汽车产品VDA6.3过程审核检查表及评分标准
2016版VDA6.3过程审核检查表
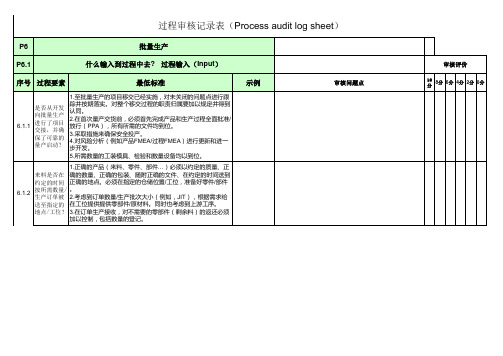
是否对原材 污染。仓储区/加工区/容器必须达到零部件/产品所需的必要的
料进行适当 整洁/清洁要求。要定义清洁周期,并且加以监控。
的仓储,所 3.加工工位/装配线上的零部件/物料的供应必须便与安全操作
6.1.3
使用的运输 。 工具/包装设 4.必须通过合适的方法,监控为特殊材料/零部件规定的仓储时
备是否适合 间以及使用有效期(最长、最短仓储时间,规定的中间临时仓
量要求? 性有影响的测量装置的校准。
4.对于影响到测量结果合试验的附属装置,要采取同样的方式
加以监控。
加工工位和
6.4.4
检验工位是 否满足具体
要求?
1.加工工位及周边布置的条件环境适合于生产操作和产品的要 求,从而可以预防或避免污染、损伤、混料。 2.这也适用于临时的和永久的返工返修、拣选、检验工位。 3.除此以外,还根据具体的工作任务,在人机工程学的基础上 对加工工位设计进行了调整。
P6.2
工作内容/过程流程(所有生产过程是否受控?)
控制计划里 的要求是否 6.2.1* 完整,并且 得到有效实 施?
1.基于控制计划的生产和检验文件完备。其中必须对检验文件 、检验设备、检验方法、检验频度/周期、重新评定等加以规 定。 2.这些文件必须随时可获取。 3.对于影响到产品特性/质量的过程参数必须加以完整地描述。 过程参数和检验特性必须带有公差。 4.在过程控制图上规定控制限,控制限可探测、可追溯。 5.针对过程要求和检验特性,要对发现的不符合项以及启动的 措施加以记录。 6.对过程异常所要采取的措施(反应计划),相关责任人必须 清楚,实施措施并加以记录。 7.如产品对生产工艺有特殊要求,那么相关的机器/工装/辅助 设备的参数数据要在控制计划和/或生产检验文件中加以规定 。 8.详细规定返工条件,并且在过程中加以保障(零部件标识, 重新检验)
过程审核检查表-VDA6.3

是否有对现有供方的质量绩效进行评估?
是否有识别并评价供应链中的风险,并通过适当措施加以降低(应急策略)?
P5.2是否在供应链中考虑了顾客的要求?
如:是否规范了对顾客要求的沟通与传递,并确保可追溯性?
顾客要求包括:图纸、零部件以及质量协议及其他适用的标准?
生产测试证明在量产条件下(模具、设备、周期、人员、制造和检验规范等)的整个生产过程满足质量能力要求?
审核产品:审核部门:PDT小组(研发/工程主导)审核员:陪审员:审核日期:
序
号
过程
要求
提问及要点
分值
审核记录
10
8
6
4
0
P4
产
品
和
过
程
开
发
的
实
现
P4.7是否为确保顾客关怀/顾客满意/顾客服务和使用现场失效分析建立了过程?
审核产品:审核部门:品保、生产(冲压/成型/装配)审核员:陪审员:审核日期:
序
号
过程
要求
提问及要点
分值
审核记录
10
8
6
4
0
P6
过
程
分
析
/
生
产
P6.2
过程
流程
6.2.1控制计划的要求是否完整并得到有效落实?
如:生产和检验文件中是否完整地给出了所有重要信息(检验特性、设备、检验方法、检验频度、全尺寸检验、功能检验等)?
审核产品:审核部门:PDT小组(研发/工程主导)审核员:陪审员:审核日期:
序
号
过程
要求
vda6.3过程审核清单-打分表

特性是否按“D-零件”管理?有关材料、功能、寿命、可靠性的特性1.4是否可靠保存生产及技术资料最少15年生产工艺,参数规定,检验计划,能力验证,检具监控,安全数据表等1.5存档文件是否包含所有重要数据?--零件原始数据(包括更改状态)--检验特性(实际值/额定值)--可靠性试验--在产生偏差时的说明及改进措施1.6存档资料是否保证任何时间均可很快地得到任何一份资料整个生产过程(包括二次配套厂)的产品资料与检验资料必须按炉号/批号存档1.7对“D-特性”有影响的配套厂是否也对责任零件进行同样的验证?1.8是否审核对“D-特性”有影响的配套厂,并提供结果证明?1.9 是否具有欧共体安全数据表,化学品法规,危险材料规定以及化学品禁用用法规,是否是最新版本,是否规定了有关责任?2.产品和过程是大部分否2.1对所有影响“D-特性”的过程参数是否作出文字规定,是否定期检查这些过程参数并记录存档?定期检查的结果记录2.2是否对“D-特性”进行了过程能力验证或在缺少验证时,进行100%检验?(要求:批量开始时,C pk≥1.33,批量生产六个月后Cpk≥1.67,并持续改进)2.3“D-特性”的检验方法是否适合于发现缺陷?(检具的能力验证,精度与公差相符,保养与标定)2.4是否通过足够的标记来确保其可追溯性?(零件原始数据,生产日期,批号/炉号供货日期,供货单)2.5是否充分地考虑了所有的D特性2.6是否对提供大众汽车公司的材料就环境承受方面的科学鉴定进行超越供货期以后的跟踪,并在情况严重时通告大众汽车公司?3.人员3.1是否对影响/从事于D特性有关的人员进行职责教育必须对遵守法规,偏差/不符合时的后果,职责,信息流,隔离,标识的要求进行教育(规定、纪要、通过签字来确认)3.2对外籍人员是否用他们本国语言的指导书?或有掌握语言的证明?3.3人员资格是否用他们本国语言的指导书?或有掌握语言的证明?(对过程的质量控制/通过训练和抽样方式复查,考核)3.4在需要更换人员时是否有其他具有良好素质的人员可供使用?。
VDA6.3过程审核评分准则

--零部件有受到损伤的风险
--零部件混合/错误的安装导致过程故障
--用于发现缺陷的检验和测量工具不适用
--员工一方面接受的培训不足,另一方面对故障
模式也不了解
--产品上有缺陷(不能满足功能性,产品的 使用受到严重限制,顾客对其不能开展进一 步的制造)
--机器/设备/工装不适用,不完整或者完全没有 到位
--没有定义生产参数/检验要求 --没有启动改进计划 --没有对改进计划的有效性开展证明 --企业或者内部目标方面存在严重偏差 --重要特性相关要求的落实情况不足
--没有为人员提供必要的资格培训
--于有关要求的落实情况不足,导致顾客那 里发生功Biblioteka 缺陷过程审核的评分风险评分表
评分 10 8 6
4
0
产品风险 --产品没有任何缺陷,满足技术要求
过程风险 --满足了技术要求/产品和过程的技术规范要求
--产品上有缺陷(但不影响到功能,使用或者在 过程中的进一步制造),需要加以改进
--生产流程中存在轻度的故障
--过程中存在薄弱环节,但被及时发现和排除
--产品上有缺陷(但不影响到功能,缺陷会导致 使用时或者在过程中的进一步制造时发生故障) --没有满足过程能力要求(特殊特性) --在接下来的过程中将对缺陷加以返工 --检验时发现缺陷,有缺陷的零部件
--产品的生产不能满足过程可靠性的要求,特殊 特性部分超差
--没有满足约定的过程能力要求(特殊特性) --对特殊特性没有开展系统的监控
--缺陷将导致严重的过程故障
--需要开展筛选行动
--在接下来的过程/检验中不一定能够发现缺陷, 从而加以筛选或者返工
--需要开展返工
--报废率高,或者需要开展大量的单独返工
汽车产品VDA 过程审核检查表及评分标准
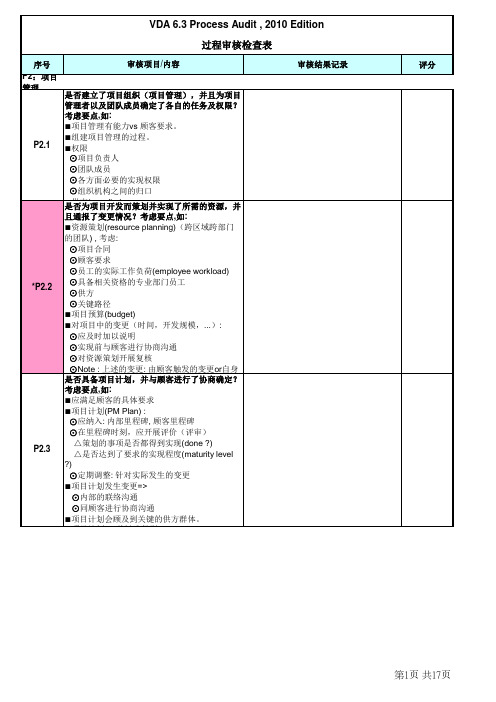
⊙试运行计划(trailling plan), 必须包含 △材料 △零件 △分总成(subassemblies) △生产制造过程: 原型件(prototype) + 试生产
阶段 (pre-production)
⊙测试、检查和检验设备策划(equipment planning)
⊙项目负责人 ⊙团队成员 ⊙各方面必要的实现权限 ⊙组织机构之间的归口 是 ■供否方为(项su目pp开lie发r) 而策划并实现了所需的资源,并 且通报了变更情况?考虑要点,如: ■资源策划(resource planning)(跨区域跨部门 的团队) , 考虑: ⊙项目合同 ⊙顾客要求 ⊙员工的实际工作负荷(employee workload) ⊙具备相关资格的专业部门员工 ⊙供方 ⊙关键路径 ■项目预算(budget) ■对项目中的变更(时间,开发规模,...): ⊙应及时加以说明 ⊙实现前与顾客进行协商沟通 ⊙对资源策划开展复核 ⊙Note : 上述的变更: 由顾客触发的变更or自身 是否具备项目计划,并与顾客进行了协商确定? 考虑要点,如: ■应满足顾客的具体要求 ■项目计划(PM Plan) : ⊙应纳入: 内部里程碑, 顾客里程碑 ⊙在里程碑时刻,应开展评价(评审)
prototype ⊙试生产阶段pilot run ⊙系列生产阶段serial production
是否在系列生产条件下进行了试生产,以获得生 产批准/放行?考虑要点,如: ■必须开展试生产/ 生产测试
⊙生产因素和影响进行评价=> 整改 (corrections)
⊙批量生产过程中,避免瓶颈以及质量损失
⊙质量管理计划(QM Plan, i.e. control plan) 人力资源是否到位并且具备资格?考虑要点,如: ■过程[人力资源策划]
VDA6.3-2016审核表(附自动评分)
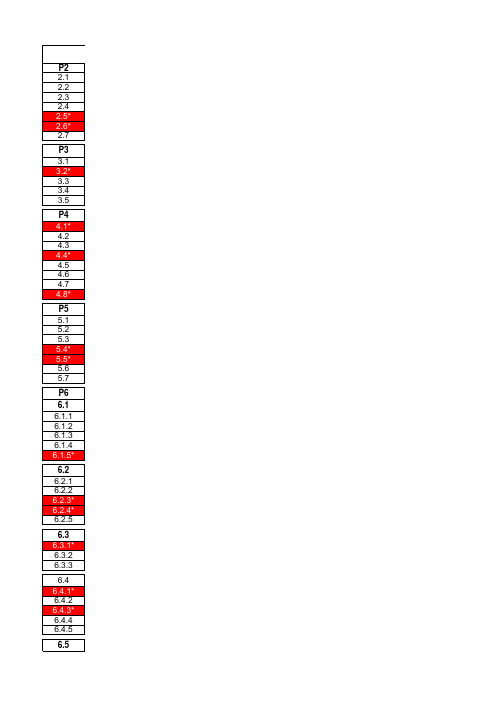
是否为制造过程设定目标要求? 对收集的质量和过程数据是否可以开展评价? 一旦与产品和过程要求不符,是否对原因进行分析,并且检验纠正措施的有效性? 对过程和产品是否定期开展审核?
过程应取得怎样的成果?过程成果/输出) 产量/生产批量是否是根据需要确定的,并且有目的地运往下道工序?
是否根据要求对产品/零部件进行适当仓储,所使用的运输设备/包装方式是否与产品/零部件的特殊特性相 互适应?
所有生产过程是否受控?(工艺流程) 控制计划里的要求是否完整,并且得到有效实施? 对生产操作是否重新进行批准/放行? 特殊特性在生产中是否进行控制管理? 对未批准放行件和/或缺陷件是否进行管控? 是否确保材料/零部件在流转的过程中不发生混合/弄错?
哪些岗位为过程提供支持?(人力资源) 员工是否能胜任被委派的工作? 员工是否清楚被委以的产品和过程质量监控的职责和权限? 是否具备必要的人力资源?
通过哪些资源落实了过程?(物质资源) 使用的生产设备是否可以满足顾客对产品的特定要求? 生产设备/工具的维护保养是否受控? 通过使用的测量和试验设备,是否能够有效地监控质量要求? 加工工位以及检验工位是否满足具体的要求? 是否根据要求,正确的存放工具、装置和检验工具?
过程实现的效果如何?(有效性、效率、减少浪费)
P2 2.1 2.2 2.3 2.4 2.5* 2.6* 2.7
P3 3.1 3.2* 3.3 3.4 3.5
P4 4.1* 4.2 4.3 4.4* 4.5 4.6 4.7 4.8*
P5 5.1 5.2 5.3 5.4* 5.5* 5.6 5.7
P6
6.1 6.1.1 6.1.2 6.1.3 6.1.4 6.1.5*
产品和过程开发的策划 针对产品和过程的具体要求是否已明确? 在产品和过程要求已明确的基础上,是否对可行性进行跨职能分析? 是否具有产品和过程开发事项的详细计划? 顾客关怀/顾客满意/顾客服务以及现场失效分析方面的事项是否具有相应计划? 是否对产品和过程开发所需的资源进行策划?
VDA6.3过程审核评分准则
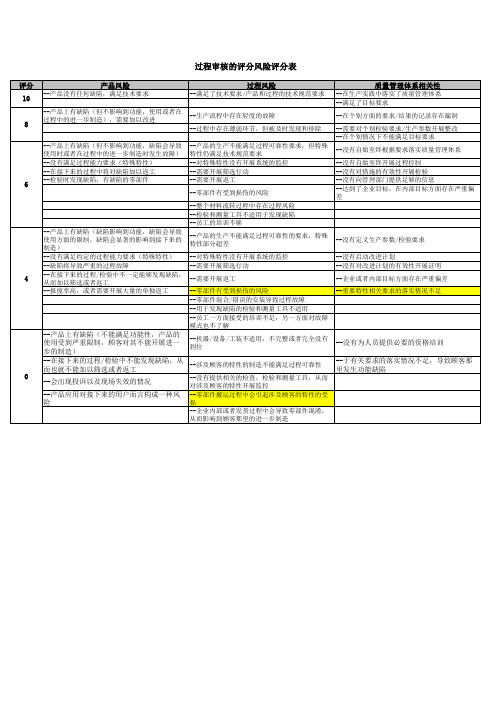
8
6
--产品上有缺陷(但不影响到功能,缺陷会导致 使用时或者在过程中的进一步制造时发生故障) --没有满足过程能力要求(特殊特性) --在接下来的过程中将对缺陷加以返工 --检验时发现缺陷,有缺陷的零部件
--产品的生产不能满足过程可靠性要求,但特殊 特性仍满足技术规范要求 --对特殊特性没有开展系统的监控 --需要开展筛选行动 --需要开展返工 --零部件有受到损伤的风险 --整个材料流转过程中存在过程风险 --检验和测量工具不适用于发现缺陷 --员工的培训不够
--会出现投诉以及现场失效的情况
--没有定义生产参数/检验要求 --没有启动改进计划 --没有对改进计划的有效性开展证明 --企业或者内部目标方面存在严重偏差 --重要特性相关要求的落实情况不足
0
--产品上有缺陷(不能满足功能性,产品的 --机器/设备/工装不适用,不完整或者完全没有 使用受到严重限制,顾客对其不能开展进一 到位 步的制造) --在接下来的过程/检验中不能发现缺陷,从 --涉及顾客的特性的制造不能满足过程可靠性 而也就不能加以筛选或者返工
4
--产品上有缺陷(缺陷影响到功能,缺陷会导致 使用方面的限制,缺陷会显著的影响到接下来的 制造) --没有满足约定的过程能力要求(特殊特性) --缺陷将导致严重的过程故障 --在接下来的过程/检验中不一定能够发现缺陷, 从而加以筛选或者返工 --报废率高,或者需要开展大量的单独返工
VDA6.3检查表-评分矩阵+要素说明+评审提问表

பைடு நூலகம்评审结果
产品和过程开发的策划
2.1 是否已经具有产品和过程的特定要求? 2.2 基于所确定的产品和过程要求,是否以多功能小组的形式,对制造可行性进行了评审?
产品和过程开发的实现
3.1 是否编制了产品-FMEA/过程-FMEA,并在项目进程中进行了更新,同时确定了纠正措施? 3.2 基于要求,是否在不同阶段具有所需的能力证明和放行? 3.3 为了确保批量生产的开始,是否对项目导入生产进行了控制?
供方管理
4.1 是否只选择获得批准/放行且具备质量能力的供方? 4.2 是否在供应链上考虑到了顾客要求?
4.3 对于外包产品和服务,是否获得了所需的批准/放行? 4.4 是否确保了外包产品和服务的质量? 4.5 是否对进厂的货物进行了适宜的储存?
过程分析/生产 什么进入过程?过程输入
5.1.1 是否在开发和批量生产之间进行了项目交接? 5.1.2 是否对原材料进行了适宜的仓储,运输设备/包装方式是否与原材料的特殊特性相适应?
过程有效性水平
5.5.1 是否为产品和过程设定了目标要求? 5.5.2 当与产品和过程的要求有偏差时,是否进行了原因分析,并检查了纠正措施的有效性? 5.5.3 是否定期进行了过程和产品审核?
过程应该产出什么?(输出)
5.6.1 在产品和过程方面,是否符合了顾客要求?
顾客支持/顾客满意/服务
6.1 顾客在质量管理体系,产品(交付时)和过程方面的要求是否得到了满足? 6.2 是否具有能够有效地开展缺陷零件分析的过程? 0 批准的供方 受控的供方 禁止的供方 最多7个提问的评审结果为“黄色” 没有提问的评审结果为“红色” 最多14个提问的评审结果为“黄色” 没有提问的评审结果为“红色” 最少15个提问的评审结果为“黄色” 没有提问的评审结果为“红色” 0 绿色 0
汽车产品VDA6.3过程审核检查表及评分标准
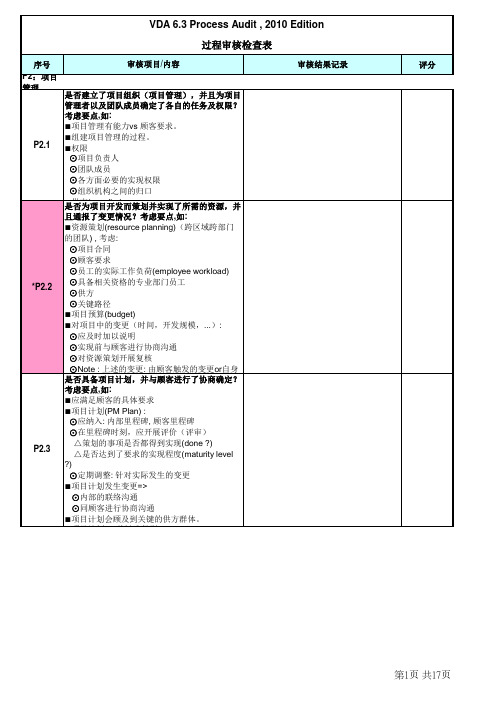
P2.6
*P2.7
P3:产品和过程开发的策划
第2页 共17页
序号
审核项目/内容 是否已经具有产品和过程的特定要求?考虑要 点,如: ■开发的产品的要求都已经到位(req’t known) ■过程[识别顾客的QMS要求+ 开发和过程要求] ■检查: 询价和合同文本(i.e. contract review) ■不满足要求的情况下=> ⊙通知顾客,或 ⊙顾客“放行”/ 同意(在合同的情况下)。 ■记录: 顾客在下级供方或者原材料选择的要求 ■识别特殊特性(SC) ⊙自身要求 ⊙顾客要求,法律法规要求 ⊙生产制造过程 ⊙产品用途/使用的特性 基于所确定的产品和过程要求,是否以多功能小 组的形式,对制造可行性进行了评审?考虑要 点,如: ■规范[可制造性(可行性)评价] ■检验: 合同和询价文本的可行性开展 ■过程: 确定产品要求 ⊙包括那些顾客没有明确说明的要求(例如法 律法 规要求) ■考虑: ⊙经验(教训) ⊙未来的期望 ■规范: 报价审批过程 ⊙相关负责/参与的部门确认顾客要求的可行性 △采购 △开发 △生产计划 △生产 △质量管理策划 △物流... ■ 报价阶段 : 考虑产能(capacity) 是否为产品和过程开发编制了相关的计划 (plans) ?考虑要点,如: ■项目计划下,专门的计划(specific plans) 包含 ⊙产品和过程开发 ⊙特定活动的具体时间点/時期(timing dates & period) ⊙里程碑(milestone) :内部的和顾客的,确定 △考量指标 △关键路径 ⊙生产测试… ⊙外包的过程和服务 ■内部开发计划(internal development plans) : ⊙与项目事件表(project timing plan) 协调一致 △尤其里程碑的考量指标(metric for each milestones) ⊙更新 ⊙包括质量管理策划(QM Planning), 其内容: △检验策划 △检验设备策划 △风险分析(e.g. DFMEA, PFMEA) ■针对批量生产,提供具备相关过程技术经验的
汽车产品VDA6

汽车产品VDA6.3过程审核检查表及评分标准VDA 6.3是一个过程审核评分准则,其中包括了评分准则和每个要素的评分。
评分准则中,完全符合得10分,绝大部分符合得8分,部分符合得6分,小部分符合得4分,完全不符合则不得分。
绝大部分符合指满足了约3/4以上的规定要求,并且没有特别的风险。
少于10分的情况需要采取纠正措施,没有评审问题的填“n.b.”,最少需要评审全部问题的2/3.有特殊风险的问题需要特别注意。
每个要素的评分公式为各相关问题实际得分的总和除以各相关问题满分的总和乘以100%。
审核结果的综合评分要素包括项目管理、产品和过程开发的策划、产品和过程开发的实现、供方管理、过程分析/系列生产和顾客支持/满意/服务。
综合评分公式为各要素得分的平均值。
过程分析/管理中的乌龟图包括了输入、工作内容、支持过程、材料、资源、效率、输出/结果和零件运输。
审核结果的综合评分分为ABCE四个等级,符合率高于90%且各要素得分均高于80%为A级,符合率高于80%且各要素得分均高于70%为B级,否则为C级。
降级规则为如果A级不满足条件,则评为B级,如果B级不满足条件,则评为C级。
P2:项目管理在审核项目/内容审核结果记录评分时,需要考虑是否建立了项目组织并为项目管理者以及团队成员确定了各自的任务及权限。
在组建项目管理的过程中,需要考虑项目管理的能力与顾客要求之间的平衡。
P2.1在确定权限时,需要考虑项目负责人、团队成员、各方面必要的实现权限以及组织机构之间的归口。
同时,需要考虑是否为项目开发而策划并实现了所需的资源,并且通报了变更情况。
在资源策划时,需要考虑项目合同、顾客要求、员工的实际工作负荷以及具备相关资格的专业部门员工。
P2.2在考虑供方时,需要关注关键路径。
同时,需要对项目预算进行管理,并在项目中的变更(时间、开发规模等)发生时及时加以说明,并与顾客进行协商沟通。
变更可分为顾客触发的变更、自身内部的变更以及供方触发的变更。
VDA6.3-2016版-过程审核提问检查表
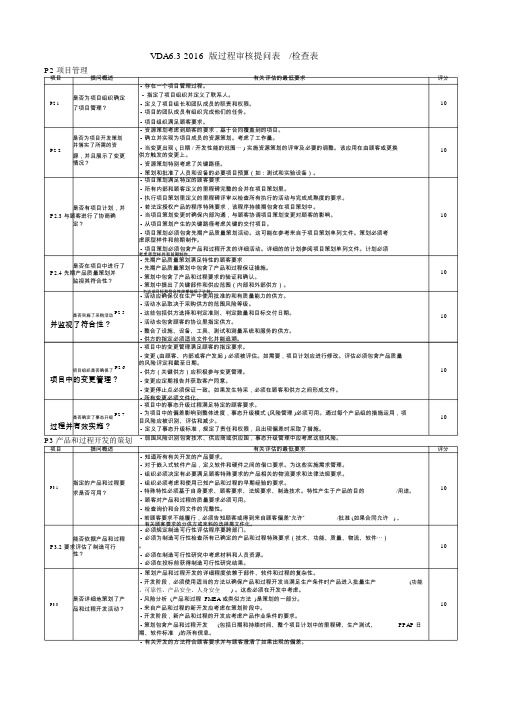
P2 项目管理项目提问概述是否为项目组织确定P2.1了项目管理?是否为项目开发策划并落实了所需的资P2.2源,并且展示了变更情况?是否有项目计划,并P2.3 与顾客进行了协商确定?是否在项目中进行了P2.4 先期产品质量策划并监视其符合性?是否实施了采购活动P2.5 并监视了符合性?项目组织是否确保了P2.6 项目中的变更管理?是否确定了事态升级P2.7 过程并有效实施?P3 产品和过程开发的策划项目提问概述指定的产品和过程要P3.1求是否可用?能否依据产品和过程P3.2 要求评估了制造可行性?是否详细地策划了产P3.3品和过程开发活动?VDA6.3 2016 版过程审核提问表/检查表有关评估的最低要求-存在一个项目管理过程。
-指定了项目组织并定义了联系人。
-定义了项目组长和团队成员的职责和权限。
-项目的团队成员有组织完成他们的任务。
-项目组织满足顾客要求。
-资源策划考虑到顾客的要求,基于合同覆盖到的项目。
-确立并实现为项目成员的资源策划。
考虑了工作量。
-当变更出现 ( 日期 / 开发性能的范围⋯ ) 实施资源策划的评审及必要的调整。
该应用在由顾客或更换供方触发的变更上。
-资源策划特别考虑了关键路径。
-策划和批准了人员和设备的必要项目预算(如:测试和实验设备)。
-项目策划满足特定的顾客要求-所有内部和顾客定义的里程碑完整的合并在项目策划里。
-执行项目策划里定义的里程碑评审以检查所有执行的活动与完成成熟度的要求。
-若法定授权产品的程序特殊要求,该程序持续期包含在项目策划中。
-当项目策划变更时确保内部沟通,与顾客协调项目策划变更对顾客的影响。
-从项目策划产生的关键路径考虑关键的交付项目。
-项目策划必须包含先期产品质量策划活动。
这可能在参考来自于项目策划单列文件。
策划必须考虑原型样件和前期制作。
-项目策划必须包含产品和过程开发的详细活动。
详细的的计划参阅项目策划单列文件。
计划必须考虑原型样件和前期制作。
VDA6.3过程检查表

—进行/报请维修与保养
—零件准备/贮存
—进行/报请对检测、试验设备的检定和校准。
4.1.3员工是否适合于完成所交付的任务并保持其素质?
—过程上岗指导/培训/资格的证明
小明回答
—产品以及发生缺陷的知识
—对安全生产/环境意识的指导
—资格证明(例如:焊接证书,视力测定,厂内机动车驾驶证)。
4.1.4是否有包括上岗规定的人员配置计划?
—图纸/订货要求/规范
—质量保证协议
—检验方法、检验流程、检验频次的商定
3.3是否评价供货实物质量?与要求有偏差时是否采取措施?
—质量会谈的纪要
是否发生过来料质量问题(现场IQC)检验记录,处理结果。重新测量的依据夏敏回答
—改进计划的商定与跟踪
—改进后零件的检验记录和测量记录
—对重点缺陷/有问题供方的分析评定。
要素1:过程开发的策划
1.1是否已具有对产品的要求?
---顾客要求
---法规,标准,规定
---物流方案
---技术供货条件(TI)
---质量协议/目标协议
---重要特性
---材料
1.2是否已具有过程开发计划,是否遵守目标值?
---顾客要求
---成本
---进度表:策划认可/采购认可,样件(样车)/试生产,批量生产起始
3.4是否与供方就产品与过程的持续改进商定质量目标,并付诸落实?
—工作小组(由各相关部门组成)
供应商管理方面,是否有供应商的目标、指标要求。夏敏回答
—确定质量、价格及服务的定量目标
—在提高过程受控状态的同时降低检验成本
—减少废品(内部/外部)
---提高顾客满意程度。
3.5对已批量供货的产品是否具有所要求的批量生产认可,可落实所要求改进措施?
汽车行业VDA6.3过程审核检查表及评分标准
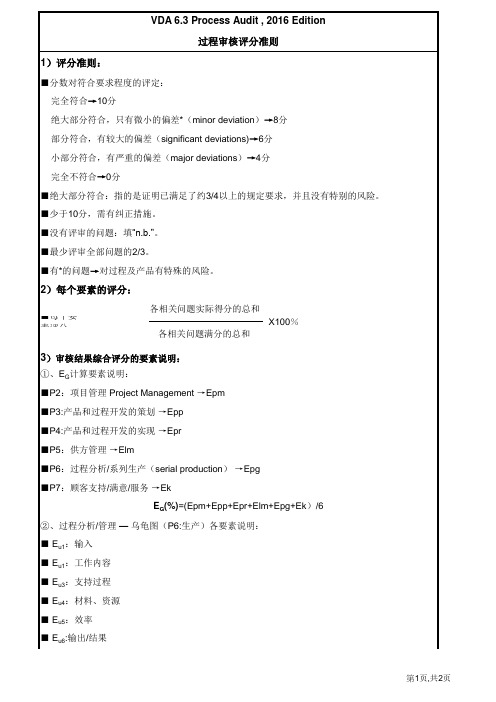
第2页,共2页
完全不符合→0分
■绝大部分符合:指的是证明已满足了约3/4以上的规定要求,并且没有特别的风险。
■少于10分,需有纠正措施。
■没有评审的问题:填“n.b."。
■最少评审全部问题的2/3。
■有*的问题→对过程及产品有特殊的风险。
2)每个要素的评分:
■每个要 素评分
各相关问题实际得分的总和
X100% 各相关问题满分的总和
3)审核结果综合评分的要素说明: ①、EG计算要素说明: ■P2:项目管理 Project Management →Epm ■P3:产品和过程开发的策划 →Epp ■P4:产品和过程开发的实现 →Epr ■P5:供方管理 →Elm ■P6:过程分析/系列生产(serial production) →Epg ■P7:顾客支持/满意/服务 →Ek
过程审核评分准则
■ Eu7:零件运输(Transport/Parts Handling) 4)审核结果的综合评分Overall Assessment:
总符合率EG(%) EG>=90
对过程的评定 符合
级别名称 A
80=<EG<90
有条件符合
B
EG<80
不符合
C
■审核结果的综合评分-降级规则
如果EG≥90%, 且P2…P7、E1…En、EU1…Eu7都>80%,评为A级;反之,则评为B级(A→B)
VDA 6.3 Process Audit , 2016 Edition
过程审核评分准则
1)评分准则:
VDA6.3量产产品过程审核检查表

1、不同状态产品应分区域存放 2、不合格品或返工品标注标识 3、隔离区域产品要有不能擅自进入的措施跟进
P 6.2.6
是否采取了措施,防止在材料/零部件流转的过 程中,发生混合/搞错的情况?
1、合理/优化的材料和零部件流转,防止不同物料发生混合 2、必须确保能够识别错误装配件,并能够及时地加以剔除 3、针对剩余料、隔离件、返工件以及经过产品审核后再用的零部件 等,重新投入生产的程序,必须进行明确的规范 4、对于内部搁置的剩余料,必须清点数量,相应加以标识并储存好
运行证据
1、作业文件、检验文件易于得到 2、检测工具配置到位 3、过程参数一览表 4、过程质量控制卡界限设定 5、设备、工装模具编号 6、设备能力证明
P 6.2.2
对生产工艺流程是否进行了放行,并且对设置数 据进行了采集?
P 6.2.3
使用的生产设备是否可以满足客户对具体产品提 出的要求?
*P 6.2.4
1、过程指标设定 2、对过程实现数据收集与评价 3、当未达成目标时的原因分析和改进记录
1、编制了质量控制卡;对过程数据以及过程参数进行了监控 2、一旦过程出现问题,及时采取了措施并加以记录 3、对于过程的偏差,如对产品有影响,就必须得到客户批准 4、缺陷类型及其发生频次,应记录并分析评价,同时采取针对性的措 施 5、对缺陷成本加以记录,并按失效原因进行评价
1、产品标识/物资流转卡 2、防止不良品混合的管理文件
P 6.3 哪些岗位为过程提供了支持?(人力资源)
最低要求/与评价的相关性
出发点
P 6.3.1
在监控产品/过程质量方面,是否将相关的责权 和权限委托给了员工?
职责
关注点
1、对于员工各自工作范围内的职责、任务以及权限必须加以描述 2、必须定期以合适的方式,推动和提供员工的质量意识 3、应定期向员工通报客户处的质量状况 4、员工应被包括到持续改进过程当中
VDA6.3审核标准

提问 员工是否按照《设备点检、保养指导卡》进行点检和保养设备? (观察设备保养的实际状况,检查设备点检表填写是否规范) 操作人员上岗资质是否认定?人员素质表是否及时更新? 员工上岗前是否经过工艺、设备、质量、安全等培训,并达标?(员工操作)
员工是否掌握本岗位所有相关的作业要求(控制计划、作业指导书、安全操作规程 、测量作业指导书等),并按照执行?(能够回答出本岗位的产品特性和技术要求 等,观察实际操作) 员工是否掌握本岗位所有测量设备的操作要求,并按照执行?(观察零件测量)
审核要点
相关文件
编号:QCZ12.005/001-001
证据
记录
得分
第 2 页,共 6 页
条款编号 审核要点
6.2.3*
审核要点
6.2.4* 审核要点
6.2.5 审核要点
6.2.6 审核要点
6.3 6.3.1
审核要点
6.3.2*
提问
加工条件变更后再生产是否进行首件检验并记录数据?(停机或过程中断、更换原 材料或厂家、刀具/夹具调整/更换、过程出现不合格调整、设备维修/调整、工艺参 数更改) 所使用的生产设施是否可以满足顾客对产品的特定要求?
6.1.2
是否能在正确的时间、正确的地点(库位、工位)获得所需数量/生产批次数的原材 料?
审核要点
生产现场是否只供应当前装配(生产)状态的零件,对于不装配或加工的零件做出 明确的标识防止混用?
对备件/安全周转量等是否有规定并遵照执行?剩余数量是否按要求合理地中间周转 存放?
6.1.3
审核要点
6.1.4 审核要点
操作人员上岗资质是否被认定?员工是否具备本岗位的操作资格(操作证或岗位资 格证)? 是否有人力资源安排计划? 是否有各级人员年度培训计划并遵照执行? 是否有岗位技能图表,岗位技能图表是否能体现员工所在岗位的技能水平? 员工所操作的岗位是否与技能图表一致? 关键岗位是否有顶岗人员?顶岗人员是否具有相应能力? 通过哪些资源实现了过程?(物资资源) 生产设施/工装的维护及保养是否受控? 是否定期对设备/工装进行全面生产性维护(TPM)? 设备故障病史卡、相同故障频次率记录、备件、备件清单是否齐全? 停用或使用过的工装/工具/设备等是否给予必要的标识,防止混用? 工装/工具/设备等是否进行日常点检,保证使用的状态合格? 通过使用的测试、检验和测量设备,是否能有效地检查质量要求? 是否具有在控制计划/作业指导书中规定的测量设备并且适用? 测量设备是否有合格证明,并在有效期内?(绿漆/合格证) 对控制计划中标明关键产品特性的测量设备是否进行了MSA分析? 是否有《测量作业指导书》并按照执行?(观察操作者测量零件? 测量设备故障或送检的时候是否有代替的检测方案,方案是否可行? 生产工位和测试/检验区域是否满足要求? 有照明要求的工序或工作台是否满足照明要求? 工位设计是否依据人机工程学?(是否便于操作) 岗位上产生的废弃物是否按照要求分类收集处置? 工位器具配备是否齐全? 工装、设施和测试/检验设备是否被正确地存放? 工装、设施和测试/检验设备是否定置摆放,并保持整齐、清洁? 工装、设施和测试/检验设备存放是否有防止生锈、磕碰的措施? 过程实现的效果如何?(有效性、效率、减少浪费) 是否为产品和过程设定了目标要求?
VDA6.3----过程审核,VDA6.5产品审核,内审检查表
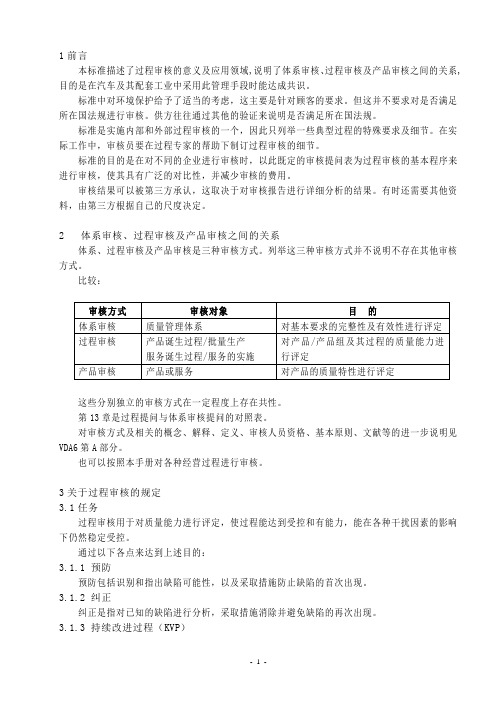
1前言本标准描述了过程审核的意义及应用领域,说明了体系审核、过程审核及产品审核之间的关系,目的是在汽车及其配套工业中采用此管理手段时能达成共识。
标准中对环境保护给予了适当的考虑,这主要是针对顾客的要求。
但这并不要求对是否满足所在国法规进行审核。
供方往往通过其他的验证来说明是否满足所在国法规。
标准是实施内部和外部过程审核的一个,因此只列举一些典型过程的特殊要求及细节。
在实际工作中,审核员要在过程专家的帮助下制订过程审核的细节。
标准的目的是在对不同的企业进行审核时,以此既定的审核提问表为过程审核的基本程序来进行审核,使其具有广泛的对比性,并减少审核的费用。
审核结果可以被第三方承认,这取决于对审核报告进行详细分析的结果。
有时还需要其他资料,由第三方根据自己的尺度决定。
2 体系审核、过程审核及产品审核之间的关系体系、过程审核及产品审核是三种审核方式。
列举这三种审核方式并不说明不存在其他审核方式。
比较:这些分别独立的审核方式在一定程度上存在共性。
第13章是过程提问与体系审核提问的对照表。
对审核方式及相关的概念、解释、定义、审核人员资格、基本原则、文献等的进一步说明见VDA6第A部分。
也可以按照本手册对各种经营过程进行审核。
3关于过程审核的规定3.1任务过程审核用于对质量能力进行评定,使过程能达到受控和有能力,能在各种干扰因素的影响下仍然稳定受控。
通过以下各点来达到上述目的:3.1.1 预防预防包括识别和指出缺陷可能性,以及采取措施防止缺陷的首次出现。
3.1.2 纠正纠正是指对已知的缺陷进行分析,采取措施消除并避免缺陷的再次出现。
3.1.3 持续改进过程(KVP)持续改进的意义在于用许多细小的改进来优化整个体系。
过程审核的措施落实以后可以改进过程,使过程更有能力、更稳定可靠。
3.1.4 质量管理评审过程审核帮助企业最高管理者得出质量管理体系的各部分是否有效的结论。
3.2 原因过程审核可以分为计划内(针对体系和项目)和计划外(针对事件)审核。
VDA6.3过程审核汽车产品品质管理
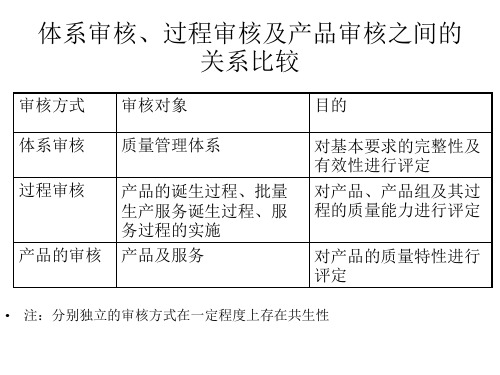
末次会议
• 1,末次会议是审核员在审核期间发现的所 有情况的总结
• 2,审核员要对审核的结果进行说明、解释 并说明什么地方有缺陷及有改进的潜力, 同时说明审核结果的理由
• 3,必须确定纠正措施的完成期限 • 4,被审核人员要在审核结果上签名确认审
核结果
纠正措施
• 定义:是针对审核中发现的缺陷要在商定 期限内完成纠正措施的实施计划
须对措施进行修订,必要时需指定复审计划。
复审的可能
• 1,完整的审核并需重新进行评定 • 2,只对具体的有关过程 (部分过程)进行
复审,必须要对有缺陷的项目进行复审。
审核报告及存档
审核报告包括下列项目: —过程负责人/参加审核人员 —过程描述(范围)如:设备、工艺、产品、服务 —审核的原因 —结果描述(产品生产/实施服务符合质量要求的程度) —降级标准并说明理由 —措施完成期限 —应急措施 —不能评定的审核问题或增加的审核问题 —对每个审核提问项的说明 —对发现的缺陷要指出所参照的文件 注:A,在审核报告中只对审核过程中和末次会议上讨论的项目进行描述。 对每项缺陷要指出其在审核提问表中对点进行如下描述: 1,问题描述 2,发现的情况(例如:缺陷的类型、缺陷的地点) B,在审核报告中也可以提审核中发现的优缺点。
过程审核提问表
• A,产品诞生过程 —产品开发策略 —产品开发实施 —过程开发策略 —过程开发实施 • B,批量生产 —供方/原材料 —生产 —人员/素质 —生产设备/工装 —运输/搬运/贮存/包装 —缺陷分析/纠正措施/持续改进 —服务/顾客满意程度
结构
提问表可分为: • 关于两个主过程和每个要素的综述 • 提问 —要求/说明 —需考虑要点,审核时各相关的点必须加以
否是已具有过程开发计划、是否遵 循目标值
- 1、下载文档前请自行甄别文档内容的完整性,平台不提供额外的编辑、内容补充、找答案等附加服务。
- 2、"仅部分预览"的文档,不可在线预览部分如存在完整性等问题,可反馈申请退款(可完整预览的文档不适用该条件!)。
- 3、如文档侵犯您的权益,请联系客服反馈,我们会尽快为您处理(人工客服工作时间:9:00-18:30)。
②、过程分析/管理—乌龟图(P6:生产)各要素说明:
■Eu1:输入
■Eu1:工作内容
■Eu3:支持过程
■Eu4:材料、资源
■Eu5:效率
■Eu6:输出/结果
■Eu7:零件运输(Transport/Parts Handling)
4)审核结果的综合评分Overall Assessment:
■记录
P2.6
项目是否有质量管理计划?是否对其执行情况进行了定期监察以确保其符合性?考虑要点,如:
质量管理计划
■包含在项目计划中
■根据顾客要求/合同(CSR / Contract)
■包含:
⊙产品质量保障规范(外部及內部)
⊙有关键的交付品目(critical delivery items)
⊙定义并任命了相关负责的人员
■过程[识别顾客的QMS要求+开发和过程要求]
■检查:询价和合同文本(i.e. contract review)
3)审核结果综合评分的要素说明:
①、EG计算要素说明:
■P2:项目管理Project Management→Epm
■P3:产品和过程开发的策划→Epp
■P4:产品和过程开发的实现→Epr
■P5:供方管理→Elm
■P6:过程分析/系列生产(serial production)→Epg
■P7:顾客支持/满意/服务→Ek
⊙具备相关资格的专业部门员工
⊙供方
⊙关键路径
■项目预算(budget)
■对项目中的变更(时间,开发规模,...):
⊙应及时加以说明
⊙实现前与顾客进行协商沟通
⊙对资源策划开展复核
⊙Note :上述的变更:由顾客触发的变更or自身内部的变更or供方触发
P2.3
是否具备项目计划,并与顾客进行了协商确定?考虑要点,如:
总符合率EG;=90
符合
A
80=<EG<90
有条件符合
B
EG<80
不符合
C
■审核结果的综合评分-降级规则
如果EG≥90%,
且P2…P7、E1…En、EU1…Eu7都>80%,评为A级;反之,则评为B级(A→B)
如果EG≥80%,
且P2…P7、E1…En、EU1…Eu7都>70%,评为B级;反之,则评为C级(B→C)
⊙事态升级的标准(escalation criteria)
⊙规定了责权关系以及权限(responsibility &
authority)
■记录:证明(事态升级)的有效性。
■风险
⊙技术
⊙供方
⊙交货国家
P3:产品和过程开发的策划
P3.1
是否已经具有产品和过程的特定要求?考虑要点,如:
■开发的产品的要求都已经到位(req’t known)
完全不符合→0分
■绝大部分符合:指的是证明已满足了约3/4以上的规定要求,并且没有特别的风险。
■少于10分,需有纠正措施。
■没有评审的问题:填“n.b."。
■最少评审全部问题的2/3。
■有*的问题→对过程及产品有特殊的风险。
2)每个要素的评分:
■每个要素评分(%)=
各相关问题实际得分的总和
各相关问题满分的总和X100%
⊙团队成员
⊙各方面必要的实现权限
⊙组织机构之间的归口
■供方(supplier)
*P2.2
是否为项目开发而策划并实现了所需的资源,并且通报了变更情况?考虑要点,如:
■资源策划(resource planning)(跨区域跨部门的团队) ,考虑:
⊙项目合同
⊙顾客要求
⊙员工的实际工作负荷(employee workload)
:记录
■定义的过程[记录所有变更]
■说明变更(highlight)
■和顾客协商沟通、评价
■影响到产品质量的变更=>风险评价
■供方(关键群体)参与
■对变更停止的时间点:明确的定义、遵守
■如果不能遵守,则在顾客和供方之间必须以书面形式加以记录。
■SOP之前的变更时间段:不会影响到产品质量。
■变更的实现:考虑SOP之前剩余的时间
VDA 6.3 Process Audit , 2010 Edition
过程审核检查表
序号
审核项目/内容
审核结果记录
评分
P2:项目管理
P2.1
是否建立了项目组织(项目管理),并且为项目管理者以及团队成员确定了各自的任务及权限?考虑要点,如:
■项目管理有能力vs顾客要求。
■组建项目管理的过程。
■权限
⊙项目负责人
■应满足顾客的具体要求
■项目计划(PM Plan) :
⊙应纳入:内部里程碑,顾客里程碑
⊙在里程碑时刻,应开展评价(评审)
△策划的事项是否都得到实现(done ?)
△是否达到了要求的实现程度(maturity level ?)
⊙定期调整:针对实际发生的变更
■项目计划发生变更=>
⊙内部的联络沟通
⊙同顾客进行协商沟通
VDA 6.3 Process Audit , 2010 Edition
过程审核评分准则
1)评分准则:
■分数对符合要求程度的评定:
完全符合→10分
绝大部分符合,只有微小的偏差*(minor deviation)→8分
部分符合,有较大的偏差(significant deviations)→6分
小部分符合,有严重的偏差(major deviations)→4分
⊙总体项目的时间安排(timing)
⊙考虑产品和过程技术规范=>验证和确认
■定期监控(regular check)
*P2.7
是否建立了事态升级程序,及其是否得到了有效的实施?考虑要点,如:
■过程[事态升级模型(风险管理)Escalation]
⊙对于项目中的不符合情况,一旦影响到总体的时
间表
⊙考虑具体的顾客要求
*P2.5
组织内部以及顾客处的相关负责人员是否参与了变更控制系统?考虑要点,如:
■变更管理的人员及其代理人(Change managemet personnel)
⊙顾客
⊙组织内部
⊙供方
■一套变更的规定change regulation(变更的负责人,分发,处
理时间,事态升级路径)。
■必须满足“顾客就变更管理的要求(CSR for handling change)
■项目计划会顾及到关键的供方群体。
■项目计划=>关键路径则(critical path)
■质量管理计划(QM plan) :项目计划的组成部分。
P2.4
项目组织是否在项目进程中提供了可靠的变更管理?考虑要点,如:
■变更管理需要满足特定的顾客要求。
■变更的可行性检验(manufacturing feasibility check)