储罐倒装法施工工艺
储罐气吹顶升倒装施工工法

可编辑修改精选文档,希望能帮到您Q B中国石化集团企业(通用工艺)标准第四建设公司★静设备工程卷★FCC/TS04.14-13储罐气吹顶升倒装法通用施工工艺2006-12-20发布 2007-01-01实施中国石化集团第四建设公司技术处发布储罐气吹顶升倒装通用施工工艺1 适用范围本工法适用于容积为3000m3到10000m3的立式圆筒形拱顶钢制焊接储罐的施工。
2 引用文件a)《立式圆筒形钢制焊接储罐施工及验收规范》GB50128-2005;b)《钢结构工程施工质量验收规范》GB50205-2001;c)《石油化工立式圆筒形钢制储罐施工工艺标准》SH3530-2001;d)《承压设备无损检测》JB/T4730.1-2005~JB4730.6-2005;e)《现场设备、工业管道焊接工程施工及验收规范》GB50236-2001;f)《石油化工施工安全技术规程》SH3505-1999。
3 施工准备3.1施工图纸审核3.2到货钢材检验a)到货钢材及配件必须有出厂合格证、质量证明书;b)到货钢板表面不得有气孔、裂纹、夹渣等现象。
钢板表面锈蚀深度不得超过0.5mm;c)焊接材料应具备合格证明书,当对焊材质量有怀疑时应对焊材成分进行复验;d)施工用胎具、机具:加减丝、千斤顶、倒链、砂轮机、真空箱、水泵的准备。
4 施工工艺4.1总体施工方案a)在现场铺设一个平台,也可选择已有的车间厂房,准备好相关的设备、机具,进行工厂化的预制,对成品和半成品严格检验,为保证现场的安装质量创造条件;b)需整体热处理的板采用炉内热处理的方式,不需要整体热处理的管口可在安装完后在现场进行热处理;c)利用鼓风机进行气吹顶升安装罐壁板,主体安装完成后进行附件的安装和上水试验。
4.2施工工艺流程施工工艺流程见下页:b)排版直径一般放大0.1%,罐底排版时,边角异形板与边缘板间留100mm的搭接余量。
中幅板的短边尺寸不得小于700mm,所有相邻焊缝的距离不小于300mm;c)罐底板的预制可以采用机械加工,也可以采用氧-乙炔焰切割加工。
拱顶储罐倒装法施工工艺流程

拱顶储罐倒装法施工工艺流程下载温馨提示:该文档是我店铺精心编制而成,希望大家下载以后,能够帮助大家解决实际的问题。
文档下载后可定制随意修改,请根据实际需要进行相应的调整和使用,谢谢!并且,本店铺为大家提供各种各样类型的实用资料,如教育随笔、日记赏析、句子摘抄、古诗大全、经典美文、话题作文、工作总结、词语解析、文案摘录、其他资料等等,如想了解不同资料格式和写法,敬请关注!Download tips: This document is carefully compiled by theeditor.I hope that after you download them,they can help yousolve practical problems. The document can be customized andmodified after downloading,please adjust and use it according toactual needs, thank you!In addition, our shop provides you with various types ofpractical materials,such as educational essays, diaryappreciation,sentence excerpts,ancient poems,classic articles,topic composition,work summary,word parsing,copy excerpts,other materials and so on,want to know different data formats andwriting methods,please pay attention!拱顶储罐倒装法施工工艺流程详解拱顶储罐作为一种常见的大型储罐,其建设过程中的施工工艺至关重要。
大型储罐施工工法(倒装法安装)8552
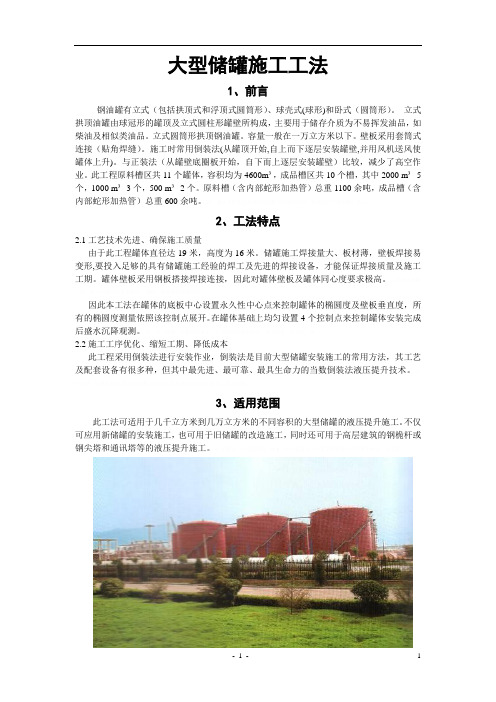
大型储罐施工工法1、前言钢油罐有立式(包括拱顶式和浮顶式圆筒形)、球壳式(球形)和卧式(圆筒形)。
立式拱顶油罐由球冠形的罐顶及立式圆柱形罐壁所构成,主要用于储存介质为不易挥发油品,如柴油及相似类油品。
立式圆筒形拱顶钢油罐。
容量一般在一万立方米以下。
壁板采用套筒式连接(贴角焊缝)。
施工时常用倒装法(从罐顶开始,自上而下逐层安装罐壁,并用风机送风使罐体上升)。
与正装法(从罐壁底圈板开始,自下而上逐层安装罐壁)比较,减少了高空作业。
此工程原料槽区共11个罐体,容积均为4600m³,成品槽区共10个槽,其中2000 m³5个,1000 m³3个,500 m³2个。
原料槽(含内部蛇形加热管)总重1100余吨,成品槽(含内部蛇形加热管)总重600余吨。
2、工法特点2.1工艺技术先进、确保施工质量由于此工程罐体直径达19米,高度为16米。
储罐施工焊接量大、板材薄,壁板焊接易变形,要投入足够的具有储罐施工经验的焊工及先进的焊接设备,才能保证焊接质量及施工工期。
罐体壁板采用钢板搭接焊接连接,因此对罐体壁板及罐体同心度要求极高。
因此本工法在罐体的底板中心设置永久性中心点来控制罐体的椭圆度及壁板垂直度,所有的椭圆度测量依照该控制点展开。
在罐体基础上均匀设置4个控制点来控制罐体安装完成后盛水沉降观测。
2.2施工工序优化、缩短工期、降低成本此工程采用倒装法进行安装作业,倒装法是目前大型储罐安装施工的常用方法,其工艺及配套设备有很多种,但其中最先进、最可靠、最具生命力的当数倒装法液压提升技术。
3、适用范围此工法可适用于几千立方米到几万立方米的不同容积的大型储罐的液压提升施工。
不仅可应用新储罐的安装施工,也可用于旧储罐的改造施工,同时还可用于高层建筑的钢桅杆或钢尖塔和通讯塔等的液压提升施工。
4、工艺原理及特点4.1、倒装液压提升工艺原理液压提升利用液压提升装置(成套设备)均布于储罐内壁圆周处,先提升罐顶及罐体的上层(第一层)壁板,然后逐层组焊罐体的壁板。
十万方大型储罐倒装施工方案

十万方大型储罐倒装施工方案在大型储罐倒装施工中,施工方案的合理性和可行性对整个工程的顺利进行至关重要。
本文将针对十万方大型储罐倒装施工提供详细的方案,确保施工过程安全、高效、顺利进行。
一、前期准备工作在施工前,首先需要对施工现场进行详细的勘察和测量,确保施工现场的平整度和承重能力满足倒装工艺的要求。
同时,需要对施工人员进行专业的培训和安全教育,确保他们能够熟练操作施工设备并严格遵守安全操作规程。
二、施工工艺流程1. 现场搭设支撑架首先需要在储罐底部搭设稳固的支撑架,以确保储罐倒装过程中能够保持稳定。
支撑架的选择和布置需要根据储罐的具体结构和重量进行合理设计。
2. 安装起重设备在支撑架搭设完毕后,需要安装起重设备,如起重机械或吊车等。
起重设备的选择需要考虑到储罐的重量和高度,确保能够顺利完成倒装操作。
3. 倒装施工倒装施工过程中,需要严格按照施工方案进行操作。
首先将储罐从基础上分离,并使用起重设备逐步将储罐倒装至预定的位置。
在倒装过程中需要分阶段进行,确保倒装过程平稳、有序。
4. 完工验收储罐倒装完成后,需要进行完工验收。
通过检查储罐的外观和内部结构,确保倒装施工没有造成储罐结构的破坏和泄漏等安全隐患。
同时还需要对施工现场进行清理,确保施工现场的整洁和安全。
三、施工安全措施在进行大型储罐倒装施工过程中,需要严格遵守安全操作规程,保障施工人员和设备的安全。
具体的安全措施包括但不限于: - 施工现场设置安全警示标识,确保施工人员能够清晰了解施工区域的危险区域和安全通道。
- 对施工人员进行岗前安全培训,明确施工操作规程和安全事项。
- 定期对施工设备进行检查和维护,确保设备运行正常。
- 在施工现场设置安全防护网和安全围栏,避免施工人员误入危险区域。
四、施工质量控制为保障施工的质量,需要在施工过程中进行严格的质量控制。
具体的质量控制包括但不限于以下几个方面: - 施工过程中设置监控点,定期对施工进行检查和验收。
储罐罐安装倒装方法

储罐罐安装倒装方法引言储罐作为一种常见的储存液体或气体的设备,广泛应用于石油化工、食品饮料、医药等行业。
在储罐的安装过程中,倒装是一种常用的施工方法。
本文将介绍储罐罐安装倒装的相关内容,包括倒装方法、倒装流程和注意事项等。
倒装方法储罐罐安装的倒装方法主要有以下几种:堆倒法堆倒法是将储罐放置在地面上,并使用吊车或起重机将储罐从底部侧翻到目标位置的一种方法。
该方法操作简单,适用于一般尺寸较小的储罐。
运输架倒装法运输架倒装法是在储罐底部安装运输架,然后使用吊车或起重机将储罐从底座上侧翻到目标位置的一种方法。
该方法适用于较大尺寸的储罐,能够提高安装效率。
吊梁倒装法吊梁倒装法是在储罐顶部安装吊梁,并通过吊车或起重机将储罐从顶部倒置到目标位置的一种方法。
该方法适用于较大尺寸和较重的储罐,但需要保证吊梁的安全性和稳定性。
倒装流程储罐罐安装的倒装流程一般包括以下几个步骤:1. 准备工作:根据倒装方法选择相应的设备和工具,检查设备是否正常运转,确保施工区域的安全。
2. 安装底座或运输架:根据倒装方法的不同,安装相应的底座或运输架,并进行固定和检查。
3. 安装吊梁:如果选择吊梁倒装法,需要在储罐顶部安装吊梁,并确保吊梁的安全和稳定。
4. 倒装过程:使用吊车或起重机将储罐从底部或顶部侧翻到目标位置,需要保持稳定,并确保施工人员的安全。
5. 定位和固定:倒装完毕后,对储罐进行定位和固定,确保储罐稳定和安全。
6. 检查和测试:对安装完毕的储罐进行检查和测试,检查其安装是否符合规范,保证其使用的安全性。
注意事项在进行储罐罐安装倒装时,需要注意以下几个事项:1. 安全第一:施工人员要戴好安全帽、安全鞋,并使用符合规范的吊车或起重机进行操作,确保施工人员的安全。
2. 合理分配重心:在倒装过程中,需要合理分配储罐的重心,并根据实际情况调整倒装角度,以减少倒装过程中的风险。
3. 保护储罐壁板和配件:在倒装过程中,需要采取措施保护储罐壁板和配件,避免受损和变形。
十万方大型储罐倒装施工方案

十万方大型储罐倒装施工方案一、施工背景二、施工准备1.确定施工场地,并对场地进行平整、清理,确保没有障碍物和杂物。
2.对施工现场进行测量,确定施工机械的位置和储罐倒装的具体要求。
3.调集所需的施工机械和设备,如起重机、吊车等。
4.安排人员到场施工,包括机械操作人员、安全员等。
三、施工步骤1.检查储罐的结构完整性和表面的光洁度,确保储罐没有任何损坏和污染。
2.准备好大型起重机,并将其稳定固定在施工现场。
3.将储罐放置在起重机下方,并使用吊车将储罐抬升至合适的高度。
4.将储罐倾斜至适当的角度,并进行固定。
5.检查储罐的安全固定,确保不会出现任何移动和倾斜的情况。
6.检查施工现场的安全措施,确保施工人员和机械的安全。
7.完成储罐倒装施工后,进行清理和整理现场,确保没有遗留杂物和施工垃圾。
四、安全措施1.施工现场要设置专门的警示标识,并采取必要的封闭措施,防止外来人员进入。
2.在施工现场设置专门的交通指示牌,指示人员和机械的行进方向,确保施工现场的交通畅通。
3.施工人员要佩戴个人防护用品,包括安全帽、防护服、防护手套等。
4.机械操作人员要经过专门培训,并具备相应的资格证书。
5.施工过程中,要定期检查机械设备的完好性和安全性能,确保其正常运行。
六、施工效果评估通过以上步骤的施工,储罐的倒装工作能够顺利进行,施工现场秩序井然,施工人员和机械的安全得到了保障。
七、总结十万方大型储罐倒装施工方案的制定和实施,为大型储罐倒装施工提供了具体的指导,保障了施工的顺利进行和人员、设备的安全。
但在具体施工过程中,仍需根据实际情况进行具体操作,并严格遵守相关的安全规范和操作规程。
简述储罐倒装法的工艺流程

简述储罐倒装法的工艺流程下载温馨提示:该文档是我店铺精心编制而成,希望大家下载以后,能够帮助大家解决实际的问题。
文档下载后可定制随意修改,请根据实际需要进行相应的调整和使用,谢谢!并且,本店铺为大家提供各种各样类型的实用资料,如教育随笔、日记赏析、句子摘抄、古诗大全、经典美文、话题作文、工作总结、词语解析、文案摘录、其他资料等等,如想了解不同资料格式和写法,敬请关注!Download tips: This document is carefully compiled by theeditor. I hope that after you download them,they can help yousolve practical problems. The document can be customized andmodified after downloading,please adjust and use it according toactual needs, thank you!In addition, our shop provides you with various types ofpractical materials,such as educational essays, diaryappreciation,sentence excerpts,ancient poems,classic articles,topic composition,work summary,word parsing,copy excerpts,other materials and so on,want to know different data formats andwriting methods,please pay attention!储罐倒装法是一种用于大型储罐建造的方法,主要是通过倒装的方式进行施工,下面是储罐倒装法的详细工艺流程:一、前期准备1.1 设计阶段:根据储罐的用途、规模、地质条件等因素,确定储罐的尺寸、结构形式、材料等。
储罐倒装法施工工艺

储罐施工工艺一、概述储罐施工工艺已经很成熟,各个项目根据设计要求和结合自身特点,采用正装法或倒装法。
我这里介绍倒装法,与正装法相比,不管从安全、质量、工期、经济效益等方面,倒装都有较大的优势。
倒装法操作控制简单、可靠、危险性小,因此已经越来越多的被采用。
我主要介绍常规储罐的采用倒装法的施工工艺。
施工工艺流程安安基半技装装础成术材现验品质料场收检量机平、验安具面放、全准布线堆交备置放底罐底板安装、焊接、质量检验提升用桅杆、胀圈、吊耳、缆风绳等安装、调试第 1 带罐壁板及顶圈角钢安装、焊接(从上到下计),质量检验顶盖中心支撑设置顶盖预装配用胎模设置、顶盖扇形板拼接、焊接、检验罐顶盖安装、焊接、质量检验第二带~倒数第二带壁板安装、焊接、质量检验最下面一带壁板安装、焊接、与罐底板装配、焊接、质量检验提升设施拆除、清理罐体其它附件安装罐体充水试验、沉降观察罐内外清扫交工资料整理竣工验收二、施工准备2.1 技术准备2.1.1 贮罐施工前,应具备有施工图和设计有关文件、施工单位编制并经建设单位、监理审批的施工方案、原材料及配件的质量证明书、国家或行业的施工及验收规范。
2.1.2 施工前,有关人员应熟悉图纸及有关技术文件、法规,通过图纸会审,明确贮罐建设工程相关专业配合要求。
贮罐的焊接技术人员应根据相关规范及焊接工艺要求进行焊接施工。
2.1.3 贮罐施工技术人员应根据现场实际情况和施工技术文件,编制有针对性的、切实可行的施工技术方案及作业指导书,并进行相应的技术交底。
明确贮罐安装的质量标准及检验方法,编制质量保证措施,准备各种计量器具及施工记录。
2.1.4 预制加工前要根据图纸、材料规格及施工规范的要求绘制贮罐排版图,经建设单位、监理单位审批后方可作为施工依据。
●罐底排版应考虑下列要求:(1)底板中幅板排版直径应考虑罐底边缘板焊接收缩量比设计直径大 1.5 -2/1000。
罐底边缘板外圆直径加收缩量。
(2)罐底边缘板宽度按设计图纸尺寸。
储罐倒装法的施工程序(3篇)

第1篇一、施工准备1. 搭建施工平台:根据储罐的尺寸和形状,搭建一个稳固的施工平台,以便进行储罐的组装和焊接作业。
2. 预制储罐构件:根据设计图纸,预制储罐的各个构件,如罐底、罐壁、罐顶等,确保构件尺寸准确、质量合格。
3. 准备焊接设备:确保焊接设备(如焊机、焊条等)齐全、完好,以满足施工需求。
4. 组建施工队伍:组织一支经验丰富的施工队伍,包括焊工、起重工、电工、安全员等。
5. 制定施工方案:根据储罐的尺寸、形状、材料等,制定详细的施工方案,包括施工步骤、工艺要求、质量控制措施等。
二、施工程序1. 罐底组装:将预制好的罐底板、罐底圈等构件按照设计要求进行组装,并确保罐底水平、垂直度符合要求。
2. 罐壁组装:将罐壁板按照设计要求进行组装,采用倒装法逐层向上装配,确保罐壁的垂直度和圆度。
3. 罐顶组装:将罐顶板、罐顶圈等构件按照设计要求进行组装,采用倒装法逐层向上装配,确保罐顶的水平和圆度。
4. 罐体焊接:对罐底、罐壁、罐顶等构件进行焊接,确保焊缝质量合格。
焊接过程中,注意控制焊接顺序、焊接参数和焊接变形。
5. 罐体检测:对焊接完成的罐体进行检测,包括外观检查、尺寸测量、无损检测等,确保罐体质量符合设计要求。
6. 罐内检查:对罐体内进行检查,清理焊渣、锈蚀等杂质,确保罐内清洁。
7. 罐体防腐:对罐体进行防腐处理,包括涂装底漆、面漆等,确保罐体使用寿命。
8. 罐体验收:对完成组装、焊接、防腐等工序的储罐进行验收,确保储罐质量符合设计要求。
三、施工注意事项1. 确保施工平台稳固,防止因平台晃动导致罐体变形。
2. 严格按照施工方案进行操作,确保施工质量。
3. 加强施工过程中的安全防护,确保施工人员安全。
4. 严格控制焊接参数,避免因焊接质量问题导致罐体变形。
5. 定期对罐体进行检查,确保罐体质量。
6. 施工过程中,做好环境保护工作,减少施工对环境的影响。
通过以上施工程序,可以确保储罐倒装法施工的顺利进行,提高储罐的施工质量和使用寿命。
大型储罐倒装法施工立焊自动焊接工艺

3 0 4 0A, 接 电压 3 - 4V, 丝 伸 出长 度 3 - 0 - 2 焊 04 焊 5
选 用 16 . mm; 丝 牌 号 根 据母 材 材 质 对应 选 择 ; 焊 保 护气 体 采用 C :气 体 纯度 大于 9 .%; O, 95 焊接 电流
4 结 论
采 用储 罐 倒 装 法 施 工 立缝 的 自动 焊 接 工 艺 原 理和 正装 法施 工 的立 缝 自动 焊接 工艺 相 同 , 体操 具 作有较 大 的 改进 , 倒装 法施 _ 立 缝 自动焊机 在 罐 如 [ 体 外地 面 操 作 , 效 高 且安 全 性 好 ; 工 立缝 下 安 装 引 弧板 , 接质 量更 易保 证 。 焊
32 焊 接 工 艺 .
焊 接 设 备 采 用 D 6 0电 源 + E A 气 电立 焊 C0 V G
接 前 检 查 控 制 线 路 、 接 电缆 、 却 水 线 和 焊 焊 冷 Cz O 气线 是否 连接正 常 。 查焊接 轨道 , 检 确保 小车行 走 通 畅 。 查 气瓶 压力 、 检 保证 气路 畅通 。 气 电立 焊焊 接 参数 为 : 电立 焊 焊丝 直径 全 部 气
形 弧板 。
坡 口根部 或外 侧 都 易产 生熔 合不 好 的缺 陷 ; 收弧 焊
接 时 , 免 焊枪 和 上 层 壁板 连 电打 火 , 以用 减 少 避 可 焊 丝 干伸 长 的方 法 , 熄弧 板 坡 口内 收弧 焊 接 。 在 背 面水 冷铜 块 封堵 照 片如 图 3所示 , 面 焊接操 作 如 正
所 示 , 口宽度 a 滑块 成 型槽 宽度 一3 4mi)对 口 坡 m (- l , 1
间 隙 b 4 6m = ~ m。
a
图 3 背 面 水 冷 铜 块 封 堵
储罐倒装法安装施工的常用方法

倒装法是目前大型储罐安装施工的常用方法,其工艺及配套设备有很多种,但其中最先进、最可靠、最具生命力的当数倒装法液压提升技术。
该技术是北京中建建筑科学技术研究院(原中建一局科研所)于1993年研制成功的,并于当年通过了中建总公司的技术鉴定,鉴定意见为:储罐步进液压提升装置为国内首创,大型储罐倒装法用液压提升装置及工艺具有国际先进水平。
该技术1994年被列为建设部科技成果重点推广项目; 1995年又列为国家级科技成果重点推广项目。
通过多年的推广应用已形成了“大型储罐倒装法液压提升成套技术”、“横跨双楼通讯塔整体液压提升施工技术” 等施工技术。
大型储罐倒装法(或钢桅杆、通讯塔和钢尖塔等)用液压提升施工成套技术是已SQD—160—100s.f松卡式千斤顶(承载力 16t,液压行程100mm)为主体,配以不同型号的液压泵站和液压管路系统等配件,组成大型储罐(或钢桅杆、通讯塔和钢尖塔等)液压提升施工成套设备,可适用于大型储罐(拱顶罐、浮顶罐和内浮顶罐、钢桅杆、通讯塔和钢尖塔等)的提升施工。
液压提升原理利用液压提升装置(成套设备)均布于储罐内壁圆周处,先提升罐顶及罐体的上层(第一层)壁板,然后逐层组焊罐体的壁板。
采用自锁式液压千斤顶和提升架、提升杆组成的液压提升机,当液压千斤顶进油时,通过其上卡头卡紧并举起提升杆和胀圈,从而带动罐体(包括罐顶)向上提升;当千斤顶回油时,其上卡头随活塞杆回程,此时其下卡头自动卡紧提升杆不会下滑,千斤顶如此反复运动使提升杆带着罐体不断上升,直到预定的高度(空出下一层板的高度)。
当下一层壁板对接组焊后,打开液压千斤顶的上、下松卡装置,松开上下卡头将提升杆以及胀圈下降到下一层壁板下部胀紧、焊好传力筋板,再进行提升。
如此反复,使已组焊好的罐体上升,直到最后一层壁板组焊完成,从而将整个储罐安装完毕。
液压提升特点特点采用倒装法液压提升施工大型储罐具有以下特点:1.液压提升平稳、安全、可靠。
拱顶储罐倒装法施工工艺流程
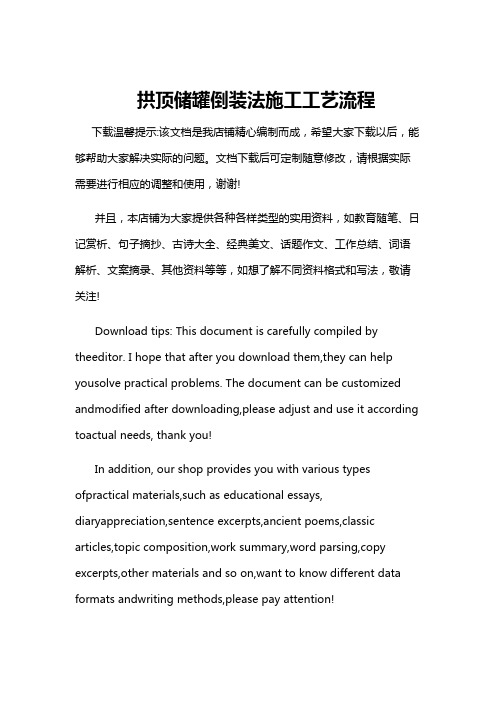
拱顶储罐倒装法施工工艺流程下载温馨提示:该文档是我店铺精心编制而成,希望大家下载以后,能够帮助大家解决实际的问题。
文档下载后可定制随意修改,请根据实际需要进行相应的调整和使用,谢谢!并且,本店铺为大家提供各种各样类型的实用资料,如教育随笔、日记赏析、句子摘抄、古诗大全、经典美文、话题作文、工作总结、词语解析、文案摘录、其他资料等等,如想了解不同资料格式和写法,敬请关注!Download tips: This document is carefully compiled by theeditor. I hope that after you download them,they can help yousolve practical problems. The document can be customized andmodified after downloading,please adjust and use it according toactual needs, thank you!In addition, our shop provides you with various types ofpractical materials,such as educational essays, diaryappreciation,sentence excerpts,ancient poems,classic articles,topic composition,work summary,word parsing,copy excerpts,other materials and so on,want to know different data formats andwriting methods,please pay attention!拱顶储罐倒装法施工工艺流程一、准备工作阶段1.确定工艺方案和施工图纸,准备所需的材料和设备。
储罐倒装法施工工艺

储罐施工工艺一、概述储罐施工工艺已经很成熟,各个项目根据设计要求和结合自身特点,采用正装法或倒装法。
我这里介绍倒装法,与正装法相比,不管从安全、质量、工期、经济效益等方面,倒装都有较大的优势。
倒装法操作控制简单、可靠、危险性小,因此已经越来越多的被采用。
我主要介绍常规储罐的采用倒装法的施工工艺。
施工工艺流程二、施工准备2.1技术准备2.1.1贮罐施工前,应具备有施工图和设计有关文件、施工单位编制并经建设单位、监理审批的施工方案、原材料及配件的质量证明书、国家或行业的施工及验收规范。
2.1.2施工前,有关人员应熟悉图纸及有关技术文件、法规,通过图纸会审,明确贮罐建设工程相关专业配合要求。
贮罐的焊接技术人员应根据相关规范及焊接工艺要求进行焊接施工。
2.1.3贮罐施工技术人员应根据现场实际情况和施工技术文件,编制有针对性的、切实可行的施工技术方案及作业指导书,并进行相应的技术交底。
明确贮罐安装的质量标准及检验方法,编制质量保证措施,准备各种计量器具及施工记录。
2.1.4预制加工前要根据图纸、材料规格及施工规范的要求绘制贮罐排版图,经建设单位、监理单位审批后方可作为施工依据。
●罐底排版应考虑下列要求:(1)底板中幅板排版直径应考虑罐底边缘板焊接收缩量比设计直径大1.5-2/1000。
罐底边缘板外圆直径加收缩量。
(2)罐底边缘板宽度按设计图纸尺寸。
罐底由中幅板和边缘板组成,边缘板的径向宽度不得小于规范要求,在罐壁内侧至中幅板收缩缝之间不得小于650mm,伸出罐壁外侧不得小于50mm。
并应在圆周方向均匀布置。
2.1.5做好基础检查验收,基础应符合设计文件和规范要求;做好基础检查验收记录。
基础验收合格具备施工条件,经建设单位同意方可进行罐底施工。
2.2施工现场准备2.2.1施工场地应设置:材料、半成品存放场地;加工场地、办公设施等。
场地应平整,道路应畅通,临时用水、用电线路应按要求敷设。
2.2.2制作有关检测样板、模板,按规定制作内外弧板,拱顶板模具及角钢圈模具。
大型储罐液压提升倒装工法汇总

大型储罐液压提升倒装施工工法目录1. 前言-------------------------------------------------------------------12. 施工工艺及操作要点-----------------------------------------------------23. 施工计划与劳动力组合--------------------------------------------------104. 机具配备--------------------------------------------------------------125. 质量控制--------------------------------------------------------------136. 安全技术措施----------------------------------------------------------147. 技术经济分析----------------------------------------------------------168.应用实例---------------------------------------------------------------161. 前言大型储罐制作安装工程,液压提升倒装法施工工艺已被施工单位广泛应用。
2004年,我公司购置了一套SQD-160型罐体液压装置,为在公司范围内推广应用,特编制本工法。
基本原理:在储罐组焊过程中,利用液压提升装置均布于储罐内壁圆周处,提升罐体壁板及罐顶,逐层组焊储罐壁,采用行程放大式液压提升机和中心控制盘组成的液压提升系统,工作时,提升机上的油泵带动液压提升机顶轴不断上升,绷紧钢丝绳,直到顶定高度,当下一层壁板对接后,液压油缸将胀圈下降到下一层壁板下部胀紧,焊好限位筋板,如此反复,使已组焊好的罐体上升,直到最后一带壁板焊完。
- 1、下载文档前请自行甄别文档内容的完整性,平台不提供额外的编辑、内容补充、找答案等附加服务。
- 2、"仅部分预览"的文档,不可在线预览部分如存在完整性等问题,可反馈申请退款(可完整预览的文档不适用该条件!)。
- 3、如文档侵犯您的权益,请联系客服反馈,我们会尽快为您处理(人工客服工作时间:9:00-18:30)。
储罐施工工艺、概述储罐施工工艺已经很成熟,各个项目根据设计要求和结合自身特点,采用正装法或倒装法。
我这里介绍倒装法,与正装法相比,不管从安全、质量、工期、经济效益等方面,倒装都有较大的优势。
倒装法操作控制简单、可靠、危险性小, 因此已经越来越多的被采用。
我主要介绍常规储罐的采用倒装法的施工工艺。
施工工艺流程、施工准备技术准备贮罐施工前,应具备有施工图和设计有关文件、施工单位编制并经建设单位、监理审批的施工方案、原材料及配件的质量证明书、国家或行业的施工及验收规范。
施工前,有关人员应熟悉图纸及有关技术文件、法规,通过图纸会审,明确贮罐建设工程相关专业配合要求。
贮罐的焊接技术人员应根据相关规范及焊接工艺要求进行焊接施工。
贮罐施工技术人员应根据现场实际情况和施工技术文件,编制有针对性的、切实可行的施工技术方案及作业指导书,并进行相应的技术交底。
明确贮罐安装的质量标准及检验方法,编制质量保证措施,准备各种计量器具及施工记录。
预制加工前要根据图纸、材料规格及施工规范的要求绘制贮罐排版图,经建设单位、监理单位审批后方可作为施工依据。
•罐底排版应考虑下列要求:1)底板中幅板排版直径应考虑罐底边缘板焊接收缩量比设计直径大-2/1000 。
罐底边缘板外圆直径加收缩量。
2)罐底边缘板宽度按设计图纸尺寸。
罐底由中幅板和边缘板组成,边缘板的径向宽度不得小于规范要求,在罐壁内侧至中幅板收缩缝之间不得小于650mm伸出罐壁外侧不得小于50mm并应在圆周方向均匀布置。
做好基础检查验收,基础应符合设计文件和规范要求;做好基础检查验收记录。
基础验收合格具备施工条件,经建设单位同意方可进行罐底施工。
施工现场准备施工场地应设置:材料、半成品存放场地;加工场地、办公设施等。
场地应平整,道路应畅通,临时用水、用电线路应按要求敷设。
制作有关检测样板、模板,按规定制作内外弧板,拱顶板模具及角钢圈模具。
储罐在预制、组装及检验过程中所使用的样板弦长不得小于2m直线样板的长度不得小于1m测量角焊缝的变形的弧形样板,其弦长不得小于1m样板采用〜厚度的铁皮制作,周边应光滑、整齐。
并注明部件名称及曲率半径。
制作提升抱杆、涨圈、中心柱伞架、罐顶支撑圈、罐顶预制胎、加固弧板、卡具、吊装吊耳吊升装置壁板卷弧用胎具等专用器材。
施工预制场地应平整,纵横方向各挖两条排水沟,以方便下雨天雨水的及时排出,保证雨后及时恢复施工。
施工现场四周铺设一条环向运输道路,路面中间部分应高出预制场地堆料部分约100mm以满足下雨后吊车、拖车的行走要求。
预制场内的用电采用埋地电缆,一定要安全可靠,不得破损和绝缘层老化,在有车辆经过处要用钢套管保护,严格遵守变配电安全操作规程。
施工机具准备按照施工机具计划配备施工机械,并保证机具性能完好,及时填写机械运转记录。
主要机械设备:电焊机、卷板机坡口加工机、切割机、烘干箱、X 光探伤机、超声波探伤仪、磁粉探伤仪器、油压机、试压泵、液压顶升装置、真空泵等,滚板机、半自动切割机按照施工平面布置图进行安装、调试。
主要工具:气焊工具、磨光机、千斤顶、大锤等。
起重吊装工具:链式手拉葫芦、索具、卸扣和轧头、钢钎撬棍、起重机、卷杨机等。
测量及计量器具:水准仪、钢卷尺、水平仪、直角尺、经纬仪等,所用计量检测器具齐备,并经检验合格。
施工材料准备贮罐所用的钢板、型材和附件及焊接材料符合设计文件的要求并有质量证明书,钢材质量证明书中应标明钢号、规格、化学万分、力学性能、供货状态及材料的标准。
焊条质量合格证明书应包括熔敷金属的化学成份和机械性能;低氢型焊条还应包括扩散氢含量。
无质量合格证明书的焊接材料不允许使用。
当对质量合格证明书有疑问时,应对焊接材料进行复验,合格后方可使用。
钢板必须逐张进行外观检查,表面不得有气孔、结疤、拉裂、折叠、夹渣和压入的氧化皮,且不得有分层,表面质量符合现行的钢板标准。
钢板的表面锈蚀减薄量、划痕深度应符合下表规定:存放过程中,应防止钢板产生变形,所垫木块应保证垂直方向上在一条直线上, 钢板下方严禁用带棱角的物件垫底。
外购、标准件、加工件等均应有材质证明书和合格证。
作业人员 参加焊接的焊工应是具有相应资质的持证焊工。
各工种施工人员已到位,无损检测人员应由具有相应资格的人员担任。
三、排板及预制 罐底板 排板示意图:边缘板带弓形边缘板排板示意图中幅板不带弓形边缘板排板示意图排板及预制要求:(1)、罐底的排板直径,宜按设计直径放大% %(2)、弓形边缘板沿罐底半径方向的最小尺寸,不应小于700mm非弓形边缘板最小直边尺寸,不应小于700mm.(3)、中幅板的宽度不应小于1000mm长度不应小于2000mm与弓形边缘板连接的不规则中幅板最小直边尺寸,不应小于700mm(4)、底板任意相邻焊缝之间的距离,不应小于300mm(5)弓形边缘板尺寸偏差:弓形板示意侧板排板示意图:90 180 270排板及预制要求:各圈壁板的纵焊缝宜向同一方向逐圈错开,相邻圈板纵缝间距宜为板长的1/3,且不应小于300mm见图中L。
底圈壁板的纵焊缝与罐底边缘板的对接焊缝之间的距离,不应小于300mm(3) 开孔和罐壁焊缝之间的距离:1)罐壁厚度大于12mm接管与罐壁板焊后未进行消除应力热处理时,开孔接管或补强板外缘与罐壁纵环焊缝之间的距离,应大于焊角尺寸的8倍,且不应小于250mm2)罐壁厚度不大于12mm或接管与罐壁板焊后进行消除应力热处理时,开孔接管或补强板外缘与罐壁纵焊缝之间的距离不应小于150mm与罐壁环焊缝之间的距离,不应小于壁板厚度的倍,且不应小于75mm(4)罐壁上连接件的垫板周边焊缝与罐壁纵焊缝或接管、补强圈的边缘角焊缝之间的距离,不应小于150mm与罐壁环焊缝之间的距离,不应小于75mm如不可避免与罐壁焊缝交叉时,被覆盖焊缝应磨平并进行射线或超声波检测,垫板角焊缝在罐壁对接焊缝两侧边缘最少20mm处不焊。
(5)抗风圈和加强圈与罐壁环焊缝之间的距离,不应小于150mm(6)包边角钢对接接头与壁板纵向焊缝之间的距离,不应小于200mm(7)直径小于25m的储罐,其壁板宽度不应小于500mm长度不应小于1000mm直径大于或等于25m的储罐,其壁板宽度不应小于1000mm长度不应小于2000mm(8)采用倒装时每带侧板预留100mm在组装焊接完成封口时割除多余部分。
(9)壁板下料尺寸偏差:罐顶排板要求:顶板任意相邻焊缝的间距,不应小于 200mm加强肋加工成型后,用弧形样板检查,其间隙不应大于 2mm 每块顶板应在胎具上与加强肋拼装成型,焊接时应防止变形。
顶板成型后脱胎,用弧形样板检查,其间隙不应大于10mm四、底板安装罐底板安装 罐底采用带垫板的对接接头时,垫板应与对接的两块底板贴紧,并点焊固 定,其缝隙不应大于1mm 罐底板对接接头间隙,设计图无要求时可参照下表:焊接方法钢板厚度8( mm间隙(mm焊条电弧焊不开坡口6 5± 1 开坡口S> 67± 1 气体保护焊不开坡口6 3± 1 6<§< 104± 1 开坡口 10<§< 21 5± 1设计为条形基础的,底板可点焊固定在底部支撑梁上。
壁板示意图(2) 单块顶板本身的拼接,宜采用对接。
(3) (4)罐底板焊接L/■\\、4■-|4厂X__ F41■ZL卜.-=3r—二—J•3--2----2----1- -1---2-2--1--1- -1-■ J_-1--1- -1- >3-/带弓形底板焊接示意图罐底板的焊接,应采用收缩变形最小的焊接工艺及焊接顺序进行。
且宜按下列顺序进行。
1)中幅板焊接时,先焊短焊缝,后焊长焊缝。
初层焊道应采用分段退焊法或跳焊法。
2)弓形边缘板的焊接,宜符合下列规定: 1)首先施焊靠外缘300mn 部位的焊缝。
在罐底与罐壁连接的角焊缝焊完后且边缘板与中幅板之间的收缩缝施焊前, 完成剩余的边缘板对接的焊缝和中幅 板的对接焊缝。
弓形边缘板对接焊缝的初层焊, 宜采用焊工均匀分布, 对称施焊方法。
罐底与罐壁连接的角焊缝,在底圈壁板纵焊缝焊接完成后施焊,由数名焊工从罐内,外沿同一方向进行分段焊接。
初层焊采用分段退焊或跳焊法。
罐底板的检验储罐底板由于是直接安装于基础上,采用传统的探伤及拍片无法进行,般采用罐底板抽真空的方法进行检验。
五、桅杆设置底板焊接完成后,进行第一带板(从上往下计)的组对焊接,完成后即须进 行倒装桅杆的设置。
开始组装侧板时, 须先行设置组对基准, 组对基准采用在底板上设置靠码的形 式进行。
2) 3) 收缩缝的第一层焊接,采用分段退焊或跳焊法。
3) 非弓形边缘板的罐底不宜留收缩缝。
罐体基准圆(内径)100>- / / <•冬 靠码(电焊牢固)1靠码桅杆设置示意图:罐体靠码示意图桅杆高度根据侧板高度确定,等于板高 +吊具高度—300mm其D\.&Ji ;iO~、丿「j4]ia-pk'立柱在加固时,直径大于20m 采用剪刀撑,直径小于、等于 20m 采用斜支撑,剪刀撑间隔1跨加设1组,支撑根据现场材料情况采用。
顶部水平拉杆须密 闭为整体,在支撑及水平拉杆加设前须检查立柱的垂直度,以尽量垂直为原则。
、、■ i■—广K I h J_ jj. I立柱底板(与罐底板满t\\立柱间距展开尺寸控制在5〜6m为宜。
吊装荷载计算吊装用葫芦、索具、缆风绳等的计算:根据罐体重量确定葫芦、索具、倒装用短桅杆示意图(短桅杆以© 159无缝钢管为例)200 200倒装用胀圈示意图胀圈示意图缆风3( 0 159X 4.5-300 X 200X 165 =200024底杆桅至4根/ 75X8(b 159X 4.5短桅杆头部大样短桅杆底部大样胀圈千斤顶罐壁5-300 X 300 X16300〜/ 75X8千斤顶i '--ih=千斤顶高度千斤顶* '' 千斤顶卡板,5 =12〜16 间距2000胀圈、卡板、方楔安装大样胀圈、吊耳、托板安装大样胀圈采用[20槽钢煨制对焊而成,焊接完成后采用样板检查是否符合要求,胀圈分为四瓣制作,中间预留 4个16吨千斤顶顶紧高度(由于胀圈在顶紧时受罐侧板方楔肿0胀圈[20 \\托板-160 X 75X 10间距20001225—60160I5^6吊耳3=20力不大,一般采用16t 千斤顶完全能满足要求),胀圈每隔2m 采用方形卡板与罐 体侧板焊接。
千斤顶与胀圈示意:罐顶盖一般呈球状,分为中心板和扇形大板。
因受材距的限制,扇形大板一 般需在胎模具上由几块板拼焊而成。
胎模具呈倒置的球面,将待拼装的顶板吊入模具内,用压梁压紧,先拼焊成 扇形大板,然后再装上纵环向加劲肋条,并进行焊接。