自动线控制
基于PLC技术的自动化生产线控制系统设计

基于PLC技术的自动化生产线控制系统设计自动化生产线是现代工业生产中的关键技术之一,能够提高生产效率、降低成本、提高产品质量和稳定性。
而PLC(Programmable Logic Controller,可编程逻辑控制器)作为现代自动化控制系统的核心,具有可编程、多功能、高可靠性等特点,被广泛应用于各个行业的自动化生产线控制系统中。
设计基于PLC技术的自动化生产线控制系统需要遵循以下几个步骤:1.系统分析和规划:首先,需要对整个生产线的工艺流程进行分析和规划,确定需要自动化控制的环节和目标,确保自动化系统能够满足生产需求。
2.设计电气和机械硬件:根据分析和规划的结果,设计电气和机械硬件,包括传感器、执行器、电机、开关等元件的选型和布置,确保硬件的可靠性和稳定性。
3. PLC程序设计:根据工艺流程和硬件设计,编写PLC的控制程序。
PLC的控制程序可以使用各种编程语言,如传统的ladder diagram(梯形图)、structured text(结构化文本)等,根据需要选择合适的编程语言。
4.联机调试和测试:在控制程序编写完成后,将PLC与整个系统进行联机调试和测试,确保各个环节的传感器、执行器和PLC之间的通信和控制正常运行。
5.故障检测和维护:设计自动化生产线控制系统时,需要考虑到故障检测和维护的问题。
可以利用PLC的故障诊断功能,实时监测传感器和执行器的状态,并通过人机界面或网络等方式报警和通知工作人员。
在设计基于PLC技术的自动化生产线控制系统时,需要考虑以下几个方面的问题:1.系统可靠性:自动化生产线控制系统需要具有高可靠性,确保生产线的稳定运行。
因此,需要选择具有高可靠性的PLC设备,并设计备份和冗余系统以应对可能的故障。
2.通信与网络功能:现代自动化生产线控制系统通常需要与其他系统进行通信和数据交换。
因此,设计时需要考虑PLC的通信和网络功能,确保系统能够与其他设备进行数据传输和控制。
自动生产线控制技术概述【文献综述】

⾃动⽣产线控制技术概述【⽂献综述】⽂献综述电⽓⼯程及⾃动化⾃动⽣产线控制技术概述摘要:⾃动⽣产线简称为⾃动线。
是⼀种能够实现产品⽣产过程⾃动化的机器体系。
它是按照⼀定的⼯艺顺序排列若⼲台⾃动机床,然后⽤⼯件传送装置和控制系统连接起来进⾏⾃动加⼯的连续⼯作。
从⽽提⾼⼯作效率及劳动⽣产率,并降低⽣产成本,提⾼产品的精度与⼯艺。
关键词:⾃动线;⽣产线;PLC;控制⽹络1 引⾔从⼆⼗世纪⼆⼗年代开始,我国的机械制造业中开始出现⾃动⽣产线。
由于现代化⼯业技术的飞速发展,特别是电⼦元件等⾏业的突飞猛进,企业对⽣产与其对应的产品配件的⽣产效率和产品精度的要求就越来越严格[1]。
因此对落后的技术与陈旧的设备进⾏改⾰,使其在⽣产过程中能符合更⾼的⾃动化要求,从⽽为企业减免不必要的⿇烦与损失,进⽽提⾼经济效益与⽣产效益。
采⽤⾃动⽣产线能够在有限时间内⽣产出⼤量的产品,⼯艺先进,可靠⽽且稳定。
⾃动⽣产线⼜被⼈们称为⾃动线,所谓⾃动线就是能使得⽣产过程⾃动化的体系。
它可以通过传送系统和控制系统来操控⽣产零件,并伴有巡查和信号控制系统来监控零件。
通过这样⼀套完整的系统来进⾏⾃动化的加⼯,检测,装卸及运输。
实现了产品⽣产的⾼度连续化及连续⾃动化的⽣产线[2]。
2 ⾃动⽣产线控制系统2.1⾃动⽣产线的发展及特点⾃动⽣产线是由最早期的流⽔⽣产线发展⽽来的。
最早是在机械制造中出现了组合机床,随后改⾰称为了组合机床⾃动线。
之后在汽车制造业中出现了流⽔⽣产线和半⾃动⽣产线。
并经过⾜够时间的⾰新演变成了今天的⾃动⽣产线。
⾃动⽣产线通过⼀套完整的体系来控制系统进⾏⾃动化的加⼯,在⼤批量的⽣产过程中采⽤⾃动⽣产线还具有提⾼劳动⽣产率,改善⽣产条件,缩短了⽣产周期,降低⽣产成本等众多优势。
是可以为企业创造经济效益和保障产品均衡性的重要制造设备[3]。
2.2⾃动⽣产线的组成及应⽤范围⾃动⽣产线简称为⾃动线。
是⼀种能够实现产品⽣产过程⾃动化的机器体系。
基于PLC的自动化生产线控制系统设计与优化
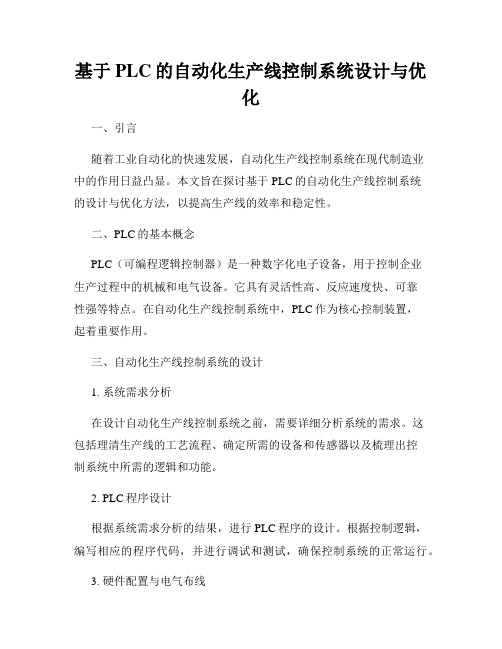
基于PLC的自动化生产线控制系统设计与优化一、引言随着工业自动化的快速发展,自动化生产线控制系统在现代制造业中的作用日益凸显。
本文旨在探讨基于PLC的自动化生产线控制系统的设计与优化方法,以提高生产线的效率和稳定性。
二、PLC的基本概念PLC(可编程逻辑控制器)是一种数字化电子设备,用于控制企业生产过程中的机械和电气设备。
它具有灵活性高、反应速度快、可靠性强等特点。
在自动化生产线控制系统中,PLC作为核心控制装置,起着重要作用。
三、自动化生产线控制系统的设计1. 系统需求分析在设计自动化生产线控制系统之前,需要详细分析系统的需求。
这包括理清生产线的工艺流程、确定所需的设备和传感器以及梳理出控制系统中所需的逻辑和功能。
2. PLC程序设计根据系统需求分析的结果,进行PLC程序的设计。
根据控制逻辑,编写相应的程序代码,并进行调试和测试,确保控制系统的正常运行。
3. 硬件配置与电气布线根据自动化生产线的布局和控制要求,进行PLC的硬件配置和电气布线。
选择合适的PLC型号和模块,将其连接到相应的设备和传感器上,并进行电气连接,确保信号传输的稳定。
4. HMI界面设计设计人机界面(HMI),使操作人员能够直观地监控和控制整个生产线。
通过HMI界面,可以实时显示设备的状态、报警信息、生产数据等,方便操作和管理。
四、自动化生产线控制系统的优化1. 数据采集与分析利用PLC控制系统中的数据采集功能,实时获取生产线中的各种数据。
通过对数据的分析和统计,可以找出潜在的问题和改进的空间,为系统优化提供依据。
2. 节能与环保优化自动化生产线控制系统的同时,应注重能源的节约和环境的保护。
通过控制设备的启停、调整工作参数等方式,达到节能减排的目的。
3. 故障诊断与维护建立完善的故障诊断与维护机制,可以大大提高生产线的可靠性和稳定性。
及时发现并解决故障,减少生产线的停机时间,提高生产效率。
五、总结与展望基于PLC的自动化生产线控制系统设计与优化是提升制造业竞争力的重要手段。
工作台自动往返控制线路工作原理

在当今社会,工作效率和自动化程度越来越受到重视。
其中,工作台自动往返控制线路是一种重要的自动化设备,其工作原理对于提高生产效率和减少人力成本具有重要意义。
本文将深入探讨工作台自动往返控制线路的工作原理,并就其在工业生产中的应用进行详细分析。
一、工作台自动往返控制线路的概念1.1 工作台自动往返控制线路的定义工作台自动往返控制线路是指一种能够实现自动来回移动的控制系统,其通过预设的程序和信号来实现工作台在工作区域内自动移动的功能。
1.2 工作台自动往返控制线路的组成工作台自动往返控制线路主要由控制器、传感器、执行机构等组成。
控制器负责指挥和控制整个系统的运行,传感器用于感知工作环境,执行机构则实现工作台的移动。
二、工作台自动往返控制线路的工作原理2.1 传感器感知工作环境工作台自动往返控制线路首先通过传感器对工作环境进行感知,包括检测工作区域的障碍物、测量工作区域的距离等。
2.2 控制器进行信号处理传感器采集到的信息将被传输到控制器中进行信号处理,控制器根据这些信息来决定工作台的移动方向、速度和距离。
2.3 执行机构实现工作台移动控制器发出指令后,执行机构就会根据控制信号来实现工作台的移动,包括正向运动、反向运动以及停止等。
三、工作台自动往返控制线路的应用3.1 工业生产中的应用工作台自动往返控制线路广泛应用于自动化生产线上,能够大大提高生产效率和降低人力成本,尤其在装配线、流水线等场景中表现突出。
3.2 其他领域的应用除了工业生产,工作台自动往返控制线路也被应用于仓储物流系统、医疗器械制造等领域,为智能制造和智能产业提供了有力支持。
四、个人观点和理解在我看来,工作台自动往返控制线路是一种极具实用性和前景的自动化设备,其在工业生产中的应用前景广阔。
随着科技的不断发展,工作台自动往返控制线路将会在更多领域得到应用,并为人类社会带来更多便利。
在这篇文章中,我们深入探讨了工作台自动往返控制线路的工作原理及其在工业生产中的应用。
智能制造中的自动化生产线控制与网络连接模块设计
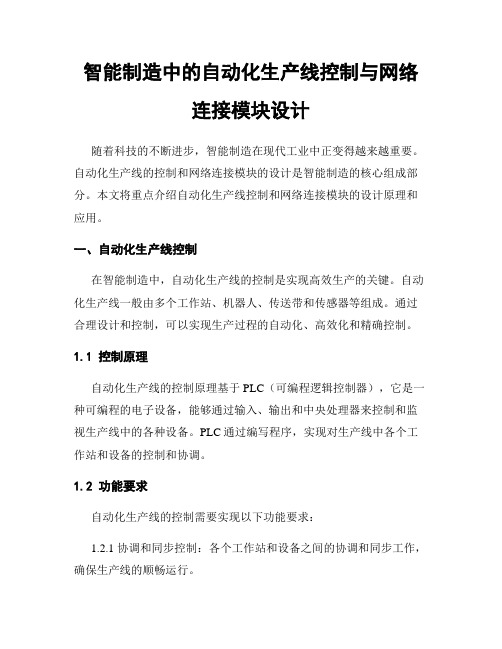
智能制造中的自动化生产线控制与网络连接模块设计随着科技的不断进步,智能制造在现代工业中正变得越来越重要。
自动化生产线的控制和网络连接模块的设计是智能制造的核心组成部分。
本文将重点介绍自动化生产线控制和网络连接模块的设计原理和应用。
一、自动化生产线控制在智能制造中,自动化生产线的控制是实现高效生产的关键。
自动化生产线一般由多个工作站、机器人、传送带和传感器等组成。
通过合理设计和控制,可以实现生产过程的自动化、高效化和精确控制。
1.1 控制原理自动化生产线的控制原理基于PLC(可编程逻辑控制器),它是一种可编程的电子设备,能够通过输入、输出和中央处理器来控制和监视生产线中的各种设备。
PLC通过编写程序,实现对生产线中各个工作站和设备的控制和协调。
1.2 功能要求自动化生产线的控制需要实现以下功能要求:1.2.1 协调和同步控制:各个工作站和设备之间的协调和同步工作,确保生产线的顺畅运行。
1.2.2 故障监测和报警:通过传感器对设备和工作站进行监测,一旦出现故障,及时发出警报并采取相应措施。
1.2.3 工艺优化:通过实时监测和调整,优化生产工艺参数,提高生产效率和产品质量。
1.2.4 数据采集和分析:收集生产数据,进行数据分析和挖掘,为生产线的优化和改进提供决策支持。
二、网络连接模块设计在现代智能制造中,自动化生产线需要与上位机、监控系统和其他设备进行网络连接,实现实时数据传输和远程控制。
网络连接模块的设计是实现智能制造的关键。
2.1 网络通信协议网络连接模块需要支持一种或多种网络通信协议,例如以太网、无线网络和物联网等。
通过网络通信协议,自动化生产线可以与其他设备进行实时数据交换和控制指令传输。
2.2 数据传输和处理网络连接模块需要能够实现数据的高效传输和处理。
对于大数据量的传输,需要优化数据传输的速率和延迟;对于数据的处理,可以使用数据压缩和加密等技术来提高效率和安全性。
2.3 安全性和稳定性在网络连接模块的设计中,安全性和稳定性是至关重要的。
基于PLC的自动化生产线控制系统设计与实现
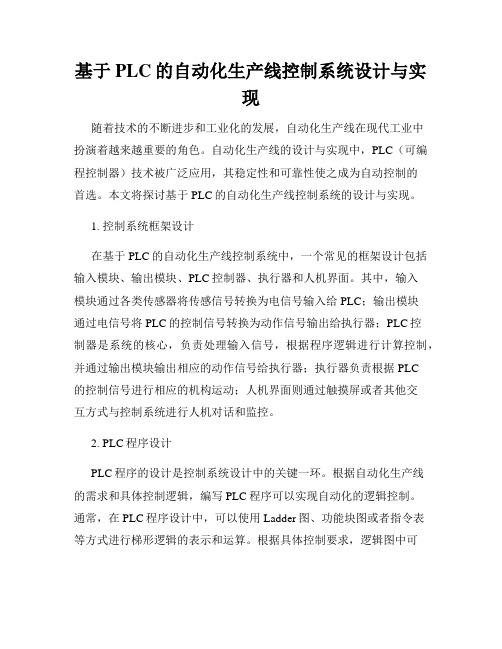
基于PLC的自动化生产线控制系统设计与实现随着技术的不断进步和工业化的发展,自动化生产线在现代工业中扮演着越来越重要的角色。
自动化生产线的设计与实现中,PLC(可编程控制器)技术被广泛应用,其稳定性和可靠性使之成为自动控制的首选。
本文将探讨基于PLC的自动化生产线控制系统的设计与实现。
1. 控制系统框架设计在基于PLC的自动化生产线控制系统中,一个常见的框架设计包括输入模块、输出模块、PLC控制器、执行器和人机界面。
其中,输入模块通过各类传感器将传感信号转换为电信号输入给PLC;输出模块通过电信号将PLC的控制信号转换为动作信号输出给执行器;PLC控制器是系统的核心,负责处理输入信号,根据程序逻辑进行计算控制,并通过输出模块输出相应的动作信号给执行器;执行器负责根据PLC的控制信号进行相应的机构运动;人机界面则通过触摸屏或者其他交互方式与控制系统进行人机对话和监控。
2. PLC程序设计PLC程序的设计是控制系统设计中的关键一环。
根据自动化生产线的需求和具体控制逻辑,编写PLC程序可以实现自动化的逻辑控制。
通常,在PLC程序设计中,可以使用Ladder图、功能块图或者指令表等方式进行梯形逻辑的表示和运算。
根据具体控制要求,逻辑图中可以包含计数器、定时器、比较器等功能模块,实现对传感信号的监测、计数和定时控制等功能。
3. 实时监测与报警处理在自动化生产线控制系统中,实时监测和报警处理是非常重要的环节。
通过PLC与各类传感器的连接,可以实时监测生产线中的各项参数和状态。
一旦出现异常情况,PLC可以及时发出报警信号,并通过人机界面向操作员提示异常信息。
同时,PLC还可以与其他设备进行联动控制,实现故障自动排除或者设备自动停机等功能,保证生产线的安全和稳定运行。
4. 网络通信与数据分析随着信息化的发展,自动化生产线控制系统的网络通信与数据分析功能也变得越来越重要。
通过将PLC与上位机或者云平台进行网络连接,可以实现远程监控和管理。
自动化控制线线径计算公式

自动化控制线线径计算公式引言。
自动化控制系统是现代工业生产中不可或缺的一部分,它可以通过控制各种设备和机器来实现生产过程的自动化操作。
在自动化控制系统中,线线径的计算是一个重要的参数,它直接影响着系统的稳定性和性能。
本文将介绍自动化控制线线径的计算公式及其应用。
1. 线线径的概念。
线线径是指在自动化控制系统中,用于传输电气信号或电力的导线的直径。
在实际应用中,线线径的选择直接影响着电气信号的传输质量和电力传输的效率。
因此,合理选择线线径对于系统的稳定性和性能至关重要。
2. 线线径的计算方法。
线线径的计算方法通常是根据导线的电流载荷和电压降来确定的。
一般来说,可以使用下面的公式来计算线线径:线线径 = (电流载荷×系统电阻)/(电压降×导线长度×导线材料电阻率)。
其中,电流载荷是指系统中的电流负载,系统电阻是指系统中的总电阻,电压降是指导线两端的电压差,导线长度是指导线的实际长度,导线材料电阻率是指导线材料的电阻率。
3. 线线径计算的应用。
线线径的计算可以应用于各种自动化控制系统中,比如工业生产中的电力传输系统、自动化机器人系统、智能家居系统等。
通过合理计算线线径,可以确保系统的电气信号传输质量和电力传输效率,从而提高系统的稳定性和性能。
4. 线线径计算的实例。
假设一个工业生产中的电力传输系统,其电流载荷为100A,系统电阻为0.1Ω,电压降为5V,导线长度为10m,导线材料电阻率为1.72×10^-8Ω·m。
根据上面的公式,可以计算出线线径为:线线径 = (100A × 0.1Ω)/(5V × 10m × 1.72×10^-8Ω·m)≈ 0.058mm。
通过这个实例可以看出,合理计算线线径可以帮助工程师选择合适的导线规格,从而确保系统的稳定性和性能。
5. 结论。
线线径的计算是自动化控制系统中的一个重要参数,它直接影响着系统的稳定性和性能。
自动化生产线控制技术研究及应用
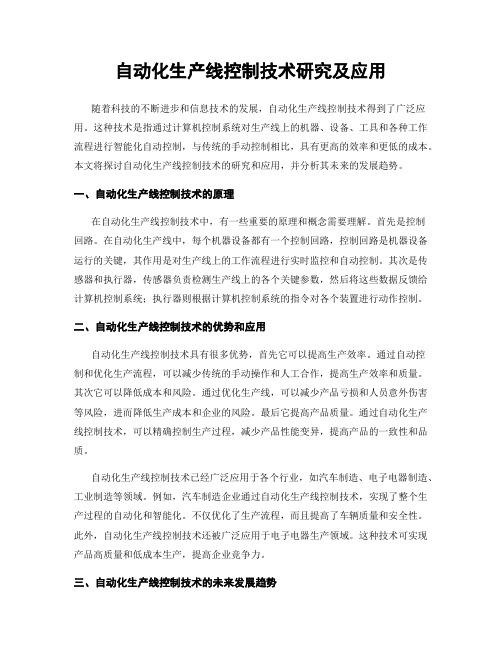
自动化生产线控制技术研究及应用随着科技的不断进步和信息技术的发展,自动化生产线控制技术得到了广泛应用。
这种技术是指通过计算机控制系统对生产线上的机器、设备、工具和各种工作流程进行智能化自动控制,与传统的手动控制相比,具有更高的效率和更低的成本。
本文将探讨自动化生产线控制技术的研究和应用,并分析其未来的发展趋势。
一、自动化生产线控制技术的原理在自动化生产线控制技术中,有一些重要的原理和概念需要理解。
首先是控制回路。
在自动化生产线中,每个机器设备都有一个控制回路,控制回路是机器设备运行的关键,其作用是对生产线上的工作流程进行实时监控和自动控制。
其次是传感器和执行器,传感器负责检测生产线上的各个关键参数,然后将这些数据反馈给计算机控制系统;执行器则根据计算机控制系统的指令对各个装置进行动作控制。
二、自动化生产线控制技术的优势和应用自动化生产线控制技术具有很多优势,首先它可以提高生产效率。
通过自动控制和优化生产流程,可以减少传统的手动操作和人工合作,提高生产效率和质量。
其次它可以降低成本和风险。
通过优化生产线,可以减少产品亏损和人员意外伤害等风险,进而降低生产成本和企业的风险。
最后它提高产品质量。
通过自动化生产线控制技术,可以精确控制生产过程,减少产品性能变异,提高产品的一致性和品质。
自动化生产线控制技术已经广泛应用于各个行业,如汽车制造、电子电器制造、工业制造等领域。
例如,汽车制造企业通过自动化生产线控制技术,实现了整个生产过程的自动化和智能化。
不仅优化了生产流程,而且提高了车辆质量和安全性。
此外,自动化生产线控制技术还被广泛应用于电子电器生产领域。
这种技术可实现产品高质量和低成本生产,提高企业竞争力。
三、自动化生产线控制技术的未来发展趋势自动化生产线控制技术未来有很大的发展前景。
首先,其规模将进一步扩大。
公司企业、高校实验室等机构将进一步投入研发和应用,生产线上的自动化设备将进一步升级,产业规模将不断扩大。
工业自动化流水线控制系统设计与实现

工业自动化流水线控制系统设计与实现随着科技的不断进步和发展,工业自动化成为现代工业生产的重要组成部分。
在大多数生产过程中,流水线系统被广泛应用,以提高生产效率和降低劳动力成本。
因此,设计和实现一个高效可靠的工业自动化流水线控制系统至关重要。
一、设计和规划流水线系统在设计工业自动化流水线控制系统之前,首先要对整个生产过程进行分析和规划。
这包括确定生产线上所需的机械设备、传感器和执行器,以及确定物料的流动路径和工艺流程。
此外,还需要考虑生产速度、生产质量和安全性等因素。
通过仔细的规划和设计,可以确保流水线系统的高效运行和最佳生产结果。
二、选用合适的硬件设备选用合适的硬件设备对于流水线控制系统的设计和实现至关重要。
这些设备包括PLC(可编程逻辑控制器)、传感器、执行器和人机界面等。
PLC是流水线控制系统的大脑,它负责接收和处理传感器信号,并控制执行器的动作。
传感器用于检测物料的位置、速度和质量等信息,而执行器用于控制物料的运动和加工过程。
人机界面可以方便操作人员对流水线系统进行监控和控制。
三、开发和编程控制系统流水线控制系统的开发和编程是设计和实现过程中的核心部分。
在编程控制系统时,需要根据实际需求编写相应的逻辑控制程序。
这些程序包括流水线的启动和停止、物料的进料和出料、故障检测和处理等功能。
此外,还需要编写相应的报警和记录日志的程序,以便及时发现和处理异常情况。
通过精确和可靠的编程,可以确保流水线控制系统的稳定运行和高效生产。
四、测试和调试系统在流水线控制系统设计和实现完成后,需要进行测试和调试。
这包括检查硬件设备的连接和功能是否正常,验证编程逻辑是否准确和可靠。
通过实际测试,可以发现和解决潜在的问题,确保系统的稳定性和可靠性。
五、优化和改进系统工业自动化流水线控制系统的设计和实现是一个持续改进的过程。
一旦系统开始运行,就可以通过监控和分析实时数据来优化系统的性能和效率。
根据生产过程中的实际需求,可以进行系统参数的调整和优化,以提高生产效率和质量。
基于PLC的自动化生产线控制系统设计

基于PLC的自动化生产线控制系统设计自动化生产线控制系统设计是现代工业生产的重要组成部分,其通过使用计算机和程序控制装置,实现对生产线上各个设备的协调运行和监控。
在本次任务中,我将介绍基于PLC(可编程逻辑控制器)的自动化生产线控制系统设计。
首先,我们需要了解PLC的基本概念和工作原理。
PLC是一种专门用于工业自动化控制的计算机控制设备,具有高速、可靠和灵活的特点。
它由CPU、输入/输出模块和通信模块等组成,可以通过编程来实现对各个输入和输出模块的控制。
接下来,我们需要进行自动化生产线的布局设计。
根据生产线的具体需求,我们可以将其分为不同的工作区域,每个区域包括一组设备和工作站。
在设计过程中,需要考虑设备之间的物料流动、工作站的工艺要求以及工作效率等因素,以确保生产线的流程畅通和产能最大化。
然后,我们可以开始进行PLC程序的设计。
根据生产线的工艺流程和操作要求,我们可以编写程序来控制各个设备的启停、速度调节、报警监测等功能。
为了提高生产效率和故障诊断能力,我们可以使用事件触发、定时器和计数器等技术来实现自动化控制。
在设计PLC程序时,我们需要合理划分输入和输出模块,将输入模块用于接收传感器的信号,如温度、压力和位置等,将输出模块用于对执行元件的控制,如电机、气缸和阀门等。
此外,我们还需要考虑数据的传输方式和通信协议,以确保各个设备之间的数据交互和信息共享。
在PLC程序设计完成后,接下来是PLC系统的调试和测试。
我们可以使用仿真软件来验证程序的正确性和可靠性,在确保没有异常情况和逻辑错误后,将程序下载到实际的PLC设备中进行实时运行和调试。
在调试过程中,可以使用在线监控功能来实时查看PLC的运行状态,以确保生产线的正常运行。
最后,我们需要对自动化生产线控制系统进行优化和改进。
根据实际运行情况和需求变化,我们可以不断对PLC程序进行优化和改良,以提高系统的稳定性和可靠性。
此外,我们还可以采用数据采集和分析技术,对生产线进行监测和优化,以实现最佳生产效率和质量。
《自动生产线控制系统设计》任务书

《自动生产线控制系统设计》任务书一、课题全自动生产线控制系统设计二、设计目的以模块化生产加工系统(MPS)为对象,全面了解全自动生产线的运行模式,通过对模块化生产加工系统(MPS)中单模块和多模块联网的控制设计,全面了解和掌握PLC控制系统的设计方法,包括控制系统的硬件电路设计、控制系统的程序设计、PLC和PLC之间的通讯、系统调试,同时熟悉触摸屏人机界面和组态软件在全自动生产线上的应用。
三、使用设备1. 模块化生产教学系统(MPS);2. 安装WINDOWS操作系统的PC机(配备FXGXWIN、EB500、KINGVIEW软件);3.MT506/T/C/M触摸屏;4. PC与PLC、PC与MT506/T/C/M、PLC与MT506/T/C/M的通信电缆。
四、设计要求现代工业生产要求高效率,愈来愈多的工厂采用PLC、人机界面等自动化器件构建的全自动生产线来提高生产效率。
PLC控制具有功能强、可靠性高、配置灵活、使用方便及体积小、重量轻等特点,被广泛用于自动化控制的各个领域。
触摸屏产品可以作为设备的操作面板兼显示器使用,触摸屏的触控面板可以被用户自由定义分页和自制控制菜单,灵活地定义各种按钮、设置开关等画面。
LCD显示屏也可以被灵活地定义成各种样式的状态指示灯、仪表显示面板、文字信息提示等画面,在触摸屏人机界面上定义过的输入输出变量将不占用PLC的I/O点,简化了电气控制系统的结构,提高了设备运行的可靠性。
组态软件是一种构造方便、用于控制设备和过程监控装置(如计算机)之间通信的人机界面软件,被称为“监控和数据采集系统”。
它可以在任何需要的时候把设备的运行现场的信息实时地传送到控制室,为管理人员提供实时和历史数据,优化控制现场作业,提高生产率和产品质量。
因此,人机界面产品在工业控制中获得了广泛应用。
本次设计以苏州瑞思机电公司的MPS 系统为对象,学习三菱PLC控制器的使用和联网控制的实现,学习触摸屏人机界面和“组态王”组态软件的基本应用。
小车自动往返控制线路的工作原理
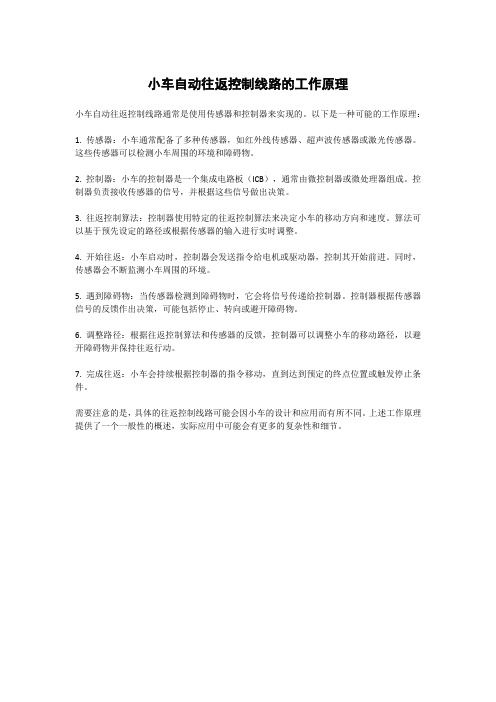
小车自动往返控制线路的工作原理
小车自动往返控制线路通常是使用传感器和控制器来实现的。
以下是一种可能的工作原理:
1. 传感器:小车通常配备了多种传感器,如红外线传感器、超声波传感器或激光传感器。
这些传感器可以检测小车周围的环境和障碍物。
2. 控制器:小车的控制器是一个集成电路板(ICB),通常由微控制器或微处理器组成。
控制器负责接收传感器的信号,并根据这些信号做出决策。
3. 往返控制算法:控制器使用特定的往返控制算法来决定小车的移动方向和速度。
算法可以基于预先设定的路径或根据传感器的输入进行实时调整。
4. 开始往返:小车启动时,控制器会发送指令给电机或驱动器,控制其开始前进。
同时,传感器会不断监测小车周围的环境。
5. 遇到障碍物:当传感器检测到障碍物时,它会将信号传递给控制器。
控制器根据传感器信号的反馈作出决策,可能包括停止、转向或避开障碍物。
6. 调整路径:根据往返控制算法和传感器的反馈,控制器可以调整小车的移动路径,以避开障碍物并保持往返行动。
7. 完成往返:小车会持续根据控制器的指令移动,直到达到预定的终点位置或触发停止条件。
需要注意的是,具体的往返控制线路可能会因小车的设计和应用而有所不同。
上述工作原理提供了一个一般性的概述,实际应用中可能会有更多的复杂性和细节。
基于PLC 技术的自动化生产线控制系统设计

技术创新基于PLC技术的自动化生产线控制系统设计王文魁(辽宁建筑职业学院辽宁辽阳111000)摘要:随着现代工业技术的发展,自动化控制技术普遍应用于矿业等领域。
在近些年产业转型压力的影响下,使用自动化生产线是企业生产的必然趋势。
制造业总提高生产效率是企业发展的核心竞争力。
自动化生产线由送料加工输送与分拣等单元组成,各单元有控制工作的PLC,信号经PLC处理后发出执行原件动作指令,用PPI通信协议完成各单元通信,设计完成PLC控制的软硬件自动化生产线。
关键词:PLC技术自动化生产线控制系统设计工业生产中图分类号:p45.13文献标识码:A文章编号:1674-098X(2022)01(a)-0040-03 Design of Automatic Production Line Control System Based onPLC TechnologyWANG Wenkui(Liaoning Jianzhu Vocational College,Liaoyang,Liaoning Province,111000China)Abstract:With the development of modern industrial technology,automatic control technology is widely used in mining and other fields.Under the pressure of industrial transformation in recent years,the use of automatic production lines to reduce labor costs is an inevitable trend of enterprise production.Improving the production efficiency of manufacturing industry is the core competitiveness of enterprise development.The automatic production line is composed of units such as feeding processing,conveying and sorting.Each unit has a PLC to controlthe work,the signal is processed by the PLC and then issues the action instruction to execute the original,the communication of each unit is completed with PPI communication protocol,and the software and hardware automatic production line controlled by PLC is designed.Key Words:PLC technology;Automatic production line;Control system design;Industrial production中华人民共和国成立后,中国制造业迅速发展,由于微电子技术、控制技术飞速发展,计算机技术广泛应用为机械制造领域带来新技术,计算机技术发展促进工业自动化技术的进步,自动化技术影响了其他诸多领域。
基于PLC的自动化生产线控制系统分析

• 65•自动化的生产线具备着组装灵活、安全性高以及构造较为简单等多种优点,可以根据实际需求和车间的大小来增减设备,这也使其成为了现代化企业中建造生产线的重要选择。
因此,本文首先对自动化生产线控制系统的整体架构加以明确,然后对自动化生产线控制系统的内部硬件构成展开分析,在此基础上提出基于PLC 的自动化生产线控制系统的设计措施。
1 自动化生产线控制系统的整体架构如图1所示,自动化生产线内部的控制系统主要是由PLC 、位置传感器、工业计算机、电机驱动器以及工业摄像头等所构成。
在整体控制系统当中,三自由度的滑台是其内部的核心部件,其是由X 、Y 、Z 三个不同方向的线性模组以及与之对应的步进电机组成,完全能够通过PLC 来为驱动器发送准确的控制信号,有效控制滑台当中的三个分支,使其能够按照规定中的坐标来进行移动。
通常情况下,X 轴方向应当尽量与流水线内部的传输带维持一种平行的状态,可以利用齿轮带动皮带这一简单的驱动方式使得X 轴对应的步进电机能够更好的发挥出自身的驱动作用,实现高速运转的直线行驶,保证定位的准确性、平稳性。
而其中的横向机构就可以由Y 轴步进电机进行驱动,其整体驱动方式与X 方向基本一致,主要目的就在于能够更好的配合X 方向来完成坐标的定位工作。
升降机则是由Z 轴的步进电机进行驱动,在驱动方式上与前两者并无太大差异,在实际工作中主要就是顺着垂直的方向来上下运转,实现对各种工件的放置和抓取。
这一控制系统的主要功能有以下几个方面:一是能够实现自动操作与手动操作之间的选择;二是可以实现更加精准的控制;三是能够对工件图像进行更加准确的捕获,及时计算出与之对应的坐标;四是具备良好的安全保护功能。
图1 系统的总体设计2 自动化生产线控制系统内部的硬件构成自动生产线控制系统内部的硬件,主要是由传感器、执行部件、网络通信系统以及PLC 等所组成的。
PLC 的型号相对较多,但其内部的工作原理以及主要结构却基本一致,都是由电源、主机、外部设备接口以及拓展器接口组成的,其拥有抗干扰能力强、可靠性高以及使用较为方便等优点。
基于PLC的自动化生产线控制系统软件设计
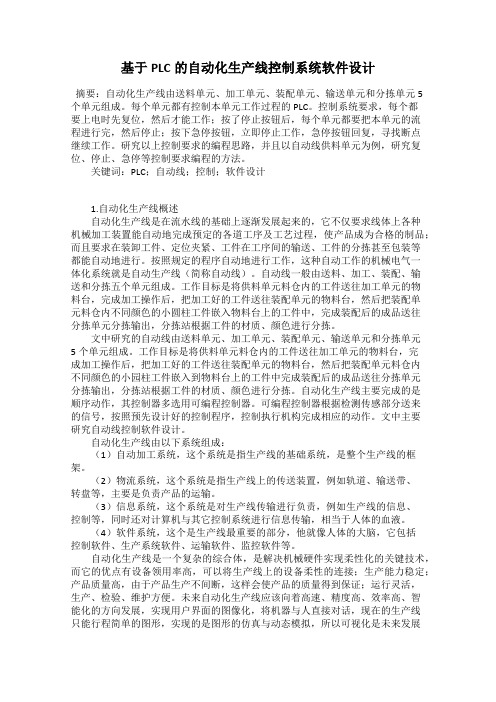
基于PLC的自动化生产线控制系统软件设计摘要:自动化生产线由送料单元、加工单元、装配单元、输送单元和分拣单元5个单元组成。
每个单元都有控制本单元工作过程的PLC。
控制系统要求,每个都要上电时先复位,然后才能工作;按了停止按钮后,每个单元都要把本单元的流程进行完,然后停止;按下急停按钮,立即停止工作,急停按钮回复,寻找断点继续工作。
研究以上控制要求的编程思路,并且以自动线供料单元为例,研究复位、停止、急停等控制要求编程的方法。
关键词:PLC;自动线;控制;软件设计1.自动化生产线概述自动化生产线是在流水线的基础上逐渐发展起来的,它不仅要求线体上各种机械加工装置能自动地完成预定的各道工序及工艺过程,使产品成为合格的制品;而且要求在装卸工件、定位夹紧、工件在工序间的输送、工件的分拣甚至包装等都能自动地进行。
按照规定的程序自动地进行工作,这种自动工作的机械电气一体化系统就是自动生产线(简称自动线)。
自动线一般由送料、加工、装配、输送和分拣五个单元组成。
工作目标是将供料单元料仓内的工件送往加工单元的物料台,完成加工操作后,把加工好的工件送往装配单元的物料台,然后把装配单元料仓内不同颜色的小圆柱工件嵌入物料台上的工件中,完成装配后的成品送往分拣单元分拣输出,分拣站根据工件的材质、颜色进行分拣。
文中研究的自动线由送料单元、加工单元、装配单元、输送单元和分拣单元5个单元组成。
工作目标是将供料单元料仓内的工件送往加工单元的物料台,完成加工操作后,把加工好的工件送往装配单元的物料台,然后把装配单元料仓内不同颜色的小园柱工件嵌入到物料台上的工件中完成装配后的成品送往分拣单元分拣输出,分拣站根据工件的材质、颜色进行分拣。
自动化生产线主要完成的是顺序动作,其控制器多选用可编程控制器。
可编程控制器根据检测传感部分送来的信号,按照预先设计好的控制程序,控制执行机构完成相应的动作。
文中主要研究自动线控制软件设计。
自动化生产线由以下系统组成:(1)自动加工系统,这个系统是指生产线的基础系统,是整个生产线的框架。
基于PLC的自动化生产线控制系统设计
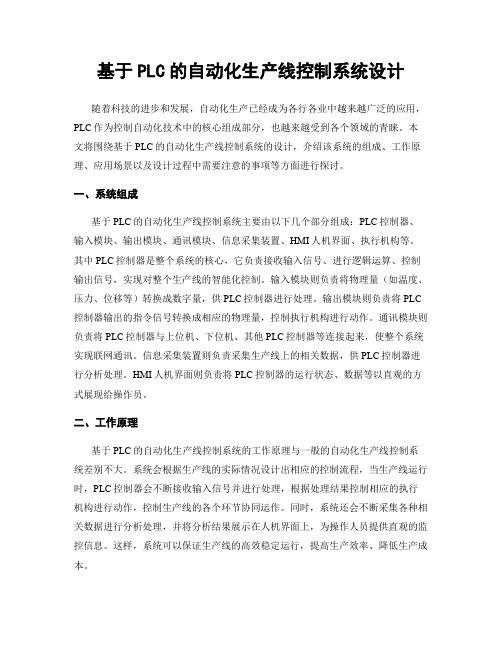
基于PLC的自动化生产线控制系统设计随着科技的进步和发展,自动化生产已经成为各行各业中越来越广泛的应用,PLC作为控制自动化技术中的核心组成部分,也越来越受到各个领域的青睐。
本文将围绕基于PLC的自动化生产线控制系统的设计,介绍该系统的组成、工作原理、应用场景以及设计过程中需要注意的事项等方面进行探讨。
一、系统组成基于PLC的自动化生产线控制系统主要由以下几个部分组成:PLC控制器、输入模块、输出模块、通讯模块、信息采集装置、HMI人机界面、执行机构等。
其中PLC控制器是整个系统的核心,它负责接收输入信号、进行逻辑运算、控制输出信号,实现对整个生产线的智能化控制。
输入模块则负责将物理量(如温度、压力、位移等)转换成数字量,供PLC控制器进行处理。
输出模块则负责将PLC 控制器输出的指令信号转换成相应的物理量,控制执行机构进行动作。
通讯模块则负责将PLC控制器与上位机、下位机、其他PLC控制器等连接起来,使整个系统实现联网通讯。
信息采集装置则负责采集生产线上的相关数据,供PLC控制器进行分析处理。
HMI人机界面则负责将PLC控制器的运行状态、数据等以直观的方式展现给操作员。
二、工作原理基于PLC的自动化生产线控制系统的工作原理与一般的自动化生产线控制系统差别不大。
系统会根据生产线的实际情况设计出相应的控制流程,当生产线运行时,PLC控制器会不断接收输入信号并进行处理,根据处理结果控制相应的执行机构进行动作,控制生产线的各个环节协同运作。
同时,系统还会不断采集各种相关数据进行分析处理,并将分析结果展示在人机界面上,为操作人员提供直观的监控信息。
这样,系统可以保证生产线的高效稳定运行,提高生产效率、降低生产成本。
三、应用场景基于PLC的自动化生产线控制系统具有广泛的应用场景。
首先,在重复性较高的生产过程中,该系统可以取代人力完成繁琐的操作,不仅减轻了人力负担,而且降低了操作风险,提高了生产效率,降低了生产成本。
毕业设计亚龙型自动生产线控制系统设计装配站控制
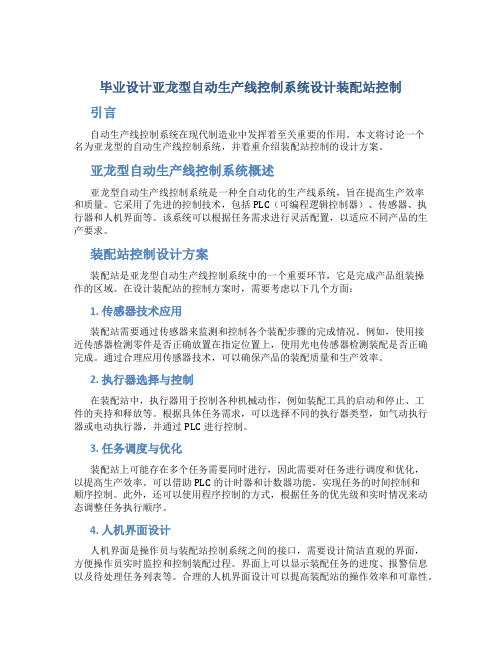
毕业设计亚龙型自动生产线控制系统设计装配站控制引言自动生产线控制系统在现代制造业中发挥着至关重要的作用。
本文将讨论一个名为亚龙型的自动生产线控制系统,并着重介绍装配站控制的设计方案。
亚龙型自动生产线控制系统概述亚龙型自动生产线控制系统是一种全自动化的生产线系统,旨在提高生产效率和质量。
它采用了先进的控制技术,包括PLC(可编程逻辑控制器)、传感器、执行器和人机界面等。
该系统可以根据任务需求进行灵活配置,以适应不同产品的生产要求。
装配站控制设计方案装配站是亚龙型自动生产线控制系统中的一个重要环节,它是完成产品组装操作的区域。
在设计装配站的控制方案时,需要考虑以下几个方面:1. 传感器技术应用装配站需要通过传感器来监测和控制各个装配步骤的完成情况。
例如,使用接近传感器检测零件是否正确放置在指定位置上,使用光电传感器检测装配是否正确完成。
通过合理应用传感器技术,可以确保产品的装配质量和生产效率。
2. 执行器选择与控制在装配站中,执行器用于控制各种机械动作,例如装配工具的启动和停止、工件的夹持和释放等。
根据具体任务需求,可以选择不同的执行器类型,如气动执行器或电动执行器,并通过PLC进行控制。
3. 任务调度与优化装配站上可能存在多个任务需要同时进行,因此需要对任务进行调度和优化,以提高生产效率。
可以借助PLC的计时器和计数器功能,实现任务的时间控制和顺序控制。
此外,还可以使用程序控制的方式,根据任务的优先级和实时情况来动态调整任务执行顺序。
4. 人机界面设计人机界面是操作员与装配站控制系统之间的接口,需要设计简洁直观的界面,方便操作员实时监控和控制装配过程。
界面上可以显示装配任务的进度、报警信息以及待处理任务列表等。
合理的人机界面设计可以提高装配站的操作效率和可靠性。
5. 故障诊断与维护在装配站运行过程中,可能会出现故障,需要及时诊断并进行维护。
为了实现快速故障诊断,可以在装配站中设置故障检测传感器,并通过PLC进行故障的判断和报警。
工业生产线(自动控制)安装和调试方案
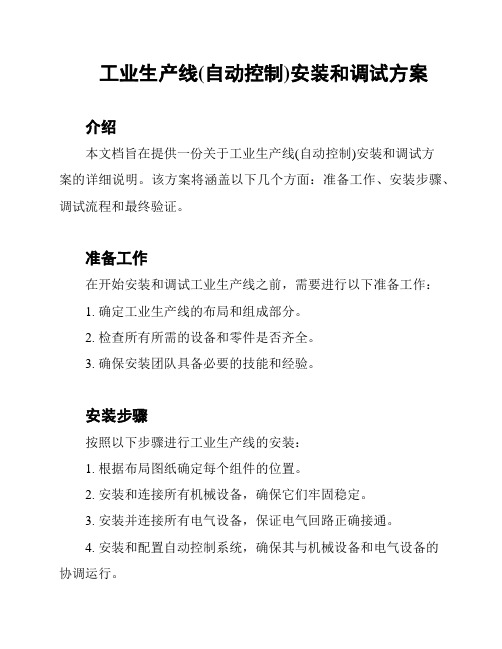
工业生产线(自动控制)安装和调试方案介绍本文档旨在提供一份关于工业生产线(自动控制)安装和调试方案的详细说明。
该方案将涵盖以下几个方面:准备工作、安装步骤、调试流程和最终验证。
准备工作在开始安装和调试工业生产线之前,需要进行以下准备工作:1. 确定工业生产线的布局和组成部分。
2. 检查所有所需的设备和零件是否齐全。
3. 确保安装团队具备必要的技能和经验。
安装步骤按照以下步骤进行工业生产线的安装:1. 根据布局图纸确定每个组件的位置。
2. 安装和连接所有机械设备,确保它们牢固稳定。
3. 安装并连接所有电气设备,保证电气回路正确接通。
4. 安装和配置自动控制系统,确保其与机械设备和电气设备的协调运行。
5. 进行安全系统的安装和设置,确保工业生产线的运行安全。
调试流程进行工业生产线调试的步骤如下:1. 启动机械设备并验证其正常运行。
2. 检查电气系统是否正常工作,确保各个设备和电路之间的连接无误。
3. 对自动控制系统进行调试,验证其能够正确地控制机械设备和电气设备的运行。
4. 进行环境测试,确保工业生产线在不同环境条件下的正常运行。
5. 运行一段时间,观察工业生产线的运行情况,排除可能出现的故障和问题。
最终验证在完成安装和调试后,需要进行最终验证以确保工业生产线的良好运行:1. 运行整个工业生产线,观察是否符合预期的生产效率和质量要求。
2. 检查自动控制系统是否稳定可靠,能够及时响应和调整。
3. 对工业生产线的各项指标进行评估,确保其达到设计要求。
4. 与工作人员进行沟通,了解是否满足他们的需求和期望。
结论通过执行上述安装和调试方案,可以确保工业生产线(自动控制)在安全、高效和可靠的状态下运行。
这将使企业能够提高生产效率,并提供高质量的产品和服务。
自动化生产线控制系统设计实践报告

自动化生产线控制系统设计实践报告英文回答:Automation plays a crucial role in modern manufacturing processes, as it allows for increased efficiency, accuracy, and productivity. In this report, I will discuss the design and implementation of an automated production line control system.To begin with, the first step in designing an automated production line control system is to clearly define the objectives and requirements of the system. This involves understanding the specific tasks that need to be performed, the desired output, and any constraints or limitations that may exist.Once the objectives and requirements are established, the next step is to select the appropriate hardware and software components for the control system. This may include programmable logic controllers (PLCs), human-machine interfaces (HMIs), sensors, actuators, and communication protocols.The PLCs serve as the brain of the system, controlling and coordinating the various components and processes on the production line. They receive input from sensors, process the data, and send output signals to actuators to perform the necessary actions. For example, if a sensor detects a product on the conveyor belt, the PLC can activate the actuator to move the product to the next station.The HMIs provide a user-friendly interface for operators to monitor and control the production line. They display real-time data, such as production rates, error messages, and machine status, and allow operators to make adjustments or intervene if necessary. For instance, if a machine malfunctions, the operator can use the HMI to stop the production line and troubleshoot the issue.In addition to hardware components, the control system also requires software programming to define the logic andbehavior of the production line. This involves creating a sequence of operations, setting up alarms and errorhandling routines, and implementing safety measures. The programming can be done using ladder logic, structured text, or other programming languages depending on the PLC manufacturer and user preference.Furthermore, communication protocols are essential for the control system to exchange data between different devices and systems. Common protocols include Ethernet/IP, Modbus, and Profibus. These protocols ensure seamless integration and interoperability between the control system and other systems, such as enterprise resource planning (ERP) software or supervisory control and data acquisition (SCADA) systems.Once the hardware and software components are selected and configured, the control system needs to be tested and validated before deployment. This involves running simulations, conducting functional tests, and verifyingthat the system meets the defined objectives and requirements. Any issues or discrepancies discovered duringtesting should be addressed and resolved to ensure the system operates smoothly in a real-world production environment.In conclusion, the design and implementation of an automated production line control system requires careful planning, selection of appropriate hardware and software components, programming, and thorough testing. By leveraging automation technologies, manufacturers can achieve higher efficiency, productivity, and quality in their production processes.中文回答:自动化在现代制造过程中扮演着重要角色,它提高了效率、准确性和生产力。
自动往返控制线路工作原理

自动往返控制线路工作原理宝子,今天咱来唠唠自动往返控制线路的工作原理呀。
你可以想象一下,有这么一个小装置,就像一个超级智能的小机器人在一条轨道上来回跑。
这个自动往返控制线路呢,主要是由一些超级厉害的电气元件组成的。
比如说接触器啦,限位开关之类的。
咱先来说说接触器这个家伙。
接触器就像是一个超级大力士的手,它可以控制电路的通断呢。
当电路需要接通的时候,接触器就啪嗒一下把电路给接上了,电流就像欢快的小水流一样在电路里跑起来了。
当不需要的时候,它又能果断地断开电路,就像关上水龙头一样干脆。
再讲讲限位开关,限位开关可有趣啦。
它就像一个小小的守门员,守在轨道的两端。
当这个跑来跑去的小装置到达轨道的一端的时候,就会碰到这个限位开关。
这个限位开关一旦被碰到啊,就像被唤醒了一样,立马给电路发送一个信号。
这个信号就像一个小暗号,告诉电路说:“到头啦,该往回走啦。
”那这整个过程是怎么实现自动往返的呢?比如说这个小装置从左边开始出发,沿着轨道一直往右走。
当它走到最右边的时候,就碰到了右边的限位开关。
这个时候呢,右边的限位开关就会把信号传给控制电路。
控制电路收到信号后,就会告诉接触器,让接触器改变电路的连接方式。
原来让小装置往右走的电路就断开了,然后接通让小装置往左走的电路。
这样,小装置就开始往回走啦,就像一个听话的小宠物一样。
然后呢,当小装置又回到左边的时候,左边的限位开关又发挥作用啦。
它也会给控制电路发信号,控制电路又让接触器再改变电路连接,小装置就又开始往右走。
就这样,小装置就在这个轨道上自动往返地跑来跑去啦。
这个自动往返控制线路在很多地方都超级有用呢。
比如说在一些生产流水线上,有一些小部件需要在两个加工点之间来回运输。
这个自动往返控制线路就可以让运输的小装置自动地在这两个点之间往返,不需要人工一直去操作,多方便呀。
而且啊,这个原理还让整个过程变得很安全呢。
因为有了限位开关这个小守门员,小装置就不会冲出轨道啦,不会像一个没头没脑的小怪兽到处乱撞。
- 1、下载文档前请自行甄别文档内容的完整性,平台不提供额外的编辑、内容补充、找答案等附加服务。
- 2、"仅部分预览"的文档,不可在线预览部分如存在完整性等问题,可反馈申请退款(可完整预览的文档不适用该条件!)。
- 3、如文档侵犯您的权益,请联系客服反馈,我们会尽快为您处理(人工客服工作时间:9:00-18:30)。
如何确定步进电机驱动器的直流供电 电源
A.电压的确定 混合式步进电机驱动器的供电电源电压一般是 一个较宽的范围(比如IM483的供电电压为12~ 48VDC),电源电压通常根据电机的工作转速和响 应要求来选择。如果电机工作转速较高或响应要求 较快,那么电压取值也高,但注意电源电压的纹波 不能超过驱动器的最大输入电压,否则可能损坏驱 动器。 B.电流的确定 供电电源电流一般根据驱动器的输出相电流I来 确定。如果采用线性电源,电源电流一般可取I的 1.1~1.3倍;如果采用开关电源,电源电流一般可 取I 的1.5~2.0倍。
1.脉冲分配器的作用
控制定子绕组通电的顺序(即控制了步进电机的转动的 方向) 控制脉冲信号的频率(即控制步进电机的转速)
2.脉冲放大器的作用
放大输入到步进电机定子绕组的电流或两端的电压
五 步进电机的工作原理
工作时,脉冲信号按一定顺序轮流加到三相绕组上, 按通电顺序不同,其运行方式有三相三拍、三相双三 拍和三相单、双六拍三种。 “三相单三拍”中的“三相”指定子有三相绕组,“拍”是指 定子绕组改变一次通电方式,“三拍”表示通电三次 完成一个循环。“三相双三拍”中的“双”是指同时有两 相绕组得电。
步进电机的分类
2.
以相数分:单相、两相、三相、四相、 五相、六相和八相等多种。增加相数 能提高性能,但电动机结构和驱动电 源会复杂,成本亦会增加。 目前以反应式步进电机应用最多。
步进电机的优点
1. 电机旋转的角度正比于脉冲数; 2. 电机停转的时候具有最大的转矩(当绕组激磁时); 3. 由于每步的精度在百分之三到百分之五,而且不会 将一步的误差积累到下一步因而有较好的位置精度和运动的 重复性; 4. 优秀的起停和反转响应; 5. 由于没有电刷,可靠性较高,因此电机的寿命仅仅 取决于轴承的寿命; 6. 电机的响应仅由数字输入脉冲确定,因而可以采用 开环控制,这使得电机的结构可以比较简单而且控 制成本 7. 仅仅将负载直接连接到电机的转轴上也可以极低速 的同步旋转。 8. 由于速度正比于脉冲频率,因而有比较宽的转速范 围。
步进电机的分类
2、以工作原理分:反应式、永磁式、永磁感应式
反应式步进电机(VR):反应式步进一般为三相,可实 现大转矩输出,步进角一般为1.5度,但噪声和振动都很 大。反应式步进电机的转子磁路由软磁材料制成,定子上 有多相励磁绕组,利用磁导的变化产生转矩。 反应式步进电动机结构简单,生产成本低,步距角小; 但动态性能差。 永磁式步进电机(PM) ):永磁式步进一般为两相,转 矩和体积较小,步进角一般为7.5度 或15度 。 永磁式步进电动机输出力矩大,动态性能好,但步 距角大。 混合式步进电机(HB):混合了永磁式和反应式的优点。 它又分为两相和五相:两相步进角一般为1.8度而五相步 进角一般为 0.72度 。 它的步距角小,出力大,动态性能好,是目前性能最 高的步进电动机
在加工站中使用的步进电机为42J1834 42J1834及驱 八 在加工站中使用的步进电机为42J1834及驱 动器M415B 动器M415B
M415B驱动器 (1)M415B两相步进电机驱动器的主 要参数: 供电电压:直流12~40V 输出相电流:0.21~1.5A 控制信号输入电流:6~20mA
பைடு நூலகம்
三 步进电机的分类
步进电机 具有结构简单、维护方便、精确度 高、启动灵敏、停车准确等性能,同时控制 输入脉冲的方式和参数,可实现连续调速, 且可获得较宽的高速范围。 1. 以工作方式分:功率式和伺服式 功率式—其输出转矩较大,能带动较大的负 载 伺服式—输出转矩较小,只能带动较小的负 载,对于大的负载需通过液压放大元件来传 动
四 步进电机的结构
以三相反应式步进电机为例来说明步进电 机的工作原理 定子由硅刚片叠压而成,共有六个 磁极,每个极上装有控制绕组,相 对两极 上的绕组串联成一组,形成 三个独立的绕组。 转子上均匀分布着1、2、3、4四个 齿或称四个极,由硅钢片或其他软
步进电机的结构
三相反应式步进电机结构简图
磁材料制成。转子齿 上不带绕组。 步进电机的转动受脉 冲信号控制,每来一 一个脉冲信号,定子 绕组通电的状态就改 变一次,而定子绕组 通电后产生的磁场对 对转子产生作用将使 转子产生一个角位移。
各种运行方式的工作原理
1.
三相单三拍运行方式 通电顺序A—B—C—A(步矩角30度) 每次只有一相绕组通电,在转换过程中,一相绕组 通电,一相绕组得电,容易发生失步,单一绕组通 电吸引转子,稳定性不好,容易在平衡位置附近振 荡,故用的较少。
A相通电
B相通电
C相通电
各种运行方式
三相双三拍运行方式 三相单、双六拍运行 通电顺序是AB-BC方式 CA-AB 通电顺序是A-AB步矩角为30度 B-BC-C-CA-A 每次两相绕组通电, 步矩角是15度 而且在转换过程中 运行中始终有一相 始终有一相绕组保 通电且步矩角较小, 持通电状态,因此 故工作稳定性好, 工作很稳定,且步 矩角与单三拍相同 但电源较复杂,实 际应用较多。
七 步进电机的驱动电路
步进电机需要一个专用电源来驱动,该电源让电机的绕组按照 特定的顺序通电,即受一系列电脉的控制而动作;步进电 机的驱动电源由环形分配器、功率放大器及其它控制电路 组成。
步进电机驱动电源组成框图
环形分配器用来对输入的脉冲进行逻辑变换,产生步进电动机工作 方式的各相脉冲序列信号 功率放大电路对环形分配电路输出信号进行放大,产生电动机所需 要的励磁电流 步进方向信号指定各相绕组导通的顺序,以改变电机的旋转方向
二相步进电机的接线信号描述
二相步进电机的接线图
谢谢大家! 谢谢大家!
步进电机
步进电机的概况
1、步进电机是一种感应电机 。 2、步进电必须由双环形脉冲信号、功率驱动 电路等组成控制系统方可使用,并不能象普 通的直流电机,交流电机在常规下使用 。 3、步进电机的运用涉及到机械、电机、电子 及计算机等许多专业知识。 4、步进电机作为执行元件,是机电一体化的 关键产品之一, 广泛应用在各种自动化控制 系统中。随着微电子和计算机技术的发展, 步进电机的需求量与日俱增,在各个国民经 济领域都有应用。
六 步进电动机的步矩角和转速
每输入一个脉冲信号,步进电机转过的角度称为步矩角, 以θ表示。步矩角不受电压波动和负载变化的影响,也不受 温度、振动等环境因素的干扰 齿距角为 t=360/Z 步距角θ为 θ=t/m=360/mz Z—转子的齿数 M—运行相数 Θ越小,精度越高,增加转子的齿数和增加相数都可减小 步距角 转速 n=60f/mz(r/min) 在一定的频率下,运行的拍数和齿数越多,步距角越小, 则转速越低
(2)参数设定 在驱动器的侧面连接端子中间有六位SW功能设置开关, 用于设定电流和细分。该站X轴、Y轴驱动器电流都设定 为0.84A,细分设定为16
序号 SW1 SW1 1 2 3 4 5 6 7 序号 1 2 3 4 5 6 7 SW1 SW1 ON OFF ON OFF ON OFF ON OFF ON OFF ON OFF ON OFF SW2 SW2 ON ON OFF OFF ON ON OFF SW2 SW2 ON OFF OFF ON ON OFF OFF SW3 SW3 ON ON ON ON OFF OFF OFF SW3 SW3 ON ON ON OFF OFF OFF OFF 细分 1 2 4 8 16 32 64 0.21 0.42 0.63 0.84 1.05 1.26 1.50 电流( ) 电流(A)
一 定义
步进电机 亦称脉冲 电机,是一种利用电 磁铁的作用原理将电 脉冲信号转换为线位 移(或角位移)的执 行元件。即电动机每 输入一个信号,步进 电机便转过一定角度。 电动机转过的总角度 与输入脉冲数成正比, 故转速与脉冲频率成 正比。
二 作用
由于步进电机的精度高、惯性小、 不会因电压波动、负载变化、温度变 化等原因而改变输出量与输入量之间 的固定关系,因此被广泛应用于自动 控制系统中。