电子类文献中英文翻译(发电机)
电力系统毕业论文中英文外文文献翻译
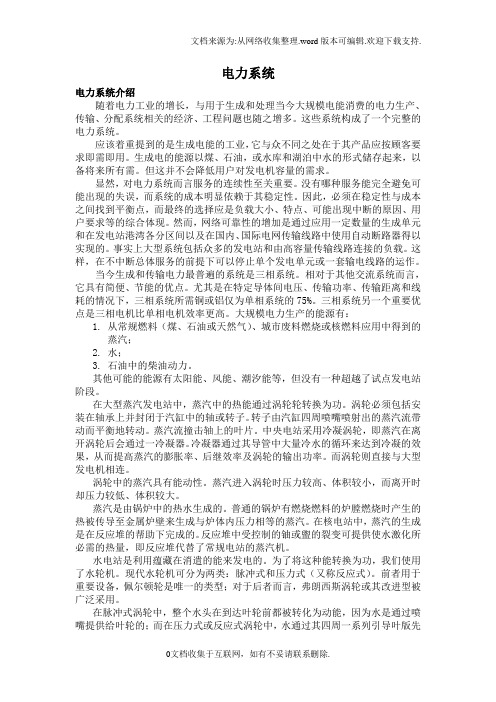
电力系统电力系统介绍随着电力工业的增长,与用于生成和处理当今大规模电能消费的电力生产、传输、分配系统相关的经济、工程问题也随之增多。
这些系统构成了一个完整的电力系统。
应该着重提到的是生成电能的工业,它与众不同之处在于其产品应按顾客要求即需即用。
生成电的能源以煤、石油,或水库和湖泊中水的形式储存起来,以备将来所有需。
但这并不会降低用户对发电机容量的需求。
显然,对电力系统而言服务的连续性至关重要。
没有哪种服务能完全避免可能出现的失误,而系统的成本明显依赖于其稳定性。
因此,必须在稳定性与成本之间找到平衡点,而最终的选择应是负载大小、特点、可能出现中断的原因、用户要求等的综合体现。
然而,网络可靠性的增加是通过应用一定数量的生成单元和在发电站港湾各分区间以及在国内、国际电网传输线路中使用自动断路器得以实现的。
事实上大型系统包括众多的发电站和由高容量传输线路连接的负载。
这样,在不中断总体服务的前提下可以停止单个发电单元或一套输电线路的运作。
当今生成和传输电力最普遍的系统是三相系统。
相对于其他交流系统而言,它具有简便、节能的优点。
尤其是在特定导体间电压、传输功率、传输距离和线耗的情况下,三相系统所需铜或铝仅为单相系统的75%。
三相系统另一个重要优点是三相电机比单相电机效率更高。
大规模电力生产的能源有:1.从常规燃料(煤、石油或天然气)、城市废料燃烧或核燃料应用中得到的蒸汽;2.水;3.石油中的柴油动力。
其他可能的能源有太阳能、风能、潮汐能等,但没有一种超越了试点发电站阶段。
在大型蒸汽发电站中,蒸汽中的热能通过涡轮轮转换为功。
涡轮必须包括安装在轴承上并封闭于汽缸中的轴或转子。
转子由汽缸四周喷嘴喷射出的蒸汽流带动而平衡地转动。
蒸汽流撞击轴上的叶片。
中央电站采用冷凝涡轮,即蒸汽在离开涡轮后会通过一冷凝器。
冷凝器通过其导管中大量冷水的循环来达到冷凝的效果,从而提高蒸汽的膨胀率、后继效率及涡轮的输出功率。
而涡轮则直接与大型发电机相连。
直流电动机中英文对照外文翻译文献

中英文对照外文翻译文献(文档含英文原文和中文翻译)外文文献:DC Motor CalculationsOverviewNow that we have a good understanding of dc generators, we can begin our study of dc motors. Direct-current motors transform electrical energy into mechanical energy. They drive devices such as hoists, fans, pumps, calendars, punch-presses, and cars. These devices may have a definite torque-speed characteristic (such as a pump or fan) or a highly variable one (such as a hoist or automobile). The torque-speed characteristic of the motor must be adapted to the type of the load it has to drive, and this requirement has given rise to three basic types of motors: 1.Shunt motors 2. Series motors 3. Compound motors Direct-current motors are seldom used in ordinary industrial applications because all electric utility systems furnish alternating current. However, for special applications such as in steel mills, mines, and electric trains, it is sometimes advantageous to transform the alternating current into direct current in order to use dc motors. The reason is that the torque-speed characteristics of dc motors can be varied over a wide range while retaining high efficiency. Today, this general statement can be challenged because the availability of sophisticated electronic drives has made it possible to use alternating current motors for variable speed applications. Nevertheless, there are millions of dc motors still in service and thousands more are being produced every year.Counter-electromotive force (cemf)Direct-current motors are built the same way as generators are; consequently, a dc machine can operate either as a motor or as a generator. To illustrate, consider a dc generator in which the armature, initially at rest, is connected to a dc source E s by means of a switch (Fig. 5.1). The armature has a resistance R, and the magnetic field is created by a set of permanent magnets.As soon as the switch is closed, a large current flows in the armature because its resistance is very low. The individual armature conductors are immediately subjected to a force because they are immersed in the magnetic field created by the permanent magnets. These forces add upto produce a powerful torque, causing the armature to rotate.Figure 5.1 Starting a dc motor across the line.On the other hand, as soon as the armature begins to turn, a second phenomenon takes place: the generator effect. We know that a voltage E o is induced in the armature conductors as soon as they cut a magnetic field (Fig. 5.2). This is always true, no matter what causes the rotation. The value and polarity of the induced voltage are the same as those obtained when the machine operates as a generator. The induced voltage E o is therefore proportional to the speed of rotation n of the motor and to the flux F per pole, as previously given by Eq. 5.1:E o = Zn F/60 (5.1)As in the case of a generator, Z is a constant that depends upon the number of turns on the armature and the type of winding. For lap windings Z is equal to the number of armature conductors.In the case of a motor, the induced voltage E o is called counter-electromotive force (cemf) because its polarity always acts against the source voltage E s. It acts against the voltage in the sense that the net voltage acting in the series circuit of Fig. 5.2 is equal to (E s - Eo) volts and not (E s + E o) volts.Figure 5.2 Counter-electromotive force (cemf) in a dc motor.Acceleration of the motorThe net voltage acting in the armature circuit in Fig. 5.2 is (E s- E o) volts. The resulting armature current /is limited only by the armature resistance R, and soI = (E s- E o)IR (5.2)When the motor is at rest, the induced voltage E o= 0, and so the starting current isI = E s/RThe starting current may be 20 to 30 times greater than the nominal full-load current of the motor. In practice, this would cause the fuses to blow or the circuit-breakers to trip. However, if they are absent, the large forces acting on the armature conductors produce a powerful starting torque and a consequent rapid acceleration of the armature.As the speed increases, the counter-emf E o increases, with the result that the value of (E s—E o)diminishes. It follows from Eq. 5.1 that the armature current / drops progressively as the speed increases.Although the armature current decreases, the motor continues to accelerate until it reaches a definite, maximum speed. At no-load this speed produces a counter-emf E o slightly less than the source voltage E s. In effect, if E o were equal to E s the net voltage (E s—E o) would become zero and so, too, would the current /. The driving forces would cease to act on the armature conductors, and the mechanical drag imposed by the fan and the bearings would immediately cause the motor to slow down. As the speed decreases the net voltage (E s—E o) increases and so does the current /. The speed will cease to fall as soon as the torque developed by the armature current is equal to the load torque. Thus, when a motor runs at no-load, the counter-emf must be slightly less than E s so as to enable a small current to flow, sufficient to produce the required torque.Mechanical power and torqueThe power and torque of a dc motor are two of its most important properties. We now derive two simple equations that enable us to calculate them.1. According to Eq. 5.1 the cemf induced in a lap-wound armature is given byE o = Zn F/60Referring to Fig. 5.2, the electrical power P a supplied to the armature is equal to the supply voltage E s multiplied by the armature current I:P a = E s I (5.3)However, E s is equal to the sum of E o plus the IR drop in the armature:E s = E o + IR (5.4)It follows thatP a= E s I= (E o + IR)I=E o I + I2R (5.5)The I2R term represents heat dissipated in the armature, but the very important term E o I is the electrical power that is converted into mechanical power. The mechanical power of the motor is therefore exactly equal to the product of the cemf multiplied by the armature currentP = E o I (5.6)whereP = mechanical power developed by the motor [W]E o= induced voltage in the armature (cemf) [V]I = total current supplied to the armature [A]2. Turning our attention to torque T, we know that the mechanical power P is given by the expressionP = nT/9.55 (5.7)where n is the speed of rotation.Combining Eqs. 5.7,5.1, and 5.6, we obtainnT/9.55 = E o I= ZnFI/60and soT =Z F I/6.28The torque developed by a lap-wound motor is therefore given by the expressionT =Z F I/6.28 (5.8)whereT = torque [N×m]Z = number of conductors on the armatureF = effective flux per pole [Wb]*/ = armature current [A]6.28 = constant, to take care of units[exact value = 2p]Eq. 5.8shows that we can raise the torque of a motor either by raising the armature current or by raising the flux created by the poles.Speed of rotationWhen a dc motor drives a load between no-load and full-load, the IR drop due to armature resistance is always small compared to the supply voltage E s. This means that the counter-emf E s is very nearly equal to E s.On the other hand, we have already seen that Eo may be expressed by the equationE o = Zn F/60Replacing E o by E s we obtainE s = Zn F/60That is,wheren = speed of rotation [r/min]E s = armature voltage [V]Z = total number of armature conductorsThis important equation shows that the speed of the motor is directly proportional to the armature supply voltage and inversely proportional to the flux per pole. We will now study how this equation is applied.Armature speed controlAccording to Eq. 5.8, if the flux per pole F is kept constant (permanent magnet field or field with fixed excitation), the speed depends only upon the armature voltage E s. By raising or lowering E s the motor speed will rise and fall in proportion.In practice, we can vary E s by connecting the motor armature M to a separately excited variable-voltage dc generator G . The field excitation of the motor is kept constant, but the generator excitation I x can be varied from zero to maximum and even reversed. The generator output voltage E s can therefore be varied from zero to maximum, with either positive or negative polarity. Consequently, the motor speed can be varied from zero to maximum in either direction. Note that the generator is driven by an ac motor connected to a 3-phase line. This method of speed control, known as the Ward-Leonard system, is found in steel mills, high-rise elevators, mines, and paper mills.In modem installations the generator is often replaced by a high-power electronic converter that changes the ac power of the electrical utility to dc, by electronic means.What happens to the dc power received by generator G? When G receives electric power, it operates as a motor, driving its own ac motor as an asynchronous generator!* As a result, ac power is fed back into the line that normally feeds the ac motor. The fact that power can be recovered this way makes the Ward-Leonard system very efficient, and constitutes another of its advantages.Rheostat Speed ControlAnother way to control the speed of a dc motor is to place a rheostat in series with the armature . The current in the rheostat produces a voltage drop which subtracts from the fixed source voltage E s, yielding a smaller supply voltage across the armature. This method enables us to reduce the speed below its nominal speed. It is only recommended for small motors because a lot of power and heat is wasted in the rheostat, and the overall efficiency is low. Furthermore, thespeed regulation is poor, even for a fixed setting of the rheostat. In effect, the IR drop across the rheostat increases as the armature current increases. This produces a substantial drop in speed with increasing mechanical load.中文译文:直流电动机的计算概述现在,我们对直流发电机有一个很好的了解,我们可以开始对直流电动机的研究了。
发电机中英文对照表

发电机Alternator转子Rotor轴Shaft铁芯Core线轴/绕线筒Bobbin爪极Pole内风扇叶Int。
Fan滑环Slip Ring定子Stator铁心core绝缘纸insulation槽楔slot wedge整流桥Rectifier极板/支架bracket整流二极管Power Diode 励磁二极管Electric Diode 电容器Capacitor绝缘材料insulation紧固件/连接件Connector 调节器Regulator碳刷架Brush Assy’支架Brush Holder电刷Carbon Brush弹簧Spring真空泵Vacuum Pump泵壳Pump Shell泵芯Pump Core盖板Cover管接头Joining其它部件Other Parts端盖Frame轴承Bearing外风扇叶Ext。
Fan皮带轮Pulley紧固件/连接件Connector 绝缘/塑料件insulation油封Oil Seal原材料Raw Material钢Steel铝Aluminum铜Copper铁Iron塑料Plastic尼龙Nylon纸Paper漆Lacquer其它Others辅料Complement包装材料Packing防潮/防锈材料Damp proof焊接材料Solder清洁/清洗材料Cleaner来源:中国汽车电机网作者:管理员发布时间:2007—06—15 abscissa axis 横坐标ac motor 交流环电动机active (passive) circuit elements 有(无)源电路元件active component 有功分量active in respect to 相对….呈阻性admittance 导纳air—gap flux distribution 气隙磁通分布air-gap flux 气隙磁通air-gap line 气隙磁化线algebraic 代数的algorithmic 算法的alloy 合金alternator 交流发电机ampere-turns 安匝(数)amplidyne 微场扩流发电机Amplitude Modulation(AM 调幅armature circuit 电枢电路armature coil 电枢线圈armature m。
(完整版)电机学英文文献翻译
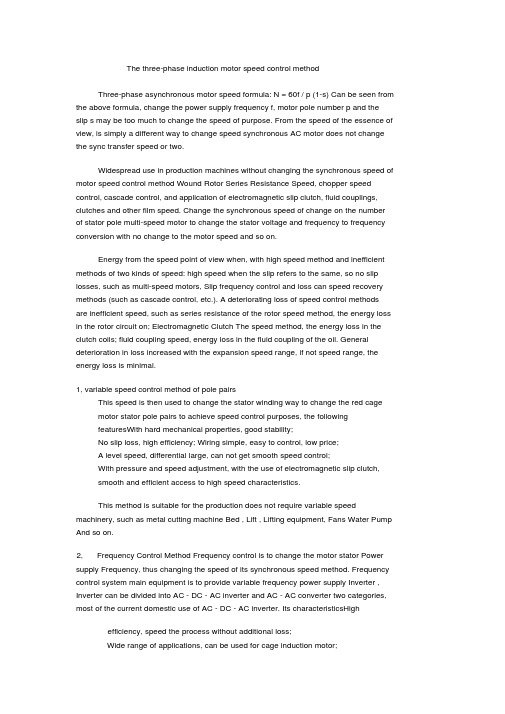
Widespread use in production machines without changing the synchronous speed of motor speed control method Wound Rotor Series Resistance Speed, chopper speed control, cascade control, and application of electromagnetic slip clutch, fluid couplings, clutches and other film speed. Change the synchronous speed of change on the number of stator pole multi-speed motor to change the stator voltage and frequency to frequency conversion with no change to the motor speed and so on.
Energy from the speed point of view when, with high speed method and inefficient methods of two kinds of speed: high speed when the slip refers to the same, so no slip losses, such as multi-speed motors, Slip frequency control and loss can speed recovery methods (such as cascade control, etc.). A deteriorating loss of speed control methods are inefficient speed, such as series resistance of the rotor speed method, the energy loss in the rotor circuit on; Electromagnetic Clutch The speed method, the energy loss in the clutch coils; fluid coupling speed, energy loss in the fluid coupling of the oil. General deterioration in loss increased with the expansion speed range, if not speed range, the energy loss is minimal.
(完整版)电机学英文文献翻译

The three-phase induction motor speed control methodThree-phase asynchronous motor speed formula: N = 60f / p (1-s) Can be seen from the above formula, change the power supply frequency f, motor pole number p and the slip s may be too much to change the speed of purpose. From the speed of the essence of view, is simply a different way to change speed synchronous AC motor does not change the sync transfer speed or two.Widespread use in production machines without changing the synchronous speed of motor speed control method Wound Rotor Series Resistance Speed, chopper speed control, cascade control, and application of electromagnetic slip clutch, fluid couplings, clutches and other film speed. Change the synchronous speed of change on the number of stator pole multi-speed motor to change the stator voltage and frequency to frequency conversion with no change to the motor speed and so on.Energy from the speed point of view when, with high speed method and inefficient methods of two kinds of speed: high speed when the slip refers to the same, so no slip losses, such as multi-speed motors, Slip frequency control and loss can speed recovery methods (such as cascade control, etc.). A deteriorating loss of speed control methods are inefficient speed, such as series resistance of the rotor speed method, the energy loss in the rotor circuit on; Electromagnetic Clutch The speed method, the energy loss in the clutch coils; fluid coupling speed, energy loss in the fluid coupling of the oil. General deterioration in loss increased with the expansion speed range, if not speed range, the energy loss is minimal.1, variable speed control method of pole pairsThis speed is then used to change the stator winding way to change the red cage motor stator pole pairs to achieve speed control purposes, the followingfeaturesWith hard mechanical properties, good stability;No slip loss, high efficiency; Wiring simple, easy to control, low price;A level speed, differential large, can not get smooth speed control;With pressure and speed adjustment, with the use of electromagnetic slip clutch,smooth and efficient access to high speed characteristics.This method is suitable for the production does not require variable speed machinery, such as metal cutting machine Bed , Lift , Lifting equipment, Fans Water Pump And so on.2, Frequency Control Method Frequency control is to change the motor stator Power supply Frequency, thus changing the speed of its synchronous speed method. Frequency control system main equipment is to provide variable frequency power supply Inverter , Inverter can be divided into AC - DC - AC inverter and AC - AC converter two categories, most of the current domestic use of AC - DC - AC inverter. Its characteristicsHighefficiency, speed the process without additional loss;Wide range of applications, can be used for cage induction motor;Speed range, features a hard, high accuracy;Technical complexity, high cost, difficult maintenance and overhaul.This method is suitable for the high accuracy, good speed performance occasions.3, cascade control method Cascade control is wound into the rotor circuit in the series of additional potential can be adjusted to change the motor's slip, to achieve speed control purposes. Most of the deterioration in power to be in series with the added potential absorbed, re-use generate additional devices to absorb the deterioration in power to return power to use or conversion of energy. Slip-power absorption under way, cascade control can be divided into Motor Cascade control, mechanical and thyristor cascade control cascade control, and multi-use cascade control thyristor, characterized byCan speed the process of deterioration in loss of feedback to the network or productionmachinery, more efficient;Installed capacity and speed range in direct proportion to investment, applicable speed range 70% -90% rated speed of production machinery;peed device failure can switch to full speed, to avoid the cut-off;Thyristor cascade speed low power factor, harmonics greater impact.This method is suitable for fans, pumps and rolling mills, mine hoist, extrusion machines.4, wound rotor motor speed control method of Series ResistanceWound Rotor Motor additional resistance in series, so that the motor slip up, motor running at low speed. The greater the resistance in series, the motor speed is lower. This method is simple, easy to control, but deteriorate the power consumption in the form of heat in the resistor. Is a class speed, soft mechanical properties.5, the stator pressure and speed adjustment methodStator voltage when changing the motor, you can get a different set of mechanical properties of curves, which were different speeds. Since the motor torque and voltage proportional to the square, the largest decline in a lot of torque, speed range of its small cage motors in general and difficult to apply. In order to expand the speed range, pressure and speed adjustment should be larger rotor resistance value cage motors, such as dedicated voltage regulator with speed torque motor, or series wound motor frequency sensitive resistors. In order to expand the range of stable operation, when the speed of 2:1 or more occasions in the feedback control should be adopted to achieve the purpose of automatic adjustment of speed.Pressure and speed adjustment is a key device to provide power supply voltage, the current way of a tandem common saturation voltage regulator Reactor , Auto Transformer And several other Thyristor Surge. Thyristor Surge is the best way. Adjusting Speed featuresPressure and speed adjustment circuit is simple, easy to realize automatic control;Poor power surge process to heat transfer in the rotor resistance in the form of consumption, low efficiency.Pressure and speed adjustment generally applies to 100KW below production machinery.6.electromagnetic speed regulating motor speed control method of electromagneticspeed regulating electric motor squirrel cage motor, electric slip clutch and DC excitation power supply (Controller) consists of three parts. DC excitation power small, usually consisting of single phase half-wave or full wave rectifiers thyristors composition, change thyristor conduction angle, you can change the magnetizing current size.Electromagnetic slip clutch armature, poles and excitation windings composed of three parts. Armature and the latter has no mechanical contact, are free to rotate. Armature motor coaxial connection active part, driven by motors; docking with the load axis magnetic pole coupling from the moving parts. When the armature poles are at rest, such as excitation windings for DC, along the circumferential surface will form a number of air gap on the n, s, of alternating polarity poles, the magnetic flux through the armature. Dang electric armature with drag motor rotating Shi, due to electric armature and pole between relative movement, and makes electric armature induction produced Eddy, this Eddy and magnetic pass mutual role produced go moments, led has pole of rotor by same direction rotating, but its speed constant below electric armature of speed N1, this is a go difference adjustable speed way, changes go difference clutch device of DC Lai magnetic current, will can change clutch device of output go moments and speed. Characteristics of electromagnetic speed regulating motor speed:appliances, structure and control circuit is simple, reliable operation, easymaintenance; speed and smooth, stepless speed regulationthe power network harmonic effects;lost speed, low efficiency.This method applies to medium and small power, requires low speed when the smooth, short run production machinery.7. the hydraulic coupler speed regulating hydraulic Coupler is a device for hydraulic drive, is made up of the pump and turbine, they collectively work wheels, placed in a sealed case. Shell filled with a certain amount of working fluid, when pump is impulse driven by rotation, in which liquid propelled by blades which rotate, and under the action of centrifugal force along the outer wheels when entering the turbine pump, to thrust to the turbine blades on the same turn, make it drive production machinery running. Power transfer capacity of the hydraulic coupler and shell filled with fluid volume sizes are consistent. In the course of work, changing the filling rate can change the coupler of turbine speed, stepless speed regulation, characterized by:power scope, can meet the needs of from a couple of different power 10-kilowattto shuqianqian;simple structure, reliable performance, easy to operation and maintenance, andlow cost;small size, capacity;easy to adjust, easy to fulfill automatic control.This method applies to the speed of the fan and water pump.三相异步电动机的几种调速方式三相异步电动机转速公式为:n=60f/p(1-s)从上式可见,改变供电频率f、电动机的极对数p及转差率s均可太到改变转速的目的。
同步电动机外文翻译文献
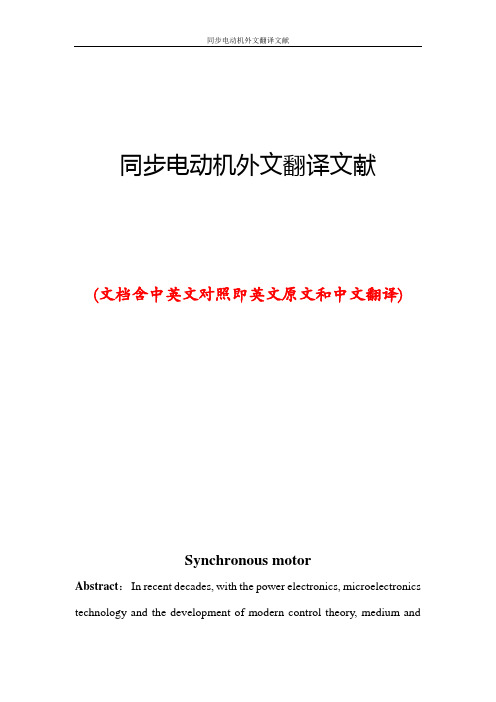
同步电动机外文翻译文献同步电动机外文翻译文献(文档含中英文对照即英文原文和中文翻译)Synchronous motorAbstract:In recent decades, with the power electronics, microelectronics technology and the development of modern controltheory, medium and small power motors in the industrial and agricultural production and people's daily lives are very broad application. Particularly in the township enterprises and household electrical appliances, need a large number of medium and small-power motors. Because of this motor development and wide application, its use, maintenance and repair work has become increasingly important,Here are just on the knowledge of synchronous motor1. Principle of operationIn order to understand the principle of operation of a synchronous motor, let us examine what happens if we connect the armature winding (laid out in the stator) of a 3-phase synchronous machine to a suitable balanced 3-phase source and the field winding to a D.C source of appropriate voltage. The current flowing through the field coils will set up stationary magnetic poles of alternate North and South.(for convenience let us assume as alient pole rotor, as shown in Fig. 50). On the other hand, the 3-phase currents flowing in the armature winding produce a rotating magnetic field rotating at synchronous speed. In other words there will be moving North and South poles established in the stator due to the 3-phase currents i.e at any location in the stator there will be a North pole at some instant of time and it will become a South pole after a time period corresponding to half a cycle. (after a time = 1/2f , where f = frequency of the supply). Let us assume that the stationarySouth pole in the rotor is aligned with the North pole in the stator moving in clockwise direction at a particular instant of time, as shown in Fig50. These two poles get attracted and Figure 50: Force of attraction between stator poles and rotor poles - resulting in production of torque in clockwise direction try to maintain this alignment ( as per L enz’s law) and hence the rotor pole tries to follow the stator pole as the conditions are suitable for the production of torque in the clockwise direction. However the rotor can not move instantaneously due to its mechanical inertia, and so it needs sometime to move. In the mean time, the stator pole would quickly (a time duration corresponding to half a cycle) change its polarity and becomes a South pole。
关于电动机的创作文献

关于电动机的创作文献英文回答:Electric Motors: A Comprehensive Overview.Electric motors are electromechanical devices that convert electrical energy into mechanical energy. They are widely used in a variety of applications, ranging from industrial machinery to consumer electronics.Principle of Operation.The basic principle of operation of an electric motor is electromagnetic induction. When an electric current flows through a coil of wire, it creates a magnetic field. If this magnetic field interacts with another magnetic field, it will cause the coil to rotate.Types of Electric Motors.There are many different types of electric motors, each with its own unique characteristics and applications. Some of the most common types include:DC motors: DC motors are powered by direct current (DC). They are relatively simple to operate and can provide a wide range of speeds and torques.AC motors: AC motors are powered by alternating current (AC). They are more efficient than DC motors and can operate at higher speeds.Synchronous motors: Synchronous motors rotate at a constant speed that is synchronized with the frequency of the AC power supply. They are used in applications where precise speed control is required.Induction motors: Induction motors are the most common type of AC motor. They are relatively simple to manufacture and can operate at a variety of speeds.Stepper motors: Stepper motors rotate in discretesteps. They are used in applications where precise positioning is required.Applications of Electric Motors.Electric motors are used in a wide variety of applications, including:Industrial machinery: Electric motors are used to power industrial machinery such as conveyors, pumps, and fans.Consumer electronics: Electric motors are used to power consumer electronics such as refrigerators, washing machines, and air conditioners.Transportation: Electric motors are used to power electric vehicles, such as cars, buses, and trains.Renewable energy: Electric motors are used to generate electricity from renewable energy sources, such as solar and wind power.Advantages of Electric Motors.Electric motors offer a number of advantages over other types of motors, including:High efficiency: Electric motors are very efficient at converting electrical energy into mechanical energy.Low maintenance: Electric motors require very little maintenance.Long lifespan: Electric motors have a long lifespan, especially when properly maintained.Quiet operation: Electric motors are relatively quiet in operation.Compact size: Electric motors are relatively compact in size, making them ideal for use in a variety of applications.Disadvantages of Electric Motors.Electric motors also have some disadvantages, including:High cost: Electric motors can be expensive topurchase and install.Limited torque: Electric motors can have limited torque, especially at low speeds.Heat generation: Electric motors generate heat when they operate, which can be a concern in some applications.Overall, electric motors are versatile and efficient devices that are used in a wide variety of applications. They offer a number of advantages over other types of motors, but they also have some disadvantages. Whenselecting an electric motor for a particular application,it is important to consider the specific requirements ofthe application and the advantages and disadvantages of different types of electric motors.中文回答:电动机,全面概述。
电子类常用英汉对照词典
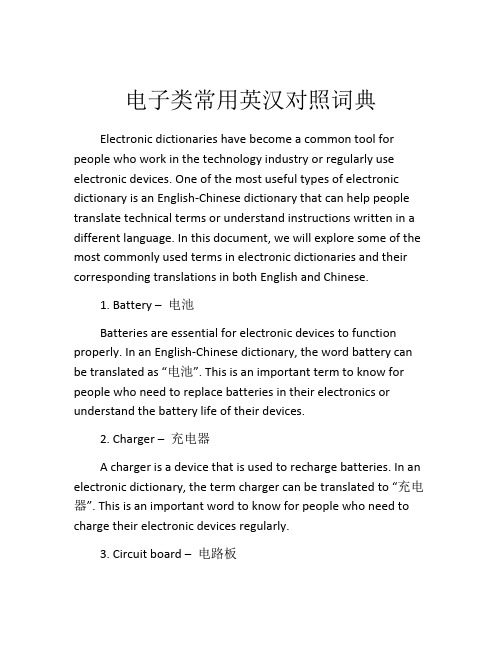
电子类常用英汉对照词典Electronic dictionaries have become a common tool for people who work in the technology industry or regularly use electronic devices. One of the most useful types of electronic dictionary is an English-Chinese dictionary that can help people translate technical terms or understand instructions written in a different language. In this document, we will explore some of the most commonly used terms in electronic dictionaries and their corresponding translations in both English and Chinese.1. Battery –电池Batteries are essential for electronic devices to function properly. In an English-Chinese dictionary, the word battery can be translated as “电池”. This is an important term to know for people who need to replace batteries in their electronics or understand the battery life of their devices.2. Charger –充电器A charger is a device that is used to recharge batteries. In an electronic dictionary, the term charger can be translated to “充电器”. This is an important word to know for people who need to charge their electronic devices regularly.3. Circuit board –电路板A circuit board is a crucial component of electronic devices. In an English-Chinese dictionary, the term circuit board can be translated as “电路板”. This is an essential term for people who work in the technology industry or regularly deal with electronic devices.4. Digital –数字化的Digital refers to electronic signals that are represented using discrete values. In a dictionary, the term digital can be translated as “数字化的”. This word is important fo r people who work in the technology industry or need to understand digital signals in order to operate electronic devices.5. Display –显示器A display refers to the visual output of electronic devices. In an English-Chinese dictionary, the term display can be translated as “显示器”. This is an important term to know for people who need to troubleshoot display issues or understand the specifications of their electronic devices.6. Input –输入Input refers to the process of entering data into electronic devices. I n a dictionary, the term input can be translated as “输入”. This word is important for people who need to understand the input options for their electronic devices or troubleshoot input issues.7. Output –输出Output refers to the process of receiving data from electronic devices. In an English-Chinese dictionary, the term output can be translated as “输出”. This is an important term to know for people who need to understand the output options for their electronic devices or troubleshoot output issues.8. Processor –处理器A processor is the central component of electronic devices that performs computations and executes instructions. In a dictionary, the term processor can be translated as “处理器”. This word is important for people who work in the technology industry or need to troubleshoot processor-related issues.9. RAM –随机存储器RAM, or Random Access Memory, is the type of memory that allows electronic devices to run multiple applications simultaneously. In an English-Chinese dictionary, the term RAM can be translat ed as “随机存储器”. This is an essential term for people who work in the technology industry or need to troubleshoot memory-related issues.10. USB –通用串行总线USB, or Universal Serial Bus, is a standard interface used for connecting electronic devices. In an electronic dictionary, the term USB can be translated as “通用串行总线”. This is an important term for people who need to connect electronic devices or troubleshoot USB-related issues.In conclusion, an English-Chinese electronic dictionary can be extremely helpful for people who work with electronic devices or need to troubleshoot technology-related issues. The above-listed terms are just a few of the many terms that can be found in these dictionaries. By understanding these terms, people can better operate their electronic devices and communicate with others in the technology industry.。
电力专业英语 英文文献翻译报告
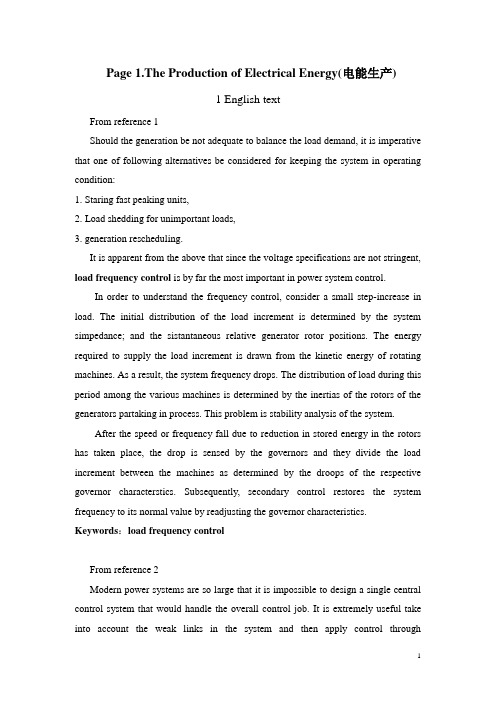
Page 1.The Production of Electrical Energy(电能生产)1 English textFrom reference 1Should the generation be not adequate to balance the load demand, it is imperative that one of following alternatives be considered for keeping the system in operating condition:1. Staring fast peaking units,2. Load shedding for unimportant loads,3. generation rescheduling.It is apparent from the above that since the voltage specifications are not stringent, load frequency control is by far the most important in power system control.In order to understand the frequency control, consider a small step-increase in load. The initial distribution of the load increment is determined by the system simpedance; and the sistantaneous relative generator rotor positions. The energy required to supply the load increment is drawn from the kinetic energy of rotating machines. As a result, the system frequency drops. The distribution of load during this period among the various machines is determined by the inertias of the rotors of the generators partaking in process. This problem is stability analysis of the system.After the speed or frequency fall due to reduction in stored energy in the rotors has taken place, the drop is sensed by the governors and they divide the load increment between the machines as determined by the droops of the respective governor characterstics. Subsequently, secondary control restores the system frequency to its normal value by readjusting the governor characteristics. Keywords:load frequency controlFrom reference 2Modern power systems are so large that it is impossible to design a single central control system that would handle the overall control job. It is extremely useful take into account the weak links in the system and then apply control throughdecomposition. The demarcation of load frequency control and Mavar voltage control characteristics is one such decomposition. Geographical and functional decomposition are successfully applied to power systems and this leads to the concept of area control.A modern power system can be divided into several areas for load frequency control. Each control area fulfils the following:1.The area is a geographically contious portion of a large interconnected area, which adjusts its own generation to accommodate load changes within its precincts.2.Under normal conditions of operation, it changes bulk power with neighboring areas.3.Under abnormal conditions of operation, it may deviate from predetermined schedules and provide assistance to any neighboring control area in the system.4.It is expected, in addition, to partake with the other areas in the system in a suitable manner in the system frequency regulation.The rotors of all generators in a control area swing together for load change. Thus, a coherent group of generators within a geographical region may constitute a control area which is connected to other similar areas by weak tie lines.Keywords:areas load frequency controlFrom reference 3For plant loading schedules in thermal systems, load prediction up to two hours in advance is necessary while for unit commitment schedules prediction up to 24 hours is sufficient. Also, at all sations and control centers, short-time prediction is needed for storage and display of advance information. Based on this information, predictive security assessment of the system is made. This also helps to contain the rates of change of generator outputs within their permissible limits.For the implementation of economic scheduling of generation using digital computers, detailed estimates of the future load demands are essential in order to allow sufficient time for the calculation and implementation of the generator schedules. Whatever method is envisaged for the calculation of such economic schedules consistent with the security and spare requirements of the system, the schedules should be calculatedevery 15 or 30 minutes and each economic schedule should be a predictive one ,for at least about 30 minutes ahead of event. It is then obvious that the predictions are to be revised frequently in the light of any fresh information so as to minimize the estimation errors.Peak load demand forecasts are useful in determining the investment required for additional generating and transmission capacities required. Forecasts for planning require data extending over several previous years. Meaningful forecasts can be obtained with lead time of 3 to 5 years.Keywords:load predictionFrom reference 4In this method, the load is separated into two main components. The first component is a base load which is of fixed value and the second a variable component which is a function of the weather conditions.Estimates can be made 24 hours ahead, using the weather forecast. The temperature base for weighting the effect of the predicated temperature on the load is the normal, mean temperature of the month. The normal, mean temperature of the month has zero weight. Similarly the change in consumers demand due to cloudy weather may be assumed to vary in direct proportion to the degree of cloudiness. This in turn may be expressed by an illumination index with fair, clear sky corresponding to zero weight.The base load is determined from past records. Proper weighting of the elements of the weather will be attained only after several trials. The method of prediction stabilizes after this trial period. It may be noted that the base loads for week days and weekend will generally be different for any hour.Using these base loads, a load estimate based on the best available weather forecast can be made using proper weighting of meteorological factors like temperature, cloudiness, wind velocity, etc.Keywords:proper weighting of the elements of the weather2 中文翻译及分析出自文献1:万一发电量不足以平衡负荷需求,要使电力系统处于运行状态,必须考虑采取以下选择方法中的一种:1、启动快速峰荷机组2、对不重要的用户实行拉闸断电3、重新制定发电计划从上述情况来看,电压技术的要求并不严格,目前为止负荷频率控制是电力系统控制中最重要的手段。
电机和传动部件外文文献翻译、中英文翻译
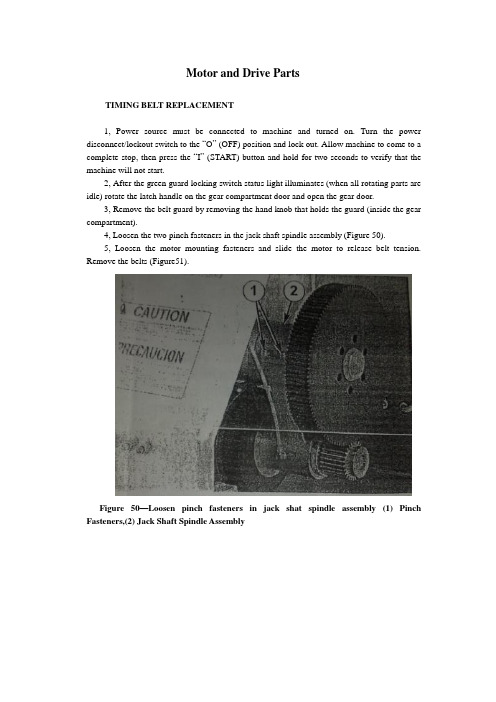
Motor and Drive PartsTIMING BELT REPLACEMENT1, Power source must be connected to machine and turned on. Turn the power disconnect/lockout switch to the “O” (OFF) position and lock out. Allow machine to come to a complete stop, then press the “I” (START) button and hold for two seconds to verify that the machine will not start.2, After the green guard locking switch status light illuminates (when all rotating parts are idle) rotate the latch handle on the gear compartment door and open the gear door.3, Remove the belt guard by removing the hand knob that holds the guard (inside the gear compartment).4, Loosen the two pinch fasteners in the jack shaft spindle assembly (Figure 50).5, Loosen the motor mounting fasteners and slide the motor to release belt tension. Remove the belts (Figure51).Figure 50—Loosen pinch fasteners in jack shat spindle assembly (1) Pinch Fasteners,(2) Jack Shaft Spindle AssemblyFigure 51 – Timing Belts(1)TIMING BELT TENSION1, Use the motor tension wrench to slide the motor and apply tension to the timing belts. The pin on the wrench fits in a hole on the support housing(Figure52). The pinch fasteners in the jack shaft spindle assembly must be properly tension both belts. Tighten the motor mounting fasteners, and then tighten the pinch fasteners in the jack shaft spindle assembly.Figure 52 – Using the motor to apply belt tension. (1) Motor Tension Wrench2, Replace belt guard and tighten with the hand knob.3, Close and rotate latch handle connecting the gear compartment door and support housing.Electrical AssemblyINSPECTIONW ARNING: In the event of an electrical problem, only a qualified electrician should inspect or repair the fault. Voltages dangerous to life exist in the starter enclosure! The power disconnect/lockout switch must be in the “O”(OFF) position. Live voltages are still present in the box even though disconnect is off. Always disconnect and lock out power source before beginning electrical inspection or repair.The electrical assembly must be in good working condition before operating this machine. For a description of the amplifier and safety switch operation and method for checking this system. Electrical schematics are located in the starter enclosure. Refer to Figures53 and 54 and inspect the following:Figure 53 –Starter enclosure interior with variable frequency drive. (1) Disconnect Switch, (2) Guard Locking Switch Power Disconnect, (3) Main Fuses, (4) Earthing Terminals, (5) Transformer, (6) Transformer Fuses Block, (7) Variable Frequency Drive, (8) Contactor, (9) Standstill Monitor, (10) Control RelayFigure 54 – Starter enclosure interior, across-the-line start. (1) Disconnect Switch, (2) Guard Locking Switch Power Disconnect, (3) Main Fuses, (4) Earthing Terminals, (5) Transformer, (6) Transformer Fuse Block, (7) Overload Relay, (8) Contactor, (9) Standstill Monitor, (10) Control RelayStarter enclosure: Inspect interior of starter enclosure for corrosion. If a significant amount of water accumulates in the bottom of the starter enclosure, check the breather drain. Breather drain should be free from obstruction. Excess water could also indicate an opening or loose fitting that allows water to enter the enclosure. Check all access points to the enclosure. Check gasket around door and window. Inspect push/pull stop button, “I”(START) push button assemblies, selector switches and pilot light assembly for damage or corrosion. Replace rubber boots and pilot light lens if damaged.NOTE: Electrical components that fail due to water or chemical contamination are not covered under the warranty.Fuses: Remove transformer fuses, located in the transformer fuse blocks. Check with an ohmmeter or continuity light. If one fuse is replaced, all others of that type fuse should also be replaced.Machines equipped with variable frequency drive(VFD):The drive currently in use is the GPD315/V 7. If the digital display on the drive is not illuminated when the machine is energized, contact Urschel Laboratories.Standstill monitor: Terminals should be tight and free from corrosion. Monitor must be replaced if damaged.Power line filter (CE compliant machine with VFD): See the electrical assemblies illustrations in the “Parts” section of this manual for part locations.Guard locking switches:Replace or straighten actuator key if it is damaged or bent. Check cords for cuts or abrasions. If the green guard locking switch status light does not illuminate when power to the machine is connected, contact Urschel Laboratories. Switch must be replaced if it has been forced open while locked. Use only new screws that are supplied with the switch. Manual release must be in “lock” position when removing and replacing lid( Figure 55).Figure 55 – Guard Locking Switch. (1) Green Guard Locking Switch Status Light, (2) Guard Locking Switch Manual ReleaseGreen status light must be inside the lens when replacing the lid. To maintain watertight features, securely tighten the seven screws for the lid until there is no gap between lid and switch assembly. Do not over tighten.NOTE:The two screws located under the lid on the guard locking switch act as special dowel pins locking the switch assembly into place and must not be substituted.Interrupt switch: Terminals should be tight and free from corrosion. Recommended torque is 5.0 inch pounds (80 inch ounces) or 0.56 Newton-meters. Check sensor, actuator and cord for damage. Switch should be replaced if any defect or damage is defected. Check switch alignment. Actuator must be aligned and within 1/32 (8mm) of sensor to complete safety switch circuit (Figure 56).WARNING: Always perform the guard locking/interrupt switch system test before operating the machine.Figure 56 –Interrupt switch sensor and actuator must be aligned and within 1/32”(8mm). (1) Sensor, (2) ActuatorV ARIABLE FREQUENCY DRIVE PROGRAMMINGA replacement variable frequency drive must have frequencies programmed after the drive has been installed into the electrical enclosure. Refer to the “Speed Chart” on your machine or on page 30 in this manual and program the replacement unit according to the following procedure.WARNING: Starter enclosure must be energized in order to program the drive. Voltages dangerous to life exist when equipment is open and energized! Only a qualified electrician should inspect, install, or program variable frequency drive.1, Turn power disconnect/lockout switch to “O”(OFF). Open starter enclosure door. Operate the power disconnect/lockout switch mechanism in the enclosure to turn power on.2, Set the selector switches to the first drive frequency to be programmed. The frequency drive has a digital operator with a display (Figure 57). The display for the GPD 315/V7 drive will read the lowest setting allowed.Figure 57 – FPD 315 Drive, digital operator. (1) Digital Display,(2) Numeral Change Key, (increase), (3) Numeral Change Key, (decrease), (4) Read/Write Key3, Enter the speed in the display in hertz. Increase or decrease the value with the “numeral change” keys. See the chart for frequency settings.CAUTION: Do not attempt to over speed the motor! Over speeding could create a safety hazard and cause excessive wear on machine parts. Under speeding will cause the motor to overheat.4, With the value correctly displayed and flashing, press the “DATA/ENTER” or “ENTER” key. The display will stop flashing, indicating that the value has been entered.NOTE:Altering preprogrammed speeds will permanently change these values. To return to original settings, follow steps 1-4.5, Operate the power disconnect/lockout switch mechanism in the enclosure to turn power off. Close and lock starter enclosure door.Knife CareKNIFE CARE GUIDELINESKnives should be inspected and sharpened or replaced at regular intervals depending upon operating conditions, type of product and hours of operation. Follow these guidelines for bestresults:1, Do not attempt to remove all defects from the knife edge by sharpening.This practice results in shortened knife life. Small defects will not affect knife performance.2, New knives should not be installed beside worn knives. This arrangement may result in poor quality cuts. Keep all the knives from one spindle in a set and sharpen them together. Periodically check knife width or diameter to make sure all the knives in a set are the same size.3, Recommended minimum dimensions: The following minimum dimensions are intended to give satisfactory results for most applications. However, each customer must look at the quality of cut on his product to determine at what point knives are resharpened beyond usefulness. The minimum dimensions stated are intended to give satisfactory results for most applications. Some customers may be able to give satisfactory results from knives ground smaller, but some may notice a deterioration in quality of out before the minimum size is reached. Measure crosscut knives from the cutting edge to the back of the knife unless otherwise noted; measure the diameter of circular knives unless otherwise noted.SHARPENING EQUIPMENTUrschel Laboratories manufactures machines to quickly and efficiently sharpen knives. The following machine are available;Model WG honing machine is used to sharpen slicing knives and crosscut knives (straight cut only). For the Model DC, use workrest 33224 for 42281 and 42446 crosscut knives and slicing knife insert .Use workrest 33225 for 42460 crosscut knives. Use workrest 33256 for all other slicing knives.Model CKG honing machine is used to place the best possible edge on circular knives. The Model CKG can be purchased from the factory ready to sharpen 3-1/2”circular knives for the Model DC. Honers that are not set up to sharpen 3-1/2” circular knives must have certain parts installed. Use the following procedure:W ARNNING: Honers place an extremely sharp edge on knives; handle knives with care!1, Make sure the honer is unplugged from the power source.2, Install hone assembly, knife holder hub and edge roller stud for 3-1/2’’circular knives (Figure 58). The hone assembly (part number 33083) contains the hone bracket and internal parts, the shield and the honing wheel. The stud on the hone bracket is installed in the second hole from the motor shaft (4” knife position). The knife holder hub (part number 33081) is installed with the raised diameter facing out. The edge roller stud (part number 33023) is installed with the set screw in the second spot drilled hole from the outside end (Note that this part number has remained thesame but the part has been modified. The stud should have four spot drilled holes.) 3, Position the hone shield in as far as possible by loosening the screw and sliding the shield. Retighten the screw.4. Pull the knife clamp hub out of the clamping position. Hold a knife against the knife holder hub. Loosen the set screw in the motor shaft hub and slide the hub and knife on the motor shaft until the knife just touches the honing wheel. Tighten the set screw.5, Adjust the knife clamp if necessary. The knife clamp should hold the knife against the hub tight enough so that it cannot be rotated yet not so tight that it drives the motor back and distorts the base (the brake arm assembly must be properly adjusted to test for knife rotation). To adjust the knife clamp, loosen the two locking nuts and move the clamp in or out.6, Place a knife in the honer and sharpen in the normal manner (see the Model CKG instruction manual for more information). If too much of the knife edge is removed, readjust the hub. If insufficient metal is removed, loosen the screw on the hone shield and slide the hone slightly forward against the knife edge.BUFFINGWARNING: Only qualified trained personnel should buff knives. Use adequate eye and respiratory protection, and a properly guarded buffing wheel. Hold knife securely. Never attempt to catch a dropped knife! Should you drop a knife during the buffing operation, move away and let it tall.When crosscut knives are sharpened by grinding, filing or honing, a slight wire edge may be produced. Buffing will remove this wire edge.Install two to four 10" (254 mm) diameter buffing wheels side by side between flanges at least2" (51 mm) in diameter. Buffing wheels and bars of buffing compound are available from Urschel Laboratories (see “Tools", page67).Turn on the buffer (3600RPM) and hold the bar of buffing compound firmly against the outside diameter of the buffing wheels to apply alight coating of compound. Apply compound frequently to obtain sharp edges quickly.NOTE: If excess compound is applied, the wheel will harden, making it ineffective.Should this occur, Use a buffing wheel rake, available from an industrial supplier, to soften the wheel.When holding knives, be cautions and use a firm grip. Hold the knife firmly with the bevel side up, parallel with and just below the center line of the shaft of the buffer (Figure 58). Push the knife edge into the buffing wheel, penetrating the wheel 1/16"-1/8"(1.5-3mm). Move the knife endwise and buff the entire edge across the buffing wheel with a steady rapid movement in each direction. Several rapid passes are better than one or two slow ones. Do not hold the knife in one area of the buffing wheel too long as the edge may heat and burn. If a burr or wire edge remains, turn the knife over and buff with the bevel side down. Continue buffing, switching from side to side, until wire edge or burr is gone.Sharpen all sides of crinkle knife edges by tipping the knife endwise at a slight angle, first in one direction and then in the other. Next, the knife is held straight and level to buff the remainder of the cutting edge.With bevel side up, sharpen side surface of crinkle knife edge by tipping the knife endwise at a slight angle, first in one direction and then in the other. Next, the knife is held straight and level tobuff the remainder of the cutting edge.Figure 58 –Model CKG honing machine set to sharpen 3-1/2”circular knives (1) Hone Bracket, (2) Mounting Position for Hone Assembly, (3) Knife Holder Hub, (4) Set Screw,(5) Edge Roller Stud (set screw seats in second hole), (6) Hone Shield, (7) Screw, (8) Knife Clamp Hub, (9) Locking Nuts, (10) Honing WheelFailure to obtain sharp edges by buffing may be caused by the following:1, Edges may be too dull or blunt. Blunt edges must always be ground or filed to restore a bevel width and angle similar to that found on a new knife.2, Knives must be correctly held against the buffing wheel (Figure 59).3, Too little or too much buffing compound on the wheel.4, Undersize buffing wheels. Discard the buffing wheels when they are worn to8-3/4" (222 mm) diameter.Figure 59 – Correct position (top) and incorrect position (bottom) for knife during buffing .(1) Knife, (2) Buffing WheelPROBLEM CAUSE CORRECTIONMachine Does Not Start Power disconnect lockout switch isin the "O"(OFF)positionTurn power disconnect lockoutswitch to the "I"(ON) position. Manual release on either of theguard locking switches is in the"unlock" positionTurn manual release to the"lock" position on bothswitches, page 17.Guard locking switch powerdisconnect is in the"O"(OFF)positionTurn guard locking switchpower disconnect to the"I"(ON) position, page 54.Push/pull stop button is not pulledout after being pushedPull push/pull stop button out,page 28.Covers and guards not securelyclosedMake certain covers andguards are securely closed.Check for bent or twistedbrackets that will preventswitches from lining up. See"Covers and Guards",pages34-35.VFD fault or warning Not error code displayed onVFD. Turn disconnect off.电机和传动部件同步带置换1,电源必须与机器连接并打开。
电子类文献中英文翻译(发电机)
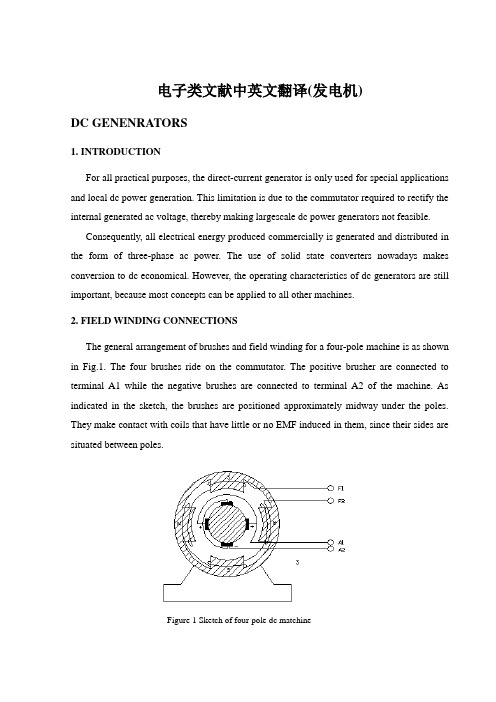
电子类文献中英文翻译(发电机)DC GENENRATORS1. INTRODUCTIONFor all practical purposes, the direct-current generator is only used for special applications and local dc power generation. This limitation is due to the commutator required to rectify the internal generated ac voltage, thereby making largescale dc power generators not feasible.Consequently, all electrical energy produced commercially is generated and distributed in the form of three-phase ac power. The use of solid state converters nowadays makes conversion to dc economical. However, the operating characteristics of dc generators are still important, because most concepts can be applied to all other machines.2. FIELD WINDING CONNECTIONSThe general arrangement of brushes and field winding for a four-pole machine is as shown in Fig.1. The four brushes ride on the commutator. The positive brusher are connected to terminal A1 while the negative brushes are connected to terminal A2 of the machine. As indicated in the sketch, the brushes are positioned approximately midway under the poles. They make contact with coils that have little or no EMF induced in them, since their sides are situated between poles.Figure 1 Sketch of four-pole dc matchineThe four excitation or field poles are usually joined in series and their ends brought out to terminals marked F1 and F2. They are connected such that they produce north and south poles alternately.The type of dc generator is characterized by the manner in which the field excitation is provided. In general, the method employed to connect the field and armature windings falls into the following groups (see Fig.2):Figure2 Field connections for dc generators:(a)separately excited generator;(b)self-excited,shunt generator;(c)series generator;(d)compound generator;short-shunt connection;(e)compoundgenerator,long-shunt connection.The shunt field contains many turns of relatively fine wire and carries a comparatively small current, only a few percent of rated current. The series field winding, on the other hand, has few turns of heavy wire since it is in series with the armature and therefore carries the load current.Before discussing the dc generator terminal characteristics, let us examine the relationship between the generated voltage and excitation current of a generator on no load. The generated EMF is proportional to both the flux per pole and the speed at which the generator is driven, EG=kn. By holding the speed constant it can be shown the EG depends directly on the flux.To test this dependency on actual generators is not very practical, as it involves a magnetic flux measurement. The flux is produced by the ampere-turns of the field coils: in turn, the flux must depend on the amount of field current flowing since the number of turns on the field winding is constant. This relationship is not linear because of magnetic saturation after the field current reaches a certain value. The variation of EG versus the field current If may be shown by a curve known as the magnetization curve or open-circuit characteristic. For this a given generator is driven at a constant speed, is not delivering load current, and has its field winding separately excited.The value of EG appearing at the machine terminals is measured as If is progressively increased from zero to a value well above rated voltage of that machine. The resulting curve is shown is Fig.3. When Ij=0, that is, with the field circuit open circuited, a small voltage Et is measured, due to residual magnetism. As the field current increases, the generated EMF increases linearly up to the knee of the magnetization curve. Beyond this point, increasing the field current still further causes saturation of the magnetic structure to set in.Figure 3 Magnetization curve or open-circuit characteristic of a separately excited dc machineThe means that a larger increase in field current is required to produce a given increase in voltage.Since the generated voltage EG is also directly proportional to the speed, a magnetization curve can be drawn for any other speed once the curve is determined. This merely requires anadjustment of all points on the curve according ton n x E E G G ''=where the quantities values at the various speeds.3. VOLTAGE REGULATIONLet us next consider adding a load on generator. The terminal voltage will then decrease (because the armature winding ha resistance) unless some provision is made to keep it constant. A curve that shows the value of terminal voltage for various load currents is called the load or characteristic of the generator.Figure 4 (a) directs current it to urge the generator load characteristics; (b) circuit diagramFig.4 shows the external characteristic of a separately excited generator. The decrease in the terminal voltage is due mainly to the armature circuit resistance RA. In general,A A G t R I E V -=where Vt is the terminal voltage and IA is the armature current (or load current IL) supplied by the generator to the load.Another factor that contributes to the decrease in terminal voltage is the decrease in flux due to armature reaction. The armature current established an MMF that distorts the main flux, resulting in a weakened flux, especially in noninterpole machines. This effect is calledarmature reaction. As Fig.4 shows, the terminal voltage versus load current curve does not drop off linearly since the iron behaves nonlinear. Because armature reaction depends on the armature current it gives the curve its drooping characteristic.4. SHUNT OR SELF-EXCIITED GENRATORSA shunt generator has its shunt field winding connected in parallel with the armature so that the machine provides its own excitation, as indicated in Fig.5. The question arises whether the machine will generate a voltage and what determines the voltage.For voltage to “build up” as it is called, there must be some remanent magnetism in the field poles. Ordinarily, if the generator has been used previously, there will be some remanent magnetism. We have seen in Section 3 that if the field would be disconnected, there will be small voltage Ef generated due to this remanent magnetism, provided that the generator is driven at some speed. Connecting the field for self-excitation, this small voltage will be applied to the shunts field and drive a small current through the field circuit. If this resulting small current in the shunt field is of such a direction that it weakens the residual flux, the voltage remains near zero and the terminal voltage does not build up. In this situation the weak main pole flux opposes the residual flux.Figure 5 Shunt generator:(a)circuit;(b)load characteristicIf the connection is such that the weak main pole flux aids the residual flux, the inducedvoltage increases rapidly to a large, constant value. The build-up process is readily seen to be cumulanve. That is, more voltage increases the field current, which in turn increases the voltage, and so on. The fact that this process terminates at a finite voltage is due to the nonlinear behavior of the magnctic circuit. In steady state the generated voltage is causes a field current to flow that is just sufficient to develop a flux required for the generated EMF that causes the field current to flow.The circuit carries only dc current, so that the field current depends only on the field circuit resistance, Rf. This may consist of the field circuit resistance Rf, the field current depends on the generated voltage in accordance with Ohm ’s law.It should be evident that on a new machine or one that has lost its residual flux because of a long idle period, some magnetism must be created. This is usually done by connecting the field winding only to a separate dc source for a few seconds. This procedure is generally known as flashing the field.Series GeneratorsAs mentioned previously, the field winding of a series generator is in series with the armature. Since it carries the load current the series field winding consists of only a few turns of thick wire. At no load, the generated voltage is small due to residual field flux only. When a load is added, the flux increases, and so does the generated voltage. Fig.7 shows the load characteristic of a series generator driven at a certain speed. The dashed line indicates the generated EMF of the same machine with the armature open-circuited and the field separately excited. The difference between the two curves is simply the IR drop in the series field and armature winding, such that)(S A A G t R R I E V +-=where RS is the series field winding resistance.Figure 7 Series generator: (a)circuit diagram;(b)load characteristicsCompound GeneratorsThe compound generator has both a shunt and a series field winding, the latter winding wound on top of the shunt winding. Fig.8 shows the circuit diagram. The two windings are usually connected such that their ampere-turns act in the same direction. As such the generator is said to be cumulatively compounded.The shunt connection illustrated in Fig.8 is called a long shunt connection. If the shunt field winding is directly connected across the armature terminals, the connection is referred to as a short shunt. In practice the connection used is of little consequence, since the shunt field winding carries a small current compared to the full-load current. Furthermore, the number of turns on the series field winding. This implies it has a low resistance value and the corresponding voltage drop across it at full load is minimal.Curves in Fig.9 represents the terminal characteristic of the shunt field winding alone. By the addition of a small series field winding the drop in terminal voltage with increased loading is reduced as indicated. Such a generator is said to be undercompounded. By increasing the number of series turns, the no-load and full-load terminal voltage can be made equal; the generator is then said to be flatcompounded. If the number of series turns is more than necessary to compensate for the voltage drop, the generator is overcome pounded. In that case the full-load voltage is higher than the no-load voltage.Figure 9 Terminal characteristics of compound generators compared with that of the shunt generatorThe overcompounded generator may be used in instances where the load is at some distance from the generator. The voltage drops in the feeder lines are the compensated for with increased loading. Reversing the polarity of the series field in relation to the shunt field, the fields will oppose each other more and more as the load current increase. Such a generator is said to be differentially compounded. It is used in applications where feeder lines could occur approaching those of a short circuit. An example would be where feeder lines could break and short circuit the generator. The short-circuit current, however, is then limited to a “safe” value. The terminal characteristic for this type of generator is also shown in Fig.9. Compound generators are used more extensively than the other types because they may be designed to have a wide varity of terminal characteristics.As illustrated, the full-load terminal voltage can be maintained at the no-load value by the proper degree of compounding. Other methods of voltage control are the use of rheostats, for instance, in the field circuit. However, with changing loads it requires a constant adjustment of the field rheostat to maintain the voltage. A more useful arrangement, which is now common practice, is to use an automatic voltage regulator with the generator. In essence, the voltage regulator is a feedback control system. The generator output voltage is sensed and compared to a fixed reference voltage deviation from the reference voltage gives an error signal that is fed to a power amplifier. The power amplifier supplies the field excitation current. If the error signal is positive, for example, the output voltage is larger than desiredand the amplifier will reduce its current drive. In doing so the error signal will be reduced to zero.TRANSFORMER1. INTRODUCTIONThe high-voltage transmission was need for the case electrical power is to be provided at considerable distance from a generating station. At some point this high voltage must be reduced, because ultimately is must supply a load. The transformer makes it possible for various parts of a power system to operate at different voltage levels. In this paper we discuss power transformer principles and applications.2. TOW-WINDING TRANSFORMERSA transformer in its simplest form consists of two stationary coils coupled by a mutual magnetic flux. The coils are said to be mutually coupled because they link a common flux. In power applications, laminated steel core transformers (to which this paper is restricted) are used. Transformers are efficient because the rotational losses normally associated with rotating machine are absent, so relatively little power is lost when transforming power from one voltage level to another. Typical efficiencies are in the range 92 to 99%, the higher values applying to the larger power transformers.The current flowing in the coil connected to the ac source is called the primary winding or simply the primary. It sets up the flux φ in the core, which varies periodically both in magnitude and direction. The flux links the second coil, called the secondary winding or simply secondary. The flux is changing; therefore, it induces a voltage in the secondary by electromagnetic induction in accordance with Lenz’s law. Thus the primary receives its power from the source while the secondary supplies this power to the load. This action is known as transformer action.3. TRANSFORMER PRINCIPLESWhen a sinusoidal voltage V p is applied to the primary with the secondary open-circuited, there will be no energy transfer. The impressed voltage causes a small current Iθ to flow in the primary winding. This no-load current has two functions: (1) it produces the magnetic flux in the core, which varies sinusoidally between zero and φm, where φm is the maximum value of the core flux; and (2) it provides a component to account for the hysteresis and eddy current losses in the core. There combined losses are normally referred to as the core losses.The no-load current Iθ is usually few percent of the rated full-load current of the transformer (about 2 to 5%). Since at no-load the primary winding acts as a large reactance due to the iron core, the no-load current will lag the primary voltage by nearly 90º. It is readily seen that the current component I m= I0sinθ0, called the magnetizing current, is 90ºin phase behind the primary voltage V P. It is this component that sets up the flux in the core; φ is therefore in phase with I m.The second component, I e=I0sinθ0, is in phase with the primary voltage. It is the current component that supplies the core losses. The phasor sum of these two components represents the no-load current, orI0 = I m+ I eIt should be noted that the no-load current is distortes and nonsinusoidal. This is the result of the nonlinear behavior of the core material.If it is assumed that there are no other losses in the transformer, the induced voltage In the primary, E p and that in the secondary, E s can be shown. Since the magnetic flux set up by the primary winding,there will be an induced EMF E in the secondary winding in accordance with Faraday’s law, namely, E=NΔφ/Δt. This same flux also links the primary itself, inducing in it an EMF, E p. As discussed earlier, the induced voltage must lag the flux by 90º, therefore, they are 180º out of phase with the applied voltage. Since no current flows in the secondary winding, E s=V s. The no-load primary current I0 is small, a few percent of full-load current. Thus the voltage in the primary is small and V p is nearly equal to E p. The primary voltage and the resulting flux are sinusoidal; thus the induced quantities E p and E s vary as a sine function. The average value of the induced voltage given byE avg = turns× change in flux in a given time given timewhich is Faraday’s law applied to a finite time interval. It follows thatE avg = N 21/(2)m f = 4fNφm which N is the number of turns on the winding. Form ac circuit theory, the effective or root-mean-square (rms) voltage for a sine wave is 1.11 times the average voltage; thusE = 4.44fNφmSince the same flux links with the primary and secondary windings, the voltage per turn in each winding is the same. HenceE p = 4.44fN p φmandE s = 4.44fN s φmwhere E p and Es are the number of turn on the primary and secondary windings, respectively. The ratio of primary to secondary induced voltage is called the transformation ratio. Denoting this ratio by a, it is seen that a = p sE E = p s N N Assume that the output power of a transformer equals its input power, not a bad sumption in practice considering the high efficiencies. What we really are saying is that we are dealing with an ideal transformer; that is, it has no losses. ThusP m = P outorV p I p × primary PF = V s I s × secondary PFwhere PF is the power factor. For the above-stated assumption it means that the power factor on primary and secondary sides are equal; thereforeV p I p = V s I s from which is obtainedp s V V = p s I I ≌ p sE E ≌ aIt shows that as an approximation the terminal voltage ratio equals the turns ratio. The primary and secondary current, on the other hand, are inversely related to the turns ratio. The turns ratio gives a measure of how much the secondary voltage is raised or lowered in relation to the primary voltage. To calculate the voltage regulation, we need more information.The ratio of the terminal voltage varies somewhat depending on the load and its power factor. In practice, the transformation ratio is obtained from the nameplate data, which list the primary and secondary voltage under full-load condition.When the secondary voltage V s is reduced compared to the primary voltage, the transformation is said to be a step-down transformer: conversely, if this voltage is raised, it is called a step-up transformer. In a step-down transformer the transformation ratio a is greater than unity (a>1.0), while for a step-up transformer it is smaller than unity (a<1.0). In the event that a=1, the transformer secondary voltage equals the primary voltage. This is a special type of transformer used in instances where electrical isolation is required between the primary and secondary circuit while maintaining the same voltage level. Therefore, this transformer is generally knows as an isolation transformer.As is apparent, it is the magnetic flux in the core that forms the connecting link between primary and secondary circuit. In section 4 it is shown how the primary winding current adjusts itself to the secondary load current when the transformer supplies a load.Looking into the transformer terminals from the source, an impedance is seen which by definition equals V p / I p . From p s V V = p s I I ≌ p sE E ≌ a , we have V p = aV s and I p = I s /a.In terms of V s and I s the ratio of V p to I p isp p V I = /s s aV I a= 2s s a V I But V s / I s is the load impedance Z L thus we can say thatZ m (primary) = a 2Z LThis equation tells us that when an impedance is connected to the secondary side, it appears from the source as an impedance having a magnitude that is a 2 times its actual value. We say that the load impedance is reflected or referred to the primary. It is this property oftransformers that is used in impedance-matching applications.4. TRANSFORMERS UNDER LOADThe primary and secondary voltages shown have similar polarities, as indicated by the “dot-making” convention. The dots near the upper ends of the windings have the same meaning as in circuit theory; the marked terminals have the same polarity. Thus when a load is connected to the secondary, the instantaneous load current is in the direction shown. In other words, the polarity markings signify that when positive current enters both windings at the marked terminals, the MMFs of the two windings add.Since the secondary voltage depends on the core flux φ0, it must be clear that the flux should not change appreciably if E s is to remain essentially constant under normal loading conditions. With the load connected, a current I s will flow in the secondary circuit, because the induced EMF E s will act as a voltage source. The secondary current produces an MMF N s I s that creates a flux. This flux has such a direction that at any instant in time it opposes the main flux that created it in the first place. Of course, this is Lenz’s law in action. Thus the MMF represented by N s I s tends to reduce the core flux φ0. This means that the flux linking the primary winding reduces and consequently the primary induced voltage E p, This reduction in induced voltage causes a greater difference between the impressed voltage and the counter induced EMF, thereby allowing more current to flow in the primary. The fact that primary current I p increases means that the two conditions stated earlier are fulfilled: (1) the power input increases to match the power output, and (2) the primary MMF increases to offset the tendency of the secondary MMF to reduce the flux.In general, it will be found that the transformer reacts almost instantaneously to keep the resultant core flux essentially constant. Moreover, the core flux φ0drops very slightly between n o load and full load (about 1 to 3%), a necessary condition if E p is to fall sufficiently to allow an increase in I p.On the primary side, I p’ is the current that flows in the primary to balance the demagnetizing effect of I s. Its MMF N p I p’ se ts up a flux linking the primary only. Since the core flux φ0 remains constant. I0 must be the same current that energizes the transformer at no load. Theprimary current I p is therefore the sum of the current I p’ and I0.Because the no-load current is relatively small, it is correct to assume that the primary ampere-turns equal the secondary ampere-turns, since it is under this condition that the core flux is essentially constant. Thus we will assume that I0 is negligible, as it is only a small component of the full-load current.When a current flows in the secondary winding, the resulting MMF (N s I s) creates a separate flux, apart from the flux φ0 produced by I0, which links the secondary winding only. This flux does no link with the primary winding and is therefore not a mutual flux.In addition, the load current that flows through the primary winding creates a flux that links with the primary winding only; it is called the primary leakage flux. The secondary- leakage flux gives rise to an induced voltage that is not counter balanced by an equivalent induced voltage in the primary. Similarly, the voltage induced in the primary is not counterbalanced in the secondary winding. Consequently, these two induced voltages behave like voltage drops, generally called leakage reactance voltage drops. Furthermore, each winding has some resistance, which produces a resistive voltage drop. When taken into account, these additional voltage drops would complete the equivalent circuit diagram of a practical transformer. Note that the magnetizing branch is shown in this circuit, which for our purposes will be disregarded. This follows our earlier assumption that the no-load current is assumed negligible in our calculations. This is further justified in that it is rarely necessary to predict transformer performance to such accuracies. Since the voltage drops are all directly proportional to the load current, it means that at no-load conditions there will be no voltage drops in either winding.中文翻译①直流发电机1.介绍关于所有实际目的来说,直流发电机仅用于特殊场合与地方性发电厂。
电力系统毕业论文中英文外文文献翻译
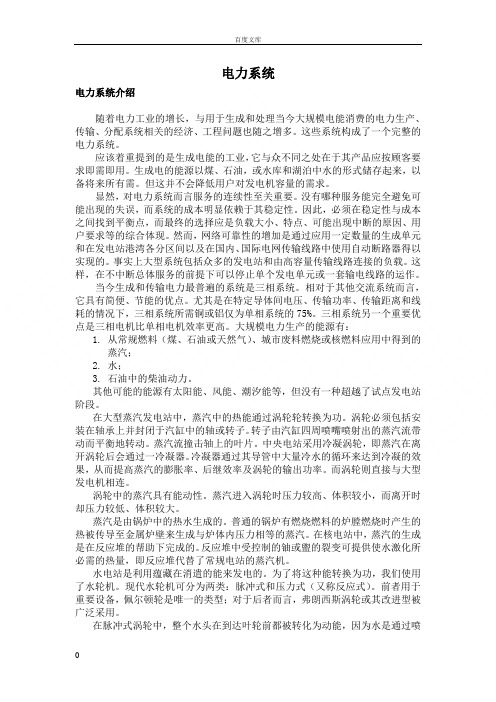
电力系统电力系统介绍随着电力工业的增长,与用于生成和处理当今大规模电能消费的电力生产、传输、分配系统相关的经济、工程问题也随之增多。
这些系统构成了一个完整的电力系统。
应该着重提到的是生成电能的工业,它与众不同之处在于其产品应按顾客要求即需即用。
生成电的能源以煤、石油,或水库和湖泊中水的形式储存起来,以备将来所有需。
但这并不会降低用户对发电机容量的需求。
显然,对电力系统而言服务的连续性至关重要。
没有哪种服务能完全避免可能出现的失误,而系统的成本明显依赖于其稳定性。
因此,必须在稳定性与成本之间找到平衡点,而最终的选择应是负载大小、特点、可能出现中断的原因、用户要求等的综合体现。
然而,网络可靠性的增加是通过应用一定数量的生成单元和在发电站港湾各分区间以及在国内、国际电网传输线路中使用自动断路器得以实现的。
事实上大型系统包括众多的发电站和由高容量传输线路连接的负载。
这样,在不中断总体服务的前提下可以停止单个发电单元或一套输电线路的运作。
当今生成和传输电力最普遍的系统是三相系统。
相对于其他交流系统而言,它具有简便、节能的优点。
尤其是在特定导体间电压、传输功率、传输距离和线耗的情况下,三相系统所需铜或铝仅为单相系统的75%。
三相系统另一个重要优点是三相电机比单相电机效率更高。
大规模电力生产的能源有:1.从常规燃料(煤、石油或天然气)、城市废料燃烧或核燃料应用中得到的蒸汽;2.水;3.石油中的柴油动力。
其他可能的能源有太阳能、风能、潮汐能等,但没有一种超越了试点发电站阶段。
在大型蒸汽发电站中,蒸汽中的热能通过涡轮轮转换为功。
涡轮必须包括安装在轴承上并封闭于汽缸中的轴或转子。
转子由汽缸四周喷嘴喷射出的蒸汽流带动而平衡地转动。
蒸汽流撞击轴上的叶片。
中央电站采用冷凝涡轮,即蒸汽在离开涡轮后会通过一冷凝器。
冷凝器通过其导管中大量冷水的循环来达到冷凝的效果,从而提高蒸汽的膨胀率、后继效率及涡轮的输出功率。
而涡轮则直接与大型发电机相连。
电子类常用中英文翻译对照表
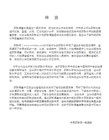
M(motor) 电动机
MCT(MOS controlled gyrator) 场控晶闸管
MIC(microphone) 话筒,微音器,麦克风
EPROM(erasable programmable read only memory) 可擦可编程
只读存储器
EEPROM(electrically EPROM) 电可擦可编程只读存储器
ESD(electro-static discharge) 静电放电
BCR(buffer courtier reset) 缓冲计数器
BZ(buzzer) 蜂鸣器,蜂音器
C(capacitance,capacitor) 电容量,电容器
CATV(cable television) 电缆电视
CS(control signal) 控制信号
D(diode) 二极管
DAST(direct analog store technology) 直接模拟存储技术
DC(direct current) 直流
分微分(控制器)
LAS(light activated switch)光敏开关
LASCS(light activated silicon controlled switch) 光控可控
硅开关
LCD(liquid crystal display) 液晶显示器
ADM(adaptive delta modulation) 自适应增量调制
ADPCM(adaptive differential pulse code modulation) 自适应
差分脉冲编码调制
永磁发电机外文翻译

本科生毕业设计(论文)文献翻译设计(论文)题目:车用永磁发电机电子稳压器(驱动和保护电路设计)分院:专业班级:姓名:学号:指导教师:教师职称:完成日期:毕业设计(论文)文献翻译1.所译外文资料:The Promising Future of Permanent Magnet GeneratorSHI Li-wei1, ZHANG Xue-yi1, GENG Song-liang1, WANG Ya-lin1, LI Ai-jun1,LI Xian-wen2[Abstract] After the introduction of the late automobile generator, the outstanding advantage of permanent magnet generator is presented systemically, and the promising appliance prospect is thus declared.[Key words] eletric engineering; generator; summarize; permanent magnet1 A motor generator status quo at home and abroadAt present, domestic and foreign automotive generator is Silicon ectifier generators. The electricity generator from a magnetic field winding, the field winding rotor easily destroyed, disconnected, power consumption, and must be provided by the exciting current batteries can power generation, this will inevitably increase the cost of the automobile. Silicon Rectifier generators with a brushless slip ring structure, slip ring diameter, high-speed, brushless easy to wear, short life expectancy, the high failure rate; other is the brushless generators, it increases the magnetic field gap , MFL, material utilization low and high cost. Domestic agricultural vehicles used by the generators is mainly ferrite magnets alternators, 200 W power in the following, not directly to the agricultural vehicle with the blowing rain, the plane heater, electric speakers, such as DC power, nor can the battery charging.At present, many domestic and foreign research institutes, enterprises invested a great deal of funds for permanent magnet motor generator Development of work. Are:(1) Permanent Magnet DC generator. Or through the use of ferrite materials and rare earth permanent magnets Series electronic regulator and generator windings and structural re-design, generating a stable output voltage direct current.(2) hybrid excitation generators. Its main magnetic field provided by the permanentmagnet, the field winding only regulate magnetic field, to overcome the Silicon Rectifier brushless slip ring generators installed with the shortcomings of complex structures, low cost performance.2 permanent magnet generators main advantages(1) structure is simple, reliable work. Permanent magnet generators to avoid a power generator excitation of the field winding-burning, carbon brush and disconnected, easy to wear slip-ring problems, improve reliability. Electronic regulators and as one of the generators, so that the generators of DC output, small size, light weight, the use of maintenance-friendly.(2) a single-phase dual-half-wave controlled rectifier technology. SCR to achieve with two DC output voltage regulator to replace the silicon rectifying the six generators Zheng Liuguan composed of three-phase rectifier bridge and regulating the rotor exciting current size of the electronic regulator. As the auto generator power, the output voltage to 14 V, output current, current per PN junction decline after a 0.7 V. By Q = IUt is understood that the current is, the more heat. PN junction of the large number of fever is not only a waste of the effective power generators, cooling and solve a difficult problem. Power generator output in the same circumstances, single-phase dual-half-wave controlled rectifier regulator circuit power consumption, comparable bridge rectifier circuit of low power consumption 50 percent, reduce the heat to raise the output power, and that the circuit - StabilityPressure, rectifier in one, greatly reducing costs.(3)More then 350 W generator, a high magnetic NdFeB rare earth permanent magnet materials, efficient use of our unique rare earth resources, rare metals and copper to reduce our dependence on foreign imports. The permanent magnetic materials with high energy product, the smaller size will be able to provide large enough magnetic field, making the internal structure of compact generators, small size, light weight. Simplify the structure of the rotor also made to reduce the rotor moment of inertia, practical speed increase over the power (that is, power, volume ratio) to achieve a higher value. 750W of NdFeB permanent magnet generators and350 W silicon rectifying the quality of a generator. The permanent magnet materials also have a high residual magnetism induction intensity and coercive force, to magnetic curve for a straight line, almost no irreversible demagnetization.(4) less than 350 W for the generators, ferrite magnets used materials. Because this material is non-REE cobalt, nickel and other metals, low prices. Ferrite magnets used for rotor material, generator performance can also achieve the use of agricultural vehicles requirements. According to generator power output parameters corresponding select permanent magnetic materials, generators can meet performance requirements, but also improve the economic generators, and better meet the needs of the market.(5) high efficiency. Permanent magnet excitation generators, no electric field winding power consumption, which alone can improve the efficiency of electricity generation from 10% to 15%. The design of a permanent magnet rotor rotor, the need to provide exciting current rotating magnetic field, the rotor is also no electricity brushless excitation rotor and slip ring between the mechanical wear and tear, it can improve the efficiency of generating more than 5 percent.(6) wide use, charging effect distinctions. Generator not only has the regulator function, but also output DC, for battery charging, or direct-drive DC needed for the blowing rain, the plane heater, electric speakers, and so on. V oltage regulation of small, can effectively prevent the battery plate sulfide, will not charge less, will not be a charge. In the process of charging always maintain a small amount of Export, and will not produce large bubble. This is not a lot of electrolyte depletion and pollution battery surface, but also effectively avoid the intense Export and because of the active material loss,Thus extended battery life.3 prospect of permanent magnet generatorsFarm vehicle ferrite magnets alternator has been widely applied in China. It uses parallel regulator technology (as shown in Figure 1), a stable output voltage alternating current, with outstanding cost performance, it is proved in practice agricultural vehicles generating the optimal choice. Because of large passenger carsand power generators, especially in large air-conditioned car idling at greater consumption of electricity, silicon rectifying generators can only rely on increased transmission ratio to improve low-speed performance, and the permanent magnet generators in power than when idling Exciting-high output power generators doubled, to tackle the vehicle idling consumption big problem.Figure 1 exchange regulator principle of constant pressure generatorPermanent magnet motor generator, the structure and its advanced high-performance, the decision of the vitality of the product and market competitiveness, will replace silicon rectifying generators, improve the electrical system of the automobile the overall level of China's automobile industry to promote technology Progress. Therefore, high-efficiency, cost-effective and high stability of the permanent magnet generators will have a high value of theoretical research and broad application prospects for promotion.中文:具有开发前途的车用永磁发电机史立伟1,张学义1,耿松亮1,王亚林1,李爱军1,李贤温2[摘要] 分析了车用发电机的发展现状,总结了永磁发电机的高效率、高性能价格比及高稳定性的特点,指出了永磁发电机具有广阔的应用前景。
(完整版)电机学英文文献翻译

(完整版)电机学英文文献翻译The three-phase induction motor speed control methodThree-phase asynchronous motor speed formula: N = 60f / p (1-s) Can be seen from the above formula, change the power supply frequency f, motor pole number p and the slip s may be too much to change the speed of purpose. From the speed of the essence of view, is simply a different way to change speed synchronous AC motor does not change the sync transfer speed or two.Widespread use in production machines without changing the synchronous speed of motor speed control method Wound Rotor Series Resistance Speed, chopper speed control, cascade control, and application of electromagnetic slip clutch, fluid couplings, clutches and other film speed. Change the synchronous speed of change on the number of stator pole multi-speed motor to change the stator voltage and frequency to frequency conversion with no change to the motor speed and so on.Energy from the speed point of view when, with high speed method and inefficient methods of two kinds of speed: high speed when the slip refers to the same, so no slip losses, such as multi-speed motors, Slip frequency control and loss can speed recovery methods (such as cascade control, etc.). A deteriorating loss of speed control methodsare inefficient speed, such as series resistance of the rotor speed method, the energy loss in the rotor circuit on; Electromagnetic Clutch The speed method, the energy loss in the clutch coils; fluid coupling speed, energy loss in the fluid coupling of the oil. General deterioration in loss increased with theexpansion speed range, if not speed range, the energy loss is minimal.1, variable speed control method of pole pairsThis speed is then used to change the stator winding way to change the red cagemotor stator pole pairs to achieve speed control purposes, the followingfeaturesWith hard mechanical properties, good stability;No slip loss, high efficiency; Wiring simple, easy to control, low price;A level speed, differential large, can not get smooth speed control;With pressure and speed adjustment, with the use of electromagnetic slip clutch,smooth and efficient access to high speed characteristics.This method is suitable for the production does not require variable speed machinery, such as metal cutting machine Bed , Lift , Lifting equipment, Fans Water Pump And so on.2, Frequency Control Method Frequency control is to change the motor stator Power supply Frequency, thus changing the speed of its synchronous speed method. Frequency control system main equipment is to provide variable frequency power supply Inverter , Inverter can be divided into AC - DC - AC inverter and AC - AC converter two categories, most of the current domestic use of AC - DC - AC inverter. Its characteristicsHigh efficiency, speed the process without additional loss;Wide range of applications, can be used for cage induction motor;。
风力发电机毕业论文英文文献翻译

附录一英文文献Wind Energy Introduction1.1 Historical DevelopmentWindmills have been used for at least 3000 years, mainly for grinding grain or pumping water, while in sailing ships the wind has been an essential source of power for even longer. From as early as the thirteenth century, horizontal-axis windmills were an integral part of the rural economy and only fell into disuse with the advent of cheap fossil-fuelled engines and then the spread of rural electrification.The use of windmills (or wind turbines) to generate electricity can be traced back to the late nineteenth century with the 12 kW DC windmill generator constructed by Brush in the USA and the research undertaken by LaCour in Denmark. However, for much of the twentieth century there was little interest in using wind energy other than for battery charging for remote dwellings and these low-power systems were quickly replaced once access to the electricity grid became available. One notable exception was the 1250 kW Smith–Putnam wind turbine constructed in the USA in 1941. This remarkable machine had a steel rotor 53 m in diameter, full-span pitch control and flapping blades to reduce loads. Although a blade spar failed catastrophically in 1945, it remained the largest wind turbine constructed for some 40 years (Putnam, 1948).Golding (1955) and Shepherd and Divone in Spera (1994) provide a fascinating history of early wind turbine development. They record the 100 kW 30 m diameter Balaclava wind turbine in the then USSR in 1931 and the Andrea Enfield 100 kW 24 m diameter pneumatic design constructed in the UK in the early 1950s. In this turbine hollow blades, open at the tip, were used to draw air up through the tower where another turbine drove the generator. In Denmark the 200 kW 24 m diameter Gedser machine was built in 1956 while Electricite´de France tested a 1.1 MW 35 m diameter turbine in 1963. In Germany, Professor Hutter constructed a number of innovative, lightweight turbines in the 1950s and 1960s. In spite of these technical advances and the enthusiasm, among others, of Golding at the Electrical Research Association in the UK there was little sustained interest in wind generation until the price of oil rose dramatically in 1973.The sudden increase in the price of oil stimulated a number of substantial Government-funded programmes of research, development and demonstration. In the USA this led to the construction of a series of prototype turbines starting with the 38 m diameter 100 kW Mod-0 in 1975 and culminating in the 97.5 m diameter 2.5 MW Mod-5B in 1987. Similar programmes were pursued in the UK, Germany and Sweden. There was considerable uncertainty as to which architecture might prove most cost-effective and several innovative concepts were investigated at full scale. In Canada, a 4 MW vertical-axis Darrieus wind turbine was constructed and this concept was also investigated in the 34 m diameter Sandia Vertical Axis Test Facility in the USA. In the UK, an alternative vertical-axis design using straight blades to give an ‘H’ type rotor was proposed by Dr Peter Musgrove and a 500 kW prototypeconstructed. In 1981 an innovative horizontal-axis 3 MW wind turbine was built and tested in the USA. This used hydraulic transmission and, as an alternative to a yaw drive, the entire structure was orientated into the wind. The best choice for the number of blades remained unclear for some while and large turbines were constructed with one, two or three blades.Much important scientific and engineering information was gained from these Government-funded research programmes and the prototypes generally worked as designed. However, it has to be recognized that the problems of operating very large Figure 1.1 1.5 MW, 64 m diameter Wind Turbine (Reproduced by permission of NEG MICON)wind turbines, unmanned and in difficult wind climates were often under-estimated and the reliability of the prototypes was not good. At the same time as the multi-megawatt prototypes were being constructed private companies, often with considerable state support, were constructing much smaller, often simpler,turbines for commercial sale. In particular the financial support mechanisms in California in the mid-1980s resulted in the installation of a very large number of quite small(<100 kW) wind turbines. A number of these designs also suffered from various problems but,being smaller, they were in general easier to repair and modify. The so-called 'Danish' wind turbine concept emerged of a three-bladed,stall-regulated rotor and a fixed-speed, induction machine drive train. This decep-tively simple architecture has proved to be remarkably successful and has now been implemented on turbines as large as 60 m in diameter and at ratings of 1.5 MW. The machines of Figures 1.1 and 1.2 are examples of this design. However, as the sizes of commercially available turbines now approach that of the large prototypes of the 1980s it is interesting to see that the concepts investigated then of variable-speed operation, full-span control of the blades, and advanced materials are being used increasingly by designers. Figure 1.3 shows a wind farm of direct-drive, variable-speed wind turbines. In this design, the synchronous generator is coupled directly to the aerodynamic rotor so eliminating the requirement for a gearbox. Figure 1.4 shows a more conventional, variable-speed wind turbine that uses a gearbox, while a small wind farm of pitch-regulated wind turbines, where full-span control of the blades is used to regulate power, is shown in Figure 1.5.Figure 1.2 750 kW, 48 m diameter Wind Turbine, Denmark (Reproduced by permission of NEG MICON)Figure 1.3 Wind Farm of Variable-Speed Wind Turbines in Complex Terrain (Reproduced by permission of Wind Prospect Ltd)Figure 1.4 1 MW Wind Turbine in Northern Ireland (Reproduced by permission of Renew-able Energy Systems Ltd)The stimulus for the development of wind energy in 1973 was the price of oil and concern over limited fossil-fuel resources. Now, of course, the main driver for use of wind turbines to generate electrical power is the very low C emissions (over the entire life cycle of manufacture, installation, operation and de-commissioning)Figure 1.5 Wind Farm of Six Pitch-regulated Wind Turbines in Flat Terrain (Reproduced by permission of Wind Prospect Ltd)and the potential of wind energy to help limit climate change. In 1997 the Commis-sion of the European Union published its White Paper (CEU, 1997) calling for 12 percent of the gross energy demand of the European Union to be contributed from renewables by 2010. Wind energy was identified as having a key role to play in the supply of renewable energy with an increase in installed wind turbine capacity from 2.5 GW in 1995 to 40 GW by 2010. This target is likely to be achievable since at the time of writing, January 2001, there was some 12 GW of installed wind-turbine capacity in Europe, 2.5 GW of which was constructed in 2000 compared with only 300 MW in 1993. The average annual growth rate of the installation of wind turbines in Europe from 1993-9 was approximately 40 percent (Zervos, 2000). The distribution of wind-turbine capacity is interesting with, in 2000, Germany account- ing for some 45 percent of the European total, and Denmark and Spain each having approximately18 percent. There is some 2.5 GW of capacity installed in the USA of which 65 percent is in California although with increasing interest in Texas and some states of the midwest. Many of the California wind farms were originallyconstructed in the 1980s and are now being re-equipped with larger modern wind turbines.Table 1.1 shows the installed wind-power capacity worldwide in January 2001 although it is obvious that with such a rapid growth in some countries data of this kind become out of date very quickly.The reasons development of wind energy in some countries is flourishing while in others it is not fulfilling the potential that might be anticipated from a simple consideration of the wind resource, are complex. Important factors include the financial-support mechanisms for wind-generated electricity, the process by which the local planning authorities give permission for the construction of wind farms,and the perception of the general population particularly with respect to visual impact. In order to overcome the concerns of the rural population over the environ-mental impact of wind farms there is now increasing interest in the development of sites offshore.1.2 Modern Wind TurbinesThe power output, P, from a wind turbine is liven by the well-known expression:P=where ρ is the density of air (1.225 kg/), is the power coefficient, A is the rotor swept area, and U is the wind speed.The density of air is rather low, 800 times less than that of water which powershydro plant, and this leads directly to the large size of a wind turbine. Depending on the design wind speed chosen, a 1.5 MW wind turbine may have a rotor that is more than 60 m in diameter. The power coefficient describes that fraction of the power in the wind that may be converted by the turbine into mechanical work. It has a theoretical maximum value of 0.593 (the Betz limit) and rather lower peak values are achieved in practice (see Chapter 3). The power coefficient of a rotor varies with the tip speed ratio (the ratio of rotor tip speed to free wind speed) and is only a maximum for a unique tip speed ratio. Incremental improvements in the power coefficient are continually being sought by detailed design changes of the rotor and, by operating at variable speed, it is possible to maintain the maximum power coefficient over a range of wind speeds. However, these measures will give only a modest increase in the power output. Major increases in the output power can only be achieved by increasing the swept area of the rotor or by locating the wind turbines on sites with higher wind speeds.Hence over the last 10 years there has been a continuous increase in the rotor diameter of commercially available wind turbines from around 30 m to more than 60 m. A doubling of the rotor diameter leads to a four-times increase in power output. The influence of the wind speed is, of course, more pronounced with a doubling of wind speed leading to an eight-fold increase in power. Thus there have been considerable efforts to ensure that wind farms are developed in areas of the highest wind speeds and the turbines optimally located within wind farms. In certain countries very high towers are being used (more than 60-80 m) to take advantage of the increase of wind speed with height.In the past a number of studies were undertaken to determine the 'optimum size of a wind turbine by balancing the complete costs of manufacture, installation and operation of various sizes of wind turbines against the revenue generated (Mollyet al. 1993). The results indicated a minimum cost of energy would be obtained with wind turbine diameters in the range of 35-60 m, depending on the assumptions made. However, these estimates would now appear to be rather low and there is no obvious point at which rotor diameters, and hence output power, will be limited particularly for offshore wind turbines.All modern electricity-generating wind turbines use the lift force derived from the blades to drive the rotor. A high rotational speed of the rotor is desirable in order to reduce the gearbox ratio required and this leads to low solidity rotors (the ratio of blade area/rotor swept area). The low solidity rotor acts as an effective energy concentrator and as a result the energy recovery period of a wind turbine, on a good site, is less than 1 year, i.e., the energy used to manufacture and install the wind turbine is recovered within its first year of operation (Musgrove in Freris, 1990).附录二英文翻译风能介绍1.1发展历史风车的使用至少已有三千年,主要用于磨粒或泵站水,而在帆船风已成为不可缺少的电力来源甚至更长的一段时间。
用英文写关于发电机的作文

用英文写关于发电机的作文英文:As a generator, I have a very important role in providing electricity to many different places and people.I work by converting mechanical energy into electrical energy, which is then distributed through power lines to homes, businesses, and other locations.One of the most important components of a generator is the rotor, which is the rotating part of the generator that contains the wire coils. When the rotor spins, it creates a magnetic field that interacts with the stationary coils of wire in the stator, producing an electrical current.Another important component of a generator is the fuel source. Many generators run on gasoline or diesel fuel, while others may use natural gas, propane, or even renewable energy sources like wind or solar power.In addition to providing power during emergencies or power outages, generators are also used in many other applications. For example, they are often used on construction sites where there is no access to electrical power, or in remote areas where there is no electrical grid.Overall, generators play a crucial role in our modern society by providing the electricity that powers our homes, businesses, and other essential infrastructure.中文:作为一台发电机,我在为许多不同的地方和人们提供电力方面扮演着非常重要的角色。
外文翻译---发电机和变压器

附录一英文原文Generator And TransformerThe turbine turns the rotor of the electric generator in whose stator are embedded three windings. In the process mechanical power from the turbine drive is converted to three phase alternating current at voltages in the range of 11kV to 30kV line to line at a frequency of 60 Hz in the United States. The voltage is usually stepped up by transmission to remote load centers.A generator (also called an alternator or synchronous generator)is shown in longitudinal cross section; the transverse across section is approximately round. The roctoe is called round or cylindrical or smooth. We note that steam-driven turbine-generators are usually two-pole or four-pole, turning at 3600 rpm or 1800 rmp, espectively, corresponding to 60Hz.The high speeds are needed to achieve high steam turbine efficiencies. At these rotation rates, high centrifugal forces limit rotor diameters to about 3.5 ft for two pole and 7 ft for four-pole machines.The average power ratings of the turbine-generator units we have been describing have been increasing,scince1960s, fromabout 300MW to about 600MW,with maximum sizes up to about 1300MW.Inceased ratings are accompained by increased rotor and stator size, and with rotor diameters limited by centrifugal forces, the rotor lengths have been increasing. Thus in the larger sizes, the rotor lengths may be five to six times the diameters. These slender rotors resonate at critical speeds below their rated speeds and care is requied in operation to avoid sustained operation at these speeds.A Transformer is a device that changes ac electric energy at one voltage level into ac electric energy at another voltage level through the action of a magnetic field. It consists of two or more coils of wire wrapped around a common ferro magnetic core. These coils are not directly connected. The only connection between the coils is the common magnetic flux present within the core.One of the transformer windings is connected to a source of ac electric power, and the second(and perhaps third)transformer winding supplies electric power to load. The transformer winding connected to the power source is called the primary winding or input winding, and the winding connected to the power source is called the primary winding or output winding. If there is a third winding on the transformer, it is calledthe tertiary winding.Power transformer is constructed on one of two types of cores. One type of construction consists of a simple rectangular laminated piece of steel with the transformer windings wrapped around two sides of the rectangle. This type of construction is known as core form. The other type consists of a three-legged laminated core with the windings wrapped around the center leg. This type of construction is known as shell form. In either case, the core is constructed of thin laminations electrically isolated from each other in order to reduce eddy currents to a minimn.The primary and secondary windings in a physical transformer are wrapped one on top of the other with low-voltage winding innermost. Such an arrangement serves two purpose: (1)It simplifies the problem of insulating the high-voltage winding from the core. (2)It results in much less leakAge flux than would be the two windings were separated by a distance on the core.Power transformers are given a variety of different names, depending on there use in power systems. A transformer connected to the output of a generator and used to step its voltage to transmission levels is sometimes called a unit transformer. The transformer at the other end of thetransmission line, which steps the voltage down from transmission levels, is called a substation transformer. Finally, the transformer that takes his distribution levels, is called a distribution transformer. All these devices are essentially the same-the only difference among them is their intended use.In addition to the various power transformer, two-special purpose transformers are used with electric machinery and power systems. The first of these special transformers is a device specially designed to sample a high voltage and produce a low secondary voltage directly proportional to it. Such a transformer is called a potential transformer. A power transformer also produces a secondary voltage directly proportional to its primary voltage; the different between a potential transformer and a power transformer is that the potential transformer is designed to handle only a very small current. The second type of special transformer is a device designed to provide a secondary current much smaller than but directly proportional to its primary current. This device is called a current transformer.Transformers come in many sizes. Some power transformers are as big as a house. Electronic transformers, on the other hand, can be as small as a cube of sugar. All transformers have at least one coil; most have two although they may have many more.The usual purpose of transformers is to change the level of voltage. But sometimes they are used to isolate a load from the power source.Standard power transformers have two oils. These coils are labeled PRIMARY and SECONDARY. The primary coil is the one connected to the source. The secondary is the one connected to the load .There is no electrical connection between the primary and secondary. The secondary gets its voltage by induction.The only place where you will see a STEP-UP transformer is at the generating station. Typically, electricity is generated at 13,800 volts. It is stepped up to 345,000 volts for transmission. The next stop is the substation where it is stepped down to distribution levels, around 15,000 volts. Large substation transformers have cooling fins to keep them from overheating. Other transformers are located near points where the electric power is used.The coils of transformer are electrically are electrically insulated from each other. There is a magnetic link, however. The two coils are wound on the same core. Current in the primary magnetizes the core. This produces a magnetic field in the core. The core field then affects current in both primary and secondary.There are two main designs for cores:1.The CORE type has the core inside the windings.2.The SHELL type has the core outside.Smaller power transformers are usually of the core type. The very large transformers are of the shell type. There is no different in their operation, however.Coils are wound with copper wire. The resistance is kept as low as possible to keep losses low.Transformers are very efficient. The losses are often less than 3 percent. This allows us to assume that they are perfect in many computations.Perfect means that the wire has no resistance. It also means that there are no power losses in the core.Further, we assume that there is no flux leakAge. That is, all of the magnetic flux links all of the turns on each coil.To get an idea of just how small the losses are ,we can take a look at the EXCITATION CURRENT. Assume that nothing is connected to the secondary. If you apply rated voltage to the primary, a small current flows. Typically, this excitation current is less than 3 percent of rated current supplies the power lost in the core. Core losses are due to EDDY CURRENTS and HYSTERESIS.Eddy currents circulating in the core result from induction .The core is, after all, a conductor within a changing magnetic field.Hysteresis loss is caused by the energy used in lining up magnetic domains in the core. The alignment goes on continuously, first in one direction, then in the other.The other part of the excitation current magnetizes the core. It is this magnetizing current that supplies the “shuttle power”. Shuttle power is power stored in the magnetic field and returned to the source twice each cycle. Magnetizing current is quadrature with the applied voltage.Excitation current is made up of two parts. One part is in phase with the voltage.The losses that occur in real transformers have to be accounted for in any accurate model of transformer behavior.The major items to be considered in the construction shuttle such a model are.(i)Copper losses. Copper losses are the resistive heating losses in the primary and secondary windings of the transformer. They are proportional to there turn square of the current in the windings.(ii)Eddy current losses. Eddyysteresis loss is current losses are resistive heating losses in the core of the transformer.(iii)Hysteresis losses. These losses are associated with the rearrangement of the magnetic domains in the core during each half-cycle.(iv)LeakAge flux. The fluxes which escape the core and pass through only one of the transformer windings are leakAge fluxes. These escaped fluxes produce a self-inductance in the primary and secondary coils, and the effects of this inductance must be accounted for英文译文发电机和变压器汽轮机驱动发电机的转子,通过嵌在其定子槽内的三相绕组将输入的机械能转变为三相交流电能。
- 1、下载文档前请自行甄别文档内容的完整性,平台不提供额外的编辑、内容补充、找答案等附加服务。
- 2、"仅部分预览"的文档,不可在线预览部分如存在完整性等问题,可反馈申请退款(可完整预览的文档不适用该条件!)。
- 3、如文档侵犯您的权益,请联系客服反馈,我们会尽快为您处理(人工客服工作时间:9:00-18:30)。
ENGLISH ORIGINAL TEX T①DC GENENRATORS1. INTRODUCTIONFor all practical purposes, the direct-current generator is only used for special applications and local dc power generation. This limitation is due to the commutator required to rectify the internal generated ac voltage, thereby making largescale dc power generators not feasible.Consequently, all electrical energy produced commercially is generated and distributed in the form of three-phase ac power. The use of solid state converters nowadays makes conversion to dc economical. However, the operating characteristics of dc generators are still important, because most concepts can be applied to all other machines.2. FIELD WINDING CONNECTIONSThe general arrangement of brushes and field winding for a four-pole machine is as shown in Fig.1. The four brushes ride on the commutator. The positive brusher are connected to terminal A1 while the negative brushes are connected to terminal A2 of the machine. As indicated in the sketch, the brushes are positioned approximately midway under the poles. They make contact with coils that have little or no EMF induced in them, since their sides are situated between poles.Figure 1 Sketch of four-pole dc matchineThe four excitation or field poles are usually joined in series and their ends brought out to terminals marked F1 and F2. They are connected such that they produce north and south poles alternately.The type of dc generator is characterized by the manner in which the field excitation is provided. In general, the method employed to connect the field and armature windings falls into the following groups (see Fig.2):Figure2 Field connections for dc generators:(a)separately excited generator;(b)self-excited,shunt generator;(c)series generator;(d)compoundgenerator;short-shunt connection;(e)compound generator,long-shunt connection.The shunt field contains many turns of relatively fine wire and carries a comparatively small current, only a few percent of rated current. The series field winding, on the other hand, has few turns of heavy wire since it is in series with the armature and therefore carries the load current.Before discussing the dc generator terminal characteristics, let us examine the relationship between the generated voltage and excitation current of a generator on no load. The generated EMF is proportional to both the flux per pole and the speed at which the generator is driven, EG=kn. By holding the speed constant it can be shown the EG depends directly on the flux. To test this dependency on actual generators is not very practical, as it involves a magnetic flux measurement. The flux is produced by the ampere-turns of the field coils: in turn, the flux must depend on the amount of field current flowing since the number of turns on the field winding is constant. This relationship is not linear because of magnetic saturation after the field current reaches a certain value. The variation of EG versus the field current If may be shown by a curve known as the magnetization curve or open-circuit characteristic. For this a given generator is driven at a constant speed, is not delivering load current, and has its field winding separately excited.The value of EG appearing at the machine terminals is measured as If is progressively increased from zero to a value well above rated voltage of that machine. The resulting curve is shown is Fig.3. When Ij=0, that is, with the field circuit open circuited, a small voltage Et is measured, due to residual magnetism. As the field current increases, the generated EMF increases linearly up to the knee of the magnetization curve. Beyond this point, increasing the field current still further causes saturation of the magnetic structure to set in.Figure 3 Magnetization curve or open-circuit characteristic of a separately excited dcmachineThe means that a larger increase in field current is required to produce a given increase in voltage.Since the generated voltage EG is also directly proportional to the speed, a magnetization curve can be drawn for any other speed once the curve is determined. This merely requires an adjustment of all points on the curve according to n n x E E G G ''where the quantities values at the various speeds.3. VOLTAGE REGULATIONLet us next consider adding a load on generator. The terminal voltage will then decrease (because the armature winding ha resistance) unless some provision is made to keep it constant. A curve that shows the value of terminal voltage for various load currents is called the load or characteristic of the generator.Figure 4 (a) directs current it to urge the generator load characteristics; (b) circuitdiagramFig.4 shows the external characteristic of a separately excited generator. The decrease in the terminal voltage is due mainly to the armature circuit resistance RA. In general,A A G t R I E V -=where Vt is the terminal voltage and IA is the armature current (or load current IL) supplied by the generator to the load.Another factor that contributes to the decrease in terminal voltage is the decrease in flux due to armature reaction. The armature current established an MMF that distorts the main flux, resulting in a weakened flux, especially in noninterpole machines. This effect is called armature reaction. As Fig.4 shows, the terminal voltage versus load current curve does not drop off linearly since the iron behaves nonlinear. Because armature reaction depends on the armature current it gives the curve its drooping characteristic.4. SHUNT OR SELF-EXCIITED GENRATORSA shunt generator has its shunt field winding connected in parallel with the armature so that the machine provides its own excitation, as indicated in Fig.5. The question arises whether the machine will generate a voltage and whatdetermines the voltage.For voltage to “build up” as it is called, there must be some remanent magnetism in the field poles. Ordinarily, if the generator has been used previously, there will be some remanent magnetism. We have seen in Section 3 that if the field would be disconnected, there will be small voltage Ef generated due to this remanent magnetism, provided that the generator is driven at some speed. Connecting the field for self-excitation, this small voltage will be applied to the shunts field and drive a small current through the field circuit. If this resulting small current in the shunt field is of such a direction that it weakens the residual flux, the voltage remains near zero and the terminal voltage does not build up. In this situation the weak main pole flux opposes the residual flux.Figure 5 Shunt generator:(a)circuit;(b)load characteristicIf the connection is such that the weak main pole flux aids the residual flux, the induced voltage increases rapidly to a large, constant value. The build-up process is readily seen to be cumulanve. That is, more voltage increases the field current, which in turn increases the voltage, and so on. The fact that this process terminates at a finite voltage is due to the nonlinear behavior of the magnctic circuit. In steady state the generated voltage is causes a fieldcurrent to flow that is just sufficient to develop a flux required for the generated EMF that causes the field current to flow.The circuit carries only dc current, so that the field current depends only on the field circuit resistance, Rf. This may consist of the field circuit resistance Rf, the field current depends on the generated voltage in accordance with Ohm ’s law.It should be evident that on a new machine or one that has lost its residual flux because of a long idle period, some magnetism must be created. This is usually done by connecting the field winding only to a separate dc source for a few seconds. This procedure is generally known as flashing the field.Series GeneratorsAs mentioned previously, the field winding of a series generator is in series with the armature. Since it carries the load current the series field winding consists of only a few turns of thick wire. At no load, the generated voltage is small due to residual field flux only. When a load is added, the flux increases, and so does the generated voltage. Fig.7 shows the load characteristic of a series generator driven at a certain speed. The dashed line indicates the generated EMF of the same machine with the armature open-circuited and the field separately excited. The difference between the two curves is simply the IR drop in the series field and armature winding, such that)(S A A G t R R I E V +-=where RS is the series field winding resistance.Figure 7 Series generator: (a)circuit diagram;(b)load characteristicsCompound GeneratorsThe compound generator has both a shunt and a series field winding, the latter winding wound on top of the shunt winding. Fig.8 shows the circuit diagram. The two windings are usually connected such that their ampere-turns act in the same direction. As such the generator is said to be cumulatively compounded.The shunt connection illustrated in Fig.8 is called a long shunt connection. If the shunt field winding is directly connected across the armature terminals, the connection is referred to as a short shunt. In practice the connection used is of little consequence, since the shunt field winding carries a small current compared to the full-load current. Furthermore, the number of turns on the series field winding. This implies it has a low resistance value and the corresponding voltage drop across it at full load is minimal.Curves in Fig.9 represents the terminal characteristic of the shunt field winding alone. By the addition of a small series field winding the drop in terminal voltage with increased loading is reduced as indicated. Such a generator is said to be undercompounded. By increasing the number of series turns, the no-load and full-load terminal voltage can be made equal; the generator is then said to be flatcompounded. If the number of series turns is more than necessary to compensate for the voltage drop, the generator is overcome pounded. In thatcase the full-load voltage is higher than the no-load voltage.Figure 9 Terminal characteristics of compound generators compared with that of the shunt generatorThe overcompounded generator may be used in instances where the load is at some distance from the generator. The voltage drops in the feeder lines are the compensated for with increased loading. Reversing the polarity of the series field in relation to the shunt field, the fields will oppose each other more and more as the load current increase. Such a generator is said to be differentially compounded. It is used in applications where feeder lines could occur approaching those of a short circuit. An example would be where feeder lines could break and short circuit the generator. The short-circuit current, however, is then limited to a “safe” value. The terminal characteristic for this type of generator is also shown in Fig.9. Compound generators are used more extensively than the other types because they may be designed to have a wide varity of terminal characteristics.As illustrated, the full-load terminal voltage can be maintained at the no-load value by the proper degree of compounding. Other methods of voltage control are the use of rheostats, for instance, in the field circuit. However, with changing loads it requires a constant adjustment of the field rheostat to maintain the voltage. A more useful arrangement, which is now common practice,is to use an automatic voltage regulator with the generator. In essence, the voltage regulator is a feedback control system. The generator output voltage is sensed and compared to a fixed reference voltage deviation from the reference voltage gives an error signal that is fed to a power amplifier. The power amplifier supplies the field excitation current. If the error signal is positive, for example, the output voltage is larger than desired and the amplifier will reduce its current drive. In doing so the error signal will be reduced to zero.TRANSFORMER1. INTRODUCTIONThe high-voltage transmission was need for the case electrical power is to be provided at considerable distance from a generating station. At some point this high voltage must be reduced, because ultimately is must supply a load. The transformer makes it possible for various parts of a power system to operate at different voltage levels. In this paper we discuss power transformer principles and applications.2. TOW-WINDING TRANSFORMERSA transformer in its simplest form consists of two stationary coils coupled by a mutual magnetic flux. The coils are said to be mutually coupled because they link a common flux.In power applications, laminated steel core transformers (to which this paper is restricted) are used. Transformers are efficient because the rotational losses normally associated with rotating machine are absent, so relatively little power is lost when transforming power from one voltage level to another. Typical efficiencies are in the range 92 to 99%, the higher values applying to the larger power transformers.The current flowing in the coil connected to the ac source is called the primarywinding or simply t he primary. It sets up the flux φ in the core, which varies periodically both in magnitude and direction. The flux links the second coil, called the secondary winding or simply secondary. The flux is changing; therefore, it induces a voltage in the secondary by electromagnetic induction in accordance with Lenz’s law. Thus the primary receives its power from the source while the secondary supplies this power to the load. This action is known as transformer action.3. TRANSFORMER PRINCIPLESWhen a sinusoidal voltage Vpis applied to the primary with the secondary open-circuited, there will be no energy transfer. The impressed voltage causesa small current Iθto flow in the primary winding. This no-load current has two functions: (1) it produces the magnetic flux in the core, which varies sinusoidally between zero and φm, where φm is the maximum value of the core flux; and (2) it provides a component to account for the hysteresis and eddy current losses in the core. There combined losses are normally referred to as the core losses.The no-load current Iθis usually few percent of the rated full-load current of the transformer (about 2 to 5%). Since at no-load the primary winding acts as a large reactance due to the iron core, the no-load current will lag the primary voltage by nearly 90º. It is readily seen that the current componentI m = Isinθ, called the magnetizing current, is 90º in phase behind the primaryvoltage VP. It is this component that sets up the flux in the core; φ istherefore in phase with Im.The second component, Ie =Isinθ, is in phase with the primary voltage. It isthe current component that supplies the core losses. The phasor sum of these two components represents the no-load current, orI 0 = Im+ IeIt should be noted that the no-load current is distortes and nonsinusoidal. This is the result of the nonlinear behavior of the core material.If it is assumed that there are no other losses in the transformer, the induced voltage In the primary, E p and that in the secondary, E s can be shown. Sincethe magnetic flux set up by the primary winding ,there will be an induced EMF E in the secondary winding in accordance with Faraday’s law, namely, E=NΔφ/Δt. This same flux also links the primary itself, inducing in it an EMF, E p . As discussed earlier, the induced voltage must lag the flux by 90º,therefore, they are 180º out of phase with the applied voltage. Since no current flows in the secondary winding, E s =V s . The no-load primary current I 0 is small,a few percent of full-load current. Thus the voltage in the primary is small and V p is nearly equal to E p . The primary voltage and the resulting flux aresinusoidal; thus the induced quantities E p and E s vary as a sine function. Theaverage value of the induced voltage given byE avg = turns× change in flux in a given time given timewhich is Faraday’s law applied to a finite time interval. It follows thatE avg = N 21/(2)m f = 4fNφm which N is the number of turns on the winding. Form ac circuit theory, the effective or root-mean-square (rms) voltage for a sine wave is 1.11 times the average voltage; thusE = 4.44fNφmSince the same flux links with the primary and secondary windings, the voltage per turn in each winding is the same. HenceE p = 4.44fN p φmandE s = 4.44fN s φmwhere E p and Es are the number of turn on the primary and secondary windings,respectively. The ratio of primary to secondary induced voltage is called the transformation ratio. Denoting this ratio by a, it is seen that a = p sE E = p s N N Assume that the output power of a transformer equals its input power, not a bad sumption in practice considering the high efficiencies. What we really are saying is that we are dealing with an ideal transformer; that is, it has no losses. ThusP m = P outorV p I p × primary PF = V s I s × secondary PFwhere PF is the power factor. For the above-stated assumption it means that the power factor on primary and secondary sides are equal; thereforeV p I p = V s I sfrom which is obtainedp s V V = p s I I ≌ p sE E ≌ a It shows that as an approximation the terminal voltage ratio equals the turns ratio. The primary and secondary current, on the other hand, are inversely related to the turns ratio. The turns ratio gives a measure of how much the secondary voltage is raised or lowered in relation to the primary voltage. To calculate the voltage regulation, we need more information.The ratio of the terminal voltage varies somewhat depending on the load and its power factor. In practice, the transformation ratio is obtained from the nameplate data, which list the primary and secondary voltage under full-load condition.When the secondary voltage V s is reduced compared to the primary voltage, thetransformation is said to be a step-down transformer: conversely, if this voltage is raised, it is called a step-up transformer. In a step-down transformer the transformation ratio a is greater than unity (a>1.0), whilefor a step-up transformer it is smaller than unity (a<1.0). In the event that a=1, the transformer secondary voltage equals the primary voltage. This is a special type of transformer used in instances where electrical isolation is required between the primary and secondary circuit while maintaining the same voltage level. Therefore, this transformer is generally knows as an isolation transformer.As is apparent, it is the magnetic flux in the core that forms the connecting link between primary and secondary circuit. In section 4 it is shown how the primary winding current adjusts itself to the secondary load current when the transformer supplies a load.Looking into the transformer terminals from the source, an impedance is seenwhich by definition equals Vp / Ip. From psVV= psII≌ psEE≌ a , we have Vp=aVs and Ip= Is/a.In terms of Vsand Isthe ratio of Vpto IpisppVI=/ssaVI a=2ssa VIBut Vs / Isis the load impedance ZLthus we can say thatZm(primary) = a2ZLThis equation tells us that when an impedance is connected to the secondary side, it appears from the source as an impedance having a magnitude that is a2times its actual value. We say that the load impedance is reflected or referred to the primary. It is this property of transformers that is used in impedance-matching applications.4. TRANSFORMERS UNDER LOADThe primary and secondary voltages shown have similar polarities, as indicated by the “dot-making” convention. The dots near the upper ends of the windings have the same meaning as in circuit theory; the marked terminals have the same polarity. Thus when a load is connected to the secondary, the instantaneous load current is in the direction shown. In other words, the polarity markingssignify that when positive current enters both windings at the marked terminals,the MMFs of the two windings add.Since the secondary voltage depends on the core flux φ, it must be clear thatthe flux should not change appreciably if Esis to remain essentially constantunder normal loading conditions. With the load connected, a current Iswillflow in the secondary circuit, because the induced EMF Eswill act as a voltagesource. The secondary current produces an MMF Ns Isthat creates a flux. Thisflux has such a direction that at any instant in time it opposes the main flux that created it in the first place. Of course, this is Lenz’s law in action.Thus the MMF represented by Ns Istends to reduce the core flux φ. This meansthat the flux linking the primary winding reduces and consequently the primaryinduced voltage Ep, This reduction in induced voltage causes a greater difference between the impressed voltage and the counter induced EMF, thereby allowing more current to flow in the primary. The fact that primary currentIpincreases means that the two conditions stated earlier are fulfilled: (1) the power input increases to match the power output, and (2) the primary MMF increases to offset the tendency of the secondary MMF to reduce the flux. In general, it will be found that the transformer reacts almost instantaneously to keep the resultant core flux essentially constant. Moreover, the core fluxφdrops very slightly between n o load and full load (about 1 to 3%), anecessary condition if Ep is to fall sufficiently to allow an increase in Ip.On the primary side, Ip’is the current that flows in the primary to balance thedemagnetizing effect of Is . Its MMF NpIp’ sets up a flux linking the primaryonly. Since the core flux φ0 remains constant. Imust be the same currentthat energizes the transformer at no load. The primary current Ipis thereforethe sum of the current Ip ’ and I.Because the no-load current is relatively small, it is correct to assume that the primary ampere-turns equal the secondary ampere-turns, since it is under this condition that the core flux is essentially constant. Thus we will assumethat Iis negligible, as it is only a small component of the full-load current.When a current flows in the secondary winding, the resulting MMF (Ns Is) createsa separate flux, apart from the flux φ0 produced by I, which links thesecondary winding only. This flux does no link with the primary winding and is therefore not a mutual flux.In addition, the load current that flows through the primary winding creates a flux that links with the primary winding only; it is called the primary leakage flux. The secondary- leakage flux gives rise to an induced voltage that is not counter balanced by an equivalent induced voltage in the primary. Similarly, the voltage induced in the primary is not counterbalanced in the secondary winding. Consequently, these two induced voltages behave like voltage drops, generally called leakage reactance voltage drops. Furthermore, each winding has some resistance, which produces a resistive voltage drop. When taken into account, these additional voltage drops would complete the equivalent circuit diagram of a practical transformer. Note that the magnetizing branch is shown in this circuit, which for our purposes will be disregarded. This follows our earlier assumption that the no-load current is assumed negligible in our calculations. This is further justified in that it is rarely necessary to predict transformer performance to such accuracies. Since the voltage drops are all directly proportional to the load current, it means that at no-load conditions there will be no voltage drops in either winding.中文翻译①直流发电机1.介绍对于所有实际目的来说,直流发电机仅用于特殊场合和地方性发电厂。