氨碳比分析在斯塔米卡邦尿素装置中的应用及收益
尿素装置增产降耗改造总结

21 0 2年 3 月
中 氮
肥
No 2 . Ma . 201 r 2
M — ie to e o s F ri z r P o r s S z d Ni g n u e tl e r g e s r i
尿 素 装 置增 产 降耗 改造 总结
韩 志 勇
( 大荒农业 股份有限公司浩 良河化肥分公 司 ,黑龙 江 伊春 北 13 0 ) 5 13
计 年增加 费 用 2 1万元 。 1 ( ) 总 经济效 益 7
6 结 束语
我 公 司通 过 增 建 6 / 0 th三 废 混 燃 炉 装 置 对
吹风气 锅炉 进行 节能 改造 ,降低 了原材 料 、燃 料
(W ・ ) 。共 k h]
及 动力 消耗 ,减 少 了排放 ,实 现 了循环 经济 ,增
造 新 增 1台 41 0 m 的一段 分解 分离 器 ,把加 , 0m 4 热 段和分离 段 分开 ,提 高分 离效 果 ,预精 馏 塔 与
[ 收稿 日期 ]2 1-72 0 10 —6 [ 作者简介 ]韩 志勇( 90 ) 男 , 17 一 , 山东菏泽人 , 工程师。
一
分塔分离 器合二为一 。原有 15I 7 I T 的一 分加热
扩 能至 10k/ (5 / ) 7 ta 50td ,并 对 第 2套 尿 素 装 置 进行 节能 改造 。改造后 2套 尿 素装 置总 产量 达 到 30k a以上 ,并 大 幅降 低 了生产 成本 和各 项 0 t / 消耗 。 由于第 2套 节能改 造 项 目是第 1 节能 改 套 造 的部 分 翻版 ,在此 不做 论 述 ,仅 对 第 1套老 尿
分 加 热器 的换 热 面 积 为 15I ,一 段 分 解 分 离 7 I T
斯塔米卡邦第11届尿素技术年会综述
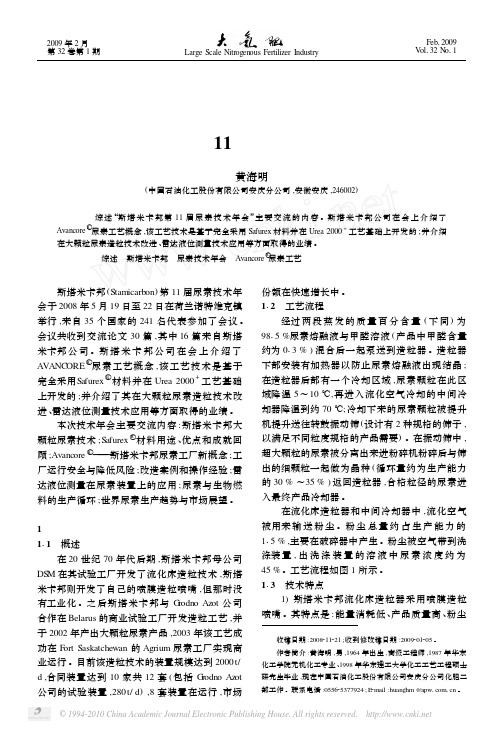
© 1994-2010 China Academic Journal Electronic Publishing House. All rights reserved.
12
设备材料全部采用Safurex ○R , 故取消了高压洗涤 器 ,并利旧中压分解循环系统作为高压尾气的洗 涤系统以降低改造费用 。由于原合成塔安装在地 面上 ,为了保证高压圈内液体靠重力流动 ,将池式 冷凝器的安装位置改到合成塔的上部 (以前通常 的设计是冷凝器和合成塔底部处在相同的安装平 面) 。将少量 CO2 直接送入合成塔 ,目的是维持合 成塔的自热平衡 ,因大部分尿素反应已在池式冷 凝器中完成 。
3) 产品中甲醛含量低 (建议加甲醛) ,只有约 013 % ,缩二脲含量仍能低于 019 % ,水含量保证低 于 013 %。粒径为 218 mm 的颗粒抗冲击强度在 35 N 以上 ,可以满足散货船运 。例如 ,从埃及运到 加拿大 ,长达 3 周的运输 ,仍能保持满意的产品质 量。
4) 每吨产品尿素消耗电力约 35~40 kW·h , 主要为流化空气鼓风机耗电 ,未含颗粒冷却耗电 (循环冷却水) 。
可以很容易地扩大装置规模 。 最新的发展使造粒能力达到 3600 t/ d ,甚至更
高 。同时取消了中间冷却器 ,洗涤部分改为酸液 洗涤 ,能耗更低 ,尾气达到排放标准 。
图 1 斯塔米卡邦大颗粒尿素造粒工艺流程
图 2 斯塔米卡邦流化床造粒器喷膜造粒喷嘴
图 3 喷膜造粒喷嘴工作原理示意
2) 由于产生的粉尘比其他造粒工艺少 ,装置 连续运行已达 150 d (埃及厂) 。一般情况下 ,造粒 器清洗 1 次的间隔时间在 90 d 以上 。
系统 、高压氨喷射器等设备 。
高压洗涤器取消后 ,在流程设计上采用了中 压洗涤替代高压洗涤 ,这一概念来源于科威特石 化工业公司 ( PIC) 的尿素装置改造 ,该技术还将应 用到在建的神华内蒙古鄂尔多斯化肥项目 。
尿素装置能耗分析及节能减排措施

尿素装置能耗分析及节能减排措施摘要:针对尿素行业高能耗的特点,结合化工节能技术和尿素生产工艺,挖掘装置节能减排的潜力,并提出相应的措施。
关键词:尿素能源节能减排影响因素前言大庆石化分公司化肥厂尿素装置是上个世纪七十年代从荷兰STAMICARBON公司引进的CO2气提法尿素生产工艺技术,该装置由荷兰大陆公司总承包,国内设计院完成配套工程的设计,于1976年建成投产。
2005年,通过引进荷兰STAMICARBON公司的并联中压技术对尿素装置进行了扩能改造,使装置的生产能力由原设计1620吨/天提高至2300吨/天。
扩能改造中新增一套并联中压系统外,还新增了一台CO2增压机、一台高压离心氨泵、一台高压离心甲铵泵以及一套蒸发系统,另外还对高压洗涤器进行了更新,这是国内首家利用并联中压技术对CO2气提法尿素生产工艺进行改造并取得成功的装置。
一、尿素生产中的影响因素及操作优化1、尿素合成反应机理及热力学模型2、尿素生产操作优化(1)选择最佳操作温度:温度是影响尿素平衡转化率的重要因素,尿素合成的平衡转化率随温度的升高而升高,但当其他条件不变时,温度超过一定值后,转化率又会下降,因此,存在一个最佳的操作温度。
要得到最大的转化率,尿素合成塔应尽可能控制在最佳操作温度下运行。
(2)提高氨碳比:提高原料的氨碳比,可以提高尿素合成的转化率。
当有过剩氨存在时,不仅有利于提高转化率,还可以抑制某些副反应。
氮碳比可以通过进料调节机构进行调节,不过高氨碳比虽然能够提高尿素合成转化率,但太多过剩氨也会造成系统利用效率下降,并使能耗升高,增大后续设备的负荷,同时也将提高系统的平衡压力,因此实际操作时氨碳比也有一个合理的最优选择范围。
(3)降低水碳比:研究表明降低水碳比,可以大幅度提高尿素转化率,水碳比每降低0.1,转化率就可提高1%以上,因此应当尽可能地降低水碳比。
要控制系统的水碳比,只能通过低压甲铵液的含水量来控制,而控制低压甲铵液的含水量又要通过对低压循环吸收系统、0.7MPa系统和水解系统进行综合调整来实现。
如何提高尿素合成塔的转化率

如何提高尿素合成塔的转化率1、有较高的合成塔操作温度,对水溶液全循环法来说,188 ℃±2 ℃;对于工业纯钛衬里的合成塔,可以适当提高合成塔操作温度;对于CO2汽提工艺来说在180 ℃~185 ℃。
2、控制好氨碳比(NH3/CO2分子比)过量氨的存在能提高尿素合成转化率。
NH3/CO2分子比 2 3 4转化率% 40 54 67.5NH3/CO2比每增加0.2转化率就增加1.0 %~1.5 %。
但氨碳比不宜大于4.5。
对水溶液全循环工艺来说,最佳的氨碳比为4.0;对于NH3或者CO2汽提工艺来说在3.0~4.0。
3、尽可能降低水碳比(H2O/CO2分子比)尿素合成塔进料中水碳比每增加0.1 %,尿素合成转化率就降低1 %左右。
尿素生产总是力求将水碳比降到最小限度。
对水溶液全循环法来说,水碳比控制在<0.7;对于NH3或者CO2汽提工艺来说在0.35左右。
4、尽量提高二氧化碳纯度,以利于转化率的提高原料二氧化碳的纯度对转化率有明显的影响。
因为二氧化碳气中惰性气量的增加,将降低气相中氨的分压,造成液相中氨浓度下降,减少了反应物浓度,使转化率下降。
CO2,% 86 88 90 92 94 96 98 100 转化率下降,% 5.6 5.0 4.4 3.7 2.9 2.2 1.3 0提高二氧化碳纯度的方法主要有:采用二氧化碳气体脱H2技术;尿素合成塔等高压圈设备采用新的耐腐蚀衬里,如采用Sandvik和Stamicarbon共同开发的Safrex双相不锈钢材料,减少或者停止二氧化碳气体中防腐空气的加入。
5、减少物料在尿素合成塔内的返混和保证物料在尿素合成塔内停留时间在40分钟~60分钟。
如:采用高效、新型的尿素合成塔内件,可以减少物料在尿素合成塔内的返混,提高转化率;采用Stamicarbon最新技术,即池式冷凝器/池式反应器的技术,既扩能,又提高尿素合成转化率。
鄂尔多斯联合化工有限公司60/104大化肥项目就是采用Stamicarbon池式冷凝器/池式反应器的技术设计了一个新的高压圈,将原流程为日本TEC(东洋工程公司)的全循环改良C法1500吨/日二套装置,扩为3500吨/日。
尿素装置节能降耗改造总结

( 1 ) 一分加热器仍用一次蒸汽加热 。 ( 2 ) 取消一 、 二分加热器冷凝液液位槽 , 一分 加热器冷 凝液 直接进 入第 l 饱 和器 , 闪蒸 出的 0 . 6 5 M P a 蒸汽用于二分塔。 ( 3 ) 二分加热器冷凝液 、 第1 饱 和塔 出液 和
一
式塔盘与多孔筛板组合形式, 安装 1 5 层D Z高效 旋流式塔盘 , 4 层多孔筛板 , 4层旋流板。
大, 所 以应加 大换 热面 积 , 以减少 新鲜 脱盐 水使 用
济, 蒸汽消耗和氨耗均偏高。故决定进 行增产改
造, 使其 产能 达到 4 2 0~ 4 5 0 t / d , 以达到 降低 汽耗
和 氨耗 的 目的。
量 。用 此次 改造 淘汰 的一 分 预 热器 ( F=1 2 8 m ) 改 作软 水冷却 器 使用 。 ( 4 ) 为 保 证 预 分 离 器 的效 果 , 将 预 分 离 器 气 相管线 直接 接 至 2台外 冷 器 之 间 , 以降低 气 相 压
分离器闪蒸分解能力 , 达到节约蒸汽的 目的。预 分离 器 气 相管 不 可 垂 直 插 入 , 应 顺 流体
方 向斜插 , 插入 处 的管径 扩至 D N 2 5 0 mm。 ( 5 ) 预分 离 器 气 相 位 置 改 动 后 , 为 保 证 预 分 离器 正 常运行 , 作 如 下 改 动 以 降低 预 分 离 器 液 相 阻力 : ① 取 消一分 预热 器 和一分气 相 分离器 ; ② 取 消 汽液混 合物 进 入 闪 蒸换 热 段 流 程 , 即一 分 气 与 二 甲液 经一蒸 热 能 回收段 混合直 接进 人 2台一 吸
( 5 ) 低 压 分 解 与 低 压 吸 收 系 统 之 间 阻 力 较
尿素装置气相、液相氨碳比分析仪分析介绍

图1
的 气体, 通过夹套伴热管道引至常压吸 收塔进行使用; 色 谱分析仪分析 N H 、 C O : 、 H z 、 0 : 、 N : 几个数据从而得到 N H # C O , 在微机 E 进行显示, 色谱 分析仪数据每 8 5 - Y 9 t  ̄ ( 有的色谱 5 分钟取—个 样 晰 个样。 分析仪用的 为A B B P G C 2 0 0 0系列 , 气相氨碳比分析仪控制指标为 3 4 — , 并和相应 的温度、 压力等联锁进行报警 , 操作 ^员根据分析值及时进行控制、 调节。 故障主要在预处理这—块, 主要原因 气相含有油类物质, 过滤效果不好, 厂 家技术 ^ 员进行了改造 , 增加了前置过滤, 目前使用效果还可以。载气为 9 9 9 9 9 % N 2 , 压力为 0 . 4 — 0 5 MP a , 样气为 N H 0 — 8 Wd 2 o 2 0 — 3 0 0 / 0 。 需要配置 的管线为夹套伴热蒸汽 ( 压力约为 0 . 6 M P a , 2 0 0 度) 、 N : ( 或空气)压力 0 . 4 — 0 5 M P a 用于吹扫,分析仪小屋里面有暖气以及空调用来控制温度; 故 障维护睛况 : —般 下 3 - 4 个月清洗过滤器—次, 标定每月标定一 . { 欠 。
图2
2 液相 氨碳 比分析仪 2 1 原理: 尿 素合成 塔 排 出的液流密度 和氨碳 比 之间成 一定 的线 陛关 阀的调节来控 制尿素样液的温度, 另—个单独的温度元件( 与密度传感 器
系, 振动垂直管作为密度传感器进行密度测量, 工作原理基于共振频率技 体) 贝 0 用于连锁跳车。在尿素样液 的管线 b丕 安装了—个流量表和—个 术。供货商为荷丰公司, 分析仪钶【 造商为 S P I E 。 荷丰公司为国内唯—供应 压力表 , 用于监测流量和压力, 如果测量数值超出了正常的操作界限, 就会 商。 发出报警信号, 如果压力过高、 尿素样液流量过低或冷却装置发生故障, 冲 2 2基本流程见图2 。 A为阀门组合( 角阀和三通整体阀) 用于取样和对 洗系统就将自动运行冷凝液通过壹 兰 体阀进人取样系统, 冲洗整个氨碳比分 管线进行隔离冲洗; B为冲冼系统 , 配置有7 巾 冼水泵 , 用于向三通阀和分析 析仪中的尿素溶液。 仪注入冲洗水; c为背压式调节器, 用于对分析仪内的压力进行控制 ; 主要 2 , 4分析仪配置: 分忻仪内部为配有密度变送精 f 【 蝉独的电子没备。 其 流程为: 在合成塔去汽提塔管线 E 进行取样( 尿素合成塔液位调节阀前 ) , 柜体内 E 置 为: 渐冰 泵一台, 冷却水流量i 固 节阀 一台, 冷却水 寸 一 压力 1 4 . 7 MP a , 温度 1 8 5 度, 根部为一 阀和—个三通整体阀, 材质要求 台, 样液流野 寸 一 台( 在分析仪柜前面) 配置冲冼 水泵一台( 1 2 3 9 l L / } l ; 防爆 为3 1 6 L M 0 D ( 或2 R E 6 9 ) , 然舌 进^ 氨碳比 分析仪, 管线均需要夹套伴热 , 等级DⅡc T 4 ) 等, 现 配蛩令 却水7 j , 管线( 用= j 却 , 最 水 在氨 / 碳比 分析仪柜体内, 尿素样液首先被冷却, 随着尿素样液的冷却压 管线) , 蒸汽 线、 仪表空气( 保持柜内( 前面 ) 正压) , 如果要在原有装置 力降低, 在柜体内安装一 毛细管减压器, 用于降低进 ^ 分析仪的压力, 最 E 进} = 谴 , 现场需要预留 合成 液管纷 澉 样口、 精馏塔洋液回收营 线、 终的压力控制是通过安装在密度 的下游的背压式调节器完成的, 该 蒸汽伴热管线等。 调节器安装在从精馏塔到 Ⅱ 热器的工艺管线 。 2 5故障以及维护情况 : 据各公司操作 人员反应维护难点在样气温度 2 3报警, 系统 : 柜体内尿素样沼 摧线 匕 的温嘎 呒 , 通过对冷却水调节 控制, 温度控制利用的为冷凝水管线 , 进口温度达到4 5 ( 下转 1样点为: 高压洗涤器气相 ; 基本流程为: 根部
降低尿素装置中压放空尾气氨含量

运行天数 (天)
27 28 31 30 31 30 13 22 24 30 30 30 326
分析次 数(次)
27 28 31 30 31 30 13 22 24 30 30 30 326
尾气氨含量超 标次数(次)
26 28 29 30 31 28 12 22 24 29 28 27 314
分析数据统计
2
E101出液氨含量高,后移至中压来分解,造成中压吸收负荷重, 通过尾气放空 中压吸收塔C101氨吸收效果差,导致中压吸收塔C101被迫加入
3
大量回流氨来稳定系统运行,C101回流氨量大导致大量气氨进入 中压回收系统而从尾气中放空 中压惰气洗涤塔C103氨吸收效果差,导致尾气中的氨不能被有效 吸收,进入放空尾气
C103放空流量 (指标<810kg/h)
1025 1002 992 1026 1034 1045 1036 1076 …… 1160 1065 1023 1045 33
制表:李林珂
时间:2014年1月25日
五 、目标可行性分析
2014年1月氨含量超标影响环节统计
序号 A B C D 影响环节 C103氨吸收效果差 C101氨吸收效果差 R101出液氨含量高 E101出液氨含量高 合 计 频次 33 23 2 1 59 累计频次 33 56 58 59 累计 (%) 55.93 94.91 98.31 100.0 100
C103放空流量 (指标<810kg/h)
1025 1002 992 1026 1034 1045 1036 1076 …… 1160 1065 1023 1045
超标次数统计
314
11
6
118
179
斯塔米卡邦和斯纳姆尿素装置解吸水解技术的对比与分析

斯塔米卡邦和斯纳姆尿素装置解吸水解技术的对比与分析为了减少尿素生产过程中所产生的工艺冷凝液对环境造成污染,并将其中的NH3和CO2回收利用,不同工艺的尿素生产装置都有与其相配套的尿素工艺冷凝液回收技术。
除了引进尿素装置中采用的尿素工艺冷凝液解吸水解技术外,国内也开发了适合于多种尿素生产工艺技术的工艺冷凝液解吸水解技术。
这些技术的采用,从根本上解决了尿素工艺冷凝液回收和利用的问题。
笔者结合生产实践,针对斯塔米卡邦和斯纳姆尿素工艺冷凝液解吸水解技术的特点,生产运行常见问题以及解决措施进行阐述和分析。
1 解吸水解的原理1.1 解吸原理解吸是吸收的反过程,吸收需要的是高压和低温,而解吸需要的则是低压和高温。
有关吸收的基本原理也适用于解吸,只是在解吸过程中,NH3和CO2组分在液相中的浓度大于气相中的平衡浓度,所以能够从液相进入气相。
离平衡浓度越远,推动力越大,则越容易解吸。
为了实现解吸应设法降低解吸组分在气相中的分压,或提高液相的平衡浓度。
脱除水中NH3和CO2在许多工业生产过程中都会遇到,例如采用溶液加热汽化法,向液相通入惰性气体的汽提法、减压解吸法、蒸汽直接加热汽提法等。
尿素工业常用的是蒸汽直接加热解吸方法。
对解吸的要求,一是解吸后的废液应不含氨,以降低尿素氨耗;二是解吸气含水量应尽量少,以利于实现系统的水平衡。
为了达到解吸废液中不含氨,首先要从技术经济角度来确定解吸压力。
一般解吸塔的操作压力比吸收系统压力高0.05MPa,以便解吸气直接送入吸收系统而得到回收,这样的流程不仅简化,而且操作方便。
如果利用副产蒸汽或其他低压蒸汽作为解吸汽提剂,而其压力等于或小于吸收系统压力时,解吸气不能自动进入吸收系统,则可先将解吸气送入解吸冷凝器冷凝成液相,再用泵把此冷凝液送至吸收系统。
这样的流程和操作较为复杂,但是解吸和吸收的压力互不影响,有利于工艺系统的稳定运行。
解吸压力一经确定,塔底排液温度也就确定。
由于排液中含NH3和CO2量很低,塔底温度实际上相当于该压力下纯水的沸点。
尿素合成氨生产原理
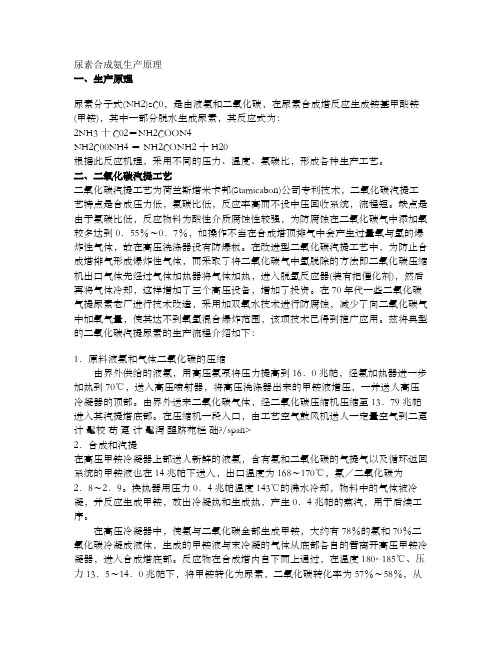
尿素合成氨生产原理一、生产原理尿素分子式(NH2)zC0,是由液氨和二氧化碳,在尿素合成塔反应生成铵基甲酸铵(甲铵),其中一部分脱水生成尿素,其反应式为:2NH3十C02=NH2COON4NH2C00NH4 = NH2CONH2十H20根据此反应机理,采用不同的压力、温度、氨碳比,形成各种生产工艺。
二、二氧化碳汽提工艺二氧化碳汽提工艺为荷兰斯塔米卡邦(Stamicabon)公司专利技术,二氧化碳汽提工艺特点是合成压力低,氨碳比低,反应率高而不设中压回收系统,流程短。
缺点是由于氨碳比低,反应物料为酸性介质腐蚀性较强,为防腐蚀在二氧化碳气中添加氧较多达到0.55%~0.7%,如操作不当在合成塔顶排气中会产生过量氧与氢的爆炸性气体,故在高压洗涤器设有防爆板。
在改进型二氧化碳汽提工艺中,为防止合成塔排气形成爆炸性气体,而采取了将二氧化碳气中氢脱除的方法即二氧化碳压缩机出口气体先经过气体加热器将气体加热,进入脱氢反应器(装有把催化剂),然后再将气体冷却,这样增加了三个高压设备,增加了投资。
在70年代一些二氧化碳气提尿素老厂进行技术改造,采用加双氧水技术进行防腐蚀,减少了向二氧化碳气中加氧气量,使其达不到氧氢混合爆炸范围,该项技术己得到推广应用。
兹将典型的二氧化碳汽提尿素的生产流程介绍如下:1.原料液氨和气体二氧化碳的压缩由界外供给的液氨,用高压氨泵将压力提高到16.0兆帕,经氨加热器进一步加热到70℃,送入高压喷射器,将高压洗涤器出来的甲铵液增压,一并送人高压冷凝器的顶部。
由界外送来二氧化碳气体,经二氧化碳压缩机压缩至13.79兆帕进入其汽提塔底部。
在压缩机一段入口,由工艺空气鼓风机送人一定量空气到二趸计髦校苟趸计髦泻醒跻苑栏础?/span>2.合成和汽提在高压甲铵冷凝器上部送人新鲜的液氨,含有氨和二氧化碳的气提气以及循环返回系统的甲铵液也在14兆帕下送入,出口温度为168~170℃,氨/二氧化碳为2.8~2.9。
尿素合成塔塔板的更新改造

尿素合成塔塔板的更新改造祁刚【摘要】@@ 沧州大化集团公司尿素装置采用斯太米卡邦二氧化碳汽提法生产工艺,尿素合成塔是整个尿素装置中最重要的设备.该设备自1977年投产以来,已经运行30余年,目前存在二氧化碳转化率较低,装置氨耗和蒸汽消耗较高等问题.2009年8月,公司在装置停车大修期间,实施了尿素合成塔的技术改造,采用了新型高效的尿素合成塔塔板,并更换了合成塔衬里.装置于2009年10月开车投用,运行情况良好,二氧化碳转化率由58.05%上升到60.05%,系统的氨耗由583 kg/t下降到581kg/t,蒸汽消耗降低了40 kg/t.笔者以下对改造方案和效果简述如下.【期刊名称】《化肥设计》【年(卷),期】2011(049)001【总页数】3页(P44-45,51)【作者】祁刚【作者单位】沧州大化集团公司,河北,沧州,061000【正文语种】中文【中图分类】TQ440.51沧州大化集团公司尿素装置采用斯太米卡邦二氧化碳汽提法生产工艺,尿素合成塔是整个尿素装置中最重要的设备。
该设备自1977年投产以来,已经运行30余年,目前存在二氧化碳转化率较低,装置氨耗和蒸汽消耗较高等问题。
2009年8月,公司在装置停车大修期间,实施了尿素合成塔的技术改造,采用了新型高效的尿素合成塔塔板,并更换了合成塔衬里。
装置于2009年10月开车投用,运行情况良好,二氧化碳转化率由58.05%上升到60.05%,系统的氨耗由583 kg/t下降到581 kg/t,蒸汽消耗降低了40 kg/t。
笔者以下对改造方案和效果简述如下。
二氧化碳汽提法尿素合成塔为多层卷焊直筒结构,内径为2 800 mm,容积为195 m3。
合成反应液由塔内的溢流管自塔底引出,进入汽提塔。
合成塔内等距安装8块多孔筛板,塔板间距为2 620 mm。
1999年该塔进行了一次设备技术改造,在下部又增加了2层筛板,塔板数增加为10块。
各层筛板的孔数不等,1~5层每层825个,6~8层每层587个,9~10层每层436个,孔径8 mm。
斯塔米卡邦和斯纳姆尿素装置解吸水解技术的对比与分析

Co a io a d An y i o s r to d dr l s c noo y b t e t mia b n n n m e l t mp rs n n alssf r Deo p i n a Hy oy i Te h l g ewe n S a c r o a d S a Ur a P a s n s n
用 的尿 素工 艺冷凝 液 解 吸水 解 技术 外 Байду номын сангаас 内也 开 发 国
De . 2 O c 01
・
化肥 设计
Ch mia e tl e sg e c lF rii rDe in z
2 ・ 2
第4 8卷 第 6期 21 00年 1 2月
斯 塔 米 卡邦 和斯 纳姆尿 素 装置 解吸 水 解
技 术 的 对 比 与 分 析
周 家 林
( 中石油塔里 木油 田 石化分公 司, 新疆 库尔勒
用 , 同工艺 的尿 素生 产装 置 都 有 与其 相 配套 的尿 不
素工艺 冷 凝 液 回收技 术 。除 了 引 进 尿 素 装 置 中采
法等 。尿 素工业 常用 的是蒸 汽直 接加热 解 吸方法 。
对解 吸的 要 求 , 是 解 吸 后 的废 液 应 不 含 氨 , 一 以降低尿 素 氨 耗 ; 是 解 吸 气 含 水 量 应 尽 量 少 , 二 以 利于 实现 系 统 的水 平 衡 。为 了达 到解 吸废 液 中 不 含氨 , 首先要 从技 术 经 济 角度来 确 定 解 吸 压力 。一
为了减 少 尿 素 生 产 过 程 中所 产 生 的工 艺 冷 凝 液对环 境造成 污 染 , 并将 其 中 的 N C , H 和 O 回收 利
度 。脱 除水 中 N C H 和 O 在许 多工业 生产 过程 中都 会遇 到 , 如 采 用 溶 液 加 热 汽 化 法 , 例 向液 相 通 人 惰 性气 体 的汽 提 法 、 压 解 吸 法 、 汽直 接 加 热 汽 提 减 蒸
斯塔米卡邦向阿塞拜疆SOCAR提供尿素造粒技术

和全 开 时 的电流输 入值 即可 实 现分程 调节
4 阿 自倍尔 阀 门定位 器运 行情 况
[ 1 ] 吴 国熙. 调节 阀使用 与维修 [ M] . 北 京 :化 学 工 业 出 版 社 ,
1 9 9 9: 2 0 8 - 21 5.
2 0 1 1 年 选 择合 成 氨装 置部 分 调节 回路 .更换
况 下整 个 阀 门调 校不 超过 5 mi n
该 智 能 阀 门定 位 器 . 如 减压 氨 罐 流量 调节 阀、 甲烷
化 气 氨冷 器 流量 调 节 阀 .进 行 阀门定 位 器换 型 改 造 测 试 经过 1 a的在 线 运 行 . 投用 的调 节 阀运 行 稳定 . 调 节 准确 。 2 0 1 2年 6月又 将合 成 氨装 置界 区
该 尿 素装 置将使 用斯塔 米 卡邦 的尿 素 2 0 0 0 p l u s池式反 应 器二 氧化 碳 汽提 设 计和 MP洗 涤 该 造 粒装
第 6期
杨淑荣等 . 阿 自倍 尔 阀 门 定 位 器在 合成 氨装 置 贝利 调 节 阀 上 的 应 用
3 9 7
需 要 改变 流 量特 性 或 阀位 响 应度 等 参数 的调 节 阀 可 通过 HA R T 2 7 5 / 3 7 5通 信装 置 自行更 改设 定 3 ) 最 后 通过 改变 输 入信 号 确认 阀位 .正 常 情
P V1 5 0 A / B、 P V1 5 3 A / B是 分程 调节 的贝利 调 节 阀 ,
换. 到 目前 为止各 调节 阀运 行稳定 。
通 过 对 贝利 调 节 阀 阀 门定 位 器 的换 型 改 造 .
锦 天 化 合 成 氨 装 置 调 节 阀 运 行 状 况 明 显好 转 用 型号 为 A V P 1 0 2 / 2 0 2智 能 阀 门定 位 器替 换 原 来 的 电/ 气 转 换器 和 阀 门定 位器 .由 2台变 为 1台 。 减 少 了一个 故 障 点 . 性价 比也大 大 提高 。 新 型 阀 门定 位 器 的更 换 , 不仅 节 约 仪 表 成 本 、 维 护 方便 。 还 在 原 阀 门定 位 器基 本 功 能 的基 础上 开发 了更 多 的优
斯塔米卡邦二氧化碳气提法尿素工艺与特点

二氧化碳气提法工艺目前已经成为国际上生产装备能力最大及建厂最多的尿素生产工艺。
由荷兰斯塔米卡邦公司(Stamicarbon )于20世纪60年代初开发出来,并于1967年正式投产。
随后在很多国家建设了斯塔米卡邦工艺的尿素工厂,目前已经建成二百多套尿素装置,总产能大概为50Mt/a ,在世界尿素总产能的占比达到45%,单套设计能力为70-200t/d 。
1 斯塔米卡邦二氧化碳气提法尿素工艺概述斯塔米卡邦二氧化碳气提法尿素工艺通常由七个工序组成:CO 2压缩和H 2脱除、液氨升压、合成尿素及CO 2汽提、低压循环、解吸水解、尿液蒸发造粒、产品包装与储存等工序。
合成尿素的原料主要包括氨和二氧化碳,它们与尿素装置本身回收的甲铵溶液经过加压后进入合成系统。
合成系统包括合成塔、气提塔、高压甲铵冷凝器和高压洗涤器等四个主要设备。
合成系统的压力为14~15MPa ,反应温度为180~185℃,氨碳比约为2.95,可以完成约60%二氧化碳转化率。
合成塔出料中含尿素、甲铵、CO 2、氨等反应熔融物,它们通过气提塔被二氧化碳气提,甲铵在气提塔中分解为氨气和二氧化碳,然后进入高压甲铵冷凝器,尿液经气提后流至精溜塔。
合成塔顶出来的气体在高压洗涤器内被来自回收塔的甲铵浓溶液吸收后,再与原料液氨一同流至高压甲铵冷凝器,氨与CO 2反应形成甲铵液,甲铵液可以进一步在合成塔内生成 尿素。
尿素从气提塔出来以后,经过精馏、闪蒸、一段蒸发及二段蒸发后,使尿液中的尿素浓缩至浓度约99.7%,再通过尿素泵将其输入到造粒塔进行喷淋造粒,从而制得颗粒状的尿素成品。
NH 3、CO 2和水蒸气从精馏塔蒸发出来以后进入到低压甲铵冷凝器,将这些蒸出的气体冷凝到氨水槽内。
当中大概九成的稀氨水进入到水解系统进行尿素的水解,再通过精馏塔进行浓缩之后进入到低压甲铵冷凝器;其余的稀氨水于中压吸收塔内吸收来自高压洗涤的尾气至某个浓度后,也进入到低压甲铵冷凝器。
它们在冷凝器形成甲铵浓溶液,再被输送到合成系统。
尿素装置增产改造总结

尿素装置增产改造总结杨艳【摘要】In order to further improve the capacity of urea unit, a medium pressure decomposition circulating system is added in urea synthesis section,so that after revamp,the capacity of the unit will be raised from 1 350 t/d to 1 650 t/d.After completion of the renovation,the properties of final product agree with expected performance,emission indexes meet the requirements, and the CO2 consumption and the NH3 consumption are both within the design targets.%为了进一步提高尿素装置产能,在尿素合成工段增设了中压分解循环系统,以期改造后装置产能从1350 t/d 提高至1650 t/d。
改造完成后,最终产品性能达到预期指标,排放指标满足要求,CO2和 NH3消耗量均在设计指标范围之内。
【期刊名称】《化肥工业》【年(卷),期】2015(000)005【总页数】4页(P36-39)【关键词】尿素;CO2;汽提法;增产改造【作者】杨艳【作者单位】山西天泽煤化工集团股份公司山西晋城 048000【正文语种】中文【中图分类】TQ441.41尿素装置增产改造总结杨艳(山西天泽煤化工集团股份公司山西晋城048000)摘要为了进一步提高尿素装置产能,在尿素合成工段增设了中压分解循环系统,以期改造后装置产能从1 350 t/d提高至1 650 t/d。
氨碳比分析仪在斯塔米卡邦尿素装置中的应用及收益.doc
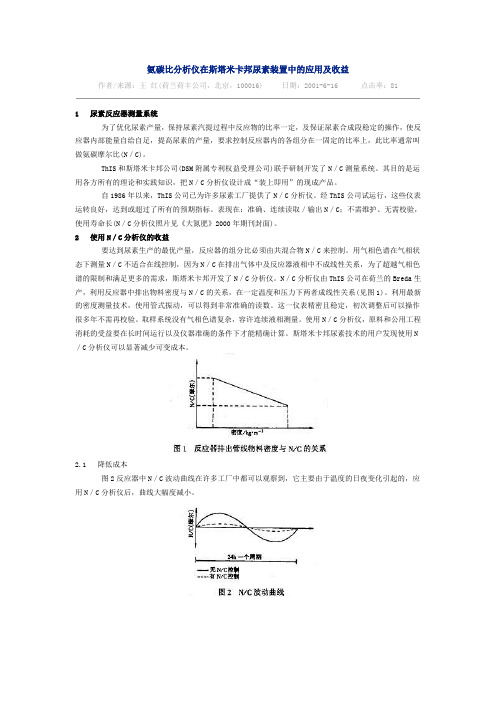
氨碳比分析仪在斯塔米卡邦尿素装置中的应用及收益作者/来源:王红(荷兰荷丰公司,北京,100016) 日期:2001-6-16 点击率:811 尿素反应器测量系统为了优化尿素产量,保持尿素汽提过程中反应物的比率一定,及保证尿素合成段稳定的操作,使反应器内部能量自给自足,提高尿素的产量,要求控制反应器内的各组分在一固定的比率上,此比率通常叫做氨碳摩尔比(N/C)。
ThIS和斯塔米卡邦公司(DSM附属专利权益受理公司)联手研制开发了N/C测量系统。
其目的是运用各方所有的理论和实践知识,把N/C分析仪设计成“装上即用”的现成产品。
自1986年以来,ThIS公司已为许多尿素工厂提供了N/C分析仪。
经ThIS公司试运行,这些仪表运转良好,达到或超过了所有的预期指标。
表现在:准确、连续读取/输出N/C;不需维护、无需校验,使用寿命长(N/C分析仪照片见《大氮肥》2000年期刊封面)。
2 使用N/C分析仪的收益要达到尿素生产的最优产量,反应器的组分比必须由共混合物N/C来控制。
用气相色谱在气相状态下测量N/C不适合在线控制,因为N/C在排出气体中及反应器液相中不成线性关系,为了超越气相色谱的限制和满足更多的需求,斯塔米卡邦开发了N/C分析仪。
N/C分析仪由ThIS公司在荷兰的Breda生产,利用反应器中排出物料密度与N/C的关系,在一定温度和压力下两者成线性关系(见图1)。
利用最新的密度测量技术,使用管式振动,可以得到非常准确的读数。
这一仪表精密且稳定,初次调整后可以操作很多年不需再校验。
取样系统没有气相色谱复杂,容许连续液相测量。
使用N/C分析仪,原料和公用工程消耗的受益要在长时间运行以及仪器准确的条件下才能精确计算。
斯塔米卡邦尿素技术的用户发现使用N /C分析仪可以显著减少可变成本。
2.1 降低成本图2反应器中N/C波动曲线在许多工厂中都可以观察到,它主要由于温度的日夜变化引起的,应用N/C分析仪后,曲线大幅度减小。
金新化工尿素装置氨碳比控制系统的设计优化

金新化工尿素装置氨碳比控制系统的设计优化
毛大军
【期刊名称】《中氮肥》
【年(卷),期】2022()2
【摘要】呼伦贝尔金新化工有限公司尿素合成塔液相氨碳比分析仪采用荷兰Stamicarbon公司研发的专利技术,并委托AMEC SPIE公司生产氨碳比分析系统,可实现尿素合成塔出液氨碳比的实时在线监测,但由于氨与CO2反应生成尿素需要较长的时间,直接采用尿素合成塔出液氨碳比控制存在一定的滞后性。
为此,金新化工对其尿素装置氨碳比控制系统进行了设计优化——将进料氨碳比与液氨量设计成串级控制回路,进料氨碳比为主变量,高压氨泵(P102A)透平转速或液氨流量(FT1202)为副变量,即通过调控尿素合成塔进料氨碳比来间接控制尿素合成塔出液氨碳比。
尿素装置氨碳比控制系统优化设计后,尿素合成系统氨碳比实现了自动控制,实验室分析次数有效减少,尿素装置运行更加稳定,工艺操作难度明显降低,为实现尿素装置的节能降耗与生产效益最大化发挥了积极的作用。
【总页数】5页(P43-46)
【作者】毛大军
【作者单位】呼伦贝尔金新化工有限公司
【正文语种】中文
【中图分类】TQ441.41
【相关文献】
1.合成氨装置ATR/KRES水碳比优化控制系统
2.优化操作降低尿素装置中压氨吸收器的氨损失
3.尿素装置氨碳比控制系统的改进
4.金新化工“5080”合成氨、尿素项目奠基
5.运用CO_2气化装置,解决“气头”尿素装置的氨碳平衡
因版权原因,仅展示原文概要,查看原文内容请购买。
- 1、下载文档前请自行甄别文档内容的完整性,平台不提供额外的编辑、内容补充、找答案等附加服务。
- 2、"仅部分预览"的文档,不可在线预览部分如存在完整性等问题,可反馈申请退款(可完整预览的文档不适用该条件!)。
- 3、如文档侵犯您的权益,请联系客服反馈,我们会尽快为您处理(人工客服工作时间:9:00-18:30)。
氨碳比分析仪在斯塔米卡邦尿素装置中的应用及收益
作者/来源:王红(荷兰荷丰公司,北京,100016) 日期:2001-6-16 点击率:81
1 尿素反应器测量系统
为了优化尿素产量,保持尿素汽提过程中反应物的比率一定,及保证尿素合成段稳定的操作,使反应器内部能量自给自足,提高尿素的产量,要求控制反应器内的各组分在一固定的比率上,此比率通常叫做氨碳摩尔比(N/C)。
ThIS和斯塔米卡邦公司(DSM附属专利权益受理公司)联手研制开发了N/C测量系统。
其目的是运用各方所有的理论和实践知识,把N/C分析仪设计成“装上即用”的现成产品。
自1986年以来,ThIS公司已为许多尿素工厂提供了N/C分析仪。
经ThIS公司试运行,这些仪表运转良好,达到或超过了所有的预期指标。
表现在:准确、连续读取/输出N/C;不需维护、无需校验,使用寿命长(N/C分析仪照片见《大氮肥》2000年期刊封面)。
2 使用N/C分析仪的收益
要达到尿素生产的最优产量,反应器的组分比必须由共混合物N/C来控制。
用气相色谱在气相状态下测量N/C不适合在线控制,因为N/C在排出气体中及反应器液相中不成线性关系,为了超越气相色谱的限制和满足更多的需求,斯塔米卡邦开发了N/C分析仪。
N/C分析仪由ThIS公司在荷兰的Breda生产,利用反应器中排出物料密度与N/C的关系,在一定温度和压力下两者成线性关系(见图1)。
利用最新的密度测量技术,使用管式振动,可以得到非常准确的读数。
这一仪表精密且稳定,初次调整后可以操作很多年不需再校验。
取样系统没有气相色谱复杂,容许连续液相测量。
使用N/C分析仪,原料和公用工程消耗的受益要在长时间运行以及仪器准确的条件下才能精确计算。
斯塔米卡邦尿素技术的用户发现使用N /C分析仪可以显著减少可变成本。
2.1 降低成本
图2反应器中N/C波动曲线在许多工厂中都可以观察到,它主要由于温度的日夜变化引起的,应用N/C分析仪后,曲线大幅度减小。
如果自动控制比率,N/C值可进二步稳定,通过控制系统来完成。
该系统也可以执行其他先进控制回路,如控制水在甲铵溶液中的含量,及合成段的NH3/CO2进料比及尿素反应器液面控制等,发挥其作用。
以两个先进控制回路为例,自动控制N/C和水在甲铵溶液中含量,由于减少了蒸汽及原料消耗,也就降低了成本,增加了产量。
由于反应器中的N/C振幅变窄,蒸汽的消耗减少2%,氨的流失减少到大约60%。
以1500t/d尿素装置100%负荷运行为例:
1)假设装置每年运行330天,以能源消耗来计算节省量,蒸汽消耗为14$/t,总值为11×104$/a。
2)假设HP洗涤器下游工段没有安装吸收器,NH3流失到空气中的量减少到约60%,每年节省大约为
2.9万美元。
3)分析实验只在重大检测及重新校验时进行。
假设一般情况下每周在汽提塔或反应器出口取样,如果安装N/C分析仪,可减少到两个月一次。
这样达到的节省为1.92×104$/a。
4)水在甲铵循环液中的量应越少越好,因为它对尿素在合成段的转化起反作用,每相对于100份甲铵液中含水量,蒸汽消耗量减少为2.5%,相应的节省量为14×104$/a。
能源和原材料消耗的总节省量为30×104$/a。
5)如安装先进控制回路,非常有可能使生产产量增加1%,每年可得到额外的利润,约为45万美元。
6)所有操作员以相同的控制参数来操作;多变量测量,得出更好的管理信息;正是有紧密的控制规范,操作流程会更接近最优化操作条件,也产生更高的生产能力。
综上所述,每年的总节省可达到74.8万美元。
由于更高效的生产及生产能力的增加,斯塔米卡邦公司已证明在一年之内就可收回总投资。
2.2 使用效果事例
以下是几个N/C分析仪用户的反馈事例:
1)加拿大SASKFERCO工厂
①使用N/C分析仪,严密的控制N/C的范围,可以达到每天产量增加40t尿素的高生产水平,在每日的操作中可以快速并更稳定的达到理想的高峰值(n CO2);②N/C分析仪改进了汽提塔周围的操作从而减少蒸汽消耗4%~5%,高压蒸汽节省又被以上提到的增加的更多的产率交换掉,并这一增加量包括在以上数值内:③安装N/C分析测量系统后,NH3和CO2的流失量有所减少,具体数值取决于汽提塔,大约节省6%;④从未取过GC样。
2)爱尔兰IFI工厂
①安装了外部压力为0.7MPa的缓冲器,NH3的流失有了显著的改进,但N/C分析仪确实帮助在开车后更快的稳定装置;②自从安装后从未再校正过;③在正常操作下分析仪性能良好,稳定。
总体评论这是一台非常有用的监测合成条件,减少流出物及氨的流失的设备。
3)美国路易斯安那TRIAD工厂
①自从N/C分析仪投入使用后,合成工段操作得非常好,反应效率增加了,汽提塔效率增加了,蒸汽效率也增加了。
少量的氨从合成工段排出,减少了再循环工段的负荷。
负荷的减量允许增加反应率,同时不需要从循环系统排出氨,而在合成段将这些氨重新利用。
预计氨效率增加量为 0.002t/t尿素,蒸汽效率为0.087t/t尿素。
②N/C分析仪是更好操作尿素装置的一个很有效的工具,氨流失量减少和生产量增加的受益比预计的还要好,认为在这之前许多操作中出现的问题都是因为反应器中的比率失调造成的。
4)沙特阿拉伯化肥公司
N/C分析仪满足需求,能连续的给出读数并不需任何校验,N/C读数总是和实验室测试结果相吻合。
3 先进过程控制系统进一步使受益最大化
节省和收益只有在尿素装置利用先进过程控制系统时才能最大化。
先进控制的设计原理可使尿素装置在更少操作间断中运行并提供更好、更快的装置管理信息,由物理平衡数据来计算推理测量值产生直接的装置信息,如浓度、尿素合成段和再循环段的关键比值。
这一连续的控制和信息将改进装置的稳定性及减少实验室分析次数。
所有关键变量可通过投有所报的专用的、灵活的 Fixtrak一体化mini DCS先进过程控制系统控制。
3.1 反应器液位控制(液面)
反应器液位控制的目的是即使在装置的负荷有极少的变化(通过改变汽提塔的入口阀)或其他控制方式情况下,也能达到一个稳定的反应器液位。
由于反应器液位的负面反应,在操纵排出阀 (USO)时,正常(自动)液面反馈控制是不能实现的。
反应器液位“控制器”既可控制NH3进料又可控制CO2进料的设定点,这种算法(偶合算法)设计的目的是确保进料比保持不变。
这一前馈控制的优点是不管液位控制器的控制性能如何,反应器的摩尔比保持不变。
控制反应器摩尔比的目的是控制液相的摩尔比在3.0~3.1之间(通过安装在下游管线的N/C分析仪来测量)。
反应器摩尔比控制器可控制NH3和CO2两者进料的流量控制器的设定点。
(偶合)算法设计的目的是不管反应器摩尔比控制器的流量比设定值如何,保证加到合成段的总量稳定。
校正原料流的摩尔比是通过(纯)CO2和NH3流量的质量计算来实现的。
3.2 对HP汽提塔O2/CO2的控制
若没有合适的预防措施,控制CO2流量会导致O2含量波动。
为了保证摄入充足的空气阻止合成设备起化学变化,需要校正CO2进料(前馈控制)。
最终的调整(由回料控制)由想要达到的浓度和氧气分析仪测定的实际数值来确定。
3.3 反应器顶部惰性气体的控制
其目的是通过调节由合成部分进料的惰性气体总量来控制惰性气体物料平衡。
惰性气体的存在对反应器中的转化起反作用,因此应保持越低越好。
因为不能直接测量惰性气体,所以控制回路是完全前馈的。
3.4 低压甲铵冷凝器
在尿素装置的再循环阶段大部分未转化的NH3和CO2从尿素溶液中除去。
甲铵溶液从液位槽经高压甲铵泵循环到高压洗涤器。
其中水量的多少对反应器中反应的转化率起反作用。
如果其中不存在水,这一操作是不可能的,因为混合物会结晶。
对LPCC这样操作的目的是使流回HP洗涤塔的甲铵液含有31%的水从而符合低压甲铵冷凝器对当前装置负荷的要求。
可操作性是通过甲铵液中自动计算量的比例来改进的(以HP甲铵泵吸入管线的密度测量及现存压力和温度测量为基础,然后通过加入水量的多少来调节)。
这一分析也可给出NH3和CO2在循环甲铵液中(控制在N/C>2.06)的比率读数。
4 结论
通过缩小N/C在反应器中的变量,发现如果安装先进过程系统:高压蒸汽消耗可减少2%, NH3散失量可减少1.6个系数,实验室分析的次数显著减少。
通过先进过程系统减少循环甲铵液中水的含量:随着水含量减少2.5%,高压蒸汽消耗也随之减少。
严格的控制制度,使可操作流程更接近规范量,从而达到更高的生产能力。
安装先进过程系统更有可能,使装置产量增加1%。