从工艺技术因素分析导致外胎钢丝圈上抽的原因
全钢载重子午胎质量缺陷产生原因及解决措施

全钢载重子午胎质量缺陷产生原因及解决措施1胎里露线胎里露线是指轮胎里面钢丝骨架材料内表面覆胶不足,钢丝露出胎里表面。
胎里露线多在肩部或侧部出现。
经过里程实验,出现露线的外胎在耐久实验15小时左右即出现肩部鼓包或爆破,基本没有使用价值,由于影响因素较多,因此,胎里露线是废品率很高的一种缺陷,也是全钢胎制造过程中最容易出现、最难解决的问题。
1.1原因分析1.1.1胎里露线主要原因是机头平宽设计偏小或在成型过程中胎圈定位撑块出现漂移造成。
成型机头宽度窄,两胎圈之间的帘线长度短,当硫化给内压时,由于胎胚外直径小于设计尺寸,伸张变形大,这样帘线会抽出内衬层导致胎里露线。
1.1.2材料分布不足也会产生胎里露线,如果胎面或垫胶的厚度或长度不够标准,在成型时强行拉伸,导致局部材料缺失,肩部内轮廓帘线伸展过渡,易出现胎里露线现象。
1.1.3内衬层的厚度及各部位的尺寸低于设计尺寸,或成型时贴合偏移,造成局部材料分布不均,或密封层的塑性过大均会造成肩部漏钢丝的现象。
1.1.4硫化定型失控也是造成成品肩部漏钢丝的不可忽视的原因。
在硫化定型时,如果定型压力不能稳定在规定值,那么在合模过程中,胎胚外直径一直处于逐渐增大的状态,这样会有肩部部分胶料随着花纹块下移,造成上模花纹块处缺胶,成品胎里肩部露线。
1.1.5硫化机机械手定位高度过低,胎胚的中心线与胶囊中心线不吻合,定型时胎胚上部过度伸张,钢丝帘线析出内衬层表面,出现露线现象。
1.2 解决措施:1.2.1 结构设计是内在因素,工艺和操作是外部因素。
若存在着普遍的胎里露线现象,并且通过X光检测,发现胎体帘线成直线排列,则应重新考虑平宽的选取,一般增大2~4mm可解决。
严格控制挤出、压型半成品部件的的尺寸,不合格的半成品部件严禁使用。
1.2.2 严格控制成型操作,每班开产前必须对成型鼓的平宽、送料架的定位尺寸进行测量,不符合要求的应通知维修人员解决后方可生产。
同时要检查各种半成品部件是否符合施工条件,不合格的半成品严禁使用。
全钢载重子午线轮胎胎圈露线的原因分析及解决措施

114 轮 胎 工 业 2019年第39卷全钢载重子午线轮胎胎圈露线的原因分析及解决措施李庆瑞,岳 爽,李忠浩,郭 优,王 欢(风神轮胎股份有限公司,河南 焦作 454150)摘要:从成型方面分析全钢载重子午线轮胎胎圈露线的产生原因,并提出相应解决措施。
通过采取调整胎侧耐磨胶厚度、减小内衬层宽度、控制钢丝圈椭圆度不大于4 mm 、调整钢丝圈直径、改变钢丝圈纤维包布缠绕层数、确保胎侧定位不偏歪、改变胎坯停放方式、合理设定成型机扇形块压力、改进三鼓成型机胶囊、正确选取成型机平宽固定值等措施,有效减少了全钢载重子午线轮胎胎圈露线现象。
关键词:全钢载重子午线轮胎;胎圈;露线;钢丝圈中图分类号:U463.341+.3/.6;TQ336.1 文章编号:1006-8171(2019)02-0114-03文献标志码:B DOI :10.12135/j.issn.1006-8171.2019.02.0114全钢载重子午线轮胎胎圈一侧或者两侧露线是比较常见的一种外观质量缺陷。
通常存在胎圈露线的有内胎轮胎会与轮辋发生摩擦,轻则磨损轮辋,重则帘线磨断,产生安全隐患;存在胎圈露线的无内胎轮胎会因与轮辋着合不严密而导致轮胎充气压力下降,影响使用安全。
随着轮胎生产工艺的优化改进,钢丝圈工序中逐渐取消了对钢丝缠绕圈半硫化,胎圈露线成为全钢载重子午线轮胎的主要质量缺陷之一。
胎圈露线的具体位置和形式多种多样,相应的解决措施亦有所不同。
本文主要从成型方面分析全钢载重子午线轮胎胎圈露线的产生原因,并提出相应解决措施。
1 胎圈露线的特征和判定标准1.1 现象描述胎圈露线是胎圈部位出现或隐约出现可见帘线的现象,如图1和2所示。
1.2 判级标准与测量方法胎圈露线的判级标准如下。
图1 胎踵与胎趾间露线图2 胎踵与防水线间露线(1)合格品:有覆胶且覆胶最薄处厚度不小于1.0 mm ,如图3所示。
(2)等外品:有覆胶且覆胶最薄处厚度小于1.0 mm ,如图4所示。
轮胎的常见问题及成因分析

轮胎的常见问题及成因分析一、一般质量问题的分析1、胎冠出胶边也称为流失胶边,是硫化时上下模合缝口不严所造成的胎面胶流出而形成的胶边,这是由于高压不稳定或掉压所引起。
2、胎冠出沟在胎面冠部形成沟状下凹因内压过热水压力下降所造成。
3、花纹错位上下模型花纹不能吻合,是模型安装时上下模没有对准花线或稳钉而引起。
4、花纹和模缝毛边是由于花纹和模型间有缝隙胶料流进缝隙间而产生的。
5、花纹棱角或缺胶成圆角主要是模型排气孔阻塞并窝藏了空气而形成花纹圆角,内压不足也会产生此类毛病。
6、胎冠侧部表面杂质或气泡表面杂质是胎坯或模型受到污染,气泡则是半成品有空气聚集,硫化出模后空气膨胀而产生的表面气泡。
7、胎侧重皮或裂口产生原因为胎侧部隔离剂涂擦过多过浓,半成品形状与模具不相吻合以及胶料流动过大等。
8、胎侧缺胶亦称为明疤,模型积水未吹干或模温过高升温过快等均会引起此类毛病。
9、胎圈凹凸不平由于水胎牙子凹凸不平或包布不平所引起。
10、胎圈包布打褶翘起或破损由于胎坯包布松散没有整修就进模硫化或出模不当刮坏所致。
11、胎圈出边产生原因与上一条相似,如果水胎牙子老化变宽也能造成这些毛病。
12、胎圈宽窄不一主要是半成品不按施工标准操作所致,如果布筒长度不足,成型第一个布筒时没有用成型棒致成型鼓张口处伸张过大,帘布宽度局部变窄造成局部材料不足,又如水胎或胶囊定型定歪也会产生这种毛病。
13、胎圈成圆形主要发生在以水胎定型硫化的外胎上,是由于水胎进出水嘴子漏水或牙子部漏水所致。
橡胶技术网14、第一层帘线裂缝因胎里隔离剂带水分或水胎沾有水分油污等,硫化时这些水分在压力作用下把胎里油皮胶挤破把帘线挤疏成裂缝状,严重的第二层帘线也受影响。
15、第一层帘线弯曲也叫帘线打弯,主要是帘线伸张不足造成,如施工设计不当或成型鼓宽度过宽,如用错成型鼓等均能引起该毛病。
16、胎里帘线凹凸不平主要是胎里杂质,或因水胎舒展不开产生打褶造成的,越野花纹或拖拉机人字花纹允许有凹坑故不在此例。
特种工程胎硫化外胎质量缺陷原因分析以及解决措施
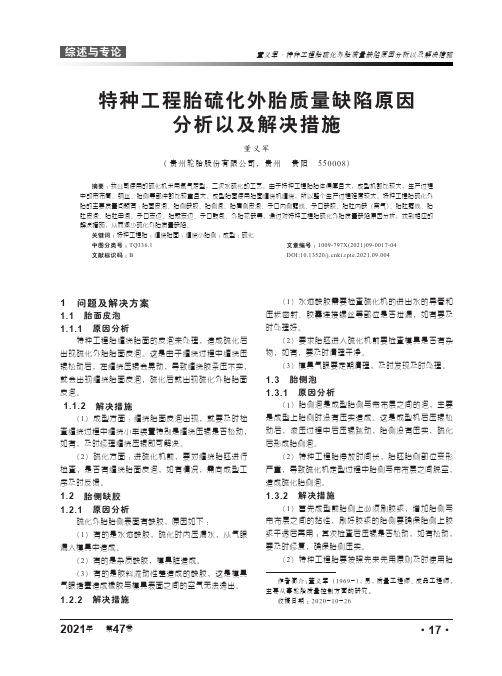
作者简介:董义军(1969-),男,质量工程师、成品工程师,主要从事轮胎质量控制方面的研究。
收稿日期:2020-10-261 问题及解决方案1.1 胎面皮泡 1.1.1 原因分析特种工程胎缠绕胎面的皮泡未处理,造成硫化后出现硫化外胎胎面皮泡。
这是由于缠绕过程中缠绕压辊松动后,在缠绕压辊会晃动,导致缠绕胶条压不实,就会出现缠绕胎面皮泡,硫化后就出现硫化外胎胎面皮泡。
1.1.2 解决措施(1)成型方面:缠绕胎面皮泡出现,就要及时检查缠绕过程中缠绕小车装置特别是缠绕压辊是否松动,如有,及时修理缠绕压辊即可解决。
(2)硫化方面:进硫化机前,要对缠绕胎胚进行检查,是否有缠绕胎面皮泡,如有情况,需向成型工序及时反馈。
1.2 胎侧缺胶1.2.1 原因分析硫化外胎胎侧表面有缺胶,原因如下:(1)有的是水迹缺胶,硫化时内压漏水,从气眼漏入模具中造成。
(2)有的是杂质缺胶,模具脏造成。
(3)有的是胶料流动性差造成的缺胶,这是模具气眼堵塞造成橡胶与模具表面之间的空气无法逸出。
1.2.2 解决措施特种工程胎硫化外胎质量缺陷原因分析以及解决措施董义军(贵州轮胎股份有限公司,贵州 贵阳 550008)摘要:我公司使用的硫化机采用氮气定型,二次水硫化的工艺。
由于特种工程胎胎体偏厚且大,成型机都比较大,生产过程中的帘布筒、钢丝、胎侧等部件都比较重且大。
成型胎面使用胎面缠绕机缠绕,所以整个生产过程难度较大。
特种工程胎硫化外胎的主要质量问题有:胎面皮泡、胎侧缺胶、胎侧泡、胎肩侧皮泡、子口内侧露线、子口缺胶、胎肚内缺(窝气)、胎肚露线、胎肚皮泡、胎肚串泡、子口支边、胎冠支边、子口鼓包、外胎花缺等。
通过对特种工程胎硫化外胎质量缺陷原因分析,找到相应的解决措施,从而减少硫化外胎质量缺陷。
关键词:特种工程胎;缠绕胎面;缠绕小胎侧;成型;硫化中图分类号:TQ336.1文章编号:1009-797X(2021)09-0017-04文献标识码:B DOI:10.13520/ki.rpte.2021.09.004(1)水迹缺胶需要检查硫化机的进出水的导管和压板密封、胶囊连接螺丝等部位是否泄漏,如有要及时处理好。
全钢载重子午线轮胎质量缺陷问题分析

全钢载重子午线轮胎质量缺陷问题分析子午线轮胎制造工艺复杂,要求精度高。
根据全钢载重子午线轮胎常见质量缺陷,进行了原因分析,并提出了相应的解决措施。
1、胎里露钢丝与肩部帘线弯曲胎里露线是指轮胎里面钢丝骨架材料内表面覆胶不足,钢丝露出胎里表面。
胎里露线多在肩部或侧部出现帘线露出或“露肋骨”现象。
在使用中胎里露出的钢丝容易损坏内胎,使轮胎胎体鼓包甚至爆破。
肩部帘线弯曲是指轮胎肩部胎体帘线出现周向弯曲。
帘线弯曲在轮胎行驶当中受力不均,使钢丝与胶的生热增加,导致轮胎脱层或爆破,引起轮胎的早期损坏。
全钢丝载重子午线轮胎胎里露线和肩部帘线弯曲是生产和使用中困扰轮胎技术人员的一大难题。
由于胎里露线和肩部帘线弯曲是相辅相成的,是一对矛盾的统一体,所以将两个问题一起讨论。
1.1 原因分析(1)胎里露钢丝与肩部帘线弯曲主要原因是机头宽度与帘线假定伸张值选取不合理。
胎体由一层钢丝帘布组成,帘线断裂伸张率为1.8~2.3之间,胎体的钢丝帘线伸张值一般在 1.0%~1.8%之间。
帘线伸张值大,成型机头宽度窄,帘线长度短。
当伸张值达到极限值;帘线会抽出内衬层导致胎里露线。
帘线伸张值小,成型机头宽度宽,帘线长度长,容易导致肩部胎体帘线弯曲。
半成品的尺寸和重量是根据材料分布图计算出来的,当半成品尺寸和质量过大,会导致胎体帘线的材料过剩从而使胎体帘线弯曲。
材料分布不足就会产生胎里露线,胎面或垫胶的厚度或长度超公差,使得肩部材料过剩,厚度增加,内轮廓帘线舒展不开,导致肩部帘线弯曲。
反之,内轮廓帘线伸展过渡,易出现胎里露线现象。
(2)胎坯外周长的大小也是影响胎里露线和肩部帘线弯曲的一个因素。
胎坯外周长达不到标准,则轮胎在硫化过程中伸张变形大,出现胎里露线;反之,胎坯外周长大,轮胎在硫化过程中伸张变形小,将易出现帘线肩部弯曲。
(3)一次法成型机传递环故障或鼓的撑块出现故障,成型过程中胎圈定位、撑块定位发生漂移或者平宽设定有误,造成内轮廓帘线较标准帘线长度增大,胎体帘线伸张不足,硫化后产生肩部帘线弯曲。
全钢轮胎钢丝圈生产工艺流程

全钢轮胎钢丝圈生产工艺流程
全钢轮胎的钢丝圈生产工艺流程大致如下:
1. 钢丝预处理:选用高强度钢丝,通过清洗、镀层(如镀锌、镀铜等防腐处理)等预处理,提高钢丝的耐腐蚀性和与橡胶的粘合性。
2. 钢丝圈成型:预处理后的钢丝通过专用设备(钢丝圈成型机)进行编织或缠绕,形成具有特定结构和强度的钢丝圈骨架。
3. 胶料准备:按照配方准备橡胶化合物,包括天然橡胶、合成橡胶、硫化剂、填充剂等,通过密炼机混炼成胶料。
4. 胶合工序:将成型的钢丝圈浸入胶料中,或者通过挤出机将胶料涂覆在钢丝圈上,确保钢丝与橡胶紧密结合。
5. 硫化定型:将胶合后的钢丝圈放入硫化罐进行高温、高压下的硫化处理,使得橡胶固化,形成稳定的全钢轮胎胎圈部分。
6. 检验与包装:硫化后的钢丝圈进行质量检测,包括外观、尺寸、力学性能等,合格品进行清洁、包装,准备用于全钢轮胎的组装生产。
常见的钢丝拉 拔缺陷

常见的钢丝拉拔缺陷有裂缝(裂纹)、发纹、拉裂、竹节、拉痕、划伤(刮伤、刮痕、擦伤)、飞翅(飞刺)、凹面(凹坑、凹陷、压痕)、麻点(麻面)结疤、分层、缩径、尺寸超差、线盘不规整、折叠等。
裂缝(裂纹)钢丝表面出现的纵向开裂现象,根据开裂程度不同,分别称为裂缝、裂纹等。
产生原因大多为原料残存有裂缝、裂纹及夹杂物等。
拉拔时由于压缩率过大或变形不均也可能产生应力裂纹。
发纹钢丝表面或内部存在的极细的发状裂纹。
产生原因是原料带有发纹或皮下气泡、细小夹杂物等。
拉裂钢丝表面出现的横向开裂现象。
产生原因是压缩率过大或拉拔速度过高,涂层或润滑条件不良,热处理制度不合理,原料化学成分局部不均,拉丝模入口锥角度太大,变形区太短等。
竹节钢丝沿纵向呈周期性的粗细不均现象,形状类似竹节。
产生原因是钢丝在卷筒上积线量过多,卷筒摇摆,涂层不均,润滑不良等。
拉痕钢丝表面出现的肉眼可见的纵向小沟,通常是恿条连续的。
轻微啦痕仅使钢丝表面发亮发白。
产生原因是拉丝模破裂或加工不良光洁度差、润滑不良等。
划伤钢丝沿拉拔方向产生的表面纵向伤痕,随伤痕程度的不同,分别叫做刮伤、刮痕、擦伤等。
产生原因是模孔中带进金属碎屑、润滑剂不洁净、含有氧化铁皮或砂等以及拉拔过程中钢丝受到模盒、拉丝机突出部分的机械损伤。
飞翅与钢丝表面大致成垂直尖锐金属薄片,一般沿拉拔方向分布,有时也称为飞刺。
产生原因是拉丝模严重破裂。
凹面钢丝表面上的局部凹陷,由于产生原因不同,有时也叫做凹坑、凹陷、压痕等。
产生原因为原料带有凹坑,拉拔前钢丝表面未洗净残留有块状氧化铁皮,石灰涂层太厚或钢丝表面粘附有脏物等,拉拔时氧化铁皮或石灰被压入钢丝表面脱落后形成口麻点钢丝表面成点状或片状分布的或密或疏的微细凹坑,较密集的针状凹点称为麻点,密集且连续分布者叫麻面。
产生原因为原料表面粗糙,压缩率小不能消除;原料或半成品严重锈蚀;原料或半成品过酸洗形成酸蚀麻点;钢丝拉拔前未洗净,残留有点状氧化铁皮,拉拔后压入钢丝表面后脱落。
轴承跑外圈的因素及解决方法

轴承跑外圈的因素及解决方法关键词:轴承跑外圈,轴承跑内圆,轴承室磨损,修复技术,碳纳米材料轴承跑外圈意思是滚动轴承与其配合的轴或孔发生了相对滑动。
轴承跑外圈对设备造成的负面影响非常大,加剧配合零件的磨损,甚至报费,损坏了设备,降低机器精度,另外,增大磨擦力,把大量能量转化成了无用的热能和噪声,降低了效率。
所以,如何修复轴承跑外圈是企业设备管理者考虑的重要问题。
本文简单介绍轴承跑外圈的影响因素及索雷工业现场修复轴承跑外圈的碳纳米技术。
轴承跑外圈的影响因素轴承与轴(孔)的配合,对轴、孔、轴承的加工精度、配合公差、安装装配精度、材质、以及使用维护方面要求非常严格,哪一方面不好都有可能使轴承跑圈。
1、配合公差:轴承与轴(孔)的配合公差有严格的标准,不同规格、精度、受力状况,使用环境等对配合公差要求不同。
滚动体与轴承内外套的磨擦为滚动磨擦,两接触面的磨擦系数都非常小,磨擦力也就非常小(当滚动体与内外套间有润滑油时,磨擦系数会更小)。
轴承与轴(孔)配合的非常紧,一般为过盈配合,少数情况为过渡配合。
相互挤压力较大,产生静摩擦,静磨擦力大于使它们相对滑动的扭力,所以轴承与轴、孔能保持相对静止,而靠滚动体与内套(或外套之间)的旋转传递机械能。
如果轴承与轴、孔的配合公差偏大,为间隙配合,挤压力变小,轴(轴承)会在扭力作用下,破坏相互间的静止,产生滑动,发生了我们称之为的“跑圈现象”,轴承内圈与轴发生滑动的称跑内圈,轴承外圈与轴承座孔发生滑动的称跑外圈。
2、加工精度、安装精度:是指轴、轴承、轴承座孔的加工工差、表面粗糙度、安装装配的精度等技术参数。
这些国家也都有行业标准。
一旦达不到标准,会影响到配合公差,造成轴承跑圈。
轴、轴承的配合位要求表面非常光滑,粗糙度Ra≤1.6μm,如果大于此,在轴承的拆装过程中会把毛刺拉掉,造成轴变细,孔变大,配合间隙变大,合理公差配合情况被破坏。
再如,安装的同轴度不够,会使轴承振动大、造成轴弯曲、载荷变大、造成轴承失效、增加更换轴承的次数、影响了轴承与轴或孔的尺寸公差,进而破坏了其与轴(孔)的配合公差,所有这一切都有可能造成轴承跑圈和轴承失效。
全钢载重子午线轮胎胎圈出边的原因分析和解决措施

494轮胎工业2019年第39卷全钢载重子午线轮胎胎圈出边的原因分析和解决措施李静(风神轮胎股份有限公司,河南焦作454000)摘要:从工艺方面分析全钢载重子午线轮胎胎圈出边的原因,并提出相应解决措施。
通过采取调整内衬层、过渡层与气密层的宽度和厚度、恢复硫化机机械手强制定中装置、确保机械手转动盘中心套筒和胶囊上卡盘立柱与套筒直径匹配、避免中心机构内芯子杆偏歪和弯曲、将变形后的椭圆形胎圈恢复为圆形以及调整机械手张开直径等措施,成品轮胎胎圈出边质量缺陷率由0.063%降低至0.015%。
关键词:全钢载重子午线轮胎;胎圈出边;胎侧中图分类号:TQ33&1+3文献标志码:B随着汽车工业的发展,对轮胎的性能要求不断提高,尤其是不同车型、使用环境等方面的细化,对轮胎质量的要求越来越高切。
全钢载重子午线轮胎胎圈是轮胎行驶过程中的主要承重部位,在装配过程中需要与轮網紧密配合,且胎圈部位部件较多、结构复杂,生产过程中一旦发生部件波动或设备异常,都将对胎坯胎圈部位的形状及胶料产生不良影响,硫化后发生胎圈出边质量缺陷,造成成品轮胎损失以及人力和物力的浪费。
本工作从工艺方面对全钢载重子午线轮胎胎圈岀边的产生原因进行分析,并提岀相应解决措施。
1胎圈整周出边因胎圈部位胶料过于充足造成胎坯胎圈直径变小,在硫化合模过程中,上钢棱圈与上卡盘配合过程挤压胎坯上胎圈,上胎圈部位胶料流入卡盘与胶囊缝隙,造成成品轮胎胎趾处出现整周垂直于胎唇方向的胶边。
1.1原因分析(1)内衬层胶料宽度和厚度过大,致使在成型作者简介:李静(1990-),女,河南驻马店人,风神轮胎股份有限公司助理工程师,学士,主要从事硫化工艺过程控制及优化、成品外观质量控制及提升等工作。
E-mail:caiyoulijing@ 文章编号:1006-8171(2019)08-0494-02DOI:10.12135/j.issn.1006-8171.2019.0&0494过程中,胎圈反包后内衬层向胎趾部位延伸过多,与胎侧耐磨胶重叠部位厚度和宽度增大,造成胎圈胶料厚度增大,胎圈直径变小。
钢丝轮胎损坏原因分析

损坏的钢丝轮胎会导致车辆在行驶过程中振动加剧,不仅影响乘坐舒 适性,还可能对车辆的其他部件造成损坏。
05
钢丝轮胎损坏预防措施
选用优质原材料
01
选用高强度、高韧性的钢丝材料,确保轮胎骨架的 强度和稳定性。
02
选择优质橡胶材料,提高轮胎耐磨性、抗撕裂性和 耐候性。
03
严格控制原材料质量,确保每批原材料符合相关标 准和要求。
添加剂问题
使用不当的添加剂或过量 添加,影响橡胶的物理化 学性能。
生产工艺因素
炼胶工艺
炼胶温度、时间控制不当,导 致橡胶熟化不充分,影响轮胎
性能。
压延工艺
压延温度、速度不匹配,造成 胶料内部气泡、脱层等缺陷。
成型工艺
成型时压力、温度控制不当, 轮胎形状不稳定,易产生变形 。
硫化工艺
硫化温度、时间控制不准确, 导致轮胎过硫或欠硫,影响轮
减少因轮胎损坏导致 的交通事故和经济损 失
汇报范围
01
02
03
04
钢丝轮胎损坏的类型和表现
损坏原因的分析和归类
预防措施和解决方案的建议
未来研究方向的展望
02
钢丝轮胎损坏现象描述
损坏类型
01
02
03
断裂
钢丝在轮胎内部发生断裂 ,导致轮胎结构受损。
腐蚀
钢丝受到化学或电化学腐 蚀,导致强度和韧性降低 。
胎使用寿命。
使用环境因素
1 2
路况
恶劣的路况如坑洼、石子等,会加速轮胎磨损和 损坏。
气候
极端温度、紫外线辐射、雨雪等气候条件对轮胎 性能产生负面影响。
3
负载
超载或负载不均会加速轮胎磨损,甚至导致轮胎 破裂。
全钢载重子午线轮胎胎圈露线的原因分析及解决措施

全钢载重子午线轮胎胎圈露线的原因分析及解决措施作者:张小平来源:《中国化工贸易·中旬刊》2019年第07期摘要:全钢载重子午线轮胎因耐磨性好、稳定性高等特点,拥有良好的发展空间。
但是,由于全钢载重子午线轮胎对于生产工艺以及生产设备的要求较高,质量缺陷在所难免。
胎圈露线作为常见质量缺陷之一,对轮胎外观以及性能造成一定影响。
本文将以轮胎成型过程为切入点,对全钢载重子午线轮胎胎圈露线的原因进行阐述分析,并提出可行有效的解决措施。
关键词:全钢载重子午线轮胎;胎圈;露线;钢丝圈1 胎圈露线概述轮胎胎圈露线,即胎圈帘线外露。
露线有三个评判等级:其一,合格品。
覆胶存在,且其最小厚度在1mm以上;其二,等外品。
覆胶存在,但最小厚度在1mm以下;其三,废品。
无覆胶,钢丝直接露出。
测量跳圈露线,可以利用针头探入深度获取覆胶厚度,也可以直接片取露线最严重部位胶料以获得最小覆胶厚度。
胎圈露线有出边露线和不出边露线两种。
前者是因成型半成品或者加工设备不达标,胎圈直径较小,胶料分布不均引起的。
胎圈存在肉眼可见的胶边现象;而后者是因防水线和胎踵之间部位的胶料不足,导致胶料流动,而出现胎圈露线缺陷。
2 原因分析及解决措施2.1 胎侧耐磨胶厚度通常情况下,全钢载重子午线轮胎的胎侧耐磨胶厚度的允许公差的范围应为±0.3mm。
当胎侧耐磨胶厚度超出标准值,则会减小胎胚直径,导致硫化装胎工序出现卡盘啃钢丝圈的现象,胶料分布不均,胎圈露线。
同时,胎侧厚度过薄,也会引起胎侧耐磨胶整体厚度变小。
从外胎施工工艺表中,可以得出防水线和胎踵二者之间胎侧厚度的额定值,通过对比分析,检测该处厚度是否符合标准,否则,厚度值过小容易引起露线问题。
解决措施:因地制宜,按照露线位置不同,有针对性调整胎侧耐磨胶的厚度。
同时,应加强质检力度,严格遵循施工工艺规范,对于尺寸不合格的成型半成品严谨使用。
2.2 气密层或过渡层宽度气密层或者过渡层的宽度过大,都会增厚胎圈底部胶料,从而引起卡盘啃钢丝圈,导致胶料分布不均,胶料少的部分容易出现露线问题。
全钢工程胎常见质量缺陷、产生原因及解决措施

全钢工程胎常见质量缺陷、产生原因及解决措施全钢工程胎常见质量缺陷、产生原因及解决措施(草稿)一、常见内在质量缺陷(X光检验)1、带束层1.1、差级不均或齐边带束层差级不均或齐边,会使轮胎两侧肩部材料分布不均,造成轮胎行驶时受力不均,较厚的一侧生热大,易产生脱空;较薄的一侧易发生肩部裂开。
产生原因:①辅助鼓的定中心装置错误,灯光标尺偏离中心线。
②带束层部件喷霜、粘合性能差,滚压时造成移位。
③成型定型时压力及宽度不合格,使胎体与带束层定型时差合不上,滚压胎冠时造成带束层偏歪。
④带束层斜边长度不合格或带束层宽窄不一。
解决措施:①检查辅助鼓定中心装置,灯光标尺必须定位于中心,供料架不许偏歪。
②带束层部件喷霜及粘合性能差的,甩出不使用。
③检查成型定型压力及宽度,不符合施工标准的应及时调整。
④对于带束层斜边长度不合格或宽窄不一的部件要甩出不使用。
1.2散线带束层断线后用胶条包边,其主要目的:一是裁断后至成型前防止帘线端边受潮;二是避免钢帘布端头处松散和提高裁断后端部与其它部件的粘合性。
散线主要产生在第二、三层带束层,带束层散线的轮胎在行驶中易局部生热大,产生脱层。
产生原因:①成型后压辊定位偏高,低压设定不合理,滚压时高压使用过早。
②带束层粘性差,不能很好地与其它带束层成为一体,在滚压时产生移位。
③垫胶贴合偏移或左右贴反。
④垫胶过薄。
⑤胎冠肩部超厚。
解决措施:①成型操作前要检查平面宽度是否符合工艺要求,防止因扇形块风压不稳定而引起组合件移位。
②调整设定好定型风压,使其符合工艺要求。
③滚压胎冠时,检查后压辊的位置,使用低风压或高风压时要掌握好风压及滚压时间。
④贴合带束层时,第二、三层带束层接头后压实,并用胶片对两侧端点包边。
⑤校正供料架、灯标(贴合部件手工加以调整)。
贴合垫胶时要注意,梯形长斜面靠向外侧。
⑥过薄的垫胶停止使用。
⑦胎冠肩部超厚停止使用。
2、胎体2.1接头开接头开主要是指钢丝帘布接头拼接不牢,在成型充气膨胀和硫化内压的作用下,拼接不牢的部位断裂开缝,缺少钢丝。
钢丝绳绳芯挤出的原因

钢丝绳绳芯挤出的原因
钢丝绳绳芯挤出的原因可能有以下几种情况:
- 钢丝绳生产过程中,外层股预变形量过大,导致内层绳和外层股没有紧密结合在一起,当钢丝绳受力时,内外层受力不均,当内层受力大于外层受力时,钢丝绳突然卸载,内层绳的反驳力大于外层,就会导致内层绳挤出的质量缺陷。
- 捻制过程中各工序的捻制应力控制不当,因35W×7钢丝绳内外层捻向相反,当内层绳的应力大于外层时,内层绳的旋转扭矩就会大于外层,内层绳向外层捻向反方向的扭力不断增大,导致外层股排列结构破坏,内层绳从结构破坏的股缝中挤出。
- 35W×7钢丝绳因其结构的特殊性,在捻制过程中,内层绳和外层打扭度数都较大,但内外层捻向相反,钢丝绳整体打扭平衡,这使得钢丝绳内部残余应力较大,未得到释放,使用过程在滑轮卷筒上不断弯曲运行,严重时导致内层绳挤出。
- 目前,国内多数钢丝绳都是采用分层捻制而成,这使得钢丝绳捻制不够紧密,使用过程中稍有不慎就会导致结构破坏,可能发生内层绳挤出的质量问题。
胎体钢丝帘布直裁机常见质量问题原因分析及解决措施

作者简介:陈峰(1978-),男,工程师,主要从事轮胎设备机械技术及管理工作。
收稿日期:2020-09-011 导开与修边工位对质量的影响和原因分析(1)导开大筒帘布在使用的过程中存在上料歪斜、边部经常打折及裁出料存在大头小尾的现象。
针对以上问题,通过分析和研究特在帘布导开处进行了改造优化,安装了纠偏装置,纠偏装置现场实物如图1所示,此装置可以彻底解决以上问题,操作人员只需按以下三个步骤进行处理即可解决。
图1 纠偏装置实物图a.查看导开纠偏功能是否开启,倘若处于关闭状态,打开该功能即可解决。
b.若纠偏功能可以确认正常开启,且无损坏现象,对需导开纠偏的地方进行调节,使其适应帘布的宽度,调节方法对班组均有培训。
胎体钢丝帘布直裁机常见质量问题原因分析及解决措施陈峰,赵杰,敖玉元,林立君,武博(杭州朝阳橡胶有限公司,浙江 杭州 310018)摘要:90度钢丝帘布裁断机,是用来在规定的宽度下,以90度角裁切未硫化的钢丝帘布,最后通过卷取装置卷成需要长度的帘布卷。
同时,可对拼接后的钢丝帘布进行贴合子口包胶及包边等操作,从而,形成一条钢丝帘布裁断与拼接的自动生产线。
本生产线生产的钢丝帘布卷是轮胎成型时的主要胎体部件。
胎体质量对轮胎的质量和使用寿命具有重要影响。
关键词:裁刀;拼接;贴胶中图分类号:TQ330.4文章编号:1009-797X(2021)09-0021-04文献标识码:B DOI:10.13520/ki.rpte.2021.09.005c.若以上两种方法仍未解决问题,则检查下最基本的错误,上料时大筒帘布中心是否位于红外线定中装置对齐处,这点有时候不注意会出现操作失误的情况。
(2)经过修边后,产生的余胶过多或者裁切不平整,在拼接后容易出现胎体病疵。
病疵产生的原因有以下五点:a.检查导开修边刀自动调节接近开关是否损坏;b.修边刀使用时间是否周期太长,刀刃已经钝化,一般使用周期为7天。
c.修边的温度没有达到标准要求,修边刀要求工作温度为80±5 ℃。
轮胎钢丝帘线拉伸性能缺陷分析及质量控制对策

作者简介:秦增辉(1987-),男,主要从事轮胎原材料、成品检测及轮胎结构设计、公司体系认证等相关工作,曾获东营市“五一劳动奖章”等多项荣誉。
收稿日期:2023-09-08我国是汽车轮胎制造大国,汽车轮胎的产量约占世界总产量的25%。
由于汽车的轮胎支撑着整辆汽车的重量,必须保证具有足够的强度和良好附着性。
然而,在轮胎生产中由于工艺标准执行问题的存在时常带来轮胎帘线拉伸性能缺陷产生,导致轮胎的强度不够,车辆在行驶时存在爆胎的隐患。
据全国交通事故原因分析,在高速路发生的事故中有42%是由轮胎造成的,所以,进行轮胎钢丝帘线拉伸性能缺陷分析,弄清发生问题的原因,采取有力措施予以解决,有利于提高轮胎生产质量,减少汽车交通事故发生。
1 子午线轮胎概述1.1 子午线轮胎的概念子午线轮胎属于特殊的轮胎结构,区别于斜交轮胎和调压轮胎,子午线轮胎的胎体帘线和外胎的几乎平行,帘线角度约等于0°,故子午线轮胎的帘线没有维系交点。
在实际的行驶中,子午线轮胎可能因为冠部附近的应力增加而出现周向伸张,导致轮胎出现辐射状的裂口。
为此子午线轮胎的缓冲层是由与胎体帘线90°相交的帘线层构成,让其在轮胎内部构成一条刚性的环形带,子午线轮胎的缓冲层不仅具有避免轮胎形变的作用,还具有固定轮胎的作用。
子午线轮胎的缓冲层又称为带束层,是子午线轮胎中主要的部件之一。
在正常的行驶中,子午线轮胎的缓冲层会承受轮胎钢丝帘线拉伸性能缺陷分析及质量控制对策秦增辉,赵淑霞,李超民,尚荣武,苟金峰(山东万达宝通轮胎有限公司,山东 东营 257500)摘要:随着社会经济发展,汽车数量日益增多,社会各界和汽车使用者对汽车性能的要求日益提高,必须对汽车轮胎制造的质量引起高度重视,其中包括对轮胎钢丝帘线拉伸性能的分析,确保汽车制造安全质量性能得到进一步改善。
本文针对子午线轮胎胎体帘线在生产过程中出现的拉伸性缺陷进行了概括,分析了缺陷产生的原因,进行了相关案例分析,并提出了相关质量把控对策。
一起起重机钢丝绳钢丝突出事件的原因分析

一起起重机钢丝绳钢丝突出事件的原因分析摘要:钢丝绳是起重机重要组成部件,钢丝绳状态的好坏关系到起重机的安全使用。
常见的钢丝绳失效原因有正常使用磨损、老化、安装不当、使用不规范等情况。
本文主要对一起因绳端防散股制作方式及温度变化引起的钢丝绳失效原因进行分析并提出改进建议。
关键词:起重机;钢丝绳;钢丝突出;温度变化;绳端防松0引言起重机钢丝绳常见的失效症状主要有可见断丝、直径减小、断股、腐蚀、畸形和损伤。
其中畸形和损伤又包括钢丝绳出现波浪形、笼状畸形、绳芯或绳股突出或扭曲、钢丝环状突出、绳径局部增大、局部扁平、扭折、折弯以及热和电弧引起的损伤。
本文主要针对一起起重机在使用中出现的钢丝绳绳芯钢丝突出异常事件,结合起重机滑轮布置、钢丝绳结构、安装情况和使用环境进行分析。
分析结果表明本起事件的主要原因与钢丝绳的绳端防松散形式部份钢丝熔焊不牢和环境温差变化大引起的物理过程有关。
1事件概况本起重机主要用于某厂房内物项吊装,重复性流水作业工况。
起升机构每循环工作周期约3分钟,起升机构吊钩组每周期均到达上限位停止点。
在一次操作接近上限位停止点时,操作员听到吊钩组与钢丝绳之间发出有“吱吱”的异常声音。
经检查发现起升机构钢丝绳尾绳(平衡梁侧)往下1米左右出现有钢丝绳散股情况,股芯有少量钢丝突出外层绳股(见图1a)。
经检查钢丝绳外层缠绕绳股无磨损,无异常损伤,其余钢丝绳均无异常情况。
检查钢丝绳端防散股措施为熔焊形式(见图1b)。
图1 事件钢丝绳情况2起升机构钢丝绳系统2.1钢丝绳设置:该起重机起升机构采用双钢丝绳起升设计,每根钢丝绳头尾端分别固定于卷筒和平衡梁上。
对于意外工况引起的单个钢丝绳断裂,另一根钢丝绳完全可以承载在起吊能力范围内的载荷,同时平衡梁偏斜触发钢丝绳断绳限位开关,起升机构断电制动器抱闸。
同时,操作者可以通过旁路操作后,将被吊物安全就位。
2.2钢丝绳型号:根据该起重机重要性分级,该起升机构依据单一故障保护原则设置双钢丝绳,由两根独立钢丝绳组成卷绕系统。
轮胎翻修技术

钢丝圈爆破的原因是什么?这主要是由于装用变形的轮辋或不符合规定的轮辋,轮胎充气低,使轮胎的子口与轮辋贴合不紧,可能在其表面上转动,增加胎趾加强部的磨损或胎圈口的磨损,同时也由于轮胎的屈挠点下降,或因轮辋生锈变形,刹车鼓温度过高而造成钢丝圈爆破。
胎侧爆破的原因是什么?一般是由于汽车超载。
轮胎的充气压力过大,汽车急转弯的甩力过大;或由于汽车下坡,坡度陡,车身重量前移,轮胎超载严重,造成胎侧折叠而引爆破。
胎面花纹开裂的原因是什么?主要是轮胎超载和充气不当造成的。
超载和高压使轮胎胎面花纹沟槽在棚紧的状态下转动。
轮胎每转动一周受到两次伸张和一次压缩的应力变形,由于花纹沟槽无时无刻地开闭,致使花纹沟槽开裂;有时轮胎低充气,胎面花纹搓揉太严重,花纹沟槽底产生皱纹,日久之后也引起花纹开裂。
钢丝刺出和钢丝圈爆破的原因是什么?这些一般是由于轮胎厂生产工艺有问题。
例如钢丝的黏和不牢,以致轮胎在使用过程中钢丝与胶分离、松散变形,导致爆破;钢丝圈制造不当,三角胶填充不牢,因而产生变形,致使钢丝松动刺出,最后爆破;有的是在生产过程中粗制滥造,钢丝没有挂胶或根本没有挂胶就绕缠,钢丝搭头捆不牢等,使轮胎在行驶中发生钢丝刺出等问题。
胎面磨耗不均的原因是什么?造成胎面磨耗不均的原因很多,现仅就容易发生的现象简述如下。
胎面上呈波浪或起伏状态磨耗不均的原因。
①前轮行驶摆动;立人轴及钢套等松紧不一致;方向盘自由行程太大,行驶时轮胎发抖等。
②装用变形轮辋,或者由于定位不对,使用中轮胎左右摇摆而产生的。
③装用高度越野花纹(特别是汽车前轮),定位若不正确,会给轮胎带来不良后果。
a. 前束安装不对,将造成胎面平齐,磨耗快。
b. 如果转向主销内倾角不正确,会使胎面磨耗不均且呈波浪形。
c. 前轮外倾角太大会引起胎面偏磨。
d. 转向主倾角太大,会使胎面磨锉粗糙及一段不均衡。
e. 主销松动,胎肩花纹磨成波浪形。
f. 前轮机太松,也会使胎肩花纹磨成小波浪状。
轮胎外胎质量缺陷及原因分析
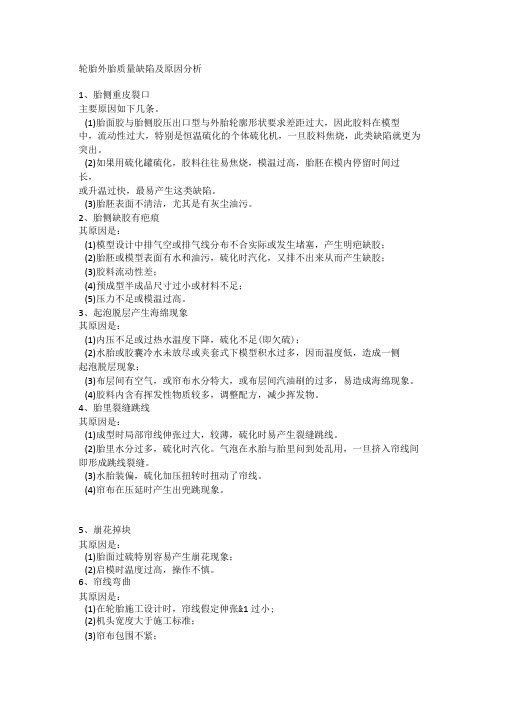
轮胎外胎质量缺陷及原因分析1、胎侧重皮裂口主要原因如下几条。
(1)胎面胶与胎侧胶压出口型与外胎轮廓形状要求差距过大,因此胶料在模型中,流动性过大,特别是恒温硫化的个体硫化机,一旦胶料焦烧,此类缺陷就更为突出。
(2)如果用硫化罐硫化,胶料往往易焦烧,模温过高,胎胚在模内停留时间过长,或升温过快,最易产生这类缺陷。
(3)胎胚表面不清洁,尤其是有灰尘油污。
2、胎侧缺胶有疤痕其原因是:(1)模型设计中排气空或排气线分布不合实际或发生堵塞,产生明疤缺胶;(2)胎胚或模型表面有水和油污,硫化时汽化,又排不出来从而产生缺胶;(3)胶料流动性差;(4)预成型半成品尺寸过小或材料不足;(5)压力不足或模温过高。
3、起泡脱层产生海绵现象其原因是:(1)内压不足或过热水温度下降,硫化不足(即欠硫);(2)水胎或胶囊冷水未放尽或夹套式下模型积水过多,因而温度低,造成一侧起泡脱层现象;(3)布层间有空气,或帘布水分特大,或布层间汽油刷的过多,易造成海绵现象。
(4)胶料内含有挥发性物质较多,调整配方,减少挥发物。
4、胎里裂缝跳线其原因是:(1)成型时局部帘线伸张过大,较薄,硫化时易产生裂缝跳线。
(2)胎里水分过多,硫化时汽化。
气泡在水胎与胎里问到处乱用,一旦挤入帘线间即形成跳线裂缝。
(3)水胎装偏,硫化加压扭转时扭动了帘线。
(4)帘布在压延时产生出兜跳现象。
5、崩花掉块其原因是:(1)胎面过硫特别容易产生崩花现象;(2)启模时温度过高,操作不慎。
6、帘线弯曲其原因是:(1)在轮胎施工设计时,帘线假定伸张&1过小;(2)机头宽度大于施工标准;(3)帘布包围不紧;(4)机头肩部弧度不适宜。
7、花纹棱角不全,有圆角现象。
其原因是:(1)胎面口型小,胎面厚度小于设计标准;(2)模型气孔堵塞或排气孔分布不合理;(3)水胎内压不足;(4)胶料流动性不好。
8、胎冠出大边其原因是:(1)如果硫化罐在硫化时高压水压力不够,或没给高压水就向水胎通过热水,或装模时,模型上的螺丝没有扭紧;(2)升温时间太长或内压过大;(3)如用硫化机,机台下沉;(4)硫化机锁模力不够,调整硫化机压力系统以满足锁模要求。
钢丝缠绕胶管常见问题、原因及解决措施
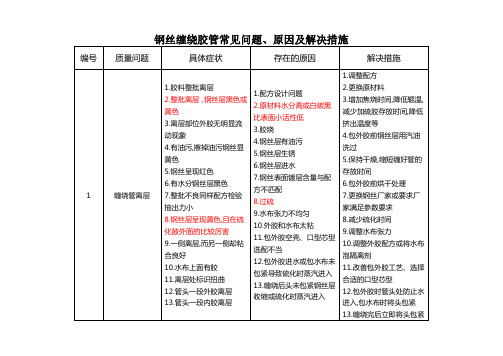
9
缠绕管缩口
1.缠绕管头部内径小于芯棒内径
1.预定型效果差
2.放线张力过大
1.严格检验预定型结果
2.控制放线张力
钢丝缠绕胶管常见问题、原因及解决措施
编号
质量问题
具体症状
存在的原因
解决措施
1
缠绕管离层
1.胶料整批离层2.整批离层,钢丝层黑色或黄色3.离层部位外胶无明显流动现象4.有油污,擦掉油污钢丝显黄色5.钢丝呈现红色6.有水分钢丝层黑色7.整批不良同样配方检验抽出力小8.钢丝层呈现黄色,且在硫化鼓外面的比较厉害9.一侧离层,而另一侧却粘合良好10.水布上面有胶11.离层处标识扭曲12.管头一段外胶离层13.管头一段内胶离层
5
缠绕波纹度大
1.钢丝层均匀胶管外径不均2.钢丝层不均匀外径也不均
1.A包胶外径不均B胶料分散不均导致膨胀不均C水布张力不均2.A缠绕口型选择过大B缠绕有赶管现象C缠绕密度太大
1.A改善包外胶工艺B提高胶料分散度C调整水布张力2.A选择合适的缠绕口型B提高内胶挺性或冷冻内胶C缠绕密度要合理