赛络纺纱单股疵点的防治措施
技术|如何减少纺纱过程中的纱疵

技术|如何减少纺纱过程中的纱疵随着客户对纱线质量要求的不断提高,纺纱企业必须把纱疵控制在正常的范围内,目前影响布面质量的有害疵点主要有粗节、细节、条干不匀、飞花、棉结和异常疵点等。
通过规范生产操作,注重设备维护保养、工艺调整和质量控制,可以将纱疵控制在正常范围内。
长期以来在成纱质量中,纱疵是纺纱过程中一个难以解决的重要问题,它严重影响了成纱的质量,也给后道针织和机织纱的用户造成了一定的损失。
一、纱疵分类根据纱疵出现的几率可分为常发性纱疵和偶发性纱疵。
常发性纱疵一般为棉结、短粗节和细节。
常发性纱疵短而小、小而多 ,一般对后工序的加工和织物影响不大 ,通常不易清除彻底 ,但对高档织物也必须控制常发性纱疵的数量。
偶发性纱疵通常是突然发生、覆盖面较广、危害较大,也叫突发性纱疵。
偶发性纱疵一般都表现为粗大、细长,该类纱疵大部分是由于生产管理不善、操作不良、设备完好及专件运转状态不良、工艺设计不合理所致。
该类纱疵大而少,但对后道工序和织物质量影响显著,所以必须清除。
纺纱企业常见的偶发性纱疵主要包括短粗节、棉结杂质、毛羽增加及条干类疵点。
在生产过程中,偶发性纱疵往往随某些影响因素的改变而突然出现,迅速波及生产线上的部分品种或区域,使某些质量指标出现较大幅度的波动。
偶发性纱疵的数量从总体上来说不是很多,但危害较大,往往会造成成纱、坯布质量降等,影响织机效率,因此是纺纱生产过程中质量控制的重要工作之一。
二、减少突发性纱疵的措施1、合理配置工艺参数改善半成品的内在质量减少纺部半成品纱疵可以有效地降低细纱千锭时断头率,从而提高产量,稳定成纱质量,降低吨纱成本,为提升企业产品竞争力创造有利条件。
梳棉工序:定期检查牵伸齿形带、圈条齿形带的张力状态和磨损情况,合理调整圈条张力,在减少圈条器拥堵的同时可以降低并条导条架断头的几率。
如气流纺车间前纺梳棉细支生产线改粗支生产线时,通过工艺优选,调整定量、速度与棉网张力的相互关系,减少了梳棉断头、接头的次数,提高了梳棉生产效率,既减轻了工人劳动强度,又改善了半成品条子质量。
纺纱过程中出现的问题及解决措施

纺纱过程中出现的问题及解决措施纺纱疵点及解决措施1. 纱线不匀原因:原料品质不佳、梳理不充分、牵伸不均匀、锭子质量差解决措施:采用优质原料、加强梳理、优化牵伸工艺、更换或维修锭子2. 毛羽原因:原料纤维过短、梳理不足、牵伸过度、加捻不当解决措施:选用较长纤维原料、加强梳理、调整牵伸工艺、优化加捻参数3. 太紧原因:牵伸过大、加捻过多、锭子调整不当解决措施:减少牵伸倍数、降低加捻强度、调整锭子4. 太松原因:牵伸不足、加捻过少、锭子调整不当解决措施:增加牵伸倍数、提高加捻强度、调整锭子5. 粗细不均原因:原料纤维粗细不均、牵伸不均匀、加捻不均匀解决措施:选用均匀原料、优化牵伸工艺、调整加捻参数6. 结头原因:原料中有杂质、梳理不充分、牵伸不均匀、加捻过大解决措施:去除原料中的杂质、加强梳理、优化牵伸工艺、降低加捻强度7. 条痕原因:原料染色不均匀、混纺原料不匹配、牵伸不均匀、加捻不均匀解决措施:均匀染色原料、选择匹配的混纺原料、优化牵伸工艺、调整加捻参数8. 花疵原因:原料中有杂色纤维、梳理不充分、牵伸不均匀、加捻不均匀解决措施:去除原料中的杂色纤维、加强梳理、优化牵伸工艺、调整加捻参数9. 脆硬原因:原料纤维成熟度差、梳理不足、加捻过度解决措施:选用成熟度高的原料纤维、加强梳理、降低加捻强度10. 棉结原因:原料中有棉结、梳理不充分、牵伸不均匀、加捻过大解决措施:去除原料中的棉结、加强梳理、优化牵伸工艺、降低加捻强度11. 裂口原因:原料纤维强度低、梳理过度、牵伸过大、加捻过大解决措施:选用强度高的原料纤维、加强梳理、优化牵伸工艺、降低加捻强度12. 僵硬原因:原料纤维弹性差、梳理不足、牵伸过大、加捻过度解决措施:选用弹性好的原料纤维、加强梳理、优化牵伸工艺、降低加捻强度13. 刺毛原因:原料纤维中含有短纤维、梳理不足、牵伸不均匀、加捻过度解决措施:去除原料中的短纤维、加强梳理、优化牵伸工艺、降低加捻强度14. 络筒时断头原因:原料强度低、梳理不足、牵伸不均匀、加捻不足、络筒张力过大解决措施:选用强度高的原料纤维、加强梳理、优化牵伸工艺、调整加捻参数、降低络筒张力。
纱疵分析及预防

纱疵分析与预防第一章:概述一、纱疵的定义纱疵顾名思义是指纱的疵点,也就是指在纺纱生产过程中所产生的疵点,由原纱产生的疵点,织入布面反映在布面上的统称为布面纱疵。
布面纱疵包括影响棉布降等的疵点和不影响降等的疵点。
后者有的可以修复,有的不能修复,有时对后加工和成品也会产生不良影响。
二、消除纱疵的重要性:纱疵直接影响棉布的在质量和外观质量,如:规律性错纬不仅影响棉布外观,而且对棉布的强力也有很大的影响,因此,布面纱疵是评定棉布质量品等的主要依据之一。
棉布的分等是由物理指标、棉结杂质与布面疵点(包括纱疵与织疵)相结合进行评定的。
布面疵点的多少直接影响棉布的下机一等品率和入库一等品率两项质量指标。
有些纱疵虽然评分不会使棉布降等,但也影响棉布的外观,需要在验布中作出标识,进行修织。
这不但要花费大量的人力和物力,而且修织后常会造成在质量的不良,影响棉布的使用效果。
纱疵、织疵多,是当前棉布质量主要问题之一,是影响棉布出口竞争能力的关键。
棉布走向国际市场,必须大力降低纱疵。
三、纱疵的分类1、按出现的规律分(1)随机产生的、零星出现的随机性纱疵,大多数无明显规律。
(2)突然发生的、大批出现的突发性纱疵,大多数有一定的规律。
2、按其形成纱疵的原因分(1)因单位长度重量变异形成的纱疵①长片段重量变异形成的纱疵包括错纬、粗经等,②短片段重量变异形成的纱疵包括条干不匀、竹节等,(2)因纱线捻度变异形成的纱疵包括紧捻、弱捻、纬缩等,(3)因纱线色差变异形成的纱疵包括油经、油纬、油花纱、煤灰纱、色经、色纬等,(4)因纱线卷绕成形变异造成的纱疵包括脱纬、稀纬(5)其它与纺纱有关或间接影响的纱疵,如接头、棉球、烂边等,3、按其形成的工序分(1)清梳车间形成的纱疵,主要有异纤、花经、花纬、布开花等,(2)前纺车间形成的纱疵主要有片段较长的错纬、粗节长度较长的竹节、长片段条干不匀等,(3)细纱车间形成的纱疵主要有错纬、条干不匀、竹节纱、紧捻、弱捻及因管纱成形不良造成的脱纬、稀纬等疵点,(4)后加工形成的纱疵,主要有多股、因紧捻纱形成的错纬等,(5)其它部门形成的纱疵,如因空调组温湿度控制不良造成的煤灰纱等。
常见疵点的形成及预防

常见疵点的形成及预防一、断经在经纱循环中,缺少一至数根经纱使布面正常纹路改变,呈经向稀条状的疵点,称为断经。
1.产生原因:①断经自停装置失灵,经纱断头后未能及时停车。
②停经片内有积花、回丝等缠绕,使断经后的停经片不能下落,或经纱断头后被邻近经纱缠绕,甚至被邻纱带入其它综眼,织入布面。
③综丝耳环被损坏,在综上下滑动过程中将经纱挂断。
④导剑钩磨损,在经纬相互交织时,将此处经纱磨断。
⑤半制品质量较差,如经纱上有棉织、杂质、飞花、回丝及并头、绞头等。
⑥工艺参数配置不合理,后梁位置过高,吊经状态不好。
2.预防办法②加强巡回检查经纱,及时清除纱上有害疵点。
②合理调整工艺参数,使吊综状态正常。
③校正停经机构,使其作用灵敏。
二、断疵经纱断头后,其纱尾织入布面内,称为断疵,其形成原因和预防办法同断经织疵。
三、经缩由于经纱张力不一致,在经纬交织过程中,布面上呈现出有条状或块状的凹凸不平的绉纱状疵点,称为经缩。
经缩又称经缩浪纹或经缩波纹。
1、产生原因①经纱毛绒过长,经纱上有棉球、大结头,回丝附着织轴上的倒断头、绞头等半制品疵点,造成经纱之间紧紧的纠缠,使经纱张力呈现忽紧忽松现象而产生经缩。
②有少数经纱张力松弛,特别是了机松纱。
2、预防办法①提高半制品质量,大力减少经纱上有害纱疵。
②合理调整经纱张力,使其大小适当。
四、吊经因紧经纱造成的经纱无屈曲、破坏、织物丰满度的现象,通常称为吊经织疵,形成原因及预防办法同经缩织疵。
五、松经部分经纱张力小于其它正常经纱时,张力小的经纱在布面上呈现松弛现象称为松经。
1、形成原因①织轴中经纱的小辫子(气股)、倒断头以及脱头现象。
②断经自停装置失灵,当经纱断在停经片前后时形成机前一段经纱松驰。
③处理绞头或对接结头时,个别经纱张力调节不当,造成松经。
④准备车间、整经工操作不慎,造成经轴卷泡,形成连续松经。
2、预防办法①提高各工种挡车工的操作水平。
②校正停经机构,使其灵敏。
六、跳花和跳纱三根及以上的经纬纱相互脱离组织,并列跳成规律和不规律的浮在布面上呈网状的称为跳花;三要以下的经纱或纬纱跳过五根及以上的纬纱或经纱浮现布面呈线状的称为跳纱。
纱线主要疵点成因分析与改善措施

纱线主要疵点成因分析与改善措施对于纯棉精梳细号纱线,从危害程度和发生频次看影响布面的有害疵点主要是粗节、细节、条干不匀、飞花、棉结和异常疵点。
为切实满足客户的要求和控制质量成本,纺纱厂必须找到纺纱生产过程中形成这些疵点的原因,并采取有效的措施控制降低疵点,从而提高纱线的质量。
粗节、细节1成因常见的布面粗节长短不等:1 cm~2 cm居多,中间粗两头渐细,大多为细纱牵伸不良、牵伸区周围游离飞花附入、粗纱条干片断不匀、粗纱疵点附入、络筒清纱参数设置不当等原因造成;少部分为细纱接头不良或络筒机捻结不良造成。
细节主要是由细纱牵伸不良和络筒捻结不良造成。
2措施对于细纱牵伸不良引起的粗节、细节,可从以下四方面预防和解决:a)降低粗纱捻度,即在不增加断头的前提下尽量采用小的粗纱捻度;b)保证细纱和粗纱牵伸元件状态良好,保持适当的胶辊研磨周期、胶圈更换周期,并随时检查是否有起槽、划痕等问题,随时解决;c)保持恒定的温湿度,避免出现短时大幅度的波动;d)优化细纱工艺,主要是隔距、上销位置和摇架压力的一致性。
对于细纱纺纱过程中产生的粗节和细节,只能利用络筒清纱器切除,这样会引起清纱器切次的增加,需要特别关注捻接质量避免因捻接不良二次形成粗节和细节。
条干不匀1成因布面呈现有规律或无规律的条干阴影;主要因牵伸元件(胶辊、胶圈、罗拉)运转失常、表面毛糙凹凸、胶辊缠花纺纱及落后锭子等纺纱专件异常造成。
2措施牵伸区工艺优化、保持良好的胶辊胶圈状态;控制好单并与粗纱的号数偏差和条干均匀度,发现异常及时隔离;及时修理细纱的坏锭及异常锭,要求挡车工走巡回遇到胶辊、胶圈、罗拉等异常情况及时报告并通知相关人员处理。
在络筒机上对清纱器设置支数变异和珠链纱疵剪切和报警参数,可切除疵点并剔出有问题的管纱。
飞花1成因纺纱生产中因清洁不及时、集棉装置故障、断头急剧增加、空调温湿度异常或气流不畅等情况引起机台上、地面和空气中飞花增加并集聚,纺纱时附入到纱体中形成飞花疵点。
常见纱线瑕疵点成因及解决办法
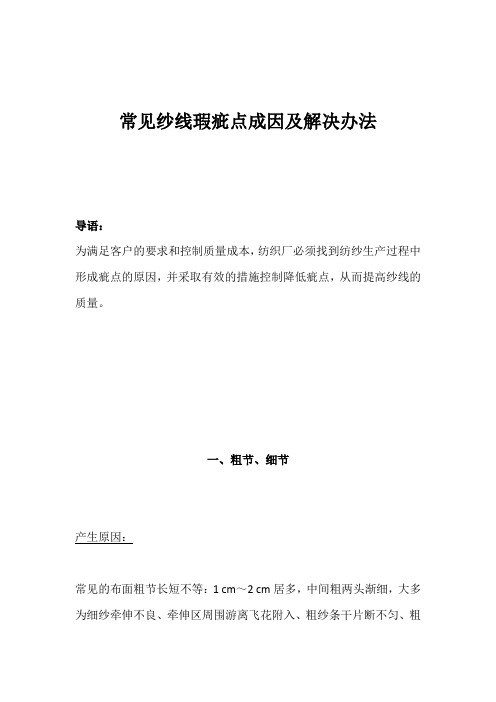
常见纱线瑕疵点成因及解决办法导语:为满足客户的要求和控制质量成本,纺织厂必须找到纺纱生产过程中形成疵点的原因,并采取有效的措施控制降低疵点,从而提高纱线的质量。
一、粗节、细节产生原因:常见的布面粗节长短不等:1 cm~2 cm居多,中间粗两头渐细,大多为细纱牵伸不良、牵伸区周围游离飞花附入、粗纱条干片断不匀、粗纱疵点附入、络筒清纱参数设置不当等原因造成;少部分为细纱接头不良或络筒机捻接不良造成。
主要是由细纱牵伸不良和络筒捻接不良造成。
解决措施:对于细纱牵伸不良引起的粗节、细节,可从以下4方面预防和解决:1)降低粗纱捻度,即在不增加断头的前提下尽量采用小的粗纱捻度;2)保证细纱和粗纱牵伸元件状态良好,保持适当的胶辊研磨周期、胶圈更换周期,并随时检查是否有起槽、划痕等问题,随时解决;3)保持恒定的温湿度,避免出现短时大幅度的波动;4)优化细纱工艺,主要是隔距、上销位置和摇架压力的一致性。
对于细纱纺纱过程中产生的粗节和细节,只能利用络筒清纱器切除,这样会引起清纱器切次的增加,需要特别关注捻接质量,避免因捻接不良二次形成粗节和细节。
二、条干不匀产生原因:布面呈现有规律或无规律的条干阴影;主要因牵伸元件(胶辊、胶圈、罗拉)运转失常、表面毛糙凹凸、胶辊缠花纺纱及落后锭子等纺纱专件异常造成。
解决措施:1)牵伸区工艺优化、保持良好的胶辊胶圈状态;2)控制好单并与粗纱的号数偏差和条干均匀度,发现异常及时隔离;3)及时修理细纱的坏锭及异常锭,要求挡车工走巡回遇到胶辊、胶圈、罗拉等异常情况及时报告并通知相关人员处理;4)在络筒机上对清纱器设置号数变异和珠链纱疵剪切和报警参数,可切除疵点并剔出有问题的管纱。
试述两种纱疵的分类、影响因素及控制措施
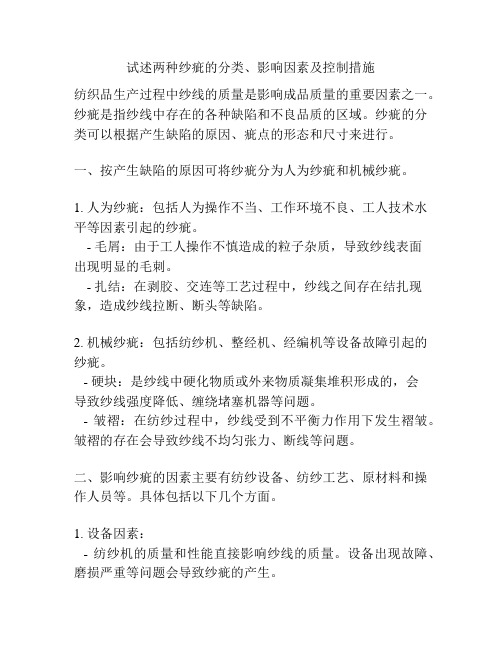
试述两种纱疵的分类、影响因素及控制措施纺织品生产过程中纱线的质量是影响成品质量的重要因素之一。
纱疵是指纱线中存在的各种缺陷和不良品质的区域。
纱疵的分类可以根据产生缺陷的原因、疵点的形态和尺寸来进行。
一、按产生缺陷的原因可将纱疵分为人为纱疵和机械纱疵。
1. 人为纱疵:包括人为操作不当、工作环境不良、工人技术水平等因素引起的纱疵。
- 毛屑:由于工人操作不慎造成的粒子杂质,导致纱线表面出现明显的毛刺。
- 扎结:在剥胶、交连等工艺过程中,纱线之间存在结扎现象,造成纱线拉断、断头等缺陷。
2. 机械纱疵:包括纺纱机、整经机、经编机等设备故障引起的纱疵。
- 硬块:是纱线中硬化物质或外来物质凝集堆积形成的,会导致纱线强度降低、缠绕堵塞机器等问题。
- 皱褶:在纺纱过程中,纱线受到不平衡力作用下发生褶皱。
皱褶的存在会导致纱线不均匀张力、断线等问题。
二、影响纱疵的因素主要有纺纱设备、纺纱工艺、原材料和操作人员等。
具体包括以下几个方面。
1. 设备因素:- 纺纱机的质量和性能直接影响纱线的质量。
设备出现故障、磨损严重等问题会导致纱疵的产生。
- 设备的调试和维护不当,使机器无法正常工作,增加了纱疵的概率。
2. 工艺因素:- 纱线的处理工艺中,各个工序的操作参数设置不合理,如张力、速度、温度等,会引起纺纱过程中的一系列问题,产生纱疵。
- 合理的工艺流程应根据不同纱线的要求进行调整,确保纱线的质量。
3. 原材料因素:- 原材料的质量影响纺纱品质,如原棉、切片、涤纶短纤等。
不同原材料的质量差异会导致不同的纱疵问题。
4. 操作人员因素:- 操作人员对设备的操作技术和纱线的质量要求程度也是影响纱疵产生的因素。
技术水平不高、操作不规范的工人容易导致纱线出现各类缺陷。
三、控制纱疵的措施主要从以下几个方面入手。
1. 提高设备质量和维护:- 选购质量可靠、性能稳定的设备,并定期进行维护与保养。
2. 严格控制工艺参数:- 在纺纱过程中,严格控制张力、温度、湿度等工艺参数,合理调整工艺流程,确保纺纱过程稳定。
织疵的产生原因及消除方法
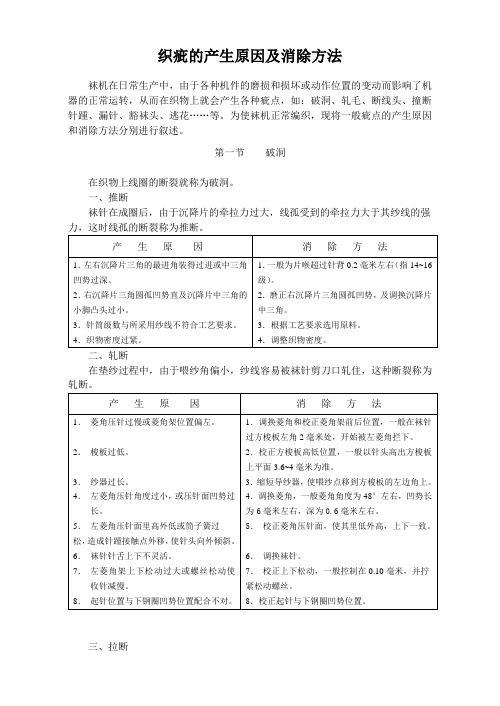
织疵的产生原因及消除方法袜机在日常生产中,由于各种机件的磨损和损坏或动作位置的变动而影响了机器的正常运转,从而在织物上就会产生各种疵点,如:破洞、轧毛、断线头、撞断针踵、漏针、豁袜头、逃花……等。
为使袜机正常编织,现将一般疵点的产生原因和消除方法分别进行叙述。
第一节破洞在织物上线圈的断裂就称为破洞。
一、推断袜针在成圈后,由于沉降片的牵拉力过大,线孤受到的牵拉力大于其纱线的强二、轧断在垫纱过程中,由于喂纱角偏小,纱线容易被袜针剪刀口轧住,这种断裂称为三、拉断在成圈过程中,由于线弧受到的张力超过其纱线的强力,这时线弧的断裂称为拉断。
四、顶断袜针成圈后,由于沉降片牵拉滞后或牵拉不足,使袜针上升时,其针头顶住旧线圈而造成纱线断裂,称为顶断。
袜针沿起针镶板上升,使针钩内的线圈移到针杆较粗的位置,由于线圈长度小六、缝合圈的轧碎(俗称缝头眼子轧碎)袜头编织结束,开始编织缝合圈时,由于机件配合不良,使个别缝合圈线弧被拉断,这种疵点称为缝合圈轧碎。
其他产生原因参看前面《拉断》的内容。
第二节合罗纹后编织平针时的疵点一、罗纹口虚环以及轧碎当罗纹口合好后,由于喂线过早,造成针钩内余线过长,在部分袜针上形成不规则的虚环,称为罗纹口虚环;这段虚环在第二转成圈时容易产生拉断,这一部位二、罗纹口漏针以及豁口当罗纹合好后,开始喂纱时,由于成圈机件配合不当,使第一只长踵袜针没有三、罗纹口花针(吊针)当罗纹合好后,在第一转成圈时,由于某些成圈机件配合不当,使部分袜针上的老线圈没有退圈,针钩内同时存在两根线弧,在第二转中脱圈,这种疵点,称为罗纹口花针。
第三节撞针在袜子编织过程中,由于某些机件的磨损或机件间相对尺寸配合不好,造成袜针、提花片、底脚片及沉降片与机件撞击的现象,称为撞针。
一、在编织袜统时袜针针踵的撞断二、在编织袜头跟时撞断长踵袜针。
三、在编织袜头跟时撞断短踵袜针。
四、菱角架进出时撞断长踵袜针。
六、提花片片踵及提花片齿撞断。
七、沉降片踵撞断第四节袜身疵点一、纵向条纹又称稀紧路。
纺纱过程中纱疵成因及防治

响 严重 , 纺 纱厂应 该严 格控 制的对 象 。 是
12 长粗节 . 是 指纱 疵 截 面积 比正 常纱 线 +4 % 上 , 5 长
Pr c s i g Pr c i e o r to Co b d Fi i h Co nt r o e sn a tc f Pu e Co t n m e ne H g u s Ya n
纱也 能满 足针织 用纱 对 布面纱疵 的要 求 了 。
1 纱 疵分类
习惯上 , 们将鸟斯特条干仪测出来 的三节 我 ( ) 为技 术性 纱疵 , 将 纱疵 分 级仪 测 出的纱 结 称 而
收 8朔 0 10 —1 2 o —92 作者简升 一 束树彬 (9 3 ) 男. 16 一 , 山东邹平凡 . 助理工程师 。
维普资讯
2 o 年第 1 02 期
山 东 坊 织 科 技
・ I 2・
纺纱过程 中纱疵 成 因及防治
宋树彬 骆世杰 张 志亮 龚 , , , 钧。
(. 1高青流云纺织有限责任公司 , 山东 高青 2 6 0 ;. 岛大学 . 5 30 2青 山东 青岛 26 7 ) 60 1
疵即 1 o万米纱疵 称 为管理性 纱疵 。 术性纱 疵 的 技 多 少主 要取决 于原 料 、 工艺 及设备 。 管理性 纱疵 而
纱疵是 指 在纺纱 过程 中产 生的疵 点 。纱疵 的 存在, 不仅 影 响到 纱 线质 量 及纺 纱 厂 的 生产 效 率 而且 也影响 棉布 的 等级 。国家现 行考 核 棉纱 的质 量标 准 ( / 9- 9 ) 规 定 了评 为 优 等纱 的 GB T38 3 中 应另 加 1 O万米 纱疵 一项 作为分 等指 标 。 因此 对 于
摘
要: 分析 纺妙 过 程 中纱疵 形 成 的原 因 , 过 实践 提 出有效 的解决 方 法 。 通
赛络纺纱应注意的几个问题

工 业 ,0 8,5 8 4 7 4 1 2 0 5 ( ):6 _7 .
参考 文献 :
状 况过 程 中找 出机 构 部 件 之 中可能 存 在 的 问题 ,
通 过 分 析 可 逐 步 改 进 相 关 部 件 的 工 作 状 态 从 而 预
知 改 进 的 结 果 , 出 改 良措 施 。 提 革新 改造 ・
[ ] 于 修 业. 纱 原 理 [ . 京 : 国纺 织 出 版社 , 5 纺 M] 北 中
() 确保两 根粗纱条的平行喂入 , 4要 防止 须
条 间交叉 重叠 或 两 根粗 纱 喂入 到 一 个 喇 叭 口, 影 响赛 络纱 的 风 格 。注 意 做好 双 孔 喇 叭 口的清 洁 。 防 止 因 喇 叭 口清 洁 不 良 或 塞 花 影 响 粗 纱 须 条 正 常
小 三角加 捻 区合 并 成 一 个 大 三角 加 捻 区 , 捻 后 加 形 成类 似股 线 结 构 的赛 络 纱 。赛 络 纱 比较 紧 密 ,
毛 羽少 , 观 光 洁 , 磨 性 好 , 感 柔 软 , 干 C 外 抗 手 条 V 和 强 力 指 标 比 同纱 号 股 线 稍 低 , 同 纱 号 单 纱 高 , 比
喂 人或破 坏粗 纱须 条 的 内在 结构 。 () 强把关 , 5加 防止 单 股 纱 流 人 到 下 工 序 。
纱 条 干恶 化 ; 距 过小 , 络 纱 结 构不 明显 , 纱 问 赛 成
毛 羽 增 加 。 可 依 据 条 干 、 力 和 毛 羽 指 标 试 验 结 强 果 进 行 对 比优 选 。 我 公 司 生 产 C2 . e 7 8t x赛 络 纱
常见织疵形成的原因及预防措施
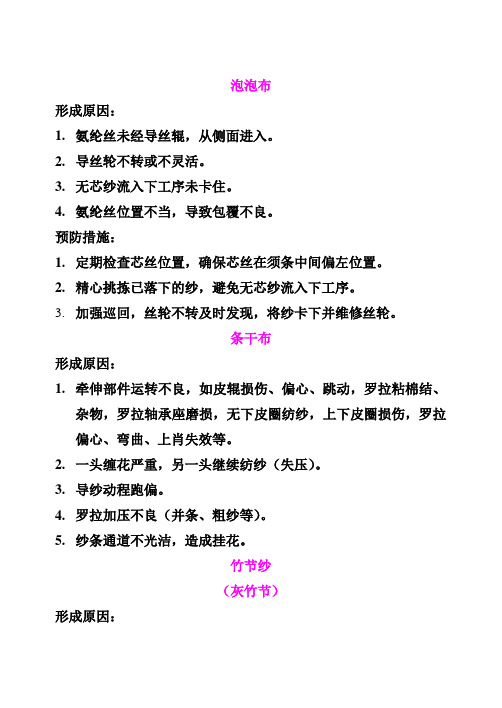
泡泡布形成原因:1.氨纶丝未经导丝辊,从侧面进入。
2.导丝轮不转或不灵活。
3.无芯纱流入下工序未卡住。
4.氨纶丝位置不当,导致包覆不良。
预防措施:1.定期检查芯丝位置,确保芯丝在须条中间偏左位置。
2.精心挑拣已落下的纱,避免无芯纱流入下工序。
3.加强巡回,丝轮不转及时发现,将纱卡下并维修丝轮。
条干布形成原因:1.牵伸部件运转不良,如皮辊损伤、偏心、跳动,罗拉粘棉结、杂物,罗拉轴承座磨损,无下皮圈纺纱,上下皮圈损伤,罗拉偏心、弯曲、上肖失效等。
2.一头缠花严重,另一头继续纺纱(失压)。
3.导纱动程跑偏。
4.罗拉加压不良(并条、粗纱等)。
5.纱条通道不光洁,造成挂花。
竹节纱(灰竹节)形成原因:1.清梳工序漏底花堆积太多,带入棉层。
2.各工序通道粘、缠、挂、堵带入(三角区、龙头,并粗、细纱牵伸通道)3.绒板、绒套、绒辊花带入(并条、粗纱、精梳、细纱)。
4.高空清洁积花掉入半成品或正在纺纱机内。
5.各工序清洁方法不当。
6.卡疵把关不严,疵点流入下工序。
7.清洁不彻底(例如粗纱斜坡、车面清洁不及时,巡回吹吸风吹入,打擦板时的飞花卷入纱条等)。
8.各工序揩车不良,油飞花粘附纱条,半成品棉条、粗纱掉地,造成污染。
三丝疵布形成原因:1.拣花间未拣净,后工序未卡住。
2.个别员工在工作场所梳头,清洁工具破损掉毛仍在使用。
应对措施:1.加强员工拣色杂责任心教育,后续工序严格执行卡疵把关制度。
2.加强管理,严格要求,杜绝在工作场所梳头现象;同时,车间定期对清洁工具检查,发现掉毛立即停止使用。
粗经、粗纬形成原因:1.粗纱断头、烂纱后未及时停车,飘入邻纱未处理干净。
2.条子粘连,机后换条子破条或机后双条喂入。
3.接头不符合操作法要求(并条、粗纱、细纱等工序)。
4.细纱断头飘入邻纱(主要是混纺纱)5.细纱续粗纱或粗纱纱尾飘入邻纱,细纱机车顶板的粗纱尾巴下垂,被卷入上排粗纱。
疵点条子形成原因:粗细条:生条:1、棉卷片段重量差异大或粘卷、破洞、头码过厚、双层卷。
整经减少疵点措施

整经减少疵点措施摘要本文档介绍了在纺织品整经过程中减少疵点的措施。
首先,我们将简要介绍整经过程和疵点的定义。
随后,我们将提出一些减少疵点的常用方法,包括优化设备操作、改进原材料选择、完善质量管理等。
最后,我们还将探讨一些新兴技术和创新方法,以期进一步提高整经质量并降低疵点。
1. 简介整经是纺织品生产中的关键工序,它涉及将经纱根据设计要求穿过织机的梭口,形成纺织品的经向结构。
然而,整经过程中常常会产生一些疵点,这些疵点包括断纱、缺纱、打耳边、扭纱等。
疵点不仅影响纺织品的外观质量,还有可能导致织物的力学性能下降。
因此,减少疵点是纺织企业追求高质量产品的重要目标之一。
在整经工艺中采取一系列措施可以有效降低疵点的发生率。
下面将介绍一些常用的措施。
2. 减少疵点的常用方法2.1 优化设备操作设备操作是整经过程中最重要的环节之一。
通过优化设备操作,可以减少疵点的发生。
以下是一些常用的优化设备操作的方法:•合理调整整经机参数:包括张力、速度、卷绕角度等。
合理调整这些参数可以减少断纱等疵点的发生。
•定期维护设备:包括清洁设备、更换磨损部件等。
定期维护设备可以确保设备正常运行,减少因设备故障引起的疵点。
•加强设备操作培训:培训操作人员,使其熟悉设备的操作和维护,提高工作技能,减少操作操作不当导致的疵点。
2.2 改进原材料选择原材料的选择对整经质量以及疵点的产生有着重要影响。
以下是一些改进原材料选择的方法:•丝线品质检测:对经纱进行丝线品质检测,包括拉力检测、扭力检测等。
只选择质量好、稳定性高的经纱,可以有效减少疵点。
•优化纱线结构:通过调整纱线结构参数,如纱线的织度、捻度等,可以改变纱线的物理性能,降低疵点的发生。
•优先选择疵点少的原料:了解供应商的原材料质量,并优先选择质量稳定、疵点少的原材料,以提高整经质量。
2.3 完善质量管理质量管理是减少疵点的关键环节,通过质量管理的完善,可以提高整经质量,并降低疵点的发生率。
避免赛络纺单根粗纱纺纱的几项措施

图4 棉纤维滑纤图4 结论通过改变包芯纱生产中芯纱与棉须条放置位置的方法,在细纱机上可直接纺制C 10t e x㊁C18.3t e x ㊁C27.8t e x 等不同号数的纯棉无捻纱㊂这种方法比常规(退捻法)的无捻纱纺制方法简单;采用该方法纺制无捻纱(Z 捻纱)时,在前罗拉喂入口处,必须保证R12t e x 长丝放置在棉须条的右侧,并与棉须条靠在一起,且最好是使用没有加捻的R12t e x 长丝;细纱机用锭子需更换为捻线机用可刹车锭子,采用捻线机接头方式解决R12t e x 长丝断头时出现的接头问题,并以前罗拉合适的速度来调整纺纱车速以防车速过快;络筒接头时需用织布结,同时必须清除掉管纱头㊁尾段纱,以保证最终成纱不出现退捻现象㊂参考文献:[1] 刘荣清,张伟敏.包芯纱的纺制[J ].纺织导报,2008(10):70-73.[2] 王同勇.导丝器对氨纶包芯纱包覆效果的影响[J ].上海纺织科技,1997,25(4):11-13.㊃革新改造㊃避免赛络纺单根粗纱纺纱的几项措施与普通环锭纺纱相比,赛络纺纱的粗纱定量相对偏轻,需要增加一倍的吊锭和导纱杆等;在粗纱退绕过程中,其退绕拉伸角度也相对普通环锭纺纱的小,容易出现单根粗纱纺纱现象㊂造成单根粗纱纺纱的主要原因可以分为设备和工艺两个方面㊂我们公司通过做好以下几个方面的工作,较好地避免了单根粗纱纺纱现象,提高了最终成纱质量㊂设备基础工作方面㊂纺赛络纺品种的机台,一定要按照周期进行部分保全,做好锭子㊁锭带盘的周期性加油工作,及时解决运转不正常的锭子,保证所有锭子运转良好;校正好锭带进出尺寸,确保锭带居中运行,锭带重锤刻度要保证一致(可用拉力弹簧秤拉好定刻度),不允许重锤松动;确保摇架压力一致;保证钳口隔距校正一致;保证吊锭灵活且一致㊂另外,要缩短细纱揩车周期和胶辊㊁胶圈调换周期㊂工艺方面㊂由于粗纱定量偏轻,粗纱捻系数相对纺普通环锭纺纱时要大15%~20%,而且粗纱捻系数设计要与细纱前后区隔距相适应,细纱后区牵伸倍数一定要小,在1.08倍~1.12倍之间,这也是避免纺赛络纱出现单根粗纱纺纱的一项重要措施㊂同时,钳口隔距也要与所纺纱线号数相适应;控制细纱锭速在合理范围;选择合适的钢丝圈型号㊂胶辊选用方面㊂选择合适的细纱前后胶辊(包括硬度㊁直径㊁胶辊表面处理方式等),纺纯粘胶赛络纺品种时宜选择邵尔硬度A 67度J -466型免处理胶辊,对其进行1∶10板涂,其防缠绕效果较好㊂细纱机台大揩车周期为每月一次,并随调大揩车周期调换胶辊和胶圈,保证成纱质量㊂操作方面㊂粗纱卷装直径不宜太大,以减少意外伸长造成的细节;内外排粗纱要结合搭条喂入同一个喇叭口,减少重量不匀率;严禁粗纱交叉㊁重叠喂入,加强牵伸区清洁,减少罗拉绕花和喇叭口积花㊂同时,自动络筒机电子清纱器参数设置时也要比纺环锭纺纱严格,特别是错号纱设置要更为严格,防止单根粗纱纺的纱卷绕到筒子上㊂经过生产实践证明,采取以上技术措施,对避免出现单根粗纱纺纱现象㊁提高最终成纱质量效果明显㊂浙江杭州精纱纺织有限公司张友平 韩新珍】56【第47卷 第12期2019年12月C o t t o nT e x t i l eT e c h n o l o g y =================================================。
JC7.38tex赛络集聚纱的质量控制措施

Qu a l i t y C o n t r o l Me a s u r e s o f J C 7 . 3 8 t e x S i r o C o n d e n s e d Ya r n
o Ha i b பைடு நூலகம் n
[ - S a u r e r( J i a n g s u )T e x t i l e Ma c h i n e r y C o . , I . t d . . J i a n g s u S u z b o u , 2 1 5 0 2 6 1
化进行操作 , 合理 科 学控 制 车 间 温 湿 度 等 , 顺 利 纺 制 出符 合 质 量 要 求 的 纱 。认 为 : 结合 车 间管理工作 , 在 纺 制 纯
棉 细 号 纱 的 过 程 中形 成 一 套 成 熟 工 艺 与技 术路 线 , 有 助 于 纯棉 细 号 纱 品 质 的提 高 。
[ 卓 郎( 江苏) 纺织机 械有限公司 , 江苏 苏 州 , 2 1 5 o z G 2
摘要: 探讨J 7 . 3 8 t e x赛络 集聚纱的工艺设 计和质量控 制措施 。J c 7 . 3 8 t e x赛络集 聚纱要依 据马 克
隆值 、 长度、 整 齐度 、 单纤维长度等指标来进行配棉 , 优 选 工 艺参 数 , 做好 设备 的维护 与保养 工作 , 严格按 照规 范
绒棉 的 马克 隆值应 选择 在 3 . 9 6 左右 , 既能 保证 成 熟度 , 又 能保证 纱 线截 面 内纤 维 的根 数 ; 细 绒棉 的 马克 隆值 应选 择在 4 . 2 5 ~4 . 4 5 , 保 证 配棉 的纤 维 粗细 合适 的 同时 , 也 可 以承 受后 道 工 序 对 纤 维 的
紧密赛络纺成纱疵品率的降低措施

紧密赛络纺成纱疵品率的降低措施侯小伟【摘要】以精梳棉27.8 tex甲配棉品种的纺制为例,探讨影响紧密赛络纺疵品率的因素.分析了吊锭间距不一致、粗纱更换不及时、网格圈周期性清洁不当及网格圈张力架弹簧失效因素对成纱疵品率的影响.研究表明,通过确保吊锭间距适当,及时更换粗纱,周期性清洁网格圈,对失效的网格圈张力架弹簧进行及时更换等措施,可有效降低紧密赛络纺成纱的疵品率.%The factors that affect the defect rate of JC 27.8 A were discussed.How the factors, such as the inconsistency of the spacing of spindles, the failure to replace the roving, the improper cleaning of the lattice apron,and the spring failure of the lattice frame influenced the defect rate were analyzed.The research showed that by ensuring appropriate distance between the spindles, replacement the roving timely, cleaning the lattice apron periodically, and replacement the failed grid ring dancer spring without delay, the defect rate of yarn could be reduced effectively.【期刊名称】《国际纺织导报》【年(卷),期】2017(045)003【总页数】5页(P22-26)【关键词】紧密赛络纺;疵品率;网格圈【作者】侯小伟【作者单位】泰山学院美术学院(中国)【正文语种】中文紧密赛络纺技术作为改善纱线品质的一种新型环锭纺纱方式,越来越受到人们的关注。
常见细纱疵点及产生原因

错支
粗纱用错,筒管用错,后皮辊加压失效
加强巡回检查,通知检修工处理
交于小组长统一处理
煤灰纱
室外空气浊度大,空气中的微粒进入纺纱车间
1.空调室做好恶劣天气预警工作。
严重偏心的单锭巡回中应及时拔出大小管纱记录大小并通知检修碰钢领板纱由当班处理拉去碰烂纱段方可投入下工序实锭脚回丝多造成冒纱工处理跳管单锭应及时处理拉去锭脚回丝若是纱管问题更换纱管重新生成形不良视情节在不影响络筒工序生产下投入下道使用否则须拉清不良粗纱用错筒管用错后皮辊加压失效加强巡回检查通知检修工处理交于小组长统一处室外空气浊度大空气中的微粒进入纺纱车间细纱提前落纱缩短纺纱时间
3.加快接头速度
4..及时处理锭子回丝
属锭带脱落,应拔出同带四锭管纱,集中送下工序处理。
毛羽纱
1.钢丝圈型号不当(过轻)
2.钢领不良
3.歪锭子
4.相对湿度较低
1.使用正确的钢丝圈型号
2.发现不良及时调换
3.通知维修工效正
4.控制好相对温湿度
交由小组集中,送下工序处理。
棉球(满天星)
钢丝圈磨灭
更换钢丝圈,遇到机台多锭满天星应记录,便于常日班检查钢领、钢丝圈周期。
2.细纱提前落纱,缩短纺纱时间。
按照煤灰纱污染程度分别处理
1.单锭导纱动程距皮辊边缘应大于3毫米。否则空锭,通知检修工处理。
2.及时掀起摇架、逐锭处理。
3.去除杂质。
4.更换裂损皮圈,无皮圈更换时,空锭处理。
5.空锭,通知检修工处理。
6.及时更换皮辊。
7.皮辊压力失效,钳爪位不正时,空锭通知检修工处理。
8.及时停机反馈。
纱疵的 防治文稿

纱疵的控制
第一部分 概述
纱疵在我们工作中是一个比较重要的问题,它 不仅影响了络筒机的生产效率、成本(回丝)的增 加等不良现象,而且也是客户反馈率最高的一项, 所以我们有必要去研究它。下面我想从什么是纱疵, 电清的认识和纱疵的预防三部分与大家一起研究。
第二部分 纱疵
一、纱疵的定义 在纺纱过程中形成的疵点称为纱疵 纱疵。纱疵实际上是与 纱疵 纱线的横截面大小紧密相联的。一般而言,正常纱的横截 面粗细变化大致在其平均纱线横截面的±50%范围以内。 这种正常的横截面粗细变化不是纱疵,而称为纱线的不匀 (也称条干不匀)。如果纱线的横截面粗细变化超出了正常 纱不匀的±50%范围,而且在某一段突然变得很粗(细), 或者逐渐变粗(细),这些是电清要消除的纱疵。
第五部分 结论
只要我们明确好产品的用途和要 求,充分发挥电清作用,用心做好 基础工作,纱疵问题一定能控制在 所要达到的质量要求。
三、纱疵的分级(23级)
1、纱疵的分级示意图
400 250 150 100 F 45 0.1 ﹣30% ﹣45% ﹣75% 1 2 4 8 H1 H2 32 I1 I2 ∞ G A4 A3 A2 A1 B4 B3 B2 B1 C4 C3 C2 C1 D4 D3 D2 D1 E
- 1、下载文档前请自行甄别文档内容的完整性,平台不提供额外的编辑、内容补充、找答案等附加服务。
- 2、"仅部分预览"的文档,不可在线预览部分如存在完整性等问题,可反馈申请退款(可完整预览的文档不适用该条件!)。
- 3、如文档侵犯您的权益,请联系客服反馈,我们会尽快为您处理(人工客服工作时间:9:00-18:30)。
数 允 许 和 正 常 牵 伸 的 前 提 下 , 可 以偏 大 设 计 。 均
胶 圈钳 口隔距宜 在 确 保 正 常牵 伸 条 件 下 , 当偏 适 小掌握 , 以利 于成纱 条干 和强力 。 ( ) 化 操 作 管 理 , 少 单 股 纱 疵 点 。要 加 4强 减 强巡 回 , 时换 粗 纱 , 及 防止 空粗 纱 ; 及 时发 现 并 要 处 理粗 纱 断头 ; 除喂 入 粗纱 中条 干不 匀 、 剔 细节 、
的 长 细 节 疵 点 , 产 品 质 量 影 响 较 大 。 由 于 纺 纱 对
1 3 ~14倍 为宜 。 喂 人 喇 叭 口间距 是 影 响 赛 .倍 . 络纺 质量 与断 头 的关 键 因素 , 根 据所 纺 品种 及 应 原料 情况合 理选 择 , 以减 少 粗 纱 断头 。粗 纱 定 量 与捻 度设计 对单 股 纱 疵 关 系 较 大 , 细纱 牵 伸倍 在
挥 瞌饵 技 术
【3 】 ・ 8 6 7 4・ C t nT xi e h o g ot e teT c n l y o l o
第 3 8卷第 1 2期 来自21 0 0年 1 2月
・
革 新 改造 ・
赛 络 纺纱 单 股 疵 点 的 防 治 措 施
棉纺 赛络 纱生 产 中易 产 生 细节 , 特别 是 单 股
张力 较低 , 纺赛 络 纺 推 荐使 用 机 械 式 断 头 白停 毛
装置 难 以推 广使 用 。 断头 后 粗 纱需 要 重 新 穿 头 ,
操作 十分 麻烦 。经过 反 复 实 践 与摸 索 , 们 针 对 我
单 股 疵 点 产 生 的 原 因 采 取 措 施 , 到 了 较 好 的 效 收 果 , 简单 介绍 如下 。 现
制 在 一 O × 0Ol 上 。 3 % 1 l 以 f 上 海 裕 丰 科 贸有 限 公 司 , 张 伟 敏 刘 荣 清
加压 偏重 掌握 , 赛络 纺条 干较好 , 牵伸一 般可 比 总
纺 传统 环 锭 纱 加 大 2 % ~3 % 。后 区牵 伸 不 宜 0 0
太大 , 以防牵 伸 力 骤 增 而 出 现牵 伸 不 良。一 般 以
异 物 等 疵 点 , 少 粗 纱 断 头 ; 现 纱 号 偏 细 或 单 股 减 发
() 1 防止单 根粗 纱跑 空 。可 推 行 集 体或 分 段
同 时 换 粗 纱 , 灭 空 粗 纱 断 头 。 粗 纱 简 脚 纱 推 荐 消
采用 Y O 2 WF 12型粗 纱 纱 尾 清 除机 。处 理 后 的短
强调 , 成 主次 不分 。罗拉 隔距 宜适 当放 大 , 拉 造 罗
电子清纱 器测 定 信号 的原 理 属 于相 对 测 量 , 疵 纱
直径 或截 面 的平均值 只有 相对 值 , 有绝 对值 , 没 这
种 电子清 纱器 只能 对信 号 突变 的纱 疵进 行 截 除 ,
对纱 疵信 号逐 渐变 化或 切除后 未重 新接 上 的长 细 或 长粗纱 疵 不起作 用 。 因此 必须 选用具 有绝对 测 量 功能 的 、 敏 度 较 高 的 电子 清 纱器 。我们 曾采 灵 用 D S一 Q S2型 电子清纱 器 , 因属 于 相 对 测量 型 , 对 长 细 节无 法 辨 别 、 除 , 清 易造 成 质量 纠 纷 , 改用 后 D S. Q S5型 的绝 对测 量 型电子 清纱 器 , 此类 质量 问 题 迎 刃而解 。一 般赛 络纺 的长 细节清 纱 门限应控
绒增 加率 小于 1 , 以 同号纱 回用 。 % 可
() 2 防止 吊锭不 良造 成 单 根 粗纱 断头 。粗 纱
吊锭 要 求 回转 灵 活 而 有 合 适 的 阻 尼 。 如 果 回 转 太 灵 活 , 造成 粗 纱 退 出太 多 而 断头 ; 果 不灵 活 , 会 如
纱 时要将 其去 除 ; 落 纱 都要 检 查 成 形偏 细 的管 每
纱, 发现后 应及 时拣 出处 理 。
( ) 用 合 适 的 电 子 清 纱 器 。 一 般 普 及 型 的 5选
则会 造 成引 出拉 断 。 () 3 合理 配 置 工 艺 , 绝 牵 伸 不 良造 成 单 根 杜 粗 纱 断头或 因粗纱 质量 不 良造成 的单 根断 头 。一 般赛 络 纺两根 有捻 粗纱 的牵 伸力 远大 于环锭 纺一 根 粗纱 的牵 伸力 , 因此 较易 产生 牵伸不 良现 象 , 导 致 单根 粗纱 断头 。赛络 纺工 艺参 数 的选择应 以保 证 正 常 牵 伸 , 少 断 头 为 基 本 前 提 , 络纱 的条 减 赛 干、 毛羽 、 裂 强 度均 优 于传 统 环 锭纺 , 断 不必 过 于