UG自动编程加工数据表
ug数控加工编程教程

ug数控加工编程教程UG数控加工编程教程简介UG编程是指采用西门子公司研发的专业3D软件UG NX,进行数控机床的数字程序的编制,简称CAM。
数控机床没有程序是不能运动的。
需要专业人员利用专业软件工具,根据产品的形状编制程序。
UG编程就是指数控机床的程序编制。
UG是当前世界最先进、面向先进制造行业、紧密集成的CAID/CAD/CAE/CAM软件系统,提供了从产品设计、分析、仿真、数控程序生成等一整套解决方案。
UG CAM是整个UG系统的数控机床程序编制的内容主要包括以下步骤:一.工艺方案分析确定加工对象是否适合于数控加工(形状较复杂,精度一致要求高),分析哪些部位需要拆铜公!确定碰穿面\擦穿面\分型面等!分析使用的刀具类型和刀具大小!毛坯的选择(对同一批量的毛坯余量和质量应有一定的要求)。
工序的划分(尽可能采用一次装夹、集中工序的加工方法)。
二.工序详细设计工件的定位与夹紧。
工序划分(先大刀后小刀,先粗后精,先主后次,尽量“少换刀”)。
刀具选择。
确定使用什么加工方法,设置好切削参数。
工艺文件编制工序卡(即程序单),走刀路线示意图。
程序单包括:程序名称,刀具型号,加工部位与尺寸,装夹示意图三.编写数控加工程序用UG设置编出数控机床规定的指令代码(G,S,M)◆直线控制数控机床(单轴数控)◆轮廓控制的数控机床:分为两坐标联动,2.5坐标联动,三坐标联动,四坐标联动,五坐标联动等数控机床。
五坐标联动是关键技术。
2)按伺服系统的控制类型分类◆开环控制的数控机床◆全闭环控制的数控机床◆半闭环控制的数控机床3)按工艺方法分类◆金属切削类数控机床:数控车床,数控铣床、数控钻床、数控磨床、数控镗床以及加工中心等。
◆金属成型类及特种加工类数控机床4)按功能水平分类:◆高、中、低档(亦称经济型)5)按驱动方式分类◆步进式◆直流伺服◆交流伺服(交流模拟、交流数字)6)按组成和功能◆开放式数控◆智能数控2.1.2 常用G代码的用法◆G00 快速定位N10 G0 X100 Y100◆G01 直线插补◆G02(G03)圆弧插补结果,这个情况下圆弧命令如下所列:G17 G03 G90 X5. Y25. I-20. J-5.; 或者G17 G03 G90 X5. Y25. R20.616.;◆G04 暂停G04 P1000 暂停1秒◆G17 G18 G19 平面选择圆弧在XY 面上G17 G02 ( G03 ) G90 ( G91 ) I_ J_ F_或G17 G02 ( G03 ) G90 ( G91 ) R_ F_圆弧在XZ 面上G18 G02 ( G03 ) G90 ( G91 ) I_ K_ F_或G18 G02 ( G03 ) G90 ( G91 ) R_ F_圆弧在YZ 面上G19 G02 ( G03 ) G90 ( G91 ) J_ K_ F_或G19 G02 ( G03 ) G90 ( G91 ) R_ F_◆G20 G21 公英制的选择G20;英制指令G21;公制指令详细说明G20,G21 的切换仅对直线轴有意义,对于旋转轴无意义。
数控自动编程操作步骤(UG--CAM模块)
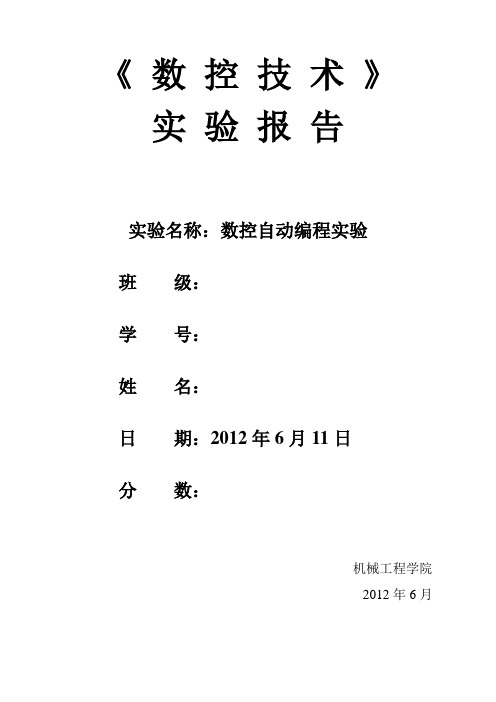
《数控技术》实验报告实验名称:数控自动编程实验班级:学号:姓名:日期:2012年6月11日分数:机械工程学院2012年6月一、实验模型的建立在UG软件中设计一个零件,零件的毛坯尺寸严格按照将要加工的毛坯尺寸设计。
设计零件图如图1所示(该毛坯的尺寸为mm50⨯50⨯)。
mmmm40图1二、自动编程在菜单栏“开始”处选择“加工”。
根据零件图可判断出是加工平面图形,选择mill_planer(两轴)。
1.创建加工坐标系及安全平面在工具条中选择“几何视图”按钮,再选择窗口左侧资源条中的“操作导航器”按钮,导航视图为“几何视图”。
双击“MCS_MILL”节点,系统弹出如图2所示的对话框。
在“指定MCS,”上选择如图3所示的上表面,在“安全平面”中选择平面,点击按钮,在偏置距离中输入5,并选择上表面,其结果如图3所示。
图2图32.创建刀具在工具条中选择“创建刀具”按钮,出现如图4所示界面。
点击“确定”,出现如图5的界面,按照加工要求输入刀具直径(本实验取的刀具直径为8mm),如图5所示,点击“确定”,完成刀具的编辑。
图4图53.创建操作。
1)在工具条中选择“创建操作”按钮,出现如图6所示界面。
在“刀具”处选择“MILL”,在“几何体”处选择“WORKPIECE”,然后点击“确定”,出现如图7所示界面。
图6图72)在“指定部件”处选择按钮,系统弹出如图8的“部件几何体”对话框,在视图窗口中选择零件模型,单击“确定”按钮。
在“指定面边界”处选择按钮,体统弹出如图9所示界面,选择加工平面如图9所示,点击“确定”按钮。
图8图93)在“指定壁铣削面”处选择按钮,体统弹出如图10所示界面,选择如图10所示的所有侧面,然后点击“确定”按钮。
4)在“切削模式”处根据需要选择“跟随部件”,如图11所示。
5)在“毛坯距离”和“每一刀的深度”处根据零件要求选择恰当的数值,如图11所示。
6)在“进给和速度”处选择,根据加工要求给出“主轴转速”和“进给速度”,如图12所示。
ug深加工的编程及技巧
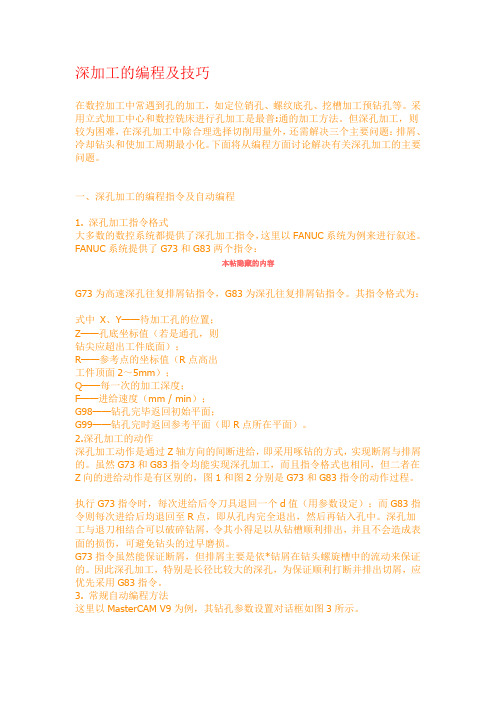
深加工的编程及技巧在数控加工中常遇到孔的加工,如定位销孔、螺纹底孔、挖槽加工预钻孔等。
采用立式加工中心和数控铣床进行孔加工是最普:通的加工方法。
但深孔加工,则较为困难,在深孔加工中除合理选择切削用量外,还需解决三个主要问题:排屑、冷却钻头和使加工周期最小化。
下面将从编程方面讨论解决有关深孔加工的主要问题。
一、深孔加工的编程指令及自动编程1. 深孔加工指令格式大多数的数控系统都提供了深孔加工指令,这里以FANUC系统为例来进行叙述。
FANUC系统提供了G73和G83两个指令:本帖隐藏的内容G73为高速深孔往复排屑钻指令,G83为深孔往复排屑钻指令。
其指令格式为:式中X、Y——待加工孔的位置;Z——孔底坐标值(若是通孔,则钻尖应超出工件底面);R——参考点的坐标值(R点高出工件顶面2~5mm);Q——每一次的加工深度;F——进给速度(mm / min);G98——钻孔完毕返回初始平面;G99——钻孔完时返回参考平面(即R点所在平面)。
2.深孔加工的动作深孔加工动作是通过Z轴方向的间断进给,即采用啄钻的方式,实现断屑与排屑的。
虽然G73和G83指令均能实现深孔加工,而且指令格式也相同,但二者在Z向的进给动作是有区别的,图1和图2分别是G73和G83指令的动作过程。
执行G73指令时,每次进给后令刀具退回一个d值(用参数设定);而G83指令则每次进给后均退回至R点,即从孔内完全退出,然后再钻入孔中。
深孔加工与退刀相结合可以破碎钻屑,令其小得足以从钻槽顺利排出,并且不会造成表面的损伤,可避免钻头的过早磨损。
G73指令虽然能保证断屑,但排屑主要是依*钻屑在钻头螺旋槽中的流动来保证的。
因此深孔加工,特别是长径比较大的深孔,为保证顺利打断并排出切屑,应优先采用G83指令。
3. 常规自动编程方法这里以MasterCAM V9为例,其钻孔参数设置对话框如图3所示。
(1)高度参数高度参数包括Clearance(安全高度)、Retract(参考高度)、Feedplane(下刀位置)、Top of stock(工件顶面)和Depth(切削深度)等。
UG编程技巧如何优化CNC加工程序

UG编程技巧如何优化CNC加工程序概述:CNC(Computer Numerical Control)编程是现代制造业中常见的加工方式之一,它通过预先编写的程序指导机床进行加工操作。
UG软件是一种常用的CNC编程工具,具有强大的功能和灵活的编程方式。
本文将探讨UG编程技巧,以优化CNC加工程序,实现更高效、精确和稳定的加工过程。
I. 基本编程技巧1.选择适当的刀具路径在编写CNC程序时,刀具路径的选择直接影响到加工效率和加工质量。
应根据具体加工要求合理选择刀具路径,如直线切割、圆弧切割等。
同时,还可以利用UG软件的自动生成路径功能,减少手动编程的工作量。
2.合理设定切削参数切削参数的设定对CNC加工过程中的刀具寿命、表面质量等有重要影响。
根据被加工材料的性质和设计要求,合理设定进给速度、转速、切削深度等参数,以达到理想的加工效果。
3.合理安排工序和切入点在编写CNC程序时,应根据被加工零件的几何特征和工艺要求,合理安排切入点和加工工序。
通过合理的切入点位置和工序顺序,可以提高加工效率和降低加工成本。
II. UG软件高级技巧1.利用图形模块化编程UG软件提供了图形模块化编程的功能,可以将常用的形状、几何元素等保存为模块,以便在不同工程中重复使用。
这样可以大大提高编程的效率,并减少错误的发生。
2.使用自定义宏指令UG软件支持自定义宏指令,与图形模块化编程相辅相成。
通过编写自定义宏指令,可以实现一键式生成复杂的加工轨迹和路径,并实现各种加工操作的自动化。
3.利用参数化编程UG软件的参数化编程功能可以将常用的加工参数和数据作为变量存储,以便后续的调整和修改。
参数化编程可以提高程序的可复用性和灵活性,减少出错的可能性。
III. 优化加工策略1.采用合理的进给方式进给方式的选择对加工效率和加工表面质量有重要影响。
在UG软件中,可以选择恒速进给、动态进给等不同的进给方式,根据具体情况进行合理选择,以获得最佳的加工效果。
UG加工中心编程实例

目录第一节孔加工------------------------(2)第二节平面铣------------------------(9)第三节表面铣------------------------(22)第四节穴型加工----------------------(26)第五节等高轮廓铣--------------------(33)第六节固定轴轮廓铣------------------(36)第一节孔加工1.1 例题1:编写孔位钻削的刀具路径图6-11.打开文件☐从主菜单中选择File→Open→***/Manufacturing/ptp-1.prt,见图6-12.进入加工模块☐从主菜单中选择Application→Manufacturing,进入Machining Environment对话框3.选择加工环境☐在CAM Session Configuration表中选择CAM General☐在CAM Setup表中选择Drill☐选择Initialize4.确定加工坐标系☐从图形窗口右边的资源条中选择Operation Navigator,并锚定在图形窗口右边☐选择Operation Navigator工具条的Geometry View图标,操作导航器切换到加工几何组视窗☐在Operation Navigator窗口中选择MCS_Mill,按鼠标右键并选择Edit,进入Mill_Orient对话框☐选择MCS_Origin图标,进入Points Constructor对话框,选择Reset,选择OK退回到Mill_Orient 对话框☐打开Clearance开关,选择Specify,进入Plane Constructor对话框☐选择棕色显示的模型最高面,并设定Offset = 5☐连续选择OK直至退出Mill_Orient对话框5.创建刀具☐从Operation Navigator工具条中选择Machine Tool View图标,操作导航器切换到刀具组视窗☐从Manufacturing Create工具条中选择Create Tool图标,出现图6-2所示对话框☐按图6-2所示进行设置,选择OK进入Drilling Tool对话框☐设定Diameter = 3☐设定刀具长度补偿登记器号码:打开Adjust Register的开关,并设定号码为5☐设定刀具在机床刀库中的编号:打开Tool Number的开关,并设定号码为5☐选择OK退出图6-2 图6-36.创建操作☐从Manufacturing Create工具条中选择Create Operation图标,出现图6-3所示对话框☐按图6-3所示进行设置,选择OK进入SPOT_DRILLING对话框7.选择循环类型及其参数☐从循环类型列表中选择Standard Drill(三角形箭头),进入Specify Number of对话框☐设定Number of Sets = 1,选择OK进入Cycle Parameters对话框☐选择Depth进入Cycle Depth对话框,选择Tool Tip Depth,设定Depth = 3,选择OK退回到Cycle Parameters对话框☐选择Feedrate进入Cycle Feedrate对话框,设定进给率值= 60,选择OK直至退回到SPOT_DRILLING对话框8.指定钻孔位置☐从主菜单选择Format→Layer Settings,使5层为可选择层(Selectable)☐从Geometry区域选择Holes图标,并选择Select进入Point对话框☐选择Select进入选择点、孔、圆弧的对话框。
UG10.0举例零件编程(详细)

10.0编程教程(方法不一定是最有效率的,供参考!)课程:UG10.0加工编写:smile云树班级:数控加工401指导教师:01机械工程系内容简介UG 10.0编程零件PDF1号。
编著者2017.4月I目录内容简介 (I)目录 (II)一、进入模块 (1)二、编程 (2)(一)分析 (2)(二)准备 (3)1.创建程序组 (3)2.创建刀具 (7)3.创建几何视图 (10)(三)开始编程 (18)第一面编程 (18)粗加工 (18)1.型腔铣 (18)2.型腔铣(参考刀具) (24)精加工 (27)1.面铣 (27)2.面铣(轮廓) (30)3.型腔铣(轮廓) (33)4.钻孔 (34)5.验证 (37)第二面 (38)粗加工 (38)1.面铣 (38)2.型腔铣 (43)精加工 (45)1.面铣 (45)2.面铣(轮廓) (47)3.验证 (50)II一、进入模块打开UG10.0,打开需要创建编程的实体,如图1。
1点击【启动】进入【加工】模块,选择如图所示模式,如图2,3。
213二、编程(一)分析材料为铝,先加工特征多的面,后加工特征少的面;特征多的面小孔为Φ8,两面最窄距离为12,键槽宽度为8;特征少的面内圆角为R8,两面最小距离为13。
加工用Φ8麻花钻,Φ12铣刀,Φ6铣刀,Φ5球刀加工。
分析时点击【分析】【测量距离】,如图4。
24(二)准备1.创建程序组选择如图所示对象,右击点击【复制】,如图5。
35 同样操作,点击【粘贴】,如图6。
6 【重命名】为“1”“2”,如图7。
47点击【创建程序】,【位置】【程序】选择【1】,名称改为“C1”,点击应用,弹出【程序】对话点击【确定】,如图8。
58同样操作,建立“J1”,如图9。
9【位置】【程序】选择【2】,【名称】创建“C2”“J2”,创建完成后如图10。
6102.创建刀具点击底部菜单栏中的【机床视图】,如图1111点击顶部菜单栏中的【创建刀具】,如图12。
UG加工数据库编程模板及参数自动化
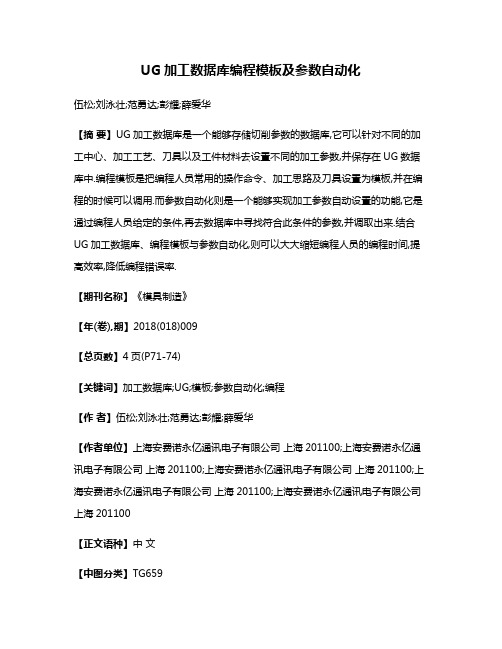
UG加工数据库编程模板及参数自动化伍松;刘泳壮;范勇达;彭耀;薛爱华【摘要】UG加工数据库是一个能够存储切削参数的数据库,它可以针对不同的加工中心、加工工艺、刀具以及工件材料去设置不同的加工参数,并保存在UG数据库中.编程模板是把编程人员常用的操作命令、加工思路及刀具设置为模板,并在编程的时候可以调用.而参数自动化则是一个能够实现加工参数自动设置的功能,它是通过编程人员给定的条件,再去数据库中寻找符合此条件的参数,并调取出来.结合UG加工数据库、编程模板与参数自动化,则可以大大缩短编程人员的编程时间,提高效率,降低编程错误率.【期刊名称】《模具制造》【年(卷),期】2018(018)009【总页数】4页(P71-74)【关键词】加工数据库;UG;模板;参数自动化;编程【作者】伍松;刘泳壮;范勇达;彭耀;薛爱华【作者单位】上海安费诺永亿通讯电子有限公司上海201100;上海安费诺永亿通讯电子有限公司上海201100;上海安费诺永亿通讯电子有限公司上海201100;上海安费诺永亿通讯电子有限公司上海201100;上海安费诺永亿通讯电子有限公司上海201100【正文语种】中文【中图分类】TG6591 UG加工数据库1.1 UG加工数据库界面介绍UG加工数据库位置:加工界面—工具—编辑加工数据库。
界面介绍:UG加工数据库界面如图1所示。
(1)加工数据。
加工数据是在确认刀具材料、切削方法及部件材料时的刀具切削参数,这三者中的条件变换后对应的刀具切削参数也会随之改变,在本文先把它们称为3个必要条件。
(2)切削方法。
切削方法即为加工工艺,在这里可以新建或更改切削方法,它可以用来区分加工的开粗、半精与精加工,是3个必要条件之一。
(3)刀具材料。
刀具材料可以用来区分刀具的种类,在这里可以区分白钢高、钨钢刀、是否有镀层及镀层的度数等。
(4)部件材料。
部件材料即为工件材料,在这里可以新建与修改不同的材料条件,也可以在这里将不同的加工中心区分开,例如,高速机—紫铜,普通机—POM等。
UG自动编程教程

3、程序组 程序组能够将操作归组并排列到程序中。例如,加工
“部件”顶端视图时需要的所有操作就可以构成一个“程序” 组。通过将操作归组,可以立即按正确的顺序,一次“输出” 许多操作,其方法是:选择程序组,然后选择“刀 具”→“操作导航器”→“输出”→“CLSF”或“Post 后处 理”。
“操作导航器”的“程序顺序”视图显示各个操作所属 的“程序”组,以及在机床刀具上执行操作的顺序。只有在 这个“操作导航器”视图中,所列操作的顺序才具关联性或 重要性。
3
三、UG NX4铣加工环境与加工术语
2、UG NX加工术语 (1)刀具 Tools (2)边界 Boundary (3)操作 Operation (4)刀轨 Tool Path (5)后置处理 Postprocess (6)加工坐标系统 MCS
4
四、UG NX4 CAM菜单与工具条
1、菜单
5
2、工具条
行加工。由于本工件没有尖角或者是很小的圆角(最小半 径为R20),对表面也没有特别高的要求,所以选用一把φ1 6平底刀进行加工,可以避免换刀操作。本工件加工的工 步分为3个:平面加工、凹槽粗加工和凹槽侧壁精加工。 通过查看手册并计算圆整,可以得到φ1 6的平底刀的转速 为600r/min,而切削进给为250mm/min。
1、平面铣概述 平面铣主要适合平面轮廓、平面区域或平面岛屿等平
面类零件的粗、精加工。通过选择不同的平面铣操作类型, 可以分别完成上述加工。
平面铣采用逐层水平和垂直方向进给加工。刀具沿水 平XY方向切削,然后沿Z轴方向运动,进入下一个水平切 削层,即所谓的2.5轴加工。在同一个切削区间,刀具使终 沿着相同的边界切削,即每一个水平切削层的刀具路径相 同,因此平面铣只能加工出直壁平底零件(侧壁垂直于底 面)。平面铣通常采用平底端铣刀。
UG编程中的模拟加工技术介绍
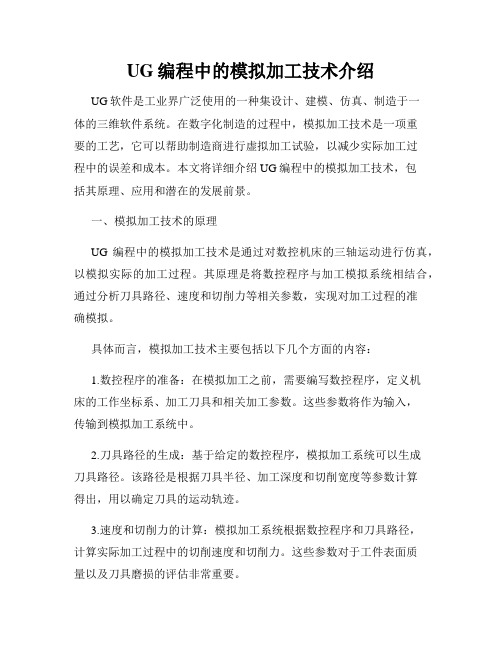
UG编程中的模拟加工技术介绍UG软件是工业界广泛使用的一种集设计、建模、仿真、制造于一体的三维软件系统。
在数字化制造的过程中,模拟加工技术是一项重要的工艺,它可以帮助制造商进行虚拟加工试验,以减少实际加工过程中的误差和成本。
本文将详细介绍UG编程中的模拟加工技术,包括其原理、应用和潜在的发展前景。
一、模拟加工技术的原理UG编程中的模拟加工技术是通过对数控机床的三轴运动进行仿真,以模拟实际的加工过程。
其原理是将数控程序与加工模拟系统相结合,通过分析刀具路径、速度和切削力等相关参数,实现对加工过程的准确模拟。
具体而言,模拟加工技术主要包括以下几个方面的内容:1.数控程序的准备:在模拟加工之前,需要编写数控程序,定义机床的工作坐标系、加工刀具和相关加工参数。
这些参数将作为输入,传输到模拟加工系统中。
2.刀具路径的生成:基于给定的数控程序,模拟加工系统可以生成刀具路径。
该路径是根据刀具半径、加工深度和切削宽度等参数计算得出,用以确定刀具的运动轨迹。
3.速度和切削力的计算:模拟加工系统根据数控程序和刀具路径,计算实际加工过程中的切削速度和切削力。
这些参数对于工件表面质量以及刀具磨损的评估非常重要。
4.碰撞检测和修正:在进行模拟加工的过程中,模拟加工系统还可以进行碰撞检测。
一旦发现机床、夹具或刀具与工件之间存在碰撞的潜在风险,系统会自动停止模拟加工,并提供相应的修正建议。
二、模拟加工技术的应用UG编程中的模拟加工技术在制造业中具有广泛的应用前景。
以下是几个典型的应用场景:1.加工优化:在实际加工之前,使用模拟加工技术可以进行多次刀具路径的优化。
通过分析不同路径的切削力和切削效率,制造商可以选择最优的加工策略,以提高加工质量和效率。
2.碰撞预防:模拟加工技术可以自动检测和预防碰撞问题。
在进行实际加工之前,模拟加工系统会通过碰撞检测功能,避免机床、夹具和刀具等与工件之间的碰撞,以减少潜在的损坏和安全风险。
3.教学培训:模拟加工技术也被广泛应用于机械加工的教学和培训领域。
- 1、下载文档前请自行甄别文档内容的完整性,平台不提供额外的编辑、内容补充、找答案等附加服务。
- 2、"仅部分预览"的文档,不可在线预览部分如存在完整性等问题,可反馈申请退款(可完整预览的文档不适用该条件!)。
- 3、如文档侵犯您的权益,请联系客服反馈,我们会尽快为您处理(人工客服工作时间:9:00-18:30)。
凸模粗加工
刀具 直径
5分 10.1 10.2 10.3 10.4 10.5 10.6 10.7 10.8 10.9
11 11.1 11.2 11.3 11.4 11.5 11.6 11.7 11.8 11.9
12 12.1 12.2 12.3 12.4 12.5 12.6 12.7 12.8 12.9
0.76 61 1620
进刀 速度
3分 500 510 520 530 540 550 560 570 580 590 600 610 620 630 640 650 660 670 680 690 700 710 720 730 740 750 760 770 780 790 800 810
UG自动编程加工数据表
自动 下刀
避让 平面 高度
2分 3分
30
31
32
33
34
35
36
37
38
39
40
41
42
43
44
45
46
47
48
49
50
51
52
53
螺旋 54
式下 55
刀, 56
角度 57
为5 58
度 59
60
61
主轴 转速
3分 1000 1020 1040 1060 1080 1100 1120 1140 1160 1180 1200 1220 1240 1260 1280 1300 1320 1340 1360 1380 1400 1420 1440 1460 1480 1500 1520 1540 1560 1580 1600 1620
曹涛 陈进勇
陈强 陈亚克 陈郑顺
程灿 丁豪 董传能 傅羲 龚康康 郭寒龙 何奋强 何正涛 胡伟勇 胡勇强 黄西西 江攀 瞿建龙 金楷 李诚泽 李嘉玮 李世昌 李志朋 林自达 刘旭 陆晶 罗恒 马子浩 庞硕位 任绍瑜 沈琛 孙鹏飞
刀具 直径
5分 16 16.1 16.2 16.3 16.4 16.5 16.6 16.7 16.8 16.9 17 17.1 17.2 17.3 17.4 17.5 17.6 17.7 17.8 17.9 18 18.1 18.2 18.3 18.4 18.5 18.6 18.7 18.8 18.9 19 19.1
Mill ing
分的 面不
zigz ag
需要
切削
AR MILL
毛坯 边界
跟随 工件
,最 小
和底
1mm
面的
刀, 角度 为5
度
通过 毛坯 ,最 复制 边界 小 粗加 和底 1mm 工操 面的
选择
作创 选择
谭宗芹 19.2
0.77 62 1640 820 13.3
0.62
62 1640 820 15.2 建
0.53 38 1160 0.54 39 1180
0.55 40 1200 0.56 41 1220
0.57 42 1240
0.58 43 1260 0.59 44 1280
0.60 45 1300 0.61 46 1320
0.62 47 1340 0.63 48 1360
0.64 49 1380 0.65 50 1400
切削 区域 选择
切削 深度
5分 4分 4分 2分 12
12.1 12.2
12.3
12.4 12.5
12.6 12.7
12.8 12.9
13 13.1
13.2
13.3 13.4
13.5 13.6
13.7 13.8
13.9 14
14.1 PLAN
14.2 14.3 14.4 14.5 14.6 14.7 14.8 14.9
杨忠禹 20.3
0.88 73 1860 930 14.4
0.73
73 1860 930 16.3
曾庆森 20.4
0.89 74 1880 940 14.5
0.74
74 1880 940 16.4
张坤 20.5
0.90 75 1900 950 14.6
0.75
75 1900 950 16.5
张宵 20.6
0.91 76 1920 960 14.7
0.76
76 1920 960 16.6
张郑权 20.7
0.92 77 1940 970 14.8
0.77
77 1940 970 16.7
赵亮 20.8
0.93 78 1960 980 14.9
0.78
78 1960 980 16.8
郑桥 20.9
0.94 79 1980 990 15
0.81 66 1720 860 13.7
0.66
66 1720 860 15.6
王燕飞 19.7
0.82 67 1740 870 13.8
0.67
67 1740 870 15.7
魏祖刚 19.8
0.83 68 1760 880 13.9
0.68
68 1760 880 15.8
夏允钱 19.9
0.84 69 1780 890 14
汪成 19.3
0.78 63 1660 830 13.4
0.63
63 1660 830 15.3
王巨壮 19.4
0.79 64 1680 840 13.5
0.64
64 1680 840 15.4
王庆隆 19.5
0.80 65 1700 850 13.6
0.65
65 1700 850 15.5
王文财 19.6
0.66 51 1420
0.67 52 1440
Face Mill ing
进行
粗加
工部 分的 面不
zigz ag
需要
切削
0.68 0.69 0.70 0.71 0.72 0.73 0.74 0.75
53 54 55 56 57 58 59 60
1460 1480 1500 1520 1540 1560 1580 1600
0.69
69 1780 890 15.9
徐彬 20
0.85 70 1800 900 14.1
0.7
70 1800 900 161 1820 910 14.2
0.71
71 1820 910 16.1
杨帆 20.2
0.87 72 1840 920 14.3
0.72
72 1840 920 16.2
15 15.1
AR PROF ILE, 也可 通过 复制 粗加 工操 作创
建
包括 部件 几何 体, 毛坯 边界 和底 面的 选择
最大 2mm ,最 小 1mm
12316333 12316334 12316335 12316336 12316337 12316338 12316339 12316340 12316341 12316342 12316343 12316344 12316345 12316346 12316347 12316348 12316349 12316350 12316351 12316352 12316353 12316354
36 2530 830 37 2535 835
38 2540 840 39 2545 845
40 2550 850 41 2555 855
42 2560 860
43 2565 865 44 2570 870
45 2575 875 46 2580 880
47 2585 885 48 2590 890
49 2595 895 50 2600 900
邹成臣 21.3
0.98 83 2060 1030 15.4
0.83
83 2060 1030 17.3
凸模精加工
避让 平面 高度
主轴 转速
进刀 速度
3分 3分 3分 30 2500 800
31 2505 805 32 2510 810
33 2515 815
34 2520 820 35 2525 825
上表面铣削
创建 操作
切削 区域 选择
切削 方式
每刀 深度
避让 平面 高度
主轴 转速
3分 3分 1分 3分 3分 3分 0.45 30 1000
0.46 31 1020 0.47 32 1040
0.48 33 1060
0.49 34 1080 0.50 35 1100
0.51 36 1120 0.52 37 1140
51 2605 905
52 2610 910 53 2615 915
54 2620 920 55 2625 925
56 2630 930 57 2635 935
58 2640 940
59 2645 945 60 2650 950
61 2655 955
62 2660 960 63 2665 965 64 2670 970 65 2675 975 66 2680 980 67 2685 985 68 2690 990 69 2695 995 70 2700 1000 71 2705 1005 72 2710 1010 73 2715 1015 74 2720 1020 75 2725 1025 76 2730 1030 77 2735 1035 78 2740 1040 79 2745 1045 80 2750 1050 81 2755 1055 82 2760 1060 83 2765 1065
进刀 速度
3分 500 510 520 530 540 550 560 570 580 590 600 610 620 630 640 650 660 670 680 690 700 710 720 730 740 750 760 770 780 790 800 810