催化燃烧方法概况_范恩荣
催化燃烧技术介绍
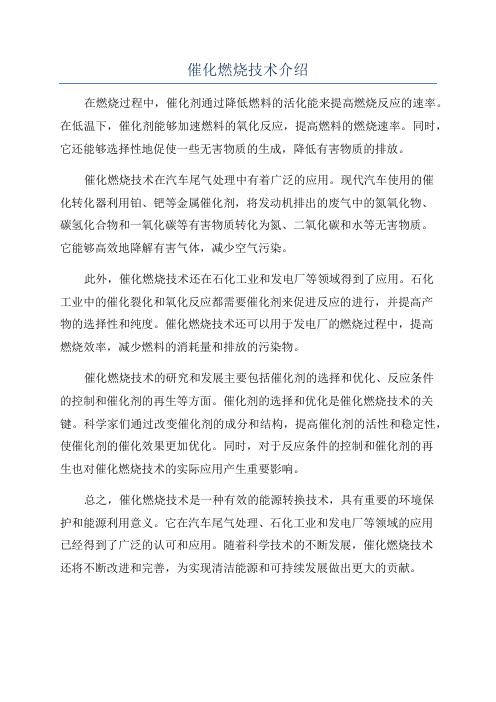
催化燃烧技术介绍
在燃烧过程中,催化剂通过降低燃料的活化能来提高燃烧反应的速率。
在低温下,催化剂能够加速燃料的氧化反应,提高燃料的燃烧速率。
同时,它还能够选择性地促使一些无害物质的生成,降低有害物质的排放。
催化燃烧技术在汽车尾气处理中有着广泛的应用。
现代汽车使用的催
化转化器利用铂、钯等金属催化剂,将发动机排出的废气中的氮氧化物、
碳氢化合物和一氧化碳等有害物质转化为氮、二氧化碳和水等无害物质。
它能够高效地降解有害气体,减少空气污染。
此外,催化燃烧技术还在石化工业和发电厂等领域得到了应用。
石化
工业中的催化裂化和氧化反应都需要催化剂来促进反应的进行,并提高产
物的选择性和纯度。
催化燃烧技术还可以用于发电厂的燃烧过程中,提高
燃烧效率,减少燃料的消耗量和排放的污染物。
催化燃烧技术的研究和发展主要包括催化剂的选择和优化、反应条件
的控制和催化剂的再生等方面。
催化剂的选择和优化是催化燃烧技术的关键。
科学家们通过改变催化剂的成分和结构,提高催化剂的活性和稳定性,使催化剂的催化效果更加优化。
同时,对于反应条件的控制和催化剂的再
生也对催化燃烧技术的实际应用产生重要影响。
总之,催化燃烧技术是一种有效的能源转换技术,具有重要的环境保
护和能源利用意义。
它在汽车尾气处理、石化工业和发电厂等领域的应用
已经得到了广泛的认可和应用。
随着科学技术的不断发展,催化燃烧技术
还将不断改进和完善,为实现清洁能源和可持续发展做出更大的贡献。
催化燃烧方案

催化燃烧方案
催化燃烧是一种采用催化剂促进燃烧反应的技术,具有高效、节能、环保等优点。
下面我将介绍一种常见的催化燃烧方案。
该方案的催化剂采用铂金催化剂,可以有效地催化燃烧反应。
具体的工艺流程如下:
首先,在燃烧系统中进气口进入燃料和空气。
然后,将燃料和空气送入燃料燃烧室,在燃料燃烧室中,添加适量的催化剂。
催化剂起到了至关重要的作用。
当燃料和空气经过催化剂时,催化剂会吸附并活化燃料分子和空气分子。
活化后的燃料分子和空气分子之间发生氧化还原反应,生成水和二氧化碳等物质,并释放出大量的热能。
与传统燃烧方式相比,催化燃烧能够提高燃料的燃烧效率,减少废气的排放。
这主要得益于催化剂具有很高的催化活性和选择性,能够在较低的温度下催化燃烧反应,使燃烧反应更加充分、高效。
另外,该方案还具有很好的节能效果。
传统燃烧方式中,燃料的燃烧需要较高的温度才能进行,而催化剂使得燃烧反应可以在较低的温度下进行,减少了能源的消耗。
此外,催化燃烧方案还能够有效地降低废气的排放。
传统燃烧方式中,因为燃料的燃烧不完全,会产生大量的有害气体和颗粒物,对环境造成污染。
而催化剂能够催化燃烧反应,提高燃
烧效率,减少有害气体和颗粒物的排放。
综上所述,催化燃烧方案采用铂金催化剂,通过催化燃烧反应使燃料和空气中的分子活化,并在较低的温度下达到高效、节能和环保的效果。
这种方案在工业生产和能源利用等领域有着广阔的应用前景。
催化燃烧的原理和应用
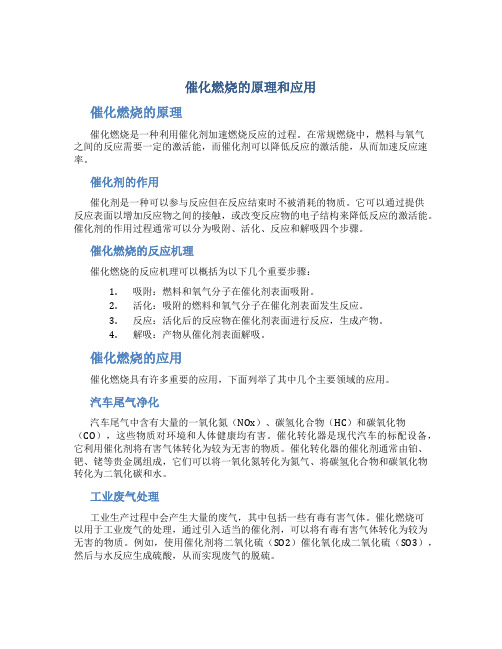
催化燃烧的原理和应用催化燃烧的原理催化燃烧是一种利用催化剂加速燃烧反应的过程。
在常规燃烧中,燃料与氧气之间的反应需要一定的激活能,而催化剂可以降低反应的激活能,从而加速反应速率。
催化剂的作用催化剂是一种可以参与反应但在反应结束时不被消耗的物质。
它可以通过提供反应表面以增加反应物之间的接触,或改变反应物的电子结构来降低反应的激活能。
催化剂的作用过程通常可以分为吸附、活化、反应和解吸四个步骤。
催化燃烧的反应机理催化燃烧的反应机理可以概括为以下几个重要步骤:1.吸附:燃料和氧气分子在催化剂表面吸附。
2.活化:吸附的燃料和氧气分子在催化剂表面发生反应。
3.反应:活化后的反应物在催化剂表面进行反应,生成产物。
4.解吸:产物从催化剂表面解吸。
催化燃烧的应用催化燃烧具有许多重要的应用,下面列举了其中几个主要领域的应用。
汽车尾气净化汽车尾气中含有大量的一氧化氮(NOx)、碳氢化合物(HC)和碳氧化物(CO),这些物质对环境和人体健康均有害。
催化转化器是现代汽车的标配设备,它利用催化剂将有害气体转化为较为无害的物质。
催化转化器的催化剂通常由铂、钯、铑等贵金属组成,它们可以将一氧化氮转化为氮气、将碳氢化合物和碳氧化物转化为二氧化碳和水。
工业废气处理工业生产过程中会产生大量的废气,其中包括一些有毒有害气体。
催化燃烧可以用于工业废气的处理,通过引入适当的催化剂,可以将有毒有害气体转化为较为无害的物质。
例如,使用催化剂将二氧化硫(SO2)催化氧化成二氧化硫(SO3),然后与水反应生成硫酸,从而实现废气的脱硫。
能源生产催化燃烧在能源生产中也有重要应用。
例如,燃气锅炉和燃气轮机利用催化剂将天然气或石油等燃料转化为热能或电能。
催化燃烧可以提高能源转换效率,减少排放物的产生。
石油化工在石油化工过程中,催化燃烧被广泛应用于各个环节。
例如,催化裂化是将重质石油馏分转化为轻质馏分的过程,催化重整是将石脑油等重质馏分转化为较高辛烷值的高级汽油的过程。
《催化燃烧技术》课件

THANKS
感谢观看
优化反应条件与设备
通过科研创新,开发出更高效、更环保的 催化剂是关键。
改进反应条件控制技术和设备,提高催化 燃烧反应效率和设备稳定性。
降低成本与提高能效
加强排放物控制与副产物处理
通过技术改进和规模化生产,降低催化燃 烧技术的成本和能耗,提高经济效益和环 保效益。
采用先进的排放物处理和副产物处理技术 ,确保催化燃烧技术的环保性能。
05
案例分析
某企业工业废气处理项目
01
02
03
案例概述
某企业面临工业废气排放 问题,需要采用催化燃烧 技术进行处理。
技术应用
采用高效催化剂和优化燃 烧技术,降低废气中的有 害物质含量。
实施效果
经过处理后,废气排放达 到国家标准,企业获得环 保认证。
某品牌汽车尾气处理系统
案例概述
某品牌汽车为满足日益严 格的环保要求,需要在尾 气处理系统中采用催化燃 烧技术。
技术挑战
催化剂活性与选择性问题
部分有毒有害物质无法被高效催化燃烧,需要研发更高效的催化 剂。
反应条件控制
催化燃烧反应需要精确控制温度、压力等反应条件,以确保反应效 率。
设备腐蚀与结焦问题
高温、高压条件下,设备腐蚀和结焦问题严重,影响催化燃烧技术 的长期稳定运行。
经济性挑战
设备投资与运行成本高
高端催化剂和精密设备导致初始投资 和运营成本较高。
技术应用
在尾气处理系统中加入催 化剂,促进有害物质的氧 化分解。
实施效果
有效降低汽车尾气中的有 害物质含量,提高车辆的 环保性能。
某燃煤电厂燃料燃烧优化实践
案例概述
某燃煤电厂为提高燃烧效率并降低污染物排放, 采用催化燃烧技术进行燃料燃烧优化。
催化燃烧法

催化燃烧法催化燃烧法是一种高效清洁燃烧技术,主要利用催化剂使有机废气在较低的温度条件下充分燃烧。
相对其他处理技术,催化燃烧具有显著的优点:起燃温度低能耗少,处理效率高,无二次污染等,使之成为目前前景广阔的VOCs有机废气治理方法之一。
高效催化燃烧催化剂是催化燃烧技术的关键核心,以块状载体作为骨架基体的催化剂称为规整结构催化剂,也称为整体式催化剂。
由于具有特殊孔道结构,这类催化剂改善了催化反应床层上的物质传递,提高了催化效率,降低了压力,减少了操作费用,在石油化工、精细化工等多相催化反应中得到越来越广泛的应用。
催化燃烧法处理 VOCs 的过程中,存在如下几种安全隐患:活性炭吸附—脱附—催化燃烧法中有活性碳起火的现象、催化氧化炉爆炸问题、整个催化燃烧治理装置起火爆炸问题。
1.活性碳起火现象及防范措施在前期的 VOCs 富集过程中,由于活性炭着火点较低而脱附温度过高,当对吸附饱和的活性炭进行脱附处理时,会由于脱附箱体内温度过高导致活性炭着火。
解决该问题可以从两个方面着手:一是采用着火点高的活性炭;二是严格控制脱附温度,使其远低于活性炭着火点。
因此可采取如下措施:严格控制脱附温度,选择质量好的脱附温度传感器,尽可能在活性炭吸附箱合适位置安装两个温度传感器;在 PLC 编程中加入脱附温度超温时停止脱附程序;同时要防患于未然,在活性炭吸附箱上方增加消防水管并连结烟气报警及自动喷淋装置,以防意外失火。
2.催化氧化炉爆炸问题及防范措施在处理高浓度 VOCs 时,由于炉内含有大量氧气,当废气浓度达到废气组份中大部分有机废气的爆炸极限时,就会有爆炸的危险。
因此,要时刻监测炉内 VOCs 浓度,在进入催化氧化炉的废气管道上安装浓度稀释装置,将高浓度废气稀释到爆炸极限下。
同时在催化氧化炉上增加压力排气阀,在压力过高时自动打开阀门进行减压排气,以防炉内温度压力过高引起爆炸(因废气在热氧化过程中迅速释放大量热能导致炉内热空气压力过大)。
促进陶瓷烧成的新途径

使氧化物陶瓷烧结致密度 强度 抗裂性 硬度和
耐磨性大大改善O 以 下 阐 述 将 超 细 金 属 粉 末 引 入 到 A12O3 和
ZFO2 为基础的陶瓷材料中对烧成和性能的影响O
收稿日期: 2001-03-129 修回日期: 2001-08-03 作者简介: 范恩荣 ( 1942-) 男 浙江绍兴人 高级工程师
4. 37
5. 51 6. 30 9.面形成了复杂成分的化合物固溶
体 < MgAl3Ti3O10化合物D , 而氧化铝实际上不熔于 ZKO2 中, 烧结的 ZKO2 有了这层膜, 阻碍它再结晶O 从岩相分析照片可以看出, 若添加量合适, 陶瓷材
由于上述两种原料粉其细度和比表面积不同
材料性能新的有效途径 尤其对于需高温烧成 技 在引入超细金属粉添加剂时 对它们的烧结反应影
术性能要求比较高的特种陶瓷 如氧化物陶瓷 钛 酸钡陶瓷等O
作为陶瓷促烧剂的金属粉必须具有大的内应 力 也就是这种金属粉贮藏有能量 所以又称为贮 能金属粉O 这类金属粉一般采用大功率脉冲电流在 惰性或化学活性 ( 氢) 介质中融化喷雾而成 也有 的采用化学沉淀方法沉淀到陶瓷配合料中O 由于超 细粉与同类大颗粒的金属材料比较 它的烧结和熔 化温度大大降低 并在氧化过程中呈现高的化学活 性O 在陶瓷材料中加入超细金属粉或化学沉淀金属 到陶瓷配合料中 可以强化陶瓷烧成过程 调节陶 瓷材料所必须的性能O
最感兴趣的是采用塑性金属添加剂 < Cu ~ N iD ,
它可以超过金属铝粉几倍量引入到陶瓷材料中, 例
如将铜超细粉末引入到陶瓷材料中, 在烧成时, 铜
可以均匀配置在氧化物颗粒之间, 形成阻尼层, 从
而 大大增加陶瓷材 料 的 抗 裂 性O 在 ZKO2 -Cu 系 统
催化燃烧工艺流程

催化燃烧工艺流程催化燃烧工艺是一种将有机物质转化为二氧化碳和水的方法,通过催化剂促进反应的进行。
在这个过程中,有机物质在高温下与催化剂发生反应,产生热能和废气。
下面是一个典型的催化燃烧工艺流程的描述:首先,将待处理的有机物质送进反应器中。
有机物质可以是液体、气体或固体,常见的有机物包括石油化工行业的废水和废气、城市垃圾焚烧产生的废气等。
在反应器中,有机物质与催化剂接触。
通常情况下,催化剂是以颗粒形式存在,可以是金属、氧化物或硅胶等。
催化剂能够提高反应速率,降低反应温度和能量消耗。
当有机物质与催化剂接触时,开始发生催化燃烧反应。
有机物质分子中的化学键被打断,生成碳氢化合物和氧化物的中间产物。
这些中间产物在催化剂的作用下进一步反应,最终生成二氧化碳和水。
同时,反应过程中还会释放出热能。
在催化燃烧反应中,需要控制反应的温度。
一般来说,反应温度要高于有机物质的沸点,以确保反应的进行。
此外,还需要控制催化剂的用量,确保足够的催化剂与有机物质接触。
当反应完成后,产生的废气会经过处理。
废气中包含大量的二氧化碳和水蒸气,还有一些少量的其他气体,如一氧化碳和氮氧化物等。
这些气体需要进行净化,以达到排放标准。
废气净化通常包括物理处理和化学处理两个步骤。
物理处理通常使用过滤器或吸附剂去除废气中的颗粒物和有机物质。
化学处理则使用氧化剂或其他化学试剂来吸收或催化转化废气中的有害物质。
最后,经过净化处理的废气可以被释放到大气中,或用于其他工业用途。
同时,还可以收集二氧化碳,用于其他化学工艺或碳捕获技术。
催化燃烧工艺流程经过催化剂的作用,能够将有机物质高效地转化为二氧化碳和水,减少了对环境的污染。
同时,催化燃烧所产生的热能也可以用于发电或其他工业用途,提高能源的利用效率。
论述催化燃烧的原理及应用
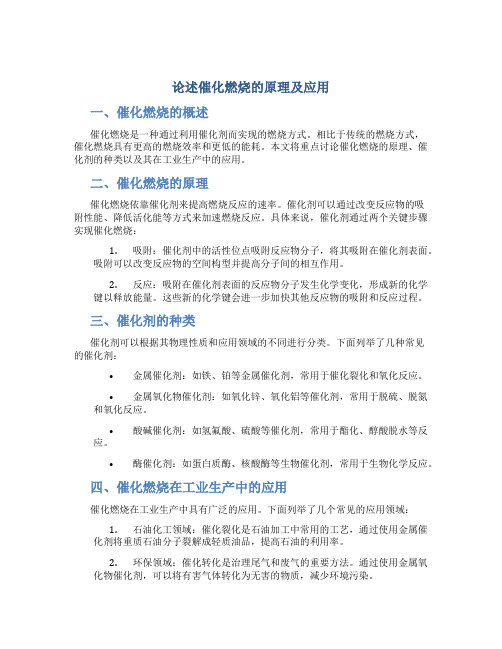
论述催化燃烧的原理及应用一、催化燃烧的概述催化燃烧是一种通过利用催化剂而实现的燃烧方式。
相比于传统的燃烧方式,催化燃烧具有更高的燃烧效率和更低的能耗。
本文将重点讨论催化燃烧的原理、催化剂的种类以及其在工业生产中的应用。
二、催化燃烧的原理催化燃烧依靠催化剂来提高燃烧反应的速率。
催化剂可以通过改变反应物的吸附性能、降低活化能等方式来加速燃烧反应。
具体来说,催化剂通过两个关键步骤实现催化燃烧:1.吸附:催化剂中的活性位点吸附反应物分子,将其吸附在催化剂表面。
吸附可以改变反应物的空间构型并提高分子间的相互作用。
2.反应:吸附在催化剂表面的反应物分子发生化学变化,形成新的化学键以释放能量。
这些新的化学键会进一步加快其他反应物的吸附和反应过程。
三、催化剂的种类催化剂可以根据其物理性质和应用领域的不同进行分类。
下面列举了几种常见的催化剂:•金属催化剂:如铁、铂等金属催化剂,常用于催化裂化和氧化反应。
•金属氧化物催化剂:如氧化锌、氧化铝等催化剂,常用于脱硫、脱氮和氧化反应。
•酸碱催化剂:如氢氟酸、硫酸等催化剂,常用于酯化、醇酸脱水等反应。
•酶催化剂:如蛋白质酶、核酸酶等生物催化剂,常用于生物化学反应。
四、催化燃烧在工业生产中的应用催化燃烧在工业生产中具有广泛的应用。
下面列举了几个常见的应用领域:1.石油化工领域:催化裂化是石油加工中常用的工艺,通过使用金属催化剂将重质石油分子裂解成轻质油品,提高石油的利用率。
2.环保领域:催化转化是治理尾气和废气的重要方法。
通过使用金属氧化物催化剂,可以将有害气体转化为无害的物质,减少环境污染。
3.能源领域:催化燃烧可以提高燃料的利用效率,减少能源消耗。
例如,在发动机内部使用催化剂可以降低汽车尾气中有害物质的排放。
4.化学合成领域:催化合成可以加速化学反应的进行,提高产物的纯度和选择性。
酸碱、金属和酶催化剂在有机合成中有着广泛的应用。
五、结论催化燃烧通过利用催化剂加速燃烧反应的速率,提高了燃烧的效率和能源利用率。
voc催化燃烧法
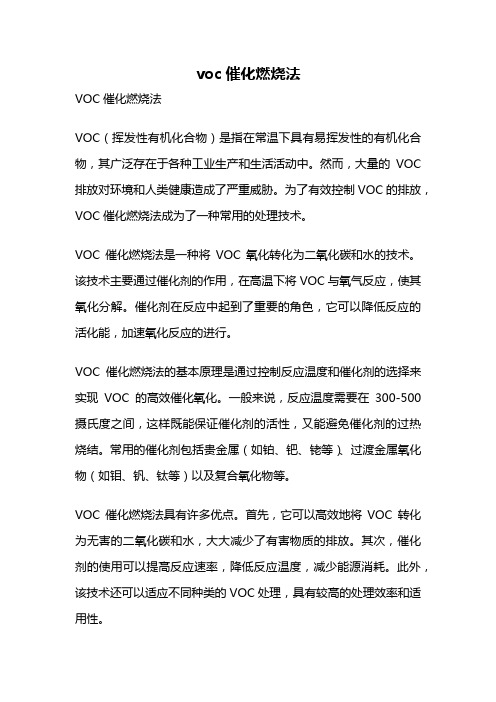
voc催化燃烧法VOC催化燃烧法VOC(挥发性有机化合物)是指在常温下具有易挥发性的有机化合物,其广泛存在于各种工业生产和生活活动中。
然而,大量的VOC 排放对环境和人类健康造成了严重威胁。
为了有效控制VOC的排放,VOC催化燃烧法成为了一种常用的处理技术。
VOC催化燃烧法是一种将VOC氧化转化为二氧化碳和水的技术。
该技术主要通过催化剂的作用,在高温下将VOC与氧气反应,使其氧化分解。
催化剂在反应中起到了重要的角色,它可以降低反应的活化能,加速氧化反应的进行。
VOC催化燃烧法的基本原理是通过控制反应温度和催化剂的选择来实现VOC的高效催化氧化。
一般来说,反应温度需要在300-500摄氏度之间,这样既能保证催化剂的活性,又能避免催化剂的过热烧结。
常用的催化剂包括贵金属(如铂、钯、铑等)、过渡金属氧化物(如钼、钒、钛等)以及复合氧化物等。
VOC催化燃烧法具有许多优点。
首先,它可以高效地将VOC转化为无害的二氧化碳和水,大大减少了有害物质的排放。
其次,催化剂的使用可以提高反应速率,降低反应温度,减少能源消耗。
此外,该技术还可以适应不同种类的VOC处理,具有较高的处理效率和适用性。
在实际应用中,VOC催化燃烧法被广泛应用于各种工业领域。
例如,印刷、油漆、溶剂和化工等行业中,VOC排放量较大,使用VOC 催化燃烧法可以有效减少环境污染。
此外,VOC催化燃烧法还可以与其他处理技术相结合,如吸附、脱附、蒸汽回收等,进一步提高处理效果。
然而,VOC催化燃烧法也存在一些挑战和改进的空间。
首先,催化剂的选择和催化剂的失活问题需要进一步研究和解决。
其次,高温下的反应条件对设备和材料的要求较高,需要考虑耐高温、耐腐蚀等特性。
此外,VOC催化燃烧法对反应废气的预处理和处理后的尾气排放控制也是一个重要的问题。
VOC催化燃烧法是一种有效控制VOC排放的技术。
通过选择合适的催化剂和控制适当的反应条件,可以实现VOC的高效催化氧化,将有害物质转化为无害的产物。
(完整)催化燃烧技术

催化燃烧技术直接燃烧、热力燃烧的分类两者的区分:是否添加燃料,热力燃烧中有一类特殊的叫催化燃烧.直接燃烧经济,常外加燃料汽油或天然气,缺点是燃烧不完全,产生NOx,大量的有害气体和烟尘,以及热辐射。
催化燃烧,是典型的气-固相催化反应,其实质是活性氧参与深度氧化作用.在催化燃烧过程中,催化剂的作用是降低反应的活化能,同时使反应物分子富集于催化剂表面,以提高反应速率。
又称无焰燃烧,燃烧完全,温度要求不高,200-450℃。
对进气有要求,不能含有硫,卤素,重金属等使催化剂中毒的元素,而且有时需要消耗辅助燃料.缺点是工艺复杂。
催化燃烧可分为:预热式:废气温度低于起燃温度自身热平衡式:废气温度高于起燃温度吸附—催化燃烧:有机废气的流量大,浓度低,温度低、采用催化燃烧需要消耗大量燃料时,可先采用吸附浓缩处理催化剂的作用:降低反应的活化能,降低反应温度,提升反应速率催化剂寿命:8000H,低于此值能保证90%的催化燃烧效率催化燃烧工艺选择垂询表垂询表有5个因素,如下风量:决定设备型号大小.浓度:决定是回收还是燃烧还是需要加浓缩吸附再处理,理论起燃浓度200mg/m³,最佳自平衡浓度2500mg/m³-3000mg/m³无需辅热(以催化燃烧为例)。
温度:温度太高不能直接进活性炭(耐温极限80℃)浓缩,可以选择沸石(150℃)。
成分:有机组分的起燃温度和热值对工艺有影响,物质的爆炸极限浓度需要衡量,进炉膛的气体控制浓度在25%LEL以下。
苯类 280℃,乙酸乙酯350℃,热值能确定辐热系统的功率。
工作周期:选择备用吸附床,一般设备工作8H不用,超过16H一定要用备用床.安装要求:场地大小是否受限,平面与高度。
催化燃烧分类1.活性炭吸附—蒸汽脱附—催化燃烧(VOC-XC)2。
活性炭吸附—冷凝回收3.低温氧化催化(VOC—CH)4。
蓄热式催化净化(RCO)5。
蓄热式热力氧化(RTO)6。
催化燃烧技术方案
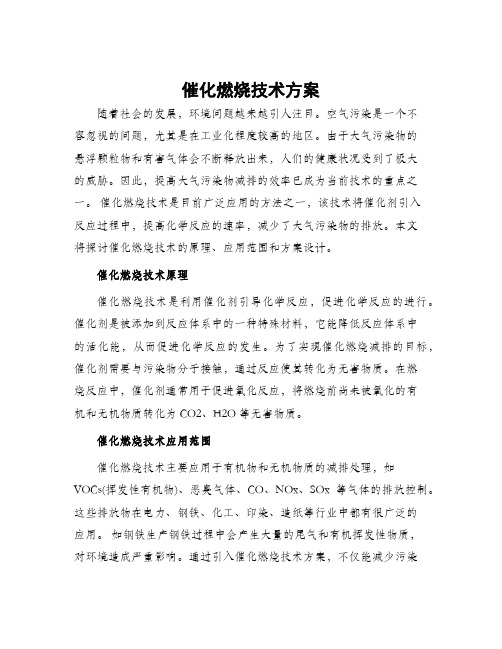
催化燃烧技术方案随着社会的发展,环境问题越来越引人注目。
空气污染是一个不容忽视的问题,尤其是在工业化程度较高的地区。
由于大气污染物的悬浮颗粒物和有害气体会不断释放出来,人们的健康状况受到了极大的威胁。
因此,提高大气污染物减排的效率已成为当前技术的重点之一。
催化燃烧技术是目前广泛应用的方法之一,该技术将催化剂引入反应过程中,提高化学反应的速率,减少了大气污染物的排放。
本文将探讨催化燃烧技术的原理、应用范围和方案设计。
催化燃烧技术原理催化燃烧技术是利用催化剂引导化学反应,促进化学反应的进行。
催化剂是被添加到反应体系中的一种特殊材料,它能降低反应体系中的活化能,从而促进化学反应的发生。
为了实现催化燃烧减排的目标,催化剂需要与污染物分子接触,通过反应使其转化为无害物质。
在燃烧反应中,催化剂通常用于促进氧化反应,将燃烧前尚未被氧化的有机和无机物质转化为CO2、H2O等无害物质。
催化燃烧技术应用范围催化燃烧技术主要应用于有机物和无机物质的减排处理,如VOCs(挥发性有机物)、恶臭气体、CO、NOx、SOx等气体的排放控制。
这些排放物在电力、钢铁、化工、印染、造纸等行业中都有很广泛的应用。
如钢铁生产钢铁过程中会产生大量的尾气和有机挥发性物质,对环境造成严重影响。
通过引入催化燃烧技术方案,不仅能减少污染物的排放,还能在降低企业环境污染的同时提高生产效率,使其满足这些行业高度环保的要求。
催化燃烧技术方案设计催化燃烧技术方案设计需要涉及到催化剂的选择和处理,反应器的设计以及气体净化等方面。
催化剂的选择不仅需要考虑其催化效率和稳定性,同时也需要考虑到其耐腐蚀性和可再生性等方面。
反应器的设计需要结合实际情况进行,包括反应器形状、大小、反应条件和温度控制等。
除此之外,为了保证催化燃烧的效率还需要将反应器和吸附塔,液体过滤器等其他设备组合起来,净化排放的气体。
在整个方案设计中需要充分考虑不同物质的特性和反应机理,在此基础上进行优化和精细化设计。
催化燃烧技术介绍

催化燃烧技术介绍催化燃烧技术是一种能够提高燃烧效率和减少污染物排放的技术。
催化燃烧是指在燃烧过程中加入催化剂,通过催化剂的作用,使得燃烧反应更加完全和高效。
催化燃烧技术在工业生产和环境保护中有着广泛的应用。
催化燃烧技术的基本原理是利用催化剂的特殊性质,降低燃烧的活化能,从而提高燃烧的速率和效率。
催化剂通常采用金属或金属氧化物制成,具有较高的表面积和较好的催化活性。
当燃料与空气经过催化剂时,催化剂表面的活性位点能够吸附燃料分子,使其发生反应。
催化剂提供了一个更有利的反应路径,使得燃料分子更容易发生氧化反应,并释放出更多的热能。
催化燃烧技术在燃烧工程中有着广泛的应用。
首先,催化燃烧可以提高燃烧效率。
在常规燃烧过程中,燃烧反应需要较高的温度才能发生,因此部分燃料无法完全燃烧,导致燃烧效率低下。
而催化剂的加入可以降低燃烧的活化能,使得燃料分子更容易与氧气发生反应,从而提高燃烧效率。
其次,催化燃烧可以减少污染物排放。
在常规燃烧过程中,燃烧产生的氮氧化物和一氧化碳等有害物质会对环境和人体健康造成影响。
而催化燃烧可以使燃料分子更充分地氧化,减少有害物质的生成。
催化燃烧技术在工业生产中有着重要的应用。
例如,在化工厂中,催化燃烧可以用于石油和天然气的燃烧过程,提高燃烧效率和产品质量。
在电力行业中,催化燃烧可以用于燃煤锅炉和燃气轮机的燃烧过程,降低污染物排放,保护环境。
此外,催化燃烧技术还可以应用于废气处理和汽车尾气净化等领域,减少有害物质的排放,改善空气质量。
催化燃烧技术的发展受到催化剂性能和催化反应机理的限制。
催化剂的选择和设计对催化燃烧的效果有着重要的影响。
目前,研究人员正在努力开发新型高效催化剂,提高催化燃烧的效率和稳定性。
此外,催化反应机理的研究也是催化燃烧技术发展的关键。
通过深入理解催化反应的机理,可以指导催化剂的设计和制备,提高催化燃烧的效果。
催化燃烧技术是一种能够提高燃烧效率和减少污染物排放的重要技术。
催化燃烧方法概况
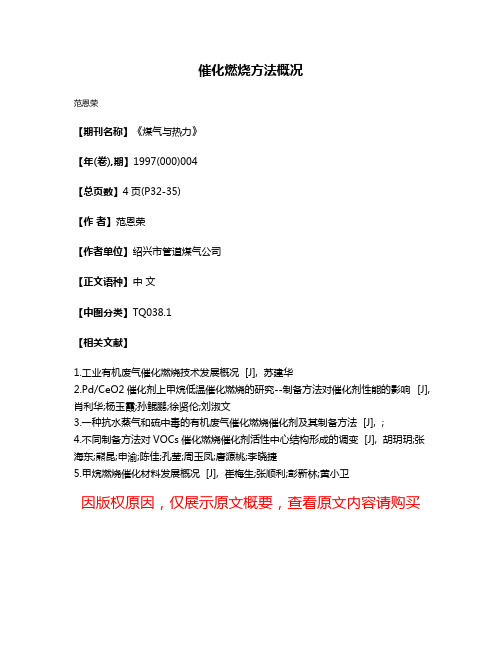
催化燃烧方法概况
范恩荣
【期刊名称】《煤气与热力》
【年(卷),期】1997(000)004
【总页数】4页(P32-35)
【作者】范恩荣
【作者单位】绍兴市管道煤气公司
【正文语种】中文
【中图分类】TQ038.1
【相关文献】
1.工业有机废气催化燃烧技术发展概况 [J], 苏建华
2.Pd/CeO2催化剂上甲烷低温催化燃烧的研究--制备方法对催化剂性能的影响 [J], 肖利华;杨玉霞;孙鲲鹏;徐贤伦;刘淑文
3.一种抗水蒸气和硫中毒的有机废气催化燃烧催化剂及其制备方法 [J], ;
4.不同制备方法对VOCs催化燃烧催化剂活性中心结构形成的调变 [J], 胡玥玥;张海东;熊昆;申渝;陈佳;孔莹;周玉凤;唐源桃;李晓捷
5.甲烷燃烧催化材料发展概况 [J], 崔梅生;张顺利;彭新林;黄小卫
因版权原因,仅展示原文概要,查看原文内容请购买。
催化燃烧法在废气中的应用分析

催化燃烧法在废气中的应用分析摘要:如今,生态环保的观念日益深入人心,建造资源节约型,环境友好型社会成了人们脱口而出的口头语。
虽然环保理念深入人心,但真正实施起来并不是那么容易,国家政府也是不断做了很多尝试。
其中催化燃烧法就是一个重要的方式,也是目前国内在废气处理方面较为成熟和先进的一种技术。
催化燃烧法主要用环保的手段处理废气,减少环境污染。
本文主要从催化燃烧法的概念,催化燃烧法的优势,催化燃烧法在工业中的应用,这三个方面进行分析,探索催化燃烧法的应用。
关键词:催化燃烧法;废气;应用随着社会的不断进步,生产生活的速度不断加快,然而废气的排放量也是不断增多。
日益增多的废气,不仅污染了环境,更是影响了人们的健康。
如何合理有效的处理废气问题,便成了当前人类社会面临的重大问题。
为了更好的做好废气的处理,便有了催化燃烧法的应用。
本文将重点对催化燃烧法这一技术进行分析研究,探索其在处理废气中所具有的优势特点,并且重点以工业中的废气为例,分析催化燃烧法在处理工业废气中的应用。
一、催化燃烧法的概念催化燃烧法,简称RCO,是一种净化废气的方法,顾名思义,就是利用催化剂,促进可燃物质的完全燃烧,它其中主要运用的是化学原理,是在催化剂的作用下,使废气里面的可燃物质在催化剂的作用下氧化分解,将VOC在200~400℃的低温条件下分解为CO2和H2O,从而达到净化废气的作用。
另外,催化燃烧是在较低温度下进行的,通过催化剂使废气中的可燃物质在较低温度下氧化分解,是净化有机废气、消除恶臭的有效手段之一。
催化燃烧法主要适用于喷涂、化工塑料、油墨印刷、制鞋粘胶、漆包线等生产产生的含有可燃物质如芳烃,含氧有机物及一氧化碳等有害物质的废气净化。
在催化燃烧法的应用中,对于催化剂的选择和使用也是有一定的要求的。
催化剂必须具有很高的活性,特别是低温活性好,从而提高催化燃料的化学转化率;催化剂还必须具有良好的热稳定性,耐高温,催化剂需要适应一定范围内的温度变化;催化剂还必须具有高强度和长寿命的特点。
第四部分 催化燃烧

图1-4显示,燃烧反应处于表面反应动力学控制与传质控制(第
Ⅰ阶段与第Ⅲ阶段)的反应热交换情况。在气体热容恒定且作绝热
近似的情形下,从催化剂表面到气相的散热速率与温度的函数是一 组平行线,其在温度轴上的截距为气体的进料温度:反应热的产生
速率与催化反应速率成正比关系,与反应温度(催化剂表面温度)服
从 Arrhenius关系,即图中的”S”型曲线。进料温度上升至Tgasi
Stabilized Thermal Combustion(CST))的方式来解决此问题。
在CST燃烧器的设计思想中,表面反应被看作自由基和热量的
稳定发生源,为均相反应提供足够的活化能量和链反应载体,即
由多相催化反应”点燃”均相反应.燃烧器的实际反应进程如 图:
在反应器前端,经过预热的起燃/空气混合器通过催化剂
空燃比增大或燃烧室温度的波动会引起燃烧链反应载体的
大量减少,催化剂的表面反应速率在高温区并不受上述效应的 干扰,因此可以作为自由基的稳定发生源,保证气相反应的稳 定进行。 在以含铅汽油为主要燃料的时期,催化剂中毒的现象影响 了催化促燃方式的推广,无铅汽油的广泛应用使得此障碍现已 基本消除。在各种气体燃料的燃烧场合,如电厂、燃气锅炉等, 传统燃烧方式有低效、高排放的特点,经催化燃烧方式改造后 的燃烧器,各种大气污染物的排放水平得到明显降低,热效率 也因高空燃比技术的引进而得到明显改善。
而且混合进料方式也减小了自由基促发NOx的产生机会,在
对几种典型催化燃烧器模型的排放测试中,NOx的浓度一般在
10ppm以下,远低于各种排放限制标准。对于燃料中N组分的氧 化反应所产生的NO,催化剂的作用虽然能够加速NO被还原的速
率,但在目前尝试的所有催化剂体系上,O2 的还原反应总是优
催化燃烧方案
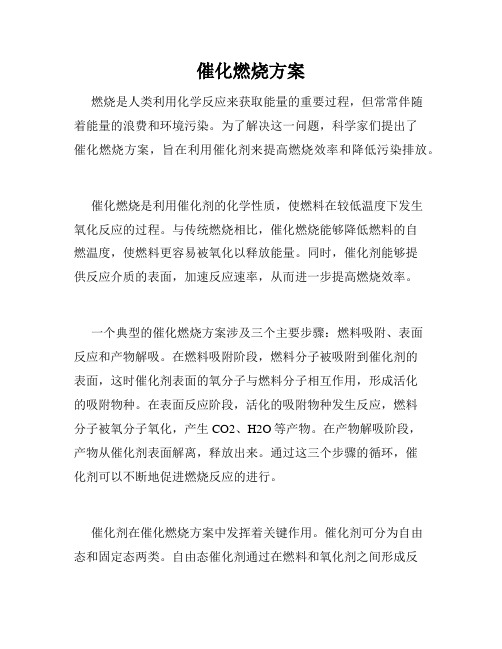
催化燃烧方案燃烧是人类利用化学反应来获取能量的重要过程,但常常伴随着能量的浪费和环境污染。
为了解决这一问题,科学家们提出了催化燃烧方案,旨在利用催化剂来提高燃烧效率和降低污染排放。
催化燃烧是利用催化剂的化学性质,使燃料在较低温度下发生氧化反应的过程。
与传统燃烧相比,催化燃烧能够降低燃料的自燃温度,使燃料更容易被氧化以释放能量。
同时,催化剂能够提供反应介质的表面,加速反应速率,从而进一步提高燃烧效率。
一个典型的催化燃烧方案涉及三个主要步骤:燃料吸附、表面反应和产物解吸。
在燃料吸附阶段,燃料分子被吸附到催化剂的表面,这时催化剂表面的氧分子与燃料分子相互作用,形成活化的吸附物种。
在表面反应阶段,活化的吸附物种发生反应,燃料分子被氧分子氧化,产生CO2、H2O等产物。
在产物解吸阶段,产物从催化剂表面解离,释放出来。
通过这三个步骤的循环,催化剂可以不断地促进燃烧反应的进行。
催化剂在催化燃烧方案中发挥着关键作用。
催化剂可分为自由态和固定态两类。
自由态催化剂通过在燃料和氧化剂之间形成反应中间体来促进燃烧反应的进行。
固定态催化剂则是被固定在反应器内部,使燃料和氧化剂在催化剂上接触,从而实现催化燃烧。
在催化燃烧方案中,常用的催化剂材料包括金属、氧化物、非金属化合物等。
金属催化剂如铂、铑、钯等常用于催化燃烧反应,具有高的催化活性和选择性。
氧化物催化剂如二氧化钛、三氧化二铁等对气相燃料的催化燃烧效果较好。
非金属化合物如硅胶、氧化铝等在工业催化燃烧中也得到了广泛应用。
然而,催化燃烧方案仍然面临一些挑战。
首先,催化燃烧过程需要精确控制催化剂的使用量和催化反应的条件,以保证催化剂的寿命和反应效率。
其次,催化剂的制备和催化反应的机理研究是催化燃烧领域亟待解决的问题。
最后,催化燃烧技术在工业应用中仍需克服成本和操作难题,以实现大规模生产和应用。
为了克服这些挑战,科学家们正在开展一系列的研究工作。
例如,他们正在研究新型催化剂材料,如金属-有机骨架材料、纳米结构材料等,以提高催化剂的活性和稳定性。
VOC 催化燃烧

VOCs 催化燃烧之五兆芳芳创作借助催化剂可使有机废气在较低的起燃温度条件下,产生无焰燃烧,并氧化分化为CO:和H:0,同时放出大量热1)起燃温度低,反响速率快,节省能源.催化燃烧进程中,催化剂起到下降VOCs 份子与氧份子反响的活化能,改动反响途径的作用.2)处理效率高,二次污染物和温室气体排放量少.采取催化燃烧处理VOCs 废气的净化率通常在95%以上,终产品主要为CO2 和H2O.由于催化燃烧温度低,大量削减NOx的生成[35].帮助燃料消耗排放的CO2 量在总CO2 排放量中占很大比例,帮助能源消耗量削减,显然削减了温室气体CO2 排放量.3)适用规模广,催化燃烧几近可以处理所有的烃类有机废气及恶臭气体,适合处理的VOCs 浓度规模广.对于低浓度、大流量、多组分而无收受接管价值的VOCs 废气,采取催化燃烧法处理是最经济公道的.表1催化燃烧与热力燃烧的比较产业上的催化剂都是由活性成分、助剂和载体等组成,其中活性组分及其散布、颗粒大小、催化剂载体对催化效果和寿命有很大的影响.用于催化燃烧VOCs的催化剂的活性成分可分为贵金属、非贵金属氧化物.贵金属是低温催化燃烧最经常使用的催化剂,其优点是具有较高的活性、良好的抗硫性,缺点是活性组分容易挥发和烧结,容易引起氯中毒、价钱昂贵,资源短缺;贵金属催化剂Pt、Pd、Ru等贵金属对烃类及其衍生物的氧化都具有很高的催化活性,且使用寿命长、适用规模广、易于收受接管,因而是最经常使用的废气燃烧催化剂.如我国最早采取的Pt—AI:0,催化剂就属于此类催化剂.但由于其资源稀少、价钱昂贵、耐中毒性差,因此,人们一直在努力寻找替代品,尽量削减其用量.非贵金属氧化物催化剂主要有钙钛矿型、尖晶石型以及复合氧化物催化剂等,价钱相对较低,也表示出很好的催化性能,如钙钛矿型催化剂低温热稳定性较好,尖晶石型催化剂具有优良的低温活性,但其缺乏之处在于催化活性相对较低,起燃温度较高.复氧化物催化剂一般认为,复氧化物之间由于存在结构或电子增刊谭明侠等:VOC催化燃烧技巧385调变等相互作用,活性比相应的单一氧化物要高.主要有以下两大类:(1)钙钛矿型复氧化物.稀土与过渡金属氧化物在一定条件下可以形成具有天然钙钛矿型的复合氧化物,通式为ABO,,其活性明显优于相应的单一氧化物.A为四面体型结构,B为八面体形结构;A和B形成瓜代立体结构,易于取代而产生晶格缺陷,即催化活性中心位,概略晶格氧提供高活性的氧化中心,从而实现深度氧化反响.罕有的有BaCuO:、LaMn03等;(2)尖晶石型复氧化物.作为复氧化物重要的一种结构类型,以AB2X4暗示,尖晶石亦具有优良的深度氧化催化活性.如对CO的催化燃烧起燃点落在低温区(约80℃),对烃类亦在低温区可实现完全氧化.其中研究最为活泼的CuMn:O.尖晶石,对芳烃的活性尤为出色.如使C,H.完全燃烧只需260℃,实现低温催化燃烧,这点具有特别实际意义.过渡金属氢化物催化剂作为取代贵金属催化剂,采取氧化性较强的过渡金属氧化物,对CH.等烃类和CO亦具有较高的活性,同时下降了催化剂的成本,罕有的有MnOx、CoOx和CuOx等催化剂.大连理工大学研制的含MnO:催化剂,在一定条件下能消除CH,OH蒸气,对C:H.O、C3H60、C6H.蒸气的清除也很有效果.催化剂载体以及负载方法载体VOC净化催化剂的载体主要有两类:一类是球状或片状;是整体式多孔蜂窝状.金属载体催化剂的优点是导热性能好、机械强度高,缺点是比概略积较小.颗粒状载体的优点是比概略积大,缺点是压降大以及因载体间相互摩擦,造成活性组分磨耗费失.蜂窝陶瓷载体是比较理想的载体型式,它具有很高的比概略,压力降较片粒柱状低,机械强度大,耐磨、耐热冲击.负载方法催化剂活性组分可通过下列方法沉积在载体上:(1)电沉积在环抱纠缠或压制的金属载体上;(2)沉积在颗粒状陶瓷资料上;(3)沉积在蜂窝结构的陶瓷资料上.催化剂失活失活催化剂在使用进程中随着时间的延长,活性会逐渐下降,直至失活.催化剂失活主要有3种类型:(1)催化剂完全失活.使催化剂失活的毒物包含快速和慢速作用毒物两大类.快速作用毒物主要有P、As等,慢速作用毒物有Pb、zn等.通常情况下,催化剂失活是由于毒物与活性组分化合或熔成合金.对于快速作用毒物来说,即便只有微量,也能使催化剂迅速失活;(2)抑制催化反响.卤素和硫的化合物易与活性中心结合,但这种结合是比较松弛、可逆且暂时性的.当废气中的这类物质被去除后,催化剂活性可以恢复;(3)沉积笼盖活性中心.不饱和化合物的存在导致碳沉积,此外陶瓷粉尘、铁氧化合物及其他颗粒物堵塞活性中心,从而影响催化剂的吸附与解吸能力,导致催化剂活性下降一j.预防措施预防催化剂活性衰减,可以采纳下列相应的措施:(1)依照操纵规程,正确控制反响条件;(2)当催化剂概略结炭时,通过吹人新鲜空气,提高燃烧温度,烧去概略结炭;(3)将废气进行预处理,以除去毒物,避免催化剂中毒;(4)改良催化剂的制备工艺,提高催化剂的耐热性和抗毒能力.催化燃烧工艺流程按照废气预热方法及富集方法,催化燃烧工艺流程可分为3种.(1)预热式.预热式是催化燃烧的最根本流程形式.有机废气温度在100℃以下,浓度也较低,热量不克不及自给,因此在进入反响器前需要在预热室加热升温.燃烧净化后气体在热互换器内与未处理废气进行热互换,以收受接管部分热量.该工艺通常采取煤气或电加热升温至催化反响所需的起燃温度.(2)自身热平衡式.当有机废气排出时温度高于起燃温度(在300℃左右)且有机物含量较高,热互换器收受接管部分净化气体所产生的热量,在正常操纵下能够维持热平衡,无需弥补热量,通常只需要在催化燃烧反响器中设置电加热器供起燃时使用.(3)吸附一催化燃烧.当有机废气的流量大、浓度低、温度低,采取催化燃烧需耗大量燃料时,可先采取吸附手段将有机废气吸附于吸附剂上进行浓缩,然后通过热空气吹扫,使有机废气脱附成为高浓度有机废气(可浓缩lO倍以上),再进行催化燃烧.此时,不需要弥补热源,就可维持正常运行引.对于有机废气催化燃烧工艺的选择主要取决于:(1)燃烧进程的放热量,即废气中可燃物的种类和浓度;(2)起燃温度,即有机组分的性质及催化剂活性;(3)热收受接管率等.当收受接管热量超出预热所需热量时,可实现自身热平衡运转,无需外界弥补热源,这是最经济的.化燃烧的应用5.1溶剂类污染物的净化处理主要污染物是三苯(苯、甲苯和二甲苯)、酮类、醇类及其它一些含氧衍生物等.詹建锋¨纠采取吸附—催化燃烧法治理彩印厂三苯废气,治理前废气浓度为1 320 mg·m一,治理后浓度小于50 mg·m一,达到地方尺度DB35/15693.刘忠生等¨4 J对主要含烃类污染物的石化污水处理场隔油池散发的废气进行处理,采取蜂窝状Pt、Pd和Ce多组分TC792H催化剂,对进口总烃体积分数1 000~6 000pL·L.1进行催化燃烧,可以使总烃去除率达97%以上,净化排气总烃体积分数小于100 IxL·L~,无恶臭气味.5.2含N有机污染物的净化含N有机污染物(如RNH2、RCONH:等),大都具有毒性和臭味,必须进行处理.火箭推进剂(CH.):NNH:是一种易溶于水和有机溶剂、具有强极性和弱碱性的有机化合物,也是一种剧毒物质.采取催化燃烧法处理火箭推进剂(CH,):NNH:(含量1%,压力0.25 MPa,气量500 m3·h.),当催化燃烧温度高于300℃,(CH,):NNH:废气去除率达99%以上,取得很好的处理效果[151.5.3对含硫有机污染物的净化制药厂、农药厂和化纤厂等在生产中会排出来CH.SH、CH,CH2SH和Cs:等有机硫污染物,对这类污染物的催化氧化,其中的s原子一般氧化成SO:或SO,,在催化剂概略上易产生强吸附,造成催化剂中毒失活.新开发的RS一1型催化剂能使反响进程生成的SO:和sO,几近100%地释放出来,使连续运行时的活性保持稳定.6结语催化燃烧技巧涉及化工、情况工程、催化反响和自动检测控制等领域,在我国仍处于成长阶段.今后的成长标的目的为:(1)提高催化剂性能.研制具有抗毒能力、大空速、比概略积)大及低起燃点的非贵金属催化剂,以下降造价和使用用度;(2)催化燃烧装置向大型化、整体型和节能型标的目的成长.。
- 1、下载文档前请自行甄别文档内容的完整性,平台不提供额外的编辑、内容补充、找答案等附加服务。
- 2、"仅部分预览"的文档,不可在线预览部分如存在完整性等问题,可反馈申请退款(可完整预览的文档不适用该条件!)。
- 3、如文档侵犯您的权益,请联系客服反馈,我们会尽快为您处理(人工客服工作时间:9:00-18:30)。
催化燃烧方法概况范恩荣(绍兴市管道煤气公司,绍兴312000)1引言燃料的燃烧很早就被人类所掌握。
但是传统的火焰燃烧存在一系列缺点,它往往达不到燃料完全燃烧的程度,从而导致在燃烧过程中,除碳氢化合物和碳被氧化成二氧化碳和水的放热反应外,还在高温下(超过1500K)的火焰中发生辅助反应,这辅助反应使部分热量损失掉,并产生有毒化合物NO x,CO及致癌的碳氢化合物。
其反应表示如下:CO-RH+O2火焰T>1500KCO2+H2O+QN2+O2NO#NO2(空气中氮)(高温NOx)RNH+O2NO X(燃料氮)(燃料NO X)从当前来讲,对于废气去毒,需要大量的投资费用和和具有一定困难。
而采用催化燃烧对于改善燃烧过程,促进完全燃烧,降低形成有毒物质的辅助反应是最有效的途径。
众所周知:催化有可能控制化学过程,它能降低反应温度,加速必要的反应,使辅助有害的或不必要的反应降低到最低限度。
对于燃烧采用催化过程,主要是促使燃料,即碳和碳氢化合物完全氧化成CO2和H2O,最大限度地放出热量,抑制产生有毒物质(NO x和CO)及致癌物质的辅助反应。
2催化燃烧和催化剂的研究催化燃烧是从发现铂丝对甲烷燃烧催化作用,而引起人们的兴趣。
实际上铂细粉对所有碳氢化合物、乙醇和氢的无焰燃烧均有催化作用。
催化燃烧第一个实际应用是用于安全矿灯和催化引燃器(点火器)。
以后把催化燃烧的研制工作注意力集中于日常生活和功率不大的低温热源如:采暖设备、发动机加热器、房间取暖用辐射加热器和壁炉。
这些设备主要是轻便、安全,能降低燃烧中有毒物质的产生。
近几年由于生态保护局势和能源日趋紧张,对催化燃烧引起更大的兴趣。
在各方面展开了一系列工作,包括基础理论的研究,开发新的催化剂和载体,建立新的燃烧过程和设备,扩大催化燃烧应用范围,尤其是在工业生产上的应用。
燃料的催化燃烧和火焰燃烧有本质不同,对于催化燃烧,有机物质氧化发生在固体催化剂表面,同时产生CO2和H2O,它不形成火焰,氧化反应温度低,大大抑制空气中的N2形成高温NO x。
而且催化剂的选择性催化作用,有可能限制燃料中含氮化合物(RNH)的氧化过程,使其多数形成分子氮(N2)。
催化燃烧反应如下:RH+O2催化剂T=700~1000KCO2+H2O+Q2 (燃料)N2+O2NO X(空气中N2)RNH+O2K1N2+CO2+H2O(燃料中含氮化合物)RNH+O2K2N2+CO2+H2O催化燃烧可以分为四类燃烧状况(见图1)。
在低温状况下燃烧,受多相氧化反应的制约,这是动力学控制燃烧状况。
在比较高的温度状况下燃烧,无论是反应动力学,或是在催化剂气孔上燃料-空气扩散速度都对催化燃烧速度有影响,这种燃烧属内部扩散控制,在进一步提高温度状况下燃烧,催化燃烧速度变化很小,这种燃烧状况的反应速度取决于燃料-空气混合物向催化剂表面的扩散速度。
在高温状况下燃烧,发现在催化剂表面,氧化反应受激励,均相燃烧占优势,使燃烧速度剧烈地增加。
在第一种燃烧状况,主要是利用低温催化燃烧,使有毒的有机化合物燃烧掉。
大多数催化加热器和取暖器及小功率的炉子都在第二燃烧和第三燃烧状况下工作。
对于火箱空间温度超过1200K 的高热负载大功率加热设备,都在第四种燃烧状况下工作,这种燃烧状况称之为催化助燃。
图1 催化燃烧反应速度与温度的关系1-动力学控制;2-过渡扩散控制;3-扩散控制;4-在催化剂表面激烈产生均相燃烧事实上催化燃烧是燃料在接近化学计量情况下进行氧化反应,并放出大量热量,所以催化剂的首要条件,必须在高温氧化反应情况下具有高的活性,此外还需有高的热稳定性、高的机械强度以及对燃料中所含毒素有高的耐腐蚀性。
研究表明:用铂、钯、最活泼的氧化物和元素周期表IV 类过渡元素氧化物,可以作为催化剂活性组份,而且复合氧化物、尖晶石型和钙钛矿型化合物比单质要好。
催化剂载体采用氧化铝和铝硅酸盐基础上的多孔细颗粒和纤维材料。
对于高热负载加热装置,最好用具有低的流体阻力的块状蜂窝状催化剂载体。
对于制备块状蜂窝状载体所采用材料与使用温度有关,可以采用氧化铝和氧化硅的混合物、锆陶瓷、碳化硅、氮化硅、莹青石和莫来石。
在某些情况下,块状陶瓷载体的机械强度和热稳定性达不到要求,可以采用高强度、高热稳定性和高耐腐蚀性的金属载体,但是金属载体仅能在1300~1400K 范围内使用。
对于催化载体承载板,采用具有添加剂变性氧化铝陶瓷,变性添加剂可以采用ZrO 2、CeO 、CS 2O 、T hO 2。
3 催化燃烧装置的研究及其应用首先,研究带固定催化层装置的加热器(燃烧器)。
固定催化层采用多孔式纤维状的催化剂,在催化层温度为900~1000K,热量向周围介质的传递是以辐射和对流型式进行。
这类催化加热器(燃烧器)中NO 2和CO 2等有毒物质浓度不超过环保要求。
这类加热器(燃烧器)燃料和空气分别输入,并且功率不大。
在国外它主要用于日常生活中,如住宅采暖。
用于汽车客仓、轮船客仓及仓库的催化取暖器(加热器),属于燃料-空气预混合的催化燃烧装置。
在俄罗斯科学院催化研究所研制成TEPMOKAT -1型,T EPM OKAT -2型,TEPMOKAT -3型预混合的燃料-空气加热器,这类加热器功率为2.5~ 3.0kW 。
对于TEPMOKAT -1型它采用添加有少量铂的过渡金属氧化物作为催化剂,催化剂涂在铝硅酸盐的纤维型载体上。
TEPMOKAT -2型、TEPMOKAT -3型加热器采用多孔金属氧化物陶瓷板作为催化剂。
T EPM OKAT -1型、TEPMOKAT -2型采用丙烷-丁烷混合物作燃料。
而TEPM OKAT -3型采用天然气作燃料。
这几类加热器不仅热效率很高(几乎达到100%),而且可以使燃料在燃烧过程中完全变成CO 2+H 2O 。
燃料燃烧程度达到99%以上,完全达到卫生标准和环境要求。
所以它很适宜作为采暖装置,用于各个方面。
上述催化燃烧加热器已投入工业性生产。
在燃气轮机的燃烧室,用催化燃烧强化燃烧过程是非常有前途的,它不仅可以提高燃气轮机效率,降低燃料消耗,而且没有必要再向燃气轮机的轮叶用冷空气冲淡烟气,同时也排除了为减少高温NO x 逸出物必须的喷水。
燃气轮机采用催化燃烧与火焰燃烧比较,CO 的逸出物减少10倍,而高温NO x 逸出物减少100倍。
但是在燃气轮机催化燃烧时,对于降低从燃料中结合的氮,所形成的燃料NO x 量的问题仍然没有解决。
据资料介绍:要使燃气轮机燃烧含氮燃料,使燃料NO x 明显减少,只有采用二段燃烧才能达到。
在二段燃烧过程中,首先建立燃料过剩区,结果在该区大多数燃料氮还原成分子氮。
在第二区使还设有燃烧的燃料进行催化燃烧。
但是二段燃烧容易产生焦炭沉积在催化剂上,使催化剂活性降低和使废气中CO 含量增加。
对于获得热量或工艺用蒸汽的锅炉,采用催化燃烧,同样能达到节能和改善环境的目的。
对于火管锅炉可以采用专门的燃烧器,这类燃烧器用高热稳定性纤维材料制成多孔园筒形结构,气态(或液态)燃料同空气混合物通过园筒体的进口到内腔,由于多孔园筒型上涂有催化剂,使燃料进行催化燃烧,从而使锅炉热效率提高,废气中CO 和NO x 等有害物质降低。
该催化燃烧器位置装在锅炉原来装燃烧器的位置,所以采用催化剂燃烧不用对锅炉进行改造。
目前国外研制成这类催化燃烧器功率为300kW,它可以用于各类火管锅炉。
对于水管锅炉的催化燃烧器,是采用碳化硅管子,在碳化硅管子外表面涂有催化剂,碳化硅管子排列在锅炉燃烧室内,碳化硅管内装置有通水热交换管。
燃料在管子表面进行催化燃烧,放出热能,通过管子之间的空间,以热辐射和对流加热热交换管内的水。
在俄罗斯科学院催化研究所研制成了使燃料完全燃烧的蜂窝状陶瓷催化剂,这类陶瓷催化剂是过渡金属氧化物,具有高的活性和机械强度。
这种蜂窝状陶瓷催化剂已在空气加热器中获得应用,这种空气加热器是燃烧天然气的两段加热装置(见图2)。
在第一室实现天然气火焰燃烧,然后被一次空气冲淡的燃烧气进入第二室,在第二室装有催化箱,催化箱是直径500mm,厚度为50~150mm 园盘,它由六边形块状蜂窝结构的陶瓷催化剂组合而成。
在催化箱上炉气温度为700~1100K,使不完全燃烧的炉气和氧化碳被完全氧化(燃烧),并使NO x 被炉气还原成N 2。
以后完全燃烧气体被二次空气冲淡,从而加热房间和其它需加热的介质。
这种空气加热器已用于加热暖室、工业贮罐、饲养场以及用氧化碳增加温室植物的营养和对蔬菜贮藏库建立保护气氛,作为工业干燥器和加热介质。
这种空气加热器热有效利用率达99%。
图2 催化空气加热器燃烧原理图催化燃烧技术用于动力工业,解决生态洁净的问题的优越性是毫无疑问的,目前它所采用的也是固定层的蜂窝状块状催化剂,是用锆陶瓷、碳化硅、堇青石、莫来石、特种合金和铁素体钢制成,但是催化燃烧技术在动力工业中,尚停留在实验室和工业试验阶段。
采用铂系列金属作为催化活性组份,涂在蜂窝结构或者螺旋形的块上会导致催化燃烧投资提高,并且煤或重油加氢作用获得的燃料不能采用铂系列催化剂,因对它有毒害作用。
所以研制新的有效催化剂和载体结构,是能否更广泛应用催化燃烧的决定性条件。
在俄罗斯科学院催化研究所研制成催化燃烧热发生器中采用似液层的催化层,这种似液催化层是颗粒状氧化物组成(见图3),在热发生器中,燃料在不高温度(800~1000K)下进行完全燃烧。
与固定催化层的热发生器比较,它的优点是在同一催化层的热发生器具有更强烈的放热效应,它可以强化各种需要热能的工业过程。
图3催化燃烧热发生器原理图已如任何沸腾层的反应器一样,似液层催化热发生器也是中空装置,在装置的下部有空气分配格子板。
在空气和燃料混合物上升运动时以及燃烧产物通过球形催化剂层时,似液层形成,热量有效地从热发生器输出,输送热的方式可以是似液层催化剂流经换热器或者从似液层催化剂直接输出热量。
具有一定尺寸的网格的水平格子板是这类催化热发生器的结构特性,这格子板起到不等温的分隔作用,沿着高度方向使装置分成两个等温区,下部为使燃料完全燃烧所必须的温度(800~1000K),上部使达到加热工作介质的温度(见图3)。
由于装置具有分隔不等温的格子板及装置上部热量向下输送,这有可能使废气温度降低到420~450K,这种热发生器可以采用未经净化的燃料(即燃料中含有硫、碱金属等成份),为此对催化剂提出了更高的要求,要求它能在最小空气过剩系数及温度在1000K左右,可以长时间使用(3000~4000小时以上),并仍保留高的活性,还要具有沸腾层工作条件下有高的抗机械磨损性(磨损率不大于0.005/天),在燃烧未净化的燃料和工业废渣时要有高的抗催化毒性。
热发生器采用过渡金属的铬酸盐或某些单质氧化物作为催化剂,这类催化剂涂在氧化铝颗粒上(即氧化铝颗粒为载体)。