11切削液的加工性能评价
切削液性能的评定方法
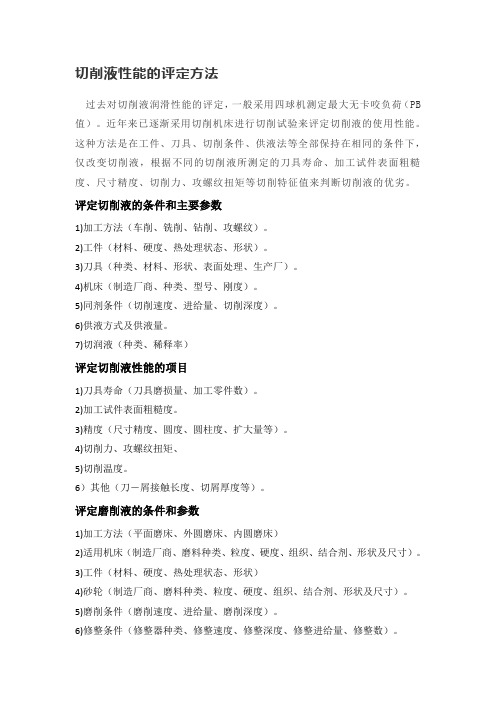
切削液性能的评定方法过去对切削液润滑性能的评定,一般采用四球机测定最大无卡咬负荷(PB 值)。
近年来已逐渐采用切削机床进行切削试验来评定切削液的使用性能。
这种方法是在工件、刀具、切削条件、供液法等全部保持在相同的条件下,仅改变切削液,根据不同的切削液所测定的刀具寿命、加工试件表面粗糙度、尺寸精度、切削力、攻螺纹扭矩等切削特征值来判断切削液的优劣。
评定切削液的条件和主要参数1)加工方法(车削、铣削、钻削、攻螺纹)。
2)工件(材料、硬度、热处理状态、形状)。
3)刀具(种类、材料、形状、表面处理、生产厂)。
4)机床(制造厂商、种类、型号、刚度)。
5)同剂条件(切削速度、进给量、切削深度)。
6)供液方式及供液量。
7)切润液(种类、稀释率)评定切削液性能的项目1)刀具寿命(刀具磨损量、加工零件数)。
2)加工试件表面粗糙度。
3)精度(尺寸精度、圆度、圆柱度、扩大量等)。
4)切削力、攻螺纹扭矩、5)切削温度。
6)其他(刀-屑接触长度、切屑厚度等)。
评定磨削液的条件和参数1)加工方法(平面磨床、外圆磨床、内圆磨床)2)适用机床(制造厂商、磨料种类、粒度、硬度、组织、结合剂、形状及尺寸)。
3)工件(材料、硬度、热处理状态、形状)4)砂轮(制造厂商、磨料种类、粒度、硬度、组织、结合剂、形状及尺寸)。
5)磨削条件(磨削速度、进给量、磨削深度)。
6)修整条件(修整器种类、修整速度、修整深度、修整进给量、修整数)。
7)供液方式及供液量。
8)磨削液(种类、稀释倍数)。
评定磨削液性能的项目1)砂轮寿命(砂轮磨损量、砂轮的磨损状态等)。
2)磨削力。
3)试件表面粗糙度及尺寸精度。
4)工件表面状态(磨削烧伤、磨削裂纹、加工变质层、残余应力)。
5)磨削温度。
6)磨削比。
磨削比的计算如下:磨削比=工件磨除量/砂轮磨损量砂轮磨损量=砂轮半径减少量x砂轮直径xπx工件宽度工件磨除量=(磨前工件高度-磨后工件高度)x 工件长度x工件宽度。
[超实用] 判断切削液性能和质量差异的简单方法
![[超实用] 判断切削液性能和质量差异的简单方法](https://img.taocdn.com/s3/m/247af489cc22bcd126ff0c93.png)
机械工厂如何简单判断不同切削液的性能和质量差异可按如下方法在工厂内对不同的切削液产品的主要性能指标进行简单可行的比较:1、润滑性能在相同设备、同样刀具并加工同样工件的情况下,比较刀具寿命(单把刀可加工的零件数或者切削距离)以及加工质量(表面光洁度)。
刀具寿命越长、加工表面光洁度越好,则切削液润滑性能越优秀。
润滑性能是切削液非常重要的指标。
直接影响加工质量和成本。
但是无法直观判断,因为你无法获知切削液的配方及其有效润滑成分的多少。
2、稳定性取原液适量放置在透明容器中静置24小时,观察原液是否有分层和杂质,是否均匀;取原液适量用自来水配制成5%稀释液在透明容器中静置15分钟,观察稀释液是否均匀,是否有分层和杂质。
上述两项有任何一项出现分层、杂质及不均匀现象。
即可判定切削液稳定性较差。
3、泡沫性能配置5%浓度稀释液并放置在透明的试剂瓶中,盖好盖子。
然后用正常力量上下摇动试剂瓶15秒钟然后静置在桌面上开始计时并观察:瓶中产生的泡沫如能在15秒内消失,则泡沫性能合格。
消失速度越快越好。
4、防锈性能及防腐蚀性能配置5%浓度稀释液适量,选取尺寸适中的所加工零件(有经过切削加工的加工面)在切削液中浸泡适当时间(半小时到数小时。
根据零件加工时间长短)后取出在空气中静置观察:多长时间以后零件出现锈蚀或者腐蚀。
基本的要求是3-5天。
时间越长,自然防锈防腐能力越长。
特别说明,对此性能用这种方法只能初略判断。
对一些特殊的材料(比如航空铝合金),往往需要严格的实验室验证。
5、抗菌能力配置5%浓度稀释液适量并在容器中静置,定期嗅闻切削液味的变化。
越早变味发臭的切削液,其抗菌能力越差。
这一项直接关系到切削液的使用寿命。
大部分产品的抑制细菌原理是靠产品配方中的杀菌剂,唯有极少量的产品(如巴索的Blasocut系列)使用先进的生物抑菌方式,有效解决了杀菌剂对皮肤的潜在危害问题。
6、抗杂油能力配置5%浓度稀释液适量并在透明容器中静置,然后在切削液中滴入适量液压油或导轨油。
切削液 标准

切削液标准
切削液是用于机械加工中润滑和冷却的液体,其标准通常涉及以
下方面:
1. 成分:切削液应包含合适的基础油、添加剂和水。
添加剂包
括防锈剂、抗菌剂、抗氧化剂等,使其具有良好的润滑性和冷却性能。
2. pH值:切削液的pH值应在不同加工材料和操作条件下具有适当的范围,以保持其性能稳定。
3. 稳定性:切削液应具有良好的化学和生物稳定性,以防止细
菌和微生物的生长和繁殖。
4. 光滑性:切削液应具有良好的润滑性,以减少摩擦和磨损,
延长切削工具的使用寿命。
5. 热性能:切削液应具有较高的冷却性能,以在高速切削中有
效地散热,防止加工部件热变形。
6. 环保性:切削液应符合环保要求,包括悬浮固体、挥发性有
机物(VOC)和重金属的要求。
7. 适用范围:切削液应适用于不同类型材料和加工操作的要求,包括锻造、轧制、车削、钻孔等。
以上是切削液的一些标准,具体标准可能会有所差异,根据具体
的需求和操作条件进行选择。
数控机床切削液的质量检测与评估方法
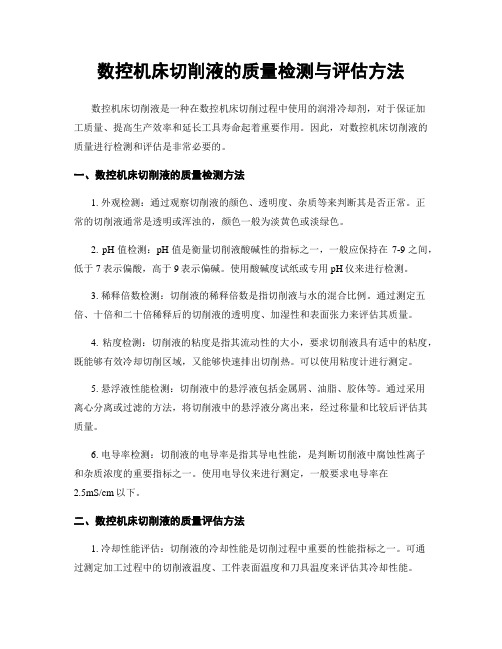
数控机床切削液的质量检测与评估方法数控机床切削液是一种在数控机床切削过程中使用的润滑冷却剂,对于保证加工质量、提高生产效率和延长工具寿命起着重要作用。
因此,对数控机床切削液的质量进行检测和评估是非常必要的。
一、数控机床切削液的质量检测方法1. 外观检测:通过观察切削液的颜色、透明度、杂质等来判断其是否正常。
正常的切削液通常是透明或浑浊的,颜色一般为淡黄色或淡绿色。
2. pH值检测:pH值是衡量切削液酸碱性的指标之一,一般应保持在7-9之间,低于7表示偏酸,高于9表示偏碱。
使用酸碱度试纸或专用pH仪来进行检测。
3. 稀释倍数检测:切削液的稀释倍数是指切削液与水的混合比例。
通过测定五倍、十倍和二十倍稀释后的切削液的透明度、加湿性和表面张力来评估其质量。
4. 粘度检测:切削液的粘度是指其流动性的大小,要求切削液具有适中的粘度,既能够有效冷却切削区域,又能够快速排出切削热。
可以使用粘度计进行测定。
5. 悬浮液性能检测:切削液中的悬浮液包括金属屑、油脂、胶体等。
通过采用离心分离或过滤的方法,将切削液中的悬浮液分离出来,经过称量和比较后评估其质量。
6. 电导率检测:切削液的电导率是指其导电性能,是判断切削液中腐蚀性离子和杂质浓度的重要指标之一。
使用电导仪来进行测定,一般要求电导率在2.5mS/cm以下。
二、数控机床切削液的质量评估方法1. 冷却性能评估:切削液的冷却性能是切削过程中重要的性能指标之一。
可通过测定加工过程中的切削液温度、工件表面温度和刀具温度来评估其冷却性能。
2. 润滑性能评估:切削液的润滑性能对机床切削过程中的摩擦和磨损起着重要作用。
可以通过测定摩擦系数和刀具磨损量来评估其润滑性能。
3. 抗菌性能评估:切削液中的细菌和真菌对切削液的质量和稳定性有一定的影响。
通过采用平皿计数法或培养法来评估切削液中的微生物数量,了解切削液的抗菌性能。
4. 稳定性评估:切削液的稳定性是指在切削过程中,切削液能够稳定地提供冷却和润滑功能。
机械加工切削液的性能研究
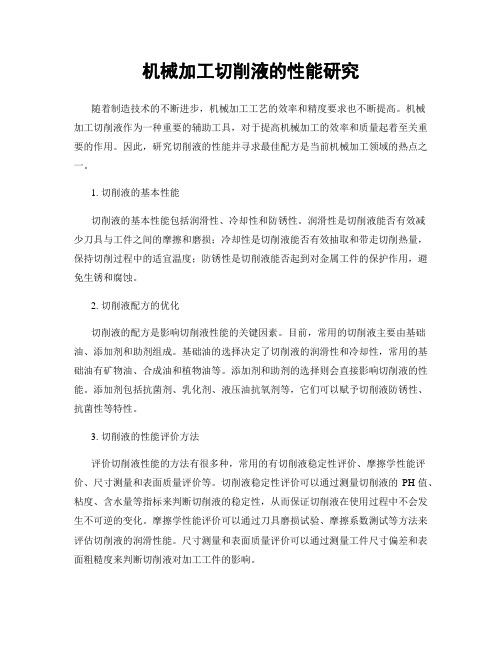
机械加工切削液的性能研究随着制造技术的不断进步,机械加工工艺的效率和精度要求也不断提高。
机械加工切削液作为一种重要的辅助工具,对于提高机械加工的效率和质量起着至关重要的作用。
因此,研究切削液的性能并寻求最佳配方是当前机械加工领域的热点之一。
1. 切削液的基本性能切削液的基本性能包括润滑性、冷却性和防锈性。
润滑性是切削液能否有效减少刀具与工件之间的摩擦和磨损;冷却性是切削液能否有效抽取和带走切削热量,保持切削过程中的适宜温度;防锈性是切削液能否起到对金属工件的保护作用,避免生锈和腐蚀。
2. 切削液配方的优化切削液的配方是影响切削液性能的关键因素。
目前,常用的切削液主要由基础油、添加剂和助剂组成。
基础油的选择决定了切削液的润滑性和冷却性,常用的基础油有矿物油、合成油和植物油等。
添加剂和助剂的选择则会直接影响切削液的性能。
添加剂包括抗菌剂、乳化剂、液压油抗氧剂等,它们可以赋予切削液防锈性、抗菌性等特性。
3. 切削液的性能评价方法评价切削液性能的方法有很多种,常用的有切削液稳定性评价、摩擦学性能评价、尺寸测量和表面质量评价等。
切削液稳定性评价可以通过测量切削液的PH值、粘度、含水量等指标来判断切削液的稳定性,从而保证切削液在使用过程中不会发生不可逆的变化。
摩擦学性能评价可以通过刀具磨损试验、摩擦系数测试等方法来评估切削液的润滑性能。
尺寸测量和表面质量评价可以通过测量工件尺寸偏差和表面粗糙度来判断切削液对加工工件的影响。
4. 切削液的优化应用和发展趋势随着机械加工技术的不断发展,对切削液的要求也在不断提高。
优化应用切削液可以提高切削效率、延长刀具寿命,减少机械加工过程中的磨损和能耗。
未来,随着环保要求的提高,切削液的绿色化和可再生性将成为发展的重点。
研发环保型的切削液,例如水基切削液和微量切削液已成为研究的热点。
总结:机械加工切削液的性能研究是一个综合性课题,涉及材料学、化学、机械学等多个学科的知识。
优化切削液配方和研究切削液的性能对于提高机械加工的效率和质量具有重要意义。
切削液在机械加工中的应用与性能研究

切削液在机械加工中的应用与性能研究引言机械加工是现代制造业中的重要环节,而在机械加工过程中,切削液的应用起着至关重要的作用。
切削液不仅可以起到冷却、润滑的作用,还能延长工具寿命、提高加工精度等。
本文将探讨切削液在机械加工中的应用及其性能研究。
切削液的应用1. 冷却与润滑在高速切削过程中,由于切削温度的升高,刀具与工件之间摩擦的产生会导致很高的热量。
而切削液的应用可以有效地冷却刀具和工件,降低切削温度,从而减少热引起的损伤。
同时,切削液还能润滑刀具与工件之间的摩擦,降低切削力,提高切削性能。
2. 清洗与防腐切削液可以通过喷射或涂覆的方式将切屑及金属屑冲洗掉,保持加工表面的清洁。
另外,切削液中添加防腐剂能有效地防止工件、机床及刀具的锈蚀,延长使用寿命。
切削液的性能研究1. pH值及稳定性切削液的pH值直接影响切削液的稳定性及防锈性能。
研究人员通过调整切削液中的添加剂浓度,如硼酸、硼氢化钠等,以及监测切削液的pH值来优化其性能。
2. 抗菌性能切削液在长时间使用、暴露于空气中易受微生物污染。
因此,研究人员致力于开发抗菌切削液。
一种常见的方法是添加抗菌剂,如三氯化铜、二氯化苯胺等,以抑制细菌和真菌的生长。
3. 润滑性切削液的润滑性对切削过程的摩擦和磨损有重要影响。
研究人员通过添加机械添加剂(如有机硼、含氟聚合物等)来改善切削液的润滑性能,减少切削力和工件表面的磨损。
4. 冷却效果切削液的冷却性能可以通过添加冷却剂和调节流体流量来改善。
研究人员还通过数值模拟等方法来优化切削液的冷却效果,在减少切削温度的同时保证工件表面的质量。
结论切削液在机械加工中的应用是不可忽视的,它能够提高切削过程的效率和质量。
通过对切削液的性能研究,可以不断改进切削液的应用效果。
因此,对切削液的应用与性能研究是机械加工领域中的一个重要课题,也将为制造业的发展做出重要贡献。
机床切削液的理化性能与评价方法概述
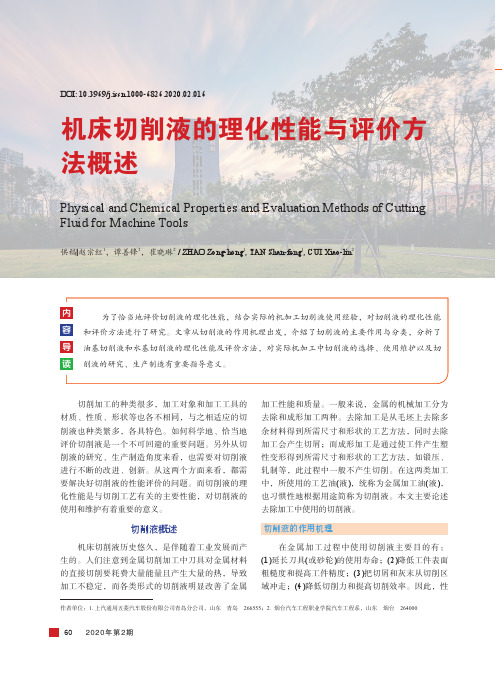
机床切削液的理化性能与评价方法概述Physical and Chemical Properties and Evaluation Methods of Cutting Fluid for Machine Tools供稿|赵宗红1,谭善锋1,崔晓琳2 / ZHAO Zong-hong1, TAN Shan-feng1, CUI Xiao-lin2DOI: 10.3969/j.issn.1000-6826.2020.02.016切削加工的种类很多,加工对象和加工工具的材质、性质、形状等也各不相同,与之相适应的切削液也种类繁多,各具特色。
如何科学地、恰当地评价切削液是一个不可回避的重要问题。
另外从切削液的研究、生产制造角度来看,也需要对切削液进行不断的改进、创新。
从这两个方面来看,都需要解决好切削液的性能评价的问题。
而切削液的理化性能是与切削工艺有关的主要性能,对切削液的使用和维护有着重要的意义。
切削液概述机床切削液历史悠久,是伴随着工业发展而产生的。
人们注意到金属切削加工中刀具对金属材料的直接切削要耗费大量能量且产生大量的热,导致加工不稳定,而各类形式的切削液明显改善了金属加工性能和质量。
一般来说,金属的机械加工分为去除和成形加工两种。
去除加工是从毛坯上去除多余材料得到所需尺寸和形状的工艺方法,同时去除加工会产生切屑;而成形加工是通过使工件产生塑性变形得到所需尺寸和形状的工艺方法,如锻压、轧制等,此过程中一般不产生切削。
在这两类加工中,所使用的工艺油(液),统称为金属加工油(液),也习惯性地根据用途简称为切削液。
本文主要论述去除加工中使用的切削液。
切削液的作用机理在金属加工过程中使用切削液主要目的有:(1)延长刀具(或砂轮)的使用寿命;(2)降低工件表面粗糙度和提高工件精度;(3)把切屑和灰末从切削区域冲走;(4)降低切削力和提高切削效率。
因此,性作者单位:1. 上汽通用五菱汽车股份有限公司青岛分公司,山东青岛 266555;2. 烟台汽车工程职业学院汽车工程系,山东烟台 264000工艺与装备Apparatus and Equipments金属加工能良好的切削液必须具有润滑、冷却、清洗和防锈等作用。
切削加工中切削液的应用对切削性能的影响分析

切削加工中切削液的应用对切削性能的影响分析引言:切削液是切削加工中必不可少的辅助工具之一,它在切削过程中扮演着冷却、润滑和清洗的重要角色。
切削液的正确应用对切削性能具有重要影响。
本文将分析切削液对切削性能的影响,包括切削液的作用原理、性能要求以及常见切削液对切削性能的影响。
同时,将探讨如何选择切削液以实现最佳切削性能。
切削液的作用原理:切削液在切削过程中发挥多种作用,主要包括冷却切削区域、润滑切削工具与工件的接触面以及冲洗切屑的作用。
切削液的冷却作用可以减缓工具和工件的温度升高,降低加工硬度和提高切削速度。
润滑作用可以减少切削摩擦,降低工具磨损,并提高切削表面质量。
冲洗作用可以清除切削过程中产生的切屑和切削液中的切削渣等杂质,有效防止堵塞切削区域。
切削液的性能要求:为了发挥切削液的最佳性能,切削液应具备以下几个方面的性能要求:1. 良好的冷却性能:切削液应具有优异的冷却性能,能够及时有效地吸收和传导切削过程中产生的热量,降低工具和工件的温度。
2. 减少切削摩擦:切削液应在切削区域形成一层润滑膜,以减少切削摩擦,降低刀具磨损,并提高加工表面质量。
3. 防止切削震荡:切削液应具有适当的黏度和粘度,在切削过程中有效减少切削震荡的产生,保证刀具与工件的稳定接触。
4. 良好的清洁性:切削液应具有良好的清洁性能,及时清除切削过程中产生的切屑和切削渣等杂质,减少切屑堵塞切削区域的发生。
常见切削液对切削性能的影响:1. 水溶性切削液:水溶性切削液是常见的切削液之一,由水、润滑剂、抗菌剂等组成。
水溶性切削液能够提供有效的冷却和润滑效果,适用于大部分切削过程。
然而,由于水溶性切削液中含水量较高,容易引起零件表面锈蚀问题。
2. 油溶性切削液:油溶性切削液由润滑油、润滑剂等组成,有效降低了零件表面锈蚀问题。
油溶性切削液在高速、高温切削过程中具有优异的润滑性能,适用于高速切削加工。
然而,油溶性切削液不易清洗,需要配备专门的清洗设备。
切削液的优点

切削液的优点
切削液具备良好的冷却性能、润滑性能、防锈性能、除油清洁功能、防腐功能、易稀释等特点,君合生产的切削液的优点主要有:
1.配方中使用了高性能的原材料,可确保切削液具有极高的生物稳定性;
2.即使用在很低的浓度时也可提供极好的防锈性能;
3.能有效抑制液雾(特别是滚动磨削时);
4.不会在量具、工具夹及刀具表面形成粘稠的残留物;
5.由于分散性好,乳化液能迅速与工件分离,故带出量很低;
6.与传统润滑液相比,初始溶液的浓度较低(4-6%);
7.使用各种水质,均可保证良好的低泡性能(包括软水);
8.产品的高润滑性可保证刀具寿命更长。
切削液的作用与性能(精)

切(磨)削液的作用与性能您现在的位置:胶体与表面化学网>> 资讯中心>> 表面张力仪应用资料>> 正文切(磨)削液的作用与性能作者:admin 转贴自:本站原创点击数:2 更新时间:2006-7-19 资讯录入:admin内容摘要:不同的冷却润滑材料的冷却效果在金属切削过程中,为提高切削效率,提高工件的精度和降低工件表面粗糙度,延长刀具使用寿命,达到最佳的经济效果,就必须减少刀具与工件、刀具与切屑之间磨擦,及时带走切削区内因材料不同的冷却润滑材料的冷却效果在金属切削过程中,为提高切削效率,提高工件的精度和降低工件表面粗糙度,延长刀具使用寿命,达到最佳的经济效果,就必须减少刀具与工件、刀具与切屑之间磨擦,及时带走切削区内因材料变形而产生的热量。
要达到这些目的,一方面是通过开发高硬度耐高温的刀具材料和改进刀具的几何形状,如随着碳素钢、高速钢硬质合金及陶瓷等刀具材料的相继问世以及使用转位刀具等,使金属切削的加工率得到迅速提高;另一方面采用性能优良的切(磨)削液往往可以明显提高切削效率,降低工件表面粗糙度,延长刀具使用寿命,取得良好和经济效益。
切削液作用有如下几方面:1.冷却作用冷却作用是依靠切削液的对流换热和汽化把切削热从固体(刀具、工件和切屑)带走,降低切削区的温度,减少工件变形,保持刀具硬度和尺寸。
切削液的冷却作用取决于它的热参数值,特别是比热容和热导率。
此外,液体的流动条件和热交换系数也起重要作用,热交换系数可以通过改变表面活性材料和汽化热大小来提高。
水具有较高的比热容和大的导热率,所以水基的切削性能要比油基切削液好。
表1-1为水和油的执参数值。
表1-1 水油的热参数值类别热导率W/(m.k)比热容J/kg.K汽化热j/g水0.634.18×1032260 油0.125~0.211.67~2.09×103167~314改变液体的流动条件,如提高流速和加大流量可以有效地提高切削液的冷却效果,特别对于对于冷却效果差的油基切削液,加大切削液的供液压力和加大流量,可有较提高冷却性能。
切削液的正确设计及其质量评估
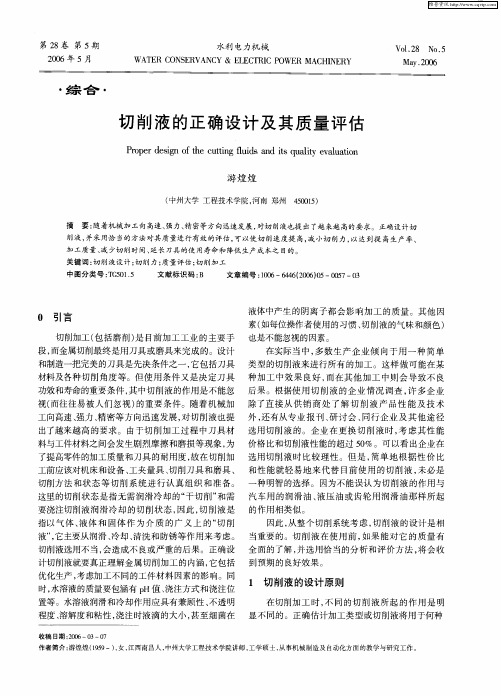
种 明智 的选 择 。 因为不 能误 认 为 切 削液 的作 用 与
液 这里的切削状态是指无需润滑冷却 的“ 干切削” 和需 汽 车 用 的润 滑 油 、 压 油 或齿 轮用 润 滑 油那 样 所 起 要浇 注切 削液 润 滑 冷却 的切 削状 态 , 因此 , 削 液 是 的作用 相类似 。 切
维普资讯
・
5・ 8
水利 电 力机 械
20 0 6年 5月
切 削过程是 首要 考 虑的 问题 。如 当车 削几何 形状 较 简单 的零件 时 , 因其 是开 放式 切削 , 削液 容易进 入 切 到切 削 区域 中 , 用 时 只要 加 注 一 定 压 力 和增 加 一 使 些 添加剂 , 即可 得 到满 意 的效果 。而 对钻 削 , 其是 尤
了提高零件 的加工 质量 和刀具 的耐 用度 , 在切 削加 选 用切削 液 时 比较 理性 。但 是 , 单 地 根 据 性 价 比 故 简 工前应该对 机床和设 备 、 夹量 具 、 削刀 具 和磨具 、 和性 能就 轻 易 地 来 代替 目前 使 用 的切 削 液 , 必 是 工 切 未 切削方 法 和状 态 等 切 削 系统 进 行 认 真 组 织 和 准备 。
计切 削液就要真正 理解 金属切 削 加工 的 内涵 , 它包 括 到预期 的 良好效果 。
优化生产 , 考虑加工不同的工件材料因素的影 响。同 时, 水溶液的质量要包涵有 p H值 、 浇注方式和浇注位 置等。水溶液润滑和冷却作用应具有兼顾性 、 不透明
1 切 削液 的设 计 原 则
切削加工 ( 括磨 削 ) 目前 加 工工 业 的 主要 手 也是不 能忽视的 因素 。 包 是 段, 而金属切 削最 终 是用刀 具或 磨具来 完成 的。设 计 和制造一把完 美的刀 具是 先决 条件 之一 , 包括 刀具 类 型 的切 削液来 进 行所有 的加 工 。这 样 做 可 能在 某 它 材料及各 种切 削 角度 等 。但 使 用 条 件 又是 决 定刀 具 种 加 工 中效 果 良好 , 在其 他 加 工 中则会 导 致 不 良 而
机械加工中的切削液性能研究报告

机械加工中的切削液性能研究报告摘要:本研究旨在探讨机械加工中切削液的性能对加工过程和切削效果的影响。
通过对切削液的成分、润滑性能、冷却性能以及抗菌性能等方面进行综合分析,本研究发现切削液的性能对提高加工效率、延长刀具寿命和改善加工表面质量具有重要作用。
因此,切削液的性能研究对于机械加工行业的发展具有重要意义。
1. 引言机械加工过程中,切削液作为一种重要的辅助工具,广泛应用于金属加工中。
切削液的性能直接影响着切削过程的稳定性和加工效果。
因此,研究切削液的性能对于提高机械加工的效率和质量具有重要意义。
2. 切削液的成分分析切削液的成分包括基础油、添加剂和稀释剂。
基础油的选择直接影响着切削液的润滑性能和冷却性能。
添加剂的种类和含量决定了切削液的抗菌性能和润滑性能。
稀释剂的选择和添加量对切削液的稀释效果和使用寿命有着重要影响。
3. 切削液的润滑性能研究切削液的润滑性能是影响切削过程中摩擦和磨损的重要因素。
研究发现,适当的润滑性能可以减少切削过程中的摩擦热和刀具磨损,提高切削效率和加工表面质量。
因此,切削液的润滑性能研究对于优化切削过程具有重要意义。
4. 切削液的冷却性能研究切削过程中产生的热量会对刀具和工件造成损伤,因此切削液的冷却性能对于保持切削过程的稳定性和提高切削效率至关重要。
研究发现,优良的切削液冷却性能可以有效降低切削过程中的温度,延长刀具的使用寿命,并且对于加工表面质量的提高也起到积极作用。
5. 切削液的抗菌性能研究切削液在使用过程中容易受到细菌和真菌的污染,造成切削液的变质和降低切削效果。
因此,研究切削液的抗菌性能对于保持切削液的稳定性和延长使用寿命具有重要意义。
一些研究表明,添加抗菌剂可以有效抑制切削液中细菌和真菌的生长,从而保持切削液的稳定性和性能。
6. 结论本研究通过对切削液的成分、润滑性能、冷却性能和抗菌性能等方面进行综合分析,发现切削液的性能对于提高机械加工的效率和质量具有重要作用。
切削液对切削加工质量的影响研究

切削液对切削加工质量的影响研究在金属切削加工过程中,切削液是起到润滑、冷却和清洁作用的重要物质。
切削液的选用和使用方法对于切削加工质量的影响至关重要。
本文将从不同角度探讨切削液对切削加工质量的影响,并提出相应的研究结论。
一、切削液对表面质量的影响切削液对表面质量的影响主要体现在以下几个方面:1. 润滑性影响:切削液的添加可以减少金属与刀具的摩擦,降低切削温度,从而有效减少表面热裂纹和切削力。
适当的润滑可以降低表面粗糙度,提高表面光洁度。
2. 冷却性影响:切削液能够吸收和带走切削过程中产生的大量热量,保持切削温度在较低的水平。
有效的冷却可以避免表面硬化、残余应力等不良现象的发生,提高加工质量。
3. 清洁性影响:切削液具有冲洗、冲刷作用,可以清除加工过程中产生的切屑和切削液中的杂质,保持加工环境清洁。
清洁度的提高可以有效防止加工表面的污染和氧化,提高表面质量。
二、切削液对尺寸精度的影响切削液对尺寸精度的影响主要表现在以下几个方面:1. 切削液的黏度:适当选择黏度合适的切削液,可以降低切削时液体底流现象的发生,有效提高尺寸精度。
2. 切削液的添加量:过多或过少的切削液添加量都会影响尺寸精度。
过多的切削液加大了液体底流的风险,过少的切削液则无法起到充分润滑冷却的作用。
3. 切削液的稳定性:稳定的切削液可以保持连续不断的润滑和冷却效果,避免因切削液性能的不稳定而引起的尺寸变化。
三、切削液对刀具寿命的影响切削液的使用与刀具寿命密切相关。
正确选择和使用切削液可以延长刀具的使用寿命,提高经济效益。
1. 切削液的性能稳定性:稳定的切削液可以减少切削温度和切削力,从而减少刀具受热和磨损的程度,延长刀具使用寿命。
2. 切削液的清洁性:切削液中的杂质和切屑会造成刀具的磨损和损坏,因此切削液的清洁性对于刀具寿命至关重要。
3. 切削液的杀菌防腐性:切削液中的细菌和真菌等会导致切削液的变质,形成酸性物质,从而对刀具进行腐蚀。
机械制造过程中切削液润滑剂性能测试与优化
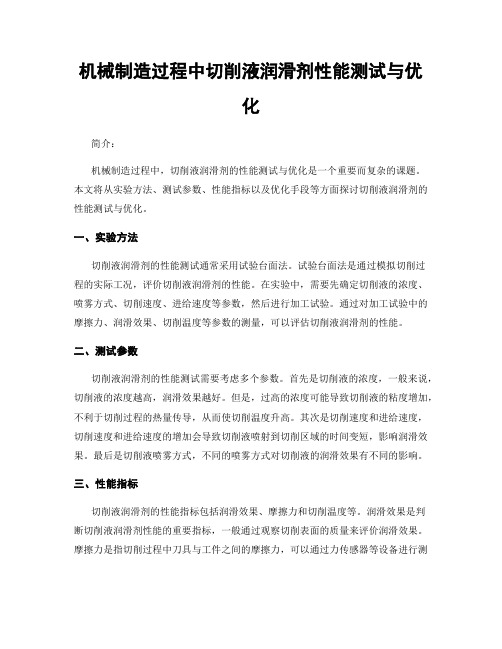
机械制造过程中切削液润滑剂性能测试与优化简介:机械制造过程中,切削液润滑剂的性能测试与优化是一个重要而复杂的课题。
本文将从实验方法、测试参数、性能指标以及优化手段等方面探讨切削液润滑剂的性能测试与优化。
一、实验方法切削液润滑剂的性能测试通常采用试验台面法。
试验台面法是通过模拟切削过程的实际工况,评价切削液润滑剂的性能。
在实验中,需要先确定切削液的浓度、喷雾方式、切削速度、进给速度等参数,然后进行加工试验。
通过对加工试验中的摩擦力、润滑效果、切削温度等参数的测量,可以评估切削液润滑剂的性能。
二、测试参数切削液润滑剂的性能测试需要考虑多个参数。
首先是切削液的浓度,一般来说,切削液的浓度越高,润滑效果越好。
但是,过高的浓度可能导致切削液的粘度增加,不利于切削过程的热量传导,从而使切削温度升高。
其次是切削速度和进给速度,切削速度和进给速度的增加会导致切削液喷射到切削区域的时间变短,影响润滑效果。
最后是切削液喷雾方式,不同的喷雾方式对切削液的润滑效果有不同的影响。
三、性能指标切削液润滑剂的性能指标包括润滑效果、摩擦力和切削温度等。
润滑效果是判断切削液润滑剂性能的重要指标,一般通过观察切削表面的质量来评价润滑效果。
摩擦力是指切削过程中刀具与工件之间的摩擦力,可以通过力传感器等设备进行测量。
切削温度是切削过程中产生的热量,过高的切削温度会导致刀具退火、变形,从而降低加工质量。
四、优化手段为了提高切削液润滑剂的性能,可以采取以下优化手段。
首先是优化切削液的配方,根据工件的材料和加工要求,选择合适的添加剂,以增强切削液的抗热性、防锈性和润滑性。
其次是优化切削液的供给方式,如调整喷雾方式和润滑剂的浓度,以提高润滑效果。
此外,还可以采取节能减排措施,如优化切削参数,减小切削力、切削温度和损耗,从而降低能耗和环境影响。
结论:切削液润滑剂的性能测试与优化是机械制造过程中的重要问题。
通过实验方法、测试参数、性能指标和优化手段等方面的研究,可以不断提高切削液润滑剂的性能,提高加工质量和效率。
切削液的优化配方与加工性能研究

切削液的优化配方与加工性能研究引言:切削液作为一种重要的切削工具,在金属加工过程中起到冷却、润滑和清洗等功能,对于保障加工质量和提高工作效率具有至关重要的作用。
因此,优化切削液的配方和研究其加工性能具有重要的意义。
本文就切削液的优化配方与加工性能进行了深入研究,并总结了相关研究成果。
一、切削液优化配方研究1.1 添加剂的优化选择切削液中的添加剂对切削液性能的改善至关重要。
根据不同的加工需要,选择合适的添加剂进行配方优化是提高切削液性能的关键。
例如,选择具有优良润滑性能的添加剂可以减小摩擦系数,提高切削液的润滑性能。
此外,添加抗菌剂和防锈剂可以有效延长切削液的使用寿命。
1.2 浓度控制的优化切削液的浓度对加工效果和成本都有着重要影响。
过高的切削液浓度会导致加工表面粗糙度过高,而过低则会影响切削液的全面使用效果。
因此,在研究中,对切削液浓度进行优化是必不可少的。
通过调整切削液的添加量和工作液的质量来控制切削液的浓度,以达到最佳的加工效果。
1.3 pH值的调控切削液pH值的调控直接影响切削液中溶解程度、防锈性能和生物稳定性等。
一般来说,较小的pH值对铁基金属加工有利,而在镁、铝等物质的切削加工过程中,较高的pH值更具优势。
因此,通过调整切削液的酸碱度,可以提高切削液的加工性能。
1.4 稳定性的改善切削液的稳定性对于保证长时间稳定运行和延长使用寿命非常重要。
切削液在长时间使用过程中容易受到污染和氧化,从而降低了其性能。
因此,研究人员通过添加稳定剂,并优化切削液的工作环境,如温度、湿度和氧气浓度等,来提高切削液的稳定性。
二、切削液的加工性能研究2.1 冷却性能的研究切削液的冷却性能是其最重要的功能之一。
研究人员通过测量不同切削液配方在冷却性能方面的数据,如冷却时间、冷却速率等,评估切削液的冷却效果。
研究结果表明,合理优化切削液的配方可以显著提高切削液的冷却性能,进而提高加工质量。
2.2 润滑性能的研究切削液的润滑性能直接影响切削刃具与工件之间的摩擦情况。
磨粉机切削液对加工性能的影响研究
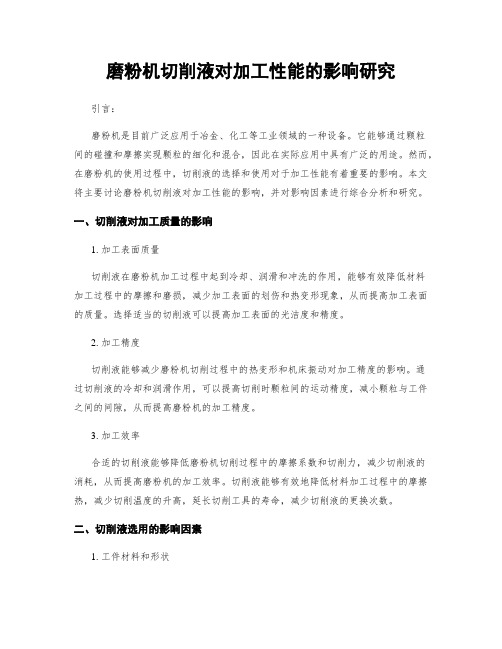
磨粉机切削液对加工性能的影响研究引言:磨粉机是目前广泛应用于冶金、化工等工业领域的一种设备。
它能够通过颗粒间的碰撞和摩擦实现颗粒的细化和混合,因此在实际应用中具有广泛的用途。
然而,在磨粉机的使用过程中,切削液的选择和使用对于加工性能有着重要的影响。
本文将主要讨论磨粉机切削液对加工性能的影响,并对影响因素进行综合分析和研究。
一、切削液对加工质量的影响1. 加工表面质量切削液在磨粉机加工过程中起到冷却、润滑和冲洗的作用,能够有效降低材料加工过程中的摩擦和磨损,减少加工表面的划伤和热变形现象,从而提高加工表面的质量。
选择适当的切削液可以提高加工表面的光洁度和精度。
2. 加工精度切削液能够减少磨粉机切削过程中的热变形和机床振动对加工精度的影响。
通过切削液的冷却和润滑作用,可以提高切削时颗粒间的运动精度,减小颗粒与工件之间的间隙,从而提高磨粉机的加工精度。
3. 加工效率合适的切削液能够降低磨粉机切削过程中的摩擦系数和切削力,减少切削液的消耗,从而提高磨粉机的加工效率。
切削液能够有效地降低材料加工过程中的摩擦热,减少切削温度的升高,延长切削工具的寿命,减少切削液的更换次数。
二、切削液选用的影响因素1. 工件材料和形状不同的工件材料和形状对切削液的选择有着不同的要求。
例如,在加工硬质材料时,需要选择具有良好润滑性和耐高温性能的切削液,以减少切削过程中的磨损和热变形现象。
而在加工柔软材料时,应选择具有良好冷却性能的切削液,以控制加工过程中的温度变化。
2. 切削液的成分和性能切削液的成分和性能直接影响着其对加工性能的影响。
一般而言,优质的切削液应具有较低的黏度、较高的闪点和较好的冷却性能。
同时,切削液中的添加剂和杂质含量也会对加工性能产生一定的影响。
3. 加工环境条件加工环境条件包括加工温度、湿度、气压等因素。
这些因素会直接影响切削液的工作状态和性能。
例如,高温环境下使用切削液,其冷却效果会受到限制,从而影响加工质量和效率。
工件材料的切削加工性的评定指标
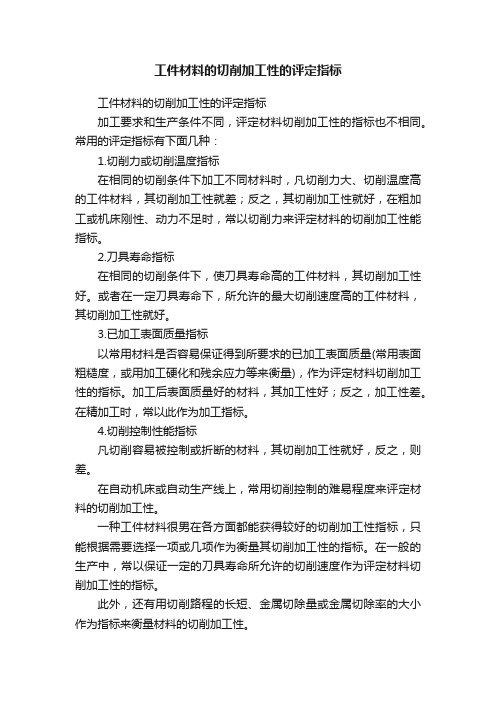
工件材料的切削加工性的评定指标
工件材料的切削加工性的评定指标
加工要求和生产条件不同,评定材料切削加工性的指标也不相同。
常用的评定指标有下面几种:
1.切削力或切削温度指标
在相同的切削条件下加工不同材料时,凡切削力大、切削温度高的工件材料,其切削加工性就差;反之,其切削加工性就好,在粗加工或机床刚性、动力不足时,常以切削力来评定材料的切削加工性能指标。
2.刀具寿命指标
在相同的切削条件下,使刀具寿命高的工件材料,其切削加工性好。
或者在一定刀具寿命下,所允许的最大切削速度高的工件材料,其切削加工性就好。
3.已加工表面质量指标
以常用材料是否容易保证得到所要求的已加工表面质量(常用表面粗糙度,或用加工硬化和残余应力等来衡量),作为评定材料切削加工性的指标。
加工后表面质量好的材料,其加工性好;反之,加工性差。
在精加工时,常以此作为加工指标。
4.切削控制性能指标
凡切削容易被控制或折断的材料,其切削加工性就好,反之,则差。
在自动机床或自动生产线上,常用切削控制的难易程度来评定材料的切削加工性。
一种工件材料很男在各方面都能获得较好的切削加工性指标,只能根据需要选择一项或几项作为衡量其切削加工性的指标。
在一般的生产中,常以保证一定的刀具寿命所允许的切削速度作为评定材料切削加工性的指标。
此外,还有用切削路程的长短、金属切除量或金属切除率的大小作为指标来衡量材料的切削加工性。
切削液的性能评定

切削液的性能评定要选择一个标准来判定切削液性能优劣是较困难的,而根据这个标准建立一个评价切削液效率的试验过程同样是一件难事。
这个问题从实验室转移到车间中会更复杂,但也可通过下述方法对切削液的性能作出评价。
刀具寿命评定采用刀具寿命评价切削液性能时,存在的主要问题是试验结果与工厂所测数据间的相关性常常很差。
因为对直刃刀具有效的切削液对成型刃刀具并不一定同样有效,反之亦然。
此外,切屑厚度对切削液的适应性也有影响。
若在同一特定加工条件下对几种切削液进行评价则要容易得多,因为通过测定刀具锐利度的变化值可得到刀具的平均寿命。
此评定即便简化了过程,但试验费用却很昂贵。
表面光洁度试验面光洁度试验不如刀具寿命试验复杂,可采用一根试验长棒,用同一刀具进行切削加工,通过表面粗糙度测量仪获得试验数据来评价切削液的性能优劣。
此评定试验,切削类型是很重要的。
如在平面铣削中,光洁的表面是由第二切削刃形成的,而在外圆铣削中,则是由主切削刃(轴向平行)形成新生面。
因而由一种加工方法获得的数据不能用于另一种加工的评定。
冷却性能评定采用某些专业技术测量切削液在实际加工中的冷却能力可判定其效率。
由于刀-屑界面的温度与刀具寿命有很好的相关性,因而刀具工作热电偶是一项非常有用的技术。
但其不足之处是不能区分温度降低是由于切削液的热传递还是由于加工中所产生热量少所致。
润滑效率评定切削液润滑效率的测定需采用一台机床刀具测力计。
在切削加工试验中,切削液的润滑作用降低了进刀力和切削力。
通过测定力的变化可计算切削液的润精效率。
切削力随进刀量的增加而增加,随切削液润滑效率的提高而降低。
若对刀具施加恒定的进刀力,则切削液的润滑效率越高,进刀量越大。
这套试验评定装置对刀屑之间的摩擦变化十分灵敏,但需一台设备以保证施加在切屑刀具上的进刀力恒定。
生理影响评价生理影响评价可通过操作人员来进行,如采用类似于过敏试验的医学研究技术进行皮肤刺激反应等。
操作人员的不同生理反应会影响到他对切削液的评价。
- 1、下载文档前请自行甄别文档内容的完整性,平台不提供额外的编辑、内容补充、找答案等附加服务。
- 2、"仅部分预览"的文档,不可在线预览部分如存在完整性等问题,可反馈申请退款(可完整预览的文档不适用该条件!)。
- 3、如文档侵犯您的权益,请联系客服反馈,我们会尽快为您处理(人工客服工作时间:9:00-18:30)。
技术讲座切削液应用技术第11讲:切削液的加工性能评价刘镇昌济南库伦特科技有限公司济南250101摘要:介绍了评价切削液加工性能的实机切削试验方法、模拟切削试验方法及切削液加工性能的综合评价方法。
关键词:切削液,性能评价,加工性能,综合评价切削加工的种类很多,加工对象和加工工具的材质、性状等往往又各不相同,与之相适应的切削液自然也当各具特色,导致切削液产品种类繁多。
如何科学地、恰当地评价和选择切削液就是个不可回避的现实问题。
另一方面,从切削液的研究、生产角度来看,需要对切削液不断地进行改进、创新。
在这两方面都需要解决好切削液的性能评价问题。
切削液的性能可分为加工性能、理化性能、环卫性能三个大的方面【1,2】。
切削液的加工性能系指切削液在切削过程中所能表现出来的效能,它直接与切削加工效果有关。
这些效果包括加工质量、加工效率、刀具损耗、切屑处理等几个主要方面,其中加工质量包括加工精度和已加工表面完整性(表面粗糙度、表面变质层、残留应力),并综合体现在工序成本中。
评价切削液加工性能的试验室方法目前尚不成熟,仍不得不依靠实际的切削试验。
通过切削试验获取切削过程的各种输出信息,并进行处理。
最后,根据这些被处理过的信息,按一定的数学模型去进行性能评价。
1评价切削液加工性能的实机切削试验方法所谓实机切削试验,就是直接在生产线或加工机床上进行切削试验,检测切削结果数据,按照一定的评价模型对受试切削液的加工性能做出评价。
实机切削试验可以归纳为三种方式:工序节拍方式、参数调整方式、综合优化方式。
1.1 工序节拍方式(1)试验方法所谓工序节拍方式,是指使用受试切削液,按照原有工艺的参数、步骤和节拍在生产线或加工机床上对零件进行切削加工,检测某些加工结果数据,对受试切削液做出性能评价。
采用工序节拍方式时,除切削液外,其余工艺条件保持不变。
因此,试验方法简单,换上受试切削液,一切按照原有工艺规程进行切削加工即可。
(2)评价指标由于工件、机床、刀具、切削用量等切削输入参数与原有加工方式相同,切削输出结果中加工效率基本上没有变化,可选用的评价指标是刀具寿命和加工质量。
加工质量指标中,又以已加工表面粗糙度较为敏感,其次是加工精度。
(3)特点与应用工序节拍方式针对某一具体的加工环境对切削液性能进行评价,这是最接近加工实态的试验方式,试验结果可靠。
由于这种试验方式具有很强的针对性,因此其评价结果的代表性也较差,即是说,在这种具体加工环境下性能优异的切削液在别的加工环境下未必如此。
此外,这种试验方式需耗费较长时间。
但由于生产节拍方式简单易行,不影响企业的生产计划,易于被企业接受,因此是目前应用最为广泛的试验方法。
1.2 参数调整方式(1)试验方法所谓参数调整方式,跟工序节拍方式一样,仍然是直接在加工机床上进行切削试验,检测切削结果数据,按照一定的评价模型对受试切削液的加工性能做出评价。
所不同的是,前者可以对切削液的供液方法和压力、流量等参数进行调整,以使切削液充分发挥其加工效能。
(2)评价指标参数调整方式所选用的评价指标与工序节拍方式相同。
(3)特点与应用参数调整方式的特点与工序节拍方式大抵相同。
由于可以对供液方法和压力、流量等参数进行调整,试验参数空间有所扩展,试验工作量必然增加。
但是,这些尝试和努力可能找到最适合的供液参数,使切削液充分发挥其加工效能,往往能够得到出乎意料的结果。
采用参数调整方式最好先在单机上进行试验,切削液及其供液参数确定后再移到生产线上实施。
1.3 综合优化方式(1)试验方法在参数调整方式的基础上,如果把可调整的试验参数进一步扩展到切削用量三要素(切削速度、进给量、背吃刀量),就是综合优化方式。
在这种方式下,可以在更为广泛的参数空间内搜索受试切削液加工效能的最佳值域。
(2)评价指标采用综合优化方式进行试验时,切削液加工性能的评价指标除刀具寿命和加工质量之外,还有加工效率指标,如:单位工序时间、每班次加工零件数、金属切除率等。
(3)特点与应用采用综合优化方式评价切削液的加工性能时,可变更的输入参数有切削液、供液方式、供液压力、供液流量、切削速度、背吃刀量、进给量等。
如果进行单因素试验,工作量将会很大。
这时,一般需要进行周密的试验方案设计。
比如,采用正交试验法,事先确定优化目标,并选择恰当的因素和水平进行试验,以较少的试验次数获得较好的试验结果。
综合优化试验方式不适合在生产线上评价切削液的加工性能,主要用于与切削液相关的技术攻关、科学研究、产品开发等场合。
1.4 用实机切削试验法评价切削液加工性能举例【3】试验方法:工序节拍方式实机试验工件:高铬耐磨铸铁内衬套(硬度HB400),直径186mm,长度413mm,壁厚20mm 试验机床:CW6163C加工方式:外圆车削试验刀具:刀片YBD052,CNMA120408,刀杆MCMNN2525P12(刀槽前角-9º,主偏角50º)切削用量:切削速度43.9m/min,进给量0.8mm/r,背吃刀量2mm受试切削液:A(合成型)、B(微乳化型)、C(非活性极压乳化型)评价指标:刀具达到磨损限时切除金属总体积试验结果:见表1表1 使用不同切削液的车削试验结果可以看出,就加工效能而言,非活性极压乳化型切削液最好;微乳化型切削液次之;合成型切削液最差。
从试验记录中也可看出,使用合成切削液时,曾发生两次闷车(卡盘打滑,工件停转),这是由于合成切削液的润滑性较差、切削力较大所致。
图1为试验现场照片。
图1 切削试验现场照片2评价切削液加工性能的模拟切削试验方法如前所述,评价切削液加工性能的实机切削试验方法虽然最接近加工实态,试验结果可靠。
但它也有一些缺点。
比如,评价结果有很大的局限性。
因为实机切削试验法的评价结果是在某一具体的加工环境中得出的,其好坏只有相对意义。
说某种切削液的加工性能好或者不好,是在特定的加工环境中与其它切削液相互比较而言。
实机切削试验法(尤其是工序节拍方式)耗费时间较长,调整参数不便;此外,在生产现场进行评价还受到各种各样的限制。
比如,不能对工件的预制状态进行精确控制,容易引起试验误差;亦不大可能对多种切削液做出性能评价,因为在生产现场更换切削液毕竟是一件颇为麻烦的事情。
所以,无论是为了现场生产选择切削液,还是为了开发和研究新型切削液,都需要建立实验室模拟试验方法。
模拟切削试验有两类:一类是在通用机床上模拟切削加工实态;另一类是设计制造专门的模拟评定试验机。
2.1 在通用机床上进行的模拟切削试验通用机床指各类车床、铣床、钻床、镗床、刨床、磨床等。
可以利用这些通用机床的固有功能来模拟各种不同的加工状态和环境,用于评价切削液的加工性能。
在设计和实施切削液的实验室模拟评价试验时,需注意以下几点:①试验应该有明确的意义。
它必须模拟金属切削过程中最重要的加工要素和条件。
也就是说,模拟的切削状态要尽可能接近实际的切削状态。
这一点至关重要;②输入参数必须是可控制的,而且对试验结果的影响应该是显著的;③作为评价指标的试验结果应便于测量,或者能够与基准液或其它参考液相互比较;④要保证试验数据的真实性、精确性和可靠性。
试验必须进行得十分仔细,同一种试验需进行多次,对检测数据取平均值。
要留意试验中出现的异常现象。
必须牢记:任何人为地为了加速试验而设置的不真实条件都将导致虚假的结论。
模拟切削试验可以直接使用实际的机械零件,但更多的是使用特制的试件。
试件的材料和热处理状态要与实际零件相同,加工部位的形状要与被加工零件相似,其余部位尽量简单,以降低成本。
在评价指标方面,除使用与加工性能有关的试验结果外,还可以在线检测切削力、切削温度等伴生效应的值作为辅助的评价指标。
模拟试验也可以采用工序节拍方式、参数调整方式或综合优化方式。
(1)单项模拟切削试验一般采用钻削、车削或铣削的方法进行模拟试验。
钻削试验法用于评价切削液的加工性能由来已久。
国内外不少学者从事过这方面的试验研究。
文献【4】比较了钻削、车削和铣削试验,认为用高速钢钻头进行钻削试验来评价不同切削液的加工性能是最好的方法。
评价指标可以是钻孔数、钻孔表面粗糙度、钻头磨损、钻削力和扭矩等。
在数控钻床上进行钻孔试验操作方便,得出的试验结果一致性较好。
(2)综合模拟切削试验美国有一家技术组织TechSolve认为【5】,由于没有一种单独的切削试验方法能够满足预测切削液加工性能的要求,建议采用四种不同的金属切削试验,每种试验考察切削液在金属去除过程中的一个不同方面的表现。
表2是作者根据文献【5】的文字说明归纳出来的试验要素一览表。
表2 用综合模拟切削试验法评价切削液加工性能的要素一览表2.2 切削液加工性能模拟评定试验机a)美国Falex攻丝扭矩试验机b)国产MRG-005型攻丝扭矩试验机图2 攻丝扭矩模拟评定试验机攻丝扭矩模拟评定试验机是一种技术上较为成熟的金属加工液模拟评价设备。
该设备使用标准丝锥和有预制底孔的标准螺母(丝锥和螺母材料的物理性能受严格控制)。
试验时,丝锥浸泡在受试切削液中进行攻丝加工,设备自动记录切削过程中攻丝扭矩的变化,并进行数据处理、输出试验结果。
攻丝扭矩模拟评定试验机最早由美国Falex公司生产面世(图2a)。
我国“八五”攻关计划列为开发项目,由济南试验机厂(现为济南试金集团有限公司)承担研制任务,并于上世纪九十年代开发成功(图2b)。
丝锥是一种多刃成形刀具,攻丝是一种低速成形切削加工方法。
由于是对称的内表面切削,刀具没有退让余地,还带有一定的挤压成分。
攻丝扭矩模拟评定试验机可用于金属加工液的润滑性能的模拟评定,包括切削液、塑性成形加工润滑剂等。
但对于无挤压成分的非成形刀具加工,尤其是中、高速切削加工用油(液),由于模拟的切削状态和实际加工环境之间的差异较大,模拟试验结果与实际加工效果之间的相关性值得进一步探讨。
3 切削液加工性能的综合评价图3 综合评价模型的计算程序流程图上述评价试验的结果若是单项指标,或者只针对1种切削液,试验结束后优劣自然分明;若评价指标有多个并且针对多种切削液,就需要进行综合评价。
综合评价的方法颇多,图3所示为作者使用过的一种切削液综合评价方法的计算程序流程【6】(数学模型略)。
因为实验结果是一组量纲不尽相同的物理量,为便于综合比较,首先须将这些物理量按一定的优劣对应关系转化为无量纲数,这种优劣对应关系称为优越性隶属函数,其函数关系一般需要由评价者根据经验和实际情况设定。
各评价指标的权系数由评价者从切削液的使用目的和加工要求出发,结合自己的知识和经验确定,通常可辅以层次分析法减轻主观失误。
输人数据后,上机运算就可立即打印出评价结果。
参考文献1 刘镇昌. 金属切削液----选择、配制与使用. 北京:化学工业出版社,20072 刘镇昌. 切削液技术. 北京:机械工业出版社,20083 庞文焕. 高铬耐磨铸铁外圆车削工艺参数优化试验研究,【学士学位论文】.指导教师刘镇昌.济南:山东大学,2006. 64 Leep, H. R., Investigation of synthetic cutting fluids in drilling, turning and milling processes,Lubrication Engineering,1981,37(12):715~7215 Jerry P. Byers. Metalworking Fluids(2nd Edition). London & New York:CRC Press, Taylor andFrancis Group, Society of Tribologists and Lubrication Engineers, 20066 刘镇昌. 磨削液的效能识别及作用机理研究,【博士学位论文】. 指导教师陈日曜. 武汉:华中科技大学(原华中理工大学),1988。