电弧炉炼钢高效化能量集成节能技术
铁合金冶炼过程的高效能量利用与节能技术

铁合金冶炼过程的高效能量利用与节能技术1. 背景铁合金作为钢铁生产的重要原料,其冶炼过程对能源的消耗相当巨大而能源的消耗不仅直接关系到生产成本,也直接影响到环境因此,研究铁合金冶炼过程的高效能量利用与节能技术,既具有重要的经济效益,也具有深远的社会意义2. 铁合金冶炼过程中的能量消耗铁合金的冶炼过程主要包括矿石的处理、熔炼、精炼和成型等几个阶段在这个过程中,能量的消耗主要体现在以下几个方面:•矿石的处理:包括矿石的破碎、研磨等过程,这些过程需要大量的电力•熔炼:主要是将矿石熔化成铁水,这个过程需要大量的燃料,如焦炭、煤气等•精炼:通过氧化还原反应等化学方法,去除铁水中的杂质,这个过程同样需要大量的能源•成型:将精炼后的铁水浇铸成合金,这个过程也需要一定的能源3. 高效能量利用与节能技术为了提高铁合金冶炼过程的能量利用效率,减少能源消耗,研究者们开发了一系列的节能技术3.1 矿石的处理在矿石的处理过程中,通过优化破碎和研磨的工艺,可以有效地减少电力的消耗例如,采用高效的破碎机和磨机,可以减少能源的消耗3.2 熔炼在熔炼过程中,可以通过提高炉子的热效率,减少燃料的消耗例如,采用先进的燃烧技术,可以使燃料燃烧得更充分,从而提高热效率3.3 精炼在精炼过程中,可以通过优化化学反应的工艺,减少能源的消耗例如,采用高效的氧化还原反应技术,可以减少能源的消耗3.4 成型在成型过程中,可以通过优化浇铸的工艺,减少能源的消耗例如,采用高效的浇铸技术,可以减少能源的消耗4. 结论铁合金冶炼过程的高效能量利用与节能技术,不仅可以降低生产成本,也可以减少对环境的影响因此,未来的研究应该更加注重这方面的技术创新和应用5. 节能技术的具体应用在铁合金冶炼的各个环节中,应用节能技术不仅可以提高能量利用率,还可以降低生产成本,减少环境污染以下是一些具体的应用实例5.1 直接还原铁技术直接还原铁技术是一种替代传统炼铁工艺的方法,其主要特点是将铁矿石直接还原为铁,省去了烧结和球团的步骤这种技术可以显著减少能源消耗,降低生产成本,同时减少环境污染5.2 熔池熔炼技术熔池熔炼技术是一种高效节能的冶炼方法,其主要特点是将熔融金属和熔剂放入一个大的熔池中进行熔炼这种技术可以提高热效率,减少能源消耗,同时提高铁合金的质量和产量5.3 电弧炉炼钢技术电弧炉炼钢技术是一种利用电弧产生的高温进行冶炼的方法,其主要特点是可以快速加热和熔化金属,从而减少能源消耗这种技术还可以精确控制冶炼过程,提高铁合金的质量和产量5.4 电磁搅拌技术电磁搅拌技术是一种利用电磁场对熔融金属进行搅拌的方法,其主要作用是提高金属的混合程度和温度均匀性,从而减少能源消耗这种技术还可以提高铁合金的质量和产量6. 节能技术的挑战与展望虽然铁合金冶炼过程中的节能技术已经取得了一定的进展,但仍面临着一些挑战首先,节能技术的应用需要投入大量的资金和技术,对于一些小型企业来说,这可能是一个难以承受的负担其次,节能技术的应用需要改变传统的冶炼工艺,这可能会对企业的生产造成一定的影响然而,随着全球能源紧张和环境问题日益严重,铁合金冶炼过程中的节能技术将会得到更多的关注和支持我们期待未来的研究能够在提高能量利用率、降低生产成本和减少环境污染等方面取得更大的突破7. 结语铁合金冶炼过程的高效能量利用与节能技术,对于降低生产成本、减少能源消耗和保护环境具有重要意义我们期待未来的研究能够在提高能量利用率、降低生产成本和减少环境污染等方面取得更大的突破8. 政策与经济激励为了推动铁合金冶炼行业的节能减排,政府部门和国际组织通常会出台一系列的政策和经济激励措施这些措施可能包括税收减免、补贴、低息贷款等,主要目的是降低企业采用节能技术的门槛,鼓励更多的企业投入节能技术的研发和应用9. 教育和培训教育和培训也是推动铁合金冶炼行业节能技术应用的重要手段通过专业培训和继续教育,可以提高企业员工对节能技术重要性的认识,增强他们的节能意识和技术能力此外,通过与高校和研究机构的合作,可以培养更多的节能技术人才,为铁合金冶炼行业的节能改造提供技术支持10. 跨部门合作铁合金冶炼过程中的节能技术改造需要多个部门的协同合作除了企业自身,还需要政府部门、科研机构、金融机构等的支持通过跨部门的合作,可以整合各方资源,形成合力,推动节能技术的研发和应用11. 结论铁合金冶炼过程中的高效能量利用与节能技术,不仅对企业的经济效益有重要影响,也对环境保护具有深远意义通过采用先进的节能技术,提高能量利用率,可以降低生产成本,提高企业竞争力同时,也能减少能源消耗,减轻对环境的影响我们期待未来的研究能够在提高能量利用率、降低生产成本和减少环境污染等方面取得更大的突破12. 展望未来随着科技的不断进步,新的节能技术将会不断涌现未来的研究应该更加注重这些新技术的研发和应用,以实现铁合金冶炼过程的高效能量利用同时,也需要进一步加强政策引导和經濟激励,推动企业采用节能技术通过教育和培训,提高企业员工的节能意识和技术能力此外,还需要加强跨部门的合作,形成合力,推动铁合金冶炼行业的节能改造13. 结语铁合金冶炼过程的高效能量利用与节能技术,对于降低生产成本、减少能源消耗和保护环境具有重要意义我们期待未来的研究能够在提高能量利用率、降低生产成本和减少环境污染等方面取得更大的突破同时,也需要进一步加强政策引导和經濟激励,推动企业采用节能技术通过教育和培训,提高企业员工的节能意识和技术能力此外,还需要加强跨部门的合作,形成合力,推动铁合金冶炼行业的节能改造14. 参考文献[由于要求不带参考文献,此处不列出]15. 附录[由于要求不带附录,此处不列出]。
电弧炉高效低耗炼钢技术阐述

电弧炉高效低耗炼钢技术阐述1、电弧炉炼钢的发展及现代电弧炉炼钢的概念自上世纪中叶至今,虽然转炉炼钢技能取得了长足的进步,但国际电炉的钢比例不断增加,从1950年的7.3%增加到2003年的33.1 %,其中美国从6.2%增加到48.9% ,2004年美国电炉钢比例达53%。
自1950年以后,电弧炉炼钢所占比例迅速上升,变成了与转炉流程相抗衡的第二大钢铁制造流程,主要原因有:(1)平炉炼钢由氧气转炉炼钢所代替,积累的废钢转由电弧炉炼钢流程来消化。
(2)超高功率电弧炉炼钢技能的成功使用,使电弧炉炼钢的功率显著进步,出产成本大幅度下降。
(3)连铸、连轧技能的成功使用,废钢-电弧炉炼钢-连轧型的“小钢厂”敏捷发展,占据了型材出产比例。
就电弧炉炼钢的现在的技能和化学能利用技能的长足进步,冶炼周期已由60min进入50-40min,因此其出产节奏已迫近转炉水平。
1993年6月,殷瑞钰和徐匡迪教授在上海召开了“当代电炉流程与工程疑问的研讨会”。
在会上,他们依据上世纪8O年代以来电炉炼钢技能的发展状况,提出了现代电炉炼钢一词及总结了现代电炉炼钢的特征。
现代电弧炉炼钢的特征总结为:高效、节能、环保、电炉出产节奏转炉化,钢的二次精粹在线化和钢的凝结进程接连化,建立在接连轧制基础上的商品专业系列化和可持续发展。
其中现代电弧炉炼钢的首要特征即是:高效低耗。
多项现代电弧炉高效低耗炼钢技能在中国得到了研讨、推行及使用与长足的发展。
2、现代电弧炉高效低耗炼钢技术在我国的应用2.1优化电弧炉炉料结构电弧炉炼钢主要固态炉料有废钢、生铁、直接还原铁(DRI)和热压块铁(HBI)等。
废钢基本来源有三种:自产废钢、加工厂废钢、循环旧废钢。
炉料结构对电弧炉炼钢的各项指标都有重大影响。
优化炉料结构不只有利于完成技能的最好化,并能给公司带来经济效益,更可以为合理的使用有限的资本提供牢靠的根据。
天津钢管公司炼钢厂具有国内容量较大的炼钢电弧炉,并且是当前我国为数不多的长时间倾加直接还原铁的电弧炉炼钢厂,研讨其炉料的构造对我国电弧炉炼钢铁源的拓宽有重要的指导意义。
高效化电弧炉炼钢技术

(壹佰钢铁网推荐)提高电弧炉炼钢的生产率、生产速率和能量利用效率是近6o年来技术发展的主流方向,有以下几点。
超高功率供电技术。
2O世纪60年代,美国联合碳化物公司提出了超高功率电弧炉(UHP—EAF)的概念,超高功率电弧炉炼钢理念主导了近60年电弧炉炼钢生产技术的发展,其中心思想是最大的发挥主变压器能力,包括以下2个方面:①提高每吨钢配置的主变压器容量,即将功率级别由200~3O0kV.A/t提高至500~600kV.A/t,70年代以后,又提高至800~1000kV.A/t。
②极大地提高最大功率供电时间的比例。
大型超高功率电弧炉的操作区问的功率因数接近于0.866,工作电流低于短路电流的二分之一,在该工况下,由于谐波的影响,冶炼过程的操作电抗不同于电路的短路电抗,操作电抗的非线性是大型电弧炉炼钢过程最重要的技术特征。
(2) 辅助能源。
电弧炉冶炼速率和吨钢电耗在很大程度上取决于废钢熔化的快慢。
电弧炉炼钢在钢铁料熔化过程中的热工特点使炉内存在3个冷区。
(3) 减少非通电时间。
减少供电功率低、占时长的还原期时间,始终是电弧炉炼钢工作者的努力方向。
8O年代以后,由于二次精炼技术的发展和普及,首先的受益者就是电弧炉炼钢过程,其后底出钢技术使非通电时间所占比例大大减少。
减少非通电时间比例方面主要有3点进步:①装备大型化、机械化和自动化水平提高;②炉料结构改善、装料次数由3次减至2次或1次;③管理水平提高,实现冶炼一精炼一连铸全流程匹配顺行。
(4) 废钢预热。
电弧炉炼钢过程中真正的节能措施是电弧炉炉气带走的能量回收利用技术。
电弧炉炼钢总能量中有10~2O的能量随烟气而排放,利用这部分能量来预热废钢,可达到提高电弧炉炼钢节能、降耗、提高生产效率的目的。
(5) 连续化生产。
在现代钢铁生产流程中,烧结、高炉炼铁以及后步的连铸、连轧基本上都实现了半连续或连续化生产,而炼钢过程仍然是至今流程中唯一间歇式操作的环节,钢铁生产的高效化进程,将促进连续化生产技术的诞生。
电炉炼钢节能措施

电炉炼钢节能措施引言随着环保意识的增强和能源成本的上升,节能已经成为了各行各业的重要议题。
在钢铁行业中,电炉炼钢是一种常见的钢铁生产工艺。
然而,传统的电炉炼钢过程存在着能源浪费的问题,需要采取节能措施来提高能源利用效率。
本文将介绍一些有效的电炉炼钢节能措施,以帮助钢铁企业减少能源消耗,提高盈利能力。
1. 优化电炉操作参数合理的电炉操作参数对节能至关重要。
以下是一些常见的优化措施:•温控系统优化:通过对电炉的温度控制系统进行优化,可以实现更精确的温度控制,避免能源的过度消耗。
•母线电压优化:对电炉的母线电压进行优化,可以实现更高效的电能转换,降低能源浪费。
•电炉功率控制:合理控制电炉的功率,避免过高或过低的功率消耗,提高能源利用效率。
2. 废气余热回收利用电炉炼钢过程中产生的废气中含有大量的热能,如果能有效利用这些余热,就可以减少能源的消耗。
以下是一些常见的废气余热回收利用措施:•废气余热锅炉:通过安装废气余热锅炉,将废气中的热能转化为蒸汽或热水,供给其他工艺过程使用或供热。
•废气余热发电:通过废气余热发电系统,将废气中的热能转化为电能,提供给电网使用,达到能源的再生利用。
•废气余热回采:通过热交换器等设备,将废气中的热能回收,供给其他工艺过程使用,减少能源的浪费。
3. 电炉热保护措施电炉炼钢过程中,合理的热保护措施可以降低能源消耗,延长设备的使用寿命。
以下是一些常见的电炉热保护措施:•保温材料优化:优化电炉的保温材料,减少热量的散失,提高能源的利用效率。
•空气冷却系统优化:通过对电炉的空气冷却系统进行优化,减少冷却的能量损失,提高能源利用效率。
•炉衬维护:定期检查和维护电炉的炉衬,保证其完整性,减少热量的散失,延长设备的使用寿命。
4. 电炉技术改进通过技术改进,可以进一步提高电炉的能源利用效率。
以下是一些常见的技术改进措施:•高效炼钢工艺:采用先进的电炉炼钢工艺,如负压炼钢等,提高炼钢效率,减少能源消耗。
金属冶炼技术突破实现高效能源利用的关键方法

金属冶炼技术突破实现高效能源利用的关键方法金属冶炼是现代工业中不可或缺的一部分。
然而,传统的金属冶炼方法过程繁琐、能源消耗大,对环境造成了严重的污染。
为了实现高效能源利用,突破传统金属冶炼技术的限制,许多创新方法不断涌现。
本文将探讨几种关键方法,帮助金属冶炼行业实现高效能源利用。
1. 电弧炉冶炼技术电弧炉冶炼技术是一种基于电能转化的高效能源利用方法。
相较于传统的炼铁和炼钢方法,电弧炉冶炼技术具有许多优势。
首先,它可以利用废旧金属进行再生冶炼,减少资源浪费。
其次,电弧炉冶炼技术具有灵活性,可以适应各种金属的冶炼需求。
最重要的是,该技术不需要预先生产铁和焦炭,减少了能源的消耗。
因此,电弧炉冶炼技术被认为是实现高效能源利用的重要方法之一。
2. 高温燃烧技术高温燃烧技术是另一种实现高效能源利用的重要方法。
在金属冶炼过程中,燃料的燃烧提供了必要的热能。
然而,传统的燃烧技术存在能源利用率低的问题。
为了解决这一问题,一种被广泛使用的方法是采用高温燃烧技术,例如高温炉和高温氧燃烧。
这些技术可以提高燃烧效率,减少燃料的用量,从而实现高效能源利用。
此外,高温燃烧技术还可以减少污染物的排放,改善环境质量。
3. 废热回收技术废热回收技术是另一个可以实现高效能源利用的关键方法。
在金属冶炼过程中,大量的热能被散发到周围环境中。
传统的金属冶炼工厂通常只利用了一小部分的热能,而大部分则被浪费。
通过采用废热回收技术,可以将这些被浪费的热能重新利用。
废热回收技术基于热交换原理,将烟气、冷却水等与高温焚烧煤炭或气体的热交换,从而回收并利用了这些废热。
这种技术可以大幅提高能源利用效率,减少能源消耗。
4. 先进金属冶炼设备除了创新的技术方法,引进先进的金属冶炼设备也是实现高效能源利用的关键。
先进设备能够通过提高冶炼过程的自动化程度和控制精度,有效减少能源的浪费。
例如,采用先进的传感器和控制系统,可以实现精确的温度控制,避免能源的过度消耗。
第四章 现代电弧炉炼钢的发展与节能

第四章现代电弧炉炼钢的发展与节能现代电弧炉炼钢的发展与节能1. 引言现代电弧炉是一种重要的钢铁冶炼设备,其发展与节能对于钢铁工业的可持续发展至关重要。
本文将详细介绍现代电弧炉炼钢的发展历程以及相关的节能技术和措施。
2. 现代电弧炉的发展2.1 电弧炉的基本原理电弧炉是利用电弧高温熔化金属的设备,其基本原理是通过电极产生电弧,在电弧的高温作用下将金属加热至熔点并进行冶炼。
2.2 电弧炉的发展历程电弧炉的发展经历了多个阶段,从最早的直流电弧炉到现代的交流电弧炉。
随着电力技术的进步和电弧炉冶炼工艺的改进,电弧炉的效率和生产能力得到了显著提高。
3. 现代电弧炉炼钢的节能技术和措施3.1 高效电极材料的应用现代电弧炉中采用高效电极材料,如碳化钙电极和石墨电极,可以提高电弧的稳定性和热效率,减少能量的损耗。
3.2 电弧炉热能回收利用通过安装热能回收装置,将电弧炉产生的热能回收利用,可以用于加热其他工艺介质或发电,提高能源利用效率。
3.3 电弧炉冶炼过程的优化通过优化电弧炉的冶炼工艺,如合理控制电弧炉的操作参数、优化冶炼炉料的配比等,可以降低能耗,提高炉渣的利用率和钢水质量。
3.4 废热利用技术的应用利用废热利用技术,如余热锅炉和废热发电技术,将电弧炉产生的废热转化为热能或电能,进一步提高能源利用效率。
4. 现代电弧炉炼钢的节能效果现代电弧炉炼钢的节能效果显著。
通过应用节能技术和措施,可以降低电弧炉的能耗,提高炼钢效率,减少环境污染。
5. 结论现代电弧炉炼钢的发展与节能对于钢铁工业的可持续发展至关重要。
通过应用高效电极材料、热能回收利用技术、优化冶炼工艺和废热利用技术,可以显著降低电弧炉的能耗,提高能源利用效率,实现绿色环保的钢铁生产。
未来,随着科技的不断进步,电弧炉炼钢的节能技术和措施还将不断创新和完善,为钢铁工业的可持续发展做出更大贡献。
电弧炉炼钢新技术-2011

珠钢手指竖井电弧炉
珠钢150t手指竖井电弧炉投产于1999年8月
珠钢手指竖井电弧炉
主要设计参数:
竖井 高8 . 35 m, 宽2 . 4 3 m, 长7 . 1 2 m 熔池直径 6.20m 炉子容量 180t 出钢量 150t 热留钢量 约30t 变压器容量 120MV· A 氧油烧嘴 6支,3.5MW/支 水冷式炉门氧枪 4000~5000Nm3/h 水冷式炉壁氧枪 1600~2000Nm3/h
余热利用
炉料预热
如何利用废气及二次 燃烧产生的热量?
在电炉炼钢的各项热损 失中,废气余热是最 容易利用的。
炉料预热
竖井炉式、双炉壳式、连续加料式等炉料预热 废钢预热技术是在高温炉气排放之前,通过废钢(炉料)产生热 交换,把热量传给废钢,提高废钢的温度,从而达到加快废钢 (炉料)熔化、降低电耗,提高生产率的目的。
该工艺与传统的废钢预热相似,只不过预热是在炉壳内 而不是在废钢料斗内进行。最初在瑞典的SKF使用; 该工艺设备的结构特点是两个炉壳共用一套电源和电极 系统,电极在两个炉壳间交替使用。
双炉壳电弧炉
双炉壳电弧炉
最初,共用电极沿轨道从一个炉壳移动到另一个炉 壳。 现在大多使用可在两炉壳间来回摆动的炉盖和电极系 统。设备一般包括:两个相同的炉壳(一个低些,一 个高些)、一个炉盖、一套电极臂和提升装置、一套 电源供应系统。 电极在两个炉壳之间交替使用,当一个炉子在熔化 时,其炉气用来预热另一个炉子的废钢。废钢被预热 的越多,能量节约的越多。
双竖井电弧炉 (Double Shaft Furnace)
1993年10月,第 一座双竖井电弧 炉分别诞生在法 国Unimetal Montereau与卢 森堡Arbed,炉 容分别为90t与 95t。
炼钢节能措施

谢谢
节能型钢包炉:采 用高效保温技术, 降低能耗
节能型炼钢工艺
采用先进的节 能型炼钢工艺, 如电弧炉炼钢、 转炉炼钢等。
01
采用节能型材料, 如节能型耐火材 料、节能型保温 材料等。
03
02
采用节能型设备, 如高效节能型加 热炉、节能型冷 却塔等。
04
采用节能型工艺 控制,如节能型 温度控制、节能 型压力控制等。
降低能源消耗
03
发展可再生能源:大力发展太阳能、风能、
水能等可再生能源,降低对化石能源的依赖
04
提高能源管理水平:建立完善的能源管理体
系,提高能源管理水平,降低能源消耗
提高能源利用效率
01
优化生产工艺: 采用先进的生
产工艺和技术, 降低能源消耗
03
节能技术应用: 采用节能技术 和设备,提高 能源利用效率
02
加强能源管理: 建立能源管理体 系,对能源消耗 进行监测和优化
04
节能意识培养: 加强员工节能 意识,提高能 源利用效率
降低能源消耗
优化生产工艺:采用先进的生产
01
工艺,降低能源消耗 节能设备:使用节能设备,降低
02
能源消耗 节能技术:采用节能技术,降低
03
能源消耗 节能管理:加强能源管理,降低
炼钢节能措施
演讲人
01
节能技术
02
能源管理
目录
03
节能政策
节能技术
节能型炼钢设备
节能型电弧炉:采 用高效节能技术, 降低能耗
节能型转炉:采用 高效燃烧技术,提 高能源利用率
节能型连铸机:采 用高效冷却技术, 降低能耗
科技成果——电弧炉炼钢高效洁净化技术

科技成果——电弧炉炼钢高效洁净化技术技术开发单位北京科技大学技术领域钢铁冶金成果简介针对电弧炉炼钢冶炼周期长、能量利用率低、生产成本高等问题,本项科技成果以高效、低耗、节能、优质生产为目标,研发了电弧炉炼钢复合吹炼技术,发明了电弧炉熔池内气-固喷吹脱磷、高效吸附脱氮、出钢在线连续喷粉脱氧等新方法,攻克了电弧炉高品质钢生产的世界难题。
1、以集束供氧、同步长寿底吹搅拌等技术为核心,开发了电弧炉复合吹炼技术,实现了电弧炉炼钢供电、供氧及底吹等单元的操作集成,满足多元炉料条件下的电弧炉炼钢复合吹炼的技术要求。
电弧炉复合吹炼2、发明了电弧炉熔池内气-固喷吹冶炼新工艺,利用钢液面下的喷枪向熔池内部直接喷射O2-CaO,依靠反应气体裹挟熔态渣粒直接反应实现快速深脱磷,颠覆了传统的渣-钢界面反应脱磷方式,冶炼终点磷含量降至0.004%,实现了电弧炉炼钢低成本快速深脱磷。
熔池内气-固喷吹3、研发了电弧炉多元介质混合喷吹脱氮工艺及装备,冶炼终点钢液氮含量由原来的0.0060%以上稳定降低至0.0045%以下,突破了电弧炉炼钢氮含量控制技术瓶颈,是炼钢洁净化技术的重大创新。
CO2-Ar动态底吹4、发明了电弧炉出钢过程在线连续喷粉脱氧技术,利用载气-脱氧粉剂高速射流直接冲击出钢钢流,碳质微粒与高温钢液快速接触,瞬态反应生成脱氧气泡实现无铝(硅)优先脱氧150-200×10-6,显著提高了合金收得率,钢中初始沉淀脱氧产物减少40-50%,产品质量明显提升。
出钢过程在线喷粉应用情况所处研究阶段:成熟技术和产品。
目前相关技术及产品在国内外广泛推广应用,已覆盖全国30%以上电炉钢产能,并出口至俄罗斯、意大利、土耳其、印度尼西亚等二十余个国家和地区。
本技术成果可推广应用至全国乃至全世界所有的短流程炼钢领域,特别是以优质特钢生产为主的电弧炉炼钢企业;且部分技术可在长流程炼钢领域推广应用。
投资估算和经济效益分析本技术投资规模约500万元,预期成本降低20-30元/吨钢,且高品质钢生产更加稳定,产品附加值明显提升。
电弧炉炼钢工艺的节能降耗技术-周卫国

电弧炉炼钢工艺的节能降耗技术周卫国(西安建筑科技大学华清学院冶金工程系,陕西西安710043)摘要:世界范围内能源价格的持续上涨,不断推动电炉炼钢工艺和操作的优化。
人们致力于最高效率条件下的最低成本生产,只有在两者兼顾的情况下,才能保证电炉炼钢工艺的竞争力。
对于复杂电弧炉炼钢工艺的优化,不仅需要丰富的炼钢知识,而且需要合适的成套工艺技术。
只有这样,才能实现炼钢过程中化学能和电能的高效利用,达到冶炼工艺的最优化。
本文介绍了世界电弧炉炼钢技术的发展,并从增加能量供应,增加输入功率和提高能量的利用效率三个方面分析了电弧炉炼钢企业所采用的主要节能技术。
关键词:电弧炉炼钢,能源效率,电能,节能降耗Energy saving technology of EAF steelmakingZHOU Wei-Guo(Xi'an University Of Architecture And Technology Huaqing College of metallurgy engineering, Xi'an Shaanxi700043)Abstract: rising energy prices worldwide, and constantly promote the optimization of EAF steelmaking process and operation. The lowest cost people committed to the highest efficiency under the conditions of production, but in both cases, in order to ensure the competitiveness of electric arc furnace steelmaking process. For the optimization of complex process of the electric arc furnace steelmaking, requires not only knowledge, but also need to complete the process of appropriate technology. Only in this way, chemical energy to achieve the steelmaking process and energy efficient use, optimal smelting process. This paper presents the development of electric arc furnace steelmaking technology, and from increasing energy supply, increasing the input power and the three aspects to improve the efficiency of energy utilization analysis of the main energy saving technologies used in electric arc furnace steelmaking enterprises.一前言电弧炉炼钢的发展及现代电弧炉炼钢自上世纪中叶至今, 尽管转炉炼钢技术取得了长足的进步, 但世界电炉钢的比例不断增长, 从1950年的713% 增长到2003 年的3311% , 其中美国从612% 增长到4819% , 2004 年美国电炉钢的比例达53% [ 1] 。
第四章 现代电弧炉炼钢的发展与节能
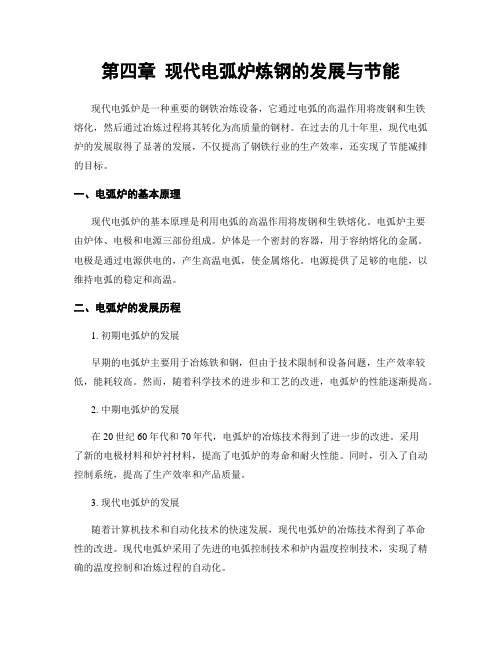
第四章现代电弧炉炼钢的发展与节能现代电弧炉是一种重要的钢铁冶炼设备,它通过电弧的高温作用将废钢和生铁熔化,然后通过冶炼过程将其转化为高质量的钢材。
在过去的几十年里,现代电弧炉的发展取得了显著的发展,不仅提高了钢铁行业的生产效率,还实现了节能减排的目标。
一、电弧炉的基本原理现代电弧炉的基本原理是利用电弧的高温作用将废钢和生铁熔化。
电弧炉主要由炉体、电极和电源三部份组成。
炉体是一个密封的容器,用于容纳熔化的金属。
电极是通过电源供电的,产生高温电弧,使金属熔化。
电源提供了足够的电能,以维持电弧的稳定和高温。
二、电弧炉的发展历程1. 初期电弧炉的发展早期的电弧炉主要用于冶炼铁和钢,但由于技术限制和设备问题,生产效率较低,能耗较高。
然而,随着科学技术的进步和工艺的改进,电弧炉的性能逐渐提高。
2. 中期电弧炉的发展在20世纪60年代和70年代,电弧炉的冶炼技术得到了进一步的改进。
采用了新的电极材料和炉衬材料,提高了电弧炉的寿命和耐火性能。
同时,引入了自动控制系统,提高了生产效率和产品质量。
3. 现代电弧炉的发展随着计算机技术和自动化技术的快速发展,现代电弧炉的冶炼技术得到了革命性的改进。
现代电弧炉采用了先进的电弧控制技术和炉内温度控制技术,实现了精确的温度控制和冶炼过程的自动化。
三、现代电弧炉的节能技术为了实现钢铁行业的可持续发展,现代电弧炉采用了一系列的节能技术,以降低能耗和减少环境污染。
1. 高效电极材料现代电弧炉采用高效的电极材料,如碳化钙电极和碳化硅电极,具有较低的电阻和较高的导电性能。
这些电极材料可以提高电弧炉的能效,并减少电能的损耗。
2. 高效炉衬材料现代电弧炉采用高效的炉衬材料,如镁砖和碳化硅砖,具有较高的耐火性能和导热性能。
这些炉衬材料可以减少炉内的热量损失,并提高炉子的热效率。
3. 智能化控制系统现代电弧炉配备了智能化的控制系统,可以实时监测和调整炉内温度和电弧稳定性。
通过精确的温度控制和电弧控制,可以减少能耗和提高生产效率。
钢铁冶炼中的能量消耗与节能技术

钢铁冶炼中的能量消耗与节能技术钢铁冶炼是现代工业中不可或缺的一环,然而,其高能耗一直是业内关注的焦点之一。
在钢铁生产过程中,能源消耗占据了相当大的比重,因此,寻求节能技术是行业持续发展的必然选择。
本文将深入探讨钢铁冶炼中的能量消耗情况,并探讨一些可行的节能技术。
首先,我们需要了解钢铁冶炼中能量消耗的主要来源。
传统的钢铁冶炼过程主要依赖于高炉炼铁和转炉炼钢,这些过程都需要大量的煤炭、焦炭和电力作为能源输入。
高炉炼铁过程中,煤炭和焦炭主要用于还原矿石中的铁氧化物,同时产生高温来熔化铁矿石。
而在转炉炼钢过程中,电力则主要用于加热和冶炼熔融的铁水。
这些传统的冶炼方法在能源利用上存在一定的浪费,因此急需引入节能技术。
针对钢铁冶炼中的能源消耗问题,许多新型节能技术已经被提出并逐渐得到应用。
其中之一是煤气化技术。
煤气化是将固体煤转化为可燃性气体的过程,通过这种方法,可以将煤炭转化为合成气,用于代替部分煤炭和焦炭在高炉炼铁过程中的使用。
相比于传统的煤炭燃烧,煤气化能够提高能源利用率,减少碳排放,从而达到节能减排的效果。
另外,炼钢过程中的电力消耗也是需要重点考虑的对象。
传统的转炉炼钢过程中,电弧炉是主要的炉型之一,而电弧炉的能效相对较低,存在较大的能源浪费。
因此,一些新型的电弧炉技术被提出,如半连续电弧炉和直流电弧炉等。
这些新技术在提高能效的同时,还能减少杂质,改善钢材的质量。
除了改进传统的冶炼工艺,还可以通过智能化技术来优化能源利用。
例如,利用先进的数据分析和人工智能技术,可以实现对冶炼过程的精确监控和控制,从而最大限度地提高能源利用率,减少能源浪费。
通过实时监测关键参数,及时调整生产工艺,避免能源的不必要消耗,实现节能减排的目标。
此外,废热回收也是一项有效的节能技术。
在钢铁冶炼过程中,大量的废热会被排放到环境中,造成能源的浪费。
而利用适当的废热回收技术,可以将这些废热转化为电力或热能,用于生产过程中的其他环节,从而达到能源再利用的目的,减少对外部能源的依赖。
电弧炉炼钢高效化的能耗状况分析

工序能耗 ei 计算式
ei=∑mi,k×ai,k
i —— i=1,2,3,4,5 代表烧结、炼铁、DRI、炼 钢和轧钢工序
k —— 工序内各能源物质和工质的种类 mi,k —— 各工序能源物质和工质的吨产品物耗 ai,k —— 能源物质和工质的折标煤系数,其中电力
折标煤系数取 0.404 kgce/kW·h
单位炉容的年利用系数增加 56 %,近8000 t•t-1•a-1,达到国际先进水平
变压器利用系数达到10848 t•(MV•A)-1•a-1 , 增加 51 %,达到国际先进水平
(3) 工序电耗和流程电耗
钢比 系数
工序 电耗
工序 烧结 高炉炼铁 DRI 炼钢 轧钢 烧结 高炉炼铁 DRI 炼钢 轧钢 流程
单位电弧炉变压器容量的年利用系数:为年合 格铸坯产量与变压器容量的比值 ( t / (MVA·a))
电耗指标
①工序电耗:该工序生产每吨产品的电耗 ( kW·h / t-产品)
② 流程电耗:为烧结、高炉炼铁、直接还原铁、 炼钢和轧钢各工序的电耗之加权和
(折算到铸坯)( kW·h / t-坯)
按钢比系数(各工序的产量与铸坯产量比)加权
工位级尺度 : 炼钢电弧炉
工序级尺度 : (五个工序)炼钢(含精炼和连铸)、 直还铁、烧结、高炉炼铁、热轧
流程级尺度: 由以上五个工序构成流程,不包 括其它辅助工序
更大尺度 :由三家企业的三个电弧炉炼钢流程 构成更大尺度
三项单元操作技术
1、合理供电 2、强化供氧 3、疏通热物流
按物料和能量在工位级、 工序级和流程级尺度集成
炉容利用系数 /t•t-1•a-1
2121 7278 7918 9160 5583 7667
大型超高功率电弧炉炼钢综合节能技术研究共3篇

大型超高功率电弧炉炼钢综合节能技术研究共3篇大型超高功率电弧炉炼钢综合节能技术研究1大型超高功率电弧炉炼钢综合节能技术研究随着钢铁工业的快速发展,节能减排成为近年来的热门话题。
大型电弧炉是钢铁工业的主要炉型之一,其炉渣量较少、操作灵活、反应温度高等优点广受钢铁企业青睐。
在电力消费方面,大型超高功率电弧炉的能耗相对较高,限制了其应用范围和生产效率。
因此,开发一系列综合节能技术成为钢铁企业的研究热点。
一、废气处理技术大型超高功率电弧炉的废气中含有大量的有害物质,直接排放会对环境造成严重污染。
常见的废气处理技术有高温燃烧、分子筛吸附、催化氧化等方法。
其中,高温燃烧主要是将废气通过高温进行燃烧,将有害物质转变为无害物质,达到净化空气的目的。
分子筛吸附技术可以将废气中的挥发性有机物(VOCs)吸附在分子筛表面,减少有害气体的排放。
催化氧化技术则是将废气通过催化剂的反应作用,将有害气体转化为无害物质。
这些废气处理技术可以有效地减少排放,保护环境。
二、废热回收技术大型电弧炉在炼钢过程中会产生大量的废热,常采用废热锅炉回收废热进行发电或供热。
废热回收技术是目前最为成熟的能源利用方式之一,可以在不增加生产成本的同时提高利润和环保效益。
在废热回收技术中,绝热材料和隔热材料的选用至关重要。
绝热材料可以有效地减少能量的散失,提高回收率;隔热材料则可以减少周围环境的热量流失,提高节能效果。
三、炉况智能控制技术炉况智能控制技术是目前炼钢行业中的一种新技术,它通过对炉内氧气含量、炉温、电极位置等参数进行修改和控制,从而达到控制炉内反应的目的。
智能控制技术可以使电弧炉的生产得到合理的运作,减少能耗,提高生产效率。
同时,智能控制技术能够确保炉内钢水的质量,提高钢铁产品的质量和生产效益。
总的来说,大型超高功率电弧炉炼钢综合节能技术研究是本行业一个非常重要的方向。
在尝试和探索这些技术的同时,我们需要不断地加强产学研合作,让学术研究和现场实践互相交流,以期成功地解决在生产过程中碰到的难题,让炼钢行业健康可持续发展针对电弧炉炼钢过程中的能源浪费和环境污染等问题,本文总结了三种主要的综合节能技术,即废气处理技术、废热回收技术和炉况智能控制技术。
安全技术之炼钢电弧炉的节电增产的有效措施

01
提高操作人员的技能水平和安全意识,使其能够熟练掌握各种
操作技巧和应对措施。
制定合理的操作规程
02
根据工艺要求和设备特点,制定科学合理的操作规程,规范操
作人员的行为。
实施定期维护保养
03
对设备进行定期检查、维护和保养,确保设备处于良好的工作
状态,延长设备使用寿命。
04
安全与节能的平衡
安全与节能的关系
开发新型的节能技术和设备,降低能 耗和减少排放,提高能源利用效率。
探索新的控制算法和智能监测技术, 实现实时监测和预警,降低事故风险 。
节能减排的可持续发展
推广绿色生产理念,加强环保意 识,促进可励企业采用新技术和设备,降
低能耗和排放。
加强国际合作,共同应对气候变 化和环境问题,推动全球可持续
重要性
随着工业生产的快速发展,安全问题越来越受到关注。安全技术的应用可以有 效降低生产事故的发生率,保障员工生命安全,提高企业的经济效益和社会形 象。
安全技术在炼钢电弧炉中的应用实例
自动化控制技术
通过自动化控制系统,实现对炼钢电弧炉的实时监测和控制,提高生产效率和安全性。例 如,采用智能传感器、PLC等设备,对炉温、压力、液面高度等参数进行实时监测和调节 ,确保生产过程的稳定性和安全性。
选用高效节能的设备
采用高效节能的电弧炉设备是实现节电增产的重 要措施。新型电弧炉具有更高的热效率和能量利 用率,能够大幅度降低能耗。
加强设备维护与管理
定期对设备进行维护和保养,确保设备处于良好 的工作状态,可以提高设备的能效和寿命。同时 ,加强设备管理,合理安排生产计划,避免设备 空转或低负荷运转。
优化炼钢工艺
通过改进炼钢工艺,可以提高炼钢效率,减少能 耗。例如,采用合适的装料方式、优化熔炼温度 和时间等。
安全技术之炼钢电弧炉的节电增产的有效措施

节电管理措施
加强用电管理
制定合理的用电计划,实行峰谷平电价策略,优 化用电结构,提高用电效率。
开展节能宣传
加强节能宣传教育,提高员工的节能意识,形成 全员参与的节能氛围。
定期进行能耗监测
对电弧炉等设备的能耗进行实时监测和记录,及 时发现和解决浪费电能的情况。
03
炼钢电弧炉的增产技术
安全技术的发展趋势和展望
物联网和大数据
人工智能和机器学习
绿色和可持续发展
物联网和大数据技术的发展为炼钢电 弧炉的安全技术提供了新的发展方向 。通过物联网技术将设备连接起来, 实现数据的实时采集和传输,再通过 大数据技术对数据进行处理和分析, 可以更好地掌握生产情况,及时发现 安全隐患,提高生产效率和质量。
热量利用率低
炼钢电弧炉在利用热量进 行炼钢时,存在热量利用 率低的问题,造成能源浪 费。
设备老化
炼钢电弧炉长时间运行, 设备老化严重,导致能耗 增加。
能耗问题
节能意识不强
炼钢企业对于节能减排的 重要性认识不足,缺乏有 效的节能措施。
技术水平落后
炼钢企业的技术水平相对 落后,缺乏先进的节能技 术和设备。
提高熔化率的措施
增加功率
通过提高电弧炉的输入功率,增加熔化速率,从而提高熔化率。
改进电极插入方式
优化电极插入方式,减少电极损耗,提高电弧能量利用效率。
采用高效炉衬材料
使用高效耐火材料作为炉衬,减少热量损失,提高熔化效率。
改进熔炼工艺的措施
合理控制熔炼温度
01
根据钢种和原料条件,合理控制熔炼温度,降低能耗。
管理不善
炼钢企业的管理不善也是 导致能耗问题的一个重要 原因,如设备维护不当、 生产计划不合理等。
电弧炉炼钢节能技术研究

电弧炉炼钢节能技术研究摘要:本文在对电弧炉炼钢基本原理全面分析的基础之上,重点分析了常见的几种技能技术。
关键字:电弧炉;炼钢;节能1前言随着我国经济的发展,能源短缺对经济发展的制约成了国家重点解决的问题。
近几年我国电弧炉炼钢技术发展迅速,部分电弧炉的技术经济指标已达到国际水平,但与国际先进水平相比还有一定差距。
节能降耗是电弧炉生产技术发展的必然趋势。
尤其是在目前我国能源紧张的情况下更要对电弧炉炼钢的节能降耗进行深入研究。
在电弧炉炼钢中,电能是其主要用的方式,如何降低电弧炉的电耗是其节能的主要思考问题。
超高功率电弧炉,电弧炉配料、装料制度,废钢预热等技术对电弧炉节能起到了很大的作用。
电弧炉炼钢的任务就是把钢铁废弃物加以处理再利用,完成钢铁原材料生产的重要任务。
2基本原理电炉是采用电能作为热源进行炼钢的炉子的统称。
按电能转换热能的方式的差异电炉可分为:电渣重熔炉,感应熔炼炉,电子束炉,等离子炉,电弧炉等几种炼钢的电炉。
世界上电炉钢产量的95%都是由电弧炉生产的,因此,电炉炼钢主要是电弧炉。
它突出的优点:电弧炉炉渣参与冶金反应,可以有效去除硫和磷,对原料的要求低,可以用废钢和铸造回料。
钢水的质量可以得到保证,且炼钢周期短,开、停炉比较方便,便于组织生产,因此应用较广泛。
它的工艺过程包括:补炉、装料、熔化期、氧化期、还原期、出钢等6个阶段。
3电弧炉炼钢过程的能量构成工业化炼钢生产是在高温、熔融的状态下进行的,这个过程需要大量的热能。
炼钢过程所需热能主要用于以下几个方面困:①保持1500~1600°C的高温,包括升温所需热量;②保证冶金过程顺利进行所需的能量;③补充其他炼钢副产物所带走的能量;④补充炼钢生产过程的热损失。
电弧炉炼钢生产过程中,电弧加热提供炼钢所需的主要能源。
在电弧炉炼钢生产的早期,电弧是单一的炼钢能源供应者,此时的电弧炉炼钢效率较低,电耗较高。
随着电弧炉炼钢技术的发展,出于提高生产率和降低电能消耗的目的,电弧炉炼钢逐渐增加了辅助能源的利用。
- 1、下载文档前请自行甄别文档内容的完整性,平台不提供额外的编辑、内容补充、找答案等附加服务。
- 2、"仅部分预览"的文档,不可在线预览部分如存在完整性等问题,可反馈申请退款(可完整预览的文档不适用该条件!)。
- 3、如文档侵犯您的权益,请联系客服反馈,我们会尽快为您处理(人工客服工作时间:9:00-18:30)。
供氧技术 ;能量集成技术 ———分时段能量集成技术 。 并介绍了能量集成技术在天津钢管集团股份有限公 司 150 t电弧炉 ,安阳钢铁集团有限责任公司 100 t电 弧炉 ,大冶特殊钢股份有限公司 60 t电弧炉炼钢生 产的实施情况 。 1 合理供电技术
电弧炉炼钢采用超高功率冶炼 ,提高熔池能量 输入密度 ,加速炉料熔化 ,大幅度缩短冶炼时间 ,从 而使电弧炉的热效率提高 ,单位电耗显著下降 。超 高功率电弧炉具有独特的供电制度 ,在整个冶炼过 程中采用高功率供电 ,熔化期采用高电压 、长电弧快 速化料 ,熔化末期采用埋弧泡沫渣操作 ,促使熔池升 温和搅拌 ,保证熔体成分和温度的均匀化 ,同时减轻 炉衬的热负荷 ,达到提高电弧炉炼钢生产率 ,降低电 耗的目的 。 1. 1 100 MVA变压器炼钢运行非线性操作电抗模型
三相交流电弧炉的供电回路示意如图 1所示 。 在炼钢过程中 ,供电电路所承受的电抗是由供电电 网至电极端头的电抗总和 ,这是电气运行操作最重 要的基本参数 。尽管有多种理论计算方法 ,但最实 用的还是直接测定 。
对于早期的小容量电炉 ,电弧炉炼钢过程所承 受的工作电抗可以通过短路实验来测定 。由于电路 处于短路状态 ,回路电压和电流都是理想的 50周正
集束射流与普通超音速射流相比具有喷射距离
图 6 集束射流和普通超音速射流对比
长 、冲击力大 、氧气利用率高和供氧装置寿命长等优
点。
根据实验和计算 ,普通超音速射流有效长度可
按公式 (2)估算 :
XS / d = 24. 7M a·P1
(2)
而集束射流的有效长 度有 所增 加 , 可 按公 式
(3)估算 :
集束射流供氧技术包括集束射流供氧 、喷吹燃 料 、喷吹碳粉等综合供氧喷吹技术 。具有传统烧嘴 的助熔功能 ,又可实现集束射流供氧脱碳及喷吹碳 粉。 2. 2 集束射流供氧的参数设计
集束射流供氧的技术核心在于集束射流参数设 计 。本研究采用冷态实验 、热态实验以及 CFX、Flu2 ent软件模拟优化等开发过程 ,给出不同供氧量的集 束射流参数设计 ,如图 6所示 :
2009年 4月 第 17卷 第 2期
河 南 冶 金 Ap r. 2009 HENAN M ETALLURGY Vol. 17 No. 2
电弧炉炼钢高效化能量集成节能技术
3
朱 荣 刘润藻 郁 健
(北京科技大学 )
整个射流装置由以下系统构成 :主氧气超音速 流股系统 、伴随流产生系统 、冷却系统 。主氧气超音 速流股位于集束射流装置的中心位置 ,伴随流位于主 氧气流股喷吹系统的外层 ,水冷系统位于装置的最外 层 ,在氧枪一端设有进水口和出水口 ; 燃料系统位于
XS / d = 24. 7M a·P1 + F ( P2 , Q2 )
(3)
式中 : XS ———有效射流长度 , mm;
D ———出口直径 , mm;
M a———马赫数 ;
P1 ———工作压力 ,M Pa; P2 ———环氧工作压力 ,M Pa; Q2 ———环氧流量 , Nm3 / h; F ( P2 , Q2 ) ———是 使集 束射 流长 度延 长的 函 数 ,与环氧压力及环氧流量的大小有关 。
现代炼钢电弧炉炉容量大 ,冶炼节奏快 ,配碳量
2009年 第 2 期
河 南 冶 金 · 3·
图 4 电气运行特性曲线
图 5 电气运行圆图
高 ,原料中大量配加生铁块 、热铁水 , 对供氧技术提 出了新的挑战 。为提高电弧炉的供氧强度 ,产生了 各种供氧方式 ,如炉门吹氧 、炉壁吹氧 、EBT吹氧等 等 。这些供氧方式主要采用的是超音速射流技术 。
2007 年 , 我 国 电 弧 炉 炼 钢 年 产 量 达 到 5843 万 t,超过了传统的电炉钢生产大国 ———美国 ,居世 界第一位 ,比德国或韩国全年总的钢产量还要多 。 但我国电炉钢在总钢产量中所占比例还不足 12% , 远低于世界平均水平 ,这意味着我国钢铁生产平均 的单位能耗和 CO2 排放都远高于世界平均水平 。 随着能源消耗 、室温气体排放控制日益严格 ,在尊重 科学发展观的今天 ,高效节能的电弧炉炼钢技术的 发展尤为重要 。
研究中使用高精度的电气测量仪表 ,在 100MVA 变压器、9 级二次电压下的炼钢过程中实测得到的 4651组 、130228个数据的散点图绘于图 2:
图 2 实测得到 XOP — I2 的散点图
可以看出 : ①在不同的二次工作电流 I2 下 ,实 际操作电抗 XOP值有所不同 ,呈非线性变化 ; ②工作 电流 I2 增大至额定电流的 1. 3 倍以后 , XOP的变化 接近平缓 ,似乎可以用来估计短路电抗 XSC。由散 点图得到该工况下的非线性操作电抗模型 ,见公式
Zhu Rong L iu Runzao Yu J ian (University of Science and Technology Beijing)
ABSTRACT The highly effective integration energy - saving technology of EAF steelmaking, as well as p roduction imp le2 mentation effect in domestic three typ ical EAF steelmaking enterp rise w ith 150 t, 100 t and 60 t EAF nom inal capacity respec2 tively. , were introduced in this article. KEY WO RD S EAF steelmaking high efficiency energy - saving
对此 ,研究开发了集束射流供氧技术 :根据可压 缩流体的原理 ,在氧气超音速射流外部增设伴随流 (这种伴随流可以是火焰 ,也可以是氧气 ) ,通过设 计氧气喷嘴的结构 、调节氧气流量和压力获得集束 射流 。伴随流对主氧气流股起着 "封套 "的作用 ,隔 绝了环境气流对主氧气流股的影响 ,使主氧气流股 形成在一定距离内不衰减的集束射流 。
摘要 介绍了电弧炉炼钢高效化能量集成节能技术 ,以及在电弧炉公称容量分别为 150 t、100 t和 60 t的国内三家典 型电弧炉炼钢企业的生产实施效果 。 关键词 电弧炉炼钢 高效化 节能
THE H IGHLY EFFECT IVE INTEGRAT IO N ENERGY - SAV ING TECHNOLO GY O F EAF STEELM AK ING
另一个难点是 :在电弧炉炼钢过程中回路所表 现出的操作电抗值 XOP并不等于短路电抗 XSC ,这是 因为炼钢过程中电弧引起的谐波所造成 。所以 ,要 想获得更换变压器以后的实际操作电抗 XOP ,就必 需在炼钢过程中测定 。所以 ,用容量为 100MVA 的 变压器取代 90MVA 的变压器 ,并不是变压器容量 的简单增大 ,也不仅仅是电压级别和工作电流的改 变 ,其深层次的技术提升是需要测定新回路的短路 电抗 XSC和新条件下炼钢过程的实际操作电抗 XOP。
(1) [1] :
XOP 3. 29exp {15. 87 / I2 }
(1)
式中 : XOP ———操作电抗 , mΩ;
I2 ———工作电流 , kA。
由式 (1)可知 ,工作电流 I2 →∞处的短路电抗
值 XSC = 3. 29mΩ。将研究所得的实测非线性操作
电抗模型和短路电抗 XSC与文献和外商提供的 XOP
0 前言 目前全世界粗钢年产量超过 13 亿 t,其中电炉
钢约占 1 /3。电弧炉炼钢消纳大量的钢铁废弃物 , 使之再生成为优质的钢材 。废钢 /电弧炉炼钢流程 每吨钢的能耗和 CO2 排放量大约是矿石 /高炉炼 铁 /氧气转炉炼钢流程的 1 /3~1 /2,因此 ,在废钢资 源允许的地区和国家都优先发展电弧炉炼钢 。
超音速射流在电弧炉炉内受高温烟气流的影 响 ,衰减较快且射流长度短 。氧气射流到达熔池处 气流速度较低且冲击力弱 ,不能穿透熔池表面进行 有效脱碳 ,切割废钢助熔能力较弱 ,氧气利用率不 高 ,节能效果较差 。为了进一步提高电弧炉炼钢的 冶炼节奏 、降低冶炼电耗 、冶炼能耗 、金属消耗和生 产成本 ,都要求采用更先进的供氧技术来提高供氧 强度和氧气利用率 。
在电弧炉炼钢过程中交流电弧并不完全是纯电 阻性质 ,其主要原因是 : ①交流电压和电流每秒钟有 100次通过零点 ,由于需保证电弧连续稳定燃烧 ,要 求电路有一定的感性 ,即炼钢过程中电气运行功率 因数 coφs ≤0. 866; ②石墨电极和含铁冷炉料 /熔池 的电子发射性质不同 ,交替处于电位由正变负或由 负变正的过程 。因此 ,交流电弧炉在实际炼钢过程 中会产生各次谐波 ,由于炼钢炉料状态 、炉况千变万 化 ,各次谐波的分量构成也不尽相同 。
3 联系人 : 朱荣 ,教授 ,博士生导师 ,北京 (100083) ,北京科技大学冶金与生态工程学院 ; 收稿日期 : 200第 2期
图 1 电弧炉的主回路示意图
弦波形 ,短路实验测得的电抗 XSC可以认为就是最 接近整个供电回路的实际电抗值 。然而 ,容量大的 炼钢电弧炉 ,短路实验变的几乎不可能实现 ,若要得 到大容量炼钢电弧炉的短路电抗值 ,必须采用新的 测量方法 。