准序化供货模式下的混装线重排序
5G考试题库

网上大学5G题库1、()属于5GC的基本功能模块答案:ABC A、AMF B、SMF C、UPFD、RFS2、“满足商用要求”网管指标有答案:ABCD A、1)接入类B、2)保持类C、3)移动性D、4)运维类3、360度全景VR直播演示方案中需要以下哪个设备答案:ABCD A、1)5GNR B、2)360全景摄像头C、3)显示屏D、4)TUE4、3GPP R16 5G语音业务会支持哪些技术?答案:ABD A、EPSFBB、VoNRC、CSFBD、SRVCC5、4/5G链路预算的主要差异答案:ACD A、1)最大带宽不同B、2)所处频段不同C、3)基站天线端口数不同D、4)终端天线端口数不同6、4G双锚点方案需要考虑的因素有?答案:CD A、4GRRU容量评估B、CPRI接口光模块容量评估C、到核心网路由的互联互通D、基站IP 地址是否新增7、5GNR版本包包含哪些版本文件答案:BC A、产品tar文件B、产品平台版本包C、基础包pkg文件D、RRU版本包8、5GNR覆盖能力提升主要依靠:答案:ABC A、MassiveMIMO B、终端能力加强C、大带宽D、30k的子载波间隔9、5GNR可以采用哪些方式来增强上行覆盖()答案:BC A、增加SDL频段B、载波聚合C、增加SUL频段D、以上均可10、5GNR目前支持的BWP带宽包括()答案:BD A、30MHz B、60MHz C、70MHz D、100MHz11、5GQcellR8139F1821T35机型的哪些通道支持5G?答案:AB A、7&8B、5&6C、3&4D、1&212、5GQCell安装时,PB与pRRU之间可以使用哪些物理介质连接?答案:ABC A、光电复合缆缆B、CAT6A网线C、CAT6网线D、CAT5E网线13、5GTUE支持的下行流数是答案:ABCD A、3 B、1 C、4 D、214、5GSA组网方式下BBU使用单板有答案:ABDE A、vPD B、vFC C、vbpc1 D、vBPc5 E、VSWc215、5G大容量保障启动前,为提高效率且保证保障顺利进行,哪些准备工作需要外场提前完成?答案:ABCD A、站点建设或改造B、单站基础性能优化C、覆盖摸底测试D、大话务参数部署16、5G大容量保障时,PM实时查询的粒度为?答案:BCD A、1s B、10sC、30sD、1分钟17、5G大容量保障时,档位分为几档?答案:BD A、20UE B、50UE C、100UE D、200UE18、5G大容量保障时,高话务档位参数按照哪些维度进行分类?答案:BCD A、1)站型B、2)带宽C、3)档位D、4)帧结构19、5G大容量保障时,高话务档位参数按照那些维度进行分类?答案:BCD A、站型B、带宽C、档位D、帧结构20、5G大容量保障时,基线参数按照哪些维度进行分类?答案:BCDA、档位B、站型C、带宽D、帧结构21、5G大容量保障时,使用的用户容量档位有哪几档?答案:ACA、200UEB、100UEC、50UED、20UE22、5G单验前,需要提前准备的工具有哪列?答案:ABCD A、带倾角功能的罗盘 B、数字万用表 C、测试笔记本 D、电子地图23、5G单验时,BBU侧验收包括哪些项?答案:ABCD A、机柜测硬件布放顺序 B、BBU单板安装验收C、光纤安装验收D、GPS安装验收24、5G单验时,站点状态核查包括哪些项目?答案:ABCD A、告警确认B、单板运行状态检查C、时钟状态检查D、小区状态检查25、5G的三大业务场景包括()答案:ABC A、URLLC B、eMMBC、mMTCD、BOB26、5G的上行物理信号包括()答案:ACD A、DM-RS B、CSI-RSC、PT-RSD、SRS27、5G定义的三个应用场景()答案:ACD A、eMBB B、eMTCC、mMTCD、uRLLC28、5G定义哪几种RRC状态答案:ABC A、RRC_CONNECTED B、RRC_IDLE C、RRC_INACTIVE D、RRC_ACTIVE29、5G独立组网的优势有答案:ABCD A、对现有2G/3G/4G网络无影响B、不影响现网2G/3G/4G用户C、可快速部署,直接引入5G新网元,不需要对现网改造D、引入5GC,提供5G新功能新业务30、5G规范定义了哪三种业务场景答案:BCD A、NB-IOT B、eMBBC、mMTCD、uRLLC31、5G核心网SMF的功能包括答案:BC A、移动性管理 B、IP地址分配C、会话管理与计费D、外部网关管理32、5G基础覆盖优化可通过哪些手段调整()答案:ABCD A、下倾角B、方位角C、pssSssPwr功率配置D、站高33、5G商用BBU—V9200交换板VSW的主要功能是:答案:BCD A、处理3GPP规定的物理层协议和帧协议B、控制管理基带单元C、提供传输接口D、提供系统时钟34、5G商用ITBBU—V9200的安装方式为答案:ABCD A、1)19英寸机柜安装B、2)挂墙安装 C、3)室外一体化机柜安装D、4)龙门架安装35、5G时隙类型中,上行自包含类型里存在()信道答案:ABCD A、PDCCH B、GP C、SRS D、PUSCH36、5G实验局组网总体原则下面哪些正确?答案:ABD A、先宏站后室分B、优先采用低频C、优先采用NSA D、CU/DU建议合设37、5G实验网阶段测试工作所需工具主要包含()答案:ACDE A、LMTB、TEMSC、DSPMonitorD、CRTE、CXT/CXA38、5G使用的主要编码方式是()答案:AC A、Polar B、TurboC、LDPCD、FMO39、5G试验网阶段测试优化工作所需工具主要包含答案:ABCDE A、LMT,B、罗德扫频仪,C、DSPMonitor,D、CRT,E、CXT40、5G室分的关键技术包括答案:ABCD A、1)超密组网 B、2)虚拟nTnR C、3)动态虚拟小区D、4)MEC增值服务方案41、5G室分建设的特征的数字化指答案:ABC A、网络结构数字化,B、运维数字化,C、业务数字化,D、建设数字化42、5G网管自定义方式配置权值时,涉及的参数包括答案:ABCD A、子波束索引B、水平及垂直波瓣宽度C、方位角D、下倾角43、5G网络建议使用4TRPAD或高频小站的用处是:答案:ABC A、热点覆盖 B、补盲覆盖C、建设难度大成本高解决方案 D、价格便宜44、5G小微站产品都有哪些类型答案:AB A、PAD B、iMacro C、Nanocell D、Qcell E、DAS45、5G站点开通,帧结构类型一般配置为答案:AD A、5ms单周期B、2.5ms单周期C、5ms双周期D、2.5ms双周期46、5G支持的参考信号有哪些答案:ABD A、SRS B、CSI-RS C、CRSD、DMRS47、5G支持的参考信号有哪些?答案:ABD A、DMRS B、SRS C、CRSD、CSI-RS48、5G支持的子载波间隔有()答案:ABCD A、15K B、30K C、60KD、120K49、5G智能网络规划需要依托的4G现网数据包括:答案:ABCD A、4G 网络数据统计B、4GMR数据C、4G现网站点数据库D、电子地图50、5NNR版本包包含那些版本文件?答案:AC A、产品tar文件B、平台版本包C、基础包pkg文件D、RRU版本包51、64TR产品推荐应用于以下哪些场景:答案:AB A、密集城区B、一般城区C、郊区D、农村52、8槽位VBPc5单板的三个MCS片的地址分别是答案:ACE A、192.254.8.16 B、192.254.8.32 C、192.254.8.48 D、192.254.8.64E、192.254.8.8053、A9611可以使用哪种电源线供电答案:CD A、2*4mm2 B、2*6mm2C、2*10mm2D、2*16mm254、A9631A有哪几款户外直流电源线缆规格可选?答案:BCD A、2*4mm2B、2*6mm2C、2*10mm2D、2*16mm255、AAPC现网当前的版本配置为SP03版本,下列哪些配置可能导致AAPC 的失败?答案:ABCD A、同一个任务内协同小区间缺少Xn配置B、协同小区间未配置邻区关系C、服务小区的初始权值的配置值未在权值库中 D、协同小区的初始权值配置值未在权值库中56、AAPC支持多种波束组合的权值寻优,支持下列哪几种波束个数组合的寻优。
生产排程 正排和倒排

请各位先看一个PPT做的例子,然后就容易理解为什么说“倒排”是ERP的第
一个误区。
三个订单案例
订单号
1
设备1
3天
设备2
2天
设备3
1天
组装
2天
接到订单时间
05/01
交货期
05/06
2
3
1天
4天
4天
2天
3天
4天
2天
2天
05/02
ERP的四个半误区
先要说明,标题不是十分准确。应该是生产现场管理的误区。但是应对小批 量多品种混线生产管理,ERP已经严重误导了用户,但是仍然把它们作为ERP优势 特征,在此就只好先把误区放在ERP的头上说了。这四个半误区是:倒排、最短 生产周期、安全库存、均衡生产以及可视化看板(半个)。
误区之一:倒排
地忙起来最重要。其他的裁纸机、装订机都不在话下,不会耽误事儿的。订单不
足,怎么排也要停机停工;订单充足,怎么排也有延期交货的。 在某些特定领域,采用倒排也是非常好的方式。比如,主部件正排,子部件
倒排。这样可以降低子部件在现场的堆放时间。前提是,生产子部件的资源能力
比较宽裕。
二、从PPT看到,倒排浪费了产能。为什么呢?这是因为在整个可以排产 的资源可用的时间片,由于倒排从中间插入强制占用,使得资源时间片被切成 零碎的,其他订单无法再利用这些资源。倒排造成优化资源的障碍,资源白白 浪费。从PPT看到,同样的订单,倒排需要增加一倍的产能才能做到和正排同 样的准时交货,产能浪费50%。演示的PPT仅仅是极其简单的例子,实际中, 生产现场极其复杂,正排的浪费都不能容忍,何况“倒排”呢。 三、大多数ERP应付排产都已经很艰难了,已经很粗了,还不要说其中增 加了很多“缓冲”。实话实说,ERP非要在属于“大系统”、“复杂系统”范 畴的小批量、多品种、混线生产的生产管理插足,实在是坏了“一世英名”。 更不能理解的是,把“专线生产”还凑合应用的“倒排”,搬到离散型制造业, 并且给它们加上“拉动式”生产模式和“JIT”这样美好的名词,真的是严重 误导了用户。 通常,对于企业来说,最重要的就是两点:准时交货和产能最大化。不明 白有哪些以订单为驱动的企业敢用“倒排”而不留缓冲。万一该交货的那天停 电怎么办?如果预留缓冲,“拉动式”还有什么意义?如果为了“倒排”,实 现“准时生产”,白白浪费了大量产能,这是哪一个企业能容忍的愚蠢行为?
SPS模式下零部件配送质量的混流装配线总装排序

Abs t r a c t :A r e s e a r c h i s c o n d uc t e d o n t ቤተ መጻሕፍቲ ባይዱ e o p t i mi z a t i o n o f t he i n p u t s e q u e n e e s i n mi x e d- mo d e l a s s e mb l y
Ke y wo r d s :s e q u e n c i n g mi x e d - mo d e l a s s e mb l y l i n e s ;d i s t r i b u t i o n b a s e d o n s e t p a r t s u p p l y;g e n e t i c a l g o —
中图分类号 : F 2 7 3 文献标 志码 : A 文章编号 : 1 0 0 7 - 7 3 7 5 ( 2 0 1 3 ) 0 2 — 0 l 1 2 . O 5
Re s e a r c h o n Se q ue n c i ng Mi x e d- Mo de l As s e mb l y Li n e s
为 目的 , 分析拣选环节筐 车排列顺序对零件拣选错配 和漏 配的影 响 , 从两方面 探讨通过安排 筐车排列顺 序以最小化 拣选 错配和漏配率 ; 同时在总装环节 , 追求零部件消耗速率均衡化。从而建立 同时考虑 总装 和零部件 配送 两 阶段优 化的混流装配线排序模型 。结合排序案例 , 证 明该排 序模 型能在平 准化 零部 件消耗的同时提高配送 质量 。 关键 词 : 混流装配排序 ;S P S物料 配送 ; 遗传算法
供应链管理中生产和运输集成的排序问题

2 c o l f a h ma isa d S se S in e h n a g No ma ie s y h n a g 1 0 3 , h n ; .S h o t e t n y t m e c ,S e y n r lUn v r i ,S e y n 0 0 5 C i a o M c c t
s o n t s u o p ln m ilc mp e iy h wig isp e d — o y o a o lx t .
Ke r s s p l h i y wo d : u p y c an;s h d l g y a i p o r m m ig c e u i ;d n m c r g a n n
维普资讯
I uta E g er g n ngm n N . ,07 n s i n i ei d d rl n n a Maae et o520
工业工程与管理
20 年第 5 07 期
文章 编号 :0 75 2 (0 7 0 —0 70 1 0 —4 9 2 0 )50 4 —4
o jci ,tu h rbe o nmi n h otl ot ss le .F rh r r , h o rso d bet e h step o l v m f mii z gt e l s i ov d u temo e tec rep n — i t ac
i g d n mi r g a n y a c p o r mm i g m e h d i r s n e .Th l o i m a e n p o e o b f iin y n t o s p e e t d e a g rt h h s b e r v d t e e f e tb c
JIT生产方式混流生产线投产排序研究论文

JIT生产方式混流生产线投产排序研究论文本文旨在探讨JIT生产方式混流生产线的投产排序问题。
投产排序是指在投产前对不同产品的生产顺序进行安排,以最大限度地提高生产效率。
在传统生产线中,通常是按照产品的生产数量和交付期限进行安排,然而在混流生产线上,由于产品种类多样,生产过程相对复杂,传统的投产排序方法已经不能满足需求。
首先,本文将通过文献综述的方式对JIT生产方式混流生产线的投产排序问题进行梳理和总结,分析已有研究的优缺点和不足之处。
其次,本文将提出一种基于优先级排序的投产排序方法,通过建立数学模型,考虑产品的交货期、生产时间和生产成本等因素,以确定最优的投产顺序,以提高混流生产线的生产效率和资源利用率。
最后,本文将通过实例分析的方式,验证提出的投产排序方法的有效性和实用性,通过对比不同的排序策略,得出最佳的投产排序方案,为企业的生产决策提供参考依据。
综上所述,本文旨在通过对JIT生产方式混流生产线投产排序问题的研究,为企业提供一种有效的生产管理方法,以满足市场需求,提高竞争力,促进企业的可持续发展。
JIT (Just In Time)生产方式是一种以订单为中心的生产模式,它旨在通过减少库存和浪费,提高生产效率和响应速度,从而降低生产成本,提高企业竞争力。
而混流生产线则是一种将多种不同产品在同一条生产线上加工生产的方式,通过优化生产资源的使用,降低生产成本和提高产能。
JIT生产方式混流生产线的投产排序问题在这样的生产环境中显得尤为重要。
本文所提出的基于优先级排序的投产排序方法将会针对混流生产线的特点进行排序,将会综合考虑产品的交货期、生产时间、生产成本以及工艺布局等因素,以确定最优的投产顺序,以提高整体生产线的生产效率和资源利用率。
这种基于优先级排序的方法将会为企业提供一种更加有效的生产管理手段,以适应市场需求的变化,提高企业的生产效率,降低成本,增强企业的竞争力。
在进行混流生产线的投产排序问题的研究过程中,我们首先需要对目前已有的相关研究进行深入的文献综述和总结。
【精益生产】汽车企业的JIT采购(二)顺序供货

汽车企业的JIT采购(二)顺序供货精益管理顾问 宋文强 (原创)库存的主要作用之一就是起到缓冲和防断档的作用。
这个防断档所需要的库存就叫安全库存。
安全库存与采购周期有关。
一般来讲,采购周期越长,就越需要被更多的安全库存。
比如:如果采购周期是4小时,即下了采购订单后,4个小时能到货,那需要备8个小时的安全库存(只是假设);那么如果采购到货周期是两天,那可能需要备两三天的安全库存;如果是越洋采购,采购到货周期是一个月,那可能需要备至少半个月的安全库存。
总之,采购到货周期与安全库存呈正相关关系。
那么有没有可能将采购到货周期降低到一个小时甚至更短呢?这样就可以接近零库存了。
在汽车行业,有一种方法来实现这这零库存采购方式,就是通过供应商顺序供货方式直接上总装线进行装配。
顺序供货是指有些零部件在整车厂和总装生产线不设零部件仓库,这些一级供应商按照总装线车辆下线顺序排列零部件的装载顺序,直接送到总装线上进行组装生产。
这些物料的体积一般较大,并且有些部品的颜色或规格根据生产计划而变化,包括:座椅、轮胎、油箱、玻璃、发动机等。
采用顺序供货直接上线方式有这么几个前提和要求:第一,运输距离短,供货周期短,供货周期要小于装配周期装配周期就是:从整车装配顺序确定点开始,到开始装配该零部件的这个时间长度。
所以,顺序供货直接上线的物料供应商一般在汽车整车厂的附近,供货距离在8公里之内甚至一两公里。
这样把装车时间、路途中的运输时间、卸车时间、车间上线时间等尽可能缩短。
这样才可能同步上线。
那么,能不能更早一点地确定总装顺序呢?大多数情况下可以,其实在周生产计划中就已经确定了总装顺序,但只是在喷涂结束后才能真正确定。
汽车总装的前道工序是喷涂,喷涂生产线下线的车辆顺序与组装生产线上线的车辆顺序有差异。
汽车组装是需要按照品种均衡的原则制定出最佳顺序,但是总装的前工序喷涂,他们的油漆颜色更换起来有些麻烦,所以,喷涂有自己的最佳顺序。
喷涂完成后,要重新排队。
IPQA工作优先排序
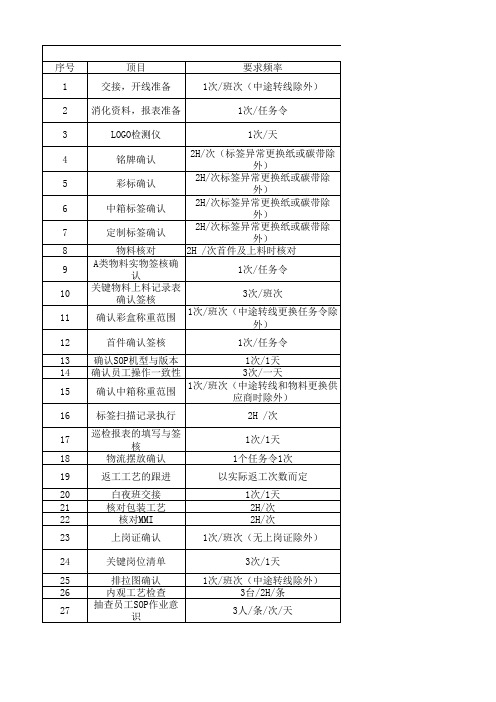
跟线IPQC
跟进返工是否按流程进行(主要是QA否机/客户 否机返工)
跟线IPQC
重大异常口头与文字的交接
跟线IPQC
核对排拉流程图中所有的包装工艺SOP内容 跟线IPQC
抽1位MMI工位测试人员
跟线IPQC
所有产线岗位人员变动,关键岗位(测试、焊 接、标签打印)人员
跟线IPQC
确认关键岗位名单与实际操作一致,有培训考 核上岗记录
跟线IPQC
确认所有工序
跟线IPQC
整机内观检查
跟线IPQC
重点关键岗位
跟线IPQC
稽查产线所有的电批与烙铁参数是否在文件范 围内
跟线IPQC
关键岗位(测试.焊接.标签打印)人员 拉体所有打印机、自动化设备、仪器 拉体所有打印机、自动化设备、仪器
拉体所有设备、仪器
跟线IPQC 跟线IPQC 跟线IPQC 跟线IPQC
序号 1
顶目 交接,开线准备
要求频率 1次/班次(中途转线除外)
IPQC稽查 项目表
2 消化资料,报表准备
1次/任务令
3
LOGO检测仪
1次/天
4
铭牌确认
2H/次(标签异常更换纸或碳带除 外)
5
彩标确认
2H/次标签异常更换纸或碳带除 外)
6
中箱标签确认
2H/次标签异常更换纸或碳带除 外)
7
定制标签确认
跟线IPQC
依据最新《电池风险稽查表》,2次一周专项稽 查,每天随时稽查
跟线IPQC
依据最新《IMEI号风险稽查表》,2次一周专项 稽查,每天随时稽查
跟线IPQC
依据最新《维修系统代码使用checklist》 跟线IPQC
自动化立体仓库的货物排序与存取效率

自动化立体仓库的货物排序与存取效率在当今快节奏的商业环境中,高效的物流和仓储管理对于企业的竞争力至关重要。
自动化立体仓库作为现代仓储技术的代表,凭借其高度自动化和空间利用率高的特点,正逐渐成为众多企业的首选。
而在自动化立体仓库中,货物的排序和存取效率直接影响着整个仓库的运行效率和经济效益。
自动化立体仓库是一种利用高层货架存储货物,通过自动化设备进行存取操作的仓库系统。
它通常由货架、堆垛机、输送机、控制系统等组成。
在这样的仓库中,货物的排序不再是简单的堆放,而是需要根据一系列的规则和策略进行优化,以提高存取效率。
货物排序的重要性不言而喻。
合理的货物排序可以减少货物的查找时间,提高堆垛机的运行效率,降低仓库的运营成本。
例如,如果将经常一起出库的货物放在相邻的位置,那么在出库时就可以一次性完成多个货物的拣选,大大提高了出库效率。
那么,如何进行货物排序呢?一种常见的方法是根据货物的出入库频率进行排序。
出入库频率高的货物被放置在容易存取的位置,比如靠近仓库出入口或者堆垛机运行路线较短的位置。
这样,在需要存取这些货物时,可以减少堆垛机的运行时间和距离,提高作业效率。
另一种货物排序的方法是根据货物的相关性进行排序。
比如,同一种产品的不同规格或者不同批次的货物可以放在相邻的位置,方便管理和拣选。
此外,还可以根据货物的重量、体积、价值等因素进行排序。
重量较大的货物放在货架底层,体积较大的货物放在空间较大的位置,价值较高的货物则需要采取更加安全和便捷的存储方式。
除了货物排序,存取策略也对自动化立体仓库的效率有着重要影响。
常见的存取策略包括先进先出(FIFO)、后进先出(LIFO)和随机存取等。
先进先出策略适用于对保质期有要求的货物,确保先入库的货物先出库,避免货物过期浪费。
后进先出策略则适用于一些特殊的行业,比如钢铁行业,新生产的钢材往往质量更好,更受欢迎。
随机存取策略则适用于对货物出入库顺序没有严格要求的情况。
在实际的仓库管理中,往往会根据货物的特点和企业的需求,综合运用多种排序和存取策略。
生产型企业电商配送中心拣选方案设计及订单排序优化

2023-11-05
CATALOGUE
目录
引言生产型企业电商配送中心拣选方案设计订单排序优化策略案例分析研究结论与展望参考文献
CHAPTER
01
引言
研究背景和意义
随着电子商务的快速发展,越来越多的生产型企业涉足电商领域,配送中心拣选作业的效率和准确性成为制约其发展的关键因素之一。
传统的拣选方法往往存在着效率低下、错误率高等问题,无法满足现代物流的需求。
因此,研究一种高效、准确、灵活的拣选方案和订单排序优化策略,对于提高生产型企业电商配送中心的运营效率和客户满意度具有重要意义。
研究目的
本研究旨在设计一种基于人工智能算法的拣选方案和订单排序优化策略,提高配送中心拣选作业的效率和准确性,降低运营成本,提高客户满意度。
拣选方案设计概述
研究目的
02
通过对拣选方案的设计和分析,提高配送中心的工作效率,降低成本,提高客户满意度。
研究方法
03
采用文献综述、案例分析和实地调研等方法,对拣选方案的设计和优化进行深入研究。
拣选流程分析
拣选方案设计要素
考虑人员数量、技能水平、工作态度等因素,确保人员配备合理。
人员因素
设备因素
本研究主要关注了拣选方案设计和订单排序优化两个方面,未考虑配送中心的库存管理、路径规划等问题。未来研究可以综合考虑多种因素,提高配送中心的运营效率。
在实际生产环境中,生产型企业的订单具有多品种、小批量的特点,本研究提出的拣选策略还需进一步优化以适应更为复杂的情况。
研究不足与展望
CHAPTER
06
参考文献
常用订单排序算法
在生产型企业电商配送中心,常用的订单排序算法包括遗传算法、模拟退火算法、蚁群算法等。
供应商按顺序来检验物品的排序模板

供应商按顺序来检验物品的排序模板供应商按顺序来检验物品的排序模板在供应商与采购商之间的交易中,物品的质量是一个至关重要的因素。
为了确保所采购的物品符合质量要求,供应商需要进行物品的检验。
而为了提高效率和准确性,供应商可以采用按顺序来检验物品的排序模板。
首先,供应商可以根据物品的类别来制定排序模板。
不同类别的物品可能有不同的质量要求和检验方法,因此将物品按照类别进行排序,有助于提高检验效率。
比如,对于食品类物品,可以将其按照不同的食品类型进行分类,分别制定相应的检验流程。
其次,供应商可以根据物品的重要程度来制定排序模板。
对于一些关键的物品,供应商可以将其排在检验队列的前面,以确保其质量符合标准。
而对于一些次要的物品,可以将其排在后面,以便在确保重要物品质量合格之后再进行检验。
此外,供应商还可以根据物品的批次来制定排序模板。
不同批次的物品可能存在差异,因此将物品按照批次进行排序,有助于对不同批次的物品进行独立的检验。
这样能够更好地掌握每个批次物品的质量状况,及时发现和解决问题。
在按顺序来检验物品的过程中,供应商还需注意一些细节。
首先,要确保每个物品都得到充分的检验,不漏检也不误检。
其次,要逐项记录检验结果,以便及时追溯物品质量问题的根源。
最后,要保持检验的准确性和一致性,避免因个人主观因素而导致的结果偏差。
总之,按顺序来检验物品的排序模板是供应商提高物品质量管理效率和准确性的重要工具。
通过根据物品类别、重要程度和批次等因素来制定排序模板,可以有效提高检验效率,减少质量风险。
然而,供应商在使用排序模板的过程中仍需注意细节,确保检验工作的全面性和准确性,以满足采购商的质量要求。
基于订单的稳定混箱垛型供箱序列的生成系统及其方法
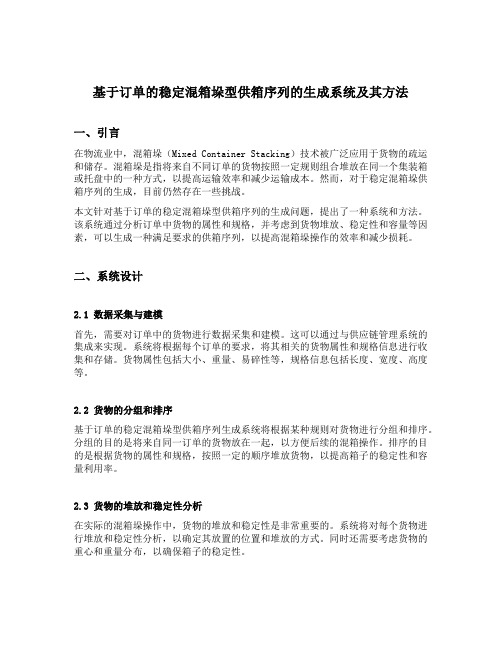
基于订单的稳定混箱垛型供箱序列的生成系统及其方法一、引言在物流业中,混箱垛(Mixed Container Stacking)技术被广泛应用于货物的疏运和储存。
混箱垛是指将来自不同订单的货物按照一定规则组合堆放在同一个集装箱或托盘中的一种方式,以提高运输效率和减少运输成本。
然而,对于稳定混箱垛供箱序列的生成,目前仍然存在一些挑战。
本文针对基于订单的稳定混箱垛型供箱序列的生成问题,提出了一种系统和方法。
该系统通过分析订单中货物的属性和规格,并考虑到货物堆放、稳定性和容量等因素,可以生成一种满足要求的供箱序列,以提高混箱垛操作的效率和减少损耗。
二、系统设计2.1 数据采集与建模首先,需要对订单中的货物进行数据采集和建模。
这可以通过与供应链管理系统的集成来实现。
系统将根据每个订单的要求,将其相关的货物属性和规格信息进行收集和存储。
货物属性包括大小、重量、易碎性等,规格信息包括长度、宽度、高度等。
2.2 货物的分组和排序基于订单的稳定混箱垛型供箱序列生成系统将根据某种规则对货物进行分组和排序。
分组的目的是将来自同一订单的货物放在一起,以方便后续的混箱操作。
排序的目的是根据货物的属性和规格,按照一定的顺序堆放货物,以提高箱子的稳定性和容量利用率。
2.3 货物的堆放和稳定性分析在实际的混箱垛操作中,货物的堆放和稳定性是非常重要的。
系统将对每个货物进行堆放和稳定性分析,以确定其放置的位置和堆放的方式。
同时还需要考虑货物的重心和重量分布,以确保箱子的稳定性。
2.4 箱子的选择和排布在进行混箱垛操作之前,需要选择合适的箱子,并确定它们的排布方式。
系统将根据货物的属性和规格,选择合适的箱子,并进行排布,以最大程度地减少空间浪费和货物损坏。
三、方法介绍3.1 货物分组和排序方法为了实现基于订单的稳定混箱垛型供箱序列的生成,系统采用了一种基于货物属性和规格的分组和排序方法。
具体步骤如下:1.将订单中的货物按照订单号进行分组;2.对于每个订单,根据货物的属性和规格进行排序,大货物优先;3.将不同订单的货物按照排序结果进行组合,形成混箱垛供箱序列。
混合装配线上物料供应的平准化排序

坚 最 霎皙 ‰ O0 . 6 唧 1 ^ 誊 耋 嚣 鐾 曩 善 : 罐摹 叠 翟 爱 ; 先 摸 术 进
“ t’ 理
维普资讯
l 6
系
统
工
程
20 0 2年
率保持 不变 . 这就是物料 的平准 化供 应问题 。因此 对原 材料 、 零部件 的供 应要求 适时适量 . 否则 . 准时制 系统将 陷
1 混合 型装 配 线
多 品种 混 台 生 产 是 准 时 化 (1 生 产 系 统 普遍 采 用 的 一 种 生 产 组 织 方 法 , 是 在 基 车 不 改 变 现 有 生 产 手 段 、 JT) 它 生
产 条 件 和 生 产 能力 的 前提 下 . 过 改 变 生 产 组 织方 法 , 同 一条 流 水 线 上 生 产 出批 量 小 、 种 多 的 系 列 产 品 。混 台 通 在 品 型装 配 线 能 够 适 应市 场 需 求 的 各 种 变 化 . 少 在 制 品 数 量 . 约 流动 资 金 、 低 成 本 、 最 短 的 时 间 里最 大 限 度 地 减 节 降 在 满足 不 同 消 费 者 的个 性 化 需 求 . 高 产 品 的 竞争 力 。混 台 装 配 线 的 一般 形 式 是 : 提
维普资讯
第 2 0卷 第 3 ( 第 1 1 ) 期 总 1期
20 0 2年 5月
系 统
工
程
V O . o. No 】2 .3
Ma y.. O 2O 2
S s e sEn ne rn y tm gi e i g
文 章 编 号 : 0 14 9 ( 0 2 0 — 0 5 0 10 —0 8 2 0 )30 1 5
( ) 个 计 划 期 Pr 内 . 同 一 条 生 产 线 上 生 产 种 规 格 的产 品 ; 1一 在
物料不齐套引起的混流装配线重排序问题

物料不齐套引起的混流装配线重排序问题刘琼;范正伟;张超勇;朱可人;刘炜琪;饶运清【摘要】针对混流装配线由于物料不齐套导致将要执行的生产排序性能恶化或不可行的问题,为保证从初始排序过渡到重排序时生产准备过程的稳定性,提出基于最小化排序偏差指标的混流装配线重排序模型.采用非支配遗传算法进行求解,为避免当前周期的能力剩余和下一周期能力不足等问题,保证生产线的整体排序性能和充分利用当前周期的装配能力,采用两周期联合优化策略和基于装配能力的分解策略.针对某空调混流装配线实例,采用所提方法求解物料不齐套引起的重排序,得到性能良好的非支配Pareto解集,并与企业现有的启发式规则的重排序结果进行比较,表明所提方法能够有效解决物料不齐套对装配线排序性能的影响.【期刊名称】《计算机集成制造系统》【年(卷),期】2014(020)007【总页数】7页(P1608-1614)【关键词】混流装配线;重排序;遗传算法;多目标优化【作者】刘琼;范正伟;张超勇;朱可人;刘炜琪;饶运清【作者单位】华中科技大学数字制造装备与技术国家重点实验室,湖北武汉430074;华中科技大学数字制造装备与技术国家重点实验室,湖北武汉430074;华中科技大学数字制造装备与技术国家重点实验室,湖北武汉430074;湖北工业大学机械工程学院,湖北武汉430068;华中科技大学数字制造装备与技术国家重点实验室,湖北武汉430074;湖北工业大学机械工程学院,湖北武汉430068;华中科技大学数字制造装备与技术国家重点实验室,湖北武汉430074【正文语种】中文【中图分类】TP3910 引言在企业生产实际中,装配过程中出现的物料不齐套往往是影响装配计划顺利执行的主要因素。
物料齐套性检查就是要求在装配工作开始前将所需零部件全部准备到位。
若产品在物料不齐套的情况下开始装配,则可能导致生产时间变长、在制品增加和生产能力下降[1]。
企业在面对物料不齐套的情况时,实际上往往通过停线来处理,或采用人工启发式规则对调度方案进行调整,尽管该方法可在一定程度上解决重排序问题,但很难得到期望的良好排序性能,因此在物料不齐套的情况下对初始生产排序进行重排序,就变得极其重要[2]。
多目标模拟退火算法求解混装线平衡与排序

多目标模拟退火算法求解混装线平衡与排序姜东;唐秋华;李梓响;吴玲【摘要】针对混流装配线平衡排序优化问题,提出了一种多目标模拟退火算法.考虑到工位负载影响装配线的生产效率、工人越过工位边界干扰生产等问题,建立了以最小工位绝对负载偏差与最小工位越界距离的优化目标.所提出的模拟退火算法在初始化中将启发式任务分配规则融入平衡问题,根据产品投产需求随机生成产品序列;引入了基于帕累托阶层和拥挤距离作为多目标适应度评价指标;对帕累托前沿解集进行重启操作,避免算法陷入局部最优;采用一种新的接受策略,提高了算法寻优能力.通过测试标准问题实验,对所提出的算法进行参数校验.将所提出的算法与快速非支配遗传算法进行对比,采用收敛性和多样性两个评价指标,验证所提出算法的优越性.【期刊名称】《机械设计与制造》【年(卷),期】2018(000)009【总页数】4页(P189-192)【关键词】混流装配线;平衡排序优化;模拟退火算法;多目标优化【作者】姜东;唐秋华;李梓响;吴玲【作者单位】武汉科技大学机械自动化学院,湖北武汉 430081;武汉科技大学机械自动化学院,湖北武汉 430081;武汉科技大学机械自动化学院,湖北武汉430081;武汉科技大学机械自动化学院,湖北武汉 430081【正文语种】中文【中图分类】TH16;F403.71 引言随着市场竞争越来越激烈以及顾客对产品的多样性需求,制造企业逐渐将生产方式由单品种大批量想多品种小批量转变。
混流装配线可以在不改变生产组织方式的前提下,在同一条装配线上同时进行多种不同型号、不同数量的产品生产。
混流装配线平衡是指在满足工序间优先关系约束的前提下,将每个产品的不同任务平均地分配到各个工作站[1],而混流装配线投产排序问题则是根据产品订单将不同类型产品排成一个投产序列,并以这个投产序列来组织混流装配线的生产[2]。
混流装配线平衡和投产排序的研究对于提高装配线的生产效率、提高资源利用率,有着重要的作用。
(重复)工序的重排序-谢于燕——【Team Center 精品培训资料】

工序的重排序
作者:谢于燕审校:薛淑卿测试版本:TC11
在TCM项目实施过程中,客户搭建完工艺BOP后,有时会需要对工序的结构进行调整,那么在TC的制造工艺规划器模块中,该如何操作实现工艺下工序的重排序呢?
接下来,我们通过一个例子来演示,首先,先进入制造工艺规划器模块,根据产品工艺制造的过程搭建一个工艺,并为工艺新建工序,如下图1所示:
图1
初步工艺BOP搭建完成后,需要对工序进行重排序,此时,选择工艺节点,点击菜单栏【制造-工序】,如下图2所示:
1
图2
在弹出的Pert视图中,通过绘制线连接各工序,如下图3所示:
图3
当工序调整完后,需要点击重排序按钮,会弹出“对工序重排序”对话框,使工序重排序在工艺BOP中生效,如下图4、图5所示:
1
图4
图5
此时再打开该工艺BOP,会发现该工艺下的工序顺序已经调整为所需要的,如下图6所示:
1
图6
通过对Pert图的调整,可以实现对工艺的重排序,满足客户实际的工艺制造流程要求。
1。
考虑混流装配线平衡及排序的供应链网络优化

考虑混流装配线平衡及排序的供应链网络优化随着社会的不断发展,顾客对于个性化、多样化以及特色化产品的追求越来越积极。
为了满足客户需求,制造企业纷纷采用混合流水装配线生产组织方式。
制造企业要想在规定的时间内满足客户需求,不仅需要供应商在合适的时间内供给合适数量的零部件,还需要制造企业能够在合适的时间内及时将成品配送给客户,并且制造企业的产品生产系统必须要高效、平稳,因此需要生产系统和供应链系统要紧密、协同工作。
研究表明,装配线平衡系统和供应链网络系统两者之间存在相互影响、相互制约的关系,在构建供应链网络系统时将装配过程和供应分销过程结合考虑,能够提高系统的准确度、可靠度和客户服务水平。
本文在多产品、多需求地、多工厂、多供应商的背景下,建立了一个需求拉动式的"供应-装配-分销"供应链网络,在优化供应链网络时,首先考虑了基于混流装配线平衡的供应链网络优化决策,然后考虑产品投产排序问题对供应链网络优化问题的影响及意义,最后研究了在资源使用数量受限制的情况下考虑混流装配线平衡的供应链网络优化问题。
通过模型建立、求解和算例设计,得到了结果,并进行了数值化分析,得到以下重要成果:(1)通过比较可以发现,在现有的需求情境下,在多个制造商产能范围之内,模型能够在多供应商、多制造商、多产品、多需求地等节点之间决策出最优的供给、装配、分销策略,使得整个供应链网络的成本最低。
(2)文章首次提出了基于最小化MAKESPAN的混合装配线投产排序的整数规划模型。
采用该模型,给定任意数量的产品组合,MAKESPAN整数规划模型总是能够得出空余时间最小的排序方案。
(3)模型能够根据投产排序约束尽可能使制造商在规定的期限内完成生产,决策出最有效减少总成本的方案。
(4)在资源量受限制的情况下,模型能够优化资源的分配情况,有效减少供应链网络的总成本。
本文在已有的"考虑简单装配线平衡的供应链网络优化"的基础上,结合实际情况,拓展到考虑混合装配线的供应链网络优化的研究,补充了该领域的研究,对企业的实际运营提供一些参考和建议。
APS的混合生产计划排序管理的方法
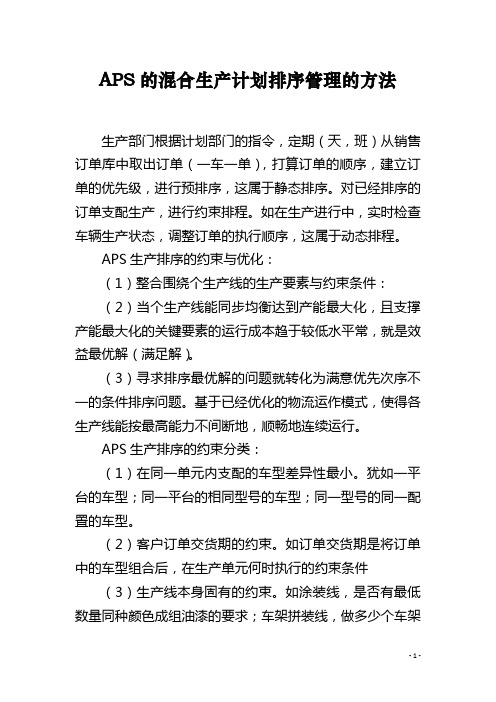
APS的混合生产计划排序管理的方法生产部门根据计划部门的指令,定期(天,班)从销售订单库中取出订单(一车一单),打算订单的顺序,建立订单的优先级,进行预排序,这属于静态排序。
对已经排序的订单支配生产,进行约束排程。
如在生产进行中,实时检查车辆生产状态,调整订单的执行顺序,这属于动态排程。
APS生产排序的约束与优化:(1)整合围绕个生产线的生产要素与约束条件:(2)当个生产线能同步均衡达到产能最大化,且支撑产能最大化的关键要素的运行成本趋于较低水平常,就是效益最优解(满足解)。
(3)寻求排序最优解的问题就转化为满意优先次序不一的条件排序问题。
基于已经优化的物流运作模式,使得各生产线能按最高能力不间断地,顺畅地连续运行。
APS生产排序的约束分类:(1)在同一单元内支配的车型差异性最小。
犹如一平台的车型;同一平台的相同型号的车型;同一型号的同一配置的车型。
(2)客户订单交货期的约束。
如订单交货期是将订单中的车型组合后,在生产单元何时执行的约束条件(3)生产线本身固有的约束。
如涂装线,是否有最低数量同种颜色成组油漆的要求;车架拼装线,做多少个车架换工装才是可以接受的。
(符合总装线的节拍)(4)生产线之间的固有约束。
如会发生总装线上要装驾驶室时,车架还未到位或规格不对等脱节现象。
(5)物料到位的约束。
可用库存不支持;高于预估的紧急要货量;供应商的供货能力;交货周期的制约;自制件的生产周期制约。
对于多产品装配混排,需要定义硬约束或软约束、软约束的优先级。
也可采用基因算法。
详细顺序约束规则包括: 完成日期:订单的提早或延迟可以被加权,可以分别对于MTS和MTO换装或调整时间:对品种间隔顺序的规则,削减换装或调整时间的铺张固定位置:订单有一定的固定位置。
如在第一个任务中放原型车的生产。
距离(空间):对某一间隔的特殊组合的特征值的限制。
如每辆敞篷车后,必需跟着有至少有两辆硬顶车。
数量:对一每天/每班规定的数量的特殊组合的特征值的限制。
车辆配载优化.
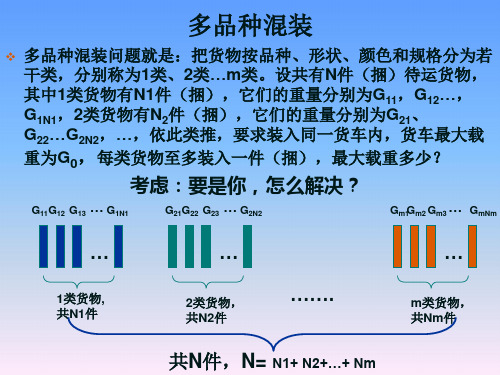
下面考虑第二种组合方案,4、6区配装,货物总量为50,正好配成 一个车。
下一步考虑第三种组合方案,5、6区配装,因为5、6区货物已配完, 不再考虑此组合方案。
依此考虑第四、五、六种方案,如表所示。
车号 1 2 3
方案序号 1 2 9
货区及货物质量
5区:10,20,20
W2 G2 W2-G2
20 23 33 27 22 25
0 13 0 13 0 13 0 13 0 13 0 13
20 7 23 10 33 20 27 14 22 9 25 12
W2=20,G2 =0或
W2-G2=20
W2=33G2
=13
W3-G3=20或33
W1=20 G1=20
从W1-G1=0处开始往前推
4区:15,10; 6区:25 1区:20,15; 7区:5
费用系数 0.45 0.60 0.90
方案序号
包含的货区
费用系数
1
各单个库区
2
4、6区
3
5、6区
4
1库、2库
5
1、3、4区
6
3、4、5、6区
7
1、3、5区
0.45 0.60 0.70 0.70 0.75 0.75 0.80
8
4、6区1、2库
9
1、3、5、7、8区
10
货场内全部货区
0.85 0.90 1.00
❖ 有这样一张待运表,需要运送到同一地点,货车载重为50:
第三阶段计算表
W3 G3 W3-G3
50
31
33
0 6 11 8 0 6 11 8 0 6 11 8
供应链管理生产调度算法
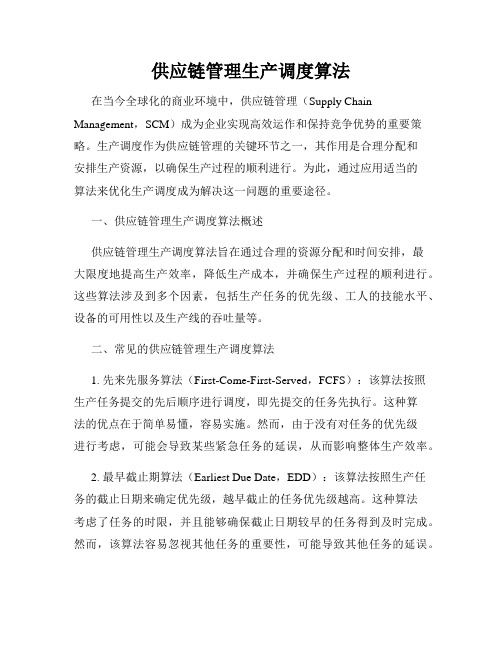
供应链管理生产调度算法在当今全球化的商业环境中,供应链管理(Supply Chain Management,SCM)成为企业实现高效运作和保持竞争优势的重要策略。
生产调度作为供应链管理的关键环节之一,其作用是合理分配和安排生产资源,以确保生产过程的顺利进行。
为此,通过应用适当的算法来优化生产调度成为解决这一问题的重要途径。
一、供应链管理生产调度算法概述供应链管理生产调度算法旨在通过合理的资源分配和时间安排,最大限度地提高生产效率,降低生产成本,并确保生产过程的顺利进行。
这些算法涉及到多个因素,包括生产任务的优先级、工人的技能水平、设备的可用性以及生产线的吞吐量等。
二、常见的供应链管理生产调度算法1. 先来先服务算法(First-Come-First-Served,FCFS):该算法按照生产任务提交的先后顺序进行调度,即先提交的任务先执行。
这种算法的优点在于简单易懂,容易实施。
然而,由于没有对任务的优先级进行考虑,可能会导致某些紧急任务的延误,从而影响整体生产效率。
2. 最早截止期算法(Earliest Due Date,EDD):该算法按照生产任务的截止日期来确定优先级,越早截止的任务优先级越高。
这种算法考虑了任务的时限,并且能够确保截止日期较早的任务得到及时完成。
然而,该算法容易忽视其他任务的重要性,可能导致其他任务的延误。
3. 关键路径算法(Critical Path Method,CPM):该算法通过确定关键路径来进行生产调度。
关键路径是指在时间上对整个项目具有最大影响力的一条路径,其上的任务不能延误,否则将导致整体项目的延误。
该算法能够提前识别可能存在的瓶颈,并对生产过程进行优化,以确保整体项目的进度。
4. 遗传算法(Genetic Algorithm,GA):遗传算法是一种启发式优化算法,模拟了生物进化的过程。
该算法通过交叉、变异等操作,不断生成新的解,并通过适应度函数对解进行评估和选择。