脱硫系统中英文对照表
脱硫外文翻译(英文)
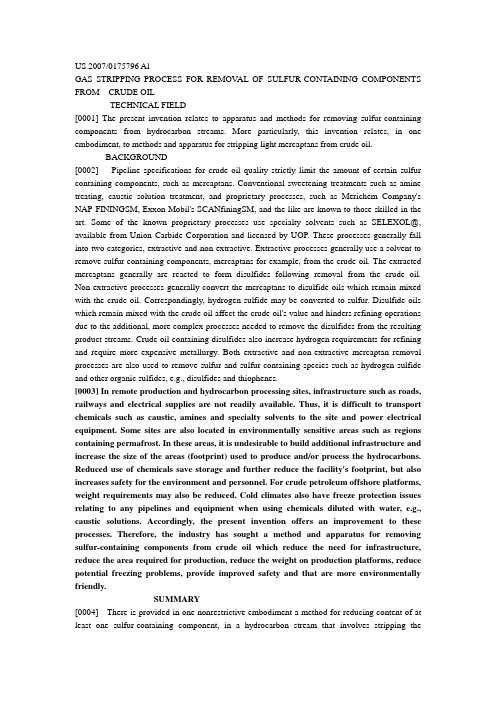
US 2007/0175796 AlGAS STRIPPING PROCESS FOR REMOV AL OF SULFUR-CONTAINING COMPONENTS FROM CRUDE OILTECHNICAL FIELD[0001] The present invention relates to apparatus and methods for removing sulfur-containing components from hydrocarbon streams. More particularly, this invention relates, in one embodiment, to methods and apparatus for stripping light mercaptans from crude oil.BACKGROUND[0002] Pipeline specifications for crude oil quality strictly limit the amount of certain sulfur containing components, such as mercaptans. Conventional sweetening treatments such as amine treating, caustic solution treatment, and proprietary processes, such as Merichem Company's NAP-FININGSM, Exxon Mobil's SCANfiningSM, and the like are known to those skilled in the art. Some of the known proprietary processes use specialty solvents such as SELEXOL@, available from Union Carbide Corporation and licensed by UOP. These processes generally fall into two categories, extractive and non-extractive. Extractive processes generally use a solvent to remove sulfur-containing components, mercaptans for example, from the crude oil. The extracted mercaptans generally are reacted to form disulfides following removal from the crude oil. Non-extractive processes generally convert the mercaptans to disulfide oils which remain mixed with the crude oil. Correspondingly, hydrogen sulfide may be converted to sulfur. Disulfide oils which remain mixed with the crude oil affect the crude oil's value and hinders refining operations due to the additional, more complex processes needed to remove the disulfides from the resulting product streams. Crude oil containing disulfides also increase hydrogen requirements for refining and require more expensive metallurgy. Both extractive and non-extractive mercaptan removal processes are also used to remove sulfur and sulfur-containing species such as hydrogen sulfide and other organic sulfides, e.g., disulfides and thiophenes.[0003] In remote production and hydrocarbon processing sites, infrastructure such as roads, railways and electrical supplies are not readily available. Thus, it is difficult to transport chemicals such as caustic, amines and specialty solvents to the site and power electrical equipment. Some sites are also located in environmentally sensitive areas such as regions containing permafrost. In these areas, it is undesirable to build additional infrastructure and increase the size of the areas (footprint) used to produce and/or process the hydrocarbons. Reduced use of chemicals save storage and further reduce the facility's footprint, but also increases safety for the environment and personnel. For crude petroleum offshore platforms, weight requirements may also be reduced. Cold climates also have freeze protection issues relating to any pipelines and equipment when using chemicals diluted with water, e.g., caustic solutions. Accordingly, the present invention offers an improvement to these processes. Therefore, the industry has sought a method and apparatus for removing sulfur-containing components from crude oil which reduce the need for infrastructure, reduce the area required for production, reduce the weight on production platforms, reduce potential freezing problems, provide improved safety and that are more environmentally friendly.SUMMARY[0004] There is provided in one nonrestrictive embodiment a method for reducing content of at least one sulfur-containing component, in a hydrocarbon stream that involves stripping thehydrocarbon stream including at least one sulfur-containing component with a gas stream having a relatively reduced level of the sulfur-containing component or no sulfur-containing component. This stripping produces a gas stream containing an increased level of sulfur-containing component(s) and a hydrocarbon stream containing a reduced level of sulfur containing component(s), i.e., S.C.C.[0005] In an alternative non-limiting embodiment there is provided a hydrocarbon processing system for processing crude oil that includes a unit for reducing content of at least one S.C.C. in a crude oil. The unit strips the crude oil including at least one S.C.C. with a gas stream having a relatively reduced level of the S.C.C. or no S.C.C. to give a gas stream containing an increased level of S.C.C. and a crude oil stream containing a reduced level of S.C.C.[0006] In still another non-limiting embodiment, there is provided a method for processing crude oil to selectively strip lighter mercaptans, e.g., methyl mercaptans and ethyl mercaptans.DETAILED DESCRIPTION[0010]It has been discovered that mercaptans, particularly light mercaptans, and other S.C.C. in general, may be removed from hydrocarbon streams, in one non-limiting embodiment crude oil, by stripping the hydrocarbon stream with a gas stream. In another non-restrictive embodiment,what is generally known in the industry as a sweet natural gas stream or a sweet gas stream comprising mostly methane or mixtures of methane, ethane, and small amounts of propanes, butanes and yet smaller amounts of heavier hydro-carbons, in various non-limiting mixtures, may be used for stripping. Generally, crude oil is used as the hydrocarbon stream to be sweetened or desulfurized in discussions herein, but it will be appreciated that the methods and apparatus herein may be usefully employed with other hydrocarbon streams. It will also be appreciated that the method will be considered successful even though all of the S.C.C. are not completely removed from the hydrocarbon stream, but the proportion of S.C.C. therein is reduced. Sweet stripping gas may be fed near the bottom of a tower at a point below the hydrocarbon feed and at a rate sufficient to provide a partial pressure of S.C.C., to extract sufficient amounts of the S.C.C., for example light mercaptans meet a specification based upon environmental specifications, downstream operations such as refining or other uses. The stripping gas may be fed at the bottom end of the tower or other location near the bottom end of the tower. The stripping gas bubbles up through the falling hydrocarbon liquid (e.g. liquid from the crude). While the gas moves up the tower it may become enriched with H2S, COS, mercaptans (particularly light mercaptans) other S.C.C. and hydrocarbons. It will be appreciated that in another non-limiting embodiment herein that the tower may be any vessel which facilitates the gas stripping, for example a spray tower, a distillation tower or a combination thereof.[0011] The crude oil may flow downward through the tower internals, for example, structured packing, random packing, sieve trays, valve trays, or disk and donut trays, or combinations thereof becoming leaner in S.C.C., e.g. mercaptan content. Meanwhile, the gas becomes richer inS.C.C. and carbon dioxide content as it bubbles up the tower and exits the tower. The gas rich in S.C.C. may be com-pressed, cooled and treated to remove S.C.C. and carbon dioxide by contacting with a physical solvent (e.g. SEL-EXOL~, available from Union Carbide Corporation or SULFINOL@, available from Shell lnternational Petroleum Co., Ltd. or LE-701 amine solvent available from Dow/Union Carbide, among others), a mercaptan-selective amine chemical solvent or a caustic solution in accordance with known techniques. The rich solvent solution may beflashed to lower pressure and regenerated using pressure difference, heat, or a combination of the two. Alternatively, the product acid gas stream may be incinerated; burned for fuel; injected into a reservoir as a gas or as a dissolved gas within a liquid; or processed to recover hydrocarbons that may have been stripped out of the crude oil along with the S.C.C. with known techniques. Acid gas handling may also be by compression for injection into underground reservoirs for enhanced oil recovery or disposal, or by dissolving the acid gas in waste oilfield brines (produced water) or fresh water prior to injection of the water for enhanced oil recovery or disposal.[0013] Processes such as liquid/liquid contacting or liquid/solid contacting to strip H2S from crude oil have been used at many locations in the oil industry. Solvent systems to remove H2S and COS, C02 and mercaptans are common in the upstream (production) and downstream (refining) sec-tors. A new aspect of the system and method(s) herein involves using a substantially large gas flow rate to remove or strip S.C.C. from liquid hydrocarbon streams, otherwise2 known as sweetening. In one non-limiting embodiment, the gas stripping process is combined with selection of a solvent for removal of the mercaptans and possibly other S.C.C. to obtain a low mercaptan and H2S (sweet) stripping gas. The term "sweet" herein when relating to crude oil or natural gasis defined as lacking appreciable amounts of sulfur or sulfur-containing components, in particular H2S and light mercaptans. In another non-limiting embodiment, "sweet" may mean containing no or less than 16 grains total sulfur per thousand standard cubic feet of gas (as H2S, COS and light mercaptans), alternatively less than 0.25 grains per thousand standard cubic feet of gas of H2S (4 ppmv). In crude oil "sweet" may mean less than 40 ppmw of light mercaptan or it may mean less than 0.5 percent total sulfur by weight. Light mercaptans are defined herein as methyl mercaptan (CH3SH) and ethyl mercaptan (C2H5SH) and the like.[0014] The hydrocarbon streams being stripped in accordance with the methods and systems described herein may be any stream containing hydrocarbons in significant amounts which also contain S.C.C., particularly light mercaptans. The hydrocarbon streams may be crude oils, synthetic crude oils; atmospheric gas oils; fuel oils; diesel oils and the like and combinations thereof in various non-limiting mixtures and embodiments. The hydrocarbon streams may contain other components including, but not necessarily limited to, water, C02, asphaltenes, acids, naphtha, paraffins, olefins, oxygenated hydrocarbons, oxygen, nitrogen, sulfur, sulfur derivatives, disulfides and aromatics, and the like and combinations thereof.[0015]Suitable gas streams to be used in stripping out light mercaptans from hydrocarbon streams include, but are not necessarily limited to, natural gas, methane, ethane, propane, butane, pentane and heavier hydrocarbons, nitro-gen, carbon dioxide, argon, helium, hydrogen, carbon monoxide and the like and combinations thereof. The stripping gas stream may be any gas stream that accomplishes the purposes and/or of the methods herein without containing components that do not appreciably interfere with those purposes and/or methods. It is expected that in some embodiments the stripping gas stream will be predominantly if not entirely in the gas phase. [0016]It will be appreciated that it is difficult if not impossible to specify in advance a particular gas stripping rate for a particular hydrocarbon stream without appreciable information and data. For instance, in one non-limiting embodiment, the gas stripping rate may depend on one or more of the following factors, many of which are interrelated, including, but not necessarily limited to, the composition of the hydrocarbon stream being treated-particularly the S.C.C., and more particularly light mercaptan content; the level of S.C.C. or mercaptan specified in the treatedproduct stream; the volume of the hydrocarbon stream; the relative volatility established for the S.C.C. or mercaptans with respect to the hydrocarbon stream components: the nature and composition of the gas stripping stream: the temperature and pressure of the stripping conditions; and the like. Nevertheless, in order to give some sense of the range of suitable stripping rates, in one non-limiting embodiment the lower and upper limits of the gas stripping rate may be about 0.1 and about l.0 MSCF per barrel of hydrocarbon, (about 18 and about 180 m3 gas/m3 hydrocarbon stream).Alternatively, the lower and upper limits of the gas stripping rate may be about 0.25 and about 0.5 MSCF per barrel of hydrocarbon (about 44 and about 89 m3/m3). In another non-restrictive version, the upper and lower limits of the gas stripping rate may be about 0.3 and about 0.4 MSCF per barrel of crude, (about 53 and about 71 m3/m3).[0017] Stripping tower conditions, the type of tower internals, the liquid and gas distribution within the tower, as well as those of the hydrocarbon feed stream and stripping gas stream are expected to be largely selected based upon mass transfer within the stripping tower; external transport concerns, such as pumping through a pipeline; and the crude composition. Keeping the viscosity of the hydrocarbon feed stream low is expected to be important to assure the stripper functions. In many situations, the crude may be transported by a long pipeline to the stripping tower and by a long pipeline to a loading terminal. Elevated temperature is important to keep the paraffin from dropping out of the pipelines and preventing gel formation in non-paraffin oils and creating problems. It should be understood that the tower operating conditions may be varied over relatively wide ranges. In addition, it should be further understood that the tower or column may be a reboiled column or a fully rectified column having a reboiler and partial condenser. Nevertheless, in order to give some sense of the operating conditions for the methods and systems discussed herein, the lower and upper temperature range limits for the hydrocarbon stream to the stripping tower may be about o and about 3500 F. (about-18 to about 1770 C.). In another non-limiting embodiment, the lower and upper temperature range limits for the hydrocarbon stream to the stripping tower may be about 70 and about 2000 F. (about 21 to about 93℃.). [0018] Similarly, the temperature of the stripping gas to the tower may be about o and about 3500 F. (about-18 to about 1770 C.). In another non-limiting embodiment, the lower and upper temperature range limits for the hydrocarbon stream to the stripping tower may be about 70 and about 2000 F. (about 21 to about 930 C.), respectively.[0019] Additionally, to give some sense of the pressure and temperature conditions for operating the tower, the lower and upper temperature ranges may be in one non-limiting embodiment about 0°F. and about 3500 F. (about-18 to about 1770 C.) respectively, and in another nonrestrictive version may be about 700 F. and about 2000 F.(about 21 to about 930 C.) respectively, and the lower and upper pressure ranges may be in one non-limiting embodiment about o psig and about 600 psig (about o to about 4.1MPa) respectively, and in another non-restrictive version may be about 15 psig and about 400 psig (about 0.1 to about2.8 MPa), respectively.[0020] The systems and methods herein will now be described in more detail with respect to FIG.1 in which overall gas stripping system 100 generally begins with hydrocarbon feed stream 12 pre-heated in feed heater 14 which is fed to stripper tower 18. Stripping tower 18 may optionally have a reboiler or be a fully rectified column with both a reboiler and partial condenser in order to control the crude oil vapor pressure and to provide energy for the separation of S.C.C. from preheated feed stream 16 0ralternatively from hydrocarbon feed stream 12, if not preheated. It must be understood that in addition to organic S.C.C., inorganic S.C.C. such as H2S in thehydrocarbon feed stream 12 may be removed by the method(s) and apparatus described. The preheated stream 16 is introduced at or near the top of stripping tower 18. Stripping gas, e.g. sweet natural gas, 20 is introduced at or near the bottom of tower 18. Stripping gas 20 is fed at a relatively high rate sufficient to provide a partial pressure of S.C.C. (e.g. methyland ethyl mercaptans) sufficiently low to produce a stripped hydrocarbon stream 22 having a reduced level of S.C.C.(e.g. methyl and ethyl mercaptans) removed at or near the bottom of tower 18, after flowing downward through the tower internals (not shown) to become leaner in S.C.C. (e.g. methyl and ethyl mercaptans). Although countercurrent con-tact is described in some embodiments herein, other modes of contact may be suitable including, but not necessarily limited to, cocurrent contact, cross-current contact and combinations of these. Stripped hydrocarbon stream 22 may be sweet crude oil in one particular, non-restrictive embodiment. The stripping gas 20 bubbles up through the liquid hydrocarbon in the tower, becoming enriched with S.C.C., and also C02 and hydrocarbons, exiting the top of the tower18 as rich gas stream 24 containing an increased level of[0021]Shown in FIG. 2 is another non-limiting embodi-ment of the invention, hydrocarbon processing system 10,where the same or similar or equivalent items as those inFIG. 1 are referred to with like reference numerals. Again,hydrocarbon feed stream 12 is pre-heated in feed heater 14 to provide the crude oil vapor pressure and to provide energy prior to the separation of S.C.C. the hydrocarbon feed stream12. The preheated stream 16 is introduced at or near the top of stripping tower 18, whereas stripping gas 20 is introduced at or near the bottom oftower 18. Stripping gas 20 is fed at a relatively high rate su街cient to provide a partial pressure of S.C.C. su伍ciently low in the depleted or stripped hydro-carbon stream 22 having a reduced level of S.C.C. removedat or near the bottom of tower 18, after flowing downwardthrough the tower to become leaner in S.C.C. The stripping gas 20 bubbles up through the liquid hydrocarbon in the tower, becoming enriched with S.C.C., and also C02 and hydrocarbons, exiting the top of the tower 18 as rich gas stream 24 containing an increased level of S.C.C.[0022] Optionally as shown in FIG. 2, rich gas stream 24may be compressed by compressor 26, producing com-pressed stream 25 which may be cooled via heat exchanger28 by cooling medium 30 in optional gas compression and cooling subsystem 32, resulting in a S.C.C. rich stream 27 which may be contain liquid, gas and mixtures thereof.Stream 27 may then be fed to S.C.C. and C02 removal subsystem 34. It will be appreciated througout the draw-ings that equipment and streams shown in dashed lines isconsidered optional, to be used in alternative non-limiting embodiments, for instance compressor 26 and heat exchanger 28.[0023] At hi~ pressure tower 36, condensed liquids may be separated from the gas phase and the resulting gas may be contacted with a lean solvent stream 48., The lean solvent stream 48 may be a mercaptan selective or other S.C.C.selective amine chemical solvent or a caustic solution, as previously mentioned, using other known technology. The rich solvent solution 38 may then be separated in low pressure tower 40 into a product acid gas 42 and a lean solvent stream 48. The product acid gas 42 may be fed to a hydrocarbon recovery unit 50 for recovery of valuable hydrocarbons. In an alternate embodiment, the acid gas 42may be injected in a reservoir for enhanced oil recovery as injection steam 43, incinerated or treated for elemental sulfur removal using known technologies (e.g., a Claus reactor) as treatment stream 47. In another non-limiting embodiment, sulfur removal subsystem 34 may be replaced with a solid bed treatment unit (not shown).[0024] Acid gas 42 may be refrigerated in the hydrocarbon recovery unit 50 to provide recovery of valuable liquid hydrocarbons 44, which may be combined with stripped hydrocarbon stream 22, that may have beeninitially stripped out in stripping tower 18 0r crude oil separation operations (not shown). In an alternate embodiment, hydrocarbon recovery unit 50 may comprise a cryogenic distillation train(not shown) which may be operated in various modes to produce a single valuable gas hydrocarbon stream 45. It will be appreciated that valuable gas hydrocarbon stream 45 may be split into multiple streams (not shown) known in the art as natural gas, ethane, propanes, LPG, butanes and pentanes plus heavier hydrocarbons and sent to storage, to a pipeline or to other uses. It is also known in the art that the recovery split(s) produced by hydrocarbon recovery unit 50 may represent various non-limiting embodiments which may be employed as driven by the economics and the design of the system. Hydrocarbon recovery unit 50 may also use distil-lation or other technologies (not shown), such as solid bed treating, to produce a second acid gas stream 46 by sepa-rating S.C.C. from the recoverable valuable liquid hydro-carbons 44, or in an alternative embodiment, the valuable gas hydrocarbons 45. The design ofthis unit, as well known in the art, will depend upon the particular S.C.C. removal process and the composition product acid gas 42 composi-tion. The second acid gas stream 46 may go to disposal, use in enhanced oil recovery or elemental sulfur recovery.[0025]In another non-limiting, optional embodiment, a second hydrocarbon recovery unit 51 may be used in addition to or alternatively to hydrocarbon unit 50 to recovervaluable liquid hydrocarbons and/or valuable gas hydrocarbons 54 from stripping gas 20. Hydrocarbon recovery unit 51 may be designed and operated like recovery unit 50, with the exception that hydrocarbon recovery unit 51 would not produce a third acid gas stream. As in the case of hydrocarbon recovery unit 50, part or all ofhydrocarbon stream 54 may be sent to storage or for other use or combined with depleted or stripped hydrocarbon stream 22, or split as stream 56 into single or multiple streams (not shown) known in the art as natural gas, ethane, propanes, LPG, butanes and pentanes plus heavier hydrocarbons. Alternatively, or in addition thereto, an optional recovered hydrocarbon stream may be used as a supplemental or make up stream 58 to stripping gas stream 20.[0026] FIG. 3 relates to an alternate embodiment of the system and method herein where equipment and streams that are the same or similar or equivalent to those in FIGS. 1 and2 are referred to with like reference numerals, where the overall hydrocarbon processing system is referred to as 60.The hydrocarbon feed stream 12 may be pre-heated in feed heater 14 to give preheated stream 16 0r introduced without being preheated at or near the top of stripping column 18, where stripping gas 20, e.g. sweet natural gas, is introduced at or near bottom of tower 18, augmented by make-up stripping gas stream 62. Stripped hydrocarbon stream 22,e.g. sweetened crude oil stream, goes to oil storage 644equipped with a vapor recovery unit (VRU)(not shown) from which is drawn stripped crude 011 66 directed to sales refining or other use.[0027] Rich gas stream 24 containing S.C.C. (and some non-sulfur containing hydrocarbons and carbon dioxide) is cooled by heat exchanger 68 transferring heat to stripping gas stream 20, before being combined with liquefied petro-leum gas (LPG) stream 72 from LPG stabilizer overhead compressor 74, water treating flash gas stream 76, 011 separation flash gas stream 78 and vapor stream 80 recovered from oil storage 64 compressed by compressor 82.Mixed gas stream 84 is compressed and cooled in gas compression and cooling subsystem 32 by first stage flashgas compressor 86, heat exchanger 88, second stage flash gas compressor 90, heat exchanger 92and may be combined with produced gas 96 from primary crude oil separation before going to gas injection section 98 as stream 100.[0028] Stream 100 is generally separated by unit 102 into injection gas stream 104 containing a relatively greater level of S.C.C. and gas stream 116 containing a relatively lower level of S.C.C. that is passed on to sulfur removal subsystem34. This separation may be conducted by any known technology. As discussed previously, injection gas stream 104may be compressed for injection into an underground reservoir, such as for enhanced oil recovery and/or disposal, or the stream 104 may be dissolved in produced water (typically waste oilfield brines) or even fresh water prior to injection of the water for enhanced oil recovery or the like.[0029] Additionally, there may be situations where it is desirable to have hydrocarbon recovery unit 51 in sequence before gas injection section 98. In the case where a solvent like propylene carbonate (e.g. Fluor Solvent) is employed,the solvent typically works best when refrigerated. In such a non-limiting embodiment, there may be benefit in including a hydrocarbon recovery unit 50, also in FIG. 2, as well.[0030] Stream 116 from gas injection section 98 goes to S.C.C. and C02 removal subsystem 34 at gas sweetening contactor 118 to condense acid gas 120 separated from the gas phase which may go on to be contacted with a physical solvent, a mercaptan selective or other S.C.C. selective amine chemical solvent or a caustic solution, as previously mentioned, using known technology or to other disposal.The rich solvent 122 is then introduced to gas dehydration contactor 124 where water 126 is removed and dehydrated gas stream 128 goes to hydrocarbon recovery unit 50 that splits out valuable hydrocarbon stream 44 (e.g. C4+, C5+ or some other valuable split), such as discussed above with respect to FIG. 3 and in another non-limiting embodiment,stream LPG 70. The gas remainder stream 130 is divided between stripping gas stream 20, fuel gas stream 134 and/or export gas stream 136.[0031] The methods and compositions herein will now be further illustrated with more specific Examples, but theseExamples are not intended to limit the methods and compositions herein in any respect, but are provided to further show and describe them. It will be appreciated that the Examples are the result of careful simulations, and that no pilot or full scale studies have yet been conducted.EXAMPLE 1[0032] With respect to gas stripping rates suitable for the methods and systems herein, a number of simulations were performed.[0033] For a crude oil stream of 150,000 BPD (24,000m3/day), one case simulated used 65 MMSCFD (l.8xl06m3/day) sweet natural gas to strip the light mercaptans t0 6 ppmw methyl mercaptan and 2 ppmw ethyl mercaptan. Feed concentrations were set at 111 ppmw methyl mercaptan and 237 ppmw ethyl mercaptan. The assumed crude oil feed temperature to the stripping tower was 2000 F. (930 C.), and the assumed stripping gas temperature was 1500 F. (660 C.).The simulation was completed at 50 psig (0.34 MPa) for the stripping tower.[0034] The temperature and pressure were set primarily by the crude oil vapor pressure that would be required for loading the oil on a tanker. It may be understood that temperature and pressure also plays a role in the simulation in establishing the mass transfer properties for the crude oil. The particular crude used in the simulation herein was very para街nic. Cloud point was around 900 F. (about 320 C.).[0035]The rates were estimated with user provided or adjusted Kij (relative volatility) data. TheHYSYS~ process modeling tool software (Aspen Technology, Inc.) denotes these terms as interaction parameters. Using the same gas rate with the original HYSYS~ provided or default Kij values resulted in 6 ppmw methyl mercaptan and 35 ppmw ethyl mercaptan; results that were not as promising. In one non-limiting model, stripping gas rates for the H2S stripping system originally proposed were 65 MMSCFD rl.8xl06 m3/day). To achieve the 6 and 35 mercaptan ppmw concen- trations, respectively, with the revised Kij data, it was possible to lower the stripping gas rate t0 43 MMSCFD ;1.2x106 m3/day). Please see the data summarized in Table I. Thus, one gas stripping range for this particular product specification may be from about 0.25 to about 0.5 MSCF per barrel of crude (about 44.5 to about 89.0 m3/m3)[0036] Using the parameters of Example l, the inlet concentration of methyl mercaptan was varied up t0 252 ppmw and ethyl mercaptan up t0 326 ppmw to evaluate the impact of the simulation method used to estimate the mercaptan content of the hydrocarbon (crude) feed stream. For the same stripping gas rate, the stripped hydrocarbon stream(product) concentrations were virtually unchanged (methyl mercaptan concentration rose by 2 ppmw; ethyl mercaptan concentration was unchanged). Although not simulated, it is expected that there is a point where the hi~er inlet concentrations would become a significant factor such that increased stripping gas rates would be needed and poten tially at some yet higher inlet concentration that the necessary increase in the stripping gas rate could result in lost column or tower e街ciency.ADDITIONAL EXAMPLES[0037]The sensitivity of the stripping gas rate in the modeling simulation was measured to various assumptions.The results are given in Table II using the adjusted Kij values.[0038] As noted, the methods and system herein for removing S.C.C. from hydrocarbon streams have an absence of caustic alkali/compounds (e.g. alkali metal hydroxides such as NaOH). There is also an absence of amine compounds and an absence of catalysts in the initial gas strippingof the hydrocarbon stream.[0039] Further, it will be appreciated that in another nonlimiting embodiment, the stripping gas stream may contain hydrogen. It will be appreciated that the method herein for stripping S.C.C. from hydrocarbon streams is a non-reacting system, that is, does not involve chemical reaction. Thus, a gas stream that contains hydrogen as a minor component, or even as a major component (greater than 50 volume %)could be employed in the method herein. In one non-limiting embodiment of the invention, the stripping method herein involves an absence of hydrogenation as a means ofremoving the S.C.C. However, as described caustic or alkali compounds, amine compounds and associated catalysts may optionally be used to remove the S.C.C. from the stripping gas stream subsequently to help in regenerating that stream,i.e. to sweeten it. EXAMPLE 2[0040] The processes and apparatus herein may be applied to hydrocarbon streams and particularly crude oils in many parts of the world. Economic comparison of the additionalpower required for compression, fuel use and solvent losses may be made against the capital and operating expenses of the other available processes for removing mercaptans from crude oil. Given the high rate of circulation of the stripping gas, the need for substantial gas compression。
化工操作及工厂装置名称英汉对照
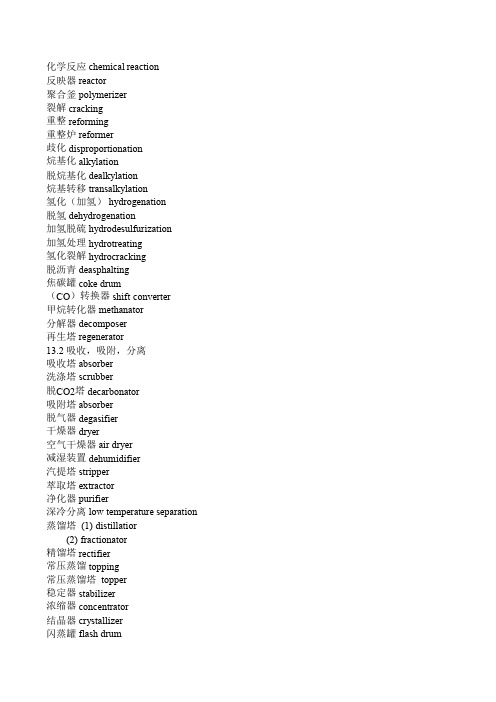
化学反应 chemical reaction反映器 reactor聚合釜 polymerizer裂解 cracking重整 reforming重整炉 reformer歧化 disproportionation烷基化 alkylation脱烷基化 dealkylation烷基转移 transalkylation氢化(加氢) hydrogenation脱氢 dehydrogenation加氢脱硫 hydrodesulfurization加氢处理 hydrotreating氢化裂解 hydrocracking脱沥青 deasphalting焦碳罐 coke drum(CO)转换器 shift converter甲烷转化器 methanator分解器 decomposer再生塔 regenerator13.2 吸收,吸附,分离吸收塔 absorber洗涤塔 scrubber脱CO2塔 decarbonator吸附塔 absorber脱气器 degasifier干燥器 dryer空气干燥器 air dryer减湿装置 dehumidifier汽提塔 stripper萃取塔 extractor净化器 purifier深冷分离 low temperature separation 蒸馏塔 (1) distillatior(2) fractionator精馏塔 rectifier常压蒸馏 topping常压蒸馏塔 topper稳定器 stabilizer浓缩器 concentrator结晶器 crystallizer闪蒸罐 flash drum分离器 separator湿气分离器 mist separator缓冲罐 knock-out drumAPI分离器 API separator油分离器 oil separator油水分离器 decanter沉淀器 settler13.3 热交换换热器 heat exchanger在线换热器 transfer heat exchanger 加热炉 furnace预热器 preheater再热器 reheater冷却塔 cooler深冷器 chiller再沸器 reboiler热缸吸再沸器 thermosiphon reboiler 蒸发器 evaporator汽化器 vaporizer冷凝器 condenser尾气冷凝器 vent condenser省煤器 economizer融解槽 melter浸没燃烧 submerged combustion废热锅炉 waste heat boiler辅助锅炉 auxiliary boiler13.4 其它接受器 receiver贮槽 (1) reservior(2) holder集气罐 accumulator缓冲器 buffer脉冲衰减装置 pulsation damper计量罐 (1) measuring tank(2) metering tank急冷塔 quencher喷射器 ejector升压器 booster循环器 recirculator加料器 feeder焚化炉 incinerator火炬(烟囱) flare stack惰性气体发生器 inert gas generator空分装置 air separation appratus 流体床操作 fluid-bed operation 造粒塔 prilling tower海水淡化装置 desalination plant。
脱硫英汉翻译
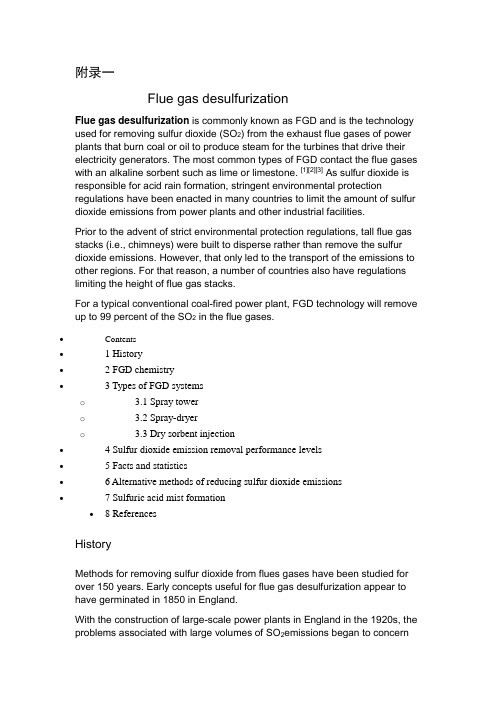
附录一Flue gas desulfurizationFlue gas desulfurization is commonly known as FGD and is the technology used for removing sulfur dioxide (SO2) from the exhaust flue gases of power plants that burn coal or oil to produce steam for the turbines that drive their electricity generators. The most common types of FGD contact the flue gases with an alkaline sorbent such as lime or limestone. [1][2][3] As sulfur dioxide is responsible for acid rain formation, stringent environmental protectionregulations have been enacted in many countries to limit the amount of sulfur dioxide emissions from power plants and other industrial facilities.Prior to the advent of strict environmental protection regulations, tall flue gas stacks (i.e., chimneys) were built to disperse rather than remove the sulfur dioxide emissions. However, that only led to the transport of the emissions to other regions. For that reason, a number of countries also have regulations limiting the height of flue gas stacks.For a typical conventional coal-fired power plant, FGD technology will remove up to 99 percent of the SO2 in the flue gases.∙Contents∙ 1 History∙ 2 FGD chemistry∙ 3 Types of FGD systemso 3.1 Spray towero 3.2 Spray-dryero 3.3 Dry sorbent injection∙ 4 Sulfur dioxide emission removal performance levels∙ 5 Facts and statistics∙ 6 Alternative methods of reducing sulfur dioxide emissions∙7 Sulfuric acid mist formation∙8 ReferencesHistoryMethods for removing sulfur dioxide from flues gases have been studied for over 150 years. Early concepts useful for flue gas desulfurization appear to have germinated in 1850 in England.With the construction of large-scale power plants in England in the 1920s, the problems associated with large volumes of SO2emissions began to concernthe public. The problem did not receive much attention until 1929, when the British government upheld the claim of a landowner against the Barton Electricity Works for damages to his land resulting from SO2 emissions. Shortly thereafter a press campaign was launched against the erection of power plants within the confines of London. This led to the imposition of SO2 controls on all such power plants.[4]During this period, major FGD installations went into operation in England at three power plants. The first one began operation at the Battersea Station in London in 1931. In 1935, the second one went into service at the Swansea Power Station. The third one was installed in 1938 at the Fulham Power Station. All three installations were abandoned duringWorld War II.Large-scale FGD units did not reappear in commercial operation until the 1970s, and most of the activity occurred in the United States and Japan.[4] As of June 1973, there were 42 FGD units, ranging in size from 5 to250 megawatts, in operation: 36 in Japan and 6 in the United States.[5]As of about 1999-2000, there were 678 FGD units operating worldwide (in 27 countries) producing a total of about 229 gigawatts. About 45% of that FGD capacity was in the United States, 24% in Germany, 11% in Japan and 20% in various other countries. Approximately 79% of the units, representing about 199 gigawatts of capacity, were using lime or limestone wet scrubbing. About 18% (or 25 gigawatts) utilized spray-dry scrubbers or dry sorbent injection systems.[6][7][8]FGD chemistrySO2 is an acid gas. Therefore, the most common large-scale FGD systems use an alkaline sorbent such as lime or limestone to neutralize and remove the SO2 from the flue gas. Since lime and limestone are not soluble in water, they are used either in the form of an aqueous slurry or in a dry, powdered form. When using an aqueous slurry of sorbent, the FGD system is referred to asa wet scrubber. When using a dry, powdered sorbent, the system is referred to as a dry system. An intermediate or semi-dry system is referred to asa spray-dry system.The reaction taking place in wet scrubbing using a CaCO3 (limestone) slurry produces CaSO3 (calcium sulfite) and can be expressed as:CaCO3 (solid) + SO2(gas) → CaSO3 (solid) + CO2 (gas)When wet scrubbing with a Ca(OH)2 (lime) slurry, the reaction alsoproduces CaSO3 (calcium sulfite) and can be expressed as:Ca(OH)2 (solid) + SO2(gas) → CaSO3 (solid) + H2O (liquid)When wet scrubbing with a Mg(OH)2 (magnesium hydroxide) slurry,the reaction produces MgSO3 (magnesium sulfite) and can beexpressed as:Mg(OH)2 (solid) + SO2(gas) → MgSO3 (solid) + H2O (liquid)Some FGD systems go a step further and oxidize theCaSO3 (calcium sulfite) to produce marketable CaSO4 · 2H2O(gypsum):CaSO3 (solid) + ½O2 (gas) + 2H2O (liquid) → CaSO4 · 2H2O (solid)Aqueous solutions of sodium hydroxide (known as causticsoda or simply caustic) may also be used to neutralize andremove SO2 from flue gases. However, caustic soda islimited to small-scale FGD systems, mostly in industrialfacilities other than power plants because it is moreexpensive than lime. It has the advantage that it forms asolution rather than a slurry and that makes it easier tooperate. It produces a solution of sodium sulfite or sodiumbisulfite (depending on the pH), or sodium sulfate that mustbe disposed of. This is not a problem in a paper mill forexample, where the solution can be recycled and reusedwithin the paper mill.Types of FGD systemsThe major types of large-scale, power plant FGD systemsinclude spray towers, spray dryers and dry sorbent injectionsystems.Spray towerThere are various types of wet scrubbers. For example, spraytowers, venturi scrubbers, packed towers and trayed towers. Slurries would cause serious erosion problems in a venturi scrubber because of the high speeds at the throat of the venturi section. Packed towers or trayed towers would plug up if handling slurries. For handling slurries, the spray tower is a good choice and it is in fact a commonly used choice in large-scale FGD systems.[3][9][10]Spray towers are used downstream of the particulate equipment (electrostatic precipitator or baghouse) where the flue gas contains very little, ifany, combustion fly ash. In a spray tower system, the sorbent slurry is simply injected via spray nozzles into a vertical tower where the slurry droplets are contacted with the upflowing flue gas.Part of the water in the slurry is evaporated by the hot flue gas and the flue gas becomes saturated with water vapor.The SO2 dissolves into the slurry droplets and reacts with the alkaline sorbent particles. The slurry falls to the bottom of the spray tower and is sent to a reaction tank where the reaction is completed and a neutral salt is formed. In a regenerable system, the residual slurry is recycled back for reuse in the spray tower. In a once-through system, the residual slurry is dewatered and either disposed of or oxidized to CaSO4 · 2H2O and sold as a by-product gypsum. Spray-dryerSpray-dryers are used upstream of the particulate removal equipment (electrical precipitator or baghouse) where the flue gas contains the combustion fly ash. In a spray-dryer system, the alkaline sorbent is usually lime slurry. The slurry is atomized and sprayed into a vessel as a cloud of fine bubbles where it contacts the hot flue gas. The water is completely evaporated by the hot gas and the residence time in the vessel (about 10 seconds) allows the SO2 and any other acid gases, such as SO3 and HCl, to react with the lime to form a dry powder of calcium sulfite, calcium sulfate and unreactedlime.[3][11][12]The dry powder is removed from the flue gas along with the combustion fly ash in the particulate removal equipment. Some of the solids from the particulate removal equipment (i.e., fly ash, calcium sulfite, calcium sulfate and unreacted lime) may be recycled and reused as part of the sorbent slurry.[12]Dry sorbent injectionThe dry FGD system simply injects powdered lime or limestone sorbent directly into the flue gas. As shown in the adjacent location diagram, the dry sorbent may be injected into any one of three locations: (1) the upper section of the steam generator, (2) the economizer section of the steam generator orthe ducting between the air preheater and the electrostaticprecipitator.[2][3][11][13]The powdered sorbent is pneumatically injected through lances designed to distribute the sorbent evenly across the flow path of the flue gas.When injected into the upper section of the steam generator, it should enter at a point where the temperature range is about 900 to 1200 °C. Injection into the economizer should be at a point where the temperature range is about 400 to 600 °C. Injection into the ducting between the preheater and the precipitator should be at point where the flue gas temperature is about 150 to 180 °C.[3][11] The SO2 reacts directly with the powdered sorbent and the spent sorbent is removed from the flue gas along with the combustion fly ash inthe particulate removal equipmentSulfur dioxide emission removal performance levelsPartial flue gas desulfurization (FGD) can achieve about 50-70 % removal of sulfur dioxide by the injection of dry limestone just downstream of the air preheater. The resultant solids are recovered in the electrostatic precipitators along with the fly ash.In power plants burning pulverized coal, wet flue gas desulfurization (FGD) that contacts the flue gases with lime slurries (in what are called wet lime scrubbers) can achieve 95% sulfur dioxide removal without additives and99+% removal with additives. Wet FGD has the greatest share of the FGD usage in the United States and it is commercially proven, well established technology.[14]The typical older FGD units in power plants burning pulverized coal within the United States achieve average sulfur dioxide emission levels of about 0.340 kg/MWh (0.22 lb SO2 /106Btu), which meets the level to which those units were permitted.The lowest demonstrated sulfur dioxide emission level (in 2005) for power plants burning pulverized high-sulfur coal within the United States was 1.08 kg/MWh (0.07 lb SO2 /106 Btu) and 0.046 kg/MWh (0.03 lb SO2 /106 Btu) for plants burning low-sulfur pulverized coal.[14]Facts and statisticsFlue gas desulfurization scrubbers have been applied to combustion units firing coal and oil that range in size from 5 MW to 1500 MW. ScottishPower are spending £400 million installing FGD at Longannet powerstation which has a capacity of over 2 GW. Dry scrubbers and sprayscrubbers have generally been applied to units smaller than 300 MW.Approximately 85% of the flue gas desulfurization units installed in the US are wet scrubbers, 12% are spray dry systems and 3% are dry injection systems.The highest SO2 removal efficiencies (greater than 95%) are achieved by wet scrubbers and the lowest (less than 80%) by dry scrubbers. However, the newer designs for dry scrubbers are capable of achieving efficiencies in the order of 90%.The capital, operating and maintenance costs per short ton ofSO2 removed (in 2001 US dollars) are:∙For wet scrubbers larger than 400 MW, the cost is $200 to $500 per ton∙For wet scrubbers smaller than 400 MW, the cost is $500 to $5,000 per ton∙For spray dry scrubbers larger than 200 MW, the cost is $150 to $300 per ton∙For spray dry scrubbers smaller than 200 MW, the cost is $500 to $4,000 per tonAlternative methods of reducing sulfur dioxide emissions An alternative to removing sulfur from the flue gases after burning is to remove the sulfur from the fuel before or duringcombustion. Hydrodesulfurization of fuel has been used for treating fuel oils.Fluidized bed combustion adds lime to the fuel during combustion. The lime reacts with the SO2 to form sulfates which become part of thecombustion ash.Sulfuric acid mist formationFossil fuels such as coal and oil contain significant amounts of sulfur.When burned, about 95 percent or more of the sulfur is generallyconverted to sulfur dioxide (SO2). This happens under normal conditions of temperature and of oxygen present in the flue gas. However, there are circumstances under which this may not be the case.For example, when the flue gas has too much oxygen and the SO2 isfurther oxidized to sulfur trioxide (SO3). Actually, too much oxygen is only one of the ways that SO3 is formed. Gas temperature is also an important factor. At about 800 °C, formation of SO3 is favored. Another way thatSO3 can be formed is through catalysis by trace metals in the fuel. This is particularly true for heavy fuel oil, where small amounts of vanadium are present. In whatever way that SO3 is formed, it does not behave likeSO2 in that it forms a liquid aerosolknown as sulfuric acid (H2SO4) mist that is very difficult to remove. Generally, about 1% of the sulfur dioxide will be converted to SO3. Since SO3 an acid gas, just as is SO2, it is also removed by the alkaline sorbents used in FGD systems.References1. ↑ Karl B. Schnelle and Charles A. Brown (2001). Air PollutionControl Technology>. CRC Press. ISBN 0-8493-9599-7.2. ↑2.02.1 SO2 Control Technologies (from website of the Institute ofClean Air Companies)3. ↑3.03.13.23.33.43.5 Air Pollution Control Technology Fact Sheet U.S.EPA publications EPA-452/F-03-0344. ↑4.04.1 Biondo, S.J. and Marten,J.C., A History of Flue GasDesulfurization Systems Since 1850, Journal of the Air PollutionControl Association, Vol. 27, No. 10, pp 948-961, October 1977.5. ↑ Beychok, Milton R., Coping With SO2, ChemicalEngineering/Deskbook Issue, October 21, 19746. ↑ Nolan, Paul S., Flue Gas Desulfurization Technologies forCoal-Fired Power Plants, The Babcock & Wilcox Company, U.S.,presented by Michael X. Jiang at the Coal-Tech 2000 InternationalConference, November, 2000, Jakarta, Indonesia7. ↑ Rubin, E.S., Yeh, S., Hounsell, D.A., and Taylor,M.R., Experience curves for power plant emission controltechnologies, Int. J. Energy Technology and Policy, Vol. 2, Nos. 1/2,20048. ↑ Beychok, Milton R., Comparative economics of advancedregenerable flue gas desulfurization processes, EPRI CS-1381,Electric Power Research Institute, March 19809. ↑ Wet FGD System Materials Cost Update, by M.G. Milobowski,Babcock & Wilcox (Presented at EPRI-DOE-EPA Combined UtilityAir Pollutant Control Symposium, August 1997)10. ↑ Air Pollution Control Technology Fact Sheet U.S.EPA publications EPA-452/F-03-01611. ↑11.011.111.2 IEA Clean Coal Center: Spray dry scrubbers forSO2 removal12. ↑12.012.1 Dry Flue Gas Desulfurization (FGD)Systems (FromBabcock and Wilcox website)13. ↑ Barbara Toole-O'Neil and Ohio Coal Development Office (Editors)(1998). Dry Scrubbing Technologies for Flue Gas Desulfurization.Springer. ISBN 0-7923-8346-X.14. ↑14.014.1 Dr. James Katzer et al and MIT Coal Energy StudyAdvisory Committee (2007).汉语翻译烟气脱硫烟气脱硫,就是泛指用烟气脱硫技术电厂燃烧煤、石油化工或其他工业废气中除去硫氧化物的技术。
电厂中英文对照
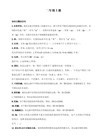
4FROM DEA 来自除氧器 FROM DEAERATOR
5TO WATER POOL 到水池
7 SH STEAM SYSTEM 过热蒸汽系统
1DRN TO BLDWN 疏水
LC SYSTEM C磨煤机系统
L D SYSTEM D磨煤机系统
L E SYSTEM E磨煤机系统
L F SYSTEM F磨煤机系统
24.MFT 主燃料跳闸 MAIN FUEL TRIP
5 FEED WATER SYSTEM 给水系统
1FLM COR 折焰角 FLAME CORE
2SPW MID HDR 水冷壁中间联箱 SPIRAL WALL MIDDLE HEADER
3ECO 省煤器 ECONOMISER
4SEP A A汽水分离器 SEPARATOR A
5TO SH ATT 到过热减温器 TO SUPERHEATER ATTEMPERATOR
7IDF A STALL A引风机喘振 INDUCED AIR FAN ASTALL
8IDF ABRG VIB HH1 A引风机轴承振动高高1 INDUCED AIR FAN A BEARING VIBRATION HIGH HIGH
9IDF A OIL STN SUPLY OIL TEMP H A引风机油站供油温度高 INDUCED AIR FAN A OIL STATION SUPPLY OIL TEMERATURE HIGH
14.OIL AB SYSTEM AB层油系统
15.OIL EC SYSTEM EC层油系统
16.OIL FD SYSTEM FD层油系统
要上传产品名称中英文对照1
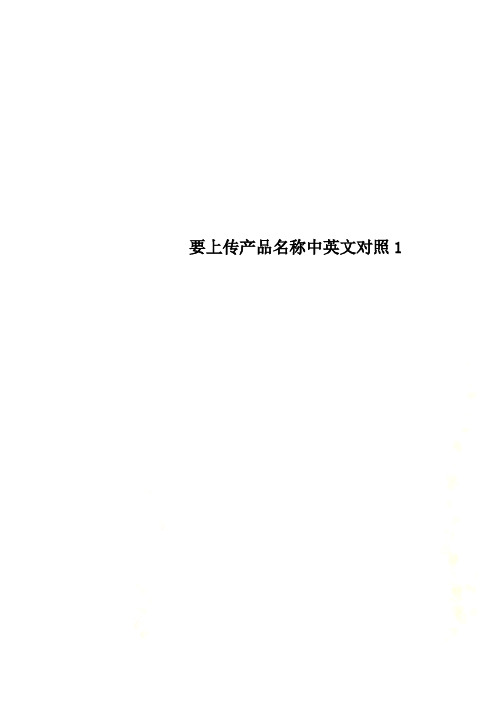
要上传产品名称中英文对照11)烘干机设备系列:Dryer Equipment Series 转筒烘干机Rotary dryer 煤泥烘干机Coal Slime Rotary Dryer 沙子烘干机Sand Rotary Dryer 生物肥烘干机Bio-Fertilizer Dryer 高湿物料烘干机High Humidity Material Dryer2)回转窑系列:Rotary Kiln Series回转窑Rotary Kiln 冶金回转窑Metallurgy Rotary Kiln 石灰回转窑Lime Rotary Kiln 水泥回转窑Cement Rotary Kiln 活性石灰生产线Active Lime Production Line输送设备系列Conveyor Series输送机系列Conveyor皮带输送机Belt Conveyor斗式提升机 Bucket Elevator振动给料机Vibrating Feeder螺旋输送机Screw Conveyor链式输送机Chain Conveyor卧式给料机Horizontal Feeder3)除尘设备系列:Dust Catcher Equipment脱硫除尘器Desulfurization Dust Catcher 袋式脉冲除尘器Beg Pulse Dust Catcher 单筒旋风除尘器Monocular Cyclone Dust Catcher 静电除尘器Static Electricity Dust Catcher湿式除尘器wet-type dust catcher 双筒旋风除尘器Binocular,Cyclone Dust Catcher4)煤气发生炉系列:Coal Gasifier Series两段式煤气发生炉Double-Stage Coal GasifierQM-1型煤气发生炉QM-1 Coal GasifierQM-2型煤气发生炉QM-2 Coal Gasifier喷煤机Coal Spraying Machine单段煤气发生炉 Single-Stage Coal Gasifier5)冷却机设备系列Cooling Machine Series冷却机Cooling Machine6)破碎设备系列Crushing Equipment Series对辊破碎机2-Roller Crusher 颚式破碎机Jaw crusher 锤式破碎机Hammer crusher 立式复合破碎机Vertical Combination Crusher 齿辊破碎机Gear-Roller Crusher 反击破碎机Impact crusher7)选矿设备系列Ore Dressing Equipment Series球磨机Energy Saving Ball Mill 浮选机Floatation separator洗砂机Sand WashingMachine 圆盘造粒机Disk Grain Making Machine 对辊造粒机2-roller Grain Making Machine振动筛Vibrating Screen。
电厂常用术语中英文对照
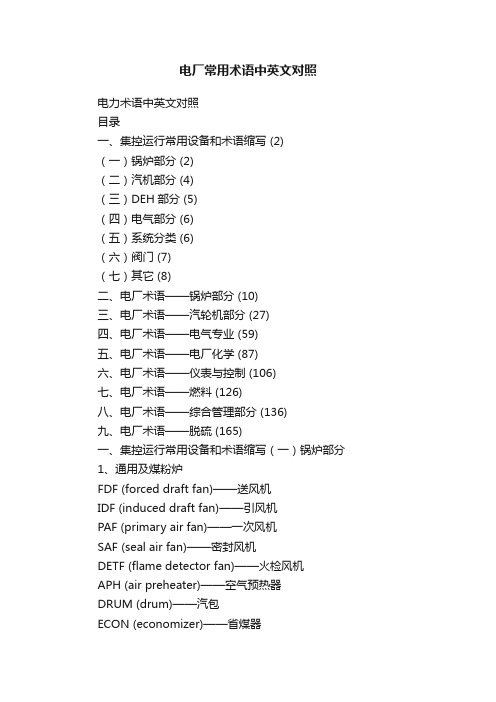
电厂常用术语中英文对照电力术语中英文对照目录一、集控运行常用设备和术语缩写 (2)(一)锅炉部分 (2)(二)汽机部分 (4)(三)DEH部分 (5)(四)电气部分 (6)(五)系统分类 (6)(六)阀门 (7)(七)其它 (8)二、电厂术语——锅炉部分 (10)三、电厂术语——汽轮机部分 (27)四、电厂术语——电气专业 (59)五、电厂术语——电厂化学 (87)六、电厂术语——仪表与控制 (106)七、电厂术语——燃料 (126)八、电厂术语——综合管理部分 (136)九、电厂术语——脱硫 (165)一、集控运行常用设备和术语缩写(一)锅炉部分1、通用及煤粉炉FDF (forced draft fan)——送风机IDF (induced draft fan)——引风机PAF (primary air fan)——一次风机SAF (seal air fan)——密封风机DETF (flame detector fan)——火检风机APH (air preheater)——空气预热器DRUM (drum)——汽包ECON (economizer)——省煤器SH (superheater)——过热器CSH (ceiling superheater)——顶棚过热器PSH (platen superheater)——屏式过热器RSH (radiation superheater)——辐射过热器LSH (low temperature superheater)——低温过热器HSH (high temperature superheater)——高温过热器RH (reheater) ——再热器LRH (low temperature reheater)——低温再热器HRH (high temperature reheater)——高温再热器PRH (platen temperature reheater)——屏式再热器CB (coal bin)——煤仓SCB(side coal bin)——侧煤仓MILL (mill)——磨煤机FEED (coal feeder)——给煤机PCC (pulverized-coal collector)——细粉分离器MILLS (mill separator)——粗粉分离器PEF (powder exhaust fan)——排粉风机PCF(pulverized coal feeder)——给粉机HPA (heat primary air )——热一次风CPA (cold primary air )——冷一次风SECA (secondary air)——二次风TA (tertiary air)——三次风SA (seal air)——密封风AR (air register)——风门OILP (oil pistol)——油枪IGNT (ignition) ——点火枪FULP (fuel pump)——燃油泵FLTK (flash tank)——扩容器FURN(furnace) ——煤粉炉炉膛2、流化床锅炉HPCB(high-pressure centrifugal blower)——高压流化风机CFBB(Circulating Fluidized-bed Boiler)——循环流化床炉膛CYCS(cyclone separator)——旋风分离器UBF(U-type back-feeder) ——U形返料器ASHC(ash cooler) ——冷渣器3、余热锅炉CVB(convection bank) ——对流管束SWS(steam/water separator) ——汽水分离器WJP(Water jet pump)——射水泵WH(water heater) ——热水器EVP(evaporator) ——蒸发器OEJ(oil ejector)——注油器OFT(oil filter)——滤油器OCL(oil cooler)——冷油器窑头余热锅炉AQCB(此处AQC指air quenching cooler,为篦冷机,不是窑头的意思,但行业习惯称窑头余热炉为AQC炉) 窑尾余热锅炉SPB(此处SP指suspension preheater,为悬浮预热器,不是窑尾的意思,但行业习惯称窑尾余热炉为SP炉) (二)汽机部分HP (high pressure cylinder) ——高压缸IP (intermediate pressure cylinder) ——中压缸LP (low pressure cylinder) ——低压缸DEA (deaerator) ——除氧器COND (condenser) ——凝汽器HPH (high pressure heater) ——高压加热器LPH (low pressure heater) ——低压加热器SSH (shaft seal heater) ——轴封加热器MFP (motor-driven feed pump) ——电动给水泵SFP (steam feed pump) ——汽动给水泵V ACP (vacuum pump) ——真空泵CEP (Condensate extraction pump) ——凝结水泵DRNP (drain pump) ——疏水泵CIRP (circulating pump) ——循环泵LIFTP (lift pump) ——顶轴油泵LUBOP (lubricating oil pump) ——润滑油泵DCOP——直流润滑油泵ACOP——交流润滑油泵HPOP——高压启动油泵MAINOP——主油泵EHP——EH油泵OTANK (oil tank) ——油箱WTANK (water tank) ——水箱HEADER——联箱SSF (shaft seal fan) ——轴封风机IFF (induced-fume fan) ——排烟风机AIRCMP(air compressing engine) ——空气压缩机(三)DEH 部分TV——高压缸主汽门GV——高压缸调节门RV——中压缸主汽门IV——中压缸调节门LV——低压缸调节门(四)电气部分GEN (generator) ——发电机XFORM (transformer) ——变压器BUS (bus bar) ——母线BRK (circuit breaker) ——断路器SWITCH (isolating switch) ——隔离开关EXCT (exciter) ——励磁机PEXCT (pilot exciter) ——副励磁机(五)系统分类feed water system ——给水系统water-steam system ——汽水系统desuperheater system ——减温水系统combustion system ——燃烧系统extraction steam system ——抽汽系统heat supply system ——热网系统lubricating oil system——润滑油系统fuel oil system——燃油系统soot blower system——吹灰系统ignition system——点火系统powder manufacturing system——制粉系统drain system——疏水系统wind-fume system——风烟系统blowdown system——排污系统condensate system——凝结水系统deaerator system——除氧器系统turbine body——汽轮机本体by-pass system——旁路系统cooling water system——冷却水系统circulation water system——循环水系统vacuum system——真空系统(六)阀门shutoff valve——截止阀check valve——单向阀motorized valve——电动阀magnetic valve——电磁阀pneumatic positioner valve——气动阀flapper valve——挡板阀steam converter valve——减温减压阀fast valve——快关阀blow down valve——吹扫阀blow down valve——排污阀(七)其它CCS(coordinated control system) ——协调控制系统SIS(supervision & information system) ——监控信息系统MIS(management information system) ——管理信息系统BF(MODE)(borler follow mode) ——锅炉跟随方式TF(MODE)(turbine follow mode) ——汽轮机跟随方式CCS(MODE)(coordinated control mode) ——协调控制方式Manual Mode——手动方式BASE MODE——基本(手动)方式ULD(unit load demand) ——机组负荷指令ADS(automatic dispatch system) ——自动调度系统UM(unit master) ——单元机组主控制器BM&TM(boiler master & turbine master) ——锅炉主控制器和汽轮机主控制器BCS(boiler control system) ——锅炉控制系统TCS(turbine control system) ——汽轮机控制系统RB(run back) ——负荷返回RD(run down) ——强迫降负荷(迫降负荷)RU(run up) ——强迫升负荷(迫升负荷)FCB(fast cut back) ——快速减负荷AGC(automatic generation control) ——自动发电控制MFT(master fuel trip) ——主燃料跳闸CP MODE(constan pressure mode) ——定压方式VP MODE(variable pressure mode) ——滑压方式MCR(maximum continuous rating) ——最大连续出力ECR(economic continuous rating)——经济连续出力B-MCR(boiler maximum continuous rating) ——锅炉最大连续出力T-MCR(turbine maximum continuous rating) ——汽轮机最大连续出力MCS(modulating control system) ——模拟量控制系统FSSS(furnace safeguard supervisory system) ——炉膛安全监控系统BMS(burner management system) ——燃烧器管理系统SCS(sequential control system) ——顺序控制系统ECS(electric control system) ——电气控制系统DEH(digital electric-hydraulic control system) ——数字电液控制系统OPC(over speed control) ——超速控制AST(autostop trip) ——自动停机遮断ETS(emergence trip systems) ——危急遮断系统ATC(automatic turbine control) ——自动汽轮机程序控制TSI(turbine supervisory instrumentation) ——汽轮机监视系统PLC(programmable logic controller) ——可编程逻辑控制器SCR(selective catalytic reduction)——选择性催化还原法二、电厂术语——锅炉部分1.临界压力锅炉supercritical pressure boiler2. 亚临界压力锅炉subcritical pressure boiler3. 超高压锅炉super-high pressure boiler4. 蒸汽锅炉steam boiler5. 蒸汽发生器steam generator6. 液态排渣锅炉wet bottom boiler7. 固态排渣锅炉dry bottom boiler8. 燃煤锅炉coal-fired boiler9. 燃气锅炉Gas-fired boiler10.燃油锅炉oil-fired boiler11.自然循环锅炉natural circulation boiler12.汽包(锅筒)锅炉drum boiler13.强制循环锅炉controlled circulation boiler14.直流锅炉once-through boiler15.复合循环锅炉combined circulation boiler16.旋风炉cyclone furnace boiler17.沸腾炉fluidized bed combustion(FBC)boiler18.循环硫化床circulating fluidized bed combustion(FBC)boiler19.增压循环硫化床锅炉pressurized circulating fluidized bed combustion(PCFBC) boiler20.链条锅炉chain-grate boiler21.热水锅炉hot-water boiler22.废热(余热)锅炉water-heat boiler, heat recover steam generator(HRSG)23.启动锅炉start-up boiler24.厂用锅炉auxiliary boiler25.垃圾焚烧锅炉refuse-fired boiler, refuse incinerator27.露天锅炉outdoor boiler28.单炉膛锅炉single furnace boiler29.双炉膛锅炉twin furnace boiler30.W火焰锅炉W-flame boiler, vertical-fired boiler31.L火焰锅炉L-shape furnace boiler32.塔式锅炉tower boiler33.箱式锅炉box-type boiler34.炉墙furnace wall35. 汽包(锅筒)drum36.封头head37.汽包封头drum end plate, drum head38.下降管downcomer39.集中下降管centralized downcomer40.分散下降管distributed downcomer41.上升管riser42.管束(排)tube bundle43.管屏tube platen44.省煤器管economizer tube45.过热器管superheated tube46.再热器管reheater tube47.蛇形管coil48.吊挂管supporting tube49.引入管inlet pipe50.引出管outlet pipe51.饱和蒸汽管saturated steam pipe52.水冷壁管water wall tube53.鳍片管finned tube, fin tube, gilled tube54.内螺纹管rifled tube, grooved tube55.吸潮管moisture absorption piping56.水冷壁water wall57.膜式水冷壁membrane wall58.内螺纹水冷壁rifled tube water wall59.联箱header60.集汽联箱steam header61.卫燃带bailey wall, refractory belt62包墙管(包覆管)wall enclosure tube63.防渣管(弗斯顿管)slag screen, feston tube64.锅炉本体boiler proper65.锅炉机组boiler unit66.锅炉构架boiler structure67.炉膛boiler framework68.燃烧器furnace69.直流式燃烧器direct-flow burner70.旋流式燃烧器turbulent burner71.低NOX燃烧器low NOX burner72.摇摆式燃烧器tilting burner73.缝隙式燃烧器split burner74.燃烧室combustion chamber75.油枪oil gun torch76.风门damper77.一次风primary air78.二次风secondary air79.三次风tertiary air80.煤粉管道pulverized coal piping81.管板tube plate82.沸点boiling temperature83.过热器superheater84.前屏过热器front platen superheater85.后屏过热器rear plate superheater86.对流过热器convection superheater87.辐射过热器radiant superheater88.屏式过热器plate superheater89.顶棚过热器ceiling superheater90.包墙过热器wall enclosure superheater91.前包墙过热器front wall enclosure superheater92.后包墙过热器rear wall enclosure superheater93.侧包墙过热器side wall enclosure superheater94.吹灰器soot blower95.转动式吹灰器rotary soot bolwer96.伸缩式吹灰器retractable soot blower97.受热面积heating surface area, heat absorption area98.炉膛容积furnace volume99.炉膛热负荷furnace heat release rate, furnace heating absorption rate 100.汽水分离器steam separator, moisture separator101.起动分离器starting separator102.再循环管recirculating piping103.暖风器steam air heater104.再热器reheater105.再热器冷段primary reheater106.再热器热段final reheater107.顶棚ceiling108.省煤器economizer109.管式省煤器tube economizer110.管式空气预热器tubular air preheater111.回转式(再生式)空气预热器regenerative air preheater, rotary air preheater112.板式空气预热器plate air preheater113.空气预热器air preheater114.三分仓空气预热器trisector regenerative air preheater115.漏风系数air leakage coefficient116.漏风率air leakage ratio117.漏风系统air leakage system118.漏风试验air leakage test119.安全门safety valve120.安全门开启压力opening pressure of safety valve121.安全门回座压力safety valve reseating pressure122.安全门压力整定试验pressure setting test of safety valve 123.安全门动作压力safety valve operating pressure124.饱和蒸汽安全门saturated steam safety valve125. 过热蒸汽安全门superheated steam safety valve126.再热蒸汽安全门reheated steam safety valve127.防暴门explosion vent128.检查孔inspection hole129.事故喷水阀emergency water spray valve130.汽包事故放水阀emergency drum drain valve 131.三通阀three-way valve132.反冲洗阀back wash valve133.取样阀sampling valve134.插板gate135.给水大旁路门feedwater overall bypass valve 136.给水小旁路门feedwater individual bypass valve 137.大板梁plate girder, upper beam138.外护板outer casing139.锅炉排污blowdown140.定期排污扩容器intermittent blowdown flash tank 141.连续排污扩容器continuous blowdown flash tank 142.灰斗ash hopper143.冷灰斗bottom ash hopper, furnace hopper144.混合器mixer145.齿圈(大牙轮)ring gear, geared ring146.空调器air conditioner147.空气压缩机air compressor148.给煤机coal feeder149.皮带式给煤机belt coal feeder150.刮板式给煤机scraper coal feeder151.叶轮式给煤机paddle coal feeder152.给粉机pulverizer coal feeder153.磨煤机coal pulverizer, coal mill154.钢球磨煤机tube mill155.中速辊式磨煤机roller mill, bowl mill, disk roll mill 156.双进双出钢求磨煤机double inlet and outlet tube mill 157.中速磨煤机medium speed mill158.风扇磨煤机beater wheel mill, beater mill159.排粉风机pulverized coal exhauster160.一次风机primary air fan161. 烟气再循环风机gas recirculation fan162.送风机forced draft fan, force fan163.引风机induced draft fan, induced fan164.离心风机centrifugal fan165.轴流风机axial-flow fan166.双速风机double speed fan167.轴流静叶可调风机adjustable static-blade axial-flow fan fixed pitch axial-flow fan168.轴流动叶可调风机adjustable moving-blade axial-flow fan variable pitch axial-flow fan169.原煤斗raw coal bunker, raw coal silo170.煤粉仓pulverized coal bunker171.输粉机pulverized coal conveyer172.刮板输粉机scraper pulverized coal conveyer 173.螺旋输粉机pulverized coal screw conveyer174.粗粉分离器classifier175.细粉分离器(旋风分离器)cyclone separator 176.锁气器air lock, flap177.减速机speed reduce178.看火孔observation hole179.人孔门man hole180.重油泵heavy oil pump181.重油加热器heavy oil heater182.汽-汽热交换器biflux183.煤气罐gas tank184.膨胀补偿节expansion joint185.直吹式制粉系统direct firing pulverizing system 186.中贮式制粉系统bin storage type pulverizing system 187.锅炉效率boiler efficiency188.锅炉热力计算boiler thermodynamic calculation 189.锅炉空气动力计算boiler aerodynamic calculation 190.锅炉水循环计算boiler water circulation calculation 191.锅炉水力计算boiler hydrodynamic calculation 192.锅炉强度计算boiler strength calculation193.锅炉热平衡boiler heat balance calculation 194.正平衡法direct balance method195.反平衡法indirect balance method196.过剩空气系数excess air coefficient197.排烟温度flue gas temperature198.单位蒸量specific evaporation199.低温腐蚀low temperature corrosion200.高温腐蚀high temperature corrosion201.结渣lagging202.结垢腐蚀deposit corrosion203.飞灰磨损fly ash erosion204炉膛负压furnace draft205.最高允许温度maximum permissible temperature 206.炉膛正压furnace pressure207.水循环water circulation208.循环倍率circulation ratio209.除尘器dust collector, precipitator210.静电除尘器electrostatic precipitator211.整流装置rectifying device212.锤打装置rapping gear213.含尘浓度dust loading concentration214.煤灰细度dust fineness。
English_consise-脱硫单词缩写
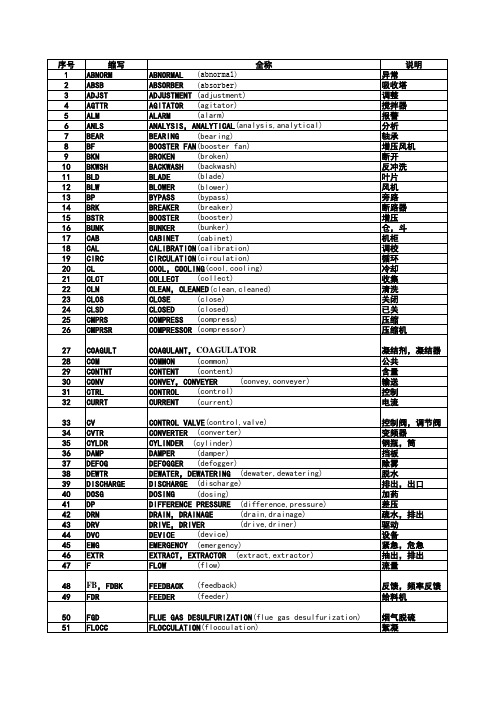
全称 (abnormal) ABNORMAL (absorber) ABSORBER ADJUSTMENT (adjustment) (agitator) AGITATOR (alarm) ALARM ANALYSIS,ANALYTICAL(analysis,analytical) ANALYSIS,ANALYTICAL (bearing) BEARING BOOSTER FAN (booster fan) (broken) BROKEN (backwash) BACKWASH BLADE (blade) (blower) BLOWER (bypass) BYPASS (breaker) BREAKER (booster) BOOSTER (bunker) BUNKER (cabinet) CABINET CALIBRATION (calibration) CIRCULATION (circulation) COOL,COOLING(cool,cooling) COOL,COOLING (collect) COLLECT CLEAN,CLEANED(clean,cleaned) CLEAN,CLEANED (close) CLOSE (closed) CLOSED (compress) COMPRESS COMPRESSOR (compressor) COAGULANT, COAGULANT,COAGULATOR (common) COMMON (content) CONTENT CONVEY, (convey,conveyer) CONVEY,CONVEYER (control) CONTROL (current) CURRENT CONTROL VALVE (control,valve) CONVERTER (converter) CYLINDER (cylinder) (damper) DAMPER (defogger) DEFOGGER DEWATER, DEWATER,DEWATERING (dewater,dewatering) DISCHARGE (discharge) (dosing) DOSING DIFFERENCE PRESSURE (difference,pressure) DRAIN, (drain,drainage) DRAIN,DRAINAGE DRIVE, (drive,driner) DRIVE,DRIVER (device) DEVICE EMERGENCY (emergency) EXTRACT, EXTRACT,EXTRACTOR (extract,extractor) (flow) FLOW (feedback) FEEDBACK (feeder) FEEDER FLUE GAS DESULFURIZATION (flue gas desulfurization) FLOCCULATION (flocculation) (filter) FILTER (filtrate) FILTRATE FLUIDIZE (fluidize) (frequency) FREQUENCY (fault) FAULT
检测报告中英文信息对照表
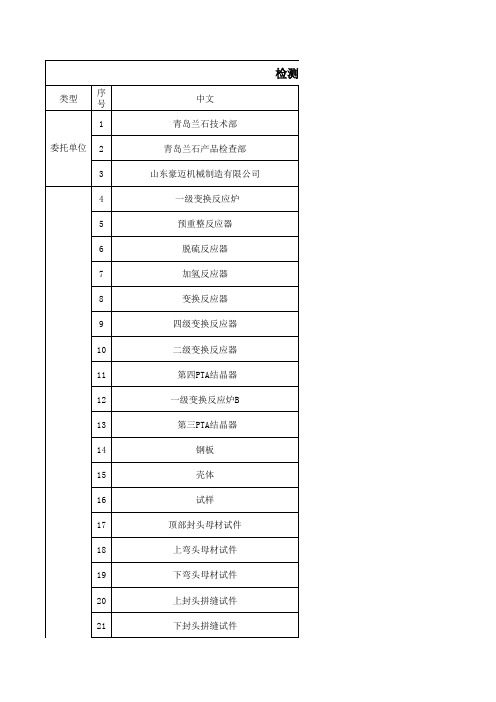
the lower ellipsoidal head base metal piece the upper head base metal piece the lower head base metal piece the longitudinal weld of shell the longitudinal welding piece of shell the circumferential weld of shell the longitudinal and circumferential weld of shell the top Head joint piece the under Head joint piece Double thread stud stud bolt the lower head cover joint piece the upper head melon petal joint plate the upper head watts valve joint plate the upper head base metal cover joint piece the lower spherical head welding test piece welding test plate The pipe and barrel welded joint specimens Barrel longitudinal seam welded joint specimens The under Headjoint Welded joint specimen The top and bottom pipe joint head Specimen GTAW+SMAW Procedure qualification test plate
DCS中英文对照表(缩写和全称)
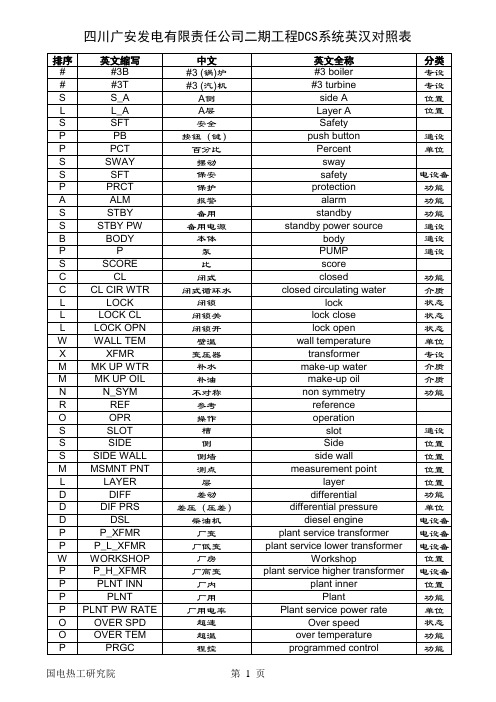
分类 专设 专设 位置 位置
通设 单位
电设备 功能 功能 功能 通设 通设 通设
功能 介质 状态 状态 状态 单位 专设 介质 介质 功能
通设 位置 位置 位置 位置 功能 单位 电设备 电设备 电设备 位置 电设备 位置 功能 单位 状态 功能 功能
国电热工研究院
第1页
四川广安发电有限责任公司二期工程DCS系统英汉对照表
英文全称
分类
flange
专设
tippler
功能
feedback
功能
reverse
状态
reversal rotation
功能
mode
功能
Discharge steam
功能
discharge water
功能
Dischar drive end
位置
isolating platen
国电热工研究院
第3页
四川广安发电有限责任公司二期工程DCS系统英汉对照表
排序 F T F R R M D D D N N I S A B B P A W A L P T R V H H H H H H H H H H H H H I P C F I W O O
英文缩写 FLAN TPLR FDBK RVRS RRT MODE
功能
High
状态
high voltage standby transformer 电设备
high voltage
状态
high pressure auxiliary
专设
high pressure header
专设
high energy spark ignitor
专设
high speed
高含硫气田工程专业术语中英文对照要点
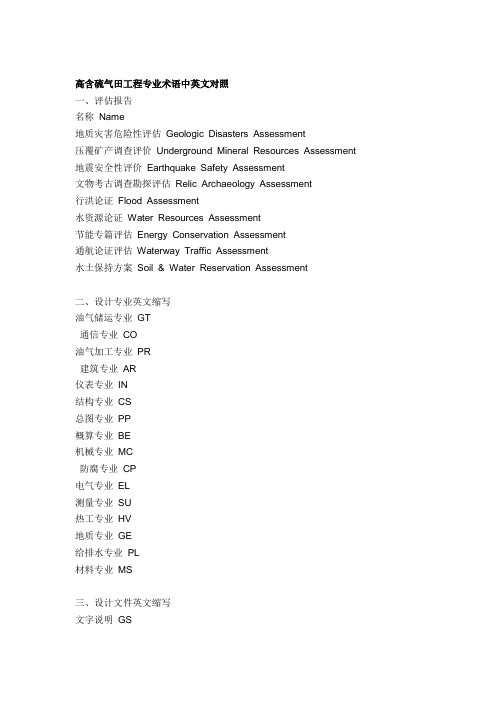
高含硫气田工程专业术语中英文对照一、评估报告名称Name地质灾害危险性评估Geologic Disasters Assessment压覆矿产调查评价Underground Mineral Resources Assessment 地震安全性评价Earthquake Safety Assessment文物考古调查勘探评估Relic Archaeology Assessment行洪论证Flood Assessment水资源论证Water Resources Assessment节能专篇评估Energy Conservation Assessment通航论证评估Waterway Traffic Assessment水土保持方案Soil & Water Reservation Assessment二、设计专业英文缩写油气储运专业GT通信专业CO油气加工专业PR建筑专业AR仪表专业IN结构专业CS总图专业PP概算专业BE机械专业MC防腐专业CP电气专业EL测量专业SU热工专业HV地质专业GE给排水专业PL材料专业MS三、设计文件英文缩写文字说明GS仪表计算数据表IC图纸(各专业图纸) DR设备技术规格书SP设备表EL设备数据表DS材料表ML其它表格OT工艺管线说明表PD四.油气储运专业设备名称Equipment Name井场Well Pad集气站Gathering Station阀室Valve Station集气干线Gas Gathering Trunk Line采气管线Gas Gathering Flow Line燃料气干线Fuel Gas Trunk Line燃料气支线Fuel Gas Branch水套加热炉Jacket Heater清管器发送装置Pig Launcher清管器接收装置Pig Receiver分离器Separator过滤分离器Filter Separator缓蚀剂储罐Inhibitor Tank防冻剂储罐Antifreeze Tank火炬Flare测试分离器Test Separator五、油气加工专业1、脱硫装置SULFUR REMOVAL UNIT 设备名称Equipment Name脱硫吸收塔Main Absorber闪蒸气吸收塔Flash Gas Absorber再生塔Regenerator原料气分离器Feed Gas Separator湿净化气分离器Treated Gas K.O. Drum闪蒸罐Flash Drum回流罐Reflux Drum胺液排放罐Amine Drain Drum贫富胺液换热器Lean/rich Exchanger贫胺液冷却器Lean Solvent Cooler贫胺液后冷却器Lean Solvent Trim Cooler重沸器Reboiler塔顶冷凝器Overhead Condenser塔顶后冷器Overhead Trim Cooler原料气过滤分离器Filter Separator胺液机械过滤器Amine Filter活性炭过滤器Activated Carbon Filter胺液后过滤器Amine trim filter/Carbon Particle Filter 排放溶液过滤器Drained Solvent Filter低压贫胺液泵LP Lean Solvent Pump高压贫胺液泵HP Lean Solvent Pump回流泵Reflux Pump新鲜溶液泵Fresh Solvent Pump排放溶液泵Drained Solvent Pump富胺液能量回收透平Fat Solvent Expander溶液补充罐Solvent Make-up Tank2、脱水装置DEHYDRATION UNIT设备名称Equipment NameTEG吸收塔TEG AbsorberTEG重沸器TEG ReboilerTEG缓冲罐TEG buffer Drum套管换热器Sleeve ExchangerTEG贫/富液换热器Lean/Rich TEG Exchanger产品气分离器Product Gas K.O. DrumTEG预过滤器TEG FilterTEG活性炭过滤器Activated Carbon FilterTEG后过滤器TEG Trim FilterTEG闪蒸罐Flash Drum再生气分液罐Regenerate gas K.O. DrumTEG储罐TEG tank氮气水封罐Water Sealed DrumTEG补充罐TEG Make-up Tank凝结水闪蒸罐Condensate K.O. Drum燃料气罐Fuel Gas K.O. Drum净化空气罐Instrument Air DrumTEG补充泵TEG Make-up PumpTEG回收泵TEG Recovery Pump蒸汽喷射泵Steam Eject pumpTEG循环泵Lean TEG Pump3、硫磺回收装置SULFUR RECOVERY UNIT设备名称Equipment Name酸气分离器Acid Gas K.O. Drum液硫封Sulfur Locks排污罐Blowdown Drum蒸汽冷凝水闪蒸罐Condensate Flash Drum余热锅炉Waste Heat Boiler一级硫磺冷凝冷却器First Sulfur Condenser二级硫磺冷凝冷却器Second Sulfur Condenser三级硫磺冷凝冷却器Third Sulfur Condenser一级再热器First Reheater二级再热器Second Reheater硫磺冷却器Sulfur Cooler锅炉给水预热器BFW Preheater液硫池蒸汽加热盘管Sulfur Pit Steam Coil主燃烧器Main Burner燃烧室Combustion Chamber主风机(蒸汽透平驱动)Main Air Blower (Turbine driven) 主风机(电机驱动)Main Air Blower (Motor driven)酸水泵Acid Gas Condensate Pump液硫泵Sulfur Pump液硫池Sulfur Pit一级反应器First Reactor二级反应器Second Reactor鼓泡器Bubble Columns蒸汽喷射器(带夹套) Steam Ejector催化剂Catalyst瓷球Ceramic Balls4、尾气处理装置TAIL GAS TREATMENT UNIT设备名称Equipment Name急冷塔Quench ColumnSCOT吸收塔SCOT Absorber酸水汽提塔Sour Water Stripper凝结水排污罐SCOT Blowdown Drum蒸汽分水器Steam/water Separator闪蒸气缓冲罐Flash Gas Buffer Drum燃料气分离器Fuel Gas K.O. Drum酸水收集罐Sour Water Collection Drum酸水汽提塔回流罐SWS Reflux Drum气体冷却器Gas Cooler急冷水冷却器Quench Water Cooler急冷塔后冷器Quench Water Trim Cooler焚烧炉余热锅炉Incinerator Waste Heat Boiler蒸汽过热器Steam Superheater酸水汽提塔热交换器SWS Heat Exchanger酸水汽提塔重沸器SWS Reboiler酸水汽提塔顶冷凝器SWS Overhead Condenser汽提水冷却器Stripped Water Cooler汽提水后冷器Stripped Water Trim Cooler急冷水过滤器Quench Water FilterSCOT燃烧器SCOT BurnerSCOT混合室SCOT Mixing Chamber焚烧炉燃烧器Incinerator Burner焚烧炉混合室Incinerator Mixing Chamber灼烧炉风机(蒸汽透平驱动)Incinerator Air Blower (Turbine driven) 灼烧炉风机(电机驱动)Incinerator Air Blower (Motor driven)急冷水泵Quench Water Pump半贫液泵(电机驱动)Semi-lean Solvent Pump (Motor Driven)半贫液泵(蒸汽透平驱动)Semi-lean Solvent Pump(Turbine Driven) 酸水汽提塔进料泵SWS Feed Pump酸水汽提塔底泵Stripped Water Pump酸水汽提塔回流泵SWS Reflux PumpSCOT反应器SCOT Reactor蒸汽喷射器SCOT Ejector烟囱StackSCOT催化剂SCOT Catalyst5、硫磺成型装置SULFUR FORMING UNIT设备名称Equipment Name液硫储罐Liquid sulfur tank净化空气罐Instrument air tank蒸汽分水器Steam water separator液硫泵Liquid sulfur pump液硫过滤系统Sulfur filter system自动称量包装码垛系统Automatic weighing, packing and stacking product line 硫磺仓库Sulfur warehouse硫磺成型机Sulfur granulator6、火炬及放空系统FLARE SYSTEM设备名称Equipment Name天然气放空火炬Nature gas flare酸气放空火炬Sour gas flare天然气放空分离器Nature gas vent separator凝液回收罐Condensate Collection Tank凝液泵Condensate pump火炬头Flare head分子封Gas seal火炬筒体Flare stack 7、空氮站AIR AND NITROGEN STATION设备名称Equipment Name空气压缩机Air compressor空气干燥器Air Drier制氮橇块Nitrogen Skid精密过滤器Nicety filter净化空气罐Instrument Air Drum非净化空气罐Plant Air Drum氮气罐Nitrogen Drumk六、仪表及自动控制通用描述COMMON DESCRIPTION设备名称Equipment Name 缩写ABB.分散控制系统Distributed Control System DCS安全仪表系统Safety Instrumentation System SIS紧急切断系统Emergency Shutdown system ESD火气系统Fire and Gas system F&G监视控制和数据采集系统Supervisory Control and Data Acquisition SCADA 可编程逻辑控制器Programmed Logic Controller PLC远程终端单元Remote Terminal Unit RTU站控系统Station Control System SCS中央控制室Central Control Room CCR操作间Operation room机柜间Equipment room/ Cabinet room大屏显示系统Large Screen Display system LSD流量类仪表FLOW INSTRUMENT设备名称Equipment Name孔板Orifice Plate文丘里流量计Venturi Flowmeter均速管流量计Averaging Pitot Tube阀式孔板节流装置Orifice Plate in quick change fitting涡轮流量计Turbine Flowmeter涡街流量计Vortex Flowmeter容积式流量计Positive Displacement Flowmeter靶式流量计Target Flowmeter超声波流量计Ultrasonic FlowmeterV型流量计V-cone Flowmeter电磁流量计Electromagnetic Flowmeter楔型流量计Wedge Flowmeter转子流量计Rotameter整流器Straightening Vane温度类仪表TEMPERATURE INSTRUMENT双金属温度计Bi-metallic temperature gauge热电偶Thermocouple表面热电偶Surface Thermocouple热电阻Resistance Temperature Detector温度变送器Temperature transmitter光学高温计Optical pyrometer温度计套管Thermowell压力类仪表PRESSURE INSTRUMENT设备名称Equipment Name压力表Manometer /Pressure gauge弹簧管压力表Burdon-tube manometer隔膜压力表Diaphragm-seal manometer /Diaphragm-seal pressure gauge 差压表Differential pressure gauge压力变送器Pressure transmitter差压变送器Differential pressure transmitter液位类仪表LEVEL INSTRUMENT设备名称Equipment Name玻板液位计Glass type level gauge磁浮子液位计Magnetic coupled indicator雷达液位变送器Radar level transmitter浮筒液位变送器Displacer level transmitter磁致伸缩液位变送器Magnetostrictive level transmitter液位开关Level switch阀门类VALVE设备名称Equipment Name球阀Ball valve单座阀Globe valve套筒阀Sleeve valve蝶阀Butterfly valve偏心旋转阀Eccentric rotary valve截止阀Globe valve角阀Angle valve电磁阀Solenoid valve六、通信设备名称Equipment Name程控电话交换系统PABX System局域网及综合布线系统LAN & Generic Cabling System防爆扩音/对讲系统Explosion-Proof Loud Speaking/Talk Back System 工业电视监视系统CCTV System电力调度系统Power Line Carrier System周界防范系统Boundary Security System光通信系统Optical Fiber communication system有线电视系统CATV System七、供配电设备名称Equipment Name变电所Substation高低压配电装置HV&LV Switchgear柴油发电机Diesel Generator油浸式变压器Oil-immersed Power Transformer干式变压器Dry-type Power Transformer有载调压开关On-load Tap Switch直流屏DC UPS微机综合自动化系统Integrated Substation Automation System应急电源Emergency Power Supply配电箱Lighting and Small Power Distribution Panel电缆桥架Cable Tray电缆沟Cable Trough架空电力线路Over-head Lines爆炸危险区域划分Hazardous Area Classification单线图Single Line Diagram电容补偿Capacitor Unit现场操作柱Local Control Station供配电系统Power Supply & Distribution SystemUPS:AC UPS八、给排水给水Water Supply设备名称Equipment Name取水深井泵房Intake Structure高位水池Elevated Tank阀门井Valve Well生产、消防水泵房Water Supply Pump Room加药设备用房Dosage Room加药间Dosage Room预沉池Pre-sedimentation Tank穿孔旋流反应斜管沉淀池Reaction Sedimentation Tank 重力式无阀滤池Valveless Filter清水池Clear Water Pit循环水厂Circulating Water Station循环水泵房Recirculating Pump House药剂间Chemical Room循环冷水池Cooling Water Tank循环热水提升池Lifting Tank冷却塔Cooling Tower污水Sewage水泵棚Water Pump Shed污泥棚Sludge Shed风机棚Fan Shed化粪池Septic Tank污水处理综合用房Sewage Treatment House格栅池Bar Screen Tank曝气调节池Aeration Tank水解酸化池Acid hydrolysis Tank缺氧池Anoxia Tank好氧池Aerobic Tank生化池Biochemical Structure沉淀池Sedimentation Tank保险池Insurance Tank污泥浓缩池Concentration Tank检修污水池Overhaul Water Tank气浮池Floatation Tank隔油池Oil Separator事故水池Emergency Tank污泥焚烧系统Sludge Incineration SystemRO反渗透用房(Reverse Osmosis) RO House九、建筑设备名称Equipment Name工艺装置循环水泵房Recirculating Water Pump House污水处理综合用房Sewage Treatment House污泥脱水及鼓风机房Sludge dewatering and air blower room生产、消防给水泵房Water supply pump room空氮站及10/0.4 KV变电所Air and nitrogen station and 10/0.4KV Transformer substation锅炉房Boiler room锅炉房10/0.4 KV变电所Boiler room10/0.4KV Transformer substation35KV变电所35KV Transformer substation中央控制室Central control room车间办公室Workshop office分析化验室Lab钢瓶使用间Cylinder room门卫Security post硫磺成型机厂房Sulfur forming plant硫磺仓库Sulfur warehouse硫磺仓库辅助用房Sulfur warehouse auxiliary room综合楼Administration building10KV变电站10KV transformer substation硫磺成型10/0.4 KV变电站10/0.4KV transformer substation for sulfur forming unit消防应急站Fire fighting and response station库房、维修及配套用房Warehouse and maintenance room空压站棚Air compression station shed取水深井泵房Intake Structure倒班生活区Living Quarter十、供热设备名称Equipment Name低压锅炉Low-pressure boiler中压锅炉Medium-pressure boiler鼓风机Air-blower引风机Induced draft fan烟囱Stack烟道Flue燃烧机Burner过热器出口集箱Export header of superheated过热器入口集箱Import header of superheated省煤器出口集箱Export header of Economizer省煤器进口集箱Import header of Economizer省煤器中间集箱Middle header of Economizer混合集箱Mixing Header低压给水泵Low-pressure water supply pump中压给水泵Medium-pressure water supply pump上锅筒Steam drum下锅筒Drum加药Chemical Dosing排污Blowdown闪蒸汽Flash vapor除氧器Deaerator除盐水泵Demineralization water pump除盐水罐Demineralization water container空气储罐Air tank清洗水泵Cleaning pump布袋过滤器Cloth envelop collector板式换热器Plate heat exchanger超滤水罐Ultra-filtration container清洗装置Cleaning device凝结水罐Condensation container除氧水泵Deaerating water pump开工锅炉给水泵Water supply pump of start-up boiler水水换热器Water-water heat exchanger一级高压泵Primary high pressure pump一级反渗透装置Primary the reverse osmosis (RO) equipment保安过滤器Nanofiltration减温器Resuperheater连续排污扩容器Continuous Blowdown Flash Tanks定期排污扩容器Regularity Blowdown Flash Tanks排污泵Blowdown Pump加药装置Chemical adding unit整流器Rectifier加盐计量泵Chemical adding metering pump浓水循环泵Thick water circulation pump清洗水箱Cleaning water container清洗过滤器Cleaned Filter综合用房:general house综合楼:administration building倒班宿舍:living quarters中国石油天然气股份有限公司西南油气田分公司: PetroChina Southwest Oil & Gasfield Company循环水系统:cooling water system自动控制:Instrumentation土木工程:Civil structure建筑:Architecture总图:Plot plan岩土工程勘察geotechnical investigation工程地质测绘engineering geological mapping岩土工程勘探geotechnical exploration原位测试in-situ tests岩土工程勘察报告geotechnical investigation report现场检验in-situ inspection现场监测in-situ monitoring岩石质量指标(RQD) rock quality designation土试样质量等级quality classification of soil samples不良地质作用adverse geologic actions地质灾害geological disaster地面沉降ground subsidence,land subsidence岩土参数标准值standard value of a geotechnical parameter废水/污水:Waste Water回注污水:Reinjection waste water气田水:Gas Field Water气田水、处理厂回注污水泄露风险及防范措施:Leakage Risks of Gas Field Water and Reinjection Waste Water in the Tre atment Plant and CountermeasuresDear Sir 翻译成“尊敬的先生”描述”-- “DESCRIPTION”“版次”--“REVISION”“应/应该”--“SHALL”“宜”--“SHOULD”“脱硫”--“SULFUR REMOVAL”“推荐/建议”--“PREFER”“审核”--“ENG APPR”“审定”--“CHIEF APPR”“内部集输工程”--“INTERNAL GATHERING SYSTEM”“说明书”改成“REPORT”.“勘察设计校审卡”统一成“quality tracing card"节流器:throttle节流嘴:throttling nozzle截止阀:Globe valve截断阀:Block valve止回阀:Check valve节流截止放空阀:Throttling, check and vent valve针阀节流压降: Needle valve throttling pressure drop双作用节流截止阀: double acting throttling and check valveXxxx室:Xxxx Section如:“油气加工室”翻译译成“PROC Section 或者PR Section”闭排灌closed drain drum自备式电站captive power station。
脱硫专业英语[1]
![脱硫专业英语[1]](https://img.taocdn.com/s3/m/6576b82a453610661ed9f45c.png)
脱硫技术常用英语术语
模拟线路,辅助程序 底部 碗式磨 脆性,易脆的 支架,托架,括号 宽度 断开,断路 断路器,隔离开关 跳闸线路 微风,煤粉 熄火,燃烧终结 电桥,跨接,桥形网络 班,组,队,大队 广播 节约用电 电刷,刷子 电刷摇环 褐煤 瓦斯保护 斗,吊斗 缓冲箱 建立 公告,公报 碰,撞击 煤仓 燃烧器 燃烧器管理系统 母线段 母线 母线支架 母联 按钮 BYP 旁路 旁路阀
C 柜 电缆 计算器 管径、尺寸、大小 卡 热的、热量 发热量、热值 发热的、热量的 热效率 取消、省略
CAPAC 电容 容抗 容量、出力、能量 (电子)板、卡 搬运机、载波、带电粒子 高频保护
CAS 串级 套管 壳、箱 偶然的、临时、不规则的 不定期检查、临时检查 人身事故、伤亡、故障 灾祸、事故 重大事故 猫爪 阴板、负极
自动调压器
Auxiliary
AUX 辅助的
Auxiliary power
厂用电
Available
有效的,可用的
Avoid
避免,回避
Avometer
万用表,安伏欧表计
Axial
轴向的
Axis
轴,轴线
Axis disp protection
轴向位移,保护
Axle
轴,车轴,心捧
B
Back
背后,反向的
Back pressure
2
脱硫技术常用英语术语
第 3 页 共 13 页
Compensation
补偿
Company
CO 公司
Company limited
CO LTD 有限公司
Complexity
复杂
Complete
完成
Component
高含硫气田工程专业术语中英文对照
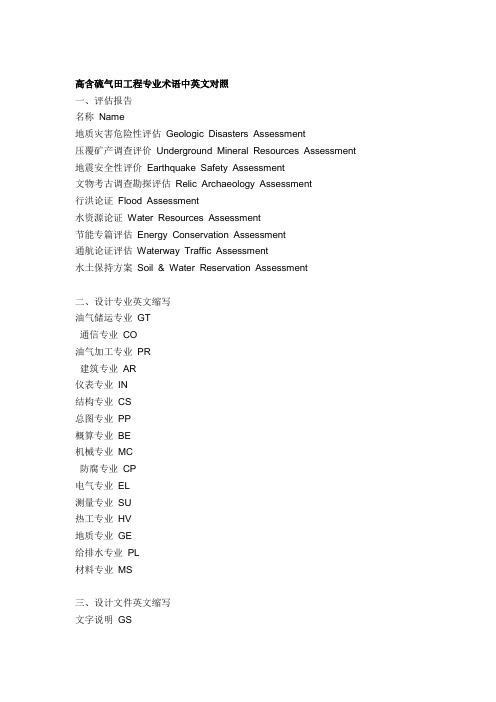
高含硫气田工程专业术语中英文对照一、评估报告名称Name地质灾害危险性评估Geologic Disasters Assessment压覆矿产调查评价Underground Mineral Resources Assessment 地震安全性评价Earthquake Safety Assessment文物考古调查勘探评估Relic Archaeology Assessment行洪论证Flood Assessment水资源论证Water Resources Assessment节能专篇评估Energy Conservation Assessment通航论证评估Waterway Traffic Assessment水土保持方案Soil & Water Reservation Assessment二、设计专业英文缩写油气储运专业GT通信专业CO油气加工专业PR建筑专业AR仪表专业IN结构专业CS总图专业PP概算专业BE机械专业MC防腐专业CP电气专业EL测量专业SU热工专业HV地质专业GE给排水专业PL材料专业MS三、设计文件英文缩写文字说明GS仪表计算数据表IC图纸(各专业图纸) DR设备技术规格书SP设备表EL设备数据表DS材料表ML其它表格OT工艺管线说明表PD四.油气储运专业设备名称Equipment Name井场Well Pad集气站Gathering Station阀室Valve Station集气干线Gas Gathering Trunk Line采气管线Gas Gathering Flow Line燃料气干线Fuel Gas Trunk Line燃料气支线Fuel Gas Branch水套加热炉Jacket Heater清管器发送装置Pig Launcher清管器接收装置Pig Receiver分离器Separator过滤分离器Filter Separator缓蚀剂储罐Inhibitor Tank防冻剂储罐Antifreeze Tank火炬Flare测试分离器Test Separator五、油气加工专业1、脱硫装置SULFUR REMOVAL UNIT 设备名称Equipment Name脱硫吸收塔Main Absorber闪蒸气吸收塔Flash Gas Absorber再生塔Regenerator原料气分离器Feed Gas Separator湿净化气分离器Treated Gas K.O. Drum闪蒸罐Flash Drum回流罐Reflux Drum胺液排放罐Amine Drain Drum贫富胺液换热器Lean/rich Exchanger贫胺液冷却器Lean Solvent Cooler贫胺液后冷却器Lean Solvent Trim Cooler重沸器Reboiler塔顶冷凝器Overhead Condenser塔顶后冷器Overhead Trim Cooler原料气过滤分离器Filter Separator胺液机械过滤器Amine Filter活性炭过滤器Activated Carbon Filter胺液后过滤器Amine trim filter/Carbon Particle Filter 排放溶液过滤器Drained Solvent Filter低压贫胺液泵LP Lean Solvent Pump高压贫胺液泵HP Lean Solvent Pump回流泵Reflux Pump新鲜溶液泵Fresh Solvent Pump排放溶液泵Drained Solvent Pump富胺液能量回收透平Fat Solvent Expander溶液补充罐Solvent Make-up Tank2、脱水装置DEHYDRATION UNIT设备名称Equipment NameTEG吸收塔TEG AbsorberTEG重沸器TEG ReboilerTEG缓冲罐TEG buffer Drum套管换热器Sleeve ExchangerTEG贫/富液换热器Lean/Rich TEG Exchanger产品气分离器Product Gas K.O. DrumTEG预过滤器TEG FilterTEG活性炭过滤器Activated Carbon FilterTEG后过滤器TEG Trim FilterTEG闪蒸罐Flash Drum再生气分液罐Regenerate gas K.O. DrumTEG储罐TEG tank氮气水封罐Water Sealed DrumTEG补充罐TEG Make-up Tank凝结水闪蒸罐Condensate K.O. Drum燃料气罐Fuel Gas K.O. Drum净化空气罐Instrument Air DrumTEG补充泵TEG Make-up PumpTEG回收泵TEG Recovery Pump蒸汽喷射泵Steam Eject pumpTEG循环泵Lean TEG Pump3、硫磺回收装置SULFUR RECOVERY UNIT设备名称Equipment Name酸气分离器Acid Gas K.O. Drum液硫封Sulfur Locks排污罐Blowdown Drum蒸汽冷凝水闪蒸罐Condensate Flash Drum余热锅炉Waste Heat Boiler一级硫磺冷凝冷却器First Sulfur Condenser二级硫磺冷凝冷却器Second Sulfur Condenser三级硫磺冷凝冷却器Third Sulfur Condenser一级再热器First Reheater二级再热器Second Reheater硫磺冷却器Sulfur Cooler锅炉给水预热器BFW Preheater液硫池蒸汽加热盘管Sulfur Pit Steam Coil主燃烧器Main Burner燃烧室Combustion Chamber主风机(蒸汽透平驱动)Main Air Blower (Turbine driven) 主风机(电机驱动)Main Air Blower (Motor driven)酸水泵Acid Gas Condensate Pump液硫泵Sulfur Pump液硫池Sulfur Pit一级反应器First Reactor二级反应器Second Reactor鼓泡器Bubble Columns蒸汽喷射器(带夹套) Steam Ejector催化剂Catalyst瓷球Ceramic Balls4、尾气处理装置TAIL GAS TREATMENT UNIT设备名称Equipment Name急冷塔Quench ColumnSCOT吸收塔SCOT Absorber酸水汽提塔Sour Water Stripper凝结水排污罐SCOT Blowdown Drum蒸汽分水器Steam/water Separator闪蒸气缓冲罐Flash Gas Buffer Drum燃料气分离器Fuel Gas K.O. Drum酸水收集罐Sour Water Collection Drum酸水汽提塔回流罐SWS Reflux Drum气体冷却器Gas Cooler急冷水冷却器Quench Water Cooler急冷塔后冷器Quench Water Trim Cooler焚烧炉余热锅炉Incinerator Waste Heat Boiler蒸汽过热器Steam Superheater酸水汽提塔热交换器SWS Heat Exchanger酸水汽提塔重沸器SWS Reboiler酸水汽提塔顶冷凝器SWS Overhead Condenser汽提水冷却器Stripped Water Cooler汽提水后冷器Stripped Water Trim Cooler急冷水过滤器Quench Water FilterSCOT燃烧器SCOT BurnerSCOT混合室SCOT Mixing Chamber焚烧炉燃烧器Incinerator Burner焚烧炉混合室Incinerator Mixing Chamber灼烧炉风机(蒸汽透平驱动)Incinerator Air Blower (Turbine driven) 灼烧炉风机(电机驱动)Incinerator Air Blower (Motor driven)急冷水泵Quench Water Pump半贫液泵(电机驱动)Semi-lean Solvent Pump (Motor Driven)半贫液泵(蒸汽透平驱动)Semi-lean Solvent Pump(Turbine Driven) 酸水汽提塔进料泵SWS Feed Pump酸水汽提塔底泵Stripped Water Pump酸水汽提塔回流泵SWS Reflux PumpSCOT反应器SCOT Reactor蒸汽喷射器SCOT Ejector烟囱StackSCOT催化剂SCOT Catalyst5、硫磺成型装置SULFUR FORMING UNIT设备名称Equipment Name液硫储罐Liquid sulfur tank净化空气罐Instrument air tank蒸汽分水器Steam water separator液硫泵Liquid sulfur pump液硫过滤系统Sulfur filter system自动称量包装码垛系统Automatic weighing, packing and stacking product line 硫磺仓库Sulfur warehouse硫磺成型机Sulfur granulator6、火炬及放空系统FLARE SYSTEM设备名称Equipment Name天然气放空火炬Nature gas flare酸气放空火炬Sour gas flare天然气放空分离器Nature gas vent separator凝液回收罐Condensate Collection Tank凝液泵Condensate pump火炬头Flare head分子封Gas seal火炬筒体Flare stack 7、空氮站AIR AND NITROGEN STATION设备名称Equipment Name空气压缩机Air compressor空气干燥器Air Drier制氮橇块Nitrogen Skid精密过滤器Nicety filter净化空气罐Instrument Air Drum非净化空气罐Plant Air Drum氮气罐Nitrogen Drumk六、仪表及自动控制通用描述COMMON DESCRIPTION设备名称Equipment Name 缩写ABB.分散控制系统Distributed Control System DCS安全仪表系统Safety Instrumentation System SIS紧急切断系统Emergency Shutdown system ESD火气系统Fire and Gas system F&G监视控制和数据采集系统Supervisory Control and Data Acquisition SCADA 可编程逻辑控制器Programmed Logic Controller PLC远程终端单元Remote Terminal Unit RTU站控系统Station Control System SCS中央控制室Central Control Room CCR操作间Operation room机柜间Equipment room/ Cabinet room大屏显示系统Large Screen Display system LSD流量类仪表FLOW INSTRUMENT设备名称Equipment Name孔板Orifice Plate文丘里流量计Venturi Flowmeter均速管流量计Averaging Pitot Tube阀式孔板节流装置Orifice Plate in quick change fitting涡轮流量计Turbine Flowmeter涡街流量计Vortex Flowmeter容积式流量计Positive Displacement Flowmeter靶式流量计Target Flowmeter超声波流量计Ultrasonic FlowmeterV型流量计V-cone Flowmeter电磁流量计Electromagnetic Flowmeter楔型流量计Wedge Flowmeter转子流量计Rotameter整流器Straightening Vane温度类仪表TEMPERATURE INSTRUMENT双金属温度计Bi-metallic temperature gauge热电偶Thermocouple表面热电偶Surface Thermocouple热电阻Resistance Temperature Detector温度变送器Temperature transmitter光学高温计Optical pyrometer温度计套管Thermowell压力类仪表PRESSURE INSTRUMENT设备名称Equipment Name压力表Manometer /Pressure gauge弹簧管压力表Burdon-tube manometer隔膜压力表Diaphragm-seal manometer /Diaphragm-seal pressure gauge 差压表Differential pressure gauge压力变送器Pressure transmitter差压变送器Differential pressure transmitter液位类仪表LEVEL INSTRUMENT设备名称Equipment Name玻板液位计Glass type level gauge磁浮子液位计Magnetic coupled indicator雷达液位变送器Radar level transmitter浮筒液位变送器Displacer level transmitter磁致伸缩液位变送器Magnetostrictive level transmitter液位开关Level switch阀门类VALVE设备名称Equipment Name球阀Ball valve单座阀Globe valve套筒阀Sleeve valve蝶阀Butterfly valve偏心旋转阀Eccentric rotary valve截止阀Globe valve角阀Angle valve电磁阀Solenoid valve六、通信设备名称Equipment Name程控电话交换系统PABX System局域网及综合布线系统LAN & Generic Cabling System防爆扩音/对讲系统Explosion-Proof Loud Speaking/Talk Back System 工业电视监视系统CCTV System电力调度系统Power Line Carrier System周界防范系统Boundary Security System光通信系统Optical Fiber communication system有线电视系统CATV System七、供配电设备名称Equipment Name变电所Substation高低压配电装置HV&LV Switchgear柴油发电机Diesel Generator油浸式变压器Oil-immersed Power Transformer干式变压器Dry-type Power Transformer有载调压开关On-load Tap Switch直流屏DC UPS微机综合自动化系统Integrated Substation Automation System应急电源Emergency Power Supply配电箱Lighting and Small Power Distribution Panel电缆桥架Cable Tray电缆沟Cable Trough架空电力线路Over-head Lines爆炸危险区域划分Hazardous Area Classification单线图Single Line Diagram电容补偿Capacitor Unit现场操作柱Local Control Station供配电系统Power Supply & Distribution SystemUPS:AC UPS八、给排水给水Water Supply设备名称Equipment Name取水深井泵房Intake Structure高位水池Elevated Tank阀门井Valve Well生产、消防水泵房Water Supply Pump Room加药设备用房Dosage Room加药间Dosage Room预沉池Pre-sedimentation Tank穿孔旋流反应斜管沉淀池Reaction Sedimentation Tank 重力式无阀滤池Valveless Filter清水池Clear Water Pit循环水厂Circulating Water Station循环水泵房Recirculating Pump House药剂间Chemical Room循环冷水池Cooling Water Tank循环热水提升池Lifting Tank冷却塔Cooling Tower污水Sewage水泵棚Water Pump Shed污泥棚Sludge Shed风机棚Fan Shed化粪池Septic Tank污水处理综合用房Sewage Treatment House格栅池Bar Screen Tank曝气调节池Aeration Tank水解酸化池Acid hydrolysis Tank缺氧池Anoxia Tank好氧池Aerobic Tank生化池Biochemical Structure沉淀池Sedimentation Tank保险池Insurance Tank污泥浓缩池Concentration Tank检修污水池Overhaul Water Tank气浮池Floatation Tank隔油池Oil Separator事故水池Emergency Tank污泥焚烧系统Sludge Incineration SystemRO反渗透用房(Reverse Osmosis) RO House九、建筑设备名称Equipment Name工艺装置循环水泵房Recirculating Water Pump House污水处理综合用房Sewage Treatment House污泥脱水及鼓风机房Sludge dewatering and air blower room生产、消防给水泵房Water supply pump room空氮站及10/0.4 KV变电所Air and nitrogen station and 10/0.4KV Transformer substation锅炉房Boiler room锅炉房10/0.4 KV变电所Boiler room10/0.4KV Transformer substation35KV变电所35KV Transformer substation中央控制室Central control room车间办公室Workshop office分析化验室Lab钢瓶使用间Cylinder room门卫Security post硫磺成型机厂房Sulfur forming plant硫磺仓库Sulfur warehouse硫磺仓库辅助用房Sulfur warehouse auxiliary room综合楼Administration building10KV变电站10KV transformer substation硫磺成型10/0.4 KV变电站10/0.4KV transformer substation for sulfur forming unit消防应急站Fire fighting and response station库房、维修及配套用房Warehouse and maintenance room空压站棚Air compression station shed取水深井泵房Intake Structure倒班生活区Living Quarter十、供热设备名称Equipment Name低压锅炉Low-pressure boiler中压锅炉Medium-pressure boiler鼓风机Air-blower引风机Induced draft fan烟囱Stack烟道Flue燃烧机Burner过热器出口集箱Export header of superheated过热器入口集箱Import header of superheated省煤器出口集箱Export header of Economizer省煤器进口集箱Import header of Economizer省煤器中间集箱Middle header of Economizer混合集箱Mixing Header低压给水泵Low-pressure water supply pump中压给水泵Medium-pressure water supply pump上锅筒Steam drum下锅筒Drum加药Chemical Dosing排污Blowdown闪蒸汽Flash vapor除氧器Deaerator除盐水泵Demineralization water pump除盐水罐Demineralization water container空气储罐Air tank清洗水泵Cleaning pump布袋过滤器Cloth envelop collector板式换热器Plate heat exchanger超滤水罐Ultra-filtration container清洗装置Cleaning device凝结水罐Condensation container除氧水泵Deaerating water pump开工锅炉给水泵Water supply pump of start-up boiler水水换热器Water-water heat exchanger一级高压泵Primary high pressure pump一级反渗透装置Primary the reverse osmosis (RO) equipment保安过滤器Nanofiltration减温器Resuperheater连续排污扩容器Continuous Blowdown Flash Tanks定期排污扩容器Regularity Blowdown Flash Tanks排污泵Blowdown Pump加药装置Chemical adding unit整流器Rectifier加盐计量泵Chemical adding metering pump浓水循环泵Thick water circulation pump清洗水箱Cleaning water container清洗过滤器Cleaned Filter综合用房:general house综合楼:administration building倒班宿舍:living quarters中国石油天然气股份有限公司西南油气田分公司: PetroChina Southwest Oil & Gasfield Company循环水系统:cooling water system自动控制:Instrumentation土木工程:Civil structure建筑:Architecture总图:Plot plan岩土工程勘察geotechnical investigation工程地质测绘engineering geological mapping岩土工程勘探geotechnical exploration原位测试in-situ tests岩土工程勘察报告geotechnical investigation report现场检验in-situ inspection现场监测in-situ monitoring岩石质量指标(RQD) rock quality designation土试样质量等级quality classification of soil samples不良地质作用adverse geologic actions地质灾害geological disaster地面沉降ground subsidence,land subsidence岩土参数标准值standard value of a geotechnical parameter废水/污水:Waste Water回注污水:Reinjection waste water气田水:Gas Field Water气田水、处理厂回注污水泄露风险及防范措施:Leakage Risks of Gas Field Water and Reinjection Waste Water in the Tre atment Plant and CountermeasuresDear Sir 翻译成“尊敬的先生”描述”-- “DESCRIPTION”“版次”--“REVISION”“应/应该”--“SHALL”“宜”--“SHOULD”“脱硫”--“SULFUR REMOVAL”“推荐/建议”--“PREFER”“审核”--“ENG APPR”“审定”--“CHIEF APPR”“内部集输工程”--“INTERNAL GATHERING SYSTEM”“说明书”改成“REPORT”.“勘察设计校审卡”统一成“quality tracing card"节流器:throttle节流嘴:throttling nozzle截止阀:Globe valve截断阀:Block valve止回阀:Check valve节流截止放空阀:Throttling, check and vent valve针阀节流压降: Needle valve throttling pressure drop双作用节流截止阀: double acting throttling and check valveXxxx室:Xxxx Section如:“油气加工室”翻译译成“PROC Section 或者PR Section”闭排灌closed drain drum自备式电站captive power station。
湿法烟气脱硫系统中英文词汇对照表
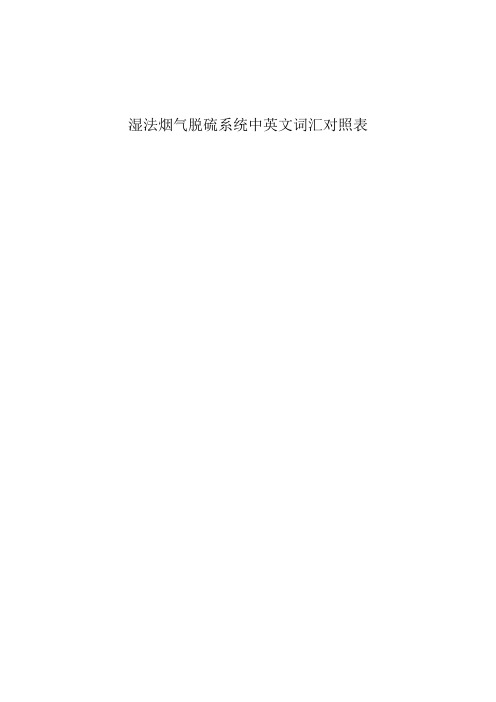
湿法烟气脱硫系统中英文词汇对照表ABSORBER 吸收塔ABSORBER AREA TRENCHES 吸收塔区排水沟ABSORBER BLEED PUMP 吸收塔排放泵(对一级脱水系统也可称为:分离器给料泵)ABSORBER ISLAND 吸收塔岛(吸收塔子系统)ABSORBER ISOLATION DAMPER 吸收塔隔离挡板ABSORBER OUTLET ISOLATION DAMPER 吸收塔出口隔离挡板ABSORBER REACTION TANK 吸收塔反应池ABSORBER RECYCLE PUMP 吸收塔再循环泵ABSORBER SHELL 吸收塔壳体ABSORPTION ZONE 吸收区ADDITIVE PUMP 添加泵ADDITIVE STORAGE TANK 添加贮罐AGITATOR 搅拌器AIR COOLED HEAT EXCHANGER 空冷式换热器AIR DRYER 空气干燥器ASH PIT 灰坑、灰池AUXILIARY STORAGE RETURN PUMP 事故浆液返回泵(备用贮存抽空泵)AUXILIARY STORAGE TANK 事故浆液储罐(备用贮罐)BACKWASH TANK 反冲洗罐BALL MILL BEARING LUBE SYSTEM 球磨机轴承润滑系统BALL MILL CLUTCH AIR RECEIVER 球磨机离合器空气接收器BALL MILL GEAR LUBE DRUM 球磨机传动装置润滑油桶BELT FILTER 皮带过滤机BOD 生物耗氧量BOOSTER FAN 升压风机BRACER 拉条、支撑条BRINE CONCENTRATOR 盐浓缩器BUCKET ELEVATOR 斗式提升机BY-PASS DAMPER 旁路挡板CAKE WASH PUMP 石膏饼冲洗泵CHEVRON VANE V形叶片CLARFIER 澄清器CLASSIFIER FEED PUMP 分离器给料泵COALESCING PREFILTER 凝聚预过滤器COD 化学耗氧量CONDENSATE PUMP 冷凝液泵(凝结水泵)CONDENSATE TANK 冷凝液罐(凝结水罐)CONTINUOUS EMISSIONS MONITORING SYSTEM 连续排放检测系统CONTROL MANIFOLD 控制总管CRUSHER 破碎机DAY BIN FEED CONVEYER 日储仓给料输送机DEWATERING AREA SUMP 脱水区排水坑DEWATERING AREA SUMP PUMP 脱水区排水坑泵DEWATERING AREA TRENCHES 脱水区排水沟DISCHARGE BLOWER 排放风机DUCTWORK 烟道DUST COLLECTOR FAN 除尘器风机EFFLUENT TRANSFER PUMP 污水输送泵ELECTRIC SIGNAL LINES 电信号管线ELECTROMAGNETIC SONIC SIGNAL ORLIGHT BEAM 电磁超声信号或光束EMBEDDED RING 预埋环EMERGENCY QUENCH SYSTEM 事故烟气冷却系统(急冷系统)ESP 静电除尘器EXPANSION JOINT 膨胀节FGD BLEED PUMP 烟气脱硫排放泵FGD BLEED TANK 烟气脱硫排放罐FILTRATE PUMP 滤液泵FILTRATE RECEIVER 滤液接收器FILTRATE RETURN PUMP 滤液返回泵FIRE WATER SYSTEM 消防水系统FLYASH STABILIZER FEED SYSTEM 飞灰稳定器给料系统FRP 玻璃钢GAS PATH SYSTEM 烟道系统GAS SAMPLING LINES 烟气取样管线GAS TO GAS HEAT EXCHANGER(GGH) 烟气换热器GRAVITY SAND FILTER 重力式沙砾过滤器GUILLOTINE DAMPER 闸板式挡板GYPSUM DEWATERING ISLAND 石膏脱水岛(石膏脱水子系统)GYPSUM STORAGE BUNKER 石膏储仓GYPSUM STORAGE SILO 石膏储仓HORIZONTAL VACUUM BELT FILTER 水平真空皮带过滤机HYDRAULIC SIGNAL 液压信号HYDROCYCLONE CLASSIFIER 水力旋流分离器I.D.FAN 引风机INLET DUCT 进口烟道INSTRUMENT IMPULSE LINES AND AUXILIARYPROCESS SUPPORT LINES 仪表脉冲和辅助工艺支撑管线INSTRUMENT PNEUMATIC SIGNAL LINES 仪表气动信号管线INTAKE FILTER-SILENCER 入口过滤器消音器INTERCEPTOR AFTERFILTER 过滤机后阻截器INTERNAL SYSTEM LINKS 内部系统连接L/G 液气比LEVEL CONTROL 液位控制LIMESTONE BALL MILL LUBE OIL RESERVOIR 石灰石球磨机润滑油罐LIMESTONE DAY BIN 石灰石日储仓LIMESTONE HOPPER 石灰石料斗LIMESTONE MIXING PUMP 石灰石混合泵LIMESTONE MIXING TANK 石灰石混合罐LIMESTONE PILE 石灰石料堆LIMESTONE POWDER SILO 石灰石粉料仓LINE SYMBOL IDENTFICATION 管线符号说明LOCAL CONTROL PANEL 就地控制盘LRT 液体停留时间MAJOR PROCESS LINES 主要工艺管线MAKE-UP WATER ISLAND 补给水岛(补给水子系统)MAKE-UP WATER TANK 补给水箱MAKE-UP(M.U.) WATER PUMP 补给水泵MASS BALANCE(MB) 物料平衡MILL PRODUCT CLASSIFIER 磨成品分离器MILL PRODUCT DISTRIBUTOR 磨成品分配器MILL RECYCLE PUMP 磨机再循环泵MILL RECYCLE TANK 磨机再循环罐MILL WEIGH FEEDER 球磨机称重给料机MINOR PROCESS LINES 次要工艺管线MIST ELIMINATION ZONE 除雾区MIST ELIMINATOR WASH PUMP 除雾器冲洗泵MIST ELIMINATOR(ME) 除雾器MOTOR STATOR WINDING 电动机定子绕组OPPOSED BLADE LOUVER DAMPER 反向叶片百叶窗式挡板OUTLET CONE 出口锥段OXIDATION AGITETOR 氧化搅拌器OXIDATION AIR BLOWER 氧化风机OXIDATION LANCE 氧化风枪PARALLEL BLADE LOUBER DAMPER 平行叶片百叶窗式挡板PEP 性能加强环PISTON OR DIAPHRAGM PUMP 活塞泵或隔膜泵POLYMER FEED SYSTEM 聚合物给料系统POTABLE WATER SYSTEM 饮用水系统PRIMARY DEWATERING HYDROCYCLONE 一次脱水水力旋流分离器PROCESS AND INSTRUMENTATION DIAGRAM 工艺和仪表图PUGMILL 搅拌机PUMP GEARBOX 泵变速箱REAGENT FEED PUMP 吸收剂给料泵REAGENT FEED TANK 吸收剂给料罐REAGENT HANDLING AREA SUMP 吸收剂处理区排水坑REAGENT HANDLING AREA SUMP PUMP 吸收剂处理区排水池泵REAGENT PREPARATION AREA TRENCHES 吸收剂处理区排水沟REAGENT PREPARATION AREA SUMP 吸收剂处理区排水坑REAGENT RECLAIM CONVEYER 吸收剂回收输送机RECLAIM WATER PUMP 回收水泵RECLAIM WATER SYSTEM 回收水系统RECLAIM WATER TANK 回收水储罐RECYCLE PUMP 再循环泵RECYCLE SPRAY PUMP 再循环喷淋泵ROTARY VACUUM DRUM FILTER 旋转式真空筒过滤机SCRAPER 刮板器SCRUBBER 洗涤器SEAL AIR FAN 密封空气风机SEAL WATER SEPARATOR 密封水分离器SEAL WATER SYSTEM 密封水系统SEAL/VENT AIR LINES 密封/通风管线SECONDARY DEWATERING HYDROCYCLONE 二次脱水水力旋流分离器SERVICE AIR COMPRESSOR SYSTEM 供风压缩机系统SERVICE AIR RECEIVER 供风接收器SILENCER 消音器SINGLE LOUVER DAMPER(BUTTERFLY) 单百叶窗式挡板(蝶式)SLURRY PREPARATION ISLAND 浆液制备岛(浆液制备子系统)SLURRY VAT 浆液筒SPLITTER BOX 分流箱SPRAY BRANCH 喷淋支管SPRAY HEADER 喷淋集管SPRAY LEVEL 喷淋层SPRAY NOZZLE 喷嘴、喷淋嘴SPRAY ZONE 喷淋区SRT 固体停留时间STACK 烟囱STIFFENER 加强筋、加强板SULFURIC ACID PUMP 硫磺酸泵SULFURIC ACID TANK 硫磺酸罐SUMP PUMP 排水坑泵SUPPORT 支承TRANSFER CONVEYOR 输送装置TRANSITION CONE 过渡区TURNING VANE 导流叶片UNDERFLOW PUMP 底流泵VACUUM PUMP 真空泵VIBRATING BIN DISCHARGER 振动卸料装置WALL RING 性能加强环WASH GRIDS 冲洗管网WASH HEADER 冲洗集管WASH NOZZLE 冲洗管嘴WASHDOWN WATER SYSTEM 清洗水系统WATER COOLED HEAT EXCHANGER 水冷式换热器WET BALL MILL 湿式球磨机WFGD SYSTEM 湿法烟气脱硫系统。
脱硫系统中英文对照表
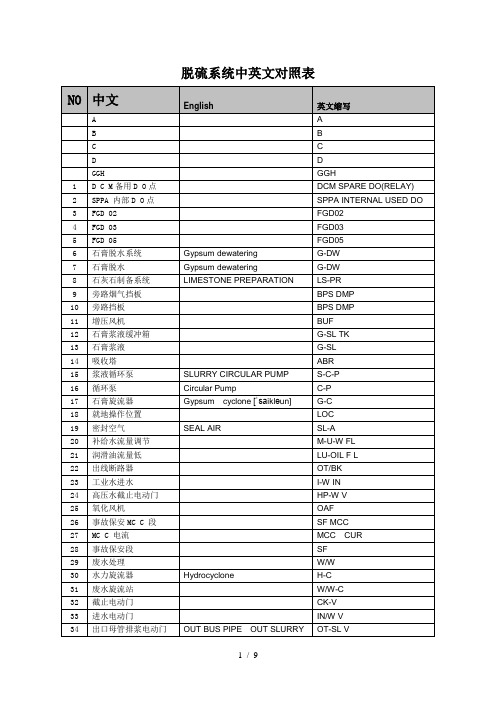
48
石灰石制备
LS-PR
49
排水坑
DRN PIT
50
自引罐
self priming
SEF
51
自引灌
self priming
SEF
52
搅拌器电机
AGR
53
低泄露风机电机
L-LK FAN
54
取样系统
SAMPLING SYSTEM
SM-S
55
事故浆液箱
EM SL TK
56
事故浆液
EM SL
57
氧化空气
180
传感器
transmitter
TSMR
181
油站
OIL ST
182
备用泵
STANDBY PUMP
S-PU
183
电加热器
HTR
184
加热器
HTR
185
超温报警
T-ALM
186
吹灰器
SO-BLWR
187
推进状态
ENGED
188
退出状态
EXTACED
189
推进指令
ENGE
190
退出指令
EXTAC
191
S-C-P
16
循环泵
Circular Pump
C-P
17
石膏旋流器
Gypsum cyclone[ˈsaikləun]
G-C
18
就地操作位置
LOC
19
密封空气
SEAL AIR
SL-A
20
补给水流量调节
M-U-W FL
21
润滑油流量低
LU-OIL F L
高含硫气田工程专业术语中英文对照
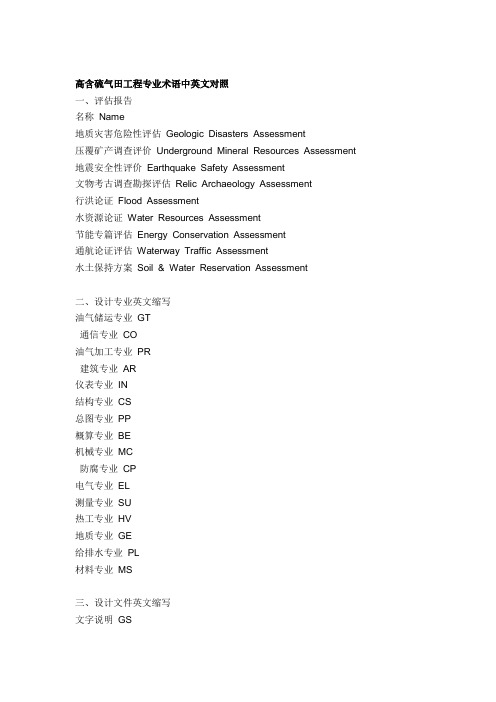
高含硫气田工程专业术语中英文对照一、评估报告名称Name地质灾害危险性评估Geologic Disasters Assessment压覆矿产调查评价Underground Mineral Resources Assessment 地震安全性评价Earthquake Safety Assessment文物考古调查勘探评估Relic Archaeology Assessment行洪论证Flood Assessment水资源论证Water Resources Assessment节能专篇评估Energy Conservation Assessment通航论证评估Waterway Traffic Assessment水土保持方案Soil & Water Reservation Assessment二、设计专业英文缩写油气储运专业GT通信专业CO油气加工专业PR建筑专业AR仪表专业IN结构专业CS总图专业PP概算专业BE机械专业MC防腐专业CP电气专业EL测量专业SU热工专业HV地质专业GE给排水专业PL材料专业MS三、设计文件英文缩写文字说明GS仪表计算数据表IC图纸(各专业图纸) DR设备技术规格书SP设备表EL设备数据表DS材料表ML其它表格OT工艺管线说明表PD四.油气储运专业设备名称Equipment Name井场Well Pad集气站Gathering Station阀室Valve Station集气干线Gas Gathering Trunk Line采气管线Gas Gathering Flow Line燃料气干线Fuel Gas Trunk Line燃料气支线Fuel Gas Branch水套加热炉Jacket Heater清管器发送装置Pig Launcher清管器接收装置Pig Receiver分离器Separator过滤分离器Filter Separator缓蚀剂储罐Inhibitor Tank防冻剂储罐Antifreeze Tank火炬Flare测试分离器Test Separator五、油气加工专业1、脱硫装置SULFUR REMOVAL UNIT 设备名称Equipment Name脱硫吸收塔Main Absorber闪蒸气吸收塔Flash Gas Absorber再生塔Regenerator原料气分离器Feed Gas Separator湿净化气分离器Treated Gas K.O. Drum闪蒸罐Flash Drum回流罐Reflux Drum胺液排放罐Amine Drain Drum贫富胺液换热器Lean/rich Exchanger贫胺液冷却器Lean Solvent Cooler贫胺液后冷却器Lean Solvent Trim Cooler重沸器Reboiler塔顶冷凝器Overhead Condenser塔顶后冷器Overhead Trim Cooler原料气过滤分离器Filter Separator胺液机械过滤器Amine Filter活性炭过滤器Activated Carbon Filter胺液后过滤器Amine trim filter/Carbon Particle Filter 排放溶液过滤器Drained Solvent Filter低压贫胺液泵LP Lean Solvent Pump高压贫胺液泵HP Lean Solvent Pump回流泵Reflux Pump新鲜溶液泵Fresh Solvent Pump排放溶液泵Drained Solvent Pump富胺液能量回收透平Fat Solvent Expander溶液补充罐Solvent Make-up Tank2、脱水装置DEHYDRATION UNIT设备名称Equipment NameTEG吸收塔TEG AbsorberTEG重沸器TEG ReboilerTEG缓冲罐TEG buffer Drum套管换热器Sleeve ExchangerTEG贫/富液换热器Lean/Rich TEG Exchanger产品气分离器Product Gas K.O. DrumTEG预过滤器TEG FilterTEG活性炭过滤器Activated Carbon FilterTEG后过滤器TEG Trim FilterTEG闪蒸罐Flash Drum再生气分液罐Regenerate gas K.O. DrumTEG储罐TEG tank氮气水封罐Water Sealed DrumTEG补充罐TEG Make-up Tank凝结水闪蒸罐Condensate K.O. Drum燃料气罐Fuel Gas K.O. Drum净化空气罐Instrument Air DrumTEG补充泵TEG Make-up PumpTEG回收泵TEG Recovery Pump蒸汽喷射泵Steam Eject pumpTEG循环泵Lean TEG Pump3、硫磺回收装置SULFUR RECOVERY UNIT设备名称Equipment Name酸气分离器Acid Gas K.O. Drum液硫封Sulfur Locks排污罐Blowdown Drum蒸汽冷凝水闪蒸罐Condensate Flash Drum余热锅炉Waste Heat Boiler一级硫磺冷凝冷却器First Sulfur Condenser二级硫磺冷凝冷却器Second Sulfur Condenser三级硫磺冷凝冷却器Third Sulfur Condenser一级再热器First Reheater二级再热器Second Reheater硫磺冷却器Sulfur Cooler锅炉给水预热器BFW Preheater液硫池蒸汽加热盘管Sulfur Pit Steam Coil主燃烧器Main Burner燃烧室Combustion Chamber主风机(蒸汽透平驱动)Main Air Blower (Turbine driven) 主风机(电机驱动)Main Air Blower (Motor driven)酸水泵Acid Gas Condensate Pump液硫泵Sulfur Pump液硫池Sulfur Pit一级反应器First Reactor二级反应器Second Reactor鼓泡器Bubble Columns蒸汽喷射器(带夹套) Steam Ejector催化剂Catalyst瓷球Ceramic Balls4、尾气处理装置TAIL GAS TREATMENT UNIT设备名称Equipment Name急冷塔Quench ColumnSCOT吸收塔SCOT Absorber酸水汽提塔Sour Water Stripper凝结水排污罐SCOT Blowdown Drum蒸汽分水器Steam/water Separator闪蒸气缓冲罐Flash Gas Buffer Drum燃料气分离器Fuel Gas K.O. Drum酸水收集罐Sour Water Collection Drum酸水汽提塔回流罐SWS Reflux Drum气体冷却器Gas Cooler急冷水冷却器Quench Water Cooler急冷塔后冷器Quench Water Trim Cooler焚烧炉余热锅炉Incinerator Waste Heat Boiler蒸汽过热器Steam Superheater酸水汽提塔热交换器SWS Heat Exchanger酸水汽提塔重沸器SWS Reboiler酸水汽提塔顶冷凝器SWS Overhead Condenser汽提水冷却器Stripped Water Cooler汽提水后冷器Stripped Water Trim Cooler急冷水过滤器Quench Water FilterSCOT燃烧器SCOT BurnerSCOT混合室SCOT Mixing Chamber焚烧炉燃烧器Incinerator Burner焚烧炉混合室Incinerator Mixing Chamber灼烧炉风机(蒸汽透平驱动)Incinerator Air Blower (Turbine driven) 灼烧炉风机(电机驱动)Incinerator Air Blower (Motor driven)急冷水泵Quench Water Pump半贫液泵(电机驱动)Semi-lean Solvent Pump (Motor Driven)半贫液泵(蒸汽透平驱动)Semi-lean Solvent Pump(Turbine Driven) 酸水汽提塔进料泵SWS Feed Pump酸水汽提塔底泵Stripped Water Pump酸水汽提塔回流泵SWS Reflux PumpSCOT反应器SCOT Reactor蒸汽喷射器SCOT Ejector烟囱StackSCOT催化剂SCOT Catalyst5、硫磺成型装置SULFUR FORMING UNIT设备名称Equipment Name液硫储罐Liquid sulfur tank净化空气罐Instrument air tank蒸汽分水器Steam water separator液硫泵Liquid sulfur pump液硫过滤系统Sulfur filter system自动称量包装码垛系统Automatic weighing, packing and stacking product line 硫磺仓库Sulfur warehouse硫磺成型机Sulfur granulator6、火炬及放空系统FLARE SYSTEM设备名称Equipment Name天然气放空火炬Nature gas flare酸气放空火炬Sour gas flare天然气放空分离器Nature gas vent separator凝液回收罐Condensate Collection Tank凝液泵Condensate pump火炬头Flare head分子封Gas seal火炬筒体Flare stack 7、空氮站AIR AND NITROGEN STATION设备名称Equipment Name空气压缩机Air compressor空气干燥器Air Drier制氮橇块Nitrogen Skid精密过滤器Nicety filter净化空气罐Instrument Air Drum非净化空气罐Plant Air Drum氮气罐Nitrogen Drumk六、仪表及自动控制通用描述COMMON DESCRIPTION设备名称Equipment Name 缩写ABB.分散控制系统Distributed Control System DCS安全仪表系统Safety Instrumentation System SIS紧急切断系统Emergency Shutdown system ESD火气系统Fire and Gas system F&G监视控制和数据采集系统Supervisory Control and Data Acquisition SCADA 可编程逻辑控制器Programmed Logic Controller PLC远程终端单元Remote Terminal Unit RTU站控系统Station Control System SCS中央控制室Central Control Room CCR操作间Operation room机柜间Equipment room/ Cabinet room大屏显示系统Large Screen Display system LSD流量类仪表FLOW INSTRUMENT设备名称Equipment Name孔板Orifice Plate文丘里流量计Venturi Flowmeter均速管流量计Averaging Pitot Tube阀式孔板节流装置Orifice Plate in quick change fitting涡轮流量计Turbine Flowmeter涡街流量计Vortex Flowmeter容积式流量计Positive Displacement Flowmeter靶式流量计Target Flowmeter超声波流量计Ultrasonic FlowmeterV型流量计V-cone Flowmeter电磁流量计Electromagnetic Flowmeter楔型流量计Wedge Flowmeter转子流量计Rotameter整流器Straightening Vane温度类仪表TEMPERATURE INSTRUMENT双金属温度计Bi-metallic temperature gauge热电偶Thermocouple表面热电偶Surface Thermocouple热电阻Resistance Temperature Detector温度变送器Temperature transmitter光学高温计Optical pyrometer温度计套管Thermowell压力类仪表PRESSURE INSTRUMENT设备名称Equipment Name压力表Manometer /Pressure gauge弹簧管压力表Burdon-tube manometer隔膜压力表Diaphragm-seal manometer /Diaphragm-seal pressure gauge 差压表Differential pressure gauge压力变送器Pressure transmitter差压变送器Differential pressure transmitter液位类仪表LEVEL INSTRUMENT设备名称Equipment Name玻板液位计Glass type level gauge磁浮子液位计Magnetic coupled indicator雷达液位变送器Radar level transmitter浮筒液位变送器Displacer level transmitter磁致伸缩液位变送器Magnetostrictive level transmitter液位开关Level switch阀门类VALVE设备名称Equipment Name球阀Ball valve单座阀Globe valve套筒阀Sleeve valve蝶阀Butterfly valve偏心旋转阀Eccentric rotary valve截止阀Globe valve角阀Angle valve电磁阀Solenoid valve六、通信设备名称Equipment Name程控电话交换系统PABX System局域网及综合布线系统LAN & Generic Cabling System防爆扩音/对讲系统Explosion-Proof Loud Speaking/Talk Back System 工业电视监视系统CCTV System电力调度系统Power Line Carrier System周界防范系统Boundary Security System光通信系统Optical Fiber communication system有线电视系统CATV System七、供配电设备名称Equipment Name变电所Substation高低压配电装置HV&LV Switchgear柴油发电机Diesel Generator油浸式变压器Oil-immersed Power Transformer干式变压器Dry-type Power Transformer有载调压开关On-load Tap Switch直流屏DC UPS微机综合自动化系统Integrated Substation Automation System应急电源Emergency Power Supply配电箱Lighting and Small Power Distribution Panel电缆桥架Cable Tray电缆沟Cable Trough架空电力线路Over-head Lines爆炸危险区域划分Hazardous Area Classification单线图Single Line Diagram电容补偿Capacitor Unit现场操作柱Local Control Station供配电系统Power Supply & Distribution SystemUPS:AC UPS八、给排水给水Water Supply设备名称Equipment Name取水深井泵房Intake Structure高位水池Elevated Tank阀门井Valve Well生产、消防水泵房Water Supply Pump Room加药设备用房Dosage Room加药间Dosage Room预沉池Pre-sedimentation Tank穿孔旋流反应斜管沉淀池Reaction Sedimentation Tank 重力式无阀滤池Valveless Filter清水池Clear Water Pit循环水厂Circulating Water Station循环水泵房Recirculating Pump House药剂间Chemical Room循环冷水池Cooling Water Tank循环热水提升池Lifting Tank冷却塔Cooling Tower污水Sewage水泵棚Water Pump Shed污泥棚Sludge Shed风机棚Fan Shed化粪池Septic Tank污水处理综合用房Sewage Treatment House格栅池Bar Screen Tank曝气调节池Aeration Tank水解酸化池Acid hydrolysis Tank缺氧池Anoxia Tank好氧池Aerobic Tank生化池Biochemical Structure沉淀池Sedimentation Tank保险池Insurance Tank污泥浓缩池Concentration Tank检修污水池Overhaul Water Tank气浮池Floatation Tank隔油池Oil Separator事故水池Emergency Tank污泥焚烧系统Sludge Incineration SystemRO反渗透用房(Reverse Osmosis) RO House九、建筑设备名称Equipment Name工艺装置循环水泵房Recirculating Water Pump House污水处理综合用房Sewage Treatment House污泥脱水及鼓风机房Sludge dewatering and air blower room生产、消防给水泵房Water supply pump room空氮站及10/0.4 KV变电所Air and nitrogen station and 10/0.4KV Transformer substation锅炉房Boiler room锅炉房10/0.4 KV变电所Boiler room10/0.4KV Transformer substation35KV变电所35KV Transformer substation中央控制室Central control room车间办公室Workshop office分析化验室Lab钢瓶使用间Cylinder room门卫Security post硫磺成型机厂房Sulfur forming plant硫磺仓库Sulfur warehouse硫磺仓库辅助用房Sulfur warehouse auxiliary room综合楼Administration building10KV变电站10KV transformer substation硫磺成型10/0.4 KV变电站10/0.4KV transformer substation for sulfur forming unit消防应急站Fire fighting and response station库房、维修及配套用房Warehouse and maintenance room空压站棚Air compression station shed取水深井泵房Intake Structure倒班生活区Living Quarter十、供热设备名称Equipment Name低压锅炉Low-pressure boiler中压锅炉Medium-pressure boiler鼓风机Air-blower引风机Induced draft fan烟囱Stack烟道Flue燃烧机Burner过热器出口集箱Export header of superheated过热器入口集箱Import header of superheated省煤器出口集箱Export header of Economizer省煤器进口集箱Import header of Economizer省煤器中间集箱Middle header of Economizer混合集箱Mixing Header低压给水泵Low-pressure water supply pump中压给水泵Medium-pressure water supply pump上锅筒Steam drum下锅筒Drum加药Chemical Dosing排污Blowdown闪蒸汽Flash vapor除氧器Deaerator除盐水泵Demineralization water pump除盐水罐Demineralization water container空气储罐Air tank清洗水泵Cleaning pump布袋过滤器Cloth envelop collector板式换热器Plate heat exchanger超滤水罐Ultra-filtration container清洗装置Cleaning device凝结水罐Condensation container除氧水泵Deaerating water pump开工锅炉给水泵Water supply pump of start-up boiler水水换热器Water-water heat exchanger一级高压泵Primary high pressure pump一级反渗透装置Primary the reverse osmosis (RO) equipment保安过滤器Nanofiltration减温器Resuperheater连续排污扩容器Continuous Blowdown Flash Tanks定期排污扩容器Regularity Blowdown Flash Tanks排污泵Blowdown Pump加药装置Chemical adding unit整流器Rectifier加盐计量泵Chemical adding metering pump浓水循环泵Thick water circulation pump清洗水箱Cleaning water container清洗过滤器Cleaned Filter综合用房:general house综合楼:administration building倒班宿舍:living quarters中国石油天然气股份有限公司西南油气田分公司: PetroChina Southwest Oil & Gasfield Company循环水系统:cooling water system自动控制:Instrumentation土木工程:Civil structure建筑:Architecture总图:Plot plan岩土工程勘察geotechnical investigation工程地质测绘engineering geological mapping岩土工程勘探geotechnical exploration原位测试in-situ tests岩土工程勘察报告geotechnical investigation report现场检验in-situ inspection现场监测in-situ monitoring岩石质量指标(RQD) rock quality designation土试样质量等级quality classification of soil samples不良地质作用adverse geologic actions地质灾害geological disaster地面沉降ground subsidence,land subsidence岩土参数标准值standard value of a geotechnical parameter废水/污水:Waste Water回注污水:Reinjection waste water气田水:Gas Field Water气田水、处理厂回注污水泄露风险及防范措施:Leakage Risks of Gas Field Water and Reinjection Waste Water in the Tre atment Plant and CountermeasuresDear Sir 翻译成“尊敬的先生”描述”-- “DESCRIPTION”“版次”--“REVISION”“应/应该”--“SHALL”“宜”--“SHOULD”“脱硫”--“SULFUR REMOVAL”“推荐/建议”--“PREFER”“审核”--“ENG APPR”“审定”--“CHIEF APPR”“内部集输工程”--“INTERNAL GATHERING SYSTEM”“说明书”改成“REPORT”.“勘察设计校审卡”统一成“quality tracing card"节流器:throttle节流嘴:throttling nozzle截止阀:Globe valve截断阀:Block valve止回阀:Check valve节流截止放空阀:Throttling, check and vent valve针阀节流压降: Needle valve throttling pressure drop双作用节流截止阀: double acting throttling and check valveXxxx室:Xxxx Section如:“油气加工室”翻译译成“PROC Section 或者PR Section”闭排灌closed drain drum自备式电站captive power station。
湿法烟气脱硫技术英语
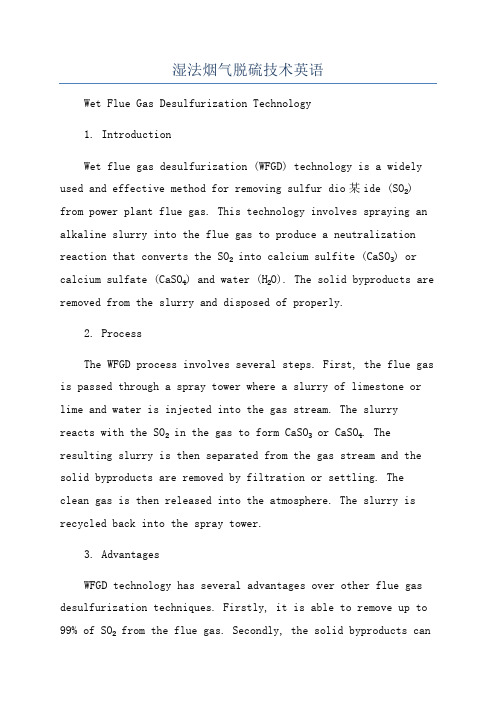
湿法烟气脱硫技术英语Wet Flue Gas Desulfurization Technology1. IntroductionWet flue gas desulfurization (WFGD) technology is a widely used and effective method for removing sulfur dio某ide (SO₂) from power plant flue gas. This technology involves spraying an alkaline slurry into the flue gas to produce a neutralization reaction that converts the SO₂ into calcium sulfite (CaSO₃) or calcium sulfate (CaSO₄) and water (H₂O). The solid byproducts are removed from the slurry and disposed of properly.2. ProcessThe WFGD process involves several steps. First, the flue gas is passed through a spray tower where a slurry of limestone or lime and water is injected into the gas stream. The slurry reacts with the SO₂ in the gas to form CaSO₃ or CaSO₄. The resulting slurry is then separated from the gas stream and the solid byproducts are removed by filtration or settling. The clean gas is then released into the atmosphere. The slurry is recycled back into the spray tower.3. AdvantagesWFGD technology has several advantages over other flue gas desulfurization techniques. Firstly, it is able to remove up to 99% of SO₂ from the flue gas. Secondly, the solid byproducts canbe easily removed from the slurry and properly disposed of, unlike other methods that produce hazardous waste. Furthermore, the process is fle某ible and can be easily adjusted todifferent operating conditions and fuel types.4. DisadvantagesHowever, the WFGD process also has some limitations. The technology is e某pensive to install and maintain, requiring large amounts of water and energy. Additionally, the process generates large amounts of sludge that must be disposed of properly, which can be costly. Finally, the process can generate secondary pollutants such as carbon dio某ide (CO₂) and nitrogen o某ides (NO某) due to the increased energy consumptionrequired to operate the system.5. ConclusionDespite these limitations, wet flue gas desulfurization technology remains a popular method for removing SO₂ from power plant flue gas. Its ability to remove up to 99% of SO₂ and the ease of disposing of solid byproducts make it an attractive option for power plant operators. However, its high cost and potential for generating secondary pollutants must be carefully considered before implementing this technology.。
脱硫英汉翻译
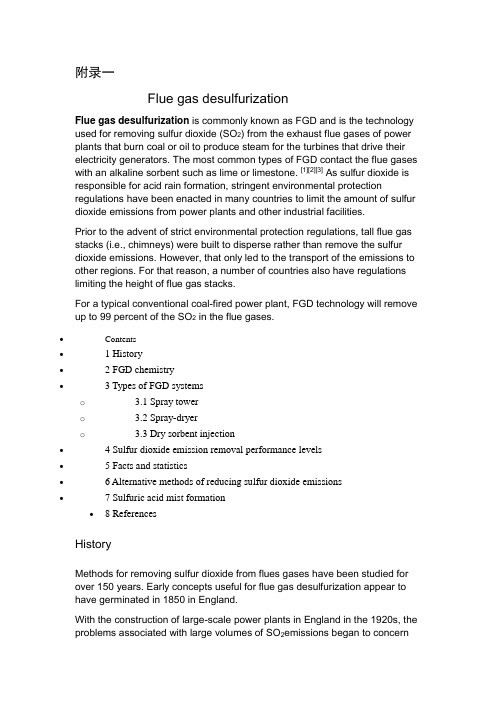
附录一Flue gas desulfurizationFlue gas desulfurization is commonly known as FGD and is the technology used for removing sulfur dioxide (SO2) from the exhaust flue gases of power plants that burn coal or oil to produce steam for the turbines that drive their electricity generators. The most common types of FGD contact the flue gases with an alkaline sorbent such as lime or limestone. [1][2][3] As sulfur dioxide is responsible for acid rain formation, stringent environmental protectionregulations have been enacted in many countries to limit the amount of sulfur dioxide emissions from power plants and other industrial facilities.Prior to the advent of strict environmental protection regulations, tall flue gas stacks (i.e., chimneys) were built to disperse rather than remove the sulfur dioxide emissions. However, that only led to the transport of the emissions to other regions. For that reason, a number of countries also have regulations limiting the height of flue gas stacks.For a typical conventional coal-fired power plant, FGD technology will remove up to 99 percent of the SO2 in the flue gases.∙Contents∙ 1 History∙ 2 FGD chemistry∙ 3 Types of FGD systemso 3.1 Spray towero 3.2 Spray-dryero 3.3 Dry sorbent injection∙ 4 Sulfur dioxide emission removal performance levels∙ 5 Facts and statistics∙ 6 Alternative methods of reducing sulfur dioxide emissions∙7 Sulfuric acid mist formation∙8 ReferencesHistoryMethods for removing sulfur dioxide from flues gases have been studied for over 150 years. Early concepts useful for flue gas desulfurization appear to have germinated in 1850 in England.With the construction of large-scale power plants in England in the 1920s, the problems associated with large volumes of SO2emissions began to concernthe public. The problem did not receive much attention until 1929, when the British government upheld the claim of a landowner against the Barton Electricity Works for damages to his land resulting from SO2 emissions. Shortly thereafter a press campaign was launched against the erection of power plants within the confines of London. This led to the imposition of SO2 controls on all such power plants.[4]During this period, major FGD installations went into operation in England at three power plants. The first one began operation at the Battersea Station in London in 1931. In 1935, the second one went into service at the Swansea Power Station. The third one was installed in 1938 at the Fulham Power Station. All three installations were abandoned duringWorld War II.Large-scale FGD units did not reappear in commercial operation until the 1970s, and most of the activity occurred in the United States and Japan.[4] As of June 1973, there were 42 FGD units, ranging in size from 5 to250 megawatts, in operation: 36 in Japan and 6 in the United States.[5]As of about 1999-2000, there were 678 FGD units operating worldwide (in 27 countries) producing a total of about 229 gigawatts. About 45% of that FGD capacity was in the United States, 24% in Germany, 11% in Japan and 20% in various other countries. Approximately 79% of the units, representing about 199 gigawatts of capacity, were using lime or limestone wet scrubbing. About 18% (or 25 gigawatts) utilized spray-dry scrubbers or dry sorbent injection systems.[6][7][8]FGD chemistrySO2 is an acid gas. Therefore, the most common large-scale FGD systems use an alkaline sorbent such as lime or limestone to neutralize and remove the SO2 from the flue gas. Since lime and limestone are not soluble in water, they are used either in the form of an aqueous slurry or in a dry, powdered form. When using an aqueous slurry of sorbent, the FGD system is referred to asa wet scrubber. When using a dry, powdered sorbent, the system is referred to as a dry system. An intermediate or semi-dry system is referred to asa spray-dry system.The reaction taking place in wet scrubbing using a CaCO3 (limestone) slurry produces CaSO3 (calcium sulfite) and can be expressed as:CaCO3 (solid) + SO2(gas) → CaSO3 (solid) + CO2 (gas)When wet scrubbing with a Ca(OH)2 (lime) slurry, the reaction alsoproduces CaSO3 (calcium sulfite) and can be expressed as:Ca(OH)2 (solid) + SO2(gas) → CaSO3 (solid) + H2O (liquid)When wet scrubbing with a Mg(OH)2 (magnesium hydroxide) slurry,the reaction produces MgSO3 (magnesium sulfite) and can beexpressed as:Mg(OH)2 (solid) + SO2(gas) → MgSO3 (solid) + H2O (liquid)Some FGD systems go a step further and oxidize theCaSO3 (calcium sulfite) to produce marketable CaSO4 · 2H2O(gypsum):CaSO3 (solid) + ½O2 (gas) + 2H2O (liquid) → CaSO4 · 2H2O (solid)Aqueous solutions of sodium hydroxide (known as causticsoda or simply caustic) may also be used to neutralize andremove SO2 from flue gases. However, caustic soda islimited to small-scale FGD systems, mostly in industrialfacilities other than power plants because it is moreexpensive than lime. It has the advantage that it forms asolution rather than a slurry and that makes it easier tooperate. It produces a solution of sodium sulfite or sodiumbisulfite (depending on the pH), or sodium sulfate that mustbe disposed of. This is not a problem in a paper mill forexample, where the solution can be recycled and reusedwithin the paper mill.Types of FGD systemsThe major types of large-scale, power plant FGD systemsinclude spray towers, spray dryers and dry sorbent injectionsystems.Spray towerThere are various types of wet scrubbers. For example, spraytowers, venturi scrubbers, packed towers and trayed towers. Slurries would cause serious erosion problems in a venturi scrubber because of the high speeds at the throat of the venturi section. Packed towers or trayed towers would plug up if handling slurries. For handling slurries, the spray tower is a good choice and it is in fact a commonly used choice in large-scale FGD systems.[3][9][10]Spray towers are used downstream of the particulate equipment (electrostatic precipitator or baghouse) where the flue gas contains very little, ifany, combustion fly ash. In a spray tower system, the sorbent slurry is simply injected via spray nozzles into a vertical tower where the slurry droplets are contacted with the upflowing flue gas.Part of the water in the slurry is evaporated by the hot flue gas and the flue gas becomes saturated with water vapor.The SO2 dissolves into the slurry droplets and reacts with the alkaline sorbent particles. The slurry falls to the bottom of the spray tower and is sent to a reaction tank where the reaction is completed and a neutral salt is formed. In a regenerable system, the residual slurry is recycled back for reuse in the spray tower. In a once-through system, the residual slurry is dewatered and either disposed of or oxidized to CaSO4 · 2H2O and sold as a by-product gypsum. Spray-dryerSpray-dryers are used upstream of the particulate removal equipment (electrical precipitator or baghouse) where the flue gas contains the combustion fly ash. In a spray-dryer system, the alkaline sorbent is usually lime slurry. The slurry is atomized and sprayed into a vessel as a cloud of fine bubbles where it contacts the hot flue gas. The water is completely evaporated by the hot gas and the residence time in the vessel (about 10 seconds) allows the SO2 and any other acid gases, such as SO3 and HCl, to react with the lime to form a dry powder of calcium sulfite, calcium sulfate and unreactedlime.[3][11][12]The dry powder is removed from the flue gas along with the combustion fly ash in the particulate removal equipment. Some of the solids from the particulate removal equipment (i.e., fly ash, calcium sulfite, calcium sulfate and unreacted lime) may be recycled and reused as part of the sorbent slurry.[12]Dry sorbent injectionThe dry FGD system simply injects powdered lime or limestone sorbent directly into the flue gas. As shown in the adjacent location diagram, the dry sorbent may be injected into any one of three locations: (1) the upper section of the steam generator, (2) the economizer section of the steam generator orthe ducting between the air preheater and the electrostaticprecipitator.[2][3][11][13]The powdered sorbent is pneumatically injected through lances designed to distribute the sorbent evenly across the flow path of the flue gas.When injected into the upper section of the steam generator, it should enter at a point where the temperature range is about 900 to 1200 °C. Injection into the economizer should be at a point where the temperature range is about 400 to 600 °C. Injection into the ducting between the preheater and the precipitator should be at point where the flue gas temperature is about 150 to 180 °C.[3][11] The SO2 reacts directly with the powdered sorbent and the spent sorbent is removed from the flue gas along with the combustion fly ash inthe particulate removal equipmentSulfur dioxide emission removal performance levelsPartial flue gas desulfurization (FGD) can achieve about 50-70 % removal of sulfur dioxide by the injection of dry limestone just downstream of the air preheater. The resultant solids are recovered in the electrostatic precipitators along with the fly ash.In power plants burning pulverized coal, wet flue gas desulfurization (FGD) that contacts the flue gases with lime slurries (in what are called wet lime scrubbers) can achieve 95% sulfur dioxide removal without additives and99+% removal with additives. Wet FGD has the greatest share of the FGD usage in the United States and it is commercially proven, well established technology.[14]The typical older FGD units in power plants burning pulverized coal within the United States achieve average sulfur dioxide emission levels of about 0.340 kg/MWh (0.22 lb SO2 /106Btu), which meets the level to which those units were permitted.The lowest demonstrated sulfur dioxide emission level (in 2005) for power plants burning pulverized high-sulfur coal within the United States was 1.08 kg/MWh (0.07 lb SO2 /106 Btu) and 0.046 kg/MWh (0.03 lb SO2 /106 Btu) for plants burning low-sulfur pulverized coal.[14]Facts and statisticsFlue gas desulfurization scrubbers have been applied to combustion units firing coal and oil that range in size from 5 MW to 1500 MW. ScottishPower are spending £400 million installing FGD at Longannet powerstation which has a capacity of over 2 GW. Dry scrubbers and sprayscrubbers have generally been applied to units smaller than 300 MW.Approximately 85% of the flue gas desulfurization units installed in the US are wet scrubbers, 12% are spray dry systems and 3% are dry injection systems.The highest SO2 removal efficiencies (greater than 95%) are achieved by wet scrubbers and the lowest (less than 80%) by dry scrubbers. However, the newer designs for dry scrubbers are capable of achieving efficiencies in the order of 90%.The capital, operating and maintenance costs per short ton ofSO2 removed (in 2001 US dollars) are:∙For wet scrubbers larger than 400 MW, the cost is $200 to $500 per ton∙For wet scrubbers smaller than 400 MW, the cost is $500 to $5,000 per ton∙For spray dry scrubbers larger than 200 MW, the cost is $150 to $300 per ton∙For spray dry scrubbers smaller than 200 MW, the cost is $500 to $4,000 per tonAlternative methods of reducing sulfur dioxide emissions An alternative to removing sulfur from the flue gases after burning is to remove the sulfur from the fuel before or duringcombustion. Hydrodesulfurization of fuel has been used for treating fuel oils.Fluidized bed combustion adds lime to the fuel during combustion. The lime reacts with the SO2 to form sulfates which become part of thecombustion ash.Sulfuric acid mist formationFossil fuels such as coal and oil contain significant amounts of sulfur.When burned, about 95 percent or more of the sulfur is generallyconverted to sulfur dioxide (SO2). This happens under normal conditions of temperature and of oxygen present in the flue gas. However, there are circumstances under which this may not be the case.For example, when the flue gas has too much oxygen and the SO2 isfurther oxidized to sulfur trioxide (SO3). Actually, too much oxygen is only one of the ways that SO3 is formed. Gas temperature is also an important factor. At about 800 °C, formation of SO3 is favored. Another way thatSO3 can be formed is through catalysis by trace metals in the fuel. This is particularly true for heavy fuel oil, where small amounts of vanadium are present. In whatever way that SO3 is formed, it does not behave likeSO2 in that it forms a liquid aerosolknown as sulfuric acid (H2SO4) mist that is very difficult to remove. Generally, about 1% of the sulfur dioxide will be converted to SO3. Since SO3 an acid gas, just as is SO2, it is also removed by the alkaline sorbents used in FGD systems.References1. ↑ Karl B. Schnelle and Charles A. Brown (2001). Air PollutionControl Technology>. CRC Press. ISBN 0-8493-9599-7.2. ↑2.02.1 SO2 Control Technologies (from website of the Institute ofClean Air Companies)3. ↑3.03.13.23.33.43.5 Air Pollution Control Technology Fact Sheet U.S.EPA publications EPA-452/F-03-0344. ↑4.04.1 Biondo, S.J. and Marten,J.C., A History of Flue GasDesulfurization Systems Since 1850, Journal of the Air PollutionControl Association, Vol. 27, No. 10, pp 948-961, October 1977.5. ↑ Beychok, Milton R., Coping With SO2, ChemicalEngineering/Deskbook Issue, October 21, 19746. ↑ Nolan, Paul S., Flue Gas Desulfurization Technologies forCoal-Fired Power Plants, The Babcock & Wilcox Company, U.S.,presented by Michael X. Jiang at the Coal-Tech 2000 InternationalConference, November, 2000, Jakarta, Indonesia7. ↑ Rubin, E.S., Yeh, S., Hounsell, D.A., and Taylor,M.R., Experience curves for power plant emission controltechnologies, Int. J. Energy Technology and Policy, Vol. 2, Nos. 1/2,20048. ↑ Beychok, Milton R., Comparative economics of advancedregenerable flue gas desulfurization processes, EPRI CS-1381,Electric Power Research Institute, March 19809. ↑ Wet FGD System Materials Cost Update, by M.G. Milobowski,Babcock & Wilcox (Presented at EPRI-DOE-EPA Combined UtilityAir Pollutant Control Symposium, August 1997)10. ↑ Air Pollution Control Technology Fact Sheet U.S.EPA publications EPA-452/F-03-01611. ↑11.011.111.2 IEA Clean Coal Center: Spray dry scrubbers forSO2 removal12. ↑12.012.1 Dry Flue Gas Desulfurization (FGD)Systems (FromBabcock and Wilcox website)13. ↑ Barbara Toole-O'Neil and Ohio Coal Development Office (Editors)(1998). Dry Scrubbing Technologies for Flue Gas Desulfurization.Springer. ISBN 0-7923-8346-X.14. ↑14.014.1 Dr. James Katzer et al and MIT Coal Energy StudyAdvisory Committee (2007).汉语翻译烟气脱硫烟气脱硫,就是泛指用烟气脱硫技术电厂燃烧煤、石油化工或其他工业废气中除去硫氧化物的技术。
脱硫专业英语
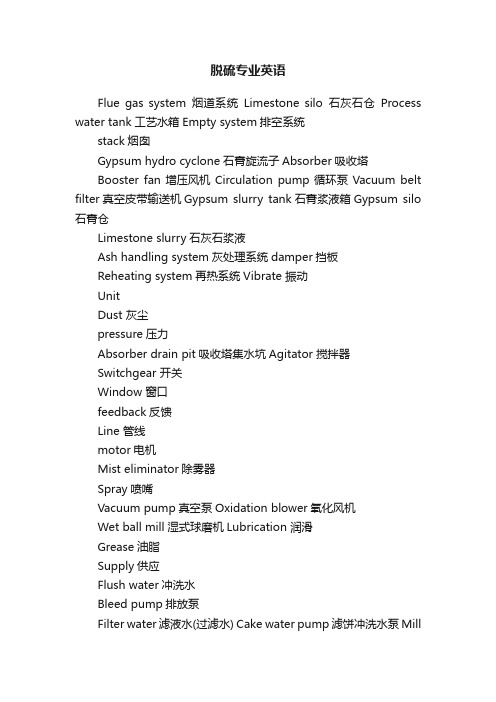
脱硫专业英语Flue gas system烟道系统Limestone silo石灰石仓Process water tank工艺水箱Empty system排空系统stack烟囱Gypsum hydro cyclone石膏旋流子Absorber吸收塔Booster fan增压风机Circulation pump循环泵Vacuum belt filter真空皮带输送机Gypsum slurry tank石膏浆液箱Gypsum silo 石膏仓Limestone slurry石灰石浆液Ash handling system灰处理系统damper挡板Reheating system再热系统Vibrate 振动UnitDust 灰尘pressure压力Absorber drain pit吸收塔集水坑Agitator 搅拌器Switchgear 开关Window 窗口feedback反馈Line 管线motor电机Mist eliminator除雾器Spray喷嘴Vacuum pump真空泵Oxidation blower氧化风机Wet ball mill湿式球磨机Lubrication 润滑Grease油脂Supply供应Flush water冲洗水Bleed pump排放泵Filter water滤液水(过滤水) Cake water pump滤饼冲洗水泵Millrecycle tank球磨机再循环箱Lmst slurry tank石灰石浆液箱Bucket elevator斗式提升机L EM storage basin事故浆液池Auxiliary system电气系统L DRNPT LMST PREPL制浆区域集水坑Actuating oil tank执行器油箱Hydraulic oil tank液压油箱Lubrication oil tank润滑油箱cooling air fan冷却风扇act oil heating执行器油加热器bear轴承fault故障Local/dcs就地/DCSStart warning启动报警density浓度feeder给料机Quiit/ackn确认Brake inching drive减速器Main drive主电机Filtrate separator滤液分离器cleaning冲洗level液位Seal gas fan密封烟气风机Hierarchy层次reset复位recirculation pump循环泵Inflow入口Outflow出口Clean gas净烟气Raw gas原烟气Vane-type separator细分离器Coarse separator 粗分离器Operator运行人员(操作员)inverting变频器screw螺旋conveyor输送机rubber橡胶Efficiency效率Flow rate流量current电流temperature温度blast blower 鼓风机AmpAn ampere.安培heater加热器, 发热器Limit Switch限位开关, 极限开关Flow Switch流量开关Seal air fanSeal 密封;隔离;堵塞Seal air fan 密封风机LPW Low pressure Water 低压水HPW Hige pressure Water 高压水Air Sequence空气吹扫清洗程序LPW Sequence低压水清洗程序HPW Sequence高压水清洗程序。
炼厂主要装置中英文

炼厂主要装置中英文及缩写
(*1)
有时,整个常减压蒸馏装置也被统称为Crude Distillation Unit(原油蒸馏单元)。
(*2)
几套加氢装置包括汽油、煤油、柴油有时会采用其它的简写形式,如DHF,因为加氢装置有加氢改质和加氢精制。
(*3)
制氢装置在炼厂中被称为了PSA,大家上次争论的PSA是制氢还是制氮问题,如果我没有记差,PSA是变压吸附的意思,是一种生产工艺,所以可能制氢、制氮都可以采用这种工艺。
炼厂自产氢气的装置实际上是CCR装置。
(*4)
炼厂中不一定包含上述所有的生产装置,取决于炼厂的原油性质及产品目标。
(*5)
装置的缩写,各家公司有自己的习惯,不是很统一。
个人感觉关键还是记住全名吧。
几种常见油品的英文
石脑油naphtha
汽油 gasoline
煤油 kerosene
柴油 diesel
瓦斯油/蜡油 gas oil
AGO 常压瓦斯油/常压蜡油
LVGO减压轻瓦斯油/减压轻蜡油
HVGO减压重瓦斯油/减压重蜡油
渣油 residue
AR 常压渣油
VR 减压渣油。
设备布置及管道布置中英文对照
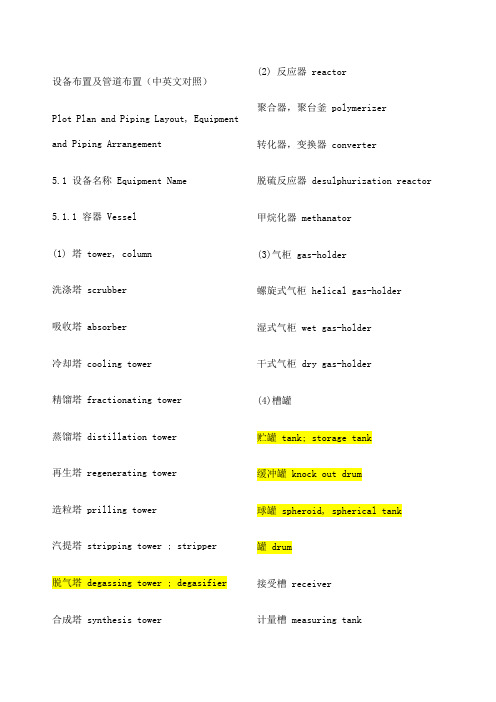
设备布置及管道布置(中英文对照)Plot Plan and Piping Layout, Equipment and Piping Arrangement5.1 设备名称 Equipment Name5.1.1 容器 Vessel(1) 塔 tower, column洗涤塔 scrubber吸收塔 absorber冷却塔 cooling tower精馏塔 fractionating tower蒸馏塔 distillation tower再生塔 regenerating tower造粒塔 prilling tower汽提塔 stripping tower ; stripper脱气塔 degassing tower ; degasifier合成塔 synthesis tower (2) 反应器 reactor聚合器,聚台釜 polymerizer转化器,变换器 converter脱硫反应器 desulphurization reactor 甲烷化器 methanator(3)气柜 gas-holder螺旋式气柜 helical gas-holder湿式气柜 wet gas-holder干式气柜 dry gas-holder(4)槽罐贮罐 tank; storage tank缓冲罐 knock out drum球罐 spheroid, spherical tank罐 drum接受槽 receiver计量槽 measuring tank加料槽 feed tank排污罐 blow down tank闪蒸罐 flash drum汽包 steam drum溶液贮槽 solution storage tank 地下槽 slop tank(5) 其它设备分离器 separator旋风分离器 cyclone分子筛 molecular sieve脱氧器 deaerator搅拌器 agitator干燥器 dryer混合器 mixer萃取器 extractor结晶器 crystallizer 澄清器 gravity settler净化器 purifier气化器 vaporizer吸附器 absorber融解槽 melter减温器 desuperheater升压器 booster喷射器 ejector喷头 sprayer火炬 flare消声器 silencer(6) 换热器、加热器、冷却器换热器 heat exchanger空冷器 air cooler水冷却器 water cooler冷凝器 condenser螺旋板式换热器spiral plate heat exchanger蒸发器 evaporator再沸器 reboiler急冷器 quencher深冷器 chiller预热器 preheater再热器 reheater加热器 heater电加热器 electric heater过热器 super heater给水加热器 feed water heater中间冷却器 inter cooler后冷却器 after cooler5.1.2 工业炉及锅炉炉子 furnace 烧嘴 burner锅炉 boiler烟囱 stack废热锅炉 waste heat boiler辅助锅炉 auxiliary boiler省煤器 economizer回热炉 direct-fired heater辐射段 radiant section对流段 convection section裂化炉 reformer焚烧炉 incinerator回转窑 rotary kiln炉管 furnace tube吹灰器 soot blower观察孔 observation door, peep door 防爆门 explosion door5.2 辅助用房名称5.2.1 生产用房分析室 analyzer room变压器室 transformer room配电室,变电所 substation, switch room 蓄电池室 battery room控制室 control room通风室 ventilating room贮藏室 storage room维修间 maintenance room办公室 office5.2.2 生活用房更衣室 locker room盥洗室,厕所 closet, lavatory, toilet 5.3 图名管道布置平面 piping arrangement plan (PAP)管道布置 piping layout轴测图 isometric drawing分区索引图 key plan初版设备布置图(“A”版) preliminary plot plan ( “A” issue)内部审查版设备布置图(“B”版) internal approval plot plan ( “B” issue)用户审查版设备布置图(“C”版) owner approval plot plan ( “C” issue)确认版设备布置图(“D”版) confirm plot plan ( “D” issue)研究版设备布置图(“e”版) planning plot plan ( “E” issue)设计版设备布置图(“F”) designing plot plan ( “F” issue)施工版设备布置图(“G”版) construction plot plan ( “G” issue)5.4 厂房、站、单元压缩机房 compressor house (room)泵房 pump house (room)洗眼站 eye washer station泡沫站 foam station软管站,公用工程站 hose station (HS), utility station成套设备 package unit设施 facilities罐区 tank yard空分装置 air separation facility5.5 设备布置设备位号 equipment item number工厂 plant工厂区界 plant limit 项目区界内侧inside battery limit (I.S.B.L.)项目区界 battery limit (BL)区界 area limit区域边界 zone limit界外 off site东 east (E)西 west (W)南 south (S)北 north (N)上 up下 down工厂北向 plant north真实北向 true north道路 road小过道 cat walk, cat way走道,过道 walk way, gangway, access way 污水坑(井) sump pit集水池 catch basin沟槽 trough预留区future area场地铺砌区 paving area非铺砌区 unpaved area碎石铺面 gravel paving橡皮铺面 rubber paving面积,区域 area体积,容积 volume (VOL)5.6 管道布置管道设计 piping design管道研究 piping study 走向研究 routing study重要管道 critical piping地上管道 above ground piping 地下管道 underground piping 管网 network of pipes管廊 pipe rack管沟 piping trench管间距 line spacing管道跨距 line span总管 header, manifold旁路 by pass排液 drain放空 vent上升管,垂直管 riser导管 conduit裸管 bare line管件直接 fitting to fitting (FTF)管段,接口 spool piece, spool取样接口 sampling connection集液包 drip leg伴热管 tracing pipe蒸汽伴热 steam tracing热水伴热 hot-water tracing电伴热 electrical tracing夹套管 jacketed line, jacketed piping 全夹套的 full jacketed平面 plan详图 detail“”视图X view “X”“”剖视A-A section “A-A”连接图 hook up drawing接续图 continue on drawing (COD)接续线 match line (M.L.)比例 scale图例 legend符号 symbol管口表 list of nozzles方位 orientation管口方位 nozzle orientation定位 location相交 intersection水平的 horizontal垂直的,立式的 vertical垂直,正交,垂直的 perpendicular 平行,平行的 parallel水平安装 horizontal installation 垂直安装 vertical installation 对称的 symmetric相反(的),对面(的) opposite顺时针方向 clock wise逆时针方向 counter clock wise计算机辅助设计 computer aided design (CAD)5.7 图面标注绝对标高 absolute elevation海平面标高 over-sea mean level (OSL)标高,立面 elevation (EL)混凝土顶面 top of concrete架顶面 top of support (TOS)钢结构顶面 top of steel梁项面 top of beam (TOB)支撑点 point of support (POS)管顶 top of pipe (TOP)管底 bottom of pipe (BOP)沟底 bottom of trench管子内底 invert (inside bottom of pipe)底平 flat on bottom (FOB)顶平 flat on top (FOT)工作点 working point (W.P.)面至面 face to face (F-F)中心至端面 center to end (C-E)中心至面 center to face (C-F)中心至中心.中至中center to center (C-C)坐标 coordinate坐标原点 origin of coordinate出口中心线 center line of discharge入口中心线 center line of suction中心线 centerline (CL)入口 inlet, suction出口 outlet, discharge排出口 exhaust距离 distance5.8 相关专业的专业词汇5.8.1 工艺(1) 图及表流程图 flow diagram工艺流程图 process flow diagram (PFD)管道及仪表流程图 piping and instrument flow diagram (PID)公用工程流程图 utility flow diagram (UFD)管线表 line list; line schedule命名表;管道表 nomenclature设备表 equipment list (schedule)(2) 流体 fluid 空气 air仪表空气 instrument air工艺空气 process air低压蒸汽 low pressure steam中压蒸汽 medium pressure steam 高压蒸汽 high pressure steam 伴热蒸汽 tracing steam饱和蒸汽 saturated steam过热蒸汽 superheated steam氧气 oxygen氢气 hydrogen氮气 nitrogen燃料气 fuel gas天然气 natural gas火炬气 flare gas酸性气 sour gas液化石油气liquefied petroleum gas (LPG)氨气 ammonia gas冷却水 cooling循环水 circulating water锅炉给水 boiler feed water热水 hot water蒸汽冷凝水 steam condensate盐水 brine工艺水 process water化学污水 chemical sewage防腐剂 corrosion inhibitor重油 heavy oil石脑油 naphtha燃料油 fuel oil润滑油 lubricating oil 密封油 sealing oil冷冻剂 refrigerant载热体 heating medium 溶剂 solvent溶液 solution母液 mother liquor单体 monomer聚合物 polymer均聚物 homopolymer共聚物 copolymer工艺液体 process liquid 工艺气体 process gas硫酸 sulphuric acid盐酸 chlorhydric acid 硝酸 nitric acid烧碱 caustic soda(3) 流体特性 fluid characteristics 蒸汽压 vapor pressure临界温度 critical temperature临界点 critical point临界压力 critical pressure比热 specific heat湿度 humidity密度 density比重 specific gravity粘度 viscosity闪点 flash point融点 melting point凝固点 freezing point浓度 concentration爆炸极限 limit of explosion有毒的 toxic 可燃的;易燃的 flammable (4) 其它回收 recovery再生 regeneration循环 circulation再循环;再生 recycle补充 make-up制备 preparation蒸汽吹扫 steaming out吹扫 purge抽空;排空 evacuation吹出 blow-off排污 blow down破真空 vacuum breaker大气腿 barometric leg备用 stand-by化学清洗 chemical cleaning净正吸入压头 net positive suction head (NPSH)进料 feed成品 product污染 contamination大气污染 atmospheric pollution环境温度 ambient temperature5.8.2 建筑、结构建筑物 building钢结构 steel structure已有钢结构 existing steel structure钢筋混凝土结构reinforced concrete construction楼面 floor平台 platform (PF)地面 ground level 栏杆 handrail楼梯 stair. stair way直梯 ladder柱 column; post; stanchion 基础 foundation; footing 梁 beam斜撑;支撑 bracing桁架;主梁 girder构件 member隔墙 partition wall墙 wall篦子板 grate; grating吊装孔 erection opening吊梁 hoisting beam棚 shelter窗 window天窗 skylight门 door防火门 fire door地漏 floor drain防火层 fire-proofing总图 general plot plan路肩 shoulder桩 pile灌浆 grouting风荷载 wind load雪荷载 snow load动力荷载 dynamic load静荷载 dead load活荷载 live load风速 wind velocity主导风向 most frequent wind direction 5.8.3 仪表盘(操作盘) panel就地盘 local panel仪表盘 instrument panel常开 normally open常闭 normally closed电缆槽(架) cable tray (channel); cable rack仪表电缆槽(架) instrument cable tray (duct)压力计 manometer; pressure gauge热电偶 thermocouple温度计 thermometer液位计 level gauge玻璃液位计 gauge glass温度计保护管 thermowell流量计 flow meter孔板 orifice变送器 transmitter连锁 interlock仪器;设备 apparatus仪器分析 instrumental analysis自动分析 automatic analysis气体分析 gas analysis化学分析 chemical analysis气相色谱仪 gas chromatograph液相色谱仪 liquid chromatograph质谱分析 mass spectrometric analysis 5.8.4 电气危险区划分hazardous area classification危险区平面图 hazardous area plan电气盘 electrical panel 配电盘 switch board电缆沟 cable trench电流 current直流 direct current交流 alternating current频率 frequency相位 phase功率因数 power factor电压 voltage电阻 resistance电容 capacitance静电 static electricity接地 grounding; earthing照明 lighting; illumination 避雷针 lightning preventer 电话 telephone电线 wire接线箱(盒) junction box 导线管 conduit tube5.8.5 设备固定鞍座 fixed saddle滑动鞍座 sliding saddle管口 nozzle人孔 manhole (MH)手孔 hand hole (HH)检查孔 inspection hole吊柱 davit切线 tangent line焊接线 welding line件号 part humbet椭圆形封头 ellipsoidal head 加强圈 reinforcing ring 接地板 earth lug吊耳 lifting lug气缸 cylinder轴 shaft轴承 bearing附件,附属设备 accessory编位号设备 itemized equipment无位号设备 non-itemized equipment 5.8.6 水道(1) 流体原水 raw water硬水 hard water软水 soft water饮用水 potable water循环冷却水给水 cooling water supply 循环冷却水回水 cooling water return脱盐水 demineralized water苦咸水(碱性水) brackish water 生活污水 sanitary sewer工业废水 industrial waste water 雨水 rain water污染雨水 contaminated rain water 消防水 fire water(2) 装置、设施软化装置 softener沉淀器 settler沉淀池 clarifier脱盐装置 demineralizer水处理 water treatment冷却塔 cooling tower中和池 neutralization tank化粪池 septic tank 渗滤井 soak-away pit井 well阀井 valve pit清扫口 clean out(3)消防消火栓 hydrant水炮 water monitor洒水器 sprinkler水喷淋 watering灭火器 fire extinguisher消防水泵 fire pump消防车 fire fighting truck泡沫消防 foam fire-fighting泡沫栓 foam hydrant泡沫炮 foam monitor消防软管接头 fire hose connection。
- 1、下载文档前请自行甄别文档内容的完整性,平台不提供额外的编辑、内容补充、找答案等附加服务。
- 2、"仅部分预览"的文档,不可在线预览部分如存在完整性等问题,可反馈申请退款(可完整预览的文档不适用该条件!)。
- 3、如文档侵犯您的权益,请联系客服反馈,我们会尽快为您处理(人工客服工作时间:9:00-18:30)。
主机开
MN-ENG ON
78
电动对开多叶
E-MT MUT-VANE
79
控制柜超温
CAB O-TMP
80
控制柜
CAB
81
排浆电动门
OT-SL V
82
冲洗水电动门
WASH VALVE
W-V
83
冲洗电动门
WASH VALVE
W-V
84
电动门
V
85
密封水
SEAL WTATER
S-WTR
86
开门
DOOR OPNED
111
高压水泵
HP PU
112
底部吹灰器
BM-S-BLW
113
全伸出位置开关
FU-EXD SW
114
高压水
HP-W
115
入口挡板
IN-DMP
116
入口挡板
OT-DMP
117
低泄漏风机
L-LK FAN
118
气动截止阀
P-CHK V
119
就地操作
LOC
120
浆液制备
SL-PR
121
滑行平台
SLIDE PLATE
OPNED
159
启状态
ON
160
停状态
OFF
161
关状态
CLSED
162
启动状态
ON
163
停止状态
OFF
164
关行程
CLOSE LIMIT
CLS LMT
165
开行程
OPN LMT
166
开力矩
TRQ ON
167
关力矩
TRQ OFF
168
全伸出
FL-EXD
169
未Hale Waihona Puke 闭UN-CLSD170
过滤布
FILT CLOTH
24
高压水截止电动门
HP-W V
25
氧化风机
OAF
26
事故保安MC C段:
SF MCC
27
MC C电流
MCC CUR
28
事故保安段
SF
29
废水处理
W/W
30
水力旋流器
Hydrocycl one
H-C
31
废水旋流站
W/W-C
32
截止电动门
CK-V
33
进水电动门
IN/W V
34
岀口母管排浆电动门
OUT BUS PIPEOUT SLURRY
S-C-P
16
循环泵
Circular Pump
C-P
17
石膏旋流器
Gypsum cyclone [?saikl?un]
G-C
18
就地操作位置
LOC
19
密封空气
SEAL AIR
SL-A
20
补给水流量调节—
M-U-W FL
21
润滑油流量低
LU-OIL F L
22
出线断路器
OT/BK
23
工业水进水
I-W IN
氧化空气
Oxidatio n Air
O-A
58
加湿水
Humidifier Water
HUM-W
59
保护动作
P-ACT
60
进出口
IN-OT
61
分析仪
An alyzer
ANLR
62
烟尘仪
DUST ANLR
63
执行机构
Actuator
ACTR
64
动调执行器
CTLR
65
紧急停机
EMG STP
66
就地/远程控制
G-DW
7
石膏脱水
Gypsum dewater ing
G-DW
8
石灰石制备系统
LIMESTONE PREPARATION
LS-PR
9
旁路烟气挡板
BPS DMP
10
旁路挡板
BPS DMP
11
增压风机
BUF
12
石膏浆液缓冲箱
G-SL TK
13
石膏浆液
G-SL
14
吸收塔
ABR
15
浆液循环泵
SLURRY CIRCULAR PUMP
L/R CTL
67
远方/就地控制
R/L CTL
68
发电机侧
GENERATORSIDE
GEN
69
充电器
CHARGR
70
主驱动
MAS
71
备用驱动
STBY
72
空压机
Compressor
CPSR
73
储气罐
AIR STG TK
74
选择为备用
SEL AS STBY
75
汽轮发电机组
TUR-GEN
76
电动调节阀
CV
P搅拌器
AGR
131
烟气
F/G
132
冷却水回水
CLG-W R-W
133
母管
HEADER
HDR
134
排空
ven tilate
VENT
135
全开
OPED
136
「全关
CSED
137
跳闸位置
OFF
138
合闸位置
ON
139
跳闸状态
OFF
140
1号机组
#1
141
2号机组
#2
142
1号机
#1
143
2号机
#2
144
脱硫系统中英文对照表
NO
中文
En glish
央文缩与
A
A
B
B
C
C
D
D
GGH
GGH
i
D C M备用D O点
DCM SPARE DO(RELAY)
2
SPPA内部D O点
SPPA INTERNAL USED DO
3
FGD02
FGD02
4
FGD03
FGD03
5
FGD05
FGD05
6
石膏脱水系统
Gypsum dewater ing
1号炉
#1
145
2号炉
#2
146
密封风机
SEAL/F
S-F
147
电机绕组
MOTOR WINDING
WDG
148
:启动指令—
149
启指令
150
停指令
STP CMD
151
停止指令
152
启动程序
STA PROG
153
停止程序
STP PROG
154
关指令
155
开指令
156
合闸指令
157
合闸
CLS
158
开状态
FLT-CLH
171
过滤器
FILTRATE
FILT
172
安全线
SAFE LINE
98
PH计
PH MER
99
除雾器:
MIST
100
第一级
1 ST
101
止面
FR
102
冲洗水
WSH-W
103
「背面
BK
104
第二级
2 ST
105
净烟气
CLG F/G
106
原烟气
RAW F/G
107
蓄电池I
BATTERY
BAT
108
电池
BATTERY
BAT
109
低泄露风机
L-LK FAN
110
烟囱
CHNY
BKN
48
石灰石制备
LS-PR
49
排水坑
DRN PIT
50
自引罐
self pri ming
SEF
51
自引灌
self pri ming
SEF
52
搅拌器电机
AGR
53
低泄露风机电机
L-LK FAN
54
取样系统
SAMPLING SYSTEM
SM-S
55
事故浆液箱
EM SL TK
56
事故浆液「
EM SL
57
OT-SL V
MV
35
皮带机
BLT
36
运行状态
ON
37
不可用
UNUSE
38
排水坑
PIT
39
石灰石浆液
LS-SL
40
石灰石
LS
41
皮带脱水机
BLTR
42
阀位反馈
PO
43
位置反馈
POS
44
终端总线
TERMINAL BUS
45
工厂总线0
PLANT BUS
46
旁路电动门
BPS MV
47
回路断线
LOOP BROKEN
87
回流流量
R-FL
88
回流管
R-FL
89
回流
R-FL
90
石膏滤液调节
GYPSUM FILTRATE WATER
G-FLT-W
91
滤液
FLT-W
92
风量
FL
93
烟道(内侧)