梯形齿同步带传动的设计
同步带及带轮设计参数

同步带及带轮设计参数1.带的选用:带是传动力的重要传递部件,选用合适的带能够提高传动效率和工作寿命。
在选用带时需要考虑以下几个参数:(1)载荷:带承载机械装置的最大工作载荷,包括静载荷和动载荷。
(2)速度:传动带的工作线速度,一般要求带的线速度小于其临界线速度。
(3)带轮类型:根据传动形式和空间限制选择合适的带轮类型,如平行轴带轮或交叉轴带轮等。
(4)工作环境:带的材料和结构要考虑工作环境的特殊要求,如高温、潮湿等。
2.带轮的选择:带轮作为传动装置的重要组成部分,对带的工作效果有很大影响。
在选择带轮时需要考虑以下几个参数:(1)齿形:带轮的齿形要与所选带的齿形相匹配,以确保传动效果良好。
(2)齿数:带轮的齿数应根据带的齿数和传动比来确定,一般要求齿数较多,以提高传动效率和工作寿命。
(3)直径:带轮的直径要考虑传动装置的装配空间和带的工作线速度,一般直径较大可以提高传动能力。
(4)材料:带轮的材料应经过合理的选择,应具有足够的强度和耐磨性。
3.其他设计参数:除了带和带轮的选用外,还有其他几个重要的设计参数需要考虑:(1)带的张紧力:根据带的类型和工作要求确定带的张紧力,过小容易造成带滑动,过大则会增加带的磨损。
(2)带的传动比:根据传动要求确定带的传动比,传动比过大容易造成过载,过小则会影响传动效果。
(3)带的中心距:根据传动装置的布局和空间限制确定带的中心距,中心距过大会增加带的松弛量,中心距过小则会增加带的张紧力。
(4)带的长度和宽度:根据带轮直径和齿数确定带的长度和宽度,过长容易产生弯曲或拉伸,过窄则会降低传动能力。
总之,同步带及带轮的设计参数涉及到多个因素,需要根据具体的传动要求和工作环境来确定。
合理选择带和带轮,并考虑其他设计参数,可以提高传动效果和延长使用寿命。
在设计过程中,还需要注意对带和带轮的维护和保养,定期检查和更换磨损严重的部件,以确保传动装置的良好工作。
同步带传动设计简介
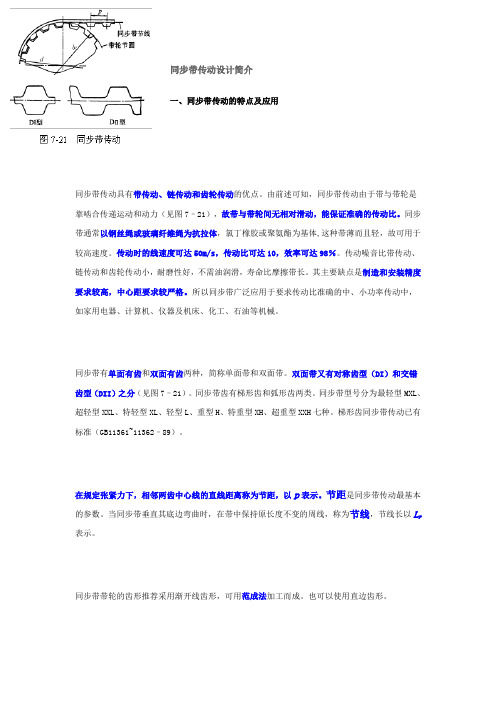
同步带传动设计简介一、同步带传动的特点及应用同步带传动具有带传动、链传动和齿轮传动的优点。
由前述可知,同步带传动由于带与带轮是靠啮合传递运动和动力(见图7–21),故带与带轮间无相对滑动,能保证准确的传动比。
同步带通常以钢丝绳或玻璃纤维绳为抗拉体,氯丁橡胶或聚氨酯为基体,这种带薄而且轻,故可用于较高速度。
传动时的线速度可达50m/s,传动比可达10,效率可达98%。
传动噪音比带传动、链传动和齿轮传动小,耐磨性好,不需油润滑,寿命比摩擦带长。
其主要缺点是制造和安装精度要求较高,中心距要求较严格。
所以同步带广泛应用于要求传动比准确的中、小功率传动中,如家用电器、计算机、仪器及机床、化工、石油等机械。
同步带有单面有齿和双面有齿两种,简称单面带和双面带。
双面带又有对称齿型(DI)和交错齿型(DII)之分(见图7–21)。
同步带齿有梯形齿和弧形齿两类。
同步带型号分为最轻型MXL、超轻型XXL、特轻型XL、轻型L、重型H、特重型XH、超重型XXH七种。
梯形齿同步带传动已有标准(GB11361~11362–89)。
在规定张紧力下,相邻两齿中心线的直线距离称为节距,以p表示。
节距是同步带传动最基本的参数。
当同步带垂直其底边弯曲时,在带中保持原长度不变的周线,称为节线,节线长以L P 表示。
同步带带轮的齿形推荐采用渐开线齿形,可用范成法加工而成。
也可以使用直边齿形。
二、同步带传动的设计同步带传动的主要失效形式是同步带疲劳断裂,带齿的剪切和压溃以及同步带两侧边、带齿的磨损。
保证同步带一定的疲劳强度和使用寿命是设计同步带传动的主要依据。
因此同步带传动设计时主要是限制单位齿宽的拉力,必要时才校核工作齿面的压力。
同步带传动的设计计算参见机械设计手册有关内容。
同步带传动简史

同步带传动简史及选型设计参考同步带传动简史1964 年美国 Uniroyal 橡胶公司首先开发出梯形齿廓同步带。
随着梯形齿的广泛应用人们发现这种同步带传动在速度稍高的时候就出现振动噪音,没法在高速场合使用。
之后人们通过光弹试验发现,梯形齿廓应力分布非常不均匀,根部有明显的应力集中现象,容易造成带齿的断裂失效,而且梯形齿参与接触的受力区域仅占整个齿侧面的 1/3 左右,表明梯形齿没有充分发挥整个带齿的承载能力。
鉴于梯形齿的以上缺点, 1973年,Uniroyal 公司开发了一种单圆弧齿廓(HTD)同步带,可以减小传动带的多边形效应,使应力分布更加合理,越来越得到广泛应用。
之后人们发现这种圆弧齿在速度提高到一定程度时又出现噪音,而且传动效率明显下降,于是美国 Uniroyal 公司对这种齿型修改成平顶圆弧齿(STPD)同步带,这种同步带可以充分的改进带齿与轮齿咬合瞬间的空气流动,从而大大改善了带齿与轮啮合因高速带来的气阻尼;上纪 90 年代末Continental ContiTech马牌公司为提高同步带传动精度和防止带走偏推出了“人”字齿同步带,齿形为平顶圆弧齿;近些年 GATES盖茨公司为实现高精度传动开发出一种精确圆弧齿(GT)同步带;今年佛山市三一自动化科技有限公司在不改变圆弧齿同步带齿形的基础上对同步轮齿形稍作改变,以便更好地适应带齿的渐开线运动,提高传动精度,然后把这种齿型做成拉刀拉制成几个常用齿数的同步轮,我们把这种同步轮叫做变形圆弧齿同步轮。
目前市面上还有不少具有一些小功能特色的齿形和为避开别人专利权而开发的小众齿形,在此就不一一细述了。
因为HTD圆弧齿和GT圆弧齿外形相近不好区分,在此着重简绍一下:HTD圆弧齿为标准圆弧齿廓,大家知道同步带齿与带轮齿啮合过程带齿相对带轮做渐开线运动,因此标准的两个圆弧在这种运动下是啮合不好的,因此GATES盖茨公司开发了GT齿,GT齿廓是通过渐开线运动而形成的带轮齿形状和带齿形状近似,实现了顺畅的咬合和优良的传递性能的并存的齿形,实际齿廓是一种近圆弧的模拟曲线。
基于UG同步带传动CAD系统设计 翻译

摘要一般计算机辅助设计(cAD)软件具有通用性,不能满足专业和特殊领域的需要。
因此,以通用cAD软件系统为平台,根据具体产品设计的需要,进行专用cAD系统的二次开发已成为现代产品设计的重要内容。
同步带传动(亦称同步齿形带传动)是一种综合了带传动、齿轮传动和链传动二者传动优点的传动方式。
其突出优点有:传动平稳、噪声小、传动比准确、传动效率高和无需润滑等。
目前,国内州司步带传动的应用已相当广泛,已成为汽车、纺织机械、办公机械与数控机床等设备的重要传动部件。
由十同步带及带轮结构的特殊性,其传动设计计算繁琐,建模过程较复杂,造成设计人员计算与二维绘图困难。
因此,实现同步带传动的计算机辅助设计和参数化建模具有非常重要的实际意义。
根据同步带传动的特点,确定齿槽为特征,通过齿槽特征的布尔运算与阵列形成同步带及带轮的齿槽和齿。
齿槽特征用关系表达式法进行参数化,将特征建模技术和参数化设计融合创建了同步带传动的参数化标准系列模型,并将一系列形状相似的模型参数存储在程序中。
设计人员可通过在UG中创建的人机交互界面,进行同步带传动的设计计算。
设计完成之后,系统将根据设计得到的参数自动修改模型参数,创建设计人员所需的产品模型。
人机交互界面分为菜单与系统对话框,用UG/Open MenuScript定制同步带传动CAD系统的主菜单和级联菜单,用UG/Open UIStyler设计系统对话框,利用UG/Open API在V C++平台上编程生成动态链接库文件(.DLL文件),实现系统对话框之间的链接和数据传递。
本系统的实现大大降低了同步带传动设计以及带与带轮二维建模的复杂性,减少了设计人员的工作量,提高了设计效率和质量,缩短了设计周期,为同步带和带轮的CAM和CAE奠定基础,目_本系统的实现对其它类型的传动也具有一定的指导和借鉴意义。
关键词:UG二次开发;CAD;同步带传动;特征建模;参数化设计;Research of Synchronous Belt Transmission CAD System Based on UGAuthor: Song LishuangMajor: Mechanical Manufacturing and Its AutomationTutor: Wang ZeheAbstractGeneral computer-aided design CAD software is universal, which can not meet theneeds of professional and special areas. Therefore, the secondary development of special system which uses common CAD software for the platform has become an important partof modern product design according to the specific needs of product design.Synchronous belt transmission is a transmission mode, which integrates the advantages of belt transmission, gear transmission and chain transmission. It is smooth,low noise, accurate, efficiency and don't need lubrication. At present, the application of synchronous belt transmission has been very extensive at home and abroad. It has becomean important transmission part in automobile, textile machinery, office machinery, CNC machine tools and so on. But its design, calculation and modeling are rather tedious and difficult. Achieving synchronous belt transmission CAD system is a very importantpractical significance.According to the characteristics of synchronous belt transmission, alveolar is identified as the feature. The teeth and alveolars of pulley and belt are formed by booleanand array of alveolar feature. Alveolar feature is parameterized by relationship expression method. Synchronous transmission parameter standard series models are created throughthe integrated use of feature modeling and parametric design. The parameters of a serfs of similar shape models are stored in the program. Designers can moth勿the series of model parameters and obtain the product model by UG interactive interface.Man-machine interface includes menu and system dialog. The main menu and threedrop-down menus are created with UG/Open MenuScript. The system dialogs are customized with UG/Open UIStyler. Dynamic link library files (.DLL files) are generatedby programming on VC++ platform with the use of UG/Open API. Then the dialogsmutual links and data transfer can be achieved.The realization of the system greatly reduces the complexity of the design process andthe workload of the designer, improves the design efficiency, shortens the design cycle andlays the foundation for the computer-aided analysis, computer-aided manufacturing of the synchronous belt and pulley. The realization of this system also has some guidance and reference for other types of transmission.Keywords: UG secondary development; CAD; Synchronous belt transmission; Feature modeling; Parametric design;目录1绪论 (1)1.1研究背景 (1)1.2国内外研究概况 (1)1.2.1 CAD技术的发展概况 (1)1.2.2参数化设计的发展概况 (3)1.2.3同步带传动CAD系统的发展概况 (4)1.3研究目的和意义及研究内容和研究方法 (6)1.3.1研究目的和意义 (6)1.3.2主要研究内容和研究方法 (7)1.4本章小结 (7)2同步带传动CAD系统的理论依据及关键技术 (8)2.1同步带传动概述 (8)2.1.1同步带传动的发展概况 (8)2.1.2同步带传动的类型 (9)2.1.3同步带传动的设计 (10)2.2参数化与特征建模理论 (20)2.2.1参数化设计技术 (20)2.2.2特征建模技术 (21)2.3 UG二次开发技术 (22)2.3.1 UG/Open MenuScript (23)2.3.2 UG/Op en UIStyler (25)2.3.3 UG/Open API (25)2.3.4 UG/Open GRIP (27)2.3.5 User Tools (27)2.4本章小结 (27)3同步带传动CAD系统的总体设计 (28)3.1系统的需求分析 (28)3.2系统的开发目标 (28)3.3系统的设计原则 (28)3.3.1系统设计的基本原则 (28)3.3.2开发工具的选择原则 (29)3.3.3人机交互界面的设计原则 (30)3.4系统的功能模块及开发流程 (30)3.4.1系统功能模块 (30)3.4.2系统开发流程 (31)3.5本章小结 (32)4同步带传动CAD系统的实现 (33)4.1配置开发环境 (33)4.1.1配置UG环境变量和缺省参数 (33)4.1.2配置VC++开发环境 (34)4.2创建系统菜单 (35)4.3创建系统对话框 (38)4.3.1同步带传动设计对话框的设计 (39)4.3.2同步带参数化建模对话框的设计 (43)4.3.3同步带轮参数化建模对话框的设计 (44)4.4创建系统工程 (45)4.5置入用户目录 (52)4.6系统运行流程图 (52)4.7本章小结 (53)5应用实例 (54)6结论与展望 (65)6.1结论 (65)6.2创新内容 (66)6.3展望 (66)参考文献 (67)在读期间已发表的学术论文 (69)作者简历 (70)致谢 (71)绪论1. 1研究背景同步带传动是在链传动的基础上综合了带传动和齿轮传动的优点而发展起来的一种传动方式。
同步带传动的设计计算和使用

同步带传动的设计计算和使用同步带传动是一种新型的机械传动(见图 i).由于它是一种啮合传动因而带和带轮之间i殳有相对滑动,从而使主从轮间的传动达到同步。
同步带传动和 y 带、平带相比具有: (i)传动准确,无滑动,能达到同步传动的目的; (2)传动效率高·一般可达驰蓐;(3)速比范围大允许线速度也高;(1)传递功率范围大。
从几十瓦到几百千瓦;(5)结构紧凑,还适用于乡轴传动等优点。
因此,同步带传动已日益弓『起各方面的注意和重视,并把这种传动应用到各种机械设备上。
相应地设计者要求有一种设计方法来台理地选择同步带传动的各项参数。
笔者根据参加制订同步带传动国家标准讨论和学术活动的体会,提出了同步带传动的设计方法及应注意的问题,以供同步带传动设计者参考直用。
同步带传动的设计准则同步带传动是以带齿与轮齿依敬啮合来传递动力。
达到同步传动的目的。
因此。
在同步带传递扭矩时,带将受拉力作用。
带齿承受剪切,而带齿的工作表面在进八和退出与轮齿啮合的过程中将被磨损。
因此同步带的主要失效形式有如下三种:(1)同步带承载绳 (又称骨架蝇,的疲劳断裂;(2)带齿的剪切破裂:(3)带齿工作表面磨损。
失去原来的形乇I}。
根据试验分析,当同步带绕于带轮时,在所包圆弧内带齿与带轮齿的啮合齿数 z.大于 6时带齿的剪切强度将大干带的抗拉强度。
同时,随着粘附于带齿工作表面上的尼龙包雍层的设置.使带齿的耐磨性有了报大的提高。
因此在同步带正常工作条件下,同步带的主要失效形式是带在变拉力作用下的疲劳断裂所以同步带传动是根据带的抗拉强度作为设计准则来进行设计的。
在 ISb5295 t同步带额定功率与传动中心距的计算,标准中,就是以此为依据提出了带宽为基准宽度的基准额定功率计算公式:Pd (T 一mv')v/100o(kw )式中:Po——某一型号同步带在基准宽度下所能抟递的基准额定功率 ( W )某一型号同步带在基准宽度下的许用工作拉力 (见表1) (Ⅳ)m——某一型号同步带在基准宽度下舳单位长度质量 g/m} v——同步带线速度 (m/s,由公式可知:L为带的许用工作拉力,m 为带在运转过程中由离心力产生的拉力。
基于某发动机适应性开发进行的同步齿形带传动系统设计

AUTO TIME55AUTOMOBILE DESIGN | 汽车设计时代汽车 1 引言自20世纪60年代美国通运公司首次将同步齿形带用于新开发的顶置式凸轮轴发动机以来,同步带迅速的在汽车发动机正时传动系统中使用。
而对同步齿形带的研究主要集中在如何提高其疲劳强度、延长使用寿命等方面。
其中CONTITECH 公司采用HNBR/ZMA 与芳纶短纤维配合制造HSN-POWER 同步带在汽油机中使用其寿命超过了240000Km ,达到了与发动机同寿命的目标[1]。
并且随着科技的进步与市场的需求,近年来国外的传动厂家如大陆、盖茨和特高均开发出了耐油同步齿形带[2]。
正时传动系统在发动机中主要起着承上启下的作用,将曲轴的旋转运动传递给凸轮轴,保证发动机能够正常运转。
目前,发动机的正时传动系统的传动方式主要有两大类,第一类是正时链条传动,第二类时同步齿形带传动。
2 正时系统概念设计正时链条与同步齿形带作为正时系统最常见的两种传动方式,各有优缺点,起具体对比见表1。
通过正时链条与同步齿形带的对比,可以看出同步齿形带在功率损耗、噪音、成本、返修难易上均优于正时链条。
并且无需润滑、传动室无需完全密封,传递功率可以满足绝大多数发动机需求,所需布置空间也满足整机布置需求,仅在使用寿命上低于正时链条。
所以,综上该款发动机选择了同步齿形带进行正时系统传动。
基于某发动机适应性开发进行的同步齿形带传动系统设计马江涛 潘圣临 胡志刚 潘丽丽 马楠哈尔滨东安汽车发动机制造有限公司 黑龙江省哈尔滨市 150060摘 要: 某发动机进行性能升级,降成本优化的适应性开发。
涉及到了正时传动系统的重新开发。
首先通过概念设计分析确认了采用同步齿形带进行传动。
然后通过系统的结构布置,各个环节的计算与分析,阐述了同步齿形带传动系统的详细设计过程。
关键词:正时传动系统;同步齿形带;预紧力同步齿形带的设计与布置主要取决于发动机的性能参数与结构形式,以及传动零件的吸收功率等等。
机械传动简述同步带传动
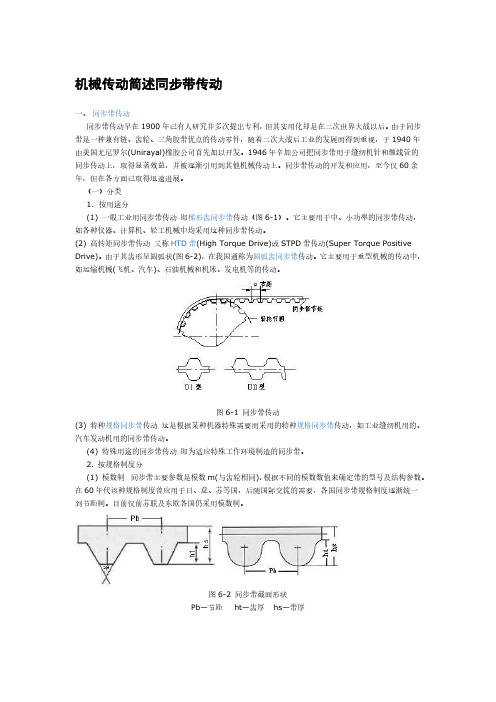
机械传动简述同步带传动一、同步带传动同步带传动早在1900年已有人研究并多次提出专利,但其实用化却是在二次世界大战以后。
由于同步带是一种兼有链、齿轮、三角胶带优点的传动零件,随着二次大战后工业的发展而得到重视,于1940年由美国尤尼罗尔(Unirayal)橡胶公司首先加以开发。
1946年辛加公司把同步带用于缝纫机针和缠线管的同步传动上,取得显著效益,并被逐渐引用到其他机械传动上。
同步带传动的开发和应用,至今仅60余年,但在各方面已取得迅速进展。
(一)分类1.按用途分(1)一般工业用同步带传动即梯形齿同步带传动(图6-1)。
它主要用于中、小功率的同步带传动,如各种仪器、计算机、轻工机械中均采用这种同步带传动。
(2)高转矩同步带传动又称HTD带(High Torque Drive)或STPD带传动(Super Torque Positive Drive)。
由于其齿形呈圆弧状(图6-2),在我国通称为圆弧齿同步带传动。
它主要用于重型机械的传动中,如运输机械(飞机、汽车)、石油机械和机床、发电机等的传动。
图6-1同步带传动(3)特种规格同步带传动这是根据某种机器特殊需要而采用的特种规格同步带传动,如工业缝纫机用的、汽车发动机用的同步带传动。
(4)特殊用途的同步带传动即为适应特殊工作环境制造的同步带。
2.按规格制度分(1)模数制同步带主要参数是模数m(与齿轮相同),根据不同的模数数值来确定带的型号及结构参数。
在60年代该种规格制度曾应用于日、意、苏等国,后随国际交流的需要,各国同步带规格制度逐渐统一到节距制。
目前仅前苏联及东欧各国仍采用模数制。
图6-2同步带截面形状Pb—节距ht—齿厚hs—带厚(2)节距制即同步带的主要参数是带齿节距,按节距大小不同,相应带、轮有不同的结构尺寸。
该种规格制度目前被列为国际标准。
由于节距制来源于英、美,其计量单位为英制或经换算的公制单位。
(3)DIN米制节距DIN米制节距是德国同步带传动国家标准制定的规格制度。
同步带传动行星机构设计

同步带传动行星机构设计1.引言1.1 概述概述部分的内容应该对同步带传动行星机构设计进行一个简要的介绍和概述。
以下是对概述部分的一个可能的内容编写:概述同步带传动行星机构作为一种常见的传动装置,其设计和应用在各个领域中都具有重要的意义。
它广泛应用于机械工程、汽车工业以及其他工业制造和机械设备领域。
本文将对同步带传动行星机构的设计进行详细阐述和讨论。
同步带传动是通过齿轮和同步带的相互配合实现传动的一种机构。
其主要特点是传动平稳、运转可靠,并且可以实现高扭矩传递。
行星机构则是一种常见的传动装置, 它由一个中心轴和围绕其旋转的若干个行星齿轮组成,具有较高的传动比和紧凑的结构设计。
本文将首先介绍同步带传动的基本原理,包括同步带的工作原理、材料选择和传动效率等方面。
其次,我们将详细讨论行星机构的结构和工作原理,包括行星齿轮的选型、配位和传动比的计算等。
最后,我们将总结同步带传动行星机构设计的重要性,并提出设计时需要注意的关键要点。
通过本文的阐述和分析,读者将能够全面了解同步带传动行星机构的设计原理和应用,为今后的实际工程设计提供参考和指导。
同步带传动行星机构的设计对于提高机械设备的传动效率和工作稳定性具有重要意义,也是工程设计中不可忽视的关键因素。
1.2文章结构2.2 要点2:提高沟通能力在现代社会中,良好的沟通能力是非常重要的,尤其是在英语这个全球通用语言的背景下。
提高沟通能力可以使我们更好地理解他人,表达自己的想法,并顺利地完成各种任务。
下面我将介绍一些提高英语沟通能力的方法。
首先,积极参与英语口语练习是提高沟通能力的关键。
只有通过实践,我们才能真正掌握如何用英语进行自如的对话。
可以加入英语学习小组或找到一个语言交换伙伴,与他们进行频繁的对话练习。
此外,利用各种资源,如英语角、在线语音聊天平台等,主动与母语为英语的人交流,以提高口语表达能力和听力理解能力。
其次,培养良好的听力习惯也是提高沟通能力的重要方面。
转向梯形机构设计报告

转向梯形机构设计报告一、引言梯形机构是一种常用于机械设计中的传动机构,可以将旋转运动转化为直线运动,被广泛应用于工程领域中各种机械装置中。
本报告主要介绍了梯形机构的设计原理、结构特点、选择和使用要点等内容。
二、设计原理梯形机构基本原理是通过两个或多个滚轮和一个传动带或链条来实现转动轴的运动。
其中,滚轮被安装在不同的位置,并用传动带或链条连接。
当驱动滚轮旋转时,传动带或链条会从一个滚轮滑落到另一个滚轮上,从而产生直线运动。
三、结构特点1.简单稳定:梯形机构结构简单,同时能够提供稳定的直线运动。
2.传动效率高:梯形机构传动效率较高,可满足大部分机械装置的需求。
3.负载能力强:梯形机构具有较高的负载能力,能够承担一定程度的重量。
4.调节方便:梯形机构可以通过调整滚轮的位置和传动带或链条的张紧度来实现不同的运动需求。
四、选择和使用要点1.根据需求选择合适的滚轮:在梯形机构设计中,滚轮的选择非常重要。
滚轮的尺寸、材质和表面处理等因素直接影响着梯形机构的运行效果和寿命。
2.合理布置滚轮位置:滚轮应该根据具体要求合理布置,保证滚轮之间的转动配合准确,同时还需要考虑机械装置的空间布局和传动路径等因素。
3.选择合适的传动带或链条:传动带或链条的选择应该符合工作环境的要求,能够承受工作负载和运动速度,同时还要考虑传动带或链条的寿命和维护成本等因素。
4.保持传动带或链条的张紧度:传动带或链条的张紧度对梯形机构的运行效果和寿命影响很大,应该定期检查和调整传动带或链条的张紧度,确保其正常工作。
五、案例分析以自动贩卖机中的货物下降装置为例,使用梯形机构实现货物从上方下降到出货口的运动。
在该案例中,根据贩卖机的设计要求,选择合适尺寸和负载能力的滚轮,并合理布置滚轮的位置。
通过调整传动带的张紧度,确保货物的平稳下降和定位准确。
六、结论梯形机构作为一种常用的传动机构,具有简单稳定、传动效率高、负载能力强等特点,在机械设计中应用广泛。
同步齿形带的计算与选型【纯经验】

同步带传动是一种带齿与带轮齿槽的啮合传动。
与齿轮啮合传动相比,它也具有瞬时速度均匀(即同步性好)和传动效率高的优点,但更比齿轮传动速比范围大、允许线速度高、轮距大、传动噪音小、功率与重量的比值大,且不需润滑、更换方便、价格低廉。
因而得到了广泛的应用。
1、同步带传动类型的选择同步带基本上都已标准化。
同步带分两大类:梯形齿形同步带和圆弧形齿形同步带。
梯形齿同步带造相对容易些,价低,但齿根应力集中,影响了承载能力和寿命,同时较大的振动、噪音和干涉也影响了带速;而弧形齿同步带应力分布较合理,干涉量也较小,其寿命比梯形齿提高约一倍。
所以,一般应选用弧形齿同步带,特别是负载较大时。
2、同步带轮型号的确定同步带轮的齿形型号和节距等啮合参数与同步带的相同,需要确定的只是齿数(或直径)和结构等。
同步带轮的齿数(或直径)一般是先确定小轮的齿数,再按传动比来定大轮齿数。
为了保证同步带的应有寿命,小同步带轮的直径要大于上表中的允许最小弯曲直径,再折算成最小齿数(盖奇同步带轮最小齿数)。
只要结构和成本允许,从同步带的寿命考虑,小轮的齿数比允许的最小齿数稍多些为好。
小轮的齿数确定后,根据传动比就可确定大轮的齿数了。
再根据结构确定两带轮的中心距,按同步带的节距计算出节线长度或总齿数。
至此,传动参数就全部确定完了。
同步带轮的结构有很多种,从形状上可分为无凸缘的(即只有两端带挡片的轮齿部分)和有凸缘的(即除了有两端带挡片的轮齿部分外还有一段圆柱凸缘)。
从与轴联结的方式看,可分三种:即螺钉、键和涨套(即所谓的免键联结)。
可以参考:同步带轮与轴连接方式螺钉连接简单,易装卸,但轴轮同心度差,且轴上要加工出对应的扁方或窝;键联结的优劣不言而喻;涨套联结性能虽好,但成本高。
根据设备结构的具体情况,按上面的分析就可确定同步带轮的结构和型号。
同步齿形带的计算与选型竖直方向设计要求:托盘及商品自重20kg (196N ),滑块运动1250mm 所需时间6s 。
梯形齿同步带传动的设计

V带传动:张紧轮设置在 松边内侧靠大轮处 (∵V带只能单向弯曲,避免过多减小包角)
1.V带的结构及基本参数
A - 1400 GB11544-89
2.带传动中的力分析
F2 Ff n1 F1 F1 = F0 +Fe/2 F2 = F0 -Fe/2 F2 n2 Ff
3.带传动的应力分析
工作时,带横截面上的应力由三部分组成:
一、定期张紧装置
采用定期改变中心距的方法来调节带的预紧力,使带 重新张紧。 1、滑道式 2、摆架式
二、自动张紧装置
将装有带轮的电动机安装在浮动的摆架 上,利用电动机的自重,使带轮随同电动 机绕固定轴摆动,以自动保持张紧力。
三、采用张紧轮的装置
当中心距不能调节时,可采用张紧轮将带张紧。
平带传动:张紧轮设置在 松边外侧靠小轮处 (∵平带可以双向弯曲,应尽量增大包角)
由紧边和松边拉力产生的拉应力;
σ1 = F 1/A MPa σ2 = F 2/A MPa
由离心力产生的拉应力;
FC qv2 C A A MPa
2 yE 由弯曲产生的弯曲应力。 b dd
MPa
1. 打 滑 •原因: 当Fe>Ffmax → 打滑 • 分析: 1. 打滑可以避免 2. 打滑先发生在小带轮处 3. 打滑→带的剧烈磨损 →失效
4. 过载保护作用
•防止措施: 1. 控制Fe< Ffmax
2. ↑F0、f、α(紧边置下)→↑Ffmax
2.弹性滑动
*原因:
后果:
带两边拉力不相等, 则弹性变形不同,带经过轮时 变形量改变,带相对轮有微量滑动
1. 带速滞后→ V1>V带>V2
V1 >V2
d d1 2.带传动传动比不稳定 i n1 n2 d d 1 (1 )
同步带的设计计算
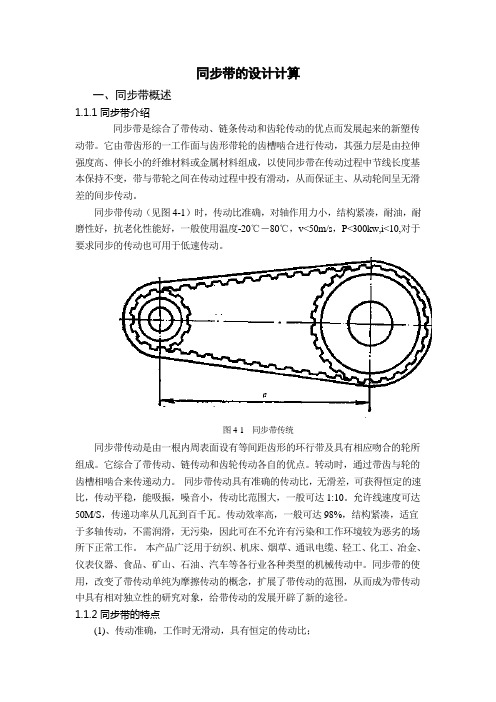
同步带的设计计算一、同步带概述1.1.1同步带介绍同步带是综合了带传动、链条传动和齿轮传动的优点而发展起来的新塑传动带。
它由带齿形的一工作面与齿形带轮的齿槽啮合进行传动,其强力层是由拉伸强度高、伸长小的纤维材料或金属材料组成,以使同步带在传动过程中节线长度基本保持不变,带与带轮之间在传动过程中投有滑动,从而保证主、从动轮间呈无滑差的间步传动。
同步带传动(见图4-1)时,传动比准确,对轴作用力小,结构紧凑,耐油,耐磨性好,抗老化性能好,一般使用温度-20℃―80℃,v<50m/s,P<300kw,i<10,对于要求同步的传动也可用于低速传动。
图4-1 同步带传统同步带传动是由一根内周表面设有等间距齿形的环行带及具有相应吻合的轮所组成。
它综合了带传动、链传动和齿轮传动各自的优点。
转动时,通过带齿与轮的齿槽相啮合来传递动力。
同步带传动具有准确的传动比,无滑差,可获得恒定的速比,传动平稳,能吸振,噪音小,传动比范围大,一般可达1:10。
允许线速度可达50M/S,传递功率从几瓦到百千瓦。
传动效率高,一般可达98%,结构紧凑,适宜于多轴传动,不需润滑,无污染,因此可在不允许有污染和工作环境较为恶劣的场所下正常工作。
本产品广泛用于纺织、机床、烟草、通讯电缆、轻工、化工、冶金、仪表仪器、食品、矿山、石油、汽车等各行业各种类型的机械传动中。
同步带的使用,改变了带传动单纯为摩擦传动的概念,扩展了带传动的范围,从而成为带传动中具有相对独立性的研究对象,给带传动的发展开辟了新的途径。
1.1.2同步带的特点(1)、传动准确,工作时无滑动,具有恒定的传动比;(2)、传动平稳,具有缓冲、减振能力,噪声低;(3)、传动效率高,可达0.98,节能效果明显;(4)、维护保养方便,不需润滑,维护费用低;(5)、速比范围大,一般可达10,线速度可达50m/s,具有较大的功率传递范围,可达几瓦到几百千瓦;(6)、可用于长距离传动,中心距可达10m以上。
同步带传动设计计算

同步带传动设计计算一、同步带基础知识:同步带传动是一种特殊的带传动,带的工作表面做成齿形与带轮的齿形相吻合,带和带轮主要靠啮合进行传动。
1)同步带分类:(1)按齿形分:同步带分为梯形齿和圆弧齿两大类。
目前梯形齿同步带应用较广,圆弧齿同步带因其承载能力和疲劳寿命高于梯形齿而应用日趋广泛。
(2)按结构分:同步带分为单面和双面同步带两种形式。
双面同步带按齿的排列不同又分为对称齿双面同步带(DA型)和交错齿双面同步带(DB型)两种。
2)常用的梯形齿同步带齿形有周节制和模数制两种。
我国规定梯形齿同步带采用周节制,周节制梯形齿同步带称为标准同步带。
周节制同步带的主要参数是节距Pb。
节距Pb是在规定的张紧力下,同步带纵向截面上相邻两齿在节线上的对称距离。
(注:同步带节线长度Lp=Pb*z)标准同步带(梯形齿)按节距大小又分为七类:MXL(2.032)一最轻型;XXL(3.175)一超轻型;XL(5.080)一特轻型;L(9.525)一轻型;H(12.700)一重型;XH(22.225)一特重型;XXH(31.750)一超重型。
同步带的标记方法:如梯形齿同步带的标记有带长代号、带型、带宽代号和标准号组成,举例:450 H100 GB/T 10414 表示:带长代号450,节线长1143mm;带型H(重型),节距为12.7mm;带宽代号100,带宽为25.4mm; GB/T10414为标准号。
模数制梯形齿同步带以模数m为基本参数(模数m=Pb/π),模数系列为1.5、2.5、3、4、5、7、10,齿形角2β=40°,其标记为:模数x齿数x宽度。
例如:橡胶同步带2x45x25表示模数为2、齿数z=45、带宽bs=25mm。
同步带属于标准件,同步带的材料主要有橡胶和聚氨酯(TTBU)两种。
设计选用时参考相关产品样本从从同步带长度系列中选择标准长度尺寸,带宽的选择经计算后从宽度系列中选用或按使用要求进行裁剪。
梯形齿同步带
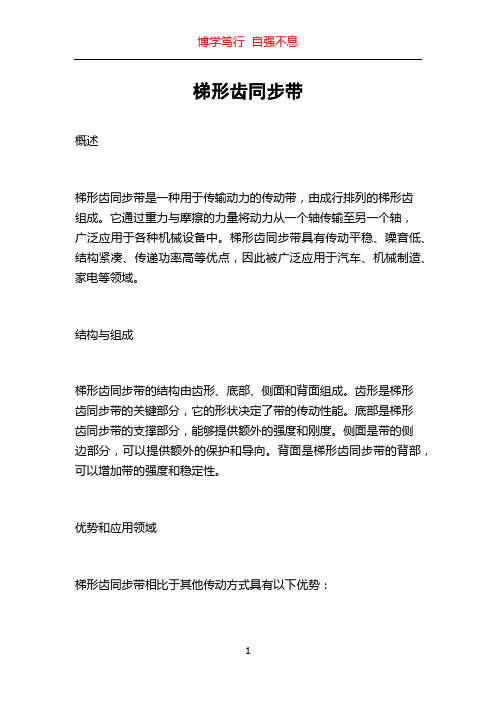
梯形齿同步带概述梯形齿同步带是一种用于传输动力的传动带,由成行排列的梯形齿组成。
它通过重力与摩擦的力量将动力从一个轴传输至另一个轴,广泛应用于各种机械设备中。
梯形齿同步带具有传动平稳、噪音低、结构紧凑、传递功率高等优点,因此被广泛应用于汽车、机械制造、家电等领域。
结构与组成梯形齿同步带的结构由齿形、底部、侧面和背面组成。
齿形是梯形齿同步带的关键部分,它的形状决定了带的传动性能。
底部是梯形齿同步带的支撑部分,能够提供额外的强度和刚度。
侧面是带的侧边部分,可以提供额外的保护和导向。
背面是梯形齿同步带的背部,可以增加带的强度和稳定性。
优势和应用领域梯形齿同步带相比于其他传动方式具有以下优势:1. 传动效率高:梯形齿同步带采用梯形齿结构,可以提供更大的接触面积,从而增加传动效率。
2. 传动平稳:梯形齿同步带的齿形设计使得在传动过程中齿与齿之间的运动非常平稳,减少了传动过程中的震动和噪音。
3. 传递功率高:梯形齿同步带由于采用梯形齿结构,能够在传递动力时提供更大的摩擦力,因此可以传输更大的功率。
由于具备以上优势,梯形齿同步带在许多领域得到广泛应用:1. 汽车工业:梯形齿同步带被广泛应用于汽车引擎系统,用于传输动力,控制汽车的运动。
2. 机械制造:各种机械设备,如机床、印刷机、包装机等,都可以使用梯形齿同步带进行传动。
3. 家电行业:家用电器中的一些需要传输动力的部件,如搅拌机、搅拌器等,也可以采用梯形齿同步带作为传动装置。
选用和维护在选用梯形齿同步带时,需要根据具体应用需求来选择带的型号和规格。
首先需要确定所需的传动功率、传动比例和传动速度,然后根据这些要求来选择适当的带宽和齿距。
此外,还需要考虑带的材料和强度,以确保带能够在工作环境下良好运行。
在使用和维护梯形齿同步带时,需要注意以下几点:1. 定期检查和调整带的张紧力,确保带的正常工作。
2. 避免带与其他物体的摩擦和碰撞,以免破坏带的表面。
3. 定期清洁带的表面,除去油污和杂质,以保持带的摩擦性能。
同步带及带轮设计计算

(5)验证带速 v
由公式 v d1n1 计算得, 60000
v
d1n1 60000
1.90m / s
vmax
40m / s ,其中 vmax
40m /
s 由表 4 查得。
(6)确定同步带的节线长度 Ln
利用 AutoCAD 作图法求节线长度,结果如下图 1 所示。
图 1 带轮示意图
由上图可得, Lp AB AD CD BD ,其中 AB CD 74.634mm 。
可以求得:弧
AB
138 2 d1 360 2
43.812mm
,
弧 BD
360
138 2 360 2
d2
182.088mm
故 Lp 74.634 2 43.812 182.088 375.168mm
表 6 L 型带(节距 9.525mm,基准宽度 25.4mm)基准额定功率 P0 (kw)
表 7 同步带宽度尺寸参考表
可根据同步带的最小许用齿数确定。查表 3 得。
选小带轮齿数: z1 12 。故大带轮齿数为: z2 i z1 2.6 12 31.2 ,圆整 z2 31 。
故: z1 12 , z2 31
(4)确定带轮的节圆直径 d1, d2
小带轮节圆直径: d1 Pb z1 / 9.52512 / 3.14 36.38mm 大带轮节圆直径: d2 Pb z2 / 9.525 31/ 3.14 93.99mm
图2带轮订购图纸表1载荷修正系数k0表2梯形同步带选型图表3带轮最小许用齿数表4同步带允许最大线速度表5l型号梯形齿同步带规格型号尺寸表表6l型带节距9525mm基准宽度254mm基准额定功率0pkw表7同步带宽度尺寸参考表
同步带设计指导书

同步带设计指导书更改记录序号修改内容概述修改人修改日期备注年—月—日同步带设计指导书一:同步带简介同步带是以钢丝绳或玻璃纤维为强力层,外覆以聚氨酯或氯丁橡胶的环形带,带的内周制成齿状,使其与齿形带轮啮合,用于传动和传送。
特点:(1)传动准确,工作时无滑动,具有恒定的传动比;(2)传动平稳,具有缓冲、减振能力,噪声低;(3)传动效率高,可达98%,节能效果明显;(4)维护保养方便,不需润滑,维护费用低;(5)速比范围大,一般可达10,线速度可达50m/s,具有较大的功率传递范围,可达几瓦到几百千瓦;(6)可用于长距离传动,中心距可达10m以上;(7)与V型带相比预紧力较小,轴和轴承上所受载荷小。
同步带可分为:RPP同步带、梯形齿同步带、圆弧齿同步带、梯形齿双面同步带、圆弧齿双面同步带等。
我们公司常选用梯形齿同步带,用于传动,下面主要介绍其选型方法。
二:同步带的选型(一)选型步骤:确定设计时的必要条件(a机械种类b传动动力c负载变动程度d1工作日时间e小带轮转速f传动比g暂定间距h其他条件计算设计动力(功率)通过简易选型表暂定皮带种类确定大小带轮的齿数、皮带长度、轴间距确定皮带宽度确认轴间距的调整量是否合适(二).选型计算实例:1.确定设计时的必要条件:设计装配机床梯形齿同步带传动。
电机为1FK7063-5AF71,其额定功率为2.29kW,额定转速为3000rpm,传动比为1,轴间距设为740mm,每天两班制工作(按16h计)。
(计算时,伺服电机和变频电机最好根据实际的使用情况设定转速,计算出实际功率;连接减速箱的,应计算出减速箱输出的转速和功率;以下计算的传动比为同步带的传动比。
)2.设计功率过负载系数根据表1、2、3得出:3.通过简易选型表暂定皮带种类:根据简易选型表小带轮转速与设计功率的关系:选择H型梯形齿同步。
4.确定大小带轮的齿数、皮带长度、轴间距:根据上表得出小带轮齿数应,根据机床空间可以选用22H型号带轮,,由于传动比为1,所以;皮带长度:;暂定轴间距;带轮节圆直径;所以根据样本选用700 H 型号同步带,5. a.确定皮带宽度皮带大致宽度基准传动容量Ps啮合补偿系数基准皮带宽度啮合齿数;接触角度;所以;查表得;;Ps=8.33kW;所以可以选用H型同步带公称宽度100(25.4mm)b.确认设计功率是否满足以下公式(该式不成立时,在选择大一号的皮带宽度):查表得:宽度075(19.1mm)。
同步带轮设计步骤

同步带轮设计步骤
同步带轮设计步骤:
1) 简化设计:根据同步带轮齿轮传动的传动功率、输入转速、传动比等条件,确定中心距、模数等主要参数。
如果中心距、模数已知,可跳过这一步。
2) 几何设计计算:设计和计算同步带轮齿轮的基本参数,并进行几何尺寸计算。
3) 强度校核:在基本参数确定后,进行精确的齿面接触强度和齿根弯曲强度校核。
4) 如果校核不满足强度要求,可以返回
同步带轮的优点
同步带轮传动是由一根内周表面设有等间距齿的封闭环形胶带和相应的带轮所组成。
运动时,带齿与带轮的齿槽相啮合传递运动和动力,是一种啮合传动,因而具有齿轮传动、链传动和平带传动的各种优点。
同步带按材质可分为氯丁橡胶加纤维绳同步带,聚氨酯加钢丝同步带,按齿的形目前主要分为梯形齿同步带和圆弧齿同步带两大类,按带齿的排布面又可分为单面齿同步带和双面齿同步带。
同步带传动具有准确的传动比,无滑差,可获得恒定的速比,可精密传动,传动平稳,能吸震,噪音小,传动速比范围大,一般可达1∶10,允许线速度可达50m/s,传动效率高,一般可达98℅―99℅。
传递功率从几瓦到数百千瓦。
结构紧凑还适用多轴传动,张紧力小,不需润滑,无污染,因而可在不允许有污染和工作环境较为恶劣的场合下正常工作。
产品用途
可允许在有污染和工作环境较为恶劣的场合下工作。
如∶机械制造、汽车飞机、纺织、轻工、化工、冶金、矿山、军工、仪器、仪表机床、农业机械及商业机械传动中。
AT5同步带

AT5同步带是同步带传动系列中应用于比较广泛的一种带型。
AT5同步带主要应用于小封装和高速运转,具有节省空间和高度稳定的的特点。
精密驱动器,如办公室机器和电脑,使用AT5型同步带是理想的解决方案。
AT5同步带设计要点:1、梯形齿形式。
2、弹性支持和牙齿结合耐用性和重量轻。
3、尼龙面临保护和加强了牙齿表面。
4、提供玻璃钢线长度的稳定性和灵活性。
AT5同步带优势:1、输功率达0.8千瓦,转速高达20000的速度。
2、AT5皮带允许使用小滑轮直径(从6毫米直径)。
3、最大数量的网状牙齿。
4、高度的步进马达使用。
5、精确的定位。
6、非常稳定。
奇龙公司的模具表在不断更新,在此只是提供部分模具表.规格节线长(毫米) 齿数规格节线长(毫米) 齿数AT5×280 280,0011,02 56 AT5×610 610,0024,.02 122 AT5×455 45,0017,91 91 AT5×630 630,0024,80 126 AT5×255 255,0010,40 51 AT5×660 660,0025,98 132 AT5×300 300,0011,81 60 AT5×710 710,0027,.95 142 AT5×340 340,0013,39 68 AT5×750 750,0029,53 150 AT5×375 357,0014,76 75 AT5×480 480,0018,90 96 AT5×390 390,0015,.35 78 AT5×3700 3700,00145,67 740 AT5×410 410,0016,14 82 AT5×3000 3000,00118,11 600 AT5×420 420,0016,54 84 AT5×2200 2200,0086,.61 440 AT5×225 22,5008,.86 45 AT5×1125 1125,0044,29 225 AT5×545 545,0021,46 109 AT5×1050 1050,0041,34 210 AT5×780 780,0030,71 156 AT5×975 975,0038,39 195 AT5×500 500,0019,69 100 AT5×825 825,0032,48 165 AT5×600 600,0023,62 120 AT5×4000 40000,0157,48 800。
同步带齿型选择

同步带齿型选择1. 引言同步带是一种广泛应用于机械传动系统中的元件,它通过同步带齿来实现传动动力的目的。
在选择合适的同步带齿型时,需要考虑多种因素,包括传动功率、转速、工作环境等。
本文将介绍同步带齿型的选择方法和注意事项。
2. 同步带齿型的分类根据齿型结构的不同,同步带齿型可以分为几种常见类型,包括直齿型、弧形齿型和梯形齿型等。
每种齿型都有其特点和适用范围。
2.1 直齿型直齿型同步带齿形简单,齿距均匀。
它适用于中小功率传动和速度较低的场景。
直齿型同步带具有传动精度高、噪音小和使用寿命长等优点。
2.2 弧形齿型弧形齿型同步带的齿形呈圆弧状,它比直齿型同步带齿距更小,能够提供更高的传动功率和更高的传动效率。
弧形齿型同步带适用于大功率传动和速度较高的场合。
2.3 梯形齿型梯形齿型同步带的齿形类似于梯形,它可以提供更大的接触面积和更高的传动效率。
梯形齿型同步带适用于中高功率传动和速度较高的场合。
3. 同步带齿型选择的因素在选择同步带齿型时,需要考虑以下因素:3.1 传动功率传动功率是选择同步带齿型的重要因素之一。
对于大功率传动,应选择适用于高功率传动的齿型,如弧形齿型或梯形齿型。
对于小功率传动,直齿型齿型也可以满足要求。
3.2 转速转速是选择同步带齿型的另一个考虑因素。
对于高转速场合,应选择适用于高速传动的齿型,如弧形齿型或梯形齿型。
对于低转速场合,直齿型齿型也可以满足要求。
3.3 工作环境工作环境也会对同步带齿型选择产生影响。
例如,如果工作环境恶劣,存在污染物或腐蚀性物质,应选择耐磨损和耐腐蚀的齿型。
3.4 可替换性在选择同步带齿型时,还需要考虑其可替换性。
一些特殊的齿型可能难以替换或较昂贵,因此应选择常见且易于替换的齿型。
4. 同步带齿型选择的步骤综上所述,选择合适的同步带齿型需要进行以下步骤:4.1 确定传动功率和转速首先,根据传动系统的要求确定传动功率和转速。
4.2 确定工作环境考虑工作环境的条件,确定是否需要耐磨损和耐腐蚀的齿型。
- 1、下载文档前请自行甄别文档内容的完整性,平台不提供额外的编辑、内容补充、找答案等附加服务。
- 2、"仅部分预览"的文档,不可在线预览部分如存在完整性等问题,可反馈申请退款(可完整预览的文档不适用该条件!)。
- 3、如文档侵犯您的权益,请联系客服反馈,我们会尽快为您处理(人工客服工作时间:9:00-18:30)。
V带轮的结构设计 三、结构尺寸
铸铁制V带轮的典型结构有以下几种:实心式、 腹板式、 孔板式和 轮辐式。
S型
带轮基准直径dd≤(2.5~3)d(d为轴的直径,
单位为mm)时,可采用实心式结构。
P型
当3d≤dd≤300mm时,带轮常采用腹板式带轮结构。
H型
当Dd ≤ 300mm,D1-d1≥100mm时,带轮通常采用孔 板式结构。
一、定期张紧装置
采用定期改变中心距的方法来调节带的预紧力,使带 重新张紧。
1、滑道式 2、摆架式
二、自动张紧装置
将装有带轮的电动机安装在浮动的摆架 上,利用电动机的自重,使带轮随同电动 机绕固定轴摆动,以自动保持张紧力。
三、采用张紧轮的装置
当中心距不能调节时,可采用张紧轮将带张紧。
平带传动:张紧轮设置在 松边外侧靠小轮处 (∵平带可以双向弯曲,应尽量增大包角)
4. 过载保护作用
•防止措施:
1. 控制Fe< Ffmax 2. ↑F0、f、α(紧边置下)→↑Ffmax
2.弹性滑动
*原因: 带两边拉力不相等, 则弹性变形不同,带经过轮时 变形量改变,带相对轮有微量滑动
后果: 1. 带速滞后→ V1>V带>V2 V1>V2
2.带传动传动比不稳定 i n1 dd1
5、确定中心距 a 及带长 Ld 6、确定小带轮啮合齿数Zm
9、计算压轴力 Fp
8、确定带宽(取标值)
bs
bs0 1.14
Pca K z P0
7、确定基准额定功率P0
V带轮的结构设计
(Structure Design of V-Belt Sheaves)
一、V带轮设计的要求
在已经确定V带的型号和直径等参数的前提下,确定带轮的 材料,结构形式,轮槽、轮辐和轮毂的几何尺寸,公差和表 面粗糙度等。
二、同步带的参数、型式、尺寸和标记
1、同步带的参数
1)节距pb
MXL、XXL、XL、L、H、XH、XXH
2)带宽bs
2、同步带的标记 420 L 050
带长 代号
带宽 代号
图 同步齿形带传动
三、设计步骤和方法
1、确定计算功率 Pca=KAP 2、根据n1、 Pca 选择带的型号 3、确定带轮Z1、Z2、dd1、dd2 N 4、验算带速v ≤Vmax
E型
当dd>300mm时,带轮常采用轮辐式带轮结构。
轮槽工作表面的粗糙度一般是1.6或3.2。
第五节 带传动的张紧装置
(The tensile equipments of belt drives) 各种材质的V带经过一定时间的运转后,就会由于塑性 变形而松弛,使预紧力F0降低。为了保证带传动的能力,应 定期检查预紧力的数值。如发现不足时,必须重新张紧,才 能正常工作。常见的张紧装置有以下几种。
P0
Fev 1000
([ ] c
b1
)1
1 e fv
Av 1000
在实际工作条件下,单根V带的额定功率为:
Pr (P0 △P0 )K L Kα
kW
由紧边和松边拉力产生的拉应力;
σ1 = F 1/A MPa σ2 = F 2/A MPa
由离心力产生的拉应力;
C
FC A
qv2 A
MPa
由弯曲产生的弯曲应力。
b
2 yE dd
MPa
1. 打 滑
•原因: 当Fe>Ffmax → 打滑
• 分析:
1. 打滑可以避免 2. 打滑先发生在小带轮处 3. 打滑→带的剧烈磨损 →失效
n2 dd1(1 )
*不可 避免
滑动率
v1 v2
v1
2.弹性滑动发生在带离开带轮的那段接触弧上 3. Fe↑ → 弹性滑动↑ → 弹性滑动 范 围↑ , 当弹
性滑动扩展到整个接触弧时, Fe≥Ffmax → 打滑
单根带所能传递的最大功率: 基本额定功率
V带传动:张紧轮设置在 松边内侧靠大轮处 (∵V带只能单向弯曲,避免过多减小包角)
1.V带的结构及基本参数 A - 1400 GB11544-89
2.带传动中的力分析
F2
F2
Ff
n1
F1
F1 = F0 +Fe/2 F2 = F0 -Fe/2
n2 Ff
3.带传动的应力分析
工作时,带横截面上的应力由三部分组成: