立方储罐施工方案
立式罐的施工方案(3篇)
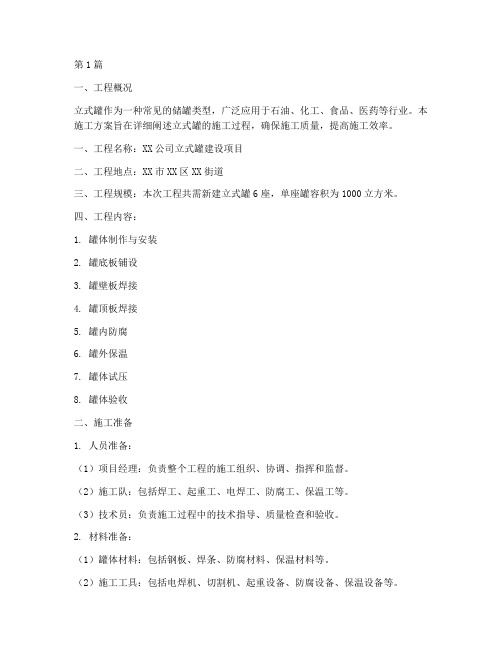
第1篇一、工程概况立式罐作为一种常见的储罐类型,广泛应用于石油、化工、食品、医药等行业。
本施工方案旨在详细阐述立式罐的施工过程,确保施工质量,提高施工效率。
一、工程名称:XX公司立式罐建设项目二、工程地点:XX市XX区XX街道三、工程规模:本次工程共需新建立式罐6座,单座罐容积为1000立方米。
四、工程内容:1. 罐体制作与安装2. 罐底板铺设3. 罐壁板焊接4. 罐顶板焊接5. 罐内防腐6. 罐外保温7. 罐体试压8. 罐体验收二、施工准备1. 人员准备:(1)项目经理:负责整个工程的施工组织、协调、指挥和监督。
(2)施工队:包括焊工、起重工、电焊工、防腐工、保温工等。
(3)技术员:负责施工过程中的技术指导、质量检查和验收。
2. 材料准备:(1)罐体材料:包括钢板、焊条、防腐材料、保温材料等。
(2)施工工具:包括电焊机、切割机、起重设备、防腐设备、保温设备等。
3. 设备准备:(1)焊接设备:电焊机、切割机等。
(2)起重设备:起重机、卷扬机等。
(3)防腐设备:喷砂机、喷漆机等。
(4)保温设备:发泡机、保温棉等。
4. 施工图纸及规范:(1)罐体设计图纸。
(2)施工规范及质量标准。
三、施工工艺流程1. 罐体制作与安装:(1)根据设计图纸,下料切割钢板。
(2)将切割好的钢板进行焊接,制作成罐体。
(3)将罐体运输至施工现场,进行安装。
2. 罐底板铺设:(1)对罐底板进行打磨、清洗。
(2)将罐底板铺设在罐体底部。
(3)对罐底板进行焊接固定。
3. 罐壁板焊接:(1)对罐壁板进行打磨、清洗。
(2)按照焊接顺序进行焊接。
(3)对焊接部位进行检查,确保焊接质量。
4. 罐顶板焊接:(1)对罐顶板进行打磨、清洗。
(2)按照焊接顺序进行焊接。
(3)对焊接部位进行检查,确保焊接质量。
5. 罐内防腐:(1)对罐内进行清洗、打磨。
(2)按照防腐工艺进行防腐处理。
6. 罐外保温:(1)对罐外进行清洗、打磨。
(2)按照保温工艺进行保温处理。
储罐基础施工方案 (3)精选全文完整版

可编辑修改精选全文完整版稳定轻烃储罐(400m³)基础施工方案一.概述1.1 工程概况本工程主要为轻烃储罐设备制作基础,基础为天然浅基础,结构为钢筋混凝土基础,施工范围约为700㎡,基础相对标高为EL.+0.000m(相当于85黄海高程+4.850m),基底相对标高均为EL.-2.200m,本项工程采用人工开挖,基坑周边按1:1.2放坡。
基坑底采用100mm厚C10素混凝土做垫层,其顶标高为EL.-2.100m,两边出基础边缘100mm,基础混凝土强度等级为C30,保护层厚50mm。
基础钢筋加工均在预制场地集中预制。
基础模板采用2.0cm厚建筑木模(胶合板),施工位置如图1所示。
1.2 主要工程量2.1 施工图甲方提供图纸(BN-DWG-TF-CS-2021 REV.0,BN-DWG-TF-CS-2022 REV.0)2.2 施工技术规范3.1技术准备:①图纸会审②对施工人员进行技术交底③了解施工现场的现状,排查地下隐蔽工程。
3.2物资准备:①施工用料准备②施工机具准备3.3 现场准备:三通一平①施工道路利用场区现有临时道路,如图2所示②施工用水利用场区现有的水源,采用水管引至施工现场③施工用电从场区现有的总配电箱接至现场各分配电④场地平整施工前拆除原有地砖(图1),平整场地3.4 平面布置见总平面布置图。
四.施工总体安排4.1 施工顺序拆除原有地砖----使用经纬仪定位、放线----验线-----土方开挖----地基验槽---- 基础垫层---二次放线、验线---预制钢筋----模板、钢筋安装---- 固定预埋件-----砼浇筑----拆模----基础验收回填----土方回填 ----二次浇注-----地面硬化养护-----交验4.2 施工进度计划本工程计划工期30天日历天400m³轻烃储罐施工位置图1 施工位置图2 现场路况五.主要工序施工方法5.1 拆除原有地砖组织施工人员将原有地砖拆除,地砖拆除后全部运送到业主指定位置,摆放整齐。
储罐施工方案范文
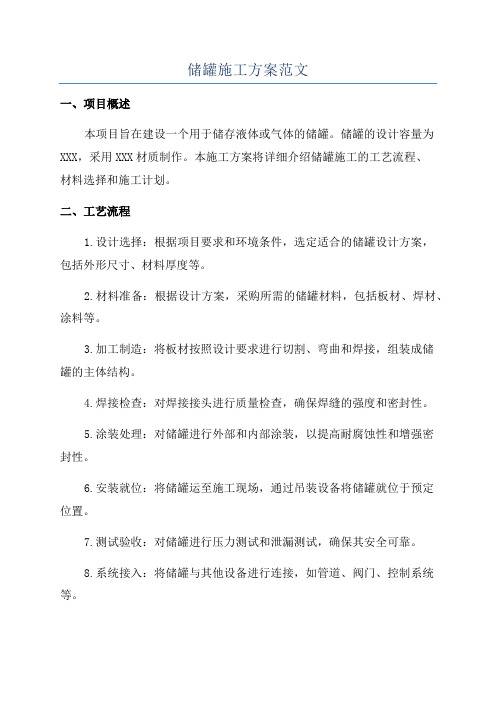
储罐施工方案范文一、项目概述本项目旨在建设一个用于储存液体或气体的储罐。
储罐的设计容量为XXX,采用XXX材质制作。
本施工方案将详细介绍储罐施工的工艺流程、材料选择和施工计划。
二、工艺流程1.设计选择:根据项目要求和环境条件,选定适合的储罐设计方案,包括外形尺寸、材料厚度等。
2.材料准备:根据设计方案,采购所需的储罐材料,包括板材、焊材、涂料等。
3.加工制造:将板材按照设计要求进行切割、弯曲和焊接,组装成储罐的主体结构。
4.焊接检查:对焊接接头进行质量检查,确保焊缝的强度和密封性。
5.涂装处理:对储罐进行外部和内部涂装,以提高耐腐蚀性和增强密封性。
6.安装就位:将储罐运至施工现场,通过吊装设备将储罐就位于预定位置。
7.测试验收:对储罐进行压力测试和泄漏测试,确保其安全可靠。
8.系统接入:将储罐与其他设备进行连接,如管道、阀门、控制系统等。
9.维护保养:储罐投入使用后,定期进行检查和保养,确保其长期稳定运行。
三、材料选择1.储罐板材:选择具有良好耐腐蚀性和机械强度的材料,如碳钢板、不锈钢板等。
2.焊材:选择符合储罐使用环境要求的焊接材料,如焊条、焊丝等。
3.涂料:选择具有良好抗腐蚀性、耐高温性和耐候性的涂料,如环氧涂料、聚氨酯涂料等。
4.辅助材料:如密封胶、垫片等,选择符合使用要求的高温耐腐蚀材料。
四、施工计划1.设计准备阶段:确定储罐设计方案,编制施工图纸,准备所需材料和设备。
2.加工制造阶段:按照工艺流程进行材料加工和制造,保证质量和尺寸准确。
3.涂装处理阶段:对储罐进行涂装处理,采用适当的涂料和涂装工艺。
4.运输安装阶段:运输储罐到施工现场,通过吊装设备将储罐安装就位。
5.系统接入阶段:将储罐与其他设备进行连接,进行测试验收。
6.维护保养阶段:储罐投入运行后,定期进行检查和保养,确保其正常运行。
五、安全措施1.施工现场设立临时围挡,确保安全。
施工人员必须佩戴安全帽、安全鞋和其他必需的个人防护用品。
1万立方米储罐安装工程施工方案
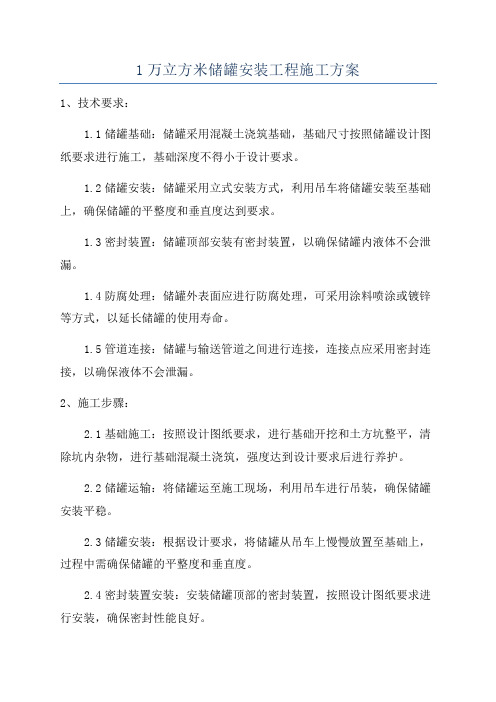
1万立方米储罐安装工程施工方案1、技术要求:1.1储罐基础:储罐采用混凝土浇筑基础,基础尺寸按照储罐设计图纸要求进行施工,基础深度不得小于设计要求。
1.2储罐安装:储罐采用立式安装方式,利用吊车将储罐安装至基础上,确保储罐的平整度和垂直度达到要求。
1.3密封装置:储罐顶部安装有密封装置,以确保储罐内液体不会泄漏。
1.4防腐处理:储罐外表面应进行防腐处理,可采用涂料喷涂或镀锌等方式,以延长储罐的使用寿命。
1.5管道连接:储罐与输送管道之间进行连接,连接点应采用密封连接,以确保液体不会泄漏。
2、施工步骤:2.1基础施工:按照设计图纸要求,进行基础开挖和土方坑整平,清除坑内杂物,进行基础混凝土浇筑,强度达到设计要求后进行养护。
2.2储罐运输:将储罐运至施工现场,利用吊车进行吊装,确保储罐安装平稳。
2.3储罐安装:根据设计要求,将储罐从吊车上慢慢放置至基础上,过程中需确保储罐的平整度和垂直度。
2.4密封装置安装:安装储罐顶部的密封装置,按照设计图纸要求进行安装,确保密封性能良好。
2.5防腐处理:对储罐外表面进行防腐处理,可采用涂料喷涂或镀锌等方式进行,确保储罐的耐腐蚀性能。
2.6管道连接:将输送管道与储罐进行连接,连接点采用密封连接,确保液体不会泄漏。
2.7测试与调试:对储罐进行压力测试和泄漏测试,确保储罐的功能正常,并进行必要的调试。
3、安全措施:3.1施工现场应设立安全警示标语,并设置安全隔离区域,禁止未经授权人员进入施工区域。
3.2施工人员应佩戴安全帽、防护眼镜、口罩等必要的个人防护用品,并遵守相关安全操作规程。
3.3施工现场应配备灭火器材,确保灭火设备的有效性。
3.4工作人员应进行安全培训,了解施工过程中的各项安全措施和应急处理方法。
3.5施工前,需检查设备的安全性能,确保施工过程中没有安全隐患。
3.6施工现场应进行定期巡视和检查,及时处理施工中出现的安全问题,并采取有效的纠正措施。
以上是关于1万立方米储罐安装工程施工方案的简要概括,具体施工方案应根据实际情况进行详细设计和制定。
罐体施工方案(3篇)
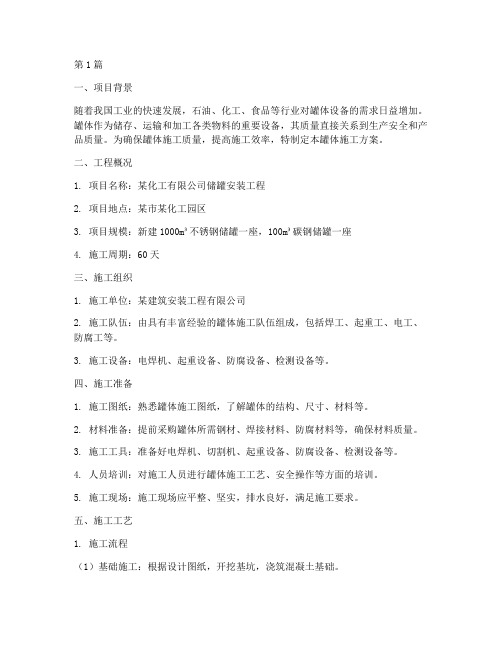
第1篇一、项目背景随着我国工业的快速发展,石油、化工、食品等行业对罐体设备的需求日益增加。
罐体作为储存、运输和加工各类物料的重要设备,其质量直接关系到生产安全和产品质量。
为确保罐体施工质量,提高施工效率,特制定本罐体施工方案。
二、工程概况1. 项目名称:某化工有限公司储罐安装工程2. 项目地点:某市某化工园区3. 项目规模:新建1000m³不锈钢储罐一座,100m³碳钢储罐一座4. 施工周期:60天三、施工组织1. 施工单位:某建筑安装工程有限公司2. 施工队伍:由具有丰富经验的罐体施工队伍组成,包括焊工、起重工、电工、防腐工等。
3. 施工设备:电焊机、起重设备、防腐设备、检测设备等。
四、施工准备1. 施工图纸:熟悉罐体施工图纸,了解罐体的结构、尺寸、材料等。
2. 材料准备:提前采购罐体所需钢材、焊接材料、防腐材料等,确保材料质量。
3. 施工工具:准备好电焊机、切割机、起重设备、防腐设备、检测设备等。
4. 人员培训:对施工人员进行罐体施工工艺、安全操作等方面的培训。
5. 施工现场:施工现场应平整、坚实,排水良好,满足施工要求。
五、施工工艺1. 施工流程(1)基础施工:根据设计图纸,开挖基坑,浇筑混凝土基础。
(2)罐体组装:按照设计要求,将罐体钢板分片组装成罐体。
(3)焊接:采用自动焊接或半自动焊接,确保焊接质量。
(4)无损检测:对焊接部位进行无损检测,确保焊接质量。
(5)防腐处理:对罐体进行防腐处理,提高罐体的使用寿命。
(6)罐体安装:将罐体安装到基础上,调整罐体位置。
(7)试压:对罐体进行试压,确保罐体密封性。
(8)验收:对罐体进行验收,确保施工质量。
2. 施工要点(1)基础施工:严格按照设计图纸进行基础施工,确保基础坚实、平整。
(2)罐体组装:按照罐体施工图纸,将罐体钢板分片组装成罐体,确保组装精度。
(3)焊接:采用自动焊接或半自动焊接,严格控制焊接电流、电压等参数,确保焊接质量。
储罐施工方案范文

储罐施工方案范文一、项目背景近年来,随着工业化的发展,各类储罐在工业生产、油气储存等领域的需求日益增长。
储罐施工是确保储罐安全运行的关键环节,正确的施工方案能够保证储罐的质量和使用寿命。
本方案旨在提供一种有效、安全的储罐施工方案。
二、施工方案1.工程准备(1)选址根据储罐的具体用途和容量要求,选择合适的场地建设储罐。
(2)土建准备进行场地平整、基础施工等土方工作,确保储罐基础稳固可靠。
(3)材料准备购买储罐施工所需材料,包括钢板、焊条、焊机等。
2.储罐制作(1)切割与焊接按照储罐设计图纸,将所需的钢板裁剪成所需形状,并进行相关的焊接工作。
(2)材料处理对焊接完成的储罐进行防腐处理,如喷涂防锈涂料等。
(3)设备安装根据储罐设计要求,安装液位计、温度计等设备。
3.储罐安装(1)提升装卸使用起重设备将储罐运输至预定位置,并进行定位、放平等工作。
(2)焊接连接根据储罐设计要求,采用焊接方式将储罐与管道、阀门等设备连接起来。
4.施工质量控制(1)质量检验对储罐的焊缝、密封性等进行质量检验,以保证施工质量符合相关标准和要求。
(2)安全考虑施工过程中要注意安全措施,确保储罐及周围区域的安全。
5.施工总结(1)验收与交付按照储罐设计要求,进行验收与交付手续。
(2)记录与总结对施工过程中的关键节点进行记录和总结,为今后施工提供参考。
三、安全措施1.施工场地安全(1)采取隔离措施,确保施工场地周围人员不受威胁。
(2)合理设置施工区域,避免与其他设施相互干扰。
2.认真执行操作规程(1)施工人员必须熟知储罐施工操作规程,并严格按照规程操作。
(2)做好施工人员的培训工作,确保施工人员具备必要的技能和知识。
3.避免火源和静电(1)在施工区域内禁止吸烟,严禁使用明火。
(2)在储罐施工过程中,严格控制静电产生和积累的可能性。
4.安全防护设施(1)施工现场应设置警示标识,明确安全区域和危险区域。
(2)施工人员应佩戴个人防护用品,如安全帽、安全鞋等。
立方米液氨储罐施工方案
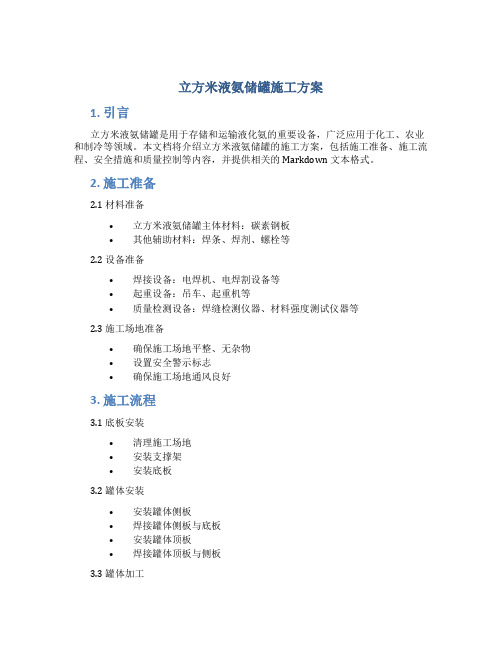
立方米液氨储罐施工方案1. 引言立方米液氨储罐是用于存储和运输液化氨的重要设备,广泛应用于化工、农业和制冷等领域。
本文档将介绍立方米液氨储罐的施工方案,包括施工准备、施工流程、安全措施和质量控制等内容,并提供相关的 Markdown 文本格式。
2. 施工准备2.1 材料准备•立方米液氨储罐主体材料:碳素钢板•其他辅助材料:焊条、焊剂、螺栓等2.2 设备准备•焊接设备:电焊机、电焊割设备等•起重设备:吊车、起重机等•质量检测设备:焊缝检测仪器、材料强度测试仪器等2.3 施工场地准备•确保施工场地平整、无杂物•设置安全警示标志•确保施工场地通风良好3. 施工流程3.1 底板安装•清理施工场地•安装支撑架•安装底板3.2 罐体安装•安装罐体侧板•焊接罐体侧板与底板•安装罐体顶板•焊接罐体顶板与侧板3.3 罐体加工•焊接加固筋•安装进出料口、排气阀等附件•焊接进出料口、排气阀等附件3.4 焊接工艺•根据焊接规范施工•进行焊接前的预热处理•使用正确的电流和电压进行焊接•焊接后进行冷却处理3.5 焊缝检测•使用焊缝检测仪器对焊缝进行检测•检测焊缝的质量和强度4. 安全措施4.1 人员安全•施工人员必须穿戴防护装备,如安全帽、防护眼镜、防护手套等•施工人员必须经过专业培训,熟悉施工操作规范和安全操作流程•施工现场必须设置安全警示标志4.2 施工场地安全•施工场地必须保持干燥,防止液氨泄露•施工场地必须远离明火和易燃物品4.3 操作安全•施工人员必须熟悉液氨的性质,了解其安全操作规范•施工人员必须严格按照操作规范进行施工•确保焊接设备和起重设备的安全使用5. 质量控制5.1 材料质量控制•检查材料证书和相关质量文件•检查材料的表面质量和尺寸规格5.2 焊接质量控制•焊接前进行预热处理•使用正确的焊接参数进行焊接•检测焊缝质量和强度5.3 安全阀和压力表检测•安装和检测液氨储罐的安全阀和压力表•确保其正常工作并符合相关安全标准结论本文档介绍了立方米液氨储罐的施工方案,包括施工准备、施工流程、安全措施和质量控制等内容。
50000方储罐基础施工方案

50000方储罐基础施工方案1.储罐基础选址首先要选择一个地势平坦,无地下水位干扰的地方作为储罐基础选址。
地质条件必须满足设计要求,并且避免地震、洪水等天然灾害的影响。
2.清理工作选址完成后,进行清理工作。
包括清除土地上的杂草,移除地表的石块和树根,并且保持地表的平整。
3.地基处理进行地基处理是为了提高地基的稳定性和承载力。
可以采用加固地基的方法,如灌注桩或钢筋混凝土带梁地基等。
4.排水系统在储罐基础施工中,必须考虑到排水系统。
要确保地表和基础周围的排水情况,以防止地下水的浸润和积水对基础的影响。
5.编制施工图纸储罐基础的施工需要有详细的图纸来指导工作。
图纸应该包括基础结构的平面布置图,截面图,连接图,以及其他相关细节。
6.基础开挖开挖基础前,必须根据图纸进行测量和标定。
开挖基础应根据设计要求进行,将地表土壤,石块等全部清除。
7.基础制作根据施工图纸和设计要求,将混凝土按照比例拌和,并倒入基础模板,进行浇注。
在浇注过程中,需要不断进行均匀振捣,以确保混凝土内部完全均匀,无空隙。
8.基础维护储罐基础完成浇筑后,需要进行养护。
养护期间必须进行水养护,并在必要时覆盖防水膜,以保持混凝土的湿润性。
9.基础验收在基础养护期结束后,需要进行基础验收。
验收主要是检查基础的质量和尺寸是否符合设计要求,并测试基础的稳定性和承载力。
储罐基础施工方案的编制需要严格按照设计要求和施工规范进行。
施工过程中要保持现场的整洁和安全,严禁乱堆乱放。
同时,应配备专业人员进行施工和监督,确保施工质量和安全。
立式储罐施工方案

立式储罐施工方案立式储罐是一种常见的储存液态物质的设备,其施工方案如下:1.选址与准备1.1 根据储罐的容量和使用需求,选择适合的场地进行建设。
1.2 清理场地,确保周围环境平整,无建筑物和其他障碍物。
1.3 充分考虑地质条件、排水情况、地下水位等因素,确保选址安全合理。
2.设计与安装2.1 根据储罐的规格与容量,确定施工图纸以及相关设计参数。
2.2 确定储罐的结构形式,一般为立式圆柱形,并根据设计要求选择合适的材料。
2.3 确定储罐的尺寸、厚度等参数,并进行相关计算。
2.4 安装基础:按照设计要求,进行基础的开挖与浇筑作业,确保基础的稳固性。
2.5 安装罐体:按照设计图纸,在基础上进行罐体的组装,并进行密封处理,确保其完整性和安全性。
2.6 安装设备:根据需要,安装阀门、管道、液位计等设备,进行连接和封闭处理。
3.涂装与保护3.1 进行储罐的涂装,选择防腐、防锈、耐化学腐蚀等特殊材料,以保护储罐的表面。
3.2 进行防护措施,如加装防雷装置、防火措施等,确保储罐的安全性。
4.验收与检测4.1 对储罐进行内部和外部的验收,包括查看焊缝、涂层、密封性等情况。
4.2 进行相关的试压、试水、试验等检测工作,确保储罐的功能性和安全性。
4.3 整理施工记录,编制竣工图纸,并进行相关备案和验收手续。
5.竣工与运行5.1 完成施工并进行相关的整理与清理工作。
5.2 启动储罐并进行运行监测,确保其正常工作。
5.3 加强日常维护,定期检查储罐及其设备的状态,进行维护和修缮。
以上就是立式储罐施工方案的基本步骤,通过合理的设计和严格的施工,可以确保储罐的安全和可靠性,以满足不同行业的需求。
罐体施工方案范文

罐体施工方案范文一、施工背景及目标根据计划,本次施工的目标是建设一个容量为5000立方米的储罐。
储罐将被用于存储液体产品,并保证其安全和可靠性。
施工过程中的关注点包括质量控制、安全防范和工期控制。
二、施工前的准备工作1.组织施工团队:成立一个专业的施工团队,包括项目经理、施工技术人员和施工工人。
每个人都必须具备相关经验和技能。
2.技术准备:准备施工所需的设备和工具,包括吊装设备、焊接设备、钢材、焊条等。
3.材料采购:根据计划,及时采购所需的材料,确保施工进度不受材料不足的影响。
4.方案设计:根据设计要求,制定详细的施工方案和施工图纸,并获得相关审批。
三、施工工序1.场地准备:对施工现场进行平整和清理,确保施工区域安全和无障碍。
2.基础施工:进行基础的挖掘和灌注工作,包括土方开挖、坑口安全加固、地下排水系统建设等。
3.罐体组装:根据施工图纸,安装罐体的底板、壁板和顶板。
确保安装时的精度和水平度,并进行焊接、磨平和防腐处理。
4.附件安装:安装储罐的附件,如进出料口、排气阀、液位计、温度计等。
确保安装正确和紧固可靠。
5.内部涂层施工:根据设计要求,对罐体进行内部涂层施工,保护罐体不受腐蚀。
6.外部涂层施工:对罐体进行外部涂层施工,保护罐体不受日晒雨淋。
7.压力测试:对储罐进行压力测试,确保其密封性和承压性能。
8.安全防护:安装安全设施,包括防火系统、防爆系统、喷淋系统等,确保储罐的安全性。
9.验收和交付:进行最终的验收工作,确保储罐符合设计要求。
完成所有合同文件和报告的交接。
四、施工过程中的质量控制1.严格按照设计要求和施工图纸进行施工,确保罐体的尺寸和形状符合要求。
2.监控焊接工艺,确保焊缝质量和强度。
3.进行材料的质量检测,确保材料符合相关标准和规范。
4.进行涂层的质量检测,确保涂层的附着力和耐腐蚀性能。
5.定期进行施工现场的巡查和检查,确保施工质量和安全。
五、施工过程中的安全防范1.制定详细的施工安全计划和应急预案,确保施工过程安全可控。
储罐专项施工方案

一、工程概况本项目为一座容积为10000m3的储罐,用于储存化工原料。
储罐采用现场制作安装的方式,主要分为底板、壁板、顶板、附件等部分。
施工地点位于某化工园区,工程预计工期为3个月。
二、施工准备1. 施工现场准备:施工场地平整,施工用水、电、路畅通;土建基础施工完毕,基础经交接合格,具备施工条件;各类施工人员配备齐全,特种设备操作人员具备相应的资质;施工用各类机具落实到位,材料、半成品、成品、废品堆放场地明确;安全防护措施落实到位。
2. 施工技术准备:认真阅读各项施工技术文件,施工前组织工程技术人员审查图纸,熟悉图纸、设计资料及有关文件,并根据图纸要求和现场情况,编制可行的施工技术方案,并经各级主管部门审批合格。
施工前由非标制作技术人员对全体施工人员进行技术和安全交底。
三、施工方法1. 储罐预制(1)底板:底板采用现场焊接,焊接前对钢板进行打磨、清洗,确保钢板表面无油污、锈蚀等。
焊接过程中采用多层多道焊,保证焊缝质量。
(2)壁板:壁板采用现场卷板成型,成型后进行焊接。
焊接过程中采用多层多道焊,保证焊缝质量。
壁板焊接完成后,进行无损检测,确保焊缝质量。
(3)顶板:顶板采用现场焊接,焊接前对钢板进行打磨、清洗,确保钢板表面无油污、锈蚀等。
焊接过程中采用多层多道焊,保证焊缝质量。
2. 储罐组装(1)底板组装:将预制好的底板放置于基础之上,进行焊接。
焊接过程中采用多层多道焊,保证焊缝质量。
(2)壁板组装:将预制好的壁板逐一安装至底板上,进行焊接。
焊接过程中采用多层多道焊,保证焊缝质量。
(3)顶板组装:将预制好的顶板安装至壁板上,进行焊接。
焊接过程中采用多层多道焊,保证焊缝质量。
3. 储罐附件安装(1)人孔:将人孔安装至罐顶,进行焊接。
(2)透气帽:将透气帽安装至罐顶,进行焊接。
(3)接管:将接管安装至罐壁,进行焊接。
四、质量保证措施1. 人员控制:确保施工人员具备相应的资质,严格执行操作规程。
2. 机具设备控制:确保施工机具设备齐全、完好,定期进行检查和维护。
储罐施工组织方案

储罐施工组织方案一、项目介绍储罐是一种用于存放液体或气体的设备,广泛应用于石油、化工、食品、制药等行业。
本项目是对一个石油化工企业的储罐进行施工。
二、施工准备1.订购材料和设备:根据施工图纸和设计要求,订购所需的储罐材料和设备,如钢板、焊枪、涂料等。
2.环境准备:确保施工现场的环境符合安全要求,包括通风、电力、照明等设施的检查和修复。
3.建立施工组织机构:确定施工组织机构,包括项目经理、施工队长、安全员等,明确各自的职责,并进行人员培训。
三、施工流程1.开挖基础:根据施工图纸,确定开挖尺寸和深度,使用挖掘机进行开挖,并进行土方回填和压实。
2.基础处理:对开挖好的基础进行处理,包括清理杂物、打墩、铺砂浆等工作。
3.基础浇筑:根据设计要求,进行混凝土浇筑,包括搅拌混凝土、输送、浇注等步骤,保证储罐底部的坚固和平整。
4.储罐立筒:根据施工图纸,将钢板切割焊接成立筒,并进行内外的清洗和除锈处理,然后将立筒竖立在基础上,并严密连接。
5.罐顶安装:安装储罐的顶部构件,包括顶板、顶角、护栏等,确保安全和密封性。
6.管道安装:根据设计要求,在储罐上安装进出口管道、排污管道等,保证畅通和安全。
7.涂装和防腐:对储罐进行涂装和防腐处理,保护罐体免受外界环境的腐蚀和损伤。
8.环境清理:在施工完成后,进行施工现场的清理和整理,包括清理杂物、回填土方等。
9.竣工验收:进行储罐的竣工验收,包括验收材料、检查设备运行情况等,确保储罐的安全和符合要求。
四、施工安全1.施工现场要设置明显的警示标志,指示出禁止通行区域和危险区域,确保施工人员的安全。
2.储罐各个部位的施工要严格按照相关规范进行,确保施工质量和安全。
3.确保施工现场的通风良好,减少有害气体的积聚,防止中毒事故的发生。
4.施工人员要穿戴好安全防护装备,如头盔、安全鞋、手套等,保护自己的安全。
五、施工质量控制1.建立施工质量控制体系,包括编制施工规范和质量监督计划,明确各个工序的质量标准和控制点。
3000立方储罐施工方案

3000立方储罐施工方案一、工程概述根据客户需求,我们公司负责设计和施工一个3000立方的储罐。
该储罐用于存储液体产品,如石化产品、化工产品等。
下面将详细介绍工程的具体施工方案。
二、工程设计1.储罐选型:根据存储液体产品的性质和容量要求,我们推荐使用钢制储罐。
储罐选用优质的钢材制造,在保证安全性和耐久性的前提下,尽量减小储罐的体积和重量。
2.储罐结构设计:储罐采用圆筒形结构,上端采用锥形或球形顶部,底部采用圆弧形或锥形底部。
此结构设计有利于均匀分布液压力和减小应力集中,增强储罐的抗风压能力。
3.材料选择:储罐采用优质碳钢材料制造,材料经过严格筛选和测试,确保材料的可靠性和耐腐蚀性。
三、施工方案1.土建工程储罐基础:根据储罐容量和所在地的地质条件,采用钢筋混凝土基础。
基础设计合理,保证储罐的稳定性和安全性。
基础地基处理:对基础地基进行处理,确保地基的稳定性和承载能力。
地下管道:在储罐旁边敷设适当位置的地下管道,方便与其他设备进行联接。
2.储罐安装制造储罐:根据设计要求,制造储罐,并进行内外防腐处理。
储罐安装:使用吊车将制造好的储罐顶升到预定位置,确保储罐与基础之间有适当的间隙。
然后通过焊接、固定等方式将储罐安装牢固。
3.配套设备安装防火设施:安装储罐附近的防火设施,如消防水泵、消防栓等,保证储罐的安全性。
管道连接:将储罐与周围设备进行适当的管道连接,确保液体的流动。
仪表安装:安装液位仪表、压力表等仪表设备,实时监测和控制储罐的运行状态。
四、安全措施1.安全生产教育培训在施工前,对参与施工人员进行安全生产教育培训,加强他们对施工安全的认识。
2.安全操作规程制定详细的安全操作规程,指导施工人员在施工过程中的安全操作。
3.安全设备配备提供必要的安全装备,包括安全帽、安全绳、防护眼镜等,确保施工人员的人身安全。
4.安全监测安装安全监测设备,如烟雾报警器、温度监测仪等,及时发现异常情况并采取相应措施。
五、质量保证1.材料质量控制严格控制材料的质量,对每批材料进行检测,确保材料符合设计要求。
3000立方储罐工程施工设计方案

3000立方储罐工程施工设计方案一、项目概况本项目为3000立方储罐的施工设计方案,主要包括储罐设计和施工方案。
储罐用于储存液体原料,具有稳定的结构和优良的密封性能。
该方案旨在确保储罐的安全使用和可靠性。
二、储罐设计方案1.储罐选材:储罐采用了耐腐蚀性能较好的不锈钢材料,能够承受液体原料的腐蚀性,并具有较高的强度和耐久性。
2.储罐结构:储罐采用圆筒形结构,顶部设有进料口和排气口,底部设有排放阀门和检修口。
储罐的底部设有支撑脚,以确保储罐的稳定性和安全性。
3.储罐密封性能:储罐采用专业密封技术,确保储罐内液体原料的不泄露和外界空气的不进入。
三、施工方案1.施工前的准备:在施工前,需要进行现场勘测和测量工作,获取储罐的实际尺寸和地质情况。
同时,还需制定详细的施工计划,包括施工顺序、施工流程和施工时间安排。
2.基础施工:首先需要进行储罐基础的施工,包括地基挖掘、基础混凝土浇筑和支撑脚的安装。
在施工过程中,需要确保基础的平整度和强度。
3.储罐组装和安装:根据储罐的设计图纸进行组装和安装工作,包括储罐本体的组装、进料口和排气口的安装以及底部阀门和检修口的安装。
在组装和安装过程中,需要确保储罐的位置、角度和密封性。
4.现场测试:在储罐安装完成后,需要进行现场测试和调试工作,包括液体原料的注入和排放、进料口和排气口的打开和关闭以及密封性能的检验。
测试过程需要确保操作的准确性和测试结果的可靠性。
5.安全操作培训:在储罐安装和测试完成后,需要对使用人员进行安全操作培训,包括储罐的使用方法、维护保养以及应急处理措施等。
培训内容需要直接关系到储罐的安全使用和可靠性。
6.竣工验收:在施工完成后,需要进行竣工验收,由相关部门对储罐的设计和施工进行检验和评估。
只有通过竣工验收,储罐才能正式投入使用。
为确保施工方案的顺利实施,需严格按照相关的安全操作规范和标准进行工作,确保储罐的质量和可靠性。
同时,还需注重施工人员的专业技能培训和安全意识教育,提高工作效率和施工质量。
大罐基础施工专项方案
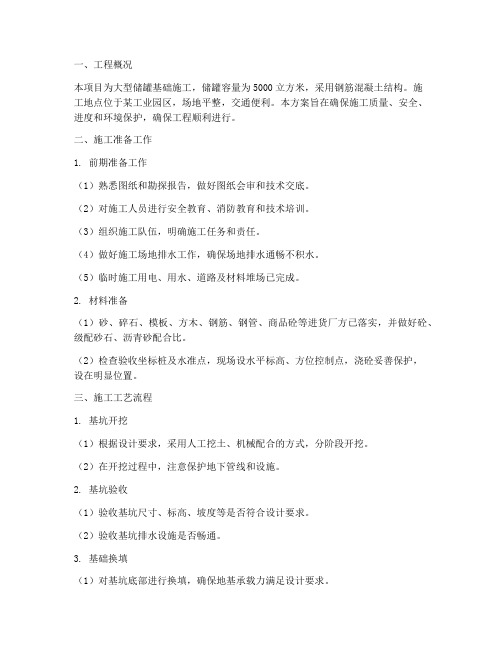
一、工程概况本项目为大型储罐基础施工,储罐容量为5000立方米,采用钢筋混凝土结构。
施工地点位于某工业园区,场地平整,交通便利。
本方案旨在确保施工质量、安全、进度和环境保护,确保工程顺利进行。
二、施工准备工作1. 前期准备工作(1)熟悉图纸和勘探报告,做好图纸会审和技术交底。
(2)对施工人员进行安全教育、消防教育和技术培训。
(3)组织施工队伍,明确施工任务和责任。
(4)做好施工场地排水工作,确保场地排水通畅不积水。
(5)临时施工用电、用水、道路及材料堆场已完成。
2. 材料准备(1)砂、碎石、模板、方木、钢筋、钢管、商品砼等进货厂方已落实,并做好砼、级配砂石、沥青砂配合比。
(2)检查验收坐标桩及水准点,现场设水平标高、方位控制点,浇砼妥善保护,设在明显位置。
三、施工工艺流程1. 基坑开挖(1)根据设计要求,采用人工挖土、机械配合的方式,分阶段开挖。
(2)在开挖过程中,注意保护地下管线和设施。
2. 基坑验收(1)验收基坑尺寸、标高、坡度等是否符合设计要求。
(2)验收基坑排水设施是否畅通。
3. 基础换填(1)对基坑底部进行换填,确保地基承载力满足设计要求。
(2)换填材料采用砂石混合料,按设计要求进行配合比。
4. 钢筋砼环墙施工(1)钢筋制作与绑扎:按设计要求制作钢筋,确保钢筋间距、保护层厚度等符合规范。
(2)模板支设:根据设计要求,采用合适的模板,确保模板的稳定性、刚度及密封性。
(3)混凝土浇筑:采用商品砼,确保混凝土质量,防止裂缝、蜂窝、麻面等质量缺陷。
5. 罐心施工(1)罐心结构层:按设计要求施工,确保结构层厚度、标高等符合要求。
(2)沥青砂绝缘层施工:按设计要求施工,确保沥青砂绝缘层的厚度、平整度等符合要求。
四、安全文明施工措施1. 施工现场设置安全警示标志,确保施工人员安全。
2. 严格执行施工现场消防安全管理制度,加强消防设施维护。
3. 做好施工现场环境保护工作,减少施工对环境的影响。
五、进度安排根据工程实际情况,制定合理的施工进度计划,确保工程按期完成。
立式储罐现场制作安装施工方案版
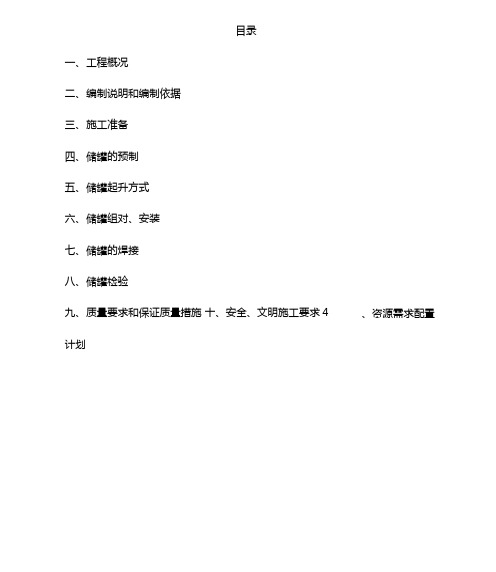
目录一、工程概况二、编制说明和编制依据三、施工准备四、储罐的预制五、储罐起升方式六、储罐组对、安装七、储罐的焊接八、储罐检验九、质量要求和保证质量措施十、安全、文明施工要求4、资源需求配置计划一、工程概况本工程是湖南海利化工股份有限公司在海利常德农药化工有限公司投资兴建杂环项目配套原材料和产品储藏的灌区子项工程,共有立式圆筒形钢制焊接储罐8台,其中100八2台,200八6台,制作安装总吨数约为10吨,其中不锈钢约6.7吨,储罐具体规格、材质如下二、编制说明和编制依据2.1编制说明由于本工程预制、组对、焊接工作量较大,且存在多出交叉作业,大大增加了本工程施工难度,为更好贯彻公司的质量方针,为建设单位提供满意的优质工程和服务,我公司将集中优势兵力,合理组织安排施工,坚持质量第一,严格控制过程,安全文明施工,确保按期完成,全力以赴争创优质工程,为达到上述目标,特编制本方案指导施工。
2.2编制依据1 )湖南海利工程咨询设计有限公司提供的设计图纸2)《立式圆筒形钢制焊接储罐施工及验收规范》GB50128- 20053)《立式圆筒形钢制焊接油罐设计规范》GB50341-20034)《石油化工立式圆筒型钢制贮罐施工工艺标准》SH3530-935)《现场设备、工业管道焊接施工及验收规范》GB50236?6)《钢制压力容器焊接规程》JB/T4709-20007)《焊接接头的基本形式与尺寸》GB985-888)《石油化工设备安装工程质量检验评定标准》SH3514-2001三、施工准备3.1施工现场准备3.1.1施工现场按照常德公司的要求进行布置,场地平整,施工用水、电、路畅通°3.1.2土建基础施工完毕,基础经交接合格,具备施工条件。
3.1.3各类施工人员配备齐全,特种设备操作人员具备相应的资质。
3.1.4施工用各类机具落实到位,并运现场至按规定位置就位。
3.1.5材料、半成品、成品、废品堆放场地明确。
3.1.6安全防护措施落实到位,消防设施准备齐全。
立方储罐制作与安装方案
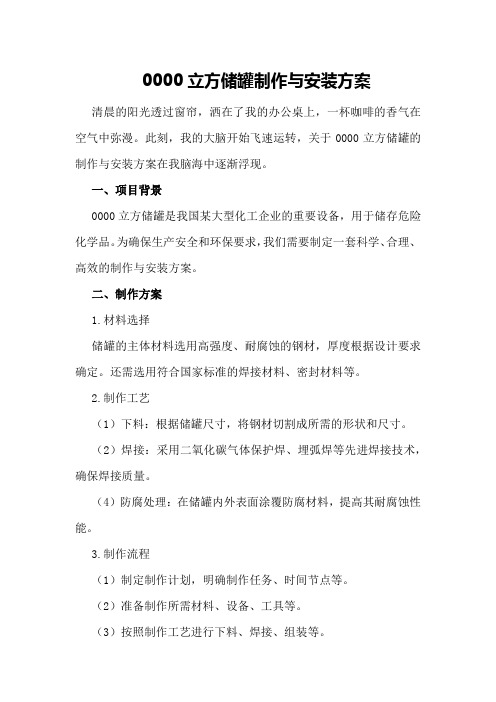
0000立方储罐制作与安装方案清晨的阳光透过窗帘,洒在了我的办公桌上,一杯咖啡的香气在空气中弥漫。
此刻,我的大脑开始飞速运转,关于0000立方储罐的制作与安装方案在我脑海中逐渐浮现。
一、项目背景0000立方储罐是我国某大型化工企业的重要设备,用于储存危险化学品。
为确保生产安全和环保要求,我们需要制定一套科学、合理、高效的制作与安装方案。
二、制作方案1.材料选择储罐的主体材料选用高强度、耐腐蚀的钢材,厚度根据设计要求确定。
还需选用符合国家标准的焊接材料、密封材料等。
2.制作工艺(1)下料:根据储罐尺寸,将钢材切割成所需的形状和尺寸。
(2)焊接:采用二氧化碳气体保护焊、埋弧焊等先进焊接技术,确保焊接质量。
(4)防腐处理:在储罐内外表面涂覆防腐材料,提高其耐腐蚀性能。
3.制作流程(1)制定制作计划,明确制作任务、时间节点等。
(2)准备制作所需材料、设备、工具等。
(3)按照制作工艺进行下料、焊接、组装等。
(4)进行防腐处理,确保储罐质量。
(5)验收合格后,交付使用。
三、安装方案1.安装准备(1)了解储罐的结构、尺寸、重量等参数,制定安装方案。
(2)准备安装所需设备、工具、吊具等。
(3)对安装人员进行技术培训,确保安装质量。
2.安装流程(1)将储罐运输至安装现场,卸车并摆放至指定位置。
(2)采用吊车将储罐吊装至基础上,调整储罐位置,使其与基础吻合。
(3)进行储罐与管道、阀门等设备的连接,确保连接牢固、密封。
(4)进行储罐的调试,检查储罐的密封性、稳定性等。
(5)验收合格后,交付使用。
四、质量保障1.严格遵循国家相关法律法规,确保制作与安装质量。
2.采用先进的生产设备和技术,提高制作与安装效率。
3.强化过程控制,对每个环节进行严格把关。
4.建立完善的售后服务体系,对储罐进行定期检查、维修。
0000立方储罐制作与安装方案旨在确保生产安全和环保要求,提高企业的经济效益。
通过科学、合理、高效的制作与安装,为企业创造价值。
M3储罐(正装)施工方案

§1000M 3储罐施工技术方案§4.10.1 概括1、本方案依据滁州瑞兴化工有限企业 3 万吨 / 年二硫化碳一期工程的二硫化碳成品储罐安装工程而编制,储罐安装工程的内容主要包含设施的组焊、安装及调试、试运转等工作。
2、一期为 2 个储罐,依据招标文件二期只增 1 台储储罐。
§4.10.2 设施技术特征储罐罐直径高度壁板圈数罐体质量主体材质<mm)<mm)<t )二硫化碳成品储罐12360112916Q235-A §4.10.3 本工程履行的施工查收规范、标准1.GB50128-2005立式圆筒形钢制焊接储罐施工及查收规范2.JB/T4735-1997钢制焊接常压容器3.JB/T4709-2000钢制压力容器焊接规程4.JB/T4730-2005承压设施无损检测5.GB50205-2001钢构造工程施工质量查收规范6.SH3046-92石油化工立式圆筒形钢制焊接储罐设计规范7.HG20583-1998钢制化工容器构造设计规定8. HG20584-1998钢制化工容器制造技术要求§4.10.4 安装施工方案1、施工方法:罐体安装采纳群桅葫芦边柱倒装法施工。
2、工作原理:群桅边柱倒装法利用均布在罐内侧边柱的手拉葫芦提高与壁板下部暂时胀紧的胀圈,使上节壁板随胀圈一同上涨到预约高度,组焊第二圈壁板,而后将胀圈松开,降至第二圈壁板下部胀紧,固定后再次起升,这样来去直至组焊完所有壁板。
3、施工程序:→顶板托架安装→顶板安装→提高装置安装→壁板自上而下逐圈顶升组装→底板角焊缝及缩短缝焊接并查验→罐体接收、构件安装→罐体充水实验→交工查收4、施工技术要求及举措A施工准备a储罐施工前,应组织相关人员熟习施工图和相关技术法例,并做好以下工作:经过图纸会审,明确与储罐施工相关的专业工程相互配合的要求。
依据出席的资料规格做好排板图的绘制。
对施工班组进行图纸技术交底工作。
9000立方储罐施工方案
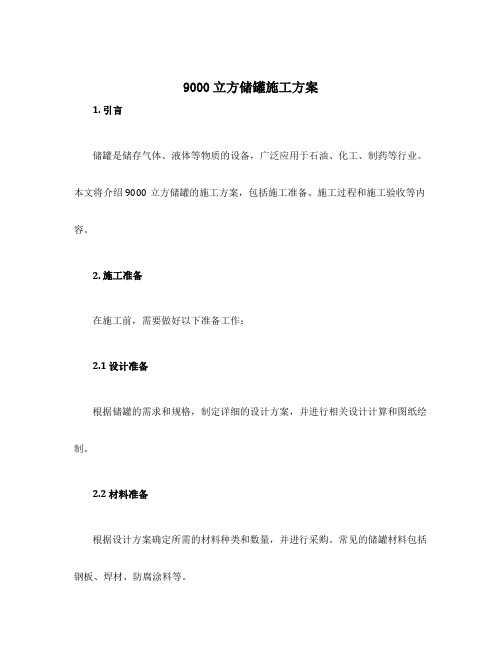
9000立方储罐施工方案1. 引言储罐是储存气体、液体等物质的设备,广泛应用于石油、化工、制药等行业。
本文将介绍9000立方储罐的施工方案,包括施工准备、施工过程和施工验收等内容。
2. 施工准备在施工前,需要做好以下准备工作:2.1 设计准备根据储罐的需求和规格,制定详细的设计方案,并进行相关设计计算和图纸绘制。
2.2 材料准备根据设计方案确定所需的材料种类和数量,并进行采购。
常见的储罐材料包括钢板、焊材、防腐涂料等。
2.3 施工人员准备组建具备相关经验和技能的施工队伍,确保施工人员具备相关证书和培训。
2.4 施工设备准备准备所需的施工设备,包括焊接设备、吊装设备、防护设备等。
3. 施工过程9000立方储罐的施工过程分为以下几个阶段:3.1 基础施工首先进行基础施工,包括地基开挖、浇筑混凝土基础等工作。
确保基础平整坚固,满足储罐的承重要求。
3.2 钢结构制作与安装根据设计方案制作钢结构,包括罐壁、罐顶、罐底等部分。
将制作好的钢结构进行吊装和安装。
3.3 焊接与检验对钢结构进行焊接,确保焊缝牢固。
同时进行相关的检验,如射线检测、超声波检测等,确保焊接质量符合要求。
3.4 防腐涂层施工钢结构焊接完成后,进行防腐涂层的施工。
选择适合的防腐涂料,并按照要求进行施工,确保储罐具有良好的防腐性能。
3.5 内外压力测试施工完成后,进行内外压力测试,检测储罐的密封性和承压能力。
确保储罐能够正常工作,并满足相关安全标准要求。
4. 施工验收施工完成后,进行施工验收。
验收内容包括:•检查储罐外观和结构是否符合设计要求;•检查焊缝质量和防腐涂层是否符合要求;•进行内部清洁和安全出口设置的检查。
如果验收通过,则可正式投入使用。
5. 安全措施在储罐施工过程中,必须严格遵守相关安全规定,包括:•确保施工人员佩戴防护装备,如安全帽、防护眼镜、防护服等;•严格按照焊接操作规程进行焊接,防止火灾和爆炸事故的发生;•施工现场要进行通风、防火等安全措施,确保施工安全。
- 1、下载文档前请自行甄别文档内容的完整性,平台不提供额外的编辑、内容补充、找答案等附加服务。
- 2、"仅部分预览"的文档,不可在线预览部分如存在完整性等问题,可反馈申请退款(可完整预览的文档不适用该条件!)。
- 3、如文档侵犯您的权益,请联系客服反馈,我们会尽快为您处理(人工客服工作时间:9:00-18:30)。
新增2台17m³立式储罐工程施工组织方案编制单位:漳州市贵安机械工业有限公司目录一、编制依据 (3)二、工程概况 (4)三、非标设备制作技术措施 (4)3.1选材下料 (4)3.2 筒体预制 (4)3.3 焊接工艺措施 (5)3.4 水压试验 (5)四、储罐基础施工技术措施 (6)4.1 施工准备 (6)4.2土方开挖 (6)4.3 操作工艺及操作技术要求 (7)4.4 罐基础回填土施工 (7)4.5 相关工种安全操作规程及注意事项 (7)4.6钢筋工程 (7)4.7 模板工程 (8)4.8 混凝土工程 (9)五、管道安装施工技术措施 (9)5.1 主要施工工序 (9)5.2 施工方法 (9)5.3 管道预制 (10)5.4 管道安装 (10)5.5 管道试验 (11)5.6 管道吹扫与清洗 (11)六、人力计划 (12)七、主要机具配置计划 (12)八、质量技术措施 (13)九、安全技术措施 (13)十、防护措施 (14)一、编制依据《钢制卧式容器》JB/T4731-2005《钢制焊接常压容器》NB/T47003.1-2009《固定式压力容器安全技术鉴察规程》TSG R0004-2009《钢制压力容器焊接规程》NB/T47015-2011《钢制化工容器制造技术要求》HG/T20584-2011《承压设备无损检测》JB/T4730-2005《输送流体用无缝钢管》GB/T8163-2008《钢制法兰、垫片、紧固件》HG/T20592-2009《容器支座》JB/T4712-2007《压力容器涂敷与运输包装》JB/T4711-2003《建筑地基处理技术规范》JGJ 79-2002《建筑地基基础工程施工质量验收规范》GB 50202-2002《石油化工钢储罐地基施工及验收规范》SH/T 3528-2005《混凝土泵送施工技术规程》JGJ/T 10-95《工业金属管道施工及验收规范》GB50235-97《现场设备、工业管道焊接工程施工及验收规范》GB50236-98 《石油化工剧毒、易燃、可燃介质管道施工及验收规范》SH501-85 《阀门检验与管理规程》SHJ518-91《管架标准图》HGJ524-91二、工程概况本项目位于厦门厦工桥箱有限公司厂内油罐仓库区,新增2台17m³立式储罐制造安装、储罐土建基础施工、管道配管及泵设备,仪表控制安装工程,该区域属于回填虚土且有明显下沉,旁边有埋地油池及开挖基坑旁有8米高防爆墙需提前做好防坍塌保护措施。
三、非标设备制作技术措施3.1选材下料3.1.1 对各种容器、非标设备,按设计蓝图经济合理安排排版图,落实板材的质证书、材质、厚度符合设计要求后,方可号料、划线。
检查板材表面不得有裂纹、起皮、严重锈蚀。
不平度不大于3mm, 点状锈蚀不超过0.3mm。
3.1.2 号料:板宽允许偏差±1mm,板长允许偏差±3mm,四角角度偏差值1mm,全长1.5mm,对角线偏差±5mm,采用自动、半自动手工均可。
3.1.3 切割:按图纸几何尺寸拼予留切口余量,切割成成品料,长度偏差±3mm,宽度偏差±1mm,板边不直度±2mm,不得有毛刺、氧化铁等异物。
切口应整齐。
3.1.4 坡口按设计要求或采用V型,具体如图1,除锈呈金属光泽。
3.1.5 拼接组对,拼接完板长允许偏差±2mm,板宽允许偏差±1mm,对角线偏差±5mm,对口错边量允许偏差≤2mm。
3.1.6 做好防变措施,每隔400~600mm处设置一块防变钢板,板厚δ=10~20mm。
并且点焊牢固。
施焊过程中经常检查,对开裂之处及时补焊,焊接完毕后拆除并磨平疤痕。
3.2 筒体预制3.2.1 筒节加工,先将板两端预弯边按设计圆弧滚圆,长度250~400mm左右,再进行筒体卷制,卷制不得一遍成型,避免出现卷制不匀,卷制前应用1~0.75mm铁皮制作内外圆弧样板,长度不得短于500 mm ,应在500~1500mm 左右,撑杆采用DN50~70的钢管,卷制成型对口不得凹陷或凸出, 凹陷深度不得大于2mm ,对口错边量不大于2mm ,对口间隙为2.5~4mm 左右,合适后临时点固,进行周长检查,并与封头周长对照,不得超过±2mm。
合格后,加强点固点,点固点必须与正式焊接一样,且应有持证焊工操作,将准备好的内径弧板按每500~1000mm 左右距离点牢在接口处,用撑杆临时支撑找圆撑杆两端直径偏差不得大于4mm ,椭圆度为±5mm。
按焊接工艺施焊,焊接后一次性调整校园。
3.2.2 筒体组对,严格按排版图,纵缝之间距离不得小于500 mm 。
筒体对口错边量不大于2mm ,对口间隙应均匀,组对完筒体直度偏差不得大于2 mm ,高度偏差±5 mm,筒体表面不得有凹凸不平,弧度应圆滑过渡,组对前坡口及两侧20~50mm 处应清理干净,呈金属光泽,点固点与正式焊接一样,需有证焊工操作。
组对合格后,每隔300mm 处加固点,每加固点长度为20~50 mm 。
按焊接工艺施焊。
3.2.3 筒节之间、筒节与封头组对时应自然对接,所有焊口不得强力对口。
3.2.4 筒体组对焊接完毕后,对纵,环焊缝按图纸设计要求进行无损检测。
3.2.5 筒体上接管附件的安装,严格按排版图定位划线,仔细对照图纸,反复核实,确认无误后方可开孔,接管与筒体、法兰与筒体垂直度水平度偏差为±1mm。
所有附件,接管接口焊缝应按要求施焊,焊脚高度控制在标准范围内。
3.2.6 附件下料制做,应按设计尺寸进行切割下料,并应清除毛刺、氧化铁,组合焊接应尺寸准确,防变形措施合理。
3.3 焊接工艺措施3.3.1 筒体纵、环焊缝采用筒内手工焊,筒外埋弧自动焊。
3.3.2 焊接完毕后,清理药皮,焊缝两侧的毛刺、飞溅等。
焊缝应圆滑过渡,焊缝具体如图2,局部咬边深度不大于0.5mm ,全长不大于10mm 。
3.3.3 所有的焊条、焊剂在焊接前,必须严格按焊接工艺进行烘焙,当天烘当天用,随用随拿,并应在保温筒内保温储存,严禁使用过期,药皮脱落,潮湿和三证不全,不合格的焊条。
3.4 水压试验3.4.1 水压试验前仔细检查所有密封处和连接部分是否可靠,所有管口是否全部安装焊接完毕,所有封口、接头不能有渗漏。
将设备的进口或出口旋转至最高点,并加装排气阀,以便充水时排出空气。
3.4.2 试验所使用的压力表精度不得低于1.5级,量程为试验压力1.5~2倍,表盘直径φ100~φ150为宜,表盘指针为0。
压力表为2块。
试压值应标注醒图 2目的红线,以便观察,压力表距观测点不宜过高或过低,约500~1500mm左右为宜,所有试验使用的压力表必须经过技监部门校验合格,方可使用。
3.4.3 水压试验应用清洁水,试验时建设单位的代表和施工项目负责人及技术负责人及监检单位应在现场监督。
3.4.4 水压试验步骤:当排气阀出水后,关闭阀门,初步检查有无漏水,然后用试压泵进水升压,并观察压力表的变化情况。
进水速度要均匀,同时不宜过快。
按设备壳程的工作压力的1.25倍进行试压,当压力达到设计压力时,进行稳压30分钟,并对容器进行一次全面检查,是否有渗漏现象,如有渗漏情况应泄压及时处理。
对泄漏点打磨后补焊,方可继续试验。
压力升至试验压力时,保压30分种,此时宏观检查无压力降,无渗漏。
严禁任何东西敲击容器。
降至设计压力,保压足够时间,再检查是否有渗漏,可用0.5磅小锤轻击焊口处检查。
如无渗漏,无压力降,无残余变形为合格,试验合格。
打开排气阀,防止造成负压,缓慢放水至无压力,用空压机将罐内的水份吹干。
设备水压试验时,严禁无关人员靠近设备。
做好试压的安全措施,以防意外事故发生。
3.4.5 水压试验合格后泄压注意事项当水压合格后,在排压时,一人站在出口侧面慢慢打开阀门,用临时排水管将出水排入地沟或回收罐内。
试验时非工作人不允许站在试验警戒线内。
水压试验完成后,将进、出口用盲板密封,以防杂物掉入设备内。
四、储罐基础施工技术措施4.1 施工准备施工前的技术交底要分级进行,由技术负责人将设计要求、施工方法、技术要求、质量标准、进度计划、安全措施、各分项工程施工的分工和配合、主要施工机具的安排和调配等,连同整个工程的施工计划,向施工机组的技术人员进行交底,并做好技术交底及记录;各施工机组技术负责人将本机组承担的工程任务及施工方法、劳动力组织、机具配备、安全措施等向本机组全体施工人员交底。
使参加施工的全体人员充分了解自己应尽的具体职责。
4.2土方开挖4.2.1 罐基础开挖前需用20#槽钢打桩,对防爆墙进行保护。
预防基坑开挖过程中坍塌危险。
4.2.2罐基础依据图纸设计标高开挖,罐地基范围内的表层土,腐殖土应全部挖除。
罐地基范围内不应有淤泥,淤泥质土及杂填土。
4.2.3施工流程:施工准备→测量放线→土方开挖→标高测量→槽底清理→验收4.3 操作工艺及操作技术要求4.3.1本工程基础坑槽边坡坡度(高:宽)为1:0.42,基地宽度安罐底尺寸每侧增加1.5米。
4.3.2基坑应分层开挖,在挖到距坑槽底200mm以内时应抄平。
清除土方,修整槽宽铲平槽底,如遇土质松软处,通知建设单位等进行验槽,以确定基础是否需要加深处理,基槽需加宽加深时,土方量根据现场实际各部位土质确定。
4.3.3开挖基槽采用单面抛土,弃土应距槽边1m以外,高度不宜超过1.5米。
弃土的坡度不大于45°,且弃土位置必须要便于材料的倒运及施工。
4.4 罐基础回填土施工4.4.1首先将开挖基槽的底层土外运,外取土质良好、密实度适中的土设计标高进行回填。
4.4.2施工流程:施工准备→测量分层高度→土方回填→标高测量→验收4.4.3 外运土用自卸式汽车运到场区外。
4.5 相关工种安全操作规程及注意事项4.5.1必须检查工具是否完好,如镐头和镐把、锹头和把是否坚固。
开挖人员应有足够的间距。
4.5.2挖掘土方应自上而下进行,不许采取掏空底脚的方法。
4.5.3在施工过程中,如遇到管线、电缆、等以及发现不能辩别的物品时,应立即停止工作,待弄清情况及采取措施后方可继续施工。
4.5.4在基础坑槽的边远缘及土壤的自然坡角范围内不得安设施工机械及通行运输机械,如经计算满足承载能力,方可安设或通行。
4.5.5所有人员不应在基坑内休息,要在合适的位置设置多处坡道,用于安全进出。
4.5.6所有机械设备必须专人统一协调、调动。
挖沟机旋转半径内严禁人员靠近。
4.6钢筋工程钢筋在内模安装好后开始绑扎。
根据设计要求,钢筋采用焊接接头,先将各段焊接好;绑扎好后焊接三个接头,采用电弧焊焊接成整体;电弧焊接头采用单面搭接焊,焊缝长260mm(12d)。