如何调较注塑工艺参数(温度、压力、速度、位置)?
注塑成型五大要素调机

注塑成型五大要素调机注塑成型是一种重要的塑料加工方法,广泛应用于各个领域。
在注塑成型过程中,调机是非常关键的环节,它直接影响到成品的质量和生产效率。
本文将介绍注塑成型的五大要素以及如何进行调机。
一、温度调控温度调控是注塑成型中必不可缺的一项要素。
合理的温度调控可以保证塑料原料的熔融状态,使其能够顺利进入模具中进行成型。
温度过低会导致塑料无法完全熔化或熔化不均匀,从而出现不良品;而温度过高则容易造成模具磨损或塑料变质。
因此,在调机过程中,需要根据具体的塑料种类和注塑机型号来合理设置温度,确保塑料的熔融状态处于最佳范围。
二、压力调控压力调控是注塑成型过程中另一个重要的要素。
通过调整注塑机的压力大小,可以控制塑料在模具中的流动速度和压实程度。
如果压力过小,塑料可能无法填充整个模具腔道,导致成品缺陷;而压力过大则容易造成模具损坏或超出产品要求的尺寸。
因此,在调机时需要根据产品要求和模具设计来合理设置压力,保证塑料能够在模具中达到理想的充填状态。
三、速度调控速度调控也是注塑成型中需要特别注意的要素。
注塑机的进料速度、射胶速度和回退速度等都需要在调机过程中进行合理设置,以确保塑料在模具中的流动和充填能够按照预定的要求进行。
不同的塑料种类和产品要求可能需要不同的速度设置,因此在调机时需要仔细研究产品的特点和要求进行相应设置。
四、冷却调控冷却调控是注塑成型中一个重要但常常被忽视的要素。
在塑料完成充填、压实后,需要进行冷却来使其固化成型。
冷却过程对成品的质量有着很大的影响,因此需要合理设置冷却时间和冷却介质的温度。
如果冷却不足,塑料可能会在脱模时变形或容易受到外界环境的影响;而过度冷却则可能导致产品表面出现气泡、翘曲等问题。
因此,在调机时需要根据具体情况合理控制冷却时间和温度,确保成品能够达到最佳的冷却效果。
五、保压调控保压调控是注塑成型过程中需要特别注意的一项要素。
在注塑机射胶结束后,需要进行一段时间的保压来确保产品在模具中的密实度和尺寸稳定性。
注塑成型工艺调整方法

注塑成型工艺调整方法注射保压时间、冷却时间注射时间、保压时间和冷却时间须根据产品厚度、模具温度、材料性能等进行设定。
注射时间设定一般以略大於螺杆完成注射行程移动的时间即可,过长的注射时间不但会产生机械磨损、能耗增加等负面影响,同时也会延长成型周期。
保压时间设定根据产品厚度来设定,薄壁产品在成型时可不用保压时间;在设定保压时间时,只要产品表面无明显凹陷即可,也可用称重法来确定,逐步延长保压时间直至产品质量不再变化的时间即可定为最佳保压时间。
冷却时间同样需根据产品厚度、模具温度、材料性能来确定,一般无定型聚合物所需冷却时间要比结晶型聚合物时间长。
注射压力、速度注射压力设定要遵循宜低不宜高的原则,只要能提供足够动力达到所要求的注射速度、使熔体能够顺利充满型腔即可,过高的压力容易使制品内产生内应力;但在成型尺寸精度较高的制品时,为防止产品收缩过度,可以采用高压力注射以减少制品脱模後的收缩。
注射速度会影响产品的外观质量,其设定应根据模具的几何结构、排气状况等进行设定,一般在保证良好的外观前提下,尽量提高注射速度,以减少充填时间。
在注射成型中,熔体在模具内流动时,模壁会形成固化层,因而降低了可流动通道的厚度,一般根据模具结构和注射速度不同,模壁会有0.2mm左右的固化层。
因此成型中通常采用较快的注射速度。
注射行程、多级注射参数在成型中,首先须确定注射行程,理论上,注射行程可按下式计算?s S1=4(CVp+Va)/ρDs2式中?sS1??注射行程 Vp?产品体积ρ?树脂密度 C?型腔数目Va?浇口体积 Ds?螺杆直径在实际生产中,若已知“产品+浇口”的总重量,则可用下式来计算注射行程?sS1=(M/Mmax)?Smax+(5~10)mm式中?s S1---注射行程,mmM?“产品+浇口”总重量,gMmax?注塑机最大注射量,gSmax?注塑机最大注射行程,mm由於浇道系统及模具各部位几何形状不同,为满足产品质量要求,在不同部位对充模熔体的流动状态(主要指流动时压力、速度)有不同要求。
注塑调机口诀

注塑调机口诀注塑调机是指在注塑机生产过程中,通过调整机器参数和工艺流程,使产品在质量、生产效率和工艺稳定性方面达到最佳状态的过程。
正确的注塑调机技术可以提高产品的质量、降低生产成本,并增加生产效率。
下面将介绍一些注塑调机的口诀,帮助操作者更好地进行调机操作。
1. 原料温度掌握在注塑加工中,原料的温度是一个重要的影响因素。
正确掌握原料温度,可以使塑料熔化均匀,进而得到高质量的成品。
因此,在进行注塑调机时,首先要确保原料的温度达到要求,通常可以根据塑料的熔点和工艺要求进行调整。
2. 注射速度调整注射速度是指注射杠杆从后退到前冲的速度,它直接影响塑料进入模腔的速度。
合理的注射速度可以保证塑料在模腔内填充均匀,避免产品出现疏松、短射等缺陷。
在进行注塑调机时,可以通过调整注射速度来达到最佳的产品质量。
3. 压力调整在注塑过程中,注射压力主要是用来克服塑料的黏性阻力,使塑料充填到模腔中。
适当的注射压力可以保证产品充填完整,减少产品变形和缺陷。
在进行注塑调机时,可以通过逐步增加或减小注射压力,观察产品的状态来确定最佳的调机参数。
4. 温度调整温度是影响注塑加工的关键参数之一。
在注塑调机中,要根据塑料的特性和产品要求,合理调整料筒、模具和油路等部位的温度,以保证塑料的熔化和流动性。
温度调整时需要注意适度,避免过高或过低导致产品质量问题。
5. 模具调整模具是注塑加工中的关键部件,直接影响产品的质量和外观。
在进行注塑调机时,要根据产品要求,合理调整模具的开模距离、模具温度和模具尺寸等参数,以保证产品的精度和表面质量。
6. 冷却时间控制冷却时间是指产品在模具中保持一定时间以使其冷却固化的时间。
适当的冷却时间可以保证产品的尺寸精度和外观质量。
在进行注塑调机时,可以通过调整冷却时间来控制产品的质量。
7. 合理调整循环周期循环周期是指注塑机从一次动作到下一次动作的时间,包括模具开合、注射、冷却等过程。
合理调整循环周期可以提高生产效率,降低成本。
注塑技术工艺参数设定技巧

注塑技术工艺参数设定技巧注塑技术是一种常用的塑料加工方法,它广泛应用于各种行业和领域。
在注塑过程中,合理设置工艺参数是确保产品质量和生产效率的重要因素之一、下面将介绍一些注塑技术工艺参数设定的技巧。
首先,合理选择注塑机的注射速度和压力。
注射速度和压力直接影响着塑料的填充时间和填充压力。
一般来说,注射速度应根据产品形状和尺寸的复杂程度来决定,较复杂的产品可以选择较慢的注射速度,以保证塑料充分填充模具腔体;而注射压力应根据塑料的熔融温度和黏度来决定,塑料黏度较高时应适当提高注射压力,以确保塑料能够充分填充模具腔体。
其次,注意控制注塑机的螺杆转速和后压。
螺杆转速的选择应根据注射速度和塑料的熔融特性来决定,一般来说,较慢的螺杆转速有助于减少熔融过程中的剪切热,从而减少塑料的熔体温度。
而后压的设置应根据塑料的收缩特性来决定,塑料收缩较大时,应适当增加后压,以避免产品出现缺陷。
另外,注塑机的保压时间和保压压力也需要合理设定。
保压时间主要取决于塑料的冷却速度,一般来说,较大的产品和较热的模具需要较长的保压时间,以确保塑料充分冷却并保持形状稳定。
而保压压力的选择应根据产品的尺寸和形状来决定,较大的产品通常需要较高的保压压力,以避免产品在冷却过程中产生缺陷。
此外,注塑机的冷却时间和冷却水温度也需要注意。
较复杂的产品和较厚的壁厚通常需要较长的冷却时间,以确保产品的表面完全冷却。
而冷却水温度应根据塑料的特性来确定,一般来说,较高的冷却水温度可以加快产品的冷却速度,但也容易引起产品缺陷。
最后,正确选择模具的设计和制造。
模具的设计和制造对注塑工艺参数的设定至关重要。
合理设计模具的进胶系统、冷却系统和顶出系统,可以提高注射速度和压力的传递效率,加快产品的冷却速度,避免产品变形和缺陷。
总之,注塑技术工艺参数的设定需要综合考虑多个因素,如产品形状和尺寸、塑料特性、模具设计等。
只有合理设置工艺参数,才能保证产品质量和生产效率的提高。
注塑工艺参数及其调整

注塑工艺参数及其调整引言注塑工艺是一种常用的塑料加工方法,它通过将熔融状态的塑料材料注入模具中,经过冷却固化后得到所需的塑料制品。
而注塑工艺参数则是决定注塑过程质量的关键因素之一。
本文将介绍注塑工艺参数的常见类型,并讨论如何进行调整以获得更好的注塑效果。
注塑工艺参数类型在注塑过程中,常见的注塑工艺参数包括注射压力、射胶时间、保压时间、熔融温度、模具温度等。
下面将详细介绍每个参数的作用和调整方法。
1. 注射压力注射压力是指塑料材料进入模具的压力大小。
适当的注射压力能够保证塑料材料充分填充模具腔,在注塑过程中起到很大的作用。
如果注射压力过大,容易导致模具磨损和变形,同时也会增加设备的负荷。
如果注射压力过小,则可能会造成模具腔内塑料充填不完全,产生产品缺陷。
因此,在实际生产中,需要根据具体的塑料材料和产品要求来调整注射压力。
2. 射胶时间射胶时间是指注塑机从塑料材料开始进入模具到完成充填的时间。
合理的射胶时间可以保证塑料材料充分填充模具,在注塑过程中起到决定性的作用。
如果射胶时间过长,可能会导致制品内部产生气泡或短射等缺陷;如果射胶时间过短,则可能会导致产品表面不光滑、短射等问题。
调整射胶时间的方法一般是通过试模进行优化,根据产品的实际情况来确定最佳射胶时间。
3. 保压时间保压时间是指在注射完成后,模具保持一定的压力以保证塑料材料充分冷却和固化的时间。
适当的保压时间可以保证产品的尺寸稳定性和内部结构的完整性。
如果保压时间过长,则会造成生产周期增加和设备负荷加大;如果保压时间过短,则可能会导致产品收缩不充分、变形等问题。
保压时间的调整一般也需要通过试模来确定最佳参数。
4. 熔融温度熔融温度是指将塑料材料加热至熔点的温度。
合适的熔融温度可以保证塑料材料充分熔融,保证注塑过程的顺利进行。
如果熔融温度过高,则可能会导致塑料材料分解、变色等问题;如果熔融温度过低,则可能会导致塑料材料未完全熔融,产生短射等缺陷。
注塑工艺中的四大调试内容

注塑工艺中的四大调试内容在注塑工艺中,调试是非常重要的步骤,它决定了产品的质量和生产的效率。
下面将介绍注塑工艺中的四大调试内容。
一、模具调试模具调试是整个注塑工艺的第一步,它直接影响产品的成型质量和生产的效率。
1. 模具安装:安装模具时需要注意模具的水平度和平行度,以确保模具的稳定性和精度。
2. 模具间隙调整:模具的间隙调整主要是指模具的合模与分模间的间隙,合理的间隙能够保证产品的尺寸精度和外观质量。
3. 模具温度控制:模具的温度对产品的成型质量有重要影响,要根据产品的要求,调整模具的温度,确保产品的尺寸和外观质量稳定。
4. 模具脱模性能调试:模具脱模性能是指产品在脱模过程中是否能够顺利脱离模具,模具的设计和加工质量直接影响产品的脱模性能。
二、注射调试注射调试是指对注射机进行调试,确保注射机能够正常运行,实现产品的正常注射。
1. 控制参数调整:根据产品的材料和工艺要求,对注射机的控制参数进行调整,包括注射压力、注射速度、保压时间等。
2. 换料和清洗:在调试之前,需要对注射机进行换料和清洗,确保新材料没有混入旧材料或杂质。
3. 润滑和保养:定期对注射机进行润滑和保养,确保注射机的运行平稳,减少故障发生的可能。
4. 注射机的故障排除:如果在调试中发现注射机有故障,需要进行及时的故障排除,保证注射机能够正常运行。
三、工艺参数调试工艺参数调试是指根据产品的材料和尺寸要求,对注塑工艺参数进行调整,以达到最佳的成型效果。
1. 注射压力和速度调整:调整注射压力和速度,控制产品的尺寸和外观质量。
2. 注射时间和保压时间调整:调整注射时间和保压时间,确保产品充填充实和保压稳定。
3. 温度控制调整:调整模具温度和熔料温度,确保产品的尺寸和外观质量稳定。
4. 冷却时间调整:调整冷却时间,以确保产品在脱模时不会变形或开裂。
四、成型品质调试成型品质调试是指对产品的尺寸和外观质量进行调试,以确保产品符合要求。
1. 尺寸精度调试:通过调整工艺参数和模具参数,控制产品的尺寸精度,确保产品的尺寸符合要求。
注塑5大要素调机方法及技巧
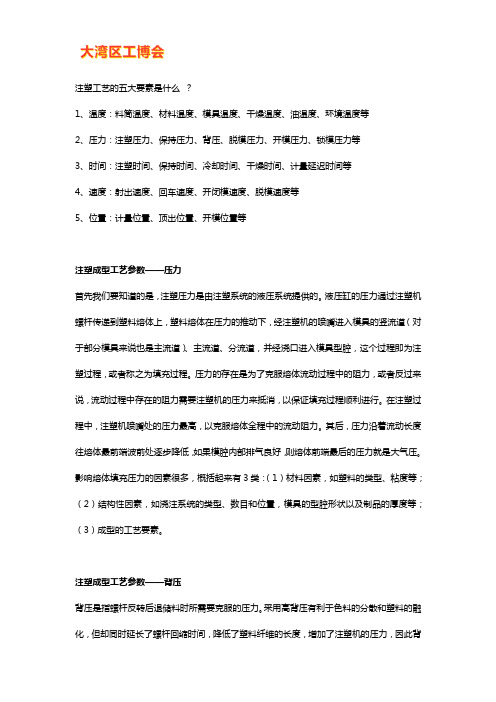
注塑工艺的五大要素是什么?1、温度:料筒温度、材料温度、模具温度、干燥温度、油温度、环境温度等2、压力:注塑压力、保持压力、背压、脱模压力、开模压力、锁模压力等3、时间:注塑时间、保持时间、冷却时间、干燥时间、计量延迟时间等4、速度:射出速度、回车速度、开闭模速度、脱模速度等5、位置:计量位置、顶出位置、开模位置等注塑成型工艺参数——压力首先我们要知道的是,注塑压力是由注塑系统的液压系统提供的。
液压缸的压力通过注塑机螺杆传递到塑料熔体上,塑料熔体在压力的推动下,经注塑机的喷嘴进入模具的竖流道(对于部分模具来说也是主流道)、主流道、分流道,并经浇口进入模具型腔,这个过程即为注塑过程,或者称之为填充过程。
压力的存在是为了克服熔体流动过程中的阻力,或者反过来说,流动过程中存在的阻力需要注塑机的压力来抵消,以保证填充过程顺利进行。
在注塑过程中,注塑机喷嘴处的压力最高,以克服熔体全程中的流动阻力。
其后,压力沿着流动长度往熔体最前端波前处逐步降低,如果模腔内部排气良好,则熔体前端最后的压力就是大气压。
影响熔体填充压力的因素很多,概括起来有3类:(1)材料因素,如塑料的类型、粘度等;(2)结构性因素,如浇注系统的类型、数目和位置,模具的型腔形状以及制品的厚度等;(3)成型的工艺要素。
注塑成型工艺参数——背压背压是指螺杆反转后退储料时所需要克服的压力。
采用高背压有利于色料的分散和塑料的融化,但却同时延长了螺杆回缩时间,降低了塑料纤维的长度,增加了注塑机的压力,因此背压应该低一些,一般不超过注塑压力的20%。
注塑泡沫塑料时,背压应该比气体形成的压力高,否则螺杆会被推出料筒。
有些注塑机可以将背压编程,以补偿熔化期间螺杆长度的缩减,这样会降低输入热量,令温度下降。
不过由于这种变化的结果难以估计,故不易对机器作出相应的调整。
注塑成型工艺参数——温度注塑温度是影响注塑压力的重要因素。
注塑机料筒有5~6个加热段,每种原料都有其合适的加工温度(详细的加工温度可以参阅材料供应商提供的数据)。
注塑机工艺参数及其调整
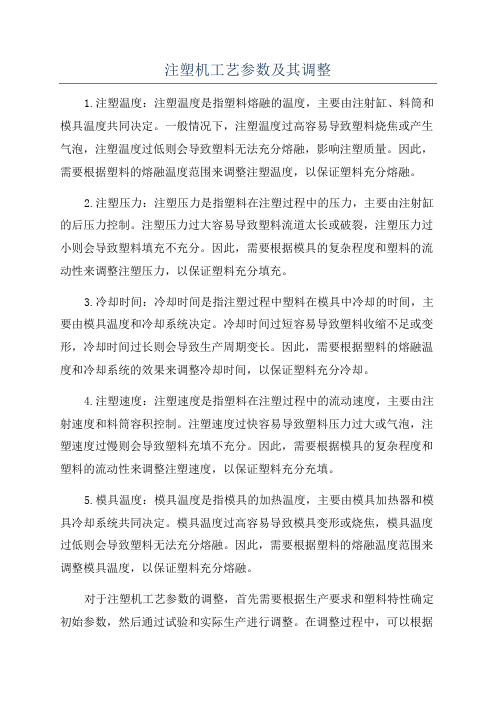
注塑机工艺参数及其调整1.注塑温度:注塑温度是指塑料熔融的温度,主要由注射缸、料筒和模具温度共同决定。
一般情况下,注塑温度过高容易导致塑料烧焦或产生气泡,注塑温度过低则会导致塑料无法充分熔融,影响注塑质量。
因此,需要根据塑料的熔融温度范围来调整注塑温度,以保证塑料充分熔融。
2.注塑压力:注塑压力是指塑料在注塑过程中的压力,主要由注射缸的后压力控制。
注塑压力过大容易导致塑料流道太长或破裂,注塑压力过小则会导致塑料填充不充分。
因此,需要根据模具的复杂程度和塑料的流动性来调整注塑压力,以保证塑料充分填充。
3.冷却时间:冷却时间是指注塑过程中塑料在模具中冷却的时间,主要由模具温度和冷却系统决定。
冷却时间过短容易导致塑料收缩不足或变形,冷却时间过长则会导致生产周期变长。
因此,需要根据塑料的熔融温度和冷却系统的效果来调整冷却时间,以保证塑料充分冷却。
4.注塑速度:注塑速度是指塑料在注塑过程中的流动速度,主要由注射速度和料筒容积控制。
注塑速度过快容易导致塑料压力过大或气泡,注塑速度过慢则会导致塑料充填不充分。
因此,需要根据模具的复杂程度和塑料的流动性来调整注塑速度,以保证塑料充分充填。
5.模具温度:模具温度是指模具的加热温度,主要由模具加热器和模具冷却系统共同决定。
模具温度过高容易导致模具变形或烧焦,模具温度过低则会导致塑料无法充分熔融。
因此,需要根据塑料的熔融温度范围来调整模具温度,以保证塑料充分熔融。
对于注塑机工艺参数的调整,首先需要根据生产要求和塑料特性确定初始参数,然后通过试验和实际生产进行调整。
在调整过程中,可以根据注塑机的控制系统和传感器实时监测关键参数的变化,以及通过对注塑件的检测来判断是否需要进一步调整。
此外,注塑机操作人员需要具备一定的经验和技术知识,以便能够合理调整参数并解决生产中出现的问题。
总结起来,注塑机工艺参数的调整是一个动态的过程,需要根据塑料特性和生产要求进行合理的调整,以获得最佳的注塑效果。
注塑工艺调机技巧
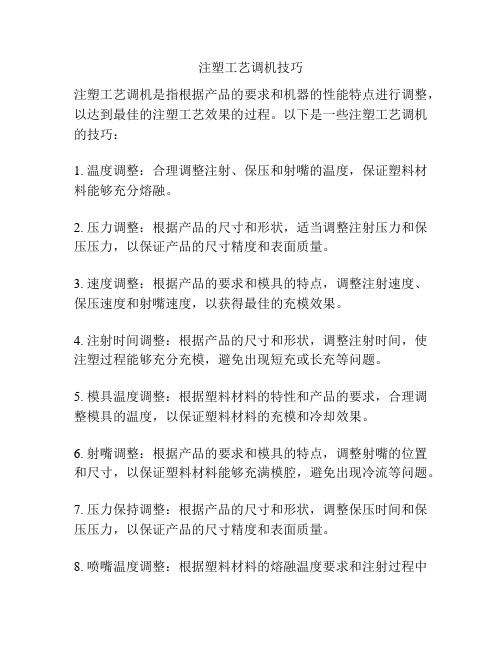
注塑工艺调机技巧
注塑工艺调机是指根据产品的要求和机器的性能特点进行调整,以达到最佳的注塑工艺效果的过程。
以下是一些注塑工艺调机的技巧:
1. 温度调整:合理调整注射、保压和射嘴的温度,保证塑料材料能够充分熔融。
2. 压力调整:根据产品的尺寸和形状,适当调整注射压力和保压压力,以保证产品的尺寸精度和表面质量。
3. 速度调整:根据产品的要求和模具的特点,调整注射速度、保压速度和射嘴速度,以获得最佳的充模效果。
4. 注射时间调整:根据产品的尺寸和形状,调整注射时间,使注塑过程能够充分充模,避免出现短充或长充等问题。
5. 模具温度调整:根据塑料材料的特性和产品的要求,合理调整模具的温度,以保证塑料材料的充模和冷却效果。
6. 射嘴调整:根据产品的要求和模具的特点,调整射嘴的位置和尺寸,以保证塑料材料能够充满模腔,避免出现冷流等问题。
7. 压力保持调整:根据产品的尺寸和形状,调整保压时间和保压压力,以保证产品的尺寸精度和表面质量。
8. 喷嘴温度调整:根据塑料材料的熔融温度要求和注射过程中
的温度变化,调整喷嘴温度,以保证塑料材料的熔融和流动性能。
以上是一些常用的注塑工艺调机技巧,通过合理的调整可以获得最佳的注塑工艺效果,提高产品的质量和产能。
注塑工艺调校及参数管理作业指导书
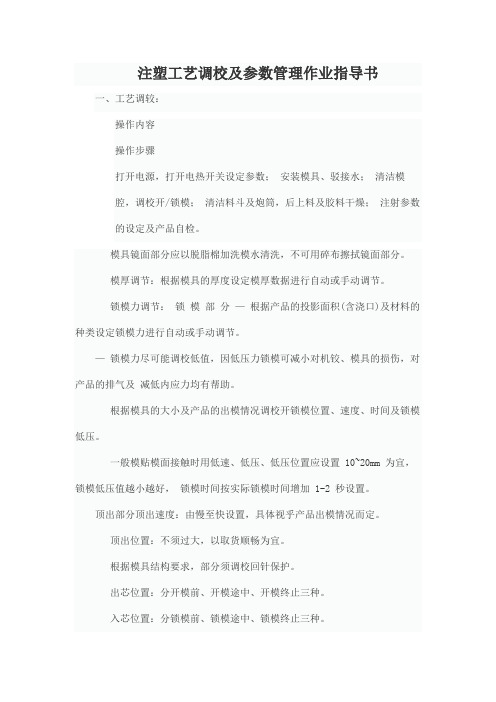
注塑工艺调校及参数管理作业指导书一、工艺调较:操作内容操作步骤打开电源,打开电热开关设定参数;安装模具、驳接水;清洁模腔,调校开/锁模;清洁料斗及炮筒,后上料及胶料干燥;注射参数的设定及产品自检。
模具镜面部分应以脱脂棉加洗模水清洗,不可用碎布擦拭镜面部分。
模厚调节:根据模具的厚度设定模厚数据进行自动或手动调节。
锁模力调节:锁模部分—根据产品的投影面积(含浇口)及材料的种类设定锁模力进行自动或手动调节。
—锁模力尽可能调校低值,因低压力锁模可减小对机铰、模具的损伤,对产品的排气及减低内应力均有帮助。
根据模具的大小及产品的出模情况调校开锁模位置、速度、时间及锁模低压。
一般模贴模面接触时用低速、低压、低压位置应设置 10~20mm 为宜,锁模低压值越小越好,锁模时间按实际锁模时间增加 1-2 秒设置。
顶出部分顶出速度:由慢至快设置,具体视乎产品出模情况而定。
顶出位置:不须过大,以取货顺畅为宜。
根据模具结构要求,部分须调校回针保护。
出芯位置:分开模前、开模途中、开模终止三种。
入芯位置:分锁模前、锁模途中、锁模终止三种。
抽芯分时间及行程控制两种抽芯,具体根据产品生产安全情况选择使用。
料筒温度:—料筒温度根据不同胶料的熔融指数要求设定,以保证胶料塑化良好能顺利充模。
—料筒温度的设置一般由加料口至喷咀段从低到高设置,但喷咀的温度为保温作用,不注塑温度需过高,保证射出顺畅即可。
—鉴别料温是否得当,应在低压低速下对空注射,适当的温度应使喷咀喷出来的料刚劲有力,不带泡、不卷曲,光亮、连续。
胶料干燥温度、时间根据不同种类的胶料及其吸水性而设定。
——版本所有 * 未经书面认可 * 不得复制 * 违者必究——执行工艺员装模工工艺员上料工工艺员确认——装模组长——工艺员—— 普通模具应以碎布擦干净模腔、型芯和顶针上的油污,必要时可使用清洗剂以及风枪等工抽芯动作模具温度的设定应考虑聚合物性质、制品大小形状、模具结构、浇道系统及环境温度等而模温设定。
注塑机调机方法与技巧

注塑机调机方法与技巧注塑机调机是指在开始生产之前,对注塑机进行调整和设置,以确保注塑过程顺利进行。
以下是注塑机调机的方法和技巧:1. 清洁和维护:在调机之前,确保注塑机的各个部件干净并正常工作。
清洁模具和喷嘴,检查模具和机器是否有损坏或磨损的地方,并及时修复。
2. 温度调整:根据注塑材料的要求,调整注塑机的加热温度。
通常需要调整的温度有料筒和喷嘴的温度、模具温度和冷却系统的温度。
确保温度稳定且符合要求。
3. 压力和流量调整:根据注塑产品的尺寸和要求,调整注塑机的注射压力和射胶速度。
通常需要调整的参数有射胶速度、压力和背压等。
确保射胶速度和压力达到注射过程的要求。
4. 注塑时间和压力保持:根据注塑产品的尺寸和要求,调整注塑机的注塑时间和保压时间。
确保注塑时间足够长,以充分填充模具腔。
5. 调整喷嘴位置和喷嘴直径:根据注塑产品的要求,调整喷嘴位置和喷嘴直径,以确保注塑产品的尺寸和形状符合要求。
优化喷嘴位置可提高产品质量和生产效率。
6. 检查冷却系统和模温控制:确保冷却系统正常工作并能有效降低模具温度。
检查冷却水流量和温度,调整冷却时间和温度控制器。
7. 注塑机调整参数记录:在调机过程中,记录和调整各个参数的数值,以备将来参考和调整。
这些参数包括温度、压力、流量、时间、位置等。
8. 运行试验:在调机完成后,进行运行试验,生产少量样品,检查产品质量和机器性能。
根据试验结果调整参数,直到满足质量要求。
以上是注塑机调机的一般方法和技巧,具体操作还需根据具体机型和注塑产品的要求进行调整。
在调机过程中,需要根据实际情况进行调整,并不断优化参数,以确保注塑过程的稳定和产品质量的达标。
注塑工艺调试的操作方法

注塑工艺调试的操作方法注塑工艺调试是指在注塑生产过程中对模具和注塑机进行调试,以确保产品质量和生产效率的过程。
下面我将详细介绍注塑工艺调试的操作方法。
1. 检查模具和注塑机在开始调试之前,首先要检查模具和注塑机是否完好无损。
检查模具是否有损坏、变形或磨损现象,并清洁模具表面。
同时,检查注塑机的各项功能是否正常,确保温度控制系统、液压系统和电气系统等正常工作。
2. 确定注塑工艺参数根据产品要求和注塑材料的性质,确定注塑工艺参数,包括注塑温度、熔融温度、冷却时间、成型周期等。
需要根据模具的结构和产品的壁厚情况合理调整参数。
3. 加热和热流道系统将热流道系统中的热流道板、热流道头安装到模具上,并按照设计要求进行连接。
然后,根据注塑材料的熔融温度和模具的冷却要求,调整热流道系统的温度。
温度过高或过低都可能影响产品的质量。
4. 定位模具将模具安装到注塑机的合适位置,并根据产品的要求进行定位调整。
确保模具和注塑机的对位精度,以免产生不必要的浪费或质量问题。
5. 注塑调试根据注塑机的工作要求和注塑工艺参数,将注塑材料投入到注塑机的料斗中,并通过零件触发开关启动注塑过程。
同时,注意观察注塑机的工作状态,检查是否有异常情况发生。
如果发现有异常,应及时停机检修。
6. 调整注塑工艺参数根据调试的情况和产品质量要求,对注塑工艺参数进行逐步调整。
例如,根据产品的缺陷情况调整注射速度、保压时间和保压压力等参数。
7. 检查产品质量在调试过程中,要不断检查产品的质量。
可以将少量试产出来进行检验,判断产品的表面质量、尺寸精度和物理性能是否符合要求。
如有问题,可以根据检查结果继续调整工艺参数,直到达到要求为止。
8. 记录调试参数在调试过程中,要详细记录每次调整的参数和调试结果,包括工艺参数、产品质量和异常情况等。
这样,在以后的生产中就可以参考这些记录,提高生产效率和产品质量。
9. 培训操作人员在调试完成后,要对操作人员进行培训,使其熟悉操作流程和注意事项。
注塑工艺技术参数的设定方法

注塑工艺技术参数的设定方法一、设定参数的准备1.确认原材料的干燥作业2.确认模具温度、炮筒温度是否正确适当3.开合模及顶针的设定参数、动作4.射出压力:先期以60-70%来进行设定5.保压:先期以40%来进行设定6.射出速度:最高速度50%设定7.螺杆转速:80RPM设定,原料温度高则转速低8.背压:约7kg/cm(油表压力)设定,查看料流状态9.射出时间:按短射板进行设定,不可过长10.冷却时间:先期较长,逐渐减短11.保压切换位置:产品的95%的状态12.计量长度及后抽设定:视原料及成型状态设定二、手动运转参数修正1.作业要领确认各温度设定已经达到正常确认炮筒内可塑化程度锁模高、低压位置观看一批产品的成型,注意冷却时间是否能让产品完全固化开模取出产品,取出是否顺利,有拖伤,拉破,变形等2.参数修正要领:实际位置的考虑温度-压力-射出位置-计量-余料量三、半自动运转参数修正计量行程的修正要领:将射出压力调整到99%,把计量行程缩小直到发生缺胶再延长至发生毛边。
四、充填速度的修正要领:在保压切换前约10mm左右将充填速度设定为做为下一段速度,然后将前一段速度上下调整,找出发生缺胶及毛边速度,找到其中一个点做为最适当的射速。
五、射出压力的修正要领:将射出压力由99%逐渐降低,记录充填时间;以产品状态最接近99%压力时的较低压力为最终压力。
六、保压的修正要领:上下调整保压,找出发生毛边和缩水压力,以其中间值为最适当。
七、射出时间(保压时间)的修正要领:射出时间刚好满足产品95%的状态时,切换保压点切换后保压时间递升,直到产品重量变化逐渐稳定为止。
八、冷却时间的修正要领:降低冷却时间,直到下列条件满足为止1.成品被顶出、夹出、修整、包装不会白化或变形2.模温能平衡而稳定九、溶胶参数的修正要领:依下列原则修正1.背压设为:5-15kg/m³,不发生银线,加热筒不发生过热。
2.调整螺杆转速,使计量时间稍短于冷却时间3.松退行程以流延、流产不产生尾巴,不粘模及成品不发生气痕为原则。
注塑机工艺四大参数设置要点有哪些【大全】

塑料成型工业设备是塑料生产中应用最多的加工机械,塑料成型机械包括注塑机、造粒机、吹塑机、滚塑机等,其产值占塑料机械总产值的80%以上,而注塑机更是塑料加工机械中占比份额最大的品种,产值约占40%。
注塑成型工艺五要素包括:压力、流量、温度、时间、位置,其中压力、流量、温度和时间最为重要,下面我们将重点谈谈注塑成型工艺这四个重要参数设置的要点。
一、压力参数设置在注射动作时,为了克服熔融胶料经过喷嘴、浇道口和模具型腔等处的流动阻力,注射螺杆对熔融胶料必须施加足够的压力才能完成注射。
注塑机主要由注射和锁模两部分组成,注射压力和锁模压力(简称:锁模力)等压力参数是注塑成型工艺的重要技术参数。
1.注射压力注射压力又称射胶压力,是最重要的注塑成型压力参数,它对熔融胶料的流动性能和模具型腔的填充有决定性的作用,对注塑制品尺寸精度、品质质量也有直接影响。
注射压力参数设置根据不同机型而设置。
常见的机型中,一般有一级,二级,三级注射压力。
在具体生产中要根据塑料原料、具体成型产品结构等来合理选取和设置压力参数。
2.锁模力锁模力是从低压锁模开始设置,经过高压锁模,直到锁模终止为止。
锁模动作分为三个阶段,锁模开始时设置快速移动模板所需要的压力参数,以节省循环时间提高效率;锁模动作即将结束时,为了保护模具,清除惯性冲击,降低锁模力参数;当模具完全闭合后,为了达到预设的锁模力,增加锁模力参数的设定值。
3.保压压力保压压力是在注射动作完成后对模具腔内的熔胶料继续进行压实,对模腔内制品冷却成型收缩而出现的空隙进行补缩,并使制品增密。
保压压力可保证模腔压力一定,一直到浇口固化为止。
常设定保压时间来控制保压压力,保压压力决定补缩位移的参量大小,决定制品质量的一致性、均匀性、致密性等重要性能,对于提高制品质量和生产效益有十分重要的意义。
设置保压压力参数的一般原则是保压压力要略小于充模力,浇口保压时间大于固化时间。
4.背压压力背压压力是指螺杆反转后退储料时所需要克服的压力。
注塑中注塑机调机技巧
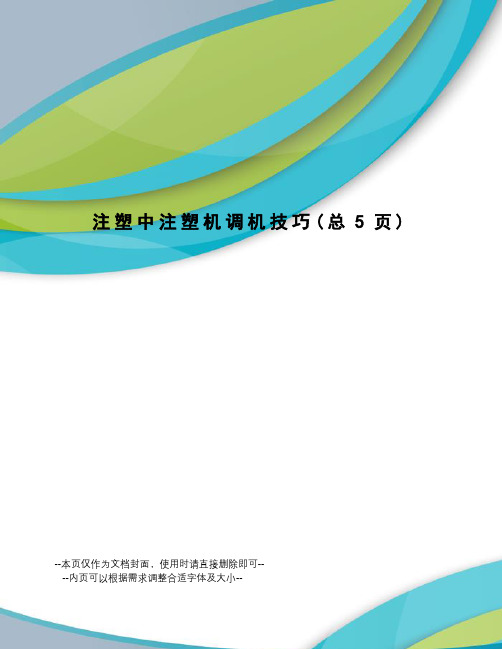
注塑中注塑机调机技巧(总5页)--本页仅作为文档封面,使用时请直接删除即可----内页可以根据需求调整合适字体及大小--注塑成型是一门工程技术,它所涉及的内容是将塑料转变为有用并能保持原有性能的制品。
注射成型的重要工艺条件是影响塑化流动和冷却的温度,压力和相应的各个作用时间。
一、温度控制1、料筒温度:注射模塑过程需要控制的温度有料筒温度,喷嘴温度和模具温度等。
前两种温度主要影响塑料的塑化和流动,而后一种温度主要是影响塑料的流动和冷却。
每一种塑料都具有不同的流动温度,同一种塑料,由于来源或牌号不同,其流动温度及分解温度是有差别的,这是由于平均分子量和分子量分布不同所致,塑料在不同类型的注射机内的塑化过程也是不同的,因而选择料筒温度也不相同。
2、喷嘴温度:喷嘴温度通常是略低于料筒最高温度的,这是为了防止熔料在直通式喷嘴可能发生的"流涎现象"。
喷嘴温度也不能过低,否则将会造成熔料的早凝而将喷嘴堵*,或者由于早凝料注入模腔而影响制品的性能3、模具温度:模具温度对制品的内在性能和表观质量影响很大。
模具温度的高低决定于塑料结晶性的有无、制品的尺寸与结构、性能要求,以及其它工艺条件(熔料温度、注射速度及注射压力、模塑周期等)。
二、压力控制:注塑过程中压力包括塑化压力和注射压力两种,并直接影响塑料的塑化和制品质量。
1、塑化压力:(背压)采用螺杆式注射机时,螺杆顶部熔料在螺杆转动后退时所受到的压力称为塑化压力,亦称背压。
这种压力的大小是可以通过液压系统中的溢流阀来调整的。
在注射中,塑化压力的大小是随螺杆的转速都不变,则增加塑化压力时即会提高熔体的温度,但会减小塑化的速度。
此外,增加塑化压力常能使熔体的温度均匀,色料的混合均匀和排出熔体中的气体。
一般操作中,塑化压力的决定应在保证制品质量优良的前提下越低越好,其具体数值是随所用的塑料的品种而异的,但通常很少超过20公斤/平方厘米。
2、注射压力:在当前生产中,几乎所有的注射机的注射压力都是以柱塞或螺杆顶部对塑料所施的压力(由油路压力换算来的)为准的。
注塑成型参数的调整指南
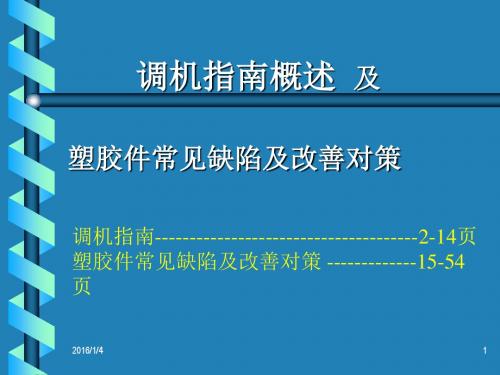
2016/1/4
缺陷: 烧焦
Defect: Diesel effect
烧焦
2016/1/4
29
烧焦改善对策
工艺:
1.降低注射速度及注射压力 2.降低料筒温度 3.降低锁模力
模具:
1.改善模具排气 2.防止包气(entrapped air)
2016/1/4
30
缺陷:走胶
Defect:incom pletely filled parts
10
2016/1/4
调机指南概述
五、速度参数: 5.1 射胶速度(V): 啤机在射胶时螺杆推动熔胶的移动速度。射胶速度主 要受射胶压力、模具型腔对熔胶的阻力、熔胶本身具备的 粘度等因素的影响,射胶压力大于型腔阻力和熔胶粘度时, 设置的射胶速度才能得以充分的发挥。如:S0 S1为V1, 此时熔胶填充型腔,需要低速中压; S1 S2为V2,此时熔 胶填充型腔,需要高速高压; S2 S3为V3 ,熔胶填充胶件 周边,需要中速低压,而且射胶速度随着模腔的填满阻力 的增大而慢慢降低,直到为零。具体各段的射胶速度的设 定,要根据熔胶流经模腔的形状而定。 5.2 螺杆转速(R):
3
2016/1/4
调机指南概述
二、温度参数(T): 啤作生产过程中的温度是根据不同胶料其设置不同, 它可分为如下几种: 2.1 局料温度: 啤作生产时需要将原料中的水份的含量局干到一定百 分比以下,称之为局料。因为水份含量高过一定比例的原 料会引起气花、剥层等缺陷。 2.2 炮筒温度: 炮筒由料斗到炮咀可分为:输送段、压缩段、计量段, 每段的加热温度统称为炮筒温度。炮筒温度由低到高。另 炮咀温度通常略低于计量末端之温度。 2.3 模具温度:
注塑工艺调试(3篇)

第1篇摘要:注塑工艺调试是注塑成型过程中的关键环节,它直接影响到注塑产品的质量和生产效率。
本文从注塑工艺调试的基本概念、影响因素、调试步骤以及常见问题及解决方法等方面进行了详细阐述,旨在为注塑工艺调试提供参考。
一、引言注塑成型是一种将热塑性塑料或热固性塑料在高温、高压条件下,注入模具中冷却固化,形成所需形状的塑料制品的成型方法。
注塑工艺调试是指通过调整注塑机及其相关设备的参数,使注塑过程稳定、高效,并满足产品质量要求的过程。
本文将对注塑工艺调试进行详细分析。
二、注塑工艺调试的基本概念1. 注塑工艺:指在一定的温度、压力和速度条件下,将塑料熔体注入模具中,经过冷却、固化等过程,形成所需形状的塑料制品的整个过程。
2. 注塑工艺调试:指在注塑生产过程中,通过调整注塑机及其相关设备的参数,使注塑过程稳定、高效,并满足产品质量要求的过程。
三、注塑工艺调试的影响因素1. 塑料材料:不同塑料材料的熔融温度、流动性、热稳定性等特性不同,对注塑工艺调试产生较大影响。
2. 模具设计:模具的结构、尺寸、冷却系统等设计对注塑工艺调试有直接影响。
3. 注塑机参数:注塑机的注射压力、注射速度、锁模力等参数对注塑工艺调试有较大影响。
4. 生产环境:生产环境中的温度、湿度、尘埃等对注塑工艺调试产生一定影响。
四、注塑工艺调试步骤1. 熔融温度调试:根据塑料材料的熔融温度,调整注塑机的加热温度,使塑料熔体达到最佳流动性。
2. 注射压力调试:根据模具结构、塑料材料特性等因素,调整注塑机的注射压力,确保塑料熔体在模具内充满均匀。
3. 注射速度调试:根据塑料材料的流动性、模具结构等因素,调整注塑机的注射速度,使塑料熔体在模具内均匀分布。
4. 模具温度调试:根据塑料材料的热稳定性、模具结构等因素,调整模具的冷却水温度,使塑料熔体在模具内快速冷却固化。
5. 模具锁模力调试:根据模具结构、塑料材料特性等因素,调整注塑机的锁模力,确保模具在注塑过程中稳定可靠。
如何调较注塑工艺参数(温度、压力、速度、位置)?
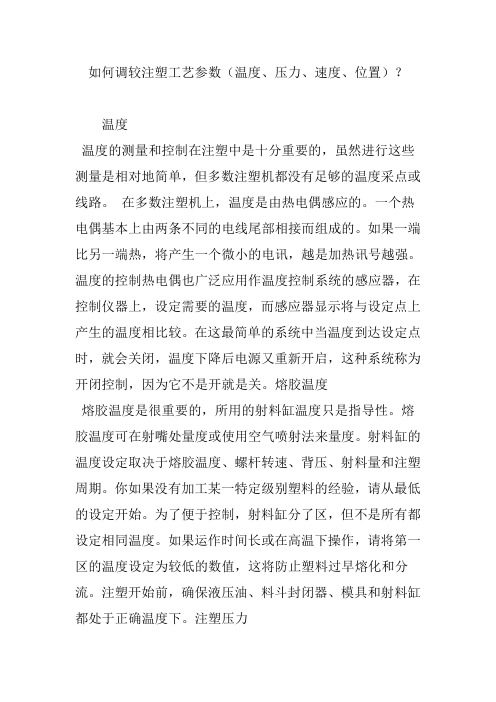
如何调较注塑工艺参数(温度、压力、速度、位置)?温度温度的测量和控制在注塑中是十分重要的,虽然进行这些测量是相对地简单,但多数注塑机都没有足够的温度采点或线路。
在多数注塑机上,温度是由热电偶感应的。
一个热电偶基本上由两条不同的电线尾部相接而组成的。
如果一端比另一端热,将产生一个微小的电讯,越是加热讯号越强。
温度的控制热电偶也广泛应用作温度控制系统的感应器,在控制仪器上,设定需要的温度,而感应器显示将与设定点上产生的温度相比较。
在这最简单的系统中当温度到达设定点时,就会关闭,温度下降后电源又重新开启,这种系统称为开闭控制,因为它不是开就是关。
熔胶温度熔胶温度是很重要的,所用的射料缸温度只是指导性。
熔胶温度可在射嘴处量度或使用空气喷射法来量度。
射料缸的温度设定取决于熔胶温度、螺杆转速、背压、射料量和注塑周期。
你如果没有加工某一特定级别塑料的经验,请从最低的设定开始。
为了便于控制,射料缸分了区,但不是所有都设定相同温度。
如果运作时间长或在高温下操作,请将第一区的温度设定为较低的数值,这将防止塑料过早熔化和分流。
注塑开始前,确保液压油、料斗封闭器、模具和射料缸都处于正确温度下。
注塑压力这是引起塑料流动的压力,可以用在射嘴或液压线上的传感器来测量。
它没有固定的数值,而模具填充越困难,注塑压力也增大,注塑线压力和注塑压力是有直接关系。
第一阶段压力和第二阶段压力在注塑周期的填充阶段中,可能需要采用高射压,以维持注塑速度于要求水平。
模具经填充后便不再需要高压力。
不过在注塑一些半结晶性热塑性塑料(如PA及POM)时,由于压力骤变,会使结构恶化,所以有时无须使用次阶段压力。
?锁模压力为了对抗注射压力,必须使用锁模压力,不要自动地选择可供使用的最大数值,而要考虑投影面积,计算一个合适的数值。
注塑件的投影面积,是从锁模力的应用方向看到的最大面积。
对大多数注塑情况来说,它约为每平方英寸2吨,或每平方米31兆牛顿,然而这只是个低数值,而且应当作为一个很粗略的经验值,因为,一旦注塑件有任何的深度,那么侧壁便必须考虑。
注塑机工艺参数设置
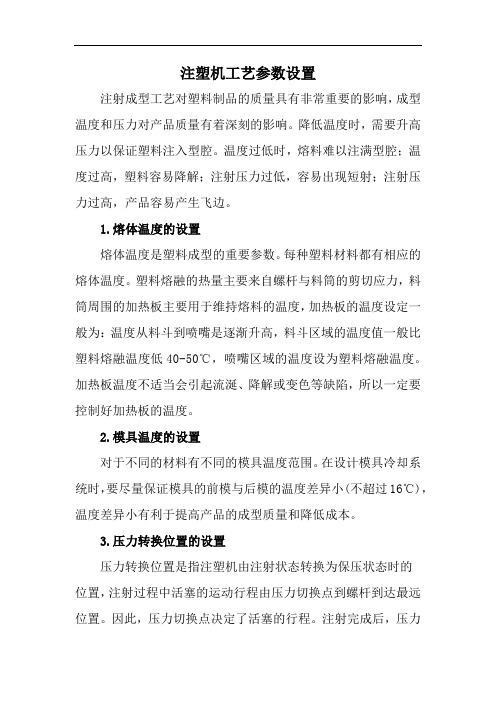
注塑机工艺参数设置注射成型工艺对塑料制品的质量具有非常重要的影响,成型温度和压力对产品质量有着深刻的影响。
降低温度时,需要升高压力以保证塑料注入型腔。
温度过低时,熔料难以注满型腔;温度过高,塑料容易降解;注射压力过低,容易出现短射;注射压力过高,产品容易产生飞边。
1.熔体温度的设置熔体温度是塑料成型的重要参数。
每种塑料材料都有相应的熔体温度。
塑料熔融的热量主要来自螺杆与料筒的剪切应力,料筒周围的加热板主要用于维持熔料的温度,加热板的温度设定一般为:温度从料斗到喷嘴是逐渐升高,料斗区域的温度值一般比塑料熔融温度低40-50℃,喷嘴区域的温度设为塑料熔融温度。
加热板温度不适当会引起流涎、降解或变色等缺陷,所以一定要控制好加热板的温度。
2.模具温度的设置对于不同的材料有不同的模具温度范围。
在设计模具冷却系统时,要尽量保证模具的前模与后模的温度差异小(不超过16℃),温度差异小有利于提高产品的成型质量和降低成本。
3.压力转换位置的设置压力转换位置是指注塑机由注射状态转换为保压状态时的位置,注射过程中活塞的运动行程由压力切换点到螺杆到达最远位置。
因此,压力切换点决定了活塞的行程。
注射完成后,压力要保持一段时间不变,以填充因冷却收缩减小的空间。
如果保压不充分,容易出现缩痕。
4.螺杆旋转速率的设置理想的螺杆旋转速率是指在注射循环最后阶段塑化完全而且不延长成型周期时的速率。
5.背压的设置背压推荐值为5-10MPa,背压过低容易导致制品不稳定;增加背压会提高摩擦力对于塑化的影响,减少塑化时间。
6. 最大注射压力的设置注射压力是熔料在螺杆前端的压力,注射压力应尽量低,以减少制品的内应力。
在注塑机中,压力设定值为最大注射压力,以保证注射压力不限制注射速率。
7.保压压力值的设置利用分析软件可以预测适当的保压压力,这个数值可以保证制品最小的缩痕、没有飞边和脱模问题。
设置合适的最低保压压力,可以减小制品内部的残余应力,从而减小制品的变形,并且可以节省原料,降低成本。
注塑问题工艺调节方法
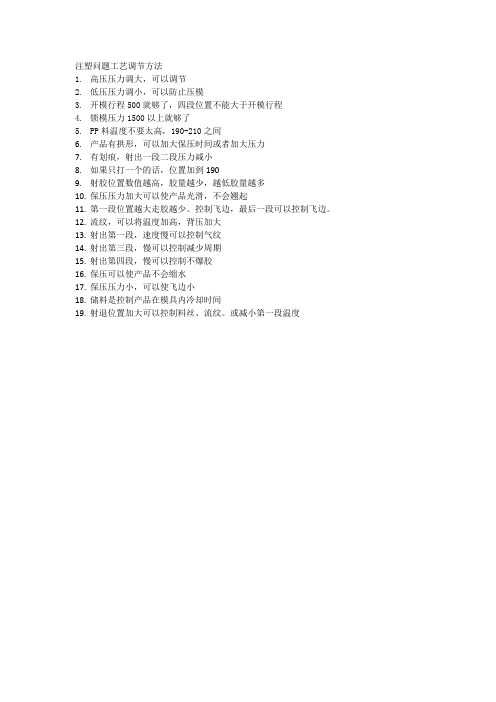
注塑问题工艺调节方法
1.高压压力调大,可以调节
2.低压压力调小,可以防止压模
3.开模行程500就够了,四段位置不能大于开模行程
4.锁模压力1500以上就够了
5.PP料温度不要太高,190-210之间
6.产品有拱形,可以加大保压时间或者加大压力
7.有划痕,射出一段二段压力减小
8.如果只打一个的话,位置加到190
9.射胶位置数值越高,胶量越少,越低胶量越多
10.保压压力加大可以使产品光滑,不会翘起
11.第一段位置越大走胶越少。
控制飞边,最后一段可以控制飞边。
12.流纹,可以将温度加高,背压加大
13.射出第一段,速度慢可以控制气纹
14.射出第三段,慢可以控制减少周期
15.射出第四段,慢可以控制不爆胶
16.保压可以使产品不会缩水
17.保压压力小,可以使飞边小
18.储料是控制产品在模具内冷却时间
19.射退位置加大可以控制料丝、流纹。
或减小第一段温度。
- 1、下载文档前请自行甄别文档内容的完整性,平台不提供额外的编辑、内容补充、找答案等附加服务。
- 2、"仅部分预览"的文档,不可在线预览部分如存在完整性等问题,可反馈申请退款(可完整预览的文档不适用该条件!)。
- 3、如文档侵犯您的权益,请联系客服反馈,我们会尽快为您处理(人工客服工作时间:9:00-18:30)。
如何调较注塑工艺参数(温度、压力、速度、位置)?温度温度的测量和控制在注塑中是十分重要的,虽然进行这些测量是相对地简单,但多数注塑机都没有足够的温度采点或线路。
在多数注塑机上,温度是由热电偶感应的。
一个热电偶基本上由两条不同的电线尾部相接而组成的。
如果一端比另一端热,将产生一个微小的电讯,越是加热讯号越强。
温度的控制热电偶也广泛应用作温度控制系统的感应器,在控制仪器上,设定需要的温度,而感应器显示将与设定点上产生的温度相比较。
在这最简单的系统中当温度到达设定点时,就会关闭,温度下降后电源又重新开启,这种系统称为开闭控制,因为它不是开就是关。
熔胶温度熔胶温度是很重要的,所用的射料缸温度只是指导性。
熔胶温度可在射嘴处量度或使用空气喷射法来量度。
射料缸的温度设定取决于熔胶温度、螺杆转速、背压、射料量和注塑周期。
你如果没有加工某一特定级别塑料的经验,请从最低的设定开始。
为了便于控制,射料缸分了区,但不是所有都设定相同温度。
如果运作时间长或在高温下操作,请将第一区的温度设定为较低的数值,这将防止塑料过早熔化和分流。
注塑开始前,确保液压油、料斗封闭器、模具和射料缸都处于正确温度下。
注塑压力这是引起塑料流动的压力,可以用在射嘴或液压线上的传感器来测量。
它没有固定的数值,而模具填充越困难,注塑压力也增大,注塑线压力和注塑压力是有直接关系。
第一阶段压力和第二阶段压力在注塑周期的填充阶段中,可能需要采用高射压,以维持注塑速度于要求水平。
模具经填充后便不再需要高压力。
不过在注塑一些半结晶性热塑性塑料(如PA及POM)时,由于压力骤变,会使结构恶化,所以有时无须使用次阶段压力。
?锁模压力为了对抗注射压力,必须使用锁模压力,不要自动地选择可供使用的最大数值,而要考虑投影面积,计算一个合适的数值。
注塑件的投影面积,是从锁模力的应用方向看到的最大面积。
对大多数注塑情况来说,它约为每平方英寸2吨,或每平方米31兆牛顿,然而这只是个低数值,而且应当作为一个很粗略的经验值,因为,一旦注塑件有任何的深度,那么侧壁便必须考虑。
背压这是螺杆后退前所须要产生及超越的压力,采用高背压虽有利于色料散布均匀及塑料熔化,但却同时延长了螺杆回位时间,减低填充塑料所含纤维的长度,并增加了注塑机的应力。
故背压越低越好,在任何情况下都不能超过注塑机注塑压力(最高定额)的20%。
射嘴压力射嘴压力是射嘴里面的压力。
它大约就是引起塑料流动的压力。
它没有因定的数值,而是随模具填充的难度加大而增高。
射嘴压力、线压力和注塑压力之间有直接的关系。
在螺旋式注塑机上,射嘴压力大约比注射压力少大约百分之十左右。
而在活塞式注塑机时压力损失可达百分之十左右。
而在活塞式注塑机时压力损失可达到百分之五十。
注塑速度这是指螺杆作为冲头时,模具的填充速度。
注塑薄壁制品时,必须采用高射速,以便于熔胶未凝固时完全填充模具,生产较为光滑的表面。
填充时使用一系列程序的射速,壁免产生喷射或困气等缺陷。
注塑可在开环式或闭环式控制系统下进行。
无论采用那种注射速度,都必须将速度值连同注射时间记录于记录表上,注塑时间指模具达到预定的首阶段射压所须的时间,乃螺杆推进时间的一部分。
模具排气由于快速填充模具的缘故,模具必须让气体排出,多数情况下这气体只是模腔中的空气。
如果空气不能排出,它会被熔融压缩,使温度上升将引起塑料燃烧。
排气位须设于夹水纹及最终注塑部分附近。
一般排气位为6至13毫米宽,0.01至0.03毫米深的槽,通常设于其中一个半模的分模面处。
保压在注塑周期的填充阶段中,可能需要采用高射压,以维持注塑速度于要求的水平。
模具填充后,就进入保持阶段,这时螺杆(起冲压器作用)推进额外的塑料以补偿塑料收缩。
这可在较低或同样高的压力下完成。
通常若首阶段采用高压,次阶段便采用较低压,不过,在注塑一些半结晶性热塑性塑料(如PA及POM时),由于压力骤变,会使结晶体结构恶化,所以有时无需使用次阶段压力。
再生塑料的使用许多注塑机使用新料和回用再生塑料(即通常所说的水口料)的混合物。
令人惊奇的是使用再生塑料可以改善注塑机的表现,即它的使用产生了更一致的注塑件,但值得注意的是,再生料在使用前最好要先除去粉尘,以免引起塑料进料量的差异而导致注塑件颜色分布偏差。
再生塑料的确切使用比例要根据实验的数来确定,这个数据必须是在不影响注塑件的物理性质的前提下得来的,一般的经验值是在15%至25%之间。
品质控制注塑件最终的特点(重量和大小)与生产条件:如垫料大小、注塑压力和流量之间在紧密发联系。
这表示在许多情况下,有可能在没有真正对注塑釿进行任何测量之前就可以检查到注塑件是否令人满意。
在每次注塑中,对选择的参数进行量并比较设定或储的数值。
只要测量值在预先选择的范围,控制系统就判定该注塑件可以接受。
如果测量超出设定的限制,该注塑件将会被废弃,或者,如果只是超出了一点,就要停下来等有资格人士第二次检测。
现在的注塑机配备了录影机、电脑系统,这样在注塑时,每一个塑件都与储存的要求映像相比较。
每一个注塑件都要和标准注塑件的尺寸和视觉上的缺陷相比较。
记录注塑条件永远不可忘记注塑的目的是在特定时间内按指定的成本生产符合品质要求的注塑件。
要做到这点,基本是做准确的记录。
在许多注塑机上按钮就可以做到这点。
若没有按钮,应该完成适当的记录单并保留注塑样本,作为将来的参考。
停机最重要的是采取一个合理的停机过程,这样便可节省大量时间和金钱。
如果你要停机,正例如燃烧塑料,那么便没有需要泻出塑料。
你可能会节省完全关闭和清洁注塑机的费用。
暂时的停顿若注塑机暂停运作,更须多次将余胶喷清或让别的塑料来通过注塑机清洗射料缸的剩余塑料。
遇上塑料退色,喷清的次数就要增加。
进行轻微修理时,射料缸的加热器须调校至最低值,以尽量减低热分解的可能。
在更现代化的注塑机上该过程可能会自动启动。
整晚的停顿注塑热塑性塑料(如PS)前,如已预先停机一晚,就只须关闭底部的滑板及射料缸加热器,将射料缸喷射干净。
射嘴完全清洁,尽量把射料缸高度冷却,等注塑机冷却后关闭所有装备,注塑机便可准备好再次加热。
热敏感性塑料若塑料在注塑机内分解可燃烧,最终变色,使注塑件变成废件。
遇此情形,便须完全关闭注塑机,喷清干净,预防方法是用一种热稳定性较高的塑料喷清遇热敏感的塑料,这样便能抵常驻随时后再加热。
为了应付塑料氧化的问题,操作者可以在射料缸中充满塑料,如PE。
塑胶制品成型时变形重要原因:成品肉厚不同,且差距过大,收缩率大小不同而产生。
射压传达不均匀,因密度高低而产生(浇口位置及型式)。
模温分布不均匀,冷却系统近浇口处要较冷,反之。
分子配向差距过大。
后结晶(结晶性塑胶)。
内应力过高。
锁模压力:锁模压力必须大于塑料射入模内之总压力,若过低塑料即可能由分模面处溢出。
压力过高又会损耗机器,模具及浪费电力。
故适当的锁模力是以成品射入模内分模面不出毛边为原则。
螺杆功能:螺杆对原料有输送、混练、排气、除湿、熔解及计量等功能,塑胶原料熔融时所需之热量有百分之七十是来自螺杆旋转时发生之磨擦热,有百分之三十是来自电热片补充之热量。
低黏度、小螺杆、熔胶转速要加快。
高黏度、大螺杆熔胶转速要放慢。
复合材料需放慢转速。
射出速度:射出速度之快慢,主要决定原料在模具之浇道中及模穴内流动之状况。
速度太快会产生毛头过饱、烧焦及粘模,太慢易造成短射缩水,结合线明显,须依实际需要分段调整。
射出压力:射出压力于射出速度有部分共同之影响,都是决定在模具内原料如何能均匀的,彻底的适量的流满各角落,压力太低会产生短射缩水,压力太高会产生毛边、粘模、内应力残留日后变形、破裂、易损坏模具,机台等。
原料温度:成型时使原料恰当熔融所需之热量及温度,因每种原料之熔融温度及比热不同而不同。
温度过低原料熔融不均则短射,色泽不均,成品内应力高。
加温过高或过久,则因流动性太好易使成品产生毛头,又因冷却温度差异使成品主生缩水,严重时则使原料分解变质甚至烧焦。
模具温度:原料将大量之热带入模具,而成品则将部分之热又散入空气中因此欲使模具保持某一不变之温度,在模具内通冷冻水、冷水、热水、热油或加电热棒,以使进出模具内之热平衡而能保持某一不变之温度。
模温太低,成品易产生短射,表面粗糙,内应力高,粘模。
模温太高,成品易产生收缩下陷、周期延长,故冷却时间、模温高低可依经验来设定。
温度控制的必要性:对成形性及成形效率而言模温高流动性佳,需要加长成品冷却时间。
模温低缩短固化时间,提高效率。
对成形品物性而言模温高结晶度高,表面性质较佳模温低材料迅速固化,成形压力大,造成残留应力。
结晶化度不均匀,易引起后结晶、尺寸不安定。
对防止成品变形而言冷却不足发生收缩下陷。
冷却不均收缩不平均,引起翘曲、扭曲。
肉厚不同、密度也会不同,收缩也会不同。
模温控制型式1、冷冻机8 ℃-15 ℃之间冷却,注意冒汗生锈之问题。
2、水温机96 ℃以内,直接补充水源。
3、油温机150 ℃以内,油温循环间接用水冷却。
4、电热片、棒200 ℃以内,小心漏电。
模具温度对注塑成型的影响:模具温度是注塑成型中最要的变量----无论注塑何种塑料,必须保证形成模具表面基本的湿润。
一个热的模具表面使塑料表面长时间保持液态,足以在型腔内形成压力。
如果型腔填满而且在冻结的表皮硬化之前,型腔压力可将柔软的塑料压在金属上,那么型腔表面的复制就高。
另一方面,如果在低压下进入型腔的塑料暂停了,不论时间多短,那么它与金属的轻微接触都会造成污点,有时被称为浇口污斑。
对于每一种塑料和塑胶件,存在一个模具表面温度的极限,超过这个极限就可能出现一种或更多不良影响(例如:组件可以溢出毛边)。
模具温度更高意味着流动阻力更小。
在许多注塑机上,这自然就意味着更快流过浇口和型腔,因为所用的注塑流动控制阀并不纠正这个改变,填充更快会在浇道和型腔内引起更高的有效压力。
可能造成溢料毛边。
由于更热的模型并不冻结那些在高压形成之前进入溢料边区域的塑料,熔料可在顶出杆周围溢料毛边并溢出到分割线间隙内。
这表明需要有良好的注射速率控制,而一些现代化的流动控制编程器也确实可以做到这点。
通常,模具温度的升高会减少塑料在型腔内有冷凝层,使熔融材料在型腔内更易于流动,从而获得更大的零件重量和更好的表面质量。
同时,模具温度的提高还会使零件张力强度增加。
模具的保温方法:许多模具,尤其是工程用的热塑性塑料,在相对较高的温度下运行,如80摄氏度或176华氏度。
如果模具没有保温,流失到空气和注塑机上的热量可以很容易地与射料缸流失的一样多。
所以要将模具一飞机骨架板隔热,如果可能,将模具的表面隔热热。
如果考虑用热流道模具,尝试减少热流道部分和冷却了的注塑件之间的热量交换。
这样的方法可以减少能量流失和预热时间。
内应力的产生及解决对策:一般射出成品定型前,存在成品内部的压力约为300kg/cm2-500kg/cm2之间,如因调整不当造成射胶压力过高,射入模内虽经过浇道、浇口、成品之间的阻力以及成品逐渐冷却,压力逐渐之降低,而存在成品内部进胶口及远端之压力不同,成品经过一段时日于热接触,内应力渐渐释放出来而造成变形或破裂。