150tLF冷轧料用钢SPHD生产实践
天铁热轧SPHC钢种冶炼生产实践

天铁 集团热 轧板有 限公 司炼 钢连铸 系统 自 2 0 07 年 4月 2 2日投产 以来 ,已成功开发 了 1 品种钢 , 0个 并于 2 0 0 7年 9月对冷轧用钢 S H P C进行开发 。 经过半 年 多的生产实 践 ,P S HC钢种 c s、 、i s的控制 ,特别是 s 含量 的控制 , i 取得 了很大 的成功 。如 何更好地减少
[摘要 ] 天铁集团热轧板有 限公 司炼钢 系统采用 D S O e —B F—L —C M工艺流程 , F C 成功开发 S HC的生产工艺 , P 解决 了
生 产 中硅 含 量 超 标 等 质量 问题 及 钢 水 流 动 性 问题 。
关键词 B OF转炉
1 前 言
L F精 炼炉 挡渣
脱氧
铝 的烧损 , 控制 L F精炼结束 后的酸溶铝 含量 , 及减少
表 1 成 分控制要求( %)
2 工 艺流 程 21 设 备 状 况 、
其中 s 含量 的控制 ,人炉铁水经过脱硫站 后 s含量能 达到 00 5 转 炉主要通过生铁块 和废 钢 的配 比进行 . %, 0 调节 , 一般 比率 为 1 :, . 1 生铁 块 s高 时 , 5 减少 s的加 入, 增加 轻废和重 废 的比例 , 量保持在 3 , 总 6t基本 能 使 s 00 8 00 5 在 . %~ .1%的范 围。 0
铁, 最后加铝铁 , 出钢 45加完 。脱氧合 金加入量如 终 /
t j
正 。
—— . 钢铁冶炼 _一 I I
。
苫
维普资讯
天淬 室 幺
点 C≤00 %. , 铝铁( 4 含铝 4 %) 2 加入参 考量 2 gt , k/钢 从
冷轧基板SPHC钢转炉直上规模化生产

2020年第2期典型冷轧基板钢种SPHC 钢属低碳、低硅、低硫铝镇静钢,具有较强的延展性及冷加工性能,用途广需求量大。
钢种特性要求决定了其基本的冶炼任务为深脱氧、深脱硫、控铝、控硅、夹杂物控制。
生产实践表明,该类钢种冶炼工艺的复杂性和难点还比较突出,传统工艺为了实现低硫目标往往采用铁水预处理工艺;为实现精确控铝、深脱氧、深脱硫、夹杂物及流动性控制往往必须采用精炼处理工艺,从而形成了铁水预处理→转炉冶炼→LF (RH )精炼→连铸的典型生产工艺流程。
传统工艺流程已经很成熟稳定了,不论在生产的稳定性和连续性、质量控制已经没有太多问题,但存在工艺流程复杂、工序多、生产成本高、效率低等问题。
在行业产能过剩、市场竞争激烈、成本控制压力大的背景下,很多冶金工作者热衷于研究精简化的生产工艺流程。
传统工艺流程中铁水预处理和精炼工序趋于省略。
SPHC 钢转炉直上浇铸的生产工艺,近年来在国内也初步取得了一定的成果,但存在的问题是生产不稳定,钢水流动性不好(絮流)、钢中Al 和S 成分控制不稳定、连浇炉数低等。
笔者在柳州钢铁集团公司柳钢转炉炼钢厂120t 转炉作业区,通过研究摸索优化工艺,解决了上述难题,实现了冷轧基板SPHC 钢转炉直上连续规模化批量生产的目的,生产过程控制稳定、钢的质量控制接近或等同于原走精炼工艺流程的水平。
因简化了生产工序,提升了生产效率,降低了生产成本。
炼钢工序工艺简介柳钢为华南地区特大型钢铁联合企业。
柳钢转炉炼钢厂为柳钢钢铁制造流程上极其重要的工序,近年来通过技术改造,已装备了目前国内主流先进的炼钢工艺装备,在产量、品种、质量上面已达到国内同类企业先进水平。
2019年钢产量达到1367万吨,品种涵盖了建筑、造船、桥梁、汽车、及其他工业用材。
采用SPHC 转炉直上工艺的主要生产现状如下:生产条件柳钢转炉炼钢厂第二作业区装备2套颗粒镁喷吹脱硫装置,3座120t 顶底复吹转炉,2台120t LF 精炼炉,1台120t RH 精炼,3台断面220mm ×(1000~1810)mm 板坯连铸机,2台断面165mm ×165mm7机7流方坯连铸机。
通钢FTSC连铸机开发SPHD低碳低硅钢的生产实践

通钢FTSC连铸机开发SPH D低碳低硅钢的生产实践翟利伟1 关春立1 毕洪志2(1.通化钢铁集团公司第三炼钢厂;2.通化钢铁集团公司技术中心,通化134003)摘 要 介绍了BOF-LF-FTSC工艺生产线生产SPHD低碳低硅钢的冶炼和薄板坯连铸工艺,重点分析了碳含量、硅含量等主要成分的控制措施和生产实践效果,为通钢FTSC工艺薄板坯连铸机顺利生产SPHD钢以及今后开发新品种钢积累了经验。
关键词 FTS C铸机,SPHD低碳低硅钢,控制措施中图分类号 TF777.7 文献标识码 BD evelopm en t of SPHD low carbon and low sili con steel i n FTSC th i n sl ab ca sterZ HA IL i w ei1,G UAN Chunli1,B I Hongzhi2(1.No.3Steel m aking Plant;2.Technol ogy Center,T onghua Ir on and Steel Gr oup Co.,L td.,T onghua134003)ABSTRACT S melting and FTSC thin slab casting p r ocesses f or SPHD l ow carbon and l ow siliconsteel at Tonghua Steel were intr oduced.Some measures t o contr ol the carbon and silicon contents inthe steel were adop ted f or qualified steel quality and s mooth casting operati on.KE Y WO R D S FTSC caster,SPHD l ow carbon and l ow silicon steel,contr ol measures 截至2006年上半年,我国已有珠钢、邯钢、包钢等12家钢铁企业的13条薄板坯(包括中薄板坯)连铸连轧生产线相继投产,产能约为3500万t/a。
SPHD钢的工艺控制措施

样钢水终 点碳控 制在 临界碳量 以上,有利于提高脱氧 剂 的回收率 ,降低钢铁料消耗,降低成本 。
2 ,2 o 中闯高新技 01 0 2 书企业 1 5 0
3 .提高一倒率,减少补吹,提高钢水的纯净度 。
4 .钢 芯铝加 入量 以精 炼炉不补 铝为原则 。出钢 时按要求加入足量钢 芯铝 ,以利于脱氧产物 的有时 间
1 .增加石 灰萤石等渣 料 的使用 量 。根据作 用定
律可提高对夹杂物 的吸附量和减少增碳 的机会 。采用
大渣量稀释炉渣 中的 ( e + n )、S O 抑制还原增 FOMO i 2
塞棒吹氩保证结晶器液面平稳 。
硅 。根据 需要加入量 在吨钢8 g k 左右 ,而 一般 的钢种
控 制 在 吨钢 3 g 左 右 。 k钢
保护浇注方式 。
( 钢水 絮流 的控制 三) S H 钢 是低 碳 、低硅 铝镇 静钢 ,而 钢 中溶解 铝 PD
含量在0 0 0  ̄0 0 0 。钢水 中的铝含量 大于0 0 % .3% .5% . 1
时 ,生成单相的A 0 ,导致钢水絮流。 1 3 2
从其氧势 图上看 出铝元素氧势最低 ,钢 水发生氧 化优先氧化铝 ,生成A 0 ,如果精炼、连铸控 制不 1 2 3
碳含 量超 标 、精 炼增硅 、连 铸 絮流 的发 生。 关键 词 : P S HD ;终点碳 ; 增硅 ; 絮流 ;工艺控 制 中图分 类号 : G3 5 T 3 文 献标 识码 : A 文章 编号 :1 0 — 3 4( 0 2) 6 0 0 — 2 09 2 7 2 1 0— 15 0
1 .转炉钢 水终点碳 。通 过数据对 比、试验 ,找 出临界碳 量 ,结合 实际操 作 ,提 高转 炉对 终 点碳 的
低碳低硅钢SPHC精炼工艺实践

图 1 同脱 氧工艺 R 不 H精炼结束后 T. O含量
3- . 2降低 R 1 H铝氧加热率 R H真空精炼过程 , 若钢包蓄热不饱和 , 真空槽 烘烤温度得不到保证 、 转炉出钢时间提前而延长 R H
・
3 ・ O
《 碳低 硅钢 S H 低 P C精 炼工 艺实践 》
工 序 时 间 、钢水 循 环 流量 控 制 不 当 等 因素 ,钢水 精
种属于低碳低硅铝镇静钢 ,该钢种成分设计见表 1 。
表1 S H P C化学成分设计 ( ) %
・
2 ・ 9
《 低碳低硅钢 S H P C精炼工艺实践 》
从 表 1 以看 出S HC 可 P 钢种 的主要 特 点 :
B F L + C O + H C 生产 工艺 , 工艺 效果 见 O + F C 、B F R + C 其 表2 。不 同生 产工 艺实 绩表 明 ,C S A 精炼 结束 后钢 中 TO 量较 高 ,连铸 浇注过 程 中A , 塞 中包 水 口 , .含 1 堵 O 连 续浇 注仅 4 7炉而 被迫 中断 生产 ,打破 “ ~ 一罐 制 ” 钢 铁界 面 平衡 。L 精 炼 过程 中 ,钢 水增 硅 、碳 得 不 F 到有 效控 制 ,硅或碳 成分 出格 综合 炼成 率仅 7.%, 5 6 因钢种 改 炼 而 中断铸 坯 热 送 ,严 重 时轧 钢 断坯 料 , 依 然打破 “ 一罐 制 ”钢 铁界 面平 衡 。R H精炼 结束 后 , 钢 中TO 定控 制在 3 .稳 5×1 0 以下 ,彻底 解决 了中包
专. 敞 黾
CI E SC T CHN L O OG Y
低 碳低 硅钢 S H P C精 炼工艺实践
何 宏侠 高祝 兵 陈露 涛
冷轧钢卷生产工艺流程

冷轧钢卷生产工艺流程英文回答:Cold-rolled steel coil production involves several steps in the manufacturing process. It starts with the selection and preparation of raw materials, followed by the rolling process, annealing, and finally, the finishing process.The first step is the selection and preparation of raw materials. High-quality hot-rolled steel coils are chosen as the starting material. These coils are inspected for any surface defects or impurities before they are sent for further processing.Next, the selected hot-rolled coils are fed into a rolling mill. The rolling mill consists of a series of rollers that gradually reduce the thickness of the steel. This process is called cold rolling. The steel passes through the rollers multiple times until the desiredthickness is achieved. Cold rolling not only reduces the thickness but also improves the surface finish and mechanical properties of the steel.After cold rolling, the steel coils undergo annealing. Annealing is a heat treatment process that involves heating the steel to a specific temperature and then slowly cooling it. This process helps to relieve internal stresses, improve the ductility, and refine the grain structure of the steel. The annealing process also enhances the flatness and surface quality of the steel coils.Once the annealing process is complete, the steel coils go through the finishing process. This includes trimming the edges, inspecting for any defects, and applying any necessary surface treatments or coatings. The finishedcold-rolled steel coils are then ready for further processing or shipment to customers.中文回答:冷轧钢卷的生产工艺流程涉及几个步骤。
本钢冷轧双相钢生产实践PPT课件

2021年6月24日星期四
第7页/共24页
工艺参数 234 650 450 650
Max.65 860
90/160 80 904 1135 100
• 双相钢生产工艺思路:
将材料加热到铁素体-奥氏体区之后,通过冷却将奥氏体转变 为马氏体的方法来获得双相组织(铁素体+马氏体),利用马氏 体的刚度及铁素体的延展性,获得具有高的抗拉强度,低的屈 强比及良好加工硬化能力的材料。
2021年6月24日星期四
第4页/共24页
本钢1850mm连续退火机组
年处理量:931,100吨 成品产量:907,800吨 产品有:CQ、DQ、DDQ、EDDQ、SEDDQ和HSS HSS包括固溶型、析出型、烘烤硬化型、双相组织型及TRIP钢等,其强 度级别为340980MPa。 成品厚度:0.3~2.5 mm 成品宽度:800~1850mm 成品卷重:5 ~15吨,中间卷重:30吨 主要产品用途:汽车板和高级家电板
SEM显微组织
第21页/共24页
➢ 本钢1850mm连续退火机组的工艺技术和设备 是具有当代世界先进水平的。
➢ 根据多次冷轧双相钢的生产经验,选择合理的 退火工艺制度并调整喷气冷却及辊式冷却的最佳 使用比率,保证了780MPa级冷轧双相钢在连续 退火机组的稳定生产。
➢ 实际生产中工艺速度波动值小于10mpm,机组 各段的带温控制在10℃的偏差范围内,小时产 量达到设计指标,最终产品性能全部满足客户需 求。
2021年6月24日星期四
第14页/共24页
过时效工艺的控制
• 由于在快冷过程中奥氏体向马氏体相变过程中体积发生 膨胀,从而与铁素体基体交互作用产生了大量的可移动 位错,过时效过程可使晶格畸变减小,从而使应力状态 改变,提高了材料的冲压性能。但当过时效温度上升到 一定程度,马氏体明显分解时,材料的屈服强度显著上 升,屈强比也随之上升。根据生产实际发现,过时效温 度在250℃左右时即满足改变应力状态又不导致马氏体 分解。
安钢150 t转炉高磷耐候钢生产实践

安钢150 t转炉高磷耐候钢生产实践吕亚;刘磊;王新志;付艳云;杨晓奇【摘要】结合现场生产实际,从转炉冶炼原材料条件、造渣制度、供氧制度、操作控制等方面分析了高磷耐候钢冶炼技术特点.生产实践表明:在正常的冶炼条件下,采用相对低的碱度2.2~2.5,并稳定炉渣中的FeO含量在15%以内是冶炼高磷耐候钢的关键;冶炼工艺优化后转炉出钢终点磷w(P)%平均可达到0.055%的水平.【期刊名称】《河南冶金》【年(卷),期】2018(026)002【总页数】3页(P33-35)【关键词】高磷耐候钢;脱磷;造渣制度;供氧制度【作者】吕亚;刘磊;王新志;付艳云;杨晓奇【作者单位】安阳钢铁集团有限责任公司;安阳钢铁集团有限责任公司;安阳钢铁集团有限责任公司;安阳钢铁集团有限责任公司;安阳钢铁集团有限责任公司【正文语种】中文0 前言对一般钢种而言,磷是钢中有害元素之一,在钢中易发生偏析,加工过程中易发生冷脆,恶化钢的性能,一般要求磷含量越低越好。
而在耐候钢中磷则可以有效提高钢铁材料在大气中的耐腐蚀指数,提高钢的耐腐蚀特性。
在耐候钢种设计时磷常作为一种有益元素被添加。
磷含量较高,采用常规工艺方法冶炼,因转炉终点出钢磷含量较低,须要补加大量的磷铁合金,转炉吹炼过程渣量大,炉渣全铁含量高,不利于生产成本的有效控制。
1 冶炼主要装备与工艺流程1.1 转炉主要工艺参数安钢第二炼轧厂150 t转炉主要工艺参数见表1。
1.2 生产工艺流程安钢第二炼轧厂含磷耐候钢的生产工艺流程:高炉铁水一混铁炉或折铁罐—150 t转炉一吹氩站一LF—双流板坯铸机2 冶炼实践与分析2.1 高磷耐候钢的冶炼技术要求高磷耐候钢是在钢中通过添加Cu、P、Cr和Ni等合金元素的低合金耐大气腐蚀结构钢,是一种通过锈蚀过程中表面合金元素的富集,使锈层逐渐趋于稳定化,从而延缓基体金属腐蚀的钢材。
其化学组分要求以高磷集装箱板SPA-H为例进行说明,具体要求见表2。
叙述冷轧带钢生产工艺流程的步骤
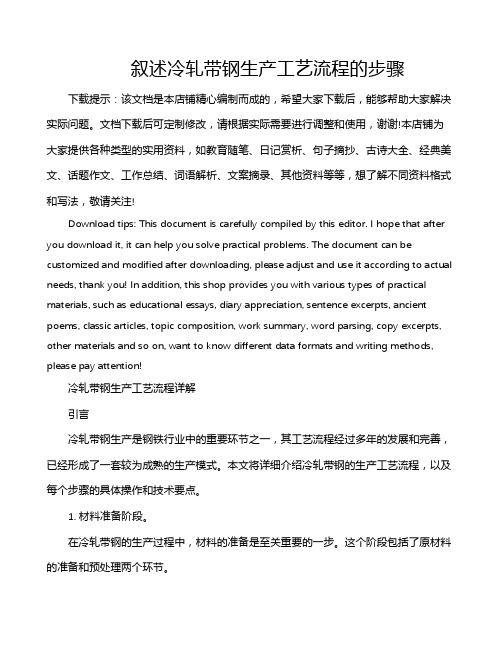
叙述冷轧带钢生产工艺流程的步骤下载提示:该文档是本店铺精心编制而成的,希望大家下载后,能够帮助大家解决实际问题。
文档下载后可定制修改,请根据实际需要进行调整和使用,谢谢!本店铺为大家提供各种类型的实用资料,如教育随笔、日记赏析、句子摘抄、古诗大全、经典美文、话题作文、工作总结、词语解析、文案摘录、其他资料等等,想了解不同资料格式和写法,敬请关注!Download tips: This document is carefully compiled by this editor. I hope that after you download it, it can help you solve practical problems. The document can be customized and modified after downloading, please adjust and use it according to actual needs, thank you! In addition, this shop provides you with various types of practical materials, such as educational essays, diary appreciation, sentence excerpts, ancient poems, classic articles, topic composition, work summary, word parsing, copy excerpts, other materials and so on, want to know different data formats and writing methods, please pay attention!冷轧带钢生产工艺流程详解引言冷轧带钢生产是钢铁行业中的重要环节之一,其工艺流程经过多年的发展和完善,已经形成了一套较为成熟的生产模式。
冷轧方管制造工艺流程

冷轧方管制造工艺流程冷轧方管是一种常见的钢管制品,广泛应用于建筑、机械制造、汽车制造等领域。
冷轧方管的制造工艺流程包括原材料准备、热轧坯料加工、冷轧成型、矫直、切割和包装等环节。
制造冷轧方管的第一步是原材料准备。
原材料通常为热轧钢带,其主要成分为碳素钢。
在原材料准备阶段,需要对热轧钢带进行检验,包括尺寸、化学成分和力学性能等方面的检测,确保原材料符合要求。
接下来是热轧坯料的加工。
热轧钢带经过剪切机的切割,将其切成一定长度的坯料。
然后,将坯料送入加热炉进行加热,以提高其可塑性和热轧性能。
第三步是冷轧成型。
加热后的坯料通过辊道进入冷轧机组,经过多道次的冷轧,逐渐形成方形的截面。
冷轧过程中,通过调整辊缝,使坯料逐渐变细,并最终形成所需的尺寸和形状。
完成冷轧成型后,需要对方管进行矫直。
矫直是为了消除冷轧过程中产生的应力和弯曲,使方管达到一定的直线度要求。
常见的矫直方法有拉矫和辊矫两种,根据方管的尺寸和要求选择合适的矫直方法。
矫直后,还需要对方管进行切割。
根据客户的需求,将方管切割成所需的长度。
切割通常采用锯床、切割机等设备进行。
最后一步是方管的包装。
经过切割后的方管需要进行包装,以便储存、运输和销售。
通常采用捆扎、打包或用塑料薄膜包装的方式进行。
冷轧方管的制造工艺流程包括原材料准备、热轧坯料加工、冷轧成型、矫直、切割和包装等环节。
每个环节都需要严格控制和操作,以确保方管的质量和尺寸符合要求。
通过科学的制造工艺流程,可以生产出高质量、精确尺寸的冷轧方管,满足不同领域的使用需求。
- 1、下载文档前请自行甄别文档内容的完整性,平台不提供额外的编辑、内容补充、找答案等附加服务。
- 2、"仅部分预览"的文档,不可在线预览部分如存在完整性等问题,可反馈申请退款(可完整预览的文档不适用该条件!)。
- 3、如文档侵犯您的权益,请联系客服反馈,我们会尽快为您处理(人工客服工作时间:9:00-18:30)。
总第159期2007年12月 南 方 金 属S OUT HERN MET ALSSu m.159December 2007 收稿日期:2006-12-26; 修订日期:2007-02-10 作者简介:单庆林(1978-),男,2002毕业于河北理工学院钢铁冶金专业,助理工程师. 文章编号:1009-9700(2007)06-0056-02150t LF 冷轧料用钢SPHD 生产实践单庆林(唐山钢铁集团有限责任公司,河北唐山063020)摘 要:唐钢150t LF (ladle furnace ))精炼炉通过对冷轧用钢成分、温度、可浇性的合理控制,精炼合格率由原来的70%提高到98%以上.关键词:精炼炉(LF );冷轧用钢;合格率中图分类号:TF 703 文献标识码:BProducti on of SPHD i n gots for cold rolli n g w ith 150t L FSHAN Q ing 2lin(The No .1RollingM ill,Tangshan Ir on &Steel Co .,L td .,Tangshan 063020,Hebei )Abstract:By strictly contr olling the compositi on,te mperature,and fl owability of the molten steel p r oduced with a 150tLF refining furnace at Tang Steel f or subsequent cold r olling,the accep tance rate of the refined steel was markedly increased fr om 70%t o above 98%.Key words:ladle furnace (LF );steel for cold r olling;accep tance rate1 引言随着唐山钢铁集团有限责任公司(以下简称“唐钢”)开发高附加值产品,为冷轧生产线提供高质量的供轧钢种SPHD 冷轧料用钢产量越来越大,一次合格率十分重要,生产初期,由于经验不足,精炼成分波动大,连浇钢水成分不稳定,经常出现C 高、S 高、Si 高、P 高等造成改判,温度控制也不稳定,造成温低回钢水断流,高温钢水拉漏以及可浇性不好等现象,一再中断生产.经过理论分析和生产实践,最终合格率达到了98%以上.为铸机提供了成分温度合格、可浇性良好的钢水.2 成分控制SPHD 钢种特点:属于低C 、低Si 、低S 、高铝供冷轧用的高附加值钢种.目标成分:w (C )<0.07%w (Mn )0.15%~0.30%w (Si )≤0.05%w (S )<0.007%w (P )<0.018%w (A l )0.020%~0.040%为了保证钢料性能(较低的强度和较好镀锌、彩涂效果),通过合理操作,将化学成分控制在目标范围内,保证钢水成分的连续性、稳定性,最终实现板材性能的稳定.2.1 C 含量控制精炼C 含量控制主要是避免增C .增C 原因:大电流冲击、电极低端剥落,加热过程钢球粘在电极上.控制方法:1)确保全程埋弧加热避免过程升温增C;2)采取合理的吹氩强度;3)尽量使用本钢种钢包;4)开机炉次因为中包要增C,故C 含量控制开机炉次比连浇炉次低.2.2 Mn 含量控制由于前期渣中Mn O 会被还原,故锰铁要等到精炼后期脱氧完全后加入,这样Mn 含量控制可以精确到0.01%.2.3 Si 含量控制SPHD 钢种要求:Si 含量小于0.05%,内控品要求在0.03%以下,Si 含量的控制成为关键,为了弄清增Si 的原因和原理,通过跟踪和数据统计,对几种增Si 的现象作了分析.2.3.1 搅拌时间长短与增Si从图1可以看出,前期Si 增加慢,中期快,后期又变慢,而且后期变化极慢.说明强搅时间长,增Si 大,但是不同炉次搅拌时间相同增Si 量不同,说明增Si 总量还受其它因素影响,在得到合格钢水所用的合理搅拌时间里,增Si 量受其它因素影响.图1 搅拌时间长短与增Si 关系2.3.2 精炼初始S 含量与增Si100炉精炼钢水统计见表1和图2.表1 初始S 含量与增Si 关系初始S 含量0.001%1015152020252530303535404050增Si 总量0.01%1.31.82.82.93.13.43.7图2 初始S 含量与增Si 关系 从图2可以看出,精炼初始S 含量与出站钢水Si 含量是正比关系.2.3.3 下渣与增Si 的关系下渣一般通过P 和挡渣率来表现,精炼过程平均增Si 为0.028%,而下渣的炉次,平均增Si 为0.035%.因此,下渣量大的炉次,增Si 较多.理论分析:碱性渣中,Ca O 、Si O 2结合成稳定硅酸钙,因而αSi O 2很小,一般不增Si,随着脱氧的进行,当αFeO 很小,αSi O 2变大时Si 就会被还原.2A l +3Si O 2=A l 2O 3+3[Si]Si +2(Fe O )=Si O 2+2(Fe )2A l +3Fe O =A l 2O 3+3Fe图1中,前期脱氧不完全,不怎么增Si;中期脱氧完全,增Si 快;然而后期脱氧完全增Si 反而较慢,因为这时随着脱氧进行以及部分Si O 2被还原,后期碱度比前期中期高了,αSi O 2随着R 升而变小,当R 很高时,增Si 变慢了.可以得出以下结论:强搅时间长短与增Si 成线性关系,但是可以通过控制R 来控制增Si 总量,通过脱氧来控制增Si 速度.表1中,初始S 含量与增Si 也说明了这个原因.从单个炉次之间比较,S 的高低与增Si 量无明显规律,因为它们之间碱度有差别故S 高,增Si 也未必多,但是大量炉次统计表明,相同碱度下,S 高,增加了搅拌时间,导致增Si 多.通过提高碱度加大渣量,减少强搅时间,提高原料质量,从而减少增Si 量.2.4 S 含量控制该钢要求S 含量很低,为脱S 就要选好流动性好的高碱度还原渣.根据钢水S 的总含量补加石灰和萤石.2.5 A l 控制当A lS 含量控制在0.015%时,随着钢中A lS 含量的增加,钢中氧含量会有所降低;当A lS 含量控制在0.030%时,随着钢水A lS 含量的增加,钢中氧含量基本没有变化;而当钢中铝含量超过0.03%时,钢中的铝很容易与渣中氧结合,也会还原渣中的Si O 2等化合物,使钢中聚集的A l 2O 3增加,因此,A lS含量控制在0.015%~0.030%之间为宜.3 温度控制3.1 开机温度控制开机使用连用包A:1)精炼时间大于45m in;2)中包烘烤温度大于1150℃;3)出站温度中上限.B:1)精炼时间小于45m in;2)中包烘烤温度小于1150℃;3)出站温度中下限.达到A 中2条B 中1条,作为开机温度条件比较合适;达到A 中3条开机温度高;达到A 中1条开机温度低.3.2 连浇温度控制温度控制因素:1)精炼时间;2)从出站到停浇(下转第60页)75 总第159期 单庆林:150t LF 冷轧料用钢SPHC .SPHD 生产实践明确的项目,发包方喜欢采用固定合同总价法,其利于投资控制,便于工程价款的最终结算,另外发包方也想通过签订固定总价合同将合同的履约过程中的一切风险转移给承包方承担.所以固定价格合同签订前应当充分考虑施工期间,各类建材的市场风险和国家政策性调整风险.当实际完成工程量大于合同签订工程量,将会给承包商造成巨大损失.但是工程本身的实施是一个渐进的过程,只要重视,不存侥幸心理,就能预测和掌握这些风险,然后从工程管理和合同条款中找出种种理由,进行索赔,保证合同的履行,也可以确保今后结算的顺利.3)成本加酬金合同是由业主向承包商支付工程项目的实际成本,并按事先约定的某一方式支付酬金合同,业主承担了项目的全部风险,除抢险救灾工程使用外,一般很少使用.为了选择到双方认可的合同类型,业主和承包商应当综合考虑项目规模,工期长短,竞争情况,复杂程度,外部环境等因素,权衡利弊,保证合同的可执行性.合同类型一旦选定,则在工程竣工结算审计时就应该按照选定的合同价款形式执行.4 结束语加强合同管理是完成工程建设的重要保证,同时也是搞好结算管理的关键环节,因此合同的规范与严密有利于竣工结算工作的顺利进行.由于建设项目的特性,工程结算工作在实际操作中还可能碰到各种的问题,为此承发包双方都必须对建设工程施工合同给予足够的重视,在签定合同过程中,对《示范文本》中的合同协议书、通用条款和专用条款要仔细阅读理解,针对工程的具体情况和可能发生的各种问题,以及各个细节都要考虑周到,减少不确定因素,做到双方约定书面化,模糊问题清晰化,使施工合同的订立公平合理,公正有效,从而防止合同纠纷的发生,工程竣工结算工作就可以按照施工合同有条不紊地进行.(上接第57页)时间;3)包况;4)温度升到最高点次数.第4点非常重要,一般连用包如果温度开到1600℃一次温降0.8℃/m in,两次温降0.6℃/m in.1600℃出站,待浇30m in,一次温降24℃,两次温降18℃.可以看出同样温度出站温差可达6℃,这是不可忽略的,这一条件对于备用包、隔炉包同样适用.而且应用这一条件非常有利,它既保证按规定时间、温度出站,又不会因为温降过大造成温低,是减少温低回钢水的有效措施之一.4 可浇性的控制可浇性不好主要因为:1)温度低;2)杂夹物上浮时间不足,Ca/A l不够;3)Ca/A l不够.故需要通过控制合适温度,保证弱搅时间,保证A l2O3上浮,以及合理的变性处理.5 结束语唐钢精炼炉充分发挥自身特点,通过对冷轧用钢成分、温度、可浇性的合理控制,降低钢中的硫、氧、氢、氮和非金属夹杂物含量,改变夹杂物形态,以提高钢的纯净度,改善钢的机械性能;满足低碳和超低碳钢的要求;微调合金成分,将成分控制在很窄的范围内,并使其分布均匀;将钢水温度调整到浇铸所需要的范围内,减少包内钢水的温度梯度,精炼合格率由原来的70%提高到98%以上.06南 方 金 属S OUTHERN M ET ALS2007年第6期 。