PLC控制绝对位置伺服系统在转子换向器精车机中的应用
分析PLC在数控机床控制系统中的应用
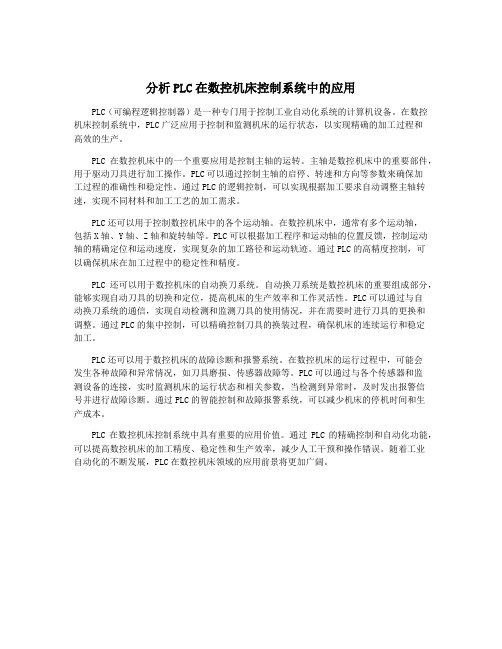
分析PLC在数控机床控制系统中的应用PLC(可编程逻辑控制器)是一种专门用于控制工业自动化系统的计算机设备。
在数控机床控制系统中,PLC广泛应用于控制和监测机床的运行状态,以实现精确的加工过程和高效的生产。
PLC在数控机床中的一个重要应用是控制主轴的运转。
主轴是数控机床中的重要部件,用于驱动刀具进行加工操作。
PLC可以通过控制主轴的启停、转速和方向等参数来确保加工过程的准确性和稳定性。
通过PLC的逻辑控制,可以实现根据加工要求自动调整主轴转速,实现不同材料和加工工艺的加工需求。
PLC还可以用于控制数控机床中的各个运动轴。
在数控机床中,通常有多个运动轴,包括X轴、Y轴、Z轴和旋转轴等。
PLC可以根据加工程序和运动轴的位置反馈,控制运动轴的精确定位和运动速度,实现复杂的加工路径和运动轨迹。
通过PLC的高精度控制,可以确保机床在加工过程中的稳定性和精度。
PLC还可以用于数控机床的自动换刀系统。
自动换刀系统是数控机床的重要组成部分,能够实现自动刀具的切换和定位,提高机床的生产效率和工作灵活性。
PLC可以通过与自动换刀系统的通信,实现自动检测和监测刀具的使用情况,并在需要时进行刀具的更换和调整。
通过PLC的集中控制,可以精确控制刀具的换装过程,确保机床的连续运行和稳定加工。
PLC还可以用于数控机床的故障诊断和报警系统。
在数控机床的运行过程中,可能会发生各种故障和异常情况,如刀具磨损、传感器故障等。
PLC可以通过与各个传感器和监测设备的连接,实时监测机床的运行状态和相关参数,当检测到异常时,及时发出报警信号并进行故障诊断。
通过PLC的智能控制和故障报警系统,可以减少机床的停机时间和生产成本。
PLC在数控机床控制系统中具有重要的应用价值。
通过PLC的精确控制和自动化功能,可以提高数控机床的加工精度、稳定性和生产效率,减少人工干预和操作错误。
随着工业自动化的不断发展,PLC在数控机床领域的应用前景将更加广阔。
伺服系统在计算机数控机床中的应用

伺服系统在计算机数控机床中的应用计算机数控机床是近年来工业制造领域的重要设备,在提高生产效率和产品质量方面发挥着关键作用。
而伺服系统作为计算机数控机床的核心组成部分之一,更是功不可没。
本文将重点探讨伺服系统在计算机数控机床中的应用,并分析其优势和发展前景。
一、伺服系统基本原理及特点伺服系统是一种控制装置,用于控制伺服电机按照预定的速度和位置运动。
它主要由伺服电机、编码器、控制器和传动装置等组成。
1. 伺服电机:伺服电机是伺服系统的动力源,通过转化电能实现机械运动。
2. 编码器:编码器用于测量伺服电机的实时位置,并将其信号反馈给控制器。
3. 控制器:控制器根据编码器的反馈信号,经过计算控制伺服电机的速度和位置。
4. 传动装置:在计算机数控机床中,传动装置主要包括滚珠丝杠和联轴器等,用于将伺服电机的运动转化为机械工具的运动。
伺服系统具有高精度、高响应速度、高稳定性和高可靠性等特点,能够满足计算机数控机床对于高精度、高速度和高自动化程度的要求。
二、伺服系统在计算机数控机床中的应用伺服系统在计算机数控机床中的应用广泛,主要集中在以下几个方面:1. 位置控制:通过编码器的反馈信号,伺服系统能够实现对机床工具的精确定位控制,确保加工件的精度和一致性。
2. 速度控制:伺服系统可以根据工艺要求,精确地控制机床工具的运动速度,保证加工件的高效率和高质量。
3. 加减速控制:伺服系统具有良好的动态响应性能,可以实现快速的加减速控制,提高机床的生产效率。
4. 转矩控制:伺服系统能够根据负载情况,实时调整伺服电机的转矩输出,保证机床工具在不同负载情况下的稳定性和可靠性。
5. 故障诊断:伺服系统配备了完善的故障检测和诊断功能,能够及时发现和定位故障,提高机床的可维护性和可靠性。
三、伺服系统的优势和发展前景伺服系统在计算机数控机床中的应用具有以下优势:1. 高精度:伺服系统能够实现微小位置调整,提高工件加工的精度和一致性。
2. 高速度:伺服系统具有很高的响应速度,使机床工具能够快速移动和转换加工动作。
分析PLC在数控机床控制系统中的应用

分析PLC在数控机床控制系统中的应用PLC(可编程逻辑控制器)是一种常用于工业控制系统中的数字化电子设备,它具有高度可编程性、可靠性和灵活性,广泛应用于自动化控制领域。
在数控机床控制系统中,PLC作为控制核心,发挥着重要作用。
本文将分析PLC在数控机床控制系统中的应用,并探讨其优势和存在的问题。
PLC在数控机床控制系统中的应用主要体现在以下几个方面:(1)控制系统核心:PLC作为数控机床的控制核心,负责接收传感器反馈的信号,进行逻辑判断和控制指令的执行。
它能够实现各种复杂的控制算法和逻辑运算,保证数控机床的精度和稳定性。
(2)运动控制:PLC可以通过专门的运动控制模块实现对数控机床各个轴的运动控制,包括位置、速度、加减速度的控制。
它可以根据预设的运动路径和参数,精确地控制数控机床各个部件的运动。
(3)人机交互:PLC可以与数控机床的人机界面(HMI)进行通信,实现对数控程序的编辑、调试和监控。
通过触摸屏或者按键输入,操作人员可以方便地对数控机床进行参数设定和运行控制。
(4)故障诊断:PLC具有灵活的故障诊断功能,可以监测系统各个部件的运行状态和信号输入输出情况,快速定位和排除故障,提高数控机床的可靠性和稳定性。
2. PLC在数控机床控制系统中的优势(1)灵活可编程:PLC可以根据数控机床的不同需求进行编程,灵活实现各种逻辑控制和运动控制功能。
它的编程语言丰富多样,包括梯形图、功能块图、指令表等,适应性强。
(2)可靠性高:PLC具有高可靠性和稳定性,能够长时间连续运行并保持稳定的控制性能。
其硬件结构简单、易于维护,适用于工业环境的恶劣条件。
(3)易于扩展和升级:PLC系统具有良好的扩展性和升级性,可以根据数控机床的需求进行功能扩展和性能升级,满足生产技术的不断发展和变化。
(4)生产效率高:PLC能够实现高速运算和快速响应,可以提高数控机床的加工效率和生产速度,实现自动化生产和大批量生产。
虽然PLC在数控机床控制系统中具有诸多优势,但也存在一些问题需要解决:(1)系统集成性差:由于PLC系统通常是由多个独立的模块组成,不同模块之间的集成性较差,存在互操作性和数据交换的问题,导致系统的整体性能受到一定影响。
浅析伺服系统在数控机床中的应用及发展
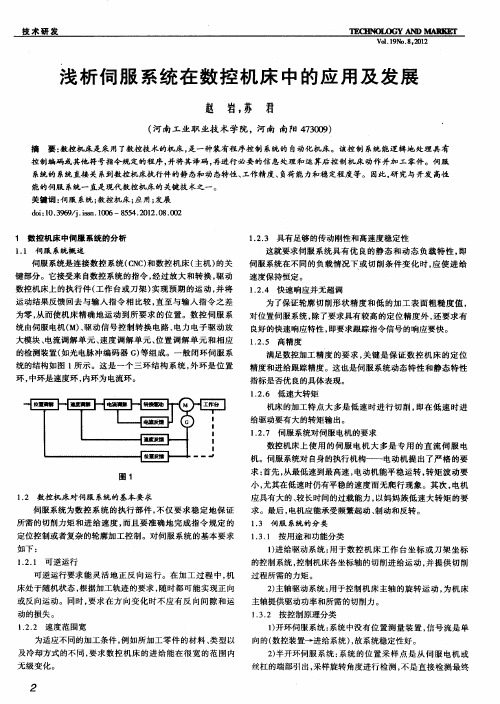
智能化
伺 服 器 控 制 模 式 的 智 能 化 , 在 内 部 预 先 编 程 如
实 现 某 种 运 动 轨 迹 , 制 本 站 点 周 边 的 1 口, 带 主 从 跟 随 控 0 内 模式调整 , 电子 凸轮 等 。
问题 , 如电刷和换 向器 易磨 损 , 护工作 量 大 , 维 成本 高等 。② 交流伺服 系统。其进 给运动系统采用 交流感应 异步伺 服 电机 和永磁 同步伺 服电机 。交流伺服系 统的优点 除 了具 有稳定性 好 、 速性 好 、 度高 的特点 外 , 快 精 与直 流伺 服 电机系 统相 比有
如下 :
13 1 按用途和功能分类 ..
1进 给驱动系 统 : ) 用于数 控机 床工 作 台坐标 或 刀架坐 标 的控制系统 , 控制机床各坐标轴 的切削进给运 动 , 并提供 切削
过 程 所 需 的力 矩 。
12 1 可 逆 运 行 ..
可逆运行要求 能灵 活地 正反 向运行 。在加工 过程 中, 机
控制编码或其他符 号指令规 定的程序 , 并将其译码 , 再进行 必要 的信 息处理和运算后控 制机床 动作 并加 工零件。伺服 系统 的 系统直接 关 系到数控机床执行件 的静 态和动 态特性 、 工作精度、 负荷 能力和稳 定程度等 。因此, 究与开发 高性 研
能 的伺 服 系统 一 直 是现 代 数 控 机 床 的 关键 技 术之 一 。 关键 词 : 服 系统 ; 控 机 床 ; 用 ; 展 伺 数 应 发 di1 .99jin 10 —85 . 1 .8 02 o:0 36/. s.0 6 542 20 .0 s 0
132 按控制原理分类 .. 1开环伺 服系统 : ) 系统 中没有 位置测 量装置 , 号流是 单 信 向的( 数控装置一 进给系统) 故系统稳定性好。 , 2 半开环伺服 系统 : ) 系统 的位 置采样 点是 从伺 服 电机 或 丝杠 的端部 引出 , 采样旋转角度进行检 测 , 不是直接 检测最 终
分析PLC在数控机床控制系统中的应用
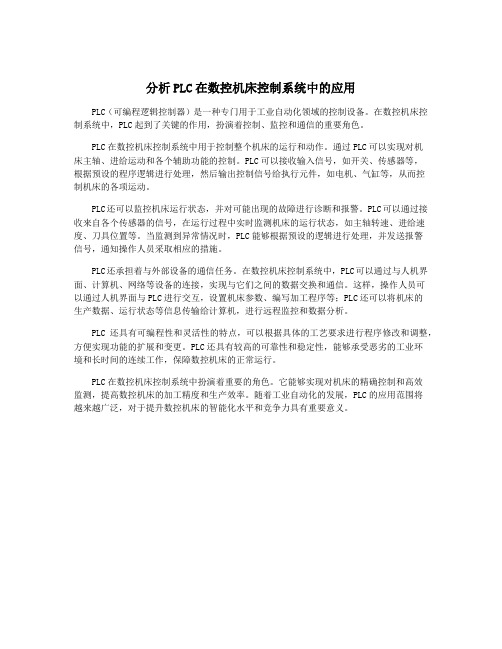
分析PLC在数控机床控制系统中的应用PLC(可编程逻辑控制器)是一种专门用于工业自动化领域的控制设备。
在数控机床控制系统中,PLC起到了关键的作用,扮演着控制、监控和通信的重要角色。
PLC在数控机床控制系统中用于控制整个机床的运行和动作。
通过PLC可以实现对机床主轴、进给运动和各个辅助功能的控制。
PLC可以接收输入信号,如开关、传感器等,根据预设的程序逻辑进行处理,然后输出控制信号给执行元件,如电机、气缸等,从而控制机床的各项运动。
PLC还可以监控机床运行状态,并对可能出现的故障进行诊断和报警。
PLC可以通过接收来自各个传感器的信号,在运行过程中实时监测机床的运行状态,如主轴转速、进给速度、刀具位置等。
当监测到异常情况时,PLC能够根据预设的逻辑进行处理,并发送报警信号,通知操作人员采取相应的措施。
PLC还承担着与外部设备的通信任务。
在数控机床控制系统中,PLC可以通过与人机界面、计算机、网络等设备的连接,实现与它们之间的数据交换和通信。
这样,操作人员可以通过人机界面与PLC进行交互,设置机床参数、编写加工程序等;PLC还可以将机床的生产数据、运行状态等信息传输给计算机,进行远程监控和数据分析。
PLC还具有可编程性和灵活性的特点,可以根据具体的工艺要求进行程序修改和调整,方便实现功能的扩展和变更。
PLC还具有较高的可靠性和稳定性,能够承受恶劣的工业环境和长时间的连续工作,保障数控机床的正常运行。
PLC在数控机床控制系统中扮演着重要的角色。
它能够实现对机床的精确控制和高效监测,提高数控机床的加工精度和生产效率。
随着工业自动化的发展,PLC的应用范围将越来越广泛,对于提升数控机床的智能化水平和竞争力具有重要意义。
PLC及伺服控制技术在精密定位控制上的运用
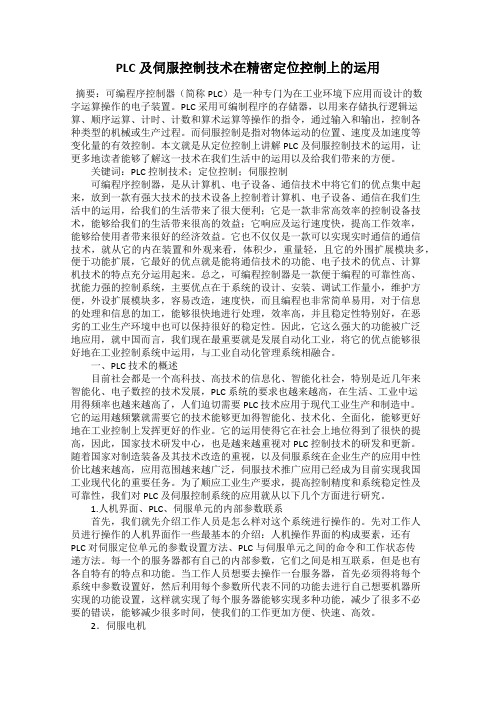
PLC及伺服控制技术在精密定位控制上的运用摘要:可编程序控制器(简称PLC)是一种专门为在工业环境下应用而设计的数字运算操作的电子装置。
PLC采用可编制程序的存储器,以用来存储执行逻辑运算、顺序运算、计时、计数和算术运算等操作的指令,通过输入和输出,控制各种类型的机械或生产过程。
而伺服控制是指对物体运动的位置、速度及加速度等变化量的有效控制。
本文就是从定位控制上讲解PLC及伺服控制技术的运用,让更多地读者能够了解这一技术在我们生活中的运用以及给我们带来的方便。
关键词:PLC控制技术;定位控制;伺服控制可编程序控制器,是从计算机、电子设备、通信技术中将它们的优点集中起来,放到一款有强大技术的技术设备上控制着计算机、电子设备、通信在我们生活中的运用,给我们的生活带来了很大便利;它是一款非常高效率的控制设备技术,能够给我们的生活带来很高的效益;它响应及运行速度快,提高工作效率,能够给使用者带来很好的经济效益。
它也不仅仅是一款可以实现实时通信的通信技术,就从它的内在装置和外观来看,体积少,重量轻,且它的外围扩展模块多,便于功能扩展,它最好的优点就是能将通信技术的功能、电子技术的优点、计算机技术的特点充分运用起来。
总之,可编程控制器是一款便于编程的可靠性高、扰能力强的控制系统,主要优点在于系统的设计、安装、调试工作量小,维护方便,外设扩展模块多,容易改造,速度快,而且编程也非常简单易用,对于信息的处理和信息的加工,能够很快地进行处理,效率高,并且稳定性特别好,在恶劣的工业生产环境中也可以保持很好的稳定性。
因此,它这么强大的功能被广泛地应用,就中国而言,我们现在最重要就是发展自动化工业,将它的优点能够很好地在工业控制系统中运用,与工业自动化管理系统相融合。
一、PLC技术的概述目前社会都是一个高科技、高技术的信息化、智能化社会,特别是近几年来智能化、电子数控的技术发展,PLC系统的要求也越来越高,在生活、工业中运用得频率也越来越高了,人们迫切需要PLC 技术应用于现代工业生产和制造中。
PLC技术在数控机床电气控制系统中的应用
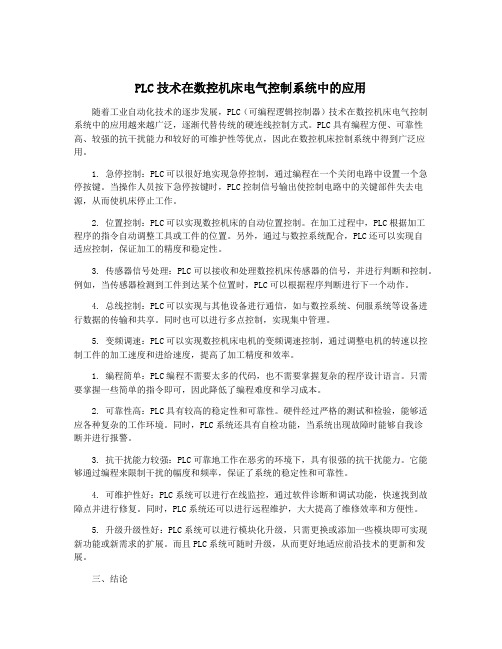
PLC技术在数控机床电气控制系统中的应用随着工业自动化技术的逐步发展,PLC(可编程逻辑控制器)技术在数控机床电气控制系统中的应用越来越广泛,逐渐代替传统的硬连线控制方式。
PLC具有编程方便、可靠性高、较强的抗干扰能力和较好的可维护性等优点,因此在数控机床控制系统中得到广泛应用。
1. 急停控制:PLC可以很好地实现急停控制,通过编程在一个关闭电路中设置一个急停按键。
当操作人员按下急停按键时,PLC控制信号输出使控制电路中的关键部件失去电源,从而使机床停止工作。
2. 位置控制:PLC可以实现数控机床的自动位置控制。
在加工过程中,PLC根据加工程序的指令自动调整工具或工件的位置。
另外,通过与数控系统配合,PLC还可以实现自适应控制,保证加工的精度和稳定性。
3. 传感器信号处理:PLC可以接收和处理数控机床传感器的信号,并进行判断和控制。
例如,当传感器检测到工件到达某个位置时,PLC可以根据程序判断进行下一个动作。
4. 总线控制:PLC可以实现与其他设备进行通信,如与数控系统、伺服系统等设备进行数据的传输和共享。
同时也可以进行多点控制,实现集中管理。
5. 变频调速:PLC可以实现数控机床电机的变频调速控制,通过调整电机的转速以控制工件的加工速度和进给速度,提高了加工精度和效率。
1. 编程简单:PLC编程不需要太多的代码,也不需要掌握复杂的程序设计语言。
只需要掌握一些简单的指令即可,因此降低了编程难度和学习成本。
2. 可靠性高:PLC具有较高的稳定性和可靠性。
硬件经过严格的测试和检验,能够适应各种复杂的工作环境。
同时,PLC系统还具有自检功能,当系统出现故障时能够自我诊断并进行报警。
3. 抗干扰能力较强:PLC可靠地工作在恶劣的环境下,具有很强的抗干扰能力。
它能够通过编程来限制干扰的幅度和频率,保证了系统的稳定性和可靠性。
4. 可维护性好:PLC系统可以进行在线监控,通过软件诊断和调试功能,快速找到故障点并进行修复。
PLC控制伺服电机应用实例
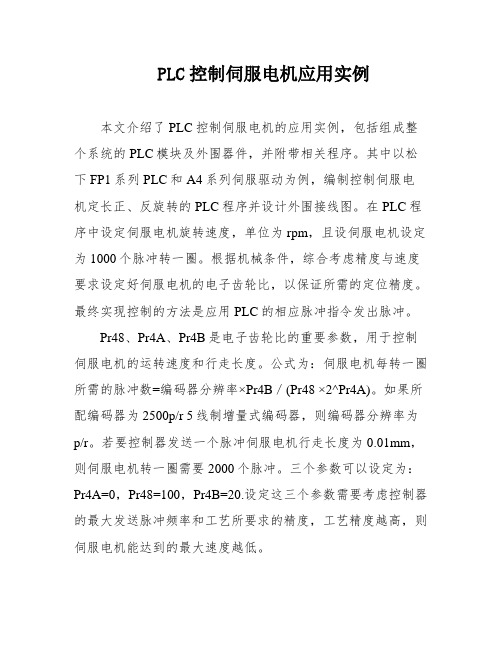
PLC控制伺服电机应用实例本文介绍了PLC控制伺服电机的应用实例,包括组成整个系统的PLC模块及外围器件,并附带相关程序。
其中以松下FP1系列PLC和A4系列伺服驱动为例,编制控制伺服电机定长正、反旋转的PLC程序并设计外围接线图。
在PLC程序中设定伺服电机旋转速度,单位为rpm,且设伺服电机设定为1000个脉冲转一圈。
根据机械条件,综合考虑精度与速度要求设定好伺服电机的电子齿轮比,以保证所需的定位精度。
最终实现控制的方法是应用PLC的相应脉冲指令发出脉冲。
Pr48、Pr4A、Pr4B是电子齿轮比的重要参数,用于控制伺服电机的运转速度和行走长度。
公式为:伺服电机每转一圈所需的脉冲数=编码器分辨率×Pr4B/(Pr48 ×2^Pr4A)。
如果所配编码器为2500p/r 5线制增量式编码器,则编码器分辨率为p/r。
若要控制器发送一个脉冲伺服电机行走长度为0.01mm,则伺服电机转一圈需要2000个脉冲。
三个参数可以设定为:Pr4A=0,Pr48=100,Pr4B=20.设定这三个参数需要考虑控制器的最大发送脉冲频率和工艺所要求的精度,工艺精度越高,则伺服电机能达到的最大速度越低。
松下FP1-40 T型PLC的程序梯型图如下:S7-200 PLC在数字伺服电机控制中的应用。
首先需要了解PLC如何控制伺服电机。
本应用实例选择的是位置控制模式,采用差动驱动方式的脉冲输入回路,方便实现对两部电机的控制。
PLC与伺服放大器的接线图如下:L+为公共PLC端子,接24VDC正端,通过控制内部晶体管的开关使得输出Q呈现不同的电平信号或发出脉冲信号。
L+一PG—P lM—L+为脉冲输入回路,PLC控制该回路中的发光二极管的亮灭,形成脉冲编码输入。
L+一NG—NP一1M—L+为电机旋转方向控制回路,当该回路的发光二极管点亮时,电机正转,否则反转。
为防止电流过大烧坏内部的发光二极管,需要外接电阻R,其阻值的计算如下:根据公式(1),可以选择R=3.9KO。
Q02 PLC控制伺服电动机系统在机床转台上的应用
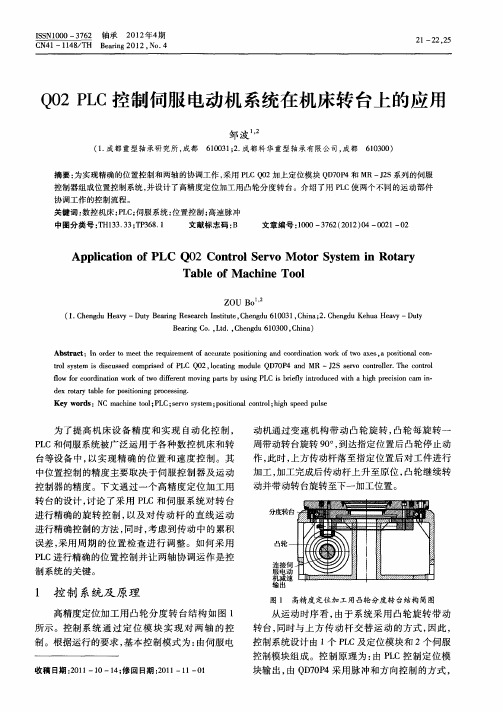
二 Z
轴承
2 1 年4 0 2 期
CN 41—1 4 / H Be rng201 , 18 T a i 2 No. 4
Q 2P C控制伺服 电动机 系统在机床转 台上 的应用 0 L
邹 波 ’
(. 1 成都重型轴承研 究所 , 成都 6 0 3 ;. 10 12 成都科华重型轴承有限公 司, 成都 60 0 ) 130
上 的感应 开 关 检 验 是 否 超 过 行 程 , 成 转 台 运 动 形
服控制器采用 M R— 2 , JS 可以使 用脉冲加方 向的 输入方式及 R 22和 R 42的通信方式。 S3 S2 由于定 位模块 Q 7 P D 0 4采 用 开环 脉 冲输 出 ( 4
轴 开路集 电极 输 出型 ) 无 法对 系 统 中 的伺 服 电动 ,
为 了提 高 机 床 设 备 精 度 和 实 现 自动 化 控 制 , P C和 伺服 系统 被 广泛 运 用 于 各种 数 控 机 床 和转 L
动机 通 过变 速 机 构 带 动 凸轮 旋 转 , 凸轮 每 旋 转 一 周带 动转 台旋 转 9 。到达 指定 位 置后 凸 轮停 止动 0, 作 , 时, 此 上方 传 动杆落 至 指 定位 置 后对 工 件进 行 加工 , 工完成 后 传动 杆 上升 至 原位 , 加 凸轮 继续 转 动并 带 动转 台旋转 至下 一加 工位 置 。
台等设备 中, 以实现精确 的位 置和速度控制。其
中位 置控 制 的精度 主要 取 决 于 伺 服控 制 器 及 运动
控制器的精度 。下文通过一个高精度定位加工用 转台的设计 , 讨论 了采用 P C和伺服 系统对转 台 L 进行精确的旋转控制 , 以及对传 动杆 的直线运动 进行精确控制的方法 , 同时 , 考虑到传动 中的累积 误差 , 采用 周 期 的 位 置 检 查 进 行 调 整 。如 何 采 用
如何采用PLC控制伺服电机的精确定位

如何采用PLC控制伺服电机的精确定位1 PLC定义PLC主要是指数字运算操作电子系统的可编程逻辑控制器,用于控制机械的生产过程。
PLC的特点是性能稳定可靠,一般由大公司如三菱,LG、台达、西门子等生产制造,质量可靠,使用寿命长,其次PLC的扩展性好,一般可通过简单方法实现多种专业的功能,如AD/DA功能,波形输出功能,PID模糊控制功能等。
PLC可采用代码编程或者梯形图编程,逻辑清楚,编程简单,适合于初学者学习和使用,因此用途广泛。
目前PLC已经在世界各地的重要控制系统中发挥了重要的作用。
大到航天航海,小到普通家用电器,都有它的身影,特别是制造工厂,更是得到了大量的使用。
2 伺服电机定义伺服电机主要靠脉冲来定位,基本上可以这样理解,伺服电机接收到1个脉冲,就会旋转1个脉冲对应的角度,从而实现位移,因为,伺服电机本身具备发出脉冲的功能,所以伺服电机每旋转一个角度,都会发出对应数量的脉冲,这样,和伺服电机接受的脉冲形成了呼应,或者叫闭环,如此一来,系统就会知道发了多少脉冲给伺服电机,同时又收了多少脉冲回来,这样,就能够很精确的控制电机的转动,从而实现精确的定位,可以达到0.001mm。
伺服电机在要求精密控制的工业自动化设备中得到了广泛的应用,他的闭环控制功能,是步进电机无法比拟的。
在一些场合,由于步进电机没有反馈,因此当步进电机卡死或打滑会出现丢步的情况,从而大大影响设备使用精度,因此步进电机一般用于纯粹的转动过程,或者用于对精度要求不高的使用场合。
3 如何采用PLC控制伺服电机运转文中采用了LG品牌PLC,伺服电机采用英迈克的伺服电机及驱动器。
3.1 PLC控制伺服电机原理图PLC控制伺服电机原理如图1所示。
①PLC引脚说明。
PLC引脚P00为电机运行启动信号;PLC引脚P40属于LG PLC的专用高速脉冲通道,用于控制伺服电机驱动器。
P41属于LG PLC专用方向脉冲通道;P属于高速脉冲通道的专用高电平端,当高速脉冲通道为低电平时,电流从P流向高速脉冲通道,从而伺服电机收到高速脉冲,并执行相关控制,如转动和换向。
PLC技术在数控机床电气控制系统中的应用
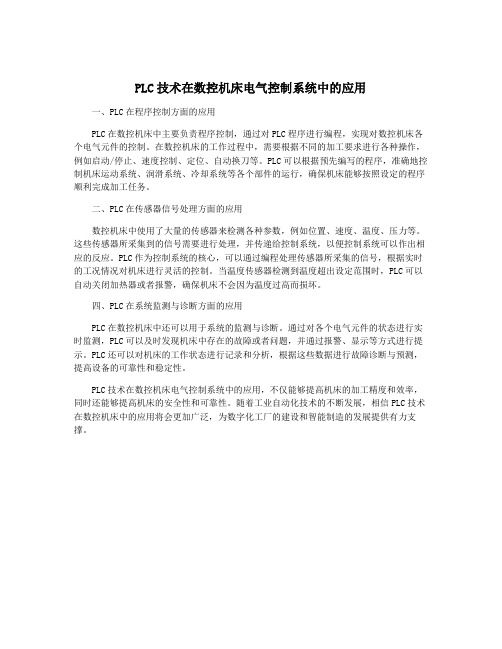
PLC技术在数控机床电气控制系统中的应用
一、PLC在程序控制方面的应用
PLC在数控机床中主要负责程序控制,通过对PLC程序进行编程,实现对数控机床各个电气元件的控制。
在数控机床的工作过程中,需要根据不同的加工要求进行各种操作,例如启动/停止、速度控制、定位、自动换刀等。
PLC可以根据预先编写的程序,准确地控制机床运动系统、润滑系统、冷却系统等各个部件的运行,确保机床能够按照设定的程序顺利完成加工任务。
二、PLC在传感器信号处理方面的应用
数控机床中使用了大量的传感器来检测各种参数,例如位置、速度、温度、压力等。
这些传感器所采集到的信号需要进行处理,并传递给控制系统,以便控制系统可以作出相应的反应。
PLC作为控制系统的核心,可以通过编程处理传感器所采集的信号,根据实时的工况情况对机床进行灵活的控制。
当温度传感器检测到温度超出设定范围时,PLC可以自动关闭加热器或者报警,确保机床不会因为温度过高而损坏。
四、PLC在系统监测与诊断方面的应用
PLC在数控机床中还可以用于系统的监测与诊断。
通过对各个电气元件的状态进行实时监测,PLC可以及时发现机床中存在的故障或者问题,并通过报警、显示等方式进行提示。
PLC还可以对机床的工作状态进行记录和分析,根据这些数据进行故障诊断与预测,提高设备的可靠性和稳定性。
PLC技术在数控机床电气控制系统中的应用,不仅能够提高机床的加工精度和效率,同时还能够提高机床的安全性和可靠性。
随着工业自动化技术的不断发展,相信PLC技术在数控机床中的应用将会更加广泛,为数字化工厂的建设和智能制造的发展提供有力支撑。
伺服系统在数控车床中的应用

伺服系统在数控车床中的应用伺服系统在机床行业领域的应用已经非常广泛因此伺服系统和机床的关系已经非常紧密。
作为数控机床的重要功能部件,伺服系统是影响系统加工性能的重要指标。
随着数控机床的发展,伺服控制系统在机床行业的应用也在不断完善,其之间的配合犹如一对老朋友,越来越默契了。
卧式数控机床由CNC控制器,伺服驱动及电机、电器柜和数控机床的机架四部分组成。
其工作原理是:通过CNC内配置的专用编程软件,将加工零件的的轨迹用坐标的方式表达出来,把这些信息转化成能使驱动伺服电机的带有功率的信号(脉冲串),控制伺服电机带动相应轴来实现运动轨迹。
同时,刀架上配有数控车刀,通过按加工材质配置相应的刀具,对固定于主轴上的加工材料进行切削,即可加工出相应的工件。
在数控机床上,伺服调控系统是其不可缺少的一部分。
其任务是把数控信息转化为机床进给运动,从而实现精准控制。
由于数控机床对产品加工时要求高,所以采用的伺服控制系统十分关键。
目前在数控机床上使用的伺服控制系统,其优点主要有:精度高,伺服系统的精度是指输出量能复现输入量的精确程度。
包括定位精度和轮廓加工精度;稳定性好,稳定是指系统在给定输入或外界干扰作用下,能在短暂的调节过程后,达到新的或者恢复到原来的平衡状态。
直接影响数控加工的精度和表面粗糙度;快速响应,快速响应是伺服系统动态品质的重要指标,它反映了系统的跟踪精度;调速范围宽,其调速范围可达0—30m/min;低速大转矩,进给坐标的伺服控制属于恒转矩控制,在整个速度范围内都要保持这个转矩,主轴坐标的伺服控制在低速时为恒转矩控制,能提供较大转矩,在高速时为恒功率控制,具有足够大的输出功率。
在机床进给伺服中采用的主要是永磁同步交流伺服系统,有三种类型:模拟形式、数字形式和软件形式。
模拟伺服用途单一,只接收模拟信号,位置控制通常由上位机实现。
数字伺服可实现一机多用,如做速度、力矩、位置控制。
可接收模拟指令和脉冲指令,各种参数均以数字方式设定,稳定性好。
浅析PLC对伺服电机的精确定位控制
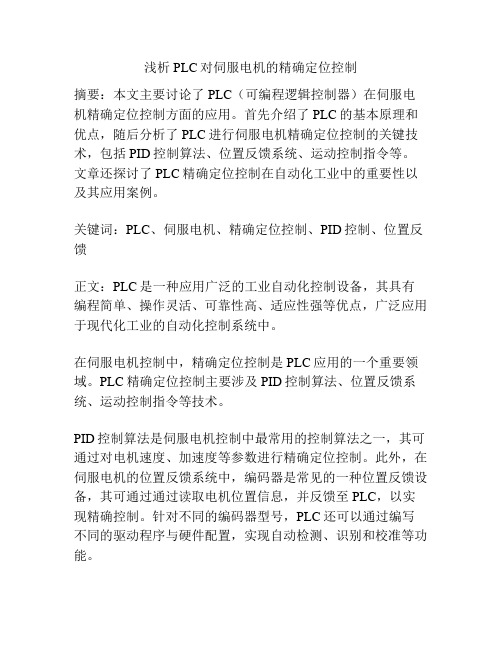
浅析PLC对伺服电机的精确定位控制摘要:本文主要讨论了PLC(可编程逻辑控制器)在伺服电机精确定位控制方面的应用。
首先介绍了PLC的基本原理和优点,随后分析了PLC进行伺服电机精确定位控制的关键技术,包括PID控制算法、位置反馈系统、运动控制指令等。
文章还探讨了PLC精确定位控制在自动化工业中的重要性以及其应用案例。
关键词:PLC、伺服电机、精确定位控制、PID控制、位置反馈正文:PLC是一种应用广泛的工业自动化控制设备,其具有编程简单、操作灵活、可靠性高、适应性强等优点,广泛应用于现代化工业的自动化控制系统中。
在伺服电机控制中,精确定位控制是PLC应用的一个重要领域。
PLC精确定位控制主要涉及PID控制算法、位置反馈系统、运动控制指令等技术。
PID控制算法是伺服电机控制中最常用的控制算法之一,其可通过对电机速度、加速度等参数进行精确定位控制。
此外,在伺服电机的位置反馈系统中,编码器是常见的一种位置反馈设备,其可通过通过读取电机位置信息,并反馈至PLC,以实现精确控制。
针对不同的编码器型号,PLC还可以通过编写不同的驱动程序与硬件配置,实现自动检测、识别和校准等功能。
运动控制指令是PLC在对伺服电机进行精确定位控制时所必须具备的能力之一。
运动控制指令通常包括“加减速”,“定时触发”和“位置比较”等多种指令,通过对不同的指令进行组合,可实现对伺服电机的多种控制需求。
除此之外,PLC在自动化工业中精确定位控制方面也具有广泛的应用。
例如,在机械加工领域中,PLC控制伺服电机的精确定位,可将零件的加工精度提高到毫米级。
总而言之,PLC在伺服电机精确定位控制方面应用广泛,其优越的控制能力和广泛的应用领域在当今自动化工业中具有重要地位。
同时,PLC精确定位控制还可以应用在物流自动化、制造业自动化、冶炼等领域,实现对各种设备的精准控制。
通过PLC的精确控制,制造业可以实现更高质量的生产,提升生产效率,并极大地降低生产成本。
伺服系统在数控加工中的应用

伺服系统在数控加工中的应用伺服系统是一种能够控制运动精度和速度的自动控制系统,它在数控加工中起着至关重要的作用。
在传统的机械加工中,人工操作存在着诸多弊端,如操作不稳定、难以精确控制等。
而伺服系统的引入,不仅提高了加工的精度和效率,还使整个数控加工过程更加便捷和智能化。
一、伺服系统的基本原理伺服系统通过控制电机实现工具的精确位置控制。
其基本原理如下:首先,传感器接收到被加工材料的位置反馈信号,并将其转换为电信号,然后信号经过放大和处理后驱动电机,使工具实现所需的运动。
同时,控制器会不断地监测和校准位置反馈信号,并对电机进行调整,以保持准确的位置控制。
二、伺服系统在数控加工中的优势1.提高加工精度:伺服系统能够实现高精度的位置控制,可以做到微米级的精度要求,使得加工件的尺寸和形状更加准确。
2.提高加工效率:伺服系统的快速响应特性能够实现高速切削,使得加工时间大大缩短,提高了生产效率。
3.减少人为误差:伺服系统通过自动控制,减少了人工操作的干预,降低了因人为误差而导致的加工不稳定性。
4.灵活性和多功能性:伺服系统可以根据加工要求进行不同的运动控制,包括直线运动、曲线运动和旋转运动,从而实现多种复杂工艺的加工。
5.自动化程度高:伺服系统可以与数控系统相结合,实现加工过程的自动化控制,从而提高生产的智能化水平。
三、伺服系统的应用领域伺服系统在数控加工中有着广泛的应用,以下列举几个典型的应用领域:1.数控车床:伺服系统可控制车床刀架和工件的移动,实现高精度的车削加工。
2.数控铣床:伺服系统可控制铣床刀具的位置和转速,实现复杂轮廓的铣削加工。
3.数控磨床:伺服系统可控制磨床磨轮的位置和转速,实现高精度的磨削加工。
4.数控钻床:伺服系统可控制钻床主轴的位置和转速,实现高精度的钻削加工。
5.数控激光切割机:伺服系统可控制激光切割机械手臂的位置和速度,实现高精度的切割加工。
总之,伺服系统在数控加工中的应用极大地提高了加工的精度和效率,使加工过程更加智能化和自动化。
分析PLC在数控机床控制系统中的应用

分析PLC在数控机床控制系统中的应用PLC(可编程逻辑控制器)在数控机床控制系统中广泛应用,主要用于控制机床的各种运动、操作和监测功能。
以下是对PLC在数控机床控制系统中应用的分析。
PLC可以实现数控机床的运动控制。
通过PLC的控制软件编程,可以精确控制机床的各种运动轴,如X轴、Y轴和Z轴等。
PLC可以实时监测机床的位置、速度和加速度等参数,并根据需要进行调整和控制。
这样可以确保机床加工工件的准确性和精度,提高生产效率。
PLC可以实现数控机床的操作控制。
通过PLC的人机界面,操作人员可以方便地对机床进行操作和控制。
PLC可以实现自动化操作,如自动上料、自动下料、自动换刀等功能。
PLC还可以实现故障诊断和报警功能,当机床出现异常情况时,PLC会及时发出警报并采取相应的措施。
PLC可以实现数控机床的监测功能。
通过PLC的输入输出模块,可以实时获取机床的各种状态信息,如温度、压力、电流等。
PLC可以对这些参数进行监测和记录,并在需要时进行报警或自动控制。
这样可以提前预防机床故障,并进行维护和保养,延长机床的使用寿命。
PLC还可以与其他设备进行通信,如传感器、执行器和上位机等。
通过与这些设备的连接,可以实现更加复杂和高级的控制功能。
可以通过PLC与传感器的连接,实现机床的自动感知和反馈控制;通过PLC与上位机的连接,实现机床的远程监控和控制。
PLC在数控机床控制系统中的应用非常广泛,主要集中在运动控制、操作控制和监测功能等方面。
PLC的使用可以提高机床加工效率和精度,降低故障率,增强机床的稳定性和可靠性。
PLC还可以与其他设备进行通信,实现更加智能化和自动化的机床控制系统。
随着技术的不断进步和发展,PLC在数控机床控制领域的应用前景将更加广阔。
伺服系统在数控机床上的应用
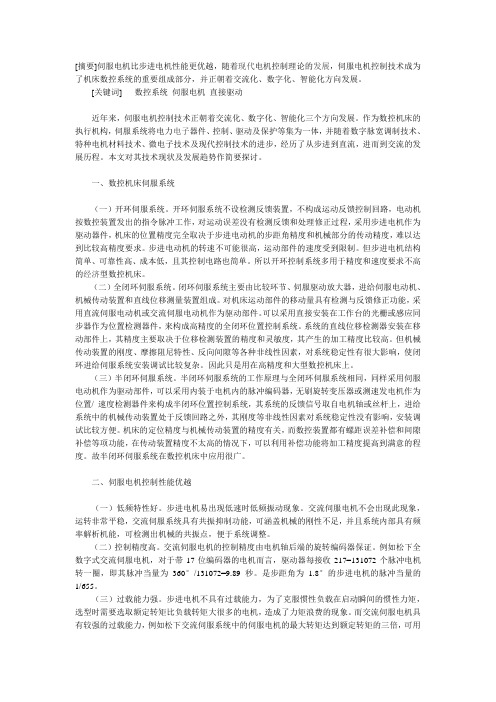
[摘要]伺服电机比步进电机性能更优越,随着现代电机控制理论的发展,伺服电机控制技术成为了机床数控系统的重要组成部分,并正朝着交流化、数字化、智能化方向发展。
[关键词] 数控系统伺服电机直接驱动近年来,伺服电机控制技术正朝着交流化、数字化、智能化三个方向发展。
作为数控机床的执行机构,伺服系统将电力电子器件、控制、驱动及保护等集为一体,并随着数字脉宽调制技术、特种电机材料技术、微电子技术及现代控制技术的进步,经历了从步进到直流,进而到交流的发展历程。
本文对其技术现状及发展趋势作简要探讨。
一、数控机床伺服系统(一)开环伺服系统。
开环伺服系统不设检测反馈装置,不构成运动反馈控制回路,电动机按数控装置发出的指令脉冲工作,对运动误差没有检测反馈和处理修正过程,采用步进电机作为驱动器件,机床的位置精度完全取决于步进电动机的步距角精度和机械部分的传动精度,难以达到比较高精度要求。
步进电动机的转速不可能很高,运动部件的速度受到限制。
但步进电机结构简单、可靠性高、成本低,且其控制电路也简单。
所以开环控制系统多用于精度和速度要求不高的经济型数控机床。
(二)全闭环伺服系统。
闭环伺服系统主要由比较环节、伺服驱动放大器,进给伺服电动机、机械传动装置和直线位移测量装置组成。
对机床运动部件的移动量具有检测与反馈修正功能,采用直流伺服电动机或交流伺服电动机作为驱动部件。
可以采用直接安装在工作台的光栅或感应同步器作为位置检测器件,来构成高精度的全闭环位置控制系统。
系统的直线位移检测器安装在移动部件上,其精度主要取决于位移检测装置的精度和灵敏度,其产生的加工精度比较高。
但机械传动装置的刚度、摩擦阻尼特性、反向间隙等各种非线性因素,对系统稳定性有很大影响,使闭环进给伺服系统安装调试比较复杂。
因此只是用在高精度和大型数控机床上。
(三)半闭环伺服系统。
半闭环伺服系统的工作原理与全闭环伺服系统相同,同样采用伺服电动机作为驱动部件,可以采用内装于电机内的脉冲编码器,无刷旋转变压器或测速发电机作为位置/ 速度检测器件来构成半闭环位置控制系统,其系统的反馈信号取自电机轴或丝杆上,进给系统中的机械传动装置处于反馈回路之外,其刚度等非线性因素对系统稳定性没有影响,安装调试比较方便。
伺服系统应用于哪儿_伺服系统应用实例

伺服系统应用于哪儿_伺服系统应用实例伺服系统(servomechanism)又称随动系统,是用来精确地跟随或复现某个过程的反馈控制系统。
伺服系统使物体的位置、方位、状态等输出被控量能够跟随输入目标(或给定值)的任意变化的自动控制系统。
它的主要任务是按控制命令的要求、对功率进行放大、变换与调控等处理,使驱动装置输出的力矩、速度和位置控制非常灵活方便。
本文首先介绍了伺服系统的组成,其次介绍了伺服系统的特点、作用及分类,最后阐述了伺服系统应用领域、应用趋势及实例,具体的跟随小编一起来了解一下。
伺服系统组成系统主要由触摸屏、PLC、伺服驱动器、永磁同步伺服电机组成,其中伺服电机是运动的执行机构,对其进行位置、速度和电流三环控制,从而达到用户的功能要求。
伺服系统的特点、作用及分类特点1、精确的检测装置:以组成速度和位置闭环控制;2、有多种反馈比较原理与方法:根据检测装置实现信息反馈的原理不同,伺服系统反馈比较的方法也不相同。
常用的有脉冲比较、相位比较和幅值比较3种;3、高性能的伺服电动机(简称伺服电机):用于高效和复杂型面加工的数控机床,伺服系统将经常处于频繁的启动和制动过程中。
要求电机的输出力矩与转动惯量的比值大,以产生足够大的加速或制动力矩。
要求伺服电机在低速时有足够大的输出力矩且运转平稳,以便在与机械运动部分连接中尽量减少中间环节;4、宽调速范围的速度调节系统,即速度伺服系统:从系统的控制结构看,数控机床的位置闭环系统可看作是位置调节为外环、速度调节为内环的双闭环自动控制系统,其内部的实际工作过程是把位置控制输入转换成相应的速度给定信号后,再通过调速系统驱动伺服电机,实现实际位移。
数控机床的主运动要求调速性能也比较高,因此要求伺服系统为高性能的宽调速系统。
主要作用1、以小功率指令信号去控制大功率负载;2、在没有机械连接的情况下,由输入轴控制位于远处的输出轴,实现远距同步传动;3、使输出机械位移精确地跟踪电信号,如记录和指示仪表等。
PLC控制绝对位置伺服系统在转子换向器精车机中的应用
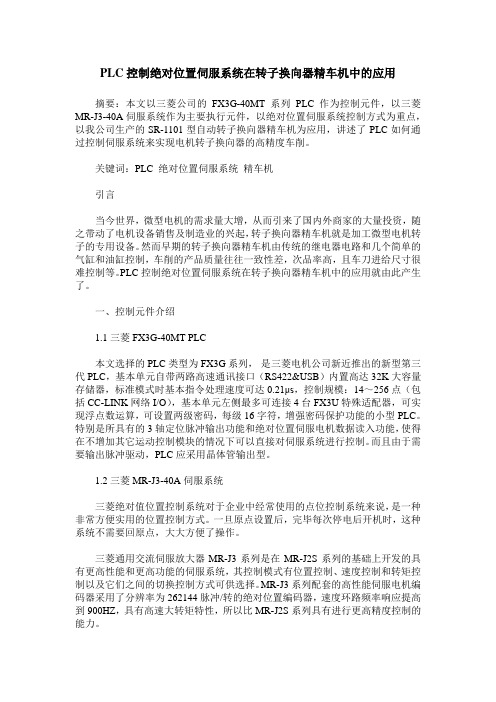
PLC控制绝对位置伺服系统在转子换向器精车机中的应用摘要:本文以三菱公司的FX3G-40MT系列PLC作为控制元件,以三菱MR-J3-40A伺服系统作为主要执行元件,以绝对位置伺服系统控制方式为重点,以我公司生产的SR-1101型自动转子换向器精车机为应用,讲述了PLC如何通过控制伺服系统来实现电机转子换向器的高精度车削。
关键词:PLC 绝对位置伺服系统精车机引言当今世界,微型电机的需求量大增,从而引来了国内外商家的大量投资,随之带动了电机设备销售及制造业的兴起,转子换向器精车机就是加工微型电机转子的专用设备。
然而早期的转子换向器精车机由传统的继电器电路和几个简单的气缸和油缸控制,车削的产品质量往往一致性差,次品率高,且车刀进给尺寸很难控制等。
PLC控制绝对位置伺服系统在转子换向器精车机中的应用就由此产生了。
一、控制元件介绍1.1三菱FX3G-40MT PLC本文选择的PLC类型为FX3G系列,是三菱电机公司新近推出的新型第三代PLC,基本单元自带两路高速通讯接口(RS422&USB)内置高达32K大容量存储器,标准模式时基本指令处理速度可达0.21μs,控制规模:14~256点(包括CC-LINK网络I/O),基本单元左侧最多可连接4台FX3U特殊适配器,可实现浮点数运算,可设置两级密码,每级16字符,增强密码保护功能的小型PLC。
特别是所具有的3轴定位脉冲输出功能和绝对位置伺服电机数据读入功能,使得在不增加其它运动控制模块的情况下可以直接对伺服系统进行控制。
而且由于需要输出脉冲驱动,PLC应采用晶体管输出型。
1.2三菱MR-J3-40A伺服系统三菱绝对值位置控制系统对于企业中经常使用的点位控制系统来说,是一种非常方便实用的位置控制方式。
一旦原点设置后,完毕每次停电后开机时,这种系统不需要回原点,大大方便了操作。
三菱通用交流伺服放大器MR-J3系列是在MR-J2S系列的基础上开发的具有更高性能和更高功能的伺服系统,其控制模式有位置控制、速度控制和转矩控制以及它们之间的切换控制方式可供选择。
- 1、下载文档前请自行甄别文档内容的完整性,平台不提供额外的编辑、内容补充、找答案等附加服务。
- 2、"仅部分预览"的文档,不可在线预览部分如存在完整性等问题,可反馈申请退款(可完整预览的文档不适用该条件!)。
- 3、如文档侵犯您的权益,请联系客服反馈,我们会尽快为您处理(人工客服工作时间:9:00-18:30)。
PLC控制绝对位置伺服系统在转子换向器精车机中的应用
摘要:本文以三菱公司的FX3G-40MT系列PLC作为控制元件,以三菱MR-J3-40A伺服系统作为主要执行元件,以绝对位置伺服系统控制方式为重点,以我公司生产的SR-1101型自动转子换向器精车机为应用,讲述了PLC如何通过控制伺服系统来实现电机转子换向器的高精度车削。
关键词:PLC 绝对位置伺服系统精车机
引言
当今世界,微型电机的需求量大增,从而引来了国内外商家的大量投资,随之带动了电机设备销售及制造业的兴起,转子换向器精车机就是加工微型电机转子的专用设备。
然而早期的转子换向器精车机由传统的继电器电路和几个简单的气缸和油缸控制,车削的产品质量往往一致性差,次品率高,且车刀进给尺寸很难控制等。
PLC控制绝对位置伺服系统在转子换向器精车机中的应用就由此产生了。
一、控制元件介绍
1.1三菱FX3G-40MT PLC
本文选择的PLC类型为FX3G系列,是三菱电机公司新近推出的新型第三代PLC,基本单元自带两路高速通讯接口(RS422&USB)内置高达32K大容量存储器,标准模式时基本指令处理速度可达0.21μs,控制规模:14~256点(包括CC-LINK网络I/O),基本单元左侧最多可连接4台FX3U特殊适配器,可实现浮点数运算,可设置两级密码,每级16字符,增强密码保护功能的小型PLC。
特别是所具有的3轴定位脉冲输出功能和绝对位置伺服电机数据读入功能,使得在不增加其它运动控制模块的情况下可以直接对伺服系统进行控制。
而且由于需要输出脉冲驱动,PLC应采用晶体管输出型。
1.2三菱MR-J3-40A伺服系统
三菱绝对值位置控制系统对于企业中经常使用的点位控制系统来说,是一种非常方便实用的位置控制方式。
一旦原点设置后,完毕每次停电后开机时,这种系统不需要回原点,大大方便了操作。
三菱通用交流伺服放大器MR-J3系列是在MR-J2S系列的基础上开发的具有更高性能和更高功能的伺服系统,其控制模式有位置控制、速度控制和转矩控制以及它们之间的切换控制方式可供选择。
MR-J3系列配套的高性能伺服电机编码器采用了分辨率为262144脉冲/转的绝对位置编码器,速度环路频率响应提高到900HZ,具有高速大转矩特性,所以比MR-J2S系列具有进行更高精度控制的能力。
二、转子换向器精车机介绍及机器工作过程
转子换向器精车机是用来车削电机转子换向器表面的专用设备,其车削的目的主要为保证转子换向器表面的位置尺寸、圆度、和粗糙度。
以下以图1为例,介绍转子换向器精车机的工作过程:
1)打开电源,各控制元件复位后,J3绝对位置伺服电机进行编码器绝对位置数据读取,完成后按下控制装置启动按钮,皮带臂上下气缸下降,到达限定位置后SQ2接通,皮带带动转子旋转。
2)J3绝对位置伺服电机旋转带动刀具前进,到位后切削气缸由右向左对转子换向器进行轴行切削,到达限定位置后SQ4接通。
3)J3绝对位置伺服电机旋转带动刀具后退,到位后皮带停止旋转,切削气缸退回到限定位置后SQ3接通。
4)绝对位置编码器数据读取,皮带譬上下气缸上升到限定位置后SQ1接通。
整机动作完成,进入下一个循环。
三、PLC的I/O使用情况和绝对位置伺服系统控制方法
1)PLC的输入控制:输入控制采用漏型控制,X0-X4自定义为绝对位置伺服系统输出信号。
X5-X12自定义为普通IN控制点,连接无电源触点,或内置式串联二极管的磁性开关等。
在使用串联二极管的磁性开关时不能串联2个以上开关。
2)PLC的输出控制:输出控制也采用漏型控制,Y0-Y7自定义为绝对位置伺服系统输入信号。
Y10-Y13自定义为普通输出点,用于控制中间继电器、电磁阀等。
负载电流大于0.5A时需要使用中间继电器或PLC输出放大板等方式进行中转。
在使用感性或电阻负载时需要在每个触点增加相应大小的熔断器(保护输出晶体管免受过载、短路等损坏)。
3)绝对位置伺服系统的控制:精车机在工作中对进刀位置控制要求非常高,所以本机控制方式采用位置控制。
脉冲输入方式使用集电极开路方式。
指令脉冲串控制方式为:负逻辑脉冲串+符号。
连接伺服电机的丝杆导程为5mm,伺服电机旋转一转所需的指令输入脉冲数为5000/转,即实际刀具前进分辩率为0.001mm/脉冲,不使用正反转行程限制。
四、主要程序介绍
1)绝对位置数据读取程序介绍:
M100为数据读取DABS指令的驱动软元件,在M100为初始常闭状态时驱
动DABS指令,伺服ON(Y4)和ABS传送模式输出(Y5),通过接收传输数据准备完毕信号(X2)和发送ABS请求信号,可一边确认相互的收发信,一边进行32+6位的数据通信。
数据是通过bit0(x0)和bit1(x1)的2位的回路进行的。
ABS数据读出结束时,执行结束标志位M8029接通,读取完成标志M1接通。
读取的数据保存到D8340(低位)D8341(高位)寄存器内。
指令驱动后5秒内未接收到数据读取完成标志(M1)接通,则读取超时软元件(T10)接通,精车机报警。
2)位置控制程序介绍:
M120为绝对位置控制DDRV A指令的驱动软元件,在M120接通后驱动DDRV A指令,脉冲口(Y0)发送相应脉冲数,发送的脉冲数值为(D8340-D200),D202为脉冲发送的频率,单位为Hz,方向信号(Y3),会根据(D8340-D200)值自动切换状态。
当脉冲发送完成后,执行结束标志位M8029接通,定位完成标志M2接通,驱动软元件M120复位,精车机的刀具定位完成。
五、结束语
SR-1101型自动转子换向器精车机采用本系统后,换向器车削的圆度和粗糙度有了质的提高,初次对刀时间也大大缩短,产品的一致辞性也非常好。
有望在今后的相应设备中得到广范应用。
由于篇幅原因,本文只对这个系统作了简要的介绍,详细控制过程请参考三菱电机的相应手册。