RH真空精炼原理及工艺简介
rh真空精炼的设备与工艺
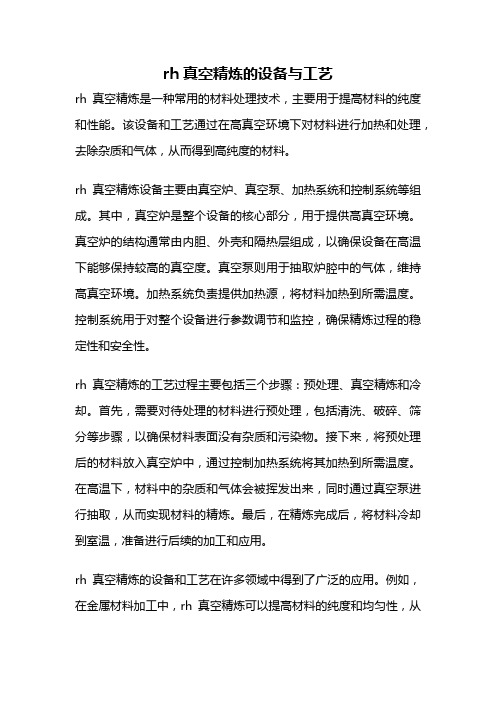
rh真空精炼的设备与工艺rh真空精炼是一种常用的材料处理技术,主要用于提高材料的纯度和性能。
该设备和工艺通过在高真空环境下对材料进行加热和处理,去除杂质和气体,从而得到高纯度的材料。
rh真空精炼设备主要由真空炉、真空泵、加热系统和控制系统等组成。
其中,真空炉是整个设备的核心部分,用于提供高真空环境。
真空炉的结构通常由内胆、外壳和隔热层组成,以确保设备在高温下能够保持较高的真空度。
真空泵则用于抽取炉腔中的气体,维持高真空环境。
加热系统负责提供加热源,将材料加热到所需温度。
控制系统用于对整个设备进行参数调节和监控,确保精炼过程的稳定性和安全性。
rh真空精炼的工艺过程主要包括三个步骤:预处理、真空精炼和冷却。
首先,需要对待处理的材料进行预处理,包括清洗、破碎、筛分等步骤,以确保材料表面没有杂质和污染物。
接下来,将预处理后的材料放入真空炉中,通过控制加热系统将其加热到所需温度。
在高温下,材料中的杂质和气体会被挥发出来,同时通过真空泵进行抽取,从而实现材料的精炼。
最后,在精炼完成后,将材料冷却到室温,准备进行后续的加工和应用。
rh真空精炼的设备和工艺在许多领域中得到了广泛的应用。
例如,在金属材料加工中,rh真空精炼可以提高材料的纯度和均匀性,从而提高材料的力学性能和耐腐蚀性能。
在半导体行业中,rh真空精炼可以去除材料中的杂质和气体,提高半导体材料的电子性能和可靠性。
此外,rh真空精炼还可以应用于陶瓷材料、玻璃材料、化工原料等领域,以提高材料的质量和性能。
rh真空精炼设备和工艺是一种重要的材料处理技术,通过在高真空环境下对材料进行加热和处理,可以提高材料的纯度和性能。
该技术在许多领域中得到广泛应用,对提高材料的质量和性能具有重要意义。
随着科学技术的不断进步,rh真空精炼设备和工艺将会得到进一步的改进和应用,为材料科学和工程领域的发展做出更大的贡献。
RH精炼炉工艺

RH精炼炉工艺摘要:介绍了RH的发展历史,对RH中最关键的真空系统原理进行了说明,介绍了莱钢RH的功能、设备及工艺,针对莱钢情况,对莱钢品种开发进行了探讨。
关键词: RH 原理工艺品种1 RH的历史与发展RH精炼全称为RH真空循环脱气精炼法。
于1959年由德国人发明,其中RH为当时德国采用RH精炼技术的两个厂家的第一个字母。
真空技术在炼钢上开始应用起始于1952年,当时人们在生产含硅量在2%左右的硅钢时在浇注过程中经常出现冒渣现象,经过各种试验,终于发现钢水中的氢和氮是产生冒渣无法浇注或轧制后产生废品的主要原因,随之各种真空精炼技术开始出现,如真空铸锭法、钢包滴流脱气法、钢包脱气法等,从而开创了工业规模的钢水真空处理方法,特别是蒸汽喷射泵的出现,更是加速了真空炼钢技术的发展。
随着真空炼钢技术的开发与发展,最终RH和VD因为处理时间短、成本低、可以大量处理钢水等优点而成为真空炼钢技术的主流,70年代开始随着全连铸车间的出现,RH因为采用钢水在真空槽环流的技术从而达到处理时间短、效率高、能够与转炉连铸匹配的优点而被转炉工序大量采用。
RH从开始出现到现在40多年来,有多项关键性技术的出现,从而加速了RH精炼技术的发展。
表1为40多年来RH技术的发展情况。
表1 RH技术发展情况2 RH系统概述RH系统设备是一种用于生产优质钢的钢水二次精炼工艺装备。
整个钢水冶金反应是在砌有耐火衬的真空槽内进行的。
真空槽的下部是两个带耐火衬的浸渍管,上部装有热弯管。
被抽气体由热弯管经气体冷却器至真空泵系统排到厂房外。
钢水处理前,先将浸渍管浸入待处理的钢包钢水中。
当真空槽抽真空时,钢水表面的大气压力迫使钢水从浸渍管流入真空槽内(真空槽内大约0.67mbar时可使钢水上升1.48m高度)。
与真空槽连通的两个浸渍管,一个为上升管,一个为下降管。
由于上升管不断向钢液吹入氩气,相对没有吹氩的下降管产生了一个较高的静压差,使钢水从上升管进入并通过真空槽下部流向下降管,如此不断循环反复。
RH资料

RH真空罐有两个咀,其中一个内部布有吹气管,处理钢液时RH真空罐的两个咀插入钢包钢液,开始抽真空,上升管钢液进入,这是由于上升管内往钢液中吹气,钢液密度较小,下降管则是钢液密度比上升管内小,从而形成循环,钢液可持续循环进行。
冶金功能:脱气(氮气,氢气),脱碳和脱氧(真空下降低一氧化碳分压,使脱碳反应持续进行到新的平衡,碳可降到20PPM以下),合金化(真空室上部有加料管道,料仓内的合金通过减压阀进入真空室),调整温度(化学升温和降温,一般是加铝后吹氧升温,加低碳钢小料降温),微调成分,终脱氧(脱氧剂可以是铝,也可以是硅锰等)。
RH真空处理一般脱气处理称为轻处理,而深脱碳合金化等处理称为本处理。
钢铁厂RH精炼真空炉,可处理什么规格的钢水?或要求什么条件RH精炼是处理高精尖板带材的炉外精炼工序,由于精炼过程中的温降、电耗、耐材消耗、节奏等,会增加成本,所以,一般材质的钢材不用,只用LF、CAS-OB 等就可以啦。
经过RH精炼处理后的钢水H含量、夹杂物等明显降低,性能明显提高。
但是,要求转炉工序提高出钢温度20度左右。
网上有的资料我都有但没有生产实践的资料------那就要生产一线去,积累经验,实际操作,总结经验,提高水平,做一个真正的原理很简单钢水经由上升管进入真空室被脱气再由下降管流回钢包如此循环,直至达到要求止把这个图看明白就可以了RH多功能真空精炼技术开发RH真空精炼技术产生于50年代末期。
在近30年的时间里,RH的功能和精炼的钢种范围不断扩大,发展成为多功能真空精炼技术,在炉外精炼中占主导地位。
至今,全世界已有100余台。
在西欧、日本、美国得到普遍推广,仅日本就有40余台,1989年日本转炉钢真空精炼率达56.5%,新日铁大分厂、川崎制铁水岛厂已全量进行RH真空精炼。
实践证明,RH真空精炼技术是提高产品质量,降低成本,扩大品种,提高炼钢生产能力,保证连铸顺行,实现全连铸,优化炼钢生产工艺的重要手段。
炉外精炼-RH

炉外精炼的基本原理:(1)吹氩的基本原理:氩气是一种惰性气体,从钢包底部吹入钢液中,形成大量小气泡,其气泡对钢液中的有害气体来说,相当于一个真空室,使钢中[H][N]进入气泡,使其含量降低,并可进一步除去钢中的[O],同时,氩气气泡在钢液中上沲而引起钢液强烈搅拌,提供了气相成核和夹杂物颗粒碰撞的机会,有利于气体和夹杂物的排除,并使钢液的温度和成分均匀。
(2)真空脱气的原理:钢中气体的溶解度与金属液上该气体分压的平方根成正比,只要降低该气体的分压力,则溶解在钢液中气体的含量随着降低。
(3)LF炉脱氧和脱硫的原理:炉外精炼的任务:炉外精炼是把由炼钢炉初炼的钢水倒入钢包或专用容器内进一步精炼的一种方法,即把一步炼钢法变为二步炼钢法。
炉外精炼可以完成下列任务:(1)降低钢中的硫、氧、氢、氮和非金属夹杂物含量,改变夹杂物形态,以提高钢的纯净度,改善钢的机械性能;(2)深脱碳,在特定条件下把碳降到极低含量,满足低碳和超低碳钢的要求;(3)微调合金成分,将成分控制在很窄的范围内,并使其分布均匀,降低合金消耗,提高合金元素收得率;将钢水温度调整到浇铸所需要的范围内,减少包内钢水的温度梯度。
RH真空循环脱气法LF具有加热和搅拌功能的钢包精炼法处理过程:用钢包车将钢包送入处理位,使真空室下降或使钢包提升,以便使吸嘴浸入钢包内的钢液以下500mm。
然后启动真空泵。
由于真空室内压力下降,钢包内钢水被吸入真空室中。
由于吸嘴中的一个喷入氩气,另一个没有,钢水便开始反复循环。
这时就可采取各种处理措施,例如脱气、吹氧、化学成分及温度调整等。
处理结束时使系统破真空。
随后退出吸嘴,将钢包送至后处理位置或交接位置。
冶金效果:在短时间就可达到较低的碳(<15ppm)、氢(<1.5ppm)、氧含量(<40ppm);仅有略微的温度损失;不用采取专门的渣对策;可准确调整化学成分,Al,Si等合金收得率在90~97%。
汽车钢板以及电工钢等是RH钢生产的典型产品。
rh真空脱碳原理

RH真空脱碳是一种钢的精炼方法,主要原理是利用真空环境下的化学反应,通过控制碳的去除过程来达到改善钢的化学成分和物理性能的目的。
在RH真空脱碳过程中,钢水被吸入真空室,与真空室内的碳反应,生成一氧化碳和二氧化碳气体。
这些气体被排出真空室,而钢中的碳含量则相应降低。
此过程的主要反应式为:Fe+C→FeC+Q(其中Q为热量)
这种方法的优点在于它可以在不改变钢中其他元素含量的前提下,精确地控制碳的含量。
此外,由于在真空环境下进行,因此可以避免常规脱碳过程中产生的脱碳层和增碳层,使得钢的性能更加均匀。
需要注意的是,RH真空脱碳过程的反应速率主要取决于真空度、温度、钢中的氧和氮含量等因素。
因此,为了获得最佳的脱碳效果,需要精确控制这些参数。
总的来说,RH真空脱碳是一种高效、精确的钢精炼方法,对于需要精确控制碳含量的钢种,如高级优质钢、不锈钢等,具有广泛的应用前景。
rh真空精炼的设备与工艺
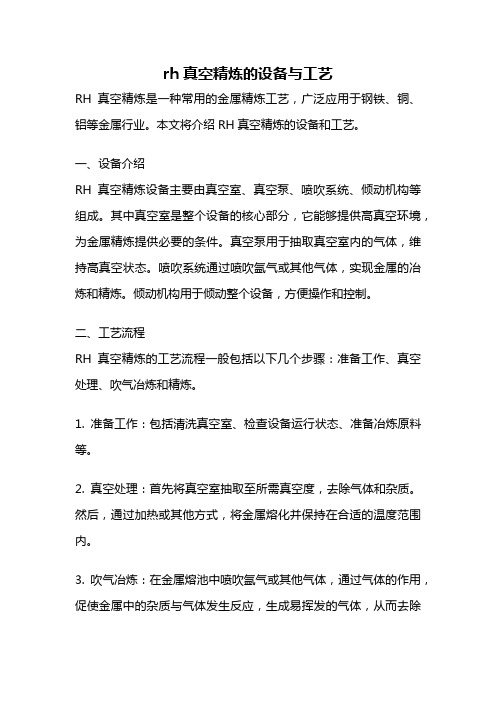
rh真空精炼的设备与工艺RH真空精炼是一种常用的金属精炼工艺,广泛应用于钢铁、铜、铝等金属行业。
本文将介绍RH真空精炼的设备和工艺。
一、设备介绍RH真空精炼设备主要由真空室、真空泵、喷吹系统、倾动机构等组成。
其中真空室是整个设备的核心部分,它能够提供高真空环境,为金属精炼提供必要的条件。
真空泵用于抽取真空室内的气体,维持高真空状态。
喷吹系统通过喷吹氩气或其他气体,实现金属的冶炼和精炼。
倾动机构用于倾动整个设备,方便操作和控制。
二、工艺流程RH真空精炼的工艺流程一般包括以下几个步骤:准备工作、真空处理、吹气冶炼和精炼。
1. 准备工作:包括清洗真空室、检查设备运行状态、准备冶炼原料等。
2. 真空处理:首先将真空室抽取至所需真空度,去除气体和杂质。
然后,通过加热或其他方式,将金属熔化并保持在合适的温度范围内。
3. 吹气冶炼:在金属熔池中喷吹氩气或其他气体,通过气体的作用,促使金属中的杂质与气体发生反应,生成易挥发的气体,从而去除杂质。
这一步骤也可以同时进行冶炼,将合金中的成分进行调整。
4. 精炼:通过控制喷吹气体和温度,进一步去除金属中的杂质,提高其纯度。
同时,还可以通过加入适量的合金元素,对金属进行合金化处理。
三、优势和应用RH真空精炼具有以下几个优势:1. 高纯度:通过去除金属中的杂质,可以大幅提高金属的纯度,满足高要求的应用场景。
2. 均质化:通过喷吹气体的作用,可以使金属中的成分更加均匀,提高合金的一致性。
3. 节能环保:采用真空精炼工艺,可以减少能源消耗,同时避免了传统冶炼过程中产生的大量废气和废渣。
4. 自动化控制:RH真空精炼设备可以实现自动化控制,提高生产效率和产品质量。
RH真空精炼广泛应用于钢铁、铜、铝等金属行业。
在钢铁行业中,RH精炼可用于脱气、脱硫、脱氮等工艺,提高钢材的质量。
在铜、铝行业中,RH精炼可用于去除金属中的氧化物和杂质,提高金属的纯度。
RH真空精炼设备和工艺在金属精炼领域具有重要的应用价值。
RH真空精炼的设备与工艺

RH真空精炼的设备与工艺RH真空精炼是一种常用的精炼方法,主要用于钢铁行业中的不锈钢和合金钢的生产。
该方法通过在真空环境中加入合适的精炼剂,能够有效地去除钢中的杂质和氧化物,并调整钢的成分和性能。
以下将详细介绍RH真空精炼的设备和工艺。
设备方面,RH真空精炼系统主要包括RH倾转炉、真空系统、废气处理系统和渣料处理系统等。
首先是RH倾转炉。
RH倾转炉是RH真空精炼的核心设备。
其主要由中间底吹氧气的底吹装置、底吹气包和真空系统组成。
底吹装置通过底吹氧气将气泡产生在钢水中,增加钢水的搅拌作用,并加快精炼作用。
底吹气包用于调整底吹氧气的流量和压力,以及维持正压状态,防止外界气体进入。
真空系统则保证整个操作过程中的真空环境,确保精炼的有效进行。
其次是废气处理系统。
在RH精炼过程中,废气中会含有大量的有害气体和杂质。
废气处理系统通过一系列的处理设备,如热交换器和吸附装置等,将废气中的有害气体和杂质去除,净化废气,以达到环境保护的要求。
同时,废气处理系统还能回收其中的一些有价值的矿物质和能量,实现资源的循环利用。
最后是渣料处理系统。
在RH精炼过程中,会产生大量的渣料。
渣料处理系统主要将这些渣料进行分类、分离和处理。
其中,一部分渣料可以通过回收再利用,另一部分则需要进行安全的处置。
因此,渣料处理系统的重要任务是实现渣料的无害化处理和资源的最大化利用。
在工艺方面,RH真空精炼的主要流程包括开始吹氩,熔化,通冶炼剂倾吐,混炼和钢水倾出等。
具体流程如下:1.开始吹氩:首先需要对RH倾转炉进行预处理,清除其中的氧气和水蒸气等杂质,以保证真空环境的形成。
然后,通过底吹装置对钢水进行底吹氩处理,将炉中的气体排除。
2.熔化:将预处理后的钢水加热至熔化温度,并通过底吹氩进一步搅拌,以提高炉内的液相搅动作用。
3.通冶炼剂倾吐:在炉内形成真空环境后,通过合适的接口,将精炼剂倾吐入炉中。
精炼剂可以是气体、粉末或液体等形式,用于去除钢中的杂质和氧化物。
RH真空精炼原理及工艺简介

RH真空精炼原理及工艺简介孙利顺(唐山钢铁股份有限公司技术中心唐山邮编063016)摘要:本文简要分析了RH真空处理的钢水循环“气泡泵”原理、真空脱气原理、真空脱氧原理、真空脱碳原理与合金化原理,介绍了本处理、轻处理、深脱碳处理等处理模式。
关键词:真空精炼;气体;夹杂物1 钢中的气体、非金属夹杂物及其对钢质量的影响钢中除了含有各种常规元素和合金元素外,还含有微量的气体(氢、氮和氧)及非金属夹杂物。
由于氧在钢中与合金元素结合成各种类型的氧化物以非金属夹杂物形式存在于钢中,所以钢中的气体通常是指溶解在钢中的氢和氮,其含量大致波动在1—100ppm之间。
虽然钢中气体和非金属夹杂物的含量不高,但对钢的质量和性能会产生较大影响,甚至导致钢材报废。
1.1氢对钢质量的影响钢中含氢有害无利,它对钢的不良影响主要表现在以下几个方面;(1)氢脆。
氢脆是氢对钢的机械性能不良影响的重要表现。
随着钢中含氢量的增加,钢的强度特别是塑性和韧性将显著下降,使钢变脆,称为氢脆。
氢脆随钢强度的增高而加剧,因此对高强度钢来说,氢脆尤为突出,高强度钢平均含氢量不到1ppm就可能出现氢脆。
(2)白点。
氢以氢原子形式溶解在钢中,在钢液中的溶解度比在固态钢中大得多。
当温度下降时,氢在钢中的溶解度降低,氢原子便扩散到显微孔隙、夹杂物附近或晶界间,结合成氢分子(2[H]={H2})。
氢分子在该处不断地聚集,同时产生巨大的压力,当其聚集压力超过该处钢的强度极限时,产生裂纹,使钢的机械性能(特别是塑性)降低,甚至断裂。
裂纹的部位常呈银白色圆点,称为白点。
(3)钢中含有较多的氢还会使钢锭产生点状偏析,以及使钢锭上涨或产生内部疏松。
1.2氮对钢质量的影响氮对钢质量的影啊表现为不良和有益两个方面。
不良影响主要表现在以下几个方面:(1)氮使钢产生时效硬化。
氮在低温下它是过饱和状态,必然从钢中析出。
但是钢中的氮不是以气体存在,而是呈弥散的固态氮化物缓慢地从钢中析出,逐渐地改变着钢地性能,使钢的强度和硬度增加,塑性和冲击韧性显著降低,这种现象称为老化或时效。
炉外精炼真空循环脱气法(RH法)与工艺介绍

5.4.4 RH钢液真空循环原理
h 0为真空室内静态下理论钢液深度。见表5-6。
表5-6 理论钢液提升高度h、h0与真空度关系
P(kPa)
35 20 15 10 8.6 2.7 0.5 0.067
h (m)
0.97 1.19 1.26 1.33 1.35 1.43 1.47 1.48
h0 (m) 槽内钢水重量(t)
钢液真空循环原理类似于“气泡泵”的作用,如图所示。当 进行真空脱气处理时,将真空室下部的两根浸渍管插入钢液 内一定深度(如200t时500 mm )后,启动真空泵将真空室抽 成真空,于是真空室内、外形成压差,钢液便从两根浸渍管 中上升到压差相等的高度(所谓的循环高度)。为了使钢液 循环,从上升管下部约三分之一处吹入驱动气体(一般为氩 气)。该气体吹入上升管内的钢液中,在上升管内瞬间产生 大量的气泡。由于受热膨胀和压力降低所引起的等温膨胀, 气体体积成百倍的增大,导致上升管中钢液(两相流)密度 变小;又由于氩气泡内的氢气、氮气的分压为零,所以钢液 内溶解的气体向氩气泡内扩散。膨胀的气体驱动钢液以约 5m/s的速度上升,成喷泉状喷入真空室内。
5.4.4 RH钢液真空循环原理
A g A 1 A 2 n R ( T s T g ) n R T sl n ( P P 1 2 ) n R T s [ l n ( P P 1 2 ) ( 1 T T g s) ]
式中:
V0—驱动气体在标准状态下的体积,m3 ; Tg—驱动气体的初始温度,K; Ts—钢液的温度,K; V1-按压力P1计算的驱动气体体积,m3; P1-驱动气体出口处的压力,Pa; P2-真空室内压力,Pa;
“气泡泵”的特性曲线
5.4.4 RH钢液真空循环原理
最新RH真空精炼技术
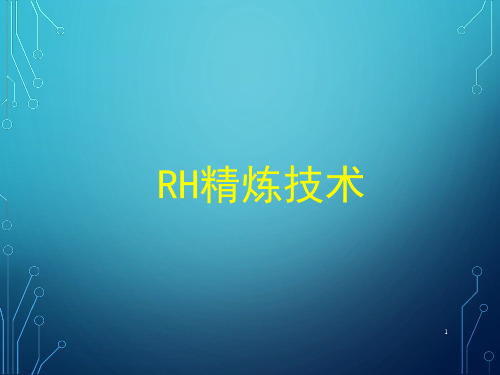
产品 热轧钢板 冷轧深冲钢板 镀层板,涂层板 锅炉板、桥梁板 造船板
产品 IF 钢 电工用钢 石油管线钢 低温用钢 超 深 冲4钢
5
特殊钢厂冶炼工艺路线
废钢
UHP
生铁
电炉
D R I/H B I
VD
轴轴承承钢钢
精炼
齿齿轮轮钢钢
优优质质弹弹簧簧钢钢
LF
大方
硬硬线线钢钢
精炼
坯连
帘帘线线钢钢
RH
铸
精炼
石石油油套套管管
RH精炼技术
__________________________________________________
1
现代纯净钢生产工艺流程
在纯净钢生产中,RH是最重要的真空精炼装置之一,
应用越来越广泛,新建钢厂多数选择RH精炼。 __________________________________________________
• 对钢水进行该钢种所必须进行的处理,(如脱氢处理,深
脱碳处理,轻处理,深脱氧处理等)。处理过程中真空度 和环流气体流量按各处理模式自动进行变换。
• 处理结束前再次测温取样,确认处理目的是否已达到。 • 合金微调及最终脱氧。 • 测温取样后关闭主真空阀,破真空。 • 钢包下降,座落到钢包台车,同时将环流气体切换成氮气。 • 钢包台车运行到喂丝工(加保温剂)位,按钢种要求喂丝,
2
钢
铁
冶
炼工艺Fra bibliotek路线 __________________________________________________
3
大型联合企业冶炼工艺流程
CAS-OB
板坯连铸
铁水脱硫 转炉复吹
rh工序流程 -回复
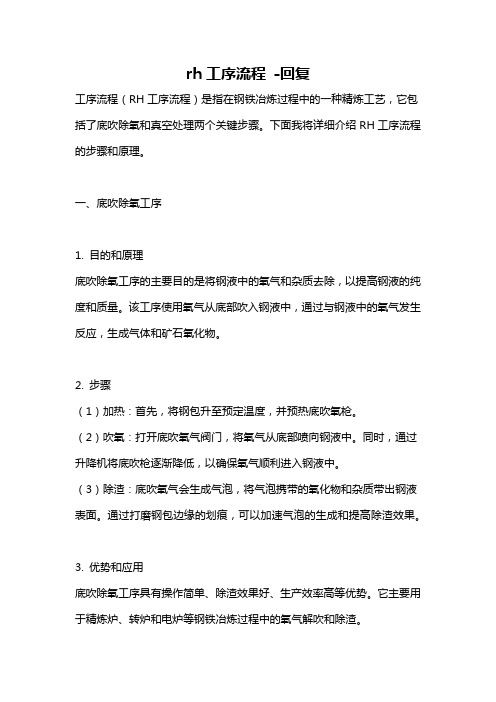
rh工序流程-回复工序流程(RH工序流程)是指在钢铁冶炼过程中的一种精炼工艺,它包括了底吹除氧和真空处理两个关键步骤。
下面我将详细介绍RH工序流程的步骤和原理。
一、底吹除氧工序1. 目的和原理底吹除氧工序的主要目的是将钢液中的氧气和杂质去除,以提高钢液的纯度和质量。
该工序使用氧气从底部吹入钢液中,通过与钢液中的氧气发生反应,生成气体和矿石氧化物。
2. 步骤(1)加热:首先,将钢包升至预定温度,并预热底吹氧枪。
(2)吹氧:打开底吹氧气阀门,将氧气从底部喷向钢液中。
同时,通过升降机将底吹枪逐渐降低,以确保氧气顺利进入钢液中。
(3)除渣:底吹氧气会生成气泡,将气泡携带的氧化物和杂质带出钢液表面。
通过打磨钢包边缘的划痕,可以加速气泡的生成和提高除渣效果。
3. 优势和应用底吹除氧工序具有操作简单、除渣效果好、生产效率高等优势。
它主要用于精炼炉、转炉和电炉等钢铁冶炼过程中的氧气解吹和除渣。
二、真空处理工序1. 目的和原理真空处理工序是在钢液中建立真空环境,将气体和杂质从钢液中蒸发和去除的工艺。
真空能够有效地降低钢液中的氧含量,减少钢液中的氧化物形成,提高钢液的纯度。
2. 步骤(1)密封:首先,将精炼炉、转炉或电炉密封,建立真空环境。
同时,启动真空系统,抽取钢包内的气体和杂质。
(2)升温和撤焦:升温至定温并投加适量的钢料,在钢包中产生剧烈的煅烧反应,并发生CO和CO2等气体生成。
(3)去气和除渣:真空系统不断抽取钢包中的气体,使钢液中的气体逐渐达到平衡,进一步提高钢液的纯度。
同时,通过钢包边缘的划痕将浮渣除去。
3. 优势和应用真空处理工序具有除氧效果好、钢液纯度高、能有效降低钢液中的气体含量等优势。
它主要应用于特殊钢种的冶炼和高要求钢材的生产。
综上所述,RH工序流程是一种在钢铁冶炼中广泛应用的精炼工艺,包括底吹除氧和真空处理两个关键步骤。
底吹除氧工序通过从底部吹氧的方式将钢液中的氧气和杂质去除,而真空处理工序则通过建立真空环境将气体和杂质从钢液中蒸发和去除。
rh精炼炉的工作原理

rh精炼炉的工作原理
RH精炼炉是一种用于钢水精炼的设备,工作原理如下:
1. 初始状态:钢水由脱氧剂(如铝、硅)去氧化剂(如氧、硫)的加入而含氧量较高,同时含有杂质元素(如硫、氮、氢)。
2. 加热:首先将RH炉加热至一定温度,以保持钢水在液态状态,并提供热能用于后续处理。
3. 充氩:通过向炉腔内注入氩气,将气氛改为惰性气体,以防止钢水与空气发生反应,减少含氧量。
4. 抽真空:通过抽取炉腔内部的气体,形成负压,实现去气的目的。
抽真空的同时,还可以去除钢水中的氧化物、氢气等气体。
5. 吹吸:将钢水中加入的精炼剂(如钙、铝、氧化钛)通过吹气混合装置喷射入钢水中。
精炼剂与钢水中的杂质发生反应,生成气体,使杂质浮于钢水表面。
吹吸的过程实际上是通过吹气在钢水内部产生的气泡使钢水得到搅拌和搅动,从而实现对杂质的混合和剥离。
6. 分离:在吹吸的过程中,通过钼室和配套的转子装置,使气泡被上升到炉腔上部,并对气泡进行持续的紊动,从而将气泡中的杂质分离出来。
分离过程主要是基于气泡的上浮和沉降的原理。
7. 钢液进出:在精炼过程中,可根据需要随时向炉腔内添加新的钢水,并从炉腔底部排出已精炼的钢水。
8. 放氩冷却:在精炼过程结束后,向炉腔内注入氩气,使炉腔内的气氛恢复到惰性气体状态,同时进行炉体冷却。
总的来说,RH精炼炉通过充氩、抽真空、吹吸、分离等一系列步骤,通过气泡搅拌和杂质的分离,使钢水中的含气及杂质得到有效去除,从而达到精炼钢水的目的。
rh炉工艺
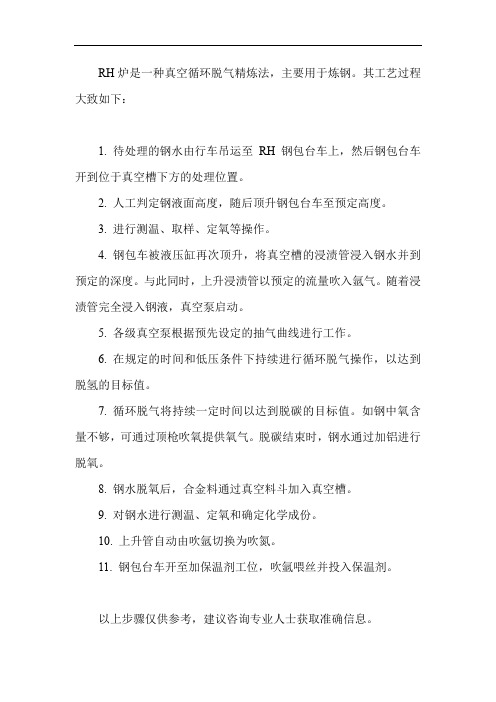
RH炉是一种真空循环脱气精炼法,主要用于炼钢。
其工艺过程大致如下:
1. 待处理的钢水由行车吊运至RH钢包台车上,然后钢包台车开到位于真空槽下方的处理位置。
2. 人工判定钢液面高度,随后顶升钢包台车至预定高度。
3. 进行测温、取样、定氧等操作。
4. 钢包车被液压缸再次顶升,将真空槽的浸渍管浸入钢水并到预定的深度。
与此同时,上升浸渍管以预定的流量吹入氩气。
随着浸渍管完全浸入钢液,真空泵启动。
5. 各级真空泵根据预先设定的抽气曲线进行工作。
6. 在规定的时间和低压条件下持续进行循环脱气操作,以达到脱氢的目标值。
7. 循环脱气将持续一定时间以达到脱碳的目标值。
如钢中氧含量不够,可通过顶枪吹氧提供氧气。
脱碳结束时,钢水通过加铝进行脱氧。
8. 钢水脱氧后,合金料通过真空料斗加入真空槽。
9. 对钢水进行测温、定氧和确定化学成份。
10. 上升管自动由吹氩切换为吹氮。
11. 钢包台车开至加保温剂工位,吹氩喂丝并投入保温剂。
以上步骤仅供参考,建议咨询专业人士获取准确信息。
炉外精炼真空循环脱气法(RH法)和工艺介绍
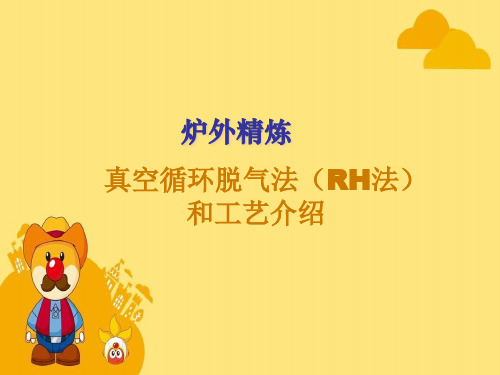
5.4.4 RH钢液真空循环原理
(2)钢液提升高度
钢液静态下理论提升高度可用下式表示:
h P0 P
g
(5-32)
式中h一钢液提升高度;m P一真空室内压力;Pa
P0一大气压;1.01×105Pa g一重力加速度;9.8N/Kg
ρ一钢液密度;取7.0×103 kg/m3
某厂钢液理论提升高度h见表5-6。
5.4.4 RH钢液真空循环原理
5.4.4 RH钢液真空循环原理
气泡进入真空室后在自由界面破裂,钢液被破碎成 小的液滴,使脱气比表面积大大增加(20~30倍),加速了 脱气过程。气体自钢液内析出被真空泵抽走,而脱气后 的钢液汇集到真空室底部,由于重量的差异,经下降管 以1~2m/s的速度返回到钢包内。未经脱气的钢液又不 断从上升管进入真空室脱气,周而复始,从而形成连续 循环过程。如此反复循环多次后达到脱气目的,脱气过 程结束。
“气泡泵”的特性曲线
5.4.4 RH钢液真空循环原理
钢液脱气后汇集到真空室底部形成高差∆B的钢液层,
按能量守恒定律可得:
mgBmu2/2
(5-29)
u 2gB
(5-30)
所以要获得 u = 1 m/s的流出速度,则要求真空室中钢液
层高度为:
Bu2/2g0.05m (5-31)
从下降管流出的钢液流动情况对钢液在钢包中混合极 为重要。实践证明,从下降管流出的钢液流速大于1m/s 时就会混合良好,且不会形成短路现象。
炉外精炼
真空循环脱气法(RH法) 和工艺介绍
5.4 RH真空循环脱气法
主要内容
5.4.1 RH法的产生及发展概况 5.4.2 RH法的冶金功能 5.4.3 RH法的设备 5.4.4 RH法钢液真空循环原理 5.4.5 RH处理工艺参数 5.4.6 RH法精炼工艺 5.4.7 RH法的的冶金效果 5.4.8 RH法的发展
RH精炼
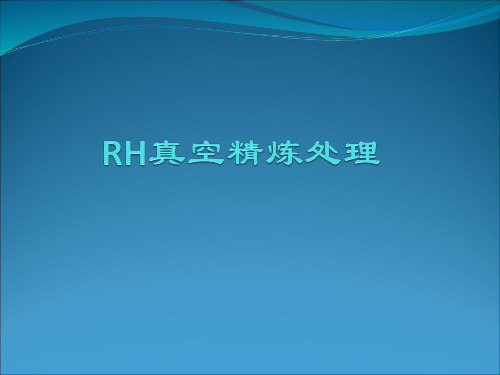
4.RH真空精炼的冶金功能
在短时间就可达到较低的碳、氢、氧含量;不用采 取专门的渣对策;可准确调整化学成分,Al,Si等合金收 得率在90~97%。汽车钢板以及电工钢等是RH钢生产的典 型产品。最初RH装置主要是对钢水脱氢,随着RH真空精炼 实践和精炼技术的发展,其冶金功能得到了充分的发展。
1)脱氢 可生产[H]≤0.00015%,延长钢水精炼时间,可使 [H]≤0.00010%。 2)脱碳 在20min处理周期内可生产出[C]≤0.002%的超低碳钢水。在脱碳过程 中,钢水中的碳和氧反应形成一氧化碳并通过真空泵排出。如钢中氧含量不够, 可通过顶枪吹氧提供氧气。脱碳结束时,钢水通过加铝进行脱氧。 3)脱氧 RH真空精炼后T[O]量可≤0.0020%,如和 LF法配合,钢水T[O]可降到 0.0010%以下。
近年来,我国钢铁企业普遍对钢水炉外精炼技术的应 用较为重视,投入大量资金上马先进的炉外精炼技术装备, 炉外精炼已经不再是特大型钢铁企业或特钢企业的专利品。 炉外精炼在提高钢材产品质量、扩大品种、提高炼钢生产 能力、保障连铸顺行、降低成本、优化炼钢生产工艺等方 面发挥着极其重要的作用,甚至成为限制环节。而RH真空 处理又是炉外精炼领域的一个突出典型。铁水预处理-转炉 复合吹炼(或电弧炉冶炼)-炉外精炼(LF、VD、VOD、RH)-连 铸,已成为越来越多的钢铁企业炼钢厂的典型流程模式。
3.在真空条件进行精炼,脱碳、脱氧、脱硫、合金化、净化钢质,减少 钢中非金属夹杂物,提高合金收得率,减小成分波动范围。冶炼出一 般平炉电炉转炉中作不能冶炼的钢种,为冶炼很多新钢种提供了一个 新的工艺。 4.RH真空精炼可以实现计算机自动控制,从而使其精炼工艺过程实现高 度的自动化。 5.由于双真空室设备和计算机自动控制的应用,使得RH真空精炼设备的 作业率大幅度提高,从而达到了LD—RH—CC三者配合连续作业。
RH精炼技术
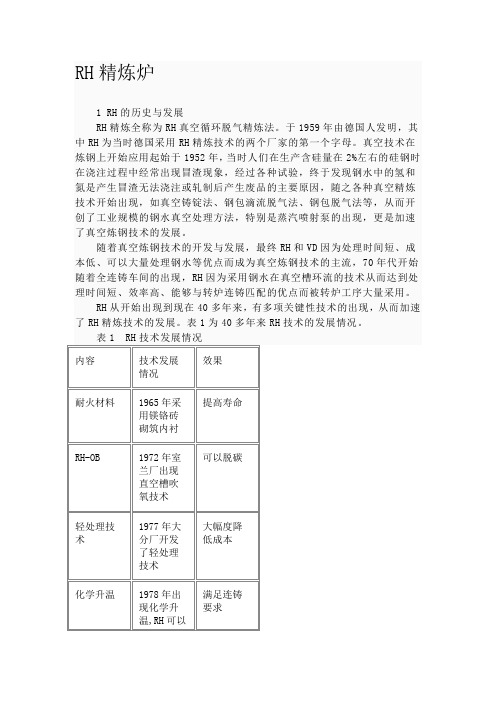
空槽内的钢水还进行一系列的冶金反应,比如碳氧反应等;如此循环脱气精炼使钢液得到净化。
经RH处理的钢水优点明显:合金基本不与炉渣反应,合金直接加入钢水之中,收得率高;钢水能快速均匀混合;合金成分可控制在狭窄的范围之内;气体含量低,夹杂物少,钢水纯净度高;还可以用顶枪进行化学升温的温度调整,为连铸机提供流动性好、纯净度高、符合浇铸温度的钢水,以利于连铸生产的多炉连浇。
3真空泵工作原理在工业炼钢生产中,现经常采用的抽真空设备主要有罗茨泵、水环泵和蒸汽喷射泵,其中以水环泵和蒸汽喷射泵最为常见。
1)水环泵工作原理水环泵中带有叶片的转了被偏心的与泵的壳体相配合,在泵体中装有适量的水作为工作液。
当叶轮顺时针方向旋转时,水被叶轮抛向四周,由于离心力的作用,水形成了一个决定于泵腔形状的近似于等厚度的封闭圆环。
水环的下部分内表面恰好与叶轮轮毂相切,水环的上部内表面刚好与叶片顶端接触(实际上叶片在水环内有一定的插入深度)。
此时叶轮轮毂与水环之间形成一个月牙形空间,而这一空间又被叶轮分成和叶片数目相等的若干个小腔。
如果以叶轮的下部0°为起点,那么叶轮在旋转前180°时小腔的容积由小变大,且与端面上的吸气口相通,此时气体被吸入,当吸气终了时小腔则与吸气口隔绝;当叶轮继续旋转时,小腔由大变小,使气体被压缩;当小腔与排气口相通时,气体便被排出泵外。
2)蒸汽喷射泵工作原理喷射泵是由工作喷嘴和扩压器及混合室相联而组成。
工作喷嘴和扩压器这两个部件组成了一条断面变化的特殊气流管道。
气流通过喷嘴可将压力能转变为动能。
工作蒸汽压强和泵的出口压强之间的压力差,使工作蒸汽在管道中流动。
在这个特殊的管道中,蒸汽经过喷嘴的出口到扩压器入口之间的这个区域(混合室),由于蒸汽流处于高速而出现一个负压区。
此处的负压要比工作蒸汽压强和反压强低得多。
此时,被抽气体吸进混合室,工作蒸汽和被抽气体相互混合并进行能量交换,把工作蒸汽由压力能转变来的动能传给被抽气体。
RH真空精炼技术
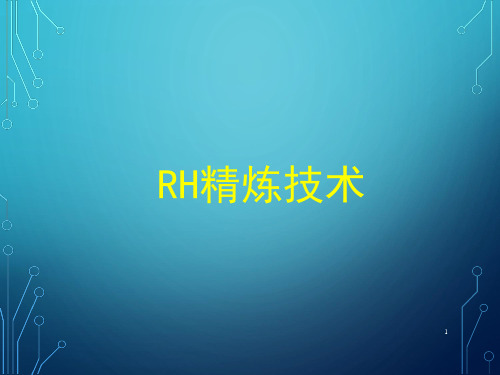
H 补偿量/℃ Kc/min-1
℃
技术水平 ≤20 ≤10 ≤15 ≤20 ≤20 ≤1.0 26.3
0.35
≤±5
(3)极低碳钢的冶炼技术(2000年~ ):为了解决极低碳钢 ([C]≤10×10-6)精炼的技术难题,需要进一步克服钢水的静压力,以
7
提高熔池脱碳速度。
RH的工作原理
钢液真空循环原理类似于
产品 IF 钢 电工用钢 石油管线钢 低温用钢 超 深 冲4钢
5
特殊钢厂冶炼工艺路线
废钢
UHP
生铁
电炉
D R I/H B I
VD
轴轴承承钢钢
精炼
齿齿轮轮钢钢
优优质质弹弹簧簧钢钢
LF
大方
硬硬线线钢钢
精炼
坯连
帘帘线线钢钢
RH
铸
石石油油套套管管
精炼
SS-V
铁水 脱硅
转炉 复吹
OD AOD
大板
脱磷 脱硫
坯连 铸
人工加保温剂。
• 钢包台车开出,用吊车将钢包吊至下工序。
12
RH法的设备
RH的主体设 备构成:
• 真空室及附
属设备;
• 气体冷却器; • 真空排气装
置;
• 合金称量台
车及加料装 置。
13
RH精炼车间示意图
RH设备示意图
RH真空室
• RH真空室形状如右图,真空室
外壳为钢板围焊成的圆筒状结构, 内衬为耐火砖。真空室下部有两 根用耐火材料制成的可以插入钢 液的浸渍管,也称升降管,其中 一根为钢液的上升管,另一个根 为钢液的下降管,浸渍管的上半 部外侧钢管结构。真空处理时钢 液沿上升管进入真空室,沿下降 管返回钢包。
炼钢rh炉工作原理
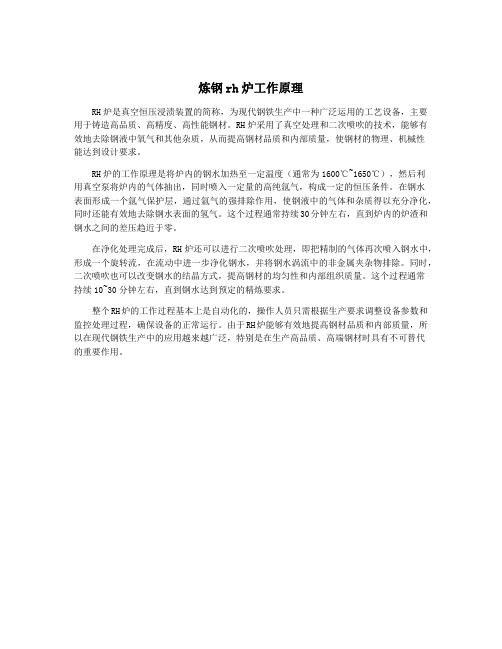
炼钢rh炉工作原理
RH炉是真空恒压浸渍装置的简称,为现代钢铁生产中一种广泛运用的工艺设备,主要用于铸造高品质、高精度、高性能钢材。
RH炉采用了真空处理和二次喷吹的技术,能够有效地去除钢液中氧气和其他杂质,从而提高钢材品质和内部质量,使钢材的物理、机械性
能达到设计要求。
RH炉的工作原理是将炉内的钢水加热至一定温度(通常为1600℃~1650℃),然后利
用真空泵将炉内的气体抽出,同时喷入一定量的高纯氩气,构成一定的恒压条件。
在钢水
表面形成一个氩气保护层,通过氩气的强排除作用,使钢液中的气体和杂质得以充分净化,同时还能有效地去除钢水表面的氢气。
这个过程通常持续30分钟左右,直到炉内的炉渣和钢水之间的差压趋近于零。
在净化处理完成后,RH炉还可以进行二次喷吹处理,即把精制的气体再次喷入钢水中,形成一个旋转流,在流动中进一步净化钢水,并将钢水涡流中的非金属夹杂物排除。
同时,二次喷吹也可以改变钢水的结晶方式,提高钢材的均匀性和内部组织质量。
这个过程通常
持续10~30分钟左右,直到钢水达到预定的精炼要求。
整个RH炉的工作过程基本上是自动化的,操作人员只需根据生产要求调整设备参数和监控处理过程,确保设备的正常运行。
由于RH炉能够有效地提高钢材品质和内部质量,所以在现代钢铁生产中的应用越来越广泛,特别是在生产高品质、高端钢材时具有不可替代
的重要作用。
rh真空槽工作原理

rh真空槽工作原理
RH真空槽是一种用于钢铁冶炼的设备,其工作原理是利用真空环境下的物理化学反应,将钢水中的杂质和气体去除,从而提高钢的质量和纯度。
RH真空槽的工作原理可以分为三个步骤:抽真空、吹氩气和加压。
首先,将钢水槽内的空气抽出,形成真空环境。
这样可以避免钢水中的氧气和氮气与钢水中的碳反应,从而减少钢水中的气体含量。
其次,通过吹氩气的方式,将钢水中的杂质和气体吹出。
氩气是一种惰性气体,不会与钢水中的元素发生反应,因此可以有效地去除钢水中的杂质和气体。
最后,加压可以使钢水中的气体更加容易被吹出,从而提高去除杂质和气体的效率。
RH真空槽的工作原理具有以下优点:首先,可以有效地去除钢水中的杂质和气体,从而提高钢的质量和纯度。
其次,可以减少钢水中的气体含量,从而降低钢水的气孔率,提高钢的密度和强度。
最后,可以减少钢水中的氧化物含量,从而降低钢的氧化程度,提高钢的表面质量和耐腐蚀性。
RH真空槽是一种高效、可靠的钢铁冶炼设备,其工作原理是利用真空环境下的物理化学反应,将钢水中的杂质和气体去除,从而提高钢的质量和纯度。
在未来的钢铁冶炼中,RH真空槽将会发挥越来越重要的作用。
- 1、下载文档前请自行甄别文档内容的完整性,平台不提供额外的编辑、内容补充、找答案等附加服务。
- 2、"仅部分预览"的文档,不可在线预览部分如存在完整性等问题,可反馈申请退款(可完整预览的文档不适用该条件!)。
- 3、如文档侵犯您的权益,请联系客服反馈,我们会尽快为您处理(人工客服工作时间:9:00-18:30)。
RH真空精炼原理及工艺简介孙利顺(唐山钢铁股份有限公司技术中心唐山邮编063016)摘要:本文简要分析了RH真空处理的钢水循环“气泡泵”原理、真空脱气原理、真空脱氧原理、真空脱碳原理与合金化原理,介绍了本处理、轻处理、深脱碳处理等处理模式。
关键词:真空精炼;气体;夹杂物1 钢中的气体、非金属夹杂物及其对钢质量的影响钢中除了含有各种常规元素和合金元素外,还含有微量的气体(氢、氮和氧)及非金属夹杂物。
由于氧在钢中与合金元素结合成各种类型的氧化物以非金属夹杂物形式存在于钢中,所以钢中的气体通常是指溶解在钢中的氢和氮,其含量大致波动在1—100ppm之间。
虽然钢中气体和非金属夹杂物的含量不高,但对钢的质量和性能会产生较大影响,甚至导致钢材报废。
1.1氢对钢质量的影响钢中含氢有害无利,它对钢的不良影响主要表现在以下几个方面;(1)氢脆。
氢脆是氢对钢的机械性能不良影响的重要表现。
随着钢中含氢量的增加,钢的强度特别是塑性和韧性将显著下降,使钢变脆,称为氢脆。
氢脆随钢强度的增高而加剧,因此对高强度钢来说,氢脆尤为突出,高强度钢平均含氢量不到1ppm就可能出现氢脆。
(2)白点。
氢以氢原子形式溶解在钢中,在钢液中的溶解度比在固态钢中大得多。
当温度下降时,氢在钢中的溶解度降低,氢原子便扩散到显微孔隙、夹杂物附近或晶界间,结合成氢分子(2[H]={H2})。
氢分子在该处不断地聚集,同时产生巨大的压力,当其聚集压力超过该处钢的强度极限时,产生裂纹,使钢的机械性能(特别是塑性)降低,甚至断裂。
裂纹的部位常呈银白色圆点,称为白点。
(3)钢中含有较多的氢还会使钢锭产生点状偏析,以及使钢锭上涨或产生内部疏松。
1.2氮对钢质量的影响氮对钢质量的影啊表现为不良和有益两个方面。
不良影响主要表现在以下几个方面:(1)氮使钢产生时效硬化。
氮在低温下它是过饱和状态,必然从钢中析出。
但是钢中的氮不是以气体存在,而是呈弥散的固态氮化物缓慢地从钢中析出,逐渐地改变着钢地性能,使钢的强度和硬度增加,塑性和冲击韧性显著降低,这种现象称为老化或时效。
老化时还引起磁导性降低,电阻增大。
(2)钢中含氮是导致蓝脆的主要原因。
所谓蓝脆是指在250—450℃这个温度范围内钢的强度升高,冲击韧性降低;由于钢在这个温度下加热时,表面发蓝而得名。
(3)钢液中含氮高时还会导致钢锭疏松甚至产生气泡,如果皮下气泡距钢锭表面太近,热轧时容易引起开裂使钢锭报废。
(4)在氮和氢同时存在的条件下,使氢的腐蚀更加剧烈,这是由于氮能生成比碳化物更稳定的氮化物,使碳从碳化物中分解出来。
从而加快了氢和碳的反应。
1.3氧对钢质量的影响氧在钢中主要以FeO形式存在。
氧对钢性能的影响即破坏钢锭的合理结构,降低钢的机械性能(如钢的塑性、韧性),残留在钢中的FeO能同钢中的FeS形成910℃的低熔点共晶体(机械混合物),分布在晶界上,从而加剧硫对钢的热脆性。
1.4非金届夹杂物对钢质量的影响钢中非金属夹杂物按其化学成分不同可分为氧化物、硫化物、氮化物等,而以氧化物(如FeO,SiO2,Al2O3),硫化物(主要是FeS,MnS)以及它们组成的各种不同成分的硅酸盐等复杂化合物,占钢中夹杂物的绝大部分。
按钢中夹杂物来源可分为内在夹杂物和外来夹杂物两类。
内在夹杂物是钢水在熔炼和冷凝过程中物理化学反应生成的、未能从钢水中排除的反应生成物,如MnO、SiO2、MnS、TiN等,这是钢中非金属夹杂物的主要部分。
外来夹杂物是在熔炼、出钢和浇铸过程中落入和混入钢水的耐火材料和炉渣(如与生铁、废钢等一起进入炉内的非金属物质)。
钢中非金属夹杂物所占数量或总体积虽然不多,但它们在钢中呈独立存在,与钢本身性质完全不同,它破坏了钢的基体的连续性,造成了组织上的不均匀,从而降低了钢的强度、塑性、韧性,使钢的冷热加工性能乃至某些物理性能变坏。
2 RH真空处理的意义随着氧气顶吹转炉几十年的发展,该种炼钢法的生产节奏、钢的冶炼品种与质量等都己基本挖掘到极限。
而现代工业的发展,对钢的产量、品种和质量等又提出了越来越高的要求,这就迫使炼钢工作者寻求新的炼钢工艺,于是产生了炉外精炼法(即二次冶炼)。
炉外精炼是把由炼钢转炉初炼的钢水倒入钢包或专用容器内进一步精炼的一种方法,即把全部冶炼任务只由转炉完成的一步炼钢法,转变为转炉只承担熔化、粗脱碳、去磷、初调成分及温度等初炼任务,然后通过二次精炼,完成脱气、脱硫、脱磷、脱碳、合金微调、温度调整等功能的分步炼钢法,从而大大地缩短了转炉的冶炼周期,提高了钢的质量,并能生产出用一步炼钢法不能生产的某些钢种(如超低碳钢等)。
实现了高效、低耗、优质和多品种的最佳化生产。
炉外精炼法起始于二十世纪50年代初期,80年代后获得了迅速发展。
RH真空处理是众多的炉外精炼法中的一种,它是1957年由原西德鲁尔(Ruhrstahl)和海拉斯(Heraeus)钢厂联合研制的真空循环脱气精炼法,取两公司名称的首字母简称而来。
RH真空处理的主要任务是脱气,并通过钢水循环使得非金属夹杂物上浮、均匀钢水成分和温度,同时通过物料添加系统使其具有脱氧、脱碳、脱硫、脱磷、成分微调等多项冶金功能。
RH工艺是与十九世纪以来迅猛发展的炼钢技术(特别是转炉炼钢)密切相关的一种二次冶金技术。
RH真空处理既是转炉充分发挥效率的可靠保证,又是为连铸提供优质钢水、稳定连铸生产的重要手段,同时在转炉与连铸之间起着重要的缓冲作用。
3 RH真空处理原理分析3.1RH处理原理概述在RH真空处理装置中,钢液的真空脱气在一个砌有耐火砖衬的真空室中进行。
真空室的底部有两个用耐火材料制成的可插入钢液中的插入管,将插入管插入钢液,对真空室抽真空形成负差,在大气压力的作用下使钢液由插入管进入真空室。
当向其中一根插入管(上升管)中通入驱动气体(惰性气体Ar),利用气泡泵的原理就能使钢包中的钢液上升,经真空室然后在重力的作用下从下降管回流入钢包而不断使钢水产生循环;同时,提升气体的另一个作用是使钢水在上升插入管内上升的过程中产生沸腾而大幅增加钢液与气相(上升插入管内钢水中的Ar气泡、真空室内的气体)的接触面积,由于气相中H2、N2的分压极低,溶解于钢液中的〔H〕、〔N〕便从钢液中逸出而进入气相。
在钢水循环的过程中,非金属夹杂物由于浮力的作用而上浮,钢水的成分和温度场分布得更加均匀,同时通过物料添加系统加入脱氧剂、脱硫脱磷剂、合金等使其具有脱氧、脱硫、脱磷,成分微调等多项冶金功能。
3.2钢水循环“气泡泵”原理由于真空室内外的压差,钢水从插入管上升进入真空室内,钢水上升的理论高度约1470mm,钢水同时受上升管驱动气体(一般为氢)的作用,像喷泉一样涌入真空室。
此时,真空室内的状态平衡受到破坏,为了保证平衡,部分钢水从下降管回到钢包中。
就这样,钢水受压差和驱动气体的作用不断从上升管涌入真空室内,并经下降管回到桶内,周而复始,实现了钢水循环。
钢水真空循环原理类似于“气泡泵”(见图1)。
当真空室底部的两个插入管插入钢水时,真空室抽成真空,大气和真空室之间形成压力差,钢水就从两个管子上升到与压差相等的高度,即循环高度B;但要实现钢水循环,还必须从上升管内输入驱动气体,驱动气体由于受热膨胀,以及压力由P1降低到P2而引起等温膨胀,即上升管内钢水与气体混合物密度降低,从而驱动钢水上升。
按能量守衡定律,气体膨胀功(A气体)等于被输送钢水上升所需的功(A钢木)与钢水和气体混合物克服上升过程中摩擦阻力所作的功(A损失)之和,即:式中V1—驱动气体按压力P1,计算的体积,m3;P1—驱动气体的压力,Pa;P2—真空室内压力,Pa;V0—准状态下驱动气体体积,m3;T1—驱动气体的温度,K;T2—钢水的温度,K;R—气体常数,8.314J/(K·mol);A钢水=M·H·g;式中M—从上升管进入真空室内的钢水量,kg;H—钢水的提升高度,m;g—重力加速度,9.81m/s2;实际上,A损失很小,A气体右边第二项值也很小,可以忽略不计,则有:可见,钢水的提升高度与驱动气体流量、压力和真空度有密切关系。
3.3真空脱气原理RH脱气方式有三种:在上升管中,钢液向氢气泡中脱气;在真空室内,钢液通过自由表面脱气;在真空室内氢气泡的破裂使钢水呈飞散的液滴而进入脱气。
气体在钢液内的溶解度与系统的压力有关,氢和氮在钢中的溶解度服从平方根定律,即冶金过程的各种化学反应都向平衡态方向自发进行。
气体在钢中的溶解与化学反应相似,抽真空降低系统内的气体分压Pe和PN,将引起平衡移动,使钢中的气体含量[H]和[N]降低。
所以要达到一定的脱气效果,就得造成一定的真空度。
溶解在钢液中的气体向气相的迁移过程由以下步骤所组成:(1)溶解在钢液中的气体原子通过扩散和对流迁移到钢液—气相界面;(2)气体原子由溶解状态转变为表面吸附状态:(3)表面吸附的气体原子彼此相互作用,生成气体分子:(4)气体分子从钢液表面脱附;(5)气体分子扩散进入气相,并被真空泵抽出。
在炼钢温度和一定真空度下,步骤(2)、(3)、(4)、(5)进行的相当迅速,脱气速度主要取决于步骤(1),即溶解在钢中的气体原子向液一气相界面的迁移。
因此,在抽真空的同时应加强钢液搅拌,加快脱气过程。
3.4真空脱氧原理在常压下碳的脱氧能力很弱,必须使用强脱氧剂(Si、Al等)脱氧,在真空条件下,碳的脱氧能力显著提高,因为碳氧反应生成CO气体,其反应式为:[C]+[O]=CO抽真空降低系统内CO的分压PCO,使化学平衡向着生成CO的方向移动,增强碳的脱氧能力,钢中的碳和氧含量降低。
在真空条件下,碳的脱氧能力达到和硅、铝相当的水平,并且碳的脱氧产物为CO气体,可以从钢液中排除,不会形成非金属夹杂物滞留在钢中影响钢的质量。
CO气体上浮过程中搅拌钢液造成沸腾,对脱氢和脱氮创造更为有利的条件。
总之,利用真空处理,可以使己经达到平衡的脱气、脱碳和脱氧反应继续进行,从而提高钢的质量。
真空度越高,各项反应的气体分压越低,反应进行的越充分。
3.5真空脱碳原理。