VD真空精炼技术与装备的发展
真空机械泵VD炉高效脱气工艺研究与应用

真空机械泵VD炉高效脱气工艺研究与应用摘要:为提高产品质量,提高特钢新区产品市场竞争力,在莱钢100电炉技术升级改造项目中,VD炉使用了机械真空泵、高效除尘、水冷屏蔽盖、干式密封、氩气分段梯度控制、吹氩模型控制以及双罐体、双罐盖等新设备、新技术、新工艺,实现了生产的顺利进行,提高了产品质量,具备开发高端产品的能力。
关键字:VD炉;机械泵;高效除尘;氩气分段梯度控制;吹氩模型控制1 引言莱钢100吨技术升级改造项目中,为了在产品结构及钢材品质方面得到进一步提升,引进VD真空精炼技术。
传统VD工艺所采用的真空设备均为多级蒸气喷射泵真空系统,但从国内外应用现状发现,多级蒸气喷射泵真空系统受到蒸气压力、温度的制约性较大,同时为遵循蒸气高效回收和利用(建设余热发电站)的理念,对VD真空系统进行研究,以确定新区VD炉的设计方案。
2 技术研究方案2.1生产线主要概况100t电炉偏心炉出钢→脱氧合金化→炉后底吹氩→LF炉底吹氩、调温、炉渣还原处理、成份精确控制→钢水钙处理→VD炉去气去夹杂→大圆坯连铸浇注→产品成材加工。
2.2 技术方案2.2.1 机械真空泵的应用目前VD设备、工艺均已成熟,传统VD工艺所采用的真空设备均为多级蒸气喷射泵真空系统,但从国内外应用现状发现,多级蒸气喷射泵真空系统受到蒸气的制约性较大,且蒸汽管道的布置会增加建设成本。
随着工艺技术的不断成熟,机械真空泵越来越多的应用到冶金行业,其具有能耗低,抽速稳定,维护简便,受外界因素影响小的特点,包钢、重钢等国内钢铁企业先后将机械真空泵应用到RH、VD等设备上,都取得了不错的效果,对此两种方式真空系统进行对比、论证,认为其可满足VD工艺技术要求,为此,莱钢120tVD真空系统决定采用干式(机械泵)真空泵。
2.2.1.1 机械真空泵系统的脱氢效果VD精炼炉内真空、强搅拌的环境为去除钢中氢创造了良好条件。
莱钢120tVD生产实践表明,钢水初始氢质量分数小于4.5×10-6,底吹Ar气流量为140~300NL/min时,钢水真空处理27min可将钢中氢脱至1.5×10-6以下,VD后平均[H]含量1.12PPM,最低达0.8×10-6,平均脱氢率73.33%,VD处理前后钢中氢含量见图2,其脱氢效果优于国内使用多级蒸气喷射泵的VD炉。
VD炉精炼工艺技术介绍
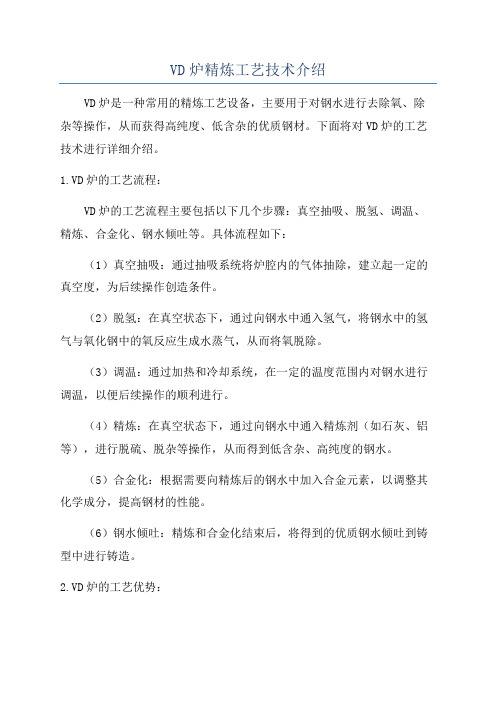
VD炉精炼工艺技术介绍VD炉是一种常用的精炼工艺设备,主要用于对钢水进行去除氧、除杂等操作,从而获得高纯度、低含杂的优质钢材。
下面将对VD炉的工艺技术进行详细介绍。
1.VD炉的工艺流程:VD炉的工艺流程主要包括以下几个步骤:真空抽吸、脱氢、调温、精炼、合金化、钢水倾吐等。
具体流程如下:(1)真空抽吸:通过抽吸系统将炉腔内的气体抽除,建立起一定的真空度,为后续操作创造条件。
(2)脱氢:在真空状态下,通过向钢水中通入氢气,将钢水中的氢气与氧化钢中的氧反应生成水蒸气,从而将氧脱除。
(3)调温:通过加热和冷却系统,在一定的温度范围内对钢水进行调温,以便后续操作的顺利进行。
(4)精炼:在真空状态下,通过向钢水中通入精炼剂(如石灰、铝等),进行脱硫、脱杂等操作,从而得到低含杂、高纯度的钢水。
(5)合金化:根据需要向精炼后的钢水中加入合金元素,以调整其化学成分,提高钢材的性能。
(6)钢水倾吐:精炼和合金化结束后,将得到的优质钢水倾吐到铸型中进行铸造。
2.VD炉的工艺优势:(1)高纯度:由于采用真空精炼技术,能够有效地去除钢水中的气体、杂质等有害元素,提高钢水的纯度和质量。
(2)高效节能:VD炉采用闭式工作,减少了钢水中的挥发损失,具有较高的加热效率和能源利用率。
(3)灵活可控:VD炉可以根据不同的工艺要求进行调整,如调节真空度、精炼时间、合金化元素等,以满足不同类型钢材的生产需求。
(4)环保安全:VD炉在操作过程中采用真空技术,不会产生大量的粉尘、废气等污染物,符合环境保护和安全生产的要求。
3.VD炉的应用领域:VD炉广泛应用于钢铁冶金领域,特别是在高品质、特种钢材的生产中起到重要作用。
它适用于生产高速钢、合金结构钢、工具钢、耐热钢、耐腐蚀钢等。
在钢铁工业中,VD炉已成为一种不可或缺的关键设备。
总之,VD炉是一种重要的精炼工艺设备,通过真空操作和精炼剂的加入,可以高效去除钢水中的氧、气体和杂质等,获得高纯度、低含杂的优质钢材。
金属冶炼中的真空冶炼技术
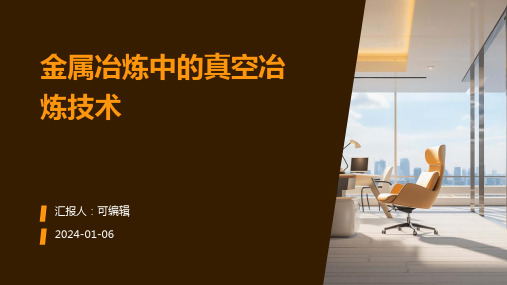
对于一些难以通过常规方法制备的特殊合金,如高强度铝合金、钛 合金等,真空感应熔炼技术也具有显著优势。
有色金属熔炼
除了钢铁等黑色金属外,真空感应熔炼技术也可应用于铜、铝等有 色金属的熔炼和提纯。
CHAPTER 03
真空电弧熔炼
真空电弧熔炼原理
真空电弧熔炼是在高真空条件下,利 用电流通过金属电极(通常为两根石 墨电极)产生电弧来熔炼金属的工艺 。
金属冶炼中的真空冶 炼技术
汇报人:可编辑 2024-01-06
目录
• 真空冶炼技术概述 • 真空感应熔炼 • 真空电弧熔炼 • 真空电子束熔炼 • 真空冶炼技术的发展趋势与展望
CHAPTER 01
真空冶炼技术概述
定义与原理
定义
真空冶炼技术是指在真空环境中进行 的金属冶炼过程,通过降低压力和气 体含量,实现金属的高效提取和纯化 。
电子枪是设备的核心部分 ,能够产生高能电子束。
真空室用于提供熔炼所需 的真空环境,同时收集和 排出熔炼过程中产生的气 体和烟尘。
控制系统用于控制设备的 各项参数,保证熔炼过程 的稳定性和准确性。
冷却系统用于控制设备的 温度,保证设备的稳定运 行。
真空电子束熔炼工艺参数
真空度
电子束功率
真空度是影响熔炼过程的重要参数,它决 定了熔炼过程中气体的分压,从而影响金 属的纯度和凝固组织。
真空电子束熔炼
真空电子束熔炼原理
电子束熔炼是一种利用高能电 子束作为热源的真空熔炼技术 。
电子束熔炼过程中,高能电子 束与金属材料相互作用,使金 属材料熔化并形成液态金属。
液态金属在真空环境下进行净 化、精炼和凝固,最终得到高 纯度、高性能的金属材料。
真空电子束熔炼设备
真空精练炉(VD、VOD)设备真空罐及真空罐车简介

真空精练炉(VD、VOD)设备真空罐及真空罐车简介孙东月【摘要】真空精练炉(VD和VOD)主要用于钢水进一步精炼。
它是将钢包置于真空罐体内,在真空条件下脱碳精炼。
是炉外精炼超低碳不锈钢和各类高级合金钢主要设备。
真空罐及真空罐车为将真空罐安装到可移动的车辆上,车上同时设有配套的冷却系统、吹氩管路和观察系统。
该真空罐及真空罐车为精炼钢包抽真空提供基础承载体。
【期刊名称】《黑龙江科技信息》【年(卷),期】2015(000)009【总页数】1页(P37-37)【关键词】真空精炼炉;精炼;真空罐及真空罐车;抽真空【作者】孙东月【作者单位】秦皇岛秦冶重工有限公司,河北秦皇岛 066318【正文语种】中文真空罐及真空罐车是将真空罐、车设计为一体车辆。
车上设有配套的水冷循环管路,吹氩管路,为精炼钢包抽真空提供基础设备。
传统上的真空罐冶炼设备真空罐为地坑固定式结构。
本次设计研制的真空罐及真空罐车为整体车辆,可实现在精炼过程中整体移动,操控方便,更加安全可靠。
以往,VD炉精炼使用的精炼罐体为固定式不可移动,需用钢包车将其精炼钢包运至后用吊车放入精炼罐体内。
随着产品设计的不断发展与完善,对新产品的不断开发与研制,将精炼罐体与运载用钢包车合为一体,实现精炼钢包的一次吊运,精炼罐体可移动,省去运载用的钢包车。
整套设备操控简单,使用安全。
最大总载重-265t;走形速度-2-20m/min(变频调速);传动方式-电动自行式,分散驱动;走行电机功率-18.5×2KW;车轮直径-φ1000;轨道中心距-4800mm;行程-47m;车轮数量-4个;定位方式-行程开关(地面安装);供电方式-滑线小车式(地面安装)。
真空罐及真空罐车主要由钢包座、车架装配、紧急事故口、从动轮组、推渣器、缓冲器、传动装置、罐上体、平台装配、布管配线、滑线供电装置、热电偶装置等部件组成。
主要机构简图如图1。
4.1 钢包座。
钢包座为低碳钢板焊接件,共两件。
VD真空精炼技术与装备的发展
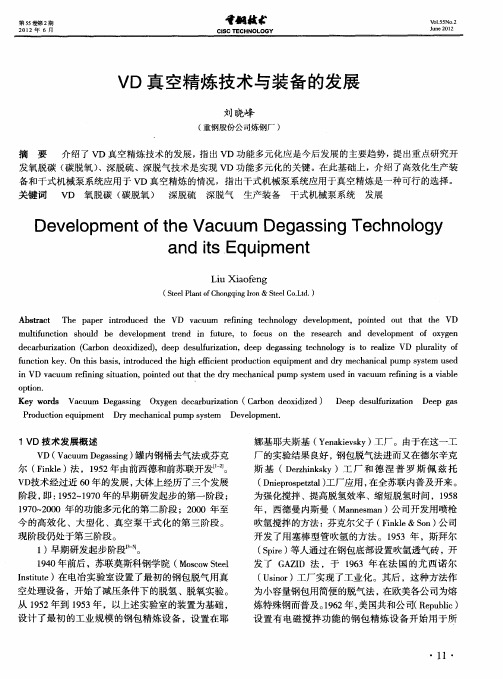
CI EC SC T HN L O OGY
VD真 空精 炼技术与装备 的发展
刘 晓峰
( 重钢股份公 司炼钢厂 )
摘
要 介 绍 了 VD真 空精 炼 技术 的发 展 , 出 V 功 能多元 化应 是今 后发 展 的主要 趋势 , 出重 点研 究开 指 D 提
发氧 脱碳 ( 脱氧 ) 碳 、深脱硫 、深脱 气技 术 是实现 VD功 能 多元化 的关键 。在此 基础 上 ,介 绍 了高效化 生产 装 备和 干式 机械 泵 系统应 用 于 vD真 空 精炼 的情 况 ,指 出干式 机械 泵系 统应 用于 真 空精炼 是一 种可行 的选择 。 关 键词 V D 氧脱 碳 ( 碳脱 氧 ) 深脱硫 深脱 气 生产 装备 干 式机 械泵 系统 发 展
超 低碳 钢 ,供应 板坯 连 铸机 ,而且 已获得 了很好 的 处理效果口 。2 世纪 8 年代中后期 ,德国Dlne 0 0 i gn l i 钢 铁公 司 、 鲁伯 一曼 内斯曼 H t n 克 ut 钢厂 开发 成功 了 e 生产 极低 硫钢 的V D ( au m T n easr T V cu akD gse )真空 大 流量搅 拌精 炼工 艺 。Dlne钢铁 公 司至今 一直采 iign l 用 该工 艺 , 年产 优质 中厚板 20万 t 0 左右 , 中 9 % 其 0 以上产 品【] 于 00 1 。 国Slc l ag钢厂 S低 . 0% 法 0 oa o ne l Fr 的一套 V 装 置 月处理 钢水 约 l D 2万t ,其 中 4 2%供 给
De elp v o men f h c u De a sn c n l y to e Va u m g s ig Te h oog t
an s, u p d i Eq i me t t n
VD真空精炼技术与装备的发展

VD真空精炼技术与装备的发展刘晓峰(重庆钢铁股份有限公司炼钢厂重庆 401258)摘要:介绍了VD真空精炼技术的发展,指出VD功能多元化应是今后发展的主要趋势,提出重点研究开发氧脱碳(碳脱氧)、深脱硫、深脱气技术是实现VD功能多元化的关键。
在此基础上,介绍了高效化生产装备和干式机械泵系统应用于VD真空精炼的情况,指出干式机械泵系统应用于真空精炼是一种可行的选择。
关键词:VD;氧脱碳(碳脱氧);深脱硫;深脱气;生产装备;干式机械泵系统;发展。
The development of vacuum Degassing technology andequipmentXiaofeng-Liu(Chongqing Iron and Steel Co., Steel Plant Chongqing 401258)Abstract :Introduced the VD vacuum refining technology development, pointed out that the VD diversity function should be the future development trend, to focus on the research and development of oxygen decarburization (Carbon deoxidized), deep desulfurization, deep degassing technology is to realize VD plurality of function key. On this basis, introduced the high efficient production equipment and dry mechanical pump system used in VD vacuum refining situation, pointed out that the dry mechanical pump system used in vacuum refining is a viable option.Key words :Vacuum Degassing;Oxygen decarburization(Carbon deoxidized);Deep desulfurization;Deep gas;Production equipment;Dry mechanical pump system;Development。
首钢第三炼钢厂的VD精炼设备系统
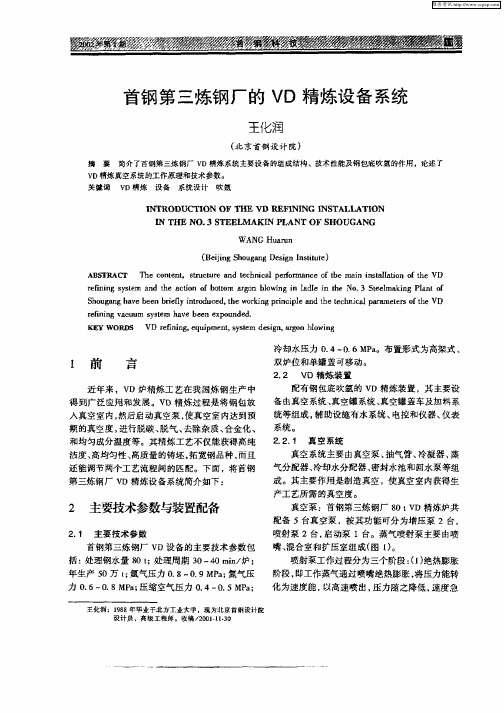
备由真空系统 、 真空罐系统 、 真空罐 盖车及加料系 统等组成 , 辅助设施有水系统、 电控和仪器、 仪表
系统 。 221 .. 真空 系统
人真空室内, 然后启动真空泵 , 使真空室内达到预 期的真空度 , 进行脱碳、 脱气、 去除杂质、 舍金化、 和均匀成分温度等。其精炼工艺不仅能获得高纯 洁度、 高均匀性 、 高质量的铸坯 , 拓宽钢品种 , 而且 还能调节两个工艺流程问的匹配。下面 , 将首钢 第三炼钢厂 V D精炼设备系统简介如下 :
真空技术在冶金工业中的应用与发展趋势
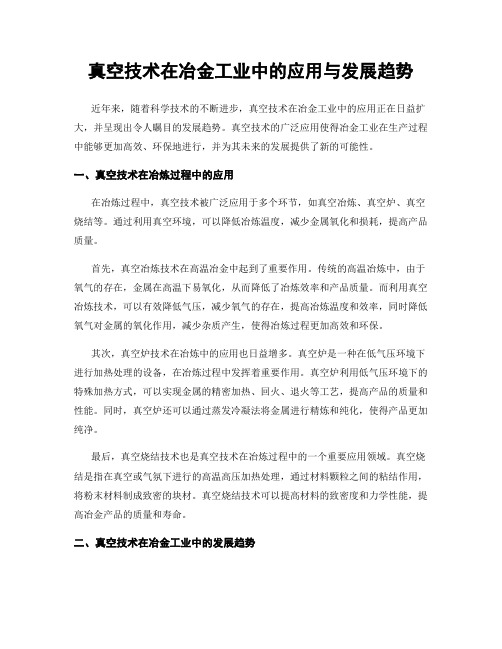
真空技术在冶金工业中的应用与发展趋势近年来,随着科学技术的不断进步,真空技术在冶金工业中的应用正在日益扩大,并呈现出令人瞩目的发展趋势。
真空技术的广泛应用使得冶金工业在生产过程中能够更加高效、环保地进行,并为其未来的发展提供了新的可能性。
一、真空技术在冶炼过程中的应用在冶炼过程中,真空技术被广泛应用于多个环节,如真空冶炼、真空炉、真空烧结等。
通过利用真空环境,可以降低冶炼温度,减少金属氧化和损耗,提高产品质量。
首先,真空冶炼技术在高温冶金中起到了重要作用。
传统的高温冶炼中,由于氧气的存在,金属在高温下易氧化,从而降低了冶炼效率和产品质量。
而利用真空冶炼技术,可以有效降低气压,减少氧气的存在,提高冶炼温度和效率,同时降低氧气对金属的氧化作用,减少杂质产生,使得冶炼过程更加高效和环保。
其次,真空炉技术在冶炼中的应用也日益增多。
真空炉是一种在低气压环境下进行加热处理的设备,在冶炼过程中发挥着重要作用。
真空炉利用低气压环境下的特殊加热方式,可以实现金属的精密加热、回火、退火等工艺,提高产品的质量和性能。
同时,真空炉还可以通过蒸发冷凝法将金属进行精炼和纯化,使得产品更加纯净。
最后,真空烧结技术也是真空技术在冶炼过程中的一个重要应用领域。
真空烧结是指在真空或气氛下进行的高温高压加热处理,通过材料颗粒之间的粘结作用,将粉末材料制成致密的块材。
真空烧结技术可以提高材料的致密度和力学性能,提高冶金产品的质量和寿命。
二、真空技术在冶金工业中的发展趋势随着冶金工业的不断发展,真空技术在其中的应用也在不断创新和完善。
未来,真空技术在冶金工业中的发展主要呈现以下几个趋势。
首先,真空技术将更加广泛地应用于新材料的开发和制备。
新材料是冶金工业的一个重要方向,而真空技术可以在新材料的制备过程中发挥关键作用。
例如,利用真空技术可以在材料的制备过程中控制气氛和温度,实现复杂材料的精密控制和调控,制得高性能的新材料。
其次,真空技术在冶金生产中的自动化和智能化水平将会不断提高。
VD设备及典型钢种的冶炼工艺
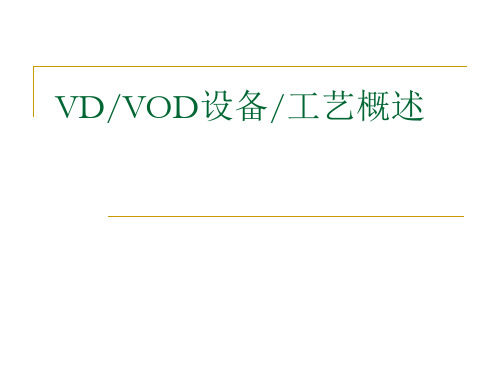
年日本开发的成分调整密封吹氩法(CAS法)。
真 空 处理
1-滴流钢包脱气法 2—真空浇注法 3—出钢脱气法 4—真空循环脱气法
从渣中转入脱氧后的钢水; 有效方法:减少渣量,不提高碱度,降低Al2O3含量,使用MgO代
替CaO
例:与大气平衡的铁液中的ω[C]=2%, ω[Ti]=2%, ω[H]=1.0×10-3%,欲 使[H]下降到0.1×10-3%,试问需要采取多大的真空度,T=1600℃。
关于脱氢时间的计算
VD精炼需考虑问题
质量定律:[C]·[O]=KCO·PCO 影响因素:进真空前温度;破真空温度;真空保持时间;真
空处理时间;Ar气流量;吨钢耗Ar量(马鞍山钢厂)
脱硫:CO分压降低,O浓度降低,为进一步脱 S提供热力学条件
夹杂物变性处理: 3Ca+Al2O3→3CaO+2Al xCaO+yAl2O3→(CaO)x(Al2O3)y 喂钙丝,使滞留在钢水中的固态Al2O3夹杂
真空度问题:真空度对应气体的最终含量 温降问题:一般认为脱气过程中温降2-
3℃/min,在初炼炉或精炼炉中考虑温度因素 脱氧效率的影响因素:进真空前温度;破真空
温度;真空保持时间;真空处理时间;Ar气流 量;吨钢耗Ar量(马鞍山钢厂)
VD前的精炼工艺要点
电炉采用氧化法,原料采用 精炼工艺:吊包入罐;启动吹氩;测温取样;
◆VD( Vacuum Degassing)法是将 转炉、电炉的初炼钢水置于真空室 中,同时钢包底部吹氩搅拌的一种 真空处理法。可进行脱碳、脱气、 脱硫、去除杂质、合金化和均匀钢 水温度、成分等处理。其主要设备 由真空系统、真空罐系统、真空罐 盖车及加料系统组成。适于生产各 种合金结构钢、优质碳钢和低合金 高强度钢。
RH、LF和VD炉外精炼技术

通电时,采用小流量吹 Ar,均匀温度又不引起大的 液面波动.
28
③造渣制度
目 的:
脱S、脱O、去夹杂; 提高炉衬寿命; 防止钢水二次氧化,提高合 金收得率。
基本制度:
渣料加入量8-10Kg/t; 分 批 加 入 , 出 钢 过 程 加 4050%,其余待化渣后分2-3次加入; 炉渣过稠加CaF2,炉渣过稀加 CaO.
4
2.炉外精炼的发展
• 20世纪30年代 • 20世纪40年代 • 20世纪50年代 • 20世纪60,70年代 • 20世纪80年代
多的R(理包HD有(种精-HO循C形炼)BA环使渣高式)大泵真炉,S在钢理合在V,真发钢用C进,,问抽空;金低水O提真A空真展水高行D微S世速法真进升空处-空,质碱O调脱理真,蒸 用吹空 行、B广脱D量及度S)(空H氩度 脱泛汽 于温气;以合V,R、L处脱应度下 气基A喷 钢HF成提D理,处氧用R钢对 处础射 水H上、,
7
4.炉外精炼方法的共同特点
• ①理想的精炼气氛条件,通常应用真空、 惰性气氛或还原气氛;
• ②搅动钢水,采用电磁力、惰性气体或机 械搅拌的方法;
• ③为补偿精炼过程的钢水温度损失,采用 加热设施有电弧加热、等离子加热或增加 钢水中的化学热等。
8
二.RH、LF及VD法简介
RH 法 LF 法 VD 法
34
④事故搅拌装置
作 用:
在透气砖不能工作情况 下,惰性气体通过顶枪吹入 钢包,进行事故搅拌;
结 构:
顶枪安装在支撑框架上, 支撑框架安装在炉盖侧面, 顶枪通过电动机和卷筒实现 上下;
参 数:
顶枪压力:0.6-1.6MPa; 流量(max):600NL/min
VD精炼与RH精炼的投资、设备及工艺的比较

VD精炼与RH精炼的投资、设备及工艺的比较VD精炼与RH精炼的投资、设备及工艺的比较1.RH法脱气原理:它是在脱气室下部设有与其相通的两根环流管,脱气处理时,仅将环流管插入钢液,靠脱气室抽真空的压差使钢液进入脱气室中,分批连续地真空处理,并在脱气室内脱除气体。
2.RH工艺处理特点:a.脱气效果较好因进入脱气室的钢液量相对较小,或处于激烈沸腾状态,而大大增大了钢液脱气表面积,有利于脱气。
b.适于大量的钢液处理c.处理过程温降小,因钢液表面有炉渣覆盖,保温效果较好,一般处理后温降为30~50℃左右,通常处理周期为20min左右。
d.脱碳能力强,适用于低碳钢生产。
3.RH设备主要组成:脱气室本体;脱气室的支持装置及升降机构(随结构型式而定)以及移动台车等;加热装置,即对脱气室进行预热;加料系统,对钢液成分进行调整,加入脱氧剂等;真空泵及管道。
4.RH精炼效果RH精炼机能是真空冶炼和搅拌,由此产生主要效果为脱氢、脱氧和脱氮;成分、温度均匀化;去除非金属夹杂物。
a.脱氢:其脱氢率约在40~80%的范围,处理后的氢含量为1~3ppm,要达到<2ppm以下的水平比较容易,b.脱氧:一般情况,处理前的氧含量水平低,则处理后的氧含量也较低,在强脱氧的条件下,可将精炼末期的全氧量降至20ppm以下。
c.脱氮:因氮的扩散速度小,所以,在钢中氮的变化不大,经过RH处理后,钢水中氮的含量在40ppm左右,其脱氮率约为25%。
d.去夹杂:经过RH处理后,能够显著地降低钢中夹杂物量(以及氧含量)e.合金收得率提高及钢村性能的改善。
5.RH操作的特点及耐材的消耗由于RH处理的脱气室处在高温、真空和钢液激烈冲刷下工作,所处的条件相当恶劣,特别是处理高合金钢时,处理时间延长,连铸时钢液温度提高等,使耐火材料使用寿命问题更为突出。
造成对真空处理费用增大,还对设备的操作和处理能力、处理效果造成影响。
另外,其钢液循流管因钢液对管子内壁的机械磨损很大,而且管外壁易粘附炉渣,去除时造成一些破损等,造成常影响生产的产量。
杭钢100吨VD炉真空脱气工艺的开发与完善

世 纪末 世 界先进 水平 的真空 二次 精 炼设 备 , 具 有 双 工位 的处理 功 能 , 其 生 产 能 力 为年 产 7 0万 吨 。V D
炉主要 有 真 空 站 、 抽气管道 、 冷凝器 、 真空泵 、 蒸 汽 供 应 系统 、 能源动力系统 、 测 量 系统 等 组 成 。其 中 真空泵 为蒸 汽 喷 射 泵 , 共五级 ( 七个) 真空泵 , 能 够
泵, C 3冷凝 器 , 炉气 及 蒸 汽 在冷 凝 器 中与 冷凝 水 进
行热 交 换 , 部 分 蒸 汽 转 化 成 液态 水 进 入 热 水 井 , 排 到大 气 中 , 从 而 达 到 抽 出 炉气 的作 用 , 其 系统 原 理
如图是将 钢 包 置 于 真 空 罐 中进 行 真 空 处 理 , 以
度越小 , 越有利于钢中 自由气体原子的排 除, 提高
脱 气率 , 如图 2 。真 空 度 在 1 0 0 P a以 上 时 , 即使 长 ( 2 )
[ X] _ 脱气热 力 学可表 示 为
时间保温 , V D的脱氢率也不高 , 基本都维持在 3 5 % 以下。因此 , 要满足 V D脱氢要求 , 必须适 当提高真 空度 。根据 生产 实 际和设 备 抽真 空 的设 计 能力 , 优 化 后 的真 空度要 求 为 6 7 P a 。
4 m i n , 就 能够 供 出满足 工作要 求 的 1 . 4 M P a 、 2 1 0  ̄ C的
蒸汽 。
2 0 1 5年 8月 第三期
杭钢 1 0 0吨 V D炉真 空脱 气 工艺 的开发 与 完善
3 1
根据表 1 , 经V D处理后钢 中氮 、 氧、 氢气体含 量均有较大程 度的下降 , 其 中氮含量下 降了 2 7 %, 氢含 量下 降 了 5 9 %, 氧含 量 下 降 了 2 4 %, 脱 气 效 果
电炉AOD炉LF炉VD真空炉的原理与作用

电炉AOD炉LF炉VD真空炉的原理与作用1.电炉:电炉通过通电加热将电能转化为热能,用来加热原料并进行冶炼和熔炼操作。
电炉的原理是利用电流通过导体时产生的电阻发热效应。
电炉可以分为直接电炉和间接电炉两种类型。
直接电炉即高频感应加热炉,原理是通过将高频交流电导入导体中,利用导体本身的电阻使其加热;间接电炉则是通过将电流导入电极,再通过电极与物料形成电弧放电,从而加热原料。
电炉可用于生产钢铁、合金、非金属材料等。
2.AOD炉:AOD炉即精炼氧气转炉,是不锈钢冶炼中常用的设备。
AOD炉的原理是将高温的氧气与炉内的熔融金属进行反应,从而实现炉内不锈钢的冶炼和精炼。
AOD炉的作用是降低金属中的碳含量和其他杂质,调整合金成分,提高不锈钢的质量和性能。
AOD炉还可以进行脱硫、脱氮等处理。
3.LF炉:LF炉即转炉精炼炉,是钢铁冶炼过程中用于调整钢液成分和温度的设备。
LF炉的原理是通过将炉外高频电感与炉内熔融金属的电流产生耦合,利用电磁感应加热和搅拌钢液。
LF炉的作用包括去除钢液中的气泡、杂质,脱气、降温和熔化等。
LF炉还可以进行脱硫、脱氮、合金调整等处理。
4.VD真空炉:VD真空炉是真空冶炼的设备,主要用于不锈钢和合金的冶炼和精炼。
VD真空炉的原理是通过抽空炉腔,将炉内的气体压力降低到一定程度,利用炉内的电感和电极产生的电弧放电加热金属和进行冶炼。
VD真空炉的作用主要是去除钢液中的气体、氧化物等杂质,降低碳含量,调整合金成分,并且提高钢液的纯净度和质量。
综上所述,电炉是通过电能转化为热能进行冶炼的设备,AOD炉和VD真空炉是用于不锈钢和合金的冶炼和精炼的设备,LF炉则是用于钢铁冶炼中的调整成分和温度的设备。
这四种炉子在各自领域中有着重要的作用,对于提高材料质量和性能具有重要意义。
新建VD的技术特点及冶金效果

摘 要: 包头钢铁( 集团) 公司钢联股份有限 公司炼钢厂新建的 3 号 V D 真空脱 气装置, 在设计上采取了 双盖双罐位布置方式; 真空系统采用了高效多重变量真 空泵技 术和高 效冷却 除尘等先 进技术。 这些技 术的使用能够有效地提高真空泵 的使 用寿命, 缩 短 VD 的 处理周 期, 并能 较好地 与铸 机浇 铸周期 相匹 配。实践证明达到了预期的冶金效果, 提高了铸机生产率。 关键词: 炉外精炼; V D; 冶金 效果 中图分类号: T F769. 4 文献标识码: B 文章编号: 1002 1043( 2010) 03 0018 04
表 1 1 号和 3 号 VD 主要参数对比
VD 装置
1号
设计 单位 德国麦索 冶金公司
钢包容 量/ t
83
钢包自由 空间/ mm
900
处理能 抽真空能力/ 力/ 万 t ( kg# h- 1 )
725
温降/
蒸汽压 蒸汽用量/
( ∃ # min- 1 ) 力/ M Pa ( t# h- 1 )
VD精炼装置设备设计
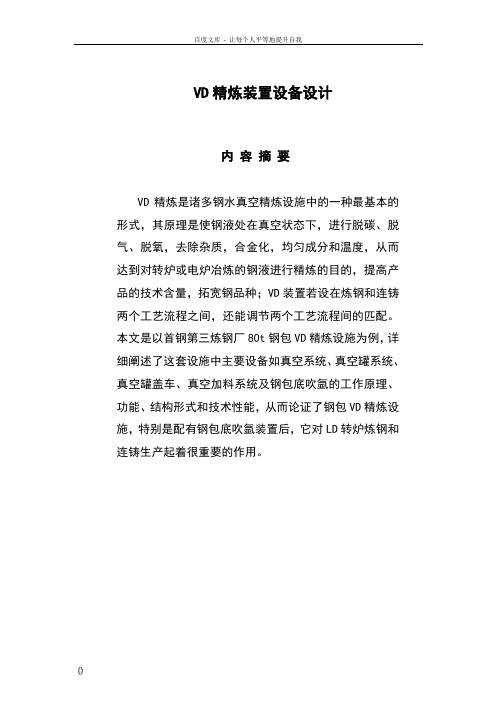
VD精炼装置设备设计内容摘要VD精炼是诸多钢水真空精炼设施中的一种最基本的形式,其原理是使钢液处在真空状态下,进行脱碳、脱气、脱氧,去除杂质,合金化,均匀成分和温度,从而达到对转炉或电炉冶炼的钢液进行精炼的目的,提高产品的技术含量,拓宽钢品种;VD装置若设在炼钢和连铸两个工艺流程之间,还能调节两个工艺流程间的匹配。
本文是以首钢第三炼钢厂80t钢包VD精炼设施为例,详细阐述了这套设施中主要设备如真空系统、真空罐系统、真空罐盖车、真空加料系统及钢包底吹氩的工作原理、功能、结构形式和技术性能,从而论证了钢包VD精炼设施,特别是配有钢包底吹氩装置后,它对LD转炉炼钢和连铸生产起着很重要的作用。
1. 前言VD(Vacuum Degassing)是指钢水真空脱气设施,它脱气的原理是由于钢液处在真空状态下,使钢液内部气体外溢,从而减少了钢液中的有害气体含量,达到纯净钢液的目的。
整个处理过程简述如下:首先将经过转炉或电炉冶炼的钢液倒入钢包中,再将钢包运送到处理工位,放入真空室内,然后启动真空泵,使真空室内达到预期的真空度,在这种氛围下,进行脱碳、脱气、去除杂质、合金化、均匀成分温度等精炼过程。
若在钢包底部配上吹氩装置,对包中钢液进行充分搅拌,就能得到更佳的精炼效果,并缩短精炼时间。
VD装置一般设在炼钢和连铸两个工艺流程之间,不仅能获得高纯洁度、高均匀性、高质量的铸坯,拓宽钢品种;而且还能调节两个工艺流程间的匹配,意义重大,为此近年来,炉外精炼在我国炼钢生产中得到充分的应用和发展。
炉外精炼方式很多,如:VD、VOD、VHD、RH、SKF等等,选用那种方式,主要决定于生产品种和连铸生产的要求。
首钢三炼钢为了提高自身产品质量和生产一些附加值高的品种钢,在精炼环节上,相继上了一台80t LF炉和一台80t VD炉,从而使该厂在市场竞争中更具灵活性和竞争力。
首钢三炼钢80t VD装置的主要技术参数如下:处理钢水量: 80t处理周期: 30~40min/炉年生产能力: 50万t布置形式:高架、双炉位、单罐盖可移动氩气压力: ~氮气压力: ~压缩空气压力: ~冷却水压力: ~2. VD装置的设备组成配有钢包底吹氩的VD装置,它的主要设备是由真空系统、真空罐系统、真空罐盖车及加料系统等组成。
VD真空精炼炉基本工艺操作规程
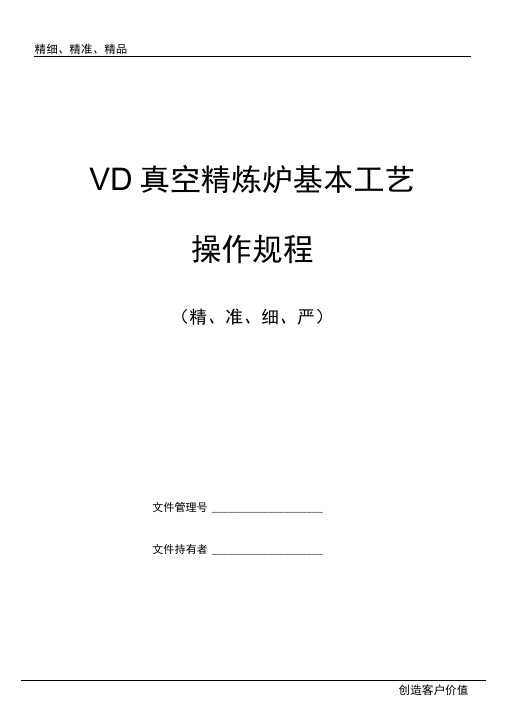
气弱搅拌10~12min),再吊入浇注位。
3.1.8加大包覆盖剂 吊包上连铸或铸锭前向钢包内加大包覆盖剂保温,加入量0.6kg/t,保证覆盖剂均匀覆盖钢液面。
4
4.1《炼钢厂分钢种工艺标准卡》
4.2其它相关技术文件
精细、精准、精品
VD
(精、准、细、严)
文件管理号
文件持有者
版本:A
更改:0
VD真空炉基本工艺操作规程
编号.
页次:1
1、工艺流程
2、VD设备性能及工艺参数
3、VD操作控制原理
4、相关技术规定
A
版本号
编写
审核
批准
批准日期
实施日期
编号:
VD
页次:2
1
1.1炼钢厂工艺流程图
电弧炉炼钢---炉外精炼(LF、VD)---连铸/钢锭
束,应将氩气流量调至80NL/min左右,然后再冲压缩空气或氮气破真空。
3.1.4为保证去气效果,要求VD处理时间》20min其中工作真空度为67Pa的高真空时间>15min或根据《炼 钢厂分钢种工艺标准卡》相关规定执行。
3.1.5温度控制:进VD温度控制在液相线+150C以上(参考值:VD处理25~30min钢水整体降温约80~85C)。
3
3.1 VD工艺操作原则
3.1.1钢包在真空罐中就位后,打开氩气阀门,将流量调至渣面轻微蠕动时停止,盖好真空罐盖,即可开始 真空处理。
3.1.2抽真空操作按相关操作规程进行。
3.1.3 VD处理过程中,要注意控制和调节吹氩流量。根据监视器观察渣面高度和喷溅情况,调节氩气流量。 在各级泵启动,真空度升高过程中,如产生溢渣和喷溅,应降低氩气流量,必要时可短时间停氩。各级 泵全部启动完毕后,包内渣面趋向稳定时,应逐渐加大氩气流量,以达到良好的脱气效果。VD处理结
VD真空系统原理与系统改造
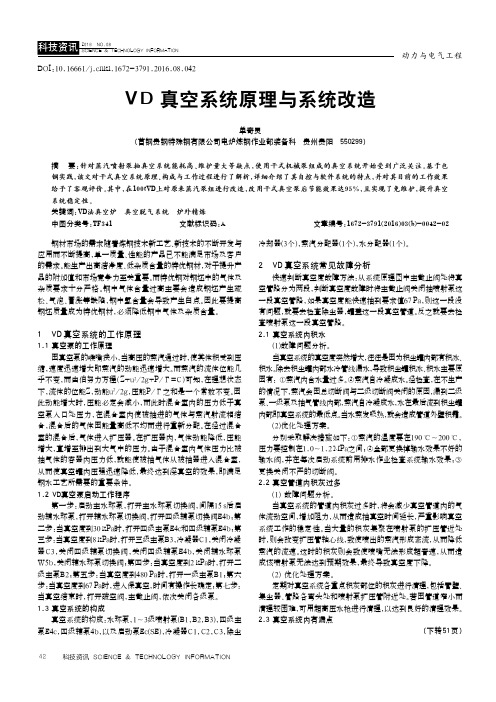
科技资讯2016 NO.08SCIENCE & TECHNOLOGY INFORMATION动力与电气工程42科技资讯 SCIENCE & TECHNOLOGY INFORMATION钢材市场的需求随着炼钢技术新工艺、新技术的不断开发与应用而不断提高,单一质量、性能的产品已不能满足市场及客户的需求。
能生产出高洁净度、低杂质含量的特优钢材,对于提升产品的附加值和市场竞争力至关重要。
而特优钢对钢坯中的气体及杂质要求十分严格。
钢中气体含量过高主要会造成钢坯产生疏松、气泡、冒涨等缺陷,钢中氢含量会导致产生白点。
因此要提高钢坯质量成为特优钢材,必须降低钢中气体及杂质含量。
1 VD 真空系统的工作原理1.1 真空泵的工作原理因真空泵的喉嘴狭小,当高压的蒸汽通过时,使其体积受到压缩,速度迅速增大即蒸汽的动能迅速增大。
而蒸汽的流体位能几乎不变,而由伯努力方程(Z+u 2/2g+P/Γ=C)可知,在理想状态下,流体的位能Z,动能u 2/2g,压能P/Γ之和是一个常数不变。
因此动能增大时,压能必定会减小,而此时混合室内的压力低于真空泵入口处压力,在混合室内使被抽进的气体与蒸汽射流相结合,混合后的气体因能量高低不均而进行重新分配。
在经过混合室的混合后,气体进入扩压器。
在扩压器内,气体动能降低,压能增大,直增至排出到大气中的压力。
由于混合室内气体压力比被抽气体的容器内压力低,就能使被抽气体从被抽器进入混合室,从而使真空罐内压强迅速降低,最终达到深真空的效果,即满足钢水工艺所需要的重要条件。
1.2 VD真空泵启动工作程序第一步:启动主水环泵,打开主水环泵切换阀,间隔15s后启动辅水环泵,打开辅水环泵切换阀,打开四级辅泵切换阀E4b;第二步:当真空度到30kPa时,打开四级主泵E4c和四级辅泵E4b;第三步:当真空度到8kPa时,打开三级主泵B3,冷凝器C1,关闭冷凝器C3,关闭四级辅泵切换阀,关闭四级辅泵E4b,关闭辅水环泵W5b,关闭辅水环泵切换阀;第四步:当真空度到2kPa时,打开二级主泵B2;第五步:当真空度到480Pa时,打开一级主泵B1;第六步:当真空度到67Pa时,进入保真空,时间有操作长确定;第七步:当真空结束时,打开破空阀,主截止阀,依次关闭各级泵。
vd等炼钢工艺流程简介

vd等炼钢工艺流程简介The process of VD refining in steelmaking is essential for producing high-quality steel. VD refining, also known as vacuum degassing, is a method used to remove unwanted gases like hydrogen and nitrogen from molten steel to improve its purity and mechanical properties. In this process, the molten steel is transferred to a vacuum chamber where it is heated and degassed, resulting in a cleaner and more homogenous product.VD炼钢工艺对于生产高品质的钢材至关重要。
VD炼钢,也被称为真空脱气,是一种用来去除熔融钢中不需要的氢气和氮气,以提高其纯度和力学性能的方法。
在这个过程中,熔融钢被转移到真空室中,在那里加热和脱气,从而获得更清洁和更均匀的产品。
One of the main benefits of VD refining is the removal of impurities in the steel, which can greatly improve the overall quality and performance of the final product. By removing unwanted gases and non-metallic inclusions, VD refining helps to enhance the mechanical properties of the steel, making it more suitable for variousapplications in industries such as automotive, construction, and manufacturing.VD炼钢的主要好处之一是去除钢中的杂质,这可以大大提高最终产品的整体质量和性能。
- 1、下载文档前请自行甄别文档内容的完整性,平台不提供额外的编辑、内容补充、找答案等附加服务。
- 2、"仅部分预览"的文档,不可在线预览部分如存在完整性等问题,可反馈申请退款(可完整预览的文档不适用该条件!)。
- 3、如文档侵犯您的权益,请联系客服反馈,我们会尽快为您处理(人工客服工作时间:9:00-18:30)。
VD真空精炼技术与装备的发展刘晓峰(重庆钢铁股份有限公司炼钢厂重庆 401258)摘要:介绍了VD真空精炼技术的发展,指出VD功能多元化应是今后发展的主要趋势,提出重点研究开发氧脱碳(碳脱氧)、深脱硫、深脱气技术是实现VD功能多元化的关键。
在此基础上,介绍了高效化生产装备和干式机械泵系统应用于VD真空精炼的情况,指出干式机械泵系统应用于真空精炼是一种可行的选择。
关键词:VD;氧脱碳(碳脱氧);深脱硫;深脱气;生产装备;干式机械泵系统;发展。
The development of vacuum Degassing technology andequipmentXiaofeng-Liu(Chongqing Iron and Steel Co., Steel Plant Chongqing 401258)Abstract :Introduced the VD vacuum refining technology development, pointed out that the VD diversity function should be the future development trend, to focus on the research and development of oxygen decarburization (Carbon deoxidized), deep desulfurization, deep degassing technology is to realize VD plurality of function key. On this basis, introduced the high efficient production equipment and dry mechanical pump system used in VD vacuum refining situation, pointed out that the dry mechanical pump system used in vacuum refining is a viable option.Key words :Vacuum Degassing;Oxygen decarburization(Carbon deoxidized);Deep desulfurization;Deep gas;Production equipment;Dry mechanical pump system;Development。
1、VD技术的发展VD(Vacuum Degassing)罐内钢桶去气法或芬克尔(Finkle)法,1952年由前西德和前苏联开发[1-2]。
VD精炼技术经过近60年的发展,大体上经历了三个发展阶段,即:1952年~1970年的早期研发起步的第一阶段;1970年~2000年的功能多元化的第二阶段;2000年至今的高效化、大型化、真空泵干式化的第三阶段。
现阶段仍处于第三阶段。
(1)早期研发起步阶段[3-5]。
1940年前后,苏联莫斯科钢学院(Moscow Steel Institute)在电冶实验室设置了最初的钢包脱气用真空处理设备,开始了减压条件下的脱氢、脱氧实验。
从1952年到1953年,以上述实验室的装置为基础,设计了最初的工业规模的钢包精炼设备,设置在耶娜基耶夫斯基(Yenakievsky)工厂。
由于在这一工厂的实验结果良好,钢包脱气法进而又在德尔辛克斯基(Derzhinksky)工厂和德涅普罗斯佩兹托(Dnieprospetztal)工厂应用,在全苏联内普及开来。
为强化搅拌、提高脱氢效率、缩短脱氢时间,1958年,西德曼内斯曼(Mannesman)公司开发用喷枪吹氩搅拌的方法:芬克尔父子(Finkle & Son)公司开发了用塞棒型管吹氩的方法。
1953年,斯拜尔(Spire)等人通过在钢包底部设置吹氩透气砖,开发了GAZID法,于1963年在法国的尤西诺尔(Usinor)工厂实现了工业化。
其后,这种方法作为小容量钢包用简便的脱气法,在欧美各公司为熔炼特殊钢而普及。
1962年,美国共和公司(Republic)设置有电磁搅拌功能的钢包精炼设备开始用于所有钢种生产。
1968年,日本住友金属(株)小仓制铁所最先使用了Interstop方式的滑动水口工业化实验,并实现实用化。
我国的VD真空精炼起步并不迟,上世纪50年代中后期就在大冶等地的工作者简介:刘晓峰(1983-),男(汉族),陕西白水人,重庆钢铁股份有限公司炼钢厂,助理工程师,从事炉外精炼工艺技术的研究。
厂建立了VD 真空脱气装置生产电工硅钢等钢种。
这个阶段的VD 吨位比较小(小于50t ),主要与电炉模铸流程匹配生产特殊钢材。
(2)功能多元化发展阶段。
在20世纪70~90年代,VD 精炼工艺逐步发展完善,重点优化VD 脱氢、脱氮、脱氧、脱硫等工艺,研发氧脱碳处理工艺。
在欧美许多钢厂(特别是电炉流程钢厂)应用得到了广泛的应用。
20世纪90年代,国内外方坯连铸机配置的二次精炼设施,都以LF 加VD 为主,主要生产高,中碳钢(包括重轨钢、钢帘线、钢绞线、胎圈丝等)、弹簧钢、合金钢等[6]。
国外有部分钢厂开始采用VD 处理来生产低硫低碳或超低碳钢,供应板坯连铸机,而且已获得了很好的处理效果[7-9]。
20世纪80年代中后期,德国Dillingen 钢铁公司、克鲁伯-曼内斯曼Hutten 钢厂开发成功了生产极低硫钢的VTD (Vacuum Tank Degasser )真空大流量搅拌精炼工艺。
Dillingen 钢铁公司至今一直采用该工艺,年产优质中厚板200万吨左右,其中90%以上产品[S]低于0.0010%[7]。
法国Sollac Florange 钢厂的一套VD 装置月处理钢水约12万吨,其中42%供给板坯连铸(主要为IF 钢),51%供给大方坯连铸(主要为钢轨钢)。
法国Dunkerque 钢厂1991年投产一套VD 装置,与已有的一套RH-OB 装置共存,处理钢水全部供给板坯连铸(其中VD 处理能力100万吨/年)[8]。
加拿大Dofasco 钢厂1987年建成的VD 装置,采用BOF-LF-VD-CC 生产工艺,年产超低碳钢(C< 0.004%)18万t [9]。
20世纪90年代,在全国几次炉外处理会议上,国家部委都在强调炉外精炼技术的战略意义和方针、措施,极大地提高了全行业对炉外精炼技术的重视程度和应用的积极性[5]。
由于VD 真空脱气装置投资较少,国内许多钢厂选用了VD 。
(3)高效化、大型化、真空泵干式化发展阶段。
随着VD 真空精炼技术的不断进步,现实了其关键技术和装备的高效化、大型化和大型机械泵应用。
其中主要代表有:双盖双罐结构布置,使VD 处理周期降低至35min 以内;挂渣式全水冷防溅盖,炉盖寿命可达到5000炉以上;采用多重变量泵(蒸汽泵)技术,VD 实现预抽真空技术;干式机械泵系统应用于VD 精炼装置。
2006年~2007年,包钢先后新建了两套VD 真空精炼装置(2#VD 和3#VD ),主要与高品质管坯和重轨钢坯生产匹配,生产能力为120万吨/年/套[10]。
2011年,目前中冶赛迪自主设计建造的最大容量的VD 设备在新余钢铁投产。
该设备与210吨LF 、420mm 特厚板坯连铸机生产特厚板,填补了国内200t 以上级别VD 真空处理装置的空白,其VD 设备和关键技术均达到国内先进水平[11]。
2002年,俄罗新斯西伯利亚钢厂建设了世界上最大的320tVD/VOD 真空处理设备,用于生产低碳钢、高级电工钢等。
1998年,由英国Edwards 公司研发的干式机械泵系统成功应用于罗马尼亚COST 钢厂18tVD/VOD 真空精炼,实现了炼钢用大型机械真空泵干式化[12]。
2、VD 精炼工艺技术的发展2.1 真空脱碳(碳脱氧)真空碳脱氧反应式为[13]:[][]()g CO O C =+ (1)T G o 334.3822200--=∆ (2)平衡常数与温度的关系为:[][]003.21160lg lg +==TP K O C COαα(3) [][]CO oc P f f O K C %1%= (4)由于碳的脱氧产物是CO 气体,在CO P 降低压力后,平衡向产生CO 的方向移动,使碳的脱氧能力提高。
通过计算可知,真空下碳的脱氧能力很强,当CO P =10132Pa 时,碳的脱氧能力超过硅,继续降压至133Pa 时,碳的脱氧能力大于铝。
但是,在实际情况下,钢液中碳的脱氧能力随着压力的降低而提高是有一定限度的,因此将真空脱氧的压力控制在10133~203Pa 即可。
VD 处理过程同样具有良好的脱碳条件。
国外已有部分钢厂(法国Sollac 钢厂、法国Dunkerque 钢厂、加拿大Dofasco 钢厂)[8-9]开始采用VD 处理来生产极低碳或超低碳钢,已获得了很好的处理效果。
国内宝钢、舞钢、汉冶特钢等也已采用了VD 真空脱碳生产低/超低碳钢[14-20],首钢[16]曾采用VD 碳脱氧工艺降低生产成本,吨钢可降成本20多元。
舞钢[17]采用90tEAF-VD-LF-VD 工艺生产低碳钢,其工艺控制包括:1)电炉出钢钢包钢水温度大于1600℃,出钢[]()C w <0.08%。
禁止加人任何脱氧剂及渣料。
2)把从开抽到破坏真空时间限定为10-12min ,真空度须达到200Pa~250Pa , 开抽温度要控制在1590~1640℃,真空过程温降为(2.2±0.2)℃/min ,氩气流量控制在2m 3/h 左右。
经此处理后,钢水[]()C w 低于0.01%,从而为保证成品[]()C w <0.05%打下了基础。
在抽真空操作中,进泵速度要均匀平衡,防止钢水剧烈沸腾引起溢渣, 真空度达到26.7kPa 左右和4kPa 左右时,出现两次真空度上升缓慢或停滞现象,说明此时C-O 反应剧烈,产生CO 较多。
宝钢[19]开发EAF-VD-LF 工艺流程生产无取向硅钢,其控制要点包括:1)电炉出钢钢水的碳含量应该控制在300ppm-500ppm ,并使钢水有适当的过剩氧,钢水的出钢温度应控制在1610-1640℃;2)采用氧化出钢工艺,出钢过程中向钢包加人一定量的铝酸钙系列预熔渣料对钢包顶渣进行适当的调节,可以为钢水在VD 过程进行脱碳处理创造良好的条件。
3)采用氧化出钢,在VD 真空脱碳后可以使钢水中碳含量达到20ppm 以下;LF 处理过程钢水的增碳和增氮得到很好的控制,至LF 处理结束,钢中碳、硫、氮含量分别达到32.5ppm 、32ppm 和47.6ppm ,钢中T[O]含量的控制也较理想,平均达到32.3ppm 。