关于机床精度稳定与保持性的研究
提高数控机床稳定性的策略

提高数控机床稳定性的策略现代制造业的发展中,数控机床被广泛应用于各个行业,其稳定性对于产品质量和生产效率有着重要的影响。
因此,提高数控机床稳定性是制造企业不可忽视的重要课题。
本文将介绍一些提高数控机床稳定性的策略。
一、优化机床的结构设计数控机床的结构设计直接影响着其稳定性。
首先,应采用高刚性的材料来制造机床,以确保其在加工过程中不会因为振动而失去精度。
其次,合理设计机床的结构,使其在加工工况下不易变形,减少刚度损失。
同时,对于一些容易受到外界干扰的部件,如传动系统和导轨,应采用隔振和降噪措施,减少振动的传导和对整机的影响。
二、提高机床的控制系统机床的控制系统是其稳定性的核心。
首先,要选用高性能的数控系统,并进行合理的参数配置,以满足工艺要求。
其次,要进行系统的精确校准和定位误差的补偿,保证加工精度和稳定性。
此外,还应采用先进的自适应控制算法、模型预测控制等手段来提高系统的动态响应和抗扰性能。
三、优化切削工艺切削工艺是机床稳定性的重要因素之一。
首先,要选择合适的刀具和切削参数,以降低加工过程中的功率消耗和振动。
其次,要进行合理的切削液选择和供液方式,以保持工件和刀具的良好冷却和润滑。
此外,还应对切削过程中的温度和振动进行监测,及时调整工艺参数,避免机床因温度升高和振动加剧而失去稳定性。
四、加强设备的维护保养设备的维护保养是保证机床长期稳定运行的重要保障。
首先,要定期对机床进行润滑和清洁,保持各个部件的良好状态。
其次,要检查和更换损坏的零部件,及时修复和调整设备。
同时,要进行定期的巡检和预防性维护,提前发现和解决潜在问题,避免机床因故障而停机。
五、加强人员培训和技术支持人员培训和技术支持是保证机床稳定性的重要保证。
制造企业应该加强对操作人员的培训,使其熟练掌握机床的特性和操作技能,正确使用和调整机床。
同时,还应建立完善的技术支持体系,及时为企业提供技术咨询和故障处理服务,解决生产中的问题。
综上所述,提高数控机床稳定性是制造企业需要重视的关键问题。
机床的精度和稳定性控制

机床的精度和稳定性控制机床是制造业中的关键设备,对于制造出高质量的产品至关重要。
机床的精度和稳定性作为机床本身的质量指标,在生产过程中起着重要作用。
本文将探讨机床精度和稳定性控制的相关内容。
一、机床精度控制1.1机床粗定位误差控制机床的粗定位误差主要是由伺服驱动和机械传动误差等因素造成的,因此需要通过以下措施来控制:(1)超前补偿技术超前补偿技术是通过补偿误差来预先调整控制量,使之达到更好的响应性和稳定性。
在机床的控制系统中,超前补偿器可以根据机床传动特性进行自动校正,并将得到的校正结果输入给控制器,以实现误差的补偿。
(2)全闭合环控制全闭合环控制是指机床精度控制中完全采用闭环控制,将伺服驱动系统、传动部件和测量系统全部组成机床控制系统环路,以实现更高的精度。
1.2机床加工误差控制机床加工误差主要包括切削力变化和温度变化造成的变形误差。
为了控制机床加工误差,可以采取以下措施:(1)加强机床的刚度加强机床的刚度可以提高机床的稳定性、减小振动,从而降低加工误差。
(2)加工划分技术加工划分是将一个规定的点阵划分成若干个小面,在加工小面时分别进行加工,从而降低加工误差。
二、机床稳定性控制机床的稳定性主要指机床在加工过程中的稳定性和静态稳定性。
以下措施可以提高机床稳定性:2.1结构设计机床的结构设计应保证机床加工过程中的稳定性和静态稳定性。
例如,采用支持点分离、刚度大的结构和铸铁导轨都可以提高机床的稳定性。
2.2伺服系统设计机床的伺服系统也是影响机床稳定性的重要因素。
伺服系统的速度响应速度和调节性能都需要得到优化设计。
2.3自适应控制自适应控制针对机床稳定性强相关的控制环节,通过对机床稳定性的分析和建模实现对机床稳定性的控制。
三、结论机床的精度和稳定性对于机械制造业的发展至关重要,机床的粗定位误差、加工误差和机床的稳定性都是机床精度和稳定性的关键因素。
通过机床结构、伺服系统设计和控制合理的自适应控制来优化控制系统,可以提高机床的精度和稳定性,达到更高水平的加工效果。
数控机床操作过程中的稳定性分析

数控机床操作过程中的稳定性分析数控机床是现代制造业中不可或缺的一种机械设备,广泛应用于金属加工、零部件加工等领域。
它的出现极大地提高了生产效率和产品质量。
然而,在实际的操作过程中,数控机床的稳定性是至关重要的因素之一。
本文将对数控机床操作过程中的稳定性进行分析,以期能更好地了解和应对这个问题。
首先,我们来了解一下什么是数控机床的稳定性。
数控机床的稳定性指的是在加工过程中,机床能够稳定地运行,保持精度、刚性和可靠性。
稳定性是保证产品加工精度和质量的重要因素,直接影响着产品的合格率以及生产成本。
在分析数控机床操作过程中的稳定性时,我们首先要考虑的是机床的结构稳定性。
即机床的整体结构是否牢固、稳定,能否承受加工过程中产生的力、扭矩等载荷。
结构稳定性不仅包括机床本身的刚性,还涉及到零部件的精度和装配质量,因为任何一个环节的问题都可能导致机床的运行不稳定。
其次,我们要分析数控机床在运行过程中的动态稳定性。
数控机床在加工过程中,主轴高速旋转,工具刀具与工件之间进行相对运动,因此要保证机床的动态稳定性,以避免因振动和共振而产生的工件变形,从而影响产品质量。
为了达到更好的动态稳定性,需要对机床进行合理的设计和参数设置,例如确定适当的切削速度、进给速度和切削深度等。
另外,数控机床的操控和编程过程也对稳定性有很大影响。
机床操作人员需要熟练掌握机床的操控技术,合理选择切削工艺参数,以及根据加工要求编写正确的加工程序。
只有在正确操作和编程的基础上,才能保证机床的稳定运行和加工质量。
因此,培养机床操作人员的技术素养和经验积累也是提高机床稳定性的重要环节。
此外,还有一些外部因素也会对数控机床的稳定性产生影响。
例如,电源电压的稳定性、环境温度、湿度等因素都可能对机床的稳定运行产生影响。
因此,在机床的选型和安装中,要考虑到这些因素并采取相应的措施,以保证机床的正常运行。
为了进一步提高数控机床的稳定性,可以采取以下措施:1. 优化机床结构,并增加加工过程中的刚性支撑,以提高机床的结构稳定性;2. 通过振动测试和模态分析,确定机床的固有频率,并对这些频率进行相应的控制和设计,以提高动态稳定性;3. 注重数控机床操作人员的培训和技术提升,确保其熟练掌握操作技巧和编程知识;4. 加强机床的维护管理,定期检查和保养机床,及时发现和解决问题;5. 对机床周围的环境进行合理的控制,保持稳定的供电和适宜的温湿度。
关于机床精度稳定与保持性的研究

关于机床精度稳定与保持性的研究徐忠和,戚克霞(齐重数控装备股份有限公司,黑龙江齐齐哈尔161005)1概述我国近十多年来,机床行业发展非常迅速,已经成为世界机床大国,但在机床精度、性能上还与世界先进国家有一段距离。
具体表现在有些机床部件精度达不到设计要求、安装调整时间长,机床精度不稳定等。
有些机床需要反复调整才能达到机床精度要求,不仅浪费人力,增加成本,而且严重影响用户使用。
为了解决这些问题,我国机床行业这些年来经过技术改造,设备更新,机床部件的精度已经达到设计要求,但在使用过程中还出现机床精度不稳定的现象。
为了解决这个难题,我们进行了系统研究。
我们在大修改造国外1960~1970年代进口滚齿机及落地镗铣床时,发现他们机床调整垫铁与地基及机床之间的接触面积达到90%以上,而我们在这一方面重视不够。
为此,对使用过程中出现精度不稳定的机床,公司派专门技术人员进行了解研究,发现机床在二次灌浆调整时,由于机床制造厂与安调人员重视程度不够,或操作方法不合理,导致调整垫铁与地基及机床与地基之间接触不正确、垫铁歪斜等现象,造成接触面积小,而且有些呈现线性接触,造成机床精度不能够具有长期保持性。
为此我们严格研究制定了机床二次灌浆的操作规程,机床精度不稳定的现象得到彻底解决,不仅安装调试时间短,而且许多机床的精度已达到国际先进水平,下面介绍如何保证机床二次灌浆。
2对调整垫铁的要求调整垫铁是连接机床与地基的关键部件,其精度至关重要。
要求各重要结合面必须进行精磨。
调整垫铁的上下斜面必须清洁无毛刺,结合面0.03mm 塞尺不入,调整垫铁与垫板和机床床脚安装必须清洁、无毛刺、接触均匀无毛刺,结合面0.03mm 塞尺不入。
调整垫铁的安装密度将直接影响机床的刚性和机床精度的稳定性,要求垫铁的密度不大于1个/500mm ,同时,在载荷密集区,可相应增加垫铁,以提高机床的刚性,保持机床的稳定性。
3机床安装二次灌浆操作3.1压浆法(使用非二次灌浆料)(1)预调安装水平将机床主体件(床身、工作台、立柱等)床脚固定好地脚螺栓后,吊放于大地基的工艺调整垫铁上,预调安装水平。
数控机床刚度与稳定性研究论文
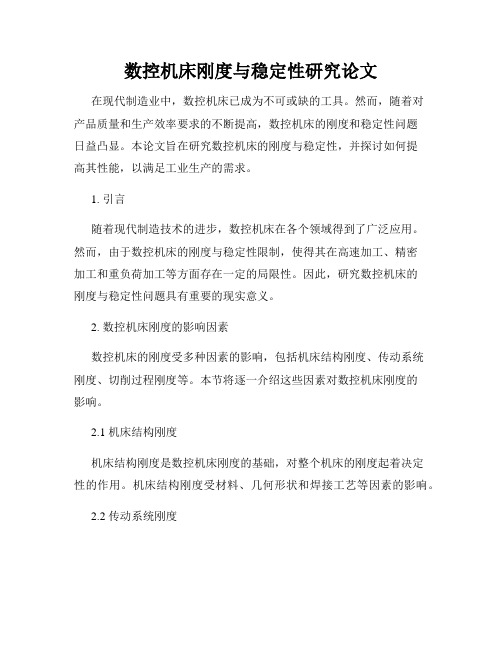
数控机床刚度与稳定性研究论文在现代制造业中,数控机床已成为不可或缺的工具。
然而,随着对产品质量和生产效率要求的不断提高,数控机床的刚度和稳定性问题日益凸显。
本论文旨在研究数控机床的刚度与稳定性,并探讨如何提高其性能,以满足工业生产的需求。
1. 引言随着现代制造技术的进步,数控机床在各个领域得到了广泛应用。
然而,由于数控机床的刚度与稳定性限制,使得其在高速加工、精密加工和重负荷加工等方面存在一定的局限性。
因此,研究数控机床的刚度与稳定性问题具有重要的现实意义。
2. 数控机床刚度的影响因素数控机床的刚度受多种因素的影响,包括机床结构刚度、传动系统刚度、切削过程刚度等。
本节将逐一介绍这些因素对数控机床刚度的影响。
2.1 机床结构刚度机床结构刚度是数控机床刚度的基础,对整个机床的刚度起着决定性的作用。
机床结构刚度受材料、几何形状和焊接工艺等因素的影响。
2.2 传动系统刚度传动系统刚度直接影响着数控机床的位置精度和运动平滑性。
传动系统刚度受传动装置、传动链条松弛以及传动元件的材料和制造工艺等因素的影响。
2.3 切削过程刚度切削过程刚度指的是数控机床在切削负荷下的刚度性能。
切削过程刚度受切削力、刀具刚度以及材料刚度等因素的影响。
3. 数控机床稳定性的研究方法数控机床的稳定性是指机床在运动过程中不发生振动,能够保持加工精度的性能。
为了研究数控机床的稳定性,人们采用了多种方法进行分析和评估。
3.1 实验方法实验方法是通过搭建实验平台,测量和记录数控机床的振动响应,以获得稳定性指标的一种方法。
通过实验方法可以获得较为直观的稳定性数据,为后续的优化设计提供依据。
3.2 数值仿真方法数值仿真方法是通过建立数学模型,利用计算机仿真软件模拟数控机床的振动和稳定性行为。
数值仿真方法可以更全面地分析机床的稳定性问题,得到详细的数值结果。
4. 改进数控机床刚度与稳定性的方法为了提高数控机床的刚度和稳定性,人们提出了多种改进方法。
高速数控机床主轴轴承精度及其保持性分析

高速数控机床主轴轴承精度及其保持性分析摘要:在机床的主轴部件之中,机床主轴轴承是确保机床运行的重要部件。
机床主轴的轴承在运行过程中会受到多方面作用的影响,不仅有轴向以及径向的载荷,而且需要注意在高速运转状态下的旋转精度与温度的变化等问题。
在实际的高速数控机床运用过程中,应该尽量提升轴承的刚度,以延长轴承的精度寿命。
同时,在提高机床主轴工作转速时,还要使其保持更高的旋转精度。
因此,对于高速数控机床主轴轴承精度及其保持性分析,有着非常重要的现实意义。
关键词:高速数控机床;主轴轴承;精度;保持性在高端装备制造行业之中,数控机床是必不可少的工作设备。
随着时代的发展,数控机床的特点也有了变化,逐渐变得更加高速化、智能化、高精度化。
近年来,我国轴承产业不断发展进步,产业经济规模已居世界轴承总量的第三位,但是与世界轴承工业强国相比,我国生产的轴承质量还存在一定差距,主要表现为高技术、高精度、高附加值的产品比例较低,相关产品的稳定性需要进一步的提高与改进。
一般情况下,精密机床使用的系列高端轴承是该设备中最精密的尖端产品,但由于国内机床轴承生产企业普遍处于研发能力弱、制造水平低、原材料等配套条件差的情况,导致国产高端轴承的精度、耐久性、性能稳定性、寿命和可靠性与国际先进水平有较大差距,因此高端机床轴承在全球范围内大多被美日欧等企业垄断,而国内机床精密主轴轴承生产企业还处于非系统化研发、制造和应用的阶段。
对高端轴承的设计和应用没有完整的产业链,对高端轴承应用需求的应对能力不足,导致我国高速高精度数控机床轴承的自主化未取得突破性进展。
在这种情况下,分析高速数控机床主轴轴承的精度及其保持性,有着非常重要的实际意义。
1、关于高速数控机床主轴轴承的相关内容概述轴承作为机床运行的“芯片”,是机床制造中重要的、关键的基础零部件之一,直接决定着机床产品的性能、质量和可靠性。
精度和切削能力是衡量机床质量的两个重要标准。
它们取决于机床的整体设计,但在很大程度上也取决于机床工件的轴承系统。
数控机床刚性与稳定性分析与优化策略
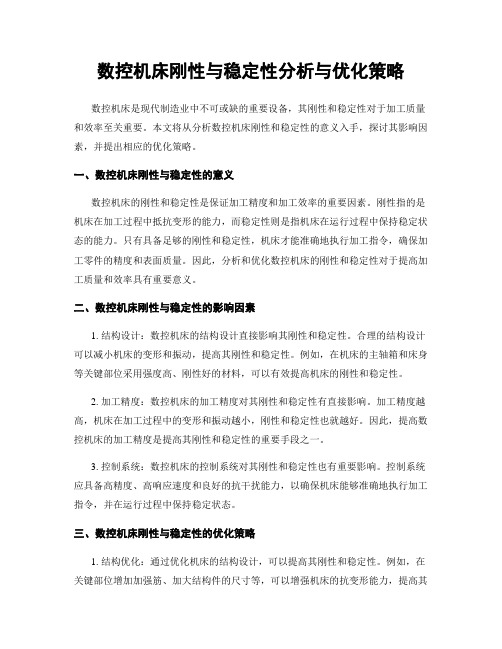
数控机床刚性与稳定性分析与优化策略数控机床是现代制造业中不可或缺的重要设备,其刚性和稳定性对于加工质量和效率至关重要。
本文将从分析数控机床刚性和稳定性的意义入手,探讨其影响因素,并提出相应的优化策略。
一、数控机床刚性与稳定性的意义数控机床的刚性和稳定性是保证加工精度和加工效率的重要因素。
刚性指的是机床在加工过程中抵抗变形的能力,而稳定性则是指机床在运行过程中保持稳定状态的能力。
只有具备足够的刚性和稳定性,机床才能准确地执行加工指令,确保加工零件的精度和表面质量。
因此,分析和优化数控机床的刚性和稳定性对于提高加工质量和效率具有重要意义。
二、数控机床刚性与稳定性的影响因素1. 结构设计:数控机床的结构设计直接影响其刚性和稳定性。
合理的结构设计可以减小机床的变形和振动,提高其刚性和稳定性。
例如,在机床的主轴箱和床身等关键部位采用强度高、刚性好的材料,可以有效提高机床的刚性和稳定性。
2. 加工精度:数控机床的加工精度对其刚性和稳定性有直接影响。
加工精度越高,机床在加工过程中的变形和振动越小,刚性和稳定性也就越好。
因此,提高数控机床的加工精度是提高其刚性和稳定性的重要手段之一。
3. 控制系统:数控机床的控制系统对其刚性和稳定性也有重要影响。
控制系统应具备高精度、高响应速度和良好的抗干扰能力,以确保机床能够准确地执行加工指令,并在运行过程中保持稳定状态。
三、数控机床刚性与稳定性的优化策略1. 结构优化:通过优化机床的结构设计,可以提高其刚性和稳定性。
例如,在关键部位增加加强筋、加大结构件的尺寸等,可以增强机床的抗变形能力,提高其刚性。
此外,还可以采用减振措施,如在机床床身上安装减振垫片等,以减小机床的振动,提高其稳定性。
2. 加工精度提升:通过提高数控机床的加工精度,可以减小机床的变形和振动,提高其刚性和稳定性。
为了提高加工精度,可以采取以下措施:提高机床的装配精度,加强机床的润滑和冷却系统,减小切削力等。
机械工程中的精确度与稳定性控制

机械工程中的精确度与稳定性控制机械工程作为一门工程学科,涉及到设计、制造和运用机械设备的各个方面。
在机械工程领域,精确度与稳定性控制是至关重要的因素。
本文将探讨机械工程中的精确度与稳定性控制的重要性,以及相关的技术和方法。
一、精确度控制在机械工程中,精确度是指产品或零部件与设计要求之间的偏差程度。
精确度控制是确保机械设备和零部件能够按照设计要求进行工作的关键因素之一。
精确度控制的目标是尽可能减小制造过程中的误差,以提高产品的质量和性能。
为了实现精确度控制,机械工程师需要使用各种测量和检测工具来监测制造过程中的偏差。
例如,精密测量仪器如千分尺、显微镜和光学测量设备可以用来测量零部件的尺寸、形状和表面质量。
通过与设计要求进行比较,机械工程师可以确定制造过程中的误差,并采取相应的措施来纠正这些误差。
此外,机械工程师还需要考虑材料的特性对精确度的影响。
不同材料的热胀冷缩系数、弹性模量和热稳定性等特性会对产品的精确度产生影响。
因此,在设计和制造过程中,机械工程师需要选择合适的材料,并考虑这些材料的特性对产品精确度的影响。
二、稳定性控制稳定性控制是指机械设备在运行过程中保持稳定性和可靠性的能力。
稳定性控制是确保机械设备能够长时间、高效地工作的关键因素之一。
稳定性控制需要考虑各种因素,包括结构设计、材料选择、制造工艺和运行条件等。
在机械工程中,结构设计是实现稳定性控制的重要方面。
机械设备的结构设计需要考虑到受力分布、刚度和振动等因素。
通过合理的结构设计,可以减小机械设备在运行过程中的振动和变形,从而提高其稳定性和可靠性。
此外,材料选择也对机械设备的稳定性产生影响。
机械工程师需要选择具有良好强度和耐磨性的材料,以确保机械设备在长时间运行过程中不会发生破损或失效。
同时,机械工程师还需要考虑材料的热稳定性和耐腐蚀性等特性,以适应不同的工作环境和工作条件。
三、精确度与稳定性控制的技术和方法在机械工程中,有许多技术和方法可用于精确度与稳定性控制。
机械系统的精度与稳定性分析

机械系统的精度与稳定性分析引言:机械系统的精度和稳定性对于现代制造业至关重要。
无论是生产设备还是消费品,都需要保证其精度和稳定性以确保性能和质量。
本文将分析机械系统的精度和稳定性,并讨论其影响因素以及如何提高系统的精度和稳定性。
一、精度分析1.1 什么是精度精度是指测量结果与实际值之间的偏差。
在机械系统中,精度表征了系统工作性能的高低。
精度高的系统能够更准确地进行测量和运动,从而提高产品质量和生产效率。
1.2 精度的影响因素机械系统的精度受到多个因素的影响,包括材料选择、工艺加工、组装精度等。
其中,材料的热胀冷缩、材料性能均匀性以及组件之间的配合间隙大小都会影响机械系统的精度。
1.3 测量精度与运动精度机械系统的精度可以分为测量精度和运动精度两个方面。
测量精度是指测量系统对于被测量物理量的准确度。
运动精度是指机械系统在运动过程中位置、速度和加速度等参数的精度。
两者相互关联,共同决定着机械系统的准确性和稳定性。
二、稳定性分析2.1 什么是稳定性稳定性是指机械系统在长时间运行过程中不发生不可预测的偏离或震动。
稳定性是机械系统工作可靠性的重要保证,对于降低损耗、延长设备使用寿命至关重要。
2.2 稳定性的影响因素机械系统的稳定性受到多个因素的影响,包括机械结构设计、传动系统的精度与稳定性、附件的遥测和控制等。
此外,外界环境因素如温度变化、湿度等也会对机械系统的稳定性产生影响。
2.3 提高稳定性的方法为了提高机械系统的稳定性,可以采取多种措施。
首先,对于机械结构设计,应该考虑加强刚度和稳定性,并合理设置减震和消声装置。
其次,传动系统的选用和精度对于稳定性有着重要影响,应该选择合适的传动方式和提高传动的精度与稳定性。
此外,附件的遥测和控制技术能够监测和调节机械系统的运行状态,进一步提高稳定性。
三、提高精度与稳定性的应用案例3.1 高精度工具机高精度工具机在数控加工中得到广泛应用。
通过采用高精度材料、精密加工工艺以及严格的组装要求,高精度工具机能够提供更高的定位精度和运动精度,从而大幅提高产品质量和加工效率。
数控机床加工精度与稳定性的研究与分析

数控机床加工精度与稳定性的研究与分析数控机床是机械制造中的重要设备,通过计算机控制和操作可以实现各种工件的复杂加工,逐渐取代人工加工成为现代制造业中不可或缺的设备。
数控机床加工精度与稳定性是数控机床的重要参数,关系到产品质量和生产效率。
本文将围绕数控机床加工精度与稳定性进行研究与分析。
一、数控机床加工精度的研究与分析数控机床加工精度是指工件加工后的尺寸偏差和形位偏差的统计指标。
在实际应用中,加工精度是数控机床的重要性能参数,它直接关系到加工成品的质量和精度。
因此,提高数控机床的加工精度是机械制造企业持续发展的迫切需要。
1.1 加工过程中误差的来源数控机床的加工精度与加工误差有着密切的关系,在加工过程中,加工误差的来源主要包括以下方面:(1)加工人员的技术水平和操作能力。
(2)机床结构的材料、加工工艺和精度。
(3)刀具的质量、刃口尺寸、材料和磨削方式。
(4)工件的材料、形状、尺寸和定位精度。
(5)切削液的性能和质量。
(6)环境因素如温度、湿度、振动等。
1.2 加工精度评价指标的研究数控机床加工精度是一种复杂的技术问题,通常采用绝对误差、相对误差、偏差、圆度、平面度、垂直度、同轴度、圆柱度等指标来评价。
这些指标有各自的装置和方法,需要在加工过程中进行严格的测量和记录。
1.3 加工精度提高的方法提高加工精度是数控机床加工质量的关键,可以采取下列方法:(1)加强操作人员的培训,提高技术水平和职业素质,减少人为误差。
(2)改进机床结构,增强机床的稳定性和刚性,减小加工误差。
(3)采用高品质的刀具,保证切削质量和切削稳定性,提高加工精度。
(4)优化工件的设计,改进制造工艺,提高加工精度和工件的定位精度。
(5)采用优质的切削液,降低温度和振动,保持加工环境的稳定性。
(6)加强加工质量的跟踪和记录,及时发现和排除各种误差。
二、数控机床加工稳定性的研究与分析数控机床加工稳定性是指机床在加工过程中的稳定性能,主要包括动态特性、静态特性和热特性三个方面。
国产数控机床精度保持性分析及研究现状
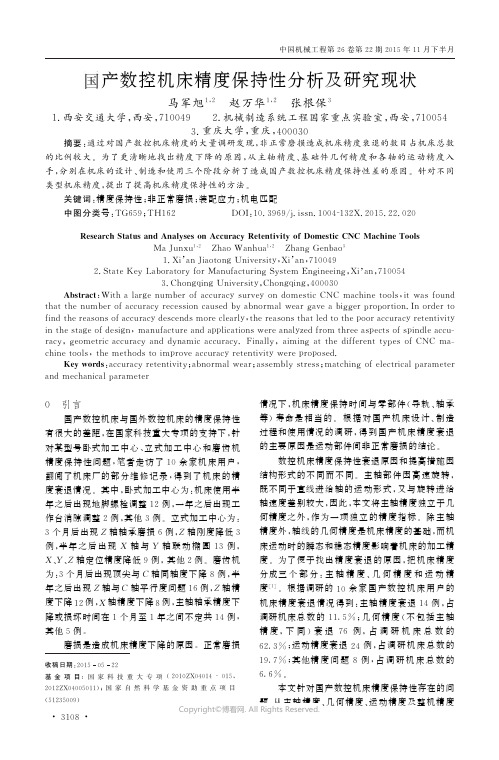
国产数控机床精度保持性分析及研究现状马军旭1,2赵万华1,2 张根保31.西安交通大学,西安,7100492.机械制造系统工程国家重点实验室,西安,7100543.重庆大学,重庆,400030摘要:通过对国产数控机床精度的大量调研发现,非正常磨损造成机床精度衰退的数目占机床总数的比例较大㊂为了更清晰地找出精度下降的原因,从主轴精度㊁基础件几何精度和各轴的运动精度入手,分别在机床的设计㊁制造和使用三个阶段分析了造成国产数控机床精度保持性差的原因㊂针对不同类型机床精度,提出了提高机床精度保持性的方法㊂关键词:精度保持性;非正常磨损;装配应力;机电匹配中图分类号:T G 659;T H 162 D O I :10.3969/j.i s s n .1004‐132X.2015.22.020R e s e a r c hS t a t u s a n dA n a l y s e s o nA c c u r a c y R e t e n t i v i t y o fD o m e s t i cC N C M a c h i n eT o o l s M a J u n x u 1,2 Z h a o W a n h u a 1,2 Z h a n g Ge n b a o 31.X i ’a n J i a o t o n g U n i v e r s i t y,X i ’a n ,7100492.S t a t eK e y L a b o r a t o r y f o rM a n u f a c t u r i n g S y s t e m E n g i n e e i n g,X i ’a n ,7100543.C h o n g q i n g U n i v e r s i t y ,C h o n g q i n g,400030A b s t r a c t :W i t ha l a r g en u m b e ro f a c c u r a c y s u r v e y ond o m e s t i cC N C m a c h i n e t o o l s ,i tw a s f o u n d t h a t t h en u m b e r o f a c c u r a c y r e c e s s i o nc a u s e db y a b n o r m a lw e a r g a v e ab i g g e r p r o po r t i o n .I no r d e r t o f i n d t h e r e a s o n s o f a c c u r a c y d e s c e n d sm o r e c l e a r l y ,t h e r e a s o n s t h a t l e d t o t h e p o o r a c c u r a c y r e t e n t i v i t yi n t h e s t a g e o f d e s i g n ,m a n u f a c t u r e a n d a p p l i c a t i o n sw e r e a n a l y z e d f r o mt h r e e a s p e c t s o f s p i n d l e a c c u -r a c y ,g e o m e t r i c a c c u r a c y a n dd y n a m i ca c c u r a c y .F i n a l l y ,a i m i n g a t t h ed i f f e r e n t t y p e so fC N C m a -c h i n e t o o l s ,t h em e t h od s t o i m p r o ve a c c u r a c y r e t e n t i v i t y w e r e p r o po s e d .K e y wo r d s :a c c u r a c y r e t e n t i v i t y ;a b n o r m a lw e a r ;a s s e m b l y s t r e s s ;m a t c h i n g o f e l e c t r i c a l p a r a m e t e r a n dm e c h a n i c a l pa r a m e t e r 收稿日期:20150522基金项目:国家科技重大专项(2010Z X 04014‐015,2012Z X 04005011);国家自然科学基金资助重点项目(51235009)0 引言国产数控机床与国外数控机床的精度保持性有很大的差距,在国家科技重大专项的支持下,针对某型号卧式加工中心㊁立式加工中心和磨齿机精度保持性问题,笔者走访了10余家机床用户,翻阅了机床厂的部分维修记录,得到了机床的精度衰退情况㊂其中,卧式加工中心为:机床使用半年之后出现地脚螺栓调整12例,一年之后出现工作台消隙调整2例,其他3例㊂立式加工中心为:3个月后出现Z 轴轴承磨损6例,Z 轴刚度降低3例,半年之后出现X 轴与Y 轴联动椭圆13例,X ㊁Y ㊁Z 轴定位精度降低9例,其他2例㊂磨齿机为:3个月后出现顶尖与C 轴同轴度下降8例,半年之后出现Z 轴与C 轴平行度问题16例,Z 轴精度下降12例,X 轴精度下降8例,主轴轴承精度下降或损坏时间在1个月至1年之间不定共14例,其他5例㊂磨损是造成机床精度下降的原因㊂正常磨损情况下,机床精度保持时间与零部件(导轨㊁轴承等)寿命是相当的㊂根据对国产机床设计㊁制造过程和使用情况的调研,得到国产机床精度衰退的主要原因是运动部件间非正常磨损的结论㊂数控机床精度保持性衰退原因和提高措施因结构形式的不同而不同㊂主轴部件因高速旋转,既不同于直线进给轴的运动形式,又与旋转进给轴速度差别较大,因此,本文将主轴精度独立于几何精度之外,作为一项独立的精度指标㊂除主轴精度外,轴线的几何精度是机床精度的基础,而机床运动时的瞬态和稳态精度影响着机床的加工精度㊂为了便于找出精度衰退的原因,把机床精度分成三个部分:主轴精度㊁几何精度和运动精度[1]㊂根据调研的10余家国产数控机床用户的机床精度衰退情况得到:主轴精度衰退14例,占调研机床总数的11.5%;几何精度(不包括主轴精度,下同)衰退76例,占调研机床总数的62.3%;运动精度衰退24例,占调研机床总数的19.7%;其他精度问题8例,占调研机床总数的6.6%㊂本文针对国产数控机床精度保持性存在的问题,从主轴精度㊁几何精度㊁运动精度及整机精度㊃8013㊃中国机械工程第26卷第22期2015年11月下半月Copyright ©博看网. All Rights Reserved.监控四个方面分析了国产数控机床在设计㊁制造和使用阶段造成精度保持性差的原因及解决方法,回顾了目前国产机床精度保持性的研究现状,并给出了提高国产数控机床精度保持性的建议㊂1 主轴精度保持性分析及研究现状主轴在设计阶段的主要任务是完成结构方案㊁分配零部件公差及确定零件间的配合;在制造阶段的主要任务是合理地施加预紧力,保证主轴刚度,限制主轴温升㊂国产主轴在精度设计时往往根据设计手册选择经济精度及其配合,在制造时根据经验选择预紧力,缺少科学计算的指导㊂使用时,主轴的温升会造成轴承间隙㊁预紧力的变化,如果在设计㊁制造时考虑不充分,就会造成轴承的非正常磨损㊂密封㊁润滑不良也将直接导致轴承非正常磨损,如图1所示㊂图1 主轴精度保持性影响因素因此,造成主轴轴承非正常磨损的因素主要为:设计阶段的轴承间隙(配合)过大或过小㊁密封及润滑结构不合理,以及制造阶段预紧力过大或过小㊂1.1 轴承间隙的合理设计设计阶段,通常为了保证主轴径向跳动精度,选择较小的轴承和主轴箱间隙㊂在结构和冷却㊁润滑参数确定的情况下,间隙越大,主轴径向跳动越大;反之,间隙越小,主轴径向跳动越小,但主轴发热变形越大,容易加剧磨损或者造成轴承卡死㊂为了提高主轴的精度保持性,合理地选择轴承与主轴箱间隙,减小轴承的非正常磨损显得尤其重要㊂B u r t o n等[2]研究了主轴在使用时温度造成角接触轴承尺寸的变化情况,并给出了计算方程,但是计算精度不够高㊂J e d r z e j e w s k i等[3]为了从热变形㊁刚度等方面来评价间隙设计结果,利用有限元法和有限差分法建立了高速加工中心主轴箱混合模型,分析了因旋转速度变化形成的离心力造成的间隙变化㊂H o l k u p等[4]同时考虑了轴承滚珠㊁滚道的接触变形线性叠加轴承外圈与轴承座的热变形来计算轴承间隙㊂K i m等[5]建立了轴承间隙随外部载荷㊁转速和操作时间变化的变形曲线,为间隙设计提供了依据㊂但是其提供的是单个轴承在各种工况下的变形量,一般情况下,主轴轴承是成组使用的㊂因此,为了提高主轴的精度保持性,减小轴承非正常磨损,在设计轴承间隙时,需要同时考虑转速变化引起的离心力造成的轴承变形㊁预紧力造成的轴承发热变形㊁主轴的冷却效果以及轴承的配置方式等的影响㊂1.2 预紧力的合理选择主轴的功能是给刀具提供足够的动力和刚度来保证正常切削工件㊂在制造阶段,为了保证主轴有足够的刚度,往往对轴承施加预紧力㊂预紧力越大,主轴刚度越大,主轴发热变形也越大,轴承越容易磨损,主轴精度保持性越差㊂合理保证服役状态下主轴预紧力,能够减小主轴轴承发热造成的非正常磨损,提高主轴精度保持性㊂K i m等[6]通过预紧力测试装置和跳动测试装置测试了不同切削条件下预紧力对跳动精度的影响,优化了主轴预紧力㊂J i a n g等[7]为了获得高转速低温升㊁低转速高刚度主轴的预紧力,建立了离心力和陀螺效应影响的轴承非线性模型,利用传递矩阵法(t r a n s f e r m a t r i x m e t h o d,T MM)分析了调压预紧时的温升和刚度,得到结论:高速时,根据主轴温度变化选择预紧力,低速时,根据主轴轴承的疲劳寿命选择预紧力㊂C h e n等[8]在分析预紧力对温升的影响时,得到结论:低速时(转速n<10000r/m i n),温升与预紧力的关系不大;高速时(转速n>10000r/m i n),由于离心力造成滚珠和内圈的接触不良,所以摩擦力增大,温升增大㊂蒋兴奇等[9]为了防止高速轴承出现内沟道或钢球表面的擦伤,同时又使轴承的运转摩擦力矩最小,给出了主轴角接触轴承最小预紧载荷的计算方法㊂给出的轴承预紧力影响因素是在主轴径向载荷很小(10N)的条件下计算得到的,不能适用于机床的切削状态㊂因此,考虑使用状态下的转速㊁切削载荷㊁温升对预紧力的影响,才能保证装配时的预紧力在使用状态下是合理的,减小预紧力设置不当造成的精度衰退,提高主轴精度的保持性㊂1.3 润滑和密封不当主轴轴承的密封和润滑不当也是造成国产数控机床主轴㊁特别是磨削类主轴轴承非正常磨损的重要原因㊂申阳等[10]统计了国产主轴轴承损㊃9013㊃国产数控机床精度保持性分析及研究现状 马军旭 赵万华 张根保Copyright©博看网. All Rights Reserved.坏的形式,指出润滑不良是主轴异常磨损的一个重要因素㊂磨削类机床由于砂轮在工作时磨粒的脱落造成冷却液中杂质过多,如果轴承密封不良更容易造成主轴轴承的磨损㊂余常武[11]针对某型号磨床主轴轴承密封不严造成主轴磨损的情况(最严重的情况是试切时轴承磨损损坏),改进了主轴密封结构,使其精度保持时间延长至17个月以上㊂由国产主轴精度保持性的分析和回顾可知,提高国产数控机床主轴精度保持性的措施应在主轴的设计和制造阶段实施㊂应考虑主轴使用工况,合理设计主轴间隙㊁选择预紧力,进而提高机床主轴精度保持性㊂2 几何精度保持性分析及研究现状根据G B18400.1‐2010中几何精度的检测项目,除去与主轴精度相关的项目,几何精度主要是与运动轴线相关的精度㊂运动轴线几何精度保持性取决于基础件精度保持性㊂基础件在设计阶段的主要任务是完成结构方案,校核刚度和强度,确定导轨安装基准面等的公差;在制造阶段的主要任务是合理地消除基础件内应力以及保证装配后的几何精度㊂国产数控机床在设计时根据设计手册选择零件的经济精度,当装配精度达不到要求时,利用试凑或者采用不恰当的拧紧等措施使基础件局部变形过大来保证几何精度,造成较大的装配应力㊂内应力消除往往根据经验,缺乏规范的工艺措施㊂如果设计时不能充分考虑装配时和使用时力㊁热等造成的基础件精度变化,就会导致精度设计不合理,进而可能造成装配时产生较大的装配应力,使用时装配应力释放导致导轨滑块安装基准变化,加剧导轨滑块磨损㊂如果制造阶段内应力释放不完全,服役时,内应力释放也将导致导轨滑块的安装基准发生变化,造成导轨滑块的非正常磨损,精度保持性下降,如图2所示㊂因此,造成导轨滑块非正常磨损的主要因素为:内应力释放变形和装配应力蠕变变形等㊂2.1 内应力消除工艺机床基础件大部分为铸件,少量为焊接件,在铸造或焊接过程中会产生一定的内应力㊂为了使内应力得到充分释放,往往采用自然失效的方式处理基础件㊂自然失效周期较长,不能满足生产时,采用热时效的方式㊂热时效耗能大,基础件大小受限于时效炉的尺寸㊂目前较为流行的是振动时效㊂L i等[12‐13]利用有限元仿真得到床身的各阶振型,作为振动时效工艺参数选择的依据,但是图2 几何精度保持性影响因素没有定量给出铸造残余应力振动时效后应力变化的大小㊂低频振动时效时零件变形量大,甚至出现破坏,H e等[14]为了防止出现这种现象,提出了超过1k H z的高频振动工艺方案,在两块焊接的钢板上进行了试验验证,得到高频振动更能均化焊接件的残余应力的结论㊂焊接件一般质量较小,但是对于大型铸件,高频振动受激振能量限制,不太合适㊂胡敏等[15]针对某型号卧式加工中心床身结构,利用模态分析选择了振动时效的激振频率㊁支撑点㊁激振点和拾振点,根据工件质量选择了激振时间,根据最大动应力和激振力的关系选择了激振力大小,并且与原有振动工艺消除应力的效果进行了对比㊂目前,对振动时效的定量研究较少,大部分工厂是按照经验对大型基础件进行振动时效处理㊂因此,为了减小内应力释放变形造成的轴线基准变形以及基准变形造成的导轨滑块非正常磨损,需要规范基础件制造时的内应力工艺,定量控制内应力的大小㊂2.2 减小装配应力的措施设计时如果没有考虑移动部件重力在全行程内造成的基础件精度变化,造成装配后的轴线几何精度达不到设计要求,现场采用不恰当的拧紧等措施使基础件局部变形过大来保证导轨的直线度㊁平行度等精度,就会产生较大的装配应力㊂机床使用时,地脚螺栓中受力较大的螺栓蠕变较快,导轨安装基准变化;同时,导轨的基准变化将加剧导轨滑块的磨损,轴线几何精度丧失㊂在设计阶段,张文凯[16]根据卧式加工中心移动部件在行程内质心位置变化造成的导轨安装基准面变形,利用A N S Y S的A P D L语言优化了地脚螺栓布局,使导轨安装面直线度由11.6μm减㊃0113㊃中国机械工程第26卷第22期2015年11月下半月Copyright©博看网. All Rights Reserved.小到了8.6μm㊂减小了为保证机床精度造成的部分地脚螺栓应力,使地脚螺栓的布局设计更加合理㊂张景和等[17]在大型非球面超精密机床上设计了卸荷浮板结构,减小了导轨负荷(导轨及其上移动部件的质量)㊂当卸荷量达到12k N时,主导轨直线度为0.375μm/600mm㊂张伯鹏等[18]针对大型数控龙门铣床横梁重力变形问题,在辅助梁上设置了3个出力可控的液压千斤顶,利用遗传算法实现了自演机制,减小了重力变形造成的误差㊂上述两种方法利用改变横梁结构,增大横梁刚度,减小了重力变形对导轨直线度的影响,间接地提高了机床的精度保持性㊂但是受机床结构影响,有些机床不能通过改变结构来增大横梁刚度,只能通过制造阶段的工艺措施来合理地保证精度㊂在制造阶段,胡万良等[19]利用压电式传感器发明了智能垫铁(Z L200910024358.7),该智能垫铁能够监测机床垫铁的受力大小,用于机床在装配时保证地脚螺栓受力均匀,减小机床使用时地脚螺栓蠕变量的不一致㊂智能垫铁只是监测了地脚螺栓的受力状况,可以再改进使其能够自动调整来保证地脚螺栓受力均匀㊂郭铁能等[20‐21]针对数控重型龙门铣床超跨距横梁由于跨度大㊁滑板滑枕质量大造成的横梁向下弯曲(最大挠度可达1mm),采用对导轨面预起拱的方法来补偿横梁变形对加工精度的影响㊂利用合理的装配工艺保证机床的精度,间接地提高了机床的精度保持性㊂单个运动轴的装配应力会造成导轨滑块的非正常磨损,运动轴间的装配应力是由于固定结合面精度的设计和装配的不合理产生的,固定结合面的螺栓蠕变会造成运动轴间的垂直度㊁平行度等精度的衰退㊂螺栓蠕变常见于高温下法兰盘连接用螺栓的蠕变,而O e h l e r t等[22]㊁N e e r a j等[23]认为,常温下金属在一定载荷下也会发生蠕变,单琳豪[24]研究了船用螺旋桨在服役时的蠕变㊂目前还缺少机床结合面螺栓蠕变造成的几何精度衰退规律㊂根据几何精度保持性的分析和回顾,提高国产数控机床几何精度保持性的措施应在机床的设计和制造阶段实施㊂考虑装配应力㊁内应力等的影响,合理设计基础件精度,规范装配工艺,避免为了保证精度而牺牲精度保持性㊂3 运动精度保持性分析及研究现状数控机床的运动精度不同于准静态下的几何精度,是机床在保证几何精度的前提下,进给时运动轴在位移㊁速度㊁加速度三个方面的瞬态和稳态精度[1]㊂运动精度取决于进给系统的机电参数是否匹配㊂数控机床较普通机床最大的优势在于多图3 加工振纹轴联动,单轴的运动不稳定决定了多轴联动误差,联动加工时将在工件表面产生振纹等,影响工件的加工质量,如图3所示㊂机床使用一段时间后,机械参数中的接触刚度和阻尼等随运动副的磨损而变化;电机线圈绕组中漆包绝缘层出现老化导致线圈间的绝缘电阻值变化,输出电磁力矩中出现谐波成分㊂机电参数不再是初始的最优匹配,就会造成运动精度的下降,精度保持性变差㊂运动精度下降之后可以通过机电参数匹配在一定程度上进行恢复㊂表1所示为某台机床在使用一段时间后的运动精度对比㊂表1 某型号机床运动精度衰退及恢复对比表参数出厂最优值1年后衰退调整后恢复机械参数传动刚度(108N/m)2.932.652.65伺服参数速度环增益(H z)7.67.69.2位置环增益(H z)333.5误差值位移波动幅值(μm)1.631.991.67速度波动幅值(mm/m i n)7.959.308.25 机电参数匹配之前,需要辨识机械参数和电机参数,然后通过一定的控制算法进行匹配㊂R e n等[25]提出了子结构参数耦合辨识方法,C e l i c 等[26]基于子结构参数耦合辨识方法提出了改进的关节参数辨识方法,对固定结合部刚度进行了辨识㊂但是数控机床非正常磨损造成的是动结合部的动力学参数变化㊂胡峰等[27‐28]在丝杠径向施加简谐振动,利用初参数解析法辨识了丝杠支撑处㊁螺母处和导轨滑块处的刚度㊂邰晓辉[29]利用I n a m u r a和S a t a方法识别了系统中的轴承㊁螺母的轴向刚度和阻尼㊂但是其辨识的只是轴承和螺母的刚度,不是整个进给系统的刚度㊂陈光胜等[30]利用编码器和光栅尺的信号作为输入信号,对进给系统机械刚度进行了辨识㊂上述辨识都是在静态下进行的,而运动精度恢复需要的是动态下辨识的机械参数㊂曹锟[31]针对高速进给系统的高阶线性模型,将M序列和匀速运动信号相叠加,改进了辨识方法,对某型号机床的直线进给轴刚度进行了辨识,并利用激光干涉仪进行了验证㊂㊃1113㊃国产数控机床精度保持性分析及研究现状 马军旭 赵万华 张根保Copyright©博看网. All Rights Reserved.J o k s i m o v i c等[32]对感应电机定子绕组匝间短路故障引起的线电流频谱变化进行了建模和仿真分析,发现相比于正常电机,匝间短路故障电机线电流频谱中出现电流基频的三次谐波,正常电机中存在谐波成分的幅值增大㊂T a l l a m等[33]利用坐标变换理论得到了感应电机定子绕组匝间短路故障的瞬态模型㊂该模型能够根据误差灵敏度函数准确预测故障线电流的正序和负序部分量值㊂N i c o l a s等[34]基于电流残差定义的故障因子对永磁同步电动机匝间短路故障进行了建模和分析,考虑使用条件和参数不确定性使得预测模型能够对匝间短路电阻小于1kΩ的故障进行准确预测㊂蒋锐权等[35]利用神经元的自学习功能,提出了适用于数控机床位置伺服控制的神经元控制器,该算法结构简单,不需要知道受控对象的结构和参数,而影响精度保持性的恰恰是结构机械参数的变化,因此这种算法不能满足要求㊂I r i s a 等[36]通过辨识伺服进给系统的数学模型,将控制参数整定转化为非线性约束方程的求解过程,此方法能够得到较满意的效果,但整定过程比较复杂㊂K u o等[37]利用遗传算法对五轴数控机床的运动控制参数进行了整定,其整定后的参数在一定程度上改善了机床加工的轮廓精度㊂陈鹏展[38]提出了先获得机械表征对象特征的参考模型,再对参考模型进行控制参数寻优的方法,既保证了控制参数整定的快速性,又能得到满意的整定结果㊂李学伟[39]针对多轴联动中,轨迹预补偿方法中误差分配为考虑各轴跟随特性而导致补偿效果不理想的问题,提出了零相差轨迹与补偿控制方法,利用加工圆弧和抛物线方案进行了验证㊂根据运动精度保持性的分析和回顾,提高数控机床运动精度保持性的措施应在机床的制造和使用阶段实施㊂机械参数的辨识㊁电机参数的辨识和合理的机电匹配算法是提高国产数控机床精度保持性的关键㊂4 整机精度监控系统调研时发现,国产数控机床在使用时,由于使用不当(如切削力过载)和维护保养不足(如润滑油不够清洁)等造成机床轴承及静压导轨等零部件的过早磨损,机床精度下降的情况也较多㊂因此,针对国产数控机床的这一特殊情况,研发整机监控系统,对机床进行工作状态监控及维护保养也能延续机床的精度保持性㊂机床在使用期间,如果机床切削力过大,将加剧主轴轴承的受力,造成轴承的非正常磨损,机床精度很快下降㊂因此,监控切削力大小,设置切削过载报警有助于延长机床的精度保持性时间㊂朱晓春[40]提出通过检测主轴和进给电动机的功率和角速度,计算出切削扭矩,来实现切削过载的在线监控㊂对切削力进行监控,不仅有利于减小刀具的磨损,而且还可以减小主轴轴承因过载造成的磨损㊂润滑液不清洁会加剧运动部件间的磨损,造成导轨滑块或者轴承精度下降㊂特别是磨削类机床,磨粒脱落在冷却液中,如果轴承密封不当,极易造成轴承的磨损[11]㊂通过对润滑液清洁度监控,及时更换不合格的润滑液,定期保养机床,也有利于提高机床的精度保持性㊂张根保等[41]建立了基于液压系统清洁度熵的关键故障源提取模型,提取出了关键故障源,对其清洁度进行了控制,这样有利于减小液压元件(如静压导轨等)的非正常磨损,提高机床的精度保持性㊂李平等[42]建立了丝杆磨损量与驱动电机做功的数学模型,利用监控驱动电机做功的总量来决定丝杆是否需要维护㊂丝杠的磨损影响半闭环控制机床的定位精度和重复定位精度㊂陈宇[43]分析了机床关键功能部件故障数据,在有用性最大的基础上提出了最佳预防维修间隔时间模型,并求得该机床关键功能部件最佳预防维护间隔时间㊂对于不同类型的机床,需要监控的参数类型和参数的阈值范围是不同的,这需要根据机床的特点进一步研究才能确定㊂根据整机精度监控的分析和回顾,在机床的使用阶段,对机床工作状态及工作环境进行监控,适时地对机床进行维护保养,也能提高机床的精度保持性㊂对机床整机精度监控的项目有:润滑油的清洁度㊁液压系统压力㊁电机的功率㊁主轴振动㊁环境温度㊁湿度㊁空气清洁度㊂通过这些参数的监控,可实施维修时间在线预报和强制维护保养㊂5 提高国产数控机床精度保持性的建议通过国产数控机床精度保持性的分析及相关研究文献的回顾,根据调研的国产数控机床设计㊁制造过程和使用环境,针对机床的三类精度,为避免非正常磨损,提高国产数控机床精度保持性,在设计㊁制造和使用阶段提出以下建议㊂(1)几何精度保持性方面㊂提高措施应集中在设计和制造阶段的精度合理保证㊂造成导轨滑块非正常磨损的主要因素有:考虑移动部件质心㊃2113㊃中国机械工程第26卷第22期2015年11月下半月Copyright©博看网. All Rights Reserved.。
如何保持数控机床技术的稳定性与可靠性

如何保持数控机床技术的稳定性与可靠性数控机床作为一种高精度、高效率的自动化加工设备,广泛应用于各个制造领域。
然而,随着技术的不断发展和机床的长期使用,数控机床技术的稳定性和可靠性也面临着一些挑战。
本文将讨论如何保持数控机床技术的稳定性与可靠性,为制造企业提供指导和建议。
首先,对数控机床进行定期维护是确保其稳定性和可靠性的重要措施。
定期维护包括设备清洁、润滑加油、零部件更换等,目的是防止设备因长时间使用而积累的污垢和磨损导致性能下降和故障发生。
制定合理的维护计划,并由专业的技术人员进行操作和监督,可以延长机床的使用寿命并提高工作效率。
其次,培训和管理机床操作人员也是关键。
操作人员需要具备良好的技术水平和丰富的经验,能够熟练使用数控机床并处理常见的故障。
因此,企业应该注重对操作人员的培训,提供系统的培训计划和培训课程,培养他们的技术能力和责任意识。
此外,建立科学的管理制度和流程,加强对操作人员的管理和监督,确保他们严格按照操作规程操作机床,遵守安全操作规定。
同时,合理的工艺设计和优化也是确保数控机床稳定性和可靠性的重要因素。
工艺设计应该根据机床的性能特点和加工工件的要求,在保证产品质量的前提下尽量降低机床的负荷和损耗。
合理的刀具选择、切削参数设置和工件夹持方式,能够减少机床的振动和磨损,提高加工效率和成品率。
此外,通过对工艺流程的优化和改进,可以进一步提高机床的稳定性和可靠性。
除了以上几点,对设备进行性能监测和数据分析也是重要的措施。
利用现代化的监测设备和数据分析技术,对机床的关键性能指标进行实时监测和记录,可以及时发现和预测潜在的故障和问题。
通过对大量的监测数据进行统计分析和研究,可以找出问题的根源和解决方案,进一步提高机床的稳定性和可靠性。
最后,加强与设备供应商的合作也是保持数控机床技术稳定性和可靠性的重要途径。
设备供应商通常具备丰富的经验和专业知识,可以为企业提供机床的技术支持和维护服务。
与供应商建立长期稳定的合作关系,定期进行技术交流和合作,可以获得及时的技术支持和维修服务,为机床的稳定性和可靠性提供保障。
数控机床可靠性技术的分析与研究

数控机床可靠性技术的分析与研究一、概述随着制造业的快速发展,数控机床作为现代制造技术的核心设备,其可靠性对于保证生产过程的稳定性和产品质量具有至关重要的作用。
数控机床可靠性技术是指研究数控机床在规定的条件下和规定的时间内,完成规定功能的能力。
这一技术的提升不仅关乎到企业的生产效率,更是决定产品竞争力的关键因素。
近年来,随着新材料、新工艺和新技术的不断涌现,数控机床的复杂性和精度要求越来越高,其可靠性问题也日益凸显。
对数控机床可靠性技术的研究和分析变得尤为重要。
通过对数控机床可靠性技术的研究,可以深入了解机床的失效模式和机理,为机床的设计、制造、使用和维护提供科学依据,进而提升机床的可靠性水平,确保生产过程的顺利进行。
同时,数控机床可靠性技术的研究也是制造业持续创新和发展的必然要求。
在全球经济一体化和市场竞争日益激烈的背景下,提高数控机床的可靠性水平,不仅可以提升企业的核心竞争力,还可以推动整个制造业的转型升级,实现可持续发展。
数控机床可靠性技术的研究与分析具有重要的理论意义和实践价值。
本文将从数控机床的可靠性定义出发,探讨其可靠性分析的方法和技术,分析影响可靠性的主要因素,并提出提高数控机床可靠性的措施和建议,以期为我国制造业的发展提供有益的参考。
1. 数控机床在现代制造业中的重要性在现代制造业中,数控机床的重要性不言而喻。
作为制造业的核心设备之一,数控机床的精度、效率、稳定性以及可靠性等性能直接影响到产品的质量和生产效率。
随着全球制造业的快速发展,特别是在中国这样的制造业大国,数控机床的需求量与日俱增。
对于数控机床可靠性技术的深入分析和研究,不仅有助于提升我国制造业的整体竞争力,更对保障国家经济安全具有重要意义。
数控机床的高精度和高效率是现代制造业追求的核心目标。
在许多高精度、高复杂度的零部件制造过程中,如航空航天、汽车制造、模具制造等领域,数控机床的作用无可替代。
其高精度加工能力能够确保零部件的尺寸精度和表面质量,满足产品性能和使用寿命的要求。
数控机床的加工精度与稳定性研究

数控机床的加工精度与稳定性研究数控机床是现代制造业中不可或缺的重要设备,其加工精度和稳定性直接影响到产品质量和生产效率。
本文将围绕数控机床的加工精度和稳定性展开研究,探讨其影响因素以及提高方法。
一、加工精度的影响因素1. 设备本身的精度:数控机床的加工精度与其自身的精度有着密切的关系。
设备的结构设计、传动系统、控制系统等都会对加工精度产生影响。
因此,在选购数控机床时,应注意选择具有高精度的设备。
2. 刀具的选择和磨削:刀具是数控机床加工过程中的重要因素之一。
刀具的质量和磨削状态直接影响到加工精度。
选择合适的刀具材料和磨削方式,能够提高加工精度。
3. 工件的材料和形状:不同材料和形状的工件对数控机床的加工精度要求不同。
一些材料如高硬度材料、难加工材料等,对机床的稳定性和切削性能要求较高。
同时,工件的形状也会对加工精度产生影响,复杂形状的工件通常需要更高的加工精度。
4. 加工工艺参数:数控机床的加工精度还与加工工艺参数密切相关。
例如,进给速度、切削速度、切削深度等参数的选择会对加工精度产生影响。
合理选择和调整这些参数,能够提高加工精度。
二、稳定性的研究与改进1. 机床结构的优化:数控机床的结构设计对其稳定性有着重要影响。
优化机床的结构能够提高其刚性和稳定性,减少振动和变形,从而提高加工精度和稳定性。
2. 控制系统的改进:数控机床的控制系统是实现稳定性的关键。
采用先进的控制算法和技术,提高控制系统的响应速度和精度,能够有效提高机床的稳定性。
3. 润滑系统的优化:数控机床的润滑系统对其稳定性和寿命有着重要影响。
优化润滑系统的设计和选用合适的润滑材料,能够减少机床的摩擦、磨损和热变形,提高机床的稳定性。
4. 检测与监控技术的应用:采用先进的检测与监控技术,能够实时监测机床的工作状态和加工精度,及时发现问题并进行调整和修正,提高机床的稳定性和加工精度。
总结起来,数控机床的加工精度和稳定性是制造业中非常重要的研究课题。
CNC机床加工中的加工精度与稳定性分析研究

CNC机床加工中的加工精度与稳定性分析研究随着工业技术的发展,计算机数控(CNC)机床在各个领域的应用逐渐增多。
CNC机床通过计算机指令控制工具的运动,具有高精度、高效率和自动化生产的优势。
然而,在CNC机床的加工过程中,加工精度与稳定性是影响加工质量的重要因素。
本文将对CNC机床加工中的加工精度与稳定性进行分析研究。
一、加工精度的影响因素CNC机床的加工精度受多种因素的影响,主要包括以下几个方面:1. 机床本身的精度:机床的结构刚度、导轨精度、传动精度等直接影响CNC机床的加工精度。
如机械结构刚度不足,导致机床变形,将影响加工零件的精度。
2. 刀具的选择与磨制:刀具的质量和形状对加工精度有着重要的影响。
选择合适的刀具材料和磨制工艺,能够保证工件的加工精度。
3. 加工参数的设置:CNC机床加工过程中,加工速度、进给速度、切削深度等加工参数的设置直接关系到加工精度。
合理的参数设置能够提高加工精度。
4. 环境温度和湿度:环境因素也会对CNC机床的加工精度造成一定影响。
温度和湿度的变化可能导致机床的膨胀和变形,从而影响加工精度。
二、加工稳定性的研究在CNC机床加工过程中,加工稳定性是确保加工质量的关键。
加工稳定性的研究主要包括以下几个方面:1. 加工振动分析:CNC机床在高速运动时会产生振动,振动可能会对加工精度和表面质量造成影响。
因此,需要进行振动分析,找出振动的原因并采取相应的措施进行控制。
2. 切削力分析:切削力是CNC加工中常见的力,对加工稳定性有一定的影响。
通过对切削力的分析,可以确定合适的切削参数,提高加工稳定性。
3. 切削液的选择与喷洒方式:切削液对CNC机床加工稳定性起着重要作用。
选择适合的切削液以及合理的喷洒方式,能够有效减少切削温度、延长工具寿命、提高表面质量。
4. 工件夹持方式的研究:工件夹持方式直接关系到工件的定位精度和加工稳定性。
研究不同的工件夹持方式,选择合适的夹具,能够提高加工精度和稳定性。
数控机床的工作稳定性与切削性能研究

数控机床的工作稳定性与切削性能研究数控机床是现代制造业中常见的一种工具,它通过计算机控制系统来实现自动化操作。
在工业生产中,数控机床的工作稳定性和切削性能是影响产品质量和生产效率的重要因素。
因此,对数控机床的工作稳定性和切削性能进行研究具有重要意义。
首先,我们来探讨数控机床的工作稳定性。
工作稳定性是指数控机床在工作过程中保持稳定状态的能力。
数控机床的工作稳定性受多种因素影响,包括机床结构、控制系统、刀具刚性等。
机床结构的稳定性是保证机床工作稳定的基础,而控制系统的性能则直接影响到机床的工作精度和稳定性。
此外,刀具刚性也是影响数控机床工作稳定性的关键因素之一。
因此,研究数控机床的工作稳定性需要考虑这些因素的综合作用。
其次,我们来探讨数控机床的切削性能。
切削性能是指数控机床在切削过程中所表现出的性能指标,包括切削力、切削温度、切削表面质量等。
切削力是数控机床切削过程中所受到的力的大小,它直接影响到切削效率和切削质量。
切削温度是指切削过程中产生的热量,过高的切削温度会导致刀具磨损加剧和工件变形等问题。
切削表面质量则是评价数控机床切削性能的重要指标之一,它直接影响到产品的质量和外观。
因此,研究数控机床的切削性能需要对切削力、切削温度和切削表面质量等指标进行综合分析和评价。
在研究数控机床的工作稳定性和切削性能时,我们可以采用实验方法和理论分析相结合的方式。
实验方法可以通过实际操作数控机床,收集相关数据并进行分析,从而得出数控机床的工作稳定性和切削性能。
理论分析则可以通过建立相应的数学模型,对数控机床的工作稳定性和切削性能进行预测和优化。
两种方法的结合可以提高研究的准确性和可靠性。
除了实验方法和理论分析,还可以借助先进的技术手段来研究数控机床的工作稳定性和切削性能。
例如,利用计算机仿真技术可以对数控机床的工作过程进行模拟,从而对工作稳定性和切削性能进行评估和分析。
此外,利用人工智能技术可以对数控机床进行智能化控制,提高其工作稳定性和切削性能。
立式数控加工中心的加工精度和稳定性分析

立式数控加工中心的加工精度和稳定性分析随着现代制造业对精度要求的不断提高,立式数控加工中心作为一种高精度加工设备,受到了广泛的应用和关注。
本文将对立式数控加工中心的加工精度和稳定性进行深入分析,以帮助读者更好地理解和应用该技术。
一、加工精度分析1. 加工精度的定义和重要性加工精度是指加工件在满足设计要求的前提下,上下浮动的允许范围。
在立式数控加工中心中,加工精度是评判其工艺水平和设备性能的重要指标。
加工精度直接影响加工零件的质量和准确度,对于提高产品的使用寿命和装配精度具有至关重要的作用。
2. 影响加工精度的因素立式数控加工中心的加工精度受到许多因素的影响,主要包括以下几个方面:(1) 机床的结构与刚度:机床的稳定性和刚度决定了其在高速运动和重负荷下的抗振能力,直接影响到加工精度。
(2) 主轴系统:主轴系统的精度和稳定性对加工精度有直接影响。
主轴的转动精度和热变形对于高精度加工尤为重要。
(3) 导轨系统:导轨系统的精度直接影响到加工中心的定位精度和稳定性。
导轨系统的刚度和精度决定了加工中心的加工质量。
(4) 伺服系统:伺服系统负责机床的运动控制,对加工中心的定位精度和运动稳定性起着关键作用。
(5) 刀具磨损与刀具寿命:刀具的磨损会使得加工精度下降,因此刀具的寿命和磨损情况需要经常进行监控和维护。
3. 加工精度的检测和评估为了确保加工精度的稳定和可靠,需要对立式数控加工中心进行加工精度的检测和评估。
一般常用的方法有以下几种:(1) 摸测法:通过直接测量加工件和设定座标的差值,评估加工精度。
(2) 比对法:将加工件与已知精度的标准件进行比对,通过比对测试精度。
(3) 激光干涉法:利用激光干涉的原理,精确测量加工件的形状和尺寸。
以上方法可以通过各种精度检测工具和设备来实施,如测高仪、千分尺、三坐标测量机等。
二、稳定性分析1. 稳定性的概念和意义稳定性是指立式数控加工中心在加工过程中的表现稳定性和抗干扰能力。
关于加工中心精度热稳定性控制的一些探讨

关于加工中心精度热稳定性控制的一些探讨加工中心精度热稳定性控制(一)加工中心精度热稳定性研究的意义1、加工中心精度热稳定性是加工中心机床精度的关键保障。
由于高速加工中心的工作过程涉及磨削机构的高速转动的圆柱和滑块的热变形,以及现场环境因素对机床整体加工精度的影响,因此加工中心运行时精度热稳定性问题尤为突显。
2、加工中心精度热稳定性研究可以从多个方面提高加工中心机床的加工质量。
进行精度热稳定性研究,可以在设计时采取切实有效的措施,实现加工中心机床的精度热稳定性;可以采取合理的参数和工艺结合,努力增加加工中心的稳定性;还可以检测加工数据,实时采取精度的措施,尽可能提高加工中心的精度。
(二)加工中心精度热稳定性研究的方法1、采取合理的机构结构设计和分析方法。
对加工中心机床的主要构件、结构和固有参数进行评估和优化,减少主要部件和结构的各种不确定性和摩擦,以达到较好的热稳定性。
2、采用回环控制策略。
根据加工中心热变形和现场环境因素影响性能的特点,采取有效的回环控制、优化分析,增强对精度热稳定性的控制能力。
3、采用模型和仿真方法。
以数值模型为基础,以加工和热变形为主要研究对象,结合加工精度和稳定性预测分析,仿真试验,相应的调整参数和设计参数,达到更好的加工中心精度热稳定性。
(三)加工中心精度热稳定性控制的重要性1、加工中心精度热稳定性是加工中心精度的关键保障,影响着工件在加工中心上加工精度、稳定性,以及综合加工效果,具有重要的意义。
2、加工中心精度热稳定性的调节和控制,关系到机床的功能参数,也是一个系统工程。
必须综合评价和分析,采取有效的机构设计方法,对精度热稳定性的的考虑和控制问题。
3、加工中心精度热稳定性的控制有利于大大提高机床的移动精度和加工精度,改善加工中心在高速运行时出现的精度不稳定现象,降低损失,较大程度提高产品质量和加工效率。
CNC机床加工中的加工稳定性分析与改进

CNC机床加工中的加工稳定性分析与改进CNC机床作为现代制造业中的重要工具,广泛应用于各种加工领域。
在进行加工过程中,加工稳定性是一个关键的问题,它直接影响到加工精度和加工效率。
本文将对CNC机床加工中的加工稳定性进行分析,并提出一些改进的方法。
一、加工稳定性的影响因素在分析加工稳定性之前,我们先来了解一下加工稳定性的影响因素。
首先是刀具与工件之间的相互作用力,如果刀具与工件之间的相互作用力不稳定,就会导致加工过程中的振动,从而降低加工质量。
其次是切削参数的选择,例如切削速度、进给速度和切削深度等,这些参数的选择不当也会影响加工的稳定性。
最后还有机床的结构与性能,如果机床的刚性不足或者精度较低,也会对加工的稳定性产生不利影响。
二、加工稳定性的分析在加工稳定性的分析中,我们主要关注切削过程中的振动问题。
振动是加工过程中难以避免的现象,但是我们可以通过分析振动的原因来找到解决的办法。
常见的振动形式有切向振动和径向振动。
切向振动是指在切削过程中,刀具在切削方向上产生的振动;径向振动则是指在加工过程中,刀具在切削垂直方向上产生的振动。
1. 切向振动的分析切向振动是由刀具与工件之间的相互作用力引起的。
当刀具与工件之间的相互作用力超过一定阈值时,就会产生切向振动。
为了减小切向振动,我们可以从以下几个方面进行改进:(1)选择合适的切削参数:切削速度、进给速度和切削深度都会影响切向振动的产生。
我们可以通过试验和仿真分析,选取合适的切削参数,使得相互作用力保持在合理的范围内。
(2)提高刀具的刚性:刀具的刚性越高,切向振动的产生就越小。
因此,我们可以选择更加刚性的刀具,以减小切向振动。
2. 径向振动的分析径向振动是由机床的结构与性能引起的。
机床的刚性、工作台的稳定性以及主轴的旋转精度都会对径向振动产生影响。
为了减小径向振动,我们可以考虑以下几个方面的改进:(1)提高机床的刚性:机床的刚性是减小径向振动的关键。
通过改进机床结构、加强机床的刚性,可以有效地减小径向振动。
放电加工机床的作业精度与稳定性研究

放电加工机床的作业精度与稳定性研究随着制造业的发展,放电加工技术逐渐成为制造业中重要的加工方法之一。
放电加工机床作为放电加工的核心设备,在保证加工质量的同时,其作业精度与稳定性显得尤为重要。
本文将对放电加工机床作业精度与稳定性的研究进行探讨,并针对现有研究成果进行整理和总结。
作业精度是衡量机床加工能力的一个重要指标。
对于放电加工机床而言,其作业精度主要体现在以下几个方面:定位精度、重复定位精度、加工精度和表面质量。
首先,定位精度是指机床在进行加工时,其工件能够准确地定位到理论位置的能力。
定位精度受到机床系统结构、运动控制系统、传感器等多个因素的影响。
然后,重复定位精度是指机床在多次运行后,能够重复定位到相同的位置的能力。
这需要机床具备良好的机械稳定性和动态特性。
此外,加工精度和表面质量是衡量机床加工能力的重要指标,直接影响着工件的质量和加工效率。
提高加工精度和表面质量需要从机床的结构设计、加工参数的选择和控制策略的优化等多个方面着手。
为了提高放电加工机床的作业精度和稳定性,许多研究人员在不同方向上进行了深入研究。
首先,针对放电加工机床的结构设计进行了探索和改进。
通过改善机床的刚性和减小结构的变形,能够提高机床的定位精度和重复定位精度。
其次,针对放电加工过程中的难题,研究人员通过优化加工参数和改进电极设计,提升了加工精度和表面质量。
同时,控制策略也得到了改进,比如引入自适应控制方法和优化PID控制器来提高机床的稳定性和抗干扰能力。
此外,还有研究者通过使用先进的传感器技术和机器视觉系统,实现对机床状态和加工过程的实时监控与反馈,从而提高机床的控制精度和稳定性。
值得一提的是,虽然放电加工机床的作业精度和稳定性得到了许多研究的关注并取得了一定的突破,但仍存在一些挑战和问题需要解决。
首先,放电加工机床的高刚性要求使得其结构复杂,且制造成本较高。
因此,如何在保证刚性的同时降低成本是一个亟待解决的问题。
其次,放电加工机床的加工效率较低,这主要受到放电加工过程中的放电频率限制和电极材料的烧蚀影响。
- 1、下载文档前请自行甄别文档内容的完整性,平台不提供额外的编辑、内容补充、找答案等附加服务。
- 2、"仅部分预览"的文档,不可在线预览部分如存在完整性等问题,可反馈申请退款(可完整预览的文档不适用该条件!)。
- 3、如文档侵犯您的权益,请联系客服反馈,我们会尽快为您处理(人工客服工作时间:9:00-18:30)。
调整垫铁的安装密度将直接影响机床的刚性和机床精度的稳定性, 要求垫 铁 的密度不大于: 1 个/ 5 0 0 a r m, 同时. 在载荷密集区, 可相应增加垫铁, 以 提高
机 床 的刚性 , 保持 机 床的稳 定性 。
为了解决这些问题, 我国机床行业这些 年来经过技术改造, 设备更新, 机床
的。 煤 矿井 下生产过 程 中, 本 身就受 着水 、火 、 瓦斯、 煤尘 , 顶板 五大 自然 灾
害的制约, 在生产过程中, 采、掘、机、运、通等工序和环节配合不当就会造 成故障 和事故, 甚至可以酿成大涡, 严重危及职工的安全, 不论任何煤矿均存在
[ 摘 要】 保证机床精度稳定与保持性 , 在机床安装过程二次灌浆操作要领, 其中压浆法操作较为复杂 , 时间长, 成本较低, 而二次灌浆料法, 操作较为简单, 时 间短 , 成本较 高 。 【 关键词 ] 二 次 灌浆 精 度 稳定性 中图分类号 : T V4 2 +1 . 3 文 献标识 码 : A 文章 编号 : 1 0 0 9 — 9 1 4 X( 2 0 1 2 ) 1 3 — 0 0 3 4 —0 2
部 件的精 度 已经 达 到设计要 求 , 但在使用 过程 中还 出现 机床精度 不稳 定 的现 象 。为 了解 决这个 难题 , 我们进 行了系统 研究 。我 们在大 修改 造 国外 6 0 -7 0 年 代进 口滚齿机及 落地镗铣 床时 。 发现 他们机床 调整垫铁 与地基 及机床之 间的 接 触面积 达到 9 0 % 以上, 而我们在 这一方 面重视 不够 。为此 , 对使 用过程 中 出 现精度不稳定的机床, 公司派专门技术人员进行了解研究, 发现机床在二次灌 浆调整 时 , 由于机床制造 厂与安调人 员重视程度 不够 . 或操 作方法不 合理 , 导 致 调整 垫铁 与地基及 机床与地 基之 间接触 不正确 , 垫铁 歪斜等 现象, 造成接触 面 积小 , 而且 有 些呈现线 形接触 , 造成 机床 精度 不 能够具 有长期保 持性 。为 此我 们严格研究髓定了机床二次灌浆的操作规程, 机床精度不稳定的现象得到彻底
( c ) 将按 比例 混合好 的细砂 、 水泥 灌人二次 浇注坑上 部 预留8 O ~1 0 0 a r m高 度 4小 时。 ( d ) 安 装调整 垫铁 、压 浆
将调整垫铁上下面及床脚结合面清洁干净后 , 将其仔细的插入安装位置处 ( 图3 ) , 并反复 均 匀敲击 垫铁至 垫铁下 面与 水泥 接触 均匀无 间隙。同时 . 转动 调 整 垫铁 的方头 , 使 调 整垫铁上 面与机 床床脚 结合 面密贴 。接触 质量 用 0 . O 3塞 尺 检验 四周不 入 。 如 果达不 到要 求, 必 须清 除8 O ~l 0 0 mm高度 空 间 内水 泥 , 重 新 操 作。 压浆法 , 按着以上程序严格操作后, 养生6 -7 天. 便可进行机床二次精调
3 、需爆破的钻孔必须采取正向爆破 , 5 个孔为一组, 每打完一组钻孔后,
必 须 及时爆 破 。 4 、注 水前 , 封孔 器必须 与煤 壁紧压 , 以防止封 孔器 与煤 壁的摩擦 力 不足 , 将 封 L 器推 出 。 如 今, 这层 煤 已经顺 利的采完 , 自从采用 了此项技术 措施 以后, 采煤 面的冲 击情 况再没 有发生过 , 可 以说 冲击地压 在此 得到 了有效 控制 。 虽然 说冲击地 压 很危 险 , 也曾一 度危及 员工 的人身安 全和煤 矿 的安全 生产 , 但 只要 我们 有了 足 够 的 重视 , 采取 了积极有 效 的安全 技术措施 , 煤 矿 的安全生 产 是完全 能够实 现
值, 以减小 机 床二 次 调整 时产生 的内应 力 。 ( b ) 基础 二次灌 浆 。
基础二次灌浆分两次进行, 将按比例混合好的细砂、 水泥灌人二次浇注坑
内, 上 部预 留 8 O ~l O O mm 高度 空间( 图1 ) 。 控制H值, 按铁 铁的最 小商 度值加 I ~2 am( r 便 于 安装机 床本 身的调 整垫铁) , 并用小型 振动棒 夯实 , 固化 养生 3 ~
1概 述
不入 , 调整垫铁与垫板和机床床脚安装必须清洁、无毛刺,接触均匀无毛刺 ,
结合 面 0 . 0 3 塞 尺不 入 。
我国 近十多年来 。 机床行业 发展 非常 迅速 , 已经进入世 界机床大国 , 但在机 床精度 、性 能上 还 与世界先 进 国家有 一段距 离 。具 体表现 在有些 机床部 件精 度达不 到设 计要 求 , 安装 调整时 间长 , 机床精度 不 稳定现象 。 有些 机床需要 反 复调整 才能达到机 床精度要 求, 不仅浪 费人力 , 增加成本 , 而且严重 影响用户 使
3机床安装:次灌浆操作应按以下两种方式严格操作 ( 1 ) 压 浆、 法( 使用 非二次 灌浆料) ( a ) 预调 安装 水平 将机床 主 体件( 床身 、工作台 、立柱等 ) 床脚 固定好地 脚螺 栓后 , 吊放于大 地基的工艺调整垫铁上 , 预调安装水平。 要求精度调整值不低于机床安装精度
4天 。
解决, 不仅安装 调试时问 短, 而 且许多机床的 精度已达到国际先进水平 , 下面介
绍 如何保 证机床 二 次灌浆 . 。 0 2对调整蛰铁的要求 、 调整垫铁是连接机床与地基的关键部件, 其精度至关重要。 要求各重要结 合面必须进行精磨 调整垫铁的上下斜面必须清蓿无毛刺, 结合筒 O 0 3塞足
整 安 装水平 。 ( 2 ) 使用二 次 灌浆料法
随着水泥制品的多元化制造与使用, 机床二次灌浆料正在得到国内外机床 制 造厂商 的广 泛应 用 , 效 果优 良. 但操作 不当应起 不到应有的效 果 , 按 以下操作 方 法 操作 , 才能达 到最 佳效 果。 ( a ) 大地 浸湿 为 保证二 次 灌浆料 与 大地 基 的 良好 亲和性 , 以及二 次 灌浆料 水分 的保 持 性, 在机 束二 次灌浆 前 2 天, 须将 二次灌 浆坑进行 喷水浸 湿 , 要求 浸湿充 分 . 不 宜 有 过多的 水分 溢出 , 喷 水浸 湿可按 3 ~5 次逐渐 进行 , 如 有多 余溢 出的 水分 . 必 须 吸干 , 否则, 将 影响 二次灌 浆料 的收缩 效果。
( 图1 )
( 图 2 )
3 4 l 科 技 博 览
( 图3 )
( 图4 )
万方数据
工 业 技 术
C h i r l a s ci e n c e a n d T e c h n ol o g y K 0 v J e w
●-
薄煤层采煤 工作面卸压爆破 及高压注水技 术
工 业 技 术
| ■
C h i n a s c i e n c e a n d T e c h n o l o g y R e v i e w
关 于机 床 精度 稳 定 与保 持性 的 研究
吴 颖 曲生辉
( 齐 重数控 装备股份 有 限公司 黑龙 江 l 6 1 0 0 5 )
闫学 谦
( 黑龙江 省七 台河市龙 煤集 团七 台河分子 公司新 兴煤 矿 黑龙江 七台河 1 5 4 6 O 0 ) 技术管理 具有 超前 性 、规 划性 和指导 性 的特点 。 因此 , 技 术措施 是安 全生 产的 重要保 障 。 [ 摘 要] 加 强技 术管理 是实现 煤矿 安全生产 的 前提。 [ 关键 词] 打钻 卸压 钻 孔 卸 压爆 破 安 全生产 文章编 号 : 1 0 0 9 — 9 1 4 X( 2 0 1 2 ) 1 3 — 0 0 3 5 - 0 1 中图分 类号 : TV 5 4 2 文 献标识码 : A
随着 煤矿开采 深度的不 断增 加 , 地 质条件越来 越复 杂 , 地压 的明显增大 , 安 全生产 的形势也越 发的严 峻 , 要想实 现煤 矿安 全生产 , 必须依靠科 技技 术进 步 , 大力推 广新技术 . 新工 艺 , 新 设备 , 新 材料 , 提高广大 员工的综 合素质 , 努 力改善 井下的 工作环境 , 大家都 知道 , 煤 矿安全状 况不好 , 除受地质 和开采 的特 殊条件 制约外 。 很 大程度上 是 由于装 备和工 艺落后 , 安全 技术管理 人 员素质和 员工的 综 合素 质 不高而造 成的 。因此依靠 科技进 步来 加强技 术管理 是实现煤 矿安全 生产 的最 大动力 。 但推广 新技术 应 因地 制宜 , 做好 可行性 研 究和技 术论 证工 作, 不要盲 目行事, 另外还要有 足够的资 金投入来保 证 , 对 改善 安全条件 的新技 术和新 设 备应予 以充分重 视 , 这 个 问题 如 今显 现的 越来越 明显 , 我们煤 矿业必 须 面对 , 同时 也要尽快 解 决 , 否则安 全 生产将 十分 的被 动 。 2 0 1 1 年9 月份 , 新 兴煤 矿 六采 区回采三水 平右 一片6 0 层, 煤 层的可 采储量 为2 . 2 5 万吨 , 采 高为 0 . 5 -0 . 9 米, 平均 采高 0 . 8 米, 煤 层倾 角为 2 9 ~3 l 。, 平 均倾角 3 0 。。 煤种 为 1 / 3 焦煤, 煤层硬 度 f =1 . 3 , 层 理 不发育 , 工作 面 长度 1 5 5 米l 工作面 使 用s G B 8 O / l 2 O — T Bw型机 组 割煤 , S GB '6 3 0 / 1 1 O 溜子 运煤 , 工作 面 使用 DZ型单 体液压 支柱 支护 顶板 , 采用 “ 四 排五柱 的 布置 方 式 , 生产能 力为 1 . 0 万吨 /月 , 工 作面 配风量 为 4 0 0 m3 / mi n 。在工作 面初采期 间 , 煤壁 经 常发 出异常 的响声 , 煤 壁多处 片帮 , 割煤 时曾有煤 体瞬 间涌 出, 有冲 击的危 险 , 矿工生命安全受到了严重的威胁. 同时也制约了正常的生产组织。为此, 采煤 面停产 . 待注水卸压钻孔超前工作面6 O 米后, 方可进行生产作业。 故决定分别 组织两组专业的队伍。 分别对深孔注水和卸压爆破钻 L 进行施工, 在上巷下帮 沿煤层走向施工超前卸压钻孔, 每2米施工一个钻孔, 钻 L 深度 l 5米, 并对钻 孔采用注水预裂煤层, 使用MF 一 7 5 型橡胶封孔器进行封孔, 封孑 L 长度6 米。 注 水卸压钻 L 超前工作面不少于 6 0 米。上巷下帮及工作面施工爆破卸压钴 L , 上巷下帮每 2 米施工一个。 钻孔深度 2 米。 每个钻孔装药量为 0 . 6 k g, 爆破卸压 钻 L 超 前 工作面不 少于 6 0 米・ 工作 面煤层 松动 爆破 卸压钻 孑 L 间距 为 1 . 5 米一 个, 钻 L 深度同样为 2 . 0 米. 每孔装药量 0 . 6 k g . 每前进一刀, 都要进行一次卸 压爆破。上巷注水采用哇 ) 1 0高压管与上巷乳化液泵管相连接, 用( I ) 2 5 的高压 注水管与封孔器连接进行注水 , 在中l O 高压管处安装流量表, 以计算注水量。 煤层 注水 孔每孔 的注 水量为 2 m3 , 注水 时间为 1 小时 。所有施 工 完毕后 , 方 可进行采煤作业. 割煤时设专人跟机组进行观测。 同时每天设专人用KB D5 、 K BD 7 对 下帮及 采煤工作 面进 行扫描 , 每天对 其数 据进 行 分析 , 如有数 据异常 必须及 时 汇报。 经过 一段时间 的实验 , 效果很是 明显 , 冲击情 况得到 了明显的改善 . 煤壁片