啤酒生产过程自动控制系统设计优化
基于PLC的啤酒发酵自动控制系统设计
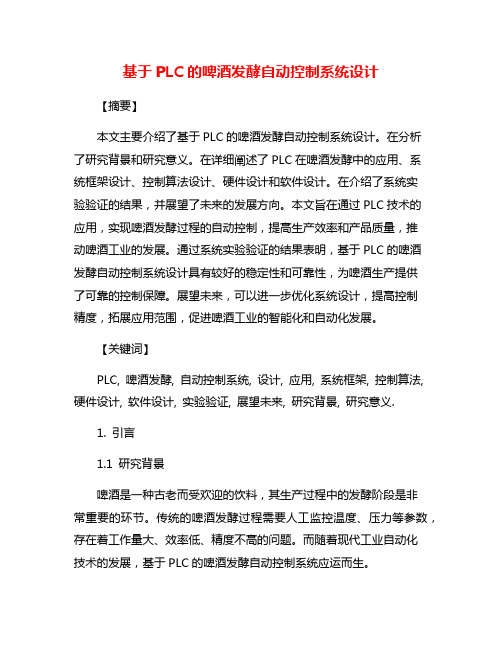
基于PLC的啤酒发酵自动控制系统设计【摘要】本文主要介绍了基于PLC的啤酒发酵自动控制系统设计。
在分析了研究背景和研究意义。
在详细阐述了PLC在啤酒发酵中的应用、系统框架设计、控制算法设计、硬件设计和软件设计。
在介绍了系统实验验证的结果,并展望了未来的发展方向。
本文旨在通过PLC技术的应用,实现啤酒发酵过程的自动控制,提高生产效率和产品质量,推动啤酒工业的发展。
通过系统实验验证的结果表明,基于PLC的啤酒发酵自动控制系统设计具有较好的稳定性和可靠性,为啤酒生产提供了可靠的控制保障。
展望未来,可以进一步优化系统设计,提高控制精度,拓展应用范围,促进啤酒工业的智能化和自动化发展。
【关键词】PLC, 啤酒发酵, 自动控制系统, 设计, 应用, 系统框架, 控制算法, 硬件设计, 软件设计, 实验验证, 展望未来, 研究背景, 研究意义.1. 引言1.1 研究背景啤酒是一种古老而受欢迎的饮料,其生产过程中的发酵阶段是非常重要的环节。
传统的啤酒发酵过程需要人工监控温度、压力等参数,存在着工作量大、效率低、精度不高的问题。
而随着现代工业自动化技术的发展,基于PLC的啤酒发酵自动控制系统应运而生。
在当前啤酒生产中推行基于PLC的发酵自动控制系统具有重要的意义。
通过引入自动化控制技术,可以提高生产效率、降低生产成本,同时还可以保证产品质量和稳定性。
基于此背景,本文将重点研究基于PLC的啤酒发酵自动控制系统设计,探索其在啤酒生产中的应用前景和发展趋势。
1.2 研究意义啤酒发酵是啤酒生产过程中至关重要的环节,控制发酵过程能够保证啤酒品质的稳定性和可控性。
基于PLC的啤酒发酵自动控制系统设计将有效解决传统手动控制中存在的调控不稳定、操作繁琐等问题,提高生产效率和产品质量。
此系统能够实现发酵过程中温度、压力、酒精含量等参数的实时监测和自动调节,确保发酵过程的精准控制和稳定运行。
研究意义在于提高啤酒生产的自动化水平和生产效率,降低人工成本,减少生产过程中的人为误操作风险,保证啤酒品质的一致性和稳定性。
基于PLC的啤酒发酵自动控制系统设计

基于PLC的啤酒发酵自动控制系统设计随着现代工业的发展,啤酒生产的自动化程度逐渐提高,传统的手工操作转变为自动控制。
本文将介绍一种基于可编程逻辑控制器(PLC)的啤酒发酵自动控制系统设计。
啤酒的发酵过程是一个复杂的化学反应过程,需要维持一定的温度、压力和PH值等参数。
传统的发酵过程需要人工监控和控制,不仅耗时耗力,而且容易产生人为误差。
采用PLC控制系统可以实现对啤酒发酵过程的自动化控制,提高生产效率和产品质量。
设计一个PLC控制器,负责监测和控制发酵过程中的各个参数。
该控制器可以通过传感器实时读取温度、压力和PH值等数据,并根据设定的控制策略进行相应的控制操作。
设计一个基于人机界面(HMI)的监控系统,用于操作员与PLC控制器的交互。
该监控系统可以实时显示发酵过程中的各个参数,并提供操作员对参数设定的控制界面。
在控制策略上,可以采用PID控制算法进行温度和PH值的控制。
PID控制算法通过调节温度和PH值的设定参数,使实际参数始终接近设定参数。
也可以设置报警机制,当温度、压力或PH值超出设定范围时,立即发出报警信号。
在硬件方面,需要选择适合的传感器和执行器。
温度传感器可以选择热电偶或温度传感器,压力传感器可以选择压力传感器,PH值传感器可以选择PH值传感器。
执行器可以选择电动阀门或蠕动泵等设备,用于自动调节温度和控制发酵过程。
在软件方面,需要编写PLC控制程序和HMI监控程序。
PLC控制程序主要包括数据采集、控制算法和控制输出等功能。
HMI监控程序主要负责数据显示、参数设定和报警处理等功能。
这些程序可以使用常见的编程语言如 ladder diagram(梯形图)或结构化文本进行开发。
基于PLC的啤酒发酵自动控制系统设计可以有效地实现对啤酒发酵过程的自动化控制,提高生产效率和产品质量。
在设计和实施过程中,需要考虑到实际工艺要求和设备性能,确保控制系统的稳定性和可靠性。
需要对系统进行综合测试和调试,以确保其正常运行。
基于PLC的啤酒发酵自动控制系统设计
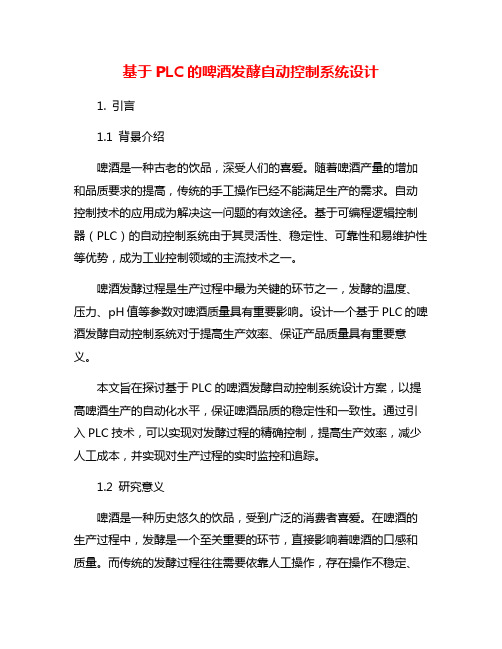
基于PLC的啤酒发酵自动控制系统设计1. 引言1.1 背景介绍啤酒是一种古老的饮品,深受人们的喜爱。
随着啤酒产量的增加和品质要求的提高,传统的手工操作已经不能满足生产的需求。
自动控制技术的应用成为解决这一问题的有效途径。
基于可编程逻辑控制器(PLC)的自动控制系统由于其灵活性、稳定性、可靠性和易维护性等优势,成为工业控制领域的主流技术之一。
啤酒发酵过程是生产过程中最为关键的环节之一,发酵的温度、压力、pH值等参数对啤酒质量具有重要影响。
设计一个基于PLC的啤酒发酵自动控制系统对于提高生产效率、保证产品质量具有重要意义。
本文旨在探讨基于PLC的啤酒发酵自动控制系统设计方案,以提高啤酒生产的自动化水平,保证啤酒品质的稳定性和一致性。
通过引入PLC技术,可以实现对发酵过程的精确控制,提高生产效率,减少人工成本,并实现对生产过程的实时监控和追踪。
1.2 研究意义啤酒是一种历史悠久的饮品,受到广泛的消费者喜爱。
在啤酒的生产过程中,发酵是一个至关重要的环节,直接影响着啤酒的口感和质量。
而传统的发酵过程往往需要依靠人工操作,存在操作不稳定、效率低下、产品质量无法保证等问题。
因此,设计一种基于PLC的啤酒发酵自动控制系统具有重要的研究意义。
首先,基于PLC的自动控制系统能够实现对发酵过程的精准控制,保障啤酒的质量稳定和一致性。
PLC技术具有高精度、高可靠性的特点,能够实时监测和调节发酵参数,确保发酵过程的稳定性和可控性。
其次,基于PLC的啤酒发酵自动控制系统可以提高生产效率,减少人力成本。
传统的人工操作需要大量的人力投入,而自动控制系统能够实现全程自动化生产,节省人力资源,提高生产效率。
总之,基于PLC的啤酒发酵自动控制系统的研究对于提高啤酒生产的质量和效率具有重要的意义,有着广阔的应用前景和市场需求。
1.3 研究目的本研究旨在设计一种基于PLC的啤酒发酵自动控制系统,以提高啤酒生产过程的自动化水平,提高生产效率,保证啤酒质量稳定性和一致性。
啤酒灌装生产线的PLC控制系统
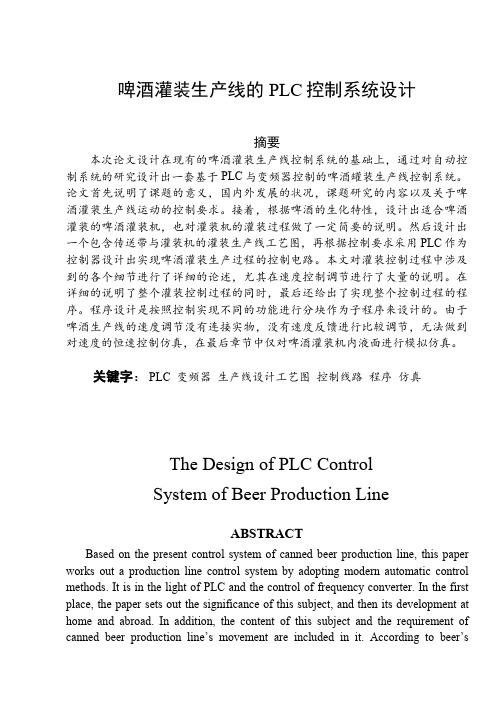
基于PLC的啤酒发酵自动控制系统设计
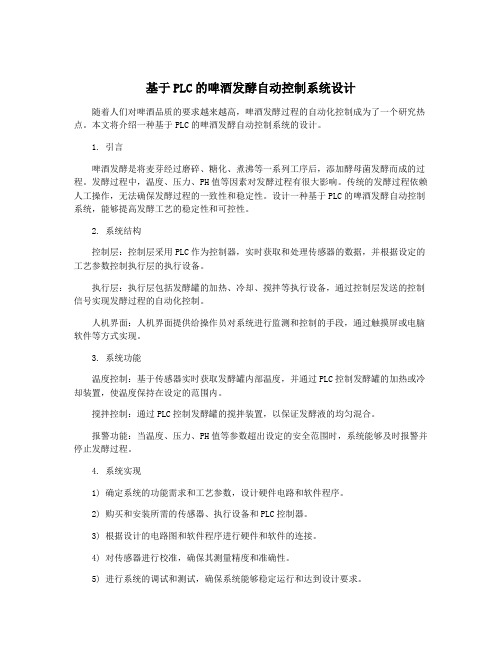
基于PLC的啤酒发酵自动控制系统设计随着人们对啤酒品质的要求越来越高,啤酒发酵过程的自动化控制成为了一个研究热点。
本文将介绍一种基于PLC的啤酒发酵自动控制系统的设计。
1. 引言啤酒发酵是将麦芽经过磨碎、糖化、煮沸等一系列工序后,添加酵母菌发酵而成的过程。
发酵过程中,温度、压力、PH值等因素对发酵过程有很大影响。
传统的发酵过程依赖人工操作,无法确保发酵过程的一致性和稳定性。
设计一种基于PLC的啤酒发酵自动控制系统,能够提高发酵工艺的稳定性和可控性。
2. 系统结构控制层:控制层采用PLC作为控制器,实时获取和处理传感器的数据,并根据设定的工艺参数控制执行层的执行设备。
执行层:执行层包括发酵罐的加热、冷却、搅拌等执行设备,通过控制层发送的控制信号实现发酵过程的自动化控制。
人机界面:人机界面提供给操作员对系统进行监测和控制的手段,通过触摸屏或电脑软件等方式实现。
3. 系统功能温度控制:基于传感器实时获取发酵罐内部温度,并通过PLC控制发酵罐的加热或冷却装置,使温度保持在设定的范围内。
搅拌控制:通过PLC控制发酵罐的搅拌装置,以保证发酵液的均匀混合。
报警功能:当温度、压力、PH值等参数超出设定的安全范围时,系统能够及时报警并停止发酵过程。
4. 系统实现1) 确定系统的功能需求和工艺参数,设计硬件电路和软件程序。
2) 购买和安装所需的传感器、执行设备和PLC控制器。
3) 根据设计的电路图和软件程序进行硬件和软件的连接。
4) 对传感器进行校准,确保其测量精度和准确性。
5) 进行系统的调试和测试,确保系统能够稳定运行和达到设计要求。
5. 结论基于PLC的啤酒发酵自动控制系统能够提高发酵工艺的稳定性和可控性,实现啤酒的生产自动化。
随着自动化技术的不断发展,基于PLC的啤酒发酵自动控制系统将会越来越普遍应用于啤酒生产过程中。
基于PLC的啤酒发酵自动控制系统设计
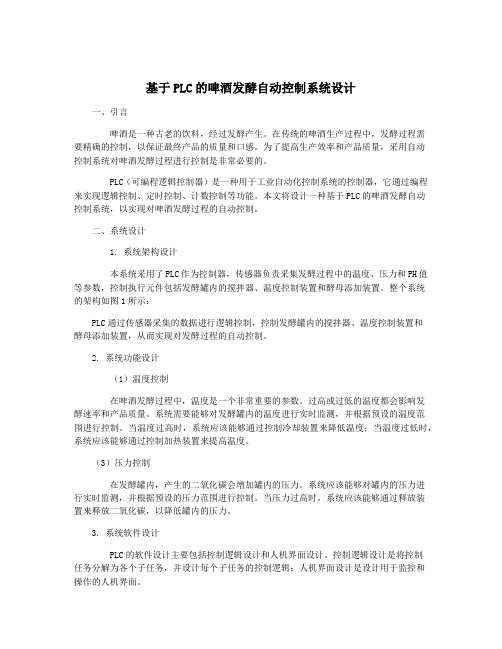
基于PLC的啤酒发酵自动控制系统设计一、引言啤酒是一种古老的饮料,经过发酵产生。
在传统的啤酒生产过程中,发酵过程需要精确的控制,以保证最终产品的质量和口感。
为了提高生产效率和产品质量,采用自动控制系统对啤酒发酵过程进行控制是非常必要的。
PLC(可编程逻辑控制器)是一种用于工业自动化控制系统的控制器,它通过编程来实现逻辑控制、定时控制、计数控制等功能。
本文将设计一种基于PLC的啤酒发酵自动控制系统,以实现对啤酒发酵过程的自动控制。
二、系统设计1. 系统架构设计本系统采用了PLC作为控制器,传感器负责采集发酵过程中的温度、压力和PH值等参数,控制执行元件包括发酵罐内的搅拌器、温度控制装置和酵母添加装置。
整个系统的架构如图1所示:PLC通过传感器采集的数据进行逻辑控制,控制发酵罐内的搅拌器、温度控制装置和酵母添加装置,从而实现对发酵过程的自动控制。
2. 系统功能设计(1)温度控制在啤酒发酵过程中,温度是一个非常重要的参数。
过高或过低的温度都会影响发酵速率和产品质量。
系统需要能够对发酵罐内的温度进行实时监测,并根据预设的温度范围进行控制。
当温度过高时,系统应该能够通过控制冷却装置来降低温度;当温度过低时,系统应该能够通过控制加热装置来提高温度。
(3)压力控制在发酵罐内,产生的二氧化碳会增加罐内的压力。
系统应该能够对罐内的压力进行实时监测,并根据预设的压力范围进行控制。
当压力过高时,系统应该能够通过释放装置来释放二氧化碳,以降低罐内的压力。
3. 系统软件设计PLC的软件设计主要包括控制逻辑设计和人机界面设计。
控制逻辑设计是将控制任务分解为各个子任务,并设计每个子任务的控制逻辑;人机界面设计是设计用于监控和操作的人机界面。
(1)控制逻辑设计控制逻辑设计首先需要确定系统的控制目标,然后根据控制目标设计各个子任务的控制逻辑,最后将各个子任务的控制逻辑组合成系统的整体控制逻辑。
对于温度控制任务,可以设计如下的控制逻辑:IF 温度 < 设定温度 - 2 THEN 打开加热装置IF 温度 > 设定温度 + 2 THEN 打开冷却装置IF 设定温度 - 2 <= 温度 <= 设定温度 + 2 THEN 关闭加热装置和冷却装置(2)人机界面设计人机界面设计主要包括监控界面和操作界面。
基于PLC的啤酒发酵自动控制系统设计

基于PLC的啤酒发酵自动控制系统设计【摘要】本文基于PLC技术,设计了一套啤酒发酵自动控制系统。
在介绍了研究背景、研究目的和研究意义。
正文部分包括系统框架设计、传感器选择与布置、控制策略设计、系统实现与调试以及性能评价。
结论部分总结了研究成果,展望了工程应用前景,并提出了存在问题与改进建议。
通过本研究,实现了啤酒发酵过程的自动化控制,提高了生产效率和产品质量,为啤酒生产领域的智能化发展提供了重要参考。
【关键词】PLC、啤酒发酵、自动控制系统、系统框架设计、传感器、控制策略、系统实现、调试、性能评价、研究成果、工程应用、问题、改进建议1. 引言1.1 研究背景研究背景中还需介绍虽然目前已有一些关于基于PLC的啤酒发酵自动控制系统设计的研究,但在实际生产中还存在着许多问题,如无法实现全自动化控制、控制策略不够精准等。
进一步深入研究和完善基于PLC的啤酒发酵自动控制系统设计,对提高啤酒生产效率、稳定产品质量具有重要意义。
本文旨在基于PLC技术,设计出一套高效、精准的啤酒发酵自动控制系统,并通过实验验证其性能,为啤酒生产实践提供可靠的技术支持。
1.2 研究目的本文旨在设计一套基于PLC的啤酒发酵自动控制系统,以实现对发酵过程的精准控制和监测。
具体目的包括:通过构建系统框架设计,实现各组件之间的有效连接和协调,确保系统的稳定运行;选择合适的传感器,并合理布置在发酵罐内,以获取实时的发酵参数数据,为后续的控制策略设计提供准确的基础数据;设计有效的控制策略,根据传感器获取的数据实现对发酵温度、PH值等参数的精准控制;通过系统实现与调试,验证系统设计的可行性,并对系统进行性能评价,确保其满足实际生产需求。
本研究旨在探索基于PLC的啤酒发酵自动控制系统在提高生产效率、保障产品质量和降低生产成本等方面的应用价值,为相关领域的研究和实际应用提供参考和借鉴。
1.3 研究意义通过引入PLC作为控制核心,可以实现对发酵过程的自动监测和调节,大大提高了生产效率和产品质量。
基于PLC的啤酒发酵自动控制系统设计
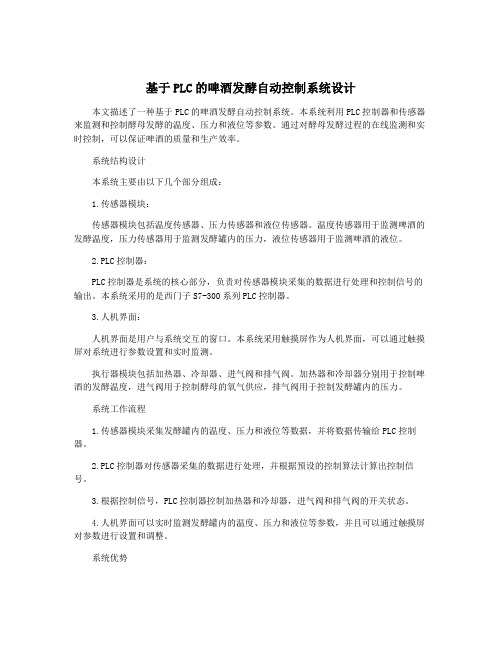
基于PLC的啤酒发酵自动控制系统设计本文描述了一种基于PLC的啤酒发酵自动控制系统。
本系统利用PLC控制器和传感器来监测和控制酵母发酵的温度、压力和液位等参数。
通过对酵母发酵过程的在线监测和实时控制,可以保证啤酒的质量和生产效率。
系统结构设计本系统主要由以下几个部分组成:1.传感器模块:传感器模块包括温度传感器、压力传感器和液位传感器。
温度传感器用于监测啤酒的发酵温度,压力传感器用于监测发酵罐内的压力,液位传感器用于监测啤酒的液位。
2.PLC控制器:PLC控制器是系统的核心部分,负责对传感器模块采集的数据进行处理和控制信号的输出。
本系统采用的是西门子S7-300系列PLC控制器。
3.人机界面:人机界面是用户与系统交互的窗口。
本系统采用触摸屏作为人机界面,可以通过触摸屏对系统进行参数设置和实时监测。
执行器模块包括加热器、冷却器、进气阀和排气阀。
加热器和冷却器分别用于控制啤酒的发酵温度,进气阀用于控制酵母的氧气供应,排气阀用于控制发酵罐内的压力。
系统工作流程1.传感器模块采集发酵罐内的温度、压力和液位等数据,并将数据传输给PLC控制器。
2.PLC控制器对传感器采集的数据进行处理,并根据预设的控制算法计算出控制信号。
3.根据控制信号,PLC控制器控制加热器和冷却器,进气阀和排气阀的开关状态。
4.人机界面可以实时监测发酵罐内的温度、压力和液位等参数,并且可以通过触摸屏对参数进行设置和调整。
系统优势本系统采用PLC控制器和传感器来监测和控制酵母发酵的温度、压力和液位等参数,具有以下优势:1.实时控制:通过对酵母发酵过程的实时控制,可以确保啤酒的质量和生产效率。
2.高精度:传感器采集数据的精度高,可以对啤酒发酵过程进行更加精准的控制。
3.智能化:PLC控制器采用先进的控制算法,可以对发酵过程进行智能化控制。
总结。
啤酒发酵自动控制系统设计
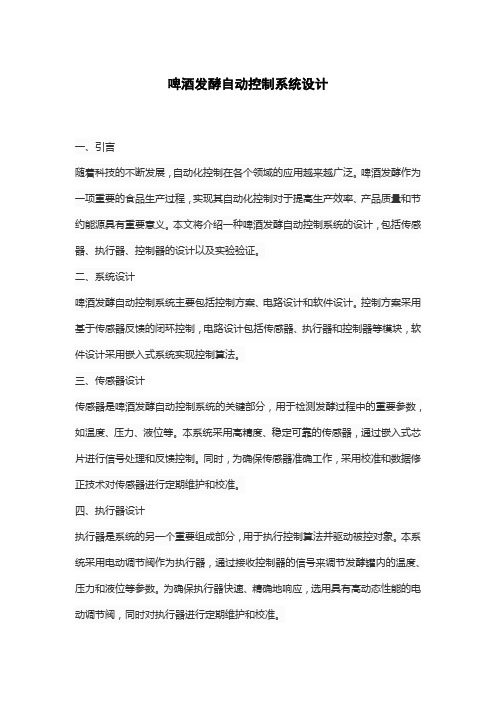
啤酒发酵自动控制系统设计一、引言随着科技的不断发展,自动化控制在各个领域的应用越来越广泛。
啤酒发酵作为一项重要的食品生产过程,实现其自动化控制对于提高生产效率、产品质量和节约能源具有重要意义。
本文将介绍一种啤酒发酵自动控制系统的设计,包括传感器、执行器、控制器的设计以及实验验证。
二、系统设计啤酒发酵自动控制系统主要包括控制方案、电路设计和软件设计。
控制方案采用基于传感器反馈的闭环控制,电路设计包括传感器、执行器和控制器等模块,软件设计采用嵌入式系统实现控制算法。
三、传感器设计传感器是啤酒发酵自动控制系统的关键部分,用于检测发酵过程中的重要参数,如温度、压力、液位等。
本系统采用高精度、稳定可靠的传感器,通过嵌入式芯片进行信号处理和反馈控制。
同时,为确保传感器准确工作,采用校准和数据修正技术对传感器进行定期维护和校准。
四、执行器设计执行器是系统的另一个重要组成部分,用于执行控制算法并驱动被控对象。
本系统采用电动调节阀作为执行器,通过接收控制器的信号来调节发酵罐内的温度、压力和液位等参数。
为确保执行器快速、精确地响应,选用具有高动态性能的电动调节阀,同时对执行器进行定期维护和校准。
五、控制器设计控制器是整个系统的核心部分,负责接收传感器的反馈信号,根据预设的控制算法对执行器进行控制,以实现啤酒发酵过程的自动化。
本系统采用嵌入式控制器,具有高可靠性、快速响应和鲁棒性等特点。
控制器通过算法优化,实现精确控制和自适应调节,以满足不同工况下的控制要求。
六、实验验证为验证啤酒发酵自动控制系统的有效性和可靠性,进行了一系列实验。
实验设置包括发酵罐、传感器、执行器和控制器等关键部件。
数据采集和处理采用专业的测试仪器进行实时监测与记录。
实验结果表明,该自动控制系统能够有效地控制啤酒发酵过程,确保产品质量和生产效率的提升。
同时,实验结果还显示,系统的稳定性和可靠性得到了充分验证,为实际生产提供了可靠保障。
七、结论本文介绍的啤酒发酵自动控制系统设计在实现生产过程的自动化和智能化方面具有显著优势。
基于PLC的啤酒发酵自动控制系统设计

基于PLC的啤酒发酵自动控制系统设计引言啤酒是一种古老的酿造饮料,而发酵是啤酒酿造过程中其中一个最关键的步骤。
发酵过程需要严格的控制温度、压力和搅拌速度等参数,以确保最终产品的质量和风味。
开发一套自动控制系统来监测和调节发酵过程是至关重要的。
本文将介绍一种基于PLC的啤酒发酵自动控制系统设计,以及其在啤酒酿造中的应用。
一、啤酒发酵过程的控制需求啤酒发酵是在一定条件下,酵母利用麦芽中的糖类产生酒精和二氧化碳的过程。
这个过程需要严格的控制来保证啤酒的质量和口感。
发酵过程中需要控制以下参数:1.温度:酵母在不同温度下会有不同的发酵速率,过高或过低的温度都会影响发酵的效果。
2.压力:发酵过程会产生大量的二氧化碳,需要通过控制压力来避免发酵罐的爆炸。
3.搅拌速度:搅拌速度会影响酵母和麦芽的接触和传质速度,从而影响发酵效果。
一套自动控制系统需要能够实时监测发酵过程中的温度、压力和搅拌速度等参数,并且能够根据实时数据对这些参数进行调节。
二、基于PLC的啤酒发酵自动控制系统设计PLC(可编程逻辑控制器)是一种专门用于工业自动化控制的设备。
它能够接收输入信号做出相应的逻辑运算,并产生输出信号来控制设备。
基于PLC的啤酒发酵自动控制系统设计如下:1.传感器和执行元件选型:系统需要使用温度传感器、压力传感器和搅拌器执行元件来感知和控制发酵过程中的各项参数。
传感器需要选择能够适应潮湿、高温环境的工业级传感器,执行元件需要选择能够承受高温、高压的设计。
2.PLC选型:根据系统的需求,选用适合的PLC型号,能够满足系统的输入输出信号需求,并且能够稳定可靠地运行在工业环境中。
3.系统架构设计:根据发酵过程的特点和需求,设计系统的硬件架构和控制逻辑。
系统需要能够同时监测和控制多个参数,并且能够在异常情况下及时报警。
系统需要能够记录历史数据以便后续分析和追溯。
4.编程设计:根据系统的硬件架构和控制逻辑,编写PLC程序,实现对发酵过程中各项参数的实时监测和控制。
基于PLC的啤酒发酵自动控制系统设计
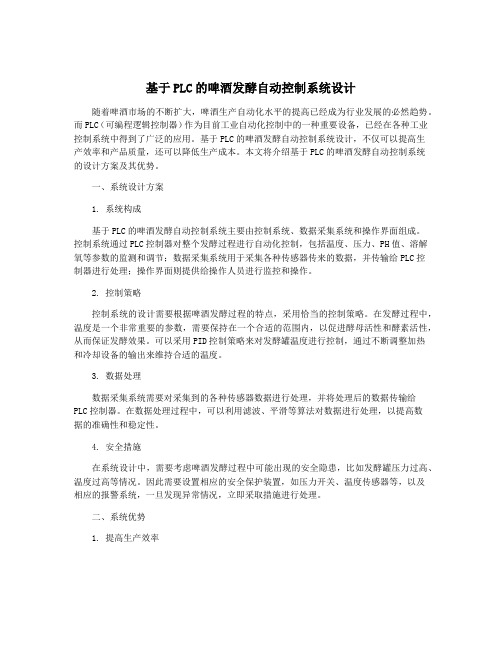
基于PLC的啤酒发酵自动控制系统设计随着啤酒市场的不断扩大,啤酒生产自动化水平的提高已经成为行业发展的必然趋势。
而PLC(可编程逻辑控制器)作为目前工业自动化控制中的一种重要设备,已经在各种工业控制系统中得到了广泛的应用。
基于PLC的啤酒发酵自动控制系统设计,不仅可以提高生产效率和产品质量,还可以降低生产成本。
本文将介绍基于PLC的啤酒发酵自动控制系统的设计方案及其优势。
一、系统设计方案1. 系统构成基于PLC的啤酒发酵自动控制系统主要由控制系统、数据采集系统和操作界面组成。
控制系统通过PLC控制器对整个发酵过程进行自动化控制,包括温度、压力、PH值、溶解氧等参数的监测和调节;数据采集系统用于采集各种传感器传来的数据,并传输给PLC控制器进行处理;操作界面则提供给操作人员进行监控和操作。
2. 控制策略控制系统的设计需要根据啤酒发酵过程的特点,采用恰当的控制策略。
在发酵过程中,温度是一个非常重要的参数,需要保持在一个合适的范围内,以促进酵母活性和酵素活性,从而保证发酵效果。
可以采用PID控制策略来对发酵罐温度进行控制,通过不断调整加热和冷却设备的输出来维持合适的温度。
3. 数据处理数据采集系统需要对采集到的各种传感器数据进行处理,并将处理后的数据传输给PLC控制器。
在数据处理过程中,可以利用滤波、平滑等算法对数据进行处理,以提高数据的准确性和稳定性。
4. 安全措施在系统设计中,需要考虑啤酒发酵过程中可能出现的安全隐患,比如发酵罐压力过高、温度过高等情况。
因此需要设置相应的安全保护装置,如压力开关、温度传感器等,以及相应的报警系统,一旦发现异常情况,立即采取措施进行处理。
二、系统优势1. 提高生产效率基于PLC的啤酒发酵自动控制系统可以实现对发酵过程的实时监测和自动控制,可以减少人工干预,提高生产效率。
系统还能够实现对发酵参数的精确控制,保证产品质量的稳定性。
2. 降低生产成本自动化控制可以减少人工操作,降低人工成本,同时节约能源和原材料的消耗,从而降低生产成本。
基于PLC的啤酒发酵自动控制系统设计
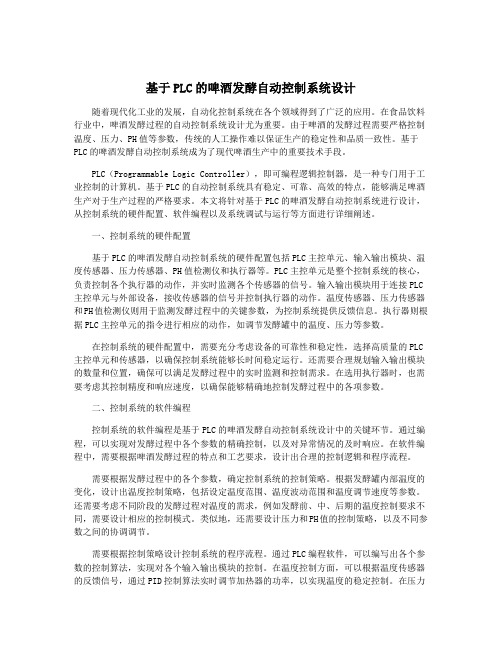
基于PLC的啤酒发酵自动控制系统设计随着现代化工业的发展,自动化控制系统在各个领域得到了广泛的应用。
在食品饮料行业中,啤酒发酵过程的自动控制系统设计尤为重要。
由于啤酒的发酵过程需要严格控制温度、压力、PH值等参数,传统的人工操作难以保证生产的稳定性和品质一致性。
基于PLC的啤酒发酵自动控制系统成为了现代啤酒生产中的重要技术手段。
PLC(Programmable Logic Controller),即可编程逻辑控制器,是一种专门用于工业控制的计算机。
基于PLC的自动控制系统具有稳定、可靠、高效的特点,能够满足啤酒生产对于生产过程的严格要求。
本文将针对基于PLC的啤酒发酵自动控制系统进行设计,从控制系统的硬件配置、软件编程以及系统调试与运行等方面进行详细阐述。
一、控制系统的硬件配置基于PLC的啤酒发酵自动控制系统的硬件配置包括PLC主控单元、输入输出模块、温度传感器、压力传感器、PH值检测仪和执行器等。
PLC主控单元是整个控制系统的核心,负责控制各个执行器的动作,并实时监测各个传感器的信号。
输入输出模块用于连接PLC 主控单元与外部设备,接收传感器的信号并控制执行器的动作。
温度传感器、压力传感器和PH值检测仪则用于监测发酵过程中的关键参数,为控制系统提供反馈信息。
执行器则根据PLC主控单元的指令进行相应的动作,如调节发酵罐中的温度、压力等参数。
在控制系统的硬件配置中,需要充分考虑设备的可靠性和稳定性,选择高质量的PLC 主控单元和传感器,以确保控制系统能够长时间稳定运行。
还需要合理规划输入输出模块的数量和位置,确保可以满足发酵过程中的实时监测和控制需求。
在选用执行器时,也需要考虑其控制精度和响应速度,以确保能够精确地控制发酵过程中的各项参数。
二、控制系统的软件编程控制系统的软件编程是基于PLC的啤酒发酵自动控制系统设计中的关键环节。
通过编程,可以实现对发酵过程中各个参数的精确控制,以及对异常情况的及时响应。
基于PLC的啤酒发酵自动控制系统设计
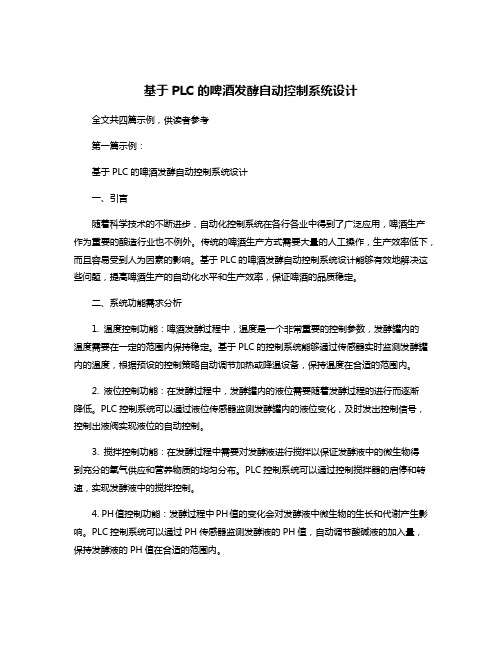
基于PLC的啤酒发酵自动控制系统设计全文共四篇示例,供读者参考第一篇示例:基于PLC的啤酒发酵自动控制系统设计一、引言随着科学技术的不断进步,自动化控制系统在各行各业中得到了广泛应用,啤酒生产作为重要的酿造行业也不例外。
传统的啤酒生产方式需要大量的人工操作,生产效率低下,而且容易受到人为因素的影响。
基于PLC的啤酒发酵自动控制系统设计能够有效地解决这些问题,提高啤酒生产的自动化水平和生产效率,保证啤酒的品质稳定。
二、系统功能需求分析1. 温度控制功能:啤酒发酵过程中,温度是一个非常重要的控制参数,发酵罐内的温度需要在一定的范围内保持稳定。
基于PLC的控制系统能够通过传感器实时监测发酵罐内的温度,根据预设的控制策略自动调节加热或降温设备,保持温度在合适的范围内。
2. 液位控制功能:在发酵过程中,发酵罐内的液位需要随着发酵过程的进行而逐渐降低。
PLC控制系统可以通过液位传感器监测发酵罐内的液位变化,及时发出控制信号,控制出液阀实现液位的自动控制。
3. 搅拌控制功能:在发酵过程中需要对发酵液进行搅拌以保证发酵液中的微生物得到充分的氧气供应和营养物质的均匀分布。
PLC控制系统可以通过控制搅拌器的启停和转速,实现发酵液中的搅拌控制。
4. PH值控制功能:发酵过程中PH值的变化会对发酵液中微生物的生长和代谢产生影响。
PLC控制系统可以通过PH传感器监测发酵液的PH值,自动调节酸碱液的加入量,保持发酵液的PH值在合适的范围内。
出预设范围,就能够及时发出故障报警信号,提醒操作人员进行相应的处理。
三、系统结构设计基于PLC的啤酒发酵自动控制系统由PLC控制器、传感器、执行机构和人机界面组成。
PLC控制器负责接收传感器采集的各个控制参数数据,根据预设的控制策略进行控制计算,并通过输出模块控制执行机构完成相应的控制动作。
传感器负责采集发酵过程中各个控制参数的数据,如温度传感器、液位传感器、PH传感器、氧气浓度传感器等。
啤酒发酵自动控制系统的开发

啤酒发酵自动控制系统的开发摘要:本文主要介绍了整个啤酒发酵监控系统的开发过程,并在传统的PID控制算法基础上提出了更为灵活进行了改进,使整个监控系统更加实用。
关键词:发酵监控系统模糊智能控制可编程控制器1 引言啤酒的发酵是一个复杂的生物化学反应过程。
针对啤酒发酵过程受许多干扰因素的影响,具有大惯性、大滞后和严重的非线性特性,以及过程对自动监控系统的要求,引入以被调变量的偏差和偏差的变化趋势为依据的模糊智能控制算法,设计了啤酒发酵过程监控系统,并讨论了系统工程的软硬件实现的问题。
系统的实际运行效果表明,该系统算法适应性和灵活性强,控制精度较高,运行效果理想,发酵过程动态特性好,啤酒生产波动小,啤酒质量稳定。
啤酒口味和实际要求的不同,啤酒的发酵工艺曲线也就不同,但是对于确定好的啤酒发酵工艺,就应严格按照工艺曲线去控制温度和压力等,这样才能保证啤酒的质量。
在啤酒发酵过程中,酵母的发酵性能受发酵温度的影响。
由于发酵中有热量释放出来,因而使发酵中的麦汁温度上升,同时促使酶反应加速。
酵母的发酵性能必须限定在一定范围内,这就是实际发酵操作中的控制工作。
整个控制工作都是由发酵控制系统来完成的。
2 啤酒发酵系统控制算法设计控制算法是整个控制系统的灵魂。
本文提出一种基于神经网络的模糊自适应PID控制方案,它一方面利用模糊逻辑的“概念”抽象能力和非线性处理能力,另一方面利用神经网络的自学习能力和任意函数的逼近能力,通过两者的有机结合寻找一个最佳的P,I,D非线性组合控制规律,以实现对未知对象进行在线控制,并具备适应控制环境变化的能力和自学习能力。
此算法既能增强系统的鲁棒性和智能性,又能使设计变得简单,易于实现。
基于神经网络的模糊PID控制系统结构主要包括四个部分:(1)传统PID控制结构由PID控制器和广义被控对象构成一个典型的闭环控制系统,只是此时的PID参数通过神经网络实现在线修改。
(2)模糊量化模块对系统的状态变量进行归档模糊化和归一化处理。
基于PLC的啤酒发酵自动控制系统设计

基于PLC的啤酒发酵自动控制系统设计1. 引言1.1 研究背景啤酒是一种古老的饮料,广泛受到人们的喜爱。
随着啤酒市场的不断扩大和消费需求的增加,啤酒生产的自动化控制系统变得越来越重要。
传统的啤酒生产过程中,发酵过程需要人工监控和调节,存在着生产效率低、产品质量不稳定等问题。
研究基于PLC的啤酒发酵自动控制系统设计具有重要意义。
在传统的啤酒生产中,发酵过程是整个生产过程中最关键的环节之一。
发酵过程中,需要监测和调节多个参数,包括温度、压力、PH 值等。
传统的控制方法往往依赖于人工经验,存在着主观性强、操作繁琐等问题。
采用基于PLC的自动控制系统能够实现对发酵参数的实时监测和自动调节,提高了生产效率和产品质量。
基于PLC的啤酒发酵自动控制系统设计是当前啤酒生产领域的研究热点之一。
通过引入PLC技术,可以实现啤酒发酵过程的自动化控制,提高生产效率,保证产品质量稳定。
本研究旨在探究基于PLC的啤酒发酵自动控制系统设计,为啤酒生产的自动化和智能化发展提供技术支持。
1.2 研究目的研究目的是设计并实现基于PLC的啤酒发酵自动控制系统,以提高生产效率和产品质量,实现发酵过程的精确监控和调节。
通过该系统,可以减少人为操作失误和提高工作效率,同时确保发酵参数稳定并符合生产要求。
利用PLC技术进行自动化控制,还可以减少人力成本并降低生产过程中的风险,提高工作安全性。
通过本研究,希望能够为啤酒生产企业提供一种先进、高效、安全的控制方案,为啤酒行业的发展和技术进步做出贡献。
2. 正文2.1 PLC在啤酒发酵中的应用啤酒生产过程中的发酵阶段对温度、压力、氧气含量等参数的精确控制至关重要。
传统的手动控制存在操作繁琐、精度低、易出错等问题,而基于PLC的自动控制系统则能够有效解决这些问题。
PLC系统还可以与其他设备和传感器进行实时数据交换,实现对发酵过程的全面监测。
通过在PLC中设定合适的控制算法,可以根据实时数据调节发酵参数,确保啤酒的发酵过程达到最佳状态。
基于PLC的啤酒发酵自动控制系统设计

基于PLC的啤酒发酵自动控制系统设计随着科技的不断发展,啤酒生产工艺也在不断创新和改进。
而自动化控制系统作为工业生产中的重要组成部分,其在啤酒发酵过程中的应用也逐渐受到关注。
本文将介绍基于可编程逻辑控制器(PLC)的啤酒发酵自动控制系统设计,详细阐述其原理、功能和优势。
一、啤酒发酵过程概述啤酒的生产过程主要包括麦芽糖化、酵母发酵、发酵后处理等阶段。
其中酵母发酵是啤酒生产的关键环节,也是整个制酒工艺过程中最为复杂的部分。
在发酵过程中,需要控制温度、pH值、搅拌速度等参数,以保证酵母在最适宜的条件下进行发酵,从而保证啤酒的品质和口感。
传统的啤酒发酵控制方法主要依靠操作工人的经验和手动调节设备的方式,存在操作不精准、易出错等问题。
而基于PLC的自动控制系统,可以实现对发酵过程的精准控制,并能够自动记录和报警,大大提高了生产效率和产品质量。
1. PLC系统架构基于PLC的啤酒发酵自动控制系统由PLC主控模块、输入输出模块、人机界面、传感器和执行器等部分组成。
PLC主控模块负责接收传感器的数据信息,并根据预设的控制策略来控制执行器进行相应的操作;输入输出模块负责与传感器和执行器之间进行信号的转换和传递;人机界面用于监控和操作整个系统,通过触摸屏或者键盘进行参数设置和实时监测。
2. 控制策略设计啤酒发酵过程中需要对温度、pH值、搅拌速度等参数进行精准控制。
在设计控制策略时,需要根据不同的发酵阶段和啤酒种类来确定相应的控制参数范围和控制逻辑。
在温度控制方面,可以根据酵母的适宜生长温度和发酵反应的温度特性,设置相应的控制策略,实现温度的保持和调节;在pH值控制方面,需要根据酵母的酸碱耐受性和发酵过程中产生的酸碱性物质来确定控制范围和控制方式;在搅拌速度控制方面,需要根据酵母的需氧性和氧气传质特性来确定控制范围和控制方法等。
3. 系统功能设计基于PLC的啤酒发酵自动控制系统可以实现温度、pH值、搅拌速度等参数的实时监测和控制,并能够实现数据的记录和报警功能。
基于PLC的啤酒发酵自动控制系统设计
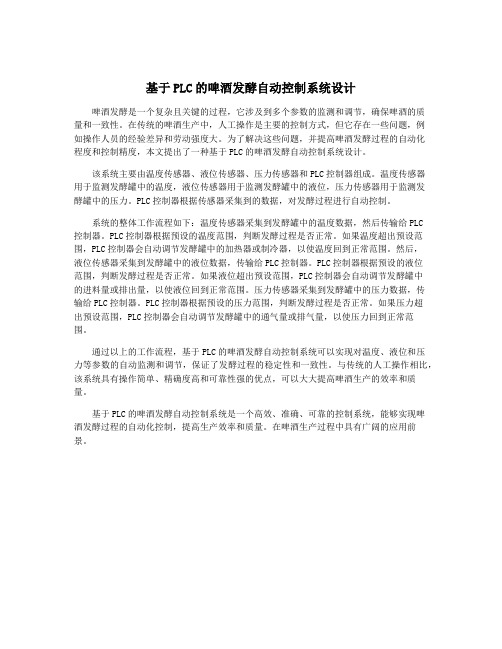
基于PLC的啤酒发酵自动控制系统设计啤酒发酵是一个复杂且关键的过程,它涉及到多个参数的监测和调节,确保啤酒的质量和一致性。
在传统的啤酒生产中,人工操作是主要的控制方式,但它存在一些问题,例如操作人员的经验差异和劳动强度大。
为了解决这些问题,并提高啤酒发酵过程的自动化程度和控制精度,本文提出了一种基于PLC的啤酒发酵自动控制系统设计。
该系统主要由温度传感器、液位传感器、压力传感器和PLC控制器组成。
温度传感器用于监测发酵罐中的温度,液位传感器用于监测发酵罐中的液位,压力传感器用于监测发酵罐中的压力。
PLC控制器根据传感器采集到的数据,对发酵过程进行自动控制。
系统的整体工作流程如下:温度传感器采集到发酵罐中的温度数据,然后传输给PLC控制器。
PLC控制器根据预设的温度范围,判断发酵过程是否正常。
如果温度超出预设范围,PLC控制器会自动调节发酵罐中的加热器或制冷器,以使温度回到正常范围。
然后,液位传感器采集到发酵罐中的液位数据,传输给PLC控制器。
PLC控制器根据预设的液位范围,判断发酵过程是否正常。
如果液位超出预设范围,PLC控制器会自动调节发酵罐中的进料量或排出量,以使液位回到正常范围。
压力传感器采集到发酵罐中的压力数据,传输给PLC控制器。
PLC控制器根据预设的压力范围,判断发酵过程是否正常。
如果压力超出预设范围,PLC控制器会自动调节发酵罐中的通气量或排气量,以使压力回到正常范围。
通过以上的工作流程,基于PLC的啤酒发酵自动控制系统可以实现对温度、液位和压力等参数的自动监测和调节,保证了发酵过程的稳定性和一致性。
与传统的人工操作相比,该系统具有操作简单、精确度高和可靠性强的优点,可以大大提高啤酒生产的效率和质量。
基于PLC的啤酒发酵自动控制系统是一个高效、准确、可靠的控制系统,能够实现啤酒发酵过程的自动化控制,提高生产效率和质量。
在啤酒生产过程中具有广阔的应用前景。
基于PLC的啤酒发酵自动控制系统设计
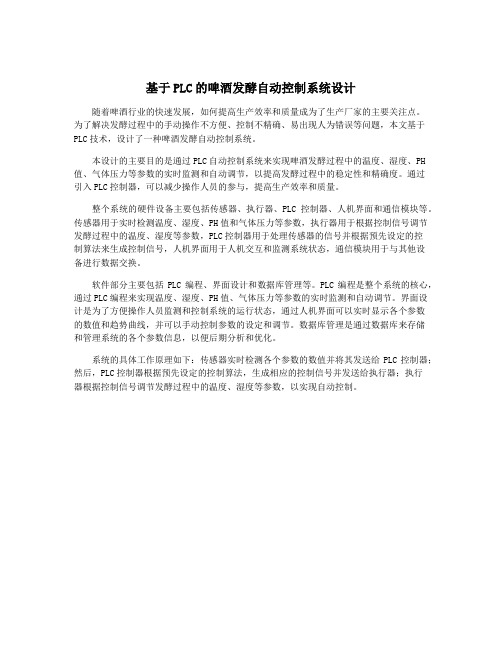
基于PLC的啤酒发酵自动控制系统设计
随着啤酒行业的快速发展,如何提高生产效率和质量成为了生产厂家的主要关注点。
为了解决发酵过程中的手动操作不方便、控制不精确、易出现人为错误等问题,本文基于PLC技术,设计了一种啤酒发酵自动控制系统。
本设计的主要目的是通过PLC自动控制系统来实现啤酒发酵过程中的温度、湿度、PH 值、气体压力等参数的实时监测和自动调节,以提高发酵过程中的稳定性和精确度。
通过
引入PLC控制器,可以减少操作人员的参与,提高生产效率和质量。
整个系统的硬件设备主要包括传感器、执行器、PLC控制器、人机界面和通信模块等。
传感器用于实时检测温度、湿度、PH值和气体压力等参数,执行器用于根据控制信号调节发酵过程中的温度、湿度等参数,PLC控制器用于处理传感器的信号并根据预先设定的控
制算法来生成控制信号,人机界面用于人机交互和监测系统状态,通信模块用于与其他设
备进行数据交换。
软件部分主要包括PLC编程、界面设计和数据库管理等。
PLC编程是整个系统的核心,通过PLC编程来实现温度、湿度、PH值、气体压力等参数的实时监测和自动调节。
界面设计是为了方便操作人员监测和控制系统的运行状态,通过人机界面可以实时显示各个参数
的数值和趋势曲线,并可以手动控制参数的设定和调节。
数据库管理是通过数据库来存储
和管理系统的各个参数信息,以便后期分析和优化。
系统的具体工作原理如下:传感器实时检测各个参数的数值并将其发送给PLC控制器;然后,PLC控制器根据预先设定的控制算法,生成相应的控制信号并发送给执行器;执行
器根据控制信号调节发酵过程中的温度、湿度等参数,以实现自动控制。
基于PLC的啤酒发酵自动控制系统设计
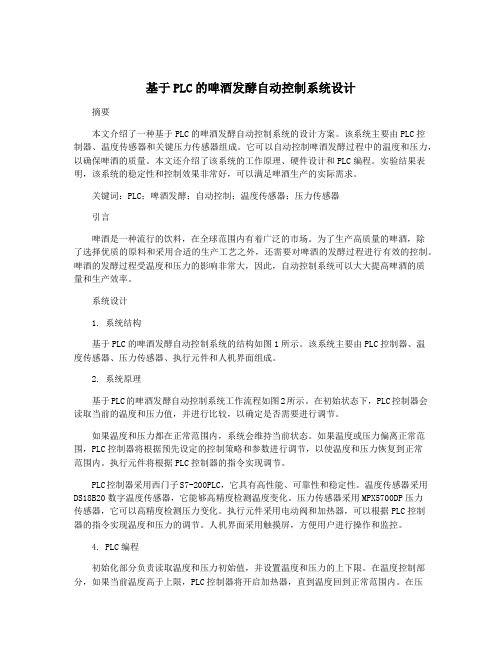
基于PLC的啤酒发酵自动控制系统设计摘要本文介绍了一种基于PLC的啤酒发酵自动控制系统的设计方案。
该系统主要由PLC控制器、温度传感器和关键压力传感器组成。
它可以自动控制啤酒发酵过程中的温度和压力,以确保啤酒的质量。
本文还介绍了该系统的工作原理、硬件设计和PLC编程。
实验结果表明,该系统的稳定性和控制效果非常好,可以满足啤酒生产的实际需求。
关键词:PLC;啤酒发酵;自动控制;温度传感器;压力传感器引言啤酒是一种流行的饮料,在全球范围内有着广泛的市场。
为了生产高质量的啤酒,除了选择优质的原料和采用合适的生产工艺之外,还需要对啤酒的发酵过程进行有效的控制。
啤酒的发酵过程受温度和压力的影响非常大,因此,自动控制系统可以大大提高啤酒的质量和生产效率。
系统设计1. 系统结构基于PLC的啤酒发酵自动控制系统的结构如图1所示。
该系统主要由PLC控制器、温度传感器、压力传感器、执行元件和人机界面组成。
2. 系统原理基于PLC的啤酒发酵自动控制系统工作流程如图2所示。
在初始状态下,PLC控制器会读取当前的温度和压力值,并进行比较,以确定是否需要进行调节。
如果温度和压力都在正常范围内,系统会维持当前状态。
如果温度或压力偏离正常范围,PLC控制器将根据预先设定的控制策略和参数进行调节,以使温度和压力恢复到正常范围内。
执行元件将根据PLC控制器的指令实现调节。
PLC控制器采用西门子S7-200PLC,它具有高性能、可靠性和稳定性。
温度传感器采用DS18B20数字温度传感器,它能够高精度检测温度变化。
压力传感器采用MPX5700DP压力传感器,它可以高精度检测压力变化。
执行元件采用电动阀和加热器,可以根据PLC控制器的指令实现温度和压力的调节。
人机界面采用触摸屏,方便用户进行操作和监控。
4. PLC编程初始化部分负责读取温度和压力初始值,并设置温度和压力的上下限。
在温度控制部分,如果当前温度高于上限,PLC控制器将开启加热器,直到温度回到正常范围内。
基于PLC的啤酒发酵自动控制系统设计

基于PLC的啤酒发酵自动控制系统设计本文针对啤酒发酵过程中的自动控制问题,设计了一种基于PLC的啤酒发酵自动控制系统。
本文分别就控制系统的硬件选型、软件设计、控制策略和系统运行等方面进行详细介绍和分析。
1、控制系统硬件选型本系统采用三菱PLC FX2N-32MR作为控制器,配合三菱触摸屏进行操作界面设计和参数设置。
控制器和触摸屏之间通过RS232进行通信,以实现数据传输和数据显示功能。
此外,本系统还选用了温度、液位、气压和流量等传感器进行数据采集。
2、软件设计本系统主要采用ST语言进行软件编写,根据实际需求设计了三个主程序:数据采集程序、PID控制程序和触摸屏控制程序。
其中,数据采集程序主要负责对传感器数据进行采集和处理,PID控制程序负责控制发酵罐内的温度、液位、气压和流量等参数,使其始终处于最优状态。
触摸屏控制程序则是用户与系统之间的交互平台,通过触摸屏可以进行参数设置和操作控制等功能。
3、控制策略本系统采用经典的PID控制算法进行参数控制。
具体而言,对于发酵罐的温度控制,系统通过温度传感器对温度进行实时监测,并将监测到的温度值与设定的目标温度进行比较,以计算出误差值。
接着,根据PID控制算法的控制策略,对比例、积分和微分三个参数进行计算,并通过控制电路将控制信号传输到加热器或冷却器上,以实现对温度的有效控制。
4、系统运行通过对系统进行实验测试,可以发现本系统具有运行可靠、控制精确、响应速度快等优点。
在实际应用中,只需设置不同的控制参数就可以实现针对不同类型啤酒的发酵控制,可广泛应用于啤酒生产企业中。
综上所述,本文基于PLC的啤酒发酵自动控制系统设计已经基本实现,具有较高的设计实用性和研究价值。
- 1、下载文档前请自行甄别文档内容的完整性,平台不提供额外的编辑、内容补充、找答案等附加服务。
- 2、"仅部分预览"的文档,不可在线预览部分如存在完整性等问题,可反馈申请退款(可完整预览的文档不适用该条件!)。
- 3、如文档侵犯您的权益,请联系客服反馈,我们会尽快为您处理(人工客服工作时间:9:00-18:30)。
李 金 宝
黑龙江生物科技职业 学院 , 黑龙江哈尔滨 ,1 5 0 0 2 5
摘 要 :啤酒生产过程自 动控制系统设计优劣直接影响啤酒生 产成本, 啤酒生产控制精度, 操作人员的体力劳动, 生产效率和安全生产。本文
从 啤酒生产过程 自动控制 系统 网络设计优化 、设 备联动 、手 自动切换 、安全 回路设 计、建立温度控制 虚拟仪 器五个方面 阐述 了啤酒生产过程 自动 化 控制系统设计优化的原 因、方 法。
关键 词 :啤酒;1 9 动控制系统; 设计i 优化
随着国家经济 的发展和人 民生活水平 的改善 ,以及 工厂 自动化水 平 的逐 步提高 ,我 国啤酒工业也 得到 了空 前发展 ,啤酒 工业 的发展对 国 民经济建设 和发展起 到了重要的促进作用。 尽 管如此 ,我 国的啤酒生产工 业 目前还存在 许多不尽如 人意的地
制系统 和发酵过程 的计算机 控制系统两部分 组成。从 自动 控制的角度
来看 ,两个 主控系统 的控 制行为存在 明显 的独立性 ,测控要 求和控制 策略也具 有很大的差异 。从 信息交流和信息 管理的角度看 ,二者 表现
出一定 的相 关性 ,两个主控 系统将通过上层 网络与领导部 门及质 量分 析部 门的管理 计算机相连 接。然而 ,整个 自动 控制系统的运行效 率受 限于 以下两方面 :一方面是 P L O在可连 接的操 作站 数量上的限制。另
啤酒生产控 制系统 的网络是 以生 产过 程为单位来 设计主控 系统 ,最常
另一 方面是 具备高效的数据 采样 方式。P L C全映射服务器是 对控
制级多个 P L C 中各种数据 的全部映射 ,所 以高效 的数 据采样 对保 证数
据实时性具有重要作用。
见的完成 整个啤酒生产过 程的全 自动 控制 ,是 由糖 化过程 的计 算机控 作者筒介 :
当P L C投入 运行后 。其工作过程一般分 为三个阶段 ,即输入采样 、用
但是提高 啤酒生产过程 的自动化水平 , 将 会是改 变上述落后面貌 的一
个极其重要 的措施。只有 运用先进 的自动化技术进 行操作和管理 ,才 能实现产 品多元化 ,才 能保证稳定 、一致 的产 品质 量 ,才能真正强 化 企 业管理 ,降低 成本 ,提 高企 业经济效益 。针对我 国啤酒生产过程 自 动 控制系统设计 水平落后 的现 状 ,本文对 啤酒生产过程 自动化控制 系 统设 计进行深入 研究 ,优化 生产过程 自动 化控制 系统设 计 ,使其更 加 有利 于啤酒 生产过程 ,降低 生产成本。啤 酒生产过程一般 不是一种恒 定 的稳态值 ,而 是随时 间变化 的优化轨迹 。例如 ,温 度工艺 曲线。 啤 酒生 产过程是一 类典型 的间歇 生产过程 ,按 生产工艺划分 为麦芽汁 制 备 、啤酒发酵 、啤 酒过滤和啤 酒灌装 四大过 程 ,每个过程 中又包含许 多生 产子工序 ,其 生产工艺 多变、生产过程 不连续 、非稳 态 ,工艺和
一
方, 1 I 啤酒产 品档 次低 ,品种少 ;翟 能耗和原料 消耗大 ; 3 很 多企业 为 中小型 啤酒厂 ,自控水平差 ,技 术含量低 ,生产 过程主要采 用简单
控 制 ,甚 至 人 工 控 制 为 主 ,这 与 高 新 技 术 飞 速 发 展 的 今 天 极 不 相 称 ;
方 面 是 MP I 通信 速 率 的 限 制 。
传输 ,P L C全 映射 服务器硬件设备 采用工业服务器 ,服务器 功能设计
方面要具备 以下两个方面 :
一
对象特 性多样 、复 杂 ,过程信 息很不完备 ,这 些特点使得优 化啤酒生
产过程 自动控 制系统 设计 具有相 当大的难度。
方面是具备可靠高效 的远程传输 方式。服务器给操作站 发送数
管理水平 欠佳 ,难 以与பைடு நூலகம்外企 业进 行竞争。
因此 ,如何提高产 品的技术含 量 ,提高生产 过程的 自动化 水平 , 提高我 国啤酒工业 的综 合实力 ,积极 参与国 际市 场竞争成 了一 个刻不 容缓 的课题 。当然 ,导致 我国啤酒生产 工业 出现 上述落后 、被 动状 态 的原 因,既有工艺水平 方面的原 因,也 有 自动化水 平等方面 的原因 ,
据采 用重复广播发送模式 ;服务器还需具 备远 程转发功能 ,将操 作站 的指令通过服 务器传导给 P L C,并 且对于远程转发的结果还 应有快速
远 程 回 读 功 能 , 以提 高 指 令 发 送 的 可 靠 性 。
1 啤酒生 产控制系统的网络需要优化 1 . 1 啤酒生产控制 系统 网络缺 陷 为了实现整套计算机 综合 自动化 系统 的可靠 性和可操作 性 ,一般
户程序执 行和输 出刷新 3个阶段。 本 文针对啤酒生 产控制系统 的网络 缺陷 ,为 了能适合 大型啤酒生
产过程 综合 自动控 制系统的通信要 求,提 出了进一步在车 间级和控制 级 中添加 P L C全 映射服务器 。构成数 据映射级 的 P L C全映射服 务器 新型 网络模式 。P L C全映射服务器实质是建立 了操作站与 P L C 间以及 操作站 与操作站间一 座高效通信 的桥梁 。为保 证数据之 间高效可靠 的
李金 宝 门9 8 1年生 / 男/ 甘肃 灵台人 / 硕士 / 讲师/ 研 究方向为啤酒生产工艺及优化
1 . 2 啤酒生产 控制系统的网络优化措施
C AN总线控制系统是一种全数字化 、全分散 、全 开放 、可互操 作 和开放式互连的新一代控 制系统 。与传统的 D CS( 集散控 制系统 )相
比,C A N总线 控制系统具有可靠性高 、可维护性好 、成本低 、实时性 好、实现 了控制管理一体化的结构体系等优点 。C A N总线控 制系统 由 监 控计算机 ( 上位机 ) 、C A N总线 和现场控制器 ( 下位机 ) 3部分构 成。 P L C作 为下位机在 啤酒发酵过程 控制可分 为检测部分 和控 制部分 。