研发初期使用本文的分析方法,对在研车型的踏板系统进行强度评估,根据工程经验优化踏板结构,甄选出合理的设计方案.参考文献:[1]花庆荣. 轿车制动感觉评估与制动感觉指数[J]. 上海汽车, 2008(6): 3537.[2]QC/T 788—2007汽车制动踏板装置性能要求及台架试验方法[S].[3]余志生. 汽车理论[M]. 北京:机械工业出版社, 2003: 71100.[4]庄茁,张帆,岑松,等. Abaqus非线性有限元分析与实例[M]. 北京:科学出版社,2005: 1063.(编辑武晓英)。
踏板30个训练方法

踏板30个训练方法踏板是一种可以锻炼腿部肌肉、提高心肺功能、增加耐力的运动器材。
下面给出30个踏板训练的方法,供参考:1. 单脚下压:用一只脚踩踏板,另一只脚保持离地,交替进行。
2. 双脚下压:双脚同时踩踏板,以加强腿部肌肉的训练。
3. 快速踩踏:尽快地踏动踏板,以增强心肺功能。
4. 反向踩踏:踩踏板时,反向踩动,逆时针或顺时针方向。
5. 前踏后踏:先将一个脚踩到前方,再将另一个脚踩到后方,交替进行。
6. 高速踏踩:在一定的时间内,尽可能多地踩动踏板。
7. 利用踏板进行高抬腿:踩动踏板的同时,抬起膝盖到胸部或以上的高度。
8. 利用踏板进行踢腿:踩动踏板的同时,向前或向后踢腿。
9. 半蹲踩踏:踩动踏板时,同时进行半蹲动作。
10. 单脚二选一:将一个脚踩踏板,另一个脚保持离地,交替进行。
11. 等长时间训练:固定时间内尽可能多地踩动踏板。
12. 等速训练:保持踩动踏板的速度恒定,进行一段固定时间的训练。
13. 多次短时训练:每次训练时间较短,但多次进行。
14. 模拟上坡训练:加大踏板阻力,模拟上坡踩踏的感觉。
15. 模拟下坡训练:减小踏板阻力,模拟下坡踩踏的感觉。
16. 前后alternation:将一个脚踩到前方,在抬起此脚的同时,将另一只脚踩到后方,交替进行。
17. 开合蹬踏:将脚踩到两侧,然后尽快地开合蹬动。
18. 双足内侧蹬踏:将双脚并紧,以内侧踩动踏板。
19. 踏踩暂停:踩一段时间后停下来,然后再继续踩。
20. 高阻力踏踩:增加踏板阻力,增加训练强度。
21. 低阻力踏踩:减小踏板阻力,提高踩踏速度。
22. 踏踏上抬:踩动踏板时,在上升到顶点时,迅速抬起双脚。
23. 对角踏踩:将一个脚踩到前方,另一个脚踩到后方外侧,交替进行。
24. 单脚跳跃蹬踏:单脚轮流跳跃蹬踏,增加平衡和协调能力。
25. 踩踏加臂力:踩动踏板的同时,用手臂进行上下摆动。
26. 双脚跳动踏:双脚同时离地,在空中交换踩踏动作。
塑料上车踏板断裂问题分析及解决措施

塑料上车踏板断裂问题分析及解决措施随着汽车工业的发展和人们对汽车使用动力的需求增加,汽车上的各种部件也在不断进行技术创新和改进。
车辆的上车踏板是一种方便乘车人员上下车的设施,通常由塑料制成。
在使用过程中,塑料上车踏板断裂的问题可能会出现,为了解决这个问题,有必要对其进行分析,并提出相应的解决措施。
塑料上车踏板断裂的主要原因可能是材料质量不过关。
塑料材料的质量直接影响着上车踏板的耐久性和使用寿命。
如果材料不合格或者生产过程中掺有不适宜的添加剂,会导致踏板在使用过程中容易发生断裂。
对材料质量进行把关,并加强原料供应商的管理,是解决这个问题的关键。
设计问题也是导致塑料上车踏板断裂的重要原因之一。
在设计上,上车踏板需要经受乘车人员的重复踩踏和外力的冲击,因此需要具备足够的强度和耐用性。
如果设计不合理或者结构不坚固,就容易出现断裂问题。
所以,在设计上应该加强对应力分析和结构优化,确保上车踏板能够承受正常使用条件下的力学载荷。
塑料上车踏板的制造工艺也是造成断裂问题的潜在因素之一。
在生产过程中,如果温度、压力、模具和成型工艺等参数控制不到位,就会导致材料的疲劳性能下降,强度减小,从而加速踏板的老化和断裂。
要通过优化制造工艺,提高工艺稳定性和一致性,减少质量波动,从而提高产品的可靠性和寿命。
针对上述问题,可以采取一系列的解决措施,以确保塑料上车踏板的安全性和可靠性。
加强原材料的筛选和质量控制。
与原料供应商建立长期稳定的合作关系,开展严格的原料检验工作,避免使用不合格的原材料。
在设计上加强强度分析和模拟仿真,优化结构和材料的选择,确保上车踏板在设计寿命内不会断裂。
然后,加强制造工艺的管理和控制,通过严格的工艺流程和参数控制,确保每一批产品的一致性和稳定性。
加强对生产设备和工艺工人的培训,提高生产过程中的操作技能和质量意识。
塑料上车踏板断裂问题是一个复杂的工程问题,需要从材料、设计和制造等多个方面综合考虑。
只有通过加强原材料管理、优化设计和改进制造工艺,才能够有效解决这个问题,提高上车踏板的质量和可靠性。
电子油门踏板的磁场仿真和实验研究

0 引 言
电子油门踏板分为接触式和非接触式,接触式电子油门踏 板存在易磨损和寿命短的缺点而逐渐被淘汰,现在普遍采用基 于霍尔原理 的 非 接 触 式 电 子 油 门 踏 板。 Micronas公 司 生 产 的 霍尔芯片不仅能实现在线校准的功能,还具有一致性好、寿命 长 、精 度 高 等 优 点 ,得 到 了 广 泛 的 使 用[1]。
目前,对于霍尔传感器工作的磁场研究普遍采用经验公式 和实验的方式,这种方法使得其研究更繁琐,得到的精度会比 较低。对于不 同 尺 寸 和 性 质 的 磁 铁,求 出 其 解 析 式 会 更 加 困
收稿日期:2016 06 27; 修回日期:2016 07 18。 基 金 项 目 :浙 江 省 公 益 性 技 术 应 用 研 究 计 划 (2015C31081)。 作者简介:徐 源(1990 ),男,重 庆 开 县 人,硕 士 研 究 生,主 要 从 事 汽 车 零 部 件 检 测 ,测 试 计 量 技 术 等 方 向 的 研 究 。 郭 斌(1977 ),男,山东日照人,副 教 授,主 要 从 事 汽 车 电 子 技 术、 自 动 化 检 测 装 置 、精 密 检 测 技 术 等 方 向 的 研 究 。
电子油门踏板的磁场仿真和实验研究
徐 源,郭 斌,袁月峰
(中国计量大学 计量测试工程学院,杭州 310038)
摘要:对于汽车电子油门踏板利用可编程霍尔传感器将踏板的位置变化转换为线性模拟电压输出,具有产品一致性好、寿命长等优点 正越来越获得广泛应用;针对踏板磁钢片位置布局不良容易导致的传感器校准异常和输出非线性等问题,进行了踏板旋转件永磁磁路分析, 并用 ANSYS软件进行了磁场有限元建模仿真,分析了踏板旋转角度和传感器位置安装之间的影响因素,并在电子油门性能检测平台上进行 了实验验证;实验结果表明,双路输出式电子油门踏板的输出线性度达到1.45%,同步度指标为0.12%,符合产品技术标准。
- 1、下载文档前请自行甄别文档内容的完整性,平台不提供额外的编辑、内容补充、找答案等附加服务。
- 2、"仅部分预览"的文档,不可在线预览部分如存在完整性等问题,可反馈申请退款(可完整预览的文档不适用该条件!)。
- 3、如文档侵犯您的权益,请联系客服反馈,我们会尽快为您处理(人工客服工作时间:9:00-18:30)。
7.69 12.74 14.26 18.89 21.4l
64.76 41.6l 34.65 13.43 1.88
采用(2),(4),(6),(7)
采用(2),(4),(6),(7) 采用(2),(4),(6),(8)
(a)常规分析
万方数据
第S2期
王梁,等:汽车踏板强度模拟方法
果差异较大,不能很好地反映实车情况
[4 J庄茁,张帆,岑松,等.AI,aqus非线性有限元分析与实例[M].北京:科学出版社,2005:10-63.
(编辑武晓英)
万方数据
.厶∥
,夕。jj莎夕
/:。.,j夕
图9
不同分析方案与试验的误差对比
图9中,汽车踏板强度分析与试验测试结果的 误差计算公式为 误差百分率=(试验一分析)/试验 4
图7 踏板试验模型
结束语
采用试验与分析相结合的手段,利用Abaqus有
3.2分析与试验结果对比 以上各方案的对比结果见图8,可知采用 CASE4探讨的模拟方法所建立的分析模型,强度分 析与试验测试的载荷-位移曲线具有较好的一致性, 踏板加载点最大位移相差很小,误差仅为1.88% (见图9);而常规分析所采用的模拟方法与试验结 参考文献:
(a)系统原理
发生变形.
图4尼龙衬套
操纵汽车踏板装置时,踏板臂、套筒、塑料衬套
(Ij)工作原理
及销轴之间会产生相对旋转.该运动连接关系,可使 用Abaqus中的Hinge单元或建立接触副的方式进 行模拟.Hinge单元不仅提供构件之间力和力矩的
图2踏板液压系统原理示意
踏板液压系统的受力关系为
万方数据
力.该压力直接关系到车辆的制动距离或离合系统 的行程大小.踏板液压系统遵循帕斯卡定律3,其
工作原理见图2(b).
图3
踏板套筒及销轴受力示意图
为避免金属结构件之间相互接触造成磨损,减 小噪音,便于装配和增大接触摩擦力,在设计过程
中,套筒与销轴之间会存在一定的间隙,用于布置开 口的尼龙衬套,尼龙衬套模型见图4.踏板臂在绕销 轴旋转过程中,尼龙衬套承受扭转载荷,在开口位置
strength
simulation
which
can
enhance
the
analysis
the
early
project
development stage. Key words:automobile;pedal system;simulation method;test result
0
引
言
强度要求’纠如下: 踏板装置在纵向力作用下,踏板表面的永久变 形量≤5 mm,且无裂纹或损坏等缺陷. 试验加载方法是按实车状态同定踏板机构总 成,将踏板机构输出端与负载机构连接,并将踏板臂 在T作行程的中间位置固定.在踏板几何中心点,施 加所规定的垂直于踏板表面的纵向力并保持5 s,测 量加载点的纵向位移(变形)量.
147
从各模拟方法的分析结果来看,对于该类踏板
结构,销轴及套筒采用柔性体、尼龙衬套,并且采用
接触方法模拟连接,对踏板强度分析影响最大.
3分析与试验的对比
3.1试验设备及测试模型
——7.f
一-E验
—・一甯攫_;}币
试验测试所用的设备为MTS系统公司提供的
模拟试验系统.汽车踏板机构按实车状态固定安装 在专用试验台上,考虑到踏板不同构件之间的安装 间隙,试验前先对踏板机构进行预加载,然后按照试 验流程进行汽车踏板的强度试验,踏板试验模型见 图7.
会产生微小变形,但如果踏板结构设计的不合理,在 纵向加载工况容易造成套筒和销轴部分结构屈服严 重,导致支撑踏板臂端部的结构产生较大的变形.根 据前文分析丁况所描述的杠杆比原理,最终造成踏 板臂加载点位移过大.
图1 某车型踏板系统
踏板臂及助力装置连接臂与套筒之间采用烧焊 连接.从受力角度看,套筒同时承受弯曲与扭转组合
Strength simulation method of automotive pedal
WANG Liang,WANG Xuesheng,LI An,ZHOU Xinglong
(Department of CAE Design Simulation and Methods,Cherv.Autonu)bile Co.,Ltd.,Wuhu 241009,Anhui,China)
模拟方法
试验 常规分析
CASEl CASE2 CASE3 CASE4
21.82
高的模拟方法.
在模型细节方面,主要考虑销轴及套筒、焊接区 域和踏板臂转轴处尼龙衬套等的模拟方法以及是否 考虑接触等,具体为: (1)销轴及套筒采用rigid单元模拟;
采用(I),(5),(7) 采用(2),(3),(5),(7)
表1
方案
汽车踏板不同模拟方案描述及分析
使用Abaqus软件对汽车踏板强度进行模拟,其 中踏板支架采用壳单元模拟,焊点采用rod单元模
拟,踏板臂采用实体单元模拟,模型中考虑材料非线 性。4i.通过几种不同建模方法,将得到的仿真结果 与试验结果对比,探讨适合该类踏板且分析精度较
分析结果对比
结果/mm 偏差/% 分析与试验
(6)考虑尼龙衬套的影响,尼龙衬套采用实体 单元建模,定义为PA66+30%弹塑性材料; (7)套筒、尼龙衬套及销轴之间的运动连接关 系采用hinge连接; (8)套筒、尼龙衬套及销轴之间的运动连接关
图5 2.3.2 Abaqus中HINGE单元的说明
系采用接触算法连接. 不同方案采用的模拟方法和分析结果对比见表 1,最重要的 交互系统之一.踏板系统强度不足,会影响行车安 全;刹车时的“软”、“硬”关系到顾客操纵踏板时身 体感官的综合感觉.‘¨因此考察汽车踏板系统的强 度是否满足目标要求,具有十分重要的意义. 依据行业标准及试验方法,对一系列踏板系统 进行强度分析,探讨影响踏板强度分析精度的因素, 以保证分析与试验结果的一致性,提升CAE在汽车 踏板开发初期的分析精度. 1
载荷的作用,见图3.因此,在建立踏板模型时,所建 立的烧焊区域大小,会对套筒或销轴产生的屈服程 度和扭转变形大小造成直接影响.如果套筒或销轴 本身屈服严重,同样会造成踏板加载点位移过大.
2.2分析工况介绍 踏板液压系统原理示意见图2,可知,根据踏板 杠杆比原理,驾驶员在操纵汽车踏板系统装置时,垂 直施加在踏板面的载荷F。放大为施加在助力装置 上的驱动力F.,然后通过液压系统得到执行装置上 的载荷F,,最终得到汽车踏板液压系统的管道压
146
计算机辅助工程
2013丘
模拟,而且可以模拟构件之间的摩擦.Abaqus中 Hinge单元的说明见图5.
(2)销轴及套筒采用实体网格模拟,充分考虑
二者的柔性; (3)踏板臂与套筒之间焊接区域大小未考虑实 车情况,采用实体网格模拟;
(4)踏板臂与套筒之间焊接区域大小根据实车 情况建立模型,采用实体网格模拟; (5)不考虑尼龙衬套的影响;
ensuring better consistency between the analysis results and the
researched.Under the condition of
test
results,a method is proposed for the
accuracy in
pedal system
文章编号:1006—087】(2013)S2.0144.04
汽车踏板强度模拟方法
王梁, 汪学生,
李安,
周兴龙
(奇瑞汽车股份有限公司CAE设计仿真和方法部,安徽芜湖241009)
摘要:基于Abaqus对踏板强度分析的不同模拟方法进行研究,并结合试验结果探讨踏板子系统及 不同构件之间连接关系对分析结果的影响.在保证分析与试验结果一致性较好的情况下,形成一套 汽车踏板强度的模拟方法,从而提升项目开发初期的分析精度. 关键词:汽车;踏板总成;模拟方法;试验结果 中图分类号:U463.5;TBll5.1 文献标志码:B
[I] [2] [3]
限元软件,对汽车踏板模型的模拟方法进行探讨.结
果认为,在保证分析结果与试验数据一致性较好、分
析结果准确性的同时,可以在项目研发初期使用本 文的分析方法,对在研车型的踏板系统进行强度评
估,根据工程经验优化踏板结构,甄选出合理的设计
方案.
花庚荣.轿车制动感觉评估与制动感觉指数[J].上海汽车.2008(6):35-37. QC/T 788—2007汽车制动踏板装置性能要求及台架试验方法[s]. 余志生.汽车理论[M].北京:机械工业出版社,2003:71—100.
万方数据
第S2期 一定影响.
王梁,等:汽车踏板强度模拟方法
F.
p
145
以一款比较复杂的可变杠杆比汽车踏板为例, 结合试验结果,探讨汽车踏板强度的模拟方法,该踏 板系统结构见图1.
2万
(1)
F2=A2P
.s2=S1笔
2.3汽车踏板子系统模拟方法研究
2.3.1
汽车踏板模拟方法探讨
通常情况下,在操纵汽车踏板过程中,支撑支架
2汽车踏板系统模拟
2.1汽车踏板系统简介 典型的汽车踏板系统总成南支撑支架、踏板臂、 套筒、销轴和尼龙衬套等组成.研究发现,各子系统 模拟方法不同,会对汽车踏板强度的分析结果产生
汽车踏板性能要求和试验方法
汽车行业标准QC/T 788--2007对汽车踏板的
收稿日期:2013-08—20 作者简介:王粱(1983一),男,河南新野人,工程师,硕士研究生,研究方向为结构设计仿真,(E-mail)wanglian99@mychery.(Ⅷ1
Abstract:Based
on
Abaqus,the different pedal sv,stem strength analysis methods and the effect of the