炼油节能材料
炼油企业能源审计案例

炼油企业能源审计案例近日,一家炼油企业进行了一次能源审计,以评估公司的能源消耗和节能潜力,旨在降低能源成本和环境污染,提高生产效率。
以下是此次能源审计的案例内容。
一、能源使用状况该炼油企业使用的能源主要包括天然气、原油、燃料油和柴油。
其中,天然气占能源使用总量的比例最大,约为80%。
原油、燃料油和柴油分别占用20%不到的比例。
二、能源消耗数据通过对企业不同工段的能源消耗数据进行统计,审计人员发现,炼油过程中的转化过程和传热过程是最主要的能源消耗环节。
能源消耗表明,裂解炉、蒸馏塔和换热器在其中占有重要的地位。
三、节能措施1. 优化设备配置炼油企业将原有的两套蒸馏塔改为三塔流程,设置两组改良后的换热器,更换传热效率更高的材料,能够有效节省能源并提高工作效率。
2. 排放废热回收鉴于炼油过程中排放的热量高且大量损失,企业引入排放废热回收装置,对产生的废热进行回收利用。
通过回收废热,企业能够为自身创造更多的能源利益,同时,合理利用资源,实现节能减排,符合绿色环保理念。
3. 采用新型节能设备企业引进新型换热器,以更高的传热效率,从根本上减少对钢材的技术复杂度和占用面积。
四、实施效果根据统计数据表明,企业接受此方案后,每年可以节省能源70万吨,相当于每年2.5亿元的直接节能成本和减排经济效益。
五、结论从以上能源审计案例来看,炼油企业能够通过设施改造、废热回收等措施,降低能源成本,增加经济效益,兼顾环境保护,实现可持续发展。
企业需要加强自身的能源管理,建立科学合理的能源使用计划,促进企业转型升级,更快形成一种绿色发展模式。
同时行业标准和政策导向也是非常重要的一个方面。
石油炼制中常减压装置的节能分析

石油炼制中常减压装置的节能分析石油炼制过程中的常减压装置是一种非常重要的设备,它通过将高温高压的原料油降压至合适的温度和压力,从而为下一步的炼制工序提供了合适的条件。
在炼油工业中,常减压装置占据着非常重要的地位,因此如何提高其能效和节能减排成为了当前炼制企业亟待解决的问题之一。
本文将就石油炼制中常减压装置的节能性能进行分析与探讨。
常减压装置通过将高压、高温气体减压至低温低压气体,达到冷凝和液化的目的。
它的节能性能主要体现在以下几个方面:1. 器件优化:常减压装置中的调压阀、换热器、压缩机等器件的设计和选择对于节能至关重要。
通过优化设计和选型,可以减少能量损失,提高能效。
2. 热能回收:在减压过程中,往往伴随着大量的热能损失。
通过热交换器的设计和应用,可以实现热能的回收和再利用,提高能源利用率。
3. 过程优化:合理的工艺设计和运行控制对于节能也起着至关重要的作用。
通过减少不必要的能量消耗,优化过程流程,实现能源的最大化利用。
4. 新技术应用:随着科技的不断发展,新材料、新工艺、新技术不断涌现,如使用高效节能的换热器、节能调压阀等,也为常减压装置的节能提供了新的途径。
在实际的炼制过程中,石油企业可以通过对常减压装置的技术改造和优化来实现节能减排的目标,并且能够获得可观的经济效益。
加强对常减压装置人员的培训和技术支持,也是提高其节能性能的重要手段。
传统的常减压装置在工作过程中存在许多不足之处,主要表现在以下几个方面:1. 能耗较高:传统的常减压装置由于设计和工艺的限制,能耗较高,能效较低。
3. 设备老化:由于长期运行,设备容易老化,导致性能下降,能效降低。
为了解决传统常减压装置存在的问题,提高其能效和节能性能,炼制企业可以采取以下措施:1. 技术改造:对现有的常减压装置进行技术改造,采用新材料、新工艺和新技术,提高其能效和节能性能。
2. 设备更新:更新老化设备,选择高效节能的调压阀、换热器等器件,提高能源利用率。
天津石化炼油节能优化措施及节能效果
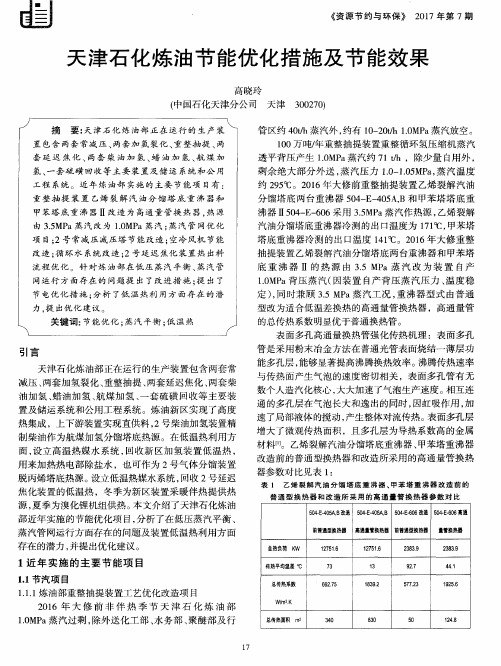
关键 词 : 节 能优化 : 蒸汽 平衡 : 低 温 热
的总传热系数明显优于普通换热管 。
表 面 多孑 L 高通 量换 热 管强 化传 热 机理 :表 面 多孔
引 言 天 津 石化 炼 油部 正在 运 行 的生产 装 置 包含 两 套 常 减压 、 两套 加 氢裂 化 、 重 整抽 提 、 两套 延 迟 焦化 、 两 套 柴 油加氢 、 蜡油加氢 、 航煤加氢 、 一 套 硫 磺 回收 等 主 要 装 置及 储 运 系统 和公 用 工程 系 统 。炼油 新 区实现 了高度
热集成 ,上下游装置实现直供料 , 2 号柴油加氢装置精
制柴 油 作 为航 煤加 氢 分馏 塔底 热 源 。在 低 温热 利 用方
速了局部液体 的搅动 , 产生整体对流传热 。 表面多孔层 增 大了微观传热面积 ,且多孔层为导热系数高的金属
材料 _ 1 ] 。 乙烯 裂 解 汽油 分馏 塔底 重 沸器 、 甲苯塔 重 沸 器 改造 前 的普 通 型换热 器 和改 造所 采用 的高 通量 管 换热 器 参数 对 比见 表 1 :
管是采用粉末冶金方法在普通光管表面烧结一薄层功 能多孔层 , 能够显著提高沸腾换热效率。 沸腾传热速率 与传热面产生气泡的速度密切相关 ,表面多孔管有无 数个 人造 汽 化核 心 , 大 大加 速 了气泡 生产 速度 。 相互 连
通 的多孔 层 在气 泡 长大 和逸 出的 同时 , 因虹 吸作用 , 加
表 1 乙烯 裂 解 汽 油 分 馏 塔 底 重 沸器 、 甲苯 塔 重 沸 器 改 造前 的
面, 设立高温热媒水 系统 , 回收新 区加氢装置低温热 , 用来加热热 电部 除盐水 ,也可作为 2 号气体分馏装置
脱 丙 烯塔 底热 源 。 设 立低 温 热媒 水 系统 , 回收 2号 延迟 焦化 装 置 的低温 热 ,冬 季 为新 区装 置 采 暖伴 热 提供 热 源, 夏 季 为溴化 锂 机组 供热 。 本 文介绍 了天津 石化 炼油 部 近 年实 施 的节 能优 化 项 目 , 分析 了在 低 压蒸 汽 平衡 、 蒸 汽 管 网运行 方 面存 在 的 问题 及装 置 低温 热 利 用方 面 存 在 的潜力 , 并 提 出优化 建议 。
炼油储运环节的节能措施

炼油储运环节的节能措施炼油储运环节是整个石油产业链中不可或缺的一环,它涉及到原油的储存、炼制和运输等重要环节。
在这个环节中,能源消耗较大,大量的二氧化碳排放也是一个重要问题。
节能减排成为炼油储运环节面临的重要挑战之一。
为了减少能源消耗和二氧化碳排放,各个国家和企业都在积极探索采取一系列节能措施来促进环境可持续发展。
接下来,我们将结合当前的炼油储运环节实际情况,探讨一些常见的节能措施。
一、炼油节能措施1. 优化设备结构炼油储运环节中的设备种类繁多,设备的制造、安装和运行都需要大量的能源。
优化设备结构是节能的重要手段之一。
通过对设备的结构和工艺流程进行优化,可以降低能源消耗,同时提高产能和产品质量。
采用高效节能的新型分馏塔、蒸馏柱和换热器等设备,减少炼油过程中的能源损耗,实现节能降耗的目的。
2. 推广清洁能源炼油过程消耗大量的化石能源,如燃料油、天然气等。
为了降低二氧化碳排放和减少环境污染,部分企业已经开始推广清洁能源,如天然气、生物质能等。
利用生物质能发电,替代传统的燃煤发电,可以有效减少碳排放,实现节能环保的目的。
3. 循环利用废热炼油储运环节中会产生大量的废热,如果能有效利用这些废热,就可以达到节能的目的。
采用热泵技术将废热转化为可供生产和生活使用的热能。
利用余热发电也是一种常见的废热利用方式,通过热能发电,不仅可以节约能源,还可以降低企业的运行成本。
4. 优化炼油工艺对于炼油过程中的热力系统和蒸馏系统,可以通过技术改造和工艺优化来降低能源消耗。
采用新型的分离蒸馏技术和膜分离技术,能够使炼油过程中的蒸馏效率大幅提高,减少炼油所需的能源消耗。
5. 强化能源管理炼油储运环节的能源管理是实现节能减排的关键。
通过建立健全的能源管理体系和制定科学的能源计量管理制度,可以有效监控和调控能源的使用状况,提高能源利用效率,实现节能减排的目标。
1. 优化储罐结构油品的储存是炼油储运环节中重要的部分,大型的储罐构建和维护都需要大量的能源。
化工节能低碳稿件范文

化工节能低碳稿件范文随着全球经济的快速发展和人们生活水平的提高,化工行业在全球范围内得到了广泛的应用和发展。
然而,化工生产所带来的能源消耗和碳排放也成为了环境保护的一大难题。
为了实现可持续发展,在化工行业中推行节能低碳已经成为当务之急。
化工企业可以通过改进生产工艺来实现节能低碳。
通过优化工艺流程和提高设备能效,化工企业可以降低能源消耗和碳排放。
例如,在炼油过程中,引入先进的催化剂和反应器可以提高产品收率和能效,减少废气排放。
此外,化工企业可以利用余热回收技术,将废热转化为可再生能源,进一步提高能源利用率。
化工企业还可以通过优化原材料的选择和利用,实现节能低碳。
合理选择原材料可以降低生产过程中的能源消耗和碳排放。
例如,选择低能耗的替代原材料或改进生产工艺,可以减少能源消耗并减少废物产生。
化工企业还可以采用循环经济模式,将废弃物转化为资源,实现资源的最大化利用。
化工企业还可以通过加强能源管理和技术创新来推动节能低碳。
建立全面的能源管理体系,制定能源消耗和碳排放的减排目标,并通过监测和评估来实现目标的落实。
同时,化工企业还应积极推动技术创新,加大对节能低碳技术的研发和应用。
例如,开发新型催化剂、高效反应器和节能设备,可以进一步提高化工生产的能效和环境友好性。
在推行节能低碳的过程中,政府和企业应当加强合作,共同推动化工行业的绿色发展。
政府可以出台相关政策,提供经济和政策支持,鼓励企业开展节能低碳的研究和实践。
化工企业应当积极响应政府的号召,制定并执行节能低碳的发展战略,不断提高环境管理和技术创新能力。
化工节能低碳是化工行业可持续发展的重要方向。
通过改进生产工艺、优化原材料选择、加强能源管理和技术创新等措施,化工企业可以实现节能低碳,减少能源消耗和碳排放,促进绿色发展。
政府和企业应当加强合作,共同推进化工行业的绿色转型,为可持续发展做出贡献。
只有坚持节能低碳理念,化工行业才能在未来的发展中取得更大的成就。
《高耗能行业重点领域节能降碳改造升 级实施指南(2022年版)》

附件1炼油行业节能降碳改造升级实施指南一、基本情况炼油行业是石油化学工业的龙头,关系到经济命脉和能源安全。
炼油能耗主要由燃料气消耗、催化焦化、蒸汽消耗和电力消耗组成。
行业规模化水平差异较大,先进产能与落后产能并存。
用能主要存在中小装置规模占比较大、加热炉热效率偏低、能量系统优化不足、耗电设备能耗偏大等问题,节能降碳改造升级潜力较大。
根据《高耗能行业重点领域能效标杆水平和基准水平(2021年版)》,炼油能效标杆水平为7.5千克标准油/(吨·能量因数)、基准水平为8.5千克标准油/(吨·能量因数)。
截至2020年底,我国炼油行业能效优于标杆水平的产能约占25%,能效低于基准水平的产能约占20%。
二、工作方向(一)加强前沿技术开发应用,培育标杆示范企业。
推动渣油浆态床加氢等劣质重油原料加工、先进分离、组分炼油及分子炼油、低成本增产烯烃和芳烃、原油直接裂解等深度炼化技术开发应用。
(二)加快成熟工艺普及推广,有序推动改造升级。
1.绿色工艺技术。
采用智能优化技术,实现能效优化;采用先进控制技术,实现卡边控制。
采用CO燃烧控制技术提高加热炉热效率,合理采用变频调速、液力耦合调速、永磁调速等机泵调速技术提高系统效率,采用冷再生剂循环催化裂化技术提高催化裂化反应选择性,降低能耗、催化剂消耗,采用压缩机控制优化与调节技术降低不必要压缩功消耗和不必要停车,采用保温强化节能技术降低散热损失。
2.重大节能装备。
加快节能设备推广应用。
采用高效空气预热器,回收烟气余热,降低排烟温度,提高加热炉热效率。
开展高效换热器推广应用,通过对不同类型换热器的节能降碳效果及经济效益的分析诊断,合理评估换热设备的替代/应用效果及必要性,针对实际生产需求,合理选型高效换热器,加大沸腾传热,提高传热效率。
开展高效换热器推广应用,加大沸腾传热。
推动采用高效烟机,高效回收催化裂化装置再生烟气的热能和压力能等。
推广加氢装置原料泵液力透平应用,回收介质压力能。
炼油催化剂有哪些

炼油催化剂有哪些炼油催化剂是炼油工业中必不可少的重要材料,通过催化剂的作用可以加速反应速率,并提高炼油产物的质量和产量。
炼油催化剂种类繁多,下面将介绍几种常见的炼油催化剂。
1. 饱和剂饱和剂是一种针对石蜡烃的催化剂,主要作用是通过热裂解来提高石蜡烃的转化率。
饱和剂的使用可以降低石蜡烃对石化设备的腐蚀性,提高产品的品质和产量。
2. 双组分催化剂双组分催化剂一般是由金属氧化物和载体组成的。
这类催化剂在炼油中具有很广泛的应用,可以用于重整、裂化、异构化等反应过程中。
双组分催化剂具有较高的活性和选择性,可以有效提高产品的产量和降低能耗。
3. 渣油加氢催化剂渣油加氢是炼油过程中的一个重要环节,目的是降低油品中的硫和氮等有害成分的含量,提高产品的质量。
渣油加氢催化剂主要是由金属催化剂和载体组成,通过在高温、高压环境下,使硫、氮等有害成分和氢气发生反应,从而实现脱硫、脱氮的目的。
4. 焦炭燃烧催化剂焦炭燃烧催化剂是炼油过程中用于燃烧余热的催化剂。
在炼油过程中产生的焦炭可以被收集和再利用,通过添加焦炭燃烧催化剂,可以提高焦炭的燃烧效率,并减少热能的浪费。
5. 蜡烃异构化催化剂蜡烃异构化催化剂主要用于将线性烷烃转化为支链烷烃,提高汽油的辛烷值。
蜡烃异构化催化剂通常由酸性催化剂和金属催化剂组成,通过在合适的温度条件下,使线性烷烃发生分子骨架的重排,从而实现异构化的目的。
6. 氨催化脱氮剂氨催化脱氮剂主要用于炼油过程中的脱氮环节。
炼油原料中的氮会导致催化剂中毒和设备腐蚀等问题,因此需要进行脱氮处理。
氨催化脱氮剂通过在高温、高压的条件下,使氮与氢发生反应,生成氨气和水脱除油品中的氮。
7. 裂化催化剂裂化催化剂是炼油中广泛应用的催化剂之一,主要用于裂化反应,将较重的烃类分子裂解成较轻的烃类分子。
这有助于提高汽油的辛烷值和增加轻质烃类产品的产量。
裂化催化剂一般是由酸性催化剂和金属催化剂组成,具有很高的催化活性和选择性。
总而言之,炼油催化剂是炼油工业中不可或缺的重要材料,不同种类的催化剂在炼油过程中扮演着不同的角色。
炼化企业节能降耗技术措施探讨

炼化企业节能降耗技术措施探讨摘要:随着全球人口的不断增加和工业生产方式的不断进步,传统的炼化生产方式无论是在技术层面,还是在成本层面都越来越难以适应炼化行业的发展要求。
因此,本文就针对炼化企业的节能降耗进行分析,为炼化企业的良好发展提供保障。
关键词:炼化企业;节能降耗;技术措施一、炼油化工概述炼化企业主要通过对原油进行加工炼制生产汽油、柴油等石油产品获取利润。
通常而言,炼油企业在钻井平台获取原油后,处于石油化工生产的第二阶段。
在炼油化工过程中,炼化企业会以蒸馏的方式对原油进行精炼,将处于极端环境中的原油分离成不同的烃类。
在炼化企业炼制原油,使原油组分分离后,炼化企业可以生产各类石油产品,如汽油、柴油、煤油、润滑剂、沥青等,再将这类石油化工产品售卖至各个行业,可以发挥极大的用途。
以润滑剂为例,在蒸馏过后,润滑剂可以即刻向工厂出售,其他产品也可在精炼后向其余厂家售卖,一家大型炼化企业每日可对数十万桶原油进行加工处理,生产上万吨石油化工产品。
在整个炼化过程中,通常将炼油环节视为“下游”部门,原油产地,即油田则被视为“上游”部门。
同时,“下游”这一术语还与炼油环节在石油化工产品价值链中的作用相关,除了对原油进行精炼之外,炼化企业还要与相关企业、政府部门等石油产品需求者进行沟通。
美国能源情报署(EIA)相关研究表明,截至目前,全球每日约有1亿桶原油经过炼化企业加工,生产汽油、馏分燃料等石油化工产品数百万吨,即便如此,却仍然难以满足全球范围内对石油化工产品的大量需求,炼化企业还需进一步提升其生产效率。
二、“双碳”目标下炼化企业面临的形势(一)市场驱动炼油向化工转型国内成品油市场受“双碳”政策影响,产品结构不断调整。
同时,受节能减排技术不断提高及替代能源快速发展的影响,成品油需求量增速逐渐放缓。
据预测,我国汽油需求将于“十四五”末期达到峰值,煤油需求在2040年前后达到峰值,柴油消费已处于达峰后期。
我国化工产品需求量增长空间巨大,预计2035年后达峰。
炼油储运环节的节能措施

炼油储运环节的节能措施随着能源需求的不断增加,炼油行业也面临着能源消耗和环境污染等问题。
炼油储运环节的能耗较大,如何节能减排成为了行业发展的重要课题。
为此,炼油企业需要采取一系列节能措施,提高能源利用效率,减少能源消耗和环境污染。
一、减少能耗,提高能源利用效率1.优化炼油工艺流程通过对炼油生产流程进行优化,减少能源的消耗,例如通过改进催化剂、提高精炼效率、减少能量损失等方法,提高炼油厂的能源利用效率。
2.采用节能设备炼油企业可以考虑引进先进的节能设备,如高效换热器、节能泵、节能照明等,以降低能耗、提高能效。
3.优化生产计划合理调整生产计划,避免因生产过剩或不足导致的能源浪费。
并且采用先进的计划管理系统,实现生产过程的智能化、自动化。
4.能源回收利用在炼油储运环节中,很多废热、废气可以通过技术手段进行回收利用,用于发电、供暖等,从而减少能源消耗。
5.加强节能管理通过建立科学完善的节能管理体系,对能源使用进行监控、计量以及分析,及时发现并解决能源浪费问题。
二、环保措施1.减少废水排放炼油生产过程中会产生大量的废水,其中含有各种有害物质,对环境造成很大的污染。
炼油企业可以通过建立完善的废水处理系统,将废水进行处理,达到排放标准。
2.降低废气排放合理选择燃烧设备、提高燃烧效率以及采用先进的废气处理技术,减少废气的排放,降低对大气环境的影响。
3.加强环保监测加强对环境污染的监测,及时发现和处理环境污染问题,确保环境的安全和可持续发展。
三、提高工人节能意识1.员工培训加强对员工的节能意识培训,提高员工对能源节约和环保的认识,让员工从自身做起,积极参与节能减排工作。
2.设立节能奖惩制度建立完善的节能奖惩制度,激励员工节约能源、减少浪费行为,推动全员参与节能工作。
四、技术创新1.开展节能技术研究炼油企业应加大对节能技术的研发和应用,引进并运用符合国际标准的新型节能设备和技术,促进技术进步和产业升级。
2.转型升级积极引入互联网、大数据、人工智能等新技术,实现炼油生产全流程的数字化、智能化管理,提高生产效率,减少能源消耗。
炼油化工企业节能降耗技术分析

炼油化工企业节能降耗技术分析炼油化工企业是我国经济中的重要产业,但在生产过程中,能源消耗占据了相当大的比重。
为了实现可持续发展,提高能源利用效率是非常重要的。
节能降耗技术在炼油化工企业中的应用,有助于减少能源消耗、改善生产效率,降低污染排放,提高企业核心竞争力。
1. 废热利用技术炼油化工过程中的废热含量很高,如果能利用这些废热,将能够大幅度减少能源消耗。
目前,常用的废热利用技术包括:余热锅炉、余热回收系统、蒸汽排烟器、热泵等。
废热锅炉是企业中较为常见的废热利用设备,它能够将废热转化为蒸汽、热水等热能,再把它们送回生产过程中重复利用。
2. 节能设备炼油化工生产过程中,大量机械设备需要用电来驱动。
而节能设备的应用能够大幅度降低用电量,达到节能的效果。
例如,智能逆变器、伺服电机等,能够根据设备的负荷情况,调整驱动电力的大小,从而达到省电、减少能源消耗的效果。
此外,选择高效率的设备也是企业实现节能降耗的有效途径。
3. 低温分馏技术传统的分馏技术,大多是采用高温方式将原油或石化产品分离出各种成分。
而低温分馏技术则可以在低温下进行分离,这样能够达到节能降耗的效果。
低温分馏技术包括:冷凝回收技术、凝汽吸收技术、气液膜分离技术等,这些技术能够将重复利用的材料进行分离和回收,减少废料和排放,完成节能降耗目标。
4. 空气压缩节能技术炼油化工企业中广泛使用的空气压缩机消耗较多的电力,同时也会产生大量的热能。
空气压缩节能技术可以在压缩空气的同时,回收并再利用压缩时产生的热能,节约电力消耗。
比如空气动力润滑系统、变频控制技术、精细化压缩技术等,这些技术既能提高空气压缩效率,又可以实现能源的回收利用。
总的来说,炼油化工企业的节能降耗是一项长期、系统性的工程。
企业需要在产品技术上不断创新,完善生产流程,降低能源和资源的消耗,同时加强员工教育,提高对节能降耗的认识,全员参与,共同推进节能降耗工作的开展。
MTBE生产装置节能降耗优化措施
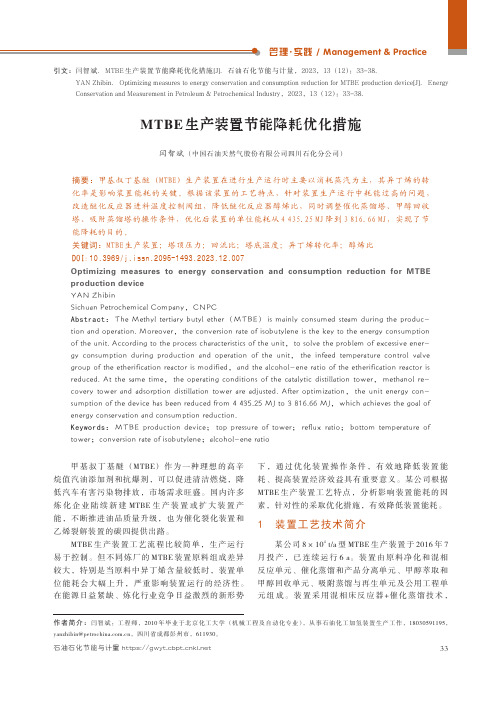
管理·实践/Management &Practice甲基叔丁基醚(MTBE)作为一种理想的高辛烷值汽油添加剂和抗爆剂,可以促进清洁燃烧,降低汽车有害污染物排放,市场需求旺盛。
国内许多炼化企业陆续新建MTBE 生产装置或扩大装置产能,不断推进油品质量升级,也为催化裂化装置和乙烯裂解装置的碳四提供出路。
MTBE 生产装置工艺流程比较简单,生产运行易于控制。
但不同炼厂的MTBE 装置原料组成差异较大,特别是当原料中异丁烯含量较低时,装置单位能耗会大幅上升,严重影响装置运行的经济性。
在能源日益紧缺、炼化行业竞争日益激烈的新形势下,通过优化装置操作条件,有效地降低装置能耗、提高装置经济效益具有重要意义。
某公司根据MTBE 生产装置工艺特点,分析影响装置能耗的因素,针对性的采取优化措施,有效降低装置能耗。
1装置工艺技术简介某公司8×104t/a 型MTBE 生产装置于2016年7月投产,已连续运行6a。
装置由原料净化和混相反应单元、催化蒸馏和产品分离单元、甲醇萃取和甲醇回收单元、吸附蒸馏与再生单元及公用工程单元组成。
装置采用混相床反应器+催化蒸馏技术,MTBE 生产装置节能降耗优化措施闫智斌(中国石油天然气股份有限公司四川石化分公司)摘要:甲基叔丁基醚(MTBE)生产装置在进行生产运行时主要以消耗蒸汽为主,其异丁烯的转化率是影响装置能耗的关键。
根据该装置的工艺特点,针对装置生产运行中耗能过高的问题,改造醚化反应器进料温度控制阀组,降低醚化反应器醇烯比,同时调整催化蒸馏塔、甲醇回收塔、吸附蒸馏塔的操作条件,优化后装置的单位能耗从4435.25MJ 降到3816.66MJ,实现了节能降耗的目的。
关键词:MTBE 生产装置;塔顶压力;回流比;塔底温度;异丁烯转化率;醇烯比DOI :10.3969/j.issn.2095-1493.2023.12.007Optimizing measures to energy conservation and consumption reduction for MTBE production device YAN ZhibinSichuan Petrochemical Company,CNPCAbstract:The Methyl tertiary butyl ether (MTBE)is mainly consumed steam during the produc-tion and operation.Moreover,the conversion rate of isobutylene is the key to the energy consumption of the unit.According to the process characteristics of the unit,to solve the problem of excessive ener-gy consumption during production and operation of the unit,the infeed temperature control valve group of the etherification reactor is modified,and the alcohol-ene ratio of the etherification reactor is reduced.At the same time,the operating conditions of the catalytic distillation tower,methanol re-covery tower and adsorption distillation tower are adjusted.After optimization,the unit energy con-sumption of the device has been reduced from 4435.25MJ to 3816.66MJ,which achieves the goal of energy conservation and consumption reduction.Keywords:MTBE production device;top pressure of tower;reflux ratio;bottom temperature of tower;conversion rate of isobutylene;alcohol-ene ratio 作者简介:闫智斌:工程师,2010年毕业于北京化工大学(机械工程及自动化专业)引文:闫智斌.MTBE 生产装置节能降耗优化措施[J].石油石化节能与计量,2023,13(12):33-38.YAN Zhibin.Optimizing measures to energy conservation and consumption reduction for MTBE production device[J].Energy Conservation and Measurement in Petroleum &Petrochemical Industry,2023,13(12):33-38.闫智斌:MTBE 生产装置节能降耗优化措施第13卷第12期(2023-12)根据正碳离子反应理论,混合碳四原料中的异丁烯和原料甲醇在大孔径强酸性催化剂的作用下,反应生成MTBE 产品。
炼油储运环节的节能措施

炼油储运环节的节能措施
炼油储运环节是石油行业中非常重要的一个环节,也是石油资源利用过程中能源消耗
和环境污染较大的环节之一。
为了节约能源、保护环境,炼油储运环节需要采取一系列的
节能措施。
以下是一些常见的炼油储运环节的节能措施:
1. 智能控制系统:通过应用智能控制系统,可以实现对炼油储运系统的自动化控制,提高能源利用效率,减少能源的浪费。
2. 节能设备的应用:采用节能设备,如高效节能泵、高效节能压缩机等,可以有效
降低能源消耗,提高设备的效率。
3. 废热利用:在炼油过程中产生的废热可以通过废热回收设备进行回收利用,用于
加热、蒸汽发生等用途,减少能源消耗。
4. 能源优化管理:建立完善的能源管理体系,通过监测、调节和优化能源的使用,
实现能源的有效利用,减少能源的浪费。
5. 节能技术改造:对现有的炼油储运设施进行技术改造,采用先进的节能技术,如
低温蒸馏技术、节能改造技术等,提高能源利用效率。
6. 节能意识培训:加强员工的节能意识培养,提高员工对能源节约的重要性的认识,促使他们在工作中积极参与节能活动,减少能源的浪费。
7. 系统维护和管理:定期进行设备维护和管理,保持设备的良好运行状态,避免能
源浪费和环境污染。
8. 转型升级:通过技术创新和工艺改进,逐步实现炼油储运过程的绿色化、智能化,促进炼油储运行业的可持续发展。
炼油储运环节的节能措施需要从设备、技术、管理等多个方面入手,通过加强能源管
理和技术创新,实现能源的高效利用,减少能源消耗和环境污染,推动炼油储运行业的可
持续发展。
炼油化工企业的节能应用进展

炼油化工企业的节能应用进展关键词:炼油化工企业节能应用进展实现炼油化工企业的节能降耗是“十二五”规划的重要目标之一,也是转变经济发展模式、构建环境友好型社会的必经之路。
然而,当下的节能减排工作进展并不顺利,自2009年以来,重污染高耗能行业增长迅速,包括电力、钢铁、有色金属冶炼、炼油化工等行业,这无疑增加节能减排工作的难度。
炼油化工企业一方面为社会提供了能源,一方面又是能源最大的消耗者,要实现炼油化工行业的可持续发展,企业必须勇于担起节能减排的重任,转变经济发展模式,提高核心竞争力。
一、化工能量系统在节能技术上的应用1.夹点技术在节能技术中的应用在化工生产过程中,用来进行能量的转化、使用、回收等相关设备构建的系统称之为化工能量系统。
蒸汽系统、冷却处理系统、动力能源系统、回收换热系统等都是化工能量系统的分支。
夹点就是换热过程中热物流与冷物流之间存在的一个温差最小的点[1],夹点技术是回收换热系统中的一个关键点,热量能否得到有效的回收,关键在于夹点处的温度差。
利用夹点技术对全局能源进行优化,并且对系统的复杂改造、扩大容量、能源消耗与动力之间的潜在关系等进行总结,提出切实可行、有效的设计方案。
2.数字规划在节能技术上的应用把研究问题中得出的所有数据整合成函数和有约束条件的数学模型,并通过最佳途径找出既满足数学模型约束条件,又能使函数值最小的那个解,这就叫数字规划。
这种方法自身有一定的局限性,所以在操作过程中,要简化较为复杂的实际问题,在简化过程中,难免会有误差,再加上数字计算的不透明性,导致这个方法在实际操作中有一定的难度。
二、设备和装置的改进在节能技术中的应用1.加热炉的改进在节能技术上的应用目前最为有效且应用最广的节能途径就是降低排烟温度,要让排烟温度下降,主要可以从以下几点着手:一,改进换热器,提高换热效率,水工质的换热器就是运行效率比较高的一种;二,改进材料质量,防止露点被腐蚀,新开发的nd钢在这方面取得了较为理想的效果。
国外炼厂节能技术及能耗评价方法简介

国外炼厂节能技术及能耗评价方法简介能耗费用在炼厂现金操作费用中占有很大比例,其控制的好坏直接影响到炼厂现金操作费用的高低,是炼厂可控费用的主要方面之一,按统一价格计算,国内炼厂能耗费用平均占现金操作费用的50%左右,国外炼厂的比例约为40%,与国外同行业相比,国内大部分炼油企业在能耗方面还存在较大差距。
同时。
也可以看出炼油企业是高耗能企业,节能潜力较大。
为此,深入了解节能技术、原理以及国外节能评价方法,对进一步促进国内炼油企业的节能工作具有非常重要的现实意义。
一国外炼厂节能技术及先进经验能量消耗是炼油厂最大的单项操作费用,按照美国索罗门公司(Solomon)的能量密度指数(Energy Intensity Index, EII)和美国凯毕西先进过程技术公司(简称KBC公司)的最佳技术指数(Best Technology Index,BTI)来衡量,炼油厂作为一个整体能源利用效率并不高,炼油厂的平均能耗约为“最佳技术”炼厂水平的两倍。
因此,炼油厂能量消耗系统存在很大的节能潜力,即使在能源利用效率较高的炼油厂也同样如此。
炼油是微利型企业,竞争很激烈,企业之间使用的是相似生产技术和生产相似产品,除了规模、管理、产品有所差别以外,相互之间的主要差异就在于能源利用效率(简称能效)。
由此,人们可能会认为管理层的注意力和投资主要会集中在提高能效项目上。
然而,事实并非如此,根据国外的资料介绍,整个炼油行业在提高能效项目方面的投资仅占总建设投资的约5%。
在过去的10年中,能效较高的炼油厂的能效平均提高了约6%,能效较差的炼油厂能效提高了12%。
考虑到这些能效较差的炼油厂能耗是最佳技术水平的2.5倍,显然12%不是一个很高的数字。
节能潜力很大而实际投入却相对很少的矛盾是有其历史原因的。
世界主体炼油企业的形成是在70年代和80年代,当时炼油企业获利性较强,两次世界能源危机以后,炼油行业逐步转化为微利行业,而且重点从规模经济、装置大型化等方面来赢得效益,当时的节能意识并不很强烈,节能技术与设备发展比较缓慢,节能理论也并不十分完善。
中国炼油企业能源构成和转换技术的发展趋势
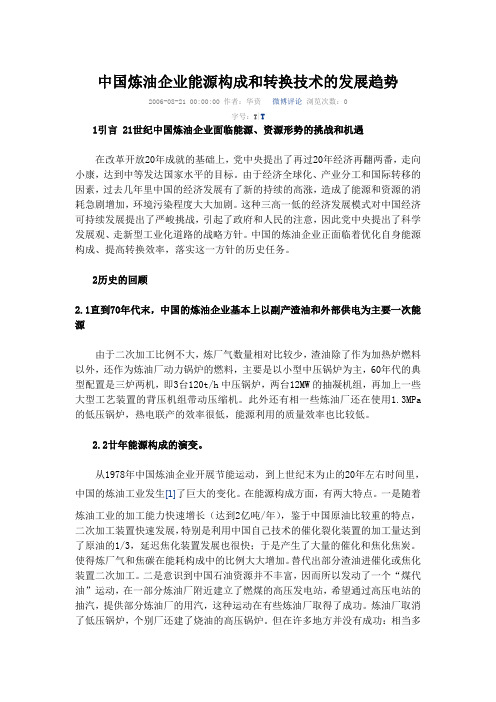
中国炼油企业能源构成和转换技术的发展趋势2006-08-21 00:00:00 作者:华贲微博评论浏览次数:0字号:T|T1引言 21世纪中国炼油企业面临能源、资源形势的挑战和机遇在改革开放20年成就的基础上,党中央提出了再过20年经济再翻两番,走向小康,达到中等发达国家水平的目标。
由于经济全球化、产业分工和国际转移的因素,过去几年里中国的经济发展有了新的持续的高涨,造成了能源和资源的消耗急剧增加,环境污染程度大大加剧。
这种三高一低的经济发展模式对中国经济可持续发展提出了严峻挑战,引起了政府和人民的注意,因此党中央提出了科学发展观、走新型工业化道路的战略方针。
中国的炼油企业正面临着优化自身能源构成、提高转换效率,落实这一方针的历史任务。
2历史的回顾2.1直到70年代末,中国的炼油企业基本上以副产渣油和外部供电为主要一次能源由于二次加工比例不大,炼厂气数量相对比较少,渣油除了作为加热炉燃料以外,还作为炼油厂动力锅炉的燃料,主要是以小型中压锅炉为主,60年代的典型配置是三炉两机,即3台120t/h中压锅炉,两台12MW的抽凝机组,再加上一些大型工艺装置的背压机组带动压缩机。
此外还有相一些炼油厂还在使用1.3MPa 的低压锅炉,热电联产的效率很低,能源利用的质量效率也比较低。
2.2廿年能源构成的演变。
从1978年中国炼油企业开展节能运动,到上世纪末为止的20年左右时间里,中国的炼油工业发生[1]了巨大的变化。
在能源构成方面,有两大特点。
一是随着炼油工业的加工能力快速增长(达到2亿吨/年),鉴于中国原油比较重的特点,二次加工装置快速发展,特别是利用中国自己技术的催化裂化装置的加工量达到了原油的1/3,延迟焦化装置发展也很快;于是产生了大量的催化和焦化焦炭。
使得炼厂气和焦碳在能耗构成中的比例大大增加。
替代出部分渣油进催化或焦化装置二次加工。
二是意识到中国石油资源并不丰富,因而所以发动了一个“煤代油”运动,在一部分炼油厂附近建立了燃煤的高压发电站,希望通过高压电站的抽汽,提供部分炼油厂的用汽,这种运动在有些炼油厂取得了成功。
炼油工艺的节能环保措施分析

炼油工艺的节能环保措施分析炼油工艺是一个能源密集型的行业,消耗大量的燃料和电能,同时排放大量的废气、废水和废渣。
为了保护环境和节约能源,炼油工艺需要采取一系列的节能环保措施。
一、引进新工艺通过引进新的炼油工艺,可以降低炼油过程中的能耗和物料损失,同时减少污染物的排放。
例如,采用催化裂化技术可以将较重的石油馏分转化为高辛烷值的汽油,同时降低能耗和SO2、NOx等污染物的排放。
二、优化生产工艺在现有的生产工艺基础上,通过优化工艺流程,可以提高能源利用率和环保水平。
例如,在炼油过程中采用低温分馏、高效蒸馏等优化工艺,可以降低能耗和废气排放。
同时,对生产过程中的废渣进行资源化利用,可以减少废物的产生和对环境的影响。
三、改造设备四、增加自备电力在炼油生产流程中,需要大量的电力供应。
通过增加自备电力设施的建设,可以减少对外部电力的依赖,降低生产成本,同时能够减少对环境的污染。
五、严格控制废气、废水和废渣的排放对于产生的废气、废水和废渣,要进行科学管理和处置。
采用物理、化学和生物等多种方式进行处理,达到减少排放和对环境的影响的目的。
严格落实环保相关法律法规,对超标排放的企业要予以约束和惩罚。
六、开展节能宣传通过开展节能宣传和教育,提高员工的节能意识,增强企业的环保责任感,促进企业转型升级和可持续发展,实现经济效益和环保效益的双赢。
总之,要实现炼油行业的节能环保,需要从各个方面入手进行综合治理。
通过引进新工艺、优化工艺流程、改造现有设备、增加自备电力、严格控制排放、开展节能宣传,才能够实现节能减排和环境保护的目标,推动经济可持续发展。
能耗计算与评价方法宣贯材料

因为设计能耗计算方法中,没有评价方法,只能使用此评 价方法。所以设计时的单位能量因数能耗与实际将有所不同,必 须注意此差别。
1.2 炼油厂能耗的定义与计算规则 1.2.1 炼油厂能耗是炼油厂在统计期内,对实际消耗的 各种能源,如各种燃料、动力(电、蒸汽)和耗能工 质等,进行综合计算所得的能源消耗量。
各种能源和耗能工质在进行综合计算时,均不得 漏计和重计。
炼油厂能耗的定义与国家标准《综合能耗计算通
则》GB-2589-90中的能耗定义相同。
1.2.2 炼油厂中消耗的压缩风、氮气等其它耗能工质,一般情况 下不计入工艺装置能耗中,生产这类工质的空压站、氧气站等, 应作为辅助系统进行能耗统计。但如果压缩风、氮气形成的能耗 占装置能耗的比例较大时,应计入装置能耗,同时应在辅助系统 能耗计算中,将已计入装置能耗的部分予以剔除。
1.3.2 炼油装置
由炼油装置能耗定额和联合装置的单位能量因数能耗评价装置 能耗水平。
炼油装置能耗定额指某类工艺装置应达到的先进能耗指标, 可用于对比评价工艺装置的能耗水平。
对联合工艺装置,由于各消耗项难以分开,可使用联合装置 的能耗定额和单位能量因数能耗进行评价。
1.3.3 辅助系统
由辅助系统的能耗定额、单位能量因数能耗和实际能量换算 系数评价辅助系统的用能水平。
2 能耗计算方法
2.1 综合能耗量
综合能耗量是统计对象(炼油装置、辅助系统或全厂)在统计 期内,消耗的各种能源的总和。其计算通式如下:
E=∑MiRi+Q 式中:E—统计对象综合能耗量,kg/年(月、季);
Mi—某种能源或耗能工质的实物消耗或输出量,t(kWh)/年 (月、季);
Ri—对应某种能源或耗能工质的能量换算系数,kg/t(kWh); Q—与外界交换的有效能量折为一次能源的代数和,kg/年(月、 季)。
炼油化工企业节能降耗技术分析

炼油化工企业节能降耗技术分析炼油化工企业作为能源消耗大户,节能降耗是保证企业可持续发展的关键。
随着能源价格上涨和环保法规的加强,企业不得不思考如何降低能源消耗和生产成本。
本文将从技术上探讨炼油化工企业节能降耗的一些方法和措施。
一、使用高效设备石化行业是高能耗、高污染行业,而设备是产生能耗和减少污染的主要工具。
使用高效设备是实现节能降耗的重要手段。
这里的高效设备主要指能够满足生产需要,同时降低能源消耗、废物排放的设备。
例如:采用节能型发酵罐替换常规发酵罐,采用新技术、新材料等高效氢气分离膜替代常规氢气分离膜,使用干法脱硫技术等。
二、优化生产工艺炼油化工企业生产工艺优化旨在提高生产效率,同时减少能源消耗和废物排放。
例如:采用喷雾蒸馏塔代替传统塔式分离技术,采用压缩空气余热回收技术等。
生产效率提高,不仅可以提高企业产品质量和产能,而且还能节约微观能源和资源。
可见,优化生产工艺是降低企业生产成本和提高生产效益的重要途径。
三、加强能源管理能源管理是实现节能控耗的关键环节,它主要涉及能源的采购、使用、管理、监测等方面。
能源管理的目的是在保证生产不间断的前提下,合理使用能源,避免浪费和无效消耗。
例如:制定合理的能源消耗标准、能源计量监测系统、定期检查设备,排查能耗浪费环节等。
只有通过有效的能源管理,才能够发现和解决能耗过高的问题,实现企业节能降耗。
四、发展循环经济发展循环经济是实现炼油化工企业可持续发展的重要途径。
循环经济是一种经济模式,它将废弃物转化为资源,减少资源的浪费,提高资源的利用价值。
例如:废水、废气、废液等可再利用。
通过循环经济,可以真正实现节能降耗,减少对自然资源的依赖。
炼油化工企业的节能降耗是一个综合性问题,需要在场地规划、工艺设计、设备选型、供能方式、能源管理等方面进行全方位的考虑和部署。
只有不断提升技术、改进工艺、优化管理,才能够实现炼油化工企业的可持续发展。
- 1、下载文档前请自行甄别文档内容的完整性,平台不提供额外的编辑、内容补充、找答案等附加服务。
- 2、"仅部分预览"的文档,不可在线预览部分如存在完整性等问题,可反馈申请退款(可完整预览的文档不适用该条件!)。
- 3、如文档侵犯您的权益,请联系客服反馈,我们会尽快为您处理(人工客服工作时间:9:00-18:30)。
第一章节电案例 (3)案例1 联合二机泵差别化管理 (3)案例2 3#制氢鼓引风机变频节电 (5)案例3 4#常减压蒸馏减压塔鼓风机节电改造 (5)案例4 石蜡加氢高压原料泵叶轮减级降低电耗 (6)案例5 降低轻糠罐区泵输送压力,降低电耗 (6)案例6 优化工艺操作,降低氢压机用电 (6)案例7 变频技术应用---1#提升泵使用变频器节电 (7)案例8 操作优化---停开浮选池,减少开泵频率节能 (7)案例9 一催化开2#风机运行优化 (8)案例10 精制罐区焦化汽油直供加氢流程改造 (9)案例11 秋冬季节循环水场采用分散布水方式 (9)增强自然冷却作用节约风机用电 (9)第二章节汽案例 (10)案例1 1号加氢自产蒸汽供航煤加氢改造 (10)案例2 三催化装置锅炉节能改造 (12)案例3 4#常减压蒸馏机械抽真空系统节电节蒸汽改造 (13)案例4 尾气装置放空中压蒸汽接入低压蒸汽管网使用 (14)案例5 中压蒸汽凝结水直接注入硫冷凝器回用 (15)案例 6 中压锅炉水连续排污热水改进中压蒸汽冷凝水分离罐增产低低压蒸汽 (15)案例7 沥青车间节汽改造 (16)案例8 石蜡成型装置及白土装置蜡罐改用热水维温 (18)案例9二次加工原料优化流程改造 (19)案例10 优化蒸汽操作节约蒸汽 (21)案例11 石蜡加氢优化操作,降低蒸汽用量 (21)案例12 原料罐区加强管理,优化用汽节能 (22)案例13 新苯抽提0.7MPa闪蒸蒸汽用于渣油罐加热维温及管带管线伴热改造 (23)第三章节水案例 (23)案例1 节水减排----监护池生化风机改用回用水冷却 (23)案例2 东循、南循增加雨水回收设备回收后期雨水 (24)案例3 雨季时统筹调配后期雨水及回用水减少新鲜水用量 (25)案例4 石蜡加氢装置精细调节,降低循环水单耗 (26)案例5 MTBE装置优化循环水使用 (27)案例6 3#常减压蒸馏装置煤油热联合停用水冷器 (27)案例7 联合五车间优化冷换设备,节约循环水消耗 (28)第四章其它案例 (28)案例1 2#焦化装置加热炉节能技术改造 (28)案例2 2#焦化装置脱吸塔重沸器E-203/1改用柴油作为热源流程优化.. 29 案例3 3#加氢装置E105改造项目 (30)案例4 三糠醛加强操作管理,降低糠醛单耗 (32)案例5 三号常减压蒸馏装置换热网络节能调优 (32)案例6 脱油一二段滤液自循环 (33)案例7 一催化增加原料缓冲罐热联合改造项目 (34)第一章节电案例案例1 联合二车间机泵差别化管理节电1、项目背景根据机泵能量传输过程,机泵存在系统效率高低情况(η),η=η1η2η3η4,%,其中η1,η2,η3,η4—分别为电机效率、电机与机泵间的传动效率、机泵效率、管路效率,每一台机泵都有各自不同的系统效率。
即,在同一负荷下,即使是同一位号的两台机泵耗电量也可能有所不同,通过比较运行与备用机泵现场电流值找出差异,同时联系电工对运行机泵测量电流和每天的实际消耗量,以确定找出同一位号电耗最少的设备。
在充分调研和普查的基础上,针对联合二各装置生产任务和各操作单元设备运行的实际情况,制定落实了优化工艺生产方案节电措施,取得显著的节电效果。
提出了“对运行机泵或风机和备用机泵或风机实行节电差别化管理”的方案。
2、改进内容为分别出哪台机泵省电,渣油加氢和制氢装置分别测量了各机泵、风机的电流或电量。
具体情况如下:渣油加氢装置对除P102A(高压进料泵)、长期不开的机泵或风机(如AC203等)及变频或带有液力透平的机泵的备用机泵未进行“差别化”普查外,其余机泵、风机都进行了电流普查。
各机泵、风机电流对比情况见下表。
表1 渣油机泵“差别化”管理电流普查情况表制氢装置除长期不开的机泵、风机未进行“差别化”普查外,其余机泵、风机都进行了普查。
各机泵、风机耗电对比情况见下表。
表2 制氢机泵“差别化”管理电量普查情况表3、改进前由于各台机泵无序使用,各套装置每天用电量时高时低,对每天耗电量变化情况难以把握。
4、改进后经过生产试验,得到了出乎意料的结果。
从数据比较发现,制氢装置C2001A 系统效率较高,相同负荷下比C2001B每天节电3000KWh,P2003B在相同负荷下比P2003A电流下降5A,每天节电1500KWh。
因此,在正常情况下,投用最省电的设备,每天就可节电4500KWh。
4、效果及经济效益计算制氢的C2001A在相同负荷下比C2001B每天节电3000KW.h,P2003B在相同负荷下比P2003A每天节电1500KW.h。
投用最省电的设备,仅此两台机泵每天就可节电4500KW.h,每天节约2790元。
渣油加氢“差别化”管理效果也是比较明显,如P103A/B两台泵电流相差15A,AC202A/B相差16A,AC201B/D/F/H与AC201A/C/E/G相差22.5A等.如果全部投用低耗电机泵或风机,粗略估算每天可减少电量近1000 KW.h,相当于停开近10台低压机泵,每天节省电费620元。
该方案在炼油分部各装置进行推广。
案例2 3#制氢鼓引风机变频节电1、项目背景制氢鼓风机C2003A和引风机C2002A在负荷低时显得富余较多,档板开度经常分别在40%及30%以下,负荷较低时可以分别降低到20%及5%左右,电流分别为135A及35A,在电耗浪费的同时,也增加了加热炉的瓦斯消耗,如果增加变频器,将鼓、引风机的档板全开,将可以有效降低鼓、引风机的电耗的同时,可以明显降低加热炉的瓦斯消耗,起到一举两得的功效,经济效益比较明显。
2、改造内容在制氢鼓风机C2003A和引风机C2002A各增设一台变频器;引调节器入DCS,并进行组态;工艺原则流程不变,但电气线路和仪表控制系统需改造。
3、改造前制氢鼓风机C2003A和引风机C2002A在负荷低时显得富余较多,档板开度经常分别在40%及30%以下,负荷较低时可以分别降低到20%及5%左右,电流分别为135A及35A,在电耗浪费的同时,也增加了加热炉的瓦斯消耗。
4、改造后鼓引风机投用变频后,引风机每天节电3500KWh,鼓风机每天节电800KWh,其技术经济性可行。
5、效果及经济效益相同负荷下,引风机工频每天耗电4900 KWh,投用变频每天耗电1300 KWh,节电3600 KWh;鼓风机投用变频后每天节电800KWh。
案例3 4#常减压蒸馏减压塔鼓风机节电改造1 改造前四蒸馏装置减压炉由于风道挡板卡涩无法全关,使装置在加工轻质原油时,风量需求偏小的情况下,造成炉氧含量偏高达6.0%,炉热效率仅有89.5%。
2 改造内容四蒸馏装置鼓风机C102电机加装变频器。
3 改造后该项目实施投用后使鼓风机电机电流从40A降低至20A,不仅节电7.6KWh,且炉子空气氧含量降至3.0%,较之前下降了3.0个百分点,炉子热效率也已提高至90.5%,比之前提高了1.0个百分点。
4 效果及经济效益既节电又减少了加热炉的燃料消耗量,年节电6万KW·h,节约成本3万多元,年节约燃料消耗466吨,节约成本190万多元。
案例4 石蜡加氢高压原料泵叶轮减级节电1 项目背景石蜡加氢装置原料蜡高压进料泵由于无法安装变频器使用,泵出口阀前后压差高达2.0MPa以上,节流损失较大。
2 改造前情况泵出口压力约9.0MPa。
3 改造后情况泵202/2叶轮由原来的28级减至23级、泵202/3叶轮由原来的28级减至22级,泵出口压力降至约7.0MPa,泵电流由原来的200A降至约150A。
4 效果及经济效益按电机消耗功率公式N=3×I×U×cosφ×10-3(KW),电机功率因数取0.85算,泵全年可节电为:1.732×(200-150)×380×0.85×10-3×8400 =234963(KWh),按电价0.55元/KWh计算,每年可节省电费为12.92万元。
案例5 降低轻糠罐区泵输送压力,降低电耗1 项目背景润滑油轻糠罐区泵5、6作为第三套糠醛精制的原料泵,第三套糠醛精制装置的脱气塔8,其液位控制一直由调节阀控制着保持一定的水平,以保证装置的生产平稳。
2 改进内容通过优化三糠醛塔8液位控制方法,可以把轻糠罐区泵5、6的泵出口压力降低。
3 改进前泵出口压力有1.1MPa,耗电量一直居高不下(大约900KWh/日)。
4 改进后泵出口压力降低到0.6MPa。
耗电量降低了450KWh/日。
5 效果及经济效益每年可节电:450×330 =14.85(万KWh),每年可节约电费:0.55×14.85≈8.17(万元)。
案例6 优化工艺操作,降低氢压机用电1 项目背景石蜡加氢装置新氢压缩机是装置的耗电大户,约占装置总电耗的60%,机的负荷、效率、系统压力大小对电耗大小都有不同程度的影响,我们通过对比发现,机201/1与机201/2在50%负荷及相同的系统压力下的电耗相差较大,机201/1较机201/2平均每天要节省电耗约500KWh。
2 改进内容(1) 根据原料蜡质量较好的情况,氢蜡比(体)降至100左右、反应压力保持约5.25MPa的较低状态下操作,保持氢压机50%负荷下运行。
(2) 在无特殊情况下都要保持机201/1运行。
3 改进前在氢压机50%负荷下,氢压机平均每天电耗约3800 KWh。
4 改进后在氢压机50%负荷下,氢压机平均每天电耗约3300 KWh。
5 效果及经济效益全年可节电182500 KWh,年效益为11.32万元。
案例7 污水处理装置1#提升泵使用变频器节电1 项目背景污水处理装置在非雨季生产中,1#提升泵出口压力偏高、流量偏大,导致能源的浪费。
2 改造前情况1#提升泵出口压力偏高、流量偏大,导致能源的浪费。
3 改造后情况2009年1月投用1#提升泵变频器1台,使提泵出口压力和流量趋向合理。
4 效果及经济效益投用1#提升泵变频器后,电流下降30A左右,每小时节电量11.4KWh。
按照年运行时间8000小时,电价0.55元/KWh计算,每年可产生经济效益:0.55×11.4×8000=50160(元)案例8 污水处理装置操作优化,停开浮选池,减少开泵频率节电1 项目背景根据含油污水处理量,适当减少一级浮选池进水个数,节约能耗。
由于冬季含油污水量少,大约400~450m3/h,按设计能力,浮选装置只开5个池即可,减少3个池进水,这样,就可以减少一台回流泵(75KW),3台内循环泵(33.6KW),3台刮渣机(2.3KW),3台搅拌机(12KW),共节省122.9KW,达到节能目的。