预控图
控制图类型

控制图的类型2011-5-12 16:54|发布者: 小编H|查看: 2293|评论: 5摘要: 4.2.1 均值极差图――对于计量型数据而言,这是最常用最基本的控制图。
它用于控制对象为长度、重量、强度、纯度、时间和生产量等计量值的场合...4.2.1 均值极差图――对于计量型数据而言,这是最常用最基本的控制图。
它用于控制对象为长度、重量、强度、纯度、时间和生产量等计量值的场合。
Xbar控制图用于观察分布均值的变化,R控制图用于观察分布的分散情况或变异度的变化,Xbar-R图将二者联合运用,用于观察分布的变化。
4.2.2 均值极差图――控制图是用标准差图(S图)代替极差图(R图)。
极差计算简便,故R图得到广泛应用,但当样本大小n>10或n>12,这时用极差估计总体标准差的效率降低,要用S图来代替R图。
4.2.3 中位数极差图――用中位数图(Xmed图)代替均值图(Xbar图)。
中位数指一组按大小顺序排列的数列中居中的数。
例如,在数列2、3、7、13、18,中位数为7,在数列2、3、7、9、13、18,有偶数个数据,中位数规定为中间两个数的均值,即=8。
中位数的计算比均值简单,多用于现场需要把测定数据直接记入控制图进行控制的场合,为了简便,规定用奇数个数据。
4.2.4 单值移动极差图――用于对每一个产品都进行检验,采用自动化检查和测量;取样费时、昂贵以及化工过程,样品均匀,多抽样也无太大意义的场合。
X-Rs不能获得较多的信息,判断过程变化的灵敏度要差一些。
4.2.5 指数权重移动均值图4.2.6 运行图――运行图不是控制图,它只直接反映产品质量特性数据的变化情况,而没有反应过程统计受控的稳定控制线。
仅仅供掌握测量值的变化曲线。
4.2.7 预控图――它根据用户给定的控制百分率来确定控制线的一种控制图,该控制图分别以红,黄,绿三种颜色区域表示过程失控,警戒和受控状态。
控制线计算简单方便,控制图清晰醒目。
预控制图
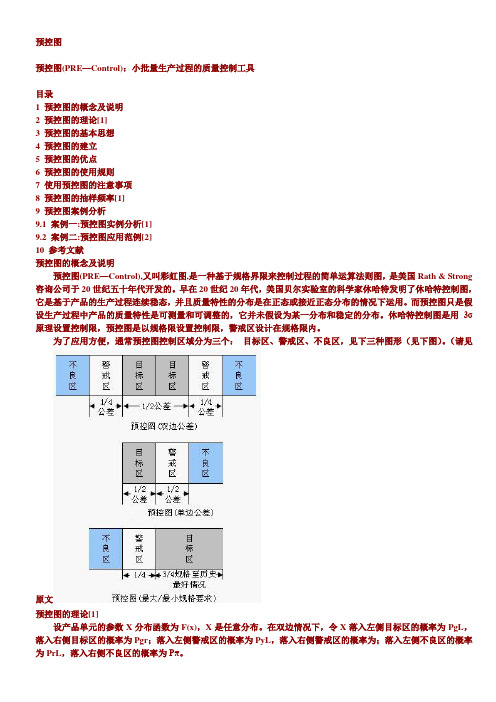
预控图预控图(PRE—Control):小批量生产过程的质量控制工具目录1 预控图的概念及说明2 预控图的理论[1]3 预控图的基本思想4 预控图的建立5 预控图的优点6 预控图的使用规则7 使用预控图的注意事项8 预控图的抽样频率[1]9 预控图案例分析9.1 案例一:预控图实例分析[1]9.2 案例二:预控图应用范例[2]10 参考文献预控图的概念及说明预控图(PRE—Control),又叫彩虹图,是一种基于规格界限来控制过程的简单运算法则图,是美国Rath & Strong 咨询公司于20世纪五十年代开发的。
早在20世纪20年代,美国贝尔实验室的科学家休哈特发明了休哈特控制图,它是基于产品的生产过程连续稳态,并且质量特性的分布是在正态或接近正态分布的情况下运用。
而预控图只是假设生产过程中产品的质量特性是可测量和可调整的,它并未假设为某一分布和稳定的分布。
休哈特控制图是用3σ原理设置控制限,预控图是以规格限设置控制限,警戒区设计在规格限内。
为了应用方便,通常预控图控制区域分为三个:目标区、警戒区、不良区,见下三种图形(见下图)。
(请见原文预控图的理论[1]设产品单元的参数X分布函数为F(x),X是任意分布。
在双边情况下,令X落入左侧目标区的概率为PgL,落入右侧目标区的概率为Pgr;落入左侧警戒区的概率为PyL,落入右侧警戒区的概率为;落入左侧不良区的概率为PrL,落入右侧不良区的概率为Pπ。
令X落入目标区的概率为Pg(在双边情况下,Pg = PgL + Pgr);令X落入警戒区的概率为Py(在双边Pr = PyL + Pyr)。
令X落入目标区的概率为(在双边情况下,Pg = PgL + Pgr);令X落入警戒区的概率为Py(在双边情况下,Py = PyL + Pyr);令x落入不良区的概率为Pr(在双边情况下,Pr = P rL + Pπ)。
可以启动预控图于工程控制的概率为PS,其条件为接连5个样品的参数值落在目标区内,故。
预控图

预控图预控图(PRE—Control):小批量生产过程的质量控制工具预控图的概念及说明预控图(PRE—Control),又叫彩虹图,是一种基于规格界限来控制过程的简单运算法则图,是美国Rath & Strong咨询公司于20世纪五十年代开发的。
早在20世纪20年代,美国贝尔实验室的科学家休哈特发明了休哈特控制图,它是基于产品的生产过程连续稳态,并且质量特性的分布是在正态或接近正态分布的情况下运用。
而预控图只是假设生产过程中产品的质量特性是可测量和可调整的,它并未假设为某一分布和稳定的分布。
休哈特控制图是用3σ原理设置控制限,预控图是以规格限设置控制限,警戒区设计在规格限内。
为了应用方便,通常预控图控制区域分为三个:目标区、警戒区、不良区,见下三种图形(见下图)。
[编辑]预控图的理论[1]设产品单元的参数X分布函数为F(x),X是任意分布。
在双边情况下,令X落入左侧目标区的概率为P gL,落入右侧目标区的概率为P gr;落入左侧警戒区的概率为P yL,落入右侧警戒区的概率为;落入左侧不良区的概率为P rL,落入右侧不良区的概率为Pπ。
令X落入目标区的概率为P g(在双边情况下,P g = P gL + P gr);令X落入警戒区的概率为P y(在双边P r = P yL + P yr)。
令X落入目标区的概率为(在双边情况下,P g = P gL + P gr);令X落入警戒区的概率为P y(在双边情况下,P y = P yL + P yr);令x落入不良区的概率为P r(在双边情况下,P r = P rL + Pπ)。
可以启动预控图于工程控制的概率为P S,其条件为接连5个样品的参数值落在目标区内,故。
在启动预控图于工程控制后,每一次抽样抽两个样品A、B:两个数据全落在目标区的概率为,;一个数据落在目标区、另一个数据落在警戒区的概率为2P_gP_y;两上数据都落在警戒区的概率为P^2_y;两个数据中有一个落在不良区,另一个落在非不良区的概率为2P_r(1-P_r);两个数据都落在不良区的概率为。
SPC测试100题
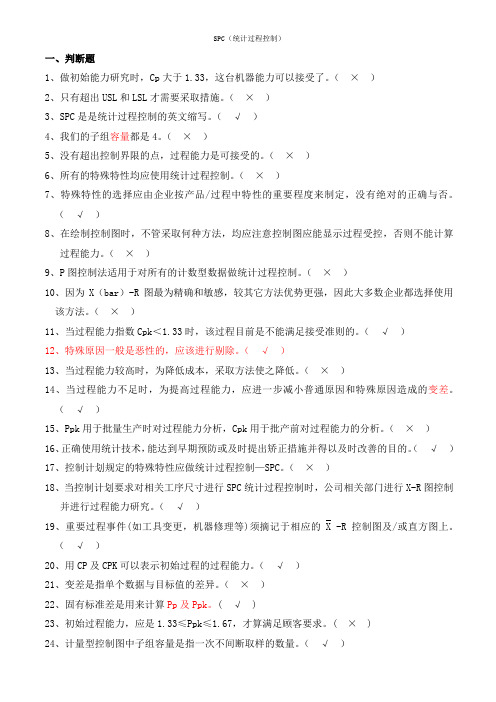
一、判断题1、做初始能力研究时,Cp大于1.33,这台机器能力可以接受了。
(×)2、只有超出USL和LSL才需要采取措施。
(×)3、SPC是是统计过程控制的英文缩写。
(√)4、我们的子组容量都是4。
(×)5、没有超出控制界限的点,过程能力是可接受的。
(×)6、所有的特殊特性均应使用统计过程控制。
(×)7、特殊特性的选择应由企业按产品/过程中特性的重要程度来制定,没有绝对的正确与否。
(√)8、在绘制控制图时,不管采取何种方法,均应注意控制图应能显示过程受控,否则不能计算过程能力。
(×)9、P图控制法适用于对所有的计数型数据做统计过程控制。
(×)10、因为X(bar)-R图最为精确和敏感,较其它方法优势更强,因此大多数企业都选择使用该方法。
(×)11、当过程能力指数Cpk<1.33时,该过程目前是不能满足接受准则的。
(√)12、特殊原因一般是恶性的,应该进行剔除。
(√)13、当过程能力较高时,为降低成本,采取方法使之降低。
(×)14、当过程能力不足时,为提高过程能力,应进一步减小普通原因和特殊原因造成的变差。
(√)15、Ppk用于批量生产时对过程能力分析,Cpk用于批产前对过程能力的分析。
(×)16、正确使用统计技术,能达到早期预防或及时提出矫正措施并得以及时改善的目的。
(√)17、控制计划规定的特殊特性应做统计过程控制—SPC。
(×)18、当控制计划要求对相关工序尺寸进行SPC统计过程控制时,公司相关部门进行X-R图控制并进行过程能力研究。
(√)19、重要过程事件(如工具变更,机器修理等)须摘记于相应的 X -R控制图及/或直方图上。
(√)20、用CP及CPK可以表示初始过程的过程能力。
(√)21、变差是指单个数据与目标值的差异。
(×)22、固有标准差是用来计算Pp及Ppk。
( √ )23、初始过程能力,应是1.33≤Ppk≤1.67,才算满足顾客要求。
产品质量回顾标准操作程序
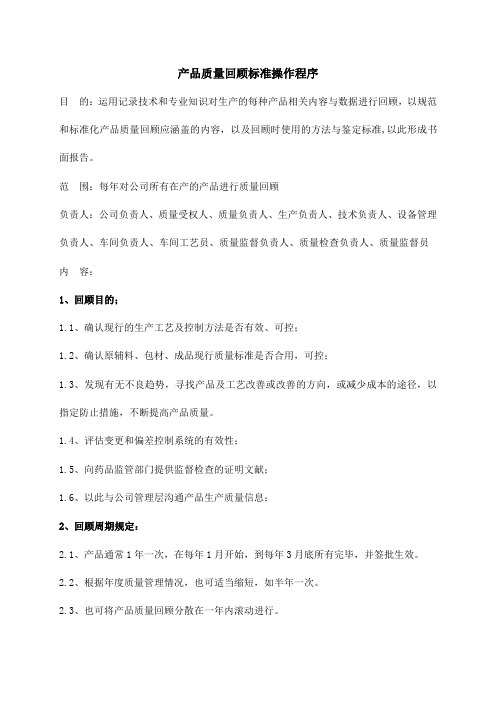
产品质量回顾标准操作程序目的:运用记录技术和专业知识对生产的每种产品相关内容与数据进行回顾,以规范和标准化产品质量回顾应涵盖的内容,以及回顾时使用的方法与鉴定标准,以此形成书面报告。
范围:每年对公司所有在产的产品进行质量回顾负责人:公司负责人、质量受权人、质量负责人、生产负责人、技术负责人、设备管理负责人、车间负责人、车间工艺员、质量监督负责人、质量检查负责人、质量监督员内容:1、回顾目的;1.1、确认现行的生产工艺及控制方法是否有效、可控;1.2、确认原辅料、包材、成品现行质量标准是否合用,可控;1.3、发现有无不良趋势,寻找产品及工艺改善或改善的方向,或减少成本的途径,以指定防止措施,不断提高产品质量。
1.4、评估变更和偏差控制系统的有效性;1.5、向药品监管部门提供监督检查的证明文献;1.6、以此与公司管理层沟通产品生产质量信息;2、回顾周期规定:2.1、产品通常1年一次,在每年1月开始,到每年3月底所有完毕,并签批生效。
2.2、根据年度质量管理情况,也可适当缩短,如半年一次。
2.3、也可将产品质量回顾分散在一年内滚动进行。
3、回顾的环节:3.1、年度产品回顾计划制定:3.1.1、每年1月15日前,由质量监督主管,制定回顾计划,并经公司负责人批准后,下发至各相关部门。
3.1.2、年度产品回顾,可制定为一次性完毕;如在每年的1到4月内;也可以滚动安排,在一年内,分阶段,分批次完毕。
3.2、信息收集与报告编制:各部门按计划规定对相应信息/数据收集,并汇总和分析各类数据的工作,并按计划规定期限,上交至质量监督员处,进行最后的报告编制汇总分析工作。
3.3、报告审批:报告编制结束后,由质量部门召集相关部门人员,对报告内容进行讨论,统一意见后,分别由生产负责人、技术负责人、质量负责人签字,最后由公司负责人签字批准。
3.4、报告分发:报告批准后,将由质量部门文献管理员,在数据库中列出,供各部门查阅使用。
质量管理的新七种工具
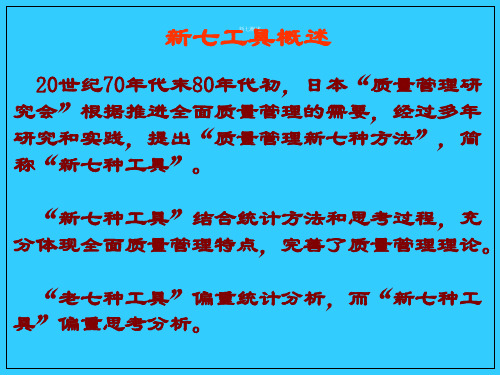
头脑风暴法 头脑风暴法又称畅谈法、集思法、智力激励法、脑力激荡法,是采用会议形式,引导每个参加会议的人围绕某个中心议题,充分解放思想、激发灵感,在自己头脑中掀起风暴,毫无顾忌,畅所欲言地发表独立见解的一种集体创造思维的方法。 主要用途有: 1 识别存在的质量问题并寻求解决方法; 2 识别潜在的质量改进机会; 3 用于绘制因果图、系统图、亲和图。
新七工具的应用范围 1 方针目标管理、计划实施 2 新品开发、成本管理、安全生产 3质量设计、保证、改进,QC活动等
关联图 对具有原因—结果,或手段—目的等逻辑关系的一系列有关问题的要素用箭线连接起来并找出主要因素的方法。可以用于分析整理各种复杂因素交织一起的多目的情形。 主要用途: 1 制订企业方针计划和实施措施; 2 制订生产过程不良品对策; 3 制订工序管理故障对策; 4 制订QC小组目标规划; 5 改善各部门质量工作; 6 改善企业各项工作质量。
关联图的类型 1 按应用形式分 多目的型 单一目的型 2 按结构形式分 中央集中型 单向汇集型 关系表示型 应用型
亲和图的绘制步骤 1 确定主题 2 收集资料 3 资料卡片化 4 汇总整理卡片 5 制作标签卡片 6 作图
亲和图应用的常见错误 1 应用范围错误 2 问题复杂化 3 用作因果图论证 4 采用逻辑思维画成关联图
系统图 系统图就是倒立状态的因果图,是根据目的找出手段,而又将上一级手段作为目的找出手段,按顺序层层展开的树状图。 系统图有从左到右单侧展开型和自上而下宝塔型两种形式。 主要用途有: 1 用于措施展开; 2 用于因果分析; 3 矩阵图配合使用。
亲和图 亲和图是KJ法的主体,是日本川喜田二郎首创的,是一种收集信息、按相互亲近程度用图形进行归纳整理并找出解决问题思路的图示技术。 亲和图不象关联图用逻辑推理来明确因果关系,而是按情理性归类。只适用需要时间慢慢解决、不易解决而非解决不可的问题,不适用速战速决或简单的问题。 主要用于归纳整理收集到的意见、观点和想法等语集资料 2 用短句词汇归纳要素 3 根据关系连接要素 4 改进图形表明问题要因
6Sigma的50种应用工具

6Sigma的50种应用工具1. Analysis Covariance 协方差分析2. Analysis of Variance 方差分析3. Binominal Distribution 二项分布4. Brainstorming Techniques 脑力风暴法5. Cause and Effect Matrix 因果图6. Check Sheets 检查表7. Chi-square Distribution 卡方分布8. Chi-square Test for Goodness-fit 卡方测试的拟合优度9. Chi-square Test of Independence 独立性的卡方测试10. Confidence Intervals 置信区间11. Control Cards 控制图表12. Correlation Methods 相关分析法13. Cross Tabulation Tables 交叉表14. Date Collection Sheets 数据收集表15. Exponential Distribution 指数分布16. F Distribution F分布17. F Test F测试18. Failure Mode and Effect Analysis 潜在缺陷模式及影响分析19. Full Factorial Experiment Designs 全因子DOE实验20. Factional Factorial Experiment Designs 分步DOE实验21. Group Screening Experiment Designs 分组筛选DOE22. Fishbone diagrams 鱼刺图23. Force Field Diagrams 作用因子分析24. Histograms 直方图25. Hypothesis Construction 假设测试26. Indexes of Location 位置指数27. Indexes of Process Capability 工序能力指数28. Indexes of Variability 变异度指数29. Line Bar Pie Charts 线形、条形、饼形图30. Mathematical Transformations 数学变位31. Median Test 中位数分析32. Normal Test 正态分布33. Parto Diagrams and Charts 柏拉图34. Performance Figures of Merit 性能图35. Performance Tolerancing 公差性能36. Poisson Distribution 泊松分布37. Positrol Logs 记录表38. Pre-Control 预控图39. Process Flow Diagrams 工序流程图40. Random Number Generation 随机数表41. Random strategy Experiment Designs 实验设计随机性策略42. Regression 回归分析43. Response Surface Experiment Designs 简便实验设计法44. Root-sun-of-squares 均方根45. Sample Size Equations and Tables 抽样方程及抽样计划46. Statistical Process Control Charts SPC控制图47. Statistical Tables 统计表48. T Distribution T公布49. T Test T测试50. Tests for Randomness随机测试笔者过去曾经担任软件协会顾问,负责辅导中小企业e化。
Minitab操作及应用教程

特别是当类别数小于 2 时,测量系统中将没有可以控制过程的值,因为一部分无法与另 一部分区分开。当类别数为 2 时,数据可以分为两个组,即高低组。当类别数为 3 时,数据可以分为三个组,即高中低组。值为 5 或更大表示可接受的测量系统。
量具公差(辨别力)
表示测量部件时特定量具所具有的辨别力或测量增量。实践原则(称为十分规则) 表明工具辨别力应该将过程公差分成十个或更多部分。量具公差 < 过程公差/10 。
与任何其他过程一样,测量系统既有常见原因的变异,也有特殊原因的变异。要 控制测量系统变异,必须首先识别变异的来源,然后必须排除或减少这些多种多 样的原因。
主效应和主效应图
与方差分析和试验设计结合在一起使用,以检查一个或多个因子的水平均值之间的 差值。当因子的不同水平对响应的影响不同时,就存在一个主效应。主效应图中绘 制的各因子水平的响应平均值由一条线连接在一起。 要寻找的一般模式: · 当线为水平时(平行于 x 轴),表示不存在主效应。因子的每个水平以相同方式 影响响应,而且响应平均值在所有因子水平上都相同。 · 当线不处于水平时,表示存在主效应。因子的不同水平对响应的影响不同。线越 陡峭,主效应的量值越大。
测量系统变异
当测量某个过程的输出时,既要考虑部件间的变异,又要考虑测量系统变异。例 如,您有一个刚好为 5.00 克的已知标准。经过多次称重后获得了以下读数:5.01 克、4.99 克、4.97 克、5.03 克 和 5.01 克。这些测量值之间的差异是由测量系统 变异造成的。但是,如果您称量来自生产线上的不同部件,则所出现的差异是由 于测量系统变异导致的呢还是由于部件本身的实际差异导致的?使用 Minitab 的测 量系统分析工具可以确定变异的来源。如果测量系统变异大于部件间变异,则测 量值可能无法提供有用的信息。
SPC预控图学习笔记
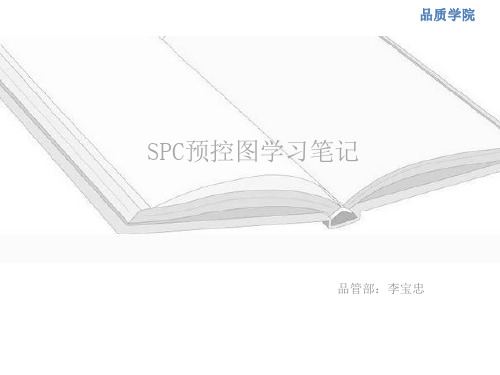
品质学院
• 在生产过程中随机抽取1件产品,其落入绿区的概率为86.64%。
• 若连续抽取5件产品,它们全部落入绿区的概率为 0.86645=0.48819(即概率为48.819%) ,说明过程要达到这一要求 只有48.819%的可能性。
• 而实际上达到了,证明了过程质量特性值的分布中心(平均值) 与规格中心(目标值)是重合的,而且过程能力也满足要求,符 合预控制图的假设条件,可以正式开始应用预控制图了。
以规格限作为控制限 限
• 红绿灯信号方法的一个应用 • 目的是对不合格的控制而不是过程控制 • 控制基于规范而不是过程变差
预控制图的基本原理
品质学院
– 控制图在生产过程中是过程控制有效的工具,但往往受 到以下几方面的限制:
• 作任何类型的控制图都需要预先取得20~25组的预备数据。 取得预备数据往往需要一定的时间,这对于小批量生产过 程来说是无法实现的。
红
×黄
×××绿××
黄
红
预控图的应用
品质学院
预控图的使用方法
步骤三:预控图的抽样频率 确定抽样频率的建议方法: 把两次停机(即两对黄点)之间的平均时间间隔除以6; 先根据生产线历史情况试定一个抽样周期(例如一小时抽一次),每次 抽两个产品,测其参数,到出现不通过,停止为止,其间隔为T(可试验 几次,求平均的T)。把T/6作为抽样周期。 例如:以1小时为周期,10次后出现不通过,即T=10,则10/6=1.5小时为 周期。
1/2公差
1/2公差
1/2公差
1/4公差
预控图(单边公差)
不良区 警戒区 目标区
1/4公差
3/4规格至历史最好情
况
预控图(最大、最小规格要求)
预控制图的基本原理
SPC
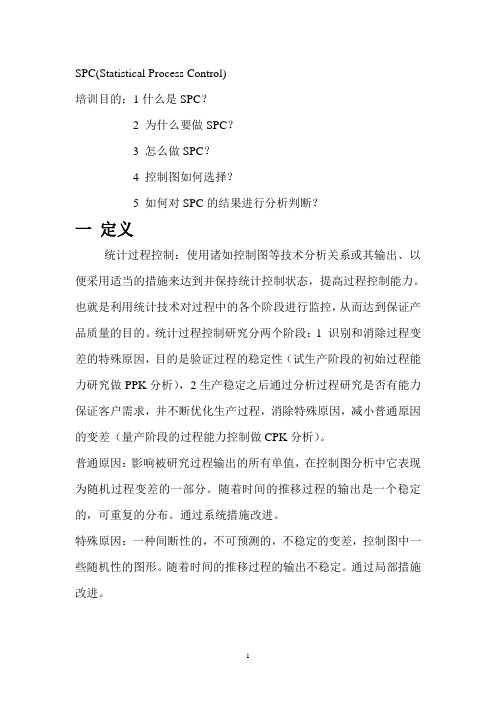
SPC(Statistical Process Control)培训目的:1什么是SPC?2 为什么要做SPC?3 怎么做SPC?4 控制图如何选择?5 如何对SPC的结果进行分析判断?一定义统计过程控制:使用诸如控制图等技术分析关系或其输出、以便采用适当的措施来达到并保持统计控制状态,提高过程控制能力。
也就是利用统计技术对过程中的各个阶段进行监控,从而达到保证产品质量的目的。
统计过程控制研究分两个阶段:1 识别和消除过程变差的特殊原因,目的是验证过程的稳定性(试生产阶段的初始过程能力研究做PPK分析),2生产稳定之后通过分析过程研究是否有能力保证客户需求,并不断优化生产过程,消除特殊原因,减小普通原因的变差(量产阶段的过程能力控制做CPK分析)。
普通原因:影响被研究过程输出的所有单值,在控制图分析中它表现为随机过程变差的一部分。
随着时间的推移过程的输出是一个稳定的,可重复的分布。
通过系统措施改进。
特殊原因:一种间断性的,不可预测的,不稳定的变差,控制图中一些随机性的图形。
随着时间的推移过程的输出不稳定。
通过局部措施改进。
二SPC目的1 科学技术发展的要求2 公司质量体系认证的需要3 客户的需要4 实践的证明三SPC使用的工具1 计数型(离散型)随机变量分布——“0-1”分布,又称二项分布b (n、p)(只有两个结果,成功/失败,yes/no)。
2计数型(离散型)随机变量分布——泊松分布π(λ)3 计量型(连续型)随机变量分布——正态分布(直方图、分布图、正态分布、正态分布表)4 中心极限定理(1 随机变量的独立性2 正态样本均值的分布3非正态样本均值的分布)四SPC原理1 产品质量控制的两种模型A 缺陷检测——控制输出,事后把关——结果导向B 反馈统计——控制过程,预防缺陷——过程导向2 产品过程的四类情况3 SPC控制图3.1 控制图的功能A 现场人员了解过程变差并使之达到统计受控状态;B 有助于过程在质量和成本上持续、可预测的保持;C 对已达到统计受控的过程采取措施,不断减少普通原因变差,以达到提高产品质量、降低成本、提高生产效率;D 区分变差的特殊原因和普通原因,作为采取局部措施或系统措施的依据。
预控图培训讲义
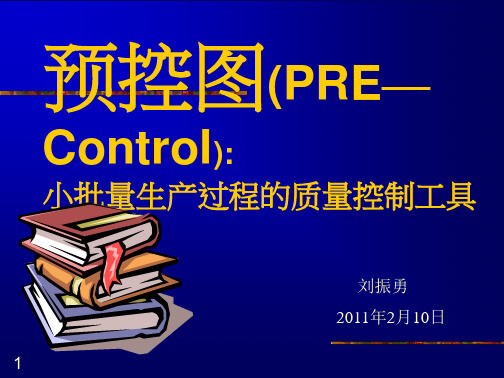
预控图的理论
可以启动预控图于工程控制的概率为PS,其条件为 可以启动预控图于工程控制的概率为 接连5个样品的参数值落在目标区内 个样品的参数值落在目标区内,故。 在启动预控图于工程控制后,每一次抽样抽两个样 在启动预控图于工程控制后 品A、B:两个数据全落在目标区的概率为 两个数据全落在目标区的概率为,;一个数 据落在目标区、另一个数据落在警戒区的概率为 另一个数据落在警戒区的概率为 2P_gP_y;两上数据都落在警戒区的概率为 两上数据都落在警戒区的概率为P^2_y;两 个数据中有一个落在不良区,另一个落在非不良区的 个数据中有一个落在不良区 概率为2P_r(1-P_r);两个数据都落在不良区的概率为 两个数据都落在不良区的概率为 。 注:它们的总和是。 因此每一次抽样通过概率为
戒区的概率为P^2_y;两个数据中有一个落在不良区,另一个落在非不良区的概率为 另一个落在非不良区的概率为2P_r(1-P_r);两个数据都落在不良区的概率为 。
预控图的理论
注:也可把判别通过与否的准则修改一下 也可把判别通过与否的准则修改一下,若第一数据 落在不良区,就判不通过(不必等第二数据酌结果 不必等第二数据酌结果),则 公式稍有变化。 在两次停止问的6次抽样都通过的概率为 ,此时批不合 次抽样都通过的概率为 格品率为Pr,因此通过抽样交付的批产品的平均交付不 因此通过抽样交付的批产品的平均交付不 合格品率为。 [例]如果X是正态分布N(µ,σ) µ,σ),设上下规格限距离正好 为6σ,则当X的µ正好在中心线上时 正好在中心线上时,有。 Cp = 1,Pg=85.73%,P_y=14.00%,P_r=0.27% =85.73%,P_y=14.00%,P_r=0.27% 于是每一次抽样通过的概率Pp算出为97.50% 于是每一次抽样通过的概率 =97.5%^6×0.27%=85.91% 0.27%=85.91%×0.27%=0.23%
123质量管理
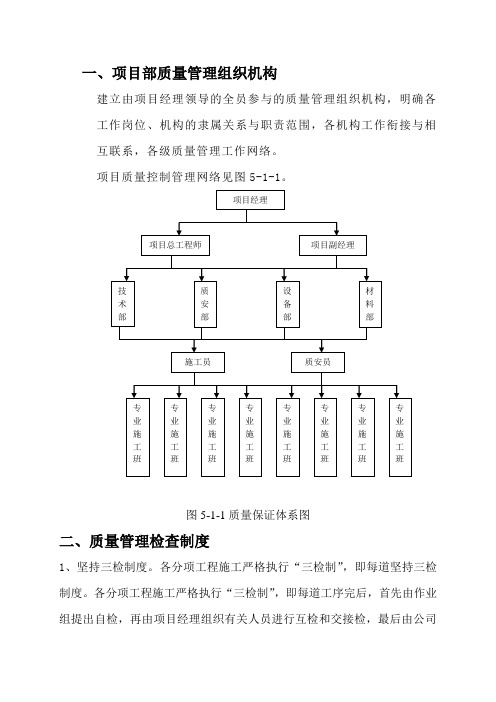
一、项目部质量管理组织机构建立由项目经理领导的全员参与的质量管理组织机构,明确各工作岗位、机构的隶属关系与职责范围,各机构工作衔接与相互联系,各级质量管理工作网络。
项目质量控制管理网络见图5-1-1。
图5-1-1质量保证体系图二、质量管理检查制度1、坚持三检制度。
各分项工程施工严格执行“三检制”,即每道坚持三检制度。
各分项工程施工严格执行“三检制”,即每道工序完后,首先由作业组提出自检,再由项目经理组织有关人员进行互检和交接检,最后由公司质检员组织有关人员进行专检。
隐蔽工程在作好“三检制”的基础上,还要请甲方、设计院、监理、质监等单位代表进行隐蔽验收。
2、建立严格的质量检查制度。
在项目进行“三检制”的基础上,公司对工程质量实行“三级检查”,即公司每月对公司承建的所有工程的工程质量检查一次,分公司每半个月对所承建的工程质量检查一次,项目经理部每周对自已施工项目的工程质量检查一次。
3、建立严格的奖罚制度。
在工程施工前或施工过程中,项目经理要组织有关人员,根据公司有关规定,制定出符合本工程施工的较为详细的规章制度和奖罚措施,特别是保证工程质量的奖罚措施,对施工质量好的作业人员进行重奖,对于违章施工造成质量事故的作业人员进行重罚,不允许在本工程施工中出现不合格品。
在施工任务单上要由专职质检员签署质量等级,对质量不合格的施工任务单不得计发工资;同时,要把合格等级的工日和优良等级的工日的单价工资拉开挡次,以激励作业人员多干优良等级工日,从而提高工程质量。
4、建立严格的技术交底制度。
在工程施工中,各分部分项工程和比较复杂的施工工序,各工种各专业技术人员都必须编制详细的技术措施,提出具体的施工方法、•注意事项以及操作方法,质量要求等,由各工种专业施工员(工长)组织作业人员进行书面交底,使每个作业人员做到心中有数,按程序施工,确保工序的施工质量。
三、质量保证技术措施在本工程施工中,对各工种专业制定出质量保证措施,对于各工种各专业的质量保证技术措施,由各分部分项技术主管编制,并向施工人员作详细的交底,由质量检查员监督实施。
【doc】控制图的界限修正
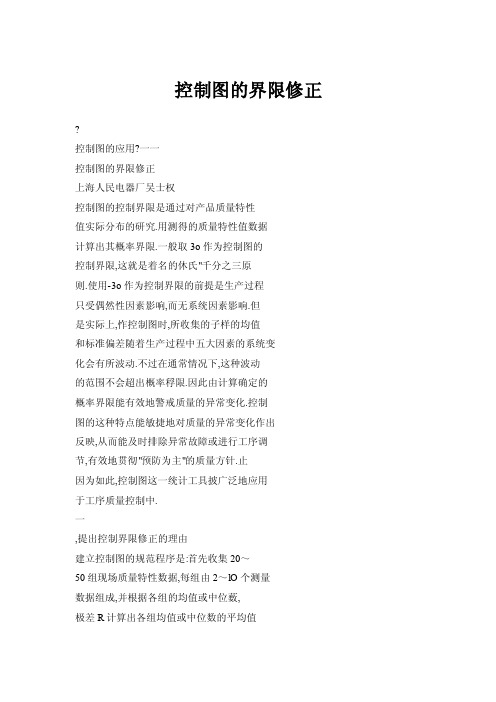
控制图的界限修正控制图的应用?一一控制图的界限修正上海人民电器厂吴士权控制图的控制界限是通过对产品质量特性值实际分布的研究.用测得的质量特性值数据计算出其概率界限.一般取3o作为控制图的控制界限,这就是着名的休氏"千分之三原则.使用-3o作为控制界限的前提是生产过程只受偶然性因素影响,而无系统因素影响.但是实际上,怍控制图时,所收集的子样的均值和标准偏差随着生产过程中五大因素的系统变化会有所波动.不过在通常情况下,这种波动的范围不会超出概率稃限.因此由计算确定的概率界限能有效地警戒质量的异常变化.控制图的这种特点能敏捷地对质量的异常变化作出反映,从而能及时排除异常故障或进行工序调节,有效地贯彻"预防为主"的质量方针.止因为如此,控制图这一统计工具披广泛地应用于工序质量控制中.一,提出控制界限修正的理由建立控制图的规范程序是:首先收集20~50组现场质量特性数据,每组由2~lO个测量数据组成,并根据各组的均值或中位薮,极差R计算出各组均值或中位数的平均值耳或和极差R的平均值,最后以+A或x+mA2R为x控制图的上控制界限UCL或x控制图的上控制界限UC以A莨或mA一R为X一控制图的下控制界限LCL{或x控制图的下控制界限LCL以D4R为R控制图的上控制界限UCL,IDR为R控制图的下控制界限LCL,共同组成控制图的控制界限.有关的系数A,m,D,D4等均可根据所选择的组样本个数11以及样本组大小K和风险率大小Ⅱ从控制图用系数表和有关数理统计表中查取.根据上述方法建立起来的控制界限只考虑到工序能力6o,只要质量波动稳定在6o之~8一内即认为正常.而实际上,我们检验产品质量是否台格的掏;准则是规格的要求.即其测茸值是否在公差范围之内.因而在使用控制图时往往会出现这样的情况:x控制图或-X控制图的点子,常常落在控制界限t某一侧)之外.而其样本的测量值却又都符合产品的技术标准.并有一定公差裕度.对于上述界外点子.一般会判其为失控点子.并要进行异常因的调查和工序调整.尤其是在工序能力指数CP值较高的情况下,而其分布中心和公差中心的偏离系数£又较大的情况下,这种现象特别严重,因此常常会产生虚假的警报,并要为此花费相当可观的调整工时,影响了工序的正常运行.这种情况同生产者风险Ⅱ过大的情况颇为相似.这样的控制界限,无论从实用性,还是从经济性来说.都显得要求过严完全有理由放弃对这种实际上不需调整的"警戒信号的调整工作.同样.在工序能力指数小于1的情况下,根据上述方法确定的控制界限容易产生判断失误,出现尽管点子都落在控制界限之内,而实际的质量却是已有不少子样不符合规格要求,产生了不少废品.这种警报迟钝的现象同消费者风险p过大情况很相似.因而在确定控制界限时,十分有必要考虑规格界限和工序能力指数之间的关系.避免发生上述二种情况,使得工序控制中应用的控制图控制界限与规格界限柏吻合,保证生产过程中的质量处于稳定的受控状态二,警戒系数的导八在实际工序能力指数cpk大于l时,如果把规格界限(公差,引入控制图控制图的话,则规格界限必然位于控制界限的两侧,并留有一定裕度;其问.控制图的分布中心和上.下控制界限随着生产过程的质量波动会在规格界限之问漂移众所周知.xR控制图或xR控制图分别由控制统计量集中位置的x控制图或x控制图和控制离散程度的极差R控制图组成.其中叔控制图往往会由于工装,刃具,模具等逐渐磨损的系统因素,致使分布中心和公差中心不仅不能重台,而且使其偏离系数逐渐增大,因而经常发现打在控制图上的点子偏向中心线的一侧,被误认为异常.为纠正这种界外的所谓异常点子,叉得花出很大的代价,有时甚至始终无法排除.如果我们仔细分析一下规格标准和控制界限之间的关系,就不难发现,在确定的技术标准下,公差带的宽度是不变的,而分布中心和上,下控制界限划会随着工序的变化,其分布的状态也随之变化=我们作一有公差界限(规格要求)的控制图控制图的应用'l?一一一一.一一一一一一s一圈1带公差界限的控制髓(图lj,并假定分布中心CL与公差中心Tm重台,上,下控制界限之间的区域用】来表示,上控制界限uCL与规格上限su或下控制界限LcL与规格下限s之间的区域用U来表示.规格上,下界限以外的区域用nl来表示.则落入各个区域内点子的统计意义,可用表l来说明.表1各区域内点子的统计意义区域落入该匹域内点子的统计意义该区域为控制区.落入控制区的点子.大概率是受控状态,表示生产过程稳定,工序处于受控状l志其置信度取决于昕选的0值.表明这种情况下生产出来的产品合格率一般能达到帕.7该区域为警戒区.落八警戒区的点子,是异常点子.说明质量的分布状态起了显着变化.(0变【l太.或l|偏离控制中心线.)失控的点子中有町能包含着一定量的不符合技术要求的产品该区域为废品区.落入废品区的点子,大概率为失控程度严重.表示生产过程不稳定,工序处于l¨严重失控状态,废品率明显上升,有叮能出现成批报废.在分布的离散程度具有趋向性地渐渐变小时,其工序能力指数必然会随之变大,因而规格界限与控制界限之间的区域【【会随之扩大.如果我们假定工序能力6o,T,质量的分布界限为3o,而且一?T"t公差的中心值)时,那么,警戒区U的幅度就会显着缩小,而控制区l则必然会相应扩大,由于控制界限仍符台3o原则,因此扩大后的控制区(区域I)的控制界限仍维持着应有的检出能力由此,我们可以引进一个警戒系数的概念,取x控制图的警戒系数为Aw,-X.控制图的警戒系数为A并根据平均极差的大小来确定警戒区的大小.这样能够压缩警戒区的领域,避免产生完全符台技术要求和达到控制精确嚏(3o原则)要求的所谓失控点子.三,控制界限的修正应用警戒系数的概念,可以用下列修正公式来取代标准的控制图公式,将控制界限作一变换.用uRL育和uRL鼢别代替uc和UC,URL嗣nuR【分别是经修正后的一R控制图被一R控制图中的控制图被控制图的9~-控制图的应用?…一...一一~一..'一~上控制界限.用LRLt和LRh分别代替LCLt和LCL,, LRL和LRh分别是经修正后的x—R控制图和曼一R控制图中的控制图控制图上的下控制界限.对一R控制图的x控制图进行修正可得: URL=S一AwRLRLT=SL+AwR对一R控制图的控制图进行修正可得: URLy=S.一ARLRL=SL+A#疑这里的Su为规格的上界限,S为规格的下界限,曩为平均极差.上述公式分别用警戒系数A和A苷来代替控制图确定控制界限时所采用的系数A和m,A,这里的区别在于:A和A.用来决定警戒区区域的大小,而和m,A2则用来决定控锏区区域的大小.一般来说,标准型一R控制图或一R控制图,其收集的数据组越多,则所得控制界限越小,而修正型控制界限却相反,前者以分布中心为准,而后者在保证CP ≥l的条件下,以规格界限为准.在计算标准型控制界限或修正型控制界限时,推荐选用表2所列的有关系数.表2控制界阳用系数表,\系数ADjATT1】AAn\d21.8803.2670.886'07791.880O.7181.O232.5730.5910.7491.1870.58840.729——{2.2820.4860.728O.79606605.S772.il504300.7130.691059760.4832.O040.395O.7010.549063770.419lJ-0761.蛇40.370O.6920.5090.6028l1_373I161.8640351O.6800.昭2062l.330.[841.dO.357O.6730.4120.5981003I}8I12231.770.325O.66603630.61i四,观察与分析生产现场应用控制图的目的在于控制工序的稳定.如果控制图上显示出非管理状态,那必然是工序发生了异常,需要采取措施.经修正控制界限的又控制图及控制图的观察方法基本上与普通的控制图雷同:首先看各点子是否都在控制界限之内,点子越出界外(包括落在线上的)即为异常.接着看界内点子的排列是否有缺陷,即点子应体现只受偶然因素影响,不受系统因素影响.由于经修正后的界限,其实际分布中心往往和所取的控制中心线有偏移,因此在观察10时,就不能刘板地把大多数点子位于中心线一侧作为判断异常的依据.例如以某质量控制点收集的数据作图,.在X控制图上打点的四十个点子中,就有34点在总体中心线CL=的(上方)一侧,若以该批样本数据的均值为中心,则两侧的点子数就基本上相同(19;21),因而采用修正界限的控制图时,一侧性问题,一般可以不予考虑.采用修正型控制界限,由于控制区域扩l夫,使不少原来界外的点子,落入了修正界限之内.能够大幅度地降低调整的工作量.一...~......一......一...一~~~...一~......一...一一~.--一一.-.控制图的庙片j' 五警戒系数的确定表2所列的警戒系数Aw和A拍q依据是什么呢?是休氏区分两类质量因素的理论,即以30作为控制原则.通常又R控制图的X控制界限由公式130f或!A来确定,其中公式A中的系数A=兰d,因此在总体参数u和0未知时,可以通过子样用系数A来估算x控制图的控制界限.由于T±3o=十三√n,因此,当用聂/d来估计o,并用估计时,则得:-,一'±A2R:又id2R现在假定工序能力指数CP值为l,上,下控制界限的区域可以应用3o来对工序进行控制,只要分布的集中位置没有发生显着变化,工序就处于稳定状态.修正型控制界限是建筑在扩大控制区域,而又能维持工序能力指数为1时的警戒区应具有的警戒区域.以X—R控制图的x控制图的界限修正为侧:.=去=击=器~……c】)夸CP=l则R:_『Td:……(2)设CP=1时,两种界限值一致即UCL=URLi (3).+A2R=S一A_RAR=s.一一A2茛.当8=0时,即分布中心和公差中心T重叠时,那么=Tx,ifi.f1.s.一丈=÷T.A=一A (4)用式(2】代入式(4)得:?得A'下一'了/=五3最终得Aw=÷一A2 (5)例如当n=5时,利用公式(5一)可以求出警戒系数Aw.首先从数理统计表中查出n=5时的A和d2,接着把查得的A2=0.577和dz2.326 代入式(5)因此得Aw-主一A壶一o.557a2Z?zb=1.2898—0.557=0.7l28--'0.7l3同样方法可以求出FI=2~lO的各个Aw 系数值.其数值参见表2.据此推广应用,也可以求出一R控制图的文控制图的警戒系数A.设CP=l则UCL=URLr就是文tn3A2R=s一A《RA=S.文一m3A2录当£+0时则柚R=T—m,A裒:(6)f7)'c=而T::=d得R:代入式(7)b即Ai3一mA…-(8)用这一公式可以求出警戒系数A诺修正控制界限的常用数据可查阅本文表2.从警戒系数A中看出.在两个相邻的样-控皋U图的应用-一.'.一一.'.一一一一一一一一一一....'.一' 书个数之间.样本数人的偶数样串的中位数控制图的警戒系数A反而比其数目大的奇数样本的大.并没像A稍B样,随样本数增大而有规律地减小;因而系数呈参差不齐的锯齿状:(并且随着样本数增大.系数值逐渐趋近)这是由于偶数中位数取中间两个数均值的缘故一六,灵活应用在应用修正型控制图时,如果工序能力指数相当充分,此时町以相应修正警戒系数数值.适当扩大警戒区的区域.减少发生第二种错误的概率.在修正A和Aw时.应似据工序隧力指数的人小,选择相应的修正工序能力指数数值为确保使用的修IF型控I图的经济,有效,适当扩大控制区域,对维持g6ff,J俭出能力具有实用意义=推荐的修正工序能力指数如表3所示表3修正指数参数表工序能指敬cpf修正工序能州数值cp-25i1.1.~.{.1lII.1.Ic¨上L;1.表41学正的警戒系数===■AAn,,,.1.11.!I.g31.1J.21.诳1.I:J1.1{【lIJ.6551.㈨{1.J1ll1.633l】.}127I.II-I.335I).0.虬11.17lI).H7J.1)21【.:川I).)l1.坼【.1{3)『1.HJ21).J711.J3Ll一).21c_857【.1)25.2cII).l={}lI.一f"{I).75}lJ_町3【.1l27r).XO2lJ_0【3J.一i57I1.7I2lc.820.811.85lI.H【lI.I)27I-.2il1.83【.91;H一).77lc_(1HI.|l(J【1.舯1l}.93【lII}.76lI..(;2I-.ll_7¨)【1.8(17l}?93【'为了计算的方便,将修正指数Cp【为1.1,I.2和1.33时的相应修正警戒系数A.w和A面值列一表式(表4)可供使用时参考.如果在使用修正型控制图的过程中,证实工序的分布中心和公差中心一致,则可以进而改用预控图.其效果将会更佳一一般说来,标准型控制图,修正型控制图和预先控制图三者可以根据工序的历史和工序能力的变化情况相互转化:在工序情况不太明嘹的情况下,可以先应用标准型控制图:随着对工序稳定性确认.在充分掌握工序能力指数在1.33以上的历史资料之后.町以修正控制图的控制界限,以减少因虚假警报而调整工序的频次.如果修正界限的控制图使用情况良好,工序一直处于较稳定的状态,则可以进一步改用预先控制图.町以省去计算样组平均值和扳差的麻烦.甚至以在操作人员十分熟悉工序的前提下.作检测不打点,以预控限来监察工序,达到简便地一12控制工序质量的目的.七,结论在xR,R控制图中,X和控制图主要是反映和控制样组分布的集中位置.而R控制图则反映和控制样组分布的离散程度在工序能力指数^=或者等于】.33时.只要分布的离散性没有显着变化,分市的集中位置即使偏离0.其分布晦线仍位丁经修正的控制界限之内因此落在控制界限之内的点子.都能判断为处f受控状态的JE常点子.宴践证明,应用修正控制界限的方法,其控制效果仍旧十分良好,即能在维持其置信度的前提下,允许比标准控制界限有更宽阔的控制区域.从而I丁以大量减少调整工序的时问. 因此无链是一种值得夫力推广应用的经济.fI 效,实用的控制图法。
SPC介绍V1.1
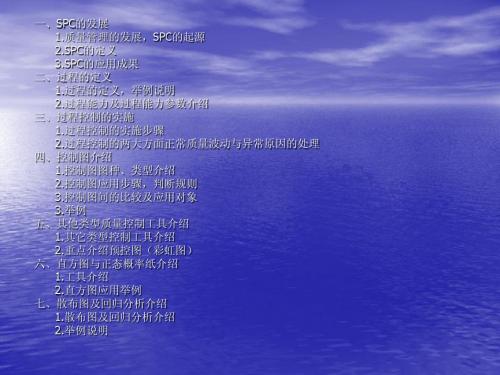
过程能力指数
• 过程能力指数指过程能力满足规格质量要
求的程度。符号记为CP
CP = T/B = T/6σ=TU – TL/6σ = TU - TL/6S 式中: • T—产品质量特性值的规格质量要求,即公 差范围: • TU—上公差(规格)界限: • TL—下公差(规格)界限: • σ—产品质量特性值总体分布标准差: • S—产品质量特性值样体分布标准差: • CP—产品质量特性的过程能力指数: • B—过程实现产品质量特性的过程能力:
统计过程控制理论的发展
• SPC理论和控制图方法的应用就是实现全过程的预防的最
有效的方法。然而,常规控制图的应用捕捉到过程中的异 常先兆,但并不能告知是何种异常,何处异常,异常的原 因是什么,即不能实现对过程异常的诊断。 1982年张公绪教授提出两种质量诊断理论,开辟了统计质 量诊断理论的新方向,使统计过程控制(SPC)上升为统 计过程控制诊断(SPCD),也就是进入了统计过程控制 发展的第二阶段。 20世纪末,SPCD又发证为SPCDA(统计过程控制、诊断 与调整),是统计过程控制发展的第三阶段。
1)计量值控制图 • 以正态分布为理论基础所设计的控制图。 计量值控制图所控制的是计量值数据正态 分布的样本分布特征值;常用的计量值控 制图有以下四种: • 1.均值-标准差控制图( ); • 2.均值-极差控制图( ) • 3.中位数-极差控制图( ) • 4.单值-移动极差控制图( )
2)计数值控制图 • 计件值控制图和计点值控制图。计件值控 制图的控制对象以二项分布为理论基础所 设计;计点值控制图的控制对象以泊松分 布为理论基础设计。 • 1.不合格品率控制图(P控制图) • 2.不合格品数控制图(Pn控制图) • 3.缺陷数控制图(C控制图) • 4.单位缺陷数控制图(U控制图)
预控图

目标:掌握预控图基本原理及使用方法
• 主要内容: • • 预控图的基本概念 • • 预控图的使用方法
一:预控图基本概念
又叫彩虹图,是一种基于规格界限来控制过程的简单运算法则图, 通 常预控图控制区域分为三个: 目标区、警戒区、不良区。
预控图的优点
• • • • • • • 1、所需的数据比控制图少,减少了工作量; • 2、控制规格与公差规格相同,简单易懂; • 3、可以及时发现趋势,起到预防作用; • 4、可适用于小批量生产,灵活有效; • 5、计量型和计数型都可适用; • 6、使用颜色表示工序状态,直观易懂。
• 每天的生产是从上午9点开始的,该质检员测得9点钟生产的头5个产 品和10点钟生产的5个产品的尺寸。
时间
9点 10点 5.013 5.019 5.011 5.017
产品样本
5 5.011 5.018 5 5.2 5.2
该质检员认为当时的生产是正常的,如果使用预控 图,您会得出什么结论?生产过程是否需要调整? 从什么时候就应该开始调整?
使用预控图的口诀: “ 有个红灯就得停; 两个黄灯也不行; 一绿一黄没关系; 两个绿灯肯定行!”
例如:
启动生产过程,进行首件检验几种情况
பைடு நூலகம்
X X X
X X
X XX
XXXXX
X
三、预控图实施案例
一个专业生产套管的工厂,其产品 5±0.02cm,该公司以前的质量控制方法是质 检员每隔1个小时到生产现场抽取连续生产 的5个产品,如果存在尺寸超差的情况,就 马上采取措施。不幸的是,尽管采取了这 么“严格”的质量控制手段,该公司依然 存在7%左右的不合格品率,看来尺寸超差 的现象还是没有被控制住!
二.预控图使用方法
预控制图培训资料

1、 工程规范上线USL:表示产品特性的规格上限,如板厚1.5mm,公差为±0.13时,其USL为1.63 2、 工程规范下线LSL:表示产品特性的规格下限,如板厚1.5mm,公差为±0.13时,其LSL为1.37 3、 中心线SL:表示产品特性的规格中心线。
录中。测量的结果根据以下规则处理: a) 2件全落入绿区,过程正常。继续执行。 b) 2件中1绿1黄,过程正常。继续执行。 c) 2黄分别在两个区域。过程不正常。认为标准偏差过大。
采取纠正措施。即分析造成数据分散的原因,消除原因, 调整过程,再从第1条开始。 d) 2黄落在同一个区域。过程不正常。认为数据中心偏离过 大。要分析造成数据中心偏移的原因,采取纠正措施。然 后,从第1条开始。 e) 只要有1个落入红色区域,认为过程能力不满足要求,要 采取纠正措施,从第1条开始。
预控制图的使用步骤
1、开班时,检验员连续抽取5个产品,测量该特性值并填写在 《预控制图数据表》中,(对于预控制图数据中填写了数据 的,在该产品的首件两检卡中不用再重复填写,只需将首件 产品放置在首件两检台上)。如果:
a) 全部落入目标(绿色)区域。则认为该过程特性的数据分 布中心和规格中心是重合的。过程能力是满足要求的。即认 为是正常生产,可以执行第2条。
预控制图
预控图的概念及说明
预控图(PRE—Control),又叫彩虹图,是一种基于规格界限来 控制过程的简单运算法则图,是美国Rath & Strong咨询公 司于20世纪五十年代开发的。早在20世纪20年代,美国贝 尔实验室的科学家休哈特发明了休哈特控制图,它是基于 产品的生产过程连续稳态,并且质量特性的分布是在正态 或接近正态分布的情况下运用。而预控图只是假设生产过 程中产品的质量特性是可测量和可调整的,它并未假设为 某一分布和稳定的分布。休哈特控制图是用3σ原理设置控 制限,预控图是以规格限设置控制限,警戒区设计在规格 限内。
关于控制图以下陈述正确的是
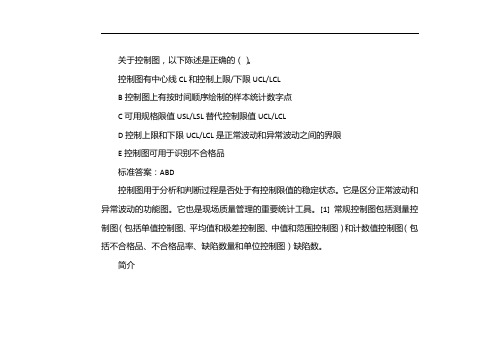
关于控制图,以下陈述是正确的()。
控制图有中心线CL和控制上限/下限UCL/LCLB控制图上有按时间顺序绘制的样本统计数字点C可用规格限值USL/LSL替代控制限值UCL/LCLD控制上限和下限UCL/LCL是正常波动和异常波动之间的界限E控制图可用于识别不合格品标准答案:ABD控制图用于分析和判断过程是否处于有控制限值的稳定状态。
它是区分正常波动和异常波动的功能图。
它也是现场质量管理的重要统计工具。
[1] 常规控制图包括测量控制图(包括单值控制图、平均值和极差控制图、中值和范围控制图)和计数值控制图(包括不合格品、不合格品率、缺陷数量和单位控制图)缺陷数。
简介世界上第一个控制图是由美国贝尔电话实验室质量研究组过程控制组学术带头人休·哈特博士提出的。
[3]随着控制图的诞生,控制图已成为科学管理的重要工具和不可缺少的管理工具。
它是一个带有控制边界的图形,用于区分原因是偶然的还是系统的。
它可以提供有关系统存在的信息,并确定生产过程的受控状态。
[1] 根据其用途,控制图可分为两类。
一种是用于分析的控制图,用于控制生产过程中质量特性值的变化,以检查过程是否处于稳定受控状态;另一种控制图主要用于发现生产过程中是否存在异常。
防止生产不合格产品。
定义控制图又称控制图,是通过统计方法设计的用于测量、记录和评价过程质量特性的图表,以监视过程是否处于受控状态。
图中有三条平行于水平轴的直线:Cl(中线)、上控制限(UCL)和下控制限(LCL),并按时间顺序提取样本统计的跟踪序列。
UCL、Cl和LCL统称为控制限值,通常设置为±3个标准偏差。
中心线是受控统计的平均值,控制上限和下限与中心线之间的距离是标准偏差的几倍。
如果控制图中的跟踪点不在UCL和LCL 之外,或者UCL和LCL之间的跟踪点排列不是随机的,说明过程异常。
[4]控制图解释1实时图形反馈处理工具。
2设计的目的是告诉操作者什么时候做或不做。
- 1、下载文档前请自行甄别文档内容的完整性,平台不提供额外的编辑、内容补充、找答案等附加服务。
- 2、"仅部分预览"的文档,不可在线预览部分如存在完整性等问题,可反馈申请退款(可完整预览的文档不适用该条件!)。
- 3、如文档侵犯您的权益,请联系客服反馈,我们会尽快为您处理(人工客服工作时间:9:00-18:30)。
预控图(PRE—Control):小批量生产过程的质量控制工具
预控图的概念及说明
预控图(PRE—Control),又叫彩虹图,是一种基于规格界限来控制过程的简单运算法则图,是美国Rath & Strong咨询公司于20世纪五十年代开发的。
早在20世纪20年代,美国贝尔实验室的科学家休哈特发明了休哈特控制图,它是基于产品的生产过程连续稳态,并且质量特性的分布是在正态或接近正态分布的情况下运用。
而预控图只是假设生产过程中产品的质量特性是可测量和可调整的,它并未假设为某一分布和稳定的分布。
休哈特控制图是用3σ原理设置控制限,预控图是以规格限设置控制限,警戒区设计在规格限内。
为了应用方便,通常预控图控制区域分为三个:目标区、警戒区、不良区,见下三种图形。
预控图的基本思想
预控图是一种非常简便的质量控制工具,其基本思想如下:
(1)过程开始前预先控制。
(2)预控图直接与规格(公差)界限相联系,易于理解。
(3)不需计算控制界限,直接用单个样品的实测值对过程做出判断。
预控图的建立
首先第一步要做的是应用预控图的资格确定,相当于制作休哈特控制图的“分析用控制图”。
一般取5个样品进行测量,如果5个样品的测量数据全部落在目标区域,说明过程均值基本没有大偏移,可以使用预控图。
但是,只要有1个样品的测量数据落在目标区域之外,则需要对过程进行整顿调整,直至5个样品数据全部落在目标区域以内。
在判定满足预控图
的应用条件之后,即可进行预控图的操作。
每一次抽样抽两个产品单元A、B,周期性地连续测量A、B一对产品的数据,如果数据都落在一个警戒区,说明过程的均值有偏移,过程需要暂停生产,进行调整;如果分别落在两边的警戒区,说明过程的变异变大,过程需要整顿,调整标准偏差;如果任何一个落在不良区,过程都需要整顿,其它过程无需整顿调整。
预控图的优点
1、预控图具有抽样检测工作量少和简单易懂的程序,以及合理的统计原理,困此它为操作者的工序质量控制提供了一种有效的方法。
2、对操作者素质的要求一般均可达到。
顼控图要求操作者满足以下三点要求操作者必须知道工序产品什么才是合格f操作者具有判断产品是否合格的工具(量具、标准、仪器);当工序发生偏差时,操作者必须能够进行修正。
以上这三点要求是对任何操作者自控的工序应必备的先决条件。
3、使用预控图可以较好地调动操作者在质量管理中担负起责任。
通过实施预控图,操作者要密切地观察操作过程,不断地确定产品是否合格,工序是否需要调整。
由于预控图很少发出错误信息,从而减少不必要的调整,这不仅使操作者对预控法建立了信心,而且对生产优质产品的能力也产生了更大的自信心。
4、常规控制图按其控制对象分为计量值控制图与计数值控制图。
但预控图不仅适用于计量值也适用于计数值(过或不过)的情况。
对于计量值数据,可在量具的,测量面上中心部位涂以绿色,在其外涂以黄色,规格界限外涂以红色。
利用这种量具就会使操作者很快知道应继续生产、停止生产还是应当提起往意再测量第二个产品,而不一定要读出具体的测量值。
对于过与不过的计数值情况下,除了有标示公差界限的一般量规以外,还可提供预控线或绿区界限的量规。
这样就使预控图具有更广泛的应用场合。
预控图的使用规则
•2个数据点落在绿色区域,继续运行该过程;
•一个数据落在黄色区域,一个数据落在绿色区域;
•2个点落在黄色区域(同一区),调整过程;
•2个点落在黄色区域(相反区),停止过程,并调查;
•1个点落在红色区域, 停止过程,并调查;
•每当过程被调整,在开始取样前,过程生产的5个连续的零件必须落在绿色区域。
使用预控图的注意事项
1.绘制控制图时所抽取的管理用数据,不须以工序稳定状况下为前提,否则,所计算出的控制上下线有可能超过公差范围。
2.使用控制图时注意与标准化操作结合起来,例如对孔加工来说,可根据孔径的规格范围分别采用铰刀、浮动铰刀加工或单刀光孔。
3.抽样时问应从过程中工艺状况的变化情况而定。
4.控制图应在生产现场中及时分析。
如果发生异常,应先从取样、计算、打点等问题检查无误后,再从生产方面找原因。
5.当工艺手段已发生变化,或原有控制图已使用了较长时间,应重新复审预控制图。
6.预控图将正常状态判断为异常,风险率约为2.5%,将异常状态列为正常而误报警的可能性约为2%。