碳素工具钢中碳化物微细化热处理工艺
机械加工常见热处理工艺

渗碳渗碳热处理渗碳:是对金属表面处理的一种,采用渗碳的多为低碳钢或低合金钢,具体方法是将工件置入具有活性渗碳介质中,加热到900--950摄氏度的单相奥氏体区,保温足够时间后,使渗碳介质中分解出的活性碳原子渗入钢件表层,从而获得表层高碳,心部仍保持原有成分。
相似的还有低温渗氮处理。
这是金属材料常见的一种热处理工艺,它可以使渗过碳的工件表面获得很高的硬度,提高其耐磨程度。
概述渗碳(carburizing/carburization)是指使碳原子渗入到钢表面层的过程。
也是使低碳钢的工件具有高碳钢的表面层,再经过淬火和低温回火,使工件的表面层具有高硬度和耐磨性,而工件的中心部分仍然保持着低碳钢的韧性和塑性。
渗碳工件的材料一般为低碳钢或低碳合金钢(含碳量小于0.25%)。
渗碳后﹐钢件表面的化学成分可接近高碳钢。
工件渗碳后还要经过淬火﹐以得到高的表面硬度﹑高的耐磨性和疲劳强度﹐并保持心部有低碳钢淬火后的强韧性﹐使工件能承受冲击载荷。
渗碳工艺广泛用于飞机﹑汽车和拖拉机等的机械零件﹐如齿轮﹑轴﹑凸轮轴等。
渗碳工艺在中国可以上溯到2000年以前。
最早是用固体渗碳介质渗碳。
液体和气体渗碳是在20世纪出现并得到广泛应用的。
美国在20年代开始采用转筒炉进行气体渗碳。
30年代﹐连续式气体渗碳炉开始在工业上应用。
60年代高温(960~1100℃)气体渗碳得到发展。
至70年代﹐出现了真空渗碳和离子渗碳。
分类按含碳介质的不同﹐渗碳可分为气体渗碳、固体渗碳﹑液体渗碳﹑和碳氮共渗(氰化)。
气体渗碳是将工件装入密闭的渗碳炉内,通入气体渗剂(甲烷、乙烷等)或液体渗剂(煤油或苯、酒精、丙酮等),在高温下分解出活性碳原子,渗入工件表面,以获得高碳表面层的一种渗碳操作工艺。
固体渗碳是将工件和固体渗碳剂(木炭加促进剂组成)一起装在密闭的渗碳箱中,将箱放入加热炉中加热到渗碳温度,并保温一定时间,使活性碳原子渗人工件表面的一种最早的渗碳方法。
液体渗碳是利用液体介质进行渗碳,常用的液体渗碳介质有:碳化硅,―603‖渗碳剂等。
第二节冷作模具材料及热处理规范

① 要求耐磨性和热硬性高的模具: 1020~1040℃淬火,520~540℃三次回火。
②要求韧性好、变形小的模具:960~980℃分级淬火, •270~290℃回火二次。
• Cr12钢: •只适用于制造冲击负荷小、耐磨性要求高的冲 切薄硬钢板的冲裁模。
• Cr12MoV和Cr12Mo1V1钢: •广泛用于制造大截面、形状复杂的重载模具,如切 边模、落料模、滚边模、拉丝模。
Cr12Mo1V1脆断倾向最小,模具寿命是 Cr12MoV的几倍。
PPT文档演模板
第二节冷作模具材料及热处理规范
•
抗压强度较低
• ②高温淬火及高温 •性能特点:具有高耐磨性、热硬性及较高抗压强度。
• ③中温淬火及中温回火 •性能特点:最好的韧性,较高的断裂韧度。
• Cr12 型钢淬火可采用空冷、油冷、分级淬火,
回火可采用油冷或空冷,回火次数1~3次。
PPT文档演模板
第二节冷作模具材料及热处理规范
•3、应用范围
•2)退火与正火 • 退火工艺:加热790~830℃,等温700~720℃, 保温1~2h,炉冷至550℃出炉。 • 锻造不良,出现网状碳化物或粗大晶粒时,需正火。
• 正火工艺:930~950℃保温后空冷
PPT文档演模板
第二节冷作模具材料及热处理规范
•3)淬、回火 •图2~6、2~7为CrWMn钢的力学性能与淬火温度的关系:
•正火工艺: • 加热温度 930~950℃。 • 冷却方式 小型模块,空冷;较大模块, 鼓风或喷雾;大型范
•3)淬火与回火
•淬火加热温度:830~860℃,油冷。 尺寸较大或分级淬火的模具,宜选840~860℃。 尺寸较小模具,宜选830~850℃。 箱式炉加热应比盐浴炉加热温度高。
钢材的热处理有以下几个方法

钢材的热处理有以下几个方法※均质退火处理简称均质化处理(Homogenization),系利用在高温进行长时间加热,使内部的化学成分充分扩散,因此又称为『扩散退火』。
加热温度会因钢材种类有所差异,大钢锭通常在1200℃至1300℃之间进行均质化处理,高碳钢在1100℃至1200℃之间,而一般锻造或轧延之钢材则在1000℃至1200℃间进行此项热处理。
※完全退火处理完全退火处理系将亚共析钢加热至Ac3温度以上30~50℃、过共析钢加热至Ac1温度以上50℃左右的温度范围,在该温度保持足够时间,使成为沃斯田体单相组织(亚共析钢)或沃斯田体加上雪明碳体混合组织后,在进行炉冷使钢材软化,以得到钢材最佳之延展性及微细晶粒组织。
※球化退火处理球化退火主要的目的,是希望藉由热处理使钢铁材料内部的层状或网状碳化物凝聚成为球状,使改善钢材之切削性能及加工塑性,特别是高碳的工具钢更是需要此种退火处理。
常见的球化退火处理包括:(1)在钢材A1温度的上方、下方反复加热、冷却数次,使A1变态所析出的雪明碳铁,继续附着成长在上述球化的碳化物上;(2)加热至钢材A3或Acm温度上方,始碳化物完全固溶于沃斯田体后急冷,再依上述方法进行球化处理。
使碳化物球化,尚可增加钢材的淬火后韧性、防止淬裂,亦可改善钢材的淬火回火后机械性质、提高钢材的使用寿命。
※软化退火处理软化退火热处理的热处理程序是将工件加热到600℃至650℃范围内(A1温度下方),维持一段时间之后空冷,其主要目的在于使以加工硬化的工件再度软化、回复原先之韧性,以便能再进一步加工。
此种热处理方法常在冷加工过程反复实施,故又称之为制程退火。
大部分金属在冷加工后,材料强度、硬度会随着加工量渐增而变大,也因此导致材料延性降低、材质变脆,若需要再进一步加工时,须先经软化退火热处理才能继续加工。
※弛力退火处理弛力退火热处理主要的目的,在于清除因锻造、铸造、机械加工或焊接所产生的残留应力,这种残存应力常导致工件强度降低、经久变形,并对材料韧性、延展性有不良影响,因此弛力退火热处理对于尺寸经度要求严格的工件、有安全顾虑的机械构件事非常重要的。
gcr15钢碳化物细化处理工艺

gcr15钢碳化物细化处理工艺该文档旨在介绍GCR15钢碳化物细化处理工艺的研究背景、目的和主要内容。
研究背景:GCR15钢是一种常用的轴承钢,其碳化物细化处理可以提高材料的硬度和耐磨性,从而增强其使用寿命和性能。
因此,对于GCR15钢的碳化物细化处理工艺进行深入研究具有重要的理论和实践意义。
研究背景:GCR15钢是一种常用的轴承钢,其碳化物细化处理可以提高材料的硬度和耐磨性,从而增强其使用寿命和性能。
因此,对于GCR15钢的碳化物细化处理工艺进行深入研究具有重要的理论和实践意义。
研究目的:本文旨在探索并优化GCR15钢的碳化物细化处理工艺,以提高材料的性能和使用寿命。
通过深入分析不同处理参数和工艺条件对钢材性能的影响,为进一步优化制造工艺提供参考和指导。
研究目的:本文旨在探索并优化GCR15钢的碳化物细化处理工艺,以提高材料的性能和使用寿命。
通过深入分析不同处理参数和工艺条件对钢材性能的影响,为进一步优化制造工艺提供参考和指导。
研究目的:本文旨在探索并优化GCR15钢的碳化物细化处理工艺,以提高材料的性能和使用寿命。
通过深入分析不同处理参数和工艺条件对钢材性能的影响,为进一步优化制造工艺提供参考和指导。
研究目的:本文旨在探索并优化GCR15钢的碳化物细化处理工艺,以提高材料的性能和使用寿命。
通过深入分析不同处理参数和工艺条件对钢材性能的影响,为进一步优化制造工艺提供参考和指导。
主要内容:本文将从以下几个方面展开研究:主要内容:本文将从以下几个方面展开研究:主要内容:本文将从以下几个方面展开研究:主要内容:本文将从以下几个方面展开研究:碳化物细化处理工艺的基本原理碳化物细化处理工艺的基本原理碳化物细化处理工艺的实验设计和方法不同处理参数对GCR15钢材性能的影响工艺参数优化及性能改善方案结论和展望通过对GCR15钢碳化物细化处理工艺的研究,我们期望能够为提高钢材性能和使用寿命提供有效的工艺改进方案,为相关领域的发展和应用做出贡献。
碳钢的分类热处理简介

钢和铁的区别铁是一种化学元素,是地球上最常见到的一种物质。
但是在现实生活中,纯粹意义的的“铁”我们几乎是看不到的。
我们平时说的铁一般包括生铁和熟铁,严格说,它们都不是纯粹意义上的“铁”,都是以铁元素为主的合金。
钢也是以铁元素为主合金,钢与铁的主要区别是含碳量不同。
人们由铁矿中提取铁,将矿石、焦炭和石灰石(助熔剂)在高炉中冶炼,使氧化铁还原成生铁(或铸铁)。
所得生铁一般含铁90%~95%,碳3%~4.5%和少量的硅、锰、硫、磷等。
生铁是炼钢或熟铁(锻铁)的原料,含碳量在0.2%~2.1%之间的铁合金称为钢。
生铁在平炉、转炉或电炉中进一步冶炼除去碳、硅、磷等杂质,可得各种组成的钢。
钢加上其他金属元素,还可以构成不同的合金钢,如日常的不锈钢就是含有铬,镍等其他元素的合金钢。
钢材就是含碳量大于0.05%,小于0.2%的铁碳合金。
铁是大自然赏赐给人内的恩物,将开采的铁矿石放入高炉中冶炼后即得到生铁,生铁按不同冶炼工艺和用途可分为炼钢生铁和铸造生铁。
炼钢生铁是一种含碳量>2%的铁碳合金,同时也含有少量的硅,锰,硫,磷等元素,其中硅和锰是有利元素,按一定比例存在于钢铁中可以显著提高材料的强度.硬度和耐腐耐磨性,而硫和磷则有害,会分别造成钢铁的热脆性和冷脆性,降低材料性能。
把炼钢用生铁放入炼钢炉中按一定比例熔炼,将得到的钢液浇铸成型,冷却后即得到钢锭或铸坯,供轧制成各种型材,为了获得不同性能的钢材,还会在熔炼过程中加入铬.镍.钼.钨.钒等微量元素,而这些化学成分决定了钢材的不同特性。
其中“铬”可以增加钢材的耐腐蚀性,通常国际上把含铬量大于13%的钢材称为不锈钢。
镍可以增加钢材的强度和韧性,钼可以防止钢材变脆,钨可增加钢材的耐磨损性,别看钨的硬度较低,只有大约40s,但它们的抗磨损能力非常高,钒可增加钢材的抗磨损性和延展性。
生铁――含C为2.0~4.5%钢――含C为0.05~2.0%熟铁――含C小于0.05%低碳钢-含碳量小于0.25%碳素结构钢-含碳量大多在0.7%以下中碳钢-含碳量在0.25~0.6%碳素工具钢-含碳量一般在0.65~1.35%高碳钢-含碳量大于0.60%高速钢-又称锋钢,含碳量一般在0.7~1.65%,含钨 5.5~19%,600摄氏度下工作时,硬度能保持在HRC60以上。
碳素工具钢的球化处理新工艺

中 , T 8钢 经 淬 火后 , 其 组织 为 马 氏体 和 届
氏 体 1 分 散度 大 且 不 稳 定 未 完全 溶解 的 碳 化 物 导 致 基 体 组 织 的 成分 极不 均 匀 , 在 随后 的 球 化 温 度 Ar附近 高温 回火 过 程 中, 或 以 原 有 的 细 小 碳 化 物 质 点为 核 心 , 或 在 基 体 组 4 2
维普资讯
赛 2
从 r艺完 成 时 阃 上 看 , 新 球 化 工 艺 比 常 规 球 化 退 火 工艺 减 少 约 2 。 退 火 质 量 也 比 O
较 好 , 耗 能 低 , 效 率 高 。 但不 足之 处 是 , 在
常 化 ^ }4 6 2 规球 退l 2I 1 q 7
J 租夹具 上 进行 压 缩试 验 。 结果 表 明; 在 尚 未
(1) 原 材 料 存 在 的 缺 陷 一 显 微 沟
材
料表 面存 在 一 定 数 量 的 显 微 沟 。 在 压 缩 试 验
压 缩 到 工 作 长 度 ,弹 簧便 发 生 了 粉 碎 性破
坏 。 为 此 , 我们 调 整 了热 处理 工艺 参 数 , 对 其 余 的 弹 簧 世行 了重 新处 理 , 试 装时 束 发 生 破 断 现 象 , 在实 际行 车试 验 中, 也 达到 了 预 效果。 { 失效 弹 簧 理化 检 验 .
断 口呈 脆 性 断 裂 形 式 , 断 裂 源始 于 裂 纹
缩试 验 时 , 夹 杂 物 附 近产 生应 力 集 中, 最 终 导 致 弹 簧 断 裂。
(3) 热处 理工 艺不 适 宜 根 据 断 口和 4 3
金 属 热 处 理 1 9 年 第 8期 90
2 ~6 . 。1 3} 2
合金钢及其热处理工艺

合金钢及热处理工艺第一篇结构钢各类结构钢的含碳量及热处理方法第一节调质钢调质钢分低淬透性调质钢中淬透性调质钢高淬透性调质钢一、低淬透性调质钢油淬临界直径最大为30~40mm,合金元素种类少,总含量不大于2.5%,常用的有铬钢、锰钢、铬硅钢和含硼钢。
女口30Cr、35Cr、40Cr、45Cr、30Mn2、35Mn2、40Mn2、45Mn2、50Mn2、42Mn2V、40MnB 等(一)40Cr过热倾向不大,淬火性较好,回火稳定性较高,经调质后能获得较高的综合机械性能。
因此它是应用最广的调质钢之一。
40Cr有两种加工路线;1)硬度较高(HB341~451)锻造-正火(退火)-加工-调质2)硬度较低(HB255~285)锻造-调质-加工调质前是否进行正火或退火,关键在于锻造的掌握上,掌握得好,可以从略。
淬火温度水淬830~850C ;油淬850~870C。
40Cr也可以制造经表面硬化处理的零件,如气体碳氮共渗,感应加热。
(二)45Mn2能促进钢的晶粒长大,显著提高钢的淬透性,45Mn2有较敏感的回火脆性,高温回火后要快冷(水或油中冷却)。
淬火温度810~840C,油淬。
(三)硅锰钢硅全部溶入铁素体,固溶强化效果显著,但含量过多(>2%)将会较多地降低塑性和韧性。
硅能提高淬透性,单一不明显,与锰或铬复合加入,效果显著。
但与锰或铬共存,回火脆性敏感。
此外,含硅的钢易产生脱碳现象。
常用的有35SiMn和42SiMn,它们既没有锰钢那样容易过热,也没有硅钢那样容易脱碳,但高温回火后必须快冷。
(四)含硼调质钢硼突出的作用是提高淬透性,并且加入量很少(0.0005~0.001%)时就效果显著,当有效硼在0.001%以下时,淬透性随含硼量增加增加,当超过0.001%,淬透性保持不变,超过0.003%冲击韧性下降,即”硼脆”超过0.007%引起热脆性,增加热加工困难.含硼量一般都控制在0.0005~0.0035%可代替1.6%Ni、0.3%Cr、0.2%Mo、0.2~0.7%Mn 的作用.微量硼对钢的过热倾向与回火脆性倾向略有增大的作用,而对回火稳定性则无影响.在淬火冷却时,硼有促进未淬透部分出现针状铁素体的作用,使钢的韧性降低,40MnB 锻造后,为改善组织,提高切削性,进行预先热处理,通常采用正火,而不是退火,以防止硼相析出造成硼脆。
结构钢的种类

第一节结构钢的种类、规格、用途结构钢是指符合特定强度和可成形性等级的钢。
可成形性以抗拉试验中断后伸长率表示。
结构钢一般用于承载等用途,在这些用途中钢的强度是一个重要设计标准。
结构钢包括碳素结构钢、合金结构钢、低合金结构钢、耐热结构钢等。
一、碳素结构钢碳素结构钢是碳素钢的一种。
含碳量约0.05%~0.70%,个别可高达0.90%。
碳素钢是指碳含量低于2%,并有少量硅、锰以及磷、硫等杂质的铁碳合金。
工业上常指含碳量小于1.35%,除铁、碳和限量以内的硅、锰、磷、硫等杂质外,不含其他合金元素的钢。
碳素钢的性能主要取决于含碳量。
含碳量增加,钢的强度、硬度升高,塑性、韧性和可焊性降低。
与其它钢类相比,碳素钢使用最早,成本低,性能范围宽,用量最大。
(一)分类1.按含碳量分为:(1)低碳钢(碳含量为0.04%~0.25%) (含碳量小于0.04%时称为工业纯铁。
(2)中碳钢(碳含量为0.25%~0.6%)(3)高碳钢(碳含量为0.6%~1.35%)2.按质量分为:(1)普通碳素钢,其有害杂质磷、硫含量均小于0.05%。
包括:甲类钢:A类钢,保证力学性能乙类钢:B类钢,保证化学成分特类钢:C类钢,保证力学性能和化学成分)如:Q235A,Q235B,Q235C,Q235D,SS400等。
(SS400:第一个S表示钢(Steel),第二个S表示“结构”(Structure),400为下限抗拉强度400MPa,整体表示抗拉强度为400 MPa的普通结构钢)。
(2)优质碳素钢,有害杂质磷、硫含量均小于0.04%;高级优质碳素钢,有害杂质磷、硫含量小于0.03%--如:45,S50C,S45c,P20等等。
3.按用途分为(1)碳素结构钢主要用于制造各种结构件和机器零件,一般属低碳钢和中碳钢;(2)碳素工具钢用于制造刀具、量具、模具等,一般属高碳钢。
(二)普通碳素结构钢简称普通碳素钢,这种钢含有害杂质(P、S等)和非金属夹杂物较多,但价格便宜,用途很多,用量很大,主要用于铁道、桥梁、各类建筑工程,制造承受静载荷的各种金属构件及不重要不需要热处理的机械零件和一般焊接件。
钢的热处理基本工艺
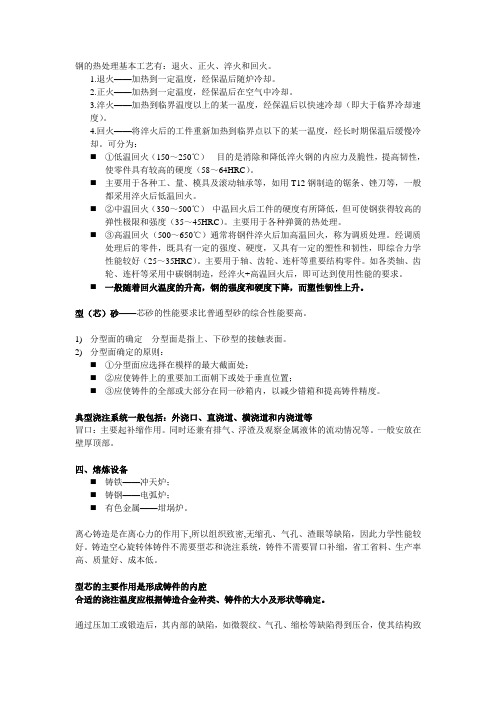
钢的热处理基本工艺有:退火、正火、淬火和回火。
1.退火——加热到一定温度,经保温后随炉冷却。
2.正火——加热到一定温度,经保温后在空气中冷却。
3.淬火——加热到临界温度以上的某一温度,经保温后以快速冷却(即大于临界冷却速度)。
4.回火——将淬火后的工件重新加热到临界点以下的某一温度,经长时期保温后缓慢冷却。
可分为:⏹①低温回火(150~250℃)目的是消除和降低淬火钢的内应力及脆性,提高韧性,使零件具有较高的硬度(58~64HRC)。
⏹主要用于各种工、量、模具及滚动轴承等,如用T12钢制造的锯条、锉刀等,一般都采用淬火后低温回火。
⏹②中温回火(350~500℃)中温回火后工件的硬度有所降低,但可使钢获得较高的弹性极限和强度(35~45HRC)。
主要用于各种弹簧的热处理。
⏹③高温回火(500~650℃)通常将钢件淬火后加高温回火,称为调质处理。
经调质处理后的零件,既具有一定的强度、硬度,又具有一定的塑性和韧性,即综合力学性能较好(25~35HRC)。
主要用于轴、齿轮、连杆等重要结构零件。
如各类轴、齿轮、连杆等采用中碳钢制造,经淬火+高温回火后,即可达到使用性能的要求。
⏹一般随着回火温度的升高,钢的强度和硬度下降,而塑性韧性上升。
型(芯)砂——芯砂的性能要求比普通型砂的综合性能要高。
1)分型面的确定分型面是指上、下砂型的接触表面。
2)分型面确定的原则:⏹①分型面应选择在模样的最大截面处;⏹②应使铸件上的重要加工面朝下或处于垂直位置;⏹③应使铸件的全部或大部分在同一砂箱内,以减少错箱和提高铸件精度。
典型浇注系统一般包括:外浇口、直浇道、横浇道和内浇道等冒口:主要起补缩作用。
同时还兼有排气、浮渣及观察金属液体的流动情况等。
一般安放在壁厚顶部。
四、熔炼设备⏹铸铁——冲天炉;⏹铸钢——电弧炉;⏹有色金属——坩埚炉。
离心铸造是在离心力的作用下,所以组织致密,无缩孔、气孔、渣眼等缺陷,因此力学性能较好。
铸造空心旋转体铸件不需要型芯和浇注系统,铸件不需要冒口补缩,省工省料、生产率高、质量好、成本低。
T10A碳素工具钢的热处理工艺技术分析

T10A碳素工具钢的热处理工艺技术分析T10A碳素工具钢的热处理工艺技术分析【摘要】基于T10A材料的冲裁模具在现代工业领域的应用范围相当广,但冲模失效的现象却普遍存在,其极大地制约着模具制作质量的提高。
冲模失效的影响因素往往与冲裁模的制作环境、冲裁模的制作材料、毛坯的制作质量和冲裁模的热处理工艺间存在着某种关联。
本文就T10A碳素工具钢的热处理工艺技术展开讨论。
【关键词】T10A;热处理工艺;冲裁模;碳素工具钢基于T10A碳素工具钢的冲裁模具在现代机械工业领域的应用非常广,而机械工业的生产效率很大程度上直接取决于冲裁模具的制作质量。
冲模失效是冲裁模具制作的最大阻碍,基于其成因的分析可知,锻造方法的合理性和热处理工艺的改进具有现实意义,即实现冲裁模具使用性能的提高和使用寿命的延长。
本文结合具体案例,就T10A碳素工具钢的热处理工艺展开讨论。
1.冲裁模工作条件和性能要求冲裁模是完成冲压生产的必要装备,即冲压生产工艺方案的落实离不开模具结构的支持。
冲裁模的制作质量和制作精度直接影响着冲压零件的质量和精度,而冲压生产效率和冲裁模使用性能和寿命直接取决于冲裁模结构的先进性和合理性。
源于冲裁模尺寸、形状、精度和生产条件的差异,冲裁模结构和类型也不尽相同。
1.1工作条件冲裁模多用作板材的落料和板材的冲孔。
源于凹凸模具的刃口即为模具的工作部位,其必然会承受模具工作阶段产生的剪切力、冲击力、弯曲力和摩擦力。
1.2性能要求源于冲裁模具的工作条件,即在冲裁阶段,冲裁模具承受着弯曲应力和摩擦力,冲裁模具必须具备足够高的抗弯曲强度、抗压强度、韧性、耐磨性和硬度(见表一),且其还应该具备较小的热处理变形量和低廉的造价。
需注意,冲裁模具的制作板材决定了冲裁模具的性能指标。
就板材厚度而言,冷冲裁模具包括板厚大于1.5mm的厚板冲裁模和板厚≤1.5mm的薄板冲裁模,其中薄板冲裁模要求板材的耐磨性要高;厚板冲裁模要求板材的抗弯曲强度、耐磨性和强韧性要高,以防冲裁模具断裂。
碳素工具钢的加工工艺路线

碳素工具钢的加工工艺路线
1. 材料准备和检验:首先,选取合格的碳素工具钢材料,并进行必要的材料检验,确保符合加工要求。
2. 热处理:将碳素工具钢材料进行热处理,包括加热、保温和冷却,以调整其组织和性能,提高硬度和耐磨性。
3. 钻孔:根据工件要求,采用钻孔工艺在碳素工具钢上进行加工,以便后续的铣削、车削等工序。
4. 铣削:采用数控铣床或加工中心进行加工,将碳素工具钢材料精细加工成所需形状和尺寸。
5. 粗车、精车:根据工件要求,使用车床进行粗车和精车加工,使碳素工具钢材料表面粗糙度和尺寸精度达到要求。
6. 热处理二次加工:对加工后的工件进行再次热处理,以进一步改善材料性能。
7. 精加工和磨削:采用磨床进行精加工和磨削,使碳素工具钢材料达到高精度和光洁度要求。
8. 表面处理:对碳素工具钢材料进行表面处理,例如镀铬、喷涂等,以提高其
耐腐蚀性能和美观度。
9. 检验和包装:对加工后的碳素工具钢产品进行严格的检验,确保其质量符合标准要求,然后进行包装,准备发货。
T12钢热处理工艺要点

金属材料与热处理技术课程设计题目:T12钢热处理工艺课程设计院(系):冶金材料系专业年级:材料1201负责人:陈博唐磊,杨亚西,合作者:谭平,潘佳伟,多杰仁青指导老师:**2013年12月热处理工艺课程设计任务书热处理工艺卡目录基本资料 (4)工艺规范 (5)T12锉刀热处理 (6)1锉刀材料的选择 (6)2锉刀的热处理工艺 (6)2.1 球化退火的具体工艺 (6)2.2 T12钢制锉刀,其工艺路线如下: (6)2.3淬火 (7)2.4回火 (8)2.5 局部淬火 (9)3 热处理后组织金相分析 (9)4质量检验 (14)5缺陷分析 (15)参考文献 (16)表1、碳素工具钢化学成分序号 牌号化学成分 C MnSi S P 不大于1 T7 0.65-0.74 ≤0.40≤0.350.030 0.035 2 T8 0.75-0.84 3 T8Mn 0.80-0.90 0.40-0.60 4T9 0.85-0.94 ≤0.40 5T10 0.95-1.04 6T11 1.05-1.14 7T12 1.15-1.24 8T13 1.25-1.35工艺规范1、临界点温度 (近似值)Ac1 =730°C 、, Accm =820°C 、 Ar1 =700°C2、正火规范正火温度 850~870°c, 空冷, 硬度 269 ~341HBW3、普通退火规范退火温度 760 ~770°C, 保温2 ~4h, 再以 <30°C/h 冷速, 随炉缓冷到 500 ~600°C,出炉空冷。
4、等温球化退火规范1) 760 ~770°C ×2 ~4h, 680~700°C ×4 ~6h, 等温后炉冷到 500 ~600°C, 出炉空冷, 硬度≤207HBW2) 750 ~770°C ×1~2h, 680 ~700°C ×2 --3h, 硬度 179 ~207HBW, 珠光体组织2~4级, 网状碳化物等级≤2级。
碳素工具钢的热处理及其应用

碳素工具钢的热处理及其应用在机械工业生产中会使用各种各样的冲模,通常的冲裁模大多采用T10A,模具制作的好坏,直接影响着生产效率的提高。
根据多年的实践经验,冲模失败的原因,大都集中在尺寸磨损及镦粗折断现象。
造成这些失效的原因是多方面的,正确选材、采用合理的锻造方法、制定和改进热处理工艺,对提高模具的使用效能,延长模具使用寿命尤为重要。
现就以T10A为材质的冲孔及落料模为例,根据模具使用条件、所要求的机械性能、及模具制造过程中所采取的热处理工艺等几个方面进行分析说明。
冲裁模工作条件落料、冲孔和修边模、刃口经多次冲击、摩擦和弯曲应力,多数模具需要有复杂的形状和精确的尺寸,冲孔和落料冲头、经受压、弯、冲击和磨损。
下料剪切经受磨损、压缩和弯曲载荷。
冲裁模使用性能及材料要求由于冲裁模在冲裁时模具承受很大的摩擦力及弯曲应力,因此要求具有高的弯曲和抗压强度、高的耐磨性及足够的韧性,硬度要大,同时希望热处理变形小,价格要低廉。
根据冲裁模的工作条件和性能要求,选用T10A为冲裁模模具材料,由于该材料具有高的强度和耐磨性,容易锻造和切削加工,而且价格便宜,因而广泛采用。
碳素工具钢含碳量高,其塑性与结构钢相比较差,为减轻热处理时的淬裂现象,碳素工具钢的纯洁度要求严格,对S、P含量一般均限制在0 02%~0 03%以下。
毛坯的制作冲裁模,一般要经过锻造进行毛坯操作,碳素工具钢一般锻造性能良好,锻造过程中对表面脱碳要严加注意,加热时间要尽量缩短,其次要严格控制锻压比,一般要大于4,锻造后,空气冷却。
始锻1200℃,终锻800℃。
热处理工艺1 预先热处理锻造后为了给后序的加工、最终热处理工序作好准备,应消除锻件内的应力,改善组织,并使其具有合适的硬度和稳定细小的组织,以利于机械加工。
因此锻件要在毛坏状态下进行预先热处理。
T10A碳素工具钢,一般采取球化退火,使渗碳体成球状均匀分布,若锻件沿晶界出现网状碳化物时,则先进行正火处理,消除网状碳化物,然后进行球化退火。
- 1、下载文档前请自行甄别文档内容的完整性,平台不提供额外的编辑、内容补充、找答案等附加服务。
- 2、"仅部分预览"的文档,不可在线预览部分如存在完整性等问题,可反馈申请退款(可完整预览的文档不适用该条件!)。
- 3、如文档侵犯您的权益,请联系客服反馈,我们会尽快为您处理(人工客服工作时间:9:00-18:30)。
碳素工具钢中碳化物微细化热处理工艺
作者:尹金枝罗秀艳李喜月张伟
来源:《信息技术时代·下旬刊》2018年第04期
摘要:碳素工具钢原料来源易取得,切削加工性良好,热处理后可以得到高硬度和高耐磨性。
本文以T10钢为例研究碳素工具钢的性能。
T10钢淬透性低,且耐热性差(250℃),在淬火加热时不易过热,仍保持细晶粒,韧性尚可,强度及耐磨性均较T7-T9高些,但热硬性低,淬透性仍然不高,淬火变形大。
本文主要围绕T10的四组淬火处理实验及一组对比实验进行金相与硬度的对比。
关键词:碳素工具钢;T10钢;热处理;淬火介质;金相组织图
引言
T10钢优点是可加工性好,来源容易;但淬透性低、耐磨性一般、淬火变形大。
因钢中含合金元素微量,耐回火性差,硬化层浅,因而承载能力有限[1]。
虽有较高的硬度和耐磨性,但小截面工件韧性不足,大截面工件有残存网状碳化物倾向。
T10钢在淬火加热(通常达800℃)时不致于过热,淬火后钢中有过剩未溶碳化物,所以比T8钢具有更高的耐磨性,但淬火变形收缩明显。
由于淬透性差,硬化层往往只有1.5~
5mm;一般采用220~250℃回火时综合性能较佳。
热处理时变形比较大,故只适宜制造小尺寸、形状简单、受轻载荷的模具[2]。
1 化学成分
碳C:0.95~1.04(质量分数,%)、硅Si:≤0.35、锰Mn:≤0.40、硫S:≤0.020、磷P:≤0.030、铬Cr:允许残余含量≤0.25 、镍Ni:允许残余含量≤0.20、铜Cu:允许残余含量
≤0.30。
2 淬火加热温度的选择
淬火时的具体加热温度主要取决于钢的含碳量,可根据Fe-Fe3C相图确定对于T10钢(过共析钢),Ac1为730℃,其加热温度为 Ac1 + 30~50℃,即770℃、780℃、790℃。
若加热温度不足(低于Ac1),则淬火组织中将出现铁素体而造成强度及硬度的降低。
3 保温时间的确定
淬火加热时间是将试样加热到淬火温度所需的时间及在淬火温度停留保温所需时间的总和[3]。
加热时间与钢的成分、工件的形状尺寸、所需的加热介质及加热方法等因素有关,一般
可按照经验公式来估算。
温时间的经验公式为:t=αKD(分钟),其中:D是工件有效厚度,单位为mm; K是加热系数,一般K=1.5~2.0分钟/mm。
T10淬火处理:770-790,淬火介质水、油、冰水、醋。
4 实验结果
实验后测得T10经过四种热处理工艺后的硬度对比如下表所示。
硬度对比分析:
T10钢在处理前的硬度普遍在165~175HBW之间,在經过淬火处理后硬度普遍在60~64HRC之间,即在780℃时即使是不同的淬火介质(水、冰、醋、油)处理后T10钢的硬度都能得到提高,也表明单就对于提高T10钢的硬度方面来讲本实验的不同淬火介质都是可以的。
金相组织分析:
通过本实验对水、冰水、油、醋和对比试样金相组织图的分析。
发现淬火介质为油,冰水的晶粒致密度较醋,水晶粒致密度好一点,且油的晶粒致密度较冰好一些。
但单对于本实验来说相差并不大。
5 总结
通过本实验对硬度和金相组织的结合分析发现淬火介质排序为油,冰水,水,醋。
再进一步说明如果结合实行生产冰水,醋(醋中含醋酸有可能会损坏钢材表面)淬火有很大的局限性即工厂化大型零件淬火的可行为水淬为主。
小型零件淬火水淬油淬均可,但要是对钢材表面有较高的要求推荐油淬。
参考文献
[1]吴晶.丁红燕金属材料实验指导[M].江苏:镇江市江苏大学出版社.2009.
[2]邵红红.金属组织控制技术与设备[M].北京:北京大学出版社.2011.
[3]赵步青.工具用钢热处理手册[M].北京:北京市机械工业出版社.2014。