预硫化胎面精细硫化工艺(论文)
废旧轮胎_预硫化翻新_技术

2
3 4 5 6 7
47.4 540 8 110 0.2730
良好 合格
(2)节约钢铁资源。 每条轮胎都要钢丝圈,生产新胎需要消耗大量的钢铁资 源, 随着以钢丝为胎体骨架材料的子午线轮胎的普及, 轮胎产 业对钢铁资源的需求量也越来越大。而翻新轮胎更够循环利
合格
用钢铁材料, 在很大程度上节约钢铁资源。 (3)循环利用有限资源。 将废旧轮胎进行预硫化翻新, 由此来循环利用有限资源。
图 1 废旧轮胎预硫化翻新工艺路线
—— 科协论坛 ・ 2012 年第 12 期 (下) ——97Leabharlann 资源环境与 节能减灾
构成轮胎的众多成分, 如其中大多橡胶、 胎体骨架尼龙帘 线的原料都是石油,以及在配胶和生产加工轮胎过程中需要 的化工原料都消耗石油。据试验显示,翻新一条卡车轮胎平 均耗石油 28L, 相比于生产新的轮胎消耗石油 84L, 可见, 翻新 轮胎如果能够得到推广可以在很大程度上节约石油资源。
3.2 产品名称及外观
参考文献: [1] 传统热硫化翻新法制约了轮胎翻新业的发展[Z].
图 2 子午线轮胎 3.3 产品优点 (1)节约石油资源。 —— 科协论坛 ・ 2012 年第 12 期 (下) ——
98
资源环境
与 节能减灾
废旧轮胎 “预硫化翻新” 技术
□ 沈沛鸿 王孟良
710018) (长安大学汽车学院 摘 陕西・西安
要: 随着汽车产业的迅速发展, 轮胎的产业也随之迅猛发展。 而对于废旧轮胎的处理, 目前大多采用直接掩
埋或者堆放, 这就对土地资源具有了一定的需求。然而随着土地价格的上涨, 此种处理废旧轮胎的方法愈发困 难; 另一方面, 轮胎直接报废极其浪费橡胶资源和钢铁资源, 废旧轮胎堆放易污染环境, 滋生蚊蝇, 传播疾病。 该 技术致力于研究规范国内尚属起步阶段的轮胎翻新工艺, 尤其是子午线轮胎的翻新工艺, “预硫化翻新” 利用 技 术, 使翻新轮胎的质量以及性能达到了国际标准, 远优秀于国内厂家翻新的废旧轮胎。 关键词: 废旧轮胎 中图分类号: X73 预硫化翻新技术 新轮胎 文章编号: 1007-3973 2012) ( 012-097-02
轮胎硫化工艺条件的优化
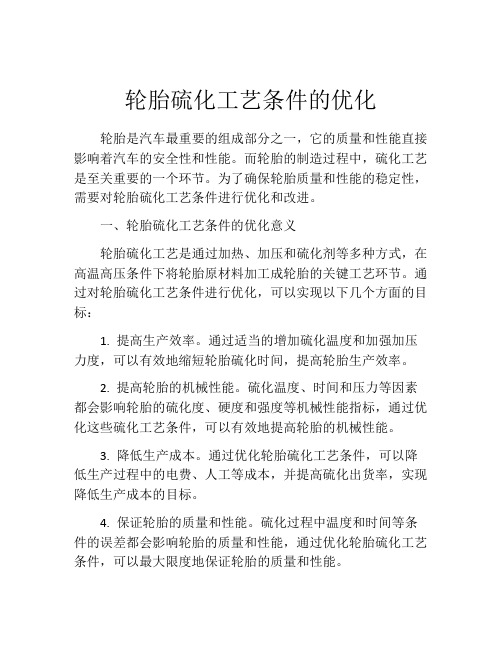
轮胎硫化工艺条件的优化轮胎是汽车最重要的组成部分之一,它的质量和性能直接影响着汽车的安全性和性能。
而轮胎的制造过程中,硫化工艺是至关重要的一个环节。
为了确保轮胎质量和性能的稳定性,需要对轮胎硫化工艺条件进行优化和改进。
一、轮胎硫化工艺条件的优化意义轮胎硫化工艺是通过加热、加压和硫化剂等多种方式,在高温高压条件下将轮胎原材料加工成轮胎的关键工艺环节。
通过对轮胎硫化工艺条件进行优化,可以实现以下几个方面的目标:1. 提高生产效率。
通过适当的增加硫化温度和加强加压力度,可以有效地缩短轮胎硫化时间,提高轮胎生产效率。
2. 提高轮胎的机械性能。
硫化温度、时间和压力等因素都会影响轮胎的硫化度、硬度和强度等机械性能指标,通过优化这些硫化工艺条件,可以有效地提高轮胎的机械性能。
3. 降低生产成本。
通过优化轮胎硫化工艺条件,可以降低生产过程中的电费、人工等成本,并提高硫化出货率,实现降低生产成本的目标。
4. 保证轮胎的质量和性能。
硫化过程中温度和时间等条件的误差都会影响轮胎的质量和性能,通过优化轮胎硫化工艺条件,可以最大限度地保证轮胎的质量和性能。
二、轮胎硫化工艺条件的优化方法1. 优化硫化温度和时间。
随着硫化温度的升高,硫化速度和硫化度也会随之增加。
但是当温度过高的时候,不仅会增加硫化丝的断裂可能性,还会导致轮胎变形和硫化不均匀等问题。
因此,在硫化温度和硫化时间之间需要进行平衡,找到二者之间的最佳组合。
2. 加强加压力度。
加压力度是影响硫化度和轮胎硬度的重要因素。
通过加强加压力度,可以有效地提高轮胎硫化质量和机械性能,并缩短硫化时间。
3. 采用新型硫化剂。
目前市场上流行的硫化剂主要有硫、硫代硫酸酯、过氧化物等。
通过选择合适的硫化剂,可以对轮胎硫化工艺条件进行优化,并有效提高轮胎的硬度和强度,以及耐久性和耐磨性等性能指标。
4. 采用自动化控制系统。
通过采用现代化的自动化控制系统,可以有效地控制轮胎硫化过程中的温度和时间等条件,提高硫化质量和生产效率,并减少操作人员的劳动强度和误操作可能性。
轮胎硫化的流程

轮胎硫化的流程轮胎硫化是轮胎生产过程中的一个关键环节,它通过在高温和高压条件下将轮胎芯体与胶料牢固地粘结在一起,使轮胎获得所需的强度和耐磨性。
下面将详细介绍轮胎硫化的流程。
一、胶料的制备在轮胎硫化过程中,胶料的选择和制备是非常重要的。
胶料通常由天然橡胶、合成橡胶、填充剂、助剂等组成。
这些原材料经过配方调配、混炼和加工处理后,形成胶料,用于轮胎硫化过程中的胎面、侧壁、底胎等部位的覆盖。
二、芯体的制备芯体是轮胎的主体结构,它由帘布、钢丝和胶料组成。
首先,将帘布和钢丝按照设计要求进行编织和编织成帘布带和钢丝圈。
然后,将胶料涂覆在帘布带上,并将钢丝圈嵌入其中,形成芯体的预制件。
三、模具的准备模具是轮胎硫化过程中用于成型的工具。
根据轮胎的尺寸和形状设计制作模具,并将其安装在硫化机上。
模具的选择和安装要保证与轮胎设计相符,以确保硫化过程中轮胎的成型质量。
四、预硫化在正式的硫化过程之前,通常需要进行预硫化处理。
预硫化是为了加强芯体和胶料的粘结,提高硫化后轮胎的强度和耐磨性。
预硫化的条件一般为低温、低压和短时间,以避免芯体和胶料过早硫化。
五、硫化硫化是轮胎生产中最关键的步骤之一。
在硫化机中,将预硫化后的轮胎芯体放置在模具中,并加入胶料。
然后,以高温和高压的条件下进行硫化。
硫化温度一般在130℃至180℃之间,硫化时间根据轮胎尺寸和硫化要求而定,一般在20分钟至60分钟之间。
在硫化过程中,硫化机通过加热和加压,使胶料中的硫化剂和胶料发生化学反应,形成交联结构,使轮胎芯体与胶料牢固地粘结在一起。
同时,硫化过程中产生的热量也会使胶料膨胀,填充模具中的空腔,使轮胎成型。
六、冷却和脱模硫化完成后,轮胎需要经过冷却和脱模处理。
冷却的目的是使轮胎迅速降温,使胶料固化,保证轮胎的成型质量。
脱模是将硫化后的轮胎从模具中取出,通常采用涂覆模具表面的脱模剂,以便轮胎能够顺利脱模。
七、修整和检验硫化后的轮胎经过冷却和脱模处理后,需要进行修整和检验。
轮胎硫化工艺条件的优化

轮胎硫化工艺条件的优化随着我国高速公路的进展和汽车性能的提高,人们对汽车行驶的安全性和舒服性提出了更高的要求,因此对轮胎的使用性能也有了更高的要求。
这就要求轮胎不仅在结构设计上要有所突破,而且轮胎硫化工艺的制定不能再停留在依照体会或半体会的方法上,沿用过去〝宁过勿欠〞的观念,而是应利用运算机模拟轮胎的实际硫化历程并运算其各部位的硫化程度,确定合理的硫化条件,从整体上提高轮胎的性能。
如此不仅可提高轮胎质量,而且可节约大量能源,提高硫化设备的利用率。
轮胎有限元模型的建立、轮胎硫化过程温度场信息的模拟以及轮胎硫化程度的运算参见文献[1~3]。
本文仅讨论轮胎硫化程度的阻碍因素,并对硫化工艺条件进行优化。
1轮胎硫化过程模型的建立依照175/70R13半钢子午线轮胎的材料分布图,建立有限元分析的几何模型和材料模型,如图1所示。
定义模型与热板接触处为第一类边界条件,温度为165℃。
胶囊与过热水之间通过对流换热,由于橡胶的导热系数专门小,因此传热的要紧热阻是橡胶的热阻,此处也可简化为第一类边界条件[1,2],温度为180℃。
模型与外界空气之间有对流换热,由于模型外表面覆盖绝热保温材料,因此换热可忽略不计,此边界可作为绝热边界处理。
轮胎出模后与空气之间有自然对流换热和辐射换热[2]。
模具初始温度取80℃,轮胎初始温度为25℃,胶囊初始温度为100℃。
2硫化程度的阻碍因素2.1硫化时刻应用轮胎硫化过程模拟有限元模型在边界条件不变的情形下(热板温度165℃,胶囊内过热水温度180℃,分别求出图1所示3点过热水循环)时刻为10,12,14和16min时的温度2时刻关系,将结果代入运算硫化程度的程序中,求出各点在不同过热水循环时刻下的硫化程度,如图2所示。
由图2可见,在所研究的时刻范畴内,过热水循环时刻与3个节点位置处的硫化程度均呈线性关系,但对各部位的阻碍程度不同,过热水循环时刻对胎体层和带束层硫化程度的阻碍比对胎面胶硫化程度的阻碍大得多,这是因为在硫化过程中胎体层和带束层更靠近胶囊的缘故。
轮胎硫化新工艺通过鉴定

轮胎硫化新工艺通过鉴定的报告,800字
本报告就新轮胎硫化工艺的鉴定情况做一个详细报告。
一、新轮胎硫化工艺试验
新轮胎硫化工艺试验分为热处理和表面处理两部分,在此两部分中,我们进行了全面的测试来评估新工艺的效果。
1、热处理试验
热处理是硫化轮胎的关键步骤,我们采用国际先进的最新热处理工艺,以保证轮胎的性能,首先将轮胎进行加热,然后根据不同类型的轮胎温度也不同,在避免轮胎烧伤的同时确保硫化效果。
测试结果表明,采用新工艺处理的轮胎能够有效提升硬度和抗拉强度,达到质量要求。
2、表面处理试验
表面处理是硫化轮胎的第二个步骤,此部分的处理对轮胎的外观性能有很大的影响,我们采用新型的表面处理工艺,提高了轮胎的耐磨性,防止轮胎的磨损,达到客户期望的抗磨损性能。
测试结果表明,采用新工艺处理的轮胎耐磨性有了很大的提高,满足客户要求。
二、新轮胎硫化工艺性能检测结果
新轮胎硫化工艺的检测结果证明,新工艺对轮胎的硬度和抗拉强度以及耐磨性有了质的提高,测试结果如下:
•硬度:原始硬度为UmH2,新工艺后提升至UmH3,提升17%。
•抗拉强度:原始强度为125kgf /cm2,新工艺后提升至
135kgf/cm2,提升8%。
•耐磨性:原始耐磨性为1000km,新工艺后提升至1500km,提升50%。
三、结论
新轮胎硫化工艺是一种有效的轮胎加工工艺,它既能提高轮胎硬度和抗拉强度,又能提高轮胎的磨损耐久性,为轮胎生产提供了更好的保障。
通过上述试验,我们得出结论,新轮胎硫化工艺鉴定的硬度、抗拉强度和耐磨性均达到要求,可以满足轮胎质量要求。
轮胎硫化工艺的优选

作者简介:谭德征(1966 ),男,浙江浦江人,杭州中策橡胶有限公司高级工程师,学士,主要从事子午线轮胎配方设计工作。
轮胎硫化工艺的优选谭德征(杭州中策橡胶有限公司,浙江杭州 310008)摘要:轮胎硫化时间决定成品轮胎的过硫或欠硫,从而影响产品质量。
确定轮胎硫化时间可以采用传统方法、硫化测温法或发泡点测定法。
通过硫化测温并对轮胎各部件的胶料配方调整后,可使轮胎在硫化过程中各部位胶料基本同时达到正硫化,从而取得最优的硫化效果。
关键词:轮胎;硫化;硫化测温中图分类号:TQ330.6+7 文献标识码:B 文章编号:1006 8171(2005)02 0109 03硫化是制造轮胎的最后工序,硫化质量的好坏直接关系轮胎产品的质量和成品合格率。
自1839年美国人Goodyear 发现橡胶硫化至今,人们对硫化所用材料和工艺以及硫化机理的研究从未间断过。
硫化是一个微观的分子反应过程,由于混炼胶中原材料较多,性能各不相同,反应非常复杂,因此对硫化的研究一般都是采用对硫化后的胶料进行各种分析(如游离硫含量、溶胀、撕裂强度、永久变形及生热等),根据产品对各项性能(如耐磨、耐刺、耐热及耐油等)的要求不同,对配方、结构和硫化工艺进行适当的调整,从而达到设计要求。
硫化的三要素为时间、温度和压力,其中时间和温度具有密切的关联性。
本文对与轮胎硫化相关的一些主要方面进行分析。
1 准确确定硫化时间传统轮胎硫化时间的确定是通过对各部件胶料硫化后的游离硫含量和溶胀等测定数值进行比较,再用硫化仪对各部件胶料进行测定,测得其正硫化时间,以确定合理的硫化时间。
由于硫黄由高浓度部位向低浓度部位迁移,而且很难准确区分不同配方胶料的种类,因此所测数据误差相对较大,且工作量很大,对轮胎这种多配方和多部件的制品来说不太合适。
比较快捷的方法是通过硫化测温确定硫化时间。
在轮胎不同部位埋入热电偶,输入各胶料的活化能,计算出设定温度下的等效硫化时间,与设定温度下的硫化仪数值t 90比较,确定最终硫化时间。
轮胎硫化工艺条件的优化
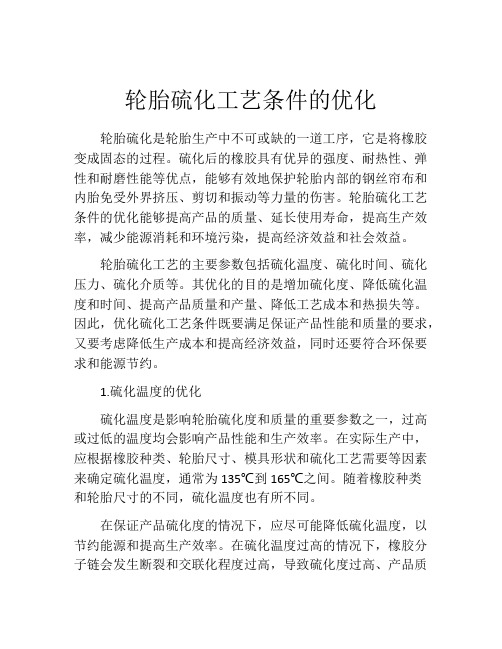
轮胎硫化工艺条件的优化轮胎硫化是轮胎生产中不可或缺的一道工序,它是将橡胶变成固态的过程。
硫化后的橡胶具有优异的强度、耐热性、弹性和耐磨性能等优点,能够有效地保护轮胎内部的钢丝帘布和内胎免受外界挤压、剪切和振动等力量的伤害。
轮胎硫化工艺条件的优化能够提高产品的质量、延长使用寿命,提高生产效率,减少能源消耗和环境污染,提高经济效益和社会效益。
轮胎硫化工艺的主要参数包括硫化温度、硫化时间、硫化压力、硫化介质等。
其优化的目的是增加硫化度、降低硫化温度和时间、提高产品质量和产量、降低工艺成本和热损失等。
因此,优化硫化工艺条件既要满足保证产品性能和质量的要求,又要考虑降低生产成本和提高经济效益,同时还要符合环保要求和能源节约。
1.硫化温度的优化硫化温度是影响轮胎硫化度和质量的重要参数之一,过高或过低的温度均会影响产品性能和生产效率。
在实际生产中,应根据橡胶种类、轮胎尺寸、模具形状和硫化工艺需要等因素来确定硫化温度,通常为135℃到165℃之间。
随着橡胶种类和轮胎尺寸的不同,硫化温度也有所不同。
在保证产品硫化度的情况下,应尽可能降低硫化温度,以节约能源和提高生产效率。
在硫化温度过高的情况下,橡胶分子链会发生断裂和交联化程度过高,导致硫化度过高、产品质量下降、能源浪费和环境污染等问题;而在硫化温度过低的情况下,硫化度不足、产品质量差、生产效率低等问题也会出现。
因此,在优化硫化温度时,需要综合考虑橡胶种类、轮胎尺寸、模具形状、硫化时间和压力等多种因素,根据实际情况来确定最佳硫化温度,以平衡硫化度、产品性能和生产效率三者之间的关系。
2.硫化压力的优化硫化压力是影响轮胎硫化度和质量的另一个重要参数,它直接影响轮胎的形状和几何尺寸。
在实际生产中,硫化压力与硫化温度、时间和介质等参数一起控制,以保证产品硫化度和合格率。
在优化硫化压力时,需要考虑橡胶种类、轮胎尺寸、模具形状、压力区域等因素。
一般来说,硫化压力应该高于橡胶的流动点压力,以避免橡胶在硫化过程中发生形变和变形。
浅论轮胎翻新关键技术及行业发展前景

浅论轮胎翻新关键技术及行业发展前景肖 军一、轮胎翻新的意义汽车轮胎在使用过程中直接与各种条件的路面接触,易粘附路面上各种污物,这些污物有一些会浸入轮胎橡胶表面造成轮胎橡胶失光。
被污物浸蚀后的轮胎将失去原有纯正黑色,而呈现灰黑色,影响汽车视觉效果,且这种失光通过清洗无法解决。
轮胎橡胶受浸蚀很容易老化、变硬,失去原有的弹性及耐磨性,因此,轮胎要定期进行翻新保护处理。
谈起翻新轮胎,许多消费者闻之色变,将其等同于假冒伪劣产品。
实际上,一些发达国家出于环保目的,规定某些轮胎必须多次翻新使用。
在欧美市场,米其林公司甚至承诺:一条轮胎要经过3次翻新后才会丢弃。
我国目前有几百家轮胎翻新企业,但翻新率仅约3%,不仅远低于世界第一轮胎翻新大国美国约14%的翻新率,也低于世界平均6%的翻新率。
轮胎翻新是将已经磨损的旧轮胎,在可能的范围内进行修理,使其变为能重新使用的轮胎。
翻新轮胎不是翻新被废弃的轮胎,而是翻新仍具使用价值的旧轮胎。
翻新一条旧轮胎所消耗的原材料,只相当于制造同等规格新轮胎的30%左右,价格也仅为新轮胎的30%左右,能够极大地节约橡胶资源。
一条正常使用的轮胎,胎面磨光只用去整条轮胎经济价值的30%左右,其70%左右的剩余价值不加以利用就太可惜了。
在使用保养良好的条件下,一条轮胎可以多次翻新,如棉帘线轮胎可翻新1~2次,锦纶帘线轮胎可翻新2~4次,钢丝轮胎可翻新4~6次。
随着翻新技术和产品质量的不断提高,翻新轮胎在市区使用最高总里程已达30万km以上,长途运输使用也超过15万km。
每条轮胎翻新所耗用的原材料和费用,一般仅占新胎的15%~50%,与制造新胎相比,可节约大量的物资(如橡胶、帘布、炭黑、钢丝等)和开支。
因此,翻新轮胎在国民经济中具有重要经济意义。
翻新轮胎是旧轮胎综合利用的积极途径,是轮胎工业的延伸和加工再利用,对于促进资源综合利用,促进经济增长方式转变和可持续发展,富有积极意义。
就其前景而言,旧轮胎翻新与轮胎工业一样是汽车工业交通运输中所不可缺少的一个行业。
废旧轮胎预硫化翻新工艺技术关键

条轮 胎 可 以反复 多 次 翻新 。 冷 翻轮胎 由于 采用 的是
高压硫化 的胎 面结 实 而又耐 磨 。
力 01 ~ . M a ,能确保胎体打磨前 的弧度要求 , . 0 0 P) 5 2 提 高 打磨 精度 ,保证 胎 体 与胎 面胶 弧度 相 吻合 ,提 升
翻胎耐 磨 寿命 。
青 海 科 技
21 年第 6 00 期
废 1 胎 预硫 化 翻 新 工 艺技 术 关键 日轮
武 辉 ,马宏 斌 , I 宁 ,刘 、 延 西宁 佳 8 02 ) 10 1 ( 海省 机械 科学 研究 所 ,青海 青
摘 要 :本文对废 旧轮胎预硫化翻新生产过程中的关 键技术进行 了分析归纳 。
轮胎 翻新 法 ,国外 已经 很普 及 ,我 国这几 年才 刚 刚兴
起 ,但 由于 一 些 生产 厂 家 对 其 生 产 工 艺 还不 够 重 视 ,
造成 轮胎 翻新 质量 存 在 缺 陷 。本 文对 废 旧轮 胎 预硫 化 Байду номын сангаас
翻新 工艺 中 的技 术关 键进 行 了归 纳 。
每条 轮 胎 都拥 有 一个 预 定 的轮 冠 宽 度 、侧 面及 半 径 ,胎 体 打磨 要 根 据 不 同 的胎 体 设 定 合 理 的 打 磨 参
关 键 词 :废 旧 轮 胎 ;预硫 化 翻新 ;技 术 关 键
1 引 言
预计 2 1 0 0年 我 国汽 车 保 有 量 将 达 到 7 0 0 0万 辆 ,
较 明显 暴露 ( 此方 法 有 一定 危 险应 在 安 全有 保 证 的条 件下 进行 ) ,如无 异 常可投 入加 工 。 由于 旧轮 胎 流于 市场 的时 间太 长 ,胎体 表 面难 免
电子束辐照预硫化技术在轮胎轻量化中的应用

283电子束辐照预硫化技术在轮胎轻量化中的应用任乔伟,谭 苗,杜 凡,杨 姣,党 飞(陕西延长石油集团橡胶有限公司,陕西 咸阳 712000)摘要:研究电子束辐照预硫化技术在轮胎轻量化中的应用。
采用经过电子束辐照预硫化的胎体,可以减薄、减窄过渡层,从而减小轮胎质量,降低生产成本,并且轮胎不会出现胎里露线现象,同时不会影响成品轮胎的充气外缘尺寸、高速性能和耐久性能。
关键词:轮胎;电子束辐照;预硫化技术;胎体帘布;轻量化中图分类号:TQ330.38+9;TQ330.6+7 文章编号:2095-5448(2021)06-0283-03文献标志码:A DOI :10.12137/j.issn.2095-5448.2021.06.0283由于轮胎行业是全球橡胶消耗的最大行业,轮胎的轻量化和高性能化必然成为其发展趋势。
电子束辐照预硫化是轮胎轻量化的有效方法。
国外众多技术先进的轮胎公司采用电子束辐照预硫化技术生产轮胎,降低了橡胶消耗,提高产品质量。
但电子束辐照预硫化技术在我国起步较晚,轮胎企业应用较少。
轮胎电子束辐照预硫化技术不改变原轮胎生产工艺,仅用电子加速器对轮胎半部件进行辐照预硫化,电子加速器发射的高能电子束产生高活性粒子,使胶料在常温下交联形成三维结构,通过预硫化实现初步定型,性能更加稳定[1-8]。
本工作研究胎体帘布经过电子束辐照预硫化后,对轮胎性能及质量的影响。
1 实验1.1 主要原材料压延后正常存放的胎体帘布和压延后经过电子束辐照预硫化的胎体帘布。
1.2 主要设备CG4/610×1750-S 型四辊压延机,意大利艾克里公司产品;VMI245-SL 型一次法成型机,荷兰VMI 公司产品;LLY -B1220/1715×2型硫化机,浙江荣升机械有限公司产品;GX -YLSN -1112型高速/耐久性试验机,青岛高测科技股份有限公司产品;DD500keV /150mA 型电子加速器,电子束能量为0.45~0.5 MeV ,电流为150 mA ,辐照剂量为25 kGy ,江苏达胜加速器制造有限公司产品。
轮胎翻新胎体及预硫化胎面打磨的质量控制

一、打磨粗糙度质量的控制轮胎的所有打磨面应具有合适的粗糙程度,这是为了保证胎体与新贴上的黏合胶之间形成足够的黏着接触面。
理论上讲,表面粗糙程度在一定范围内,粗糙度较大,接触面就较多,黏合效果越好;反之,粗糙度较小,接触面就较小,黏合效果较差。
但实践表明,打磨粗糙度不能太大,否则会形成沟槽,粘合胶界面容易窝藏空气;粗糙度太大,更有可能在表面产生浮胶,阻碍界面的黏合。
一般来讲,较适宜的粗糙度为RMA3~RMA4。
打磨面性能与其黏合力有重要关系。
黏合力主要来源于物理粘合与化学键结合。
黏合技术是一门学问,如有突破会带来翻胎技术革命。
1.打磨速度和进给量与打磨粗糙度的关系(1)打磨进给量与粗糙度的关系通常情况下,当打磨速度恒定时,如进给量较大,打磨面粗糙度较大;反之,进给量较小,打磨粗糙度较小。
实际操作中可用这种方式在一定范围内来调整想要得到的磨面粗糙度。
(2)打磨速度与粗糙度的关系当进给量恒定时,在一定变化范围内打磨速度较快,打磨面粗糙度较大;反之,打磨速度较慢,轮胎翻新胎体及预硫化胎面打磨的质量控制余广华 中国轮胎循环利用协会第九届技术委员会副主任打磨面粗糙度较小。
以这种方式调整想要得到的磨面粗糙度,其效果非常有限,因此,相对用的较少。
2.整圆打磨进给量的控制方法和要点轮胎整圆打磨加工原理和控制方法与机床(车削磨)加工有相同之处,当工具和设备确定之后,人工操作(轮胎旋转速度、打磨工具转速)可以通过调整进给量来获得需要的粗糙度。
(1)进给量的一般控制方法多数情况下,进给量的控制方法与设备操作性能及胎体打磨前状况有关。
例如,在先进的智能设备中,采用电脑程序自动控制打磨,可预先设定好打磨程序中的必要参数(有的设备中包括了进给量),打磨过程中不需要人工干预。
但目前这类设备在我国的应用并不多。
我国普遍采用充气仿形打磨机,打磨时每一次进给量都需人工操作或调整。
整圆打磨进给量的控制一般采用匀速进给方式:即每一次进给相同的量为1.5~2mm(工程机械轮胎可达3~4mm)。
农用外胎硫化前胎坯的预处理及硫化用水胎的控制
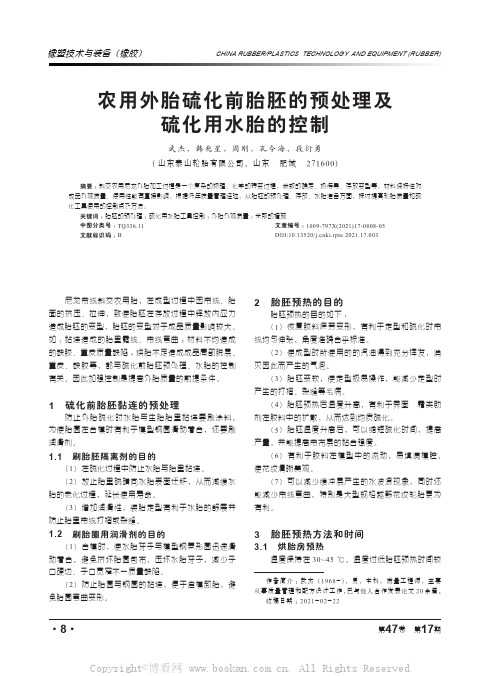
第47卷 第17期·8·作者简介:武杰(1968-),男,本科,质量工程师,主要从事质量管理和配方设计工作,已与他人合作发表论文20余篇。
收稿日期:2021-02-22尼龙帘线斜交农用胎,在成型过程中因帘线、胎面的挤压、拉伸,致使胎胚在存放过程中释放内应力造成胎胚的变型,胎胚的变型对于成品质量影响较大。
如:黏连造成的胎里露线、帘线弯曲;材料不均造成的缺胶、重皮质量缺陷;烘胎不足造成成品局部脱层、重皮、缺胶等,都与硫化前胎胚预处理、水胎的控制有关。
因此加强控制是提高外胎质量的前提条件。
1 硫化前胎胚黏连的预处理防止外胎硫化时水胎与生胎胎里黏连要刷涂料,为使胎圈在合模时有利于模型钢圈滑动着合,还要刷润滑剂。
1.1 刷胎胚隔离剂的目的(1)在硫化过程中防止水胎与胎里黏连。
(2)放止胎里硫磺向水胎表面迁移,从而减缓水胎的老化过程,延长使用寿命。
(3)增加润滑性,装胎定型有利于水胎的舒展并防止胎里帘线打褶或裂缝。
1.2 刷胎圈用润滑剂的目的(1)合模时,使水胎牙子与模型钢菱形圈迅速滑动着合,避免挤坏胎圈包布,压坏水胎牙子,减少子口硬边、子口宽窄不一质量缺陷。
(2)防止胎圈与钢圈的黏连,便于启模卸胎,避免胎圈弯曲变形。
农用外胎硫化前胎胚的预处理及硫化用水胎的控制武杰,韩兆星,周刚,孔令海,段衍勇(山东泰山轮胎有限公司,山东 肥城 271600)摘要:斜交农用尼龙外胎加工过程是一个复杂的物理、化学的转变过程,参数的确定、热传导、存放变型等,材料独特性对成品外观质量、使用性能有直接影响。
根据多年质量管理经验,从胎胚的预处理、存放、水胎准备方面,探讨提高轮胎质量和硫化工具使用的控制点及方法。
关键词:胎胚的预处理;硫化用水胎工具控制;外胎外观质量;采取的措施中图分类号:TQ336.11文章编号:1009-797X(2021)17-0008-05文献标识码:B DOI:10.13520/ki.rpte.2021.17.0032 胎胚预热的目的胎胚预热的目的如下:(1)恢复胶料疲劳变形,有利于定型和硫化时帘线均匀伸张,角度准确合乎标准。
预硫化胎面翻新工艺
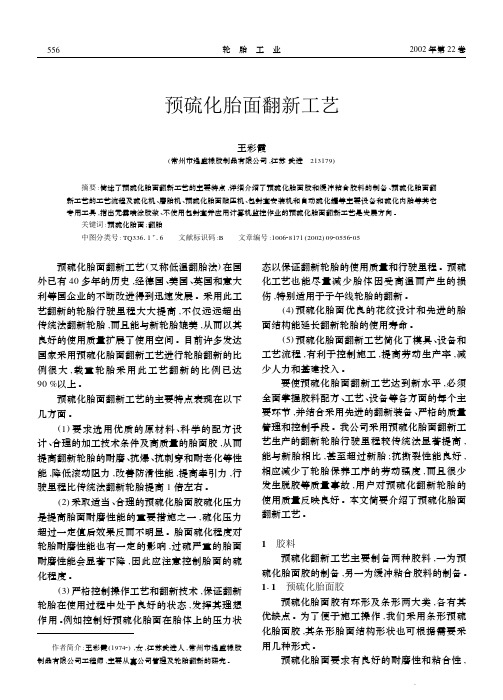
预硫化胎面翻新工艺王彩霞(常州市逸盛橡胶制品有限公司,江苏武进 213179) 摘要:简述了预硫化胎面翻新工艺的主要特点,详细介绍了预硫化胎面胶和缓冲粘合胶料的制备、预硫化胎面翻新工艺的工艺流程及硫化机、磨胎机、预硫化胎面贴压机、包封套安装机和自动硫化罐等主要设备和硫化内胎等其它专用工具,指出无需喷涂胶浆、不使用包封套并应用计算机监控作业的预硫化胎面翻新工艺是发展方向。
关键词:预硫化胎面;翻胎中图分类号:TQ33611+16 文献标识码:B 文章编号:100628171(2002)0920556205 预硫化胎面翻新工艺(又称低温翻胎法)在国外已有40多年的历史,经德国、美国、英国和意大几方面。
(1)要求选用优质的原材料、科学的配方设计、合理的加工技术条件及高质量的胎面胶,从而提高翻新轮胎的耐磨、抗爆、抗刺穿和耐老化等性能,降低滚动阻力,改善防滑性能,提高牵引力,行驶里程比传统法翻新轮胎提高1倍左右。
(2)采取适当、合理的预硫化胎面胶硫化压力是提高胎面耐磨性能的重要措施之一,硫化压力超过一定值后效果反而不明显。
胎面硫化程度对轮胎耐磨性能也有一定的影响,过硫严重的胎面耐磨性能会显著下降,因此应注意控制胎面的硫化程度。
(3)严格控制操作工艺和翻新技术,保证翻新轮胎在使用过程中处于良好的状态,发挥其理想作用。
例如控制好预硫化胎面在胎体上的压力状 作者简介:王彩霞(19742),女,江苏武进人,常州市逸盛橡胶制品有限公司工程师,主要从事公司管理及轮胎翻新的研究。
利等国企业的不断改进得到迅速发展。
采用此工艺翻新的轮胎行驶里程大大提高,不仅远远超出传统法翻新轮胎,而且能与新轮胎媲美,从而以其良好的使用质量扩展了使用空间。
目前许多发达国家采用预硫化胎面翻新工艺进行轮胎翻新的比例很大,载重轮胎采用此工艺翻新的比例已达90%以上。
预硫化胎面翻新工艺的主要特点表现在以下态以保证翻新轮胎的使用质量和行驶里程。
- 1、下载文档前请自行甄别文档内容的完整性,平台不提供额外的编辑、内容补充、找答案等附加服务。
- 2、"仅部分预览"的文档,不可在线预览部分如存在完整性等问题,可反馈申请退款(可完整预览的文档不适用该条件!)。
- 3、如文档侵犯您的权益,请联系客服反馈,我们会尽快为您处理(人工客服工作时间:9:00-18:30)。
硫化翻新轮胎的工艺研究探索提要:本文为生产翻新轮胎用的预硫化胎面实现精细硫化提供一种研究试验方法。
胎面是厚制品,由表及里,具有不同程度的不等温硫化特性。
在生产现场胎面硫化压力和温度基本稳定的情况下,通过现场试验与实验室测试结果相结合,用经典的阿累尼乌斯方程计算硫化时间的方法,再经过实际应用并加以验证其计算的精确性。
通过罐硫化对胎面继续硫化效应和老化性能的影响及数据分析,提出了对胎面硫化时间的修正,尽可能实现胎面的精确预硫化。
本文对各种厚度的预硫化胎面确定工艺时间提出了具体的测试和研究方法,有一定实用性。
关键词:预硫化胎面精细硫化工艺一、预硫化轮胎翻新精细硫化工艺重要的意义目前,我国预硫化翻新轮胎翻新产量估计已超过800万条,胎面产量不低于7万吨。
胎面精细硫化,就是要使胎面达到最佳性能的一种工艺或方法。
实现胎面精细硫化,对于提高胎面质量增加胎面耐磨性,提高生产效率,节约能源等方面,都具有相当重要的意义。
本文仅针对胎面硫化温度进行研究,胎面硫化实际上要经历两个阶段,即胎面预硫化和轮胎罐硫化。
目前多数企业基本上都是根据经验进行,或多或少地存在一些过硫或欠硫现象。
二、精细硫化原理概述预硫化翻新轮胎胎面作为一类橡胶制品,其硫化程度的分析和判断非常重要。
首先将测到的各部位胶料的时间一温度对应值列表或绘成曲线,需将胎面的最高受热界面(胎面与模具接触表面)和最低受热界面(胎面中部)找出,利用等效硫化时间计算方法,求出最高和最低受热界面的等效硫化时间。
再将各部位胶料的等效硫化时间与该胶料在实验室的正硫化时间进行比较,在胎面中部必须达到正硫化的要求时,以胎面表面的硫化程度不超出该胶料的硫化平坦范围佳。
当然,也可以将测得的所有温度与时间(t—x)曲线的等效硫化时间全部计算出来,以便精确地分析各部位胶料在硫化结束后的硫化程度的差异。
三、胎面精细硫化研究橡胶制品硫化三要素是压力、温度和时间,精细硫化要研究的问题应该是:针对具体的产品,这些要素在允许变化的范围内,如何采取最佳的硫化工艺方法,以取得最好的品质。
本文仅研究探讨不同厚度的胎面硫化温度和时间的关系,因为在模压法硫化工艺中,一旦设备和模具确定,压力也随之确定。
因此,胎面精细硫化的关键在于温度与时间的控制。
在采用蒸汽或其它加热方式的模硫化工艺中,完全可以采用简单的技术来控制模具进汽压力或温度,从而较方便地控制和稳定模具实际温度。
故本文仅针对在生产现场胎面硫化温度基本稳定的情况下,对不同厚度的胎面如何精确控制相应的硫化时间;同时,必须考虑到在二次罐硫化中对胎面继续硫化,以及工艺不稳定情况等因素。
2.胎面生产现场的温度检测(1)对胎面硫化设备的功能要求胎面硫化设备是由福建三明市宏新橡机制造有限公司根据我们提出的要求专门订制的,正常硫化时各测点间相互差值应控制在2℃。
考虑到加热温度的均匀性,每块热板应分多段蒸汽进出(7.5米机应不少于5段),并在热板上的每段安装温度传感器(共计25只),在控制台上有温度显示及温度超限报警系统,目的是监视和提示各点温度值及其偏差,以便操作者采取适当措施。
因此,设备具有以下功能:1)设备的硫化温度在145℃-160℃之间,因公司燃气锅炉自带蒸汽压力稳定系统,可根据蒸汽供应情况设定设备允许最佳基准温度。
2)要求PLC及控制系统有以下功能:①贮存硫化过程数据各点温度、系统压力、时间。
要求不少于三天工作日数据容量②同屏显示:当前时间-温度、时间-压力曲线。
温度值可采用低频率循环扫描取样。
③随时查询历史数据曲线,每屏曲线要求有日期和时间,以便追溯质量问题。
④输出接口:有USB转换接口,便于数据保存在办公电脑中。
有RS485接口,也便于与本公司现有的生产车间网络数据系统相联。
⑤要求胎面花沟排气顺畅。
排气时的压力、排气时间秒数、排气次数,可在屏上设置。
⑥要求排完气后正硫化的加压过程分三级逐步加压,用户可设定每级加压值和间隔时间。
设定后整个硫化过程自动完成。
3)提供与PC机的通信与显示编辑软件,以方便在PC机上显示、编辑、贮存上述曲线及画面。
要求编辑软件在PC机上曲线坐标分度值可变换,压缩和拉伸,以便观察曲线细节;用户可对曲线及画面进行文字标注。
(2)生产现场胎面硫化的温度检测方法胎面是较厚的橡胶制品,但由于采用双面加热硫化,其硫化速度还不算太慢。
检测点必须是胎面升温最慢的部分(最低受热面)才有代表性。
胎面胶温度监测取点方法及装置如图2所示。
图2 预硫化胎面胶温度监测点及方法示意图图中胎面厚度为19mm,上下模板温度稳定在151±1℃,PLC以每10秒钟的频率自动循环采样,因篇幅关系,数据只取其主干(每分钟一次)。
为了比较已硫化胎面胶和生胎面胶的传热升温速度,将两类胎面胶(相同的规格和厚度)用同样方法同时进行测试,其采样及测试数据如表2所示。
表2 胎面胶中部监测点随时间的硫化升温过程数据表根据表2数据,可直接用Excel自动生成升温曲线,如图3所示。
图3 已硫化胎面和生胎胶硫化温度监测升温图从图3可以看出,这两类胶升温情况是有所不同的:一是生胎面胶在合模加压毕出现拐点,这是因为模具对胶料施加压力,使其充满模具并发生形变的同时,对胶料做功导致升温加快;二是生胎面保持了较高的升温速度,胶料硫化过程伴随着化学放热反应,因而生胎面胶的升温比已硫化好的胎面胶要快一些;除此之外,这两类胶料的导热系数没有多大差别。
3.计算预硫化胎面的等效硫化时间在等温硫化的情况下,可用阿累尼乌斯方程求出在不同硫化温度条件下的等效硫化时间。
在实验中用硫化仪在不同温度时测试胶料硫化特性,或硫化薄制品当属此类情形。
(1)计算胎面胶的硫化反应活化能△E根据表1的胎面胶硫化仪数据计算硫化反应活化能△E,用阿累尼乌斯关于化学反应速度与温度关系的经验方程式可导出硫化温度和时间的关系为:方程式1方程式1中的x1和x2分别是用温度 t1、t2硫化时的工艺正硫化时间(tc90),因方程式1左端为分式,所以计算结果与时间x的计算单位无关,这里用min,如表1所示。
t1、t2为硫化温度,计算单位用热力学温度K;R为气体常数R=8.3143,量纲单位用J/(mol·K)。
△E为硫化反应活化能,量纲单位用J/mol,实验证明,在一定的温度范围内△E为常量。
将表1中的硫化温度和时间数据代入式1可计算出△E:式中用到的时间已化为十进制。
△E仅与胎面胶料的配方及实际使用的材料有关,可理解为单位胶料硫化所需的能量。
(2)计算等效硫化时间所谓等效硫化时间是对基准而言,本例中的基准温度是150℃,基准时间是硫化仪中对应的工艺正硫化时间(本例的tc90=13:13)。
这里要计算的等效硫化时间,就是实际生产胎面时所需的最小工艺硫化时间。
胎面是厚制品,特别是胎面中部的硫化要经历一个不等温的硫化过程,图3中的升温曲线明确地表达了这一点。
换言之,硫化温度是随时间变化的连续函数。
在不等温硫化计算中,应用阿累尼乌斯方程,可在试验容许的温度范围内比较精确表征硫化反应速率和温度之间的关系。
方程式2方程式2中,K为硫化反应速率常数;A为常数;其它符号与式1的含意相同。
由方程式2可以得到在试验温度(T)时,对应于基准硫化温度(T0)时的相对硫化速度(V)。
方程式3方程式3中,K、K0分别是温度 T 和 T时的硫化反应速率常数。
按规定,上述方程中的这些参量是常量或相对固定的参数,用大写字母表示;而下式中的变量则要用小写表示。
由图2可知,由于胎面中部(温度传感器监测点)的硫化是不等温过程,这一点的温度用(t)表示,它是随时间(x)连续变化的函数,即t=f(x),对应于基准温度(T)时的等效硫化时间(x*)可用下式计算:方程式4方程式4中,x 为硫化结束时的时间;x s 是硫化起始时间;V0 是基准硫化温度T0 时的相对硫化速率,V0=1方程式5方程式5中的参数t是根据生胎胶硫化监测的升温曲线,用Excel自动生成的拟合函数,如图4所示。
拟合函数表达式如下:图4 生胎胶硫化监测的升温曲线及拟合函数曲线方程式5是一个参数方程积分,很难化解为几个简单不定积分函数。
只能借助计算机数学软件,采用数值算法,在给定域内求近似解。
这里应用更简便的方法,可根据表中数据,用数学求和公式来求数值解,并借助电子表格Excel,引用方程式5计算等效硫化时间(x*)的值。
因此应设:方程式6根据表中温度和时间的采样数据,每30秒钟取样一次,△x=0.5min,任意时刻 xi 对应温度值ti, T=150+273,t=ti+273,因为方程式6中温度计算值要用热力学温度,并以胎面正常硫化温度作为基准温度T,采用求和公式计算,精度在2%以内。
减小△x能进一步提高精度。
方程式7从表3可知,应设开始硫化时间x s =x1=1(min),开始硫化温度t1 =50.8(℃),结束时刻x40=21(min),x i 共有40项。
方程式7所得结果的计算过程见表3最后一行。
表3 生胎面胶中部监测点等效硫化时间(x*)计算数据表方程式7所得等效硫化时间x*=13.68 min,如图5所示,它表示一个面积的无量纲,故这个面积的量纲仍用概念,笔者认为可理解成硫化效应。
因纵坐标WI时间单位表示。
所以,它的X轴上的值才是真正意义上的等效硫化时间,其含意=150℃硫化时的硫化效应相是胎面胶中部监测点处的硫化效应,与硫化仪在T同时,X轴所对应的硫化时间,如图5和表3所示,胎面的等效硫化时间应为21 min。
图5 胎面中部监测点达到与硫化仪相同的硫化效应时所需时间解析图4.罐硫化对胎面继续硫化效应前面通过对胎面生产硫化等效硫化时间的研究和分析,在确定的胎面厚度及硫化温度的条件下,计算出精确的工艺硫化时间。
但这个时间并不能直接使用,必须考虑在罐中的二次硫化效应对胎面的影响。
(1)罐硫化中罐内与胎面中部监测点的升温过程采用与图2原理相同的方法对罐硫化中罐内与胎面中部监测点的升温过程进行测试,曲线如图8所示。
图8 罐硫化中罐内与胎面中部监测点升温曲线(2)罐硫化对胎面的硫化效应由图8可见,硫化罐温上升较快,约40min。
为计算简便,这里可忽略胎面中部在115℃以前的时间对其产生的继续硫化作用,直接用正硫化温度时的硫化强度W与时间来计算。
方程式8值相同,其含意是胎面方程式8的计算值与表3中数据t=115℃所对应的Wi中部在t=115℃时的硫化强度只有T=150℃时的12%,由图8可知,在80min时达到115℃,硫化结束时间为190 min,在罐中胎面继续硫化时间为:X=190-80=110min故罐硫化对胎面继续硫化效应E为:方程式9E就是罐硫化过程中对胎面进行二次硫化所产生的继续硫化效应。
四、结论与分析1.二次罐硫化对胎面硫化效应的影响分析根据上述硫化原理分析,罐硫化对胎面产生了二次硫化效应,其程度等效于胎面首次硫化,换言之,生胎面的一次硫化是多余的。