PFMEA案例
六步法pfmea案例

六步法pfmea案例全文共四篇示例,供读者参考第一篇示例:案例背景:某家汽车零部件制造公司在生产过程中发现了一个频繁出现的问题:某零部件的尺寸偏差过大,导致装配时无法完全契合,进而影响产品的性能和质量。
为了解决这一问题,公司决定使用六步法PFMEA 进行分析和改进。
步骤一:确定分析范围团队确定了分析的范围为某零部件的生产工艺。
他们明确了问题的具体表现,以及对产品性能和质量的影响。
团队还确定了分析的目的是为了找出可能引起零部件尺寸偏差的潜在故障模式,并制定相应的控制措施。
步骤二:收集相关信息团队开始收集相关信息,包括零部件的设计图纸、生产工艺流程、设备参数、材料性质等。
他们还对生产现场进行实地考察,观察生产过程中的关键环节,并与相关工程师和操作人员进行沟通交流,了解他们对问题的认识和看法。
步骤三:识别潜在故障模式通过分析收集到的信息,团队识别出了可能导致零部件尺寸偏差的潜在故障模式。
包括:材料供应质量不稳定、设备操作不规范、工艺参数设置不当等。
每个故障模式都被赋予一个风险等级,以确定其重要性和优先级。
步骤四:确定故障影响团队分析每个故障模式的影响范围,包括对产品性能、质量、交付时间等方面的影响。
他们还评估了每个故障模式的可能性和频率,以确定其潜在风险。
步骤五:制定改进控制措施基于对故障模式和影响的分析,团队制定了一系列改进控制措施,以降低潜在风险。
加强材料供应商管理、优化生产工艺流程、规范设备操作规程等。
每个控制措施都被赋予一个责任人和执行时间表,以确保实施和落实。
步骤六:跟踪和持续改进团队制定了一个跟踪和持续改进计划,以监控改进控制措施的执行情况和效果。
他们定期对实施情况进行评估和审查,继续识别和解决可能存在的风险和问题,确保质量和性能的持续提升。
通过六步法PFMEA的分析和改进,该汽车零部件制造公司成功解决了零部件尺寸偏差的问题,提高了产品的质量和性能,降低了生产过程中的风险和损失,进一步提升了企业的竞争力和市场地位。
PFMEA培训资料
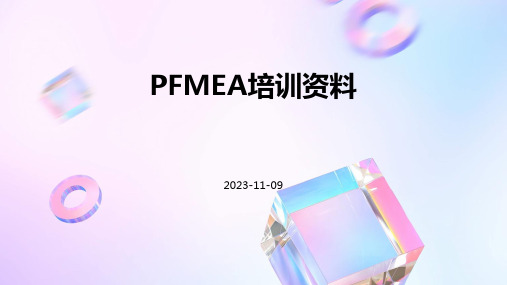
强化风险管理 随着人们对风险管理重视程度的 提高,PFMEA将在未来更加注重 对高风险失效模式的控制和管理 。
扩大应用范围 目前PFMEA主要应用于制造业, 未来可能会扩展到其他领域,如 服务业、医疗保健等。
提供一些实际的PFMEA分析报告案例,以便学员了解 PFMEA分析报告的编写方法和格式,为学员自己编写 PFMEA分析报告提供参考。
感谢您的观看
THANKS
通过服务PFMEA分析,可以识别和评估服 务过程中潜在的故障模式和风险,优化服务 流程,提高客户满意度。
详细描述
服务PFMEA分析是一种在服务设计和实施 阶段对服务过程进行详细分析的质量工具, 通过对服务流程的各个环节进行分析,识别 出潜在的故障模式和风险,评估其对服务过 程的影响程度,制定出有效的改进措施,优 化服务流程,提高客户满意度和忠诚度。
流程分析
总结词
对产品或过程的制造、装配、检测等流程进行详细分析是PFMEA的必要步骤。
详细描述
了解制造、装配、检测等流程中涉及的操作步骤和工艺要求,分析流程中可能出 现的问题和缺陷,以便在后续功能分析和风险分析中针对性地进行预防和改进。
功能分析
总结词
对产品或过程的功能进行分析,明确功能要求和性能指标是 PFMEA的关键步骤。
。
预防措施
预防措施是针对潜在故障模式采增 加防护装置、提高检测频率等。
在PFMEA中,预防措施通常是 在分析阶段确定的,需要综合考 虑设计、制造、使用等多个环节
的风险因素。
改进措施
改进措施是针对已经出现的故 障模式采取的措施,旨在消除 或降低故障的影响。
新版(七步法案例)PFMEA

头下R角偏小 一冲设计不合理 模具制作有偏差 冷墩时光钉直径偏大
5
增加抽风机或空调
2 检查/核对 2
6
要求供应商对模具尺寸进行 中限管理并提供出货检验报
告
3
目视/ 核对/检测
2
6
每隔两个小时对锁紧螺丝紧 固一次
3
检查
2
8
修理模具R角位置
3 检测 2
8
修改一冲相关尺寸
3 检测 2
6
要求供应商对模具尺寸进行 中限管理并提供出货检验报
05 热处理
硬度检测 (维式硬度计)
产品外观及硬度性能符合图纸 目视检测产品外观及仪器检测产品硬度性
要求
能符合图纸要求
电镀后表面发黑
产品从清洗区清除杂质后进入淬火炉进行
渗碳淬火(预热区860℃-60/+20℃,保温
产品表面硬度与芯部硬度需符 区900℃ ±10℃,淬火区 860℃ ±10
合图纸工艺要求:
完成状态
结合经验重新设计一冲模具
2020/3/10 8 2 1 ※ L
完成状态
严格要求模具厂商按我司图纸尺寸制作 2020/3/10 6 2 1
L
我司模具按图纸中限尺寸设计,并要求模具厂 完成状态 商对每批模具进行尺寸检验并提供检验报告到 2020/3/10 7 2 1 ※ L
我司核对
完成状态
要求牙板供应商严格按标准要求设计牙板并提 供检测数据报告
提供检测报告
对
高成
2020/3/10
要求牙板供应商严格按标准要求设计牙板
目视/核 对
董茂文
2020/3/10
将主模模腔尺寸定义在中限并要求供应商 目视/核
PFMEA-失效模式分析

02
失效模式分析
失效模式定义
失效模式定义
01
失效模式是指产品或过程中可能出现的不满足设计意图、技术
要求或操作规范的状或现象。
失效模式分类
02
根据失效的性质和影响程度,失效模式可以分为功能失效、性
能失效、安全失效、适应性失效等类型。
失效模式分析方法
03
失效模式分析方法包括故障树分析、事件树分析、故障模式与
制定改进措施和预防措施
01
根据分析结果,制定针对性的改进措施,以提高产品或过程的 性能、安全性和可靠性。
02
制定预防措施,降低失效模式的发生风险,包括设计优化、工
艺改进、环境控制和使用指导等。
跟踪改进措施和预防措施的实施效果,持续改进,确保产品质
03
量和过程稳定。
04
PFMEA案例分析
案例一:汽车刹车系统PFMEA分析
识别关键特性,确定分析的重点,确 保分析的准确性和有效性。
列出潜在的失效模式
通过头脑风暴、历史数据分析和经验总结等方法,列出可能的失效模式,确保覆盖全面。
对失效模式进行分类和整理,以便后续分析。
分析失效模式的后果
分析失效模式对产品或过程性能、安 全性、可靠性和符合性等方面的影响 。
评估失效模式对客户满意度和生产成 本的影响,以便制定有效的改进措施 。
主观性
在评估失效模式的严重程度、发生频率和检测难度时,可能存在 主观性,导致结果的不一致。
静态性
PFMEA通常在产品开发阶段进行,而后期的更改和改进可能未 被考虑。
PFMEA未来发展方向
人工智能与机器学习应用
利用人工智能和机器学习技术辅助PFMEA分析,提高识别失效模式 的准确性和效率。
PFMEA分析范例
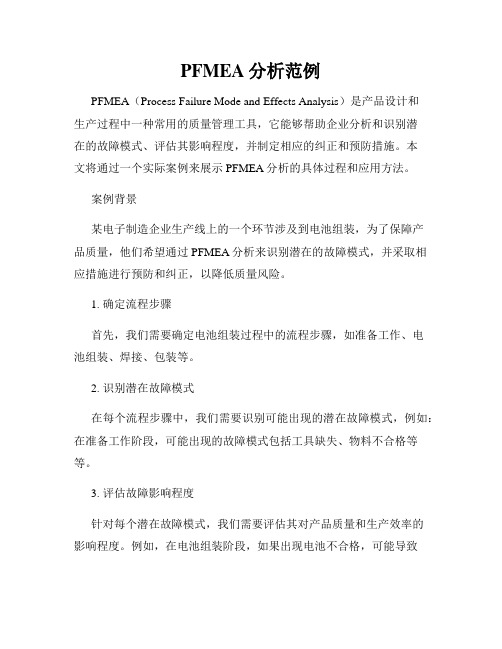
PFMEA分析范例PFMEA(Process Failure Mode and Effects Analysis)是产品设计和生产过程中一种常用的质量管理工具,它能够帮助企业分析和识别潜在的故障模式、评估其影响程度,并制定相应的纠正和预防措施。
本文将通过一个实际案例来展示PFMEA分析的具体过程和应用方法。
案例背景某电子制造企业生产线上的一个环节涉及到电池组装,为了保障产品质量,他们希望通过PFMEA分析来识别潜在的故障模式,并采取相应措施进行预防和纠正,以降低质量风险。
1. 确定流程步骤首先,我们需要确定电池组装过程中的流程步骤,如准备工作、电池组装、焊接、包装等。
2. 识别潜在故障模式在每个流程步骤中,我们需要识别可能出现的潜在故障模式,例如:在准备工作阶段,可能出现的故障模式包括工具缺失、物料不合格等等。
3. 评估故障影响程度针对每个潜在故障模式,我们需要评估其对产品质量和生产效率的影响程度。
例如,在电池组装阶段,如果出现电池不合格,可能导致产品连接不可靠,影响产品性能,同时还会增加后续检测和返工的工作量。
4. 确定风险等级结合故障模式的影响程度,我们可以根据一定的评估标准来确定每个故障模式的风险等级。
例如,可以设定高、中、低三个等级,将电池不合格列为高风险等级。
5. 制定预防和纠正措施对于高风险等级的故障模式,我们需要制定相应的预防和纠正措施,以降低潜在风险。
例如,对于电池不合格的风险,可以建立严格的供应商管理制度,提高物料检测的精度和效率。
6. 实施和跟踪制定好预防和纠正措施后,我们需要将其纳入到生产实践中,并建立相应的跟踪机制,及时评估其实施效果,并根据需要对措施进行调整和改进。
通过以上几个步骤的分析和实施,电子制造企业可以在电池组装过程中减少故障发生的概率,并及时采取纠正措施,以确保产品质量和生产效率的稳定性和可持续性。
总结PFMEA作为一种常用的质量管理工具,可以帮助企业在产品设计和生产过程中识别潜在故障模式,并制定相应的预防和纠正措施。
pfmea优秀案例
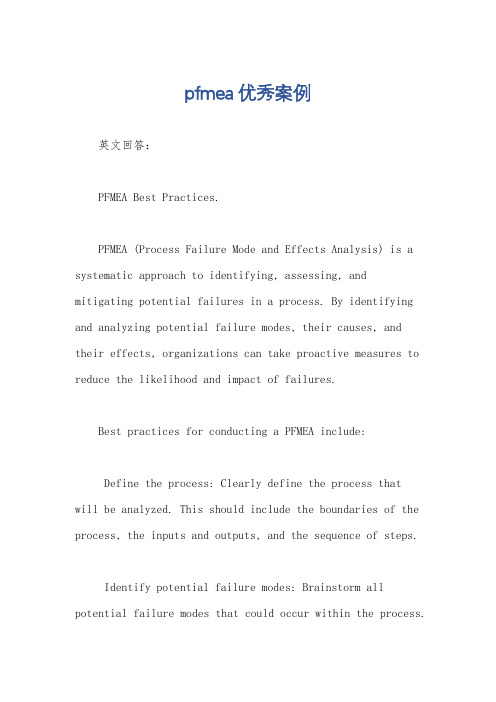
pfmea优秀案例英文回答:PFMEA Best Practices.PFMEA (Process Failure Mode and Effects Analysis) is a systematic approach to identifying, assessing, andmitigating potential failures in a process. By identifying and analyzing potential failure modes, their causes, and their effects, organizations can take proactive measures to reduce the likelihood and impact of failures.Best practices for conducting a PFMEA include:Define the process: Clearly define the process thatwill be analyzed. This should include the boundaries of the process, the inputs and outputs, and the sequence of steps.Identify potential failure modes: Brainstorm all potential failure modes that could occur within the process.This should be done by considering all aspects of the process, including equipment, materials, people, and procedures.Analyze the causes of failure modes: For each failure mode, identify the potential causes. These causes should be specific and actionable.Assess the effects of failure modes: Determine the potential effects of each failure mode. This should include both the immediate effects on the process and the ultimate effects on the customer or end user.Assign risk priority numbers (RPNs): Assign an RPN to each failure mode based on its severity, occurrence, and detectability. The RPN helps prioritize failure modes for mitigation.Develop mitigation strategies: For each failure mode with a high RPN, develop mitigation strategies to reduce the likelihood and impact of the failure. These strategies should be specific and actionable.Implement mitigation strategies: Implement the mitigation strategies that have been developed. This may involve making changes to the process, equipment, materials, people, or procedures.Monitor and evaluate the effectiveness of mitigation strategies: Monitor the effectiveness of the mitigation strategies that have been implemented. This may involve tracking the occurrence of failure modes and assessing the impact of the mitigation strategies.By following these best practices, organizations can improve the effectiveness of their PFMEA process and reduce the likelihood and impact of failures.中文回答:PFMEA优秀案例。
挤出PFMEA第四版实例

挤出PFMEA第四版实例一、本文概述1、PFMEA的定义和重要性PFMEA,即过程失效模式与影响分析,是一种用于评估制造过程中潜在失效模式的工具。
它帮助我们识别、评估和排序潜在的制造过程缺陷,以便在生产之前采取预防措施,从而提高产品质量、降低成本并减少交货期延误。
PFMEA的核心价值在于它能够系统地分析制造过程中的潜在风险,并量化这些风险对最终产品质量的影响。
通过这种方式,我们可以提前发现潜在问题,并在产品设计和制造过程中采取有效的纠正措施。
在汽车制造、电子设备、医疗器械和其他高风险领域,PFMEA已经成为质量管理和持续改进的重要组成部分。
它不仅有助于提高产品质量,还为组织提供了一种实用的工具,以识别和解决潜在的制造过程问题,从而提高生产效率、降低成本并增强市场竞争力。
总之,PFMEA是一种重要的质量管理工具,能够识别和评估制造过程中的潜在失效模式,从而采取预防措施,提高产品质量、降低成本并减少交货期延误。
在未来,随着生产过程日益复杂化和客户需求多样化,PFMEA的重要性将进一步提升。
2、PFMEA的历史和发展PFMEA(Process Flure Mode and Effects Analysis)是一种用于评估和改善制造业过程中潜在失效模式的工具。
自1960年代初期以来,PFMEA已经被广泛应用于各种行业,并且已经成为许多质量和安全标准的要求。
最初的PFMEA方法是在1960年代初期由美国宇航局(NASA)开发的。
当时,NASA正在开发一套新的宇宙飞船系统,他们需要一种可靠的方法来确保制造过程中的质量和安全性。
于是,PFMEA作为一种特殊的故障模式分析方法,能够系统地识别和评估生产过程中潜在的失效模式及其影响。
随着时间的推移,PFMEA逐渐在汽车、电子、医疗和其他制造业中得到广泛应用。
到了1980年代,PFMEA已经成为ISO质量管理体系(ISO 9000)的一部分,并且被广泛接受为行业标准。
新版pfmea七步法案例
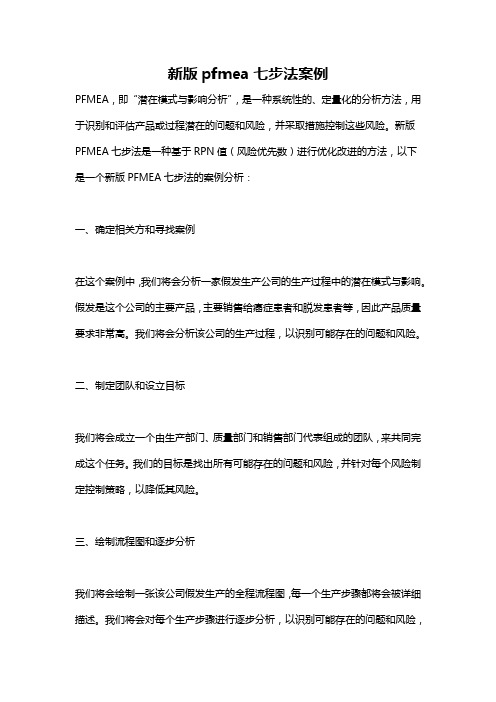
新版pfmea七步法案例PFMEA,即“潜在模式与影响分析”,是一种系统性的、定量化的分析方法,用于识别和评估产品或过程潜在的问题和风险,并采取措施控制这些风险。
新版PFMEA七步法是一种基于RPN值(风险优先数)进行优化改进的方法,以下是一个新版PFMEA七步法的案例分析:一、确定相关方和寻找案例在这个案例中,我们将会分析一家假发生产公司的生产过程中的潜在模式与影响。
假发是这个公司的主要产品,主要销售给癌症患者和脱发患者等,因此产品质量要求非常高。
我们将会分析该公司的生产过程,以识别可能存在的问题和风险。
二、制定团队和设立目标我们将会成立一个由生产部门、质量部门和销售部门代表组成的团队,来共同完成这个任务。
我们的目标是找出所有可能存在的问题和风险,并针对每个风险制定控制策略,以降低其风险。
三、绘制流程图和逐步分析我们将会绘制一张该公司假发生产的全程流程图,每一个生产步骤都将会被详细描述。
我们将会对每个生产步骤进行逐步分析,以识别可能存在的问题和风险,包括机器故障、材料缺陷、操作不当等等。
四、评估风险严重程度我们将根据RPN 值来评估每个风险的严重程度。
RPN 值根据三个因素计算出来:发生的概率、可能的影响和检测的能力。
我们将会为每个可能存在的风险计算RPN 值,并按照此数值对每个风险进行排序。
我们将把RPN 值高于100 的所有风险作为紧急问题来对待。
五、确定控制措施和负责人我们将为每个评级高的风险制定控制措施,并确定控制措施的执行者、实施时间和监督人员。
这些措施可能包括调整制造过程、提高质检要求、增加维护保养频率、教育员工如何正确操作、规范化标准工艺等等。
六、执行和跟踪控制措施我们将严格执行控制措施并按时完成项目,同时跟踪每个控制措施的效果和改进情况。
我们将进行定期的审核和改进,以保证控制措施的持续有效性。
七、更新和维护PFMEA表我们将定期更新和维护我们的PFMEA表,并将其作为质量管理的一项重要工具。
PFMEA案例(2[1].2)
![PFMEA案例(2[1].2)](https://img.taocdn.com/s3/m/9113fc0e5f0e7cd18425361e.png)
工序号及 加工内容
潜在失效 模式
潜在失 效后果
分 类
潜在失效起 因/机理
频 度 O
R P N
现行控 制措施
建议措施
采取措 施
严 重 度
频 度
探 测 度
R P N
P007 装配
内弧板与 其他弧板 不一致
排壳排 链器无 法在炮 箱上锁 紧
8
零件一致性 差,装配基 准不一致
8
3
19 2
装配前 进行检 查
装配前对 零件进行 检查,统 一装配基 准
排壳排链器工艺潜在失效模式及后果(PFMEA)分析(机加)
措施执行结果 工序号及 加工内容
潜在失效 模式
潜在失 效后果
严 重 度 S
分 类
潜在失效起 因/机理
频 度 O
探 测 度 D
R P N
现行控 制措施
建议措施
责任 和目 标完 成日 期
采取措 施
严 重 度
频 度
探 测 度
R P N
P003 钻/ 钻,扩, 铰孔 φ28+0.21 0, φ29+0.21 0。
增加工序 6A,进行 油压机压 装;指定 专门人员 加工;压 装严格压 力和时间。 增加高精 度设备, 定员,定 机,定切 削。
221车间 2004.01
8
2
2
32
P014/镗/ 镗内孔, 保证尺寸 ,形状公 差和表面 粗糙度要 求。
①尺寸及 形置公差 超差。
后续工序 加工余量 不够。
7
G
①机床精度低。 ②切削速度不 匹配。 ③刀、量具使 用不对。
8
3
19 2
工人现 场控制
PFMEA 过程失效模式及后果分析
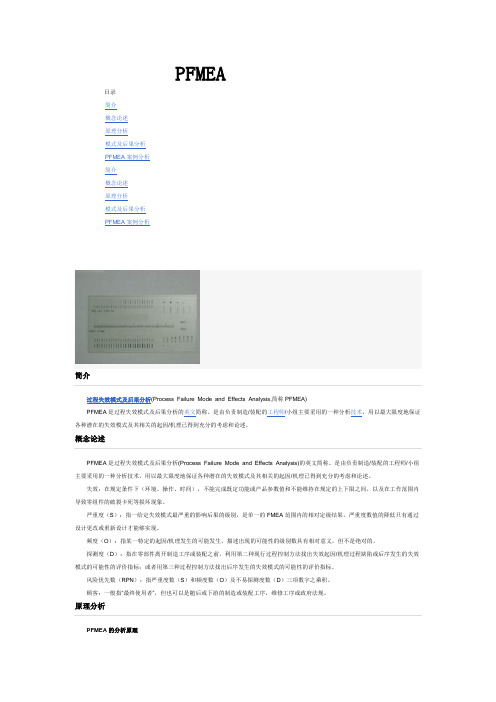
PFMEA目录简介概念论述原理分析模式及后果分析PFMEA案例分析简介概念论述原理分析模式及后果分析PFMEA案例分析简介过程失效模式及后果分析(Process Failure Mode and Effects Analysis,简称PFMEA)PFMEA是过程失效模式及后果分析的英文简称。
是由负责制造/装配的工程师/小组主要采用的一种分析技术,用以最大限度地保证各种潜在的失效模式及其相关的起因/机理已得到充分的考虑和论述。
概念论述PFMEA是过程失效模式及后果分析(Process Failure Mode and Effects Analysis)的英文简称。
是由负责制造/装配的工程师/小组主要采用的一种分析技术,用以最大限度地保证各种潜在的失效模式及其相关的起因/机理已得到充分的考虑和论述。
失效:在规定条件下(环境、操作、时间),不能完成既定功能或产品参数值和不能维持在规定的上下限之间,以及在工作范围内导致零组件的破裂卡死等损坏现象。
严重度(S):指一给定失效模式最严重的影响后果的级别,是单一的FMEA范围内的相对定级结果。
严重度数值的降低只有通过设计更改或重新设计才能够实现。
频度(O):指某一特定的起因/机理发生的可能发生,描述出现的可能性的级别数具有相对意义,但不是绝对的。
探测度(D):指在零部件离开制造工序或装配之前,利用第二种现行过程控制方法找出失效起因/机理过程缺陷或后序发生的失效模式的可能性的评价指标;或者用第三种过程控制方法找出后序发生的失效模式的可能性的评价指标。
风险优先数(RPN):指严重度数(S)和频度数(O)及不易探测度数(D)三项数字之乘积。
顾客:一般指“最终使用者”,但也可以是随后或下游的制造或装配工序,维修工序或政府法规。
原理分析PFMEA的分析原理PFMEA的分析原理如下表所示,它包括以下几个关键步骤:(1)确定与工艺生产或产品制造过程相关的潜在失效模式与起因;(2)评价失效对产品质量和顾客的潜在影响;(3)找出减少失效发生或失效条件的过程控制变量,并制定纠正和预防措施;(4)编制潜在失效模式分级表,确保严重的失效模式得到优先控制;(5)跟踪控制措施的实施情况,更新失效模式分级表。
新版(七步法案例)PFMEA 紧固件 螺栓

完成状态 与供应商协商包依装规范作业
目视/核 对
沈伦玉 2020/3/10
完成状态
供应商每批提供材质证明, 公司每批抽检材质成分
实际完成时 间
严 重 度
频 度
探 测 度
特 殊 特 性
AP
备注
2020/3/10 6 1 1
L
2020/3/10 8 1 1
L
01 材料进料
无漏检/错检
检测来料线径符合图纸要求
告
2 检验/核对
3
目视/ 核对/检测
2L 2L
6
每隔两个小时对锁紧螺丝紧 固一次
3 检验
2L ★
8 修理模具R角位置
3 检测
2L ※
8 修改一冲相关尺寸
3 检测
2L ※
要求供应商对模具尺寸进行 6 中限管理并提供出货检验报
告
2
目视/ 核对/检测
2L
7
将主模模腔尺寸定义在中限 并要求供应商提供检测报告
02 材料保管领用
作业员
03 冷墩成型
仓库环境
作业员
3/16 一模二冲 冷墩机
敲击模块 金相测试仪 作业员
04 辗制螺纹
004车 搓牙机
检测材质成分符合标准要求
分析材质符合ROHS环保要求
控制原料账目/标签与实物一 致
核对标签与实物一致 核对账目与实物一致
机械性能未能满足要求,导致退 货
材质成分未符合要求
PFME
A-
公司
XXXXXX
生产场所 XXXXXX
客户
XXXXXX
过程责任 XXXXXX
多功能小组 XXXXXXXXXXXXX
项目 车型年/项目
PFMEA案例(全套表格)
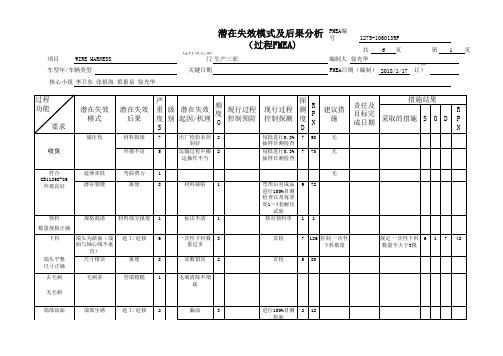
责任及 目标共完 成日期
措施结果 采6 取页的措施 S 第O
R D3 P 页
N
产品应在试验要 求的条件下工作
正常
包装
端部生锈
外观不良 3
管材缺陷 1 包装袋破损 2
抽检
10 80
目测
8 48
为保护产品及数 量清点防止失效 对成品进行封头
及捆绑
0
0
00
0
0
00
评分
等级
Cp或者Cpk值
等
级
(
顾
客
评分
是 用
级 别
潜在失效 起因/机理
频 度 O
现行过程 控制预防
现行过程 控制探测
探 测 度 D
R P N
建议措 施
责任及 目标共完 成日期
措施结果 采6 取页的措施 S 第O
R D6 P 页
N
1 似乎不会发生 1.67≤Cpk
非
常
低
(
被
识
别
力
1
强 的
顾
客
指
摘
的
程
度
)
1-2
自工序可以 检出
③ 发生频率>3&检出难易度>5
项目
WIRE HARNESS
车型年/车辆类型
核心小组 李卫东 张祖海 黄惠泉 徐光华
潜在失效模式及后果分析 FMEA编 号 (过程FMEA) 过程责任部
1275-1060139F 共 6页
第1页
门 生产三部
编制人 徐光华
(修
关键日期
FMEA日期(编制) 2018/1/17 订)
过程 功能
要求
收货
潜在失效 模式
aiag vda pfmea例子
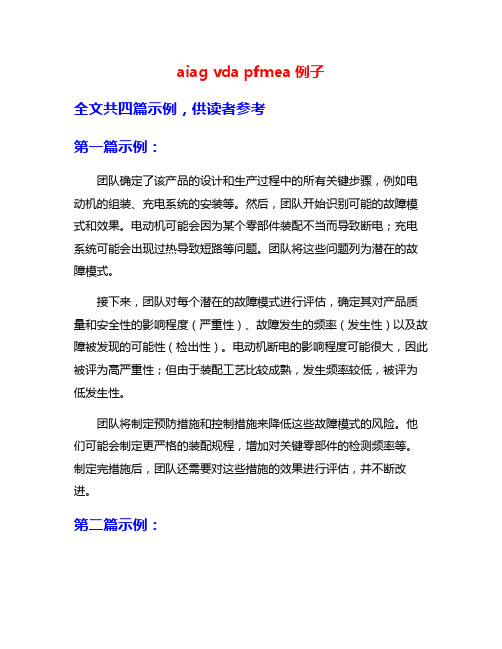
aiag vda pfmea例子全文共四篇示例,供读者参考第一篇示例:团队确定了该产品的设计和生产过程中的所有关键步骤,例如电动机的组装、充电系统的安装等。
然后,团队开始识别可能的故障模式和效果。
电动机可能会因为某个零部件装配不当而导致断电;充电系统可能会出现过热导致短路等问题。
团队将这些问题列为潜在的故障模式。
接下来,团队对每个潜在的故障模式进行评估,确定其对产品质量和安全性的影响程度(严重性)、故障发生的频率(发生性)以及故障被发现的可能性(检出性)。
电动机断电的影响程度可能很大,因此被评为高严重性;但由于装配工艺比较成熟,发生频率较低,被评为低发生性。
团队将制定预防措施和控制措施来降低这些故障模式的风险。
他们可能会制定更严格的装配规程,增加对关键零部件的检测频率等。
制定完措施后,团队还需要对这些措施的效果进行评估,并不断改进。
第二篇示例:AIAG VDA PFMEA是指根据国际汽车行业标准组织(AIAG)和德国汽车工程师协会(VDA)共同制定的一种过程失效模式及影响分析方法。
这种方法是为了帮助汽车行业的供应链伙伴在产品设计和生产过程中识别和解决潜在的故障模式,从而提高产品质量和可靠性。
在本文中,我们将以实际案例为例,介绍AIAG VDA PFMEA的具体应用及其重要性。
故障模式及影响分析(FMEA)是一种常见的质量管理工具,其目的是通过系统性地识别和排除产品和过程中的潜在故障模式,以确保产品的质量和可靠性。
在汽车行业,产品设计和生产过程中存在着各种各样的潜在故障模式,如设计错误、工艺不当、零部件失效等,这些故障模式可能会导致产品的功能失效、安全性降低,甚至对用户造成伤害。
AIAG VDA PFMEA是结合了AIAG和VDA两个国际汽车行业标准组织的最佳实践而制定的一种FMEA方法。
它强调了全面性和系统性,要求参与方从产品设计、制造、测试、维修等全过程来考虑潜在故障模式,并评估其可能的影响程度和频率。
PFMEA教程(五大工具)

05
PFMEA总结与展望
PFMEA的优势与不足
优势
PFMEA是一种系统性的故障模式和影响分析方法,能够全面评估产品或 过程的潜在故障模式及其对系统的影响。
PFMEA提供了一种结构化的风险评估工具,有助于识别和优先处理高风 险故障模式。
PFMEA的优势与不足
• PFMEA强调跨部门合作和沟通,有助于促进团队协作和 资源整合。
项目管理
在项目管理中,PFMEA可以用于 评估项目实施过程中可能出现的 风险和问题,制定相应的预防措 施。
பைடு நூலகம்
02
PFMEA实施步骤
明确分析对象和范围
确定PFMEA分析的对象和范围,明 确分析的重点和目标。
收集相关资料和信息,了解产品的功 能、结构、制造工艺、使用环境等。
列出潜在的失效模式
通过头脑风暴、专家判断等方法,列出产品在制造、使用过程中可能出现的失效 模式。
它通过分析流程中可能发生的故障模式,评估其发生概率、 严重程度和可检测性,从而确定预防措施的需求和优先级。
PFMEA目的
识别潜在的故障模式
01
PFMEA通过对流程的详细分析,找出可能发生的故障模式,为
预防措施提供依据。
评估故障影响
02
PFMEA分析故障模式对产品、系统或流程性能的影响,以便了
解其对最终产品或服务质量的潜在风险。
案例二:汽车行业PFMEA分析
要点一
总结词
要点二
详细描述
系统化分析
汽车行业PFMEA分析需要从系统角度出发,对发动机、底 盘、车身、电气等各个子系统进行失效模式和影响分析, 以确保整车性能和安全性。
案例三:医疗器械PFMEA分析
pfmea案例

pfmea案例PFMEA案例。
PFMEA(Process Failure Mode and Effects Analysis)是一种用于识别和评估制造过程中潜在故障模式及其影响的方法。
它可以帮助企业在生产过程中提前识别潜在的问题,并采取相应的措施进行预防,从而提高产品质量和生产效率。
下面我们将通过一个实际的案例来介绍PFMEA的应用。
在某汽车零部件生产企业,他们使用PFMEA来分析生产线上的焊接工艺。
首先,团队收集了关于焊接工艺的所有相关信息,包括焊接设备、焊接材料、操作流程等。
然后,团队针对每个潜在的故障模式进行分析,包括焊接接头断裂、焊接温度过高、焊接时间过长等。
接着,团队对每种故障模式的可能影响进行评估,比如焊接接头断裂可能导致产品失效,焊接温度过高可能导致材料变形等。
最后,团队制定了针对每种故障模式的预防措施,比如加强对焊接工艺的监控,优化焊接参数,加强员工培训等。
通过PFMEA的分析,该企业发现了一些潜在的问题,并及时采取了相应的措施进行预防,从而避免了可能导致产品质量问题的故障发生。
这不仅提高了产品质量,也降低了生产成本,提高了生产效率。
通过以上案例可以看出,PFMEA作为一种有效的质量管理工具,在生产过程中发挥着重要作用。
它可以帮助企业在生产过程中及时发现潜在的问题,并采取预防措施,从而提高产品质量,降低生产成本,提高生产效率。
因此,建议更多的企业在生产过程中引入PFMEA方法,以提升竞争力,满足市场需求。
综上所述,PFMEA在制造业中具有重要意义,通过对潜在故障模式和影响进行分析和评估,有助于企业提前预防问题的发生,提高产品质量和生产效率。
希望更多的企业能够重视PFMEA的应用,从而在激烈的市场竞争中脱颖而出。
PFMEA案例(7.2)
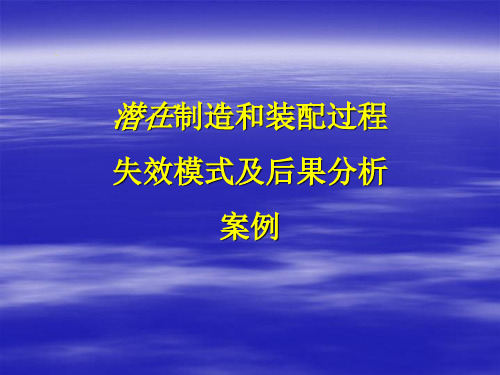
失效模式及后果分析
案例
do
something
案例一、导气筒PFMEA分析
表1:导气筒《工艺潜在失效模式及后果(PFMEA)分析表》
案例一、导气筒PFMEA分析
表1:导气筒《工艺潜在失效模式及后果(PFMEA)分析表》
案例一、导气筒PFMEA分析
表1:导气筒《工艺潜在失效模式及后果(PFMEA)分析表》
案例六
表1:导气筒《工艺潜在失效模式及后果(PFMEA)分析表》
感谢阅读
感谢阅读
案例六
表1:导气筒《工艺潜在失效模式及后果(PFMEA)分析表》
案例六
表1:导气筒《工艺潜在失效模式及后果(PFMEA)分析表》
案例六
表1:导气筒《工艺潜在失效模式及后果(PFMEA)分析表》
案例六
表1:导气筒《工艺潜在失效模式及后果(PFMEA)分析表》
案例六
表1:导气筒《工艺潜在失效模式及后果(PFMEA)分析表》
案例二、摇架工艺 PFMEA分析
表1:导气筒《工艺潜在失效模式及后果(PFMEA)分析表》
案例三、摇架工艺 PFMEA分析
表1:导气筒《工艺潜在失效模式及后果(PFMEA)分析表》
案例四、排壳排链器PFMEA分析
表1:导气筒《工艺潜在失效模式及后果(PFMEA)分析表》
案例五、排壳排链器PFMEA分析
表1:导气筒《工艺潜在失效模式及后果(PFMEA)分析表》
案例六
表1:导气筒《工艺潜在失效模式及后果(PFMEA)分析表》
案例六
表1:导气筒《工艺潜在失效模式及后果(PFMEA)分析表》
案例六
表1:导气筒《工艺潜在失效模式及后果(PFMEA)分析表》
PFMEA案例

30
检查与评估现有的操纵方法
生产部
7﹑
装扣钩
漏装扣钩/扣钩装的位置不正确
线束装入车辆时困难或者安装失败
6
操作员未依规定操作
3
培训操作人员并重点标注图面要求
依照图面规定操作/100%外观检验
2
54
检查与评估现有的操纵方法
生产部
6
扣钩插入的深度不充分
2
培训操作人员并重点标注图面要求
依照图面规定操作/100%外观检验
装线盆入线不正确
3
用正确的装线盆/架
操作员检验
3
36
绝缘破皮,导线断线
端子铆线困难/导通测试不良
4
*裁线机故障/刀片设置太低/刀片用旧;*短路或者开路
5
保护保养/点检
100%检查
2
40
2﹑
压端子
端子变形
铆线端子插入壳仔困难
6
送料爪的变化导致端子经导流板时不正确
2
加大清洁/润滑端子机活动部门的频次
PQC每小时巡检/操作员自检
3
பைடு நூலகம்36
检查与评估现有的操纵方法
工程部
铆线端子插入壳仔后不合格
6
端子在导流板卡住而被硬拉出铆线
2
加大清洁/润滑端子机活动部位的频次
PQC每小时巡检/操作员自检
3
36
检查与评估现有的操纵方法
工程部/品管部/生产部
拉力不够
端子铆线不正确
8
▲
模座/刀座松动
2
保护保养/操纵正确的C/H
每小时拉力测试;巡检
3
48
灯炮装配线束时困难
5
检查图面脏污或者褪色未及时更换
六步法pfmea案例
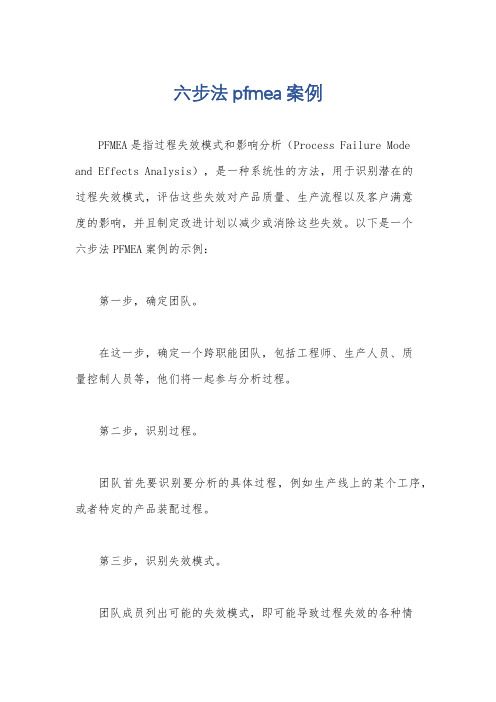
六步法pfmea案例
PFMEA是指过程失效模式和影响分析(Process Failure Mode and Effects Analysis),是一种系统性的方法,用于识别潜在的
过程失效模式,评估这些失效对产品质量、生产流程以及客户满意
度的影响,并且制定改进计划以减少或消除这些失效。
以下是一个
六步法PFMEA案例的示例:
第一步,确定团队。
在这一步,确定一个跨职能团队,包括工程师、生产人员、质
量控制人员等,他们将一起参与分析过程。
第二步,识别过程。
团队首先要识别要分析的具体过程,例如生产线上的某个工序,或者特定的产品装配过程。
第三步,识别失效模式。
团队成员列出可能的失效模式,即可能导致过程失效的各种情
况,例如机器故障、操作失误、材料缺陷等。
第四步,确定失效影响。
团队评估每种失效模式对产品质量、生产流程以及客户满意度的影响程度,确定其严重性。
第五步,确定改进措施。
针对每种失效模式,团队制定相应的改进措施,例如改进工艺流程、提高操作技能、加强设备维护等。
第六步,实施改进并监控。
团队将改进措施付诸实施,并持续监控过程,确保改进效果符合预期,必要时对改进措施进行调整。
通过这六个步骤,团队可以全面地分析潜在的失效模式,并采取相应的措施来提高产品质量和生产效率。
PFMEA案例的实施可以帮助企业减少质量问题和生产故障,提高客户满意度,从而提升竞争力。
PFMEA第五版案例
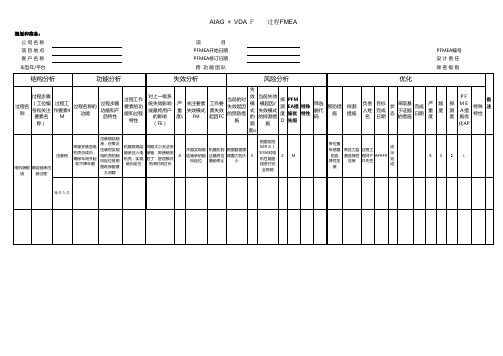
称)
过程工作 要素的功 能和过程
特性
对上一级系 统失效影响 或最终用户
的影响 (FE)
严 关注要素 重 失效模式 度s FM
失
工作要 素失效 起因FC
当前的对 失效起因 的预防措
施
效 模 式 的 频
当前失效 模起因/ 失效模式 的探测措
施
探 PFM 测 EA措 特殊 度 施优 特性 D 先级
度o
压装 D先生
பைடு நூலகம்
尚 示 完 成
83 2 L
操作人员
AIAG ﹠ VDA F 过程FMEA
规划和准备: 公司名称 项目地点 客户名称 车型年/平台
项
目
PFMEA开始日期 PFMEA修订日期
跨 功能团队
PFMEA编号 设计责任 保密级别
结构分析
功能分析
失效分析
风险分析
优化
过程步骤
过程名 称
(工位编 号和关注
要素名
过程工 作要素4
M
过程名称的 功能
过程步骤 功能和产
机器将烧结 间隙太小无法安 轴承压入电 装轴,即使轴安 机壳,实现 后了,舒适模式
轴向定位 关闭时间过长
8
大间隙
不能实现烧 机器在到 根据数据表
结轴承的轴 达最终位 调整力的大 5
向定位 置前停止
小
根据规范 MRKJ 5036对电 机性能曲 线进行完
全探测
2
M
带位置 传感器
的选 择性压
装
带压力监 过程工 测选择性 程师P #####
筛选 器代 码
预防措 施
探测 措施
负责 人姓
名
目标 完成 日期
- 1、下载文档前请自行甄别文档内容的完整性,平台不提供额外的编辑、内容补充、找答案等附加服务。
- 2、"仅部分预览"的文档,不可在线预览部分如存在完整性等问题,可反馈申请退款(可完整预览的文档不适用该条件!)。
- 3、如文档侵犯您的权益,请联系客服反馈,我们会尽快为您处理(人工客服工作时间:9:00-18:30)。
潜在失效 模式
潜在失效 后果
严 潜在失效 频 重 级 现行过程 起因/机 度 度 别 控制预防 理 O S
2 涂油后存放 时间过长 零件滑落 6 2
探 R 现行过程 测 P 控制探测 度 N D
巡检 进行100%目测 检验 2 8 24 32
建议措 施
措施结果 责任及 R 目标完 3 页 共 第 D 2P 采取的措施 S O 成日期 N
7 5 出厂检验未 控制好 运输过程中 搬运操作不 当 2 2
探 R 现行过程 测 P 控制探测 度 N D
每批进行0.3% 抽样目测检查 每批进行0.3% 抽样目测检查 7 7 98 70
建议措 施
无 无
措施结果 责任及 目标完 采取的措施 S O D 成日期
R P N
符合 GB11258-89 外观良好
3
首检
7 126 控制 一次性 下料数量 5 80
生产科 2003.6.1
规定 一次性下料 6 数量不大于3根
1
7
42
端头平整 尺寸正确 去毛刺 无毛刺 端部涂油
报废 管端粗糙
8 1
2
首检
端部生锈
返工/返修
2
漏涂
3
进行100%目测 检验
2
12
过程 功能 要求
均匀、完全 装配 零件按顺序正确 装配 端部成型
使用扭力扳手 抽检 7 56
建议措 施
措施结果 责任及 R 目标完 3 页 共 第 D 3P 采取的措施 S O 成日期 N
页
10 80
端部生锈
外观不良
3
包装袋破损
2
目测
8
48
为保护产品及数 量清点防止失效 对成品进行封头 及捆绑 0 0 0 0 0 0 0 0
8
64
顾客不满意
4
G
未符检具
2
8
64
工作减弱
7
吹气时间不 够
2
100%检验
4
56
过程 功能 要求
耐压试验 产品应在试验要 求的条件下工作 正常 包装
潜在失效 模式
压力降低
潜在失效 后果
泄漏
严 潜在失效 频 重 级 现行过程 起因/机 度 度 别 控制预防 理 O S
8 接头松动 管材缺陷 1 1
探 R 现行过程 测 P 控制探测 度 N D
页
零件漏装
返工/返修
孔歪
制动液渗漏
10
下料后管端 平面为斜面 因冲击使冲 头夹子移位
2 3 3 3 1 2 2 2 3
首件进行目测 检查 每批进行首件 和末件检查
100%检验
3
60 生产科 2003.6.1 每周调整一次夹 10 子 1 5 50
100%检验 100%检验 100%检验 100%检验 100%检验 100%检验 100%检验
延伸率低 潜在裂缝
弯曲费力 报废
1 8 材料缺陷 1 弯形后对成品 进行100%目测 检查以及每季 度1-4套耐压 试验 核对领料单 9 72
无
领料 数量规格正确 下料
规格混淆
材料部分报废
1标识不清1 Nhomakorabea1
1
端头为斜面(端 面与轴心线不垂 直) 尺寸错误 毛刺多
返工/返修
6
一次性下料 数量过多 读数错误 毛刺清除不 彻底
首检
不定时进行校 核
断裂 按照弯形夹具进 行正确弯形 校形 与标准件保持一 致 吹气 保证油管内部清 洁、畅通 内腔清洁度低 变形
产品报废
8
管材缺陷 ·杂质 ·延伸率低 ·潜在裂缝
1
在下料前进行 弯形后对成品 目测检查 进行100%目测 检查以及每季 度1-3套耐压 试验 每批进行 0.1-0.3%抽查
5 150 定期调整夹 子 5 5 5 5 5 5 5 15 15 35 10 10 10 75
外圆大 外圆小 内孔小 重抛 压伤 尺寸正确 外观端正 弯形 毛刺 弯形不到位
不稳定 不稳定 工作减弱 不稳定 不稳定 不稳定 顾客不满意
1 1 7 1 1 1 5
G G G G G
送料偏多 送料偏少 送料偏多 管材缺陷 冲头粘铁屑 毛刺清除不 彻底 损坏的工装
潜在失效模式及后果分析 过程FMEA FMEA) (过程FMEA)
项目 车型年/车辆类型 核心小组 过程责任 关键日期
FMEA编号 共 编制人 FMEA日期(编制) (修订) 3 页 第 1 页
过程 功能 要求
接收原材料
潜在失效 模式
碰压伤
潜在失效 后果
材料报废 外观不良
严 潜在失效 频 重 级 现行过程 起因/机 度 控制预防 度 别 理 O S