焦油加氢技术及行业分析
煤焦油加氢技术研究现状及展望
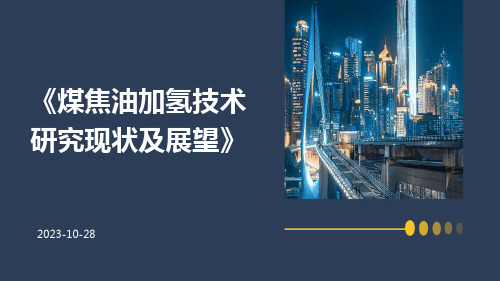
04
煤焦油加氢技术问题与挑战
煤焦油是一种组成复杂的有机混合物,其加氢过程涉及到多种化学反应和物质转化,技术难度较大。
煤焦油加氢过程复杂
技术瓶颈问题
在煤焦油加氢过程中,催化剂的活性和稳定性对反应效果具有决定性影响,但目前所使用的催化剂仍存在活性不足的问题。
催化剂活性不足
为了达到较好的加氢效果,煤焦油加氢过程需要严格的反应条件,如高温、高压、高氢气分压等,这增加了技术的难度和成本。
最后,对产生的副产品进行进一步处理,得到其他有用的化工产品。
然后,将反应后的产物进行分离和精制,得到清洁能源产品。
煤焦油加氢技术流程包括原料准备、加氢反应、产品分离和精制等步骤。
03
煤焦油加氢技术研究现状
起步较晚但发展迅速
01
我国在煤焦油加氢技术方面的研究起步相对较晚,但通过引进吸收、自主研发等途径,目前已取得了一定的成果,并逐渐缩小了与发达国家的差距。
未来研究方向应为开发高效、环保、节能的煤焦油加氢技术,提高产品质量和附加值,降低生产成本和环境污染。
张三. (2018). 煤焦油加氢技术研究进展及展望. 煤炭加工与综合利用, (6), 1-8.
参考文献
王五. (2020). 基于煤焦油的加氢技术及其产品应用研究. 能源与环保, 42(3), 123-128.
环保压力大
未来发展需求
加强基础研究
进一步深入研究煤焦油加氢过程中的化学反应机制和物质转化规律,为技术的改进和优化提供理论支持。
05
煤焦油加氢技术究
过程集成与优化
环保与资源利用
强化科技创新支持
政府应加大对煤焦油加氢技术研发的投入,鼓励企业与高校、科研院所合作,推动技术成果转化。
焦油加氢

煤焦油加氢技术就是采用固定床加氢处理技术将煤焦油所含的S、N等杂原子脱除,并将其中的烯烃和芳烃类化合物进行饱和,来生产质量优良的石脑油馏分和柴油馏分。
一般煤焦油加氢后生产的石脑油S、N含量均低于50ppm,芳潜含量均高于80%;生产的柴油馏分S含量低于50ppm,N含量均低于500ppm,十六烷值均高于35,凝点均低于-35℃~-50℃,是优质的清洁柴油调和组分。
1、煤焦油加氢技术概述1.1煤焦油的主要化学反应煤焦油加氢为多相催化反应,在加氢过程中,发生的主要化学反应有加氢脱硫、加氢脱氮、加氢脱金属、烯烃和芳烃加氢饱和以及加氢裂化等反应:①加氢脱硫反应②加氢脱氮反应③芳烃加氢反应④烯烃加氢反应⑤加氢裂化反应⑥加氢脱金属反应1.2、影响煤焦油加氢装置操作周期、产品质量的因素主要影响煤焦油加氢装置操作周期、产品收率和质量的因素为:反应压力、反应温度、体积空速、氢油体积比和原料油性质等。
1.2.1反应压力提高反应器压力和/或循环氢纯度,也是提高反应氢分压。
提高反应氢分压,不但有利于脱除煤焦油中的S、N等杂原子及芳烃化合物加氢饱和,改善相关产品的质量,而且也可以减缓催化剂的结焦速率,延长催化剂的使用周期,降低催化剂的费用。
不过反应氢分压的提高,也会增加装置建设投资和操作费用。
1.2.2、反应温度提高反应温度,会加快加氢反应速率和加氢裂化率。
过高的反应温度会降低芳烃加氢饱和深度,使稠环化合物缩合生焦,缩短催化剂的使用寿命。
1.2.3、体积空速提高反应体积空速,会使煤焦油加氢装置的处理能力增加。
对于新设计的装置,高体积空速,可降低装置的投资和购买催化剂的费用。
较低的反应体积空速,可在较低的反应温度下得到所期望的产品收率,同时延长催化剂的使用周期,但是过低的体积空速将直接影响装置的经济性。
1.2.4、氢油体积比氢油体积比的大小主要是以加氢进料的化学耗氢量为依据,描述的是加氢进料的需氢量相对大小。
煤焦油加氢比一般的石油类原料,要求有更高的氢油比。
煤焦油加氢
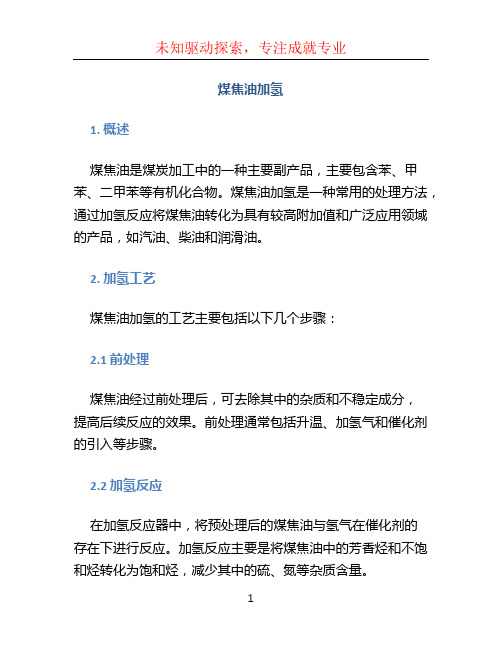
煤焦油加氢1. 概述煤焦油是煤炭加工中的一种主要副产品,主要包含苯、甲苯、二甲苯等有机化合物。
煤焦油加氢是一种常用的处理方法,通过加氢反应将煤焦油转化为具有较高附加值和广泛应用领域的产品,如汽油、柴油和润滑油。
2. 加氢工艺煤焦油加氢的工艺主要包括以下几个步骤:2.1 前处理煤焦油经过前处理后,可去除其中的杂质和不稳定成分,提高后续反应的效果。
前处理通常包括升温、加氢气和催化剂的引入等步骤。
2.2 加氢反应在加氢反应器中,将预处理后的煤焦油与氢气在催化剂的存在下进行反应。
加氢反应主要是将煤焦油中的芳香烃和不饱和烃转化为饱和烃,减少其中的硫、氮等杂质含量。
2.3 分离和后处理经过加氢反应后,产物中会产生水、含硫化合物等副产物,需要进行分离和后处理。
分离可以通过蒸馏等方式进行,将不同沸点的产物分离开,得到目标产品。
后处理主要是对分离得到的产品进行进一步的处理,如除硫、脱色等。
3. 加氢催化剂催化剂在煤焦油加氢中起到重要作用,能够加速反应速率,提高产物质量。
常用的加氢催化剂主要有镍基和钼基催化剂。
3.1 镍基催化剂镍基催化剂具有高活性和良好的选择性,在煤焦油加氢中得到广泛应用。
镍基催化剂能够有效催化芳香烃的饱和反应,提高产物的质量。
同时,镍基催化剂的价格相对较低,成本较为优势。
3.2 钼基催化剂钼基催化剂具有较高的催化活性和较好的硫化物抑制能力,在煤焦油加氢中也得到广泛应用。
钼基催化剂能够有效催化煤焦油中的硫化物,降低产品的硫含量,提高产品质量。
4. 应用领域煤焦油加氢产物主要包括汽油、柴油和润滑油等。
这些产品在交通运输、工业生产和农业领域都有广泛的应用。
4.1 汽油经过煤焦油加氢后产生的汽油具有较高的辛烷值和低的硫含量,适用于汽车燃料。
汽油作为交通运输领域的重要能源,具有巨大的市场需求。
4.2 柴油煤焦油加氢产生的柴油具有高的脱硫能力和较低的含硫量,适用于柴油发动机使用。
柴油作为工业生产和农业机械的重要燃料,也有着广泛的市场。
煤焦油加氢技术简介

19
加氢裂化-加氢处理(FHC-FHT) 反序串联工艺
◇该工艺设置两个串联使用的反应段,R1装填高耐水、 抗结焦和高脱氮活性的加氢精制催化剂,用于新鲜原 料和R2反应产物的深度加氢处理,R2反应段装填根 据特定需要优选的加氢裂化催化剂,用于循环油深度 加氢转化。
氮含量/μg·g-1
<1.0
芳潜(C9),% >160℃柴油馏分
>75 -10#柴油调合组分
密度(20℃)/kg·m-3
850.0~880.0
硫含量 μg·g-1
<10
凝点/℃
≯-10
十六烷值(实测)
≮40
18
加氢裂化-加氢处理(FHC-FHT) 反序串联工艺
◇根据煤焦油(包括蒽油)、页岩油等非常规原 料高含氮、含氧的特征,FRIPP开发了具有 自主知识产权的加氢裂化-加氢处理(FHCFHT)反序串联工艺技术,其原则流程图如 图3所示。
量大,价格相应上涨,因此,从煤焦油中生产轻质燃 料油产品,是综合利用煤炭资源,提高企业经济效益 的有效途径之一。
3
煤焦油加氢工艺
◇采用环境友好的加氢法工艺。利用煤焦油中合适 馏分,生汽油调和组分,已经在工业 装置上成功应用,并进行了长期稳定运转,产品 质量达到设计要求。
13
加氢精制-加氢处理两段法加氢工艺
◇该设置加氢精制和加氢处理两个反应段,加氢 处理催化剂含有分子筛组分,低温煤焦油馏分 经过加氢精制过程后,生成油中的水、有机氮 对可使加氢裂化催化剂中毒,很难实现长周期 运转。所以加氢精制生成油需要换热冷却后, 进入高压和低压分离器,分离出的液体物流通 过气提塔分离出生成水,再进入加氢处理反应 段,进一步改质来改善产品质量。原则流程图 见图2。
我国煤焦油加氢产业发展现状与展望
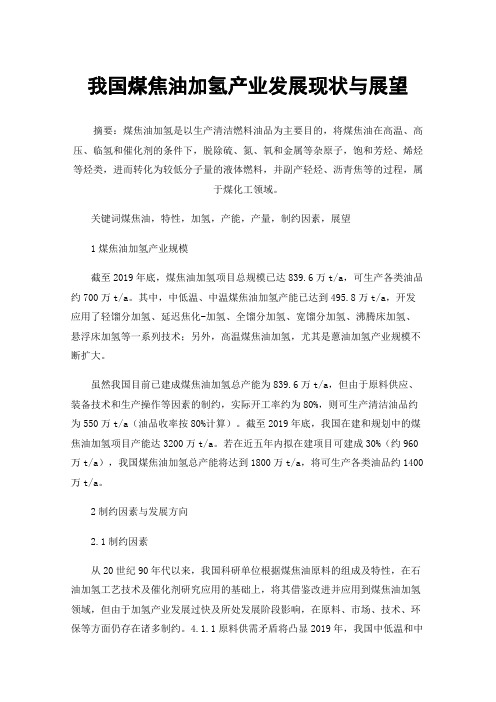
我国煤焦油加氢产业发展现状与展望摘要:煤焦油加氢是以生产清洁燃料油品为主要目的,将煤焦油在高温、高压、临氢和催化剂的条件下,脱除硫、氮、氧和金属等杂原子,饱和芳烃、烯烃等烃类,进而转化为较低分子量的液体燃料,并副产轻烃、沥青焦等的过程,属于煤化工领域。
关键词煤焦油,特性,加氢,产能,产量,制约因素,展望1煤焦油加氢产业规模截至2019年底,煤焦油加氢项目总规模已达839.6万t/a,可生产各类油品约700万t/a。
其中,中低温、中温煤焦油加氢产能已达到495.8万t/a,开发应用了轻馏分加氢、延迟焦化-加氢、全馏分加氢、宽馏分加氢、沸腾床加氢、悬浮床加氢等一系列技术;另外,高温煤焦油加氢,尤其是蒽油加氢产业规模不断扩大。
虽然我国目前已建成煤焦油加氢总产能为839.6万t/a,但由于原料供应、装备技术和生产操作等因素的制约,实际开工率约为80%,则可生产清洁油品约为550万t/a(油品收率按80%计算)。
截至2019年底,我国在建和规划中的煤焦油加氢项目产能达3200万t/a。
若在近五年内拟在建项目可建成30%(约960万t/a),我国煤焦油加氢总产能将达到1800万t/a,将可生产各类油品约1400万t/a。
2制约因素与发展方向2.1制约因素从20世纪90年代以来,我国科研单位根据煤焦油原料的组成及特性,在石油加氢工艺技术及催化剂研究应用的基础上,将其借鉴改进并应用到煤焦油加氢领域,但由于加氢产业发展过快及所处发展阶段影响,在原料、市场、技术、环保等方面仍存在诸多制约。
4.1.1原料供需矛盾将凸显2019年,我国中低温和中温煤焦油产量共有约660万t,相应已投产的加氢项目规模为495.8万t;高温煤焦油产量约为1850万t,其中蒽油馏分产量约为410万t,相应已投产的加氢规模为343.8万t。
若考虑煤焦油在其他深加工应用领域的拓展,加氢产业原料供需基本平衡。
2.1.2产品市场变数较多按照国家汽油、柴油质量指标要求,煤焦油加氢项目所生产的汽油辛烷值和柴油十六烷值均不达标且较低,出厂售价亦低于石油炼制产品。
焦油加氢相关技术

焦油加氢相关技术煤焦化煤焦化又称煤炭高温干馏。
以煤为原料,在隔绝空气条件下,加热到950℃左右,经高温干馏生产焦炭,同时获得煤气、煤焦油并回收其它化工产品的一种煤转化工艺。
煤气化煤气化是一个热化学过程。
以煤或煤焦为原料,以氧气(空气、富氧或纯氧)、水蒸气或氢气等作气化剂,在高温条件下通过化学反应将煤或煤焦中的可燃部分转化为气体燃料的过程。
煤的气化类型可归纳为五种基本类型:自热式的水蒸气气化、外热式水蒸气气化、煤的加氢气化、煤的水蒸气气化和加氢气化结合制造代用天然气、煤的水蒸气气化和甲烷化相结合制造代用天然气。
煤液化是把固体煤炭通过化学加工过程,使其转化成为液体燃料、化工原料和产品的先进洁净煤技术。
根据不同的加工路线,煤炭液化可分为直接液化和间接液化两大类。
煤的液化方法主要分为煤的直接液化和煤的间接液化两大类。
(1)煤直接液化煤在氢气和催化剂作用下,通过加氢裂化转变为液体燃料的过程称为直接液化。
裂化是一种使烃类分子分裂为几个较小分子的反应过程。
因煤直接液化过程主要采用加氢手段,故又称煤的加氢液化法。
(2)煤间接液化间接液化是以煤为原料,先气化制成合成气,然后,通过催化剂作用将合成气转化成烃类燃料、醇类燃料和化学品的过程。
煤炭直接液化是把煤直接转化成液体燃料,煤直接液化的操作条件苛刻,对煤种的依赖性强。
典型的煤直接液化技术是在400摄氏度、150个大气压左右将合适的煤催化加氢液化,产出的油品芳烃含量高,硫氮等杂质需要经过后续深度加氢精制才能达到目前石油产品的等级。
一般情况下,一吨无水无灰煤能转化成半吨以上的液化油。
煤直接液化油可生产洁净优质汽油、柴油和航空燃料。
但是适合于大吨位生产的直接液化工艺目前尚没有商业化,主要的原因是由于煤种要求特殊,反应条件较苛刻,大型化设备生产难度较大,使产品成本偏高。
直接煤直接液化示意图液化[1]是在高温(400℃以上)、高压(10MPa以上),在催化剂和溶剂作用下使煤的分子进行裂解加氢,直接转化成液体燃料,再进一步加工精制成汽油、柴油等燃料油,又称加氢液化。
煤焦油加氢技术简介

煤焦油加氢技术简介煤焦油是从炼焦煤中分离出来的一种黑色粘稠液体,它是重要的化石能源原材料。
一方面,煤焦油可以用于生产苯、酚、己二酸等重要基础化工产品,另一方面,煤焦油中的许多成分也是有价值的燃料。
因此,如何更高效的利用煤焦油成为煤化工产业的关键之一。
煤焦油加氢技术正是一个可行的路径之一。
煤焦油加氢技术是指利用加氢反应将煤焦油中的多环芳烃、杂原子、硫和氮等杂质去除,同时将其转化成高附加值燃料或化学品的技术。
通过加氢技术,可以将煤焦油中的大分子碳氢化合物裂解成小分子烃类,并减少含硫、含氮等杂质,从而提高燃料质量。
煤焦油加氢技术的实施需要一定的条件。
首先,需要有高品质的煤焦油作为原料。
其次,加氢反应需要高温高压下进行。
一般情况下,反应温度在400℃~450℃,压力在30MPa~50MPa之间。
第三,加氢反应需要使用催化剂。
目前,常用的催化剂有氧化铝、氧化硅、氧化硫、氧化钡、硫化镍、氧化钠、氧化铜等。
煤焦油加氢技术可以制备多种燃料或化学品。
一种主要的产品是煤焦油加氢燃料油。
煤焦油加氢燃料油在克服了煤焦油成分复杂、热值低、不稳定等弊端后,其性能已经接近天然气和石油产品。
同时,煤焦油加氢燃料油也具有很高的燃烧效率和低排放。
除了煤焦油加氢燃料油,煤焦油加氢技术还可以用于制备沥青增稠剂、合成沥青、合成轻质基础油、煤焦油蜡等多种化学品。
煤焦油加氢技术的优势在于其可以充分利用煤资源,减少对非再生能源的依赖,同时也可以减少工业排放,达到减排的效果。
总之,煤焦油加氢技术是一种可行的利用煤焦油资源的方式。
通过加氢反应,可以将煤焦油中的杂质剔除,制备多种高附加值燃料或化学品,从而达到节能减排的效果。
随着技术的不断进步,相信煤焦油加氢技术将会在未来的煤化工产业中扮演越来越重要的角色。
高温煤焦油加氢技术和国内生产状况
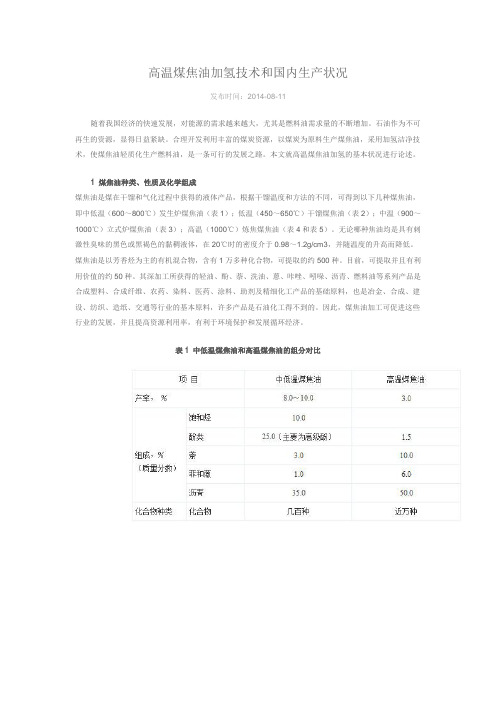
高温煤焦油加氢技术和国内生产状况发布时间:2014-08-11随着我国经济的快速发展,对能源的需求越来越大,尤其是燃料油需求量的不断增加。
石油作为不可再生的资源,显得日益紧缺。
合理开发利用丰富的煤炭资源,以煤炭为原料生产煤焦油,采用加氢洁净技术,使煤焦油轻质化生产燃料油,是一条可行的发展之路。
本文就高温煤焦油加氢的基本状况进行论述。
1 煤焦油种类、性质及化学组成煤焦油是煤在干馏和气化过程中获得的液体产品,根据干馏温度和方法的不同,可得到以下几种煤焦油,即中低温(600~800℃)发生炉煤焦油(表1);低温(450~650℃)干馏煤焦油(表2);中温(900~1000℃)立式炉煤焦油(表3);高温(1000℃)炼焦煤焦油(表4和表5)。
无论哪种焦油均是具有刺激性臭味的黑色或黑褐色的黏稠液体,在20℃时的密度介于0.98~1.2g/cm3,并随温度的升高而降低。
煤焦油是以芳香烃为主的有机混合物,含有1万多种化合物,可提取的约500种。
目前,可提取并且有利用价值的约50种。
其深加工所获得的轻油、酚、萘、洗油、蒽、咔唑、吲哚、沥青、燃料油等系列产品是合成塑料、合成纤维、农药、染料、医药、涂料、助剂及精细化工产品的基础原料,也是冶金、合成、建设、纺织、造纸、交通等行业的基本原料,许多产品是石油化工得不到的。
因此,煤焦油加工可促进这些行业的发展,并且提高资源利用率,有利于环境保护和发展循环经济。
表1 中低温煤焦油和高温煤焦油的组分对比表2 低温煤焦油化学分析和金属元素分析表3 中温煤焦油化学分析和金属元素分析表4 高温煤焦油化学分析和金属元素分析表5 高温煤焦油金属含量分析(μg/g)2 煤焦油加氢原理、分类及特点2.1 加氢原理煤焦油中含有大量的芳烃、胶质、沥青质,在高温、高压和催化剂的作用下,经过加氢精制和加氢裂化并裂解开环,可使煤焦油中大量的不饱和烃、芳烃、胶质、沥青质饱和,获得低分子量的饱和烃,加氢脱出S、N、O和金属杂原子,降低了硫和芳烃的含量,改善其安定性,可获得石脑油和优质燃料油添加剂。
煤焦油加氢技术
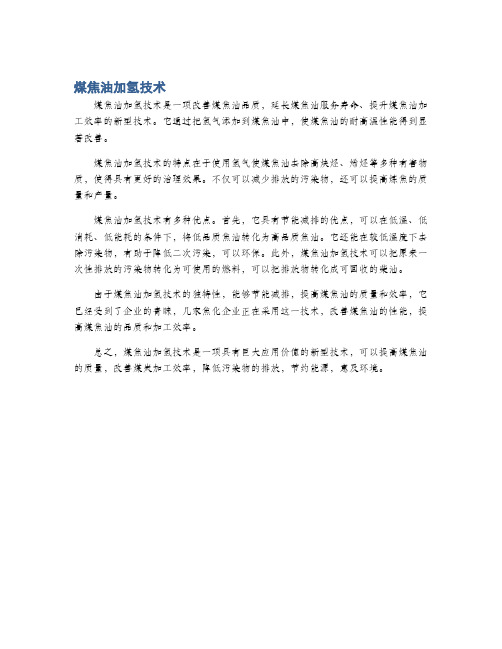
煤焦油加氢技术
煤焦油加氢技术是一项改善煤焦油品质,延长煤焦油服务寿命、提升煤焦油加工效率的新型技术。
它通过把氢气添加到煤焦油中,使煤焦油的耐高温性能得到显著改善。
煤焦油加氢技术的特点在于使用氢气使煤焦油去除高炔烃、烯烃等多种有害物质,使得具有更好的治理效果。
不仅可以减少排放的污染物,还可以提高炼焦的质量和产量。
煤焦油加氢技术有多种优点。
首先,它具有节能减排的优点,可以在低温、低消耗、低能耗的条件下,将低品质焦油转化为高品质焦油。
它还能在较低温度下去除污染物,有助于降低二次污染,可以环保。
此外,煤焦油加氢技术可以把原来一次性排放的污染物转化为可使用的燃料,可以把排放物转化成可回收的柴油。
由于煤焦油加氢技术的独特性,能够节能减排,提高煤焦油的质量和效率,它已经受到了企业的青睐,几家焦化企业正在采用这一技术,改善煤焦油的性能,提高煤焦油的品质和加工效率。
总之,煤焦油加氢技术是一项具有巨大应用价值的新型技术,可以提高煤焦油的质量,改善煤炭加工效率,降低污染物的排放,节约能源,惠及环境。
中低温煤焦油加氢技术介绍
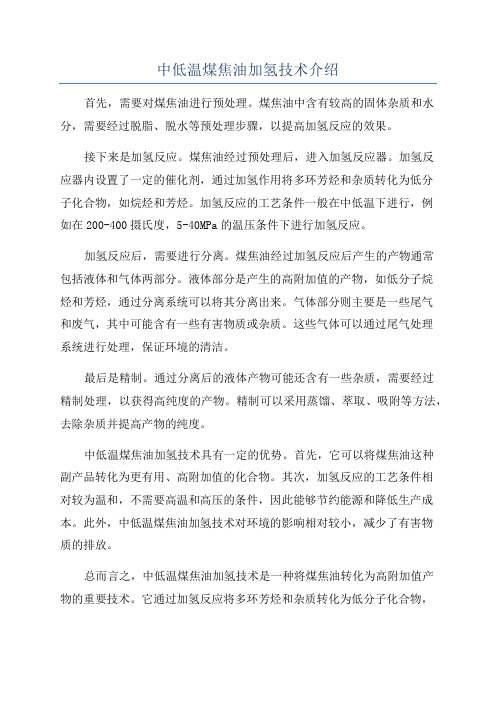
中低温煤焦油加氢技术介绍首先,需要对煤焦油进行预处理。
煤焦油中含有较高的固体杂质和水分,需要经过脱脂、脱水等预处理步骤,以提高加氢反应的效果。
接下来是加氢反应。
煤焦油经过预处理后,进入加氢反应器。
加氢反应器内设置了一定的催化剂,通过加氢作用将多环芳烃和杂质转化为低分子化合物,如烷烃和芳烃。
加氢反应的工艺条件一般在中低温下进行,例如在200-400摄氏度,5-40MPa的温压条件下进行加氢反应。
加氢反应后,需要进行分离。
煤焦油经过加氢反应后产生的产物通常包括液体和气体两部分。
液体部分是产生的高附加值的产物,如低分子烷烃和芳烃,通过分离系统可以将其分离出来。
气体部分则主要是一些尾气和废气,其中可能含有一些有害物质或杂质。
这些气体可以通过尾气处理系统进行处理,保证环境的清洁。
最后是精制。
通过分离后的液体产物可能还含有一些杂质,需要经过精制处理,以获得高纯度的产物。
精制可以采用蒸馏、萃取、吸附等方法,去除杂质并提高产物的纯度。
中低温煤焦油加氢技术具有一定的优势。
首先,它可以将煤焦油这种副产品转化为更有用、高附加值的化合物。
其次,加氢反应的工艺条件相对较为温和,不需要高温和高压的条件,因此能够节约能源和降低生产成本。
此外,中低温煤焦油加氢技术对环境的影响相对较小,减少了有害物质的排放。
总而言之,中低温煤焦油加氢技术是一种将煤焦油转化为高附加值产物的重要技术。
它通过加氢反应将多环芳烃和杂质转化为低分子化合物,提高了煤焦油的附加值。
该技术具有温和的工艺条件和环境友好的特点,有望在煤炭加工和利用过程中发挥重要作用。
中低温煤焦油加氢技术汇总
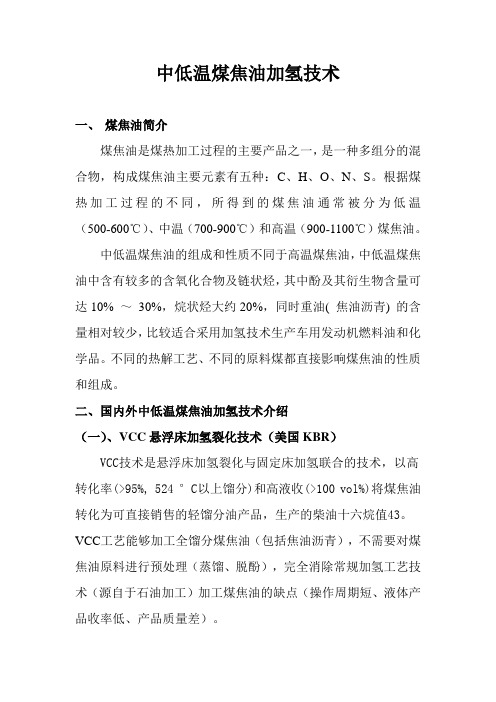
中低温煤焦油加氢技术一、煤焦油简介煤焦油是煤热加工过程的主要产品之一,是一种多组分的混合物,构成煤焦油主要元素有五种:C、H、O、N、S。
根据煤热加工过程的不同,所得到的煤焦油通常被分为低温(500-600℃)、中温(700-900℃)和高温(900-1100℃)煤焦油。
中低温煤焦油的组成和性质不同于高温煤焦油,中低温煤焦油中含有较多的含氧化合物及链状烃,其中酚及其衍生物含量可达10% ~30%,烷状烃大约20%,同时重油( 焦油沥青) 的含量相对较少,比较适合采用加氢技术生产车用发动机燃料油和化学品。
不同的热解工艺、不同的原料煤都直接影响煤焦油的性质和组成。
二、国内外中低温煤焦油加氢技术介绍(一)、VCC悬浮床加氢裂化技术(美国KBR)VCC技术是悬浮床加氢裂化与固定床加氢联合的技术,以高转化率(>95%, 524 °C以上馏分)和高液收(>100 vol%)将煤焦油转化为可直接销售的轻馏分油产品,生产的柴油十六烷值43。
VCC工艺能够加工全馏分煤焦油(包括焦油沥青),不需要对煤焦油原料进行预处理(蒸馏、脱酚),完全消除常规加氢工艺技术(源自于石油加工)加工煤焦油的缺点(操作周期短、液体产品收率低、产品质量差)。
1、建设及投资估算(按50万吨/年处理量):工艺设计:基础设计需3个月,工艺包设计需6个月。
建设周期:关键设备制造需13个月,设备安装需3个月。
建设投资:设备投资额约8亿元,技术转让及工艺包投资额约1000万美元,折合人民币6070万元,合计8.607亿元。
添加助剂:添加剂的使用量7㎏/吨原料,50万吨/年处理量使用添加剂3500吨,添加剂4000元/吨,合计添加剂费用0.14亿元。
装置能耗:装置能耗为1939.27MJ/t。
2、工艺特点VCC 技术能够处理多种原料,单套最大处理能力可达270万吨/年,包括从炼厂渣油一直到煤,以及煤油混合物,脱油沥青,加拿大油砂沥青减压渣油,减粘减压渣油,催化裂化油浆,乙烯裂解焦油,煤焦油,煤沥青,用过的润滑油,切削油,脱脂剂残余液,用过的氯代溶剂,油漆残渣,变压器油,废加氢精制催化剂,失活的活性炭和回收的塑料等。
煤焦油加氢产业发展趋势

煤焦油加氢产业发展趋势煤焦油加氢技术是一项重要的工业反应技术,能够减少煤炭等化石燃料的二氧化碳排放,并提供清洁的能源和原料。
煤焦油加氢不仅可以解决能源和环境问题,还可以推动煤炭产业的高质量发展。
本文将从加氢技术的发展背景、煤焦油加氢的意义、技术路线和趋势等方面对煤焦油加氢产业发展进行分析。
一、煤焦油加氢技术的发展背景煤炭是我国的主要能源之一,但也是主要的温室气体排放源之一。
煤焦油是煤炭的副产物,含有大量的杂质和有害物质,对环境造成污染。
因此,发展煤焦油加氢技术具有重要的意义。
煤焦油加氢技术是一种将煤焦油转化为清洁能源和原料的技术。
通过加氢反应,可以将煤焦油中的杂质去除,得到高品质的燃料和化工原料。
该技术不仅可以解决煤焦油的利用问题,还能减少煤炭燃烧产生的污染物的排放。
煤焦油加氢技术最早出现在20世纪60年代,当时主要用于石油加工和化工行业。
随着环境保护和能源消耗问题的日益突出,煤焦油加氢技术逐渐引起了人们的关注。
特别是近年来,我国能源供需关系紧张,环境污染严重,煤焦油加氢技术逐渐成为解决这些问题的关键技术之一。
二、煤焦油加氢的意义煤焦油加氢技术具有广泛的应用前景和重要的战略意义。
1. 解决能源问题煤炭是我国主要的能源之一,但煤炭燃烧会产生大量的二氧化碳和其他污染物。
煤焦油加氢技术可以将煤焦油转化为清洁燃料,减少对煤炭的需求,降低二氧化碳排放。
2. 优化煤炭结构煤炭的质量和结构对其利用效果有重要影响。
通过煤焦油加氢技术,可以将煤焦油中的有害物质去除,得到高品质的燃料和化工原料,提高煤炭的综合利用效果。
3. 促进经济发展煤焦油加氢技术的应用可以促进较大规模的加氢项目建设,推动煤炭产业的升级和转型。
同时,该技术还可以提供清洁能源和原料,为其他行业提供支撑。
4. 减少环境污染煤焦油中含有大量的杂质和有害物质,会对环境造成严重的污染。
通过加氢处理,可以去除煤焦油中的污染物,减少对环境的影响。
三、煤焦油加氢技术的发展趋势煤焦油加氢技术在我国的发展已经取得了一定的成果,但与国际先进水平相比,还存在一定的差距。
煤焦油加氢技术概述

煤焦油加氢生产技术概述煤焦油的组成特点是硫、氮、氧含量高,多环芳烃含量较高,碳氢比大,粘度和密度大,机械杂质含量高,易缩合生焦,较难进行加工。
煤焦油加氢生产技术首先将煤焦油全馏分原料采用电脱盐、脱水技术将煤焦油原料脱水至含水量小于0.05%,然后再经过减压蒸馏切割掉含机械杂质的重尾馏分,以除去机械杂质(与油相不同的相,表现为固相的物质),使机械杂质含量小于0.03%,得到净化的煤焦油原料。
净化后的煤焦油原料经换热或加热炉加热到所需的反应温度后进入加氢精制(缓和裂化段)进行脱硫、脱氮、脱氧、烯烃和芳烃饱和、脱胶质和大分子裂化反应等,之后经过进入产品分馏塔,切割分馏出汽油馏分、柴油馏分和未转化油馏分;未转化油馏分经过换热或加热炉加热到反应所需的温度后进入加氢裂化段,进行深度脱硫、脱氮、芳烃饱和大分子加氢裂化反应等,同样进入产品分馏塔,切割分馏出反应产生的汽油馏分、柴油馏分和未转化油馏分。
氢气自制氢装置来,经压缩机压缩后分两路,一路进入加氢精制(缓和裂化)段,一路进入加氢裂化段。
经过反应的过剩氢气通过冷高分回收后进入氢气压缩机升压后返回加氢精制(缓和裂化)段和加氢裂化段。
— 1工艺原理及特点1.1原料过滤根据煤焦油含有大量粉粒杂质的特点,设置超级离心机和自动反冲洗过滤器,以避免系统堵塞,尤其是反应器压降的过早提高。
1.2电脱盐由于原料来源不同,常规的炼厂油品加氢装置不需设置电脱盐系统。
鉴于煤焦油中含有较多的水份和盐类,本装置在原料过滤系统之后设置了电脱盐系统,以达到脱水、脱盐的目的。
1.3减压脱沥青原料中含有较多的也能影响反应器运行周期的胶质成分,不能通过过滤手段除去。
通过蒸馏方式,可以脱除这部分胶质物,并进一步洗涤除去粉粒杂质。
为避免结焦,蒸馏在负压下进行。
1.4加氢精制加氢精制反应主要目的是:1、烯烃饱和——将不饱和的烯烃加氢,变成饱和的烷烃;2、脱硫——将原料中的硫化物氢解,转化成烃和硫化氢;3、脱氮——将原料中的氮化合物氢解,转化成烃和氨;4、脱氧——将原料中的氧化合物氢解,转化成烃和水。
神木天元化工公司煤焦油加氢技术经济效益分析
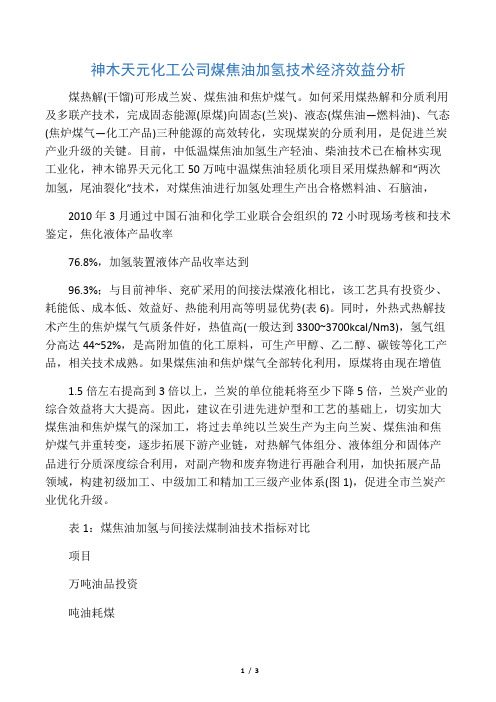
神木天元化工公司煤焦油加氢技术经济效益分析煤热解(干馏)可形成兰炭、煤焦油和焦炉煤气。
如何采用煤热解和分质利用及多联产技术,完成固态能源(原煤)向固态(兰炭)、液态(煤焦油—燃料油)、气态(焦炉煤气—化工产品)三种能源的高效转化,实现煤炭的分质利用,是促进兰炭产业升级的关键。
目前,中低温煤焦油加氢生产轻油、柴油技术已在榆林实现工业化,神木锦界天元化工50万吨中温煤焦油轻质化项目采用煤热解和“两次加氢,尾油裂化”技术,对煤焦油进行加氢处理生产出合格燃料油、石脑油,2010年3月通过中国石油和化学工业联合会组织的72小时现场考核和技术鉴定,焦化液体产品收率76.8%,加氢装置液体产品收率达到96.3%;与目前神华、兖矿采用的间接法煤液化相比,该工艺具有投资少、耗能低、成本低、效益好、热能利用高等明显优势(表6)。
同时,外热式热解技术产生的焦炉煤气气质条件好,热值高(一般达到3300~3700kcal/Nm3),氢气组分高达44~52%,是高附加值的化工原料,可生产甲醇、乙二醇、碳铵等化工产品,相关技术成熟。
如果煤焦油和焦炉煤气全部转化利用,原煤将由现在增值1.5倍左右提高到3倍以上,兰炭的单位能耗将至少下降5倍,兰炭产业的综合效益将大大提高。
因此,建议在引进先进炉型和工艺的基础上,切实加大煤焦油和焦炉煤气的深加工,将过去单纯以兰炭生产为主向兰炭、煤焦油和焦炉煤气并重转变,逐步拓展下游产业链,对热解气体组分、液体组分和固体产品进行分质深度综合利用,对副产物和废弃物进行再融合利用,加快拓展产品领域,构建初级加工、中级加工和精加工三级产业体系(图1),促进全市兰炭产业优化升级。
表1:煤焦油加氢与间接法煤制油技术指标对比项目万吨油品投资吨油耗煤吨油耗水吨油耗电吨油成本(含税)煤焦油加氢4060万元1.35吨3.42吨188kWh2348元间接法制油9750万元4.48吨(xx4.8吨)11.45吨(xx11.48吨)745kWh(xx698 kWh)3565元煤焦油加氢/间接法0.4160.3010.2990.250.659注:煤焦油加氢以40万吨装置测算;原煤按250元/吨计。
煤焦油加氢项目的前景分析

绪论世界能源消费结构:石油30%^ 32%天然气17%^ 19%煤炭27%^ 28%其余:原子能、水能、太阳能、风能等。
我国能源消费结构中:煤炭占较大,约70%左右,近年来,我国煤制油等能源化工项目建设和投产,有力的推动了我国石油替代能源战略实施,可邮箱的提升煤炭资源的价值。
因此,煤化工的多联产技术是一项符合我国国情的煤炭综合利用技术,对我国经济的可持续发展有着特殊的重要意义。
煤多联产生产过程中产生的副产物煤焦油用于生产汽油、柴油和燃料油,对替代我国部分石油资源具有重要意义。
[多联产方案主要有:煤一电一气工艺、煤一气一化工产品、煤一焦一油工艺、煤一焦一化工产品]一、煤及煤焦油资源1、煤和煤焦油发展现状①我国属于:石油资源短缺,天然气资源不足,煤炭资源相对丰富的国家。
中国煤炭资源可开采储量为2040 X 108t (其中:烟煤75%无烟煤12%褐煤13沟位居世界第二位。
2009年我国煤炭开采量29.6 X 108t ,占世界第一位。
按其储采比计可采80年左右,但人均占有量只有世界人均占有量的60%左右,煤炭的消费只占一次能源消费的70%未来50年内,能源的70%消费还依靠煤炭。
②煤焦油是煤炼焦和煤气化生产过程中的主要产物。
a:产量2004〜2008年中国煤焦油产量530X 104t /, 820X 104 t。
递增13.6%, 2009 年1100X 104t (焦炭产量35 3 00 X 104t )。
b:回收率:2008年71.3%,有330X 104t未被回收。
c:加工量:仅占回收煤焦油的62% 297X 104t被烧掉。
2、煤焦油制燃料油资源②烟煤和褐煤资源低变质烟煤,经全国第三次煤炭资源预测结果,垂深2000米的浅的低变质烟煤量为242 1 5.10 X 108t,占全国煤炭资源量的53.2%。
预测低变烟煤分布:主要在西北地区:54.2%华北地区:43.0%东北地区:2.69%各省分布:陕西:34.9%内蒙:27.9%新疆:20.3%褐煤资源:贮量(已查明为1334.69 X 108t )占全国煤炭资源总量的13.07%,占非炼焦煤的18.05%。
中低温煤焦油加氢技术浅析
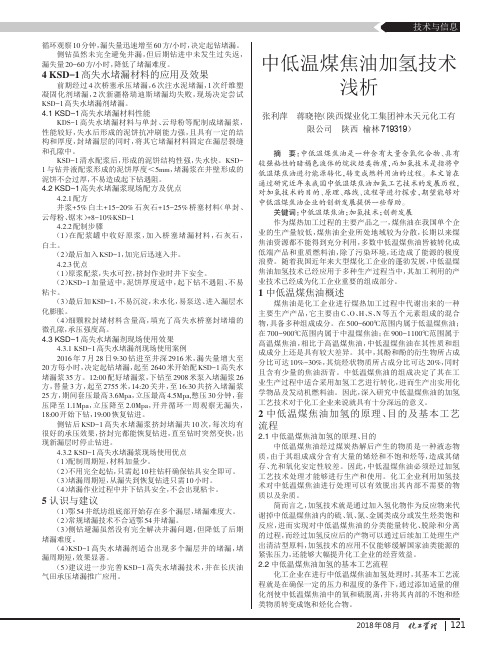
2018年08月循环观察10分钟,漏失量迅速增至60方/小时,决定起钻堵漏。
侧钻虽然未完全避免井漏,但后期钻进中未发生过失返,漏失量20-60方/小时,降低了堵漏难度。
4KSD-1高失水堵漏材料的应用及效果前期经过4次桥塞承压堵漏,6次注水泥堵漏,1次纤维塑凝固化剂堵漏,2次新疆格瑞迪斯堵漏均失败,现场决定尝试KSD-1高失水堵漏剂堵漏。
4.1KSD-1高失水堵漏材料性能KDS-1高失水堵漏材料与单封、云母粉等配制成堵漏浆,性能较好,失水后形成的泥饼抗冲刷能力强,且具有一定的结构和厚度,封堵漏层的同时,将其它堵漏材料固定在漏层裂缝和孔隙中。
KSD-1清水配浆后,形成的泥饼结构性强,失水快。
KSD-1与钻井液配浆形成的泥饼厚度<5mm ,堵漏浆在井壁形成的泥饼不会过厚,不易造成起下钻遇阻。
4.2KSD-1高失水堵漏浆现场配方及优点4.2.1配方井浆+5%白土+15-20%石灰石+15-25%桥塞材料(单封、云母粉、锯末)+8-10%KSD-14.2.2配制步骤(1)在配浆罐中收好原浆,加入桥塞堵漏材料,石灰石,白土。
(2)最后加入KSD-1,加完后迅速入井。
4.2.3优点(1)原浆配浆,失水可控,挤封作业时井下安全。
(2)KSD-1加量适中,泥饼厚度适中,起下钻不遇阻、不易粘卡。
(3)最后加KSD-1,不易沉淀,未水化,易泵送、进入漏层水化膨胀。
(4)细颗粒封堵材料含量高,填充了高失水桥塞封堵墙的微孔隙,承压强度高。
4.3KSD-1高失水堵漏剂现场使用效果4.3.1KSD-1高失水堵漏剂现场使用案例2016年7月28日9:30钻进至井深2916米,漏失量增大至20方每小时,决定起钻堵漏,起至2640米开始配KSD-1高失水堵漏浆35方。
12:00配好堵漏浆,下钻至2908米泵入堵漏浆26方,替量3方,起至2755米,14:20关井,至16:30共挤入堵漏浆25方,期间套压最高3.6Mpa ,立压最高4.5Mpa,憋压30分钟,套压降至1.1Mpa ,立压降至2.0Mpa ,开井循环一周观察无漏失,18:00开始下钻,19:00恢复钻进。
煤焦油加氢技术在生产实践中的应用

煤焦油加氢技术在生产实践中的应用煤焦油加氢工艺技术属于煤化工领域,涉及一种新型煤焦油加氢工艺和催化剂。
此项目对煤焦油的合理利用尤其对环境保护具有重要意义。
对高温煤焦油进行加氢处理,选择合适的加氢条件,生产汽、柴油调和组分,以提升焦化副产品煤焦油的产品附加值。
我国是世界焦炭生产大国,焦炭年产量约占世界焦炭总产量的近50%左右,在生产焦炭的同时还副产较多的低经济价值的煤焦油和焦炉煤气。
煤焦油作为重要的炼焦副产品,产量约占炼焦煤的4%左右,煤焦油气味较大,燃烧烟气中含有大量的SOx和NOx,对环境造成了严重污染,因此,采用加氢技术,可以大大降低对环境的危害。
煤焦油加氢成套技术将可以满足煤炭行业由煤焦油生产优质汽油、柴油调和馏分油的市场需求。
随着世界经济,特别是发展中国家经济的不断发展,对液体发动机燃料的需求量越来越大。
由于诸多因素的影响和制约,石油资源日趋紧张,这样给以煤为原料制取液体发动机燃料提供了很好的机会和广阔的空间,因此对煤焦油加氢技术的研究日益重要。
煤焦油是煤在干馏和气化过程中获得的液体产品。
按干馏温度和加工方法的不同可以分为高温煤焦油、中温煤焦油和低温煤焦油,它们的组成和性质有很大的不同。
高温煤焦油的组成特点是硫、氮、氧含量高,多环芳烃含量高,碳氢比大、粘度和密度大,机械杂质含量高,易缩成生焦,较难进行加工。
高温煤焦油加氢技术首先是将煤焦油全馏分原料采用电脱盐、脱水技术将煤焦油原料脱水至含水量小于百分之0.05,然后再经过减压蒸馏切割掉含机械杂质的重尾馏分,以除去机械杂质,得到净化的煤焦油原料。
净化后的煤焦油原料经换热或者加热炉加热到所需的反应温度后进入加氢精制进行脱硫、脱氮、脱氧、烯烃和芳烃饱和、脱胶质和大分子裂化反应等,之后经过进入产品分馏塔,切割分馏出汽油馏分、柴油馏分和未转化油馏分;未转化油馏分经过换热或加热炉加热到反应所需的温度后进入加氢裂化段,进行深度脱硫、脱氮、芳烃饱和和大分子加氢裂化反应等,同样进入产品分馏塔,切割分馏出反应产生的汽油馏分、柴油馏分和未转化油馏分。
- 1、下载文档前请自行甄别文档内容的完整性,平台不提供额外的编辑、内容补充、找答案等附加服务。
- 2、"仅部分预览"的文档,不可在线预览部分如存在完整性等问题,可反馈申请退款(可完整预览的文档不适用该条件!)。
- 3、如文档侵犯您的权益,请联系客服反馈,我们会尽快为您处理(人工客服工作时间:9:00-18:30)。
焦油加氢技术及行业分析1.1 国内外煤焦油加氢工艺技术概况(1)国外工艺技术概况二十世纪二次世界大战前,德国首次完成“煤和煤焦油的高压加氢技术”,这是现代“加氢裂化”技术的起源,它以煤为原料的高压加氢,其工艺流程由三段组成:第一段是煤糊的悬浮床液相加氢,以铁-半焦为催化剂(代号为10927),在压力70MPa、温度470~475℃、空速0.70h-1的条件下(或在压力20~22MPa、温度<430℃、空速0. 31 h-1的条件下)进行加氢反应,把煤糊转化为汽油、中油和重油,1926年首次工业应用;第二段是气相加氢,以纯硫化钨为催化剂(代号为5058),脱除中油中的硫、氮化合物,1931年首次工业应用;第三段是加氢裂化,以硫化钨-HF活化的白土为催化剂(代号为6434),在压力22MPa、温度400~420℃、空速0.64 h-1的条件下,把精制后的中油转化为汽油和柴油,1937年首次工业应用;后来又研究开发了硫化钨-硫化镍-氧化铝催化剂(代号为8376),在压力30MPa、温度360~440℃、空速0.42 h-1的条件下,把精制后的中油转化为汽油和柴油,1942年首次工业应用。
虽然在第二次世界大战结束以前,这项技术在工业上得到了比较多的应用,但由于反应压力高、空速低、消耗氢气多,在第二次世界大战以后并没有继续应用,特别是石油的大量发现和开采,石油炼制技术的迅速发展,也限制了这项技术的应用。
尽管如此,其工艺、催化剂和高压设备制造技术都为现代加氢技术特别是加氢裂化技术的发明和应用奠定了基础。
,二十世纪六十年代,美国、前苏联完成了大量的煤焦油加氢、煤加氢法制合成油的研究工作,因原油价格低廉,煤焦油加氢生产油品无经济性,故相关技术的工业化未进行。
二十一世纪后,国际原油价格一路飞升,直接刺激石油替代能源产业兴起,但由于西方各国环保法规的限制,西方各国很少生产焦碳、焦油,故焦油加氢的工业化未进行。
根据煤焦油的理化性质特点,业内认为能够实现含沥青质原料油加氢提质的方法有两种:沸腾床加氢和鼓泡床加氢。
两种技术的共同点在于对反应器、泵、阀核心设备和组件都有很高要求。
不同地方在于:沸腾床加氢技术采用上流气液固三相沸腾式加氢反应器、反应温度410~440℃,采用条形颗粒状的钼系催化剂;鼓泡床加氢技术采用上流浆态鼓泡式加氢反应器、反应温度460~480℃,采用粉末状的铁系催化剂。
以沸腾床工艺为特征的加氢工艺设备维护复杂、设备磨损/折旧大,所涉及的颗粒状钼系催化剂成本高,需在线卸剂补剂。
该技术目前主要用于渣油加氢领域。
成熟的工艺主要有AXENS(NA)公司的H-Oil工艺及CHEVRON LUMMUS GLOBAL(CLG)公司的LC-Fining工艺。
两种工艺技术来源于同一家公司,不同之处在于前者使用外循环,后者使用内循环。
鼓泡床工艺为特征的渣油加氢工艺催化剂消耗大,存在含废催化剂油浆处理问题,但所涉及的铁系催化剂要便宜许多。
我们认为该技术更适合含沥青质的煤焦油加氢。
鼓泡床加氢技术主要用于煤直接液化制油、煤油共炼、沥青质重油加工。
二战时期德国的煤直接液化制航空煤油采用该工艺。
经过多年的开发,当前较为成熟的鼓泡床加氢工艺主要有意大利埃尼集团的EST工艺及德国Veba公司的VCC工艺。
目前该技术的所有权人是BP石油,并与美国KBR公司合作开发相关工艺,其在中国市场的独家合作伙伴为延长石油。
延长石油与KBR在陕西榆林合作建设的50万吨/年煤油共炼项目,原料采用50%的煤粉与50%的减压渣油,总投资15.7亿,目前处于停车检修状态。
同样仿制BP/KBR的VCC技术,华石能源在河南鹤壁投资建设了10万吨/年高温煤焦油加氢装置,该装置尚未投产。
国外煤焦油加氢工艺相比国内呈现出大型化、多样性等特点。
美国KBR公司的VCC(Veba-Combi-Cracking)悬浮床加氢裂化技术含液相加氢处理(LPH)和气相加氢处理(GPH)两个过程。
其原理为:(1)原料与添加剂和氢气混合后进入悬浮床反应器,发生热裂化反应,并在高压临氢状态下加氢饱和。
其中进料中残炭、胶质、沥青质在特定的添加剂作用下发生热裂化和加氢饱和的过程,基本没有焦炭的产生。
(2)悬浮床热裂化的产物进入热高压分离器中分离,清洁的气体产物去固定床反应器在进一步加氢裂化和加氢精制,生产出优质的石脑油和轻柴油调和组分。
分离出的固体物质主要是焦炭,可造粒当燃煤使用。
VCC技术可解决固定床加氢裂化无法长周期运行的难题。
并且因为能够加工重质油、高转化率、高液体收率的优点从2010年进入我国市场,于2012年和延长集团合作在榆林靖边投资建设45万t/a加氢裂化装置。
该装置将原设计压力由30MPa降到了20MPa,投运后发现给料阀磨损加剧,系统管塞严重,到目前仍未正常运行。
德国H-TEC加氢技术与VCC技术技出同源,均来自于20世纪40年代德国的煤加氢制燃料油技术。
当时德国有12套加氢装置运行,原料为煤焦油、煤、褐煤、重油等,产品覆盖德国90%的燃料油需求。
20世纪后期,博特落普工厂(KAB)承继了德国加氢技术,开展直接煤液化/重油改质。
2001年成立的H-TEC公司,主要成员为KAB厂技术研发骨干,工艺、设备、维修工程师及操作人员,在重油改质和煤焦油加氢领域,具有35年工程经验,可以提供鼓泡床加氢技术支持服务、成熟的技术方案和设计、指导装置开车。
委内瑞拉重油是全世界最难加氢的重油之一。
H-TEC鼓泡床加氢技术对催化剂要求不高,但对设备要求较高,系统压力达到30MPa,温度460~480℃,设备投资大,系统操作难度高。
(2)国内工艺技术概况1)技术概况目前,国内煤焦油加氢技术正处在一个发展时期,在国内目前正在运行和拟建的企业已达10余家。
根据各种技术的特点,可以归纳为如下5类:①轻馏分油固定床加氢技术;②延迟焦化-固定床加氢技术;③悬浮床加氢技术;④宽馏分固定床加氢技术;⑤全馏分固定床加氢技术。
以上已实现工业化的典型煤焦油加氢技术也均存在一定的弊端,如煤焦油全馏分油固定床加氢技术存在原料适应性差、催化剂寿命短、对原料预处理效果要求高等弊端,这些诸多弊端对装置长周期稳定运行造成了一定的影响。
延迟焦化-固定床加氢裂化联合技术的工艺流程复杂,且有约15%的煤焦油转化成焦炭,致使煤焦油资源没有得到充分利用。
2)蒽油固定床加氢技术蒽油加氢技术,采用加氢精制-加氢裂化固定床技术,对蒽油和洗油混合料进行加氢处理,生产一号轻质煤焦油和二号轻质煤焦油产品。
3)全馏分固定床加氢技术陕煤化集团神木富油能源科技有限公司是承担“煤低温快速热解、煤焦油全馏分加氢”等煤炭分级分质综合利用的高新科技示范企业。
总投资9.6亿元的“2×60万吨/年煤热解及12万吨/年中低温煤焦油综合利用工程”项目的全馏分加氢已实现工业化生产,年产柴油馏分9.21万吨、石脑油1.69万吨、尾料0.9万吨。
该项目采用已获得多项发明专利的“煤固体热载体低温快速热解技术”和“煤焦油全馏分加氢多产中间馏分油成套工业化技术(FTH)”。
该项目于2009年7月开工建设,2011年9月建成试车,打通全流程,经优化改进于2012年7月6日投产。
FTH技术的重大创新之一在于中低温煤焦油的预处理技术。
先通过特制金属过滤网除去煤焦油中的喹啉不溶物,再借助电场净化设施除去煤焦油中的钙、镁、铁、钠等金属离子和水分,提高煤焦油的收率,其中净化煤焦油收率90%以上,喹啉不溶物、盐和水脱除率95%以上,脱铁率70.6%,该装置属于低温煤焦油加氢装置,加氢技术难度小,对原料进料馏分有限制,要求馏分不能大于510℃。
4)延迟焦化-固定床加氢技术陕煤化集团神木天元化工有限公司50万吨/年“煤焦油轻质化”项目,年加工中低温煤焦油50万吨,轻质化煤焦油38万吨,石油焦8.5万吨,液化气2.9万吨,液氨0.25万吨,硫磺0.1万吨。
项目采用“中低温煤焦油加氢技术”,是国内目前单套最大的“中低温焦油加氢”装置。
该项目采用延迟焦化-固定床加氢技术对中低温煤焦油进行加氢处理生产清洁燃料,2010年3月通过中国石油和化学工业联合会组织的72小时现场考核和技术鉴定,焦化液体产品收率76.8%,加氢装置液体产品收率达到96.3%。
该公司主要产品为轻质化煤焦油1#和轻质化煤焦油2#。
轻质化煤焦油1#主要由C12~C24烷烃组成,常温、常压下为焦黄色透明液体。
密度:845~885kg/m³,硫氮含量不大于0.002%,十六烷值为46.6。
该产品主要应用于使用柴油的内燃机车、船舰和柴油锅炉。
轻质化煤焦油2#是由C5~C11烷烃、环烷烃、芳烃、烯烃组成的混合物。
在常温、常压下为无色透明液体,有特殊气味,不溶于水。
密度:700~777kg/m³,硫含量不大于0.002%,烷烃含量不大于60%,芳烃含量不大于12%,烯烃含量不大于1%。
由于采用延迟焦化,将煤焦油中沥青去除,收油率大大降低。
从以上技术来看,蒽油加氢属于高温煤焦油的分离物,原料特性比较特殊,加工难度高于中、低温煤焦油,有较高的技术壁垒,从目前国内外使用情况来看,德国HTC公司鼓泡床技术、华电重工蒽油加氢技术、高温煤焦油加氢技术均能满足蒽油加氢的要求,但H-TEC提出的联合氢解工艺技术,特征是加氢鼓泡床组合后面固定床加氢提质,但H-TEC核心主要是处理含沥青原料的加氢鼓泡床。
对于协同鼓泡床组合的固定床设置,H-TEC提出两套解决方案:(A)单压系统,从鼓泡床至固定床的全流程,系统压力等级为30Mpa;(B)双压系统,鼓泡床单元采用30MPa,固定床单元采用20Mpa,其中固定床单元完全可以采用蒽油加氢固定床(设备流程与工艺不变,仅调整催化剂及其生产操作条件)。
但不论哪种方案,H-TEC认为鼓泡床加氢工艺技术要求系统压力为30MPa,因此对高压泵、高压阀、反应器要求较高。
鉴于单一的超高压系统解决方案对操作要求高,每单元都有特殊要求,尤其对于30MPa超高压设备组件,为降低风险,大部分需进口,装置投资较高。
1.2 行业分析(1)行业发展趋势从2012年开始,中国煤制油行业正式进入了商业化开发阶段。
“十二五”期间神华、伊泰、潞安、神华宁煤、兖矿和晋煤陆续推进一系列大规模煤制油项目。
据测算,我国四大煤制油示范项目于2010年形成147万吨/年产能后,2011~2013年工业规模煤制油项目处于建设阶段,没有新增产能。
从2014年开始,随着煤制油商业化装置的陆续建成投产,中国煤制油产能将迅速提升,于2016年达到1600万吨/年,由于煤制油产品具有较高的十六烷值、较高的硫氮,不能直接用于燃烧,需要匹配的调和剂进行调和,为此,生产清洁调和剂品有较微广阔的市场。
煤焦油是煤焦化、干馏和煤制气过程产生的产物之一。