高铬铸铁的切削用量优化计算
切削用量三要素计算公式

切削用量三要素计算公式切削用量三要素计算公式是指在切削过程中,根据切削速度、进给速度和切削深度来计算切削用量的公式。
切削用量是切削过程中切除材料或切削液的量,是衡量切削过程中切削效果的一个重要指标。
在切削加工过程中,切削用量的合理控制对于提高切削效果、延长刀具寿命和提高加工效率都起到至关重要的作用。
切削用量三要素包括切削速度、进给速度和切削深度。
切削速度是指刀具与工件相对运动的速度,单位通常是m/min。
进给速度是指切削刃每转一周,工件上移动的距离,单位通常是mm/rev。
切削深度是指刀具切削刃在一个工件上的进入深度,单位通常是mm。
切削用量的计算公式为:切削用量=切削速度×进给速度×切削深度切削用量的计算公式可以根据不同的切削形式和加工要求进行调整。
下面将分别介绍一些常用的切削用量计算公式。
1.对于铣削加工:切削用量=切削宽度×进给速度×加工长度其中,切削宽度是指铣刀径向切削刀具之间的距离,通常是成刀具直径的倍数。
2.对于车削加工:切削用量=切削深度×进给速度×加工长度其中,切削深度是指刀具在工件中切削的最大深度。
3.对于钻削加工:切削用量=钻孔直径×进给速度×加工长度其中,钻孔直径是指钻头直径,进给速度是指每转一周,工件上移动的距离。
4.对于镗削加工:切削用量=镗孔直径×进给速度×加工长度其中,镗孔直径是指镗刀直径。
需要注意的是,切削用量的计算公式只是一个理论值,实际加工时往往需要根据具体材料性质、刀具情况、工件形状和加工要求等因素进行适当调整。
切削用量的合理选取对于加工质量的影响非常大。
合理的切削用量可以确保工件表面质量良好,避免切削过程中产生过大的切削力和切削热量,减少工件表面的热影响区,避免刀具磨损过快和强制振动的产生,提高切削效率和工件精度。
因此,在选择切削用量时应充分考虑刀具材料、刀具形状、刀具刃数、切削方式、切削速度和切削深度等因素,并根据实际情况进行调整。
切削用量三要素的定义及公式

切削用量三要素的定义及公式好的,以下是为您生成的关于“切削用量三要素的定义及公式”的文章:在咱们日常的机械加工领域中,切削用量三要素那可是相当重要的角色。
这就好比是烹饪中的盐、糖和酱油,用量合适,才能做出美味的菜肴;在机械加工里,切削用量三要素调配恰当,才能加工出合格又精致的零件。
咱先来说说切削速度,这可是三要素中的“速度担当”。
切削速度就是刀具切削刃上选定点相对于工件的主运动的瞬时速度。
想象一下,你拿着一把锋利的刀,快速地在一块木头上划过,这个划过的速度就是切削速度。
公式是 v = πdn/1000 ,这里的 v 表示切削速度,d 是工件待加工表面或刀具的最大直径,n 是主运动的转速。
给您举个小例子吧,我之前在工厂实习的时候,有一次师傅让我加工一个圆柱形的零件。
我一开始没太注意切削速度,就按照自己的想法随便调了机器的转速。
结果呢,加工出来的零件表面那叫一个粗糙,简直没法看。
师傅过来一看,就指出是切削速度不对。
后来在师傅的指导下,我重新计算并调整了切削速度,加工出来的零件那表面光滑得跟镜子似的,我当时心里那个美啊!接下来聊聊进给量,它就像是你一步一步往前走的步伐大小。
进给量是刀具在进给运动方向上相对工件的位移量。
用 f 来表示,单位通常是 mm/r 或者 mm/行程。
比如说车床上车削螺纹,每转一圈刀具沿着轴向移动的距离就是进给量。
有一回,我们车间接到一个紧急订单,要加工一批细小的轴类零件。
我负责其中一部分,为了赶进度,我把进给量调得过大。
结果零件的尺寸偏差超出了允许范围,差点就造成了损失。
这让我深刻认识到,进给量可不能随意乱调,得根据具体的加工要求来。
最后说说背吃刀量,这是刀具切入工件的深度。
就好比你切西瓜,切下去的厚度就是背吃刀量。
用 ap 表示,单位是 mm 。
记得有一次,我在加工一个比较厚的金属板,一开始背吃刀量设置得太小,加工效率特别低,半天也没弄出个样子来。
后来我大胆地增加了背吃刀量,效率一下子就提上去了,但同时也要注意刀具的承受能力,不能一味地加大,不然刀具可能会受损。
切削用量三要素计算公式

切削用量三要素计算公式在机械加工过程中,切削用量的合理选择对于加工工件的质量、加工效率和工具寿命等方面都有着重要的影响。
切削用量的三要素包括切削速度、进给量和切削深度。
这三个因素的选择需要根据工件材料、切削工具和加工要求等因素综合考虑,以保证加工质量,并尽可能提高加工效率。
切削速度是指工件表面上单位时间内被切削掉的长度。
它是切削用量中最为重要的因素之一。
切削速度的选择受到工件材料的硬度、切削工具的材料和切削方式的影响。
一般来说,对于硬度较高的材料,切削速度应适当降低,以防止切削工具磨损过快。
而对于切削工具材料较硬的情况,可以适当提高切削速度,以提高加工效率。
切削速度的计算公式为:切削速度= π × 刀具直径× 主轴转速。
进给量是指切削刀具在单位时间内沿工件表面的运动距离。
进给量的选择需要考虑工件的尺寸和形状、切削工具的尺寸和形状以及加工要求等因素。
进给量的过大会导致切削力增大,加工表面粗糙度增加,甚至引起振动和切削工具断裂等问题;进给量过小则会降低加工效率。
因此,进给量的选择应该在保证加工质量的前提下尽可能提高加工效率。
进给量的计算公式为:进给量= 主轴转速× 进给速度。
切削深度是指切削刀具刀尖与工件表面的最大距离。
切削深度的选择需要考虑工件材料的硬度、切削工具的材料和刚性,以及加工要求等因素。
切削深度过大容易导致切削力增大,加工表面质量下降,甚至引起切削工具折断等问题;而切削深度过小则会降低加工效率。
切削深度的计算公式为:切削深度= 主轴转速× 进给速度/ 切削速度。
切削用量的合理选择对于机械加工过程至关重要。
通过对切削速度、进给量和切削深度三要素的合理计算和选择,可以最大限度地提高加工效率,保证加工质量,延长切削工具的使用寿命,从而达到经济高效的加工目的。
在实际加工过程中,需要根据具体情况进行调整和优化,以获得最佳的切削效果。
同时,还需要注意切削条件的稳定性,以确保加工过程的安全性和稳定性。
切削用量的选择和计算公式

切削用量的选择和计算公式切削用量的选择和计算是机械加工中非常重要的一环,它直接影响到加工效率、加工质量和工具的使用寿命。
正确选择和计算切削用量可以使加工过程更加稳定和高效。
本文将介绍切削用量的选择和计算公式,并探讨其在机械加工中的应用。
切削用量的选择。
切削用量是指在切削加工过程中,刀具与工件之间的相对运动距离。
切削用量的选择需要考虑到工件材料、刀具材料、切削速度、进给速度等因素。
一般来说,切削用量越大,切削效率越高,但是过大的切削用量会导致刀具磨损加剧,甚至损坏刀具。
因此,在选择切削用量时需要在保证加工效率的前提下,尽量减小刀具的磨损。
切削用量的计算公式。
切削用量的计算公式通常包括切削速度、进给速度和刀具的切削刃数。
切削速度是指刀具在工件表面的相对运动速度,通常用Vc表示,单位为m/min。
进给速度是指刀具在工件表面的进给速度,通常用f表示,单位为mm/r。
刀具的切削刃数是指刀具上切削刃的数量,通常用z表示。
根据切削速度、进给速度和刀具的切削刃数,切削用量的计算公式可以表示为:切削用量 = 切削速度×进给速度×刀具切削刃数。
在实际应用中,切削用量的计算公式可以根据具体的加工情况进行调整,以满足加工的要求。
切削用量的应用。
切削用量的选择和计算在机械加工中具有重要的应用价值。
正确选择切削用量可以提高加工效率,降低成本,提高产品质量。
同时,合理的切削用量还可以延长刀具的使用寿命,减少刀具的更换次数,降低加工成本。
在实际加工中,切削用量的选择和计算需要结合具体的加工情况进行调整。
例如,在加工硬质材料时,可以适当增大切削用量,以提高加工效率;在加工精密零件时,可以适当减小切削用量,以保证加工精度。
此外,切削用量的选择还需要考虑到刀具的类型、刀具的磨损情况、工件的材料和形状等因素。
总之,切削用量的选择和计算是机械加工中非常重要的一环。
正确选择和计算切削用量可以提高加工效率、降低成本、提高产品质量。
《切削用量》说课稿
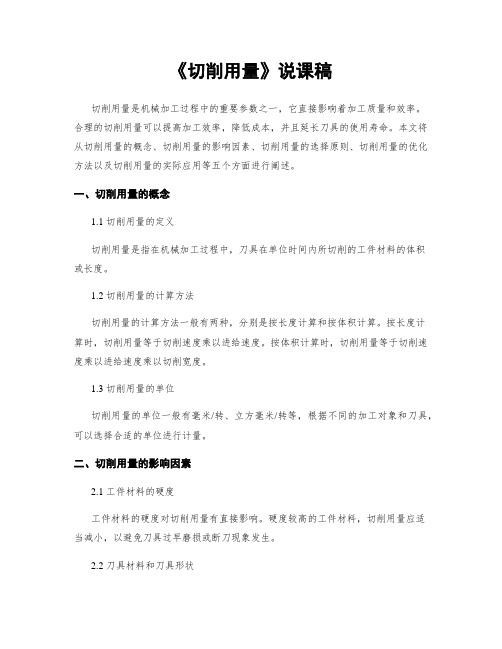
《切削用量》说课稿切削用量是机械加工过程中的重要参数之一,它直接影响着加工质量和效率。
合理的切削用量可以提高加工效率,降低成本,并且延长刀具的使用寿命。
本文将从切削用量的概念、切削用量的影响因素、切削用量的选择原则、切削用量的优化方法以及切削用量的实际应用等五个方面进行阐述。
一、切削用量的概念1.1 切削用量的定义切削用量是指在机械加工过程中,刀具在单位时间内所切削的工件材料的体积或长度。
1.2 切削用量的计算方法切削用量的计算方法一般有两种,分别是按长度计算和按体积计算。
按长度计算时,切削用量等于切削速度乘以进给速度。
按体积计算时,切削用量等于切削速度乘以进给速度乘以切削宽度。
1.3 切削用量的单位切削用量的单位一般有毫米/转、立方毫米/转等,根据不同的加工对象和刀具,可以选择合适的单位进行计量。
二、切削用量的影响因素2.1 工件材料的硬度工件材料的硬度对切削用量有直接影响。
硬度较高的工件材料,切削用量应适当减小,以避免刀具过早磨损或断刀现象发生。
2.2 刀具材料和刀具形状刀具材料和刀具形状对切削用量也有重要影响。
一般来说,刀具材料较硬、刀具形状较尖锐的刀具可以采用较大的切削用量,而刀具材料较软、刀具形状较圆钝的刀具应采用较小的切削用量。
2.3 加工精度要求加工精度要求高的工件,切削用量应适当减小,以保证加工质量。
而对于加工精度要求较低的工件,可以适当增大切削用量,提高加工效率。
三、切削用量的选择原则3.1 切削用量与切削力的关系切削用量与切削力有密切关系。
一般来说,切削用量越大,切削力也越大。
因此,在选择切削用量时,需要综合考虑切削力的大小,以避免过大的切削力对机床和刀具造成损坏。
3.2 切削用量与切削温度的关系切削用量的大小也会影响切削温度的升高。
较大的切削用量会导致切削温度升高较快,因此在选择切削用量时,需要考虑切削温度的限制,以避免刀具因过高的温度而失效。
3.3 切削用量与切削表面质量的关系切削用量的大小对切削表面质量也有一定影响。
华菱立方氮化硼刀具加工高铬铸铁的切削参数

华菱立方氮化硼刀具加工高铬铸铁的切削参数一、高铬铸铁的机加工和刀具的选用高铬铸铁是一种高硬度高强度的具有抗磨耐腐性能的高合金白口铸铁,高铬铸铁作为耐磨铸件在不做任何热处理的情况下,硬度一般在HRC45以上,抗拉强度为650~850MPa。
高铬铸铁作为难切削材料之一,硬质合金刀具很难正常加工,而陶瓷刀具由于脆性大的原因,一般只用于精加工中;在90年代以前由于难于切削的原因在一定程度上限制了高铬铸铁的应用,随着新的刀具材料的出现,高铬铸铁行业机加工刀具经历了由硬质合金到复合陶瓷再到立方氮化硼材料的过程,在一定程度上改变了高铬铸铁机加工工艺和设备投入, 也带来了高铬铸铁铸件作为抗磨铸件在工业制造领域的一度繁荣。
2003年以前由于受刀具材料的限制,硬质合金刀具和复合陶瓷刀具是加工高铬铸铁的主流,高铬铸铁加工工艺路线一般为:毛坯—软化处理(降低硬度)---粗加工----热处理(提高硬度)---精加工。
从工艺路线可以看出,两次热处理和两次装夹,不但增大了工作量,影响加工效率,也增加了机加工成本。
据统计,仅软化处理和两次机加工就使成本增加2500一3000元/吨。
华菱超硬2003年研发的BN-K1牌号立方氮化硼材料刀具,由于硬度比硬质合金和陶瓷高,而抗断裂性和抗崩损性能比陶瓷刀具高,作为高硬度铸铁常用刀具牌号,被广泛应用于35HRC—68HRC的高硬度铸铁的粗加工、断续加工和精加工。
与陶瓷刀片相比,BN-K1牌号氮化硼刀片的硬度一般在3500HV左右,是陶瓷刀片的2倍,是合金刀片的4倍。
BN-K1牌号的耐热性可达1400~l500℃,BN-K1牌号加工高铬铸铁时,在1000℃时的硬度还要高于陶瓷和硬质合金的常温硬度,高速切削高硬度白口铸铁Cr26时,BN-K1牌号刀具的耐磨性是氮化硅陶瓷的25倍,抗冲击能力是氮化硅陶瓷的2000多倍,刀具寿命可以达到氮化硅陶瓷的22~30倍。
因此BN-K1牌号刀具的切削参数比硬质合金刀具高3~5倍的速度切削高温合金和淬硬钢,这也为PCBN刀具的高速切削创造了条件。
切削用量的计算公式

切削用量的计算公式
切削用量是指在进行机械切削加工时,所使用的工具(如车刀、铣刀等)在单次切削中移除的工件材料量。
计算切削用量是非常
关键的,因为它能帮助工程师在进行加工计划时掌握切削效率和
工具寿命,从而提高加工效率和降低成本。
在进行切削用量的计
算时,可以使用下面的公式:
切削用量 = 切削速度 ×进给量 ×切削深度
其中,切削速度是指在切削工件时,工具相对于工件的线速度;进给量是指工件和刀具的相对运动速度;切削深度是指每次切削
中刀具与工件的最大接触深度。
以下是针对公式中各个参数的详细解释:
一、切削速度(Vc)
切削速度是指在进行切削加工时,工具相对于工件的线速度。
它的单位通常是米/分钟(m/min)。
切削速度的大小对工具寿命
和加工效率都有着重要的影响。
切削速度过高会导致工具快速磨损,而切削速度过低则会降低加工效率。
因此,工程师需要在选
择切削速度时,综合考虑工件材料、刀具材料、切削形式等因素。
二、进给量(f)
进给量是指工件和刀具的相对运动速度,通常以每转进给量(mm/r或inch/r)的形式来表示。
它是影响切削用量的另一个重要因素。
进给量过大会导致工件表面质量下降,而进给量过小则会减缓加工速度。
三、切削深度(ap)
切削深度是指每次切削中刀具与工件的最大接触深度。
切削深度过大会导致工具承受较大负荷,容易磨损,而切削深度过小则会影响加工效率。
综上所述,通过合理设置切削速度、进给量和切削深度,可以掌握切削用量的计算方法,提高加工效率和降低成本。
高铬铸铁铸造工艺加工刀具及切削参数

高铬铸铁铸造工艺加工刀具及切削参数高铬铸铁成分及性能高铬铸铁属金属耐磨材料、抗磨铸铁类铬系抗磨铸铁的重要分支,是继普通白口铸铁、镍硬铸铁而发展起来第三代白口铸铁。
1,高铬铸铁生产及铸造工艺1,出炉温度高铬铸铁的熔点比一般铸铁高约铸铁高,约1200摄氏度,出炉温度1500摄氏度,熔炼中频感应电炉。
2,炉衬采用酸性或碱性炉衬均可,炉衬的配比、打结、烘干和烧结均按常用工艺进行。
3,装料一般顺序加料,先将灰生铁、钼铁等难容铁合金装入炉底,而后将废钢等按照。
依次装入炉底4,脱氧待金属炉料全部熔化并提温1480摄氏度后再按顺序加工0.5%锰铁硅铁铝进行脱氧。
5,浇注在中频感应炉中融化温度不必太高,温度达到1480摄氏度即可出炉高铬铸铁的硬度KmTBcr12HRC46-56KmTBcr15moHRC46-58KmTBcr26HRC46-56高铬铸铁生产工艺要点1,高铬铸铁铸造性能较差,其热导率低,塑性差,收缩量大,且有大的热裂和冷裂倾向,在铸造工艺上要将铸钢和铸铁的特点结合起来考虑,2,造型宜采用水玻璃硅砂封强度高且透气性好的砂型,涂料耐火度高的高铝粉或镁粉与酒精混合伴制为获得细晶粒组织和好的表面质量,在铸件外形不大复的情况下金属型铸造广泛采用。
3,由于高铬铸件的冒口不易切除,因此造型时在冒口形式上宜采用侧冒口。
高铬铸铁热处理工艺1,退火一般生产中采用快速退火工艺升温至950度并保温三个小时停炉,随后随炉冷却至400度然后打开炉门。
继续缓冷至300一下出炉至室温。
2,淬火将机械加工后的铸件室温装炉缓慢升温至600度并保温半小时半小时不超越过将炉升温至淬火温度950-980度后保温2-4小时3,回火对淬火后的铸件进行230-260的回火处理。
具体工艺为;室温装炉,升温至230-260度保温然后出炉空冷。
4,白口铸铁中国早在春秋时代就制成了抗磨性良好的白口铸铁,用作一些抗磨零件。
这种铸铁具有高碳低硅的特点,有较高的硬度,但很脆,用得最广泛的是含铬量为12%~20%的高铬白口铸铁,组织中形成(cr,Fe)7C3的碳化物。
切削用量的选择与计算

切削用量的选择与计算正确的切削用量,对于保证产品质量、提高切削效率和经济效益,具有重要意义。
切削用量的选择主要依据工件材料、加工精度和表面粗糙度的要求,还应考虑刀具合理的耐用度、工艺系统刚性及机床效率等条件。
由于切削速度V c对刀具寿命影响最大,其次为进给量f,影响最小的是背吃刀量a p,因此,选择切削用量的步骤是先确定背吃刀量a p,再选择进给量f,最后再确定切削速度V c,必要时应校验机床功率是否允许。
所以,其基本原则是:首先应选择一个尽可能大的背吃刀量a p,其次选择一个较大的进给量f,最后,在刀具耐用度和机床功率允许的情况下选择一个合理的切削速度V c。
4.1轴外圆的切削用量4.1.1确定粗车时的切削用量ap1)背吃刀量的a p的选择:工件下料为45号钢棒料,大小为62mm×90mm,粗车至Φ60mm,表面有硬化层、氧化皮或硬杂质等,但在加工余量(指半径方向上)不多并比较均匀,且加工工艺系统刚性足够,应使背吃刀量一次性切除余量A,即:a p=A,查《简明机械加工工艺手册》表11-1可知A=(50-46)/2=2mm,单边留1mm做半精车、精车余量,取粗车背吃刀量a p=1mm。
2)确定进给量f:查查《简明机械加工工艺手册》表11-1可知,f=0.4~0.5mm/r,根据机床说明书,初步选定f=0.45mm/r.3)确定切削速度V c:查查《简明机械加工工艺手册》表11-5可知,V c=2.17~2.667m/s,考虑到进给量较大取V c=2m/s。
4)确定主轴转速n,由公式:n=1000v/πd=(1000×2)/(3.14×60)=10.62r/s 根据机床说明书,取n=12.5r/s。
此时切削速度为:V c=πdn/1000=(3.14×60×12.5)/1000=2.36m/s 此速度小于预得切削速度,故可用。
5)校验机床效率:查《简明机械加工工艺手册》表11-6~11-9可求得切削力的公式及相关数据。
常用切屑用量计算公式

Vc xap xfr xkc P= 60037.2 T= F力 x(D/2) =P x9549/RPM
金属去除率V=115x2x0.2=46 立方厘米每分钟 每加工一个零件的时间=100/(0.2x488)=1.02分钟 镗削功率P=(115x3x0.2x2900)/60037.2=3.35千瓦 镗削力=2900 x0.2 x3=1740牛顿=177.5公斤 镗削扭矩T=1740 x37.5=34牛顿米
P= Kc×f×Vc ×(D2-d2) D × 240000 × η
D: hole diameter d: core diamerer
T= F力 x(D/2) =P x9549/RPM 钻削功率P 钻削功率P=4500 × 0.07 ×40 ×20/240000 ×0.9=1.2KW 转速 n=40 ×1000/3.14 ×20=636rpm 扭矩 T=1.2 ×9549/636=18NM
�
U钻钻削功率和扭矩的计算 Power consuming and Torque force
例:工件材料为高合金钢,硬度HRC50,钻削直径20mm,Vc= 例:工件材料为高合金钢,硬度HRC50,钻削直径20mm,Vc= 40m/min, 0.07mm/r,Kc= 40m/min,f=0.07mm/r,Kc=4500N/mm2,η=0.9,计算钻削功率 0.9,计算钻削功率 和扭矩.
N铝=2388rpm =2388rpm vf铝=2865mm/r vf铝=2865mm/r p铝=9.16kw =9.16kw T铝=36Nm =36Nm N不锈钢=597rpm 不锈钢=597rpm vf不锈钢=716mm/r vf不锈钢 不锈钢=716mm/r p不锈钢=6.87kw 不锈钢=6.87kw T不锈钢=109Nm 不锈钢=109Nm
切削用量计算方法

切削用量计算方法嘿,咱今儿个就来讲讲切削用量计算方法。
你可别小瞧了这玩意儿,它就像是做菜时放调料一样重要呢!切削用量,简单来说就是切削过程中的各种参数,包括切削速度、进给量和背吃刀量。
这三个家伙可不得了,它们直接影响着加工的效率和质量。
先说切削速度吧,这就好比是跑步的速度。
如果跑得太快,可能就会气喘吁吁,甚至摔倒;跑得太慢呢,又达不到效果。
切削速度也是一样,太快了刀具可能磨损得厉害,工件表面质量也可能不好;太慢了又会浪费时间,降低生产效率。
那怎么来确定合适的切削速度呢?这就得考虑好多因素啦,比如刀具材料、工件材料、切削深度等等。
就好像不同的人跑步速度不一样,不同的材料加工时也有不同的“最佳速度”呢!再来说进给量,这就像是你走路的步子大小。
步子太大容易扯着蛋,步子太小又走得太慢。
进给量也是如此,太大了可能会让刀具承受不住,太小了加工时间又太长。
而且进给量还和切削速度相互配合,就像跳舞时的舞步要协调一样,它们得搭配好了,才能跳出优美的“加工之舞”。
最后是背吃刀量,这就像是一口咬下去的食物多少。
咬太多了可能噎着,咬太少了又不解馋。
背吃刀量太大,刀具容易损坏,加工难度也大;太小了又得加工好多遍,太麻烦。
那怎么来计算这些切削用量呢?这可没有一个固定的公式可以套用哦!就好像每个人做饭的口味都不一样,切削用量的计算也得根据具体情况来。
不过呢,一般可以参考一些手册、标准,或者根据经验来估算。
比如说,你要加工一个钢件,你就得先了解钢的硬度、韧性等特性,然后再根据刀具的性能来确定切削速度。
如果刀具很锋利,那切削速度可以适当提高一些;如果刀具一般般,那就得悠着点啦。
还有啊,不同的加工方法对切削用量的要求也不一样。
比如车削和铣削,它们的特点就不一样,所以计算方法也会有所不同。
总之,切削用量计算方法可不是那么简单的,得综合考虑各种因素。
这就像是一场复杂的游戏,你得掌握好规则,才能玩得转。
咱可不能马虎大意,不然加工出来的工件可就不达标啦!所以啊,朋友们,一定要重视切削用量计算方法,把它学好、用好。
第14章切削用量及其计算

第14章切削用量及其计算在机械加工中,切削过程是将刀具与工件之间产生相对运动,通过去除工件上的材料来实现零件加工的过程。
而切削用量是指在每刀刃上所去除的金属材料的量,也是衡量切削工具寿命和加工效率的重要指标之一、本章将介绍切削用量及其计算方法。
切削用量的分类:切削用量可以分为直接切削用量和间接切削用量两类。
1. 直接切削用量是指在每单位时间内切削刀具所切削的长度,通常表示为切削速度(vc)。
切削速度是衡量刀具耐用性的指标,也是衡量加工效率的重要因素之一、一般来说,切削速度越大,切削频率越高,刀具磨损越快。
因此,在选择切削速度时,需要考虑刀具耐用性和加工效率的平衡。
2.间接切削用量是指在每单位时间内切削刀具所切削的体积或质量。
常见的间接切削用量有两种,即单位时间内材料的去除率(Q)和单位时间内材料的切削功率(P)。
切削用量的计算方法:1. 切削速度(vc)的计算:切削速度的计算公式为:vc = (π * D * n)/ 1000,其中D为刀具直径,n为主轴转速。
例如,当刀具直径为80mm,主轴转速为1000rpm 时,切削速度为(π * 80 * 1000)/ 1000 = 251.33m/min。
2.单位时间内材料的去除率(Q)的计算:单位时间内材料的去除率是指每分钟切削的体积或质量,通常用mm³/min或g/min表示。
其计算公式为:Q = (vc * fz * ap)/ 1000,其中vc为切削速度,fz为每齿进给量,ap为切削深度。
例如,当切削速度为250m/min,每齿进给量为0.1mm,切削深度为2mm时,单位时间内材料的去除率为(250 * 0.1 * 2)/ 1000 = 0.5mm³/min。
3.单位时间内材料的切削功率(P)的计算:以上是切削用量的分类及其计算方法。
在实际加工中,根据工件的材料性质、加工要求和刀具类型等因素,选择合适的切削用量,可以提高加工效率和降低刀具消耗,实现经济高效的加工过程。
切削用量及加工余量的合理选择

削用量及加工余量的合理选择切削用量的选择,主要根据刀具耐用度和加工表面粗糟度,加工精度的要求。
切削用量愈大,刀具耐用度愈低。
切削速度Vc,进给量f和切削深度Ap刀具耐用度的影响不同,切削速度影响最大,进给量次之,切削深度影响最小。
(1)切削深度的选择切削深度应根据加工余量确定。
1)粗加工时,在留有精加工及半精加工的余量后,应尽可能一次走刀切除全部粗加工余量。
若粗切余量过大,不能一次切除,这时,应将第一次走刀的切削深度取大些,可占全部余量的2/3~3/4,以使精加工工序获得较小的表面粗糙度值及较高的加工精度。
2)切削零件表层有硬皮的铸、锻件或不锈钢等冷硬较严重的材料时,应使切削深度超过硬皮或冷硬层,以避免使切削刃在硬皮或冷硬层上切削。
(硬皮深度可达0.07~0.5mm)3)当冲击载荷较大(如断续切削)或工艺系统刚性较差时,应适当减小切削深度。
4)一般精切( 1.6!~ 0.8)时,可取=0.05~0.8mm;半精切( 6.3~ 3.2)时,可取=1.0~3.0mm.(2)进给量F的选择1)粗加工时,进给量主要受刀杆、刀具、机床、工件等的强度、刚度所能承受的切削力的限制,一般是根据刚度来选取。
2)精加工时,进给量主要受表面粗糙度要求的限制。
要求表面粗糙度小,应选取较小的F。
但F过小,切削厚度过薄,表面粗糙度反而大,而且刀具磨损加剧。
3)当刀具的副角较大,刀尖圆弧半径较大时,F可选较大值。
(3)切削速度的选择在保证刀具的经济耐用度及切削负荷不超过机床的额定功率的情况下选定切削速度。
1)粗车时,背后吃刀量和进给量均较大,故选较低的切削速度,精车时,则选较高的切削速度。
2)加工材料的加工性差时,切削速度选得低些。
如加工灰铸铁的切削速度比加工中碳钢低;而加工铝合金和铜合金的切削速度比加工中碳钢要高得多。
3)刀具材料的切削性能越好时,切削速度也可以越高。
如涂层硬质合金、陶瓷、金刚石和立方氮化硼刀具的切削速度。
金属切削量计算公式
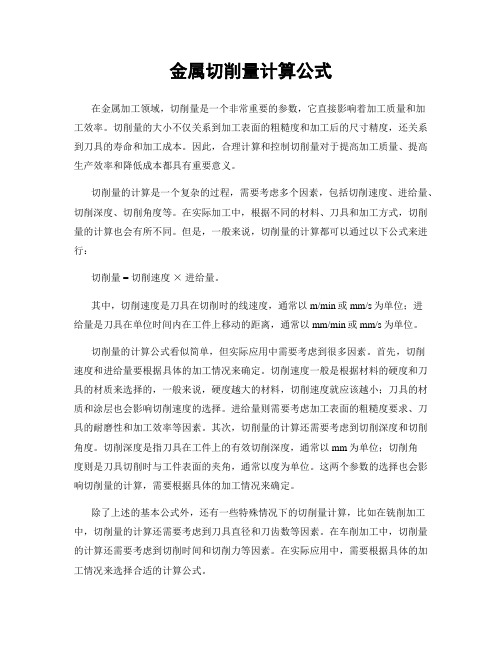
金属切削量计算公式在金属加工领域,切削量是一个非常重要的参数,它直接影响着加工质量和加工效率。
切削量的大小不仅关系到加工表面的粗糙度和加工后的尺寸精度,还关系到刀具的寿命和加工成本。
因此,合理计算和控制切削量对于提高加工质量、提高生产效率和降低成本都具有重要意义。
切削量的计算是一个复杂的过程,需要考虑多个因素,包括切削速度、进给量、切削深度、切削角度等。
在实际加工中,根据不同的材料、刀具和加工方式,切削量的计算也会有所不同。
但是,一般来说,切削量的计算都可以通过以下公式来进行:切削量 = 切削速度×进给量。
其中,切削速度是刀具在切削时的线速度,通常以m/min或mm/s为单位;进给量是刀具在单位时间内在工件上移动的距离,通常以mm/min或mm/s为单位。
切削量的计算公式看似简单,但实际应用中需要考虑到很多因素。
首先,切削速度和进给量要根据具体的加工情况来确定。
切削速度一般是根据材料的硬度和刀具的材质来选择的,一般来说,硬度越大的材料,切削速度就应该越小;刀具的材质和涂层也会影响切削速度的选择。
进给量则需要考虑加工表面的粗糙度要求、刀具的耐磨性和加工效率等因素。
其次,切削量的计算还需要考虑到切削深度和切削角度。
切削深度是指刀具在工件上的有效切削深度,通常以mm为单位;切削角度则是刀具切削时与工件表面的夹角,通常以度为单位。
这两个参数的选择也会影响切削量的计算,需要根据具体的加工情况来确定。
除了上述的基本公式外,还有一些特殊情况下的切削量计算,比如在铣削加工中,切削量的计算还需要考虑到刀具直径和刀齿数等因素。
在车削加工中,切削量的计算还需要考虑到切削时间和切削力等因素。
在实际应用中,需要根据具体的加工情况来选择合适的计算公式。
在实际加工中,切削量的计算不仅仅是一个简单的数学计算,还需要考虑到加工质量、加工效率和刀具寿命等多个因素。
因此,合理的切削量计算是一个复杂的过程,需要加工人员具有丰富的经验和良好的技术水平。
车床切削用量介绍

车床切削用量介绍车床切削用量介绍切削用量包括切削速度、进给量和背吃刀量(切削深度),俗称切削三要素。
它们是表示主运动和进给运动最基本的物理量,是切削加工前调整机床运动的依据,并对加工质量、生产率及加工成本都有很大影响。
1.切削速度它是指在单位时间内,工件与刀具沿主运动方向的最大线速度。
车削时的切削速度由下式计算:式中:——切削速度(m/s或m/min) ;——工件待加工表面的最大直径(mm);——工件每分钟的转数(r/min)。
由计算式可知切削速度,与工件直径和转数的乘积成正比,故不能仅凭转数高就误认为是切削速度高。
一般应根据与,并求出,然后再调整转速手柄的位置。
切削速度选用原则:粗车时,为提高生产率,在保证取大的切削深度和进给量的情况下,一般选用中等或中等偏低的切削速度,如取50~70m/min (切钢),或40~60m/min(切铸铁);精车时,为避免刀刃上出现积屑瘤而破坏已加工表面质量,切削速度取较高(100 m/min以上)或较低(6 m/min以下),但采用低速切削生产率低,只有在精车小直径的工件时采用,一般用硬质合金车刀高速精车时,切削速度100~200 m/min (切钢)或60~100m/min(切铸铁)。
由于同学对车床的操作不熟练,不宜采用高速切削。
2.进给量 ?它是指在主运动一个循环(或单位时间)内,车刀与工件之间沿进给运动方向上的相对位移量,又称走刀量,其单位为mm/r。
即工件转一转,车刀所移动的距离。
进给量选用原则:粗加工时可选取适当大的进给量,一般取0.15~0.4 mm/r;精加工时,采用较小的进给量可使已加工表面的残留面积减少,有利于提高表面质量,一般取 0.05~0.2 mm/r。
3.背吃刀量(切削深度)车削时,切削深度是指待加工表面与已加工表面之间的垂直距离,又称吃刀量,单位为mm,其计算式为:式中: dw——工件待加工表面的直径(mm);dm——工件已加工表面的直径(mm)。
高铬铸铁铸造工艺加工刀具及切削参数

高铬铸铁铸造工艺加工刀具及切削参数高铬铸铁成分及性能高铬铸铁属金属耐磨材料、抗磨铸铁类铬系抗磨铸铁的重要分支,是继普通白口铸铁、镍硬铸铁而发展起来第三代白口铸铁。
1,高铬铸铁生产及铸造工艺1,出炉温度高铬铸铁的熔点比一般铸铁高约铸铁高,约1200摄氏度,出炉温度1500摄氏度,熔炼中频感应电炉。
2,炉衬采用酸性或碱性炉衬均可,炉衬的配比、打结、烘干和烧结均按常用工艺进行。
3,装料一般顺序加料,先将灰生铁、钼铁等难容铁合金装入炉底,而后将废钢等按照。
依次装入炉底4,脱氧待金属炉料全部熔化并提温1480摄氏度后再按顺序加工0.5%锰铁硅铁铝进行脱氧。
5,浇注在中频感应炉中融化温度不必太高,温度达到1480摄氏度即可出炉高铬铸铁的硬度KmTBcr12HRC46-56KmTBcr15moHRC46-58KmTBcr26HRC46-56高铬铸铁生产工艺要点1,高铬铸铁铸造性能较差,其热导率低,塑性差,收缩量大,且有大的热裂和冷裂倾向,在铸造工艺上要将铸钢和铸铁的特点结合起来考虑,2,造型宜采用水玻璃硅砂封强度高且透气性好的砂型,涂料耐火度高的高铝粉或镁粉与酒精混合伴制为获得细晶粒组织和好的表面质量,在铸件外形不大复的情况下金属型铸造广泛采用。
3,由于高铬铸件的冒口不易切除,因此造型时在冒口形式上宜采用侧冒口。
高铬铸铁热处理工艺1,退火一般生产中采用快速退火工艺升温至950度并保温三个小时停炉,随后随炉冷却至400度然后打开炉门。
继续缓冷至300一下出炉至室温。
2,淬火将机械加工后的铸件室温装炉缓慢升温至600度并保温半小时半小时不超越过将炉升温至淬火温度950-980度后保温2-4小时3,回火对淬火后的铸件进行230-260的回火处理。
具体工艺为;室温装炉,升温至230-260度保温然后出炉空冷。
4,白口铸铁中国早在春秋时代就制成了抗磨性良好的白口铸铁,用作一些抗磨零件。
这种铸铁具有高碳低硅的特点,有较高的硬度,但很脆,用得最广泛的是含铬量为12%~20%的高铬白口铸铁,组织中形成(cr,Fe)7C3的碳化物。
不同材料刀具切削类型的切削用量
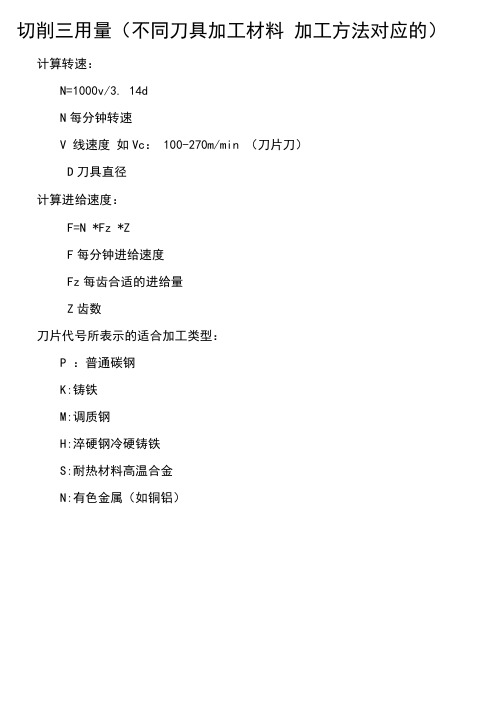
切削三用量(不同刀具加工材料加工方法对应的)计算转速:N=1000v/3. 14dN每分钟转速V 线速度如Vc: 100-270m/min (刀片刀)D刀具直径计算进给速度:F=N *Fz *ZF每分钟进给速度Fz每齿合适的进给量Z齿数刀片代号所表示的适合加工类型:P :普通碳钢K:铸铁M:调质钢H:淬硬钢冷硬铸铁S:耐热材料高温合金N:有色金属(如铜铝)加工中心常用刀具切削用量表L刀片为涂层硬质合金,刀片装在盘刀或刀杆上,加工材料以45钢为例:理论依据:涂层硬质合金刀片线速度V: 150-250m/niin (以加工45钢为例)每齿每转进给量Fz: 0. 05—0. 6mm/rad举例:计算直径251nm的刀具每分钟转速S=1000XV/3. 14X25=1000X200/3.14X25=2500r/min相对应的每分钟进给量F=FzXZXS=2X0. 5X2500=2500mm/min 注:Fz:每齿每转进给量Z:齿数S:每分钟转速F:每分钟进给量2.整体硬质合金的立铳刀和球刀(俗名鸨钢刀),加工材料以45钢为例:理论依据:鸨钢刀的线速度V: 100m/min左右(以加工45钢为例)每齿每转进给量Fz: 0. 05—0. 25mm/rad举例:计算直径10mm的刀具每分钟转速S=1000XV/3.14X10=100X100/3. 14X10 =3000r/min相对应的每分钟进给量 F=FzXZXS=4X0. 17X3000=2000mm/min分析对比:直径10mm的筲钢刀铳45钢,如改为加工铝合金,铝的硬度只有钢的三分之一,效率应提高3-4倍。
转速、吃刀深度、进给量可以提高到1.5倍。
直径10mm的铝钢刀铳铝的切削用量:S=4500r/min F=3000 mm/min ap (吃刀深度):0. 4mm3.白钢粗皮刀铳铝合金的切削用」=> ni理论分析:粗皮刀也叫波纹刀,切削的摩擦面积和摩擦阻力较小,适合大吃刀量,快速进给,和普通铳刀相比,用于高效开粗,因波纹刀侧面像螺纹的牙齿,铳削光洁度差,不适合精光。
高铬铸铁 熔炼工艺要求

高铬铸铁熔炼工艺要求(1) 出炉温度高铬铸铁的熔点比一般铸铁高,约为1200 ℃,出炉温度约为1500 ℃,熔炼选用中频感应电炉。
(2) 炉衬采用酸性或碱性炉衬均可,炉衬的配比、打结、烘干和烧结均按常规工艺进行。
(3) 装料一般按正常顺序加料,先将灰生铁、钼铁等难熔铁合金装入炉底,而后将废钢等按照下紧上松的原则装填(有助于塌料) 。
(4) 送电熔化将电炉功率调至最大进行熔化,由于Cr 的熔炼损耗较大( 约5 % ~15 %) ,故铬铁应在最后加入,通常是待废钢全部熔化后加入烤红的铬铁。
(5) 脱氧待金属炉料全部熔化并提温至1480 ℃后,再加入锰铁、硅铁及铝进行脱氧。
(6) 浇注在中频感应炉中熔化,温度不必太高,温度达到1480 ℃时即可出炉,铁液在包内应停留一段时间进行镇静,视工件大小不同可在1380 ~1410 ℃之间进行浇注。
高铬铸铁生产工艺要点(1) 高铬铸铁铸造性能较差,其热导率低,塑性差,收缩量大,且有大的热裂和冷裂倾向,在铸造工艺上要将铸钢和铸铁的特点结合起来考虑,必须充分注意铸件的补缩问题,其原则与铸钢件相同( 采用冒口和冷铁,且遵循顺序凝固原理) 。
由于合金中铬含量高,易在铁液表面结膜,所以看起来铁液流动性差,但实际上流动性较好。
(2) 造型宜采用水玻璃硅砂等强度高且透气性好的砂型,涂料应采用耐火度高的高铝粉或镁粉与酒精混合拌制。
另外,为获得细晶粒组织和好的表面质量,在铸件外形不太复杂的情况下,金属型铸造也被广泛采用。
(3) 高铬铸铁的收缩量与铸钢相近,模样制作上其线收缩率可按1. 8 % ~2 % 进行计算。
在砂型制作上,其冒口大小可按碳钢的规定进行计算,而浇注系统则按灰铸铁计算,但需把各截面积增加20 % ~30 % 。
浇冒口的选择应注意两个方面: 一是要保证铸件工作带( 使用部位) 的质量; 二是要尽量提高铸件的成品率。
(4) 由于高铬铸件的冒口不易切除,因此造型时在冒口形式上宜采用侧冒口或易割冒口。
机械加工切削用量

说明组合机床在大多数情况下是采用多刀同时加工,在同一个主轴箱上往往有各种不同的刀具,而共用一个进给系统。
因此,组合机床切削用量的选择,用计算的办法是比较复杂的。
下面参照现场采用的切削用量和一些经验数据列出了组合机床常用的切削用量,供设计时参考。
用高速钢钻头加工铸铁件的切削用量注:当采用硬质合金钻头加工铸铁时,切削速度一般为20~30米/分。
用高速钢钻头加工钢件的切削用量在钻深孔时,上述两表中所列数值应进行修正;表中所列ν应除以Kv ;表中所列s应乘以Ks。
当用高速钢钻头在铸铁件上钻深孔时,Ks=1,Kv见下表:当用高速钢钻头在钢件上钻深孔或用硬质合金钻头在铸铁件上钻深孔时,Kv、Ks见下表:用高速钢钻头加工铝及铝合金的切削用量用高速钢钻头加工黄铜及青铜的切削用量用高速钢铰刀铰孔的切削用量注:用硬质合金铰刀加工铸铁件时,ν=8~10米/分,加工铝件时,ν=12~20米/分。
用高速钢扩孔钻扩孔的切削用量注:1、当用硬质合金扩孔钻加工铸铁件时,切削速度ν=30~40m/min,加工钢件时,切削速度ν=35~60m/min2、mm:毫米;m/min:米/分;mm/r:毫米/转;镗孔的切削用量注:采用高精度的精镗头镗孔时,余量一般较小,直径上不大于0.2毫米,切削速度可以提高一些,铸铁件ν=100~150m/min,钢件ν=150~250m/min,铝合金ν=200~400m/min,巴氏合金ν=250~500m/min,而每转进给量S转则在0.03~0.1mm/r范围内。
用硬质合金端铣刀铣削的切削用量注:铣削切削用量的选择与要求的加工光洁度及效率有关,当要求较高的铣削光洁度时,则铣削速度应高一些,每齿进给量应小一些。
攻丝的切削速度孔加工常用工序间余量硬质合金车刀常用切削用量注:①刀具耐用度t=60min;ap、f 选大值,ν选小值,反之,ν选大值。
②成形车刀和切断车刀的切削速度可取表中粗加工栏中的数值。
- 1、下载文档前请自行甄别文档内容的完整性,平台不提供额外的编辑、内容补充、找答案等附加服务。
- 2、"仅部分预览"的文档,不可在线预览部分如存在完整性等问题,可反馈申请退款(可完整预览的文档不适用该条件!)。
- 3、如文档侵犯您的权益,请联系客服反馈,我们会尽快为您处理(人工客服工作时间:9:00-18:30)。
高铬铸铁的切削用量优化计算来源:数控机床网 作者:数控车床 栏目:行业动态 高铬白口铸铁是一种具有很高硬度和强度的抗腐耐磨材料,其抗拉强度为650~850MPa,铸态硬度为HRC48~55,淬火硬度为HRC55~6 2。
但这种材料又硬又脆,切削状态极不平稳,如果不能很好地解决切削加工问题,其应用将会受到很大的限制。
试验表明,用硬质合金刀具加工高铬铸铁,刀具磨损极快,切削容易形成崩脆切削,表面粗糙度大,只能用于一般的粗加工。
对于高铬铸铁的精加工,用陶瓷刀具可以取得较低的粗糙度。
但是陶瓷刀具的抗冲击能力较弱,对于切削高铬铸铁这种脆性材料更容易受到冲击,引起崩刃等刀具的破坏。
由于陶瓷刀具价格较贵,应尽量避免被破坏,因此正确合理地选择切削用量是避免刀具发生冲击崩刃破坏的有效途径。
本文在考虑刀具动态强度经济性的条件下,对用复合陶瓷刀具车削高铬铸铁渣浆阀门阀板零件外圆的切削用量进行了优化计算。
1 切削温度对复合陶瓷刀具动态性能的影响切削温度对刀具动态性能的影响,主要表现在对刀具材料机械性能的影响及切削温度场产生的附加热应力。
温度对复合陶瓷刀具机械性能的影响复合陶瓷的物理机械性能在一般情况下,都随切削温度的升高而降低。
试验表明,在一定范围内,加工钢铁零件时,复合陶瓷刀具的各项机械性能指标与温度有下列经验公式sbt=sbo(1-bt) (1) sst=ssoexp(1-ct) (2) Et=Eoexp(-dt) (3) Ht=Ho(1-kt) (4)式中:sbt,sst,Et,Ht分别为复合陶瓷刀具在温度为t时的抗拉强度、屈服极限、弹性模量和硬度:sbo,sso,Eo,Ho分别为常温下的抗拉强度、屈服极限、弹性模量和硬度:b、c、k、d为试验确定的常数。
切削温度场产生的附加热应力在连续车削加工中,当切削用量及外部环境条件不变时,可以认为在刀具前后刀面上作用有稳态热源,刀具上的切削温度场可以采用三维热传导的有限元法计算。
由于刀具是在弹性范围内工作,因此由温度引起的附加热应力为st=at(t-t0)E (9)式中:t0为无应力时的温度:at为复合陶瓷的线膨胀系数。
2 复合陶瓷的动态应力及动态强度对复合陶瓷刀具的动态应力,采用三维有限元法计算,模型如图1。
切削力Fz作用在切削刃中部,单元采用八节点三维块体元,刀具与刀体接触边为弹性约束,其余为自由边。
计算此条件下的最大应力与一般固体力学的求解方法完全相同,但考虑到温度的影响,对每个单元有(10)以此组方程构成弹性阵,进行有限元求解,可得刀具在切削力与温度场共同作用下的最大动态应力smax,若陶瓷刀具在前刀面温度为t时的强度为[st],则其动态强度条件为smax≤[st] (11)图1 应力等值图图2 计算框图3 复合陶瓷刀具材料切削用量的优化计算目标函数切削用量的优化计算是以加工成本为目标函数,生成一个零件主要包括下列费用:材料费用(Cc)构成一个零件毛坯的费用:机床费用(Cj)机床单位工时费用,包括机床的折旧费等:工装费用(Cg)生产工人及管理与辅助人员的单位工时工资:换刀及磨刀费用(Cd)生产一个零件的总费用为 Cw=Cc+(Cj+Cg)(tz+tj)+Cdtj/T (12)式中:tz为准备时间:tj为有效切削时间:T为刀具耐用度,单位皆为min。
由泰勒公式计算 T=CV+V-1/mf-1/nap-1/p (13)基本切削时间为tj=kV(Vfap) (14)上两式中:CV为常数:ap为余量。
将式(13)、式(14)代入式(12)得 Cw=Cc+tzCm+kvCm/(Vfap)+kvCd/[CVf(-1/n)+V(1-1/m)ap(1-1/p) ] (15)式中:Cm=Cj+Cg。
式(15)即为刀具切削用量优化计算的成本目标函数。
约束函数切削用量优化计算的约束函数主要有以下几个方面:切削用量取值约束。
若机床的切削速度,进给量的取值范围为(Vmax,Vmin),( fmax,fmin),则有下面的约束函数 G1(f,V)=V-V max≤0 (16) G2(f,V)=Vmin-f≤0 (17) G3(f,V)=fmax-f≤0 (18) G4(f,V)=f-fmax≤0 (19)精度约束。
若给定的表面粗糙度为Ra,则有约束函数 G5(f,V)=f-(8Rar)½≤0 (20)机床功率约束。
若机床的许用功率为p,则有下面的约束 G6(f,V)=VFz1+zfFzy-p/CFzaKFz≤0 (21)刀具耐用度约束 G7(f,V)=V1/mf1/nap1/p-CV/T0≤0 (22)上面各式中,XFz,yFz,KFz,CFz为试验常数。
刀具动态强度约束函数G8(f,V)=smax-st≤0smax为切削用量通过有限元计算的最大动态应力。
优化计算由于刀具的最大动态应力是用有限元计算的,没有定量的解析函数。
在优化计算中无法引入约束函数G8,因此在计算中我们先不考虑G8,优化出一组切削用量,再根据此组优化切削用量,用有限元法计算刀具的最大动态应力。
如满足动态强度,则此切削用量为最优,如不满足,则减小切削用量直到满足动态强度为止,此时得到的切削用量参数为最合理的切削用量。
计算框图如图2。
图3 刀具几何尺寸4 计算结果与试验原始参数机床:CA6140,转速范围,N=12~1200r/min,进给量范围f=0.08~1.59mm/r,功率P=7.5kW。
刀具:AG2复合陶瓷,力学参数:e=4550kg/m2,导热系数为22.93W/m·k,热膨胀系数a=8×10-6(℃)-1,抗弯强度 =800MPa,弹性模量E=420GPa,柏松比µ=0.24,硬度HV2400。
几何参数:g0=-5°,a0=12°,ls=-6°,负倒棱30°,宽为1mm,刀尖半径r=1mm,尺寸如图3所示。
工件:渣浆阀,表面粗糙度Ra=1.6,材料为新型铬高白口铸铁,强度680~800MPa,直径300mm,厚度40mm,单边余量3mm。
经济参数:机床费用,Cm=Cj+Cg=42元/min,换刀及磨刀费用Cd=4.8元。
准备时间tz=1.5分,Cc=130。
(以上参数为武汉海联机械厂提供)。
其他参数:m=0.23,n=0.57,p=1.33耐用度T0=60min,h=0.75,zFz=0.15,CFy=244,CFz=436,CV=2.28×103,xFy=0.9,yFy=0.55,zFy=0.3(以上参数为attopad nyay所著《陶瓷刀具在切削铸铁及钢料时的磨损特性》和试验所得)。
优化计算将上述参数代入目标函数及约束函数可得成本目标函数为 CW=136.3+332.506V-1f-1+2.229V×4f0.75 (23)各约束函数为 G1(f,V)=V-565≤0 (24) G2(f,V)=0.565-V≤0 (25) G3(f,V)=0.08-f≤0 (26) G4(f,V)=f-1.59≤0 (27) G5(f,V)=f-0.113≤0 (28) G6(f,V)=V0.85f0.75-49.5≤0 (29) G7(f,V)=V5f1.75ap0.75-2.27×1011≤0 (30)用monte-Cono算法计算可获得最小成本切削用量为V=109.8m/min,f=0.1mm/r。
在此切削用量下用有限元计算温度场见图1,由经验公式可知,此时作用在刀具上的集中力为Fz=436×2×0.10.75×109.8-0.15=92.016kgFy=244×20.9×0.10.6×109.8-0.3=29.28kg用有限元法计算切削力Fz、Fy及温度场共同作用下的应力如图2 所示。
从计算结果可以看出刀具动态强度满足要求。
切削速度V=109 .8m/min,进给量f=0.8mm/r为最优化用量。
试验结果在CA6140 车床上用V=109.8m/min,f=0.8mm/r 车削高铬白口铸铁渣浆阀阀板外圆无崩刃损坏,耐用度(VB=0.1mm时)达65分。
而原先用V=142m/min,f=0.2mm/r时发生崩刃。
5 结束语采用有限元法对刀具在切削温度场和切削力共同作用下的温度场计算是可行的。
考虑应力对刀具强度的影响,对陶瓷刀具切削高铬白口铸铁的切削用量进行优化即保证切削加工成本最低,又不会产生崩刃破坏,无疑是经济的。
网页查看:高铬铸铁的切削用量优化计算 发表评论相关资讯:铸铁1 加工淬火钢和冷硬铸铁时刀具的选用切削1 切削加工和刀具技术的现状与发展2 齿轮滚刀最短有效切削长度的计算3 CNC数控加工中刀具的选择与切削用量的确定4 陶瓷刀具低速切削时的有限元分析5 切削刀具多层涂层的力学特性和耐磨性用量1 CNC数控加工中刀具的选择与切削用量的确定2 数控车床编程如何确定切削用量与进给量3 数控加工切削用量的确定优化1 夹具的优化设计及经济性分析研究2 优化过程仪表的7点建议3 优化刀具实现铝合金零件孔的高效加工4 面向绿色制造的工艺参数优化数学模型5 ANSYS参数优化和概率设计在超声波焊接工装上的应用计算1 等误差直线逼近非圆曲线的节点计算及刀具轨迹模拟2 用AutoCAD图形计算刀具中心轨迹的方法3 GMAW温度场计算及其焊接质量的特征建模4 AutoCAD中计算二维图形的面积5 基于AutoCAD冲裁模线切割加工时刃口尺寸计算与3B指令生成数控机床网提供机床产品列表:数控机床|苏州宝玛|数控车床|线切割机床|数控切割机|电火花数控快走丝线切割机床|电火花数控慢走丝线切割机床|电火花机|电火花成型机|电火花高速小孔加工机|数控铣床|加工中心,欢迎咨询订购!。