轮胎胶料抗硫化返原性的优化
抗硫化返原剂Perkalink 900在载重子午线轮胎中的应用
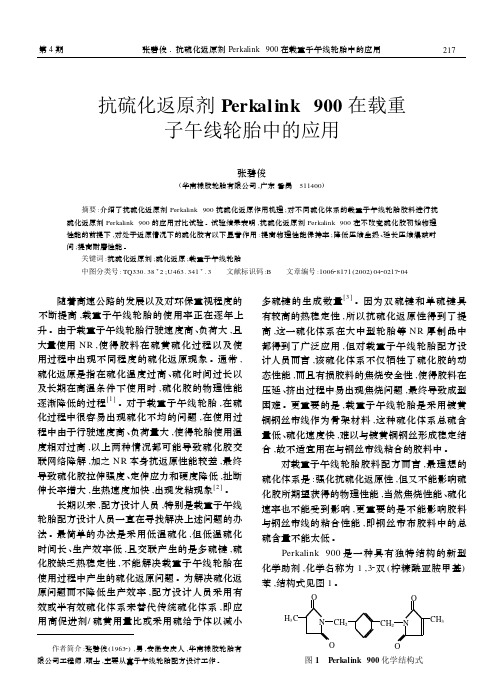
O
O
H3 C
N CH2
CH2 N
CH3
O
O
图 1 Perkalink 900 化学结构式
21 8 轮 胎 工 业 2002 年第 22 卷
Perkalink 900 是以一种新的方式 ———交联 补偿 来 加 强 抗 返 原 作 用 的 。当 返 原 发 生 时 , Perkalink 900 就产生对热稳定的碳2碳交联键 , 从而补偿了胶料中对热不稳定的多硫键的损失 , 使得硫化胶的交联密度 、物理性能都能保持不 变[4 ] 。由于 Perkalink 900 在发生返原时 , 生成 的碳2碳交联键键长与含 7 个硫原子的硫2硫交联 键键长相同 ,因此这种碳2碳交联键不仅热稳定性 好 ,而且柔顺性也好 ,使得硫化胶动态性能得以提 高 。因为 Perkalink 900 在不发生硫化返原时不 反应 ,因而胶料的焦烧安全性和硫化速度都不会 受到影响[5 ] ,这一特性也使得配方设计人员可以 在不对配方和加工工艺进行任何调整的情况下直 接使用 Perkalink 900 。
荷使用状态下的耐久性非常重要 。在返原情况 下 ,使用 Perkalink 900 的胶料的 tanδ值也都低 于未使用 Perkalink 900 的胶料 。从 A0 与 A1胶 料磨耗量对比试验情况看 ,正硫化时 ,两种胶料的 磨耗量相同 ,但在返原发生后 ,A0 的磨耗量比 A1 高出了 40. 5 %。
2. 06 3. 00 3. 39 5. 99 10. 44 0. 18 2. 89 1. 78 40. 8
1. 63 2. 64 2. 94 5. 57 10. 36 0. 17 2. 73 1. 89 32. 8
2. 44 3. 52 3. 82 6. 05 11. 71 0. 17 2. 75 2. 16 22. 9
抗硫化返原剂PK900在工程机械轮胎胎面胶中的应用

基 本 配方 : N R 1 0 0 , 炭 黑N3 3 0 5 0 , 氧 化锌
6 . 2 5 , 硬脂酸 4 0 2 0 1 , 硫黄 1 . 5 , 防 老 ̄ J I R D 1 . 5 , 防 老 剂 1 。 2 . 7 5 , 促进剂
化返原剂P K 9 0 0 、 氧化锌 ( Z n O 一 8 0 ) 、 促进剂 ( NS 一
8 0 ) 和硫黄 ( s - 8 o ) , 山东 阳谷 华泰 化工股 份有 限公 司产 品。
1 . 2 试 验配 方
化 。 由于橡 胶 材 料 的热 传 导 系数 较 小 , 硫 化 时 为 保证 升 温 最 慢 的胎 肩 部位 达 到 正硫 化 , 通 常 采 用 延 长硫 化 时 间 的方 法 , 结 果 导 致胎 体 内表 面和 胎
中图 分类 号 : T Q3 3 0 . 3 8 7 ; U4 6 3 . 3 4 1 . 5
文 献标 志码 : A
文章 编 号 : 1 0 0 6 — 8 1 7 1 ( 2 0 1 6 ) 1 1 — 0 6 7 2 — 0 4
工 程 机 械 轮胎 是 典 型 的厚 橡 胶 制 品 , 而且 许 多大 型或 巨型工 程机 械轮 胎胎 面胶 采用 天然 橡胶 ( N R ) 或 以NR 为主 的配方 , 用普 通硫黄硫 化体 系硫
1 . 1 主 要原 材料
7 0 1 2 - D型DI N磨 耗 试 验机 和G T 一 7 0 4 2 一 R E 型 回弹
性试验 机 , 中国 台湾高 铁检测仪器 有限公 司产 品 。
热稳定剂TCA-90在全钢子午线轮胎胎面基部胶中的应用
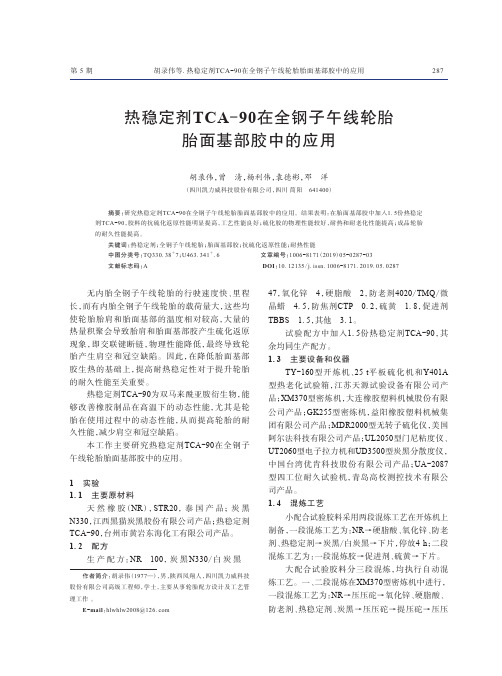
第 5 期胡录伟等.热稳定剂TCA-90在全钢子午线轮胎胎面基部胶中的应用287热稳定剂TCA-90在全钢子午线轮胎胎面基部胶中的应用胡录伟,曾 清,杨利伟,袁德彬,邓 洋(四川凯力威科技股份有限公司,四川简阳 641400)摘要:研究热稳定剂TCA-90在全钢子午线轮胎胎面基部胶中的应用。
结果表明:在胎面基部胶中加入1.5份热稳定剂TCA-90,胶料的抗硫化返原性能明显提高,工艺性能良好;硫化胶的物理性能较好,耐热和耐老化性能提高;成品轮胎的耐久性能提高。
关键词:热稳定剂;全钢子午线轮胎;胎面基部胶;抗硫化返原性能;耐热性能中图分类号:TQ330.38+7;U463.341+.6 文章编号:1006-8171(2019)05-0287-03文献标志码:A DOI:10.12135/j.issn.1006-8171.2019.05.0287无内胎全钢子午线轮胎的行驶速度快、里程长,而有内胎全钢子午线轮胎的载荷量大,这些均使轮胎胎肩和胎面基部的温度相对较高,大量的热量积聚会导致胎肩和胎面基部胶产生硫化返原现象,即交联键断链,物理性能降低,最终导致轮胎产生肩空和冠空缺陷。
因此,在降低胎面基部胶生热的基础上,提高耐热稳定性对于提升轮胎的耐久性能至关重要。
热稳定剂TCA-90为双马来酰亚胺衍生物,能够改善橡胶制品在高温下的动态性能,尤其是轮胎在使用过程中的动态性能,从而提高轮胎的耐久性能,减少肩空和冠空缺陷。
本工作主要研究热稳定剂TCA-90在全钢子午线轮胎胎面基部胶中的应用。
1 实验1.1 主要原材料天然橡胶(NR),STR20,泰国产品;炭黑N330,江西黑猫炭黑股份有限公司产品;热稳定剂TCA-90,台州市黄岩东海化工有限公司产品。
1.2 配方生产配方:NR 100,炭黑N330/白炭黑 47,氧化锌 4,硬脂酸 2,防老剂4020/TMQ/微晶蜡 4.5,防焦剂CTP 0.2,硫黄 1.8,促进剂TBBS 1.5,其他 3.1。
轮胎硫化工艺条件的优化
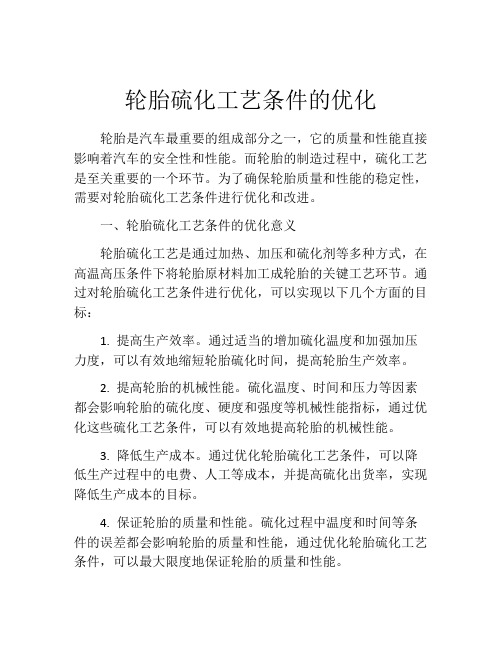
轮胎硫化工艺条件的优化轮胎是汽车最重要的组成部分之一,它的质量和性能直接影响着汽车的安全性和性能。
而轮胎的制造过程中,硫化工艺是至关重要的一个环节。
为了确保轮胎质量和性能的稳定性,需要对轮胎硫化工艺条件进行优化和改进。
一、轮胎硫化工艺条件的优化意义轮胎硫化工艺是通过加热、加压和硫化剂等多种方式,在高温高压条件下将轮胎原材料加工成轮胎的关键工艺环节。
通过对轮胎硫化工艺条件进行优化,可以实现以下几个方面的目标:1. 提高生产效率。
通过适当的增加硫化温度和加强加压力度,可以有效地缩短轮胎硫化时间,提高轮胎生产效率。
2. 提高轮胎的机械性能。
硫化温度、时间和压力等因素都会影响轮胎的硫化度、硬度和强度等机械性能指标,通过优化这些硫化工艺条件,可以有效地提高轮胎的机械性能。
3. 降低生产成本。
通过优化轮胎硫化工艺条件,可以降低生产过程中的电费、人工等成本,并提高硫化出货率,实现降低生产成本的目标。
4. 保证轮胎的质量和性能。
硫化过程中温度和时间等条件的误差都会影响轮胎的质量和性能,通过优化轮胎硫化工艺条件,可以最大限度地保证轮胎的质量和性能。
二、轮胎硫化工艺条件的优化方法1. 优化硫化温度和时间。
随着硫化温度的升高,硫化速度和硫化度也会随之增加。
但是当温度过高的时候,不仅会增加硫化丝的断裂可能性,还会导致轮胎变形和硫化不均匀等问题。
因此,在硫化温度和硫化时间之间需要进行平衡,找到二者之间的最佳组合。
2. 加强加压力度。
加压力度是影响硫化度和轮胎硬度的重要因素。
通过加强加压力度,可以有效地提高轮胎硫化质量和机械性能,并缩短硫化时间。
3. 采用新型硫化剂。
目前市场上流行的硫化剂主要有硫、硫代硫酸酯、过氧化物等。
通过选择合适的硫化剂,可以对轮胎硫化工艺条件进行优化,并有效提高轮胎的硬度和强度,以及耐久性和耐磨性等性能指标。
4. 采用自动化控制系统。
通过采用现代化的自动化控制系统,可以有效地控制轮胎硫化过程中的温度和时间等条件,提高硫化质量和生产效率,并减少操作人员的劳动强度和误操作可能性。
抗硫化返原剂pk900在全地形轮胎胎面胶中的应用
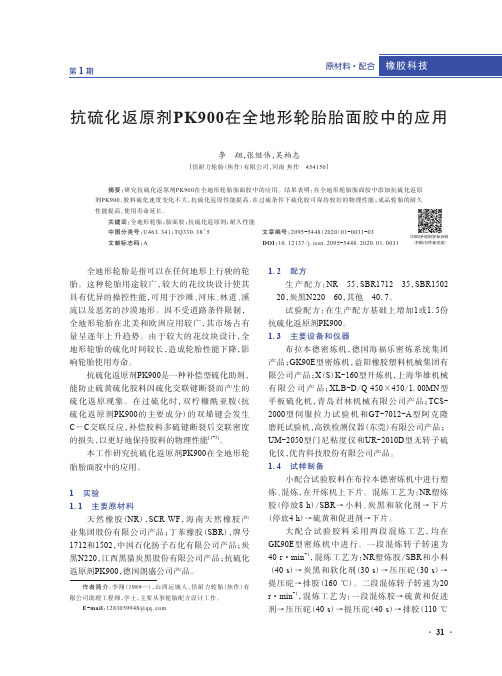
OSID开放科学标识码 (扫码与作者交流)
全地形轮胎是指可以在任何地形上行驶的轮 胎。 这 种 轮 胎 用 途 较 广,较 大 的 花 纹 块 设 计 使 其 具有优异的操控性能,可用于沙滩、河床、林道、溪 流以及恶劣的沙漠地形。因不受道路条件限制, 全 地 形 轮 胎 在 北 美 和 欧 洲 应 用 较 广,其 市 场 占 有 量 呈 逐 年 上 升 趋 势。 由 于 较 大 的 花 纹 块 设 计,全 地形轮胎的硫化时间较长,造成轮胎性能下降,影 响轮胎使用寿命。
剂PK900的胶料相比,添加抗硫化返原剂PK900的
胶料t10和t90变化不大,且添加1. 5份抗硫化返原剂 PK900的胶料硫化曲线平坦性好于添加1份抗硫化
返原剂PK900的胶料。
2. 2. 2 物理性能
小配合试验硫化胶的物理性能如表3所示。
由 于 试 验 采 用 普 通 硫 黄 硫 化 体 系,因 此 硫 化
褐色片状 80
0. 001 0. 12
褐色片状 80~90 ≤0. 003 ≤0. 50
注:1)生产企业指标。
从表1可以看出,抗硫化返原剂PK900的理化
性能符合指标要求。
2. 2 小配合试验
2. 2. 1 硫化特性
小配合试验胶料的硫化特性如表2所示。小
配合试验胶料的硫化曲线如图1所示。
从 表 2 和 图 1 可 以 看 出,与 未 添 加 抗 硫 化 返 原
小配合试验胶料在布拉本德密炼机中进行塑 炼、混炼,在开炼机上下片。混炼工艺为:NR塑炼 胶(停 放8 h)/SBR→ 小 料、炭 黑 和 软 化 剂 → 下 片 (停放4 h)→硫黄和促进剂→下片。
大 配 合 试 验 胶 料 采 用 两 段 混 炼 工 艺,均 在 GK90E型 密 炼 机 中 进 行。 一 段 混 炼 转 子 转 速 为 40 r·min-1,混炼工艺为:NR塑炼胶/SBR和小料 (40 s)→炭黑和软化剂(30 s)→压压砣(30 s)→ 提压砣→排胶(160 ℃)。二段混炼转子转速为20 r·min-1,混 炼 工 艺 为:一 段 混 炼 胶 → 硫 黄 和 促 进 剂→压压砣(40 s)→提压砣(40 s)→排胶(110 ℃
航空子午线轮胎胎侧胶配方的优化设计

航空子午线轮胎胎侧胶配方的优化设计吴洪全,黄义钢,常爱修,臧云红(青岛双星轮胎工业有限公司,山东青岛266400)摘要:对航空子午线轮胎胎侧胶配方进行优化设计。
试验结果表明:胎侧胶优选配方为天然橡胶 65,顺丁橡胶 35,炭黑N375 50,增粘树脂Koresin 2,防老剂 5.5,不溶性硫黄 1.8,促进剂TBBS 0.8,其他 8.7;与生产配方胶料相比,试验配方胶料的门尼焦烧时间延长,加工安全性和抗硫化返原性能提高,硫化胶的密度减小,拉伸强度、拉断伸长率和撕裂强度增大,耐低温和耐屈挠性能提高;成品轮胎的导电性能达到相关标准要求。
关键词:航空子午线轮胎;胎侧胶;物理性能;耐低温性能;耐屈挠性能;导电性能中图分类号:U463.341+.6 文章编号:1006-8171(2023)03-0172-05文献标志码:A DOI:10.12135/j.issn.1006-8171.2023.03.0172我国具有世界上发展很快、潜力巨大的航空市场。
据测算,2016—2035年的20年间,我国飞机保有量将由8 001架增加到34 264架,航空轮胎市场规模也相应的将由38.66亿元提高到97.76亿元,市场潜力巨大。
作为全球轮胎产销大国,我国的高端航空轮胎市场却被米其林、普利司通、固特异等国际巨头占据了95%的份额,处于绝对垄断地位[1-3]。
国内航空轮胎生产处于“卡脖子”状态。
纵观国内航空轮胎发展史,从原沈阳第三橡胶厂研制出第1批航空斜交轮胎开始,起步晚、起点低,可生产航空轮胎的厂家少,技术相对落后。
如今,航空轮胎正进入子午化扩张期,又适逢我国航空轮胎发展迎来政策利好期,多家国企、民企轮胎厂开始参与航空轮胎的研制,在注重传统航空斜交轮胎和航空子午线轮胎研发的同时,布局研发新一代航空子午线轮胎技术和产品,是追赶国际巨头、缩小差距的绝好机遇[1]。
我公司正在使用的航空轮胎胎侧胶因耐高低温性能及耐屈挠性能较差,已不能满足航空子午线轮胎的相关要求。
抗硫化返原剂在子午线轮胎胎圈护胶中的应用
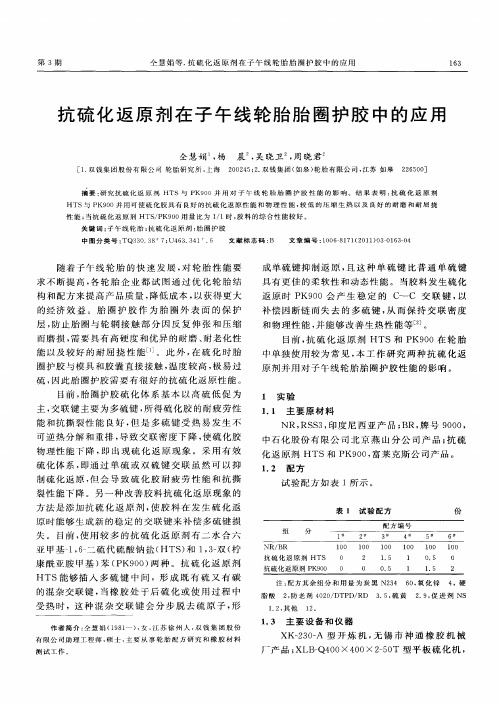
NR, S , 度 尼 西 亚 产 品 ; R, 号 9 0 , RS 3 印 B 牌 0 0
可 逆热 分解 和重 排 , 导致 交联 密度 下 降 , 使硫 化 胶
物 理 性 能 下 降 , 出 现 硫 化 返 原 现 象 。 采 用 有 效 即
中石化 股 份有 限公 司北 京 燕 山分 公 司 产 品 ; 硫 抗
关键 词 : 午 线 轮 胎 ; 硫 化 返 原 剂 ; 圈护 胶 子 抗 胎
中 图分 类 号 : TQ3 0 3 7 U4 3 3 1 . 3 . 8 ; 6 .4 6 文 献 标 志 码 : B 文章 编 号 : 0 68 7 ( 0 1 0 1 30 1 0 — i 1 2 1 ) 30 6 — 4
摘 要 : 究 抗 硫 化 返 原 剂 HT 与 P 0 研 S K9 0并 用 对 子 午 线 轮 胎 胎 圈 护 胶 性 能 的 影 响 。结 果 表 明 : 硫 化 返 原 剂 抗
HTS与 P 0 K9 0并 用 可 使 硫 化 胶具 有 良好 的 抗 硫 化 返 原 性 能 和 物 理 性 能 , 低 的 压 缩 生 热 以 及 良好 的 耐 磨 和 耐 屈 挠 较 性能 ; 当抗 硫化 返 原 剂 HTS P 0 / K9 0用 量 比为 1 l时 , 料 的 综 合性 能 较好 。 / 胶
补偿 因断 链 而失 去 的 多 硫键 , 而 保 持交 联 密 度 从 和物 理性 能 , 能 够改 善生 热性 能等 I 。 并 2 ]
目前 , 硫 化 返 原 剂 HT 抗 S和 P 0 K9 0在 轮 胎
中单 独使 用较 为 常见 , 工 作研 究 两种 抗 硫 化 返 本
原剂 并用 对子 午线 轮胎 胎 圈护胶 性能 的影 响 。
橡胶内胎的硫化工艺与优化策略
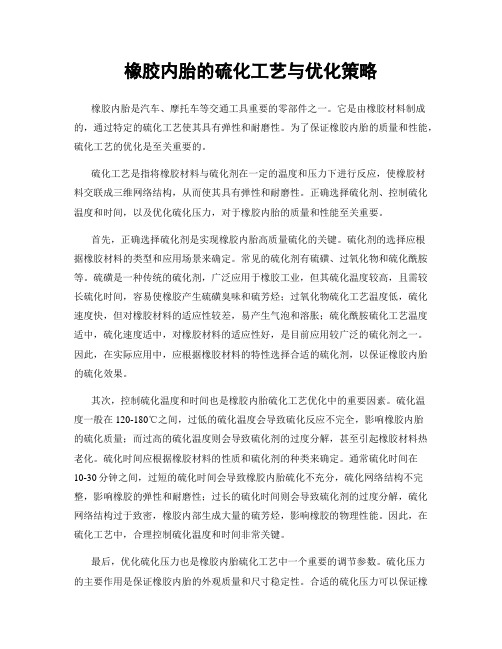
橡胶内胎的硫化工艺与优化策略橡胶内胎是汽车、摩托车等交通工具重要的零部件之一。
它是由橡胶材料制成的,通过特定的硫化工艺使其具有弹性和耐磨性。
为了保证橡胶内胎的质量和性能,硫化工艺的优化是至关重要的。
硫化工艺是指将橡胶材料与硫化剂在一定的温度和压力下进行反应,使橡胶材料交联成三维网络结构,从而使其具有弹性和耐磨性。
正确选择硫化剂、控制硫化温度和时间,以及优化硫化压力,对于橡胶内胎的质量和性能至关重要。
首先,正确选择硫化剂是实现橡胶内胎高质量硫化的关键。
硫化剂的选择应根据橡胶材料的类型和应用场景来确定。
常见的硫化剂有硫磺、过氧化物和硫化酰胺等。
硫磺是一种传统的硫化剂,广泛应用于橡胶工业,但其硫化温度较高,且需较长硫化时间,容易使橡胶产生硫磺臭味和硫芳烃;过氧化物硫化工艺温度低,硫化速度快,但对橡胶材料的适应性较差,易产生气泡和溶胀;硫化酰胺硫化工艺温度适中,硫化速度适中,对橡胶材料的适应性好,是目前应用较广泛的硫化剂之一。
因此,在实际应用中,应根据橡胶材料的特性选择合适的硫化剂,以保证橡胶内胎的硫化效果。
其次,控制硫化温度和时间也是橡胶内胎硫化工艺优化中的重要因素。
硫化温度一般在120-180℃之间,过低的硫化温度会导致硫化反应不完全,影响橡胶内胎的硫化质量;而过高的硫化温度则会导致硫化剂的过度分解,甚至引起橡胶材料热老化。
硫化时间应根据橡胶材料的性质和硫化剂的种类来确定。
通常硫化时间在10-30分钟之间,过短的硫化时间会导致橡胶内胎硫化不充分,硫化网络结构不完整,影响橡胶的弹性和耐磨性;过长的硫化时间则会导致硫化剂的过度分解,硫化网络结构过于致密,橡胶内部生成大量的硫芳烃,影响橡胶的物理性能。
因此,在硫化工艺中,合理控制硫化温度和时间非常关键。
最后,优化硫化压力也是橡胶内胎硫化工艺中一个重要的调节参数。
硫化压力的主要作用是保证橡胶内胎的外观质量和尺寸稳定性。
合适的硫化压力可以保证橡胶内胎的硫化过程中不产生气泡和缺陷,同时也可以使橡胶内胎的尺寸稳定,避免硫化过程中的变形。
使用抗硫化返原剂重新设计越野轮胎胶料来降低生热并改善性能

料制 备复 合 圆柱 ( 7 4 5 x6 mm) 。制 备 质 量 大约 为
20 0 g的 复 合 圆 柱 , 一 种 胶 料 的 质 量 均 为 大 约 每
5g 0 。通 过下 面 的顺 序沿 纵 向轴 辊 压胶 料 来 制 备
圆柱 :) 丝贴 胶胶 料 ;) 体 胶料 ;) 面底 胶 ; 1钢 2胎 3胎
来 优 化配 方 。
星
口
最后 , 单个 胶 料 的生 热 特 性 与 较 大 复合 物 部
件进 行 了对 比。
辑
3 试 验
B 一 X 和 HTS Du aik HTS 为 工 业 级 , C1M ( rl n )
由 Fe s s 国 I lx y 美 P公 司提供 。
4 。在 生热 试 验 过 程 中 使 用 温 度 记 录 仪 测 量 复 h 合试 样 的表面 温度 。使用 F R长 波红 外光 照 相 I I
机 通 过 T emoGu r h r ad进 行 成 像 和 分 析 。
3 0
橡 胶 参 考 资 料
21 0 0钲
4结 果
根 据 AS TM 6 3标 准使 用 Dol 挠仪 测 D-2 l屈 试 每个 D l试样 的生 热 。在 D l屈 挠 仪 上测 试 oi oi 体胶料 的代 表性结 果如 图 4所示 。
2 8
橡 胶 参 考 资 料
21 0 0正
使 甩 抗 硫 化 返 原 剂 重 新 设 计 越 野 轮 胎 胶 料 来 降低 生 热 并 改 善 性 能
刘 英梅 王晓霞 杜 娟 (吉林石化 公 司研 究 院高分子 合成研究 所 , 吉林 1 2 2 ) 编译 3 0 2
抗硫化返原剂ZD5在工程机械轮胎胎面胶中的应用
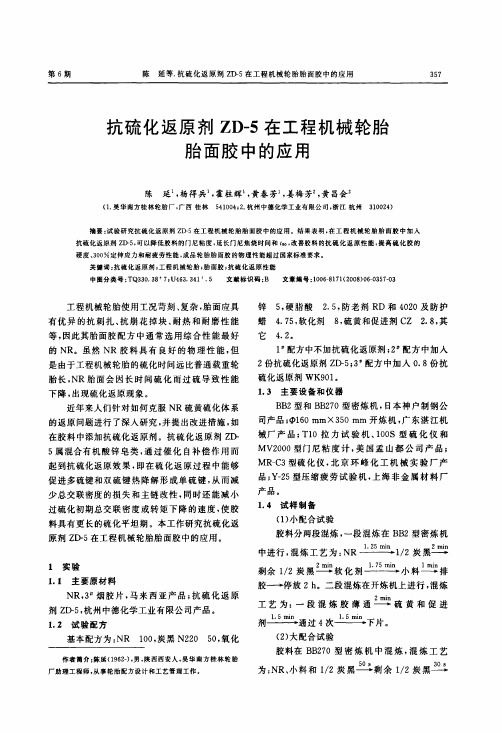
抗硫化返原剂ZD-5在工程机械轮胎胎面胶中的应用作者:陈延, 杨得兵, 霍柱辉, 黄春芳, 姜梅芳, 黄昌会作者单位:陈延,杨得兵,霍柱辉,黄春芳(昊华南方桂林轮胎厂,广西,桂林,541004), 姜梅芳,黄昌会(杭州中德化学工业有限公司,浙江,杭州,310024)刊名:轮胎工业英文刊名:TIRE INDUSTRY年,卷(期):2008,28(6)被引用次数:0次相似文献(3条)1.期刊论文李文东.路天庆.陈朋.张辉利.赵平.LI Wen-dong.LU Tian-qing.CHEN Peng.ZHANG Hui-li.ZHAO Ping 抗硫化返原剂在载重子午线轮胎中的应用研究-轮胎工业2007,27(5)研究抗硫化返原剂对胶料性能的影响,通过对比抗硫化返原剂Z500和PK900在各种硫化体系中的作用,寻求提高载重子午线轮胎胶料热稳定性的方法.结果表明,添加抗硫化返原剂胶料硫化特性变化不明显;硫化返原速度,特别是过硫后的硫化返原速度大大降低;硫化胶物理性能及其过硫后保持率提高,生热降低;抗硫化返原剂Z500更适合全钢载重子午线轮胎和工程机械轮胎的硫化条件,而PK900则更适用于高温或长时间过硫化的场合或与其它抗硫化返原剂并用.2.期刊论文高孝恒.GAO Xiao-heng提高工程机械轮胎翻新胎面胶质量的探讨-轮胎工业2005,25(8)概述国内外工程机械轮胎翻新胎面胶的生产情况及胶种和配合剂对翻新胎面质量的影响以及各类工程机械轮胎胎面胶配方主要原材料的选择原则,提出提高工程机械轮胎翻新胎面胶质量的措施:胶种以NR为主,可并用BR或SBR;采用抗硫化返原剂提高胎面耐磨性和抗崩花掉块性,并防止动态性能下降;采用改性酚醛树脂提高胎面胶的硬度、定伸应力和耐磨性.3.期刊论文吴明生.赵树高.WU Ming-sheng.ZHAO Shu-gao提高工程机械轮胎抗硫化返原性的措施-橡胶工业2005,52(7)分析橡胶的耐热性、胶料硫化返原的机理及影响因素,讨论提高工程机械轮胎抗硫化返原性的措施.指出选择合适的硫化体系、添加抗硫化返原剂、降低胶料生热、并用耐热胶种、调整轮胎不同部位胶料硫化速度的匹配性等,以及利用计算机数值模拟的方法确定合适硫化条件是提高工程机械轮胎抗硫化返原性的有效措施.本文链接:/Periodical_ltgy200806010.aspx授权使用:航天化学研究院(航天42所)(ht42s),授权号:11d4e570-f5e5-473b-bb71-9e920096f905下载时间:2011年2月22日。
天然橡胶胶料抗硫化返原性能的研究

第46卷 第19期·50·CHINA RUBBER/PLASTICS TECHNOLOGY AND EQUIPMENT (RUBBER)橡塑技术与装备(橡胶)作者简介:尹婷(1986-),女,工程师,本科,主要从事橡胶配方设计及应用工作。
收稿日期:2020-03-31厚制品在硫化过程中,由于硫化温度过高、时间过长进而产生硫化胶交联网出现裂解,发生硫化返原现象,继而导致硫化胶料的性能降低。
为了解决这一问题,保证厚制品不因为硫化时间长,里层的橡胶未硫化完全,外围的橡胶因为过硫而致使胶料性能下降,所以要提高胶料的抗硫化返原性能。
天然橡胶是一种弹性和力学性能优良的通用橡胶,被广泛应用于各个行业。
故选用天然橡胶作为此次研究的主胶料。
在天然橡胶的硫化中,由于其中含有大量顺式-1,4加成不饱和结构,使用硫磺硫化体系很容易发生硫化返原现象,严重影响了产品的性能[1],也因此限制了天然橡胶的应用,尤其是厚制品方面的应用。
故这里选用了几种不同的硫化体系另分别加入抗返原剂对天然橡胶的硫化胶抗硫化返原性能进行了试验对比,具有一定的现实意义和指导意义。
1 试验1.1 主要原材料NR :国产云南农垦云象牌天然胶SCR WF ;炭黑:金能科技股份有限公司;氧化锌、硬脂酸、防老剂、硫磺、促进剂、增塑剂、抗硫化返原剂均为市售工业级产品。
其中对硫化促进剂及抗返原剂的选用如下:CZ -次磺酰胺类促进剂,焦烧时间长,硫化速度快,硫化曲线平坦,适用于高温快速硫化及厚制品硫天然橡胶胶料抗硫化返原性能的研究尹婷1,尹莉2,孙建帮1,石臣刚1,张亚生1(1.衡橡科技股份有限公司,河北 衡水 053000;2.西安西电电工材料有限责任公司,陕西 西安 710082)摘要:研究了不同的硫化体系对天然橡胶胶料的抗硫化返原性能的影响。
结果表明,使用含硫少或不含硫的半有效或有效硫化体系,可以提高胶料的有效交联密度,提高胶料的抗返原性能,使厚制品在长时间硫化后的胶料的性能更优,减少了制品的损坏率,降低了生产成本,提高了产能。
半钢子午胎胎体帘布胶配方优化
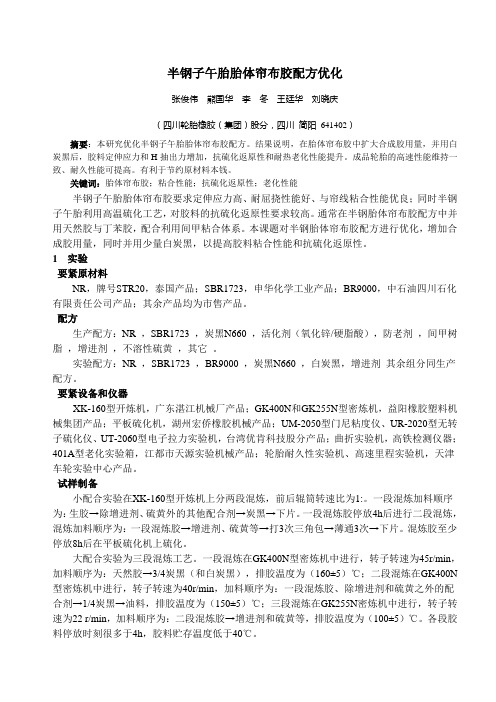
半钢子午胎胎体帘布胶配方优化张俊伟熊国华李冬王廷华刘晓庆(四川轮胎橡胶(集团)股分,四川简阳641402)摘要:本研究优化半钢子午胎胎体帘布胶配方。
结果说明,在胎体帘布胶中扩大合成胶用量,并用白炭黑后,胶料定伸应力和H抽出力增加,抗硫化返原性和耐热老化性能提升。
成品轮胎的高速性能维持一致、耐久性能可提高。
有利于节约原材料本钱。
关键词:胎体帘布胶;粘合性能;抗硫化返原性;老化性能半钢子午胎胎体帘布胶要求定伸应力高、耐屈挠性能好、与帘线粘合性能优良;同时半钢子午胎利用高温硫化工艺,对胶料的抗硫化返原性要求较高。
通常在半钢胎体帘布胶配方中并用天然胶与丁苯胶,配合利用间甲粘合体系。
本课题对半钢胎体帘布胶配方进行优化,增加合成胶用量,同时并用少量白炭黑,以提高胶料粘合性能和抗硫化返原性。
1 实验要紧原材料NR,牌号STR20,泰国产品;SBR1723,申华化学工业产品;BR9000,中石油四川石化有限责任公司产品;其余产品均为市售产品。
配方生产配方:NR ,SBR1723 ,炭黑N660 ,活化剂(氧化锌/硬脂酸),防老剂,间甲树脂,增进剂,不溶性硫黄,其它。
实验配方:NR ,SBR1723 ,BR9000 ,炭黑N660 ,白炭黑,增进剂其余组分同生产配方。
要紧设备和仪器XK-160型开炼机,广东湛江机械厂产品;GK400N和GK255N型密炼机,益阳橡胶塑料机械集团产品;平板硫化机,湖州宏侨橡胶机械产品;UM-2050型门尼粘度仪、UR-2020型无转子硫化仪、UT-2060型电子拉力实验机,台湾优肯科技股分产品;曲折实验机,高铁检测仪器;401A型老化实验箱,江都市天源实验机械产品;轮胎耐久性实验机、高速里程实验机,天津车轮实验中心产品。
试样制备小配合实验在XK-160型开炼机上分两段混炼,前后辊筒转速比为1:。
一段混炼加料顺序为:生胶→除增进剂、硫黄外的其他配合剂→炭黑→下片。
一段混炼胶停放4h后进行二段混炼,混炼加料顺序为:一段混炼胶→增进剂、硫黄等→打3次三角包→薄通3次→下片。
抗硫化返原剂ZD-5在工程机械轮胎胎面胶中的应用
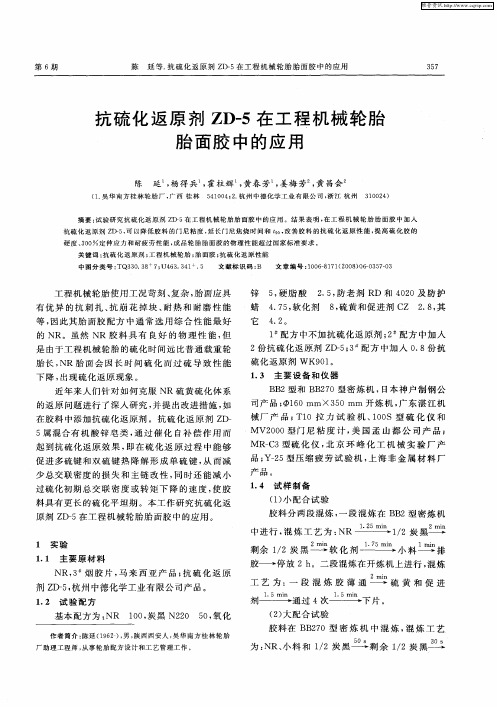
锌
5 硬脂 酸 2 5 防老 剂 R 和 4 2 , ., D 0 0及 防护
蜡
47, . 5 软化剂
8 硫黄 和促 进剂 C 2 8 其 , Z .,
它 4 2 .。
1 配方 中不 加抗 硫化 返原 剂 ; 配方 中加入 2 2份抗 硫 化返 原剂 Z 5 3 D- ; 配方 中加 入 0 8 抗 . 份 硫 化返 原剂 W Kg 1 0。 1 3 主要 设备 和仪 器 .
维普资讯
第 6 期
陈
延 等 . 硫 化 返 原 剂 Z 5 工 程 机 械 轮胎 胎 面 胶 中 的 应 用 抗 D- 在
37 5
抗硫化返原剂 Z - D 5在 工 程 机 械 轮 胎 胎 面 胶 中 的 应 用
陈 延 杨 得兵 霍柱辉 黄春 芳 姜梅 芳 黄 昌会 , , , , ,
停放 2h 。二段 混炼 在开 炼机 上进行 , 炼 混
NR, 烟胶 片 , 来 西 亚 产 品 ; 硫 化 返 原 3 马 抗
工 艺 为 : 段 混 炼 胶 薄 通 — i 黄 和 促 进 一 Z n硫 — m 剂 通 过 4次 立
() 2 大配合 试 验
剂 Z 一, 州 中德化学 工 业有 限公 司产 品 。 D 5杭
(. 华南方桂林轮胎厂 , 西 桂林 1吴 广 5 1 0 ;. 州 中德 化 学 工 业 有 限 公 司 , 江 杭 州 4042杭 浙 302) 1 0 4
摘 要 : 验研 究抗 硫 化返 原 剂 Z - 工 程 机 械 轮 胎 胎 面 胶 中 的 应 用 。结 果 表 明 , 工 程 机 械 轮 胎 胎 面 胶 中 加 入 试 D 5在 在
抗硫化返原剂KA9188在绿色载重轮胎中的应用
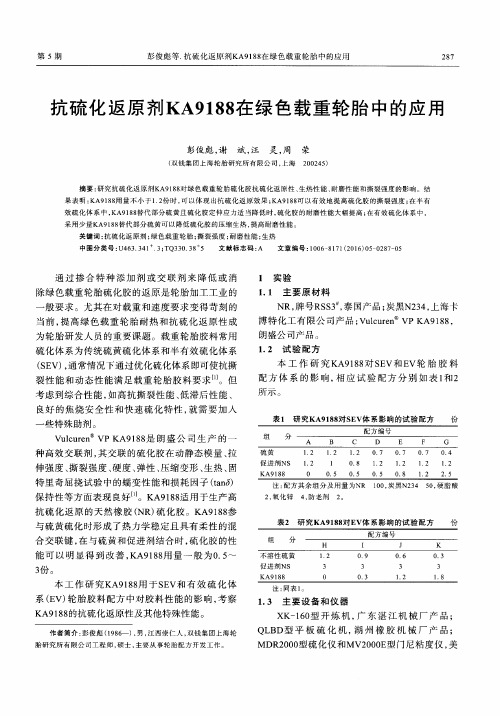
注 :配 方 其 余 组 分 及 用量 为 NR 100,炭 黑N234 50,硬脂 酸 2,氧 化 锌 4,防老 剂 2。
表 2 研 究KA9188对 EV体 系影 响 的试 验配 方 份
注 :同 表 1。
1.3 主要 设备 和仪 器 XK一160型 开 炼 机 ,广 东 湛 江 机 械 厂 产 品 ;
关键 词 :抗硫 化 返 原 剂 ;绿 色载 重 轮 胎 ;撕 裂 强 度 ;耐磨 性 能 ;生 热 中 图分 类 号 :U463.341 .3;TQ330.38 5 文献 标 志 码 :A 文章 编 号 :1006—8171(2016)05—0287—05
通 过 掺合 特 种 添 加 剂 或 交 联 剂 来 降 低 或 消 除绿 色 载重 轮胎 硫化胶 的返原是 轮 胎加工 工业 的 一 般 要 求 。尤 其 在对 载重 和速度 要 求变得 苛 刻 的 当前 ,提 高 绿 色载 重 轮胎 耐 热 和抗 硫 化 返 原性 成 为 轮胎 研发 人员 的重 要课 题 。载重 轮胎胶 料 常用 硫化 体 系为传 统硫 黄硫 化体 系 和半有 效硫 化体 系 (SEV),通 常情况 下通过优化 硫化体 系 即可使 抗撕 裂性 能 和 动态 性 能满 足 载重 轮 胎胶 料 要 求…。但 考虑 到综 合性 能 ,如高 抗撕 裂性 能 、低滞后 性 能 、 良好 的焦 烧 安全 性 和 快 速硫 化 特性 ,就需 要 加 入 一 些 特 殊 助 剂 。
1 实 验 1.1 主 要 原 材 料
NR,牌 号RSS3 ,泰 国产品 ;炭黑N234,上海卡 博特 化工 有 限公 司产 品 ;Vulcuren VP KA9188, 朗盛公 司产品 。 1.2 试 验 配方
影响硫化橡胶回弹性的因素及解决方案
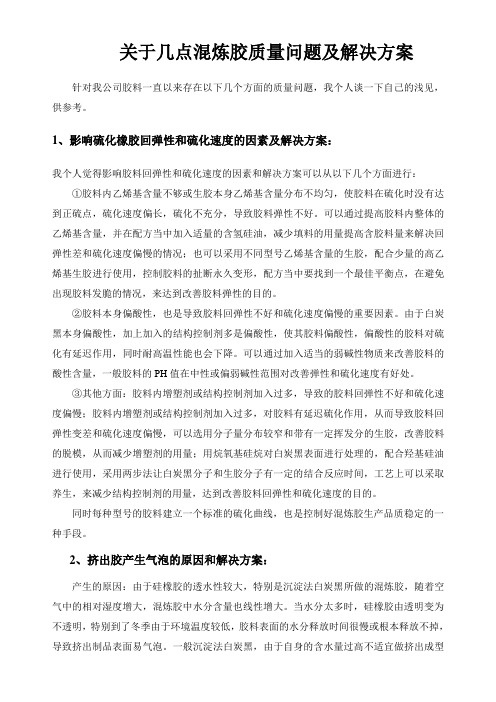
关于几点混炼胶质量问题及解决方案针对我公司胶料一直以来存在以下几个方面的质量问题,我个人谈一下自己的浅见,供参考。
1、影响硫化橡胶回弹性和硫化速度的因素及解决方案:我个人觉得影响胶料回弹性和硫化速度的因素和解决方案可以从以下几个方面进行:①胶料内乙烯基含量不够或生胶本身乙烯基含量分布不均匀,使胶料在硫化时没有达到正硫点,硫化速度偏长,硫化不充分,导致胶料弹性不好。
可以通过提高胶料内整体的乙烯基含量,并在配方当中加入适量的含氢硅油,减少填料的用量提高含胶料量来解决回弹性差和硫化速度偏慢的情况;也可以采用不同型号乙烯基含量的生胶,配合少量的高乙烯基生胶进行使用,控制胶料的扯断永久变形,配方当中要找到一个最佳平衡点,在避免出现胶料发脆的情况,来达到改善胶料弹性的目的。
②胶料本身偏酸性,也是导致胶料回弹性不好和硫化速度偏慢的重要因素。
由于白炭黑本身偏酸性,加上加入的结构控制剂多是偏酸性,使其胶料偏酸性,偏酸性的胶料对硫化有延迟作用,同时耐高温性能也会下降。
可以通过加入适当的弱碱性物质来改善胶料的酸性含量,一般胶料的PH值在中性或偏弱碱性范围对改善弹性和硫化速度有好处。
③其他方面:胶料内增塑剂或结构控制剂加入过多,导致的胶料回弹性不好和硫化速度偏慢;胶料内增塑剂或结构控制剂加入过多,对胶料有延迟硫化作用,从而导致胶料回弹性变差和硫化速度偏慢,可以选用分子量分布较窄和带有一定挥发分的生胶,改善胶料的脱模,从而减少增塑剂的用量;用烷氧基硅烷对白炭黑表面进行处理的,配合羟基硅油进行使用,采用两步法让白炭黑分子和生胶分子有一定的结合反应时间,工艺上可以采取养生,来减少结构控制剂的用量,达到改善胶料回弹性和硫化速度的目的。
同时每种型号的胶料建立一个标准的硫化曲线,也是控制好混炼胶生产品质稳定的一种手段。
2、挤出胶产生气泡的原因和解决方案:产生的原因:由于硅橡胶的透水性较大,特别是沉淀法白炭黑所做的混炼胶,随着空气中的相对湿度增大,混炼胶中水分含量也线性增大。
抗硫化返原剂在载重子午线轮胎中的应用研究
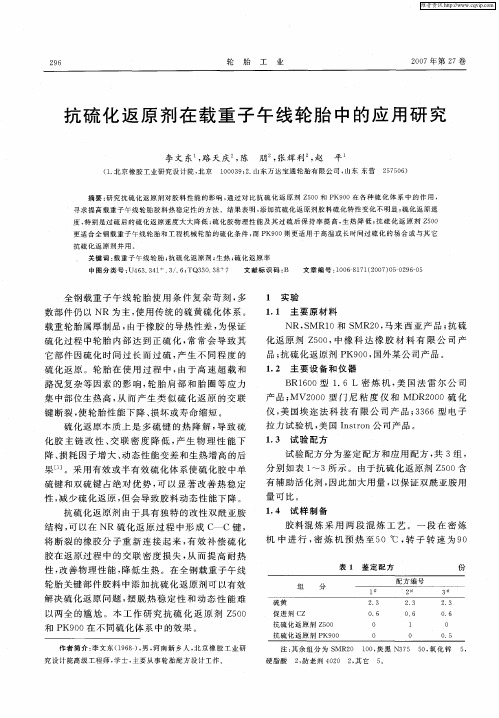
第5 期
李文东等 . 抗硫化返原荆在载重子午线轮胎中的应用研究
表 2 应 用试 验 配 方 I
性 , 少硫 化返 原 , 会 导致 胶料 动态 性能 下 降 。 减 但 抗硫 化返 原剂 由于具有 独特 的改 性双 酰亚 胺 结构 , 以在 NR硫 化返 原 过 程 中形 成 C C键 , 可 ~
试 验配方 分 为鉴定 配方 和应 用 配方 , 3 , 共 组 分 别 如表 1 ~3所示 。 由于抗 硫化 返原 剂 Z 0 5 0含 有 辅助 活化剂 , 因此加 大用 量 , 以保证 双酰 亚胺用
量可比。
1 4 试 样 制 备 .
胶 料混 炼 采 用 两 段 混 炼 工 艺 。一 段 在 密 炼 机 中进 行 , 炼 机 预 热 至 5 密 0℃ , 子 转 速 为 9 转 0
表 1 鉴 定 配 方 份
将 断裂 的橡胶 分 子 重新 连 接起 来 , 效 补 偿 硫 化 有 胶在 返原 过程 中 的交联 密度 损 失 , 而提 高 耐 热 从 性, 改善物 理性 能 , 降低 生热 。在全钢 载重 子午 线
维普资讯
26 9
轮
胎
工
业
20 0 7年 第 2 卷 7
抗 硫 化 返 原 剂 在 载 重 子 午线 轮 胎 中的应 用研 究
李 文 东 路 天庆。 陈 朋。 张辉 利。赵 平 , , , ,
(. 京 橡 胶 工业 研 究 设 计 院 , 京 1 0 3 ;. 东 万 达 宝 通 轮 胎 有 限公 司 , 东 东 营 2 7 0 ) 1北 北 0092山 山 5 5 6
硫化 返原 本质 上 是 多 硫 键 的热 降 解 , 致 硫 导
B 6 0型 1 6L密 炼 机 , 国法 雷 尔公 司 R1 0 . 美 产品; MV2 0 0 0型 门尼 粘 度 仪 和 MD 0 0硫 化 R2 0
硫化历程对轮胎胶料微观结构和性能的影响
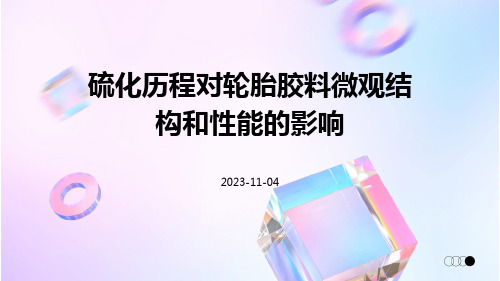
硫化时间
硫化反应需要一定的时间才能 完成,随着时间的推移,交联 反应逐渐进行,橡胶材料逐渐
获得所需的性能。
硫化温度
硫化温度对硫化反应的速度和 交联键的类型和数量有显著的 影响。高温可以加速硫化反应 ,但过高的温度可能导致橡胶
材料的老化和性能下降。
硫化压力
在轮胎制造过程中,通常会在 高温高压下进行硫化。高压可 以促进硫化剂与橡胶分子的反 应,提高交联密度,从而提高
物理性能的变化
1 2 3
交联密度
随着硫化程度的增加,轮胎胶料的交联密度增 加,分子间结合力增强,材料的硬度随之增加 。
弹性模量
硫化历程对轮胎胶料的弹性模量具有显著影响 。随着硫化时间的延长,轮胎胶料的弹性模量 逐渐增大。
热稳定性
硫化历程对轮胎胶料热稳定性有一定影响。随 着硫化时间的延长,轮胎胶料的热稳定性有所 提高。
02
轮胎胶料硫化历程的基本 原理
硫化历程的化学反应
硫化反应
橡胶分子与硫化剂(通常是硫磺)反应,生成交联的橡胶网 络。这个反应是可逆的,随着温度的升高,硫化反应会加速 。
交联反应
橡胶分子之间通过硫化剂形成的交联键,使橡胶材料具有弹 性。交联键的类型和数量对橡胶材料的性能有很大的影响。
硫化历程中的重要参数
机械性能的变化
拉伸性能
随着硫化程度的增加,轮胎胶料的拉伸强度和拉伸伸长 率呈现先增加后减小的趋势。在一定范围内,硫化时间 的延长有助于提高轮胎胶料的拉伸性能。
撕裂性能
硫化历程对轮胎胶料的撕裂性能具有重要影响。随着硫 化时间的延长,轮胎胶料的撕裂强度逐渐增大。
磨耗性能
硫化历程对轮胎胶料的磨耗性能也有一定影响。在一定 范围内,适当延长硫化时间可以降低轮胎胶料的磨耗量 。
轮胎硫化工艺条件的优化
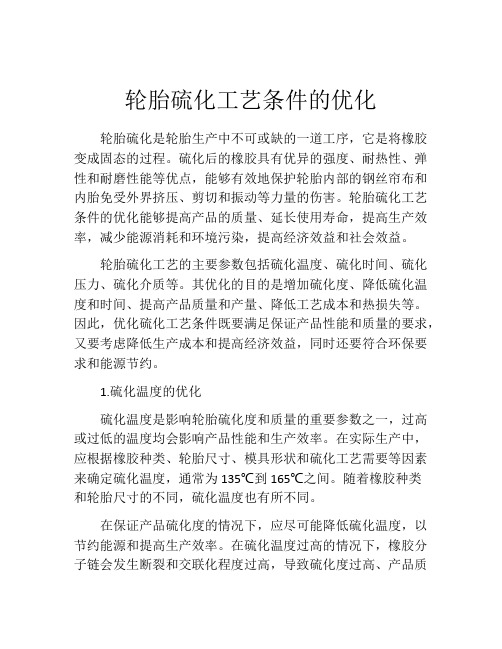
轮胎硫化工艺条件的优化轮胎硫化是轮胎生产中不可或缺的一道工序,它是将橡胶变成固态的过程。
硫化后的橡胶具有优异的强度、耐热性、弹性和耐磨性能等优点,能够有效地保护轮胎内部的钢丝帘布和内胎免受外界挤压、剪切和振动等力量的伤害。
轮胎硫化工艺条件的优化能够提高产品的质量、延长使用寿命,提高生产效率,减少能源消耗和环境污染,提高经济效益和社会效益。
轮胎硫化工艺的主要参数包括硫化温度、硫化时间、硫化压力、硫化介质等。
其优化的目的是增加硫化度、降低硫化温度和时间、提高产品质量和产量、降低工艺成本和热损失等。
因此,优化硫化工艺条件既要满足保证产品性能和质量的要求,又要考虑降低生产成本和提高经济效益,同时还要符合环保要求和能源节约。
1.硫化温度的优化硫化温度是影响轮胎硫化度和质量的重要参数之一,过高或过低的温度均会影响产品性能和生产效率。
在实际生产中,应根据橡胶种类、轮胎尺寸、模具形状和硫化工艺需要等因素来确定硫化温度,通常为135℃到165℃之间。
随着橡胶种类和轮胎尺寸的不同,硫化温度也有所不同。
在保证产品硫化度的情况下,应尽可能降低硫化温度,以节约能源和提高生产效率。
在硫化温度过高的情况下,橡胶分子链会发生断裂和交联化程度过高,导致硫化度过高、产品质量下降、能源浪费和环境污染等问题;而在硫化温度过低的情况下,硫化度不足、产品质量差、生产效率低等问题也会出现。
因此,在优化硫化温度时,需要综合考虑橡胶种类、轮胎尺寸、模具形状、硫化时间和压力等多种因素,根据实际情况来确定最佳硫化温度,以平衡硫化度、产品性能和生产效率三者之间的关系。
2.硫化压力的优化硫化压力是影响轮胎硫化度和质量的另一个重要参数,它直接影响轮胎的形状和几何尺寸。
在实际生产中,硫化压力与硫化温度、时间和介质等参数一起控制,以保证产品硫化度和合格率。
在优化硫化压力时,需要考虑橡胶种类、轮胎尺寸、模具形状、压力区域等因素。
一般来说,硫化压力应该高于橡胶的流动点压力,以避免橡胶在硫化过程中发生形变和变形。
轮胎硫化工艺条件的优化
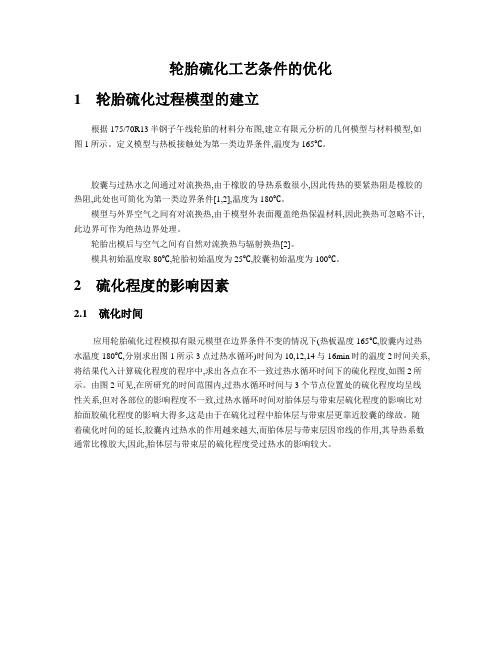
轮胎硫化工艺条件的优化1轮胎硫化过程模型的建立根据175/70R13半钢子午线轮胎的材料分布图,建立有限元分析的几何模型与材料模型,如图1所示。
定义模型与热板接触处为第一类边界条件,温度为165℃。
胶囊与过热水之间通过对流换热,由于橡胶的导热系数很小,因此传热的要紧热阻是橡胶的热阻,此处也可简化为第一类边界条件[1,2],温度为180℃。
模型与外界空气之间有对流换热,由于模型外表面覆盖绝热保温材料,因此换热可忽略不计,此边界可作为绝热边界处理。
轮胎出模后与空气之间有自然对流换热与辐射换热[2]。
模具初始温度取80℃,轮胎初始温度为25℃,胶囊初始温度为100℃。
2硫化程度的影响因素2.1硫化时间应用轮胎硫化过程模拟有限元模型在边界条件不变的情况下(热板温度165℃,胶囊内过热水温度180℃,分别求出图1所示3点过热水循环)时间为10,12,14与16min时的温度2时间关系,将结果代入计算硫化程度的程序中,求出各点在不一致过热水循环时间下的硫化程度,如图2所示。
由图2可见,在所研究的时间范围内,过热水循环时间与3个节点位置处的硫化程度均呈线性关系,但对各部位的影响程度不一致,过热水循环时间对胎体层与带束层硫化程度的影响比对胎面胶硫化程度的影响大得多,这是由于在硫化过程中胎体层与带束层更靠近胶囊的缘故。
随着硫化时间的延长,胶囊内过热水的作用越来越大,而胎体层与带束层因帘线的作用,其导热系数通常比橡胶大,因此,胎体层与带束层的硫化程度受过热水的影响较大。
表1示出了不一致过热水循环时间下相关于165℃时的等效硫化时间。
从表1能够看出,过热水循环时间每增加1min,胎体层、带束层与胎面胶相应的等效硫化时间分别延长约2.1,2.0与1.2min。
2.2蒸汽温度在硫化时间与过热水温度不变的情况下(过热水循环9min,过热水温度180℃,分别求出)蒸汽外温从155℃上升到175℃时的温度场,由所得温度场计算出相应的硫化程度。
- 1、下载文档前请自行甄别文档内容的完整性,平台不提供额外的编辑、内容补充、找答案等附加服务。
- 2、"仅部分预览"的文档,不可在线预览部分如存在完整性等问题,可反馈申请退款(可完整预览的文档不适用该条件!)。
- 3、如文档侵犯您的权益,请联系客服反馈,我们会尽快为您处理(人工客服工作时间:9:00-18:30)。
17. 4 14. 8
136
34
16
30
注 :基本配方 :SMR CV 100 ,炭黑 N330 50 ,氧化锌 510 ,硬脂酸 2. 0 ,芳烃油 510 ,防老剂 6PPD 210 。
在现有配方中添加 1~3 份 H TS 可以使 抗返原和其它物理性能得到一定改善 ,而要 获得最佳使用性能则须优化整个硫化体系 。
项 目
对比
硫黄用量/ 份
2. 5
促进剂 NS 用量/ 份
0. 6
HTS 用量/ 份
0
硫化返原 (181 ℃
×60 min) / %
35
300 %定伸应力/ MPa
144 ℃×t 90 181 ℃×t 90
14. 5 10. 1
疲劳寿命 (100 %拉伸) / kc
老化前
189
100 ℃×48 h 老
在过去几年中 ,惠利实公司推出了 2 种 新橡胶助剂 :甲基马来酰亚胺基甲基苯 (BCI2 MX) 和六亚甲基21 ,62双2硫代硫酸二钠二水 合物 ( H TS) 。与现有技术相比 ,这两种助剂 为改善硫黄硫化胶耐热老化性能提供了两种
表 1 SEV和 CV硫化体系比较
项 目
SEV
拉伸强度
=
定伸应力
1 结果与讨论 111 SEV
前面已经说过 ,当硫黄/ 促进剂硫化胶料 在生产过程或产品使用过程中暴露于过硫化 或处于高温条件下时 ,就会发生交联结构的 热降解 ,致使交联程度和交联键的性质发生 剧烈变化 。正如所预料的那样 ,硫化胶结构 上的这些变化转变为硫化胶物理性能和使用 性能下降 。这些影响的一个例子见表 2 。从 表 2 可见 ,即使采用提高热稳定性的 SEV 硫 化体系 ,胶料的性能也发生重大变化 。 112 BCI2MX
113 HTS
HTS 独特的化学结构使其能直接参与
硫化反应而生成杂交联键 。这种杂交联键在
聚合物主链的硫链上嵌入柔性六亚甲基 (见
图 2) 。
控制与聚合物主链相连的硫链长度可以
改善这种交联键的热稳定性 。交联键结构中
嵌入较长的柔软且具热稳定性的烷基可改善
胶料在动态操作条件下的屈挠性 。在现有的
硫化体系中添加 H TS 可直接改善胶料的抗
实验已经证明 ,BCI2MX 因其独特的化 学结构遵循典型的荻尔斯2阿德尔反应 (见图 1) 机理与返原过程中沿聚合物主链生成的二 烯/ 三烯反应 ,生成一种新的热稳定且长而柔 软的碳2碳交联键 ,以补偿返原造成的硫化交 联的损失 。
这种补偿反应不仅可在热降解发生时保 持交联键密度 ,进而保证胶料物理性能 ,而且 生成新的不易进一步变化且具有屈挠性和热 稳定性的交联键 。除了这种补偿作用外 ,共 轭二烯/ 三烯单元浓度的降低将对硫化胶的 诸如弹性 、拉伸强度 、抗疲劳性及抗热老化和 氧化老化等很多性能产生有利的影响 。
配方编号
1
2
3
4
33 10 20 5 31 10 19 5
15. 4 12. 4 11. 7
15. 3 14. 5 14. 6
15. 4 13. 7 11. 4
15. 4 16. 1 16. 2
100 125 130 110 90 90 110 110 90 80 95 105
BO 33 52 26 BO 30 60 27 BO 26 66 25
改善各种使用性能的起点配合列于表 6 。
表 6 HTS 配合指南
份
组分
硫黄 促进剂 硬脂酸 HTS
过硫 2. 2 1. 6 2. 7 1. 8
性能改善
高温硫化 低 HBU
1. 0
1. 3
2. 3
1. 1
0. 7
2. 4
1. 6
3. 0
通用 1. 1 1. 0 1. 6 2. 8
反应 ,而 BCI2MX 只是在出现返原时才开始 起作用 。如果两者并用 ,则可能会产生令人 感兴趣的结果 。因此做了下面的研究试验 。
原性能见表 8 。从表 8 数据清楚地看出 ,配
方 中加入BCI2MX可获得良好的抗爆破性
2 BCI2MX/ HTS 并用 显然 ,上述讨论中 BCI2MX 和 H TS 尽管
作用机理不同 ,但都能改善胶料的抗硫化返 原性 ,并且都能不同程度地提高使用性能 。
前面已经指出 ,H TS 在硫化过程中参与
6
15. 2 14. 6
160 150
30 26
12 42
5. 20 5. 12
注 : 配方 : SMR CV 100 , 炭黑 N330 50 , 氧化锌 510 ,硬脂酸 210 ,芳烃油 310 ,防老剂 6PPD 210 ,促进 剂 CBS 0. 6 ,硫黄 2. 5 ,加工助剂 Perkalink 900 110 。
胶料配方见表 7 。
表 7 试验配方
份
原材料
促进剂 NS 硫黄 BCI2MX HTS
配方编号
1
2
3
4
0. 6
0. 6
0. 6
0. 6
2. 4
2. 4
2. 4
2. 4
0
1. 0
0
1. 0
0
0
2. 0
1. 0
注 :基本配方 :SMR10 100 ,炭黑 N375 52 ,氧化锌 3. 5 ,硬脂酸 2. 0 ,芳烃油 4. 5 ,防老剂 TMQ 1. 5 ,防老 剂 6PPD 1. 0 ,石蜡 1. 0 ,防焦剂 PV I 0. 35 。
9
15. 5 13. 5
130 90
27 37
14 10
5. 11 4. 80
注 : 配方 : SMR CV 100 , 炭黑 N330 50 , 氧化锌 510 ,硬脂酸 210 ,芳烃油 310 ,防老剂 6PPD 210 ,促进 剂 CBS 1. 4 ,硫黄 114 。
表 3 BCI2MX( 1. 0 份) 对 CV硫化体系胶料 物理性能和使用性能的影响
=
扯断伸长率
-
屈挠寿命
-
撕裂强度
-
热稳定性
+
滞后损失
-
氧化稳定性
+
生热
+
注 : + 表示改进 。
CV
+/ = = + + + + -
不同的方法 。两种方法各有其独特的功能和 作用机理 ,每一种都不同程度地改善了胶料 的性能 。本文通过 H TS 和 BCI2MX 与 CV 和 SEV 硫化体系的比较 ,说明这两种方法对 解决轮胎胶料硫化返原问题所具有的潜在的 优点 。
返原性并提高胶料的性能 ,而通过优化硫黄/
62 0 轮 胎 工 业 1998 年第 18 卷
图 2 HTS 的杂交联机理
促进剂/ HTS 的比例可获得最佳使用性能 。 H TS 的优越性能的一例见表 5 。
表 5 HTS 对抗返原性的改进
当硫化胶在生产过程中过硫化或在使用 过程中暴露于厌氧热老化条件下时 ,硫黄硫 化胶料会发生硫化返原 。
多年来 ,轮胎行业已趋向采用较多促进 剂 (或使用硫给予体) 和较少硫黄以更有效地 利用所添加的硫黄 ,以较少硫原子形成交联 来获取较高的热稳定性 。我们把半有效硫化 体系 ( SEV) 与常规硫化体系 ( CV) 进行了比 较 (见表 1) ,所产生的各种折衷效果在开发 新配方时必须加以考虑 。
图 3 示出了 150 ℃下胶料的硫化特性 。 正如所预料的 ,BCI2MX 对工艺特性只有很 小甚至几乎没有什么影响 ,而 H TS 对硫化确
有影响 (硫化效率和焦烧时间都受到影响) 。
这个问题可以通过优化整个硫化体系加以克
服 。然而 BCI2MX 和 H TS 并用的硫化仪曲
线要好得多 (见图 3 中的 4 号胶料曲线) 。 BCI2MX , H TS 及其并用的胶料的抗返
性 能
数据
硫化返原 (150 ℃×60 min) / % 300 %定伸应力/ MPa 150 ℃×t 90 150 ℃×60 min 疲劳寿命 (应变能 ≠3. 5 ×103 kJ ·m - 3) / kc 150 ℃×t 90 150 ℃×60 min 生热 (100 ℃) / ℃ 150 ℃×t 90 150 ℃×60 min 爆破时间 (100 ℃) / min 150 ℃×t 90 150 ℃×60 min 交联密度[ (2Mc ,chem) - 1 ×105g·mmol/ RH] 150 ℃×t 90 150 ℃×60 min
将典型的 SEV 硫化体系 (表 2) 和采用 BCI2MX 的 CV 硫化体系进行比较 (表 3) ,显 然后者不仅保持了 CV 硫化体系的特性 ,而 且由于采用了 BCI2MX ,胶料的热稳定性和 滞后损失同时得到改善 。
BCI2MX 的用量须根据硫化返原的程度
表 4 BCI2MX的配合指南
胶 种
化后
37
生热[ 100 ℃,144 ℃×( t 90 +
5 min) ]/ ℃
20
爆破时间[ 100 ℃,144 ℃×( t 90 +
5 min) ]/ min
17
对比 + D2HTS
2. 5 0. 4 2. 0
23
15. 2 13. 3
251
51
24
17
优化 D2 HTS 体系
1. 5 1曲线确定)
进行优选 。表 4 列出了各种硫化体系 (包括
聚合物类型) 的起点推荐用量 。
图 1 荻尔斯2阿德尔反应
入配方中而又不影响胶料工艺特性的少数几 种橡胶助剂之一 ,因为它不直接参与硫化反 应 ,而只是在出现返原迹象时才发生作用 。 返原过程中由 BCI2MX 形成的热稳定交联键 对胶料物理性能的保持及如降低生热和提高 耐爆破性等使用性能的改进作用很大 (见表 3) 。