最新全套 MasterCAM第九章 美容器外壳模具加工例题精析
模具cad cam课后习题答案
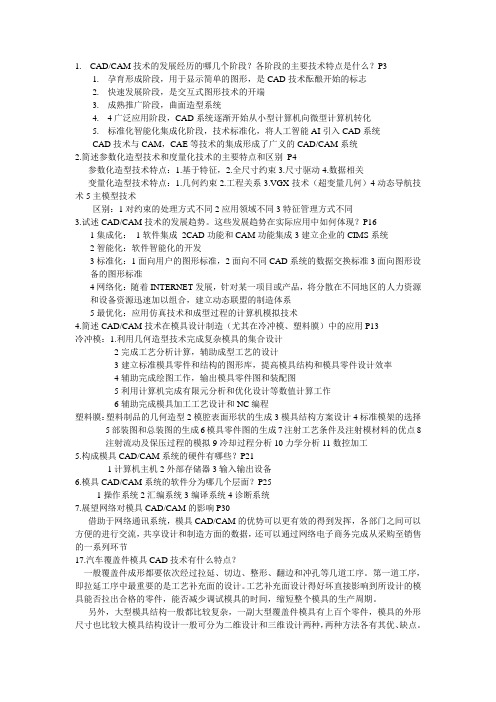
1.CAD/CAM技术的发展经历的哪几个阶段?各阶段的主要技术特点是什么?P31.孕育形成阶段,用于显示简单的图形,是CAD技术酝酿开始的标志2.快速发展阶段,是交互式图形技术的开端3.成熟推广阶段,曲面造型系统4.4广泛应用阶段,CAD系统逐渐开始从小型计算机向微型计算机转化5.标准化智能化集成化阶段,技术标准化,将人工智能AI引入CAD系统CAD技术与CAM,CAE等技术的集成形成了广义的CAD/CAM系统2.简述参数化造型技术和度量化技术的主要特点和区别P4参数化造型技术特点:1.基于特征,2.全尺寸约束3.尺寸驱动4.数据相关变量化造型技术特点:1.几何约束2.工程关系3.VGX技术(超变量几何)4动态导航技术5主模型技术区别:1对约束的处理方式不同2应用领域不同3特征管理方式不同3.试述CAD/CAM技术的发展趋势。
这些发展趋势在实际应用中如何体现?P161集成化:1软件集成2CAD功能和CAM功能集成3建立企业的CIMS系统2智能化:软件智能化的开发3标准化:1面向用户的图形标准,2面向不同CAD系统的数据交换标准3面向图形设备的图形标准4网络化:随着INTERNET发展,针对某一项目或产品,将分散在不同地区的人力资源和设备资源迅速加以组合,建立动态联盟的制造体系5最优化:应用仿真技术和成型过程的计算机模拟技术4.简述CAD/CAM技术在模具设计制造(尤其在冷冲模、塑料膜)中的应用P13冷冲模:1.利用几何造型技术完成复杂模具的集合设计2完成工艺分析计算,辅助成型工艺的设计3建立标准模具零件和结构的图形库,提高模具结构和模具零件设计效率4辅助完成绘图工作,输出模具零件图和装配图5利用计算机完成有限元分析和优化设计等数值计算工作6辅助完成模具加工工艺设计和NC编程塑料膜:塑料制品的几何造型2模腔表面形状的生成3模具结构方案设计4标准模架的选择5部装图和总装图的生成6模具零件图的生成7注射工艺条件及注射模材料的优点8注射流动及保压过程的模拟9冷却过程分析10力学分析11数控加工5.构成模具CAD/CAM系统的硬件有哪些?P211计算机主机2外部存储器3输入输出设备6.模具CAD/CAM系统的软件分为哪几个层面?P251操作系统2汇编系统3编译系统4诊断系统7.展望网络对模具CAD/CAM的影响P30借助于网络通讯系统,模具CAD/CAM的优势可以更有效的得到发挥,各部门之间可以方便的进行交流,共享设计和制造方面的数据,还可以通过网络电子商务完成从采购至销售的一系列环节17.汽车覆盖件模具CAD技术有什么特点?一般覆盖件成形都要依次经过拉延、切边、整形、翻边和冲孔等几道工序。
模具CADCAM考题及课后习题复习资料(宁波工程师考试)
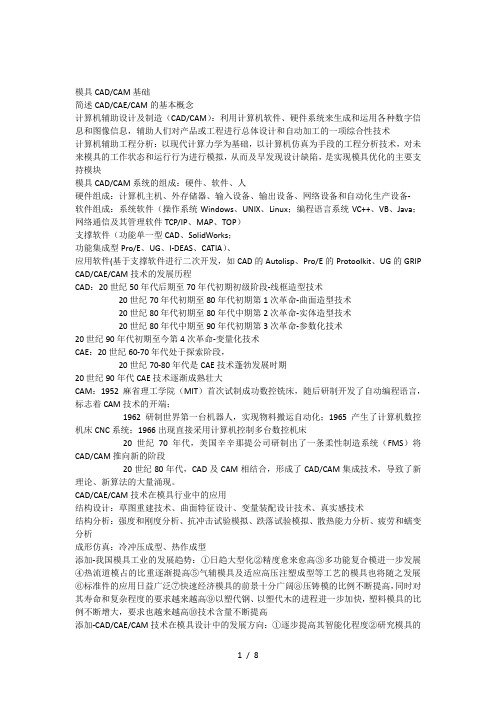
模具CAD/CAM基础简述CAD/CAE/CAM的基本概念计算机辅助设计及制造(CAD/CAM):利用计算机软件、硬件系统来生成和运用各种数字信息和图像信息,辅助人们对产品或工程进行总体设计和自动加工的一项综合性技术计算机辅助工程分析:以现代计算力学为基础,以计算机仿真为手段的工程分析技术,对未来模具的工作状态和运行行为进行模拟,从而及早发现设计缺陷,是实现模具优化的主要支持模块模具CAD/CAM系统的组成:硬件、软件、人硬件组成:计算机主机、外存储器、输入设备、输出设备、网络设备和自动化生产设备-软件组成:系统软件(操作系统Windows、UNIX、Linux;编程语言系统VC++、VB、Java;网络通信及其管理软件TCP/IP、MAP、TOP)支撑软件(功能单一型CAD、SolidWorks;功能集成型Pro/E、UG、I-DEAS、CATIA)、应用软件(基于支撑软件进行二次开发,如CAD的Autolisp、Pro/E的Protoolkit、UG的GRIP CAD/CAE/CAM技术的发展历程CAD:20世纪50年代后期至70年代初期初级阶段-线框造型技术20世纪70年代初期至80年代初期第1次革命-曲面造型技术20世纪80年代初期至80年代中期第2次革命-实体造型技术20世纪80年代中期至90年代初期第3次革命-参数化技术20世纪90年代初期至今第4次革命-变量化技术CAE:20世纪60-70年代处于探索阶段,20世纪70-80年代是CAE技术蓬勃发展时期20世纪90年代CAE技术逐渐成熟壮大CAM:1952麻省理工学院(MIT)首次试制成功数控铣床,随后研制开发了自动编程语言,标志着CAM技术的开端;1962研制世界第一台机器人,实现物料搬运自动化;1965产生了计算机数控机床CNC系统;1966出现直接采用计算机控制多台数控机床20世纪70年代,美国辛辛那提公司研制出了一条柔性制造系统(FMS)将CAD/CAM推向新的阶段20世纪80年代,CAD及CAM相结合,形成了CAD/CAM集成技术,导致了新理论、新算法的大量涌现。
数控加工8.1 综合加工实例----工具外壳凹模

8.1.4体积铣-粗加工环行铣
零件粗加工采用Ø12R4的牛鼻刀。刀具类型、工件材料和加工类型 等切削参数如表8-3所示。
参数 工件材料 刀具材料 刀具类型 刀具刃数 刀具直径
表8-3 切削参数
参数值Leabharlann 参数P20刀具圆角半径
淬层硬质合金 切削深度
牛鼻刀
预留量
2
主轴转速
12mm
进给
参数值 4mm 1.00mm 0.30mm 3000r/min 500mm/min
图8-3 “特征向导”栏
图8-4 零件加工方位
2.创建刀具
在【加工向导】工具条中单击【刀具】按钮,弹出【刀具和夹头】对
话框,按表8-2所示数据设置刀具的参数。设置好的刀具如图8-5所示,
单击【确定】按钮创建刀具。
表8-2
刀具表参数
刀具名称
刀具类型
直径(mm)
拐角半径
B12R4
牛鼻刀
12.00
4.00
8.1.1加工工艺分析
• 本例加工为一工具外壳的凹模,其中两边型腔为对称结构。该模型主要为平 面结构,中间一部分圆柱形曲面,型腔要求有良好的尺寸精度和表面粗糙度。 工件毛坯整体尺寸为158mm×140mm×50mm,采用P20的材料。工件以 底面固定安装在机床工作台上。
8.1.1加工工艺分析
• 工件的加工坐标X和Y设置在模型上表面中心,Z的原点位于上表面。本例各型 腔的深度较浅,所以加工切削量较小,形状特征也较为简单,因此可以采用 较少的工序完成整体加工。对本例的加工采用三个工序,先是采用粗加工环 行铣加工方式,刀具为B12R4环形刀,刀具直径为Ø12,圆角半径为4,切除所 有加工曲面大部分的毛坯余量,然后采用.曲面铣-根据角度精铣,刀具为 BALL06球头刀,通过设定的加工边界,完成模型曲面部分的精加工,最后采 用2.5轴-型腔铣削-平行切削,刀具为FLAT04平头刀,通过设定的加工边界将 平面部分进行精加工,达到零件加工精度要求。本例在Cimatron E 中的操作 流程如表8-1所示:
模具维修工职业技能知识题库与答案剖析
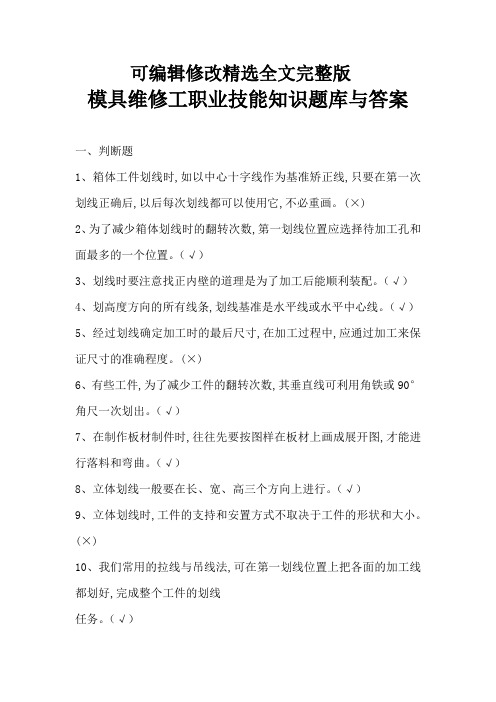
可编辑修改精选全文完整版模具维修工职业技能知识题库与答案一、判断题1、箱体工件划线时,如以中心十字线作为基准矫正线,只要在第一次划线正确后,以后每次划线都可以使用它,不必重画。
(×)2、为了减少箱体划线时的翻转次数,第一划线位置应选择待加工孔和面最多的一个位置。
(√)3、划线时要注意找正内壁的道理是为了加工后能顺利装配。
(√)4、划高度方向的所有线条,划线基准是水平线或水平中心线。
(√)5、经过划线确定加工时的最后尺寸,在加工过程中,应通过加工来保证尺寸的准确程度。
(×)6、有些工件,为了减少工件的翻转次数,其垂直线可利用角铁或90°角尺一次划出。
(√)7、在制作板材制件时,往往先要按图样在板材上画成展开图,才能进行落料和弯曲。
(√)8、立体划线一般要在长、宽、高三个方向上进行。
(√)9、立体划线时,工件的支持和安置方式不取决于工件的形状和大小。
(×)10、我们常用的拉线与吊线法,可在第一划线位置上把各面的加工线都划好,完成整个工件的划线任务。
(√)11、材料的屈服强度越低,有利于提高塑性变形后的形状精度和表面质量。
(√)12、r值是评判板料拉深性能好坏的重要指标,r值增大,拉深极限变形程度增大。
(√)13、采用波浪刃口的冲模,落料时,波浪刃口应做在凸模上。
(×)14、冲压件三座标测量,检测值X向为负值,表示测量点相对理论值向后。
(×)15、当冲床的滑块处于下死点位置,并且连杆调到最短时,滑块底面到冲床台面的距离叫冲床的最小闭合高度。
(×)16、平刃剪切适于剪切宽度小而厚度较大的板料;斜刃剪切适于剪切宽度较大而厚度较薄的板料。
(×)17、在图纸比例中,M2:1表示实物与图示比例为2:1。
(×)18、在灰铁上攻M12的螺纹孔,底孔直径应为Φ10.2。
(√)19、在其它条件相同的情况下,仅凸模圆角不同,弯曲后凸模圆角小的回弹较小。
经验Mastercam9.1编程之必看经验

经验Mastercam9.1编程之必看经验1、在写⼑路之前,将⽴体图画好后,要将图形中⼼移到坐标原点,最⾼点移到Z=0,加缩⽔率后,⽅可以加⼯,铜公⽕花位可加⼯负预留量。
2、在加⼯前还要检查⼯件的装夹⽅向是否同电脑中的图形⽅向相同,在模具中的排位是否正确,装夹具是否妨碍加⼯,前后模的⽅向是否相配。
还要检查你所⽤的⼑具是否齐全,校表分中的基准等。
3、加⼯铜公要注意的事项:1)⽕花位的确定,⼀般幼公(即精公)预留量为0.05~0.15,粗公0.2~0.5,具体⽕花位的⼤⼩可由做模师⽗定。
2)铜公有没有加⼯不到的死⾓,是否需要拆多⼀个散公来。
3)加⼯铜⼯的⼑路按排⼀般是:⼤⼑(平⼑)开粗-⼩⼑(平⼑)清⾓[$#0]光⼑⽤球⼑光曲⾯。
4)开粗⼀般教师⽤平⼑不⽤球⼑,⼤⼑后⽤⼩⼑开粗,然后将外形光到数,接着⽤⼤的球⼑光曲⾯,再⽤⼩球⼑光曲⾯不要图省事,为了些⼩的⾓位⽽⽤⼩⼑去加⼯⼤⼑过不了的死⾓可⼼限定⼩⼑的⾛⼑范围,以免直播太多的空⼑。
5)铜公,特别是幼公,是精度要求⽐较⾼的,公差⼀般选0.005~0.02,步距0.05~0.3。
铜公开粗时要留球⼑位的过⼑位,即要将铜公外形开粗深⼀个⼑半径。
6)铜公还要加⼯分中位,校表基准,⽕花放电时要校正铜⼯,⼀般校三个⾯(上,下,左,右)加⼯出的铜⼯必须有三个基准⾯。
7)铜料是⽐较容易加⼯的材料,⾛⼑速度,转速都可以快⼀点,开粗时,留加⼯余量0.2~0.5,视⼯件⼤⼩⽽定,加⼯余量⼤,开粗时⾛⼑就可以快,提⾼效率。
加⼯铜料的有关经验参数:⼑具⼤⼩1~23~56~1012~20进给率(FEED rate)50~200(50~100)200~500(50~300)500~1000(200~600)1000~2000(600~1000)主轴转速(SPINDLE)30003000~2500(2400~1200)2500~2000(1200~700)1500~2000(600~250)注:括号内为⾼速钢⼑对钢料开粗时的参数,以上⾛⼑速度是指开粗时,要光外形F=300~500,钢料光⼑F为 50~200。
模具加工试题及答案

模具加工试题及答案一、单项选择题(每题2分,共20分)1. 模具加工中,以下哪个选项不是常用的加工方法?A. 数控铣削B. 电火花加工C. 手工打磨D. 激光切割答案:C2. 在模具设计中,以下哪个参数不是影响模具强度的因素?A. 材料硬度B. 模具尺寸C. 模具表面粗糙度D. 模具形状答案:C3. 模具的冷却系统设计主要为了解决以下哪个问题?A. 提高模具的加工速度B. 减少模具的磨损C. 延长模具的使用寿命D. 减少成型件的冷却时间答案:D4. 在模具加工过程中,以下哪个步骤是用于提高模具表面质量的?A. 粗加工B. 精加工C. 热处理D. 抛光答案:D5. 以下哪个材料不是常用的模具钢?A. P20B. H13C. 45号钢D. 316不锈钢答案:D6. 以下哪个不是模具加工中常见的测量工具?A. 卡尺B. 千分尺C. 游标卡尺D. 螺旋测微器答案:C7. 模具加工中,以下哪个选项不是数控加工的特点?A. 精度高B. 灵活性好C. 劳动强度大D. 生产效率高答案:C8. 在模具加工中,以下哪个因素不会影响加工精度?A. 机床精度B. 刀具磨损C. 操作者技能D. 材料硬度答案:D9. 模具加工中,以下哪个步骤不是热处理过程?A. 退火B. 淬火C. 回火D. 抛光答案:D10. 以下哪个不是模具加工中常用的润滑剂?A. 切削液B. 润滑油C. 润滑脂D. 冷却液答案:D二、多项选择题(每题3分,共15分)1. 模具加工中,以下哪些因素会影响模具的使用寿命?A. 材料选择B. 加工精度C. 操作者技能D. 模具维护答案:A B D2. 以下哪些是模具加工中常见的误差来源?A. 机床误差B. 刀具误差C. 材料误差D. 人为误差答案:A B C D3. 模具加工中,以下哪些步骤属于后处理过程?A. 热处理B. 抛光C. 装配D. 调试答案:B C D4. 以下哪些是模具加工中常用的测量方法?A. 直接测量B. 间接测量C. 比较测量D. 非接触测量答案:A B C5. 以下哪些是模具加工中常见的问题?A. 尺寸超差B. 表面粗糙C. 材料变形D. 精度不足答案:A B C三、判断题(每题1分,共10分)1. 模具加工中,数控铣削是一种常用的加工方法。
Mastercam9.1教案(一)

Ⅰ、组织教学清点人数,安定课堂,集中学生思想,维持课堂纪律,掌握教学进程。
Ⅱ、复习引入MasterCAM9.0的用途:集成了CAD/CAM功能,有四大模块,只讲授mill(数控铣)。
Ⅲ、授新1.介绍CAM软件的使用情况。
2.学习CAM的重要性。
3.学习MasterCAM9.0的方法4.课堂要求,上机操作注意事项5.MasterCAM9.0的安装。
a.卸载b.定制安装c.破解d.汉化e.启动6.学生动手安装Ⅳ、小结MasterCAM9.0的安装Ⅰ、组织教学清点人数,安定课堂,集中学生思想,维持课堂纪律,掌握教学进程。
Ⅱ、复习引入MasterCAM9.0的安装、汉化过程Ⅲ、上机练习1.MasterCAM9.0的安装。
f.卸载g.定制安装h.破解i.汉化6.启动MasterCAM9.0进行绘图热身7.巡回指导a.指导学生进行安装。
b.指导学生进行绘图热身。
c.指导学生进行其它的操作。
Ⅳ、小结MasterCAM9.0的安装要点、方法和步骤Ⅰ、组织教学清点人数,安定课堂,集中学生思想,维持课堂纪律,掌握教学进程。
Ⅱ、复习引入数控加工编程中,对于曲面的加工编程,用人工编写程序,计算工作量大,有些根本无法完成,只有借助于计算机来完成,现在自动编程的软件的MASTERCAM,UG,POWERMILL等Ⅲ、新授课题1 认识MasterCAM9.1软件界面一、任务描述认识如图所示的Mastercam 9.1 的软件窗口界面,并对软件系统进行参数设置。
二、任务实施1.启动Mastercam 9.1 2、Mastercam 9.1软件窗口界面3、系统设置4、离开Mastercam 9.1Ⅳ、小结窗口界面、系统设置Ⅰ、组织教学清点人数,安定课堂,集中学生思想,维持课堂纪律,掌握教学进程。
Ⅱ、复习引入1、启动Mastercam 9.12、Mastercam 9.1软件窗口界面3、系统设置4、离开Mastercam 9.1Ⅲ、上机练习课题1 认识MasterCAM9.1软件界面一、任务描述认识如图所示的Mastercam 9.1 的软件窗口界面,并对软件系统进行参数设置。
模具制造技术课后习题及答案(共9单元)第2章 模具零件的机械加工

第2章模具零件的机械加工思考题与习题l.在模具加工中,制定模具零件工艺规程的主要依据是什么?答:根据模具零件的几何形状、尺寸和模具零件的技术要求,结合现有加工技术和设备情况下,能以最经济、最安全加工出高质量的模具零件作为依据。
2.在导柱的加工过程中,为什么粗(半精)、精加工都采用中心孔作定位基准?答:导柱的加工过程中,为了保证各外圆柱面之间的位置精度和均匀的磨削余量。
对外圆柱面的车削和磨削,一般采用设计基准和工艺基准重合的两端中心孔定位。
所以,在半精车、精车和磨削之前需先加工中心定位孔,为后继工序提供可靠的定位基准。
3.导柱在磨削外圆柱面之前,为什么要先修正中心孔?答:磨削前对导柱进行了热处理,导柱中心定位孔在热处理后的修正,目的是消除热处理过程中中心孔可能产生的变形和其它缺陷,使磨削外圆柱面时能获得精确定位,保证外圆柱面的形状和位置精度要求。
4.拟出图2.1所示导柱的工艺路线,并选出相应的机加工设备。
图2.1可卸导柱导柱加工工艺过程工序号工序名称工序内容设备检验1 备料Φ36mm(20号钢)2 下料按图纸尺寸考虑切削余量Φ36m m×195㎜锯床自检车床自检3 粗车外圆定位:①车端面打中心孔;车外圆到Φ34mm;②调头车端面(到尺寸190mm),打中心孔,车外圆到Φ34mm。
4 精车中心孔定位:车床专职检验员①精车外圆面到尺寸(留磨削余量0.2mm),精车R3;5 精车调头外圆定位:①车锥面到尺寸,倒角C1.5;②在端面钻M8螺纹底孔,前端按图扩孔到Φ8.4,攻丝M8,端面锪孔到尺寸。
车床6 热处理①20号钢渗碳0.8~1.2㎜;②淬火HRC58~62。
热处理炉(检验硬度、平直度)。
7 研磨中心孔外圆定位:研磨中心定位孔。
车床8 磨外圆中心孔定位:粗磨、精磨外圆、锥面磨床自检9 研磨①研磨导柱导向部分外圆10 检验专职检验员11 入库清洗、喷涂防锈润滑油后,分类用塑料薄膜包封后入库5.导套加工时,怎样保证配合表面间的位置精度要求?答:由于构成导套的主要表面是内、外圆柱表面,一般采用一次装夹后,完成对有位置精度要求的内、外圆柱表面的车削和热处理后的磨削加工就能保证配合表面间的位置精度要求。
mastercam9.0学习课件

退回高度(参考高度):是指刀具在Z向加工完一 个刀具路径后,在Z向快速提刀所达到的高度。该 高度通常低于安全高度,而高于进给高度。表示方 法有绝对坐标和相对坐标两种。
4、提示区
在荧屏的上方和下方,在操作过程中,常有一行或两行
的文字用于表明指令的状态,这是Mastercam给使用者信
息的地方。注意这个地区,特别是刚学的时候,在你不知
如何操作下去的时候,往往在这两个区域里会出现提示,
叫你下一步该如何做。
5、绘图区
绘图操作的区域。
2019/5/6
7
软件启动和退出
启动和退出
有两种用法: 1、投影加工一般用于工件表面上刻字,因为产品上的字通常 为凸形,在模具加工时为凹形,加工性较好。 此时的加工余量应选负余量,在曲面加工里,负余量不能大 于刀具的转角半径。 2、球表面的加工通常也选用投影加工。
作业: 1、重做一遍例题CAM3 2、CAM6
例3
工艺流程 分析图形
2019/5/6
9
造型实例
实验图
学习重点 1、线框绘制 2、实体造型 3、实体表面转成曲面的方法 4、曲面曲线的生成方法
• 步骤1
绘图-直线-
• 分别设置 • 荧屏视角:T, • WCS:T, • 构图面:T, • Z:0, • 作图层别:1, • 作图颜色: • 图素属性:
• 步骤2 • 绘制水平和竖直基准线,以原点
模具零件加工练习试题及参考答案
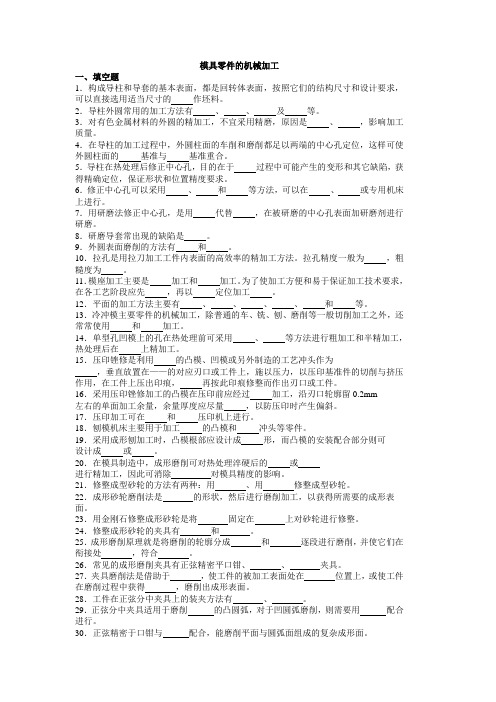
模具零件的机械加工一、填空题1.构成导柱和导套的基本表面,都是回转体表面,按照它们的结构尺寸和设计要求,可以直接选用适当尺寸的作坯料。
2.导柱外圆常用的加工方法有、、及等。
3.对有色金属材料的外圆的精加工,不宜采用精磨,原因是、,影响加工质量。
4.在导柱的加工过程中,外圆柱面的车削和磨削都足以两端的中心孔定位,这样可使外圆柱面的基准与基准重合。
5.导柱在热处理后修正中心孔,目的在于过程中可能产生的变形和其它缺陷,获得精确定位,保证形状和位置精度要求。
6.修正中心孔可以采用、和等方法,可以在、或专用机床上进行。
7.用研磨法修正中心孔,是用代替,在被研磨的中心孔表面加研磨剂进行研磨。
8.研磨导套常出现的缺陷是。
9.外圆表面磨削的方法有和。
10.拉孔是用拉刀加工工件内表面的高效率的精加工方法。
拉孔精度一般为,粗糙度为。
11.模座加工主要是加工和加工。
为了使加工方便和易于保证加工技术要求,在各工艺阶段应先,再以定位加工。
12.平面的加工方法主要有、、、、和等。
13.冷冲模主要零件的机械加工,除普通的车、铣、刨、磨削等一般切削加工之外,还常常使用和加工。
14.单型孔凹模上的孔在热处理前可采用、等方法进行粗加工和半精加工,热处理后在上精加工。
15.压印锉修是利用的凸模、凹模或另外制造的工艺冲头作为,垂直放置在——的对应刃口或工件上,施以压力,以压印基准件的切削与挤压作用,在工件上压出印痕,再按此印痕修整而作出刃口或工件。
16.采用压印锉修加工的凸模在压印前应经过加工,沿刃口轮廓留0.2mm左右的单面加工余量,余量厚度应尽量,以防压印时产生偏斜。
17.压印加工可在和压印机上进行。
18.刨模机床主要用于加工的凸模和冲头等零件。
19.采用成形刨加工时,凸模根部应设计成形,而凸模的安装配合部分则可设计成或。
20.在模具制造中,成形磨削可对热处理淬硬后的或进行精加工,因此可消除对模具精度的影响。
21.修整成型砂轮的方法有两种:用、用修整成型砂轮。
Cimatron9.0_NC功能中文说明

3-5 Axis加工模拟.................................................................................................................................. 22
所有仿真在同一界面............................................................................................错误!未定义书签。 毛胚切削更清晰, 自动检查过切和碰撞............................................................................................. 23
粗加工选项 ................................................................................................................错误!未定义书签。
改善粗加工质量、提高效率 ............................................................................................................... 1 最少毛胚宽度.......................................................................................................错误!未定义书签。 缩短空连接距离 ...................................................................................................错误!未定义书签。 空连接允许指定Z轴相对高度...............................................................................错误!未定义书签。 高速加工 (HSM)选项 – 允许控制摆线半径 ........................................................................................ 5 粗加工功能扩展到二粗,用粗加工来代替原有的二粗 .........................................错误!未定义书签。
车床加工Mastercam9.1数控车床加工教程(非常详细).

10.2.1 粗车
选择“车床的刀具路径相关设定”子菜 单中的“粗车”选项可调用粗车模组。 粗车模组用来切除工件上大余量的材料, 使工件接近于最终的尺寸和形状,为精 加工做准备。工件的外形通过在绘图区 选取一组曲线串连来定义。该模组所特 有的参数可用 “粗车的参数”选项卡来 进行设置。
该组参数的设置主要是对加工参数、走刀方 式、粗车方向与角度、刀具偏置及切进参数等 进行设置。
20
2003.07.20
“边界设置”对话 框 Mastercam
21
“夹头”选项组用来设置工件夹头。工件夹 头的设置方法与工件外形的设置方法基本相同。 其主轴转向也可设置为左向(系统默认设置) 或右向。夹头的外形边界可以用串连、矩形或 己绘制工件夹头外形来定义 顶尖通过“尾座”选项组来设置尾座顶尖的外 形,设置与夹头的外形设置相同,也可以用串 连、矩形或已绘制工件夹头外形来定义。 工件外形、夹头外形和顶尖外形设置都是用 来定义加工过程中的安全边界。在定义了安全 边界后还需定义两个安全距离,安全距离通过 “刀具位移的安全间隙”选项组来设置。其中 “快速位移”用于设定快速位移(G00)时刀 具与工件的安全间隙;“进入/退出”输入框用 于指定在进刀/退刀时刀具与工件的安全间隙。 2003.07.20 Mastercam 22
卡
Mastercam
8
车刀通常由 Insert(刀头) Holder( 刀柄)两部分组成。所以车床系统刀具 的设置包括刀具类型、刀头、刀柄及刀 具参数的设置。 1. 刀具类型
车床系统提供了一般车削、螺纹 车削、径向车削/切断、镗孔及钻孔/ 攻牙/铰孔及自设6种类型的刀具。
Mastercam 9
Mastercam 3
masterCAM9.1教程(全)

2.1.10网格点 2.1.11圆周点 2.1.12小弧
2.2 直 线 的 构 建
2.2.1 水平线
在当前构图面上生成和工作坐标系X 轴平行的线段。
2.2.2 垂直线
在当前构图面上生成和工作坐标系Y 轴平行的线段。
2.2.3 任意线段
由两个任意点生成一条直线。这两个 点可以用鼠标选取,也可以用键盘输入坐 标,可以生成一条三维直线。
删除所有的图素或某类别中的所有的图素 删除指定群组图素 删除经过前一次转换后成为结果的图素 删除重复的图素 恢复被删除的图素
(一)串连选择
将相交的若干图素沿某种方向连成一 串。串连方式可以定义起点和终点,还可 以指定串连方向。
(二)窗选
表 3-2 窗 选 菜 单 功 能 描 述
R矩形
使用鼠标以两点式拖拉出矩形窗口选取图素
第1章 基 础 知 识
1.1 MasterCAM V9.0 模块功能简介 1.2 MasterCAM V9.0 的铣削加工特点 1.3 MasterCAM VC Software, INC开发的CAD/CAM系统,是最经济有 效率的全方位的软件系统。在国内外 CAD/CAM领域,它是微机平台上装机量 最多、应用最广泛的软件,成为 CAD/CAM系统的行业标准。
2.1.5 动态绘点
可以沿选取的图素用鼠标的移动动态 的生成需要点。该图素可以是直线,曲线, 圆弧,样条曲线,实体。
2.1.6 指定长度
可以在选取的线条(直线,曲线,圆 弧,样条曲线)上生成一个与靠近选取点 的端点有一定距离的点。
2.1.7 剖切点
可以在选取的一条或多条线条(直线, 曲线,圆弧,样条曲线)上生成与指定平 面的交点。该平面称剖切平面。
第三章 几何图形的编辑和尺寸标注
Mastercam中文版教程(第2版)第09章

的起点,如图9-22(b)所示。
(b) 图9-22移动量小于容许间隙时的移动方式示例
Smooth(平滑):用于高速加工,刀
具路径沿着平滑方式越过间隙,如图 9-22
(c)所示。
( c) 图9-22移动量小于容许间隙时的移动方式示例
Follow surface(s)(沿着曲面):刀具
从一曲面刀具路径的终点沿着曲面外形移
制刀轴相对于工件除了三个方向的移动外
增加了刀轴的转动和摆动。
使用 CAD/CAM 软件进行数控编程时, 用到最多的还是对曲面进行加工。对于一 个具有较为复杂形状的工件(如模具)而 言,只有通过沿着其曲面轮廓外形进行加 工才能获得所需的形状。MasterCAM的曲 面加工系统可用来生成加工曲面、实体或 实体表面的刀具路径。实际加工中,大多 数的零件都需要通过粗加工和精加工来完 成, MASTERCAM 9 共提供了 8 种粗加工 和10种精加工类型。
在曲面粗加工参数中,下面的几个选 项是各种曲面粗加工方式所共有的,包括: 切削深度、间隙设定与高级设定。在 MasterCAM中将这几个参数单独列出,并 以弹出对话框的方式进行设置。
1.切削深度设置
图9-19 切削深度对话框
2.间隙设定
图 间 隙 设 定 对 话 框 9-20
图9-21 移动量小于容许间隙时的移动方式
Direct(横越):直接以直线切削方 式从前一刀具路径的终点移动到下一刀具
路径的起点,如图9-22(a)所示。
(a) 图9-22移动量小于容许间隙时的移动方式示例
Broken(打断):将移动量打断成 Z 方向和XY方向两段切削,刀具从前一路径 终点沿 Z方向(或 XY方向)移动,然后再 沿 XY方向(或 Z方向)移动,到下一路径
(完整版)模具cam实训
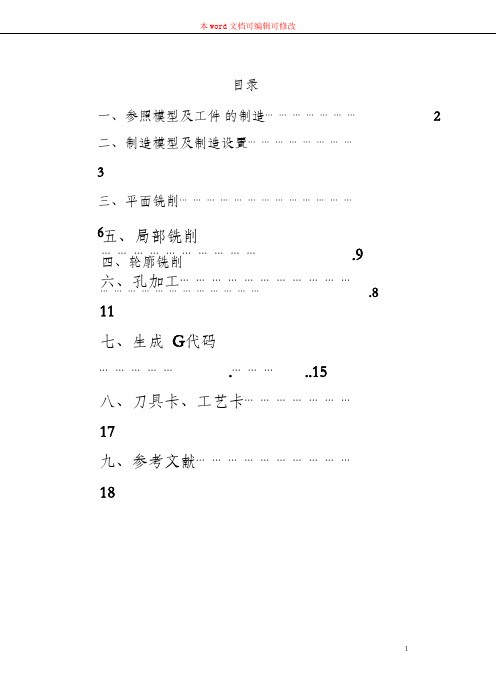
目录一、参照模型及工件 的制造⋯⋯⋯⋯⋯⋯⋯ 2二、制造模型及制造设置⋯⋯⋯⋯⋯⋯⋯⋯ 3三、平面铣削⋯⋯⋯⋯⋯⋯⋯⋯⋯⋯⋯⋯⋯ 6 四、轮廓铣削⋯⋯⋯⋯⋯⋯⋯⋯⋯⋯⋯⋯ .8五、局部铣削⋯⋯⋯⋯⋯⋯⋯⋯⋯⋯ .9六、孔加工⋯⋯⋯⋯⋯⋯⋯⋯⋯⋯⋯11七、生成 G 代码⋯⋯⋯⋯⋯ .⋯⋯⋯ ..15八、刀具卡、工艺卡⋯⋯⋯⋯⋯⋯⋯ 17九、参考文献⋯⋯⋯⋯⋯⋯⋯⋯⋯⋯ 18一、参照模型及工件的制造1、参照模型参照模型是所有 NC加工操作的基础。
在 NC加工前就要确定好参照模型,凹摸的参照模型加工如下:2、工件工件在 NC加工中可以看作是一个加工零件的毛坯,此工件留有2毫米的加工余量,如下图:二、制造模型及制造设置1、制造模型打开 Pro/E,单击【文件】→【新建】→【制造】命令,将系统默认的制造名更改为CAMSX,单击【确定】按钮选择公制模板mmns_part_solid,如下图所示:单击【确定】进入 Pro/E NC主界面,单击【制造】→【制造模型】→【装配】→【参照模型】命令,选择 MX文件【打开】,如图所示 :单击【自动】后面的【 v】,再选择【缺省】选项,单击右下角的【√】。
以此类推装配工件制造模型设定完毕后单击【完成 /返回】,如图所示:2、制造设置制造模型设定好后单击【制造设置】命令,进入【操作设置】对话框单击进入【机床设置】单击【确定】即可,单击【加工零点】中的,在 NC 的主界面中单击按住 Ctrl键,单击 FRONT平面、RIGHT平面和上表面选择【定向】单击 Y后面的【反向】使 Z轴朝上,点击确定完成坐标系的建立。
建立退刀平面,在【操作设置】对话框中单击退刀曲面后面的【↖】,在出现的对话框中点击【沿 Z轴】,输入 8或 10,点击【确定】。
三、平面铣削完成制造设置后,点击【 NC序列】→【新序列】→【加工、表面、 3 轴】→【完成】命令。
【序列设置】:选中【刀具、参数、曲面】→【完成】命令。
工程机械CADCAM课后习题答案

工程机械CADCAM课后习题答案第一章概述1.简述产品设计制造的一般过程。
答:CAD/CAM系统是设计、制造过程中的信息处理系统,它主要研究对象描述、系统分析、方案优化、计算分析、工艺设计、仿真模拟、NC编程以及图形处理等理论和工程方法,输入的是产品设计要求,输出的是零件的制造加工信息。
2.简述CAD/CAM技术的概念、狭义和广义CAD/CAM技术的区别与联系。
答:CAD/CAM技术是以计算机、外围设备及其系统软件为基础,综合计算机科学与工程、计算机几何、机械设计、机械加工工艺、人机工程、控制理论、电子技术等学科知识,以工程应用为对象,实现包括二维绘图设计、三维几何造型设计、工程计算分析与优化设计、数控加工编程、仿真模拟、信息存贮与管理等相关功能。
区别:广义的CAD/CAM技术,是指利用计算机辅助技术进行产品设计与制造的整个过程,及与之直接和间接相关的活动;狭义的CAD/CAM技术,是指利用CAD/CAM系统进行产品的造型、计算分析和数控程序的编制联系:广义的CAD/CAM技术包容狭义的CAD/CAM技术3.传统的设计制造过程与应用CAD/CAM技术进行设计制造的过程有何区别与联系?答:区别:传统的设计与制造方式是以技术人员为中心展开的,,产品及其零件在加工过程中所处的状态,设计、工艺、制造、设备等环节的延续与保持等,都是由人工进行检测并反馈,所有的信息均交汇到技术和管理人员处,由技术人员进行对象的相关处理。
以CAD/CAM技术为核心的先进制造技术,将以人员为中心的运作模式改变为以计算机为中心的运作模式,利用计算机存贮量大、运行速度快、可无限期利用已有信息等优势,将各个设计制造阶段及过程的信息汇集在一起,使整个设计制造过程在时间上缩短、在空间上拓展,与各个环节的联系与控制均由计算机直接处理,技术人员通过计算机这一媒介实现整个过程的有序化和并行化。
联系:制造过程的各个环节基本相同。
4.简述我国CAD/CAM技术发展的过程与特点。
mastercam考试文档

、填空题(每空1分,共36分)1.MasterCAM9.1分为CAD 和CAM两部分,其中CAD 部分即是计算机辅助设计部分。
2.MasterCAM9.1的工作窗口主要由标题栏、工具栏、坐标显示区、次菜单区、绘图区、信息提示区几部分组成。
3.依次选取绘图、点命令将得到绘点模式子菜单。
4.绘制一段圆弧,一般采用极坐标方式绘制。
5.二维图形的编辑方法有删除、修整、转换等功能。
6.曲面的构建方法有举升曲面、昆氏曲面、直纹曲面、旋转曲面、扫描曲面、牵引曲面。
7.曲面的编辑是通过已有的曲面利用曲面倒圆角、曲面偏移、曲面修剪(延伸)及曲面熔接等创建新的平面。
8.创建实体的方法有挤出、旋转、扫描、举升等方法创建实体。
9.工件的设置包括工件的大小、原点、材料。
10.二维刀具路径有面铣削加工、外形铣削加工、挖槽加工、钻孔加工。
二、选择题(共2题,每题2分,共4分)1.结束正在进行的操作,并返回上一级菜单的快捷键是(B )A、EndB、EscC、F1D、F22.选取次菜单区中的“Cplane:T”命令后,在主菜单区将显示( A )A、构图面子菜单B、刀具平面菜单C、绘图菜单D、视角子菜单三、简答题(共2题,每题5分,共10分)1.外形铣削加工步骤。
答:(1)串连选取加工轮廓;(2)选择刀具;(3)设置外形加工参数;(4)修改刀具路径起点;(5)修改刀具路径方向;(6)加工仿真过程.2.利用一点画矩形步骤。
答:绘图/矩形/一点/设置宽、高尺寸/确定基准点的位置/确定/放置指定基准点。
四、操作题(50分)根据已给图例,写出创建曲面和刀具路径粗、精加工的步骤。
答:一、创建线架(20分)1.构图面:F 视角:I Z=-50 (5分)绘图/圆弧/极坐标/圆心点/原点/起始角度0/终止角度180/半径R=5/确定(5分)2.Z=50 同上绘制另一个圆弧5分)3.构图面:S 视角:I Z=-50 同上画一圆弧(5分)4. Z=50 同上绘制另一个圆弧(5分)二、创建曲面(10分)1.绘图/曲面/直纹曲面/选取F面两个圆弧/执行(5分)2. 绘图/曲面/直纹曲面/选取S面两个圆弧/执行(5分)三、刀具路径(20分)1.刀具路径/工件设定/曲面加工/粗加工(1).挖槽粗加工(2).平行铣削(3).等高外形(10分)2. 刀具路径/工件设定/曲面加工/精加工(1)平行铣削(2)交线清角精加工(3)环绕等距精加工(10分)一、填空题(每空2分,共40分)1.利用MasterCAM9.1系统进行数控编程的基本步骤为CAD 、CAM 、POST。
UG模具设计基础教程(NX 6版)填空题和选择题答案
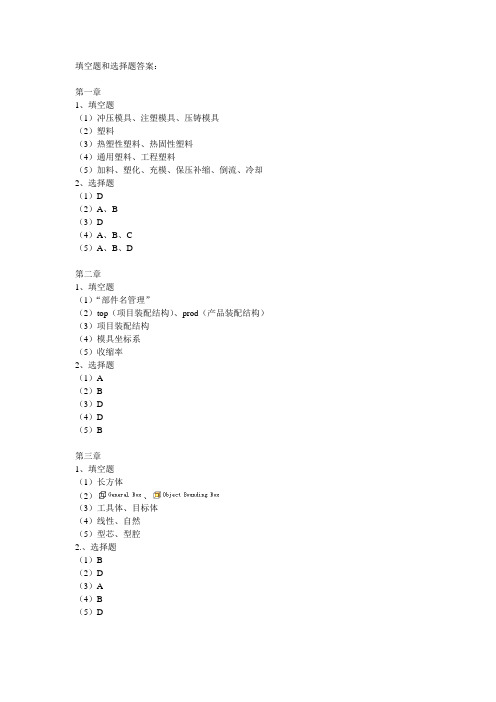
填空题和选择题答案:第一章1、填空题(1)冲压模具、注塑模具、压铸模具(2)塑料(3)热塑性塑料、热固性塑料(4)通用塑料、工程塑料(5)加料、塑化、充模、保压补缩、倒流、冷却2、选择题(1)D(2)A、B(3)D(4)A、B、C(5)A、B、D第二章1、填空题(1)“部件名管理”(2)top(项目装配结构)、prod(产品装配结构)(3)项目装配结构(4)模具坐标系(5)收缩率2、选择题(1)A(2)B(3)D(4)D(5)B第三章1、填空题(1)长方体(2)、(3)工具体、目标体(4)线性、自然(5)型芯、型腔2.、选择题(1)B(2)D(3)A(4)B(5)D第四章1、填空题(1)设计区域(2)型芯、型腔(3)“自动孔修补”(4)分型面(5)抑制分型功能2、选择题(1)C(2)A、B、C(3)D(4)C(5)D第五章1、填空题(1)定模座板、定模板、动模板、动模座板(2)可互换模架、通用模架(3)尺寸(4)分型面(5)宽度×长度2、选择题(1)A(2)B(3)A(4)B(5)B第六章1、填空题(1)使注射机喷嘴与模具浇口套对中,并决定模具在注射机上安装位置(2)顶针(3)和弹性套、衬套等配合一起使用,从而构成脱模机构(4)回程杆(5)导柱、导套2、选择题(1)B(2)D(3)A(4)C(5)D第七章1、填空题(1)浇口套(2)将熔融状态的塑料粘流体经过注塑机喷嘴在高温、高压和高速状态下,通过浇注系统进入模具型腔,并在填充和固化定型的过程中,将型腔内的气体顺利排出,且将压力传递到型腔的各个部位,以获得组织致密,外形清晰,表面光洁和尺寸稳定的塑件(3)主流道、分流道、浇口(4)主流道(5)浇口2、选择题(1)D(2)D(3)D(4)C(5)D第八章1、填空题(1)模具型腔和型芯(2)40(3)ABS和POM(4)迅速、均匀(5)塑件厚度均匀时,冷却孔至型腔表面的距离将均匀,从而使冷却均匀第九章1、填空题(1)支持用户列出模具设计过程中用到的所有标准部件,以及其相关数据,方便用户查阅(2)创建模具的工程图(3)表达部件零件之间的装配关系(4)表达各零件的结构图(5)视图管理器。
- 1、下载文档前请自行甄别文档内容的完整性,平台不提供额外的编辑、内容补充、找答案等附加服务。
- 2、"仅部分预览"的文档,不可在线预览部分如存在完整性等问题,可反馈申请退款(可完整预览的文档不适用该条件!)。
- 3、如文档侵犯您的权益,请联系客服反馈,我们会尽快为您处理(人工客服工作时间:9:00-18:30)。
第九章美容器外壳模具加工例题精析9.1 前模程序编制9.1.1 本例要点:(1)前模凹槽加工要点(2)编程过程中辅助面及辅助线的应用(3)刀补刀具的应用(4)前模加工工艺要点9.1.2 工件分析和工艺流程(1)工件分析如图9-2所示为前模图9-1CA V,型腔为凹槽,要求较高,需进行整体出铜公,分型面为圆弧面。
型腔材料为国产718。
毛坯六面已经平整。
(2)加工坐标原点X:取前模的中心Y:取前模的中心Z:取前模最高平面(3)工艺分析由于毛坯形状为立方体,所以在局部区域有较大的余量,首先采用曲面挖槽加工方式进行粗加工。
选用的刀具为D30R5圆鼻刀粗加工后,凹槽底部和交角部位`还有较多余量,所以使用等高外形加工方式进行一个整体半精刀具路径。
选用D16R0.8圆鼻刀。
进行一个曲面残料粗加工,清除半精程序所留的剩余量,选用D6平刀。
对按钮位和镜片位的碰穿面进行平行铣削精加工,注意碰穿面的加工方法,选用D8R4球刀。
对圆弧分型面进行平行铣削精加工,加工时候注意利用用辅助曲面和辅助曲线,选用D8R4球刀。
凹槽位通过半精和残料加工后,曲面比较粗糙,余量不均匀,所以再用D8R4球刀进行一个平行铣削半精加工。
注意干涉面的选用。
对前模中的平面进行推面加工,使用挖槽加工方式,选用D10平刀分型面跟平面的交角位使用球刀时加工不到位,所以再选用D10平刀进行平行铣削加工,清除根部交界位残留量表9-1美容器前模加工工步图9-1 加工步骤示意图9.1.3 程序编制步骤打开文件单击主功能表中档案→取档,在弹出的文件列表中选择正确的文件路径,并选择9-1.mc9文件,打开图形文件。
按F9键显示坐标系。
打开图层可以看到第一层是CA V,第二层是CORE,第三层是L1 ,第四层是L2 ,选择第一层,关掉其它层,然后确定,所以屏幕上只显示前模图。
将图素另存为9-1CA V.mc9。
绘制对角线,设置Z深度为最高面。
选择“回主功能表→绘图→直线→两点画线”捕捉到前模两个端点拉一条对角线。
(注:没有端点时,只需做出前模处围边界线)将构图面设为3D,移动图形,选择“回主功能表→转换→平移→所有的图素→执行→两点间”选择所有图形进行两点间的平移操作。
拾取对角线中点,再在抓点方式菜单中选择“原点”。
系统将弹出平移对话框,确认处理方式为“移动”,关闭“使用构图面属性”选项,单击确定按钮进行平移转换,将图形中心移动到坐标原点位置,按F9显示坐标系,移动后的图形如图9-2所示。
图9-2 9-1CA V前模图档点击“清除颜色”设置前模的边界盒,选择“回主功能表→刀具路径→工作设定”打开工作设定窗口,点击“边界盒”设置工件毛坯尺寸,勾选所有图素,确定,在工作设定视窗中可以看到毛坯的尺寸为X190、Y120、Z65,工件原点为X0、Y0、Z0,进给率的计算选择为依照刀具。
前模开粗常用的刀路方法是曲面挖槽,等高外形,平行式光刀。
选刀的原则是大刀开粗→小刀中粗→大刀光刀→小刀光刀。
观察前模图,画圆测量选用什么型号刀具合适。
大圆鼻刀适合切削毛坯较大,残料较多的铁料,所以在这选用D30R5圆鼻刀开粗。
加工前在前模外围作辅助曲面和加工范围线框。
如图9-3所示。
图9-3 作辅助曲面和加工范围线框1.启动曲面挖槽粗加工模组,对前模进行粗加工选择“回主功能表→刀具路径→操作管理”在操作管理员视窗中点击右键选择群组,更改操作群组名称为“D30R5 粗加工”。
选择“回主功能表→刀具路径→曲面加工”命令,设置加工面为A,CAD档和干涉面为N,定义切削范围为Y。
继续选择“粗加工→挖槽粗加工”命令,选取D30.6R5圆鼻刀,设置刀具参数。
在弹出的“曲面粗加工”视窗中选择“曲面加工参数”选项卡,设置参考高度为30(此参数应比零件最高位置点高10MM以上),进给下刀位置为3.0,加工预留量为0.2mm。
为了保证XY方向余量为0.5mm,Z方向只留0.2mm,所以在此开粗程序考虑进行刀补,就是编程选用D30.6R5圆鼻刀,预留量为0.2m。
实际加工时用D30R5的圆鼻刀。
这样就会产生XY余量=0.3+0.2,Z余量为0.2在“刀具的切削范围”选项中单击“选择”,选取图9-3中边界线框1为加工范围,执行。
在“粗加工参数”选项卡中,设置Z轴最大进给量为0.6mm。
如图9-4所示。
点击“切削深度”选项,打开加工深度设置,选择“绝对坐标”,勾选“自动调整加工面的预留量”,如图9-5所示。
图9-4 粗加工参数图9-5 切削深度的设定在“挖槽参数”选项卡中,选择“等距环切”切削方式切削间距为刀具直径的52.28%(切削间距(距离)计算方法是:{刀具直径-刀R角*2}*80%。
此方法不适用于球型刀),勾选精修,次数1次,间距为:0.2。
如图9-6所示。
图9-6 挖槽参数设定单击“确定”,系统计算出刀具加工路径,进行手动模拟和切削仿真,如图9-7所示。
捡视刀具路径的正确性,和考虑下一步程序的刀具选择,选用何种加工方法。
图9-7 实体切削仿真选择“回主功能表→档案→存档”命令,选择保存。
储存的图形文件和刀具路径。
(每编一个程序要习惯保存)2.对已生成粗加工程序的前模,进行等高外形精加工(在此处实为半精加工)从上一步对前模的检视和模拟中可以看到,凹槽底部和交角部位`还有较多余量,所以进行一个整体半精刀具路径。
选择“回主功能表→刀具路径→操作管理”在操作管理员视窗中点击右键选择群组,建立新的操作群组,自定义一个名称为“D16R0.8 半精”。
(将每一刀具设置不同群组,使程序目录条理化)选择“回主功能表→刀具路径→曲面加工→精加工→等高外形”命令,在弹出的“曲面精加工”对话框中,选取刀具直径为D16R0.8圆鼻刀(上一步粗加工挖槽选用D30R5圆鼻刀,在这考虑余量所以选用D16R0.8刀具),选择“曲面加工参数”选项卡,考虑是半精程序,所以XY预留量设为0.2mm,参数设定如图9-8所示。
单击“刀具的切削范围”选项中单击“选择”,选取线框1为加工范围,执行。
图9-8 曲面加工参数视窗在“等高外形精加工参数”视窗中,点击整体误差,设置过滤比例为1:1,设置Z轴最大进给量为0.5mm,在开放式轮廓的方向选项中勾选双向,在两区段间的路径选项中更改为打断,勾选进/退刀设置圆弧半径为6mm,扫掠角度为90。
再把切削顺序最佳化选项选中。
如图9-9所示。
图9-9 等高外形精加工参数视窗单击“切削深度”,在“切削深度设定”选项卡中,选择“绝对坐标”,设置绝对的深度,最高位置为-0.1,最低位置为-58.577,把“自动调整加工面的预留量”选项选中。
确定。
单击“确定”,系统计算出刀具加工路径,进行手动模拟和切削仿真。
捡视刀具路径的正确性,和考虑下一步程序的刀具选择,选用何种加工方法。
选择“回主功能表→档案→存档“命令,选择保存。
储存的图形文件和刀具路径。
(每编一个程序要习惯保存)3.生成曲面残料粗加工路径选择“回主功能表→刀具路径→曲面加工→粗加工→残料粗加工”命令,在曲面残料粗加工视窗中选择6.0mm平刀,“曲面加工参数”视窗中的参数设置如图9-10所示。
图9-10 曲面加工参数在“刀具的切削范围”选项中单击“选择”,选取线框1为加工范围,执行。
在“残料加工参数”选项中,参数设置如图9-11所示。
图9-11 残料加工参数单击“残料材料参数”,计算残料的依据选择“所有先前的操作”,按不同的需求来选择剩余材料的计算方式。
如图9-12所示。
图9-12 残余材料参数单击“确定”。
结果生成曲面残料粗加工刀具路径,4.对需精加工的圆弧面选择用D8R4球刀进行平行铣削精加工对需进行平行铣削精加工的面,作小范围线框和辅助面。
如图9-13所示。
A、B、C是要加工的面的加工范围线框,D是加工C位时的辅助面。
图9-13 加工范围线框选择“回主功能表→刀具路径→操作管理”在操作管理员视窗中点击右键选择群组,建立新的操作群组,自定义一个名称为“D8R4 精加工”。
选择“回主功能表→刀具路径→曲面加工→精加工→平行铣削”命令,选择所有的曲面为加工面,执行。
在弹出的“平行铣削精加工”对话框中,选取刀具直径为D8R4球刀,单击确定。
选择“曲面加工参数”选项卡,参数设定如图9-14所示。
图9-14 曲面加工参数视窗在“干涉的曲面/实体”选项中,设置干涉面预留量为0.2mm,单击“选择”出现选择干涉面菜单,单击“增加”在显示的曲面图形中选择线框B外面的曲面为干涉面,“执行”再“执行”回到曲面加工参数视窗,可以看到干涉面选项中已选中若干个面为干涉面单击“刀具的切削范围”选项中单击“选择”,选取图9-13中线框B、C为加工范围,执行。
在“平行铣削精加工参数”视窗中,点击整体误差,设置过滤比比例为1:1,整体误差为0.02mm,设置最大切削间距为0.2mm,加工角度为45。
如图9-15所示。
图9-15 平行铣削精加工参数视窗单击“间隙设定”,在“刀具路径间隙设定”选项卡中,“容许的间隙”选择距离,位移小于容许间隙时不提刀选择平滑,勾选“切削顺序最佳化”。
如图9-16所示。
单击确定。
图9-16刀具路径的间隙设定单击“确定”,系统计算出刀具加工路径,进行手动模拟和切削仿真。
捡视刀具路径的正确性。
选择“回主功能表→档案→存档“命令,选择保存。
储存的图形文件和刀具路径。
(每编一个程序要习惯保存)5.选择用D8R4球刀对分型面进行平行铣削精加工加工分型面E、F时,在第7层作G辅助面,为了加工尺寸更准确,边缘过渡时不起圆角。
如图9-17所示。
图9-17 分型面E、F和辅助面G选择“回主功能表→刀具路径→曲面加工→精加工→平行铣削”命令,选择所有的曲面为加工面,执行。
在弹出的“平行铣削精加工”对话框中,选取刀具直径为D8R4球刀,单击确定。
选择“曲面加工参数”选项卡,参数设定如图9-18所示。
图9-18 曲面加工参数视窗单击“刀具的切削范围”选项中单击“选择”,选取图9-13中两个线框A为加工范围,执行。
在“平行铣削精加工参数”视窗中,点击整体误差,设置过滤比比例为1:1,整体误差为0.02mm,设置最大切削间距为0.25mm,加工角度为45。
单击“限定深度”设置最高位置为-0.01(为了不让刀具加工最高面,所以最高位置下降0.01),最低位置为-44.3348(为了不让刀具加工下面平面,所以要将最低位置往上提0.1mm)。
如图9-19所示。
图9-19 平行铣削精加工参数视窗单击“间隙设定”,在“刀具路径间隙设定”选项卡中,“容许的间隙”选择距离,位移小于容许间隙时不提刀选择平滑,勾选“切削顺序最佳化”。
如图9-21所示。
单击确定。
图9-20 刀具路径的间隙设定单击“确定”,系统计算出刀具加工路径,进行手动模拟和切削仿真。
捡视刀具路径的正确性。