SMT标准
smt行业标准 资料

smt行业标准资料随着科技的飞速发展,电子产品在我们的生活中扮演着越来越重要的角色。
而SMT(表面贴装技术)作为电子制造业中的重要环节,对于电子产品的制造质量起着决定性的作用。
然而,由于SMT行业的发展较为迅速,各企业对于质量的理解和标准的制定并不统一,这给行业带来了一定的困扰。
因此,制定SMT行业标准是十分必要的。
一、什么是SMT行业标准?SMT行业标准是指在SMT生产过程中所应遵循的一系列技术规范和质量要求。
这些标准旨在确保产品能够达到预期的标准要求,同时提高产品的一致性和可靠性。
二、为什么需要SMT行业标准?1. 保证产品质量:SMT行业标准可以为制造商提供一个明确的准则,帮助他们在产品制造的每一个环节中遵循标准操作流程,确保产品的质量合格。
2. 提高生产效率:标准化的操作流程能够提高生产效率,减少因操作不规范而导致的延误和错误。
3. 降低成本:合理的工艺要求和标准操作可以避免浪费和返工,降低生产成本。
4. 促进行业交流和合作:通过制定统一的标准,不同企业之间可以更好地进行协作和交流,推动整个行业的发展。
制定SMT行业标准需要依靠专业知识和技术经验的积累,并结合行业的实际需求。
标准的制定过程通常包括以下几个环节:1. 调研和分析:了解当前行业的发展状况和存在的问题,收集相关资料和数据,进行分析和比较。
2. 制定标准:根据调研结果和行业需求,制定相应的标准,明确技术规范和质量要求。
3. 审查和修订:标准的制定是一个不断完善和修订的过程,需要不断收集用户的反馈和参考其他国内外标准,进行审查和修订。
4. 推广和应用:制定好的标准需要通过各种途径进行推广和应用,包括行业协会、专业培训和技术交流会议等。
SMT行业标准的应用可以从以下几个方面展开:1. 设备选型:根据标准的设备参数要求,选择适合自己生产流程的设备,确保设备的性能和稳定性。
2. 工艺参数设置:根据标准的工艺要求,进行工艺参数的设定和调整,确保生产过程的稳定性和一致性。
smt外观检验标准
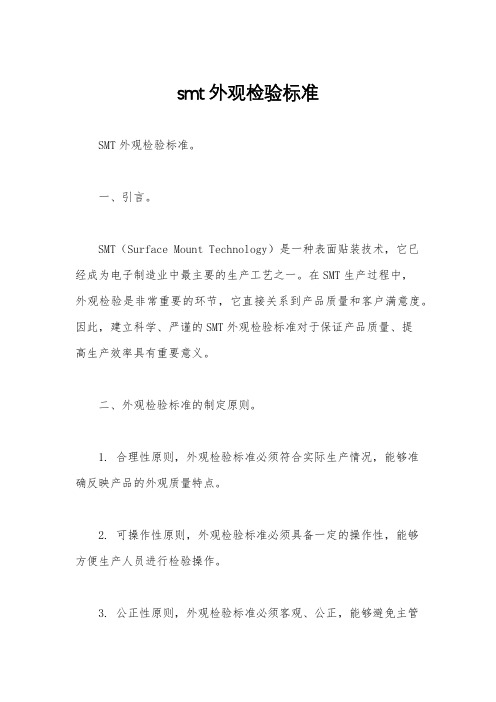
smt外观检验标准SMT外观检验标准。
一、引言。
SMT(Surface Mount Technology)是一种表面贴装技术,它已经成为电子制造业中最主要的生产工艺之一。
在SMT生产过程中,外观检验是非常重要的环节,它直接关系到产品质量和客户满意度。
因此,建立科学、严谨的SMT外观检验标准对于保证产品质量、提高生产效率具有重要意义。
二、外观检验标准的制定原则。
1. 合理性原则,外观检验标准必须符合实际生产情况,能够准确反映产品的外观质量特点。
2. 可操作性原则,外观检验标准必须具备一定的操作性,能够方便生产人员进行检验操作。
3. 公正性原则,外观检验标准必须客观、公正,能够避免主管人员的主观因素对检验结果的影响。
4. 统一性原则,外观检验标准必须统一于相关国家标准或行业标准,以确保产品质量符合法律法规的要求。
三、SMT外观检验标准的内容。
1. 焊接质量,检查焊点的焊接是否均匀、牢固,是否有焊接飞溅、焊接虚焊等现象。
2. 组件安装质量,检查元件的安装位置、方向是否正确,是否存在错装、漏装等问题。
3. 表面质量,检查PCB板表面是否有划痕、氧化、污渍等影响外观的缺陷。
4. 封装质量,检查封装件的外观是否完整,是否存在破损、变形等情况。
5. 标识质量,检查产品标识的清晰度、完整度,是否存在模糊、缺失等问题。
6. 清洁度,检查产品表面的清洁度,是否存在灰尘、油污等影响外观的因素。
四、SMT外观检验标准的执行流程。
1. 定期培训,定期对生产人员进行外观检验标准的培训,提高他们的外观质量判断能力。
2. 抽检制度,建立抽检制度,对生产线上的产品进行定期抽检,确保产品外观质量符合标准要求。
3. 记录管理,对外观检验结果进行详细记录,建立台账,以便追溯和分析问题原因。
4. 反馈改进,对发现的外观质量问题及时反馈给生产部门,并协助他们进行改进措施。
五、SMT外观检验标准的意义。
1. 保证产品质量,建立科学的外观检验标准,能够及时发现产品外观质量问题,保证产品质量符合客户要求。
SMT工艺标准
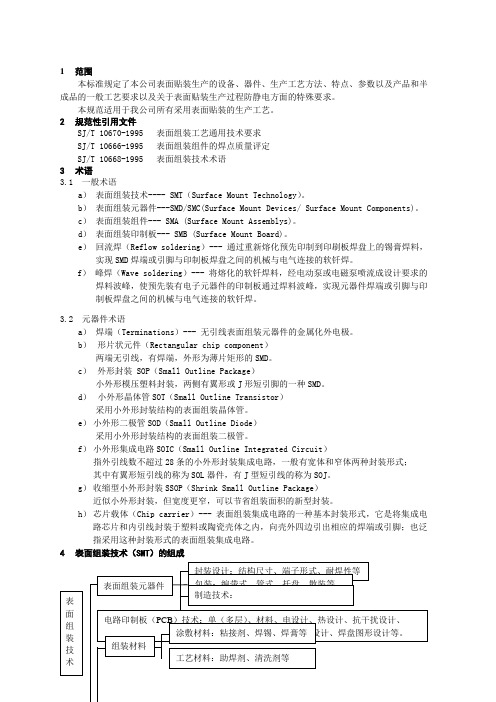
1范围本标准规定了本公司表面贴装生产的设备、器件、生产工艺方法、特点、参数以及产品和半成品的一般工艺要求以及关于表面贴装生产过程防静电方面的特殊要求。
本规范适用于我公司所有采用表面贴装的生产工艺。
2规范性引用文件SJ/T 10670-1995 表面组装工艺通用技术要求SJ/T 10666-1995 表面组装组件的焊点质量评定SJ/T 10668-1995 表面组装技术术语3术语3.1 一般术语a)表面组装技术---- SMT(Surface Mount Technology)。
b)表面组装元器件---SMD/SMC(Surface Mount Devices/ Surface Mount Components)。
c)表面组装组件--- SMA (Surface Mount Assemblys)。
d)表面组装印制板--- SMB (Surface Mount Board)。
e)回流焊(Reflow soldering)--- 通过重新熔化预先印制到印刷板焊盘上的锡膏焊料,实现SMD焊端或引脚与印制板焊盘之间的机械与电气连接的软钎焊。
f)峰焊(Wave soldering)--- 将熔化的软钎焊料,经电动泵或电磁泵喷流成设计要求的焊料波峰,使预先装有电子元器件的印制板通过焊料波峰,实现元器件焊端或引脚与印制板焊盘之间的机械与电气连接的软钎焊。
3.2 元器件术语a)焊端(Terminations)--- 无引线表面组装元器件的金属化外电极。
b)形片状元件(Rectangular chip component)两端无引线,有焊端,外形为薄片矩形的SMD。
c)外形封装 SOP(Small Outline Package)小外形模压塑料封装,两侧有翼形或J形短引脚的一种SMD。
d)小外形晶体管SOT(Small Outline Transistor)采用小外形封装结构的表面组装晶体管。
e)小外形二极管SOD(Small Outline Diode)采用小外形封装结构的表面组装二极管。
SMT贴片标准及工艺标准

印刷工艺
印刷机选择
锡膏选择
印刷精度
根据产品要求选择合适 的印刷机,确保印刷质
量。
根据产品特性选择合适 的锡膏,保证焊接质量。
印刷精度要求高,误差 需控制在一定范围内。
印刷质量检测
印刷完成后需进行质量 检测,确保无缺陷。
贴片工艺
贴片设备选择
根据产品要求选择合适的贴片 设备,确保贴片精度。
元件选择与准备
焊点完整性
焊点外观
焊点应连续、平滑,无气泡、空洞或 裂缝。
焊点应呈光亮的金属色,无氧化、变 色等现象。
焊点强度
焊点应牢固,能承受一定程度的压力 和振动,不易脱落。
元件位置标准
元件位置准确性
元件应放置在正确的位置,偏差 不超过允许范围。
元件方向正确性
元件的方向应符合电路设计要求, 极性元件方向正确。
焊点外观检测
焊点外观需光滑、连续、无气泡、无杂质。
检测工艺
01
功能检测
对产品进行功能检测,确保满足设 计要求。
尺寸检测
对产品尺寸进行检测,确保符合规 格要求。
03
02
外观检测
对外观进行检测,确保无明显缺陷。
可靠性检测
对产品进行可靠性检测,确保满足 使用要求。
04
SMT贴片质量标准
03
焊点质量标准
贴片材料的表面质量
贴片材料的表面应光滑、无缺陷,以确保良好的贴装效果。
辅助材料标准
1 2
粘合剂材料
用于固定电子元件的粘合剂应具有适当的粘性和 耐温性能。
清洁剂材料
用于清洁贴片表面的清洁剂应无腐蚀性、无残留 物。
3
包装材料
用于包装贴片产品的包装材料应具有保护性、防 潮性和抗震性。
SMT产品检验标准
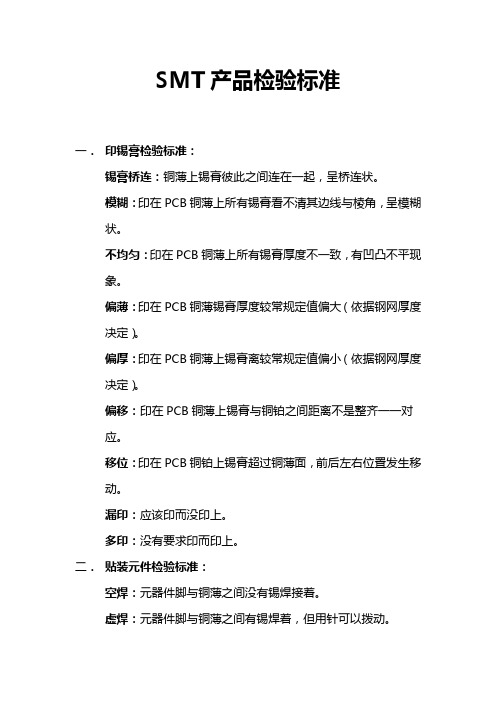
SMT产品检验标准一.印锡膏检验标准:锡膏桥连:铜薄上锡膏彼此之间连在一起,呈桥连状。
模糊:印在PCB铜薄上所有锡膏看不清其边线与棱角,呈模糊状。
不均匀:印在PCB铜薄上所有锡膏厚度不一致,有凹凸不平现象。
偏薄:印在PCB铜薄锡膏厚度较常规定值偏大(依据钢网厚度决定)。
偏厚:印在PCB铜薄上锡膏离较常规定值偏小(依据钢网厚度决定)。
偏移:印在PCB铜薄上锡膏与铜铂之间距离不是整齐一一对应。
移位:印在PCB铜铂上锡膏超过铜薄面,前后左右位置发生移动。
漏印:应该印而没印上。
多印:没有要求印而印上。
二.贴装元件检验标准:空焊:元器件脚与铜薄之间没有锡焊接着。
虚焊:元器件脚与铜薄之间有锡焊着,但用针可以拨动。
元器件脚与铜薄之间有锡焊着,用针不可以拨动,但通电测试不稳定。
短路:元器件脚与脚相靠在一起。
元器件脚与脚之间有焊锡或锡珠造成两者连在一起。
元器件脚与脚之间有杂物造成两者连在一起。
冷焊:焊锡点表面灰暗粗糙,不平滑,未完全溶化。
多锡:附着在元器件脚上锡量超出正常吃锡量要求。
少锡:附着在元器件脚上锡量少于正常吃锡量要求。
偏移:元器件端面与铜薄之间不是整齐一一对应的。
错位:元器件端面超过铜薄面,前后左右位置发生称动。
锡洞/针孔:元器件脚与铜薄之间的焊锡表面有针孔或小洞。
锡尖:元器件脚与铜薄之间的锡表面有尖长的锡尖。
错件:不符合文件(BOM、ECN、样板等)要求。
在精度上有差异,影响电性功能。
实测值不符合规定要求,出现较大差异。
未按位置贴装,位置不正确。
混料:元器件中出现不同类型、不同规格的料。
翻件:元器件本体与规定方向上下面旋转180度。
方向极性:元器件本体方向与PCB焊盘设计规定方向不相对应。
极性反:元器件本体正负极与PCB焊盘设计规定极性不相对应。
漏件/多件:未按规定用量贴装,用量不正确。
损件:元器件本体表面或边角局部出现缺损痕迹。
立碑:元器件一端面向上倾斜或一端面向上翘起。
划伤:元器件本体表面局部出现类刀割或手指划的痕迹。
SMT常用标准
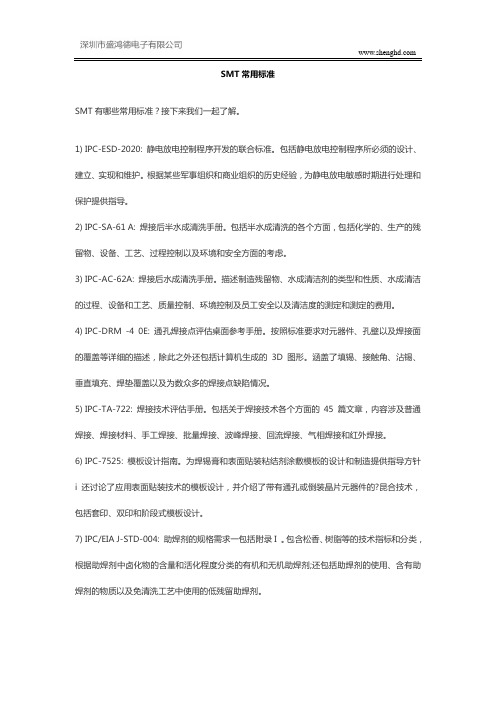
SMT常用标准SMT有哪些常用标准?接下来我们一起了解。
1)IPC-ESD-2020: 静电放电控制程序开发的联合标准。
包括静电放电控制程序所必须的设计、建立、实现和维护。
根据某些军事组织和商业组织的历史经验,为静电放电敏感时期进行处理和保护提供指导。
2)IPC-SA-61 A: 焊接后半水成清洗手册。
包括半水成清洗的各个方面,包括化学的、生产的残留物、设备、工艺、过程控制以及环境和安全方面的考虑。
3)IPC-AC-62A: 焊接后水成清洗手册。
描述制造残留物、水成清洁剂的类型和性质、水成清洁的过程、设备和工艺、质量控制、环境控制及员工安全以及清洁度的测定和测定的费用。
4)IPC-DRM -4 0E: 通孔焊接点评估桌面参考手册。
按照标准要求对元器件、孔壁以及焊接面的覆盖等详细的描述,除此之外还包括计算机生成的3D 图形。
涵盖了填锡、接触角、沾锡、垂直填充、焊垫覆盖以及为数众多的焊接点缺陷情况。
5)IPC-TA-722: 焊接技术评估手册。
包括关于焊接技术各个方面的45 篇文章,内容涉及普通焊接、焊接材料、手工焊接、批量焊接、波峰焊接、回流焊接、气相焊接和红外焊接。
6)IPC-7525: 模板设计指南。
为焊锡膏和表面贴装粘结剂涂敷模板的设计和制造提供指导方针i 还讨论了应用表面贴装技术的模板设计,并介绍了带有通孔或倒装晶片元器件的?昆合技术,包括套印、双印和阶段式模板设计。
7)IPC/EIA J-STD-004: 助焊剂的规格需求一包括附录I 。
包含松香、树脂等的技术指标和分类,根据助焊剂中卤化物的含量和活化程度分类的有机和无机助焊剂;还包括助焊剂的使用、含有助焊剂的物质以及免清洗工艺中使用的低残留助焊剂。
8)IPC/EIA J-STD -005 :焊锡膏的规格需求一包括附录I 。
列出了焊锡膏的特征和技术指标需求,也包括测试方法和金属含量的标准,以及粘滞度、塌散、焊锡球、粘性和焊锡膏的沾锡性能。
SMT国标

SJ 中华人民共和国电子行业标准SJ/T 10668-2002代替SJ/T 10668-1995表面组装技术术语Terminology for surface mount technology002-10-30发布2003-03-01实施中华人民共和国信息产业部发布前言本标准是对SJ/T 10668-1995 《表面组装技术术语》的修订。
本标准的修订版与前版相比,主要变化如下:——增加了部分新内容;——对前版的部分术语进行了修改和删除。
本标准由电子工业工艺标准化技术委员会归口。
本标准起草单位:信息产业部电子第二研究所。
本标准主要起草人:李桂云、王季娥、石萍、甄元生、宋丽荣。
本标准予1995年首次发布。
本标准自实施之日起代替并废止SJ/T 10668-1995《表面组装技术术语》标准1 范围本标准供电子组装行业及其他相关行业在制订国家标准、行业标准、企业标准和指导性技术文件以及编写教材、技术书籍、技术交流及论文报告时使用。
本标准界定了表面组装技术中常用的术语,本标准适用于电子工业的组装技术和其他相关行业的电子组装技术、互连技术和制造工艺。
2 一般术语2.1 组装 assembly 将若干元件、器件或组件连接到一起。
2.2 表面组装技术 surface mount technology(SMT)表面安装技术表面贴装技术将无引线的片状元件(表面组装元器件)安放在基板的表面上,通过浸焊或再流焊等方法加以焊接的组装技术。
2.3 表面组装组件 surface mount assembly(SMA)表面安装组件采用表面组装技术制造的印制板组装件。
2.4 表面组装元器件 surface mount component(SMC)表面安装元器件 surface mount device(SMD)表面贴装元器件外形为短形片状、圆柱形或异形,其焊端或引脚制作在同一平面内,并适用于表面组装的电子元器件。
2.5 芯片直接组装 chip on board(COB)一种将集成电路或晶体管芯片直接安装、互连到印制板上的组装技术。
SMT工艺标准
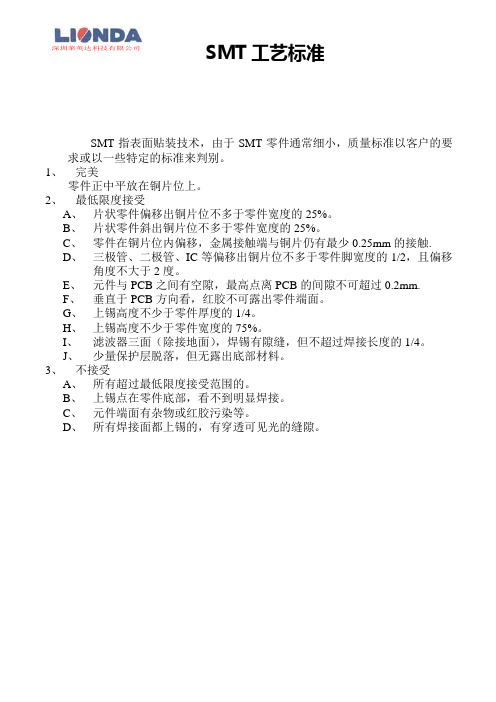
SMT 工艺标准
SMT 指表面贴装技术,由于SMT 零件通常细小,质量标准以客户的要求或以一些特定的标准来判别。
1、 完美
零件正中平放在铜片位上。
2、 最低限度接受
A 、 片状零件偏移出铜片位不多于零件宽度的25%。
B 、 片状零件斜出铜片位不多于零件宽度的25%。
C 、 零件在铜片位内偏移,金属接触端与铜片仍有最少0.25mm 的接触.
D 、 三极管、二极管、IC 等偏移出铜片位不多于零件脚宽度的1/2,且偏移
角度不大于2度。
E 、 元件与PCB 之间有空隙,最高点离PCB 的间隙不可超过0.2mm.
F 、 垂直于PCB 方向看,红胶不可露出零件端面。
G 、 上锡高度不少于零件厚度的1/4。
H 、 上锡高度不少于零件宽度的75%。
I 、 滤波器三面(除接地面),焊锡有隙缝,但不超过焊接长度的1/4。
J 、 少量保护层脱落,但无露出底部材料。
3、 不接受
A 、 所有超过最低限度接受范围的。
B 、 上锡点在零件底部,看不到明显焊接。
C 、 元件端面有杂物或红胶污染等。
D 、 所有焊接面都上锡的,有穿透可见光的缝隙。
《SMT外观检验标准》

片式元件侧面偏位(侧面偏移)1.侧面偏移时,最小连接宽度(C)不得小于元件焊端宽度(W)或焊盘宽度(P):二级1/2,三级3/4;按P与W的较小者计算。
MA片式元件末端偏移(末端偏移)不允许在Y轴方向有末端偏移(二级、三级)MA城堡型端子(侧面偏移)最大侧面偏移宽度(A)不得大于城堡宽度(W)的(二级1/2)(三级1/4).MA城堡型端子(末端偏移)不接受任何末端偏移B(二级、三级)MA圆柱状元件(侧面偏移)侧面(水平)移位宽度(A)不得大于其元件直径(W)或焊盘宽度(P)的1/4.按P与W的较小者计算。
(二级、三级)MA圆柱状元件(末端偏移)不接受任何末端偏出B(二级、三级)MA圆柱状元件末端连接宽度末端连接宽度(C)大于元件直径(W),或焊盘宽度(P)中的1/2.(二级、三级)MAJ形引脚元件(侧面偏移)侧面偏移(A)不得大于引脚宽度(W)的(二级1/2)/(三级1/4).MAJ形引脚元件(末端偏移)末端偏移B不作定义,但需确保侧面连接最小长度(D)不得小于引脚宽度(W)的150%.MA偏移鸥翼型引线元件(侧面偏移最大侧面偏移(A)不得大于引脚宽(W)的(二级1/2或0.5mm,取较小者)/(三级1/4或0.5mm,取较小者)MA鸥翼型引线元件(末端偏移1、脚长L小于3倍引线宽度W不允许出现偏出B;2、偏出违反最小电气间隙MA表面贴装面阵列焊料球偏出,违反最小电气间隙MA底部有散热面端子元器件二级/三级:1、散热面端子的侧面偏出不大于端子宽度的25%;2、散热面端子的末端偏出焊盘;3散热面末端端子的连接宽度与焊盘接触区域的润湿小于100%;4、散热面偏出违反最小电气间隙MA反贴/反白元件翻贴片式元器件的电气要素面朝下.(即:丝印面向下)片式电阻常见。
一级可接受,二三级制程警示MI立碑片式元件不允许焊接元件有斜立或直立现象(元件一端脱离焊盘焊锡而翘起)MA焊锡高度无引脚元件最小填充高度F为焊料厚度G加城堡高度H的(二级25%)/(三级50%)MA侧立片式元件不允许宽、高比超过(二级2/1)/(三级1.25/1)的元件侧立(元件本体旋转90度贴放)片式电容常见MA偏移错件所有物料不接受贴装元件规格与要求不符的现象MA少件所有物料不允许有出现元件漏贴的现象MA反向有极性元件不接受有极性元件方向贴反(备注:元件上的极性标志必须与PCB板上的丝印标志对应一致)MA多件所有物料不允许有空位焊盘贴装元件MA连锡/短路所有元件1、横跨在不应该相连的导体上的焊接连接;2、焊料跨接到毗邻的非公共导体或元器件上。
SMT检验标准

称发行版次1、电阻水平方向偏移,其基板焊点一端的空余长度 1. L2≧L*1/3,O大于或等于另一端空余长度的1/3,为最大允收限度; 2. L2<L*1/3,NG .如果小于另一端空余长度的1/3则拒收。
L2L 1、两元件之间最小间隔在0.5mm以上为最大允收;1. W≧0.5mm,OK;2、两元件之间最小间隔小于0.5mm 拒收。
2. W<0.5mm,NG .零件直立拒收! 文字面帖反拒收。
1、按正面贴装,元件的两端置于基板焊点的中央位置。
1、元件偏移突出基板焊点的部份是元件宽度的25% 以下为最大允收限度,如果超出25%则拒收。
1、元件水平方向偏移,其基板焊点一端的空余长度 1. L2≧L*1/3,O 大于或等于另一端空余长度的1/3,为最大允收限度;2. L2<L*1/3,NG .如果小于另一端空余长度的1/3则拒收。
L2L 1、两元件之间最小间隔在0.5mm以上为最大允收;1. W≧0.5mm,OK;2、两元件之间最小间隔小于0.5mm 拒收。
2. W<0.5mm,NG .零件直立拒收!(垂直方向)(水平方向)电阻偏移(水平方向)零件间隔电容、电感类实装页码判 定 說 明图 示 说 明SMT 通用检验标准电容、电感偏移标准模式电容、电感偏移零件间隔零件直立电阻帖反项 目零件直立W 零件直立拒收文字面(翻白)R757文字面电阻不可帖反(文字面OK W W1W1≧W*25%,NG W 零件直立拒收称发行版次1、元件倾斜突出焊点的部份须小于元件宽度的25%,反之则拒收。
(NG)1、三极管的三个引脚处于焊点的中心位置。
1、三极管的引脚超出焊点的部份须小于或等于引脚 1. w1≦W*1/2, OK ; 宽度的1/2;若大于1/2则不良。
2. w1>W*1/2, NG ;1、三极管的引脚超出焊点的部份须小于或等于引脚 1. L1≦L*1/2, OK ; 平坦段长度的1/2;若大于1/2则拒收。
SMT检验标准

偏位 变形 倾斜 沾锡 浮焊 裂锡 锡洞 开裂 断线 短路 漏红胶 标示不 零件孔 损件 零件脚 翘 焊点腐
描述 规格或参数与BOM要求不符。 应有之零件的位置而无。 不应有的位置而有零件 。 有极性的元件方向反。 焊盘上未沾锡且未与零件焊接上。 零件脚未沾附锡或表面沾锡经大头针拔脚便松动。 零件焊盘有锡但未与零件焊接上或焊点未吃锡零件引焊线或铜 箔未接触到或被松香隔离 。 零件一端立起与其应导通的线路形成断路 。 贴片零件吃锡量不足于零件厚度的1/3及IC类零件吃锡少于脚厚 的1/2。 两独立相邻,且不同线路的焊点因焊锡、锡渣、锡丝连通。 呈球状的锡存于 PCB 或零件周围, 锡珠直径不大于 0.15mm或 存于两脚间引起短路 。 IC 或其它零件折脚未入插槽或孔。 IC 或其它零件脚插错位置。 IC 及其它零件在同一 PCB 板上多种厂牌或混成其它规格的物 PCB 板水印不得超过 PCB 板面积的 1/4。 焊锡表面暗晦无光泽或成粗糙粒状表面,引线与铜箔未完全溶 元件脚未露出锡点,锡点未成弧状扩散。 贴片零件等吃锡超过零件顶端加上零件厚度一半的高度或成一 圆球状锡点或 PCB 板呈锐角或呈圆球状。 零件本体或脚发生氧化生锈情形。 焊点发黑,不光亮,不上锡。 所有零件均需于 PCB 平贴或至最低部。 IC 及脚座与各型 CON插座不得浮起超过 0.5MM。 电阻、电容、二极管等元件小于或等于 1MM,单过浮起小于或 等开 2MM。 大功率电阻、二极管等元件浮高大于或等于 3MM 。 片状器件超过器件焊接宽度之 1/3 。 PLCC、SOP 器件超过器件脚宽之 1/4。 QFP 器件超过器件脚宽之 1/4 。 PCB 或零件遭挤迫,重压导致变形。 零件于 PCB 板成垂直,若有倾斜,不得超过 15 度,且不得超过 PCB 板边。 PCB 板或零件本体不得沾有锡或锡渣。 零件引脚浮于焊锡表面未被覆盖。 锡点破裂或裂纹深入焊锡内部。 焊锡表面有缺口或小洞超出锡点焊盘面积 20%以上。 插座开裂长度小于或等于三针宽度。 应导通的线路未导通。 焊点间焊锡或锡脚造成短路。 红胶溢到焊盘上影响焊接 。 元件印字不良无法辨认其规格和方向。 制程因素(如锡膏熔化,过锡炉)造成零件孔、螺丝孔等堵塞 零件表面损伤、缺角只影响外观。 零件损伤、破裂会影响电气性能或装配。 QFP 或 SOP 等零件脚翘起,未平贴板面,翘起高度为超过零件 脚的厚度 。 焊锡点未清洗干净,造成焊点腐蚀或暗色或氧化。
smt外观检查标准

smt外观检查标准SMT外观检查标准。
一、引言。
SMT(Surface Mount Technology)是一种表面贴装技术,广泛应用于电子元器件的生产中。
在SMT生产过程中,外观检查是非常重要的环节,它直接关系到产品的质量和可靠性。
本文档旨在制定SMT外观检查标准,以确保产品外观质量符合要求,提高产品的可靠性和竞争力。
二、外观检查标准。
1.焊接质量。
1.1焊点外观,焊点表面应光滑平整,无裂纹、气泡、凹坑等缺陷。
1.2焊盘外观,焊盘应平整,无氧化、锈蚀等现象。
1.3焊料外观,焊料应均匀,无虚焊、溢出等情况。
2.元器件安装。
2.1元器件位置,元器件应安装在指定位置,无偏移、歪斜等情况。
2.2元器件间距,元器件之间应保持适当间距,避免短路等问题。
2.3元器件损坏,元器件表面应无划痕、磨损等损坏现象。
3.印刷质量。
3.1印刷位置,印刷应准确无误,无偏移、重影等情况。
3.2印刷质量,印刷应均匀、清晰,无残留、漏印等情况。
3.3印刷剥离,印刷应牢固,无剥离、脱落等现象。
4.外观质量。
4.1外观检查,产品外观应整洁,无划伤、污渍等现象。
4.2标识清晰,产品标识应清晰可见,无模糊、掉色等情况。
4.3封装完整,产品封装应完整,无开裂、变形等问题。
5.包装质量。
5.1包装完好,产品包装应完整,无破损、变形等情况。
5.2包装标识,包装标识应清晰,无模糊、错位等现象。
5.3包装数量,包装数量应准确无误,避免漏装、多装等问题。
三、结论。
SMT外观检查是确保产品质量的重要环节,本文档制定了一系列的外观检查标准,涵盖了焊接质量、元器件安装、印刷质量、外观质量和包装质量等方面。
通过严格执行这些标准,可以有效提高产品的质量和可靠性,提升企业的竞争力,满足客户的需求。
希望全体员工都能认真遵守这些标准,共同努力,为公司的发展贡献力量。
四、附录。
1.外观检查标准示意图。
2.外观检查记录表。
3.外观检查标准执行流程图。
以上即为SMT外观检查标准的文档内容,希望能够对相关人员在SMT生产过程中有所帮助,提高产品的质量和可靠性。
SMT(贴片)检查标准
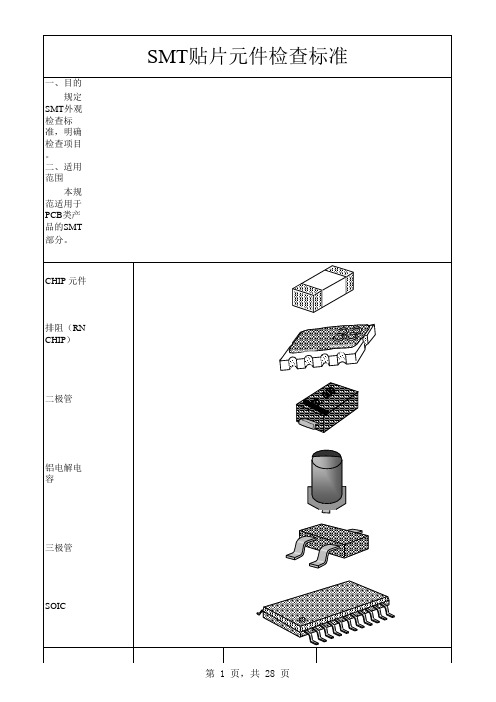
●
B区
B区
⑷金手指缺口:A区有缺口为不合格,B区缺损,凹进超过整体面积的20% 凹点 为来、不合格。 金手指 <20%
B
A 合格
B
A区
⑸金手指针孔 ●A区0.13mm以下的可接受一个,一个以上为不合格
第 4 页,共 16 页
SMT贴片元件检查标准
●
B区0.5mm以下的可接受两个,两个以上为不合格 0.05mm以下的忽略不计。 多孔区域须小于接触片的10%,大于10%为不合格 A区
但偏移部分的焊电极不可与其它电路接触
引脚偏移 LEAD偏移为LEAD宽度的1/3以下。
PAD
LEAD宽度
引線和鄰近焊盤之間的間隔為0.08mm以上。 引脚偏移
0.08mm以上
PAD 第 9 页,共 16 页
LEAD
SMT贴片元件检查标准
引脚浮起 整个引脚浮起为不合格,但有焊锡相连、端部浮起在0.3mm以下允许通过
●
●
B区两个不在同一侧 合格
⑹金手指污染
● ●
A区不允许有任何污染现象 B区不可有超过0.05mm2的油迹、白色结晶膜等残留表面 油迹,松香
胶纸迹 不合格 ⑺金手指残留铜箔 ●边缘整齐,无细铜丝与其它线路相连、相碰
铜丝短路
●
不合格 边缘批缝须在以下范围:当 L1〈 0.5mm时,L2≥ 0.15mm 当 L1≥ 0.5mm时,L2≥ 0.2mm
金手指 L1 L2 铜箔批缝
⑻绿油
●
从金手指上部引出的线路暴露于外,绿油没有覆盖的地方不得超过0.5mm, 且暴露部分必须是镀金部分
第 5 页,共 16 页
SMT贴片元件检查标准
●
绿油覆盖金手指不 得超过0.5mm 金手指
SMT贴片行业标准及工艺行业标准

因好壞直接關系到生產品質,故有一定之標準。
二:印刷品質
1.錫膏保存及使用
將錫膏置於冷藏庫(攝氏0°--10°C,相對濕度3555%)保存。 有效期從製造日起4-5個月內使用完畢為宜。
錫膏自冷藏庫取出後,在室溫25°C 的環境下至少回 溫8小時以上,方可使用。
PCB零件加熱至錫膏溶點溫度
恆溫區:使PCB及各種不同之零件有足夠時間吸收 熱量,以達到均溫,同時Flux完全揮發
回焊區:已活化的Flux及完全熔化的錫膏,開始進 行焊接功能
冷卻區:焊接功能完成,已熔化的錫膏快速冷卻完 成焊接
升溫區
恆溫區 預溫區
回焊區
冷卻區
圖七
二:回焊效果 1.回焊後之焊點應光滑,有光澤,吃錫性好,焊點
與零錫焊應呈弧形。(如圖)
2.具有良好的導電性:即焊錫相互擴散形成合金屬. 3. 具有一定的強度:即焊點必須具有一定抗拉強度和抗 衝擊韌性.
4.回焊時盡量使用N2,回焊效果更佳。
三:不良焊點.
生產中由於PCB線路設計,生產中工藝控制以及錫膏的 選擇等因素影響,均會出現不良焊點,所出現的不良時點主 要有以下几種:
一般貼片機分高速機和泛用機。
高速機是以極快的速度將細小零件吸取❹裝著於基 板上。
泛用機是識別大零件的外形或腳位能精準著裝於基 板上
貼片機貼裝精密度非常高,貼裝之零件坐標一定要 準確,不能有反向,缺件現象。
二:貼片的主要不良現象 1.偏移 即貼裝之零件偏離所應貼裝的位置(如圖五)
偏移
2.反向
圖五
有極性之零件角度貼裝錯誤(如圖六)
8.反向 反向的指有極性之零件,極性錯誤
1.少錫,錫量過多,過厚。
SMT检验标准

A
1. w21. < a1>A 拒收
拒 收 L1
拒收
允 收
允收
6、元件 与板的间
红
1、偏移
胶
量大于
印
1/5元件
刷
宽度或大 于1/5焊
盘宽度;
元件偏移拒收 示范
2、元件 与板的间 隙超过
0.15mm
3。元器
件左右偏
移角度超
过+/—5
度
1、胶量
胶量不足、不
不足; 2、胶量
均拒收示范 不均;
拒收 拒收
胶量偏
L
间隔<05mm 拒收
元件直立拒收
电阻不可 文字面(翻白)
元件浮高拒收 1、元件与板的浮高距离≤0.15mm为最大允收,否则拒
示范
收;
拒收
名
称 项 目
福建德晖实业有限公司
SMT 检验标准
判 定 說 明
文件编号 DH-PG-SMT-001 生效日期 2015/3/1
发行版次
A01
页码
4/7
图 示 说 明
类
+/—5度。
实
装
标 准
元件间隔拒收 1、两元
示范
件 2、之两间元最
件之间最
W
元件立件拒收 1、元 示范 件立件拒
元件贴反拒收 1、文 示范 字面贴反 拒收。
元件浮高拒收 1、元件与板的浮高距离≤0.15mm为最大允收,否则拒
示范
收;
拒收
OK
A≥20%元件 宽 拒收
1. L2 ≧ L*1/4, OK ; 2. L2<L *1/4, NG .
示范
1、印刷 图 2、形涂与焊 污 , 不两 可焊 允
SMT国标

SJ 中华人民共和国电子行业标准SJ/T 10668-2002代替SJ/T 10668-1995表面组装技术术语Terminology for surface mount technology002-10-30发布2003-03-01实施中华人民共和国信息产业部发布前言本标准是对SJ/T 10668-1995 《表面组装技术术语》的修订。
本标准的修订版与前版相比,主要变化如下:——增加了部分新内容;——对前版的部分术语进行了修改和删除。
本标准由电子工业工艺标准化技术委员会归口。
本标准起草单位:信息产业部电子第二研究所。
本标准主要起草人:李桂云、王季娥、石萍、甄元生、宋丽荣。
本标准予1995年首次发布。
本标准自实施之日起代替并废止SJ/T 10668-1995《表面组装技术术语》标准1 范围本标准供电子组装行业及其他相关行业在制订国家标准、行业标准、企业标准和指导性技术文件以及编写教材、技术书籍、技术交流及论文报告时使用。
本标准界定了表面组装技术中常用的术语,本标准适用于电子工业的组装技术和其他相关行业的电子组装技术、互连技术和制造工艺。
2 一般术语2.1 组装 assembly 将若干元件、器件或组件连接到一起。
2.2 表面组装技术 surface mount technology(SMT)表面安装技术表面贴装技术将无引线的片状元件(表面组装元器件)安放在基板的表面上,通过浸焊或再流焊等方法加以焊接的组装技术。
2.3 表面组装组件 surface mount assembly(SMA)表面安装组件采用表面组装技术制造的印制板组装件。
2.4 表面组装元器件 surface mount component(SMC)表面安装元器件 surface mount device(SMD)表面贴装元器件外形为短形片状、圆柱形或异形,其焊端或引脚制作在同一平面内,并适用于表面组装的电子元器件。
2.5 芯片直接组装 chip on board(COB)一种将集成电路或晶体管芯片直接安装、互连到印制板上的组装技术。
SMT质量标准
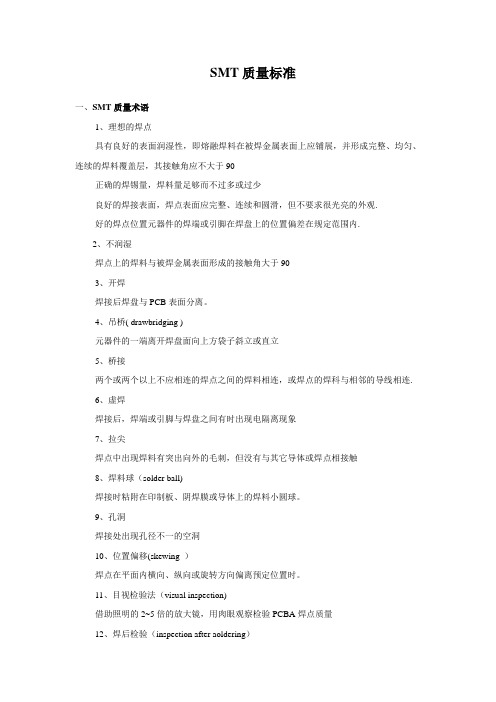
焊点上的焊料与被焊金属表面形成的接触角大于90
3、开焊
焊接后焊盘与PCB表面分离。
4、吊桥(drawbridging)
元器件的一端离开焊盘面向上方袋子斜立或直立
5、桥接
两个或两个以上不应相连的焊点之间的焊料相连,或焊点的焊科与相邻的导线相连.
6、虚焊
焊接后,焊端或引脚与焊盘之间有时出现电隔离现象
三、检验标准的准则
印刷检验
总则:印刷在焊盘上的焊膏量允许有一定的偏差,但焊膏覆盖在每个焊盘上的面积应大于焊盘面积的75%。
缺陷
理想状态
可接受状态
不可接受状态
偏移
连锡
锡膏沾污
锡膏高度变化大
锡膏面积缩小、少印
锡膏面积太
大
挖锡
边缘不齐
点胶检验
理想胶点:烛=焊盘和引出端面上看不到贴片胶沾染的痕迹,胶点位于各个焊盘中间,其大小为点胶嘴的1。5倍左右,胶量以贴装后元件焊端与PCB的焊盘不占污为宜。
检查方法:依据检测标准目测检验或借助放大镜检验。
3)贴片检测
a.元件的贴装位置情况;b.有无掉片;c.有无错件;
检查方法:依据检测标准目测检验或借助放大镜检验.
4)回流焊接检测
a.元件的焊接情况,有无桥接、立碑、错位、焊料球、虚焊等不良焊接现象.b.焊点的情况.
检查方法:依据检测标准目测检验或借助放大镜检验.
二、SMT检验方法
在SMT的检验中常采用目测检查与光学设备检查两种方法,有只采用目测法,亦有采用两种混合方法。它们都可对产品100%的检查,但若采用目测的方法时人总会疲劳,这样就无法保证员工100%进行认真检查。因此,我们要建立一个平衡的检查(inspection)与监测(monitering)的策略即建立质量过程控制点。
- 1、下载文档前请自行甄别文档内容的完整性,平台不提供额外的编辑、内容补充、找答案等附加服务。
- 2、"仅部分预览"的文档,不可在线预览部分如存在完整性等问题,可反馈申请退款(可完整预览的文档不适用该条件!)。
- 3、如文档侵犯您的权益,请联系客服反馈,我们会尽快为您处理(人工客服工作时间:9:00-18:30)。
点检要领点检周期1Fra bibliotek伤痕,打痕
无
目视确认网板表面无伤痕,打痕
开始工作,切换机种时
2
网板的松紧程度
无松弛
用手轻拍网板,发出干脆的响声.注意,不要弄破网板.
开始工作,切换机种时
3
保护胶带
无剥离,破坏
目视确认保护胶带无剥离,破坏
开始工作,切换机种时
A面
有破损时,A面:剥掉胶带.B面:剥掉胶带,然后再贴上一层.
焊锡膏印刷检验标准与改进办法
项目
印刷状态
对不良品采取的对策
1
良品
2
位置偏移
一部分偏移→重新定做印刷网板
全体偏移→调整认识位置和设定位置
全体偏移时→检查基板尺寸→OK:调整印刷机
NG:PCB不良
3
溢出
调整网板与PCB间距,使之为0
调整印压.压入量,刮刀移动速度
增加网板清扫次数
减少焊锡量
确认PCB与网板是否平行
更换刮刀
更换焊锡膏
6
遗漏
调整网板与PCB间距,使之为0
动作顺序:PCB下降后,刮刀上升
7
没
印刷
添加锡膏或更换焊锡膏
更换刮刀
更换印刷网板
印刷注意的问题及印刷网板的定期点检
注1)穿防静电鞋
注2)焊锡膏的使用方法,参照QW66-0026
注3)按照下面表格的项目,定期点检印刷网板,并做好记录.
NO.
点检项目
调整网板与PCB间距,使之为0
调整印压,压入量
调整刮刀移动速度
4
抹擦
清扫网板焊锡膏的交换
更换刮刀减少刮刀角度增加焊锡量
调整网板与PCB间距,使之为0
减慢刮刀移动速度
清扫印刷网板增加焊锡量
增大印压,压入量增加0.1mm
交换焊锡膏减慢刮刀移动速度
更换刮刀减少刮刀角度
5
挖缺
减少印压值,压入量减少0.1mm
金属板
B面
保护胶带
丝织品