磨机端面裂纹原因分析 处理方法 论文
磨床磨削裂纹原因的分析与对策

磨床磨削裂纹的产生原因分析与对策分析磨削裂纹的产生原因,与磨削前各加工过程所产生的缺陷,如材料表层中存在网状碳化物、非金属夹杂、组织疏松、成分偏析、晶界上的淬火变形等有关;裂纹通常与烧伤同时出现。
当工件表层的残余拉应力超过材料的抗拉强度时,就会产生磨削裂纹。
磨削裂纹的产生原因和减小磨削裂纹的方法如下:1、正确选用砂轮,例如可采用颗粒较粗、较软、组织较疏松的砂轮;保证修整后砂轮的锋利。
2、保证磨削时的冷却条件,设法使冷却液能有效地渗透到工件的磨削区中。
3、合理选择磨削用量,例如提高工件的转速,采用较小的径向进给量等。
磨削时如果磨削工艺参数选择或操作不当,工件表面温度达到150~200度时表面因马氏体分解,体积缩小,而中心马氏体不收缩,使表层承受拉应力而开裂,产生的裂纹会与磨削方向垂直,裂纹相互平行。
当磨削温度在200度以上时,表面由于产生索氏体或托氏体,这时表层发生体积收缩,而中心则不收缩,使表层拉应力超过脆断抗力而出现龟裂现象。
4、工件表面渗层碳浓度过高,会使工件表面产生过多的残余奥氏体.从而容易导致产生烧伤和裂纹。
因此,表面碳浓度增加,则降低了磨削性能,一般表面碳浓度应控制在0.75%-0.95%范围以内。
5、碳化物分布应均匀,粒度平均直径不大于0.001m;碳化物形态应为球状、粉状或细点状沿网分布,不允许有网状或角状碳化物。
6、热处理时.表面或环境保护不当会产生表面氧化,这样在工件上就会产生一层薄的脱碳层,这层软的脱碳层会引起砂轮过载或过热,从而造成表面回火,工件磨削时容易出现裂纹。
7、如果冷却不充分,磨削时零件表面温度有时可能高达820~840度或更高,则由于磨削形成的热量足以使表面薄层重新奥氏体化,并再次淬火而形成淬火马氏体,表面形成二次淬火的金相组织。
此外,磨削形成的热量使零件表面温度升高极快,这种组织应力和热应力导致磨削表面出现磨削裂纹。
8、使用金刚滚轮修整砂轮的内滚道磨床加工的零件有裂纹,还与配置的金刚滚转速、转向、金刚石的粒度、磨损情况、修砂轮时电主轴的转速、修砂轮时与滚轮磨合停留的时间等因素有关。
球磨机筒体端盖与筒体结合处开裂原因分析及处理办法

步扩散 , 有可能导致中空轴与简体脱离的严重后果。 接到该厂的求助通知 ,我们马上组织了有关的工程技术
人员赶赴现场作原因分析并讨论处理方案。经分析, 认为导致
可能产生裂纹的原因有以下几点:
1 材质问题。制造厂没有严格按照磨机制造工艺质量要 . 求控制生产 , 未能在开料前对钢板周边探伤, 取样进行化学成 分、 理化试验, 以确认板材各项指标均符合要求后再下料:因 此如果选材不符合技术要求或质量差,弯曲强度不够或钢板 内早有微小裂纹隐患 , 磨机简体和端盖在受反复交变应力作 用下表面产生纵横交叉的裂痕 , 导致疲劳断裂。
()大齿轮结构由原齿圈与幅板焊接式改为轮毂与齿圈 7
4 磨机在加工制造 、 . 运输和安装过程中不经意形成的
沟痕 , 产生了裂纹、 断裂。这种沟痕常常是无意中在磨机简
体或端盖材料中留下的, 如用錾子 、 洋冲或别的工具在简体 表面冲打、 刻划出沟槽等表面缺陷。再如用火焰割去焊死在 简体上的安装运输辅具时没有磨削平整且没有消除其表面
缺陷而形成沟痕。
空负荷试验 ( 旋向为正常工作旋转方向) 试验时经过测量记 。 录, 各轴承温度、 润滑油温 、 噪音、 振动及从观察孔处检查齿
螺栓联结组装结构( 如图 2 , )消除焊接应力等缺陷。
轮副啮合情况均正常, 符合技术要求。
(0 1)现场整机安装 、 调试 ( 按大型减速机有关要求规
端盖接合处产生裂纹。
齿 轮 连 接 法兰
6 .由于该磨机为熟料磨, 磨机作业时磨内温度高, 磨外温 度低, 磨机内外温差太大也会造成热应力, 进而加剧了裂纹的
扩展。
分析出上述原因后 , 我们马上讨论修复对策。经研究, 我 们制定了两套方案 第一种为优质修理方案: 把两主轴承座上 盖打开, 把整个回转部分拆卸下来, 拉回制造厂, 对简体裂纹 进行修复。 因修复后简体会产生一定的变形, 要重新上大卧车 对简体与中空轴连接面 、 简体与大齿轮连接面加工, 把中空轴 大平面 、 口及轴颈上立车机加工 ,把中空轴与简体的铰制 止 孔、 大齿轮与简体连接法兰的铰制孔重新铰制 , 然后重新组装
钢球磨煤机端盖裂纹修复技术

钢球磨煤机端盖裂纹修复技术摘要:对某电厂钢球磨煤机出口端盖出现长度达5100mm的贯穿性的裂纹进行分析,主要详细讲述裂纹修复技术,对球磨机使用单位的检修工作起到一定借鉴作用。
关键词:球磨机;端盖;裂纹;修复1 基本概况某440t/h电站锅炉采用球磨机、中间储仓式制粉系统,钢球磨煤机是电站锅炉的制粉系的重要设备之一,通过撞击、挤压、研磨或破碎等方法将煤磨制成粉,从而为电厂锅炉燃烧提供必需的燃料(1)。
球磨机为沈阳重机械集团有限责任公司生产的MTZ-32/58型钢球磨,筒体材质为ZG35,端盖壁厚100mm,该设备已使用13年。
2014年8月B侧磨煤机出口端盖发现漏粉现象,停运后发现位于轴颈与筒体联接圆弧过渡区域有裂纹,长度达5100mm,占整个圆周的4/5,筒体内部拆除衬板后,确认全部为贯穿性裂纹。
2 端盖出现裂纹原因分析磨煤机端盖在制造过程当中,会存在残余应力。
安装后磨煤机端盖长期承受磨煤机筒体及筒内钢球、煤粉等重量,端盖中分面以上部位将受到挤压作用力,中分面以下部位将受到拉作用力,磨煤机转动时,端盖受力也不断的反复变化,经过长期运行,有残余应力的地方最终发展成为疲劳源,最终产生裂纹。
3 裂纹修复处理技术(1)处理前必须对筒体加固处理措施,即将磨煤机出口端筒体第1、2圈衬瓦拆除,用12号槽钢6条进行米字型支撑,再同规格的槽钢在米字架与出口端盖之间进行支撑加固。
(2)对端盖内侧进行矫正,保证内侧齐平,不得有错口现象。
在筒体内侧制作一螺杆拉紧装置(见图1),将端盖裂纹最大错口处(#1螺栓孔对应)向内拉平,打百分表找正,控制在1.5mm。
(3)端面错口校正后对端盖进行加固处理,加固位置端盖内侧3、6、9、12区(见图2),采用300×100×30mm的钢板。
(4)修复前原始数据的测量:将磨煤机进口轴颈按螺旋管螺栓孔等分16等份,在出口轴颈两侧各装两个百分表(如图3所示),用以测量轴颈各等份的径向和轴向数据变化情况,并做好记录,然后根据测量的数据算出轴肩的张口程度。
球磨机焊接修复端盖裂纹的一例

球磨机焊接修复端盖裂纹的一例某发电厂3号机组锅炉为原苏联生产的THE22l/C系列HE670/140型锅炉,配有2台7T[BM370/850型钢球磨煤机。
磨煤机的出人口端盖和大罐焊为一体,如图l所示。
端盖直径为3500mm,端盖中部带有空心轴,简体用两端的空心轴支撑在2个下端为球面支撑面的大瓦上,大罐空心轴外径2000mm,球面瓦宽700mm,端盖内壁衬有波浪形钢瓦,端盖与轴瓦之间用M45x230mm螺栓连接。
端盖最大厚度为120mm,材质为ZG35。
某次该炉的4l号磨煤机停运时发现人口端盖空心轴根部的圆周方向螺孔与螺孔之间产生裂纹,裂纹总长度约2.8m,占空心轴根部圆周长度的40%。
为了防止裂纹继续扩展,导致空心轴根部断裂而损坏磨煤机,该厂决定在现场不拆卸端盖进行端盖裂纹的焊接修复。
进行焊接修复时,拆下钢瓦后发现人口端盖的内外壁已裂透,内壁裂纹长约1.8m.(1)该球磨机端盖为ZG35中碳钢铸件,结构庞大(直径3500mm厚度120mm),拘束度大,淬硬倾向高,易产生冷裂纹。
(2)端盖与大罐焊为一体,属动载结构。
要求焊接修复区域不仅有足够的静载强度而且要具有一定的抗低周疲劳性能,以满足端盖动载荷的要求。
(3)端盖为转动部件,焊接时必须防止发生轴向串动和径向振动,并应严格控制焊接修复后的焊接变形量。
对于大型铸钢部件裂纹的修复,传统的加工坡口方法是采用碳弧气刨消除裂纹和开制坡口,用该方法加工的坡口渗碳层厚度较大,给坡口的打磨工作带来很大困难,同时碳当量的提高使焊接性能降低,这样既降低了生产效率,又影响端盖裂纹焊接修复质量川。
因此,本次焊接修复工作采用G0l—300型专业氧—乙炔气刨(以下简称专用气刨)代替碳弧气刨刨除裂纹和开制坡口。
这样可以减少氧化渣量,避免渗碳层的出现,省略了打磨工序和焊前端盖预热工序,大大提高了生产效率。
为了降低端盖裂纹焊接修复后的变形量,应采用XStu形坡口,如图2所示。
采用多层多道焊和分段跳焊法,焊后用专用气动风铲跟踪锤击焊缝,进行热处理并且在热态下低速转动球磨机。
球磨机入口端盖裂纹原因分析及处理

1 球磨机技术参数及主要问题磨煤机运行已达25年,具体参数如表1所示。
通过检查发现,磨煤机入口端盖出现贯穿性裂纹,宽度达10~15mm ,最大错位17mm ,如图1所示;从空心轴外侧衬板螺栓处,裂纹沿中空轴端盖内圈周长5900mm ,横向裂纹有3道,分别为800mm 、700mm 和800mm 。
表1 磨煤机技术参数型号DTM350/600筒体长度/mm 3500转速/(rad/min )17.69筒体直径/mm 5980机器出力计算出力43.84;额定出力30入口端盖总重及材质总重11200kg ;材质ZG351图1 磨煤机入口端盖贯穿性裂纹情况2 球磨机裂纹原因分析磨煤机型式为DTM350/600筒式低速磨煤机,生产厂家是北京电力设备厂。
磨煤机入口端盖直径3500mm ,与大齿轮一起与筒体入口侧法兰联结;入口内部端面共安装3排端衬板,共计48块、96个螺孔;端盖端面厚度中外圈100mm ,内圈120mm ,材质为ZG35。
该球磨机使用时间已超过25年,属于超期服役,存在金属晶体变形、疲劳过载等情况,原磨煤机转向为顺时针旋转,4年前后更改为逆时针旋转;端盖连接螺栓在运行中出现过多次断裂,说明端盖受力已出现问题。
从现场端盖裂纹裂纹趋势看,裂纹贯穿整个螺孔,未进行止裂,说明局部受力过大,端盖已出现塑性变形。
3 处理过程根据现场检查情况,拆除入口端盖第1、2排衬板,进行裂纹修复;第3排只对出现裂纹部位衬板进行拆除,进行局部修复。
3.1 校正为使焊后变形量小,对端盖进行校正,将错位顶平。
第一,加固前的准备。
制作专用工具,使裂纹恢复,在恢复过程中,在空心轴颈两侧制作支架,采用采用磁力表座固定百分表检测空心轴的径向偏差,将磨机空心轴进行16等份,并一一对应检测,调整空心轴径向偏差,直至达到标准。
第二,检修规程规定。
大齿轮装配后的最大径向跳动<1.3mm ,轴向晃动<1.8mm ;大齿轮径向跳动在每1000mm 节圆直径上不大于0.25mm ;端面跳动在每1000mm 节圆直径上不大于0.35mm ;空心轴颈的最大径向跳动<1.0mm 。
磨削烧伤裂纹的产生及控制

磨削烧伤裂纹的产生及控制文章简述了磨齿的原理和方法,主要研究磨削裂纹的形态及产生裂纹的原因,及提出提高含碳量从标准的0.8%~0.9%提高到1%~2%。
并从热处理和冷加工方面,如工艺参数、冷却介质、工作环境,磨具等方面提出一系列防止磨齿裂纹的措施。
标签:磨削烧伤;裂纹;塑性变形;磨削余量;磨削用量磨齿是齿轮精加工的一种方法,磨齿不仅能纠正齿轮预加工产生的各项误差,而且能加工淬硬的齿轮,加工精度高。
1 磨齿的原理和方法锥砂轮磨齿原理。
在这里我们提到的都是指外齿轮,锥砂轮磨齿是按照齿轮和齿条的啮合原理进行的。
砂轮相当于假象齿条上的一个齿,齿轮的节圆沿齿条的节线作纯滚动。
被磨齿轮装在头架的主轴上,沿节线一面作横向往复移动,一面通过传动机构使被磨齿轮随主轴绕自身轴线作反复转动,被磨齿轮的移动和转动必须保持一定的相对关系,齿轮旋转一转,其移动距离应等于被磨齿轮节圆的圆周长,这样就可以磨出要求的渐开线齿形。
在磨斜齿轮时,砂轮和齿轮的相对运动相当于斜齿条的啮合原理进行的。
斜齿条的倾斜角等于斜齿轮的螺旋角,砂轮往复运动的斜线和齿轮轴线之间的夹角也应等于这一倾斜角;砂轮锥面的角度应等于斜齿条的法向齿形角。
磨完一个齿槽后,应进行分度磨下一个齿槽,工件的分度运动是当工件从一端展成到另一端时,进行一次分度,也可以进行双行程分度,即当工件展成一个往复后,进行一次分度。
为了磨出齿轮整个宽度上的齿面,砂轮还必须沿齿轮轴向进行往复运动。
2 磨齿烧伤裂纹的产生我们公司使用从德国引进的数控磨齿机,这种磨齿机的生产效率低于其他磨齿机,可以同时磨削轮齿的两面,砂轮刚性好,磨削用量也较大,所以难免产生磨削烧伤、裂纹。
这两种常见现象均属于磨齿工序的表面质量问题,它是由齿轮的材料、热处理的方式和磨削三个方面的原因所产生的现象。
从表面上看这一问题与生产效率相矛盾,然而没有质量就没有效益,这是我们都清楚的,众所周知的。
所以它是对应统一的关系。
磨齿过程中,裂纹主要是金属晶体产生塑性变形。
磨机端面裂纹的原因分析与处理方法

磨机端面裂纹的原因分析与处理方法我厂有一台Φ3.8*13m的水泥球磨机自2003年安装以来运转良好,但在2010年6月9日更换进料中空轴时发现磨机端面与中空轴联接的螺栓孔处有裂纹。
裂纹已经发展到了1080mm左右,但可以看出裂纹没有裂透。
我厂决定实施现场焊接修复工艺。
采用了特殊焊接工艺,有效的防止裂纹扩大,获得了满意的效果。
标签:筒体裂纹焊接坡口磨机筒体与中空轴由螺栓联接,在交变应力作用下连续运行是水泥磨机体的薄弱环节,筒体端面出现裂纹对球磨机以后的运转产生很大的影响。
本文主要介绍我厂对球磨机筒体端面出现裂纹的修补方法。
1 裂纹形成的原因这条裂纹长约1080mm,出现在筒体端面穿过螺栓孔,是一个应力集中的部位。
裂纹穿过5个螺栓孔,前后联接7个螺栓孔(如图1),由球磨机在运转过程中周期性的将交变载荷通过螺栓传到从裂纹的位置可以判断裂纹属于应力疲劳型的,裂纹的形成是由磨机在旋转过程由螺栓传给中空轴造成的。
2 确定修复方法采用J427Ni碳钢焊条,这种焊条具有优良的焊接工艺性能及良好的力学性能,低温冲击韧性好,飞溅少,脱渣易,焊接轻松,效率高,可进行全位置焊接。
焊接前,将焊条按要求烘干预热2-3h,温度200℃-350℃,然后,放在保温箱中保温,随用随取,每次取出量最多不能超过10根。
正刨逆焊,层与层之间必须搭接压缝,每层焊接正反向交替进行,选择直流反极性及小范围参数(焊条的许用电流为130~150A),焊接电流尽量采取许用电流的下限参数。
由于是多层焊接,第1层焊缝易出现裂纹,选用小电流低焊速焊接。
2.1 开坡口为了减少金属的填充量,选用较小的坡口角度,采用单面“U”型坡口的型式。
端面厚为100mm,采用内外都开坡口,先在外面开深60mm宽600mm 的坡口(等外面坡口焊好后在从内壁错开开深60mm宽600mm的坡口,这样焊缝就能有效的结合,如图2)。
开坡口采用碳弧气刨,使用Φ8mm的碳棒,电焊机采用硅整流直流电焊机(GS-500SS),接法为反接,焊接电流为240~400A,压缩空气为0.6~0.7MPa,沿裂纹进行气刨,气刨后用钢丝刷清理焊渣,最后用Φ150磨光机对坡口两侧内壁打磨修整,以除去渗碳层和清理坡口,达到施焊条件。
磨削裂纹产生的原因及措施

淬火工件磨削加工过程中,磨削部位容易产生浅、细长、肉眼几乎无法辨别的磨削裂纹,常见的磨削裂纹有三种形状:龟裂或网状裂纹、直线状和弧状。
磨削裂纹产生的原因是:
1、热处理
热处理过程中,淬火温度高,产生过热组织;回火不充分,存在较大的内应力和较多的残余奥氏体;渗碳件渗碳层中的网状碳化物析出严重等,造成工件在后续磨削过程中产生磨削裂纹。
3、如果已产生磨削裂纹,如果未超过加工余量,可进行多次低温回火,去除磨削应力,再按正确的磨削加工方法加工,磨去裂纹深度进行挽救。
2)正确选择砂轮结构和硬度级别,以获得自由磨削效应。
3)陶瓷和金属作粘结剂的砂轮,适用于磨削热较高的场合;树脂粘结砂轮,适用磨削热较小的场合。脆性较大的粘结剂,磨粒容易脱落,有利于使砂轮保持锐利状态。
4)SiC磨料磨削钢和铁基耐热合金时,产生强烈的化学磨损,刚玉类磨料磨削钢时无此反应。相反,刚玉类磨料磨削玻璃、硅酸盐类陶瓷涂层时,会产生强烈的化学反应,SiC磨料无此反应。
2、冷却
磨削过程中,工件表面瞬间温度高达820℃,冷却不充分时,磨削产生的热量会使磨削表面薄层重新奥氏体化,随后在自身基体的激冷作用下,再次淬火为马氏体,表面层产生附加的组织应力,磨削是交替重复过程,累计的拉应力超过Байду номын сангаас件表面抗拉强度时,会产生龟裂或网状裂纹。
3、磨削过程中进刀量过大
磨削进刀量太大,温度剧烈升高,表层达到约300℃左右,则发生第二次收缩,产生第二种磨削裂纹;与磨削方向基本垂直的、有规则排列条状裂纹。如果局部严重磨削烧伤出现,则产生弧形裂纹。
4、磨料选择
砂轮磨料种类有刚玉、碳化硅、金刚石、氮化硼等,当选择的与工件不匹配时,会产生裂纹。
磨削裂纹的控制措施是:
磨削裂纹的分析与对策
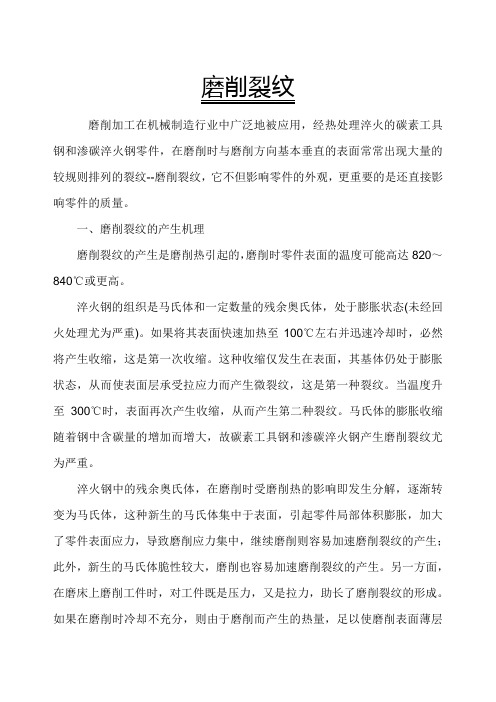
磨削裂纹磨削加工在机械制造行业中广泛地被应用,经热处理淬火的碳素工具钢和渗碳淬火钢零件,在磨削时与磨削方向基本垂直的表面常常出现大量的较规则排列的裂纹--磨削裂纹,它不但影响零件的外观,更重要的是还直接影响零件的质量。
一、磨削裂纹的产生机理磨削裂纹的产生是磨削热引起的,磨削时零件表面的温度可能高达820~840℃或更高。
淬火钢的组织是马氏体和一定数量的残余奥氏体,处于膨胀状态(未经回火处理尤为严重)。
如果将其表面快速加热至100℃左右并迅速冷却时,必然将产生收缩,这是第一次收缩。
这种收缩仅发生在表面,其基体仍处于膨胀状态,从而使表面层承受拉应力而产生微裂纹,这是第一种裂纹。
当温度升至300℃时,表面再次产生收缩,从而产生第二种裂纹。
马氏体的膨胀收缩随着钢中含碳量的增加而增大,故碳素工具钢和渗碳淬火钢产生磨削裂纹尤为严重。
淬火钢中的残余奥氏体,在磨削时受磨削热的影响即发生分解,逐渐转变为马氏体,这种新生的马氏体集中于表面,引起零件局部体积膨胀,加大了零件表面应力,导致磨削应力集中,继续磨削则容易加速磨削裂纹的产生;此外,新生的马氏体脆性较大,磨削也容易加速磨削裂纹的产生。
另一方面,在磨床上磨削工件时,对工件既是压力,又是拉力,助长了磨削裂纹的形成。
如果在磨削时冷却不充分,则由于磨削而产生的热量,足以使磨削表面薄层重新奥氏体化,随后再次淬火成为淬火马氏体。
因而使表面层产生附加的组织应力,再加上磨削所形成的热量使零件表面的温度升高极快,这种组织应力和热应力的迭加就可能导致磨削表面出现磨削裂纹。
二、磨削裂纹的特征磨削裂纹与一般淬火裂纹明显不同,磨削裂纹只发生在磨削面上,深度较浅,且深度基本一致。
较轻的磨削裂纹垂直于或接近垂直于磨削方向的平行线,且规则排列的条状裂纹,这是第一种裂纹。
较严重的裂纹显龟甲状(封闭网络状),其深度大致为0.03-0.15mm。
用酸腐蚀,裂纹明显易见。
这是第二种裂纹。
三、磨削裂纹的防止措施磨削工艺方面(1)磨削裂纹的产生是因为磨削热所致,所以降低磨削热是解决磨削裂纹的关键。
磨煤机大齿轮裂纹分析与处理
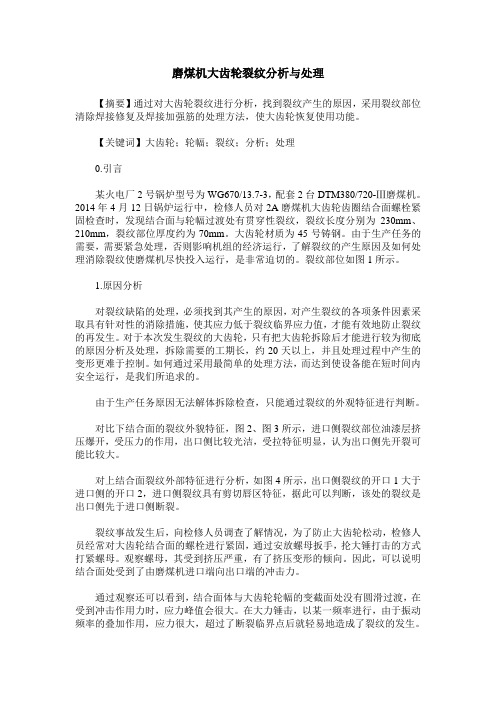
磨煤机大齿轮裂纹分析与处理【摘要】通过对大齿轮裂纹进行分析,找到裂纹产生的原因,采用裂纹部位清除焊接修复及焊接加强筋的处理方法,使大齿轮恢复使用功能。
【关键词】大齿轮;轮幅;裂纹;分析;处理0.引言某火电厂2号锅炉型号为WG670/13.7-3,配套2台DTM380/720-Ⅲ磨煤机。
2014年4月12日锅炉运行中,检修人员对2A磨煤机大齿轮齿圈结合面螺栓紧固检查时,发现结合面与轮幅过渡处有贯穿性裂纹,裂纹长度分别为230mm、210mm,裂纹部位厚度约为70mm。
大齿轮材质为45号铸钢。
由于生产任务的需要,需要紧急处理,否则影响机组的经济运行,了解裂纹的产生原因及如何处理消除裂纹使磨煤机尽快投入运行,是非常迫切的。
裂纹部位如图1所示。
1.原因分析对裂纹缺陷的处理,必须找到其产生的原因,对产生裂纹的各项条件因素采取具有针对性的消除措施,使其应力低于裂纹临界应力值,才能有效地防止裂纹的再发生。
对于本次发生裂纹的大齿轮,只有把大齿轮拆除后才能进行较为彻底的原因分析及处理,拆除需要的工期长,约20天以上,并且处理过程中产生的变形更难于控制。
如何通过采用最简单的处理方法,而达到使设备能在短时间内安全运行,是我们所追求的。
由于生产任务原因无法解体拆除检查,只能通过裂纹的外观特征进行判断。
对比下结合面的裂纹外貌特征,图2、图3所示,进口侧裂纹部位油漆层挤压爆开,受压力的作用,出口侧比较光洁,受拉特征明显,认为出口侧先开裂可能比较大。
对上结合面裂纹外部特征进行分析,如图4所示,出口侧裂纹的开口1大于进口侧的开口2,进口侧裂纹具有剪切唇区特征,据此可以判断,该处的裂纹是出口侧先于进口侧断裂。
裂纹事故发生后,向检修人员调查了解情况,为了防止大齿轮松动,检修人员经常对大齿轮结合面的螺栓进行紧固,通过安放螺母扳手,抡大锤打击的方式打紧螺母。
观察螺母,其受到挤压严重,有了挤压变形的倾向。
因此,可以说明结合面处受到了由磨煤机进口端向出口端的冲击力。
解决磨削裂纹的新思路、新途径
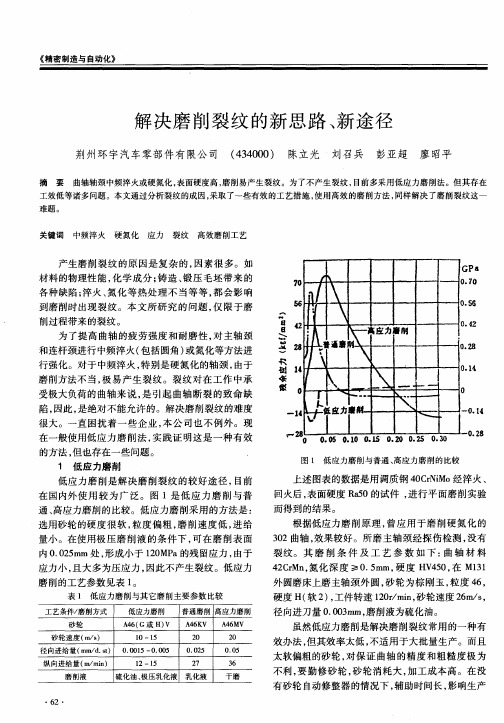
裂纹。
53 保持砂轮微刃锋利的方法是: . ①选用物理 性能好的磨料; ②勤修砂轮, 采用能自 动修整砂轮的
参考文献
[〕 1 孟少农主编,机械加工工艺手册》 ,, 章。 《 1 1 4 3 机械工业出 版社, 9 年 18 9 [〕 2 朱培瑜等著,淬火裂纹及磨削裂纹》 机械制造》1 3 《 《 ,8 年 9
1期 0
图2 冷却喷嘴
《 精密制造与自动化》
解决磨削裂纹的新思路、 新途径
荆州环宇汽车零部件有限公司 (300 陈立光 刘召兵 彭亚超 廖昭平 440 )
摘 要 曲轴轴颈中 频淬火或硬氮化, 表面硬度高, 磨削易产生裂纹。为了不产生裂纹, 前多采用低应力磨削法。 目 但其存在 工效低等诸多问题。本文通过分析裂纹的成因, 采取了一些有效的工艺措施, 使用高效的磨削方法, 同样解决了磨削裂纹这一
1 低应力磨削
渊 l\ ’ }
卜 通奋
。\ / \ } }
I、
训
1
I }} “m ”
i
\
人
‘. ̄. .一 习
一 { 入
戈}
a 卜 l }
{ 一 !
一I ‘
、 ̄
图1 低应力磨削与普通、 高应力磨削的比较
低应力磨削是解决磨削裂纹的较好途径, 目前 在国内外使用较为广泛。图 1 是低应力磨削与普 通、 高应力磨削的比较。低应力磨削采用的方法是: 选用砂轮的硬度很软, 粒度偏粗, 磨削速度低, 进给 量小。在使用极压磨削液的条件下, 可在磨削表面 内005 形成小于 10 P 的残留应力, . m处, 2m 2M a 由于 应力小, 且大多为压应力, 因此不产生裂纹。低应力 磨削的工艺参数见表 I o
DTM350600型球磨机端盖开裂原因分析及对策
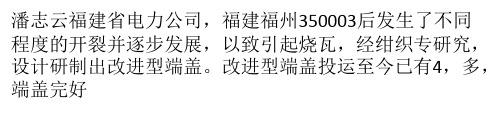
常,符合工厂标准2.2用应变电测法对0挪350600塑球磨机 的端盖进行现场应力测量,实测结果为在不旋转状态下, 轴颈根部轴颈和盖的连接处下方的最大拉应力为19.17,
3,上方最大压应力为12.073;而针对这种测试状态下的 有限元计算结果相应16.933和14.44河,3可,实测和计算 结果两者基本相符,结果是可信的用遥测位变仪实测
能维护即可满足业务变化的需要。在报装流程及工作单 流程设计中采用了标准模板思想,根据业务要求通过变 更模板来改变流程。它的主要功能子系统有报装电子系 统电量电费子系统用电
检查子系统电能计量子系统综合治理子系统综合查询子 系统领导查询子系统和多媒体查询咨询子系统。鉴定委 员会认为该系统结构合理,功能全面,界面友好,工作 可靠性较高,满足了用
比较密集的微缩孔,并打性断裂于焊接热裂纹,未焊透 等焊接缺陷在焊接残余应力及磨煤机夂变应力作用的结 果2.6从运行条件看,由于投产初期,燃用福建无烟煤锅 炉效率只有78左
右,为了满足燃烧要求,球磨机经常,天241连续满出力 运行,有的甚至加大钢球载,使球磨机处于超额定电流 下运行,再加上福建无烟煤硬度大,4磨性系数达1.4,为 了有利燃烧
,设计煤粉细度0为58,增加了煤粉磨制时间。这切都加 重了端盖的负担。由于福迮尤烟煤挥发分低,煤的荇火 温度高,难燃,因而热风温度高达400以上,使得磨煤机 进口风温尚,
将使端盖强度,所降低,裂纹萌生和扩展加快,这是般 电厂类磨的不同之处绽上所述,造成球磨机端盖开裂的 重要原因足焊接残余成力过大;铸造缺陷和焊接热裂纹 未焊透等焊接缺陷在焊
结束语改进型球磨机端盖于1995年6月首先在永安火电厂 9号磨使用,随后的43内对其余几台球磨机端盖全部更换 成上述改进型端盖。运行最长的至今已有43多,般都运 行233
20CrMnTi齿轮端面磨削裂纹原因分析
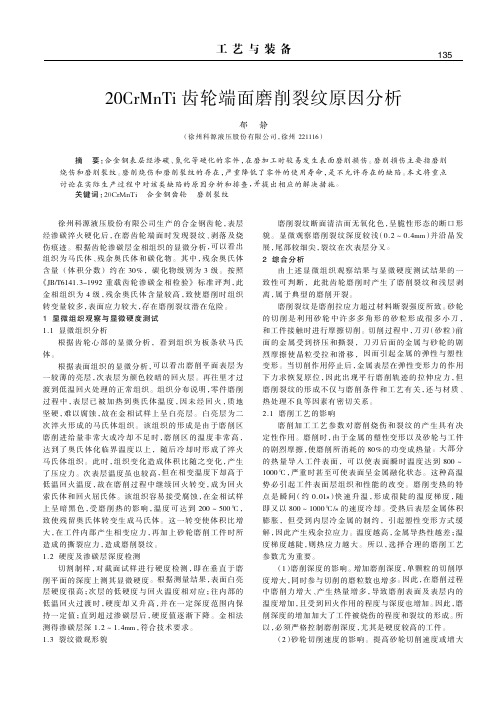
徐州科源液压股份有限公司生产的合金钢齿轮,表层经渗碳淬火硬化后,在磨齿轮端面时发现裂纹、剥落及烧伤痕迹。
根据齿轮渗碳层金相组织的显微分析,可以看出组织为马氏体、残余奥氏体和碳化物。
其中,残余奥氏体含量(体积分数)约在30%,碳化物级别为3级。
按照《JB/T6141.3-1992重载齿轮渗碳金相检验》标准评判,此金相组织为4级,残余奥氏体含量较高,致使磨削时组织转变量较多,表面应力较大,存在磨削裂纹潜在危险。
1显微组织观察与显微硬度测试1.1显微组织分析根据齿轮心部的显微分析,看到组织为板条状马氏体。
根据表面组织的显微分析,可以看出磨削平面表层为一较薄的亮层,次表层为颜色较暗的回火层。
再往里才过渡到低温回火处理的正常组织。
组织分布说明,零件磨削过程中,表层已被加热到奥氏体温度,因未经回火,质地坚硬,难以腐蚀,故在金相试样上呈白亮层。
白亮层为二次淬火形成的马氏体组织。
该组织的形成是由于磨削区磨削进给量非常大或冷却不足时,磨削区的温度非常高,达到了奥氏体化临界温度以上,随后冷却时形成了淬火马氏体组织。
此时,组织变化造成体积比随之变化,产生了压应力。
次表层温度虽也较高,但在相变温度下却高于低温回火温度,故在磨削过程中继续回火转变,成为回火索氏体和回火屈氏体。
该组织容易接受腐蚀,在金相试样上呈暗黑色,受磨削热的影响,温度可达到200~500℃,致使残留奥氏体转变生成马氏体。
这一转变使体积比增大,在工件内部产生相变应力,再加上砂轮磨削工件时所造成的撕裂应力,造成磨削裂纹。
1.2硬度及渗碳层深度检测切割制样,对截面试样进行硬度检测,即在垂直于磨削平面的深度上测其显微硬度。
根据测量结果,表面白亮层硬度很高;次层的低硬度与回火温度相对应;往内部的低温回火过渡时,硬度却又升高,并在一定深度范围内保持一定值;直到超过渗碳层后,硬度值逐渐下降。
金相法测得渗碳层深1.2~1.4mm ,符合技术要求。
1.3裂纹微观形貌磨削裂纹断面清洁而无氧化色,呈脆性形态的断口形貌。
磨削裂纹成因

摘要:采用光学显微镜、显微硬度计、扫描电镜等测试手段,对柴油机油泵阀磨削加工表面上的裂纹进行了分析。
得出,其裂纹系磨削不当造成的磨削裂纹。
对磨削造成的表面变质层的组织形态及硬度变化等进行了分析研究。
主题词:磨削裂纹磨削变质层白亮层1 引言磨削加工是机械零件制造中的常用工序,磨削过程中由于磨削力及磨削热的作用,工件表面的显微组织、成分及性能都可能发生变化。
工件表层不仅产生塑性变形,而且温度急剧升高,常可达数百摄氏度以上,有时甚至引起表层材料的局部熔融。
另一方面,在受冷却液及工件自身导热的作用下,工件表面又被急速冷却,即表层既被瞬时加热到高温,而又受到激冷。
因此,如果磨削工艺参数控制不当,很容易产生裂纹。
本工作以磨削加工后,经探伤发现有裂纹的柴油机油泵阀为研究对象,对裂纹进行分析研究。
柴油机油泵阀的材料为GCr15。
热处理工艺:850℃保温30min油淬,150℃回火2h(淬火后未经冰冷处理)。
2 测试方法及结果2.1 金相检验在裂纹处沿油泵阀横截面切割并制成金相试样,用4%HNO3酒精溶液侵蚀后在金相显微镜下观察,试样表层有一层白亮层,此为二次淬火马氏体;试样次表层侵蚀后颜色较深,为高温回火组织;心部为回火马氏体+碳化物,见图1和图2。
这说明在磨削过程中,磨削热使最表层温度升高到相变点Ac1以上,致使表层的组织重新奥氏体化,随后受到磨削液及工件自身的急速冷却作用,产生了二次淬火马氏体,它不易被侵蚀,呈亮白色。
从试样表层向里,温度逐渐降低,次表层温度接近Acl时,产生了高温回火,析出了大量碳化物,使之较易侵蚀。
在金相显微镜下可明显地看到在试样的表层组织(二次淬火马氏体)与心部组织(回火马氏体+碳化物)之间有一热影响区为高温回火组织。
图4为在金相显微镜下所见到的KnooP硬度压痕。
从图上压痕的大小可以看到,试样最表层的硬度最高,从表向里,硬度急剧降低,随之硬度慢慢升高趋于平和,其变化规律与图3吻合。
2.3扫描电镜分析(1) 裂纹观察用扫描电镜对磨削表面进行观察,裂纹形成于油泵阀尖角附近,并观察到两条基本平行的裂纹,见图5。
如何处理球磨机筒体开裂的问题
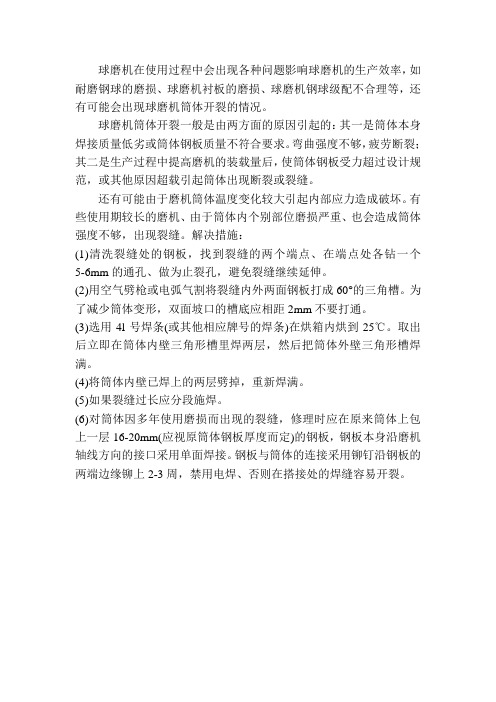
球磨机在使用过程中会出现各种问题影响球磨机的生产效率,如耐磨钢球的磨损、球磨机衬板的磨损、球磨机钢球级配不合理等,还有可能会出现球磨机筒体开裂的情况。
球磨机筒体开裂一般是由两方面的原因引起的:其一是筒体本身焊接质量低劣或筒体钢板质量不符合要求。
弯曲强度不够,疲劳断裂;其二是生产过程中提高磨机的装载量后,使筒体钢板受力超过设计规范,或其他原因超载引起筒体出现断裂或裂缝。
还有可能由于磨机筒体温度变化较大引起内部应力造成破坏。
有些使用期较长的磨机、由于筒体内个别部位磨损严重、也会造成筒体强度不够,出现裂缝。
解决措施:
(1)清洗裂缝处的钢板,找到裂缝的两个端点、在端点处各钻一个5-6mm的通孔、做为止裂孔,避免裂缝继续延伸。
(2)用空气劈枪或电弧气割将裂缝内外两面钢板打成60°的三角槽。
为了减少筒体变形,双面坡口的槽底应相距2mm不要打通。
(3)选用4l号焊条(或其他相应牌号的焊条)在烘箱内烘到25℃。
取出后立即在筒体内壁三角形槽里焊两层,然后把筒体外壁三角形槽焊满。
(4)将筒体内壁已焊上的两层劈掉,重新焊满。
(5)如果裂缝过长应分段施焊。
(6)对筒体因多年使用磨损而出现的裂缝,修理时应在原来筒体上包上一层16-20mm(应视原筒体钢板厚度而定)的钢板,钢板本身沿磨机轴线方向的接口采用单面焊接。
钢板与筒体的连接采用铆钉沿钢板的两端边缘铆上2-3周,禁用电焊、否则在搭接处的焊缝容易开裂。
锻造和热处理过程中裂纹形成原因分析

锻造和热处理过程中裂纹形成原因分析发布时间:2021-05-20T10:33:30.803Z 来源:《基层建设》2020年第31期作者:裴一飞[导读] 摘要:裂缝很常见,生产过程往往是锻造和热处理过程。
航空工业哈尔滨飞机工业集团有限公司黑龙江哈尔滨 150000摘要:裂缝很常见,生产过程往往是锻造和热处理过程。
锻造裂纹通常在高温下发生,在锻造过程中会延伸并接触空气,形成裂纹中氧化的皮肤。
此框形成的裂纹不仅厚而且多,裂纹的两端不相连,尖端相对圆。
所处理的裂纹的形状和性能与锻造裂纹不同。
出现热处理后的裂纹是因为加热时该元素出现裂纹,导致在裂纹的咸晶方向上脱碳,最终结构比锻造裂纹厚。
对于和零件尤其如此本文收集了大量裂缝方式,分析总结了裂缝的原因。
最后,裂缝分为三类。
关键词:锻造、热处理;裂纹形成原因;过程;存在缺陷;前言裂纹是锻造和热处理中常见的缺陷之一,也是锻造行业中的热点和难点。
但是,锻造零件产生裂纹的可能性很大,因此必须研究锻造和热处理过程中的裂纹,并分析裂纹的原因。
一、锻造缺陷与热处理缺陷过热燃烧。
过度燃烧意味着加热温度高,切割机又大又不均匀,没有金属光泽,玻璃周围有氧化和渗碳。
造成裂缝。
当锻造温度较高或最终温度较低时,容易产生裂纹。
另一个裂缝是在水的钻井和冷却后形成的。
缩小范围。
表面缺陷是冲压、切割、板材磨损、穿孔等造成的。
在随后的钻孔中,观察到锻造体中存在表面氧化等缺陷以形成折弯。
通过显微镜观察,你可以看到弯曲周围明显的碳流失。
过火裂缝。
这些裂缝大多发生在MCU改造后,因此裂缝周围的微观结构与其他区域没有显着差异,也没有渗碳。
二、实验方法1.试样制备和宏观观察在试验前的第一阶段,只需对所选杆的工件裂纹进行宏观观察,在观察过程中,选择要测量的区域。
下一步是手动剪切选定区域,使其垂直于镜像且长度小于10 mm。
采样方法可能会有所不同,但在采样时必须选择温度和环境。
如果样品温度过高,可以使用冷水冷却样品,以免由于样品在回收过程中过热而改变事件的内部组织。
磨削裂纹的产生
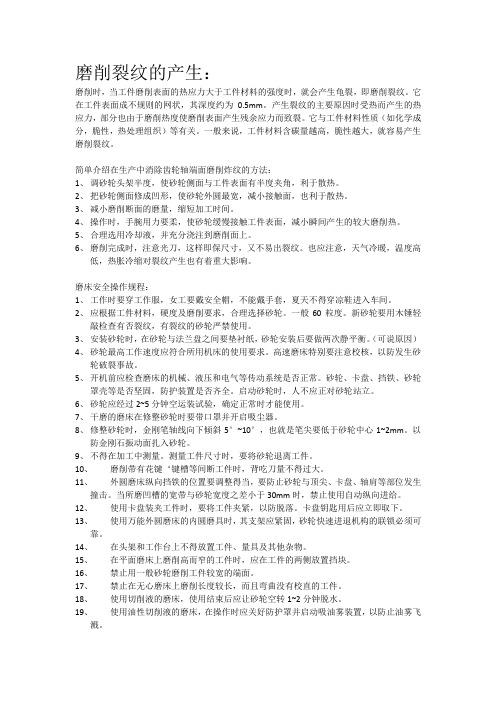
磨削裂纹的产生:磨削时,当工件磨削表面的热应力大于工件材料的强度时,就会产生龟裂,即磨削裂纹。
它在工件表面成不规则的网状,其深度约为0.5mm。
产生裂纹的主要原因时受热而产生的热应力,部分也由于磨削热度使磨削表面产生残余应力而致裂。
它与工件材料性质(如化学成分,脆性,热处理组织)等有关。
一般来说,工件材料含碳量越高,脆性越大,就容易产生磨削裂纹。
简单介绍在生产中消除齿轮轴端面磨削炸纹的方法:1、调砂轮头架半度,使砂轮侧面与工件表面有半度夹角,利于散热。
2、把砂轮侧面修成凹形,使砂轮外圆最宽,减小接触面,也利于散热。
3、减小磨削断面的磨量,缩短加工时间。
4、操作时,手腕用力要柔,使砂轮缓慢接触工件表面,减小瞬间产生的较大磨削热。
5、合理选用冷却液,并充分浇注到磨削面上。
6、磨削完成时,注意光刀,这样即保尺寸,又不易出裂纹。
也应注意,天气冷暖,温度高低,热胀冷缩对裂纹产生也有着重大影响。
磨床安全操作规程:1、工作时要穿工作服,女工要戴安全帽,不能戴手套,夏天不得穿凉鞋进入车间。
2、应根据工件材料,硬度及磨削要求,合理选择砂轮。
一般60粒度。
新砂轮要用木锤轻敲检查有否裂纹,有裂纹的砂轮严禁使用。
3、安装砂轮时,在砂轮与法兰盘之间要垫衬纸,砂轮安装后要做两次静平衡。
(可说原因)4、砂轮最高工作速度应符合所用机床的使用要求。
高速磨床特别要注意校核,以防发生砂轮破裂事故。
5、开机前应检查磨床的机械、液压和电气等传动系统是否正常。
砂轮、卡盘、挡铁、砂轮罩壳等是否坚固,防护装置是否齐全。
启动砂轮时,人不应正对砂轮站立。
6、砂轮应经过2~5分钟空运装试验,确定正常时才能使用。
7、干磨的磨床在修整砂轮时要带口罩并开启吸尘器。
8、修整砂轮时,金刚笔轴线向下倾斜5°~10°,也就是笔尖要低于砂轮中心1~2mm。
以防金刚石振动面扎入砂轮。
9、不得在加工中测量。
测量工件尺寸时,要将砂轮退离工件。
10、磨削带有花键‘键槽等间断工件时,背吃刀量不得过大。
磨煤机端盖裂纹处理技术探讨
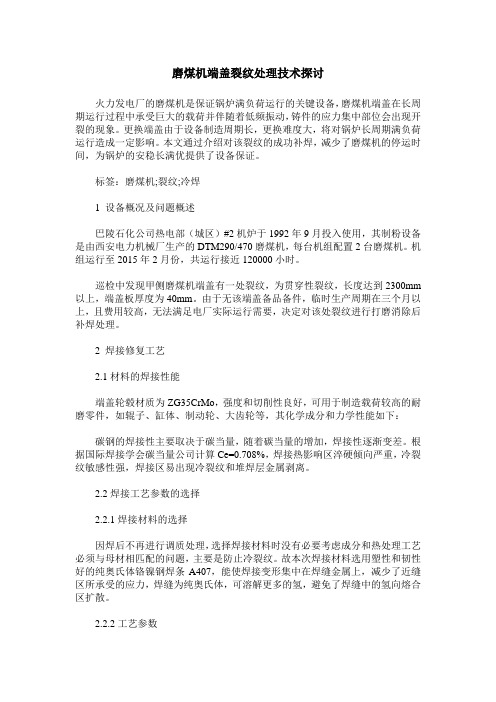
磨煤机端盖裂纹处理技术探讨火力发电厂的磨煤机是保证锅炉满负荷运行的关键设备,磨煤机端盖在长周期运行过程中承受巨大的载荷并伴随着低频振动,铸件的应力集中部位会出现开裂的现象。
更换端盖由于设备制造周期长,更换难度大,将对锅炉长周期满负荷运行造成一定影响。
本文通过介绍对该裂纹的成功补焊,减少了磨煤机的停运时间,为锅炉的安稳长满优提供了设备保证。
标签:磨煤机;裂纹;冷焊1 设备概况及问题概述巴陵石化公司热电部(城区)#2机炉于1992年9月投入使用,其制粉设备是由西安电力机械厂生产的DTM290/470磨煤机,每台机组配置2台磨煤机。
机组运行至2015年2月份,共运行接近120000小时。
巡检中发现甲侧磨煤机端盖有一处裂纹,为贯穿性裂纹,长度达到2300mm 以上,端盖板厚度为40mm。
由于无该端盖备品备件,临时生产周期在三个月以上,且费用较高,无法满足电厂实际运行需要,决定对该处裂纹进行打磨消除后补焊处理。
2 焊接修复工艺2.1材料的焊接性能端盖轮毂材质为ZG35CrMo,强度和切削性良好,可用于制造载荷较高的耐磨零件,如辊子、缸体、制动轮、大齿轮等,其化学成分和力学性能如下:碳钢的焊接性主要取决于碳当量,随着碳当量的增加,焊接性逐渐变差。
根据国际焊接学会碳当量公司计算Ce=0.708%,焊接热影响区淬硬倾向严重,冷裂纹敏感性强,焊接区易出现冷裂纹和堆焊层金属剥离。
2.2焊接工艺参数的选择2.2.1焊接材料的选择因焊后不再进行调质处理,选择焊接材料时没有必要考虑成分和热处理工艺必须与母材相匹配的问题,主要是防止冷裂纹。
故本次焊接材料选用塑性和韧性好的纯奥氏体铬镍钢焊条A407,能使焊接变形集中在焊缝金属上,减少了近缝区所承受的应力,焊缝为纯奥氏体,可溶解更多的氢,避免了焊缝中的氢向熔合区扩散。
2.2.2工艺参数为避免过热区奥氏体晶粒粗化,减轻高温回火区的软化,获得对冷裂纹敏感性低的组织,应使焊缝在高温停留时间短而冷却速度慢。
成型磨齿裂纹产生原因分析及工艺优化措施
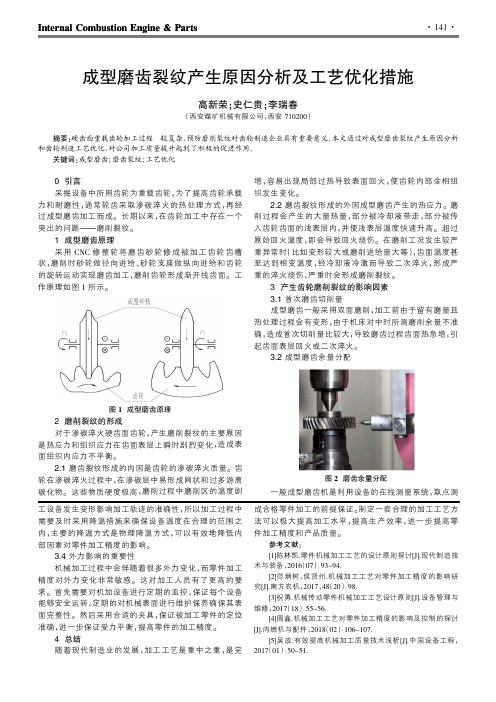
图1成型磨齿原理2磨削裂纹的形成对于渗碳淬火硬齿面齿轮,产生磨削裂纹的主要原因是热应力和组织应力在齿面表层上瞬时剧烈变化,造成表面组织内应力不平衡。
2.1磨齿裂纹形成的内因是齿轮的渗碳淬火质量。
齿轮在渗碳淬火过程中,在渗碳层中易形成网状和过多游离碳化物。
这些物质硬度极高,磨削过程中磨削区的温度剧图2磨齿余量分配一般成型磨齿机是利用设备的在线测量系统,工设备发生变形影响加工轨迹的准确性,所以加工过程中需要及时采用降温措施来确保设备温度在合理的范围之主要的降温方式是物理降温方式,可以有效地降低内部因素对零件加工精度的影响。
3.4外力影响的重要性机械加工过程中会伴随着很多外力变化,而零件加工精度对外力变化非常敏感。
这对加工人员有了更高的要成合格零件加工的前提保证。
制定一套合理的加工工艺方法可以极大提高加工水平,提高生产效率,进一步提高零件加工精度和产品质量。
参考文献:陈林凯.零件机械加工工艺的设计原则探讨[J].2016(07):93-94.范炳树,侯贤州.机械加工工艺对零件加工精度的影响研南方农机,2017,48(20):98.机械传动零件机械加工工艺设计原则[J].18):55-56.机械加工工艺对零件加工精度的影响及控制的探讨图3齿槽对中位置磨齿对中后,为防止首次切削量过大,须扩大公法线加即给必要的安全距离,安全距离一般保证此时需考虑加工齿轮结构形状及变形后的最大磨削余量与最小磨削余量。
从磨削条件优化正确选择砂轮并优化修整参数采用成型磨齿,磨削齿面渗碳淬火硬度的齿轮,使用适合渗碳淬火硬齿面齿轮磨削的G19VSP-PSX砂轮。
在保证齿面光洁度情况下,粗磨用粒度小的,精磨用粒度大的。
采用金刚石修整轮并优化修整参数,使砂轮达到最佳修磨效果。
调整冷却位置,以达到最佳冷却效果在磨削前,检查油嘴位置、冷却液压力、过滤系统是否图4冷却管位置通过对成型磨齿裂纹形成原因分析和齿轮冷热加工大大降低了齿轮磨削裂纹概率,提高了齿轮加为企业创造了良好的经济效益。
CF250齿圈端面磨削裂纹原因分析

CF250齿圈端面磨削裂纹原因分析李加荣(江苏奔航齿轮有限公司江苏淮安223001)摘要:本文通过对CF250齿圈端面磨削裂纹的产生原因的分析,探讨了端面磨削裂纹产生与磨削工艺、磨轮材料及热处理工艺的关系,并提出了解决办法。
2009年12月12日我公司在磨CF250.37.203齿圈(如下图)内止口时有21件端面发现严重的裂纹,有个别零件甚至有剥落现象。
本批质量问题的出现,数量大,情况严重,引起了全公司上下的一致重视。
为此,我们组织相关人员对此现象进行分析。
一、产品简图如下生产工艺如下:1、热处理工艺热处理加工采用渗碳淬火工艺,具体工艺参数如下:设备:UBE600型可控气氛多用炉渗碳淬火渗碳工艺:920℃碳势Cp1.05,4小时,920℃碳势Cp0.8,0.5小时,降温至810℃保温30分钟(降温及淬火保温段碳势Cp=0.8)淬入100℃分级淬火油40分钟清洗,低温回火烘箱,CF250齿圈简图 180℃±10℃保温3小时。
T处为为磨加工面2、磨加工工艺设备:M2120砂轮型号:WA60AVPDA 125X45X50砂轮转速:6000r/min零件转速:500r/min进刀量:0.05mm冷却液种类:M-2磨削液冷却液冲击方向:距磨削点处约20mm的齿轮内表面二、相关检验结果1、产品材料:20CrMnTi具体成份如下表:从实物金相组织看,表面有少量未转变的淬火马氏体,说明回火不太充分。
3、我们还对对渗碳淬火后磨前零件进行解剖检查,未发现裂纹,其金相结果同产生裂纹的实物检查,对热前零件进行检查,也未发现原材料中有锻造缺陷。
三、检查结果分析:1、从原材料的检查结果看,材料符合要求,也未发现锻造问题;2、从对热后磨前的零件检查结果看,没有产生淬火裂纹;3、从硬度检查及金相检查结果看,所得硬度和金相组织均很优良,说明热处理渗碳淬火工艺完全符合要求,但回火不太充分,可能与所用回火烘箱密封性能差有关。
- 1、下载文档前请自行甄别文档内容的完整性,平台不提供额外的编辑、内容补充、找答案等附加服务。
- 2、"仅部分预览"的文档,不可在线预览部分如存在完整性等问题,可反馈申请退款(可完整预览的文档不适用该条件!)。
- 3、如文档侵犯您的权益,请联系客服反馈,我们会尽快为您处理(人工客服工作时间:9:00-18:30)。
磨机端面裂纹的原因分析与处理方法摘要:我厂有一台φ3.8*13m的水泥球磨机自2003年安装以来运转良好,但在2010年6月9日更换进料中空轴时发现磨机端面与中空轴联接的螺栓孔处有裂纹。
裂纹已经发展到了1080mm左右,但可以看出裂纹没有裂透。
我厂决定实施现场焊接修复工艺。
采用了特殊焊接工艺,有效的防止裂纹扩大,获得了满意的效果。
关键词:筒体裂纹焊接坡口
磨机筒体与中空轴由螺栓联接,在交变应力作用下连续运行是
水泥磨机体的薄弱环节,筒体端面出现裂纹对球磨机以后的运转产生很大的影响。
本文主要介绍我厂对球磨机筒体端面出现裂纹的修补方法。
1 裂纹形成的原因
这条裂纹长约1080mm,出现在筒体端面穿过螺栓孔,是一个应力集中的部位。
裂纹穿过5个螺栓孔,前后联接7个螺栓孔(如图1),由球磨机在运转过程中周期性的将交变载荷通过螺栓传到从裂纹
的位置可以判断裂纹属于应力疲劳型的,裂纹的形成是由磨机在旋转过程由螺栓传给中空轴造成的。
2 确定修复方法
采用j427ni碳钢焊条,这种焊条具有优良的焊接工艺性能及良好的力学性能,低温冲击韧性好,飞溅少,脱渣易,焊接轻松,效率高,可进行全位置焊接。
焊接前,将焊条按要求烘干预热2-3h,温度200℃-350℃,然后,放在保温箱中保温,随用随取,每次取出量最多
不能超过10根。
正刨逆焊,层与层之间必须搭接压缝,每层焊接正反向交替进行,选择直流反极性及小范围参数(焊条的许用电流为130~150a),焊接电流尽量采取许用电流的下限参数。
由于是多层焊接,第1层焊缝易出现裂纹,选用小电流低焊速焊接。
2.1 开坡口为了减少金属的填充量,选用较小的坡口角度,采用单面“u”型坡口的型式。
端面厚为100mm,采用内外都开坡口,先在外面开深60mm宽600mm的坡口(等外面坡口焊好后在从内壁错开开深60mm宽600mm的坡口,这样焊缝就能有效的结合,如图2)。
开坡口采用碳弧气刨,使用φ8mm的碳棒,电焊机采用硅整流直流电焊机(gs-500ss),接法为反接,焊接电流为240~400a,压缩空气为0.6~0.7mpa,沿裂纹进行气刨,气刨后用钢丝刷清理焊渣,最后用φ150磨光机对坡口两侧内壁打磨修整,以除去渗碳层和清理坡口,达到施焊条件。
2.2 焊接的实施焊接跟随坡口走,由一端逐渐焊向另一端。
在焊接过程中,要用钢丝刷和角向磨光机清理飞溅物和药皮等杂物,由于现场的条件限制每层焊接均采用锤击焊缝金属的方法消除焊件的残余应力,并用角向砂轮机和放大镜,由专职人员反复检查焊缝是否有裂纹,如有裂纹必须重新焊接,直到没有裂纹为止,以保证焊接质量。
待裂纹全部焊接完毕后,还要用超声波探伤仪进行一次全面的探测,确认无任何焊接缺陷,确保焊接质量。
首先打底焊:选用φ3.2mm的焊条,尽量采用小电流、慢速度、短电弧且电弧不间断焊接,以窄焊道、多道焊方法连续完成焊接,焊条
不能摆动,减少熔合比,减少裂纹倾向,收弧时要注意填满弧坑。
打底焊是整个焊接的基础,一定要保证焊接质量。
打底焊应该焊两遍。
然后填平焊:填平焊选用φ4.0mm的焊条,采取短电弧在坡口横
截面上横焊。
在焊接过程中,焊条摆动到两端,并稍作停留,以保证焊肉与母材熔合好。
当坡口焊平后,必须用超声波探伤仪进行1次探伤监测,在保证没有焊接缺陷的情况下,再焊1层盖面焊层。
最后盖面焊:盖面焊采取高电压、小电流的慢速度施焊,严格保证焊趾外平缓圆滑过渡,焊缝饱满、均匀、整齐,焊缝表面光滑平整,不能有“咬肉”现象。
在外端面焊好之后,开始从筒体的内壁开坡口,并用同样的焊接方法进行焊接(如图2)。
3 处理后的试运行
为使磨体端面因焊接而产生的残余应力能缓慢均匀消除,以确
保水泥磨安全正常运行,我们制定了试运行方案。
如下表: 试运行期间要对试运行的电流、跳动、窜动、温度等情况做好记录,数值波动在允许的范围内进入连续运转阶段。
4 结论
我厂水泥磨机端面裂纹的焊接技术是属于大厚度钢件现场焊接,无法经过热处理,极易产生熔合区域的热裂纹和冷裂纹,但是采取
跟随坡口分层焊接避免了这一点,焊接完成后设备检验合格,投入
运行至今未见任何异常现象,证明了这次补焊成功。