钢包吹氩喂铝线工艺的应用
底吹氩技术在安钢30t钢包上的设计及应用

1 前 言
钢包底吹氩是现代炼钢工艺过程 中必不可少的
一
素:
( 透气芯的尺寸要满足吹氩工艺所需透气量 的 1 )
大小。
个环节 , 它是通过安装在钢包底部 的透气 砖 向钢
( 为防止修包 时浇注料灌人透气砖 内和使用时 2 ) 被冷钢、 残渣覆盖 , 透气砖 的高度应 稍高于包 底包
维普资讯
第2 9卷第 5期
20 07年 1 0月
甘
肃
冶
金
V0 . 9 No 5 12 . Oc . 2 0 t ,0 7
GANS U METAI URCY
文 章 编 号 :624 6 (0 7 0 -0 5 ) 17 -4 1 2 0 )50 1 43
( 便于浇注料 的振动操作 , 3 ) 使透气砖与浇注料 接触密实 , 确保使用时安全而不会发生漏钢事故 。 根据 以上要求 , 透气砖 的外形结构尺寸进行 对
了设 计 , 图 1 见 。
2 钢 包底吹氩技术 的设计及应用
21 透气 砖 的设 计 与选择 .
2 1 1 透 气砖 的 结构设 计 . .
衬。
液中吹人氩气等惰性气体 , 使钢液在钢包 内产生环 流, 对钢水进行充分搅拌 , 使添加在钢水中的合金 、 脱氧剂 、 脱硫剂等快速熔 化、 分散 , 促使钢液成分和 温度的均匀 , 吸附钢液中的夹杂物 , 去除钢中的非金 属夹杂和有害气体 , 从而达到净化钢液 目的, 其使用 效果远远高于钢包顶吹氩。安钢第二炼钢厂过去采 用 钢包 吹氩枪 顶 吹 的 吹氩 方 式 , 着对 钢 水 质 量 的 随 要求越来越高 , 已不能满足提高钢水质量的需要 。
≤O. 2 MPa 。
考虑到该厂出钢温度高及钢包使用寿命长的特
钢包自动底吹氩装置在炼钢厂的应用及生产工艺实践

关 键词 : 精炼钢包 ; 自动吹氩装置 ; 底吹氩
中图分类号 :F 6 . T 79 9 文献标 识码 : B
Ap l a i n a d Pr c i e o he Au o a i to g n Bl wi p i to n a tc f t t m tc Bo t m Ar o o ng c
酒钢二炼钢厂是个全新的炼钢厂 ,2 顶底复 10t 吹转炉所配套 的精炼处理方式主要 以 L F炉为主 , 并且工艺设计上以炉后吹氩站与精炼炉合二为一。 钢包吹氩采用单透气砖偏 心布置方式 , 气体介质 为
氩气 , 最高供气 压力 16 M a . P 。吹氩装置采用钢包
自 动底 吹氩装置与数字吹氩 系统相结合 , 此套 系统 从设计上 自动化程度高 、 控制精度高 , 操作上简便 、
钢 包 自动 底 吹 氩装 置在 炼 钢 厂 的应 用 及 生产 工 艺 实践
阮 强, 程子建 , 王意龙
嘉峪关 750 3 10) ( 酒泉钢铁集团公司 二炼钢厂 , 甘肃
摘 要: 本文通过对本厂钢包 自 动底 吹氩装 置的恢复使用 , 了 自 比较 动底吹装置与传统 的底 吹方式 的优缺点 , 通过 生产实践及 比较 , 钢包 自动底 吹氩装 置结合 数字 吹氩 系统 是可靠 、 先进的钢包 自动 化吹氩技 术 , 具推广应 用的价 极
De c fRe n ng La l n S e l a i g Pln  ̄ e o f i d e i tem k n a t i
R AN Qag H N ii , U i ,C E G Z-a WAN iog n jn G Y — n l
( h eo dSel kn l t f IC J yga 3 10, hn ) T eScn t maigPa S O, i uun75 0 C ia e n oJ a
双透气砖钢包吹氩技术

双透气砖钢包吹氩技术的应用摘要:通过应用钢包双透气砖吹氩技术,提高了钢包底吹率,减少了钢包底吹氩死区,使钢水成分和温度更加均匀,并降低钢中夹杂、减少铸坯成分偏析,因而提高了钢水质量及轧材性能的稳定。
1前言莱芜钢铁股份有限公司炼钢厂(简称莱钢炼钢厂)为了保证钢水成分合格率及均匀性,采取精炼平台氩后取样快速反馈措施,应用精炼在线成分微调技术工艺,实现成分的预知预控,以适应转炉快节奏生产的需要。
但是在钢包底吹氩方面,由于单透气砖钢包吹氩存在死区,搅拌不均匀,易造成成分偏析,从而影响轧材质量,或者钢包底吹不开,对生产组织带来了较大的影响。
为此,通过对吹氩工艺进行研究与分析,提出了双透气砖钢包吹氩技术工艺。
2双透气砖钢包吹氩工艺2.1 双透气砖在钢包中的位置在双透气砖钢包中,两块透气砖的位置如图1所示。
图中,水口和原透气砖安装位置不变(半径中心处);新透气孔位置在钢包中心线到内衬距离的1/2处;电极外接圆直径为钢包内衬直径的1/3。
图1 钢包双透气砖安装位置示意图2.2 双透气砖钢包吹氩分析根据单透气砖吹氩搅拌的特征,氩气泡引起钢液的循环流动大体可以分为气-液卷流区、水平流区、熔池壁附近的向下流区、熔池下部的向心流区。
通过氩气泡群所产生的浮力驱动钢液向上流动,从而带动各区域的钢水进行循环流动,达到均匀成分及温度的目的。
由于单透气砖位置在钢包内衬到钢包中心线1/2处,钢包另一侧水口周围则成为死区,钢水搅拌能力较弱,成分、温度及脱氧均匀性较差,夹杂物上浮能力也比较弱(如图2所示),当氩气流股较弱时,不能带动整个钢包内钢水的循环流动,这种表现尤为突出。
在生产中发现,大包开浇取样时,钢样冒碳花现象严重;开浇3min时取样(约浇7~8t钢)没有出现这种现象;另外,在中包烘烤较好的情况下,第一炉多次出现少量皮下气泡。
这充分说明在钢包水口周围存在死区,开浇后,这部分钢水先通过水口流出,由于未能充分均匀搅拌,导致这部分钢水脱氧程度弱,钢中氧含量平均在145×10-6左右,致使轧材出现皮下气泡、性能不合等质量问题。
钢包底吹氩工艺开发

钢包底吹氩工艺开发摘要:钢包底吹氩工艺是一种有效的钢水处理方法,通过向钢包底部吹入氩气,使钢水中的杂质和气体充分上浮,达到净化钢水的目的。
本文主要介绍了钢包底吹氩工艺的原理、开发过程及应用效果,阐述了该工艺对提高钢水质量和连铸效率的影响。
一、钢包底吹氩工艺原理钢包底吹氩工艺的原理是在钢包底部通过特制的喷嘴向钢水中吹入氩气。
氩气在钢水中形成气泡,气泡在上升过程中会吸附钢水中的杂质,并携带杂质上浮,从而达到净化钢水的目的。
同时,氩气的搅拌作用还可以使钢水成分和温度更加均匀,提高钢水的质量。
二、钢包底吹氩工艺开发钢包底吹氩工艺的开发主要包括工艺流程设计、设备选型和控制系统优化三个环节。
首先,需要确定合适的氩气流量、压力和喷嘴结构,保证氩气能够充分搅拌钢水。
其次,需要根据钢包容量、钢水处理量和现场实际情况选择合适的设备型号和数量。
最后,需要对控制系统进行优化,确保工艺过程的稳定性和可靠性。
三、钢包底吹氩工艺应用效果钢包底吹氩工艺在多个钢铁企业得到了广泛应用,并取得了良好的应用效果。
首先,该工艺可以显著提高钢水质量,降低钢水中杂质含量,提高钢材的力学性能和耐腐蚀性能。
其次,该工艺可以显著提高连铸效率,降低铸造成本,提高钢铁企业的经济效益。
此外,该工艺还可以减少铸坯裂纹、提高铸坯质量,延长铸坯使用寿命。
四、结论钢包底吹氩工艺是一种有效的钢水处理方法,通过向钢包底部吹入氩气,可以显著提高钢水质量和连铸效率。
该工艺的开发和应用对于提高钢铁企业的产品质量和经济效益具有重要意义。
未来,还需要进一步研究和优化钢包底吹氩工艺,以推动钢铁工业的持续发展。
在铜冶金工业中,新型双侧吹熔池熔炼工艺设备的应用已经成为了一种趋势。
这种工艺设备可以提高铜金属的产量和质量,同时降低能耗和污染物排放,为铜冶金工业的可持续发展做出了巨大的贡献。
铜冶金工业是一个重要的基础工业,对于国民经济和科学技术的发展具有重要意义。
然而,传统的铜冶金工艺存在一些问题,如能耗高、污染物排放量大、产量低等。
莱钢90t LF/VD精炼钢包智能吹氩技术的开发与应用

2 0 1 3 年第 4 期
拌 能 够为 夹杂 物上 浮 提供 动力 学条 件 , 并促 进钢 渣
界面反应 。
N L / m i n ; 2 ) 真空 保持 5 mi n , 采用 强吹模 式 , 流量 设定 为8 0 N L / m i n ; 3 ) 真空 保持 5—1 0 mi n , 采用 强强 吹模 式, 流量设 定为 1 5 0 N L / mi n ; 4 ) 真空保 持最后 5 m i n ,
图4 吹氩搅拌过程夹杂物相对含量的变化趋 势
从图 1 ~3 可 以看 出 : 吹气搅拌 可显 著降低夹 杂
收稿 日期 : 2 0 1 3 — 0 6 — 1 3 作者简 介 : 张飞 , 男, 1 9 8 5 年生, 2 0 0 8 年 毕业于安徽工业大学冶金工 程 专业 。现为山钢股 份莱芜分公 司特钢事业 部助理工 程师 , 从事 炼钢工艺技术工作 。
8
脱 氧 夹杂 物平 均 尺寸 增大 了约 5 倍, 颗粒 数 量 降低
了3 —4 个 数量级 。从 图 5 可 以看 出 : 采用 1 5 0 L / mi n 底 吹流量 , 可实 现夹 杂物 的有效 去 除 。钢 水 吹氩搅
张飞等
莱钢 9 0 t L F / V D 精炼钢包智能吹氩技术 的开发与应用
夹杂物 上浮时 间与底吹流量 的关系见 图 5 。
4
砉3
2
1 0
时 间/ s
时间/ s
时 间/ s
图1 夹杂物 C 与搅 拌时间关 系
图2 夹杂物 开 o . 与搅拌时间的关系
图3 夹杂物 ‰ 与搅拌时间的关 系
夹杂物直径, m n 一不 同吹氩时间夹杂物数量密度 ; 冠一 不同吹氩时 间夹杂物 当量
钢包底吹氩控制系统的优化设计

钢包底吹氩控制系统的优化设计钢包底吹氩控制系统是钢铁生产过程中的重要环节,其优化设计能够提高钢铁生产的效率和质量。
本文将从钢包底吹氩控制系统的原理、优化设计的目的和方法以及实际应用效果等方面进行探讨。
一、钢包底吹氩控制系统的原理钢包底吹氩控制系统是通过控制钢包底部喷口的氩气流量和压力来实现钢水的混合和温度控制。
钢包底吹氩控制系统的主要组成部分包括氩气供应系统、氩气流量控制系统、氩气压力控制系统和温度控制系统等。
二、优化设计的目的和方法优化设计的目的是提高钢铁生产的效率和质量。
具体方法包括以下几个方面:1.优化氩气供应系统,确保氩气的稳定供应和质量。
2.优化氩气流量控制系统,提高氩气流量的精度和稳定性。
3.优化氩气压力控制系统,确保氩气压力的稳定和可靠性。
4.优化温度控制系统,提高钢水的温度控制精度和稳定性。
三、实际应用效果钢包底吹氩控制系统的优化设计在实际应用中取得了显著的效果。
通过优化设计,钢铁生产的效率和质量得到了大幅提升。
具体表现在以下几个方面:1.钢水的温度控制精度和稳定性得到了显著提高,减少了钢铁生产中的温度偏差和浪费。
2.钢水的混合效果得到了改善,减少了钢铁生产中的不均匀性和质量问题。
3.钢铁生产的效率得到了提高,减少了生产时间和成本。
4.钢铁生产的质量得到了提高,减少了废品率和质量问题。
综上所述,钢包底吹氩控制系统的优化设计是钢铁生产中的重要环节,其优化设计能够提高钢铁生产的效率和质量。
通过优化氩气供应系统、氩气流量控制系统、氩气压力控制系统和温度控制系统等方面的设计,可以实现钢水的混合和温度控制,从而提高钢铁生产的效率和质量。
在实际应用中,钢包底吹氩控制系统的优化设计取得了显著的效果,为钢铁生产的发展做出了重要贡献。
钢包自动底吹氩装置在炼钢厂的应用及生产工艺实践

钢包自动底吹氩装置在炼钢厂的应用及生产工艺实践【钢包自动底吹氩装置在炼钢厂的应用及生产工艺实践】1. 引言钢铁产业作为现代工业发展的重要支柱之一,在我国经济中占据着重要地位。
在钢铁生产过程中,炼钢环节是至关重要的,而钢包自动底吹氩装置则是炼钢过程中的一项关键技术。
本文将探讨该装置在炼钢厂的应用及生产工艺实践。
2. 钢包自动底吹氩装置的概述钢包自动底吹氩装置是一种用于钢包冶炼过程中的技术装备,主要用于钢液脱气、脱硫和除杂等工艺操作。
该装置通过控制氩气的吹入速度和位置,有效降低了钢液中的氧含量,提高了钢液的质量,并减少了气体夹杂物。
3. 钢包自动底吹氩装置的应用价值3.1 提高钢液质量钢包自动底吹氩装置可以通过控制底吹氩气的流量,使钢液中的氧含量得到有效控制,从而提高钢液的质量。
较低的氧含量可以减少夹杂在钢液中的氧化物,从而提高钢的纯度和抗氧化性能。
3.2 降低能耗和减少环境污染传统的底吹氩工艺通常需要大量的能耗,而钢包自动底吹氩装置通过精确控制氩气的流量和位置,可以使得氩气的利用效率得到最大化,从而降低能耗。
在钢包自动底吹氩装置中,废气净化装置的使用可以有效减少废气的排放,减少对环境的污染。
4. 钢包自动底吹氩装置的生产工艺实践4.1 工艺参数的选择在使用钢包自动底吹氩装置时,需要合理选择工艺参数,包括底吹氩气的流量、压力和温度等。
通过对工艺参数的优化选择,可以使底吹氩气的效果达到最佳状态,从而更好地保障钢液的质量。
4.2 灵活调整工艺钢包自动底吹氩装置可以通过对底吹氩气的流量和位置进行灵活调整,以适应不同的钢种和冶炼工艺要求。
在实际生产中,根据不同的冶炼任务和钢液的质量要求,可以对底吹氩气进行适当的调整,以保证钢液质量的稳定。
5. 个人观点与理解钢包自动底吹氩装置作为一项先进的炼钢技术装备,在提高钢铁产品质量和减少环境污染方面具有不可替代的重要作用。
我认为,在未来的钢铁生产中,钢包自动底吹氩装置将会越来越广泛应用,并不断得到改进和升级,以满足更高的质量要求和环境标准。
钢包吹氩喂铝线工艺的应用

维普资讯
钢 包 吹 氩 喂 铝 线 工 艺 的 应 用
气 泡 , 随 氩气 上浮 , 并 从而 达到 净化 钢液 的作用 。 () 1 吹氩 压力 ( 表压 )
PA : P + 2 r y + P + P c/
0 2MP 。 为 保 证 氩 气 有 一 定 的搅 拌 能 力 , 装 . a 瓶 () 2 吹氩 时 问 夹 杂物 上浮 需要 一定 的 时问 , 吹氩 时 间太短 , 夹
值 和 现 场 观测 渣 面波 动 情 况 , 吹压 压 力 范 围为 0 1 .
~
形 成细 小分 散 的氩气 泡 , 加 与钢液 接触 面积 , 夹 增 使 杂 物粘 附在 氩气 泡 上 上 浮 , 解 在钢 中 的其 他 气 体 熔 中 。因在氩 气泡 内分 压 为零 , 他 气 体 扩 散进 入 氩 其
成 弥散分 布 的气 泡 , 钢水 接触 面积 小 , 与 不利 于 去除 夹杂 、 体 ; 气 另外 , 还容 易造 成钢 水 液面 翻滚 激烈 , 钢 液裸 露 喷溅 , 击 碎 乳 化 的 炉 渣 卷 入 钢 中 , 渣 相 被 钢 混, 导致严 重 的二 次氧 化和 降温 。因此 吹氩 时 , 根 应 据钢 液 面的 翻滚程 度 来 调 整 压 力 大 小 , 以控 制渣 面 有 波 动起 伏 、 翻滚 或 偶 露 钢 液 面为 宜 。根 据 计算 小
的钢包 喂铝 线 炉外精 炼工 艺 。
由上式 可 见 , 吹氩 压 力 主要 取 决 于 钢包 内钢 液 的静 压力 , P 即 >P
P :P ‘g ・h
式 中 :—— 钢液 密度 , p 一般 为 70 0k/ 0 g m ; ^ —— 钢 液深 度为 1 3m 左 右 。 .
喂线技术在铸造生产中的

2.球铁方面 2.球铁方面 1).投资少, 见效快; 1).投资少, 2).结果稳定,重现性好; 2).结果稳定,重现性好; 3).合金收得率高,消耗量少; 3).合金收得率高,消耗量少; 4).操作简单,维护方便; 4).操作简单,维护方便; 5).处理作业的温降小; 5).处理作业的温降小; 6).可对作业产生的烟气进行管理,消除对环境的 6).可对作业产生的烟气进行管理,消除对环境的 污染; 7).渣少,且是干渣,容易去除; 7).渣少,且是干渣,容易去除;
敬请批评指正
谢谢大家
8).增硅少,因而可大量使用回炉料; 8).增硅少,因而可大量使用回炉料; 9).适合各种规模的铸造厂与处理包; 9).适合各种规模的铸造厂与处理包; 10).可在一次操作中完成脱硫、球化和孕育等处理; 10).可在一次操作中完成脱硫、球化和孕育等处理; 11).不用覆盖,也不用凉包; 11).不用覆盖,也不用凉包; 12).灰铁和球铁的生产可随意进行转换; 12).灰铁和球铁的生产可随意进行转换; 13).可进行球化衰退挽救; 13).可进行球化衰退挽救; 14).能实现处理作业机械化和自动化; 14).能实现处理作业机械化和自动化; 15).可生产重量为熔炼能力一倍的铸件。 15).可生产重量为熔炼能力一倍的铸件。
那些铸造厂能从包芯线工艺应用中 获得好处
1.有意提高铸钢件质量以及降低成本的铸钢厂; 1.有意提高铸钢件质量以及降低成本的铸钢厂; 2.力图改善球铁生产并使其生产自动化的先进铸 2.力图改善球铁生产并使其生产自动化的先进铸 造厂; 3.由于处理时间很长因而存在温度和衰退问题的 3.由于处理时间很长因而存在温度和衰退问题的 铸造厂; 4.任何具有烟雾等影响工作环境问题的铸造厂; 4.任何具有烟雾等影响工作环境问题的铸造厂; 5.用同一基铁或冲天炉高硫铁水生产灰铁和球铁, 5.用同一基铁或冲天炉高硫铁水生产灰铁和球铁, 并希望一次完成脱硫及镁处理的铸造厂;
喂线法处理工艺在球墨铸铁生产中的应用

喂线法处理工艺在球墨铸铁生产中的应用喂线法是一种常用的球墨铸铁加工技术,它通过为熔化的金属提供充
足的液态金属,使得铸件在凝固时不会出现缩孔和夹杂。
喂线法主要分为
内喂线和外喂线两种,其应用于球墨铸铁生产中具有如下优点:
1.提高铸件质量:喂线法可以消除铸件的缩孔和夹杂缺陷,使得铸件
的密度和强度更加均匀一致。
2.简化工艺流程:喂线法可以减少一些复杂的加工操作,比如修补钩、打洞等,从而提高生产效率。
3.减少废品率:喂线法可以使得铸件的表面更加光滑,同时减少铸件
的凸包、裂缝等废品的产生。
4.稳定性强:喂线法可以在整个铸造过程中保持稳定的液态金属供应,从而保证铸件的质量和稳定性。
总之,喂线法是一种主流的球墨铸铁生产加工技术,它具有一系列显
著的优点,不仅能够保证质量、提高产量,还能够降低生产成本,因此受
到了广泛的应用。
高锰钢吹氩喂线技术的开发与改进

故采用透气砖底吹方式 , 氩气利用率高、 作用发挥 比
较 充分 。透 气砖 愈靠 近包 底边 缘 , 混匀 时 间愈 短 , 但 对 包壁 的冲蚀严 重 ; 透气砖 愈 靠 近包杆 , 匀 时间 愈 混
长, 但对包杆 的冲蚀严重。 综合包衬 的使用寿命及钢
液 纯净 度 的考虑 ,所 以将 透气 砖设 置在 包底 半 径 中
第3 6卷
V0 .6 13
第1 0期
No 1 .0
铁 道 技 术 监 督
RA 1 A IW Y QUAI—Y C TR I ON OI I
研 究 与交 流
Sl UDY 1 AND COMM INI: J ( A HONS
高锰钢 吹氩 喂线技 术 的开发 与改进
钡 铝 复 合 粉剂 外 包 一层 钢 皮 成 为 喂线 用 的包 芯线 ,
气体 、 夹杂物的效果 由初生气泡的直径 、 气泡在钢液 中的上升速度 、 留时间决定 。 吹氩操作时要求钢 停
收 稿 日期 : 0 8 0 — 2 2 0 — 6 1
作者简介: 葛志远 , T程师
钙 、 、 的熔点都低于 l 0 ; 钡 铝 0o 而且钙 的沸点仅 0 C
02 03MP ; . . ~ a 透气 砖 D 15mm。 = 0
13 温 度参 数 的选择 . 高 锰钢 的钢液 流动 性是 很好 的 ,当钢 液 中碳为 0 6 锰 为 1 %时 。 钢的液相线温度 为 1 0 . %. 9 3 高锰 0o 4 C,
致 密度 辙叉 。 随着铁 路运 输对 高锰 钢辙 叉要 求 的提
弧炉 冶炼 ,3t 1 钢包 、 出钢 量 1 , 0t塞杆 底 注 式 浇注 ,
2 吹 氩 喂 线 的工 艺 改进
钢包底吹氩工艺实践

钢包底吹氩工艺实践
钢包底吹氩工艺是一种重要的焊缝加强补强方式,尤其适用于铝
合金和低偏差元件的焊接表面。
氩焊是利用压缩空气将氩离子推入接
头金属中,从而形成良好的焊接连接的工艺。
在氩焊的焊接过程中,
会放出很大的热量,使接头金属中的残留缝及缝外深度处的杂质都会
完全护熔而溶出。
在熔融接头中产生的局部抗拉、抗压能力比焊接前
更强。
然而,由于实际施工地处不同气候,海拔不同高度等原因,空
气中气体浓度也会发生变化。
再加上氩焊的熔融深度较深,氩焊的负
极电极受焊接表面及熔池形成相应的电势,因此,需要控制接头焊接
的护熔剂浓度和电位大小,以及焊接的深度,来保证氩焊的焊接质量。
80+t钢包底吹氩提高吹成率的生产实践
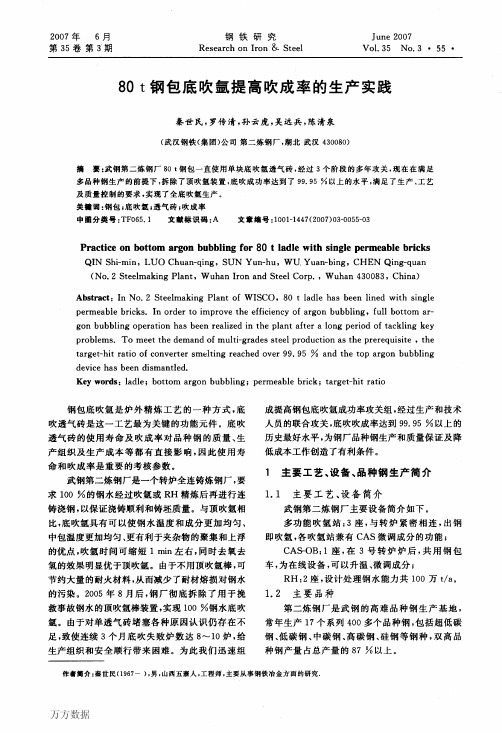
优化底吹氩管路系统,减少氩气压
力损失
攻关初期发现3个吹氩站的出钢前试气、出 钢过程吹氩、实际吹氩3个过程的流量、压力不 同,我们分析了原因,并采取了以下措施: (1)优化底吹氩管路,缩短了底吹氩金属管的 长度,减少了压力损失; (2)优化了金属软管的快速接头,原设计为液 压油用接头,我们认为不太适合高压氩气管路,故 作了修改,减少了因快速接头问题引起的底吹失 败; (3)提高了吹氩总压,正常情况下,透气砖前 进口压力0.8 MPa即可以吹起来,但如果管路压 力稍有波动,或透气芯清烧稍有异常,底吹即可能 失败,为此,我们利用全厂年修的时机,将底吹氩 管网作了修改,进口氩气压力上升到了1 MPa以 上,杜绝了因压力波动引起的底吹失败。
the prerequisite,the
top argon
target—hit ratio of
smelting reached
over
99.95少6 and the
bubbling
device has been dismantled. Key words:ladle;bottom argon bubbling;permeable brick;target-hit ratio
此阶段主要工作:研制透气砖芯、套砖、座砖、 接缝料等相关耐材;研制外装透气砖机械;外装透 气砖安装及热换操作技术。
3.3
钢液搅拌引起的对工作面的冲刷与侵蚀。当 氩气气流吹人钢液溶池时,气流回击并打击透气 砖出气口前沿,给出气口四周耐火材料一定的冲 击力。钢包底部钢水运动加剧,气相和液相相互 作用形成湍流,对底吹透气砖产生剪切、冲刷作 用,尤其是底吹透气砖高于包底时,损毁的速度加 快,高于包底部分很快被冲刷掉。
即吹氩,各吹氩站兼有CAS微调成分的功能; CA孓OB:1座,在3号转炉炉后,共用钢包 车,为在线设备,可以升温、微调成分; RH:2座,设计处理钢水能力共100万t/a。
钢包全程吹氩自动对接技术的研究与应用
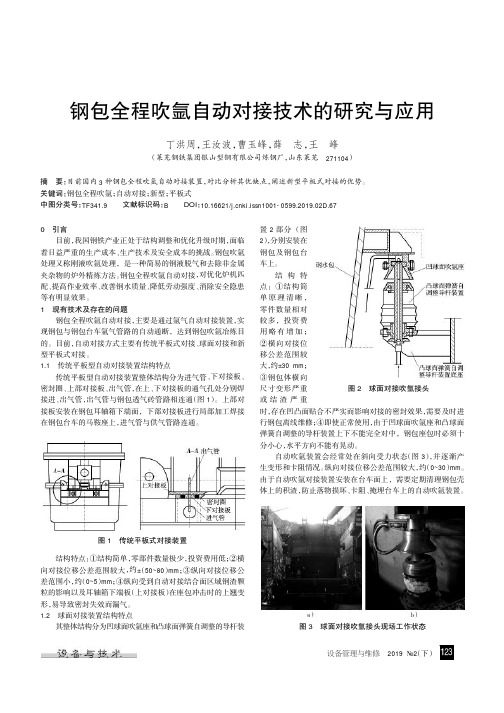
图 7 某钢厂台车下部接头工作现场
小;设计有单向阀,吹氩结束后可自动关闭。下部接头自动吹灰 炼炉的冶炼过程中,钢水喷溅至精炼炉盖、炉下吊顶、钢包包沿
机构可防止粉尘杂物堆积;下部接头进气管口设计有防尘挡板, 等表面上。
防止杂物进入;O 形密封圈压紧力可以通过压紧力调整组件进
对接装置在转炉放钢、台车出站、挂钩或座包时,钢渣受到
新型平板式对接装 置结构分为上部接头和 下部接头 2 部分:上部 接头为平面钢板与钢包 图 4 钢包加盖后向包盖铰接侧倾斜 耳轴箱连接固定,下部 接头与钢包台车马鞍座连接固定,下部接头设计有密封圈、上下 伸缩补偿弹簧、自动吹灰机构(图 5)。
2 3 种对接装置的结构对比与应用情况(表 员) 3 自动对接装置受工作环境的影响及预防 3.1 钢渣
行调整、设定(图 6、图 7)。
温度冷热的急剧变化或受机械振动影响而脱落至台车马鞍座的
相对其他自动吹氩接头,新型平板式对接装置的特点为:淤工 自动对接装置外露表面上,导致在对接装置工作时影响密封性
作组件相对复杂,上对接板、O 形密封圈、下部接头、软管等易损件均 能,缩短密封圈、对接头寿命。
可拆卸,维护更换方便;于横向对接公差范围大,约依80 mm,对接成
较多钢厂正在推广应用表员3种对接装置的结构对比与应用情况图4钢包加盖后向包盖铰接侧倾斜图5新型平板式对接装置示意图6某钢厂钢包上部接头工作现场图7某钢厂台车下部接头工作现场骳髇髗设备管理与维修2019翼2下少对钢渣的承接面积并对接触面周边做倒角处理也可以实现钢渣的自动下滑
钢包全程吹氩自动对接技术的研究与应用
图 1 传统平板式对接装置
结构特点:淤结构简单,零部件数量极少,投资费用低;于横 向对接位移公差范围较大,约依(50~80)mm;盂纵向对接位移公 差范围小,约(0~5)mm;榆纵向受到自动对接结合面区域钢渣颗 粒的影响以及耳轴箱下端板(上对接板)在座包冲击时的上翘变 形,易导致密封失效而漏气。 1.2 球面对接装置结构特点
转炉钢包自动吹氩模型开发与应用

涟钢科技与管理 2018年第1期·43·转炉钢包自动吹氩模型开发与应用谭大进1 冯力力2(1.涟钢210转炉厂;2.涟钢检修中心)摘 要 针对转炉工序钢包吹氩不规范和直上钢种难以精确控制钢水软吹问题,通过将出钢过程详细分解、每个分解步骤标识钢包吹氩时间与流量,在转炉钢包吹氩一级机对整个操作进行编程,成功开发钢包自动吹氩模型。
应用结果表明,钢包自动吹氩系统使转炉钢包吹氩更加规范、直上钢种软吹控制稳定和降低了工人劳动强度,解决了由于吹氩控制不当引起钢水倒包、合金未熔化和连铸塞棒上涨等问题。
关键词 钢包 自动吹氩 模型为促进转炉合金化过程合金的熔化,钢包需要吹氩,钢包吹氩的主要方式为底吹氩和顶吹氩,在国内基本都为钢包底吹氩。
涟钢210转炉厂转炉工序钢包底吹氩存在以下问题:①钢包底吹氩控制方式为人工操作,有时操作工忘记在出钢前打开氩气阀,在钢水已出一部分后才打开,在出钢温度低和钢包透气砖透气性不完全通畅的条件下,致钢包吹氩不起或较小,合金无法熔化,甚至引起在精炼工序倒包;②操作班组为了氩站温度指标,在出钢过程只在加合金时吹氩,合金搅拌时间较短,合金没有完全熔化,导致氩站成分不具代表性,没有对LF 操作起指导作用,影响LF 的处理时间;③直上钢种要求出完钢加完铝合金后必须软吹一定时间,由于软吹流量较小,钢包氩气流量为人工手动控制阀门调整,难以精确控制,软吹流量控制不稳定,影响钢水夹杂物的上浮。
为解决如上问题和降低工人劳动强度,决定自行开发转炉钢包自动吹氩模型。
1 钢包底吹氩系统设计图210转炉厂转炉区域钢包底吹总管设有1个总调节阀,每个支管单独设置1个切断阀和调节阀,另外在炉后设置有一个手动开关的旁通阀,具体见图1。
图1 210转炉厂转炉区域钢包底吹氩设计图2 钢包自动吹氩流量与时间控制策略2.1 钢包吹氩流量控制策略a. 倾动转炉到开始出钢信号位置后开始中等流量吹氩,其目的为:一是进行出钢前钢包吹扫;二是对转炉碳粉预脱氧进行有效搅拌。
板坯连铸中间包吹氩冶金新技术开发与应用
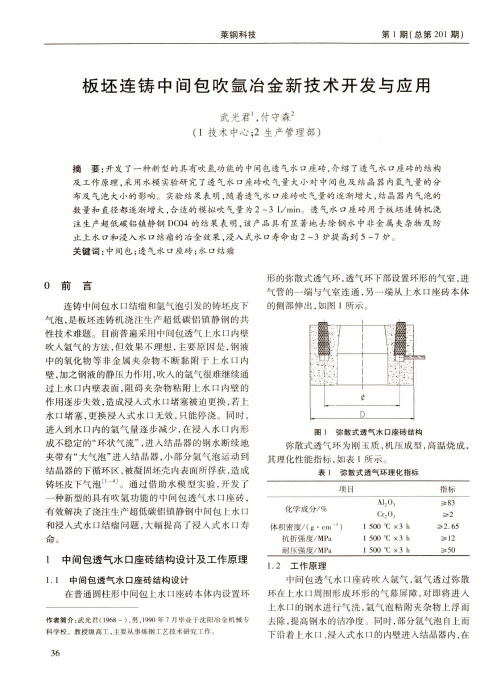
莱钢科技第1期(总第201期)板还连铸中间包吹氩冶金新技术开发与应用武光君、付守森2(1技术中心;2生产管理部)摘要:开发了 一种新型的具有吹氩功能的中间包透气水口座砖,介绍了透气水口座砖的结构及工作原理,采用水模实验研究了透气水口座砖吹气量大小对中间包及结晶器内氩气量的分布及气泡大小的影响。
实验结果表明,随着透气水口座砖吹气量的逐渐增大,结晶器内气泡的数量和直径都逐渐增大,合适的模拟吹气量为2 ~3 L/min。
透气水口座砖用于板坯连铸机浇注生产超低碳铝镇静钢DC04的结果表明,该产品具有显著地去除钢水中非金属夹杂物及防止上水口和浸入水口结瘤的冶金效果,浸入式水口寿命由2 ~3炉提高到5 ~7炉。
关键词:中间包;透气水口座砖;水口结瘤/"V “. —»—〇刖m连铸中间包水口结瘤和氩气泡引发的铸坯皮下 气泡,是板坯连铸机浇注生产超低碳铝镇静钢的共 性技术难题。
目前普遍采用中间包透气上水口内壁 吹入氩气的方法,但效果不理想,主要原因是,钢液 中的氧化物等非金属夹杂物不断黏附于上水口内 壁,加之钢液的静压力作用,吹人的氩气很难继续通 过上水口内壁表面,阻碍夹杂物粘附上水口内壁的 作用逐步失效,造成浸人式水口堵塞被迫更换,若上 水口堵塞,更换浸人式水口无效,只能停浇。
同时,进入到水口内的氩气量逐步减少,在浸人水口内形 成不稳定的“环状气流”,进人结晶器的钢水断续地 夹带有“大气泡”进人结晶器,小部分氩气泡运动到 结晶器的下循环区,被凝固坯壳内表面所俘获,造成 铸坯皮下气泡n通过借助水模型实验,开发了 一种新型的具有吹氩功能的中间包透气水口座砖,有效解决了浇注生产超低碳铝镇静钢中间包上水口 和浸人式水口结瘤问题,大幅提高了浸入式水口寿 命。
1中间包透气水口座砖结构设计及工作原理1.1中间包透气水口座砖结构设计在普通圆柱形中间包上水口座砖本体内设置环作者简介:武光君(丨%8-),男,1990年7月毕业于沈阳冶金机械专科学校。
钢包底吹氩作用
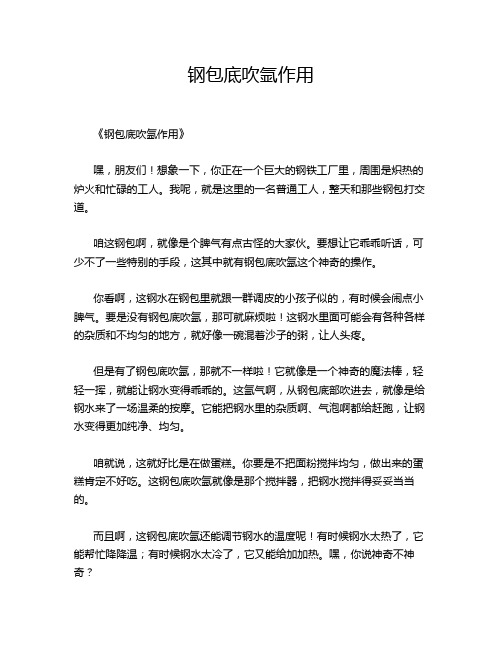
钢包底吹氩作用《钢包底吹氩作用》嘿,朋友们!想象一下,你正在一个巨大的钢铁工厂里,周围是炽热的炉火和忙碌的工人。
我呢,就是这里的一名普通工人,整天和那些钢包打交道。
咱这钢包啊,就像是个脾气有点古怪的大家伙。
要想让它乖乖听话,可少不了一些特别的手段,这其中就有钢包底吹氩这个神奇的操作。
你看啊,这钢水在钢包里就跟一群调皮的小孩子似的,有时候会闹点小脾气。
要是没有钢包底吹氩,那可就麻烦啦!这钢水里面可能会有各种各样的杂质和不均匀的地方,就好像一碗混着沙子的粥,让人头疼。
但是有了钢包底吹氩,那就不一样啦!它就像是一个神奇的魔法棒,轻轻一挥,就能让钢水变得乖乖的。
这氩气啊,从钢包底部吹进去,就像是给钢水来了一场温柔的按摩。
它能把钢水里的杂质啊、气泡啊都给赶跑,让钢水变得更加纯净、均匀。
咱就说,这就好比是在做蛋糕。
你要是不把面粉搅拌均匀,做出来的蛋糕肯定不好吃。
这钢包底吹氩就像是那个搅拌器,把钢水搅拌得妥妥当当的。
而且啊,这钢包底吹氩还能调节钢水的温度呢!有时候钢水太热了,它能帮忙降降温;有时候钢水太冷了,它又能给加加热。
嘿,你说神奇不神奇?我记得有一次,我们正在处理一批钢水,结果发现钢水的质量不太好。
大家都急得团团转,不知道该怎么办才好。
这时候,我们的老师傅就说:“快,试试钢包底吹氩!”于是,我们赶紧启动了设备,看着氩气呼呼地往钢包里吹。
嘿,你还别说,没过多久,那钢水就变得不一样了,质量明显提高了不少。
大家都松了一口气,纷纷对钢包底吹氩竖起了大拇指。
这钢包底吹氩的作用可不仅仅是这些哦!它还能让钢水的流动性更好,就像是给钢水加了润滑油一样,让它在后续的加工过程中更加顺畅。
你说,要是没有这钢包底吹氩,我们的钢铁生产该怎么办呢?它就像是我们钢铁工人的得力助手,默默地为我们的工作贡献着力量。
所以啊,朋友们,可别小看了这钢包底吹氩。
它虽然看起来不起眼,但在钢铁生产中却起着至关重要的作用。
它让我们的钢铁更加优质,让我们的工作更加顺利。
钢包吹氩气的作用

钢包吹氩气的作用钢包吹氩气是一种常见的钢铁冶炼工艺,它在钢铁生产中起着至关重要的作用。
本文将从多个方面介绍钢包吹氩气的作用和意义。
钢包吹氩气可以有效地改善钢水的质量。
钢水在冶炼过程中容易受到氧气和杂质的污染,影响钢材的质量。
通过钢包吹氩气可以将钢水中的氧气和杂质从钢水中除去,使钢水更加纯净。
氩气可以与钢水中的氧气反应生成氧化物,进而形成气泡,从而提高钢水的纯度。
此外,氩气还可以与钢水中的杂质发生化学反应,将杂质从钢水中移除,进一步提高钢水的质量。
钢包吹氩气还可以有效地控制钢水的温度。
在钢铁冶炼过程中,钢水的温度是一个非常重要的参数。
钢水温度的变化会直接影响到钢材的质量和性能。
通过钢包吹氩气可以对钢水进行加热或冷却,以控制钢水的温度。
当钢水温度过高时,可以通过吹氩气冷却钢水,使其温度降低到合适的范围;当钢水温度过低时,可以通过吹氩气加热钢水,使其温度升高到合适的范围。
通过钢包吹氩气控制钢水的温度,可以保证钢水在冶炼过程中保持在适宜的温度范围,提高钢材的质量和性能。
钢包吹氩气还可以改善钢水的流动性。
在钢铁冶炼过程中,钢水的流动性对于冶炼过程和钢材质量都有很大的影响。
通过钢包吹氩气可以改变钢水的表面张力和黏度,减少钢水的黏附性,提高钢水的流动性。
良好的钢水流动性可以使钢水在冶炼过程中更加均匀地进行混合和反应,提高钢材的均匀性和一致性。
钢包吹氩气还可以保护钢水和钢包的安全。
钢水在冶炼过程中容易受到氧气和其他气体的污染和侵蚀,从而导致钢水质量下降。
通过钢包吹氩气可以在钢水表面形成一层氩气保护层,阻隔空气和杂质对钢水的污染和侵蚀,保护钢水的安全。
此外,钢包吹氩气还可以保护钢包内壁,防止钢水对钢包内壁的腐蚀和侵蚀,延长钢包的使用寿命。
钢包吹氩气在钢铁冶炼中具有多种作用。
它可以改善钢水的质量,控制钢水的温度,改善钢水的流动性,保护钢水和钢包的安全。
钢包吹氩气是钢铁冶炼过程中不可或缺的重要工艺,对于提高钢材的质量和性能具有重要的意义。
- 1、下载文档前请自行甄别文档内容的完整性,平台不提供额外的编辑、内容补充、找答案等附加服务。
- 2、"仅部分预览"的文档,不可在线预览部分如存在完整性等问题,可反馈申请退款(可完整预览的文档不适用该条件!)。
- 3、如文档侵犯您的权益,请联系客服反馈,我们会尽快为您处理(人工客服工作时间:9:00-18:30)。
文章编号:1007 6034(2007)03 0020 02钢包吹氩喂铝线工艺的应用刘建军(铁道部驻中国南车集团眉山车辆厂验收室,四川眉山620032)摘 要:介绍了钢包吹氩喂铝线工艺,通过该工艺的应用及效果对比,认为钢包吹氩喂铝线能明显的提高钢的内在品质。
关键词:钢包;吹氩;喂铝线中图分类号:T F769.9 文献标识码:B铸钢摇枕、侧架是货车转向架的关键部件,其质量好坏直接影响到行车安全。
为进一步提高铸钢件的内在质量,满足日益提高的技术要求,结合铸造工厂现状,中国南车集团眉山车辆厂在原有钢包吹氩的基础上,又选定了投资少、见效快、适合12t钢包的钢包喂铝线炉外精炼工艺。
1 钢包吹氩喂线设备概况12t钢包,有效装载空间下底为 1200mm,上部为 1400mm,高为1300mm。
瓶装氩气,减压阀,耐压胶管,透气砖,移动式喂线机,线盘。
2 吹氩喂铝线工艺主要参数2.1 吹氩工艺主要参数氩是一种惰性气体,不熔解于钢液中,也不与钢中元素反应,不影响钢中化学成分的稳定,不会生成新的夹杂。
吹氩通过透气砖,将氩输送进入钢液中,形成细小分散的氩气泡,增加与钢液接触面积,使夹杂物粘附在氩气泡上上浮,熔解在钢中的其他气体中。
因在氩气泡内分压为零,其他气体扩散进入氩气泡,并随氩气上浮,从而达到净化钢液的作用。
(1)吹氩压力(表压)P A r=P tr+2 / +P sg+P st式中:P A r 吹氩压力(表压),MPa;P tr 管道压力损失,M Pa。
压力表装在出口附近,可忽略不计;P sg 渣层静压力,M Pa。
渣层薄可忽略不计;P st 钢包内钢液静压力,M Pa;2 / 气泡形成克服表面能的压力损失,MPa。
收稿日期:2007-02-26作者简介:刘建军(1972-),男,工程师,本科。
由上式可见,吹氩压力主要取决于钢包内钢液的静压力,即P A r>P st。
P st=g h式中: 钢液密度,一般为7000kg/m3;h 钢液深度为1.3m左右。
P st=7000!9.8!1.3=89180Pa=0.089M Pa则吹氩压力P A r大于0.089MPa,氩气才可能吹通。
理想的吹氩压力应该是氩气流能遍布钢包,氩气泡在钢液内呈均匀分布。
吹氩压力过小,氩气的搅拌能力弱,还可能造成透气砖堵塞;吹氩压力过大,氩气形成气柱,不能形成弥散分布的气泡,与钢水接触面积小,不利于去除夹杂、气体;另外,还容易造成钢水液面翻滚激烈,钢液裸露喷溅,被击碎乳化的炉渣卷入钢中,钢渣相混,导致严重的二次氧化和降温。
因此吹氩时,应根据钢液面的翻滚程度来调整压力大小,以控制渣面有波动起伏、小翻滚或偶露钢液面为宜。
根据计算值和现场观测渣面波动情况,吹压压力范围为0.1 ~0.2MPa。
为保证氩气有一定的搅拌能力,瓶装氩气要求瓶压不小于0.5M Pa。
(2)吹氩时间夹杂物上浮需要一定的时间,吹氩时间太短,夹杂脱除精炼效果不好;吹氩时间太长,既温降大,又因包壁被冲涮而带入耐材夹杂增多。
吹氩时间一般为5~10m i n,可视钢水温度、渣物情况等适当调整。
(3)透气砖位置吹氩为钢包偏心单孔底吹。
偏心底吹氩有利于钢包内部钢液的混合和温度均匀化,以及夹杂物排除。
为避免和减少对钢包塞杆和钢包壁的冲涮,吹氩砖中心位置确定在包塞杆对侧,距包底中心150 mm处。
吹氩压力和时间在生产中影响因素较多。
如透20冷热工艺 机车车辆工艺 第3期2007年6月气砖使用后期,透气孔部分堵塞,透气效果差,需较大压力;渣层厚,钢水多,需较大压力。
钢液温度高,可采用较大压力。
2.2 包内喂铝线工艺主要参数铝在钢中作脱氧剂用时,其作用是脱氧定氮,并细化晶粒,阻抑低碳钢的时效,提高钢在低温下的韧性等。
因铝的熔点低、密度小、易氧化,加入包内的铝块易上浮氧化或被钢渣包裹,造成铝的收得率低,残铝控制不稳定,铝氧化生成夹杂增多。
为此,采用包内喂铝线来替代钢包内加环状铝块的工艺。
(1)喂线量钢中残铝要求为0.02%~0.08%,含铝量高,吸氧能力增强,形成A l2O3夹杂增多,而生产的钢种对A l2O3夹杂要求较高,故对钢中预期铝含量定为中下限。
为防止出钢后Si、M n的氧化,出钢前炉内终脱氧插铝块0.5kg/t左右(视还原期脱氧状况调整),炉内插铝出钢后,在包中喂铝线。
喂线量=钢水量!(预期铝含量-喂线前铝含量)/铝线纯度/铝的收得率铝线纯度化验值为97%,喂线前钢中残铝含量取0.010%,铝的收得率预取70%(实际生产中进行校核),实验预期铝含量取0.040%。
则吨钢喂线量=1000!(0.04%-0.01%)/97%/70%=4.4kg/t。
(2)喂线速度喂线速度要求将铝线射入钢包的中下部(钢包深度的2/3)弥散开进行沉淀脱氧。
喂线速度过快,铝线对包底有冲击,并在包底熔化,弥散分布差。
喂线速度过慢,铝线在钢包的上部熔化上浮,钢包底部钢液的脱氧差。
喂线速度设定为1m/s,能保证铝线达到钢包中下部位。
喂线时铝丝应垂直穿过渣层进入钢液,喂线部位一般在吹氩嘴旁,喂线过程用较小压力吹氩,喂完线后适当增加压力,应保持继续吹氩不小于1m i n。
钢包吹氩喂铝线过程为:出钢前包内吹氩,以清除管道中空气,置换钢包内的空气,减少钢水氧化;出钢过程中以较小压力吹氩;出钢完后测温,并视钢液面波动情况调整压力;钢包运输到喂线平台处喂线;喂线完后,估计温度达到允许浇铸温度中上限后测温,温度适合停吹氩气;吊运浇铸。
为保证透气砖的透气性能,每次浇铸完后要及时用氧清理透气砖表面的残钢和残渣。
3 实验、检测及分析表1为未吹氩喂线和吹氩喂线2种工艺炼钢时测得的钢中非金属夹杂物及氧含量检验结果。
表1 钢中非金属夹杂物及氧含量检验结果处理方式取样炉数夹杂物总量/%A l2O3杂物/%!(O)/!10-6范围平均范围平均范围平均未吹氩喂线160.0205~0.03550.02580.0083~0.01180.009783~11096吹氩喂线100.0115~0.02070.01510.0048~0.00750.005640~10063从表1可见,吹氩喂铝线后,钢中夹杂总量平均下降了41%,A l2O3夹杂平均下降了42%,氧含量平均下降了34%。
吹氩喂线后,除降低夹杂和氧含量外,吹氩还使钢液温度均匀性好,基本消除了高温裂纹,降低了浇铸后期包眼堵塞频次。
表2为在钢包中喂铝线和投铝块2种工艺试验时检测的残铝量情况。
表2 钢包喂铝线和投铝块残铝检测结果炉次终脱氧炉内加铝块量/kg t-1残铝/%包内加铝(块/线)量/kg t-1残铝/%包内加铝收得率/%包内加铝平均收得率/%2-59380.01660.02413.72-59480.01260.016 6.9投铝块炉次2-59680.01050.02020.615.8 1-53640.00770.02222.11-53750.00660.01515.52-60240.00650.04070.12-60350.00850.04882.5喂铝线炉次2-60530.00540.02654.167.5 1-54040.00760.04868.31-54140.00540.03062.5(下转第28页)21 钢包吹氩喂铝线工艺的应用3.3 新工装定位的优点从新工装的结构原理和使用步骤可知,不需要多少组装经验,也不用反复测量、反复调整即可对牵引拉杆座梁进行定位,而且整个过程只需1~2名铆工,大大提高了工作效率,同时也保证了工件的定位精度。
(1)与传统辅助工装杆相比较,新工装的定位精度高,并且解决了传统辅助工装杆不能定位高度尺寸715.5mm和705.5mm的缺憾。
(2)用新工装定位减轻了操作者的劳动强度,组焊所需的工时定额会下降,从而提高了组焊效率,降低了机车制造成本。
(3)用新工装定位提高了操作者的安全性,组装定位时操作者与天车配合,只需小撬棍和手锤即可完成牵引拉杆座梁的定位,避免了烤火调修或者野蛮作业。
(4)新工装具有很好的柔性,可通过更换支臂的位置或样杆的尺寸满足多车型牵引拉杆座梁的焊接定位。
4 结束语工装投入使用后,通过2个批次试验证明,新工装操作简易,不但很好地保证4对牵引拉杆座梁定位精度,而且工件质量稳定,不会随人员因素变化而波动,没有出现定位尺寸超差的返工返修。
同时,新工装还大大地减轻了操作者的劳动强度。
总之,在新制一定批量的机车时,利用该工装对牵引拉杆座梁焊接进行定位,能够获得较好的经济效益和社会效益。
∀(编辑:施翠燕)(上接第21页)表3为小批量生产中残铝含量分布对比情况。
表4为小批量生产中钢的性能检测统计对比表。
表3 小批量生产中残铝含量分布对比情况w(A l)含量范围/%<0.020.020~0.030.03~0.040.04~0.050.05~0.06总 计加铝块炉次炉数/炉398451264204比例/%19.141.22512.7 2.0100喂铝线炉次炉数/炉05857010170比例/%0 2.95041.2 5.9100由表2、表3可知,包内喂铝线炉次,铝的收得率高于投铝块炉次50%,耗铝低,每吨钢节省0.4kg铝以上;包内喂铝线炉次在减少了铝的加入量的前提下,残铝含量高,易控制在要求范围。
表4 生产小批量炉次性能检测统计对比炉数 屈服强度/M Pa抗拉强度/M Pa延伸率/%断面收缩率/%冲击功/J100炉喂线34153727.24962 100炉未喂线34354026.74649由表4可见,小批量(100炉)生产检测表明,强度稍有下降,塑性、冲击上升,综合机械性能上升。
综上所述,喂铝线炉次,铝收得率高,钢水残铝易于控制在工艺要求范围,比较稳定;而且耗铝量低;气体、夹杂有所降低,综合机械性能有所上升。
4 结论(1)采用钢包吹氩喂铝线工艺,能有效的降低钢中的氧和钢中的非金属夹杂物含量。
(2)采用钢包喂铝线取代钢包投铝块,能有效的提高铝的收得率,控制残铝在要求范围,既节约成本又提高产品质量。
(3)钢包吹氩喂铝线投资小,设备改动小,操作简便,便于推广使用。
∀(编辑:施翠燕)28工装设备 机车车辆工艺 第3期2007年6月。