大型储罐施工工法(倒装法安装)_secret
浅谈大型储罐倒装施工技术

浅谈大型储罐倒装施工技术1引言成品油是重要的战略资源和国计民生的重要商品,随着国民经济的快速发展,对成品油的需求越来越大。
作为成品油市场稳定供应的重要基础设施成品油钢制储罐,其应用越来越广泛,储罐的设计容积也逐渐增大。
以往大型储罐的安装基本采用正装法,只有小型储罐采用倒装法。
目前,国内大型储罐( 5 万~ 10 万m ³) 倒装已有许多成功的先例,因其避免了正装法高空作业多、吊车及脚手架费用高、效率低等缺点,倒装法已越来越多地被建筑施工单位所采用。
2工程实物量本工程 5 万m3 内浮顶罐内径为Ф60m ,总高29 . 179m 。
罐体总重1313 . 8t ,设计参数及罐体钢板规格尺寸分别见表1 、表2 。
3液压提升机构的组成及工作原理3.1液压提升机构的组成液压提升机构由液压站、油路管线、提升系统三部分组成,如图 1 、图 2 所示。
提升架结构由两根[16 槽钢构成。
千斤顶为穿心式双作用液压千斤顶,单台千斤顶额定载荷16 . 5t ,步进行程为l00mm ;上下卡头为穿心自锁式卡头。
系统整体结构简单,几何尺寸小,重量轻,安全可靠。
3.2液压提升机构的工作原理提升支架下部提升杆上安装拖板以托住胀圈,提升架上安装有液压千斤顶(双作用油缸),顶上有上下两个油嘴。
工作时,启动集中控制台的油泵,高压油经高压油管从下油嘴进人缸内,由于上卡头自动锁住提升杆,此时下卡头松开,在油压作用下,油缸内活塞上升,通过提升杆拖住胀圈使罐体上升,千斤顶的每次行程为IOOmm 。
回油时,高压油从上油嘴进人,此时下卡头自动抱紧提升杆,静止不动。
在油压作用下,活塞下行一个行程,然后再上升、下降。
如此循环往复,即可实现液压提升罐体,进行倒装组焊贮罐。
当最上圈(第八圈)壁板提升组焊完后,即可松开上下卡头,将提升杆放下,下移胀圈,进行下一圈(第七圈)壁板的提升,依次类推,直到罐体组焊完毕。
3.3 液压提升机技术参数3.4BY 型液压控制柜技术参数(见表 4 )按照上表液压控制柜产品说明书的规定,50000m³选用BY - 60 型液压控制柜的动力站。
大型储罐倒装施工液压提升工法
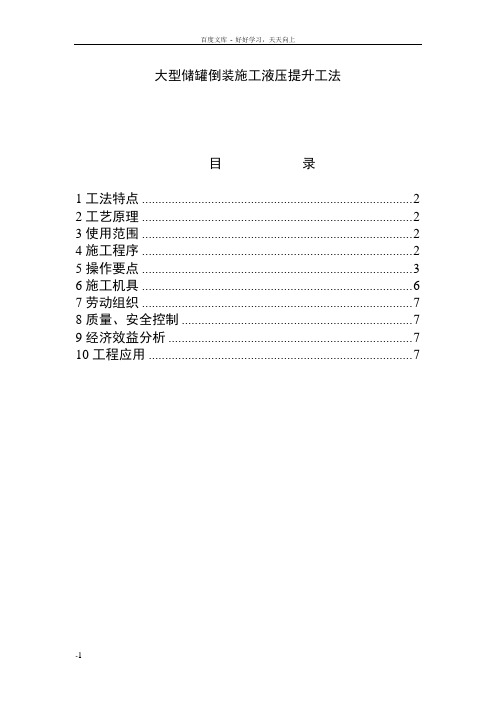
大型储罐倒装施工液压提升工法目录1工法特点 (2)2工艺原理 (2)3使用范围 (2)4施工程序 (2)5操作要点 (3)6施工机具 (6)7劳动组织 (7)8质量、安全控制 (7)9经济效益分析 (7)10工程应用 (7)本工法是对原有工艺方法的提高和创新,在受力方式、动力源、可靠性、经济性等方面有新的进步。
1工法特点倒装法施工,改高处作业为地面作业。
改顶升方式为提升方式,使受力由受压改为受拉。
机械机构改为液压机构,出力大,机构小。
个别控制改为中央控制。
运动部分改润滑为无润滑。
改连续提升为步进提升,提升高度(理论上)不受限制。
改刚性受力为球面自位式弯矩卸载机构。
机械效率、体积重量、出力、安全等都较原施工方法提高。
2工艺原理倒装法原理金属圆柱形储罐主体由三部分组成:罐底、壁板、罐顶。
罐体高度主要由各节壁板形成。
正装法的程序是:罐底→各层壁板→罐顶。
罐体越来越高,必须高处作业。
倒装法的程序是:罐底→罐顶→上层壁板→提升→下层壁板→提升→各层壁板。
主体施工全部地面作业,不仅安全、工效高,而且节省了吊机、脚手架等费用。
罐顶和上层壁板的提升必须用胀圈。
胀圈按罐内径作为若干段,每两段间用千斤顶胀紧在罐壁上,并焊接筋板来保证胀圈向罐体的传力。
提升机构提升胀圈,则将罐顶及上层壁板升起。
焊完下层壁板再将胀圈装到下层壁板上。
重复工作,直至完成全部壁板施工。
液压提升原理动力来自中央控制台,其中包括电机、油泵、油箱、换向阀、安全阀、压力表、按扭盘、配油器、16组截止阀等。
高压油经软管送至双作用油缸,通过换向阀实现油缸的往复动作。
活塞杆是空心的,中间穿一提升杆。
在油缸的上、下各有一个自位单向卡头(是本局的专利技术,专利号:.8),在油缸往复运动时,可自动完成提升杆的步进式工作。
提升杆拉动滑板,滑板沿支架的轨道移动。
在滑板上装有两块托板,用托板提动胀圈,使罐体提升,实现倒装工艺要求。
滑板与支承架轨道间采用无润滑衬板。
支承架应有一定的高度、强度和刚度。
大型储罐的施工工法

大型储罐液压顶升、自动焊、倒装施工工法陕西化建工程有限责任公司中油吉林化建工程有限公司王智杰何丹杨峰斌李丽红1.前言随着我国经济的快速发展和人民生活水平的不断提高,能源消耗急剧增长,石油和成品油的需求剧增。
目前我国已变成石油进口大国,石油已成为国家重要的战略物资,它直接关系到我国的经济发展、社会稳定和国家安全,增加原油储备迫在眉睫,因此,我国对国家石油储备库和成品油库的建设给予了高度的重视。
大型立式钢制储罐是非常重要的储运设备,越来越多地被应用于原油、成品油等储运工程中,其中立式圆筒形拱顶储罐和浮顶储罐最为普遍。
因此,立式圆形储罐的制作安装也不断更新发展。
大型储罐的预制、罐体提升及焊接是储罐制安的主要工序,直接影响储罐制安的施工质量。
同时,储罐制安工作中,主要的工作量集中在焊接工序上。
在当今施工行业,自动焊技术已经渗入到储罐制安工艺中,但自动焊机以储罐“正装”为基准进行设计。
我公司在大型储罐制安中,为了减少高空作业量,减少脚手架的投入等,习惯于“倒装法”作业。
为此,我公司技术人员与焊机厂进行多次研讨,将适用于“正装法”的悬挂式“横焊机”改造成适用“倒装法”的轨道式“横焊机”,同时,在罐体提升过程中,为了更稳、更快,用“液压顶升”设备代替了原来的电动倒链。
将自动焊、液压顶升等先进的施工工艺融入到“倒装法”施工工艺之中,另外在自动焊方面采用自行研发的了“单面焊双面成型”技术。
本施工工艺,经过实践证明安全、可靠、先进。
罐体的焊接质量能够满足规范要求,同时克服了“正装法”的一些不足,是一项值得在同行业推广的施工工法。
2.工法特点2.1大型立式储罐主体制作安装方法有“正装法”和“倒装法”两种,本施工工法是以“倒装法”为基础研发的。
2.2本施工工法主要是将自动焊接技术及液压顶升技术应用于储罐的“倒装法”施工工艺中。
2.3本施工方法主要是将“正装法”的“埋弧横焊机”进行了改造,即从“悬挂式”改造成“轨道式”,使之与“倒装法”相适应。
储罐罐安装倒装方法

储罐罐安装倒装方法引言储罐作为一种常见的储存液体或气体的设备,广泛应用于石油化工、食品饮料、医药等行业。
在储罐的安装过程中,倒装是一种常用的施工方法。
本文将介绍储罐罐安装倒装的相关内容,包括倒装方法、倒装流程和注意事项等。
倒装方法储罐罐安装的倒装方法主要有以下几种:堆倒法堆倒法是将储罐放置在地面上,并使用吊车或起重机将储罐从底部侧翻到目标位置的一种方法。
该方法操作简单,适用于一般尺寸较小的储罐。
运输架倒装法运输架倒装法是在储罐底部安装运输架,然后使用吊车或起重机将储罐从底座上侧翻到目标位置的一种方法。
该方法适用于较大尺寸的储罐,能够提高安装效率。
吊梁倒装法吊梁倒装法是在储罐顶部安装吊梁,并通过吊车或起重机将储罐从顶部倒置到目标位置的一种方法。
该方法适用于较大尺寸和较重的储罐,但需要保证吊梁的安全性和稳定性。
倒装流程储罐罐安装的倒装流程一般包括以下几个步骤:1. 准备工作:根据倒装方法选择相应的设备和工具,检查设备是否正常运转,确保施工区域的安全。
2. 安装底座或运输架:根据倒装方法的不同,安装相应的底座或运输架,并进行固定和检查。
3. 安装吊梁:如果选择吊梁倒装法,需要在储罐顶部安装吊梁,并确保吊梁的安全和稳定。
4. 倒装过程:使用吊车或起重机将储罐从底部或顶部侧翻到目标位置,需要保持稳定,并确保施工人员的安全。
5. 定位和固定:倒装完毕后,对储罐进行定位和固定,确保储罐稳定和安全。
6. 检查和测试:对安装完毕的储罐进行检查和测试,检查其安装是否符合规范,保证其使用的安全性。
注意事项在进行储罐罐安装倒装时,需要注意以下几个事项:1. 安全第一:施工人员要戴好安全帽、安全鞋,并使用符合规范的吊车或起重机进行操作,确保施工人员的安全。
2. 合理分配重心:在倒装过程中,需要合理分配储罐的重心,并根据实际情况调整倒装角度,以减少倒装过程中的风险。
3. 保护储罐壁板和配件:在倒装过程中,需要采取措施保护储罐壁板和配件,避免受损和变形。
大型储罐液压顶升倒装施工工法(2)

大型储罐液压顶升倒装施工工法大型储罐液压顶升倒装施工工法一、前言大型储罐的制作和安装是工业项目中重要的环节之一,传统的安装方式需要大量的人力和时间,同时存在一定的安全隐患。
为了提高施工效率和安全性,大型储罐液压顶升倒装施工工法应运而生。
本文将详细介绍该工法的特点、适应范围、工艺原理、施工工艺、劳动组织、机具设备、质量控制、安全措施、经济技术分析和工程实例。
二、工法特点大型储罐液压顶升倒装施工工法具有以下几个特点:高效、安全、灵活。
相比传统的制作、安装方式,该工法能够大大缩短施工周期,减少人力投入,提高施工效率。
同时,在施工过程中,采用液压顶升倒装技术,增加了施工的安全性,减少了人员伤害的风险。
此外,该工法能够适应各类大型储罐的制作和安装,广泛应用于石油、化工、液化气等领域。
三、适应范围大型储罐液压顶升倒装施工工法适用于直立式、卧式、顶升式、碎片式等各种类型的大型储罐。
无论是钢质储罐还是混凝土储罐,该工法都能胜任。
四、工艺原理该工法通过液压顶升倒装技术来实现大型储罐的制作和安装。
首先,在施工现场安装并连接液压缸和支撑装置。
然后,在顶部安装储罐底板,并使用液压缸进行顶升。
当储罐底部离地面一定高度后,通过倒装机具进行翻转,将储罐翻倒至正确位置。
最后,完成储罐的各项安装和连接工作。
五、施工工艺该工法的施工过程分为以下几个阶段:场地准备,液压顶升和倒装,储罐连接和测试。
在场地准备阶段,需要进行场地清理和平整,确保施工现场的安全和清洁。
在液压顶升和倒装阶段,通过液压顶升和倒装机具将储罐翻转至正确位置。
在储罐连接和测试阶段,完成各项管路的连接和测试工作。
六、劳动组织大型储罐液压顶升倒装施工工法的劳动组织主要包括工程经理、工程师、操作工等。
工程经理负责施工计划的制定和协调;工程师负责施工过程的监督和技术支持;操作工负责施工机具和设备的操作和维护。
七、机具设备该工法所需的机具设备包括:液压顶升机具、倒装机具、吊车、钢管脚手架、焊接设备等。
十万方大型储罐倒装施工方案

十万方大型储罐倒装施工方案一、施工背景二、施工准备1.确定施工场地,并对场地进行平整、清理,确保没有障碍物和杂物。
2.对施工现场进行测量,确定施工机械的位置和储罐倒装的具体要求。
3.调集所需的施工机械和设备,如起重机、吊车等。
4.安排人员到场施工,包括机械操作人员、安全员等。
三、施工步骤1.检查储罐的结构完整性和表面的光洁度,确保储罐没有任何损坏和污染。
2.准备好大型起重机,并将其稳定固定在施工现场。
3.将储罐放置在起重机下方,并使用吊车将储罐抬升至合适的高度。
4.将储罐倾斜至适当的角度,并进行固定。
5.检查储罐的安全固定,确保不会出现任何移动和倾斜的情况。
6.检查施工现场的安全措施,确保施工人员和机械的安全。
7.完成储罐倒装施工后,进行清理和整理现场,确保没有遗留杂物和施工垃圾。
四、安全措施1.施工现场要设置专门的警示标识,并采取必要的封闭措施,防止外来人员进入。
2.在施工现场设置专门的交通指示牌,指示人员和机械的行进方向,确保施工现场的交通畅通。
3.施工人员要佩戴个人防护用品,包括安全帽、防护服、防护手套等。
4.机械操作人员要经过专门培训,并具备相应的资格证书。
5.施工过程中,要定期检查机械设备的完好性和安全性能,确保其正常运行。
六、施工效果评估通过以上步骤的施工,储罐的倒装工作能够顺利进行,施工现场秩序井然,施工人员和机械的安全得到了保障。
七、总结十万方大型储罐倒装施工方案的制定和实施,为大型储罐倒装施工提供了具体的指导,保障了施工的顺利进行和人员、设备的安全。
但在具体施工过程中,仍需根据实际情况进行具体操作,并严格遵守相关的安全规范和操作规程。
大型钢制圆筒式储罐的导链式倒装法施工技术

大型钢制圆筒式储罐 的导链式倒
装法施工技术
一 吴长贵 谷 波 邓卫国 朱勇昆 中国化学工程第 四建设公司 湖南岳阳 4 20 1 00 摘 要 导链 式倒装法是一种设备投资较少 、 施工方法简便、 施工质量稳定可靠 的方法 , 以往常用于 分析在 2 0 0 钢制储罐中采用 了导链 式倒装法取得了成功 。在类似 工程上有借鉴作用 。 0 0 m 关键词 导链式倒装法 大型钢制圆筒式储罐 原理 工艺流程
因为正装法施工 , 随着罐 体越来越 高 , 高空 作业 困难 , 很难保证
4 l油 工 设O5 2 化 建 l0 石 .
升 。当升到预定位置时 , 即可进行上 下圈壁 板之 间的组对 。当全 部 组对 、 焊接完毕后 , 再利 用导链装置 将涨 圈放下 , 重新设 置于
第 二 圈 壁板 下 口 ( 板 下 口应 留 出组 对 位 置 ) 然 后 再 提 升 罐 体 、 壁 ,
的典型工程 。以往采用导链式倒装法安装钢制立式储罐的多为
3 0m 0 0 以下 的 中小 型 储罐 , 用 于 2 0 0 这 样 大 型 的钢 制立 运 00 m
()充气顶升法虽说其工装成本要 比液压顶升法低, 2 但充气
顶 升法 的整 套 装 置 安 装 复 杂 , 节 繁 多 。特 别 是 每 次提 升 前 , 环 提 升 装置 的 回位 安 装都 要 花 费很 多 时 间 ,在 一 定 程 度 上 制 约 了 工 程 进 度 的 加 快 。 次 , 气 顶升 法 提 升 罐 体 是 利用 压 缩 空 气进 行 其 充 顶 升 的 , 体 在 上 升 过 程 中的 平 稳性 比 较难 以控 制 。另 外 , 气 罐 充
大型储罐液压顶升倒装施工技术
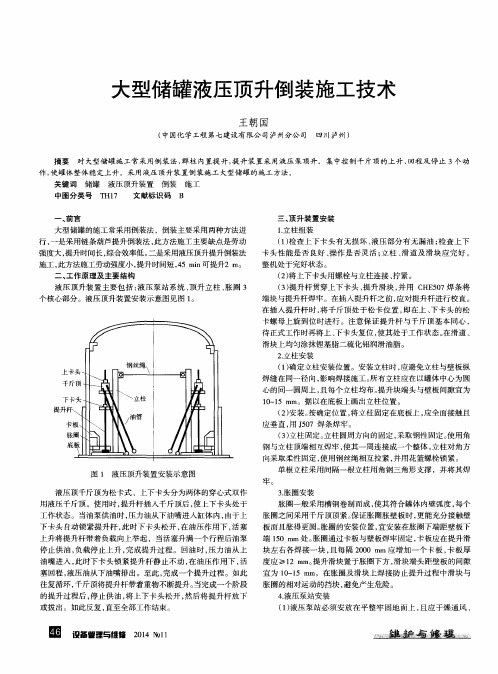
胀 圈的相对运 动的挡块 , 避免产生危险 。
4 . 液压泵站安装 ( 1 ) 液压泵站必 须安放在平整 牢固地面上 , 且应干燥通 风 、
田 设 备 管 理 与 维 修2 0 1 4 N o l l
j缝 盎 翅 一
高温渣 浆泵轴承故 障分析及处理
焊缝在同一径 向 , 影响焊接施工。 所有立柱应在 以罐体中心为圆 心的 同一圆周上 , 且每个立柱均布。 提升块端头与壁板间隙宜为 1 0 ~ 1 5 mm。据 以在底板上画出立柱位置 。
提
( 2 ) 安装 。 按确定位 置 , 将立柱固定在底板上 , 应全面接触且 应垂直 , 用J 5 0 7焊条焊牢。
二、 工 作 原 理 及 主 要结 构
( 1 ) 检查上下卡头有无损 坏 、 液压部分有无漏 油 ; 检查上下 卡 头性能是否 良好 、 操作是 否灵活 ; 立柱 、 滑道及 滑块应 完好 。 整机处于完好状态 。
( 2 ) 将 上 下 卡 头用 螺 栓 与立 柱 连 接 、 拧 紧。
卡螺母 上旋到位时进行 。注意保证提升杆 与千斤顶基本 同心 ,
待正式工作 时再将上 、 下卡头复位 , 使其处 于工作状 态。 在滑道 、 滑块上均匀涂抹锂基脂二硫化钼润滑油脂 。
2 . 立 柱 安 装
( 1 ) 确 定 立 柱 安 装 位 置 。安 装 立 柱 时 , 应 避 免立 柱 与壁 板 纵
大型储罐液压顶 升倒装施工技术
王朝 国
( 中国化 学工程 第七建设有 限公 司泸州分公 司 四川泸州)
摘要 关键词 对大型储罐施 工常采用倒装法 , 群柱 内置提升 , 提升装置采用液压 泵顶升 。集中控 制千斤顶的上升 、 回程 及停止 3个动 储罐 液压顶升装置 倒装 施工
大型钢制储罐液压提升倒装法施工工法(2)

大型钢制储罐液压提升倒装法施工工法大型钢制储罐液压提升倒装法施工工法一、前言大型钢制储罐在工业领域中扮演着重要的角色,而其施工过程中涉及到储罐的倒装与安装,是一个关键的环节。
大型钢制储罐液压提升倒装法施工工法作为一种先进的施工工艺,在现代化工程中得到了广泛应用,本文将对该工法的特点、适应范围、工艺原理、施工工艺、劳动组织、机具设备、质量控制、安全措施与经济技术分析进行详细介绍。
二、工法特点大型钢制储罐液压提升倒装法施工工法具有以下特点:1. 施工速度快:液压提升倒装技术使得储罐的倒装过程更加高效,大大缩短了施工周期。
2. 施工质量高:倒装法使得储罐在施工过程中减少了变形和应力集中的可能性,提高了储罐的使用寿命。
3. 施工安全性较高:液压倒装法能够实现储罐的稳定倒装,减少了倒装过程中的安全风险。
4.施工精确度高:倒装法能够精确控制液压力的大小,保证储罐倒装的平稳进行。
5. 施工成本相对较低:相对于传统的借助起重设备的倒装法,液压倒装法更加经济实用。
三、适应范围大型钢制储罐液压提升倒装法施工工法适用于各类规模较大的储罐倒装,可以广泛应用于石化、化工等行业中。
四、工艺原理大型钢制储罐液压提升倒装法施工工法是基于以下工艺原理:1. 液压原理:利用液压油将大型钢制储罐升起并倒装,通过液压系统控制液压力与速度,实现储罐的稳定倒装。
2. 倒装原理:储罐倒装可以使得罐底焊缝更容易进行焊接,同时减少变形可能性,提高施工质量。
五、施工工艺大型钢制储罐液压提升倒装法施工工艺主要包括以下阶段:1. 预处理阶段:包括施工场地的准备,对储罐进行清洗、除氧等处理,确保施工环境的洁净与安全。
2.铺垫阶段:放置铺垫物,为液压提升倒装提供良好的基础。
3. 提升阶段:利用液压系统将大型钢制储罐升空,通过倒装装置将储罐倒置,实现底部焊接。
4. 固定阶段:对储罐进行固定,防止其倾斜或下滑。
5. 检测与清理阶段:对倒装焊接部位进行检测,以确保焊缝质量;清理施工现场。
大型储罐倒装法
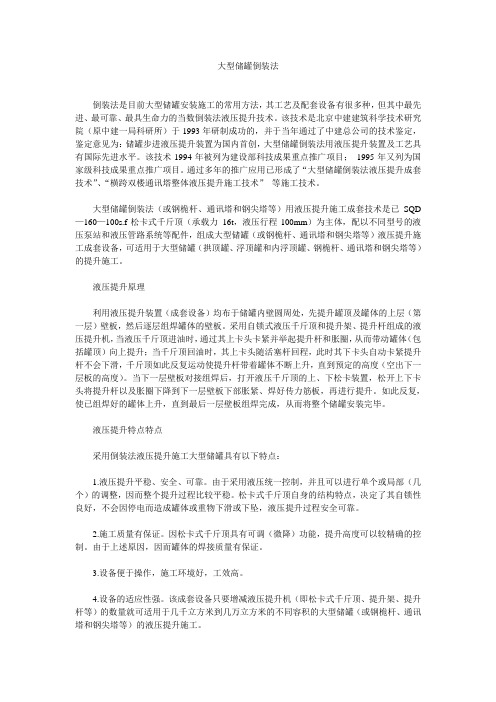
大型储罐倒装法倒装法是目前大型储罐安装施工的常用方法,其工艺及配套设备有很多种,但其中最先进、最可靠、最具生命力的当数倒装法液压提升技术。
该技术是北京中建建筑科学技术研究院(原中建一局科研所)于1993年研制成功的,并于当年通过了中建总公司的技术鉴定,鉴定意见为:储罐步进液压提升装置为国内首创,大型储罐倒装法用液压提升装置及工艺具有国际先进水平。
该技术1994年被列为建设部科技成果重点推广项目;1995年又列为国家级科技成果重点推广项目。
通过多年的推广应用已形成了“大型储罐倒装法液压提升成套技术”、“横跨双楼通讯塔整体液压提升施工技术”等施工技术。
大型储罐倒装法(或钢桅杆、通讯塔和钢尖塔等)用液压提升施工成套技术是已SQD —160—100s.f松卡式千斤顶(承载力16t,液压行程100mm)为主体,配以不同型号的液压泵站和液压管路系统等配件,组成大型储罐(或钢桅杆、通讯塔和钢尖塔等)液压提升施工成套设备,可适用于大型储罐(拱顶罐、浮顶罐和内浮顶罐、钢桅杆、通讯塔和钢尖塔等)的提升施工。
液压提升原理利用液压提升装置(成套设备)均布于储罐内壁圆周处,先提升罐顶及罐体的上层(第一层)壁板,然后逐层组焊罐体的壁板。
采用自锁式液压千斤顶和提升架、提升杆组成的液压提升机,当液压千斤顶进油时,通过其上卡头卡紧并举起提升杆和胀圈,从而带动罐体(包括罐顶)向上提升;当千斤顶回油时,其上卡头随活塞杆回程,此时其下卡头自动卡紧提升杆不会下滑,千斤顶如此反复运动使提升杆带着罐体不断上升,直到预定的高度(空出下一层板的高度)。
当下一层壁板对接组焊后,打开液压千斤顶的上、下松卡装置,松开上下卡头将提升杆以及胀圈下降到下一层壁板下部胀紧、焊好传力筋板,再进行提升。
如此反复,使已组焊好的罐体上升,直到最后一层壁板组焊完成,从而将整个储罐安装完毕。
液压提升特点特点采用倒装法液压提升施工大型储罐具有以下特点:1.液压提升平稳、安全、可靠。
大型钢制立式储罐的导链式倒装法施工
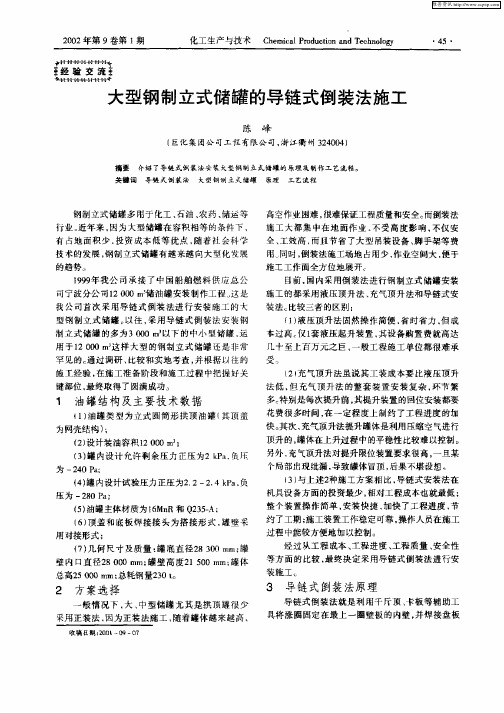
() 内设计 允许剩余压力正压为2ka负 压 3罐 P ,
为 一 4 a 2 0P ;
约 了工期 ; 施工装置工作稳定可靠, 操作人员在施工 过程 中能较 方便地 加以控 制 。 经过从工较 , 最终决定采用导链式倒装法进行安
装 施工 。
壁内 口直径2 0 m; 8 0m 罐壁高度2 0 i; 0 1 0B 罐体 5 n 总高2 0 m; 钢 量20t 500m 总耗 3 。
行 业 年来 , 近 因为 大型 储罐 在 容积 相 等的 条件 下 , 有 占地 面积 少 , 资 成 本 低 等优 点 , 着社 会 科 学 投 随 技 术的 发展 , 钢制 立式储 罐有 越 来越 向大型 化 发展 的趋 势 。 19 年我 公 司 承接 了 中 国船 舶 燃 料 供 应 总 公 99 司宁波分 公 司1 0 油 罐安 装制 作工 程 。 是 20 0m储 这 我 公 司首 次 采 用 导链 式 倒 装 法 进行 安 装施 工 的 大 型 钢 制立 式 储 罐 以往 , 用导 链 式 倒 装 法 安装 钢 采 制 立 式 储 罐 的 多为 300m 以下 的 中小 型储罐 , 0 ’ 运
用于1 0 200m 这样大型 的钢制立式储罐还是非常 罕 见 的 通过 调研 、 比较 和实 地 考查 , 根据 以往 的 并
施 工经验 , 施 工 准备 阶段 和施 工 过程 中把 握 好关 在 键部 位 , 终取得 了 圆满成 功 。 最
I 油罐结构及主要技术数据
十万方大型储罐倒装施工方案
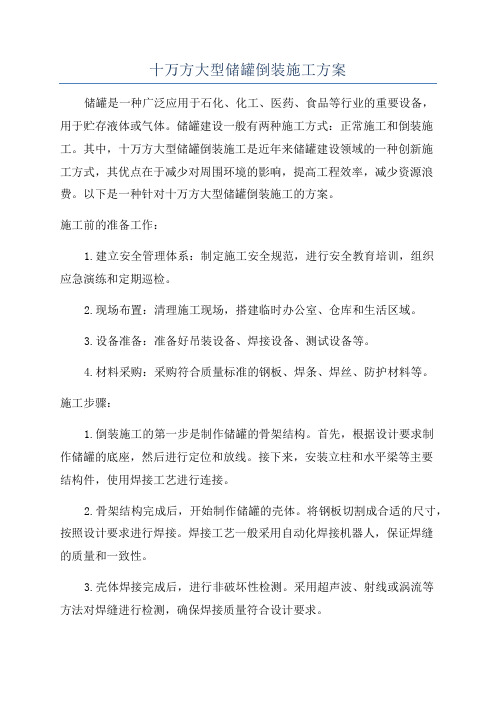
十万方大型储罐倒装施工方案储罐是一种广泛应用于石化、化工、医药、食品等行业的重要设备,用于贮存液体或气体。
储罐建设一般有两种施工方式:正常施工和倒装施工。
其中,十万方大型储罐倒装施工是近年来储罐建设领域的一种创新施工方式,其优点在于减少对周围环境的影响,提高工程效率,减少资源浪费。
以下是一种针对十万方大型储罐倒装施工的方案。
施工前的准备工作:1.建立安全管理体系:制定施工安全规范,进行安全教育培训,组织应急演练和定期巡检。
2.现场布置:清理施工现场,搭建临时办公室、仓库和生活区域。
3.设备准备:准备好吊装设备、焊接设备、测试设备等。
4.材料采购:采购符合质量标准的钢板、焊条、焊丝、防护材料等。
施工步骤:1.倒装施工的第一步是制作储罐的骨架结构。
首先,根据设计要求制作储罐的底座,然后进行定位和放线。
接下来,安装立柱和水平梁等主要结构件,使用焊接工艺进行连接。
2.骨架结构完成后,开始制作储罐的壳体。
将钢板切割成合适的尺寸,按照设计要求进行焊接。
焊接工艺一般采用自动化焊接机器人,保证焊缝的质量和一致性。
3.壳体焊接完成后,进行非破坏性检测。
采用超声波、射线或涡流等方法对焊缝进行检测,确保焊接质量符合设计要求。
4.进行表面处理和防腐涂层施工。
对焊接缝进行抛丸清理,去除焊渣和氧化物,然后进行底漆、中漆和面漆的施工。
5.安装储罐的附件设备,如进出口管道、排放管道、支撑架等。
进行管道的焊接和连接,确保管道畅通、稳固。
6.进行压力测试和泄漏测试。
使用泄漏检测仪器对储罐的密封性、抗压性进行测试,确保储罐的安全性。
7.进行储罐的竖立和定位。
使用起重机将储罐吊装至指定位置,并进行调整和固定。
8.完成施工后的清理工作。
清理施工现场,回收和妥善处理废弃材料和废水等。
施工注意事项:1.施工过程中,要严格执行安全规范,确保施工人员的人身安全。
2.施工过程中,要根据设计和施工文件进行质量控制和检验,确保施工质量。
3.在储罐竖立和定位时,要确保起重机的稳定性和承载能力,防止因储罐倾倒而导致事故。
大型储罐液压提升倒装法施工技术

论大型储罐液压提升倒装法施工技术摘要本文主要介绍了大型储罐液压提升倒装工艺原理、施工工序、提升架和胀圈的设计及液压千斤顶数量的确定,归纳了该施工方法独具的优点和推广应用前景。
主题词油罐液压传动装置安装技术1. 前言随着我国石油化工工业的不断发展,国内对大型储罐的需求量不断增加。
多年来储灌主要采用中心柱法、气吹法、水浮正装法进行储罐施工,由于储罐逐渐向大型化发展,有些施工技术已不能满足施工要求,在大型储罐的建造中正在用液压提升倒装法取代以往采用的其它施工方法。
液压提升倒装法的技术要求并不苛刻,安全可靠、施工手段用料少、安装速度快、对储罐的各种建造参数易于调控。
避免了气吹法出现的冒顶和吹偏事故的风险,是目前比较理想一种储罐建造施工新方法。
2. 工艺原理和施工工序2.1、液压提升工艺原理利用均布在储罐内侧的提升架,在其上安装有起重作用的上、下限位单向卡头,其中上卡头带有液压油缸,动力来自中央控制台,高压油经软管送至双座拥油缸(上卡头),通过换向阀实现油缸的往复动作。
活塞干是空心的,中间穿有钢制提升杆,在油缸往复运动时,可自动完成提升杆的步进式工作。
提升杆带动提升架上的滑板,滑板沿提升架上的轨道移动,在滑板上装有两开托板,用托板上提与罐壁下部临时固定的胀圈,是第一圈壁板随胀圈上升岛预定高度,组焊第二圈壁板,然后将上、下卡头松开,胀圈降至第二圈壁板下部胀紧、固定,如此往复,使罐体提升,实现倒装法施工工艺要求。
2.2、松卡式液压千斤顶工作原理松卡式液压千斤顶工作原理就是由一个液压泵带动多个立柱上的千斤顶,千斤顶中间有一个圆钢芯(直径约为40mm,长为3m,圆钢下端有一个钢托,和圆钢连在一起,靠它托起壁板),千斤顶卡住圆钢,带动圆钢向上升,每升一次的行程为100mm(根据不同的型号,行程有所不同),每一次行程结束时,千斤顶里有一个锁紧圆钢的装置,不至于圆钢下落,也就是说壁板不下落,千斤顶再回到原来的状态,再起升,再回落,往复运动,直至把圆钢提升到我们需要的高度(环缝对口状态)。
储罐倒装法施工工艺
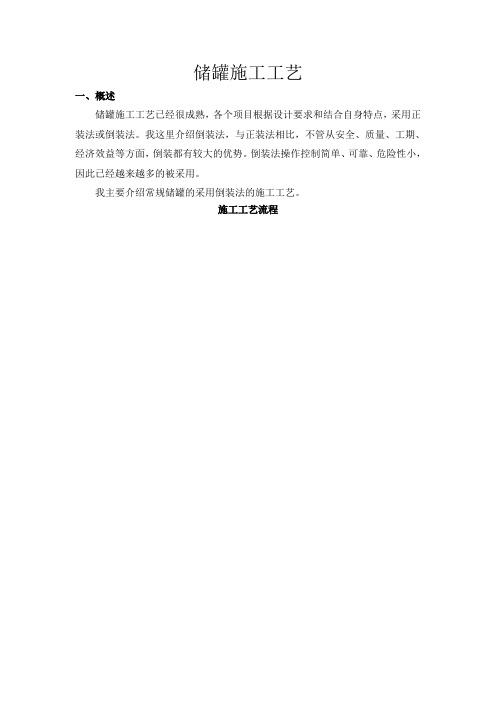
储罐施工工艺一、概述储罐施工工艺已经很成熟,各个项目根据设计要求和结合自身特点,采用正装法或倒装法。
我这里介绍倒装法,与正装法相比,不管从安全、质量、工期、经济效益等方面,倒装都有较大的优势。
倒装法操作控制简单、可靠、危险性小,因此已经越来越多的被采用。
我主要介绍常规储罐的采用倒装法的施工工艺。
施工工艺流程二、施工准备技术准备贮罐施工前,应具备有施工图和设计有关文件、施工单位编制并经建设单位、监理审批的施工方案、原材料及配件的质量证明书、国家或行业的施工及验收规范。
施工前,有关人员应熟悉图纸及有关技术文件、法规,通过图纸会审,明确贮罐建设工程相关专业配合要求。
贮罐的焊接技术人员应根据相关规范及焊接工艺要求进行焊接施工。
贮罐施工技术人员应根据现场实际情况和施工技术文件,编制有针对性的、切实可行的施工技术方案及作业指导书,并进行相应的技术交底。
明确贮罐安装的质量标准及检验方法,编制质量保证措施,准备各种计量器具及施工记录。
预制加工前要根据图纸、材料规格及施工规范的要求绘制贮罐排版图,经建设单位、监理单位审批后方可作为施工依据。
●罐底排版应考虑下列要求:(1)底板中幅板排版直径应考虑罐底边缘板焊接收缩量比设计直径大-2/1000。
罐底边缘板外圆直径加收缩量。
(2)罐底边缘板宽度按设计图纸尺寸。
罐底由中幅板和边缘板组成,边缘板的径向宽度不得小于规范要求,在罐壁内侧至中幅板收缩缝之间不得小于650mm,伸出罐壁外侧不得小于50mm。
并应在圆周方向均匀布置。
做好基础检查验收,基础应符合设计文件和规范要求;做好基础检查验收记录。
基础验收合格具备施工条件,经建设单位同意方可进行罐底施工。
施工现场准备施工场地应设置:材料、半成品存放场地;加工场地、办公设施等。
场地应平整,道路应畅通,临时用水、用电线路应按要求敷设。
制作有关检测样板、模板,按规定制作内外弧板,拱顶板模具及角钢圈模具。
储罐在预制、组装及检验过程中所使用的样板弦长不得小于2m,直线样板的长度不得小于1m,测量角焊缝的变形的弧形样板,其弦长不得小于1m。
5000t浓硫酸贮罐倒装施工工法
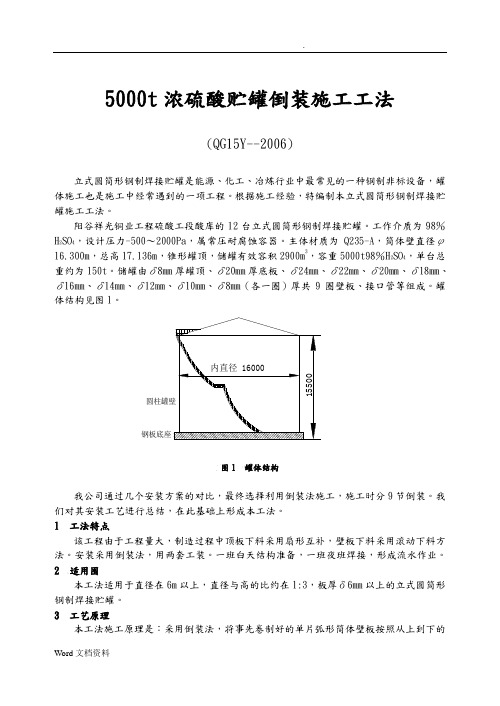
5000t浓硫酸贮罐倒装施工工法(QG15Y--2006)立式圆筒形钢制焊接贮罐是能源、化工、冶炼行业中最常见的一种钢制非标设备,罐体施工也是施工中经常遇到的一项工程。
根据施工经验,特编制本立式圆筒形钢制焊接贮罐施工工法。
阳谷祥光铜业工程硫酸工段酸库的12台立式圆筒形钢制焊接贮罐。
工作介质为98%H2SO4,设计压力-500~2000Pa,属常压耐腐蚀容器。
主体材质为Q235-A,筒体壁直径φ16.300m,总高17.136m,锥形罐顶,储罐有效容积2900m3,容重5000t98%H2SO4,单台总重约为150t。
储罐由δ8mm厚罐顶、δ20mm厚底板、δ24mm、δ22mm、δ20mm、δ18mm、δ16mm、δ14mm、δ12mm、δ10mm、δ8mm(各一圈)厚共9圈壁板、接口管等组成。
罐体结构见图1。
钢板底座图1 罐体结构我公司通过几个安装方案的对比,最终选择利用倒装法施工,施工时分9节倒装。
我们对其安装工艺进行总结,在此基础上形成本工法。
1 工法特点该工程由于工程量大,制造过程中顶板下料采用扇形互补,壁板下料采用滚动下料方法。
安装采用倒装法,用两套工装。
一班白天结构准备,一班夜班焊接,形成流水作业。
2 适用围本工法适用于直径在6m以上,直径与高的比约在1:3,板厚δ6mm以上的立式圆筒形钢制焊接贮罐。
3 工艺原理本工法施工原理是:采用倒装法,将事先卷制好的单片弧形筒体壁板按照从上到下的顺序在现场分节组装成一圈,提升一定高度后,接着组装下一圈,并与上一圈焊接,再提升一定高度,再组装下一圈,依此往复,直到整个筒体现场组装完成。
4 施工工艺流程底板组装→锥顶支架组装→提升装置安装→顶圈壁板及顶圈包边角钢组装→1、2圈壁板组装→胀圈安装→提升→3圈围板结构焊接检验→胀圈放下后安装→提升→4圈围板结构焊接检验→至最后共9圈→辅件安装→检验。
5 操作要点本工程罐体倒装时最大起重量约为120t。
在现场共设置16根扒杆,根据《起重机械为1.1,稳定系数K2为1.1后,算出单根立柱的最大手册》每根扒杆立柱取动载荷系数K1πEI/(μl)2计算P理论受压, μ取一端固定,一端起重量P实际受压。
大型储罐室内倒装施工工法 (2)

大型储罐室内倒装施工工法一、前言大型储罐室内倒装施工工法是一种现代化、高效率、高安全性和高质量的施工工法,是在传统的储罐施工工程中逐步形成的一种新型建筑技术,具有广泛的适用范围和不可替代的优越性。
二、工法特点大型储罐室内倒装施工工法具有如下几个特点:1、高效率:该工法在施工过程中,采用全封闭、全自动化的施工方式,用专业的机器设备实现同步的施工,提高了施工速度,缩短了施工周期;2、高质量:该工法施工过程中采用全程质量控制和全程检验制度,保证了施工过程中的每一个环节都能被严格把控,从而保证了施工质量;3、高安全性:该工法在施工过程中,采用全封闭、全自动化的施工方式,有效的解决了传统施工过程中的安全隐患问题;4、适用范围广:该工法适用于各种类型的储罐,而且在施工的过程中可以实现高效、快速、简便、安全的施工;5、故障率低:该工法采用先进的机器设备,可以降低人力投入,减少了人为操作的失误率,从而有效地提高了施工质量和效率。
三、适应范围该工法适用于各种类型的储罐,包括常压、低温、低压、高温、高压等类型的储罐,无论是石化、化工、制药还是粮食等行业的储罐,都可以使用该工法施工。
四、工艺原理大型储罐室内倒装施工工法主要是通过对施工工法与实际工程之间的联系、采取的技术措施进行具体的分析和解释,让读者了解该工法的理论依据和实际应用。
1、核心机器设备该工法的核心机器设备是倒装施工机器人,通过该机器人的作用,可以实现罐体内外壁的平滑喷涂、衬里涂装、填充物安装等施工任务;2、施工操作流程该工法主要包括施工前期准备、机器设备安装与调试、施工过程、施工质量检验等施工环节。
其中施工过程包括罐体内外壁的平滑喷涂、衬里涂装、填充物安装等工作,通过机器设备的操作实现同步施工,提高施工效率;3、施工质量控制该工法施工过程中,采用全程质量控制和全程检验制度,在每一个施工环节都进行详细的监测和检验,及时发现施工过程中的问题,保证施工质量;4、施工安全要求该工法重视施工安全问题,在施工过程中坚持人员防护、机器设备安全等方面的措施,实现安全施工。
大型储罐液压提升倒装工法汇总

大型储罐液压提升倒装施工工法目录1. 前言-------------------------------------------------------------------12. 施工工艺及操作要点-----------------------------------------------------23. 施工计划与劳动力组合--------------------------------------------------104. 机具配备--------------------------------------------------------------125. 质量控制--------------------------------------------------------------136. 安全技术措施----------------------------------------------------------147. 技术经济分析----------------------------------------------------------168.应用实例---------------------------------------------------------------161. 前言大型储罐制作安装工程,液压提升倒装法施工工艺已被施工单位广泛应用。
2004年,我公司购置了一套SQD-160型罐体液压装置,为在公司范围内推广应用,特编制本工法。
基本原理:在储罐组焊过程中,利用液压提升装置均布于储罐内壁圆周处,提升罐体壁板及罐顶,逐层组焊储罐壁,采用行程放大式液压提升机和中心控制盘组成的液压提升系统,工作时,提升机上的油泵带动液压提升机顶轴不断上升,绷紧钢丝绳,直到顶定高度,当下一层壁板对接后,液压油缸将胀圈下降到下一层壁板下部胀紧,焊好限位筋板,如此反复,使已组焊好的罐体上升,直到最后一带壁板焊完。
- 1、下载文档前请自行甄别文档内容的完整性,平台不提供额外的编辑、内容补充、找答案等附加服务。
- 2、"仅部分预览"的文档,不可在线预览部分如存在完整性等问题,可反馈申请退款(可完整预览的文档不适用该条件!)。
- 3、如文档侵犯您的权益,请联系客服反馈,我们会尽快为您处理(人工客服工作时间:9:00-18:30)。
大型储罐施工工法1、前言钢油罐有立式(包括拱顶式和浮顶式圆筒形)、球壳式(球形)和卧式(圆筒形)。
立式拱顶油罐由球冠形的罐顶及立式圆柱形罐壁所构成,主要用于储存介质为不易挥发油品,如柴油及相似类油品。
立式圆筒形拱顶钢油罐。
容量一般在一万立方米以下。
壁板采用套筒式连接(贴角焊缝)。
施工时常用倒装法(从罐顶开始,自上而下逐层安装罐壁,并用风机送风使罐体上升)。
与正装法(从罐壁底圈板开始,自下而上逐层安装罐壁)比较,减少了高空作业。
此工程原料槽区共11个罐体,容积均为4600m³,成品槽区共10个槽,其中2000 m³5个,1000 m³3个,500 m³2个。
原料槽(含内部蛇形加热管)总重1100余吨,成品槽(含内部蛇形加热管)总重600余吨。
2、工法特点2.1工艺技术先进、确保施工质量由于此工程罐体直径达19米,高度为16米。
储罐施工焊接量大、板材薄,壁板焊接易变形,要投入足够的具有储罐施工经验的焊工及先进的焊接设备,才能保证焊接质量及施工工期。
罐体壁板采用钢板搭接焊接连接,因此对罐体壁板及罐体同心度要求极高。
因此本工法在罐体的底板中心设置永久性中心点来控制罐体的椭圆度及壁板垂直度,所有的椭圆度测量依照该控制点展开。
在罐体基础上均匀设置4个控制点来控制罐体安装完成后盛水沉降观测。
2.2施工工序优化、缩短工期、降低成本此工程采用倒装法进行安装作业,倒装法是目前大型储罐安装施工的常用方法,其工艺及配套设备有很多种,但其中最先进、最可靠、最具生命力的当数倒装法液压提升技术。
3、适用范围此工法可适用于几千立方米到几万立方米的不同容积的大型储罐的液压提升施工。
不仅可应用新储罐的安装施工,也可用于旧储罐的改造施工,同时还可用于高层建筑的钢桅杆或钢尖塔和通讯塔等的液压提升施工。
4、工艺原理及特点4.1、倒装液压提升工艺原理液压提升利用液压提升装置(成套设备)均布于储罐内壁圆周处,先提升罐顶及罐体的上层(第一层)壁板,然后逐层组焊罐体的壁板。
采用自锁式液压千斤顶和提升架、提升杆组成的液压提升机,当液压千斤顶进油时,通过其上卡头卡紧并举起提升杆和胀圈,从而带动罐体(包括罐顶)向上提升;当千斤顶回油时,其上卡头随活塞杆回程,此时其下卡头自动卡紧提升杆不会下滑,千斤顶如此反复运动使提升杆带着罐体不断上升,直到预定的高度(空出下一层板的高度)。
当下一层壁板对接组焊后,打开液压千斤顶的上、下松卡装置,松开上下卡头将提升杆以及胀圈下降到下一层壁板下部胀紧、焊好传力筋板,再进行提升。
如此反复,使已组焊好的罐体上升,直到最后一层壁板组焊完成,从而将整个储罐安装完毕。
4.2、倒装法液压提升特点1)液压提升平稳、安全、可靠。
由于采用液压统一控制,并且可以进行单个或局部(几个)的调整,因而整个提升过程比较平稳。
松卡式千斤顶自身的结构特点,决定了其自锁性良好,不会因停电而造成罐体或重物下滑或下坠,液压提升过程安全可靠。
2)施工质量有保证。
因松卡式千斤顶具有可调(微降)功能,提升高度可以较精确的控制。
由于上述原因,因而罐体的焊接质量有保证。
3)设备便于操作,施工环境好,工效高。
4)设备的适应性强。
该成套设备只要增减液压提升机(即松卡式千斤顶、提升架、提升杆等)的数量就可适用于几千立方米到几万立方米的不同容积的大型储罐(或钢桅杆、通讯塔和钢尖塔等)的液压提升施工。
液压泵站可根据实际工况,设置在合理位置。
对于大型储罐而言,液压泵站可置于罐体内,也可置于罐外或两个罐体中间(当两台罐体安装由一台泵站控制制时)进行施工控制。
液压泵站分手动和自控两种,其施工适应性强、技术性能价格比优良的特点十分明显。
5)工期短、成本低、经济效益好。
由于成套设备的现代化程度高,提升速度快,因而施工成本低,经济效益好。
5、施工主要程序及控制要点5.2、操作要点5.2.1预制部分:1、底板预制程序1) 底板中幅板制作尺寸和边缘板制作尺寸按底板排板图要求。
①除弧线外圆外,其他边全部采用半自动切割机进行切割(含坡口),边缘板两头坡口均为30°,不留钝边;②每座罐预留二块边缘板只加工一端坡口,另一端暂不加工坡口作调节尺寸误差用。
2) 预制好的底板要进行防腐,每块板边缘留50 mm不刷涂料。
2、壁板制作程序1) 壁板制作在预制场平台上进行。
2) 壁板制作坡口角度及钝边应符合图纸中的要求。
3) 壁板可采用直角法对钢板取直角,尺寸的允许偏差,应符合下表的规定:4) 壁板卷制后,应立放在平台上用样板检查,垂直方向用直线样板检查,其间隙不得大于2 mm样板检查,水平方向上用弧形样板检查,其间隙大于4 mm。
5) 每座罐每圈壁板均有一块板的一头不用切割及开坡口,留到现场安装时量准尺寸再下料。
6) 壁板制作好后,应对每块板根据排板图上的编号用白色油漆在钢板上做好标记。
7) 制作合格后的壁板应放在弧形胎具上,在中间运输同样使用胎具。
3、盘梯分段制作程序1) 盘梯分段制作先按图纸尺寸将盘梯侧板下好料,然后在侧板内表面将每块踏步板位置划好线。
2) 将盘梯侧板在预制平台上侧立固定好,接预先划好的线组对踏步板,整个盘梯从中间分开两段预制,全部点固焊好后再施焊。
4、顶板预制1) 罐顶瓜皮板,采取先拼板后下料形式(另绘制下料图),瓜皮板本身采取对接焊缝。
2) 下料时,每块顶板中部的宽度要确保成形后能满足设计要求的搭接量。
3) 下料时要求两对角线之差的绝对值不大于5mm,并逐一编号标记,作好原始记录。
4) 每台罐瓜皮板预制前需制作至少1个专门胎具,以便顶板的成型。
5) 瓜皮板筋按图纸要求施工,筋板应调平调直,按图要求滚圆,筋板间采用搭接连接,搭接长度为筋板宽度的两倍。
6) 成形后的瓜皮板用弦长为2m的弧形样板检查核准,间隙不大于10mm,在运输过程中要防止变形,吊装时采用多吊点起吊。
7) 中心顶板制作时直径比图纸尺寸放大100mm。
5、包边角钢、加强圈预制1) 包边角钢、加强圈等先按4根一排拼接点焊好,再利用滚板机进行滚弧,用核准的弧形样板检查,然后在平台上用千斤顶校准弯曲弧度,采用弦长为2m的弧形样板检查,间隙不能大于4mm。
2) 每根包边角钢两端至少要割除150mm长,才能保证安装时接头处的圆弧过渡。
3) 构件预制要求翘曲度≤L/1000(L为构件长度),滚圆后与弧形样板间隙≤2mm。
6、焊接H型钢预制1) 按拱顶半径进行放样、下料。
用弧形样板检查腹板的弧度,偏差不能超过1mm。
超过误差范围的应先进行矫正后才能组对。
2)在预制平台上装好卡具后组对H型钢腹板和翼板,点焊完成后用卡具卡紧型钢后按两个焊工从中间往两边分段退焊。
3)焊接完成后检查成型情况,对变形的地方用火焰加热进行矫正。
5.2.2安装顺序底板安装→顶圈壁板安装→顶部包边角钢安装→顶板安装→倒数第二圈壁板安装→胀圈及提升装置安装→其他各圈壁板安装→底板收尾→盘梯、平台栏杆安装→附件的开孔及安装→充水试验→防腐(面漆)1、罐底安装1) 油罐基础经复验合格,底板防腐经甲方认可合格后进行安装。
2) 基础放线在基础上放出中心线,并划出边缘板外缘的圆周线。
弧线应用样板划出(样板弧长2 m)。
然后按排板方位划出边缘板对接缝位置线。
3) 铺设边缘板分两边对称铺设,注意对接缝点焊上垫板。
对接缝间隙为外窄(宜为6~7 mm)内宽(宜为8~12 mm)的不等间隔隙。
每台罐留有两块活动板到最后按实际尺寸下料。
4) 铺设中幅板中幅板的铺设,从中心开始向两边进行。
一般应先铺长条形板,再铺设龟甲板,三板搭接处注意按图纸或规范要求切角。
5) 罐底焊接罐底焊接必须严格按焊接技术措施进行,先焊中幅板,后焊边缘板;先焊短缝,后焊长缝;焊工均布,隔缝焊接,分段退焊,严禁一遍成型。
罐底收缩缝应在底圈壁板和罐底板之间的角缝施焊完后才能进行。
6) 探伤及试漏A)厚度大于和等于10mm的罐底边缘板,每条对接焊缝的外端300mm的范围内应进行射线探伤;厚度为6~9mm的罐底边缘板,每个焊工施焊的焊缝,应按上述方法至少抽查一条。
B) 三层钢板搭接部分接头焊缝的根部焊道焊接完后沿三个方向各300mm范围内进行渗透检验,全部焊完后,再进行渗透检测。
C) 底板焊接及探伤工作完成以后,所有焊缝应采用真空试漏法对焊缝进行严密性检查,试验负压值不能低于53Kpa,无渗漏为体格。
2、顶圈壁板安装1) 考虑焊接收缩量和罐底的坡度,罐壁板的放线内半径R应比设计值大10mm。
2) 在罐底上放线找出罐底板中心点,划出十字线,按直径在罐底上画出圆周线并打上样冲眼。
划圆周线时用弧形样板划圆弧线。
3) 在罐底板上沿圆周方向每隔600mm左右焊接一个壁板临时水平支撑,支撑用钢管φ159×8加钢板δ8制作,高度为400mm。
以便施工人员进出储罐并且保证罐内通风。
并且在支座上焊接δ6×30×50的限位档板。
见下图:4) 将壁板吊至安装位置后用卡具打紧,并在内壁焊上调节斜撑(如图-1所示),每块板设置三个调节斜撑。
a.调节专用斜撑b.固定壁板专用斜撑图—1 顶圈壁板调整、固定示意图5) 通过专用卡具调整纵缝间隙为2~4mm,通过调节斜撑调整罐壁板垂直度及上口水平度。
先找正一块确保其垂直度,水平度满足要求后以此板作基准调整其他板。
整圈板调整完以后,再复测一次纵缝间隙,壁板垂直度,上口水平度,然后按图-1所示将壁板固定,每块板分别固定两板头(离立缝1 m)和板中三处。
注意围板前先将罐底板垫平,并用水准仪测量其水平度,其最大水平度偏差应不大于6 mm。
6) 壁板调整好以后进行下列检测:①纵缝接头间隙检查:用塞尺(或焊缝检验尺)检查,每条纵缝检查上、中、下三处,间隙为2~4 mm。
②罐壁上口水平度检查:每块板中间处,用水准仪检测,相邻两板的不平度不应大于2 mm,任意两点的最大不平度不应大于6 mm。
③壁板垂直度检查。
每块测两板头和中间三处,为了防止风的影响,线坠浸入装满水的铁桶内,测量的垂直度允许偏差3 mm。
7)立缝焊接。
焊前在每条焊缝内侧分别焊上三块圆弧型的抗变形板(板厚为δ14),并调整好圆弧度。
8)顶圈壁板安装情况检查。
①内半径检查8个点,在离罐底1 m高的位置用钢卷尺测量,当储罐直径D≤12.5m时,其半径允许偏差±13 mm,当储罐直径12.5<D≤45m时,其半径允许偏差±19mm。
②垂直度检查每块板测2个点,垂直度允许偏差3 mm。
③角变形检查,组装焊接完以后,用2 m长的弧形样板检查每条纵缝上、中、下三处,凹凸度不大于12 mm。
罐壁的局部凹凸变形应平缓,不得有突然起伏且凹凸度不大于15 mm。
④上口水平度检查,每块板用水准仪测量板中间,不平度不应大于6 mm。