浅谈常规热模锻的润滑
轧钢设备的润滑管理
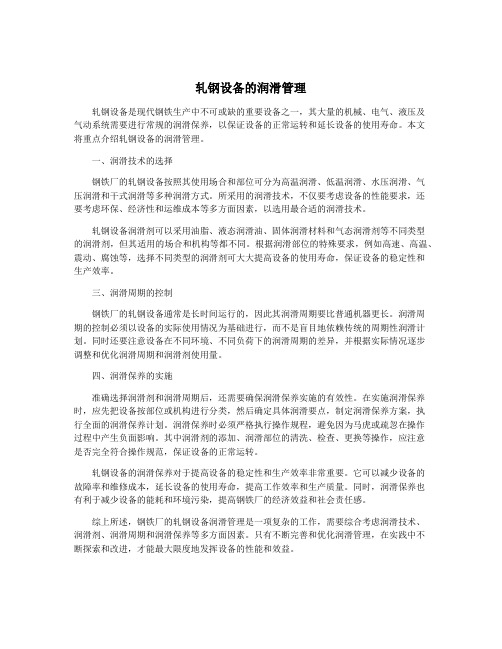
轧钢设备的润滑管理轧钢设备是现代钢铁生产中不可或缺的重要设备之一,其大量的机械、电气、液压及气动系统需要进行常规的润滑保养,以保证设备的正常运转和延长设备的使用寿命。
本文将重点介绍轧钢设备的润滑管理。
一、润滑技术的选择钢铁厂的轧钢设备按照其使用场合和部位可分为高温润滑、低温润滑、水压润滑、气压润滑和干式润滑等多种润滑方式。
所采用的润滑技术,不仅要考虑设备的性能要求,还要考虑环保、经济性和运维成本等多方面因素,以选用最合适的润滑技术。
轧钢设备润滑剂可以采用油脂、液态润滑油、固体润滑材料和气态润滑剂等不同类型的润滑剂,但其适用的场合和机构等都不同。
根据润滑部位的特殊要求,例如高速、高温、震动、腐蚀等,选择不同类型的润滑剂可大大提高设备的使用寿命,保证设备的稳定性和生产效率。
三、润滑周期的控制钢铁厂的轧钢设备通常是长时间运行的,因此其润滑周期要比普通机器更长。
润滑周期的控制必须以设备的实际使用情况为基础进行,而不是盲目地依赖传统的周期性润滑计划。
同时还要注意设备在不同环境、不同负荷下的润滑周期的差异,并根据实际情况逐步调整和优化润滑周期和润滑剂使用量。
四、润滑保养的实施准确选择润滑剂和润滑周期后,还需要确保润滑保养实施的有效性。
在实施润滑保养时,应先把设备按部位或机构进行分类,然后确定具体润滑要点,制定润滑保养方案,执行全面的润滑保养计划。
润滑保养时必须严格执行操作规程,避免因为马虎或疏忽在操作过程中产生负面影响。
其中润滑剂的添加、润滑部位的清洗、检查、更换等操作,应注意是否完全符合操作规范,保证设备的正常运转。
轧钢设备的润滑保养对于提高设备的稳定性和生产效率非常重要。
它可以减少设备的故障率和维修成本,延长设备的使用寿命,提高工作效率和生产质量。
同时,润滑保养也有利于减少设备的能耗和环境污染,提高钢铁厂的经济效益和社会责任感。
综上所述,钢铁厂的轧钢设备润滑管理是一项复杂的工作,需要综合考虑润滑技术、润滑剂、润滑周期和润滑保养等多方面因素。
热模锻压机常见故障分析及排除方法

1)制动器打滑,压力机不能制动
2)制动器发热
1)摩擦片(块)磨损;制动弹簧力不够;摩擦片(块)沾油
2)未接冷却水;制动器行程调整不当,制动器脱不开
1)更换摩擦片(块);调整弹簧力或成组更换弹簧;清洗摩擦片(块)
2)接通冷却水,保证冷却水温度低于40度,调整制动器行程
5
1)V带打滑
2)V带严重磨损或磨损不匀
热模锻压机常见故障分析及排除方法
1
闷车
1)封闭高度调整过低(新安装模具易出现这种情况)
2)锻件温度低,毛坯尺寸大
3)离合器,制动器凸轮开关调整不当
4)电动机达不到额定转速,电动机传动带松
5)离合器内部进油,摩擦盘打滑
6)大带轮摩擦保险打滑或螺栓预紧力不够
1)重新调整封闭高度尺寸
2)控制锻件温度,检查毛坯尺寸
2)离合器调整不当,摩擦盘变形,弹簧失效等造成离合器不能完全脱开
3)偏心轴轴承套磨损严重,间隙过大;偏心轴曲柄轴向止推环磨损严重,轴承座紧固螺栓松
1)检查空气管路,保证压缩空气压力符合要求,清洗或更换摩擦片
2)调整离合器各摩擦盘及活塞行程;更换或修复变形的摩擦盘,成组更换弹簧
3)修复轴承套,更换轴向止推环;重新坚固螺栓,楔紧楔铁
1)V带太松
2)V带太紧,两轮的型槽未对准或不平行
1)调整电动机座,适当涨紧V带
2)调整电动机座,适当放松V带;调整带轮位置,对准带轮槽
6
空运转时电流过高
1)摩擦盘间隙调整不当
2)脱落的摩擦片(块)在主动盘和被动盘之间产生摩擦
3)活塞行程小或活塞与气缸之间掉进杂物,将活塞卡住
4)传动带过紧
1)重新调整摩擦盘间隙
2)清除脱落的摩擦片(块)
浅谈铝轧制工艺和润滑
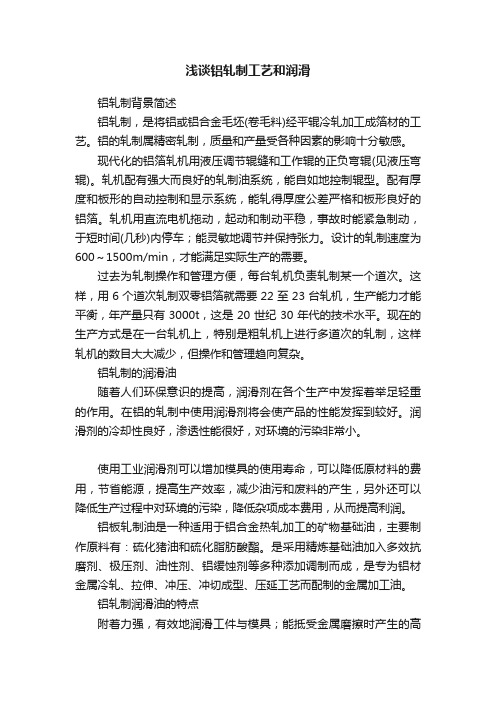
浅谈铝轧制工艺和润滑铝轧制背景简述铝轧制,是将铝或铝合金毛坯(卷毛料)经平辊冷轧加工成箔材的工艺。
铝的轧制属精密轧制,质量和产量受各种因素的影响十分敏感。
现代化的铝箔轧机用液压调节辊缝和工作辊的正负弯辊(见液压弯辊)。
轧机配有强大而良好的轧制油系统,能自如地控制辊型。
配有厚度和板形的自动控制和显示系统,能轧得厚度公差严格和板形良好的铝箔。
轧机用直流电机拖动,起动和制动平稳,事故时能紧急制动,于短时间(几秒)内停车;能灵敏地调节并保持张力。
设计的轧制速度为600~1500m/min,才能满足实际生产的需要。
过去为轧制操作和管理方便,每台轧机负责轧制某一个道次。
这样,用6个道次轧制双零铝箔就需要22至23台轧机,生产能力才能平衡,年产量只有3000t,这是20世纪30年代的技术水平。
现在的生产方式是在一台轧机上,特别是粗轧机上进行多道次的轧制,这样轧机的数目大大减少,但操作和管理趋向复杂。
铝轧制的润滑油随着人们环保意识的提高,润滑剂在各个生产中发挥着举足轻重的作用。
在铝的轧制中使用润滑剂将会使产品的性能发挥到较好。
润滑剂的冷却性良好,渗透性能很好,对环境的污染非常小。
使用工业润滑剂可以增加模具的使用寿命,可以降低原材料的费用,节省能源,提高生产效率,减少油污和废料的产生,另外还可以降低生产过程中对环境的污染,降低杂项成本费用,从而提高利润。
铝板轧制油是一种适用于铝合金热轧加工的矿物基础油,主要制作原料有:硫化猪油和硫化脂肪酸酯。
是采用精炼基础油加入多效抗磨剂、极压剂、油性剂、铝缓蚀剂等多种添加调制而成,是专为铝材金属冷轧、拉伸、冲压、冲切成型、压延工艺而配制的金属加工油。
铝轧制润滑油的特点附着力强,有效地润滑工件与模具;能抵受金属磨擦时产生的高温。
保证连续有效的油膜厚度,避免模具的局部刮伤或烧结;具有优异的极压抗磨性,优良的润滑性能,减少模具磨损,减少产品毛刺;防锈性能好,防止工件腐蚀。
极高润滑效果,在塑性变化中不断提供高效润滑减摩膜,能有效地提高工件表面质量,有效减少划痕、划伤、烧结焊合、破裂等现象的发生;优异的极压性能保证在高、深、难的加工工况下,有效提高工件的质量和加工功率,增加模具寿命。
热模锻压机常见故障分析及排除方法

1)调整导轨间隙
2)清洗导轨面及清除划痕,过滤润滑油
3)检查各供油管道,调整主,辅导轨
4)更换摩擦片;调整离合器,制动器凸轮开关位置
3
1)压力机正常工作时,离合器打滑
2)离合器发热
3)离合器跳动或窜动
1)气压降低,离合器内部进油,摩擦盘打滑,摩擦片磨损严重
1)V带太松
2)V带太紧,两轮的型槽未对准或不平行
1)调整电动机座,适当涨紧V带
2)调整电动机座,适当放松V带;调整带轮位置,对准带轮槽
6
空运转时电流过高
1)摩擦盘间隙调整不当
2)脱落的摩擦片(块)在主动盘和被动盘之间产生摩擦
3)活塞行程小或活塞与气缸之间掉进杂物,将活塞卡住
4)传动带过紧
1)重新调整摩擦盘间隙
3)按要求调整凸轮开关
4)检修电动机,保证电动机额定转速,重新预紧传动带
5)清洗摩擦盘,摩擦片(块)
6)拆检摩擦保险,预紧螺栓
2
1)滑块卡死
2)滑块导轨面研伤有划痕
3)导轨面缺少润滑油
4)滑块不能停在上死点位置
1)滑块导轨间隙小
2)油脏或导轨面进入氧化皮或其他杂物
3)润滑油路堵塞,主,辅导轨(象鼻形滑块)间隙调整不当
2)清除脱落的摩擦片(块)
3)调整活塞行程,清除杂物
4)调整传动带松紧适宜
7
压力机连击(即一次行程控制不住)
1)凸轮开关失灵
2)离合器摩擦片(块)脱落卡住
3)进气头卡住,离合器不排气
1)检修凸轮开关
2)排除破碎脱落的摩擦片(块)
3)拆检进气头
2)离合器调整不当,摩擦盘变形,弹簧失效等造成离合器不能完全脱开
浅谈金属压力加工中的摩擦与润滑

浅谈金属压力加工中的摩擦与润滑发布时间:2022-09-25T05:10:09.480Z 来源:《科学与技术》2022年第10期5月作者:闫亮[导读] 近些年来,随着科技的不断发展,金属压力加工工艺也逐渐进步闫亮天津冶金集团天材科技发展有限公司天津市摘要:近些年来,随着科技的不断发展,金属压力加工工艺也逐渐进步,通过液压系统施加外力作用在模具或相应的轧机设备,使坯料产生形变达到所需要的比例和尺寸的过程。
在加工过程中,由于钢铁表面粗糙程度的不同,会产生摩擦力,摩擦力的存在会使得压制或轧制过程变得非常困难,因此,为了抵消摩擦力,采用相应的润滑技术来提高加工的精准度,金属压力加工润滑技术最早是由英国人提出的,随着金属材料成型技术的发展,国内很多科学家也展开这方面的研究,并研制出种类繁多的润滑剂,如:石墨润滑剂、拉延油等。
关键词:润滑技术;金属压力加工;技术应用中图分类号:TE626 文献标识码:A 引言金属加工液,又称金属加工润滑剂,是指在金属及其合金的切割、冲压、轧制和拉拔等各种加工过程中使用的润滑剂。
它是金属加工过程中的重要支撑材料。
金属工作液的主要功能是润滑、冷却、防锈和清洁。
它的使用可以提高加工的表面光洁度,延长刀具的使用寿命,提高生产效率。
金属加工液由基本成分和添加剂组成。
基本成分是金属加工液的主要成分。
乳液和微乳液是指基础油,合成液是指主要成分,如聚醚、合成酯或大量水。
1 摩擦和润滑的机理在金属压力加工的实施中,主要分为吸附摩擦、干摩擦、液体摩擦等许多方面。
在金属压力加工过程中,金属工件的晶体在受到外力作用后会沿滑动方向滑动。
根据宏观分析,在金属塑性变形的实现过程中,在滑移单元的协同作用下会出现滑移。
因此,对于特定的塑性变形,它是一个金属剪切流动变形的过程。
因此,加工中的摩擦力可以有效地克服流动剪切力。
在金属压力加工的实施过程中,需要将润滑剂直接添加到刀具和工件之间的间隙中,以减少接触载荷,并确保其自身承受的应力始终处于相对较低的状态。
铝合金热模锻润滑机理研究与应用

第!"卷第!期#$%&!" '$&!!"#$%&$'()*+,%&$)-./&"0"$1()*)年+月,-./()*)铝合金热模锻润滑机理研究与应用李伟华 董选普 陈晓君 吴香清!华中科技大学材料成形与模具技术国家重点实验室"湖北武汉0!))10#摘要 针对传统铝合金热模锻润滑剂进行成膜性和摩擦系数试验"结果表明"含磷酸盐水基石墨在模具表面形成化学反应膜"摩擦系数最小且随温度变化平稳$油基石墨和石墨润滑脂接触面大部分为薄膜润滑"试样表面光洁度较高%同时针对石墨和油斑难清理及环境污染的缺点"提出一种新型环保无石墨润滑剂"可降低摩擦系数和提高试样表面光洁%关键词 铝合金$热模锻$润滑机理!"#&$%&'()('*&+,,-&$%%%.'(/%&0%$%&%'&中图分类号 12'3)&$) 文献标识码 4 文章编号$%%%.'(/% 0%$% %'.56,6789:7-;7<<=+97>+?-?@=A B 8+97>+?-C 69:7-+,C@?87=A C +-A C7==?D :?>;+6@?8E +-EF #G 6+.:A 7"!"H 2I A 7-.<A "JKL HI +7?.*A -"G MI +7-E .N +-E!23435657849$:43$:7$;<435:=4%>$:?=.@4.AB =5C <$-%AD 5E F .$%$@7"G -4H F $.@I .=J 5:K =37$;2E =5.E 54.AD 5E F .$%$@7"L -F 4.0!))10"M F =.4#4B ,>879>&D F 5;=%?N ;$:?=.@O :$O 5:374.A ;:=E 3=$.E $5;;=E =5.3F $3;$:@=.@%-9:=E 4.3KP 5:535K 35A ;$:3:4A =3=$.4%4%-?=.-?4%%$7/D F 5:5K -%3K K F $P3F 433F 5E F 5?=E 4%:54E 3=$.;=%?=K ;$:?5A $.3F 5?$%A K -:;4E 5973F 5P 435:N 94K 5A @:4OF =35E $.N 34=.=.@O F $K O F 435"4.A 3F 5;:=E 3=$.E $5;;=E =5.3=K 3F 5K ?4%%5K 34.A K 349%5P =3F 35?O 5:43-:5E F 4.@=.@$?$K 3$;3F 5E $.34E 3K -:;4E 5953P 55.$=%N 94K 5A %-9:=E 4.3@:4O F =354.A @:4O F =35@:54K 5%-9:=E 43=$.34Q 5K $.3F =.;=%?%-9:=E 43=$.E $.A =3=$."4.A 3F 5K -:;4E 5$;K O 5E =?5.F 4K 4@$$A ;=.=K F /<54.P F =%5";$:3F 5@:4O F =354.A $=%K O $3K 4:5A =;;=E -%33$E %54.4.A 3F 5O :$9N %5?$;5.J =:$.?5.34%O $%%-3=$."4.5P 37O 5$;5.J =:$.?5.34%%7;:=5.A %7.$.N @:4O F =35%-9:=E 4.3KP 4K O -3;$:P 4:A /R 3E 4.:5A -E 5;:=E 3=$.E $5;;=E =5.34.A =?O :$J 53F 5K ?$$3F K -:;4E 5$;3F 5K 4?O%5/O 6DP ?8;,&4%-?=.-?4%%$7$F $3;$:@=.@$%-9:=E 43=$.?5E F 4.=K ?收稿日期 ())S N *(N )S $修订日期 ()*)N )!N !)基金项目 国家重大专项!())S H T )0))")**#$材料成形与模具技术国家重点实验室基金项目!)()(**)))+#作者简介 李伟华!*S U +V #男"硕士研究生$通讯作者&董选普电子信箱 %=P 5=F -4))1 *(+&E $?$A $.@T O?4=%&F -K 3&5A -&E . 随着我国航空航天工业的发展"铝合金热模锻件需求量越来越大"精度要求也越来越高"而锻件的质量直接与模具的润滑有关%但是国内针对铝合金热模锻的润滑研究相对较少"尤其是对铝合金热模锻润滑剂性能的分析(*0)"同时市场上针对铝合金热模锻的润滑剂类型单一"常为石墨系润滑剂(()"虽然石墨具有优良的高温润滑性"但石墨的黑和脏"使得热锻环境恶劣"危害工人健康"并污染环境(!)%因此"本文针对铝合金热模锻工艺"通过对水基石墨"油基石墨和石墨润滑脂这!种传统润滑剂进行成膜性和摩擦系数试验"对比分析了上述润滑剂的成膜性"摩擦系数"试样表面及环境污染情况"同时针对石墨的缺点"对传统模锻润滑剂进行改进"建立了新型环保润滑模型"配制了*种无石墨润滑剂"取得了良好的试验结果%* 试验材料及方法$&$ 试验材料国内模锻用润滑剂通常由!部分组成&!*#主要起润滑作用的基体"如胶体石墨"二硫化钼"硬脂酸盐等$!(#载体又称溶剂"如水"矿物油等$!!#改善润滑剂综合性能的添加剂"如增粘剂*抗氧化剂*极压剂*防锈剂和防腐剂等"同时根据载体的不同"可将润滑剂分为水基型"油基型和润滑脂!种类型(0)%本试验选用的润滑材料有胶体石墨"硬脂酸钠及硬脂酸钙"并配制了如表*试验用润滑剂%$&0 成膜性试验通常铝合金热模锻温度范围为!+)0U )W "模具预热的温度在(") 0()W "因此该成膜性试验模具的加热温度取其预热温度的上限即0()W "然后用喷涂或手工涂抹上润滑剂%该试验的目的是检验润滑剂的高温成膜延展性"对于油基体润滑剂可检测其燃烧情况"水基体润滑剂则可以检测粘结剂性能"同时还可分析其环境污染方面的问题%表$ 试验用润滑剂17B =6$ FA B 8+97->>6,>序号名称成分*水基石墨*水"胶体石墨(水基石墨(水"胶体石墨"磷酸钠!油基石墨*矿物油"胶体石墨0油基石墨(矿物油"胶体石墨"硬脂酸钙"石墨润滑脂矿物油"胶体石墨"硬脂酸钠$&' 摩擦系数试验本试验采用圆环镦粗法即将一定尺寸的圆环件在平砧间进行压缩变形"由圆环件的变形情况推算接触面上的摩擦系数%圆环试样材料为+X )(!8B (#"其尺寸及精度要求见图*%本试验测试了表*所列润滑剂的高温摩擦系数"其测试温度分别为!1)"!S )"0*)"0!)和0")W %测试时将配制好的润滑剂喷涂或手工刷涂在上下模具上"喷涂之前应用丙酮清洗模具和圆环试样表面"去除表面油污杂质等%图* 圆环试样尺寸及精度>=@&* 24?O %5K =H 54.A O :5E =K =$.$;:=.@( 试验结果分析0&$ 试验润滑剂成膜性分析表(为成膜性试验结果"从表(可以得出&水基石墨(中的磷酸盐与模具表面生成化学反应膜"膜的结合强度高"膜中石墨颗粒分布较均匀"多次使用该润滑剂则模具表面的石墨层很难清理"而水基石墨*则是石墨颗粒松散的附着在模具表面"用水很容易清洗掉$油基石墨*的铺展性要比水基石墨要好"但是油份烧损严重"致使石墨颗粒不能均匀分布"而油基石墨(中的硬脂酸盐在此温度下已熔化成液态"使得石墨颗粒分布较为均匀$石墨润滑脂中石墨分布与油基石墨(相同"但三者残留油膜均不易清理(")%另外从环保的角度来看&以上"种润滑剂均有不同程度的环境污染"水基石墨使用时产生的水汽和烟尘中混有一氧化碳和石墨颗粒"很容易对人体造成危害"还可能造成电器短路事故$油基石墨中油份烧损时产生的油烟均是一些不完全燃烧的气体和烟尘"对环境的危害更为严重%表0 成膜性试验17B =60 L Q <68+C 6->7=@+=C 序号使用方式环境影响成膜及铺展状态*喷涂水汽"烟尘成膜"不牢靠"颗粒分布不均(喷涂水汽"烟尘成膜"牢靠"颗粒分布均匀!刷涂油烟成膜"油份烧损严重"颗粒分布不均0刷涂油烟成膜"油份烧损严重"颗粒分布较均匀"刷涂水汽"油烟成膜"油份烧损严重"颗粒分布较均匀0&0 试验润滑剂摩擦系数分析图(为试验润滑剂的高温摩擦系数测试结果"从图(可以看出&在!1) 0")W 温度范围内"水基石墨(的摩擦系数最小"水基石墨*的最大"中间依次为油基石墨(*石墨润滑脂及油基石墨*$随着温度的升高"水基石墨**油基石墨*及水基石墨(摩擦系数均呈上升趋势"其中水基石墨*上升趋势最明显"增加将近了)&*("油基石墨*和水基石墨(则变化较为平稳$石墨润滑脂和油基石墨(的摩擦系数则随温度的升高而出现一定的波动"其差值不超过)&)"%由前面的分析可知"水基石墨*形成的润滑膜是石墨颗粒松散的附着在模具表面"压缩过程中很容易发生破坏从而产生粘模"而水基石墨(则在模具表生成化学反应膜"压缩过程中不容易破坏"但是石墨受环境因素如温度*水分*气氛等有部分消耗"使得其润滑性有一定的降低$油基石墨*则在模具表面形成化学吸附膜"模具与试样接触面大部分为边界流体润滑"而在油份烧损严重的地方则由石墨起润滑作用"而油基石墨(也是形成化学吸附膜"与油基石墨*不同的是在油份缺失的地方则是由硬脂酸盐和石墨共同起润滑作用"其中硬脂酸盐则呈液态或熔融态"增大了边界流体润滑面积"增强了模具与试样间的润滑$石墨润滑脂主要成分与油基石墨相同"其润滑原理是一致的%0&' 圆环试样表面分析图!为!S )W 下压制圆环试样的表面情况"从图!可以看出"整体上采用油基石墨和石墨润滑脂压制的圆环试样表面比水基石墨要光洁"油基石墨和石墨润滑脂的试样表面有残留油斑"水基石墨的试样表面则有残留石墨层"这都是很难清理的$水基石墨*的试样表面凹凸不平"这是由于石墨颗粒"1*第!期李伟华等&铝合金热模锻润滑机理研究与应用图( 试验用润滑剂高温摩擦系数>=@&( Y T O5:=?5.34%F=@F N35?O5:43-:5%-9:=E4.3;:=E3=$.E$5;;=E=5.3是松散的吸附在模具表面"压缩时润滑膜很容易破坏"致使试样与模具接触并产生粘模"而水基石墨(的试样表面则较为平整$油基石墨*刷涂到上下模具上时"润滑膜大部分为液态"油份烧损的部分则由石墨来起润滑作用"而油基石墨(和石墨润滑脂中油份烧损的部分"不仅有石墨还有液态的硬脂酸盐"在压缩的过程中石墨与模具接触较少"因此残留在试样表面的石墨颗粒比油基石墨*要少%图! !S)W圆环试样表面!4#水基石墨* !9#水基石墨( !E#油基石墨*!A#油基石墨( !5#石墨润滑脂>=@&! 2-:;4E5$;:=.@K4?O%543!S)W!4#L435:N94K5A@:4O F=35* !9#L435:N94K5A@:4O F=35( !E#Z=%N94K5A@:4O F=35* !A#Z=%N94K5A@:4O F=35( !5#[:4O F=35@:54K50&/ 传统润滑模型的改进及应用通过上述!方面的分析"能够对这"种润滑剂有较为清晰的了解"这"种润滑剂均为石墨系润滑剂"鉴于石墨的污染与难清理等问题"本文对传统的石墨型润滑剂进行改进"提出*种新型的润滑模型"如图0所示%本文采用硬脂酸钙为润滑材料(+)"乙醇为载体"再加入适量\#]"其中\#]作用有(点&一是使硬脂酸钙颗粒均匀分散在乙醇液体中$二是增强硬脂酸钙与金属模具表面的结合%当该润滑剂喷涂到模具表面时"乙醇迅速挥发掉"短时间内在\#]的作用下硬脂酸钙颗粒均匀分散于模具表面"随着压缩的进行"\#]开始软化和烧损"而硬脂酸钙也熔化成液态"于是在试样与模具表面形成了一层液态润滑膜"可明显减少粘模的发生%从图"可以看出"改进润滑剂的摩擦系数均比传统润滑剂要小"随温度变化也相对平稳"另外从图+可以看出"改进润滑剂的试样表面有明显的改善"残留的硬脂酸钙用热水很容易清理掉"整个测试过程中除了酒精迅速挥发外"其他对环境的污染均较小%图0 改进润滑模型>=@&0 R?O:$J5A%-9:=E43=$.?$A5%图" 改进润滑剂与传统润滑剂摩擦系数对比>=@&" R?O:$J5A%-9:=E4.3;:=E3=$.E$5;;=E=5.3E$?O4:5AP=3FE$.J5.3=$.4%%-9:=E4.3K! 结论!*#水基石墨(在模具表面形成化学反应膜使得其膜的稳定性均高于物理吸附的水基石墨**油基石墨**油基石墨(及油基石墨!"其摩擦系数也明显较小且随温度变化平稳%!(#油基石墨和石墨润滑脂大部分接触面为边界流体润滑状态使得其试样表面的光洁度均高于水基石墨"但是残留的油斑和石墨很难清理%+1*锻 压 技 术 第!"卷图+ !S)W改进润滑剂与传统润滑剂试样表面对比4 改进润滑剂 9 水基石墨( E 油基石墨( >=@&+ R?O:$J5A%-9:=E4.3$;K4?O%543!S)WE$?O4:5AP=3F E$.J5.3=$.4%%-9:=E4.3K4 R?O:$J5A%-9:=E4.3 9 L435:N94K5A@:4O F=35(E Z=%N94K5A@:4O F=35( ! 依照改进润滑膜型配制的润滑剂与传统润滑剂相比 摩擦系数明显降低 试样表面光洁得到改善 残留硬脂酸钙容易清理且对环境的污染减小参考文献* 朱本 高爱华 陈能秀 等/铝合金精密模锻润滑剂的研究与应用 , /中南冶金学院学报 *S S* (( ! (S0!))/ ( 姜瑞虎 于群/热锻润滑剂的开发与应用 , /山东机械 *S S0 0 !*!0/! 王文斌 胡汉国 张华豪/环保型热模锻压剂的研制及应用 , /汉南石油 ())( *+ ( """1/0 吴代斌/热模锻润滑剂的探讨 , /金属成形工艺 *S S!** 0 *+"*++/" 赵振铎 邵明志 张昭锋 等/金属塑性成形中的磨擦与润滑 < /北京 化学工业出版社 ())0/+ 聂振江/轻合金热模锻用粉末状无石墨工艺润滑剂 , /轻合金加工技术 *S1! " 00"*/11*第!期李伟华等 铝合金热模锻润滑机理研究与应用。
热模锻压力机的规格及参数

热模锻压力机的规格及参数热模锻压力机作为金属成形领域的关键设备之一,在工业制造中具有广泛应用。
本文深入解析热模锻压力机的规格和参数,包括结构特点、压力范围、温度控制等方面,旨在帮助读者更全面地了解该设备,并为其在实际应用中提供参考。
一、引言热模锻压力机是一种用于加热金属材料并通过压力塑性变形的设备,广泛应用于航空、汽车、能源等行业。
了解其规格和参数对于合理选择和使用设备至关重要。
二、热模锻压力机的规格特点结构特点:机身结构:热模锻压力机通常采用坚固的钢结构,以确保在高压力和高温环境下的稳定运行。
传动系统:常见的传动方式包括液压传动和机械传动,传动系统的设计直接关系到设备的性能。
控制系统:先进的控制系统能够确保热模锻压力机在加热、锻压等过程中具有精准的控制和监测功能。
压力范围:额定压力:热模锻压力机的额定压力通常是其设计和制造的重要参数,决定了设备在实际工作中的承载能力。
调整范围:一些热模锻压力机具有可调的压力范围,以适应不同工件的锻压需求。
三、热模锻压力机的参数解析温度控制:加热方式:热模锻压力机通常通过电加热或火炉加热方式,确保工件达到适宜的锻造温度。
温度控制精度:先进的温度控制系统能够提供高精度的温度控制,确保工件在锻造过程中达到设计要求的温度。
锻造能力:锻造频率:热模锻压力机的锻造频率影响到生产效率,不同工艺要求可能需要不同频率的锻造。
最大锻造尺寸:参数中的最大锻造尺寸是设备能够处理的工件的最大尺寸,对于选择设备时需要考虑工件的大小。
能效和环保:能效设计:先进的能效设计可以降低能耗,提高设备的工作效率,符合节能环保的要求。
废气处理:热模锻压力机在工作过程中可能产生废气,设备是否配备废气处理系统对于环保意识的提高至关重要。
四、实际应用中的建议工艺匹配:在选择热模锻压力机时,需要充分考虑工件的材料、形状和尺寸等因素,确保设备的规格和参数与实际工艺需求相匹配。
系统集成:如果热模锻压力机需要与其他设备进行配合工作,建议采用可以实现系统集成的设备,以提高整体工作效率。
热模锻工艺介绍 180813
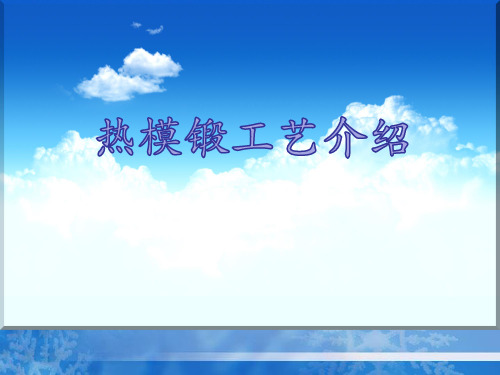
1)模锻锤: G=(3.5~6.3)KF(公斤) 2)热模锻压力机 P=(6.3~7.4)F(吨) 圆形锻件:P=8(1-0.001D)(1.1+20/D)2 FБbt 非圆形:P=8(1-0.001D)(1.1+20/D)2 (1+0.1 )FБbt 3)平锻机 P=5(1-0.001D)(D+10)2Бbt 4)螺旋压力机 P=KБbtF
热模锻压力机 (曲柄压力机)
和同样能力的模锻锤相比, 热模锻压力机的初次投资 大,但维护费用低,动力 消耗小。
和摩擦压力机模锻相比, 生产率较高,便于自动化。
热模锻压力机结构复杂, 制造条件要求高。
螺旋压力机种类:
摩擦螺旋压力机 电动螺旋压力机 离合器螺旋压力机 液压传动螺旋压力机
1、摩擦压力机靠飞轮积蓄 的能量工作,原则上可多次打击 干大活。实际有效打击次数不超 过3次。
键块分别紧固在锤头和下模座
的燕尾槽中。
•
燕尾使模块固定在锤头
(或砧座)上,使燕尾底面与
锤头(或砧座)底面紧密贴合。
•
楔铁使模块在左右方向定
位。键块使模块在前后方向定
位。
热模锻压力机与模锻锤相比,其 工作特性为: (1)静压成形,无震动和噪音; (2)机架和曲柄连杆机构的刚性 大,工作时弹性变形小; (3)滑块行程一定,每一模锻工 步只要一次行程完成; (4)导向精度和承受偏载的能力 强; (5)有上下顶件装置,便于锻件 脱模。
部分汽车件产品
转向系统 Steering System
制动系统 Braking System
传动系统 Drive System
➢ 转向系统 Components of Steering System
紫铜触指精锻过程中的摩擦与润滑
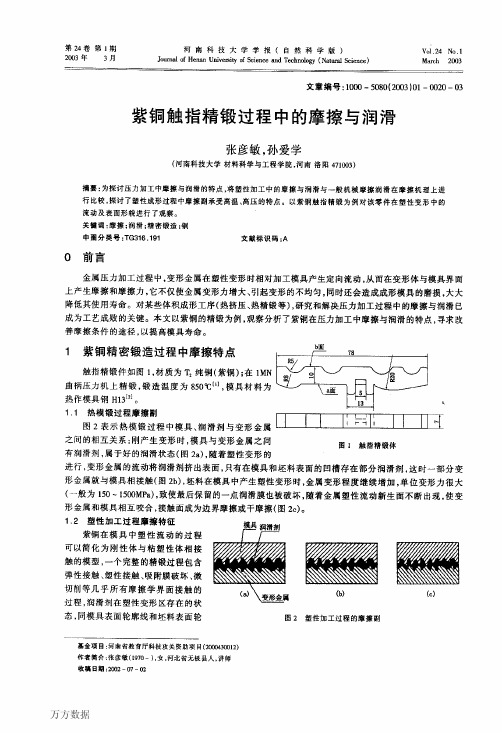
第1期张彦敏等:紫铜触指精锻过程中的摩擦与润滑廓线的凸凹状态密切相关。
随着变形力的增加,变形金属和模具之间的润滑剂逐渐减少,最后只存在于凹槽中;单位压力继续增加,则摩擦副中较硬的模具突起压人到较软的坯料中,使塑性接触面积急剧增加,金属塑性流动时伴随严重的摩擦与磨损。
高温、高压下精锻过程中,模具的工作面与粘性流动的金属变形体之间的摩擦称为塑性摩擦。
虽然界面问有润滑剂作为隔离层,但由于变形体的塑性变形和流动,使摩擦副表面面积接触率接近于1(甚至有时大于1)。
如图3所示,虽然接触面积不存在摩擦体绝对接触,但实际接触面积比一般机器摩擦大得多01。
1.3塑性加工中摩擦副承受高压图图(a)一般机器摩擦(b)塑性摩擦精锻过程中,单位变形力高达150~1500MPa,是一般机器摩图3压力加工摩擦界面示意图擦的几十至上百倍,从而使产生隔离层的润滑剂被大量挤出,隔离层变薄,局部形成边界摩擦或干摩擦使摩擦系数加大;高的单位变形力使摩擦面的实际接触面积增加,因而摩擦力大大增加;并且塑性变形出现的金属新生面有强烈的化学活性,与模具表面易产生分子咬合和很强的粘着能,使金属流动阻力进一步加大。
金属与模具界面之间的边界摩擦或干摩擦状态,使高压下模具表面微凸峰压入金属表面,并使金属翅性流动时在其表面产生划痕,犁削下的金属在高压下形成磨片。
最终氧化膜碎片和变形金属剥落碎片形成磨粒。
严重恶化变形金属与模具界面的摩擦条件。
1.4塑性加工中高温的影响高温下变形金属表面产生的氧化膜在精锻变形过程中大部分随变形金属被挤出,剩余部分破碎形成硬质点,分布在模具和坯料之间。
润滑剂在高温下也会部分分解。
高温变形金属流动过程中,表层变形剧烈,同时塑性流动使变形金属新生表面不断出现“】。
2紫铜合金塑性变形后表面微观形貌观察自精锻件上切取lOmm×lOmm×lOmm试样,经丙酮清洗后再经超声波清洗,在JSM.35CF扫描电镜上观察与模具接触面微观形貌。
锻模基础知识讲座-精选

2-2 锻模的基本失效形式 锻模在上述复杂条件下工作,其失 效形式也复杂多样。其基本失效形式有 型腔部分的模壁断裂、燕尾开裂、型腔 表面的热疲劳、塑性变形和磨损。
一、模具的断裂 模具的断裂不仅影响 生产,而且危及人身安全,是最危险的 一种失效形式。
1、模具断裂的类型 按断裂的性质,可分 为早期脆性断裂和机械疲劳断裂两种类型。
3、较高的回火稳定性和良好的抗氧 化性:在工作时不致因受热产生硬度 下降的现象,防止模具产生早期塑变、 和型腔表面粗糙度下降。 4、淬透性能好:能使尺寸较大的锻 模在整个截面上性能一致性。 5、良好的加工工艺性能:便于热加 工和切削加工。
其二是多模膛锻造时燕尾与锤头和 砧座的燕尾槽接触,而两侧是悬空的, 由于上述隐患的存在,偏心打击时燕尾 根部转角处应力集中较大而造成破坏;
其三设计不合理、制造不良或设备 与模具结合部变形造成模块两侧(肩部) 与锤头、模座接触,而使燕尾悬空,更 容易造成破坏;
其四是模具本身材质和锻造缺陷及 纤维方向不对、燕尾部分热处理硬度偏 高,也易造成这种破坏。燕尾部位硬度 低对裂纹萌生的抗力低,硬度过高则对 裂纹扩展的抗力低。一般燕尾部分的硬 度应比模腔部分低HRC 5~7度。
因此,对于已产生热裂纹 的锻模,在使用到一定程度时 要及时焊补和翻修,防止模具 断裂。
三、型腔表面的磨损 锻模在机械负荷和热负 荷双重作用下,一方面坯料对型腔表面产生 冲击性的接触应力,另一方面坯料塑变流动 对型腔表面产生强烈的摩擦。在型腔表面与 坯料滑动摩擦较小的部位(在模具的突出 部),由于较大接触应力的重复作用,易使 形腔表面产生小块剥落,形成痘状麻坑。在 型腔表面受坯料滑动摩擦较大的部位(在模 腔的口部和飞边槽桥部),由于摩擦切应力 和热负荷的作用,易产生氧化磨损和热粘着 磨损,坯料与模具型腔局部发生粘合,继而 在粘合处产生擦伤沟槽,在粘合处产生破坏。
金属塑性加工的润滑(金属加工之二)
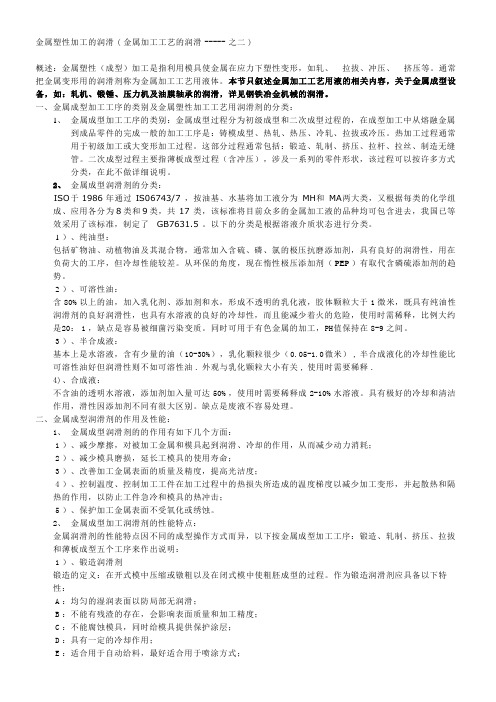
金属塑性加工的润滑(金属加工工艺的润滑-----之二)概述:金属塑性(成型)加工是指利用模具使金属在应力下塑性变形,如轧、拉拔、冲压、挤压等。
通常把金属变形用的润滑剂称为金属加工工艺用液体。
本节只叙述金属加工工艺用液的相关内容,关于金属成型设备,如:轧机、锻锤、压力机及油膜轴承的润滑,详见钢铁冶金机械的润滑。
一、金属成型加工工序的类别及金属塑性加工工艺用润滑剂的分类:1、金属成型加工工序的类别:金属成型过程分为初级成型和二次成型过程的,在成型加工中从熔融金属到成品零件的完成一般的加工工序是:铸模成型、热轧、热压、冷轧、拉拔或冷压。
热加工过程通常用于初级加工或大变形加工过程。
这部分过程通常包括:锻造、轧制、挤压、拉杆、拉丝、制造无缝管。
二次成型过程主要指薄板成型过程(含冲压),涉及一系列的零件形状,该过程可以按许多方式分类,在此不做详细说明。
2、金属成型润滑剂的分类:ISO于1986年通过IS06743/7,按油基、水基将加工液分为MH和MA两大类,又根据每类的化学组成、应用各分为8类和9类,共17类,该标准将目前众多的金属加工液的品种均可包含进去,我国已等效采用了该标准,制定了GB7631.5。
以下的分类是根据溶液介质状态进行分类。
1)、纯油型:包括矿物油、动植物油及其混合物,通常加入含硫、磷、氯的极压抗磨添加剂,具有良好的润滑性,用在负荷大的工序,但冷却性能较差。
从环保的角度,现在惰性极压添加剂(PEP)有取代含磷硫添加剂的趋势。
2)、可溶性油:含80%以上的油,加入乳化剂、添加剂和水,形成不透明的乳化液,胶体颗粒大于1微米,既具有纯油性润滑剂的良好润滑性,也具有水溶液的良好的冷却性,而且能减少着火的危险,使用时需稀释,比例大约是20:1,缺点是容易被细菌污染变质。
同时可用于有色金属的加工,PH值保持在8-9之间。
3)、半合成液:基本上是水溶液,含有少量的油(10-30%),乳化颗粒很少(0.05-1.0微米),半合成液化的冷却性能比可溶性油好但润滑性则不如可溶性油.外观与乳化颗粒大小有关,使用时需要稀释.4)、合成液:不含油的透明水溶液,添加剂加入量可达50%,使用时需要稀释成2-10%水溶液。
金属材料的润滑性和加工

金属材料的润滑性和加工1.1 润滑性的定义:润滑性是指金属材料在摩擦过程中,减少摩擦阻力、降低磨损和散热的能力。
1.2 润滑性的重要性:润滑性对于金属材料的加工过程至关重要,良好的润滑性能有效降低加工过程中的摩擦阻力,延长工具的使用寿命,提高加工效率,降低能耗,减少磨损和污染。
1.3 润滑性的影响因素:(1)金属材料的种类和状态(如晶粒度、晶体结构等);(2)温度和压力;(3)润滑剂的种类和性质(如粘度、极性、化学稳定性等);(4)表面 roughness 和形状误差等。
二、金属材料的加工2.1 金属材料的加工方法:(1)铸造:通过熔融金属浇铸成型的方法,制成所需的形状和尺寸的零件;(2)锻造:通过对金属材料施加压力,使其产生塑性变形,从而获得所需的形状和尺寸的零件;(3)焊接:通过加热或加压,使金属材料局部熔化,并冷却凝固成整体的方法;(4)切削加工:利用切削工具将金属材料切除,获得所需形状和尺寸的零件;(5)磨削加工:利用磨削工具对金属表面进行磨削,以提高表面粗糙度和尺寸精度;(6)电加工:利用电能对金属材料进行加工的方法,包括电火花加工、激光加工等。
2.2 金属材料加工过程中的润滑和冷却:(1)润滑:通过润滑剂减少摩擦阻力,降低磨损,提高加工效率和工件质量;(2)冷却:通过冷却液降低金属材料的温度,减少热应力,防止变形和裂纹。
2.3 金属材料加工中的质量控制:(1)控制加工过程中的温度和压力,以保证材料的塑性变形和加工质量;(2)控制润滑剂的种类和性质,以保证良好的润滑性能;(3)控制表面 roughness 和形状误差,以满足工件的使用要求。
以上是关于金属材料的润滑性和加工的知识点介绍,希望对您有所帮助。
习题及方法:1.习题:润滑性对金属材料的加工过程有何影响?方法:润滑性能够减少金属材料在加工过程中的摩擦阻力,降低磨损,提高加工效率和工件质量。
因此,在实际加工过程中,应选择合适的润滑剂,以提高润滑性能。
热模锻工艺流程

热模锻工艺流程我呀,今天就想和大家唠唠热模锻这个超酷的工艺流程。
这热模锻啊,就像是一场金属的华丽变身秀,那可老精彩了。
咱先得从原材料说起。
这就好比做饭,你得先有食材一样。
热模锻的原材料大多是各种金属坯料。
这些坯料可不能随随便便就拿来用,得先检查检查呢。
质检员老王那可是个仔细人儿,他拿着各种工具,这儿量量,那儿看看,眼睛瞪得像铜铃似的。
要是这坯料有啥缺陷,老王就会大喊:“嘿,这可不行,这坯料不合格,就像那病恹恹的小鸡,可经不住后面的折腾。
”合格的坯料呢,就要开始加热了。
这加热就像是给金属坯料洗个热水澡,让它浑身暖洋洋的,变得柔软好塑形。
加热炉就像一个大蒸笼,坯料放进去,温度蹭蹭往上升。
操作加热炉的小李可不敢马虎,眼睛时刻盯着温度表。
他常说:“这温度要是控制不好,就像炒菜盐放多放少一样,整个热模锻就全毁了。
”要是温度低了,金属硬邦邦的,就像个倔脾气的老头,根本不愿意变形;温度高了呢,金属可能就像融化的冰淇淋一样,变得太软,失去了应有的强度。
等坯料加热到合适的温度,就该进入模具进行锻造了。
这模具就像是金属的塑形师,决定了最后成品的模样。
锻造工人小赵那肌肉可是相当发达,他熟练地把热乎乎的坯料放到模具里。
小赵说:“这时候就像在捏泥巴,不过这泥巴可烫得很,而且得按照严格的形状来捏。
”压力机一压下来,那可是千钧之力,“轰”的一声,坯料就开始按照模具的形状发生改变了。
这过程就像把一个任性的孩子教育成守规矩的小大人一样,压力之下,坯料乖乖听话,从原来的形状变成了模具设定的形状。
在锻造的过程中,还得注意一些细节呢。
比如说润滑,这就好比给模具和坯料之间涂一层润滑油,让它们之间的摩擦小一点,就像滑冰的时候给冰鞋擦油一样。
负责润滑工作的小张可认真了,他说:“要是不润滑好,那模具和坯料就会互相‘掐架’,磨损得特别快,这可不行。
”锻造完成后,可还没结束呢。
这刚锻造出来的工件还带着一身的热乎劲儿,而且表面可能还不那么光滑平整。
热模锻液压机安全操作及保养规程

热模锻液压机安全操作及保养规程引言热模锻液压机是一种高端的金属成形机,广泛用于汽车、航空、航天、军工等领域的金属材料加工。
在使用过程中,必须严格遵守操作规程和安全保养措施,以确保人员安全和设备的稳定运行。
本文将详细介绍热模锻液压机的安全操作规程和保养方法,以供参考和实践。
一、安全操作规程1、使用前检查在使用热模锻液压机之前,必须进行以下检查:1.行走部位,如电动传动、液压马达、连接管路、光杆、曲柄机构等,应完好无损;2.传动部位,如主轴、凸轮、链轮、摆臂等,应清洁、润滑。
凸轮、摆臂等零部件间隙应调整到规定值;3.液压系统应检查油位是否符合要求,液压泵、阀门是否正常,调压阀设置是否合理、动作是否准确。
2、安全操作1.操作人员必须熟悉机器的结构及使用方法,必须按规程操作;2.操作时必须使用统一规格的预压件和定位块,保证模具的安装正确;3.每个操作步骤必须确认无人员在裸露等危险地方,启动才可进行;4.操作人员必须在警戒线外站立,切勿越线或趴上机器检查;5.操作人员必须集中精力,注意听指挥,同时注意自身安全。
6.热模锻液压机开启后,禁止打开保护装置。
3、紧急处理当热模锻液压机发生电力、液压、气动和电子四个方面的故障时,应按照以下紧急处理方法进行:1.紧急切断电源:将变压器、电容器、断路器等电源开关置于“OFF”位置。
2.切断液压进口管:停止油泵运转,切断液压进口管,以避免压力下降得太快而对机械设备造成损坏。
3.通知相关人员:立即通知设备操作人员和维修工程师进行处理,并启动维修程序。
二、保养方法1、日常保养日常保养主要包括以下几个方面:1.定期清洗液压油箱,在保证设备清洁干净的情况下,使用相对应的液压油;2.定期对液机进行注油,检查连接部位是否松动等并及时紧固;3.检查齿轮的抱合是否均匀、摩擦扭矩是否正常等;4.定期检查轴承、液压接头、缸体等零部件是否有磨损或者故障现象,必要时更换零部件。
2、定期保养定期保养应该根据使用频度和工作状态进行,以期达到最佳的工作状态和生命周期:1.定期检查主要零部件的状况,尤其是轴承和缸体等部件的磨损情况,并进行必要的维修或更换;2.定期检查各部件的松动情况,如发现存在应加紧或更换螺栓等,以保证设备的结构和性能稳定;3.定期检查液压油的清洁度和油位,及时更换过期的液压油,以保证油压等参数稳定;4.定期对控制回路进行检查、维修或替换,以保证设备电气控制正常可靠。
浅析金属压力加工中的摩擦与润滑
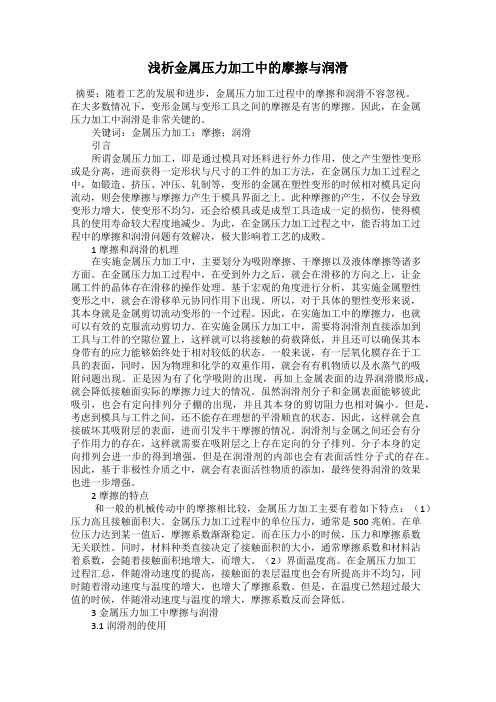
浅析金属压力加工中的摩擦与润滑摘要:随着工艺的发展和进步,金属压力加工过程中的摩擦和润滑不容忽视。
在大多数情况下,变形金属与变形工具之间的摩擦是有害的摩擦。
因此,在金属压力加工中润滑是非常关键的。
关键词:金属压力加工;摩擦;润滑引言所谓金属压力加工,即是通过模具对坯料进行外力作用,使之产生塑性变形或是分离,进而获得一定形状与尺寸的工件的加工方法,在金属压力加工过程之中,如锻造、挤压、冲压、轧制等,变形的金属在塑性变形的时候相对模具定向流动,则会使摩擦与摩擦力产生于模具界面之上。
此种摩擦的产生,不仅会导致变形力增大,使变形不均匀,还会给模具或是成型工具造成一定的损伤,使得模具的使用寿命较大程度地减少。
为此,在金属压力加工过程之中,能否将加工过程中的摩擦和润滑问题有效解决,极大影响着工艺的成败。
1摩擦和润滑的机理在实施金属压力加工中,主要划分为吸附摩擦、干摩擦以及液体摩擦等诸多方面。
在金属压力加工过程中,在受到外力之后,就会在滑移的方向之上,让金属工件的晶体存在滑移的操作处理。
基于宏观的角度进行分析,其实施金属塑性变形之中,就会在滑移单元协同作用下出现。
所以,对于具体的塑性变形来说,其本身就是金属剪切流动变形的一个过程。
因此,在实施加工中的摩擦力,也就可以有效的克服流动剪切力。
在实施金属压力加工中,需要将润滑剂直接添加到工具与工件的空隙位置上,这样就可以将接触的荷载降低,并且还可以确保其本身带有的应力能够始终处于相对较低的状态。
一般来说,有一层氧化膜存在于工具的表面,同时,因为物理和化学的双重作用,就会有有机物质以及水蒸气的吸附问题出现。
正是因为有了化学吸附的出现,再加上金属表面的边界润滑膜形成,就会降低接触面实际的摩擦力过大的情况。
虽然润滑剂分子和金属表面能够彼此吸引,也会有定向排列分子棚的出现,并且其本身的剪切阻力也相对偏小。
但是,考虑到模具与工件之间,还不能存在理想的平滑顺直的状态。
因此,这样就会直接破坏其吸附层的表面,进而引发半干摩擦的情况。
锻造自动润滑装置的应用

锻造自动润滑装置的应用高红林,热加工工艺室主任,工程师,长期从事锻/铸件新产品工艺开发和改进工作,在热模锻加工工艺、有色合金铸造工艺等专业领域有丰富的从业经验,带领技术团队多次获得公司科技创新奖、先进班组、全省劳动竞赛优秀班组、陕西省工人先锋号等荣誉。
在整个锻造生产的成本中,模具费用是锻件成本的主要组成部分,一般占生产成本10%~25%,因此提高模具寿命可减少锻件生产成本中的模具成本。
在生产制造过程中,喷淋润滑环节是延长锻造模具寿命的重要组成部分。
在锻造生产中,锻造润滑剂成本仅占2%左右,但是对锻造模具寿命起着决定性作用。
近年来,随着锻造行业装备及技术发展,以及生产制造过程人力成本的上升,原来手工的润滑冷却方式已经越来越不被大家所接受,从质量稳定及成本角度考虑,实现自动化锻造无疑是今后大家选择的方向,锻造自动润滑装置的应用是其中必不可少的因素。
自动润滑装置方式锻造生产线目前采用的自动润滑装置主要有以下几种:一类是安装在机床外部,利用滑块抬起的空间深入模具型腔对模具进行润滑的自动润滑结构;另一种是安装在热模锻压力机的步进梁上的自动润滑装置。
⑴采用步进梁自动化锻造生产的热模锻生产线,该喷淋系统将喷淋头、喷淋液管、气管软管都安装在步进梁上方,整线集成由PLC连线控制,步进梁传输过程中对锻造完毕的上下锻造模具进行喷淋润滑。
这种结构优点可以对模具进行充分润滑,即使满工位生产也可以避免润滑过程中润滑液喷在锻件上面,但由于受往复运动和高温烘烤,易出现管线故障。
这种喷淋润滑方式仅限于采用步进梁自动化的简单中小型锻件自动化锻造模具的喷淋润滑(图1)。
图1 安装在机床外部的自动润滑装置⑵热模锻自动生产线另一种喷淋润滑方式是安装在设备上,采用摆臂式自动喷淋润滑系统。
摆动润滑装置由一个润滑喷洒单元和配液单元组成,使用高压软管和钢管将该单元和送料单元以及一个或者多个喷嘴装置相连接。
在压力机的主控台处对其进行调整,由SPS控制的阀系统可以实现非常精确的冷却水量和润滑材料混合物剂量的分配。
热模锻自动线喷淋润滑系统应用

热模锻自动线喷淋润滑系统应用发布时间:2021-11-30T03:06:09.262Z 来源:《工程建设标准化》2021年9月17期36卷作者:霍威冀强陈海鹏闫利军李云飞[导读] 本文主要针对热模锻自动线喷淋润滑系统应用展开深入探究,首先阐明了热模锻自动线自动喷淋润滑形式,然后分析了热霍威冀强陈海鹏闫利军李云飞内蒙古一机集团富成锻造有限责任公司内蒙古包头 014032摘要:本文主要针对热模锻自动线喷淋润滑系统应用展开深入探究,首先阐明了热模锻自动线自动喷淋润滑形式,然后分析了热模锻自动线柔性化生产问题,最后,总结了热模锻自动线喷淋润滑系统应用及未来发展。
关键词:热模锻;自动线喷淋;润滑引言随着热模锻自动生产线越来越广泛的应用,以及与其相关的自动喷淋系统等工艺技术的逐步完善,在产品生产的过程中,相关企业结合环保型安全的高新型材料水基无毒害高温自动脱模润滑剂和喷淋液工艺,必定会提升热锻压自动生产线的工作效率,进一步改善锻压生产环境,提高锻压模具寿命,使锻压公司取得了产品成本上差别化的竞争优势。
一、热模锻自动线自动喷淋润滑形式对于热锻自动生产线,手工喷油模具的润滑,根据生产过程的自动化,大致可分为以下几种类型。
(1)对于密封性足够大的压机锻模润滑,锻造自动生产线上的喷淋试验润滑方法可以通过锻件大小尺寸的转子夹和自动化设备上的喷淋试头安装在同一机械手上的方法,在锻造毛坯尺寸工序间自动化夹持式运转操作时,顺带进行模具喷淋润滑。
铸造在运输过程中,由于机械手要继续进行喷淋操作,使上模喷水溅到锻件上,容易造成表面温度下降过大,在造锻件前造成锻件心表温差过大、氧化皮厚等问题。
另外,锻件在自动机器人夹紧过程中,由于待完成氧化铁皮吹扫、喷淋和润滑后,锻件被冷却,因此机器人夹具受热持续时间长,在连续加工过程中,因加热时间过长,硬度急剧下降,严重影响到机器人的精确定位。
(2)使用摆臂式喷淋系统安装在模座上。
控制系统的主要部件是摆臂和上下排的喷头,当压机滑块下锻模工作时,摆臂置于模具的一侧,锻压工艺完成曲柄滑块到达上死点后,再进行锻压加工。
高强钢冲压成型润滑技术
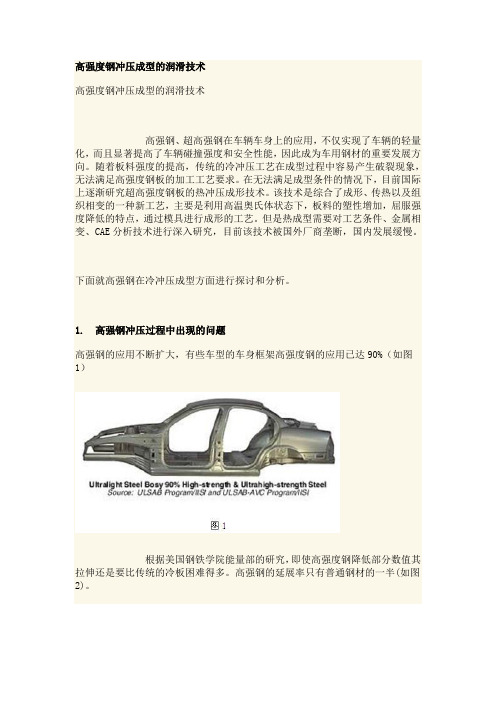
高强度钢冲压成型的润滑技术高强度钢冲压成型的润滑技术高强钢、超高强钢在车辆车身上的应用,不仅实现了车辆的轻量化,而且显著提高了车辆碰撞强度和安全性能,因此成为车用钢材的重要发展方向。
随着板料强度的提高,传统的冷冲压工艺在成型过程中容易产生破裂现象,无法满足高强度钢板的加工工艺要求。
在无法满足成型条件的情况下,目前国际上逐渐研究超高强度钢板的热冲压成形技术。
该技术是综合了成形、传热以及组织相变的一种新工艺,主要是利用高温奥氏体状态下,板料的塑性增加,屈服强度降低的特点,通过模具进行成形的工艺。
但是热成型需要对工艺条件、金属相变、CAE 分析技术进行深入研究,目前该技术被国外厂商垄断,国内发展缓慢。
下面就高强钢在冷冲压成型方面进行探讨和分析。
1. 高强钢冲压过程中出现的问题高强钢的应用不断扩大,有些车型的车身框架高强度钢的应用已达90%(如图1)根据美国钢铁学院能量部的研究,即使高强度钢降低部分数值其拉伸还是要比传统的冷板困难得多。
高强钢的延展率只有普通钢材的一半(如图2)。
高强钢屈服强度当材料被冲压成形时,会变硬。
不同的钢材,变硬的程度不同,一般高强度低合金钢只略有3 KSI增加,不到10%。
注意:双相钢的屈服强度有20KSI 增加,增加了40%多!金属在成形过程中,会变得完全不同–完全不像冲压加工开始之前。
这些钢材在受力后,屈服强度增加很多。
材料较高的屈服应力加上加工硬化,等于流动应力的大大增加。
——这会引起需要更多的吨位来制作部件——它会使金属的变形温度增加(可能会燃烧或破坏不恰当的润滑剂),硬点会增加模具磨损——涂层可能会于事无补或无法持续到和预期的时间一样长。
综上所述,高强钢成形的高压力要求、回弹的增加、加工硬度的增加、高成型温度下的操作对模具及润滑都提出了挑战。
2. 润滑剂分析过去, 生产深冲或者重冲工件,大家都认为耐压型(EP) 润滑油是保护模具的最好选择。
硫和氯EP添加剂被混合到纯油中来提高模具寿命已经有很长的历史了。
钛合金玻璃润滑摘记

钛合金锻造的润滑工艺钛合金与模具表面的粘结比其他金属强烈,这是因为钛的化学活性很高,在与工具接触的部位使氧化膜发生还原作用,当滑动持续时间很长时,则为纯净表面产生大面积接触创造了条件,导致表面被焊合。
焊合的部位分布在金属沿接触面剧烈流动的区域。
钛合金的粘结倾向给热模锻和挤压造成了很大困难。
为了预防在变形过程中产生粘结和减小摩擦,必须正确地选择变形热力规范、模锻毛坯的结构要素和有效的润滑剂。
模锻钛合金所用润滑剂必须满足下述基本要求:(1)在整个变形过程中能够形成牢固而连续的保护膜。
(2)在加热和变形过程中能够保护毛坯,防止氧化和气体污染。
(3)具有良好的隔热性能,使毛坯从炉子转移到模具以及在变形过程中减少热量损失。
(4)不与毛坯和模具的表面发生化学作用。
(5)容易涂到毛坯表面上,并便于使该工序机械化。
(6)容易从锻件表面上清除。
(7)能在较长时间内保持润滑性能。
模锻钢和其他有色金属所用的润滑剂不能满足上述全部要求。
石墨与水玻璃和滑油混合的膏状润滑剂会使钛合金表面产生裂纹,其原因是表面上存着脆性的α层,在变形时被破坏。
这些裂纹是应力集中源,继续变形时可能向金属内部扩展。
对于钛合金来说,玻璃润滑剂是目前所研制的润滑剂中最好的。
在模锻和局部挤压变形条件下,如玻璃涂料的成分选择得当,则能保持液态摩擦。
玻璃润滑剂成分应含有SiO2,K2O,Na2O,CaO,Al2O3,Li2O,B2O3,BaO,MgO,PbO等氧化物。
各种牌号的玻璃粉成分见表15 表5 适用于钛合金模锻用的玻璃粉化学成分玻璃润滑剂只有在熔融状态才保持润滑性能。
润滑剂保持最佳粘度的温度范围越宽,润滑效果越好。
粘度的变化与玻璃化学成分有关(见表6)。
可降低粘度的氧化物有Li2O,Na2O,K2O,PbO,BaO;而提高粘度的氧化物是SiO2,Al2O3,ZrO2。
最佳粘度值等于102.8~104Pa·s。
表6 适于钛合金模锻用的玻璃润滑剂粘度* 在配制玻璃润滑剂时用作其他玻璃的添料。