多层压机生产中密度纤维板常见砂光质量问题分析及应对措施
连续平压法中密度纤维板常见质量问题及其解决措施
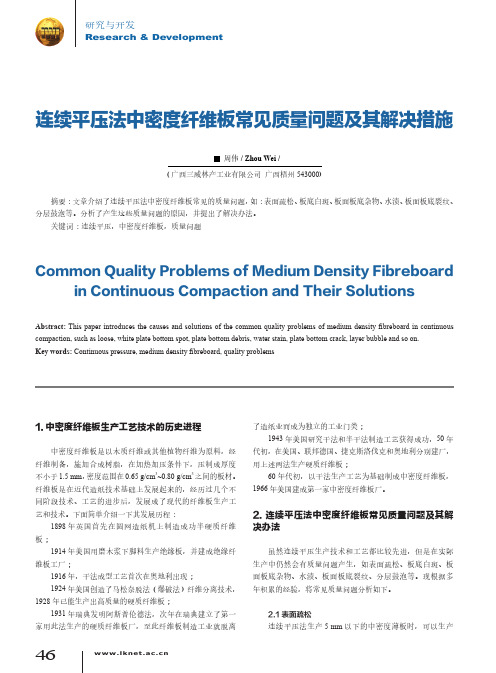
研究与开发Research & Development46w w w.l k n e t.a c.cn1.中密度纤维板生产工艺技术的历史进程中密度纤维板是以木质纤维或其他植物纤维为原料,经纤维制备,施加合成树脂,在加热加压条件下,压制成厚度不小于1.5 mm ,密度范围在0.65 g/cm 3~0.80 g/cm 3之间的板材。
纤维板是在近代造纸技术基础上发展起来的,经历过几个不同阶段技术、工艺的进步后,发展成了现代的纤维板生产工艺和技术。
下面简单介绍一下其发展历程:1898年英国首先在圆网造纸机上制造成功半硬质纤维板;1914年美国用磨木浆下脚料生产绝缘板,并建成绝缘纤维板工厂;1916年,干法成型工艺首次在奥地利出现;1924年美国创造了马松奈脱法(爆破法)纤维分离技术,1928年已能生产出高质量的硬质纤维板;1931年瑞典发明阿斯普伦德法,次年在瑞典建立了第一家用此法生产的硬质纤维板厂,至此纤维板制造工业就脱离了造纸业而成为独立的工业门类;1943年美国研究干法和半干法制造工艺获得成功,50年代初,在美国、联邦德国、捷克斯洛伐克和奥地利分别建厂,用上述两法生产硬质纤维板;60年代初,以干法生产工艺为基础制成中密度纤维板,1966年美国建成第一家中密度纤维板厂。
2. 连续平压法中密度纤维板常见质量问题及其解决办法虽然连续平压生产技术和工艺都比较先进,但是在实际生产中仍然会有质量问题产生,如表面疏松、板底白斑、板面板底杂物、水渍、板面板底裂纹、分层鼓泡等。
现根据多年积累的经验,将常见质量问题分析如下。
2.1表面疏松连续平压法生产5 mm 以下的中密度薄板时,可以生产连续平压法中密度纤维板常见质量问题及其解决措施摘要:文章介绍了连续平压法中密度纤维板常见的质量问题,如:表面疏松、板底白斑、板面板底杂物、水渍、板面板底裂纹、分层鼓泡等。
分析了产生这些质量问题的原因,并提出了解决办法。
关键词:连续平压,中密度纤维板,质量问题周伟/ Zhou Wei /(广西三威林产工业有限公司 广西梧州543000)Common Quality Problems of Medium Density Fibreboardin Continuous Compaction and Their SolutionsAbstract: This paper introduces the causes and solutions of the common quality problems of medium density fibreboard in continuous compaction, such as loose, white plate bottom spot, plate bottom debris, water stain, plate bottom crack, layer bubble and so on.Key words: Continuous pressure, medium density fibreboard, quality problems研究与开发Research & Development47International Wood Industry 2019.03压光板或者是减少砂光余量,这样能减少消耗,提高企业的经济效益,但是生产压光板时存在表面发毛现象,直接影响客户的后期使用。
层压常见质量问题原因分析和措施
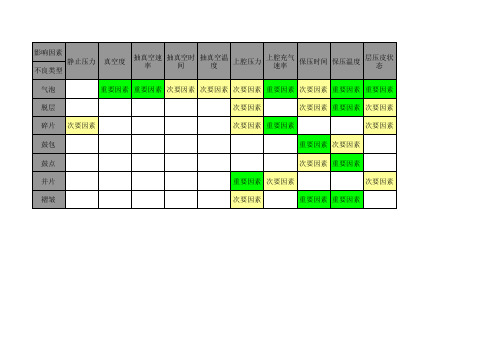
影响因素静止压力真空度抽真空速率抽真空时间抽真空温度上腔压力上腔充气速率保压时间保压温度层压皮状态不良类型气泡重要因素重要因素次要因素次要因素次要因素重要因素次要因素重要因素重要因素脱层次要因素次要因素重要因素次要因素碎片次要因素次要因素重要因素次要因素鼓包重要因素次要因素鼓点次要因素重要因素并片重要因素次要因素次要因素褶皱次要因素重要因素重要因素不良类型发生阶段不良出现的位置主要原因及形成机理不良特征组件层压机气泡进料至下盖期中间全部一般引起因素为组件进料后下盖慢或设备异常不能抽真空,EVA局部受热,局部提前固化,包裹气泡可能伴有碎片,气泡一般形状不规则抽真空全部全部一般引起因素为组件进料下盖后,真空系统运作异常,EVA泡沫化,气泡无法抽出气泡呈大麻点状,组件背板凹凸不平保压期头部汇流条不固定一般为高温引起,由于物质间的导热差异,镀锡铜带附近的EVA受高热后,内部的类过氧化物交联剂优先分解产生气泡气泡多呈长条形,附着于汇流条上,圆润保压期不固定不固定一般异物引起的气泡,需观察气泡中心位置是否有明显异物,异物的材质,易藏匿和产生气泡,如透明的覆膜,干燥剂等气泡多呈梅花状保压期不固定不固定一般油污也易引起组件气泡单个气泡面积很大,边缘圆润保压期不固定不固定1.一般水,助焊剂也易引起组件气泡2.EVA材质异常气泡边缘多呈杉树状,中间可能存在EVA结晶保压期边缘电池片之间四周一般引起因素为层压皮过紧导致对组件得覆压不足,气泡没有被及时压出气泡单个颗粒状分布于组件外缘电池片之间的相同位置保压期全部电池片之间全部1.一般引起因素为层压皮过送导致对组件整体覆压不足,气泡没有被及时压出2.真空度不足在前期也易造成类似异常气泡颗粒状不规则的分布于组件电池片之间保压期不固定固定层压机局部温度过高,导致组件局部区域的过氧化物交联剂优先分解产生气泡气泡为群聚性颗粒状,有范围充气阶段汇流条与电池片之间不固定1.上腔充气速率过慢,导致头部的汇流条与电池片之间的气泡无法被压出2.EVA的流动性较差或者绝缘小条没有与汇流条卡齐也易产生类似气泡气泡多呈长条形抽真空互联条折弯点不固定一般引起因素为互联条折弯点过高,中间滞纳气泡,难被抽出,最终停留在折弯点附近气泡不规则,圆润抽真空互联条两侧不固定1.助焊剂或者互联条上有水,易产生气泡2.焊接时的空焊,虚焊,也会在互联条两侧出现气泡前者气泡不规则,外缘呈杉树状后者气泡有明显从互联条下溢出现象保压期不固定不固定一般原因为EVA交联不均匀,涉及层压机的温度均匀性,或者在气泡区域内存在异物,异物满足使其造成交联不均匀的条件典型的缺胶型气泡,中间颜色比周围淡保压期电池片背面的EVA不固定常见于FirstEVA返工组件中,原先那层EVA经过再次高温时出现这类现象气泡有明显从电池片下溢出现象,并且满足边缘有些形状不规则的小气泡脱层保压期组件边缘固定层压机上腔存在异物,导致组件组件层压时,区域EVA被挤出而出现脱层,背面有轻微凹凸感,或层压皮运行不稳定,保压过程中出现凸起,也易出现脱层该类脱层多集中于组件边缘,形状特殊保压期不固定固定层压机局部温度不足,EVA交联后玻璃强度不够也易出现脱层保压期不固定不固定背板或者玻璃上沾有油污类物质,也容易出现脱层呈现出玻璃压花的,一般为玻璃上有油污类物质保压期全部全部Toyo和STR搭配时也易出现该类脱层,初步分析为Toyo层间剥离强度不足层压后短边缘全部一般为温度过低和背板收缩共同作用,一定条件下背板的PET还是比较厚的组件短边缘10mm以内出现白色脱层,类似于群聚微小气泡,长边有时会有,但明显比短边轻微层压后长边缘不固定一般员工在组件过热下料后,翻转组件极容易造成该异常上腔充气不固定中间由于层压机充气速率过快,层压皮对电池片施压导致电池片碎片层压后显示电池片轻微分离,无重叠现象,电池片上裂纹线整齐下盖期不固定中间层压机在下盖过程中,皮由于老化,或者上腔存在压力,导致层压皮先着陆,对电池片施压碎片层压后显示电池片飘逸明显,重叠现象严重,裂纹线整齐碎片保压期不固定不固定由于手工焊焊接出现空焊,漏锡,锡堆等异常,在层压中,电池片受力碎裂层压后电池片轻微分析,无明显重叠,裂纹线异常,甚至出现三角状碎片保压期不固定不固定由于手工焊焊接中出现隐裂,导致层压后出现碎片层压后显示电池片轻微分离,无重叠现象,电池片上裂纹线整齐层压前短边及四角不固定一般层压前员工抬动操作不正确也易导致碎片层压后显示电池片飘逸明显,重叠现象严重,裂纹线异常,会出现多裂纹线保压期中间不固定层压机进料后下盖慢或者组件抢救时,由于组件中间EVA先熔先固,易拉碎电池片碎片数量大,不规则保压期组件头尾部不固定在对汇流条和互联条焊接时,出现互联条被强拉弯曲现象,层压后出碎片明显的互联条弯曲现象鼓包保压期全部全部相同温度下,出现保压时间过长主因为时间保压期全部全部相同时间下,温度过高也易出现鼓包主因为时间保压期不固定不固定电池片背电场或背电极印刷烧结异常,易出现浆料脱落对应位置现状特殊鼓点层压后全部全部相同温度下,保压时间过短易出现鼓点主因为温度层压后全部全部相同时间下,温度过低导致EVA交联不足,收缩明显出鼓点主因为温度保压期不固定固定上腔存在异物,或EVA凝胶残留等。
连续平压法中密度纤维板常见质量问题及其解决措施

连续平压法中密度纤维板常见质量问题及其解决措施连续平压法是一种常用的密度纤维板生产工艺,通过在连续热压机上对原料进行连续热压,制成密度纤维板。
在生产过程中,常常会出现一些质量问题,影响产品的品质和使用效果。
本文将针对连续平压法中密度纤维板常见的质量问题进行分析,并提出解决措施,旨在为生产实践提供一些参考和帮助。
一、常见的质量问题1.板材表面光洁度不佳这是造成密度纤维板质量不良的重要原因之一。
表面光洁度不佳会直接影响到板材的美观性和使用寿命。
造成板材表面光洁度不佳的原因主要有以下几点:(1)原料质量差。
原料中杂质多,颗粒不均匀,容易在热压过程中形成凹凸不平的表面。
(2)热压工艺参数不当。
热压温度、时间、压力控制不准确,导致板材表面无法完全熔烧并平整。
(3)热压机模具不良。
模具表面损伤或磨损严重会直接导致板材表面不光滑。
2.板材强度不足(3)胶粘剂使用不当。
胶粘剂过量或者过少都会影响板材的强度,胶水的粘接性不佳也会导致板材强度不足。
3.板材厚度不均匀(1)原料质量差。
原料颗粒大小、含水率不同会导致成型时板材厚度不均匀。
(2)热压机压力不均匀。
热压机的压力不均匀会导致板材在成型过程中压缩不均匀,从而造成板材厚度不均匀。
4.板材含水率过高密度纤维板的含水率是影响其质量稳定性的重要因素,含水率过高会导致密度纤维板变形、开裂等问题。
造成板材含水率过高的原因主要有以下几点:(1)原料中的水分含量不均匀。
原料中水分含量不均匀,经过热压成型后板材含水率会出现不均匀分布的情况。
(3)成品储存条件不当。
成品储存环境潮湿会导致板材吸湿,含水率升高。
二、解决措施1.原料质量控制首先要从原料入手,选择优质的原料是保证生产高品质密度纤维板的基础。
应该选择颗粒均匀、含水率适中的原料,并进行严格的筛分和清洁处理,避免杂质和尘土的混入。
2.热压工艺参数调控合理的热压工艺参数是生产高品质密度纤维板的关键。
应该对热压温度、时间、压力进行准确的控制和调整,确保板材表面熔化和压实。
连续平压法中密度纤维板常见质量问题及其解决措施

连续平压法中密度纤维板常见质量问题及其解决措施【摘要】密度纤维板生产中常见质量问题包括板面平整度不佳、板材厚度不均匀、板材弯曲变形、表面脱漆和表面磨损等。
解决这些问题的措施包括加强设备维护与保养,优化生产工艺流程,加强员工培训和质量管理。
通过这些措施,可以提高密度纤维板的质量稳定性,减少生产中的质量问题,提升产品的竞争力和市场份额。
加强设备维护可以确保设备运行稳定,减少故障率;优化生产工艺流程可以提高生产效率,减少浪费;加强员工培训和质量管理可以提高员工技能水平,确保产品质量符合标准。
采取有效的措施解决常见质量问题是确保密度纤维板生产质量的关键。
【关键词】密度纤维板, 连续平压法, 质量问题, 解决措施, 板面平整度, 厚度不均匀, 弯曲变形, 表面脱漆, 表面磨损, 设备维护, 生产工艺流程, 员工培训, 质量管理.1. 引言1.1 连续平压法中密度纤维板常见质量问题及其解决措施密度纤维板是一种常见的建筑材料,在建筑、家具等领域有着广泛的应用。
在生产密度纤维板的过程中,采用连续平压法是一种常见的生产方式。
在生产过程中,常常会出现一些质量问题,影响产品的质量和市场竞争力。
本文将对连续平压法中密度纤维板常见的质量问题进行分析,并提出相应的解决措施。
板面平整度不佳是一个常见的质量问题。
板面不平整会影响板材的外观和使用功能。
解决这一问题的方法包括调整压力和温度,优化板材的成型工艺等。
板材厚度不均匀也是一个常见问题。
厚度不均会导致板材的强度和稳定性受到影响。
调整压力控制系统,优化原料配比等措施可以有效解决这一问题。
板材弯曲变形、表面脱漆和磨损等问题也需要引起重视。
加强设备维护与保养,优化生产工艺流程,加强员工培训和质量管理是解决这些问题的有效措施。
通过以上的分析和对策,可以帮助生产厂家提升密度纤维板产品的质量,提高市场竞争力,满足客户需求。
密度纤维板行业需要不断探索创新,不断改进生产工艺和技术,以提升产品质量,实现可持续发展。
多层压机生产中纤板产生厚度偏差的原因及解决方法

产时就发现在其他工 艺参数不变的情况下 , 用相 思木生
产 的板 坯 回弹 量 就 小 了许 多 。 5 2 纤 维 含 水 率 对 板 坯 的 回 弹 量 也 有 很 大 的 影 . 响。含水率高 , 回弹量就小 ; 含水率低, 则回弹量大 。 5 3 板 坯 重 量 设 定 值过 大 引起 回弹 量 大 。 . 5 4 纤 维 形 态 对 板 坯 的 回弹 量 也 有 一 定 的影 响 。 . 5 5 施 胶量不够 时, . 由于纤维结合 力不足引起 回 弹 量大 。 6 小 结 . 为 了尽量减小多层压机生产毛板的厚度偏差 , 要注 意 以下 几 个 问题 。 6 1 在 热 压 机 的 选 型 时要 考 虑 其 是 否 能满 足 厚 度 . 偏 差的要求 , 比如 是 否 有 先 进 、 理 的 压 力 和位 置控 制 合 系统 , 压 板 的 材 料 、 度 是 否 符合 要 求 , 热 厚 以及 其 加 热 介 质和加热均匀性等 。 6 2 在 铺 装 饥 的 选 择 上 , 考 虑 能 否保 证 铺装 均 . 要 匀度和稳定性 。 6 3 在 操 作 上 要 注 意 控 制 好 纤 维 的 质 量 、 水 率 . 含 和板坯 的重量 ; 热压机时一定要按照操作规程缓慢地 预 升温 , 防止压机空压和板 坯漏装 。 6 4 要 做好 设备的维修保 养工 作 , . 以保证 生产 的 连续和稳定 。
少。
4 24 脉冲气流不足或其控制 阀门失灵 。 .. 4 2 5 气流 量 不 足 或 调 整不 当 。 .. 5热压后板坯回弹量过大 . 51 原材料的变化 . . 由于 各 树 种 的性 质 不 一 样 , 生 产 出 来 的纤 维 的形 态和 塑 性 也 不 一 样 , 坯在 加 热 加 压 板 后的回弹量也不一致 . 如我厂分别采用按树与相思木生 ・综 Fra bibliotek述 ・
影响中密度纤维板质量因素及控制措施探究

影响中密度纤维板质量因素及控制措施探究摘要:由于中密度纤维板力学性能非常好,而且它的表面非常光滑,有稳定性的尺寸,所以中密度纤维板在家具制造、包装、建筑业的应用十分广范,中密度纤维板可以同过丰富的原材料来进行生产,它的生产成本比较低,这样也使它在船舶,车辆等生产行业代替了天然板材,成为这些行业必用的生产原材料。
因为中密度纤维板的如良好的市场,其销售量非常好,所以国内有许多厂家都加入到中密度纤维板的生产中来,这样的结果就是产品质量的良莠不齐,本文从如何提高中密度纤维板的质量进行探讨分析。
关键词:中密度纤维板;质量控制;探究1前言中密度纤维板的生产工艺是非常重要的,而且复杂,产品质量问题的产生大部分原因都是由于生产工艺没有达到标准。
通过对本厂这些年出现的产品问题分析,发现的问题主要有强度不够,裂缝,变形,分层等,产生这些原因还有其他方面的因素,比如一块板各部分厚度不一致,密度不一样,板冷却时间短,上下表面砂光量不均,铺装精度不够等,但最主要的原因是板子的密度、干燥后纤维含水率、胶粘剂质量及施胶量、热压工艺等因素。
为提高产品质量,提高产量最大限度地降低生产成本,获得最高经济效益需要做好以下几方面的工作。
2提高板子力学强度和性能提高原料本身性能减少树皮或腐朽材的含量;提高木片规格质量,提高木片合格率,减少碎料量、减少树皮含量;纤维粗细比例要合适,过粗影响交织、结合力,过细比表面积过大用胶量增多且自身强度削弱;控制好施胶量且均匀施胶确保胶的性能稳定;确保铺装厚度均匀厚薄稳定减少密度差异;制定合理的热压曲线,控制合适的热压等。
3做好板子密度的控制板子密度主要与原料种类及材质有关,本厂原料主要是以柞木枝桠为主的硬叶材,原料本身比重大(0.76g/om3)。
根据我厂多年来的经验,板子密度低于0.70g/om3,成品中分层、开裂、边角松软较多,而且平面抗拉强度及静曲强度都达不到标准。
当密度控制在0.76g/om3左右时,板子表面光滑,极少出现开裂分层现象,当板子密度超过0.80g/om3时板子翘曲变形很严重。
纤维板砂光缺陷调整方法
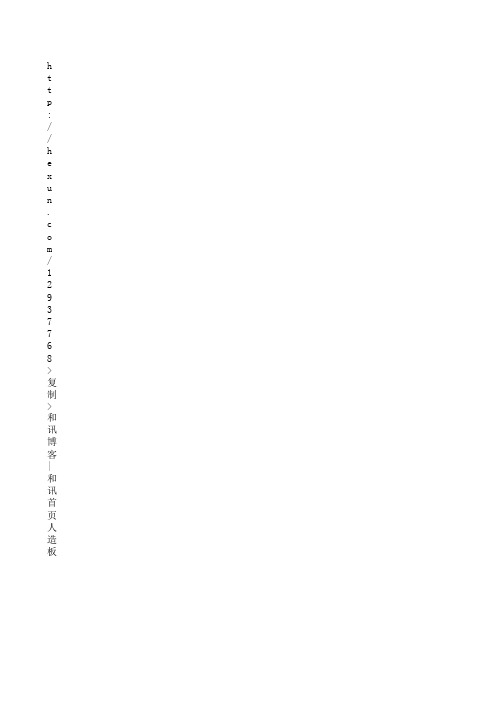
/12937768 > 复制 > 收藏 | 手机看个人门户和讯博客 | 和讯首页人造板人造板 木业 建筑装修材料 家具个人门户博客微博相册音乐转帖邮箱朋友圈好友留言进入我的家载入中自定义HTML载入中... loading快速链接[和讯博客][发表文章][博客设置][文章管理]搜索RSS 2.0使用和讯博揽订阅博客印书中密度纤维板生.砂光板出现缺陷的原因及排除方法 [转贴 2009-11-01 22:52:20]我顶字号:大 中 小1.板的开头段不平(在距板的前边80---350mm处,上下表面有明显的砂磨缺陷).原因:接触辊比衔铁平面回去的太多,进给工作台太低,衔铁前的工件太低。
当工件砂磨到大约400mm 时,工件进入中间运输辊后,工件才能获得完全的进给速度.排除方法;向前移动接触辊,同时相应地向上移动砂光机上关部。
重新调整高度指示器;2.板的开头段出现槽形砂光缺陷(在距板前边40---130mm 出现宽约100mm的槽).原因;上边衔铁与运输辊的平面距离设定0.5mm太高了,这样进给靠磨合使进给速度下降太多,结果在低速时出现局部砂磨量过大将每个衔铁和两个接触辊都向前调整0.2mm,将机器上半部分向上移动0.4mm。
重新调整高度指示器.3.板的前后边的砂光缺陷.原因;1.由于进料和出料工作台调整不当,如果砂光缺陷发生在板的上表面,是运输工作台加载弹簧高造成的.2.由于运输辊调整不良(板子表面压力不足),在距板的前边或后边大约350mm 处砂磨量过大.排除方法;1.将运输工作台加载弹簧调低.2. 调整运输辊的距离和压力.4.砂光板的横截面出现锥形.当在宽度上出现一边厚一边薄时原因;1.由于机器的上下部分不平行造成.2.由于磨垫上石墨厚度不匀或磨损使磨垫一边厚一边薄引起.3. 由于磨垫上下水平调整偏差引起排除方法;1. 按机器上下部的联接和调整说明,重新调整上下部分的平行度.2.用直木板粘上80---100 目的砂纸,将厚度不一致的石墨层研磨均匀.3. 重新调整各磨垫的水平与间距.当两侧边出现明显的锥形时原因;1.由油毛毡引起2. 由于砂带摆动磨损接触辊两端表面引起排除方法;1.在两侧板的宽度之内将油毛毡去掉大约:10mm在两侧板的宽度之外也将油毛毡去掉大约30mm由于解除了板边砂光压力产生板子两边;将略厚,这样有利于二次加工.2.将接触辊拆下进行研磨或更换新的橡胶:5.砂光板表面有振动波纹当改变进给速度时波纹距离也相应变化原因;1.由于旋转机件如接触辊,张紧辊等的动平衡精度差引起.2.由于砂带接缝不良造成.3. 由于有缺陷的轴承,轴承座或皮带轮,的松动引起的不平衡造成.4. 接触辊上覆盖的橡胶层分离造成当变更进给速度后波纹距离不变时,主要是由于运输系统的缺陷引起,如运输辊或传动机件磨损等.排除方法;接触辊在工作转速下动平衡精度应达到5---6g.2. 更换好的砂带3. 更换轴承,轴承座直径加工精度应达到0.02mm,皮带轮紧固或更换,使其达到平衡4. 更换接触辊检查.6.板表面沿进给方向出现1.细而短的条纹痕迹原因;由于砂带表面砂粒被砂子或金属破坏排除方法;更换新砂带;2.蛇形砂痕原因;由于砂带表面破坏或粘有金属等杂物,砂带摆动形成.排除方法;更换新砂带;7.板表面出现光滑发亮的斑点原因;1.砂带的砂粒已被磨掉,对板子只抛光不起切削作用.2. 进给速度和所使用砂带粒度的大小不相适应.3.前后导向衔铁接触板的表面,由于过高的压力而造成.4.由于排尘风压;风量不足,砂光粉尘停留在砂带下面,对板表面的抛光而造成.排除方法;1.更换新砂带.2.使用较低粒度的砂带或降低进给速度.3.调整衔铁高度或减少压力.4. 检查与改善排尘系统.标签: 缺陷 查看和 缺陷 相关的微博 原因 查看和 原因 相关的微博 排除方法 查看和 排除方法 相分类: 中密度纤维板(MDF)[收藏到我的转帖] [引用通告][推荐] [评论] [举报] [打印]点击数: 评论数:我 顶!觉得精彩就顶一下,顶的多了,文章将出现在更重要的位置上。
连续平压法中密度纤维板生产中常见质量问题分析

连续平压法中密度纤维板生产中常见质量问题分析张林俊,童广州,张鹏,黄威,田汝辉近年来,我国中密度纤维板生产发展速度迅猛,2005年全国各地已建和和在建中密度纤维板生产线513条,年生产能力2 148.2万m3。
国产中密度纤维板的热压机一般为多层压机,不能够生产2 ~ 6mm的薄板。
为了满足国内对高质量纤维板的需求,从国外引进了连续压机。
连续压机具有生产连续、产量高、幅面大、规格灵活等特点,使用连续压机企业生产的产品占据着国内的中高端市场。
目前国内已建和在建的连续热压生产线分连续辊压和连续平压两类。
其中1994 ~ 2004年引进3 ~ 20万m3/a连续平压生产线共23条,年生产能力共274.5万m3,还有5条连续平压线尚在建设和筹建中⑶。
虽然连续平压生产技术和工艺都比较先进,但是在实际生产中仍然会出现产品有裂纹、表面发毛、凹凸痕、水渍等缺陷,现根据几年来积累的经验,将其常见质量问题分析如下。
1 表面发毛连续平压生产6mm以下的薄板时,可以做到不砂光或者是减少砂光余量,这样减少了消耗,提高了企业的经济效益。
但是生产压光板时存在表面发毛现象,直接影响客户的后期使用。
常见的发毛现象主要有以下几种:1) 边部发毛且伴随软边(脆边)缺陷。
因为薄板生产速度比较快,为了防止入口出现叠料情况,一般情况下都会设置边部排气,在压机入口快速压榨板坯过程中向两边排气,并带走部分纤维,使得板边密度偏低发软,冷却后变脆形成脆边。
解决这种缺陷的办法是:第一,增加板坯齐边的宽度,使成品板边部发毛的部分在锯切过程中被切掉;第二,稍微调整纤维的粗细比例------细纤维中的粉尘比较多不利排气,因此生产薄板时欲提高生产速度必须加粗纤维。
另外,人口排气过程中喷出的都是一些粉尘,这些粉尘很容易粘在钢带上也造成了边部粗糙。
2) 板面不规则的发毛粗糙现象。
连续生产中如果存在这种缺陷,其可能原因一是纤维含水率低,二是钢带脏。
热压过程中,纤维的含水率主要起热传递作用。
多层压机生产中纤板产生厚度偏差的原因及解决方法

多层压机生产中纤板产生厚度偏差的原因及解决方法作者:曲英林来源:《农村实用科技信息》2010年第05期摘要:多层压机生产的中密度纤维板普遍存在毛板厚度偏差比较大的情况。
阐述了产生厚度偏差的一些原因,为了尽量减小多层压机生产毛板的厚度偏差,应注意几个问题。
关键词:多层压机厚度偏差多层压机生产的中密度纤维板普遍存在毛板厚度偏差比较大的情况。
为了减少产品在砂光工序中出现的漏砂、板面粗糙松软等质量问题,往往必须提高毛板的厚度,以保证最小的砂光余量,这不仅增加了产品的生产成本,还会引起板子密度不均匀、翘曲变形等质量缺陷,同时给砂光机的调整带来极大的困难。
笔者根据实际生产中的经验,就产生厚度偏差的一些原因进行阐述,以供同仁参考:1.液压系统位置控制不准确一般多层压机都是使用多个油缸同时工作,有的压机的各个油缸可根据各自对应位里来单独调节压力,但有的压机的全部油缸都直接与同一压力管相接,它们在任何时候的压力都是相等的,不能单独调整。
这样,就不能克服因铺装不均匀、板坯在压板中位里不对称等原因引起的厚度偏差。
2.板坯在热压板中位置不对称或偏移2.1 从后处理段出来的板垛出现倾斜,特别是生产薄板时更明显。
2.2 在显示屏上显示出两个压机位置传感器的探侧值有比较大的偏差。
2.3 检测板坯时,即使各点的单位面积重量一致,也由于厚度不一致而引起密度相差很大。
2.4 铺装线上各输送带在运行中跑偏或其中心与热压机的中心线有偏差。
2.5 铺装线上板坯宽度齐边锯的调整位置不合适3.热压板变形3.1 预热时加热不均匀,温度升高过快,特别是在冷机后预热时更易变形。
若是用蒸汽加热,在预热时由于本身加热特点的限制以及冷凝水排放不顺而不易于控制温度,这样更易引起变形。
3.2 在生产过程中出现漏装板坯、短板坯、轻板坯等情况,使压力集中加在厚度规上而引起热压板变形。
4.铺装不均匀铺装均匀度也是影响毛板厚度偏差的一个重要因素。
多层压机与单层压机或连续压机相比,铺装均匀度对毛板厚度偏差的影响更为严重。
连续平压法中密度纤维板常见质量问题及其解决措施

连续平压法中密度纤维板常见质量问题及其解决措施【摘要】密度纤维板是一种常见的建筑材料,但在连续平压法生产过程中常常会出现质量问题。
这些问题包括表面质量问题、厚度不均匀问题、弯曲变形问题、孔洞问题和漆膜脱落问题。
为解决这些问题,可以加强生产工艺管理,优化设备调试,严格质量检验,加强维护保养,提升操作技能。
通过以上措施的综合应用,可以有效提高密度纤维板的生产质量,保证产品达到标准要求,提升企业的竞争力和市场口碑。
加强对各个环节的管理和控制,提高工作人员的技术水平和责任意识,是解决密度纤维板质量问题的关键措施。
【关键词】连续平压法、密度纤维板、质量问题、解决措施、表面质量、厚度不均匀、弯曲变形、孔洞、漆膜脱落、生产工艺管理、设备调试、质量检验、维护保养、操作技能。
1. 引言1.1 连续平压法中密度纤维板常见质量问题及其解决措施密度纤维板是一种常见的建筑材料,广泛用于家具制造、装饰材料等领域。
在制作过程中,采用连续平压法是一种常见的生产工艺。
在生产密度纤维板的过程中,常常会出现一些质量问题,如表面质量问题、厚度不均匀问题、弯曲变形问题、孔洞问题以及漆膜脱落问题等。
这些质量问题不仅影响产品外观,还会降低产品的使用寿命和品质。
针对这些常见的质量问题,我们可以采取一些解决措施。
加强生产工艺管理是非常重要的,要确保每个生产环节都符合标准要求。
需要优化设备调试,确保设备运行稳定、精准。
严格质量检验也是必不可少的,及时发现问题并及时处理。
加强维护保养和提升操作技能也可以有效地减少质量问题的发生。
通过以上一系列的解决措施,可以提高密度纤维板的生产质量,确保产品的稳定性和可靠性。
加强管理、优化设备、严格检验、维护保养以及提升操作技能,是解决密度纤维板常见质量问题的有效途径。
的提出,对密度纤维板生产质量的持续改进具有积极的推动作用。
2. 正文2.1 表面质量问题在连续平压法生产密度纤维板过程中,表面质量问题是一个常见的质量问题。
中密度纤维板常见质量缺陷及产生原因
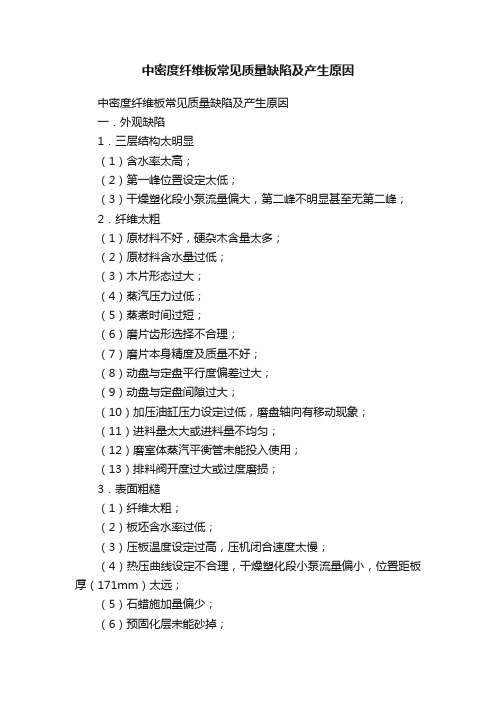
中密度纤维板常见质量缺陷及产生原因中密度纤维板常见质量缺陷及产生原因一.外观缺陷1.三层结构太明显(1)含水率太高;(2)第一峰位置设定太低;(3)干燥塑化段小泵流量偏大,第二峰不明显甚至无第二峰;2.纤维太粗(1)原材料不好,硬杂木含量太多;(2)原材料含水量过低;(3)木片形态过大;(4)蒸汽压力过低;(5)蒸煮时间过短;(6)磨片齿形选择不合理;(7)磨片本身精度及质量不好;(8)动盘与定盘平行度偏差过大;(9)动盘与定盘间隙过大;(10)加压油缸压力设定过低,磨盘轴向有移动现象;(11)进料量太大或进料量不均匀;(12)磨室体蒸汽平衡管未能投入使用;(13)排料阀开度过大或过度磨损;3.表面粗糙(1)纤维太粗;(2)板坯含水率过低;(3)压板温度设定过高,压机闭合速度太慢;(4)热压曲线设定不合理,干燥塑化段小泵流量偏小,位置距板厚(171mm)太远;(5)石蜡施加量偏少;(6)预固化层未能砂掉;(7)砂光存在砂痕砂线;(8)施胶量太低;(9)毛板控制超厚,砂光时砂掉表面致密层;4.表面异物(1)木片内含有异物(如橡胶、捆绑的绳索);(2)输送皮带脱胶掉入木片、板坯内;(3)磨室体、干燥管道积炭;(4)检修设备时设备、现场有遗留物进入纤维;(5)清扫场地所回收的料含有杂物;(6)设备、环境清扫不定时,长期存积的灰尘、纤维掉落到板坯形成局部松软;5.砂痕砂线(1)粗砂、细砂砂削量分配不合理;(2)粗砂、细砂型号及搭配不合理;(3)砂带质量不合格,易掉砂粒;(4)毛板冷却时间不够长,粘砂带;(5)砂带使用时间过长,未及时更换;(6)石墨带、羊毛垫质量不好或磨损后未及时更换;(7)接触辊、输送辊磨损严重,精度达不到要求;(8)砂架与砂架之间水平偏差过大;(9)输送辊进给速度不同步;(10)含有砂粒的砂光粉回收量太大;(11)砂光机安装存在问题,振动太大;(12)砂光机本身精度达不到要求;6.局部漏砂(1)铺装后的板坯不平;(2)板坯在输送及装板过程中局部被破坏;(3)压机同臂未能调整好,压机在快速闭合过程中局部板坯被冲坏;(4)压板变形;(5)毛板厚度不够;(6)毛板密度偏差过大;(7)毛板变形;(8)石墨带、羊毛垫质量不好或局部磨损后未及时更换;(9)接触辊、输送辊局部磨损严重;7.毛板厚度偏差大(1)原材料偏差过大;(2)板坯称不准确;(3)板坯重量控制不稳定;(4)厚度规上有杂物或厚度规已磨损;(5)位置控制器工作不正常;(6)压板变形;8.毛板分层和鼓泡(1)板坯含水率过高或含水率不均匀;(2)胶粘剂的质量及粘度和固含量不符合要求;(3)热压曲线第一峰位置太小,压力太高,表面致密层过厚;(4)压机卸压、压板张开速度过快;(5)压板温度过高或热压时间过长;(6)密度过大;9.边角松软(1)铺装不均匀,板坯边部密度偏低;(2)设备振动过大或预压机线压力设定过低,板坯输送过程中边角部位纤维倒塌、掉落;(3)推拉板变形严重,边角部位的纤维在推送过程中有倒塌、掉落现象;(4)热压工艺条件不满足,未保证胶粘剂充分固化;(5)砂光截边锯使用时间太长;10.毛边(1)横截锯链条长度不对,使板坯本身偏短;(2)预压机线压力偏小,板坯在推送过程中变短;(3)推拉板表面不光滑,板坯在推送过程中阻力过大变短;(4)推拉板表面有水或油类物质;(5)装板小车行程调整不当,板坯在装机内未送到位;(6)装板水平油缸前进行程开关调整不当,板坯在压机内未送到位;(7)压机快速闭合行程调整不当,板坯变形严重;(8)压机同臂调整不当;二.理化指标不合格1.静曲强度低(1)产品密度低;(2)压机闭合和加压速度慢,产品密度梯度小;(3)胶粘剂施加量不够、分布不均匀,板坯含水率过高或过低,造成胶粘剂固化不完全;(4)纤维原料质量差或纤维分离度低;(5)热压时间过长或不足;2.内部结合强度低(1)施胶量不够;(2)加压速度过快(产品密度梯度过大)和热压时间不足;(3)板坯内部含水率高、温度低,胶粘剂没有完全固化;(4)密度偏低;(5)回收废纤维或砂光粉比例太大;(6)板冷却时间不够,堆放温度过高,胶粘剂过度固化降解;3.尺寸稳定性差与变形(1)成型时各层密度、厚度不成比例,相差大,上、下层分布不对称且含水率不均;(2)表、芯层密度梯度过大;(3)热压时,上、下热压板或同一块热压板温差过大;(4)板冷却不够即堆放;(5)堆垛垫方高矮不一;(6)存放处空气温度大;(7)上、下表面砂光量不一,或下表面预固化严重且未砂尽;4.握钉力低(1)密度太低或太高;(2)表芯层密度梯度过大;(3)施胶量不足;5.吸湿膨胀率大(1)施胶量不足或胶粘剂未充分固化;(2)施蜡量低或分布不均匀;(3)密度低,纤维形态和质量差;(4)纤维或胶粘剂的PH值控制不合适,影响胶料固化或纤维的自身缩合;6.表面结合强度低(1)板坯含水率太低;(2)压机热压板温度太高;(3)压机闭合速度太慢;(4)热压曲线第一峰压力太低;(5)毛板超厚,砂光砂掉了致密层;(6)施胶量偏小;7.密度偏差大(1)原材料搭配不合理;(2)铺装不均匀;(3)厚度规精度发生变化;(4)压机压板平整度与温度,压力分布偏差过大;(5)板坯输送及装板过程中变形大;(6)压机同步闭合调整不当;。
多层压机生产中纤板产生厚度偏差的原因及解决方法

板坯在热压板中位置不对称时,热压板在加压过程中将不能总保持水平状态,从而引起厚度偏差,特别是在各压缸压力不可单独调节的热压机中更为明显。笔者在生产中侧试过,若在宽度方向偏移15mm,平均每层板坯左右厚度一般相差为0.1-0.2mm.
2.1板坯不对称时产生的现象
① 从后处理段出来的板垛出现倾斜,特别是生产薄板时更明显.
板坯铺装均匀度主要取决于设备和控制系统的先进性以及工人操作水平两个方面.通过控制板坯的重量和纤维在铺装室内的分布来保证铺装的均匀度。
4.1板坯纵向厚度偏差产生的原因
厚度偏差主要是由于铺装时板坯重量波动所引起的.重量波动的主要原因有如下几点:
①由于纤维料仓中的纤维不足或不均匀引起铺装室料位不稳定,从而引起板坯重量的波动.虽然铺装室料位的高度可由纤维料仓输送皮带的速度来自动控制,以保证料位高度的稳定,但纤维输送量的变化不允许太灵敏,否则会经常出现堵料的生产事故。在操作时要尽量使磨料量与压机生产量相配。
窗体底端
① 装板小车装板过程前进的最终位置设定值不合适,或板坯在托盘中的位置不准。
② 由于装板小车回程时的速度与托盘网带的速度不一致,引起板坯在热压板中前移或滞后。
③ 各层托盘网带的离合器动作不灵。
④ 板坯长度调整后没有相应改变装板位置。
3热压板变形
3.1热压板变形的原因
现在我国许多厂家的中纤板毛板厚度偏差大的原因主要是由于热压板变形引起的。热压板的变形有横向变形和纵向变形,其原因主要有以下几点:
出现的漏砂、板面粗糙松软等质量问题,往往必须提高毛板的厚度,以保证最小的砂光余量,这样不仅增加了产品的生产成本,还会引起板子密度不均匀、翘曲变形等质量缺陷,同时给砂光机的调整带来极大的困难。
连续平压法中密度纤维板常见质量问题及其解决措施

连续平压法中密度纤维板常见质量问题及其解决措施密度纤维板是一种常见的建筑用材料,其主要原料是植物纤维,经过破碎、制浆、造板等工艺加工而成。
连续平压法是密度纤维板的生产工艺之一,通过连续压制使得密度纤维板具有均匀的密度和较好的物理性能。
由于生产过程中的各种因素,密度纤维板在生产过程中常常出现一些常见的质量问题。
本文将通过对连续平压法中密度纤维板常见质量问题的分析,解释其原因,并提出相应的解决措施,以期提高密度纤维板的质量稳定性和产品可靠性。
一、密度纤维板常见质量问题及原因分析1. 表面质量问题密度纤维板的表面质量问题主要表现为表面平整度不高、有划痕或凹痕等情况。
这些问题严重影响了密度纤维板的美观度和使用性能。
造成密度纤维板表面质量问题的主要原因有:(1)原料质量不佳。
原料中含有大量的杂质和不完整的纤维,导致造板过程中表面质量不理想。
(2)造板工艺不当。
在连续平压法中,造板工艺的参数设置不合理或操作不当,会导致板材表面出现凹凸不平或划痕。
解决措施:(1)严格控制原料质量。
在使用原料前,进行严格的筛分和除杂处理,确保原料质量符合要求。
(2)合理设置造板工艺参数。
调整造板工艺参数,如温度、压力、速度等,使其符合板材表面质量的要求。
2. 密度不均匀问题密度纤维板的密度不均匀问题表现为板材内部存在密度波动或不均匀现象,导致板材的物理性能不稳定,影响了其使用寿命和安全性能。
造成密度不均匀问题的主要原因有:(1)原料分布不均匀。
原料在造板过程中分布不均匀,导致板材密度不均匀。
(2)造板机器调整不当。
造板机器在使用过程中,温度、压力等参数的不稳定会导致板材密度不均匀。
解决措施:(1)合理配比原料。
在原料的配比过程中,严格按照配方要求进行,确保原料分布均匀。
(2)定期维护造板机器。
定期对造板机器进行维护和保养,确保其参数稳定,避免因机器故障导致的板材密度不均匀问题。
二、连续平压法中密度纤维板常见质量问题的解决措施1. 加强原料质量控制如前所述,原料质量是影响密度纤维板质量的关键因素。
连续平压法中密度纤维板常见质量问题及其解决措施

连续平压法中密度纤维板常见质量问题及其解决措施1. 引言1.1 连续平压法简介连续平压法是一种常用于生产密度纤维板的工艺方法,其特点是在连续的传送带上进行板材的成型和压制。
在整个生产过程中,板材通过一系列的加热、压制和冷却环节,最终形成密度均匀、表面光滑的纤维板产品。
通过连续平压法生产的密度纤维板,在生产效率和产品质量上具有明显优势。
与传统的压延法相比,连续平压法能够实现自动化生产,提高生产效率,减少劳动力成本。
由于板材在整个生产过程中保持连续传送,可以避免因停机换模带来的产品不稳定性。
1.2 密度纤维板应用广泛密度纤维板是一种由大量细小木材纤维通过热压而成的板材,具有优良的物理性能和加工性能,因此在建筑、家具、包装等多个领域得到了广泛应用。
在建筑领域,密度纤维板常被用于地板、墙板、天花板等装饰材料的制作。
由于密度纤维板具有坚实耐用、不易变形、不易燃烧等优点,能够有效提升建筑材料的质量和使用寿命,因此备受建筑师和装修商的青睐。
在家具制造领域,密度纤维板多用于家具的板材、边框等部件的制作。
密度纤维板具有加工性能好、表面平整、不易开裂等特点,能够有效提高家具的外观质感和使用寿命,因此深受家具生产厂家和消费者的喜爱。
在包装领域,密度纤维板常被用于制作各种包装盒、托盘等包装材料。
由于密度纤维板具有抗压、抗震、防潮等特点,能够有效保护包装物品,因此被广泛运用于电子产品、食品、化妆品等领域的包装。
密度纤维板的应用广泛且多样化,不仅提升了产品的质量和性能,还为各个行业的发展提供了重要支撑。
2. 正文2.1 常见质量问题及解决措施:1. 纤维板表面不平整:纤维板表面不平整可能是由于生产工艺不当或设备问题造成的。
解决方法包括提高生产工艺水平,确保板材在生产过程中受到均匀的压力和热处理,以确保表面平整度。
定期检查和维护生产设备也是关键的措施。
2. 纤维板容易起翘变形:纤维板容易起翘变形主要是由于板材内部应力不均匀或含水率过高引起的。
影响中密度纤维板表面粗糙度的因素分析

影响中密度纤维板表面粗糙度的因素分析宋志磊(吉林森林工业股份有限公司红石中密度纤维板厂)郭旭光孟庆午(吉林新元木业股份有限公司)(北华大学)-『站参中密度纤维板(MDF)以其密度适中、强度较高、结构均匀、表面光洁、具有良好的机械加工及优良的音响效果等性能,被广泛地应用于家具、室内装饰、建筑、家用电器、包装和交通运输等行业。
20世纪90年代以来,我国MDF工业得到了迅猛的发展,MDF的应用越来越广泛。
而MDF的表面粗糙度的高低直接影响着它的使用效果。
本文结合MDF的生产实际,分析影响其表面粗糙度的因素。
1砂光工序热压后的MDF表面的预固化层密度低,纤维间结合强度亦低,从而影响其表面质量和使用性能。
为了得到坚实、平滑的板面和较精确的厚度尺寸,必须对其板面进行砂光处理。
在砂光过程中,砂带粒度、砂带砂削速度和工件进给速度以及砂带摆动频率等都直接影响板面表面粗糙度的高低。
1.1砂带粒度的选择原则上,根据砂削量和板面最终表面粗糙度要求选择砂带粒度。
砂带粒度对砂光产量及最终表面粗糙度都有直接的影响。
砂带粒度选择不合理,或者是砂光产量降低,或者得不到理想的表面粗糙度。
生产实践中砂带粒度选择一般为:粗砂40*~60*、细砂60#一8舻、精砂100·一120#(15∥、18∥)。
通常情况下,在粗砂过程中,要求把预固化层基本除去,同时完成对产品的定厚处理,以保证在细砂过程中,一方面把表层密度低、结合强度差的部分全部除去;另一方面使表面粗糙度达到一定的要求,确保在最后精砂过程中,既不增加砂带的砂削负荷,又能满足对表面粗糙度的要求。
单就表面粗糙度而言,前两道砂光都是为最后一道砂光做保证,最后一道砂光一定要满足板面最终表面粗糙度的要求。
因此,最后一道砂带粒度的选择对表面粗糙度的影响是至关重要的。
一般根据贴面工艺对板面粗糙度的要求来选择砂带粒度,通常情况下,12∥砂带就可满足表面的使用要求。
1.2砂带砂削速度和进给速度对板面表面粗糙度的影响砂带砂削速度和进给速度都对板面表面粗糙度有影响。
连续压机生产HDF_MDF常见问题的分析与改进

第22卷 第4期V ol 122 No 14木材工业CHINA WOOD IN D USTR Y 2008年7月July 2008收稿日期:2008203206; 修改日期:2008206223作者简介:杨松(1978—),男,国栋林产科技有限公司工程师。
应用技术连续压机生产H DF /MDF 常见问题的分析与改进杨松(国栋林产科技有限公司,四川双流610207)摘要: 介绍连续平压中纤板生产中常见的一些质量问题,并分析产生的原因,提出解决的方法。
关键词: 中/高密度纤维板;连续压机;质量控制;中图分类号:TS64 文献标识码:B 文章编号:100128654(2008)0420036203Q uality Control of H DF/MDF Panels Manufactured With a Continuous PressYAN G Song(Guodong Forest Technology Co 1,Ltd 1,Shuangliu 610207,Sichuan ,China )Abstract : After analyzing common quality problems and t heir causes in HDF/MDF production using a continuous p ress ,t his paper provided solutions to improve t he product performance 1K ey w ords : high /medium density fiberboard ;continuous press ;quality control 目前,国内中密度纤维板的生产以多层压机居多,因其不能生产6mm 以下的薄板,且产品存在一定的质量问题,多用于生产中低端市场的产品。
连续压机生产线具有生产连续性强、产量高、质量稳定、操作简便、生产产品的规格灵活等特点,近年来被大量从国外引进,生产的产品很快占据了国内纤维板的中高端市场。
基材及层压板可产生质量问题的查找和解决方法(12)

基材及层压板可产生质量问题的查找和解决方法在木材加工和家具制造行业中,基材及层压板是常用的材料之一。
然而,由于生产过程中的各种因素,这些材料有时会出现质量问题,例如开裂、粘接不牢固等。
本文将从查找和解决这些质量问题的角度进行探讨。
一、质量问题的查找方法1. 目视检查首先,进行目视检查是发现质量问题的第一步。
在制造过程中,工人可以通过目视检查来发现明显的问题,例如木材表面的开裂、层压板之间的空隙等。
2. 使用检测仪器除了目视检查外,还可以借助一些检测仪器来查找质量问题。
比如使用湿度计检测木材的含水率,使用超声波探测仪检测层压板的粘接情况等。
3. 抽样检验抽样检验是一种有效的查找质量问题的方法。
在生产过程中,定期从生产线上抽取样品进行检验,可以及时发现可能存在的质量问题。
二、质量问题的解决方法1. 控制生产环境保持生产环境的稳定是解决质量问题的关键。
要确保生产车间的温湿度适宜,保持空气流通良好,以防止木材吸湿开裂等问题的发生。
2. 选择优质原材料选择优质的原材料是解决质量问题的基础。
在采购木材和层压板时,要选择质量好、无明显瑕疵的材料,以确保产品质量的稳定。
3. 加强工艺管理加强工艺管理也是解决质量问题的关键。
要对生产工艺进行详细规范,加强对操作人员的培训和管理,确保每一个环节都符合标准要求。
结语总的来说,查找和解决基材及层压板质量问题需要综合运用各种方法。
只有严格控制生产过程中的各个环节,不断优化工艺和加强管理,才能生产出高质量的产品,满足市场需求。
希望本文所述方法对读者有所启发,帮助他们更好地解决质量问题,提高产品质量。
中密度纤维板砂光的主要故障分析与排除

中密度纤维板砂光的主要故障分析与排除
梁亚仁
【期刊名称】《木材加工机械》
【年(卷),期】1995(0)4
【摘要】中密度纤维板砂光的主要故障分析与排除福州人造板厂梁亚仁福州人造板厂是国有大型现代化人造板企业,主要生产中密度纤维板。
第一条生产线是1980年从美国引进的,当时配套的砂光设备是一台美国Kimwood公司制造的四头宽带砂光机。
为了提高砂光质量,1990年...
【总页数】2页(P29-30)
【关键词】中密度纤维板;弹性压板;故障分析;砂光机;福州人造板厂;石墨带;砂带张力;中心距;水平调整;压紧辊
【作者】梁亚仁
【作者单位】福州人造板厂
【正文语种】中文
【中图分类】TS653
【相关文献】
1.中密度纤维板砂光粉尘回用筛选系统改造探讨 [J], 黄武立
2.中密度纤维板裁边下脚料及砂光粉的有效利用 [J], 张雅云;李彩琴;杨昕;郭毅
3.刨花板、中密度纤维板砂光量大是什么原因?如何解决? [J],
4.砂光粉在中(高)密度纤维板企业的效用 [J], 吴剑
5.中密度纤维板砂光粉喷烧系统的技术改造 [J], 刘凤山
因版权原因,仅展示原文概要,查看原文内容请购买。
- 1、下载文档前请自行甄别文档内容的完整性,平台不提供额外的编辑、内容补充、找答案等附加服务。
- 2、"仅部分预览"的文档,不可在线预览部分如存在完整性等问题,可反馈申请退款(可完整预览的文档不适用该条件!)。
- 3、如文档侵犯您的权益,请联系客服反馈,我们会尽快为您处理(人工客服工作时间:9:00-18:30)。
Ke ywod : llyr o-rs; DF sn igd fc ;u l cnrl rsmuta e h t esM i p ;a dn eet q ai oto s y t
砂光是 中密度纤维板 ( F) MD 生产的最后工序 ,砂 产品质量的影响很大 ,尤其是需要贴面 、油漆饰面等加 光质量优劣决定了板材最终表面质量 ,因此减少砂光缺 工的强化木地板 、板式家具 、室 内门等高档下游产品 , 陷,提高产 品等级率是业 内人士特别关注的课题 。M F 要求基材表面光洁平整且无凹陷、色差 、砂痕等缺陷 , D
T C N L G 科技/ 术 讨 EH O O Y 技 探
Co mmo r c ai ee t n u tr a ue f du nSuf eQu l D fcsa dCo neme s rso a t y Me im
De st ie b ado la e t p e s n i Fb ro r nMut y r y i l Ho- rs
多层压机 生产 中密度纤维板 常 见砂光质量 问题分析及应对措施
陈文渊’ ,甘卫星 ,韦淇峰’ ,陆启亮’ ,唐贤明
1 . 广西丰林木业集团 股份有限公司, 南宁 502; . 321 2 广西大学林学院, 南宁 500 304
摘要: 探讨多层压机生产线生产的中密度纤维板常见砂光质量问题 , 如板面局部粗糙、 砂痕、 板面裂纹、 断坯痕、 粉尘斑、 胶斑等的形
成原因及相应的解决措施, 并对生产中如何提高砂光质量提出建议。
关键词: 多层压机; 中密度纤维板; 砂光缺陷; 质量控制
中 图分 类号 : S7 T 6 文献 标志码 : B 文 章 编号 :6356 21) 801—4 17— 4(02 0—000 0
Ch nW e y a G a W exig WeQ f g, u i n ag a n e n a
, ,
1Gu n x e g i o d n u t o L d, n ig5 0 2 , h n ; . o e t l g , a g i i ri , n i g5 0 0 , h n . a g i n l W o d sr C . t . F n I y Na n n 3 2 1 C ia 2 F rs yCol eGu n x v sy Na n n 0 4 C ia r e Un e t 3
基 金 项 目:国 家林 业公 益 陛行 业科研 专 项 ( 0047 );广 西 2 1000
粗糙 、断坯痕 、砂痕 、啃头和啃尾 、板面裂纹 、粉尘斑 和胶斑等 ,本文就多层压机生产M F D 常见的砂光缺陷形 成原因及解决措施进行探讨 ,并对如何提高砂光质量提
木质板材加工工程 中心能力提升建设研 究专项 ( 11 0 ); 13B 8 广西林业科研重大招标项 目 ( 桂林科字[ 1],号 )。 2 0 5 0  ̄
mu iy h t rs wee i u sd S g et n o o t mpoete u l o s dn re lo rp sd kl e o-e s r ds se . u g so s nh w oi rv h q at fa igwe a po o e . ar p c i i y n s
技 探 科技TC N L G 术 讨/ EH O O Y
出建 议 。
理热压机同时闭合机构的补偿装置 ,检查厚度规 的厚度
及安装使用情况 ,定期清除压板及厚度规上的杂物和纤 维 ,可消除此种现象。 3 板两侧边缘粗糙。 )
1 砂光缺陷成因及应对措施
1 . 面局 部粗 糙 1板
现 ,有 时 是双 面 出现 。
不合理 ,电子板坯称 的板坯密度系数设定值偏大 ,干纤
产生原因 : 1 热磨工段制备 的纤维质量较差 ,干 维料仓料位不足 ,板坯扫平辊高度不足 ,铺装机 网带边 () 燥后的纤维含水率过低 ,毛板预 固化层太厚 ,以致砂光 缘有破损都会使板坯纵向或横向铺装厚度负偏差过大 , 机未能完全砂去预固化层使板面大面积粗糙 。 2 ( )热压 导致热压后板边缘 出现此类砂光缺陷。 工艺曲线不合理。热压曲线 的压板闭合升压阶段额定压
A sat h asso m ns d gdf tad h or p nig one aue bt c T e ue f c mo n i e c te r sod u tmesrs nmei dni i e or MD ) rdcdb r : c ro a n e sn c e nc r o d m es br a u t yf b d( F pou e y
板面局部粗糙通常表现为砂光后板面局部发毛或板
面局部粗糙不光滑 ,灯光下粗糙部分呈 白色。局部粗糙 主要有以下3 种现象 :
产生原因 :此类板面缺陷是 由于板坯纵向或横向铺 装厚度负偏差过大导致的 ,板坯纵向和横向的厚度偏差
1 大 面积表 面粗糙 。此种板面缺 陷有时是单面 出 ) 取决于板坯铺装均匀性。铺装机进料摆动机构摆动角度
应对措施 :对铺装机进料摆动机构进行适 当调整 ,
力太低 ,热压后毛板的硬层密度不够导致砂光后板面不 使板坯铺装厚度均匀一致 ;检查纤维料仓的料位情况 ,
光 ;或者是热压 曲线的高压保压阶段时间不足 ,热压后 确保纤维料仓不断料 ;检查 电子板坯称的密度控制系数 板面硬化层太薄 ,以致砂光机把板面硬化层全部砂除而 设定是否合理 ;并检查扫平辊升降控制系统与电子板坯 露 出疏松的低密度层导致板面 比较粗糙。 称 的工作协调性 ,控制板坯质量和纤维在铺装室内的分
砂光的 目的是去除胶黏剂预固化形成 的表面松软层 ,提 以确保 良好的表面装饰效果 。对于连续平压机生产线生
高板面平整度和光洁度 ,使板材满足用户的厚度偏差要 产 的M F D ,砂光缺陷相对少些 ;但对于多层压机生产线 求 ,便 于二次加工 。砂光板表面质量优劣对于二次加工 生产 的M F D ,砂光板经常出现以下砂光缺陷 :板面局部