高速线材生产工艺技术
高速线材生产工艺技术

高速线材生产工艺技术
一、前言
高速线材是一种重要的金属产品,在现代工业生产中扮演着重要的角色。
本文将介绍高速线材的生产工艺技术,包括材料选取、生产工艺流程、设备及技术要点等方面的内容。
二、材料选取
高速线材的生产需要选用优质的原材料,通常是优质碳素钢、合金钢等。
这些原材料需要具备良好的硬度、强度、韧性和耐磨性等特性,以确保生产出高质量的线材产品。
三、生产工艺流程
1.原材料准备:将选用的原材料进行清洗、除铁等预处理工序。
2.热处理:通过加热、保温、冷却等工艺,调整原材料的组织结构,
提高其机械性能。
3.坯料加工:将经过热处理的原材料进行拉拔、锻造等加工,使其形
成符合要求的线材坯料。
4.精整加工:通过轧制、精整等工艺,将坯料进行细致加工,使其直
径、表面质量等达到要求。
5.检验与包装:对成品进行检验,保证质量合格后进行包装。
四、设备及技术要点
1.轧机:高速线材的生产需要使用高效的轧机设备,以保证生产效率
和产品质量。
2.管控系统:通过先进的管控系统,实现对生产过程的精确把控,保
证产品质量的稳定性和可靠性。
3.冷却技术:采用合适的冷却技术,可以有效控制产品的温度和晶粒
结构,提高线材的硬度和强度。
五、结语
高速线材的生产工艺技术是一个复杂而精密的过程,需要依靠先进的设备和技术手段,才能生产出高质量的线材产品。
同时,生产过程中的质量管控和技术创新也是至关重要的。
希望本文所介绍的内容能够为相关行业提供一定的参考和帮助。
高线生产简介

高速线材生产设备
二、轧机
高线厂15#~28#均为旋臂式轧机,15#~18#轧机布置 形式为平立交替式,传动方式为单独传动。19#~28#布置形 式为顶角45度,传动方式为集体传动。各架次轧机规格如下:
架次 规格 15#~18# φ285 19#~23# φ228 24#~28# φ170
(3)加热质量好。完全消除了粘钢、翻炉的限制,很大程度上消除了 钢坯黑印,坯料下表面也不会造成划伤
(4)能耗低。由于采用蓄热式,废气排放时经过蓄热式,蓄热体将高 温废气的热量留下给换向后的空气和煤气预热,大大降低了能耗损失。
高速线材生产设备
一、加热炉
高速线材生产设备
二、轧机
高线厂1#~14#均为短应线轧机,轧机布置形式为平立 交替式。短应力线轧机和闭口式轧机相比具有投资少,刚度 大、更换方便的特点。各架次轧机规格如下:
(1)尽量实现钢坯热送。
(2)避免强制加热,加热能力不足时可适当待温。
(3)轧制节奏允许时加大步距,减少钢坯在炉内停 留时间。
高速线材生产工艺
二、加热
4、钢坯除鳞 国内线材生产线钢坯高 压水除鳞是近几年才投入使 用的,因为以前国内线材产 品大多为建筑用材,对表面 质量要求不严格,而且线材 粗轧都有几架箱型孔,有较 好的去除氧化铁皮的效果。 随着线材产品的不断升级, 对线材产品表面质量的要求 不断提高,国内新投产的生 产线都配备了高压水除鳞设 备。
高速线材生产工艺
二、加热
1、原料
线材的原料为小方坯,一般为150*150或 160*160的连铸小方坯,单支重量一般在2~2.5吨。 由于一部分冷墩钢和硬线拉丝用线材需要有较高的 致密度,所以有些钢厂也开始采用初轧坯来做高线 的原料。
高速线材生产工艺技术
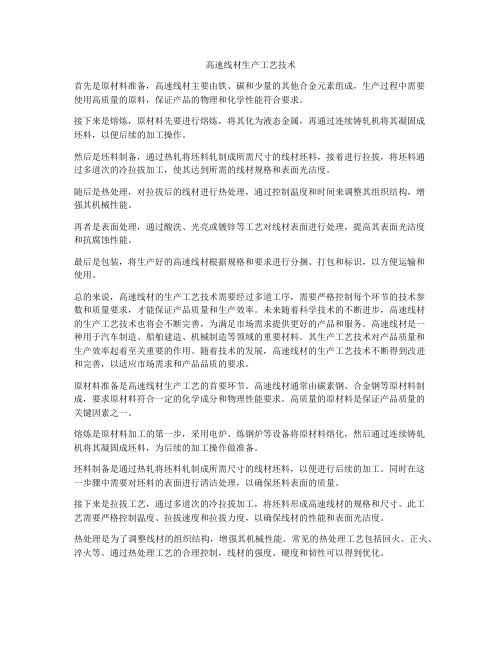
高速线材生产工艺技术首先是原材料准备,高速线材主要由铁、碳和少量的其他合金元素组成,生产过程中需要使用高质量的原料,保证产品的物理和化学性能符合要求。
接下来是熔炼,原材料先要进行熔炼,将其化为液态金属,再通过连续铸轧机将其凝固成坯料,以便后续的加工操作。
然后是坯料制备,通过热轧将坯料轧制成所需尺寸的线材坯料,接着进行拉拔,将坯料通过多道次的冷拉拔加工,使其达到所需的线材规格和表面光洁度。
随后是热处理,对拉拔后的线材进行热处理,通过控制温度和时间来调整其组织结构,增强其机械性能。
再者是表面处理,通过酸洗、光亮或镀锌等工艺对线材表面进行处理,提高其表面光洁度和抗腐蚀性能。
最后是包装,将生产好的高速线材根据规格和要求进行分捆、打包和标识,以方便运输和使用。
总的来说,高速线材的生产工艺技术需要经过多道工序,需要严格控制每个环节的技术参数和质量要求,才能保证产品质量和生产效率。
未来随着科学技术的不断进步,高速线材的生产工艺技术也将会不断完善,为满足市场需求提供更好的产品和服务。
高速线材是一种用于汽车制造、船舶建造、机械制造等领域的重要材料。
其生产工艺技术对产品质量和生产效率起着至关重要的作用。
随着技术的发展,高速线材的生产工艺技术不断得到改进和完善,以适应市场需求和产品品质的要求。
原材料准备是高速线材生产工艺的首要环节。
高速线材通常由碳素钢、合金钢等原材料制成,要求原材料符合一定的化学成分和物理性能要求。
高质量的原材料是保证产品质量的关键因素之一。
熔炼是原材料加工的第一步,采用电炉、炼钢炉等设备将原材料熔化,然后通过连续铸轧机将其凝固成坯料,为后续的加工操作做准备。
坯料制备是通过热轧将坯料轧制成所需尺寸的线材坯料,以便进行后续的加工。
同时在这一步骤中需要对坯料的表面进行清洁处理,以确保坯料表面的质量。
接下来是拉拔工艺,通过多道次的冷拉拔加工,将坯料形成高速线材的规格和尺寸。
此工艺需要严格控制温度、拉拔速度和拉拔力度,以确保线材的性能和表面光洁度。
高速线缆生产工序

高速线缆是一种通信设备连接线缆,一般用于实现短距离的高速互联通信,主要用于实现服务器,交换机,存储器等设备间的互连,是一种低成本的高速数据通信解决方案。
高速线缆基本是采用镀银导体,发泡绝缘芯线,具有优良的衰减性能和低延时,令信号传输正确无误及提高传输速度。
采用对屏蔽及总屏蔽的结构,线材具有良好的屏蔽效果,使信号避免外界干扰。
高速线缆的线对采用平行结构,所以拥有低延时差,可以实现高频宽带传输。
线材规格从30~24AWG,有2P,4P,8P 等多种结构,可满足多种应用场合。
高速线缆生产工序高速线缆的制造是一个复杂的过程,解决高速应用需要有合适的生产设备及成熟稳定的生产工艺。
在生产高速线缆产品时,材料选择,工艺参数和过程控制,电气参数的专门的实验室检测都发挥关键作用。
高速线缆是由平行线对组成,包括5个生产工序,这些工序影响着线材的各项性能。
高速线的生产的具体生产工序如下:1、绝缘芯线押出绝缘芯线是线缆生产的基础,芯线质量的好坏对后续工序有至关重要的影响。
芯线采用物理发泡聚烯烃材料,皮-泡-皮结构绝缘,线材泡孔大小一致,分布均匀,具有较高的机械强度和绝缘附着力。
在此过程中,要求生产设备具有在线监控及控制功能,确保芯线均一、稳定,控制的工艺参数包括芯线的直径、水中电容、同心度等。
2、平行对绕包包通过绕包机就是将2根绝缘芯线及地线集合在一起,同时在外面包上一层铝箔拉和一层自粘聚酯带,用于屏蔽线对及稳定绕包芯线结构。
此过程对线材性能有着重要影响,包括阻抗、延时差、衰减等,因此必须严格按工艺要求生产,并对电性能进行测试,以确保绕包芯线是符合要求的。
3、平行对成缆成缆就是通过成缆机将绕包芯线集合在一起,同时在外面包上一层聚酯带和一层铝箔麦拉带,用于屏蔽线对及稳定成缆芯线结构。
成缆工序影响着电缆的整体性能,因此在生产过程中需严格控制各绕包芯线的一致性,并对阻抗、延时差、衰减等电性能进行测试,以确保成缆芯线是符合要求的。
高线工艺及设备选用
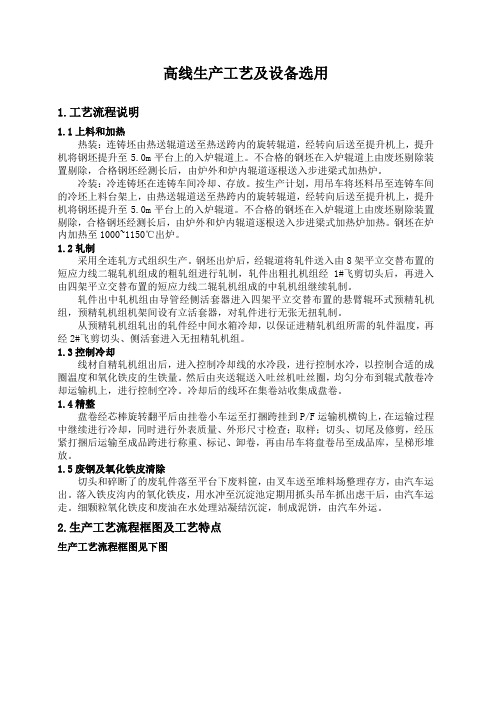
高线生产工艺及设备选用1.工艺流程说明1.1上料和加热热装:连铸坯由热送辊道送至热送跨内的旋转辊道,经转向后送至提升机上,提升机将钢坯提升至5.0m平台上的入炉辊道上。
不合格的钢坯在入炉辊道上由废坯剔除装置剔除,合格钢坯经测长后,由炉外和炉内辊道逐根送入步进梁式加热炉。
冷装:冷连铸坯在连铸车间冷却、存放。
按生产计划,用吊车将坯料吊至连铸车间的冷坯上料台架上,由热送辊道送至热跨内的旋转辊道,经转向后送至提升机上,提升机将钢坯提升至5.0m平台上的入炉辊道。
不合格的钢坯在入炉辊道上由废坯剔除装置剔除,合格钢坯经测长后,由炉外和炉内辊道逐根送入步进梁式加热炉加热。
钢坯在炉内加热至1000~1150℃出炉。
1.2轧制采用全连轧方式组织生产。
钢坯出炉后,经辊道将轧件送入由8架平立交替布置的短应力线二辊轧机组成的粗轧组进行轧制,轧件出粗扎机组经1#飞剪切头后,再进入由四架平立交替布置的短应力线二辊轧机组成的中轧机组继续轧制。
轧件出中轧机组由导管经侧活套器进入四架平立交替布置的悬臂辊环式预精轧机组,预精轧机组机架间设有立活套器,对轧件进行无张无扭轧制。
从预精轧机组轧出的轧件经中间水箱冷却,以保证进精轧机组所需的轧件温度,再经2#飞剪切头、侧活套进入无扭精轧机组。
1.3控制冷却线材自精轧机组出后,进入控制冷却线的水冷段,进行控制水冷,以控制合适的成圈温度和氧化铁皮的生铁量。
然后由夹送辊送入吐丝机吐丝圈,均匀分布到辊式散卷冷却运输机上,进行控制空冷。
冷却后的线环在集卷站收集成盘卷。
1.4精整盘卷经芯棒旋转翻平后由挂卷小车运至打捆跨挂到P/F运输机横钩上,在运输过程中继续进行冷却,同时进行外表质量、外形尺寸检查;取样;切头、切尾及修剪,经压紧打捆后运输至成品跨进行称重、标记、卸卷,再由吊车将盘卷吊至成品库,呈梯形堆放。
1.5废钢及氧化铁皮清除切头和碎断了的废轧件落至平台下废料筐,由叉车送至堆料场整理存方,由汽车运出。
高速线材轧制工艺提升与优化

高速线材轧制工艺提升与优化【摘要】高速线材轧制工艺在现有的工程实践中存在诸多问题,如生产效率低、能耗高等。
为此,本文从优化关键技术、提升工艺方法等方面进行了深入研究和探讨。
针对目前存在的问题,提出了一些改进方案,并对高速线材轧制工艺的发展趋势进行了分析和展望。
结合工艺的应用领域,探讨了其在行业中的重要性和价值。
未来,可以通过进一步提升工艺,加强研究与创新,来实现高速线材轧制工艺的进一步提升和优化。
总结了本文的研究成果,提出了未来研究方向,展望了高速线材轧制工艺的未来发展方向。
【关键词】高速线材轧制工艺、优化、提升、关键技术、方法、发展趋势、应用领域、进一步提升、未来研究方向、总结、研究背景、研究意义、研究方法。
1. 引言1.1 研究背景高速线材轧制是金属加工领域的重要工艺之一,具有广泛的应用前景。
随着社会经济的不断发展,对高速线材的需求量也在不断增加,因此如何提升和优化高速线材轧制工艺显得尤为重要。
在过去的研究中发现,现有的高速线材轧制工艺存在一些问题,如产能低、质量波动大、能耗高等。
这些问题不仅影响了生产效率,还影响了产品质量,降低了企业的竞争力。
有必要对高速线材轧制工艺进行进一步的提升和优化,以适应市场需求的变化。
通过对高速线材轧制工艺进行研究,可以找到关键的技术点,从而实现对工艺的优化。
而研究方法的选择则直接影响着研究成果的可靠性和实用性,因此需要合理选择研究方法,以确保研究的科学性和有效性。
的探讨将有助于更好地理解高速线材轧制工艺的现状及存在的问题,为后续的研究奠定基础。
1.2 研究意义高速线材轧制工艺的优化与提升具有重要的研究意义。
随着社会经济的快速发展,高速线材在建筑、交通、机械制造等领域的应用日益广泛,对高速线材的质量和性能要求也越来越高。
优化和提升高速线材轧制工艺,可以有效改善产品质量,提高生产效率,降低生产成本,提升企业的竞争力。
随着科技的不断进步和创新,高速线材轧制工艺也面临着新的挑战和机遇。
高速线材轧制工艺提升与优化

高速线材轧制工艺提升与优化袁学津(宝山钢铁股份有限公司,上海 200000)摘 要:由于传统的高速线材轧制过程存在诸多的缺陷,随着汽车工业、航空航天等高端行业对普通碳素钢线材的要求不断提高,有必要对高速线材的轧制工艺进行提升,以此提高轧制产品的精度。
本文从轧制的温度、速度等参数入手,合理分析轧制的工艺过程,这样对高速线材的轧制具有重要的作用,有效的降低了轧制的成本。
关键词:高速线材轧制;工艺;优化中图分类号:TG335.63 文献标识码:A 文章编号:11-5004(2018)05-0165-2随着新型材料的不断进步与发展,其线材的性能成为关键,而高速线材轧机是轧制的关键设备,其工艺和性能都决定这金属材料的性能[1,2]。
由于在轧制过程中,需要根据坯料参数、孔型参数及轧制参数进行设定,在利用精确的模型计算坯料在孔型轧制后的宽展,从而预判出轧制的速度,线径和温度等参数[3,4]。
因为只有确保每一道工序次的正确性,才会对轧制过程的工艺达到最佳,以此获得优秀的产品,通过设置和制定高速线材轧制的目标形状及宽度值,才能准确控制轧制节奏,获得合格的产品尺寸,故减定径轧制区域宽展预测模型的准确程度对最终成品尺寸精度起着至关重要的作用。
本文以普通碳素钢线材为研究对象,以此分析高速线材轧制的工艺与优化,这样得到性能更优的材料性能,普通碳素钢线材由于强度和屈服系数都比较高,其广泛应用于我国的汽车、航空航天和化工制备等行业,因此对普通碳素钢线材的轧制显得极为重要,高速线材轧制工艺的提升和优化可以有效的提高普通碳素钢线材的性能。
1 高速线材轧制工艺分析普通碳素钢相对于其他材料而言,在强度、刚性、性价比、耐腐蚀性等方面都具有非常良好的性能,其熔点相对较高、由于普通碳钢的提炼相对简单和成熟,塑性也比较好,在汽车工业、大型桥梁、建筑施工过程中,得到广泛的应用。
但普通碳钢的刚性比较高,其延展性,抵抗变形能力,这些性能特点使得对其加工难度较大,不利于普碳钢的轧制成型。
高速线材生产工艺技术
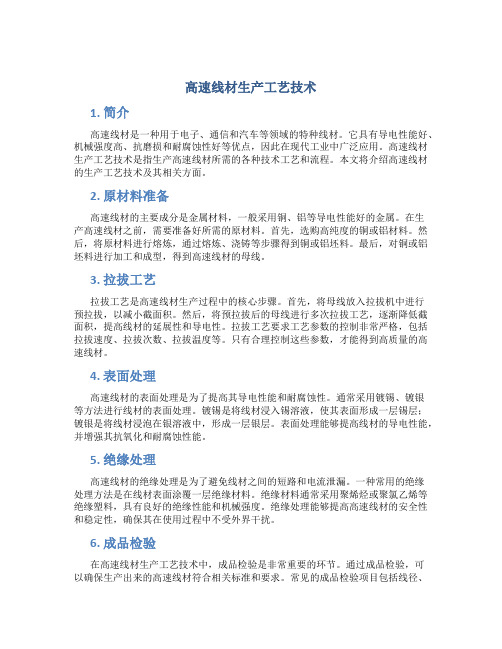
高速线材生产工艺技术1. 简介高速线材是一种用于电子、通信和汽车等领域的特种线材。
它具有导电性能好、机械强度高、抗磨损和耐腐蚀性好等优点,因此在现代工业中广泛应用。
高速线材生产工艺技术是指生产高速线材所需的各种技术工艺和流程。
本文将介绍高速线材的生产工艺技术及其相关方面。
2. 原材料准备高速线材的主要成分是金属材料,一般采用铜、铝等导电性能好的金属。
在生产高速线材之前,需要准备好所需的原材料。
首先,选购高纯度的铜或铝材料。
然后,将原材料进行熔炼,通过熔炼、浇铸等步骤得到铜或铝坯料。
最后,对铜或铝坯料进行加工和成型,得到高速线材的母线。
3. 拉拔工艺拉拔工艺是高速线材生产过程中的核心步骤。
首先,将母线放入拉拔机中进行预拉拔,以减小截面积。
然后,将预拉拔后的母线进行多次拉拔工艺,逐渐降低截面积,提高线材的延展性和导电性。
拉拔工艺要求工艺参数的控制非常严格,包括拉拔速度、拉拔次数、拉拔温度等。
只有合理控制这些参数,才能得到高质量的高速线材。
4. 表面处理高速线材的表面处理是为了提高其导电性能和耐腐蚀性。
通常采用镀锡、镀银等方法进行线材的表面处理。
镀锡是将线材浸入锡溶液,使其表面形成一层锡层;镀银是将线材浸泡在银溶液中,形成一层银层。
表面处理能够提高线材的导电性能,并增强其抗氧化和耐腐蚀性能。
5. 绝缘处理高速线材的绝缘处理是为了避免线材之间的短路和电流泄漏。
一种常用的绝缘处理方法是在线材表面涂覆一层绝缘材料。
绝缘材料通常采用聚烯烃或聚氯乙烯等绝缘塑料,具有良好的绝缘性能和机械强度。
绝缘处理能够提高高速线材的安全性和稳定性,确保其在使用过程中不受外界干扰。
6. 成品检验在高速线材生产工艺技术中,成品检验是非常重要的环节。
通过成品检验,可以确保生产出来的高速线材符合相关标准和要求。
常见的成品检验项目包括线径、电阻、绝缘层厚度、外观质量等。
通过对这些项目的检测和测试,可以判断线材的质量是否合格。
对于不合格的线材,需要进行返工或废弃,以确保产品质量。
- 1、下载文档前请自行甄别文档内容的完整性,平台不提供额外的编辑、内容补充、找答案等附加服务。
- 2、"仅部分预览"的文档,不可在线预览部分如存在完整性等问题,可反馈申请退款(可完整预览的文档不适用该条件!)。
- 3、如文档侵犯您的权益,请联系客服反馈,我们会尽快为您处理(人工客服工作时间:9:00-18:30)。
国内外线材生产现状
据不完全统计,目前世界上有近300条高速线材轧 机,其中高速无扭线材轧机约 260 套(摩根式占 170 套),年产线材约7000万吨。其中高线产量约占80% 以上,线材产量占钢材总产量 9 ~ 10 %。各国的输出 量与输人量平均在20%左右。美国是世界上最大的线 材输人国,每年线材消费量约 800 万吨,而本国每年 只生产 400 ~ 450 万吨,输人量占 40 ~ 50% ;日本是世 界上线材输出量最大国,每年线材产量约 750 万吨, 输出量约 200 万吨;世界上线材产量最大的国家是中 国, 2004 年线材实际产量为 4940 万吨(其中 1/3 以上 的线材,是复二重轧机生产的)
一般将轧制速度大于 40m/s 的线材轧机称为高 速线材轧机。 高速线材轧机的生产工艺特点:
连续、高速、无扭和控冷。其中高速轧制是最
主要的工艺特点(此外,单线、微张力、组合结构、
碳化钨辊环和自动化 )。
高速线材产品特点: 盘重大、精度高、性能优。
线材在国民经济中的作用与地位较重要,是不 可或缺的重要品种。 首先,线材产量占钢材总产量的比例很大,一 般线材产量占钢材总产量的8~10%,而我国占20%以 上; 其次,线材用途遍布国民经济各个部门,除直接 用作建筑钢材外,线材的深加工产品用途更为广泛和 重要,例如各类商品钢丝及专用弹簧钢丝、焊丝、冷 激钢丝、镀锌钢丝、通讯线、轮胎钢丝及钢帘线、高 强度钢丝及钢绞线、轴承钢丝、工具钢丝、不锈钢丝、 各种钢丝绳、钢钉、标准件等等。发达国家线材加工 比在70%左右,我国为30%左右。
轧制速度是高速线材轧机发展水平的标志, 按照轧制速度可将现代轧机分为如下几代: 第一代,1966~1969年,轧制速度43~50m/s; 第二代,1970~1975年,轧制速度50~60 m/s; 第三代,1976~1978年,轧制速度61~75m/s; 第四代,1979~1980年,轧制速度75~80m/s; 第五代,1981~1985年,轧制速度80~100m/s; 第六代,1986年以后,轧制速度100~120m/s。
现代高线轧机技术新进展
(l )无扭精轧机组。其发展趋势如下: 降低机组重心,降低传动轴高度,减少 机组的震动;强化轧机,增加精轧机组 的大辊径轧机的数量;改进轧机调整性 能。 (2)采用控温轧制与低温轧制。 (3)高精度轧制设备。 (4)粗轧机组的改进。
三、高线轧机生产工艺
高速无扭精轧工艺
高速无扭精轧工艺是现代线材生产的核 心技术之一,它是针对以往各种线材轧机存 在诸多问题,综合解决产品多品种规格、高 断面尺寸精度、大盘卷和高生产率的有效手 段。唯精轧高速度才能有高生产率。才能解 决大盘重线材轧制过程的温降问题。精轧的 高速度要求轧制过程中轧件无扭转,否则事 故频发,轧制根本无法进行。因此,高速无 扭精轧是高速线材轧机的一个基本特点。
20世纪60年代是线材生产技术发展的 兴盛与创新时期,最高轧制速度达到了 35m/s ,盘重达到了 550kg ,精度达到了 ±0.25mm 。 在轧制速度不断提高的同时也解决了 大盘重线材的控制冷却问题,因此从根本 上解决了盘重增大后,内层的线材长时间 在高温下停留生成粗大的晶粒,使内外圈 线材的力学性能差别很大、表面氧化铁皮 厚等问题。
目前我国拥有线材轧机近 110套, 其中复二重轧机占一半,横列式线材 轧机有近30套(将逐步被淘汰);其 余40多套属于高速线材轧机,其中从
国外引进的高水平线材轧机有 20多套,
国产高速线材轧机有近 20套。2004年,
全国线材生产中 ,高线比已经超过
55%;但优质硬线比约 10%,精炼比不 到30% 。
高速线材轧机一出现就显示出极大 的优越性,继美国之后,其他一些国家 和公司也纷纷创新高速线材轧机,出现 了各种机型,目前基本上有四种: 1)侧交45º 的美国摩根型; 2 ) 15º /75º 的德国德马克( Demak ) 型; 3)顶交45º 的英国阿希洛(Ashlow) 型; 4) 0º /90º平 - 立 布 臵 的 达 涅 利 (Danili)型。 各种机型各有优点,但基本工艺特 点差异不大,其中摩根机型应用最广泛。
轧后切头及切尾
高速无扭线材精轧机组采用微张力轧制,轧件 头部及尾部失张段断面尺寸大于公称断面尺寸。失 张段长度和张力值大小、机架间距以及精轧延伸系 数成正比,同所要求公称断面尺寸偏差成反比。通 常要将此超偏差段切除后交货。超差段可以在散卷 空冷运输机上用人工切除,但在延迟型控制冷却过 程中因为无保温罩段过短操作困难,而且切除头部 时容易造成线圈拉乱变形,集卷困难。目前较合理 的切除超差段是在集卷后打捆前的运输过程中,采 用倒卷系统,由人工用液压便携剪先切去轧件尾部 的超差段,之后将盘倒卷,使轧件头部超差段露在 外面,再由人工用液压便携剪切去头部超差段。
高线轧机的高质量控制要求
线材产品质量包括外形、尺寸精度、表面质量、化学 成分、金相组织及力学性能几个方面的内容。随着生产技 术的发展,用户对产品质量提出越来越高的要求。如: 目前φ5.5mm 线材的尺寸精度可达±0.lmm ,个别的甚 至可达±0.05mm。提高外形尺寸精度,一方面能减小超差 废品,提高收得率,另一方面,可为金属制品提供优质原 料,提高拉丝效率和拉模寿命,减少拉拔道次及动力消耗。 线材表面不得有裂缝、折叠、结疤、夹层等缺陷,允 许有轻微的划痕。对冷镦、高碳钢丝和琴钢丝用线材,表 面质量要求更加严格,一般必须作酸洗检查。 含碳量在0.3%以上的线材,应严格控制其表面脱碳, 否则脱碳后的线材表面变软,疲劳强度降低。
( l ) 1986 年前,无高速线材轧机,高线比为零;线 材自给率为 60 %。国内线材缺口很大,每年进口线材 200 ~ 300 万吨。国产线材质量较差,盘重小、化学成分 不稳定、表面质量差、尺寸公差大、性能也较差等。 ( 2 ) 1988 ~ 1992 年,国产线材有很大改观,高线比 近30%,线材自给率达 100%,进口逐年减少,出口逐年增 加,历史性变化的1991年,线材出口大于进口。 (3)1993~1994年,国产线材大幅增长, 但满足不了国民经济迅猛增长的需求, 造成线材大量进口,线材自给率降到 历史最低点57%。 (4)1995~1999年,国产线 材年净增长200万吨以上,高速 线材产量逐年大幅度提高, 到1999年高线比达46.7%, 这又是一个可喜变化。
高线轧机的发展
目前世界上应用最广泛的摩根型高速无扭 轧机是美国摩根( Morgan )公司 1962 年开始研 制的, 1966 年首先应用于加拿大钢铁公司哈密 尔顿( Hamilton )厂,其轧制速度 43~ 50m/s。 同时摩根公司和加拿大斯太尔摩 (Stelmo )公司 联合开发了线材轧后控制冷却系统,称之为斯 太尔摩线。 摩根新式精轧机发展经历了6个阶段,精轧 机 的 轧 制 速 度 从 第 I 代 的 43m/s , 到 第 Ⅵ 代 的 100m/,提高了1.3倍。
质量控制手段
各种高质量的线材在质量控制上需要各工序 都具备生产高质量线材的能力,即: ①保证原料质量。要求原料段具有原料检测、 检查与清理修磨的手段,使投入的原料具有生产 优质线材的条件; ②采用步进式加热炉,以保证灵活的加热制 度; ③在单线生产时粗轧采用平一立机组,减小 轧件刮伤; ④尽可能使用滚动导卫及硬面轧辊,保证轧 件表面质量。
其它差距
主要表现为线材在钢材中的比例、控 冷线材比、硬线比、合金线材比、制品用 线材比、线材直径、大规格盘条、盘重、 减面率、氧化铁皮量、散捆率、尺寸偏差、 不圆度、通条屈服应力差、含碳量、含磷 量、含硫量等方面。二、高速线材轧机的发展
高线轧机的诞生
高速线材轧机与其他先进技术一样也是时代的产物, 是冶金技术、电传电控技术、机械制造技术的综合产物。 据记载,世界上第一台线材轧机问世于17世纪,当时 是用锻坯轧制线材。18世纪中期出现了比较正规的线材轧 机,由粗轧及精轧两列横列式轧机组成,其轧速不超过 8m/s。 20 世纪初,开发了半连续式轧机。粗轧及中轧采用 连轧,精轧机组仍采用横列式轧机(复二重轧机是半连续 式轧机的一个特例)。轧制速度提高到 16m/s ,盘重增加 到 100kg 左右,尺寸精度较横列式为好,但品种及质量未 有根本好转。
【轧钢厂培训资料】
高速线材生产工艺技术
主讲:***
钢铁公司轧钢厂培训部 2008年1月
一、线材生产发展历程
概
述
线材一般是指直径为5~16mm的热轧圆钢或相 当该断面的异型钢,因以盘卷状态交货,统称为线 材或盘条。国外线材规格已扩大到Φ50mm。常见线 材多为圆断面,异型断面线材有椭圆形、方形及螺 纹形等,但生产数量很少。 线材品种按化学成分分类,一般分为低碳线材 (称软线)、中高碳线材(硬线),还有低合金与 合金钢线材、不锈钢线材及特殊钢线材(轴承、工 具、精密等)几大类。量大面广的品种属碳素钢线 材,占线材总量的80~90%。
品种质量差距
我国虽然是线材生产大国,但还 不能说是线材生产强国。目前我国还 有部分线材品种仍然依靠进口维持生 产、如钢帘线、高应力弹簧钢、不锈 钢、冷镦钢等线材。在重要用途线材 实物质量方面,与发达国家仍有较大 差距。
理化性能差距
差距主要表现在以下方面: (l)化学成分。国外线材波动小且稳定,[C]%一般波动在3 个范围;国内在6~8个范围,头尾偏析更严重。 (2)表面质量主要表现在脱碳层深度方面,国产一般为 0.023~0.14mm,最深为0.23~0.35mm;国外一般0.02~0.05mm。 (3)金相组织。进口线材实测奥氏体晶粒度为5~6级,很均 匀,索氏体一般85%以上。国产线材奥氏晶粒度2~7级,很不均 匀,索氏体一般达不到85%, (4)非金属夹杂。国产线材夹杂多且颗粒很大,尤其是A12O3 颗粒最长达133μm,一般为≥50μm,进口国外线材最大≥30μm, 一般8μm左右。 (5)钢中气体含量也普遍比国外线材高,〔H〕、〔O〕、 (N〕一般比国外线材高1~2倍甚至更高。