大型风机叶片模具温控系统的设计
风电叶片模具制作步骤介绍

风电叶片模具制作步骤介绍1. 确定设计要求在制作风电叶片模具之前,首先需要明确设计要求。
根据风电叶片的尺寸、形状和材料等要求,确定模具的设计参数。
2. 制作模具设计图纸在确定设计要求后,根据要求绘制风电叶片模具的设计图纸。
设计图纸包括叶片形状、模具尺寸、模具结构等详细信息。
可以使用CAD 软件进行绘制,确保设计准确无误。
3. 准备模具材料根据设计图纸确定的模具尺寸和形状,选择合适的模具材料。
常见的模具材料包括铝、铜、钢等。
根据具体要求,考虑模具的强度、耐磨性和可加工性等因素进行选择。
4. 制作模具原型根据设计图纸,制作模具的原型。
可以使用铣床、车床和激光切割等机械设备进行加工。
根据叶片的形状和尺寸,将模具原型雕刻或切割成相应形状。
5. 制作模具壳体使用模具原型制作模具壳体。
根据模具原型的形状,制作合适大小的模具壳体。
模具壳体包围着叶片模具,起到固定和支撑的作用。
6. 制作模具芯部制作模具芯部,用于在模具壳体内形成叶片的空间。
根据模具原型和设计图纸,制作模具芯部的形状和尺寸。
模具芯部可以使用铁、铝或塑料等材料制作。
7. 组装模具壳体和模具芯部将模具壳体和模具芯部进行组装。
将模具芯部放入模具壳体内,并严密固定。
确保模具芯部和模具壳体的精确配合,保证叶片的精度和质量。
8. 进行模具加工根据风电叶片模具的设计要求,进行模具的加工和处理。
可以使用钳工、铣床、切割机等工具进行精度加工,确保模具的形状和尺寸的准确性。
9. 进行模具调试和调整制作完成的风电叶片模具需要进行调试和调整。
通过测试模具的使用效果,发现并解决一些可能存在的问题,比如模具的拆卸和装配是否顺畅,叶片的质量是否满足要求等。
10. 进行模具试产完成模具调试和调整后,进行模具的试产。
根据风电叶片的要求制作相应数量的叶片试产。
通过试产,验证模具的可用性和叶片的质量。
11. 对模具进行维护和保养完成模具试产后,需要对模具进行定期的维护和保养。
清洁模具表面的灰尘和腐蚀物,涂抹保护剂防止生锈。
模具温度控制系统设计资料

模具温度控制系统设计资料1. 简介模具温度控制系统是用于模具加工过程中对模具温度进行精确控制的系统。
它可以确保模具在加工过程中保持恒定的温度,从而提高加工精度和产品质量。
本文将详细介绍模具温度控制系统的设计原理、组成结构以及工作原理。
2. 设计原理模具温度控制系统的设计原理主要基于模具加工过程中的热传导原理。
通过控制模具表面的温度,可以控制模具内部的温度分布,从而实现模具加工过程中的温度控制。
设计原理的主要步骤如下: 1. 在模具表面安装温度传感器,用于实时监测模具表面的温度。
2. 通过传感器将温度信号传输给控制器。
3. 控制器根据设定的温度值和实时温度值进行比较,计算需要施加的热量。
4. 通过控制系统控制加热或冷却设备,实现模具温度的精确控制。
5. 控制器不断监测温度信号,根据实时温度值调整加热或冷却设备的工作状态,保持模具温度的稳定。
3. 组成结构模具温度控制系统的主要组成结构包括温度传感器、控制器、加热或冷却设备以及控制系统。
3.1 温度传感器温度传感器用于实时监测模具表面的温度,并将温度信号传输给控制器。
常用的温度传感器有热电偶、热敏电阻和红外线传感器等。
温度传感器需要具有高精度、快速响应和耐高温等特点,以确保模具温度的准确控制。
控制器是模具温度控制系统的核心部件,负责接收温度信号、计算热量需求并控制加热或冷却设备。
控制器根据设定的温度值和实时温度值进行比较,通过控制系统控制加热或冷却设备的工作状态,从而实现模具温度的精确控制。
控制器通常采用微处理器或PLC等控制芯片,具有高精度、可靠性和稳定性。
3.3 加热或冷却设备加热或冷却设备用于向模具施加热量或冷却量,以实现模具温度的控制。
常用的加热设备有电热管、加热棒和电热板等,常用的冷却设备有冷却水系统和风扇散热系统等。
根据模具的具体需求,可以选择合适的加热或冷却设备。
控制系统是模具温度控制系统的核心部分,包括传感器、控制器和加热或冷却设备之间的数据传输、协调和控制。
1.5MW风机叶片模具加热工艺研究与技术创新
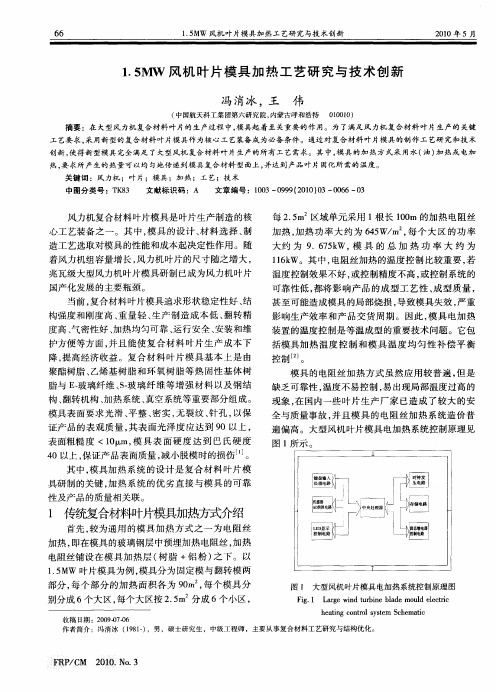
构、 翻转 机构 、 加热 系统 、 真空 系统 等重要 部分 组成 。
模 具表 面 要求 光 滑 、 整 、 平 密实 , 裂 纹 、 孔 , 无 针 以保 证 产 品 的表 观质 量 , 表 面光 泽度 应 达 到 9 其 0以上 , 表 面粗糙 度 <1 m, 具 表 面 硬 度 达 到 巴 氏硬 度 0 模
图 1 大型风机叶片模具 电加热系统控制原理 图
F g 1 L r e w n u b n ld u d ee t c i . a g i d t r i e ba e mo l lcr i h ai g c n rls se S h mai e t o to y t m c e t n c
风 力机 复合材料 叶 片模 具是 叶 片生产制 造 的核
每 2 5 区域单 元采 用 1根长 lO 的加 热 电 阻丝 .m Om 加热 , 加热 功 率 大 约 为 6 5 m , 4 W/ 每个 大 区 的 功 率
大 约 为 9 6 5 W , 具 的 总 加 热 功 率 大 约 为 . 7k 模
缺 乏可靠 性 , 温度不 易控 制 , 出现局 部 温度过 高 的 易 现 象 , 国 内一些 叶 片 生产 厂 家 已造成 了较 大 的安 在
全 与质量 事故 , 且模 具 的 电阻 丝加 热 系 统 造价 普 并 遍偏 高 。大 型风机 叶片模 具 电加热 系统控 制原 理见
图 1所示 。
收稿 日期 :2 0 -70 0 90 -6 作 者 简 介 :冯 消 冰 ( 9 1) 18 一 ,男 ,硕 士研 究 生 , 中级工程师 ,主要从事 复合材料工艺研究与结构优化 。
F / M 2 1 : . RP C 0 0 No 3
21 0 0年 第 3期
MW级风力发电叶片模具温度控制系统设计

至P L C 温 度控 制模 块E M2 3 1 ,C P U根 据 标准信 号所 对 应 实 际温 度 与 所 设 定 控 制温 度 进 行 自动运 算 , 通 过 调 节 电 阻加 热 丝 两端 电压 实 现 自动 控制 电 阻 加 热 丝温度 。系统原理 图 如图 1 所示。
式 。水 循 环 加 热方 式 主 要 通 过 加 热 器将 水 加 热 到 设 定 温 度 ,通 过 水 泵 使 之 循 环 流 经 铜 导 热 管 将 热 量 传 递 至 所 需 加 热 设 备 。 此种 方 法 存 在 升 温 速 度
Y ANG Sh u a i .YI N Xi u — y 限公 司,北京 1 0 2 1 0 1 ) 要 ;在大型风力发 电叶片生产过程 中,叶片模具温度的控制对风力发 电叶片成型及产品质量起着至
关重要 的作 用 ,因此 在叶片生产过 程中 ,对 叶片模具 内表 面温度的精确 性及均匀性提 出了严 格的要求 。本文主要介绍 7MW级大型风 电叶片模具 电阻丝加热的 电加热控制系统 , 详细介绍 该控制 系统框架结 构 、控制算 法等关键内容 。该控制系 统在实际应用 中能够较好的解决 叶片
慢 、加 热 效 率 不 高 、 热 能 浪 费 、模 具 重 量 大 大增
加 等 缺 陷 ,在温 度 要求 高 于 1 0 0 度 的碳 纤 维材 料加 热 成 型 过 程 中 ,水 加 热 系统 则无 法 达 到 要 求 。纯 电 阻丝 直 接 加 热 则 能 够 有效 避 免 上 述 缺 陷 。在 电 加 热 温 度 控 制 方 面 , 随 着风 电叶 片 尺 寸 的 增加 , 叶 片 成 型 模 具 加 热 存 在 区域 划 分 较 多 、温 度 控制 不 均 匀 、局 部 温 度过 高 或过 低 等 问 题 ,因 此对 温 度 控制 系统 有着 更高 更严 格的要 求 。 本 文 根 据 工 业 实 际 经 验 就 多 路 电 阻 丝 直 接
大型风电叶片模具型面控制研究

本 文开展 大 型风 电叶 片模具 型 面精 度控 制 等相 关研 究 , 对大 型 构 件 复合 材 料 模 具 型 面 精度 控 制设 计研 发 提供 指导 性意 见 。叶 片模 具 的 型面精 度 变形 存在 一些 共性 , 可 通 过在 多套 模 具 型 面 变形 测验 数 据的基础 上总结 、 改进 , 以尽 可 能 减 少 其 变 形 。 实验 证 明 , 通 过对 叶片模 型进行 补偿 设 计 、 采用 低 粘
面精度检测 , 检测结果偏差 ± 1 m m, 其合格率为 8 0 %
左右。
型机床的检测 、 工装夹具 的标定 、 动态安
装 时测 量半 径 ) 为4 0 m; 其 探 针 测 量精 度 为 7 m 之 内
0 . 1 2 5 mm, 1 5 m之内 0 . 1 6 5 mm, 1 5 m 以外 0 . 0 9+
量啦施
5 4
大 型风 电 叶 片模 具 型 面控 制研 究
2 0 1 4年 2 月
片模具制作进行改进 , 两套模具参数如表 1 所示。
表 1 两套叶 片模具参数
T a b l e 1 T h e p a r a me t e r s o f t wo b l a d e mo l d s
挑战 , 也更加 明确 了风 电叶片进一步 向大型化发展
的新 趋 势 J 。而 叶片模 具 是制 造风 电叶片 的最 主要 设备 , 现在 国内风 电 叶片 产 业 的规模 化 和 工艺 技 术 水 平 与 国际先 进 水 平 存 在 较 大 差距 。尤 其 是 大 型 、 复 杂 和高精 度 模 具 制造 技 术 的落 后 , 导 致 国 内市 场 大 型 叶片极 为 短 缺 的 现状 , 并 已成 为制 约 风 电产 业
风电叶片成型模具多路温度控制系统的设计

性 , 度不 易控 制 , 出现 局部 温 度 过 高 的 现 象 , 温 易 因此对 于 叶片成 型模具 的温度控 制系统 就 提 出 了 更高 的工艺 要求 。 对于兆 瓦级 大 型 风力 机 叶片 模 具 而 言 , 般 一 情况 下要求模 具 型 腔 内加 热能 力 至 少 为 8 ℃ ; 0 模
大 区按 2 5 分 成 6个小 区 , 2 5 区域单 元 .m 每 .m 采 用 1根 长 10 的 加 热 电 阻 丝加 热 , 热 度 曲 线
大 约 为 6 5 m , 个大 区 的功率 约为9 6 5 W , 4 w/ 每 .7 k
— —
终 止温度 的功率 ; 通过 模具 底面 隔热层 散失 的功 率 ; 通过 模具 外 围散 失 的功率 ;
靠性 低 , 影 响成型 件 的质量 , 将 甚至 可能 造成模 具
— —
的局 部烧 损 , 导致模 具失 效 , 重影 响生 产效率 和 严 产 品交货 周期 。因此 , 具 加 热 装 置 的 温度 控 制 模 是风 机 叶片模 具 成 型 过程 中 的重 要技 术 问题 , 主 要包 括模 具加 热温 度控 制和模 具 温度均 匀性 补偿 平衡 控 制¨ 。 针对 叶 片成 型模具加 热过 程 中 区域 划分 多且 复 杂 , 注胶 固化 、 在 温控 停止 和合模 固化 过程 中对
流程 控制 , 且满 足叶 片模具 成型 的工艺 要求 。 并 1 叶 片成 型模 具 加热 方 式 介 绍 与温 控 系统 工艺
要 求
1 1 叶片成型 模具 加热 方式 .
在感 应加 热 、 外加 热 及 电阻 加 热 等 加 热方 红 式 中 , 叶片模 具加 热来 说 , 对 电阻 丝加热 具有 元件 经久 耐用 、 修更换 方便 、 维 操作 简单 及成 本低 廉等
温控风扇系统设计 (1)

自动化系统创意设计大赛作品说明书作品名称:温控风扇系统设计队员:2015年4月目录摘要:本设计是基于STC12C5A60S2单片机技术与温度传感器测量外界温度的设计原理,进行了不同设计方案的比较,给出了设计的硬件电路,同时对各种关键硬件进行较详细的介绍,并且以流程图的方式对系统设计作出介绍。
系统主要通过温度传感器控制不同的PWM占空比输出来控制风扇的档位。
而出于方便、可选择性的考虑,系统也添加了辅助功能,就是直接手动控制风扇的档位。
关键词:STC12C5A60S2单片机,DS18B20温度传感器,PWM1、引言温控风扇在节能环保方面具有一定的作用,其工作原理除了普通的手动档位调节,主要是通过温度传感器感应外界温度,并自主地进行档位的调节,这样在风扇开着的情况下,不需进行手动就可以根据不同的外界温度进行自主调节风力大小,达到节能目的。
2、背景随着空调机在日常生活中的普遍应用,很容易想到电风扇会成为空调的社会淘汰品,其实经过市场的考验和证实,真实的并不是这样的,在空调产品的冲击下,电风扇产品仍然具有很强大的生命力,电风扇在市场的考验中并没有淡出市场,反而销售在不停的复苏中,具有强大的发展空间。
据市场调查,电风扇的不停复苏主要在以下原因:一,是电风扇虽然没有空调机的强大的制冷功能,但电风扇是直接取风,风力更加温和,比较适合老年人、儿童以及体质虚弱的人使用。
二,是电风扇经过多年的市场使用,较符合人们的使用习惯,而且结构简单、操作方便、安装简易。
三,是电风扇比起空调产品而言,其价格低廉,相对省电,更易的进入老百姓的家庭。
在目前空调还没有普及,并且并不是所有的情况下空调都适合使用的情况下,智能风扇适合人体对温度的要求,智能风扇还有具有相当作用的。
3、意义与应用1、普通电风扇的现状及存在的隐患:大部分只有手动调速,功能单一。
长时间在高负荷工作容易损坏电器,并且造成电量的损失。
2、作品可运用在家庭中,风扇的风力随温度而调节,即可以避免人因温度低吹到冷风而着凉,也可达到节能目的,可见温控风扇更具有优越性。
大型风电叶片模具分布式翻转同步控制系统
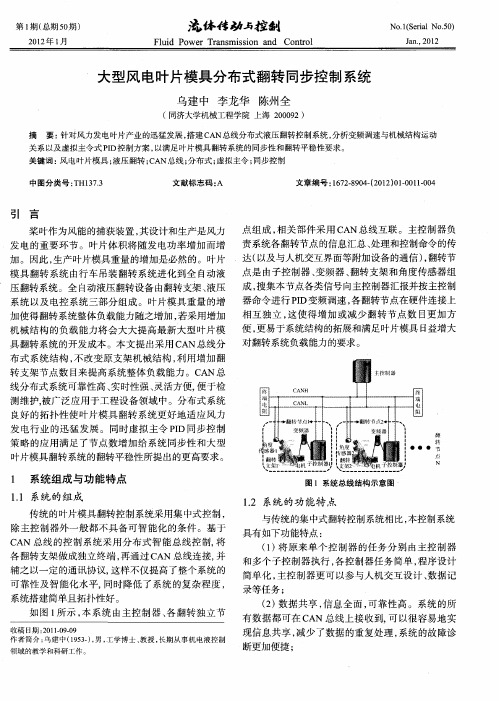
引 言
相关部件采用 C N总线互联 。主控制器负 A 桨叶作为风能的捕获装置 , 其设计和生产是风力 点组成 , 处理和控制命令 的传 发 电的重要环节。叶片体积将随发 电功率增加而增 责系统各翻转节点的信息汇总、 以及与人机交互界面等附加设备 的通信 )翻转节 , 加 。因此 , 产 叶片模 具 重量 的增加 是必 然 的。叶 片 达( 生 变频器 、 翻转支架和角度传感器组 模具翻转系统 由行 车吊装翻转系统进化到全 自动液 点是 由子控制器 、 搜集本节点各类信号 向主控制器汇报并按主控制 压翻转 系统。全 自 动液压翻转设备 由翻转支架 、 液压 成 , I 各翻转节点在硬件连接上 系统 以及 电控 系 统 三部 分 组 成 。叶 片模 具 重 量 的 增 器命令进行 PD变频调速 , 这使得增加或减少 翻转节点数 目更加方 加使得翻转系统整体负载能力随之增加 , 若采用增加 相互独立 , 便 , 易 于 系统结 构 的拓展 和 满足 叶片 模具 日益 增大 更 机械结构的负载能力将会大大提高最新大型叶片模 具 翻 转 系统 的开发 成 本 。本 文提 出采用 C AN总 线 分 对 翻转 系 统负 载能力 的要 求 。 布式系统结构 , 不改变原支架机械结构 , 利用增加翻 转支架节点数 目来提高 系统整体负载能力 。C N总 A 线分布式系统可靠性高 、 实时眭强 、 灵活方便, 便于检 测维护, 被广泛应用于工程设备领域 中。分布式系统 良好 的拓 扑 性 使 叶 片模 具 翻转 系 统更 好 地 适 应 风 力
()系统 扩充 性 强 , 品升 级快 , 4 产 开发 成本 低 , 更 加适 应风 电叶片行业 的迅 猛发 展 , 价 比高 。 性
模具毕业设计55风扇叶片注射模具设计

模具毕业设计55风扇叶片注射模具设计一、设计背景和目的风扇作为现代生活中必不可少的电器之一,其叶片的设计和制造对于风扇的性能和使用效果具有重要影响。
因此,设计一款优质、高效的55风扇叶片注射模具对于提高风扇叶片的生产效率和质量具有重要意义。
本设计旨在设计一款能够满足产品需求的注射模具,通过优化模具设计和材料选择,提高模具的使用寿命和生产效率,并保证产品的质量。
二、设计步骤和流程1.研究分析:首先对现有55风扇叶片的设计进行详细研究,并分析其结构和生产工艺。
2.模具结构设计:根据风扇叶片的形状和尺寸,设计模具的整体结构,包括模具的上模、下模和侧模的形状和尺寸等。
3.模具材料选择:根据模具的使用寿命要求和生产效率要求,选择合适的模具材料,如优质钢材或耐磨合金材料等。
4.模具加工工艺:确定模具的加工工艺和加工设备,包括模具的精度要求、加工配件的尺寸要求等。
5.模具生产和试模:根据设计要求制造模具,并进行试模,测试模具的性能和生产效果。
6.模具调试和优化:根据试模结果进行模具的调试和优化,改进模具的结构和工艺参数,提高模具的生产效率和质量。
7.模具维护和保养:制定模具的维护保养计划,定期对模具进行保养和维修,延长其使用寿命。
三、设计要求和技术方案1.叶片形状设计:根据55风扇叶片的要求,设计叶片的外形和内部结构,保证叶片的强度和风力输出效果。
2.注射模具结构设计:根据叶片形状设计模具的上模、下模和侧模等,确保注射过程中的材料流动和成型效果。
3.模具材料选择:选择优质的钢材或耐磨合金材料,提高模具的硬度和使用寿命。
4.模具加工工艺:根据设计要求确定模具的加工工艺和加工设备,保证模具的精度和质量。
5.模具试模和调试:进行模具试模和调试,测试模具的生产效率和成型质量,进行必要的参数调整和优化。
6.模具维护和保养:制定模具的维护保养计划,包括定期润滑、清洁和维修等,延长模具的使用寿命。
四、设计成果和预期效果根据以上设计流程和技术方案,预计可以设计出一款满足生产需求的55风扇叶片注射模具,具备以下特点和效果:1.提高生产效率:优化模具设计和加工工艺,提高模具的开模速度和成型效率,提高生产效率。
10MW大功率风电叶片实验台控制系统的设计及实现
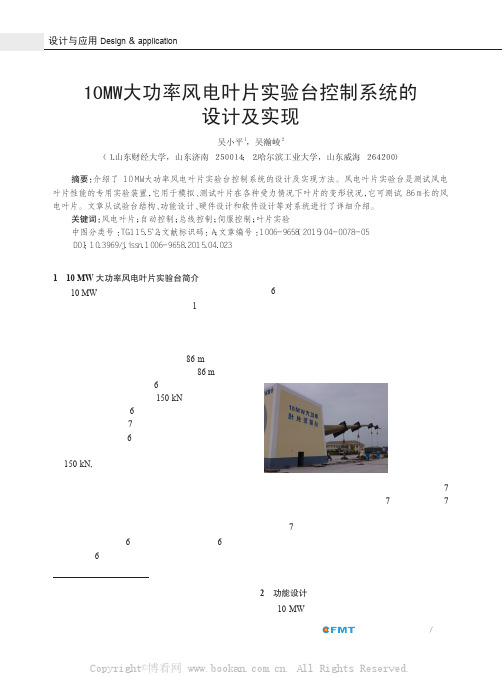
10MW大功率风电叶片实验台控制系统的设计及实现吴小平1,吴瀚崚2(1.山东财经大学,山东济南 250014;2.哈尔滨工业大学,山东威海 264200)摘要:介绍了10 MW大功率风电叶片实验台控制系统的设计及实现方法。
风电叶片实验台是测试风电叶片性能的专用实验装置,它用于模拟、测试叶片在各种受力情况下叶片的变形状况,它可测试86 m长的风电叶片。
文章从试验台结构、功能设计、硬件设计和软件设计等对系统进行了详细介绍。
关键词:风电叶片;自动控制;总线控制;伺服控制;叶片实验中图分类号:TG115.5+2;文献标识码:A;文章编号:1006-9658(2015)04-0078-05DOI:10.3969/j.issn.1006-9658.2015.04.023收稿日期:2015-03-12稿件编号:1503-878作者简介:吴小平(1962—),男,高级工程师,主要从事专用数控装备数控系统开发与研究工作.1 10 MW 大功率风电叶片实验台简介10 MW 大功率风电叶片实验台是用于模拟、测试风电叶片性能的专用实验装置(图1所示),通过对叶片上六个不同的施力点施加不同的拉力,以模拟叶片在现场的各种受力状况;可在对叶片施以各种拉力的同时,检测叶片在各种受力情况下的变形状况。
该试验台可用于测试长度在86 m 以内的各类风电叶片(迄今为止亚洲最长叶片为86 m )。
该装置能对叶片上的6个点同时同步施加不同的向下的拉力(最大拉力150 kN ),在施加拉力的过程中,实时检测这6个施力点实际受到的向下拉力,实时检测叶片上7个不同位置处叶片的变形量。
该装置难点再于对6个点施加的拉力要同时且同步,因为叶片是弹性体,每个施力点的最大拉力高达150 kN,某一施力点上拉力的微小变化,对其它施力点的拉力影响极大。
叶片上的某个施力点通过拉力传感器、动滑轮、钢丝绳、定滑轮、卷扬机与伺服电机相连,这样对该施力点的加减力就可通过控制伺服电机实现,而该点受到的实际拉力则通过拉力传感器检测。
大型风电叶片模具电加热系统设计
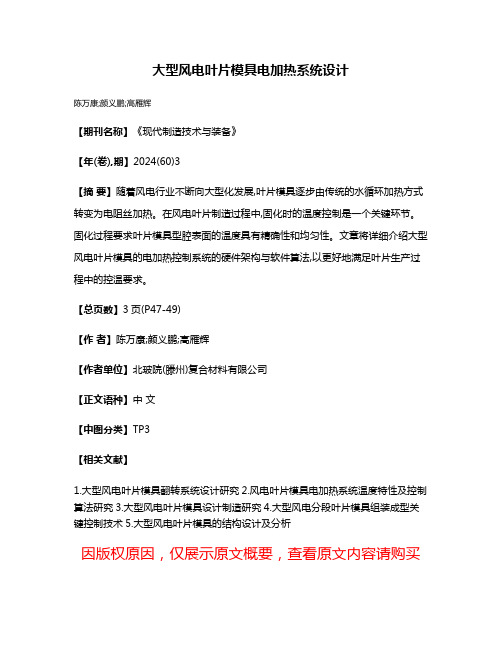
大型风电叶片模具电加热系统设计
陈万康;颜义鹏;高雁辉
【期刊名称】《现代制造技术与装备》
【年(卷),期】2024(60)3
【摘要】随着风电行业不断向大型化发展,叶片模具逐步由传统的水循环加热方式转变为电阻丝加热。
在风电叶片制造过程中,固化时的温度控制是一个关键环节。
固化过程要求叶片模具型腔表面的温度具有精确性和均匀性。
文章将详细介绍大型风电叶片模具的电加热控制系统的硬件架构与软件算法,以更好地满足叶片生产过程中的控温要求。
【总页数】3页(P47-49)
【作者】陈万康;颜义鹏;高雁辉
【作者单位】北玻院(滕州)复合材料有限公司
【正文语种】中文
【中图分类】TP3
【相关文献】
1.大型风电叶片模具翻转系统设计研究
2.风电叶片模具电加热系统温度特性及控制算法研究
3.大型风电叶片模具设计制造研究
4.大型风电分段叶片模具组装成型关键控制技术
5.大型风电叶片模具的结构设计及分析
因版权原因,仅展示原文概要,查看原文内容请购买。
大型风电叶片模具设计制造研究

玻璃钢型面
钢架支撑体
阳模代木层机加工艺过程院 吊运与固定寅对 刀寅试切与调整寅粗加工寅型面检查与修补寅精加 工寅型面检测遥
表面层主要为易打磨胶衣袁在阳模型面代木层机 加和各分段对接后喷涂袁固化后厚度约 0.5 mm袁表面 层的作用用于保证模具表面的光洁度和表面防护遥 2.3 各分段阳模对接
各分段阳模代木层经过数控 CNC 加工后袁 需要 拼接成为一个整体遥 首先通过粗调将各分段模具摆 放在相应的对接位置袁 然后根据中心线标记调整中 心轴线直线度袁 限制弦线方向移动和绕竖直轴线转 动的自由度曰 根据中心轴线长度测量控制叶展方向 移动和绕弦线方向转动的自由度曰根据型面高度尧标 高和其他设计定位基准调整前尧后缘高度袁限制上下 方向移动和绕叶根叶尖中心轴线转动的自由度遥
5 3
4 2
1
1.框架层 2.卡板层 3.纵梁预埋件 4.中间预埋件 5.壳体模具玻璃钢最外层
图 11 壳体主模具钢架截面示意图
15
Equipment Manufacturing Technology No.05袁2019
3.2 壳体主模具玻璃钢层 壳体模具根端法兰和前后缘法兰均需预留 300
mm 的操作宽度遥 壳体主模具玻璃钢层从外往内依次 为保温层尧第二层结构层尧加热层尧第一层结构层尧表 面层遥 如图 12 所示袁表面层一般为高光胶衣或碳毡袁 厚度大约 1 mm袁可采用手糊或真空灌注遥 第一层结 构层铺设短切毡和四轴向玻纤布袁厚度大约 10 mm袁 采用真空灌注袁加热层包括铝网尧铝粉尧铜管和轻木袁 厚度大约 20 mm袁 第二层结构层包括短切毡和四轴 向玻纤布袁厚度大约 10 mm袁采用真空灌注袁保温层 主要为聚氨酯泡沫袁厚度大约 50 mm遥
大兆瓦级风电机组叶片的阳模设计与制作
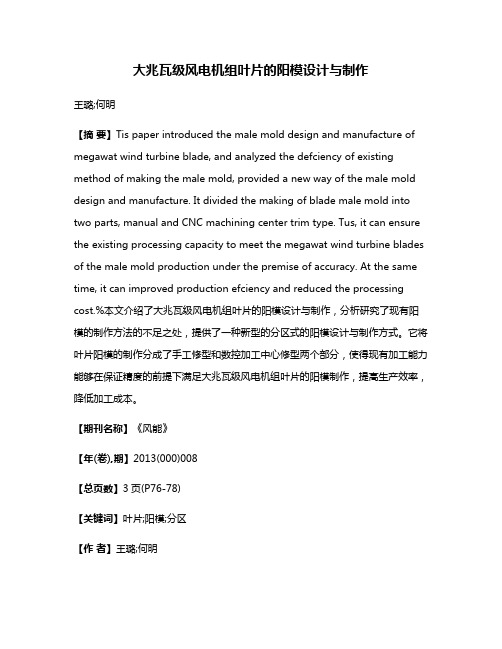
大兆瓦级风电机组叶片的阳模设计与制作王璐;何明【摘要】Tis paper introduced the male mold design and manufacture of megawat wind turbine blade, and analyzed the defciency of existing method of making the male mold, provided a new way of the male mold design and manufacture. It divided the making of blade male mold into two parts, manual and CNC machining center trim type. Tus, it can ensure the existing processing capacity to meet the megawat wind turbine blades of the male mold production under the premise of accuracy. At the same time, it can improved production efciency and reduced the processing cost.%本文介绍了大兆瓦级风电机组叶片的阳模设计与制作,分析研究了现有阳模的制作方法的不足之处,提供了一种新型的分区式的阳模设计与制作方式。
它将叶片阳模的制作分成了手工修型和数控加工中心修型两个部分,使得现有加工能力能够在保证精度的前提下满足大兆瓦级风电机组叶片的阳模制作,提高生产效率,降低加工成本。
【期刊名称】《风能》【年(卷),期】2013(000)008【总页数】3页(P76-78)【关键词】叶片;阳模;分区【作者】王璐;何明【作者单位】国电联合动力技术连云港有限公司,连云港,222069;国电联合动力技术连云港有限公司,连云港,222069【正文语种】中文【中图分类】TM614纵观全球叶片技术的发展趋势,配备较长叶片的风电机组达到额定功率所需要的额定风速相对较低,能满足更多低风速地区发展风能的需要[1]。
风电叶片模具制作步骤介绍

风电叶片模具制作步骤介绍风电叶片是风能发电机的核心部分,其质量和性能直接影响发电效果。
为了提高风电叶片的质量和效率,需要对其进行不断优化和改进。
而制作优质叶片的关键之一就是模具制作。
本文将介绍风电叶片模具制作的详细步骤。
一、模具设计模具设计是模具制作的第一步,决定了模具的尺寸和形状。
首先要根据风电叶片的外形和尺寸来设计出模具的形状和尺寸。
同时根据叶片材料的特性以及叶片工艺的需求,设计出合适的结构和壁厚等参数。
通常,模具设计需要结合CAD/CAM/CAE技术进行。
二、模具制造当模具设计完成后,需要进行模具的加工和制造。
制造模具的方法有很多种,包括CNC加工、电火花加工等。
在制造过程中,需要注意模具的平整度和精度,以及模具的结构和强度等方面的要求。
三、模具样品制作当模具制造完成后,需要进行模具样品的制作。
模具样品是模具制作过程中的一个关键环节,也是检验模具质量的重要环节。
根据模具的设计要求和叶片材料特性,制作出叶片模具的样品。
在制作过程中需要注意模具的温度、压力、速度等参数,以及模具与叶片材料之间的匹配度,确保样品的平整度和精度,以及模具的使用寿命和性能。
四、样品测试和调整当模具样品制作完成后,需要进行测试和调整。
测试叶片样品的强度、平整度、表面光洁度等各项参数,以及使用模具的方便程度和效率等方面。
根据测试结果进行调整和修改,提高叶片的质量和性能,并确定模具的可行性和适用性。
五、批量制造叶片当模具样品测试和调整完成后,可以进行批量制造叶片。
根据模具的设计要求和样品测试结果,制造出符合要求的叶片。
同时需要注意叶片的工艺流程和工艺参数,确保叶片的质量和性能,提高叶片的制造效率和降低成本。
六、模具维修和保养模具制作完成后,需要进行模具的维修和保养。
随着使用次数的增加,模具的磨损和损坏也会逐渐增加,需要进行定期的维修和保养。
维护模具的平整度和精度,增加模具的使用寿命和性能,提高制造效率和降低成本。
综上所述,风电叶片模具制作需要经过模具设计、模具制造、模具样品制作、样品测试和调整、批量制造叶片、模具维修和保养等多个环节。
叶片加热设计方案

叶片加热设计方案叶片加热设计方案:为了有效地控制叶片的温度,在叶片设计中加入加热系统是一种常见的方法。
以下是一个叶片加热设计方案的概述:1. 加热源选择:加热源可以选择电加热器、燃气加热器、蒸汽加热器等。
在选择加热源时,需要考虑加热效率、功率需求、成本等方面的因素。
电加热器通常更易操作,且可以实现精确的温度控制。
2. 加热传递方式:叶片加热可以通过对叶片表面进行直接加热或者通过通过叶片内部的流体进行间接加热。
直接加热是通过将加热源安装在叶片表面,使其直接加热叶片表面。
间接加热则是通过将加热源的热量传输到叶片内部的流体,使其间接加热叶片。
3. 温度控制系统:在叶片加热设计中,一个优秀的温度控制系统是必不可少的。
温度控制系统可以通过传感器监测叶片温度,并根据设定的温度范围来控制加热源的开关。
常用的温度控制器有PID控制器和微处理器控制器等。
4. 加热区域设计:在设计叶片加热系统时,需要确定叶片的加热区域。
通常,加热区域选取叶片的关键部位,以保证叶片在工作过程中能够保持合适的温度。
为了最大限度地提高加热效果,可以采用多个热点进行加热。
5. 加热功率计算:在确定加热区域后,需要进行加热功率的计算。
加热功率计算可以根据叶片的材质、尺寸以及所需温度变化等因素来确定。
通过计算得到的加热功率可以帮助选择合适的加热源及其参数,并且对加热时间进行合理的规划。
6. 安全措施:在叶片加热设计中,安全是一个非常重要的考虑因素。
首先,需要确保加热源与叶片之间有足够的隔离,以防止热量泄露。
其次,需要增加过温保护装置,以防止叶片过热。
此外,加热源应当采用可靠的电气设备,并且需要定期进行维护和检查。
7. 热力学分析:在设计叶片加热系统时,可以进行热力学分析,以确定加热系统的热传导效率、能源利用率等。
通过热力学分析,可以优化叶片加热系统的设计,以实现最佳的加热效果,并优化能源消耗。
综上所述,叶片加热设计方案需要综合考虑加热源选择、加热传递方式、温度控制系统、加热区域设计、加热功率计算、安全措施以及热力学分析等因素。
解读大型风机叶片建模研究

解读大型风机叶片建模研究中国玻璃钢综合信息网日期: 2010-07-14 阅读: 1895 字体:大中小双击鼠标滚屏叶片实体模型的建立叶片实体模型在ANSYS中采取自下而上的方式建立,模型建立前首先要确定叶片的翼型,翼型的形状直接影响叶片的气动性能。
风机叶片的翼型是叶片在其展长方向上某一位面的轮廓线,翼型一般是瘦长形状,其前部较厚且有小圆弧状的前缘,而其后部较薄且有一较尖的后缘,如图1所示。
为方便建模,根据750kW 叶片翼型的特点,将叶片划分为44段,共有45个截面,建立每个截面的关键点,将关键点连接成线,然后连接相应的线成面,实现叶片的实体建模。
1 建立翼型截面轮廓线叶片截面的翼型数据可以通过Profili软件得到,获得截面的关键点坐标以后,通过命令流的形式建立关键点(如图1所示),数据格式如下:翼型截面关键点建立以后,将每个截面的30个点分为6组,通过主菜单→Preprocesso→Modeling→Create→Lines→Spline→Spline thru KPs建立6条曲线,即可得到翼型的某一轮廓线,如图2所示。
在叶片的每两个翼型截面之间,以轮廓线上的曲线端点为关键点建立6条纵向直线,将叶片上所有的翼型轮廓线通过纵向直线连接起来。
2 建立叶片实体模型叶片翼型截面轮廓线共有45个,每两个截面间的曲线和直线都是对应的,因此通过主菜单→Preprocessor→Modeling→Create→Areas→Arbitrary→By Lines可以在对应的线段之间建立曲面,每两个翼型截面之间都有6个曲面,将所有的曲面建立完毕后即可得到整个叶片的实体模型,如图3所示。
由于该叶片为空心结构,为了增加强度,在叶片中间加设主梁和腹板,主梁是以玻璃纤维粗纱为增强材料的预成型件,其宽度沿着展长方向递减,而厚度则是沿着展长方向先增大然后逐渐减小,腹板是等厚渐窄的夹芯结构预成型件。
在模拟主梁时,将主梁在叶片上的区域按其形状单独分开,通过实常数赋值实现模拟。
- 1、下载文档前请自行甄别文档内容的完整性,平台不提供额外的编辑、内容补充、找答案等附加服务。
- 2、"仅部分预览"的文档,不可在线预览部分如存在完整性等问题,可反馈申请退款(可完整预览的文档不适用该条件!)。
- 3、如文档侵犯您的权益,请联系客服反馈,我们会尽快为您处理(人工客服工作时间:9:00-18:30)。
热I 2 J 。另一种较通 用的模具加 热方式 为循 环水 、 油加
热. 该方式需加装循环泵 、 加 热器等设备 . 通 常 采 取 在
复合材料型面 内预埋铜管等金 属管材 的方式 . 一般情
况下 . 金属 管材不 易折弯 随形 . 而 且 焊 接 的 难 度 大 可 靠性低 , 容 易 出现 漏 水 现 象 , 且还存在成本 高、 重 量 重 等缺点 。
承受 l 1 0 ℃以下的温度 .对于水循环加热有 良好 的适
应 性 。在 安装 过 程 中 . 通 过 热 熔 连 接 实 现 永 久 连 接后 ,
作者 简介 : 刘晓 宇( 1 9 8 7 - ) , 工学硕 士 , 研 究 方 向 为 自动 控 制技 术在 工业 领域 的应 用 。
新 能 源
大型 风机 叶片模 具温控 系统 的设 计
刘晓字 ’ , 韩 超 。 宋 晓美 ’
( 1 . 山 西大 学 自动化 系, 太原 0 3 0 0 1 3 ; 2 . 华北 电力设 计院有 限公 司热控 设 计处 . 北京 1 0 0 1 2 0 )
摘
要: 介 绍一种 基 于 P L C和循 环 水管路 加 热方式 的风 电叶 片成型模 具 温度控 制 系统的设 计 。
具 加热装 置 的温度控制 是风机 叶片模 具成型 过程 中
的 重要 技 术 问题 之 一 在叶片成型模具加热过程 中 . 有 区 域 划 分 多 且 复 杂, 在 注胶 固化 、 温 控 停 止 与 合 模 固 化 过 程 中 对 温 度 的 动 态 以 及 静 态 偏 差 要 求 严 格 的特 点 .针 对 以上 特 点. 设计基 于西 门子 P L C的 多 路 温 度 控 制 系 统 . 并 且
收 稿 日期 : 2 0 1 5 — 0 3 - 1 1
图 2 叶 片 模 具 成 型过 程 的期 望 温 度 曲线
9 5
www. c h i n a c a a a . c o m 自动化 应 用
关 键词 : P L C; 叶 片模 具 ; 温 度 控 制
中图分 类号 : T P 2 9
0引言
在 大 型风 力 发 电机 组 叶 片 的生 产 过 程 中 . 叶 片 成 型模具是核心工艺装备之一I 1 ] 。 目前 . 大 型 风机 叶 片模 具 的制 造 已成 为 阻 碍 风 机 叶 片发 展 的 主要 瓶 颈 而 叶 片 模 具 的 温 度 是 其 加 工 成 型 过 程 中 最 重 要 的 工 艺 参
这 里 采 用 改 进 型 的循 环 水 加 热 技 术 . 即 在 模 具 中
4 c c 以 内。叶片模 具成型 过程 的期 望温度 曲线 如图 2
所示。
预埋 P B ( 聚 丁烯 ) 管 的 方 式 。P B管 作 为 一 种 绿 色 管 材. 其 在 生 产 使 用 至 废 弃 过程 中均 无 毒 无 害 P B管 可
图 1 所 示
数, 影 响着叶片成型模 具 的质量 。如果 温度控制 的效
果不佳 、 控 制精 度 不 高 或 控 制 系 统 的可 靠 性 差 都 将 影 响 成 型模 具 的 质 量 .甚 至 可 能 造 成 模 具 局 部 烧 损 . 导 致模具失效 , 严 重 影 响 生 产效 率 和交 货 周 期 因此 . 模
管道无渗漏 , 耐压性能可长期保持 。目前 P B管在供水
系统 、 采 暖系统 中得 到了广泛应 用 。 是 一 种 价 格 低 廉
且 性 能 良好 地 水 路 材 料 . 非 常 适 用 于大 型 风 机 叶 片模
具 加 热 系 统 结合 风 机 叶 片 加 热 的一 些 相 关 需 求 . 设 计 了一 套 完 整 的水 循 环 加 热 系 统 来 完 成 对 模 具 的 温 度 控 制 . 如
满足叶片成型模具制造 的工艺要求
水 循 环泵 2
1叶 片成 型 模 具 加 热 工 艺
目前 . 较 为 通 用 的模 具 加 热 方 式 之 一 为 电 阻 丝 加
图1 大型 风 机 叶片 模 具 加 热 系统
2温度控制 系统设计
2 . 1温 控 系统 工 艺 要 求
对 于兆 瓦级 大 型风 力 机 组 叶 片 模 具 . 在 设 计 中要 求 模 具 型 腔 内温 度 可 达 到 8 0 %: 模 具 恒 温 保 持 过 程 中 控制精度为± 2 ℃: 在模 具 温 升 动 态 过 程 中 偏 差 控 制 在