High quality management in CNC machining process
Quality Management(英文版)(ppt 40页)

– Prevention costs: Training, surveys, implementation of quality system
– Failure costs: Rework, rejects, scrap – External Costs: Warranty, recall, handling complaints – Note – 85 % of costs are responsibility of management
8.1 Quality Planning
8.2 Quality Assurance
8.3 Quality Control
Source: pmbok guide 2000
© 2002 Robbins-Gioia, Inc.
8-3
Quality Management
• Addresses both the management of the project and of the product of the project
© 2002 Robbins-Gioia, Inc.
8-12
Quality Planning
Tools & Techniques
• Benefit/cost analysis – Cost and benefit tradeoffs of
meeting quality requirements
• Benchmarking – Comparing actual or planned project
Source: pmbok guide 2000
© 2002 Robbins-Gioia, Inc.
8-11
Quality Planning
质量管理体系术语中英文对照

质量管理体系术语中英文对照Quality Management System Terminology Chinese-English Comparison1. IntroductionQuality management systems (QMS) serve as a framework for organizations to ensure the consistent production of high-quality goods and services. In order to effectively implement QMS and communicate within a global context, it is essential to understand the terminology used. This article provides a comprehensive Chinese-English comparison of key terms commonly used in quality management systems.2. Quality Management System (质量管理体系)A QMS refers to the set of policies, processes, and procedures implemented by an organization to manage quality-related activities. The following table presents the Chinese-English comparison of some fundamental terminology used in QMS.Term / 术语 Chinese / 中文 English / 英文Quality Management System 质量管理体系Quality Management SystemQuality Policy 质量方针 Quality PolicyQuality Objectives 质量目标 Quality ObjectivesQuality Manual 质量手册 Quality ManualQuality Procedures 质量程序 Quality ProceduresInternal Audit 内审 Internal AuditManagement Review 管理评审 Management Review3. Document Control (文件控制)In order to maintain consistency and control over documentation within a QMS, document control procedures are established. The following table provides the Chinese-English comparison of terms related to document control.Term / 术语 Chinese / 中文 English / 英文Document Control 文件控制 Document ControlDocument Numbering 文件编号 Document NumberingDocument Revision 文件修订 Document RevisionDocument Approval 文件批准 Document ApprovalDocument Distribution 文件分发 Document DistributionDocument Retention 文件保留 Document Retention4. Corrective and Preventive Actions (纠正和预防措施)Continuous improvement is a key component of QMS. Corrective and preventive actions are taken to address non-conformances and prevent theirrecurrence. The following table presents the Chinese-English comparison of terms related to corrective and preventive actions.Term / 术语 Chinese / 中文 English / 英文Corrective Action 纠正措施 Corrective ActionPreventive Action 预防措施 Preventive ActionRoot Cause Analysis 根本原因分析 Root Cause Analysis Non-conformance 不符合项 Non-conformance Problem Solving 问题解决 Problem Solving5. Training and Competence (培训和能力)To ensure employees possess the necessary skills and knowledge, training programs are implemented. The following table provides the Chinese-English comparison of terms related to training and competence.Term / 术语 Chinese / 中文 English / 英文Training 培训 TrainingCompetence 能力 CompetenceSkills 技能 SkillsTraining Needs Analysis 培训需求分析 Training Needs AnalysisTraining Effectiveness 培训效果 Training Effectiveness6. Supplier Management (供应商管理)Effective supplier management is crucial for maintaining quality in the supply chain. The following table presents the Chinese-English comparison of terms related to supplier management.Term / 术语 Chinese / 中文 English / 英文Supplier 供应商 SupplierSupplier Evaluation 供应商评估 Supplier EvaluationSupplier Approval 供应商批准 Supplier ApprovalSupplier Performance 供应商绩效 Supplier Performance Supplier Audit 供应商审核 Supplier Audit7. ConclusionUnderstanding the terminology used in quality management systems is vital for effective communication and implementation of QMS practices. This article has provided a comprehensive Chinese-English comparison of key terms commonly used in QMS, covering areas such as quality management system, document control, corrective and preventive actions, training and competence, and supplier management. By familiarizing oneself with these terminologies, organizations can enhance their quality management practices and strengthen their ability to meet customer expectations and regulatory requirements.。
品质管理 中英文对照
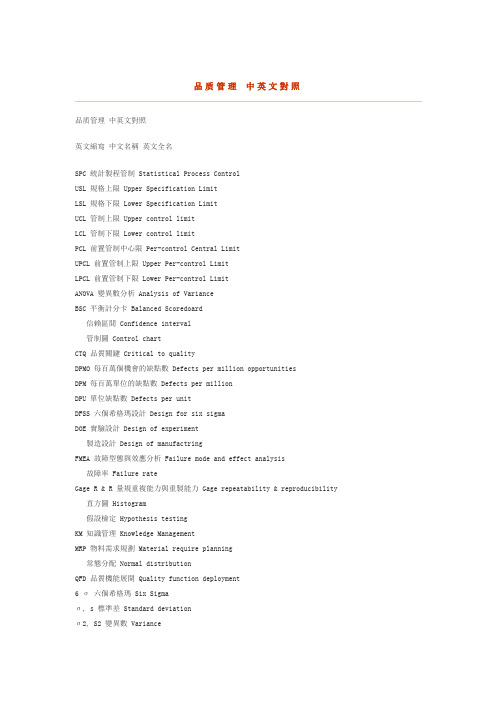
品质管理中英文對照品质管理中英文對照英文縮寫中文名稱英文全名SPC 統計製程管制 Statistical Process ControlUSL 規格上限 Upper Specification LimitLSL 規格下限 Lower Specification LimitUCL 管制上限 Upper control limitLCL 管制下限 Lower control limitPCL 前置管制中心限 Per-control Central LimitUPCL 前置管制上限 Upper Per-control LimitLPCL 前置管制下限 Lower Per-control LimitANOVA 變異數分析 Analysis of VarianceBSC 平衡計分卡 Balanced Scoredoard信賴區間 Confidence interval管制圖 Control chartCTQ 品質關鍵 Critical to qualityDPMO 每百萬個機會的缺點數 Defects per million opportunitiesDPM 每百萬單位的缺點數 Defects per millionDPU 單位缺點數 Defects per unitDFSS 六個希格瑪設計 Design for six sigmaDOE 實驗設計 Design of experiment製造設計 Design of manufactringFMEA 故障型態與效應分析 Failure mode and effect analysis 故障率 Failure rateGage R & R 量規重複能力與重製能力 Gage repeatability & reproducibility 直方圖 Histogram假設檢定 Hypothesis testingKM 知識管理 Knowledge ManagementMRP 物料需求規劃 Material require planning常態分配 Normal distributionQFD 品質機能展開 Quality function deployment6 σ六個希格瑪 Six Sigmaσ, s 標準差 Standard deviationσ2, S2 變異數 VarianceABC 作業制成本制度 Activity-Based CostingBTF 計劃生產 Build To ForecastBTO 訂單生產 Build To OrderCPM 要徑法 Critical Path MethodCPM 每一百萬個使用者會有幾次抱怨 Complaint per MillionCRM 客戶關係管理 Customer Relationship ManagementCRP 產能需求規劃 Capacity Requirements PlanningCS 顧客滿意度 Customer SatisfactionCTO 客製化生產 Configuration To OrderDVT 設計驗證 Design Verification TestingDSS 決策支援系統 Decision Support SystemEC 設計變更/工程變更 Engineer ChangeEC 電子商務 Electronic CommerceEMC 電磁相容 Electric Magnetic CapabilityEOQ 基本經濟訂購量 Economic Order QuantityERP 企業資源規劃 Enterprise Resource PlanningFMS 彈性製造系統 Flexible Manufacture SystemFQC 成品品質管制 Finish or Final Quality ControlIPQC 製程品質管制 In-Process Quality ControlIQC 進料品質管制 Incoming Quality ControlISO 國際標準組織 International Organization for Standardization ISAR 首批樣品認可 Initial Sample Approval RequestJIT 即時管理 Just In TimeMES 製造執行系統 Manufacturing Execution SystemMO 製令 Manufacture OrderMPS 主生產排程 Master Production ScheduleMRO 請修(購)單 Maintenance Repair OperationMRP 物料需求規劃 Material Requirement PlanningMRPII 製造資源計劃 Manufacturing Resource PlanningNFCF 更改預估量的通知 Notice for Changing ForecastOEM 委託代工 Original Equipment ManufactureODM 委託設計與製造 Original Design & ManufactureOPT 最佳生產技術 Optimized Production TechnologyOQC 出貨品質管制 Out-going Quality ControlPDCA PDCA管理循環 Plan-Do-Check-ActionPO 訂單 Purchase OrderQA 品質保證 Quality AssuranceQC 品質管制 Quality ControlQCC 品管圈 Quality Control CircleQE 品質工程 Quality EngineeringRMA 退貨驗收 Returned Material Approval ROP 再訂購點 Re-Order PointSCM 供應鏈管理 Supply Chain ManagementSFC 現場控制 Shop Floor ControlSO 訂單 Sales OrderSOR 特殊訂單需求 Special Order RequestTOC 限制理論 Theory of ConstraintsTPM 全面生產管理 Total Production Management TQC 全面品質管制 Total Quality ControlTQM 全面品質管理 Total Quality Management WIP 在製品 Work In Process。
品质管理英文术语大全

品质管理英文术语大全1. IntroductionIn the field of quality management, it is important to have a good understanding of the various terminology used. This document provides a comprehensive list of quality management terms in English.2. Quality Management Terms2.1 Quality•Quality: The degree to which a product or service meets the requirements and expectations of customers.•Quality Assurance: The process of systematically ensuring that a product or service meets specified requirements.•Quality Control: The process of checking that a product or service meets specified requirements.2.2 Quality Management Systems•ISO 9001: The international standard for quality management systems.•Quality Policy: A formal statement by an organization of its overall intentions and direction pertning to quality management.•Quality Objectives: The specific goals and targets set by an organization with respect to quality management.•Process Approach: Managing activities and resources as processes to achieve desired outcomes.2.3 Quality Planning•Quality Planning: The systematic process of identifying the quality-related activities that need to be performed to ensure that objectives are achieved.•Quality Metrics: The measurements used to evaluate the performance of processes, products, and services.•Risk Management: The process of identifying, assessing, and prioritizing risks to minimize or eliminate their impact on project objectives.2.4 Quality Assurance•Quality Audit: An independent examination to determine whether quality activities and related results comply with planned arrangements.•Supplier Quality Assurance: The process of assessing and ensuring the quality of products or services provided by suppliers.•Quality Management Review: An evaluation of the effectiveness and suitability of the quality management system.2.5 Quality Control•Statistical Process Control: The use of statistical techniques to monitor and control processes to ensure their stability and predictability.•Inspection: The process of examining a product or service to determine its conformity to specified requirements.•Defect: A nonconformance of a product or service with specified requirements.2.6 Continuous Improvement•Plan-Do-Check-Act (PDCA): A four-step iterative process for achieving continuous improvement.•Kzen: A Japanese term meaning continuous improvement.•Six Sigma: A data-driven approach forimproving the quality of processes by reducing variation and defects.3. ConclusionThis document has provided a comprehensive list of quality management terms in English. It is important for professionals in the field of quality management to have a good understanding of these terms in order to effectively communicate and implement quality management practices.。
质量管理模式迭代升级推动企业高质量发展

104质量管理模式迭代升级推动企业高质量发展马利军(中车青岛四方机车车辆股份有限公司)摘 要:中车青岛四方机车车辆股份有限公司基于经典质量管理理论和先进质量理念,结合多年质量管理实践经验,以政策规划与技术进步为指引,以数字化改造为手段,深入优化创新质量管理模式,实现了质量管理模式的3次迭代升级,为公司在绿色发展、行业促进、服务国家战略方面创造了卓越的经济和社会成效。
关键词:质量管理模式,迭代升级,高质量发展 DOI编码:10.3969/j.issn.1674-5698.2023.10.016Iterative Upgrading of Quality Management Model Promotes theHigh-quality Development of EnterpriseMA Li-jun(CRRC Qingdao Sifang Co., Ltd.)Abstract: Based on the classical quality management theories and modern quality concepts, combined with years of practical experience in quality management, guided by policy planning and technological progress, empowered with digital transformation, CRRC Qingdao Sifang Co., Ltd. has deeply optimized and innovated the quality management model, and realized the iterative upgrading of the quality management model for three times, and created excellent economic and social benefits for the company in green development, industry promotion, and serving the national strategy. Keywords: quality management model, iterative upgrading, high-quality development作者简介:马利军,中车青岛四方机车车辆股份有限公司总经理,正高级工程师,研究方向为企业管理创新、产业数字化转型、 精益管理等。
品质管理英文术语大全

品质管理英文术语大全在当今全球化竞争激烈的市场环境下,品质管理成为企业追求竞争优势和客户满意度的重要战略。
了解和掌握品质管理的相关英文术语,对于提升企业的品质管理水平至关重要。
本文将详细介绍品质管理领域常用的英文术语,帮助读者更深入地理解品质管理的核心概念和方法。
品质管理基础术语Quality ManagementQuality management refers to the process of overseeing and ensuring that products or services meet or exceed customer expectations. It involves creating and implementing policies and procedures to maintain and improve quality standards.Total Quality Management (TQM)TQM is a management approach that focuses on continuous improvement of processes and products to enhance customer satisfaction. It involves all members of an organization in a systematic approach to quality improvement.Quality Assurance (QA)QA is the process of ensuring that products and processes meet predefined quality requirements. It involves systematic monitoring and evaluation to ensure quality standards are met.Quality Control (QC)QC involves monitoring and measuring product or service quality to ensure that it meets specified requirements. It includes activities such as inspections, testing, and process control to identify and correct defects.品质管理工具与技术Six SigmaSix Sigma is a data-driven approach to process improvement that aims to reduce defects and improve quality by identifying and eliminating variation in processes.Lean ManufacturingLean manufacturing is a systematic approach to eliminating waste and improving efficiency in production processes. It focuses on delivering value to customers with minimal resources.Statistical Process Control (SPC)SPC is a method for monitoring and controlling processes through statistical analysis. It involves using statistical tools to identify and address process variations that may lead to defects.Root Cause AnalysisRoot cause analysis is a problem-solving technique that aims to identify the underlying causes of quality issues or defects. It involves systematically analyzing data to determine the root cause of problems.品质管理标准与认证ISO 9001ISO 9001 is an international standard that specifies requirements for a quality management system. It provides guidelines for organizations to ensure consistent quality in products and services.Quality Management System (QMS)A QMS is a set of policies, processes, and procedures for planning and executing quality management activities within an organization. It enables the organization to meet quality objectives and customer requirements.Quality CertificationQuality certification is a formal recognition that an organization meets specified quality standards. It provides assurance to customers and stakeholders that the organization has established and maintains effective quality management processes.结语品质管理是企业实现持续竞争优势的关键因素,精通品质管理的相关英文术语对于推动企业品质管理工作的开展具有重要意义。
质量控制中英文对照

质量控制中英文对照Title: Quality Control Chinese-English ComparisonIntroduction:Quality control is an essential aspect of any manufacturing or production process. It ensures that products meet certain standards and specifications to satisfy customer requirements. In this article, we will compare the terms and concepts related to quality control in Chinese and English.1. Definitions and Concepts1.1 In Chinese: 质量控制 (zhìliàng kòngzhì)In English: Quality Control1.2 In Chinese: 质量标准(zhìliàng biāozhǔn)In English: Quality Standards1.3 In Chinese: 质量管理(zhìliàng guǎnlǐ)In English: Quality Management2. Quality Control Methods2.1 In Chinese: 抽样检查(chōuyàng jiǎnchá)In English: Sampling Inspection2.2 In Chinese: 全面检查(quánmiàn jiǎnchá)In English: 100% Inspection2.3 In Chinese: 工艺控制(gōngyì kòngzhì)In English: Process Control3. Quality Control Tools3.1 In Chinese: 品质控制图(pǐnzhì kòngzhì tú)In English: Control Charts3.2 In Chinese: 故障模式和效果分析(gùzhàng móshì hé xiàoguǒ fēnxī) In English: Failure Mode and Effect Analysis (FMEA)3.3 In Chinese: 六西格玛(liù xī gé mǎ)In English: Six Sigma4. Quality Control Standards4.1 In Chinese: ISO9001标准(ISO9001 biāozhǔn)In English: ISO 9001 Standard4.2 In Chinese: TS16949标准(TS16949 biāozhǔn)In English: TS 16949 Standard4.3 In Chinese: AS9100标准(AS9100 biāozhǔn)In English: AS 9100 Standard5. Quality Control Benefits5.1 In Chinese: 提高产品质量(tígāo chǎnpǐn zhìliàng)In English: Improve Product Quality5.2 In Chinese: 降低生产成本(jiàngdī shēngchǎn chéngběn)In English: Reduce Production Costs5.3 In Chinese: 提高客户满意度(tígāo kèhù mǎnyì dù)In English: Increase Customer SatisfactionConclusion:Quality control is a crucial aspect of any industry, and understanding the terms and concepts in both Chinese and English can help facilitate communication and collaboration in a globalized world. By implementing effective quality control measures and standards, businesses can ensure the consistency and reliability of their products, leading to increased customer satisfaction and profitability.。
质量管理常用英文单词
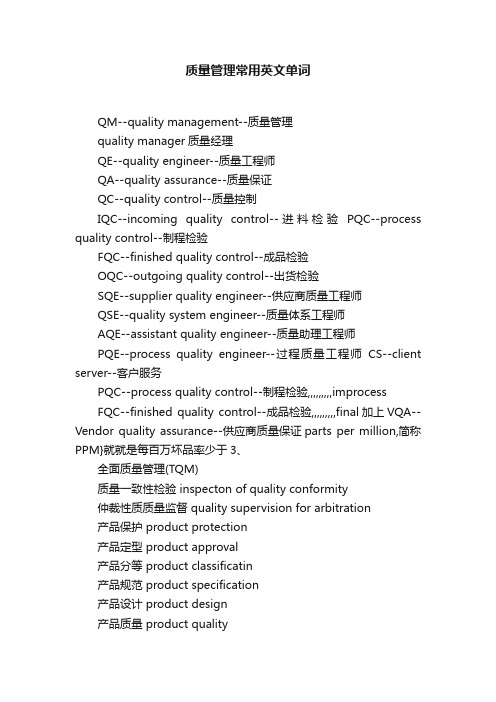
质量管理常用英文单词QM--quality management--质量管理quality manager质量经理QE--quality engineer--质量工程师QA--quality assurance--质量保证QC--quality control--质量控制IQC--incoming quality control--进料检验PQC--process quality control--制程检验FQC--finished quality control--成品检验OQC--outgoing quality control--出货检验SQE--supplier quality engineer--供应商质量工程师QSE--quality system engineer--质量体系工程师AQE--assistant quality engineer--质量助理工程师PQE--process quality engineer--过程质量工程师CS--client server--客户服务PQC--process quality control--制程检验,,,,,,,,,improcessFQC--finished quality control--成品检验,,,,,,,,,final加上VQA--Vendor quality assurance--供应商质量保证parts per million,简称PPM}就就是每百万坏品率少于3、全面质量管理(TQM)质量一致性检验 inspecton of quality conformity仲裁性质质量监督 quality supervision for arbitration产品保护 product protection产品定型 product approval产品分等 product classificatin产品规范 product specification产品设计 product design产品质量 product quality产品合格率 product percent of pass产品系列化 product seriation产品管理标准 product management standard产品计量单位 unit of measurement of product产品售后服务 after service产品质量标志 product quality mark产品质量标准 product quality standard产品质量管理 product quality management产品质量检验 product quality inspection产品质量监督检验 product quality supervision and inspection 产品质量认证标志 certification marking of product quality产品质量认证程序 certification procedure of product quality 产品质量认证制度 certification system of product quality认证 certification立法 legislation自行认证 self-certification认可 accreditation安全认证 safety certification安全认证标志 mark of safety certification强制性认证 compulsory certificate实验室鉴定 laboratory qualification实验室认证 laboratory certification自愿认证制 voluntary system of certification法规机构 regulatory authorities认证活动 certification activity认证体系 certification system认证计划 certification scheme认证机构 certification body检验机构 inspecton body许可证 licence申请人 applicant许可证持有者 licensee合格证书 certificate of conformity合格标记 mark of conformity认证体系的利用 access to certification system认证体系的参与者 participant in certification system认证体系的成员 member of certification system批准 approval型式批准 type approval测试实验室的认可 accreditation of testing laboratory认可 accreditation认可体系 accreditation system认可机构 accreditation body认可的实验室 accredited laboratory认可准则 acreditatin criteria实验室评定 laboratory assessment实验室评定者 laboratory assessor认可的实验室的试验报告 accredited laboratory test report批准签署人 approved signatory承认与批准协议 recognition and approval arrangement承认协议 recognition arrangement单边协议 unilateral arrangement双边协议 bilateral arrangement多边协议 multilateral arrangemetn互利 reciprocity平等待遇 equal treatmetn国家待遇 national treatment国家与平等待遇 national and equal treatment合格及有关的通用概念conformity and related generalconcept 合格 conformity合格测试 conformity testing合格 acceptable合格品 acceptable part合格标志 mark of conformity合格认证 conformity certification合格认证标志 mark of conformity certification 合格品标志 mark of acceptable product合格证书 certificate of conformity合格证检查 inspection by certificate合格质量检查 acceptable quality level评定合格 assessment of conformity合格评定 conformity assessment型式评价 type evaluation合格监督 conformity surveillance合格证明 verification of conformity合格保证 assurance of conformity供货商声明 supplier's declaration生产许可证 production licence一致 consensus检验 inspection不定期检验 nonperiodic inspection抽样检验 sampling inspection出厂检验 exfactory inspection第一方检验 first party inspection第二方检验 second party inspection第三方检验 third party inspection第三方认证制度 third pary certification定期检验 periodic inspection交收检验 acceptance inspeciton例行检验 routine inspeciton生产检验 produciton inspeciton生产定型检验 production approval inspeciton验收检验 acceptance inspeciton验证检验 compliance test仲裁检验 arbitration inspection制造商担保 guarantee by manufacturer百分比抽样检查 percent sampling inspection不合格判定数 rejection number不合格质量水平 rejecton quality level抽查型质量监督 sampling quality supervision环境监测 environmental monitoring抽样 sampling多次抽样 multiple sampling分层抽样 stratified sampling分层随机抽样 stratified random smapling多级抽样 multistage sampling二次抽样 double sampling试件 test piece试验报告 test report试样 test sample测试设备 testing equipment测试试验室 testing laboratority商标 trademark商品名称 trade-name测试 testing试验 test实验室间的试验比较 interlaboratory test comparisons 熟练水平试验 proficiency testing次品 defective product代用产品 substitute product定量试验 quantitative test出口管理 export control出口许可证制度 export control进口许可证制度 import licence system定额管理 quota management非关税壁垒 non-tarrif barrier关税壁垒 tariff barrier关税普遍优惠制 general preferential duties Core value(核心价值)Love 愛心Confidence 信心Decision 決心Corporate culture(公司文化)Integration 融合Responsibility 責任Progress 進步3T STRATEGYTime to market 及時切入生產Time to volume 及時大量生產Time to money 及時大量交貨FOUR CONTROL SYSTEM 四大管制系統Engineering control system 工程管制系統Quality control system品質管制系統Manufacturing control system生產管制系統Management control system經營管制系統7SClassification整理(sorting, organization)-seiri Regulation整頓(arrangement, tidiness)-seiton Cleanliness清掃(sweeping, purity)-seisoConservation清洁(cleaning, cleanliness)-seiktsuCulture教養(discipline)-shitsukeSave 節約Safety安全二:英文縮寫品質人員名稱類QC quality control 品質管理人員FQC final quality control 終點品質管制人員IPQC in process quality control 制程中的品質管制人員OQC output quality control 最終出貨品質管制人員IQC incoming quality control 進料品質管制人員TQC total quality control 全面質量管理POC passage quality control 段檢人員QA quality assurance 質量保證人員OQA output quality assurance 出貨質量保證人員QE quality engineering 品質工程人員品質保證類FAI first article inspection 新品首件檢查FAA first article assurance 首件確認CP capability index 能力指數CPK capability process index 模具製程能力參數SSQA standardized supplier quality audit 合格供應商品質評估FMEA failure model effectiveness analysis 失效模式分析FQC運\作類AQL Acceptable Quality Level 運\作類允收品質水準S/S Sample size 抽樣檢驗樣本大小ACC Accept 允收REE Reject 拒收CR Critical 極嚴重的MAJ Major 主要的MIN Minor 輕微的Q/R/S Quality/Reliability/Service 品質/可靠度/服務P/N Part Number 料號L/N Lot Number 批號AOD Accept On Deviation 特采UAI Use As It 特采FPIR First Piece Inspection Report 首件檢查報告PPM Percent Per Million 百萬分之一制程統計品管專類SPC Statistical Process Control 統計製程管制SQC Statistical Quality Control 統計品質管制GRR Gauge Reproductiveness & Repeatability 量具之再制性及重測性判斷量可靠與否DIM Dimension 尺寸DIA Diameter 直徑N Number 樣品數其它品質術語類QIT Quality Improvement Team 品質改善小組ZD Zero Defect 零缺點QI Quality Improvement 品質改善QP Quality Policy 目標方針TQM T otal Quality Management 全面品質管理RMA Return Material Audit 退料認可7QCT ools 7 Quality Control T ools 品管七大手法通用之件類ECN Engineering Change Notice 工程變更通知(供應商)ECO Engineering Change Order 工程改動要求(客戶)PCN Process Change Notice 工序改動通知PMP Product Management Plan 生產管制計劃SIP Standard Inspection Procedure 製程檢驗標準程序SOP Standard Operation Procedure 製造作業規範IS Inspection Specification 成品檢驗規範BOM Bill Of Material 物料清單PS Package Specification 包裝規範SPEC Specification 規格DWG Drawing 圖面系統文件類ES Engineering Standard 工程標準CGOO China General PCE龍華廠文件IWS International Workman Standard 工藝標準ISO International Standard Organization 國際標準化組織GS General Specification 一般規格部類PMC Production & Material Control 生產与物料控制PCC Product control center 生產管制中心PPC Production Plan Control 生產計劃控制MC Material Control 物料控制DC Document Center 資料中心QE Quality Engineering 品質工程(部)QA Quality Assurance 品質保證(處)QC Quality Control 品質管制(課)PD Product Department 生產部LAB Laboratory 實驗室IE Industrial Engineering 工業工程R&D Research & Design 設計開發部生產類PCs Pieces 個(根,塊等)PRS Pairs 雙(對等)CTN Carton 卡通箱PAL Pallet/skid 棧板PO Purchasing Order 采購訂單MO Manufacture Order 生產單D/C Date Code 生產日期碼ID/C Identification Code (供應商)識別碼SWR Special Work Request 特殊工作需求L/N Lot Number 批號P/N Part Number 料號OEM Original Equipment Manufacture 原設備製造。
quality management

Quality ManagementIntroductionQuality management refers to the process of ensuring that products or services meet or exceed customer expectations. It involves systematic activities that are implemented throughout the product lifecycle to identify, plan, control, and improve the quality of a product or service. This document provides an overview of the key concepts and principles of quality management.Key Principles of Quality ManagementQuality management is based on several key principles. These principles provide a foundation for effective quality management practices. Some of the key principles include:1.Customer Focus: The primary focus of qualitymanagement is to meet customer requirements and exceed their expectations. This involves understanding customer needs, expectations, and preferences, and aligningprocesses and resources to deliver value to customers.2.Leadership: Effective quality management requiresstrong leadership commitment and involvement. Themanagement team plays a crucial role in setting qualityobjectives, communicating the importance of quality, and providing necessary resources and support to achievethose objectives.3.Continuous Improvement: Quality management is an ongoing process of continuous improvement. It involves identifying areas for improvement, setting objectives, implementing changes, and monitoring the outcomes to ensure that desired results are achieved.4.Involvement of People: Quality management emphasizes the involvement of people at all levels of the organization. Employees are encouraged to contribute their ideas, knowledge, and skills to drive quality improvement initiatives.5.Process Approach: Quality management adopts a process approach, where all activities and tasks are viewed as interconnected processes. It involves identifying key processes, defining their inputs, outputs, and interactions, and continually monitoring and improving these processes.6.Evidence-Based Decision Making: Quality management relies on accurate and reliable data to make informed decisions. It involves collecting, analyzing, and interpreting data to identify trends, patterns, and opportunities for improvement.7.Supplier Relationships: Quality management recognizes the importance of building strong relationships with suppliers. Collaboration with suppliers helps ensure that quality standards and expectations are met throughout the supply chain.Components of Quality Management SystemA quality management system (QMS) is a set of interrelated or interacting elements that an organization uses to direct and control the quality of its products or services. The components of a QMS may vary depending on the industry and organizational context. However, some common components include:1.Quality Policy: A quality policy is a statement of anorganization’s c ommitment to quality. It outlines theorganization’s quality objectives and serves as a guide for decision-making and quality improvement activities.2.Quality Objectives: Quality objectives are specific,measurable targets that an organization sets to achieve its quality policy. These objectives are aligned with customer requirements and are monitored to ensure progresstowards meeting them.3.Quality Planning: Quality planning involves thedevelopment of a systematic approach to achieve quality objectives. It includes identifying quality requirements,establishing processes to deliver products or services that meet those requirements, and defining quality standards and criteria.4.Quality Assurance: Quality assurance activities arefocused on providing confidence that quality requirements will be met. It involves the development andimplementation of processes, procedures, and controls to prevent defects and ensure consistent quality.5.Quality Control: Quality control activities are aimedat verifying that products or services meet specifiedrequirements. It involves monitoring and measuringproduct or service characteristics, conducting inspections and tests, and taking appropriate corrective actions when non-conformities are identified.6.Continuous Improvement: Continuous improvementis an essential component of a QMS. It involvessystematically evaluating performance, identifying areasfor improvement, implementing changes, and monitoring the outcomes to ensure sustained improvement over time.7.Documentation: Documentation is a critical aspect ofa QMS. It includes procedures, work instructions, forms,records, and other documents that define and support the implementation of quality management processes.Benefits of Quality ManagementImplementing effective quality management practices can lead to numerous benefits for an organization. Some of the key benefits include:1.Improved Customer Satisfaction: By consistentlydelivering products or services that meet or exceedcustomer expectations, organizations can enhancecustomer satisfaction and loyalty.2.Increased Efficiency and Productivity: Qualitymanagement practices help identify and eliminate waste,inefficiencies, and non-value-added activities, leading toimproved operational efficiency and productivity.3.Reduced Costs: By preventing defects and reducingrework, organizations can reduce costs associated withscrap, rejections, and customer complaints.4.Enhanced Reputation and Brand Image:Organizations that consistently deliver high-qualityproducts or services build a strong reputation and brand image in the marketplace.5.Regulatory Compliance: Quality managementsystems help ensure compliance with relevant regulations, standards, and legal requirements.6.Better Decision Making: Evidence-based decisionmaking, supported by accurate and reliable data, helpsorganizations make informed decisions and drivecontinuous improvement.7.Employee Satisfaction and Engagement: Involvingemployees in quality improvement initiatives andrecognizing their contributions enhances employeesatisfaction and engagement.ConclusionQuality management is a critical aspect of ensuring customer satisfaction, operational efficiency, and continuous improvement. By implementing effective quality management practices, organizations can achieve their quality objectives, enhance their reputation, and gain a competitive edge in the marketplace.。
quality management certification

quality management certificationThere are several quality management certifications available, depending on the specific industry and country. Some well-known certifications include:1. ISO 9001: This is an international standard for quality management systems. It focuses on the implementation and maintenance of quality management and customer satisfaction.2. Six Sigma: Six Sigma is a methodology used to improve processes and reduce defects in products or services. Certifications like the Six Sigma Green Belt and Black Belt signify expertise in using Six Sigma techniques.3. Lean: Lean is a systematic approach to eliminate waste and improve efficiency in processes. Certifications like the Lean Six Sigma Yellow Belt, Green Belt, and Black Belt validate knowledge and expertise in lean principles.4. CQE (Certified Quality Engineer): Offered by the American Society for Quality (ASQ), this certification demonstrates expertise in quality engineering and various quality management principles and tools.5. CQM/OE (Certified Quality Manager/Organizational Excellence): Also offered by ASQ, this certification demonstrates a deep understanding of quality management principles and their application to organizational excellence.6. CQA (Certified Quality Auditor): This certification focuses onauditing quality management systems and validating compliance with relevant standards and regulations.It is essential to research and select the certification that aligns with your industry and career goals. Additionally, the requirements for each certification may vary, including specific education, experience, and passing an exam.。
品质管理评价提神计划
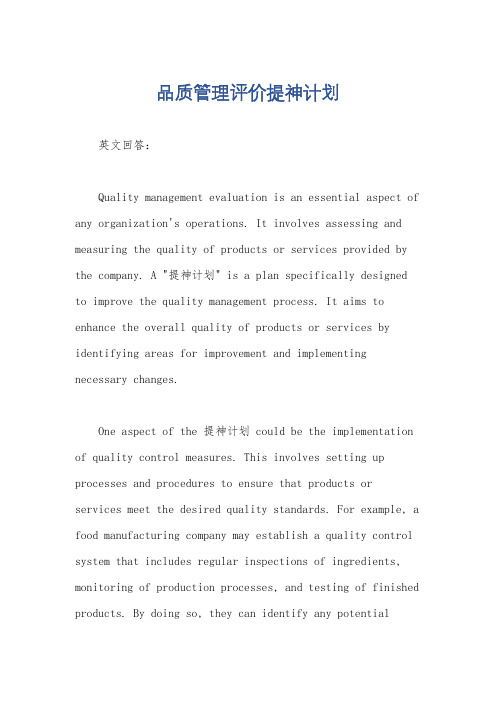
品质管理评价提神计划英文回答:Quality management evaluation is an essential aspect of any organization's operations. It involves assessing and measuring the quality of products or services provided by the company. A "提神计划" is a plan specifically designed to improve the quality management process. It aims to enhance the overall quality of products or services by identifying areas for improvement and implementing necessary changes.One aspect of the 提神计划 could be the implementation of quality control measures. This involves setting up processes and procedures to ensure that products or services meet the desired quality standards. For example, a food manufacturing company may establish a quality control system that includes regular inspections of ingredients, monitoring of production processes, and testing of finished products. By doing so, they can identify any potentialissues or defects and take corrective actions to maintain high-quality standards.Another aspect of the 提神计划 could be the training and development of employees. This is crucial as employees play a significant role in delivering quality products or services. Providing training programs and workshops can help employees understand the importance of quality management and equip them with the necessary skills and knowledge to perform their tasks effectively. For instance, a customer service team may undergo training on how to handle customer complaints and resolve issues promptly, ensuring customer satisfaction and maintaining the quality of service provided.Regular performance evaluations and feedback are also essential components of the 提神计划. By conducting performance evaluations, organizations can identify areas where employees may need improvement and provide them with constructive feedback. This helps in maintaining a high level of quality in their work. For example, a software development company may conduct regular code reviews andprovide feedback to their developers, allowing them to identify and fix any potential bugs or issues in their code, leading to higher-quality software products.In addition to these measures, the 提神计划 may also involve implementing quality improvement initiatives. This could be in the form of process improvements, such as streamlining workflows or implementing new technologies to enhance efficiency and reduce errors. It could also involve gathering customer feedback and using it to make necessary improvements to products or services. For example, a hotel may collect guest feedback through surveys or onlinereviews and use that information to make changes to their facilities or services to meet customer expectations and improve overall quality.中文回答:品质管理评价是任何组织运营中至关重要的一个方面。
机加工精度要求 英文

机加工精度要求英文Machining accuracy is a crucial aspect in the manufacturing industry, as it directly affects the quality, performance, and durability of the final product. The precision with which a part is machined determines its fitness for use and its ability to meet design specifications. Therefore, it is essential to understand and control machining accuracy to ensure the consistency and reliability of manufactured components.Machining accuracy requirements vary depending on the application and the type of material being machined. For example, high-precision machining is required for components in the aerospace, medical, and automotive industries, where parts must meet strict tolerances and performance standards. On the other hand, lower precision may be acceptable for certain applications where the parts do not require as much accuracy.To achieve the desired machining accuracy, it isnecessary to consider several factors, including machinetool precision, cutting tool selection, workpiece material, and machining processes. Machine tool precision is influenced by factors such as machine rigidity, thermal stability, and vibration control. Cutting tool selection involves choosing the appropriate tool material, geometry, and coating to match the workpiece material and machining conditions. Workpiece material properties, such as hardness, ductility, and thermal conductivity, also affect machining accuracy.Machining processes, such as turning, milling, drilling, and grinding, each have their own unique challenges and considerations. For example, turning is typically used for cylindrical parts and requires precise control of feed rate, spindle speed, and cutting depth to achieve the desired surface finish and dimensional accuracy. Milling, on the other hand, is suitable for flat and contoured surfaces and requires careful selection of cutting conditions to avoid tool wear and maintain dimensional stability.To ensure machining accuracy, it is important toimplement quality control measures throughout the manufacturing process. This includes regular machine tool maintenance and calibration, inspection of workpieces before and after machining, and the use of precision measuring equipment. Additionally, it is beneficial to employ advanced machining technologies, such as CNC machining and additive manufacturing, which provide greater control and repeatability.In conclusion, machining accuracy requirements are critical for ensuring the quality and performance of manufactured components. By considering machine tool precision, cutting tool selection, workpiece material, and machining processes, as well as implementing qualitycontrol measures, manufacturers can achieve the desired machining accuracy and produce reliable parts that meet design specifications.。
服装加工厂品质管理制度及流程

服装加工厂品质管理制度及流程英文回答:Quality Management System and Process for Garment Manufacturing Factory.1. Introduction.Quality control is an essential aspect of garment manufacturing, ensuring that products meet customer requirements and industry standards. A robust quality management system (QMS) is crucial for achieving consistent quality, reducing defects, and enhancing customer satisfaction.2. Quality Management System.2.1. Quality Policy.The QMS must be based on a clearly defined qualitypolicy outlining the organization's commitment to quality, customer satisfaction, and continuous improvement.2.2. Quality Objectives.Specific, measurable, achievable, relevant, and time-bound (SMART) quality objectives should be established to guide quality control efforts.2.3. Quality Control Plan.A detailed quality control plan outlining the processes, inspections, and acceptance criteria for each production stage should be developed and implemented.3. Quality Control Process.3.1. Inspection and Testing.Regular inspections and testing of raw materials, in-process products, and finished garments ensure adherence to quality standards.3.2. Non-Conformance Management.A system for managing non-conformances should be in place, including procedures for identifying, investigating, and correcting defects.3.3. Supplier Management.Supplier quality control requirements should be established and monitored to ensure the quality of incoming materials.3.4. Training and Development.Employees should receive adequate training in quality control techniques and industry best practices.3.5. Continuous Improvement.The QMS should include mechanisms for continuous improvement, such as quality circles and process audits.4. Quality Assurance.4.1. Customer Feedback.Customer feedback should be regularly collected and analyzed to identify areas for improvement.4.2. Third-Party Inspections.Independent third-party inspections can provide an objective assessment of product quality and compliance with standards.4.3. Certifications and Accreditations.Obtaining certifications such as ISO 9001 or SA8000 demonstrates the organization's commitment to quality and ethical practices.5. Conclusion.An effective quality management system and process are vital for ensuring the quality of garments produced by manufacturing factories. By implementing and maintaining a robust QMS, organizations can meet customer expectations, enhance brand reputation, and achieve operational excellence.中文回答:服装加工厂品质管理制度及流程。
英语作文-集成电路设计行业中的品质管理与质量保证
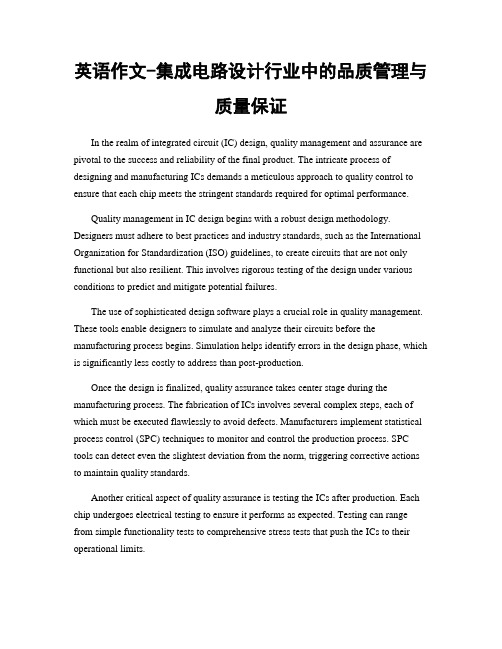
英语作文-集成电路设计行业中的品质管理与质量保证In the realm of integrated circuit (IC) design, quality management and assurance are pivotal to the success and reliability of the final product. The intricate process of designing and manufacturing ICs demands a meticulous approach to quality control to ensure that each chip meets the stringent standards required for optimal performance.Quality management in IC design begins with a robust design methodology. Designers must adhere to best practices and industry standards, such as the International Organization for Standardization (ISO) guidelines, to create circuits that are not only functional but also resilient. This involves rigorous testing of the design under various conditions to predict and mitigate potential failures.The use of sophisticated design software plays a crucial role in quality management. These tools enable designers to simulate and analyze their circuits before the manufacturing process begins. Simulation helps identify errors in the design phase, which is significantly less costly to address than post-production.Once the design is finalized, quality assurance takes center stage during the manufacturing process. The fabrication of ICs involves several complex steps, each of which must be executed flawlessly to avoid defects. Manufacturers implement statistical process control (SPC) techniques to monitor and control the production process. SPC tools can detect even the slightest deviation from the norm, triggering corrective actions to maintain quality standards.Another critical aspect of quality assurance is testing the ICs after production. Each chip undergoes electrical testing to ensure it performs as expected. Testing can range from simple functionality tests to comprehensive stress tests that push the ICs to their operational limits.Moreover, reliability testing is an integral part of quality assurance. It assesses how the IC will perform over time, considering factors like temperature, voltage, and usage patterns. Reliability testing helps predict the lifespan of the IC and ensures that it will not fail prematurely when deployed in critical applications.The commitment to quality extends beyond the production line. Quality management also encompasses the packaging and shipping of ICs. Proper packaging is essential to protect the delicate chips from physical and electrostatic damage during transportation.In conclusion, quality management and assurance in the IC design industry are multifaceted and require a concerted effort from designers, manufacturers, and quality control professionals. By adhering to rigorous standards and employing advanced testing and monitoring techniques, the industry strives to deliver ICs that are not only powerful and efficient but also dependable and durable. This relentless pursuit of quality is what underpins the reliability of the myriad devices that power our modern world. 。
机电精细化管理方案

机电精细化管理方案英文回答:Mechatronics fine management program is an essential approach to enhance the efficiency and productivity of mechanical and electrical systems. It involves the integration of mechanical engineering, electronics, control engineering, and computer science to optimize the performance of complex systems.One aspect of mechatronics fine management ispredictive maintenance. By utilizing advanced sensors and data analysis techniques, it is possible to monitor the condition of machines and predict potential failures before they occur. For example, in a manufacturing plant, sensors can be installed on machines to measure parameters such as temperature, vibration, and pressure. The data collected can be analyzed using machine learning algorithms to identify patterns and anomalies that may indicate a future breakdown. By taking proactive measures, such as schedulingmaintenance tasks or replacing worn-out components, downtime and repair costs can be significantly reduced.Another important aspect is energy efficiency. Mechatronics fine management emphasizes the optimization of energy consumption in mechanical and electrical systems. For instance, in a building automation system, sensors can be used to detect occupancy and adjust lighting and HVAC systems accordingly. By only providing the necessary amount of energy, unnecessary waste can be avoided, leading to cost savings and a more sustainable operation.Furthermore, mechatronics fine management also involves the integration of automation and robotics. By automating repetitive and manual tasks, productivity can be increased, and human errors can be minimized. For example, in a car manufacturing plant, robots can be programmed to perform tasks such as welding, painting, and assembly. This not only improves the quality and consistency of the products but also reduces the risk of accidents and injuries.In addition to the technical aspects, mechatronics finemanagement also requires effective communication and collaboration among different teams and departments. Clear instructions, regular meetings, and feedback sessions are essential to ensure smooth operations and continuous improvement. For instance, in a mechatronics project, engineers, technicians, and operators need to work together closely to design, implement, and maintain the systems. Regular meetings can be held to discuss progress, address challenges, and brainstorm ideas for improvement.中文回答:机电精细化管理方案是提高机电系统效率和生产力的重要方法。
五金品质管理流程
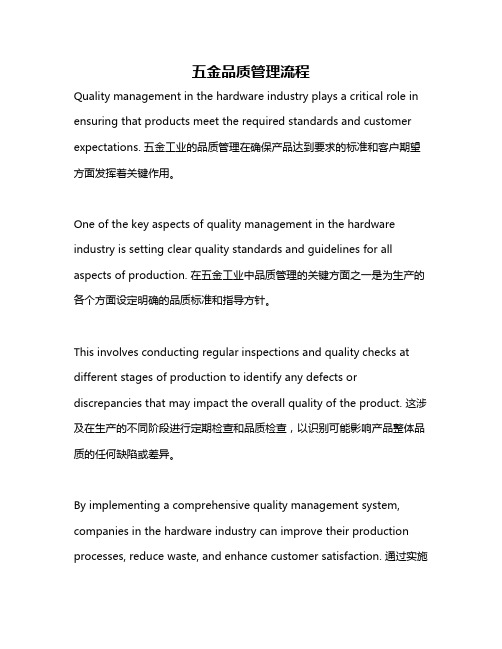
五金品质管理流程Quality management in the hardware industry plays a critical role in ensuring that products meet the required standards and customer expectations. 五金工业的品质管理在确保产品达到要求的标准和客户期望方面发挥着关键作用。
One of the key aspects of quality management in the hardware industry is setting clear quality standards and guidelines for all aspects of production. 在五金工业中品质管理的关键方面之一是为生产的各个方面设定明确的品质标准和指导方针。
This involves conducting regular inspections and quality checks at different stages of production to identify any defects or discrepancies that may impact the overall quality of the product. 这涉及在生产的不同阶段进行定期检查和品质检查,以识别可能影响产品整体品质的任何缺陷或差异。
By implementing a comprehensive quality management system, companies in the hardware industry can improve their production processes, reduce waste, and enhance customer satisfaction. 通过实施全面的品质管理体系,五金工业的企业可以改善其生产流程,减少浪费,提高客户满意度。
质量控制(英文)
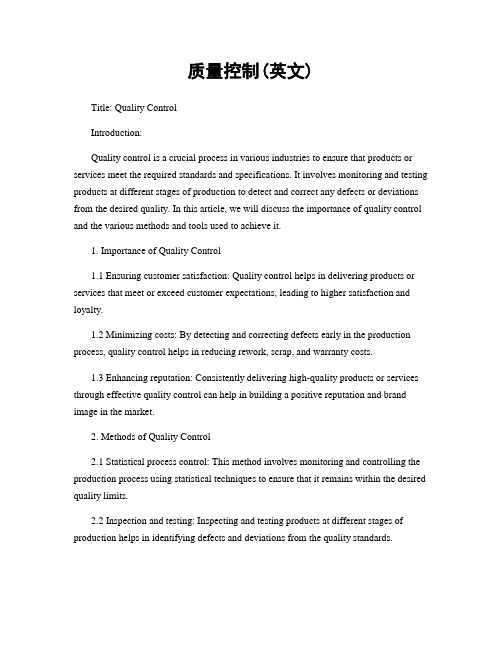
质量控制(英文)Title: Quality ControlIntroduction:Quality control is a crucial process in various industries to ensure that products or services meet the required standards and specifications. It involves monitoring and testing products at different stages of production to detect and correct any defects or deviations from the desired quality. In this article, we will discuss the importance of quality control and the various methods and tools used to achieve it.1. Importance of Quality Control1.1 Ensuring customer satisfaction: Quality control helps in delivering products or services that meet or exceed customer expectations, leading to higher satisfaction and loyalty.1.2 Minimizing costs: By detecting and correcting defects early in the production process, quality control helps in reducing rework, scrap, and warranty costs.1.3 Enhancing reputation: Consistently delivering high-quality products or services through effective quality control can help in building a positive reputation and brand image in the market.2. Methods of Quality Control2.1 Statistical process control: This method involves monitoring and controlling the production process using statistical techniques to ensure that it remains within the desired quality limits.2.2 Inspection and testing: Inspecting and testing products at different stages of production helps in identifying defects and deviations from the quality standards.2.3 Quality management systems: Implementing quality management systems such as ISO 9001 can help in establishing processes and procedures for effective quality control.3. Tools for Quality Control3.1 Control charts: Control charts are graphical tools used in statistical process control to monitor the variation in a process and detect any trends or patterns that indicate a problem.3.2 Pareto analysis: Pareto analysis is a technique used to identify and prioritize the most significant causes of quality issues based on the 80/20 rule.3.3 Six Sigma: Six Sigma is a methodology that aims to improve the quality of processes by reducing defects and variations to achieve near-perfect performance.4. Challenges in Quality Control4.1 Lack of resources: Limited budget, manpower, and time can pose challenges in implementing effective quality control measures.4.2 Changing requirements: Rapid changes in customer preferences, technology, and regulations can make it challenging to maintain consistent quality standards.4.3 Supplier quality: Ensuring the quality of raw materials and components from suppliers can be a challenge, as it directly impacts the quality of the final product.5. Continuous Improvement in Quality Control5.1 Kaizen: Kaizen is a Japanese philosophy of continuous improvement that focuses on making small, incremental changes to processes to achieve better quality.5.2 Total Quality Management (TQM): TQM is a management approach that emphasizes the involvement of all employees in the continuous improvement of quality.5.3 Lean manufacturing: Lean manufacturing principles such as reducing waste and optimizing processes can help in improving quality control and efficiency.In conclusion, quality control is essential for ensuring the consistency, reliability, and competitiveness of products or services in today's market. By understanding the importance of quality control, implementing the right methods and tools, addressing challenges, and focusing on continuous improvement, organizations can achieve higher customer satisfaction, lower costs, and a positive brand reputation.。
质量管理-品质管理体系

•
• • •
Flow chart of IQC Operation
Process of Quality Management Instrument Management Document Management
Quality Data Customer Feedback & Response Flow
Quality is designed into products, process and services, rather than obtaining quality through inspection. Quality assurance system, tools and techniques are consistently used to prevent quality problems from occurring
Quality Certificate
Taiwan Bright award
ISO9002 1997
Gaobu Bright award
ISO9002
1998
Taiwan Bright award
ISO9001 QS 9000
1999 1999
Gaobu Bright award
The relationship of quality management for Bright vs. Customer
DTS
NO
YES
Inspection
MRB
PASS
REJ
VQCR
QC Audit
PASS
NG
Screen
Return to Supplier
Waive
Warehaction
质量体系要求英语作文

质量体系要求英语作文英文回答:The requirements of a quality management system are aset of guidelines and principles that help organizations to ensure that their products and services consistently meet customer requirements and regulatory standards. These requirements are designed to help organizations achieve a high level of quality by providing a framework for planning, implementing, and maintaining effective quality management practices.The requirements of a quality management system are typically based on international standards, such as the ISO 9001 standard. These standards provide a common set of guidelines that organizations can use to implement and maintain effective quality management systems.The requirements of a quality management systemtypically include the following elements:Management responsibility: Top management must be committed to quality and must provide the necessary resources to implement and maintain an effective quality management system.Customer focus: Organizations must understand the needs and expectations of their customers and must strive to meet or exceed those needs.Process approach: Organizations must identify and manage the processes that are critical to meeting customer requirements.Continual improvement: Organizations must continuously improve their quality management system and their products and services.Evidence-based decision making: Organizations must make decisions based on data and evidence rather than on guesswork.The benefits of implementing a quality management system include:Improved customer satisfaction: Organizations that implement effective quality management systems can improve customer satisfaction by providing products and services that meet or exceed customer requirements.Reduced costs: Organizations that implement effective quality management systems can reduce costs by preventing defects, reducing waste, and improving efficiency.Increased productivity: Organizations that implement effective quality management systems can increase productivity by improving the quality of their products and services and by reducing rework and waste.Enhanced reputation: Organizations that implement effective quality management systems can enhance their reputation for quality and reliability.Increased market share: Organizations that implementeffective quality management systems can increase their market share by providing products and services that are superior to those of their competitors.中文回答:质量体系要求是一套准则和原则,可帮助组织确保其产品和服务始终符合客户要求和监管标准。