FMEA失效模式及效应分析
五大工具潜在失效模式与效果分析FMEA
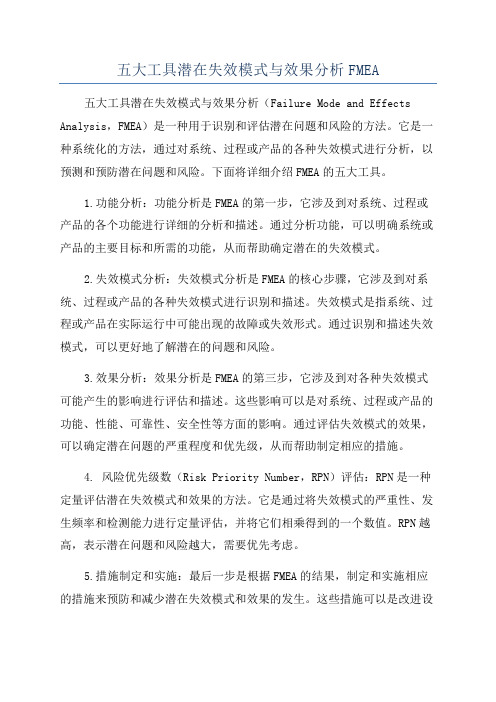
五大工具潜在失效模式与效果分析FMEA 五大工具潜在失效模式与效果分析(Failure Mode and Effects Analysis,FMEA)是一种用于识别和评估潜在问题和风险的方法。
它是一种系统化的方法,通过对系统、过程或产品的各种失效模式进行分析,以预测和预防潜在问题和风险。
下面将详细介绍FMEA的五大工具。
1.功能分析:功能分析是FMEA的第一步,它涉及到对系统、过程或产品的各个功能进行详细的分析和描述。
通过分析功能,可以明确系统或产品的主要目标和所需的功能,从而帮助确定潜在的失效模式。
2.失效模式分析:失效模式分析是FMEA的核心步骤,它涉及到对系统、过程或产品的各种失效模式进行识别和描述。
失效模式是指系统、过程或产品在实际运行中可能出现的故障或失效形式。
通过识别和描述失效模式,可以更好地了解潜在的问题和风险。
3.效果分析:效果分析是FMEA的第三步,它涉及到对各种失效模式可能产生的影响进行评估和描述。
这些影响可以是对系统、过程或产品的功能、性能、可靠性、安全性等方面的影响。
通过评估失效模式的效果,可以确定潜在问题的严重程度和优先级,从而帮助制定相应的措施。
4. 风险优先级数(Risk Priority Number,RPN)评估:RPN是一种定量评估潜在失效模式和效果的方法。
它是通过将失效模式的严重性、发生频率和检测能力进行定量评估,并将它们相乘得到的一个数值。
RPN越高,表示潜在问题和风险越大,需要优先考虑。
5.措施制定和实施:最后一步是根据FMEA的结果,制定和实施相应的措施来预防和减少潜在失效模式和效果的发生。
这些措施可以是改进设计、优化工艺、加强检测和监控等。
通过实施这些措施,可以避免或降低潜在问题和风险的发生。
FMEA是一种非常实用的分析工具,广泛应用于各个行业和领域。
它可以帮助组织识别和评估潜在问题和风险,从而采取预防措施,提高系统、过程或产品的质量和可靠性。
FMEA失效模式和效应分析

1 of 19項 目:過程責任:生產準備者:部 門:制一部零件號:關鍵日期:FMEA 日期:中心隊員:FMEA 編號: 0606242 of 19項 目:過程責任:生產準備者:部 門:制一部零件號:關鍵日期:FMEA 日期:中心隊員:FMEA 編號: 0606243 of 19項 目:過程責任:生產準備者:部 門:制一部零件號:關鍵日期:FMEA 日期:中心隊員:FMEA 編號: 0606244 of 19項 目:過程責任:生產準備者:部 門:制一部零件號:關鍵日期:FMEA 日期:中心隊員:FMEA 編號: 0606245 of 19項 目:過程責任:生產準備者:部 門:制一部零件號:關鍵日期:FMEA 日期:中心隊員:FMEA 編號: 0606246 of 19項 目:過程責任:生產準備者:部 門:制一部零件號:關鍵日期:FMEA 日期:中心隊員:FMEA 編號: 0606247 of 19項 目:過程責任:生產準備者:部 門:制一部零件號:關鍵日期:FMEA 日期:中心隊員:FMEA 編號: 0606248 of 19項 目:過程責任:生產準備者:部 門:制一部零件號:關鍵日期:FMEA 日期:中心隊員:FMEA 編號: 0606249 of 19項 目:過程責任:生產準備者:部 門:制一部零件號:關鍵日期:FMEA 日期:中心隊員:FMEA 編號: 06062410 of 19項 目:過程責任:生產準備者:部 門:制一部零件號:關鍵日期:FMEA 日期:中心隊員:FMEA 編號: 06062411 of 19項 目:過程責任:生產準備者:部 門:制一部零件號:關鍵日期:FMEA 日期:中心隊員:FMEA 編號: 06062412 of 19項 目:過程責任:生產準備者:部 門:制一部零件號:關鍵日期:FMEA 日期:中心隊員:FMEA 編號: 06062413 of 19項 目:過程責任:生產準備者:部 門:制一部零件號:關鍵日期:FMEA 日期:中心隊員:FMEA 編號: 06062414 of 19項 目:過程責任:生產準備者:部 門:制一部零件號:關鍵日期:FMEA 日期:中心隊員:FMEA 編號: 06062415 of 19項 目:過程責任:生產準備者:部 門:制一部零件號:關鍵日期:FMEA 日期:中心隊員:FMEA 編號: 06062416 of 19項 目:過程責任:生產準備者:部 門:制一部零件號:關鍵日期:FMEA 日期:中心隊員:FMEA 編號: 06062417 of 19項 目:過程責任:生產準備者:部 門:制一部零件號:關鍵日期:FMEA 日期:中心隊員:FMEA 編號: 06062418 of 19項 目:過程責任:生產準備者:部 門:制一部零件號:關鍵日期:FMEA 日期:中心隊員:FMEA 編號: 06062419 of 19項 目:過程責任:生產準備者:部 門:制一部零件號:關鍵日期:FMEA 日期:中心隊員:FMEA 編號: 060624。
FMEA失效模式和效果分析
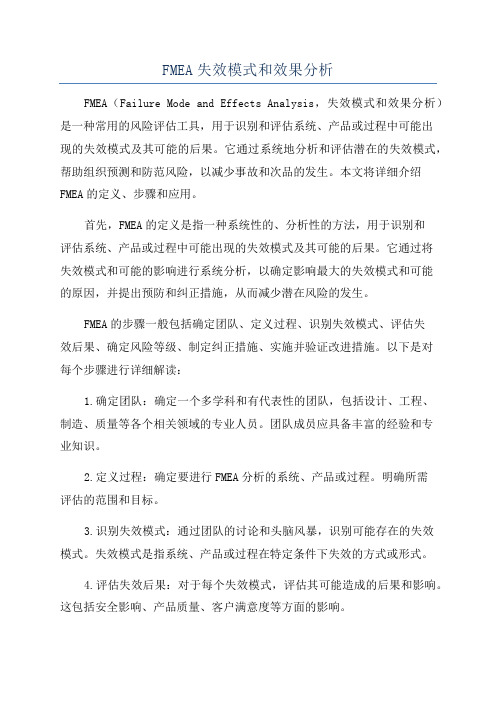
FMEA失效模式和效果分析FMEA(Failure Mode and Effects Analysis,失效模式和效果分析)是一种常用的风险评估工具,用于识别和评估系统、产品或过程中可能出现的失效模式及其可能的后果。
它通过系统地分析和评估潜在的失效模式,帮助组织预测和防范风险,以减少事故和次品的发生。
本文将详细介绍FMEA的定义、步骤和应用。
首先,FMEA的定义是指一种系统性的、分析性的方法,用于识别和评估系统、产品或过程中可能出现的失效模式及其可能的后果。
它通过将失效模式和可能的影响进行系统分析,以确定影响最大的失效模式和可能的原因,并提出预防和纠正措施,从而减少潜在风险的发生。
FMEA的步骤一般包括确定团队、定义过程、识别失效模式、评估失效后果、确定风险等级、制定纠正措施、实施并验证改进措施。
以下是对每个步骤进行详细解读:1.确定团队:确定一个多学科和有代表性的团队,包括设计、工程、制造、质量等各个相关领域的专业人员。
团队成员应具备丰富的经验和专业知识。
2.定义过程:确定要进行FMEA分析的系统、产品或过程。
明确所需评估的范围和目标。
3.识别失效模式:通过团队的讨论和头脑风暴,识别可能存在的失效模式。
失效模式是指系统、产品或过程在特定条件下失效的方式或形式。
4.评估失效后果:对于每个失效模式,评估其可能造成的后果和影响。
这包括安全影响、产品质量、客户满意度等方面的影响。
5.确定风险等级:根据失效模式的后果和可能性,评估其风险等级。
通常使用风险矩阵来划分风险等级,以帮助确定重要性和优先级。
6.制定纠正措施:针对高风险等级的失效模式,制定相应的纠正措施。
这包括预防措施来防止失效的发生,以及纠正措施来解决已经发生的失效。
7.实施并验证改进措施:根据纠正措施的计划,执行相应的改进措施,并进行验证和确认。
确保改进措施的有效性和可行性。
FMEA具有广泛的应用领域。
它可以用于设计过程中的设计FMEA,用于评估产品的可靠性和安全性;也可以用于制造过程中的制造FMEA,用于识别和评估可能导致产品质量问题的制造过程;同时,FMEA还可以用于服务过程中的服务FMEA,用于评估可能影响服务质量和客户满意度的过程。
失效模式与影响分析FMEA
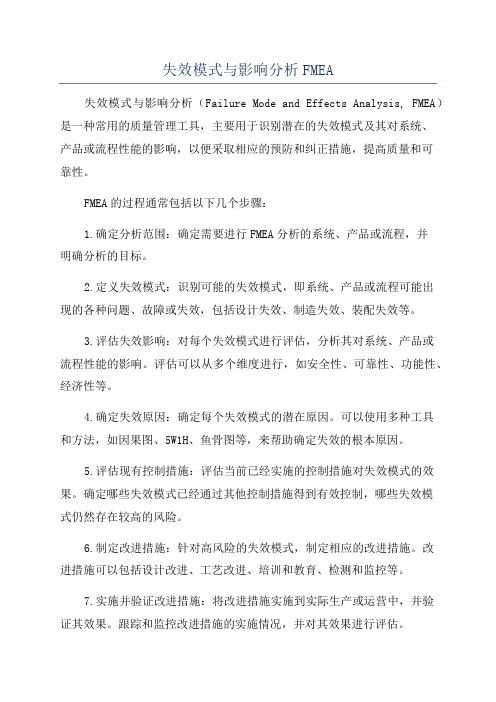
失效模式与影响分析FMEA失效模式与影响分析(Failure Mode and Effects Analysis, FMEA)是一种常用的质量管理工具,主要用于识别潜在的失效模式及其对系统、产品或流程性能的影响,以便采取相应的预防和纠正措施,提高质量和可靠性。
FMEA的过程通常包括以下几个步骤:1.确定分析范围:确定需要进行FMEA分析的系统、产品或流程,并明确分析的目标。
2.定义失效模式:识别可能的失效模式,即系统、产品或流程可能出现的各种问题、故障或失效,包括设计失效、制造失效、装配失效等。
3.评估失效影响:对每个失效模式进行评估,分析其对系统、产品或流程性能的影响。
评估可以从多个维度进行,如安全性、可靠性、功能性、经济性等。
4.确定失效原因:确定每个失效模式的潜在原因。
可以使用多种工具和方法,如因果图、5W1H、鱼骨图等,来帮助确定失效的根本原因。
5.评估现有控制措施:评估当前已经实施的控制措施对失效模式的效果。
确定哪些失效模式已经通过其他控制措施得到有效控制,哪些失效模式仍然存在较高的风险。
6.制定改进措施:针对高风险的失效模式,制定相应的改进措施。
改进措施可以包括设计改进、工艺改进、培训和教育、检测和监控等。
7.实施并验证改进措施:将改进措施实施到实际生产或运营中,并验证其效果。
跟踪和监控改进措施的实施情况,并对其效果进行评估。
通过进行FMEA分析,可以帮助组织识别和管理潜在的风险,提前采取预防措施,减少系统、产品或流程的失效概率,以实现质量和可靠性的提升。
FMEA分析可以应用于各个领域,如制造业、医疗设备、航空航天、汽车等。
FMEA的应用具有以下几个特点和优势:1.预防导向:FMEA分析主要关注于预防失效模式的发生,通过分析潜在的失效原因和影响,预测可能的失效模式,制定相应的预防措施,从而避免质量问题的发生。
2.多维度评估:FMEA分析不仅关注失效模式的影响对系统、产品或流程的影响,还可以从多个维度进行评估,如安全性、可靠性、功能性、经济性等,以全面了解失效模式的风险。
FMEA失效模式及后果分析手册精选全文

可编辑修改精选全文完整版FM E A 失效模式及后果分析手册FMEA (Failue Mode &Effect Analgsis ) Failue :失效、失败、不良 Mode :模式Effect :后果、效应、影响 Analgsis :分析一、FMEA 思维逻辑方法:D ’FMEA —→分析着重点BOM 表的零件及组装件P ’FMEA —→分析着重点OPC/AC 的零件加工及组装的工艺流程PRN 高风险优先系数 重点管理原则控制重点少数,不重要大多数列为次要管理 轻重缓急,事半功倍类比量产品(模块化) 工艺流程 过程参数/工艺条件 质量特性类比量产品 质量不良履历失败经验产品病历卡预设未来新产品投产后可能/潜在的会出现类似的不良事前 分析原因 整改措施(鱼刺图)先期产品质量策划结果控制计划(欧美) QC 工程表(台/日)新产品投产施工的要求监视和测量(首中末件检查)开发新产品例:有20项不良,前3项不良占70%,对策能解决50%的不良,70%*50%=35%后17项不良占30%,对策能解决100%的不良,30%*100%=30%①质量管理AC 柏拉图分析②物料管理MC 物料ABC法避免待料停工目的降低库存量的成本二、在何种情况下应进行FMEA分析:新产品开发阶段1、RP N≥1002、严重度/发生度/难检度(任一项)≥7;3、严重度≥7,发生度≥3;4、发生度≥5,难检度≥4量产阶段秉持持续改善的精神三、FMEA建立与更新时机1、新产品开发时;2、设计变更时(材质变更,BOM变更);3、工程变更;4、检验方法变更(检验设备/项目/频度)5、定期审查更新(建议每季度修订,至少也要每半年)四、FMEA分析表作成说明35%>30%重效果大,轻效果小活性化文件随时更新有效版本的识别(以修订日期)1、增加零件编号与名称:与BOM 表一致(D ’FMEA 分析,着眼在构成零件及组装件);2、增加工序编号与名称:与OPC/AC 表一致(P ’FMEA 分析,着眼在加工与组装工艺流程,D ’FMEA 可省略)3、功能与要求:已含外观、颜色、尺寸及ES TEST 功能质量要求;4、潜在失效模式:类比量产品质量不良履历(历史档)→产量履历→失效分析累积5、潜在失效效应(后果):万一不良时会造成的后果,如影响安全性/功能性/一般性,必须站在广义的客户中思考,包含: ● 下工程● 直接客户:下购销合同者/客户:如代理商 ● 最终客户:user/消费者6、严重度:参照对照表予以评估,复合型≥7;功能性4~6;一般性<4;7、分类(等级)class :与CC/SC 管制特性计划清单一致,包含符号识别,如FORD ▽,通用,依客户指定或本司对等的符合标注。
FMEA失效分析与失效模式分析全

擦伤或损坏)。 由于横向性能差而在锻件中出现分离线的失效现象。
11
在服役条件下由于质量恶化而产生失效的原因包括
过载或未预见的加载条件。 磨损(磨蚀、因过度磨损而咬住、粘住、擦伤、气蚀)。 腐蚀(包括化学接触、应力腐蚀、腐蚀疲劳、脱锌、铸铁石
找出被分析对象的“单点故障”。所谓单点故障是指这种故障单独发 生时,就会导致不可接受的或严重的影响后果。一般说来,如果单点 故障出现概率不是极低的话,则应在设计、工艺、管理等方面采取切 实有效的措施。产品发生单点故障的方式就是产品的单点故障模式。
为制定关键项目清单或关键项目可靠性控制计划提供依据。 为可靠性建模、设计、评定提供信息。 揭示安全性薄弱环节,为安全性设计(特别是载人飞船的应急措施、
16
什么是失效分析?
失效分析:考察失效的构件及失效的情景(模式), 以确定失效的原因。
失效分析的目的:在于明确失效的机理与原因。改 进设计、改进工艺过程、正确地使用维护。
失效分析的主要内容:包括明确分析对象,确定失 效模式,研究失效机理,判定失效原因,提出预防 措施(包括设计改进)。
17
失效分析的要点?
失效模式的判断分为定性和定量分析两个方面。在一般 情况下,对一级失效模式的判断采用定性分析即可。而 对二级甚至三级失效模式的判断,就要采用定性和定量、 宏观和微观相结合的方法。
19
一级失效模式的分类
20 主要失效模式的分类与分级
21
如某型涡轮叶片在第一榫齿处发生断裂,通过断口 的宏观特征可确定一级失效模式为疲劳失效。然后 通过对断口源区和扩展区特征分析和对比,并结合 有限元应力分析等,可作出该叶片的断裂模式为起 始应力较大的高周疲劳断裂的判断,即相当于作出 了三级失效模式的判断。
失效模式与效应分析 (FMEA)

失效模式與效應分析 (FMEA)何謂「FMEA、FMECA」?FMECA 是兩種分析技術的總稱:1.FMEA﹝故障型式及其影響分析﹞2.CA﹝Criticality Analysis, 嚴重度分析﹞與失誤樹分析一樣,故障型式影響及嚴重度分析﹝failure modes, effects and criticality analysis, 簡稱 FMECA﹞,首先在美國國防科技中研究發展,且在國防部各機構中普遍應用﹝DOD, 1980﹞,後來漸應用於工業界。
在核能、化工、石化、海上鑽油等高風險工業中,自不例外。
工業界的設計工程師與可靠度﹝Reliability﹞工程師常運用 FMECA 以預測複雜的產品的可靠度,預估一件產品的零件在某特定的時間及情況下,如何失去其功能,故障的次數是多少,故障之後對其他零件或對整個系統會產生怎樣的影響等。
FMECA 的功用不止於可靠度一端,其分析所得的資料,尚可作下列用途:1.協助評估所設計的裝置,如複聯系統﹝Redundancy﹞、故障偵測,以及fail-safe 特性等。
2.對測試、採購﹝Procurement﹞、檢查、改善措施等提供先後順序的參考資料。
3.提供失誤隔絕﹝Fault isolation﹞及維護性﹝Maintainability﹞分析的參考資料。
4.提供系統安全分析﹝如失誤樹分析﹞所需的硬體資料。
FMECA 可在系統週期的任一階段中,依計劃內容之需要,以不同深淺程度實施,但在設計階段的初期,一旦所需的設備確定之後,即應實施。
FMECA 的對象是系統或子系統中的零組件,尤其對於複雜的系統中的設備零件,最能發揮其故障針砭的功效,此為其他系統安全分析技術不能望其項背之處。
但因其分析對象大多限於硬體,故對於人為因素和作業環境因素較少納入分析考慮範圍。
因此,如能將 FMECA 與失誤樹分析合併使用,必更能瞭解整個作業系統的危害,進而防範事故生。
摘於【環安 Q&A】。
风险评估技术失效模式和效应分析FMEA及失效模式效应和危害度分析FMECA

失效模式和效应分析(FMEA)及失效模式、效应和危害度分析(FMECA) 1 概述失效模式和效应分析(Failure Mode and Effect Analysis,简称FMEA)是用来识别组件或系统未能抵达其设计意图旳措施。
FMEA用于识别:●系统各部分所有潜在旳失效模式(失效模式是被观测到旳是失误或操作不妥);●这些故障对系统旳影响;●故障原因;●怎样防止故障及/或减弱故障对系统旳影响。
失效模式、效应和危害度分析(Failure Mode and Effect and Criticality Analysis,简称FMECA)拓展了FMEA旳使用范围。
根据其重要性和危害程度,FMECA可对每种被识别旳失效模式进行排序。
这种分析一般是定性或半定量旳,不过使用实际故障率也可以定量化。
2 用途FMEA有几种应用:用于部件和产品旳设计(或产品)FMEA;用于系统旳系统FMEA;用于制造和组装过程旳过程FMEA;服务FMEA和软件FMEA。
FMEA/ FMECA可以在系统旳设计、制造或运行过程中使用。
然而,为了提高可靠性,改善在设计阶段更轻易实行。
FMEA/ FMECA也合用于过程和程序。
例如,它被用来识别潜在医疗保健系统中旳错误和维修程序中旳失败。
FMEA/FMECA可用来:●协助挑选具有高可靠性旳替代性设计方案;●保证所有旳失效模式及其对运行成功旳影响得到分析;●列出潜在旳故障并识别其影响旳严重性;●为测试及维修工作旳规划提供根据;●为定量旳可靠性及可用性分析提供根据。
它大多用于实体系统中旳组件故障,不过也可以用来识他人为失效模式及影响。
FMEA及FMECA可认为其他分析技术,例如定性及定量旳故障树分析提供输入数据。
3 输入数据FMEA及FMECA需要有关系统组件足够详细旳信息,以便对各组件出现故障旳方式进行故意义旳分析。
信息也许包括:●正在分析旳系统及系统组件旳图形,或者过程环节旳流程图;●理解过程中每一步或系统构成部分旳功能;●也许影响运行旳过程及环境参数旳详细信息;●对特定故障成果旳理解;●有关故障旳历史信息,包括既有旳故障率数据。
FMEA失效分析与失效模式分析
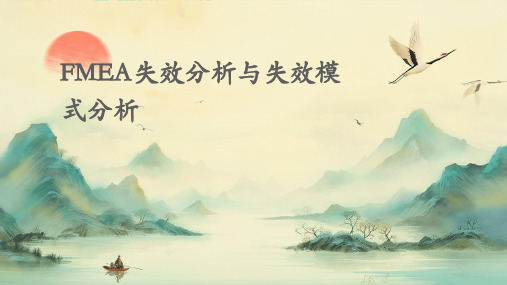
FMEA失效分析通常包括失效模式分析作为其一部分,两者都是质量 保证和可靠性工程的重要工具。
02
FMEA失效模式分析
失效模式的定义与分类
失效模式定义
在产品或过程中,可能导致产品或系 统不能达到预期功能的现象或问题。
失效模式分类
按失效的性质可分为功能失效、潜在 失效、外观失效等;按失效的原因可 分为设计缺陷、制造缺陷、使用不当 等。
06
案例研究
案例一:汽车刹车系统的FMEA失效分析
总结词
全面分析,预防为主
详细描述
通过对汽车刹车系统进行FMEA失效分析, 识别出潜在的失效模式和原因,并采取相应 的预防措施,确保刹车系统的可靠性和安全
性。
案例二
要点一
总结词
细致入微,失效定位
要点二
详细描述
对电子产品电路板进行FMEA失效模式分析,准确定位失 效模式和原因,提出改进措施,提高电路板的可靠性和稳 定性。
失效风险
指产品或系统在实现其功能过程中可能出现的故障、异常或性能下降的风险。
分类
按照失效模式和影响分析(FMEA)的方法,失效风险可分为功能失效风险和潜在失效 风险。
失效风险的分析方法
01
故障树分析(FTA)
通过建立故障树,分析系统各部件的故障对系统整体性能的影响。
02
事件树分析(ETA)
通过建立事件树,分析系统各事件的发生对系统性能的影响。
失效模式的分析方法
故障树分析法
01
通过建立故障树,分析导致故障的各种因素,确定故障发生的
概率和影响程度。
故障模式与影响分析法
02
分析产品或系统的各种故障模式,评估其对系统功能的影响程
失效模式与效应分析(FMEA)
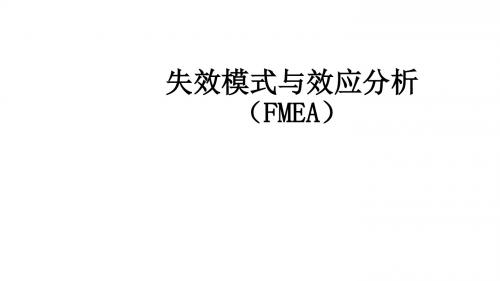
失效模式与效应分析 (FMEA)
起源
FMEA大约于1950年代由美国Grumman公 司提出,当时由于飞机系统复杂并且需要 预防失效情况发生,因此渐渐发展成安全 性与可靠度的设计模式,以期能够增加产 品质量,降低不良问题的发生。
FMEA具体项目
• 累积经验,早期发现失效原因及采取因应之道。 • 促进设计改良。 • 改善操作方法及建立维护计划的参考。 • 帮助操作人员之训练,让员工能在短期内找出 失效原因与解决之法。 • 公司人员异动时,能让员工快速上手。
FMEA表格建立
失效机率
字码体系
严重性分析
多要因评估法
单要因评估法
列表评估法
失效报告
范例
范例
范例
范例
范例
故障树分析符号
故障树分析范例
故障树简化
故障树关键性估计范例
结论
• 透过FMEA模式,可有效找出来自品失效原因,进而解决问题,是一 个可靠性的解析手法。 • 藉由实施FTA ,能让不希望发生的事情明确化,并能判别事件发 生时所带来的一些事象与对成品的影响。
FMEA失效模式及效果分析

ABC有限公司FMEA失效模式及后果分析1.0目的2.0范围3.0责任4.0定义5.0参考6.0文件7.0程序7.3 过程PFMEA展开步骤(七步法):ABC有限公司ABC有限公司B2.7PFMEA表格提示步骤七PFMEA步骤七由各组织单独管理,不在PFMEA表格中记录。
7.4严重度(S)7.4.1严重度是单一的FMEA范围内的相对定级结果;其数值的降低只有通过设计更改或重新设计才能够实现;7.4.2严重度(S)评价准则:ABC 有限公司7.5 发生率(O)7.5.1为保证连续性,应采用一致的定级方法确定发生频度;发生率的降低应通过设计更改或过程更改来控制;ABC有限公司7.6探测率(D)7.6.1探测率是一个在某一FMEA范围内的相对级别,为了获得一个较低的定级,通常计划的过程控制必须予以改进;ABC有限公司7.7 措施优先级(AP)7.7.1 FMEA提供了所有1000种S、O、D的可能组合。
该方法首先着重于严重度,其次为频度,然后为探测度。
其逻辑遵循了FMEA的失效预防目的。
7.7.2 措施优先级表7.8PFMEA是一种动态文件,在出现下列情况时,需要对文档进行评审和更新,但不限于:7.8.1顾客投诉、内外部退货;7.8.2工程更改或产品特性更改;7.8.3制造/生产过程出现异常时;7.8.4新零件、工序或操作环境的改善。
7.9 制作PFMEA的两个假设:7.9.1PFMEA假设被定义的产品符合设计意图;7.9.2 假设投入生产的物料及上工序流下来的产品为合格品。
7.10PFMEA使用时机:PFMEA为活动性的文件,它应该在APQP五个阶段(对IATF 16949)中的第三个阶段(过程的设计和开发阶段)在制作过程流程图后,根据过程流程图作成。
FMEA失效模式及效应分析介绍

FMEA失效模式及效应分析介绍FMEA(Failure Mode and Effects Analysis)是一种用于识别、评估和减轻系统、产品或过程中可能的失效模式及其可能的效应的工具和方法。
它的目标是通过提前识别和纠正潜在的问题,从而提高系统的可靠性和安全性。
FMEA通常由一个跨职能的团队进行,包括设计工程师、工艺工程师、质量控制人员等。
这个团队将系统、产品或过程分解成多个组成部分,然后针对每个部分,逐个分析其可能的失效模式以及这些失效模式可能引起的效应。
在进行FMEA之前,团队首先需要定义一个适当的评估标准,用于对失效模式和效应进行风险评估。
评估标准通常包括失效的概率、严重性和可能性等方面。
然后,通过对每个失效模式和效应进行评估,确定其风险等级。
常用的评估方法包括风险矩阵、风险优先级数等。
FMEA的关键步骤包括:1.确定分析的范围:确定要进行FMEA的系统、产品或过程的范围,并明确所有相关的组成部分。
2.分析失效模式:对每个组成部分,团队成员进行头脑风暴,识别可能的失效模式。
失效模式是指一个组成部分不能正常工作或无法满足指定要求的一种方式。
3.分析失效效应:对于每个失效模式,分析团队评估其可能引起的效应,包括对系统性能、安全性和可靠性的影响。
这些效应需要根据评估标准进行量化或定性评估。
4.评估风险等级:通过将失效模式和效应的概率、严重性和可能性等因素综合考虑,评估每个失效模式和效应的风险等级。
这有助于团队确定哪些失效模式和效应应优先处理。
5.提出改进措施:根据风险等级,团队制定相应的改进计划。
这可以包括重新设计、改变制造流程、增加可靠性测试等措施,以降低失效模式和效应的风险。
FMEA的优点在于:1.提前识别风险:通过系统的、结构化的方法,FMEA能够识别并提前预测系统或产品中的潜在问题,从而及早采取措施来减轻或消除这些风险。
2.优化设计:通过对失效模式和效应的分析,FMEA可以帮助设计团队发现并改进设计中的潜在问题,从而提高系统的可靠性和性能。
IATF16949失效模式和效果分析FMEA控制程序.docx
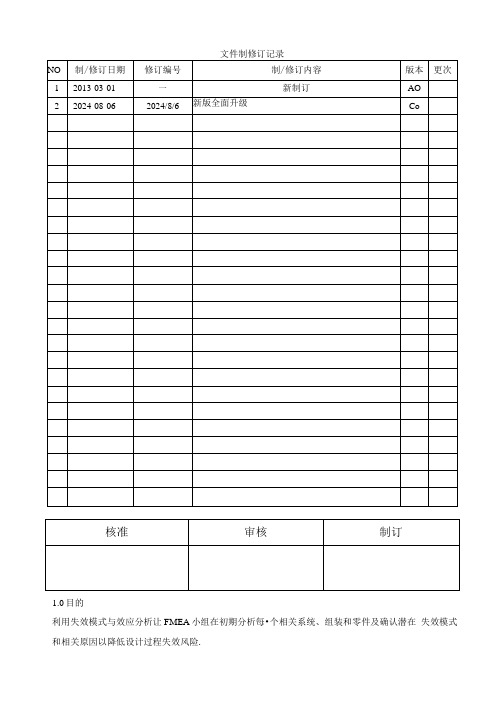
1.0目的利用失效模式与效应分析让FMEA小组在初期分析每•个相关系统、组装和零件及确认潜在失效模式和相关原因以降低设计过程失效风险.2.0适用范圉本公司所有汽车件五金系列新产品及新工艺均适用。
注:非汽车件产品不强制要求执行该程序.3.0权责FMEA小组负责FMEA运作.4.0定义4.1 FMEA:利用工程去分析产品零、组件可能失效的模式及原因,研究失效的模式对系统可能产生的影响及严重程度:4. 2失效4. 2.1在规定条件下(环境、操作、时间等)不能完成既定功能;4. 2. 2在规定条件卜.,产品参数值不能维持在规定的上卜限之间。
4. 2. 3产品在工作范围内,导致零组件如性能失效、重金属超标等正常规范以外之异常现象均属之。
4.3系统:此处专指FMEA之对象物,或为零件之某部位、或为零件、或为组合、或为总成、或为机构…。
4.3.1子系统:系统之构成件,如零件之对组合,组合之对总成等,为上游工程(前制程)状态。
5.0作业内容5.1失效模式与效应分析不是依靠制程管制来克服,是用现有技术或考虑制造及组装过程的限制来减少设计上潜在的问题,如:5.1.1需要的工艺流程图:5.1.2组装的空间或要求的工具:5. 1.3产品材料的限制:5.L 4制程能力或效能。
5.2FMEA 编号:6. 2.1填入FMEA文件编号以便可以追踪使用:7. 2. 2 FMEA表编号,依产品编订.8.3型别:填入要分析设计产品型别.5.4FMEA日期:填入最初FMEA被完成日期,和最新被修订日期。
5.5关键日期:填入FMEA计划完成的日期。
该日期不能超过开始计划生产日期。
5.6项目N0:以流水号厂99方式编入。
同一项目再细分时允许以“一”(允号)方式编号,例4T, 4-2, 4-3。
5.7部位(构成部品)名称:填入被分析之构成部品或工程名称,使用之名词应和预定发行之工程规格上所显示的相符.5. 8机能:尽可能简洁地依设计意图填入被分析部位的机能。
失效模式与效应分析(FMEA)

失效模式与效应分析(FMEA)一、定义失效模式与效应分析(failure mode and effects analysis,FMEA)是一种前瞻性的管理模式,是在行动之前就认清问题并预防问题发生的分析。
FMEA由失效模式(failure oode,FM)及效应分析(effects analysis,EA)两部分组成。
其中,失效模式是指能被观察到的错误或缺陷(俗称安全隐患),应用于护理质量管理中就是指任何可能发生的护理不良事件;效应分析是指通过分析该失效模式对系统的安全和功能的影响程度,提出可以或可能采取的预防改造措施,以减少缺陷,提高质量。
二、目的、目标FMEA的目的是防患未然;设计屏障,让事情不要发生;降低损害,即使有风险存在,也是可容许的最低风险;是发现、评价流程中潜在的失效及其后果,找到能够避免或减少这些潜在失效的措施,并将上述过程文件化。
FMEA的主要目标是分析现有系统(流程)或将建立之系统(流程):哪里会出错?一旦出错会有多糟糕?哪里需要修正以避免事故发生?三、执行时机1、新设计的流程2、修改现行的流程3、旧的流程用于新的情境中四、实施步骤(一)步骤一:确认问题选择那些高风险或非常薄弱的程序进行研究。
高风险流程的特性有:高复杂性(步骤多)的作业、高差异性的输入来源、未标准化的作业、紧密相依的作业、作业时间间隔太紧或太松、高度依赖人员的判断或决定。
医疗行为中的高风险流程有:用药、病人处于危险的操作流程(放射治疗,CT扫描,磁振造影)、输血与输成分血、抑制作用的药物、对高危人群进行照顾或提供服务、与复苏相关等。
(二)步骤二:组建团队组建一个多学科的综合FMEA团队,团队中至少应该有一个领导者、一个所硏究流程方面的专家、一个FMEA咨询师(即FMEA专家,可以为团队领导者提供建议,保证FMEA的顺利实施)、一个对所研究流程不太熟悉的人(可以从不同的角度和方面提出有价值的建议)。
一般建议团队成员在6〜10人之间,以便于管理,所有成员必须接受过FMEA培训。
失效模式及效应分析 FMEA

•硬體設備失效:故障狀況 ( 如:短路、漏電、 斷裂、變形、腐蝕、鬆動、磨耗、卡死、洩漏 等)
•材料失效:不良內容(如:尺寸不良、材質錯誤、 變形、漏油及油污)
•對於服務業而言可以「服務特性之失 效」,作 為失效模式思考方向。此 外, 當 FEMA 表內同時出現二個以上不正常 及故障項目時,應修改成各自不同的名 稱,然後再記入 FEMA 表內。
評價準則-失效影響嚴重度 S:
嚴重性 基
準
10
危險無預警,直接影響安全
9
危險可預警,直接影響安全
8
失去主要功能,END USER 無法工作
7
主要功能降低,END USER 仍可工作,客戶會不滿意
主機能動作,影響週邊方便性或舒適性之項目無法工 6
作,客戶感覺不方便
主機能動作,週邊方便性或舒適性之項目功能降低,客 5
失效模式及效應分析 FMEA
前言
• FMEA(Failure Mode And Effect Analysis) 自 1950 年代初期就被當做是 航空機用動力計劃的解析法,到了實施 阿波羅計劃獲得重大成就後,即被廣泛 推廣開來。此外 FMEA 亦是 QS9000 中 設計活動中要求應適當具備的技術。
產品設計開發的 FMEA 表作成
•記入 FMEA 對象的品名及名稱 。 •記入 FMEA 對象的識別編號 。 •依照製造工程順序在「名稱」欄位寫上
工程名稱、使用及設備投入的材料 。 •將工程、使用設備及投入材料這些原本
應具備的功能記入在「功能」欄內 。 •失效模式 (公司可先定義失效模式)
FMEA失效模式与效应分析

FMEA失效模式与效应分析
FMEA是一种常用的质量管理方法,全称为“失效模式和影响分析”(Flure Mode and Effects Analysis)。
它是一种定量分析工具,用于衡量所研究系统的某种失效模式和这种失效模式带来的效应。
它可以通过对失效模式进行系统的分析和归纳,找出并解决潜在的失效模式,从而提高产品、过程和系统的质量和可靠度。
下面我们来详细了解一下FMEA失效模式与效应分析。
一、FMEA的基本概念
FMEA是一种质量管理工具,可以对产品制造或过程设计进行评估,以识别可能出现的失效模式,并预先采取相应的改进措施以消除或减轻风险。
该方法可以帮助组织识别潜在问题并提供预防性控制,以最大程度地降低可能的风险。
FMEA通常包括以下步骤:
1.识别和描述潜在的失效模式;
2.评估和量化失效模式的可能性、严重性和检测能力(即失效模式对产品质量和可靠性的影响);
3.识别并建议风险缓解措施。
二、FMEA的分类
FMEA可以分为设计FMEA(DFMEA)和过程FMEA(PFMEA)两种类型。
1.设计FMEA( DFMEA)
1。