切削液性能的评定方法
11切削液的加工性能评价
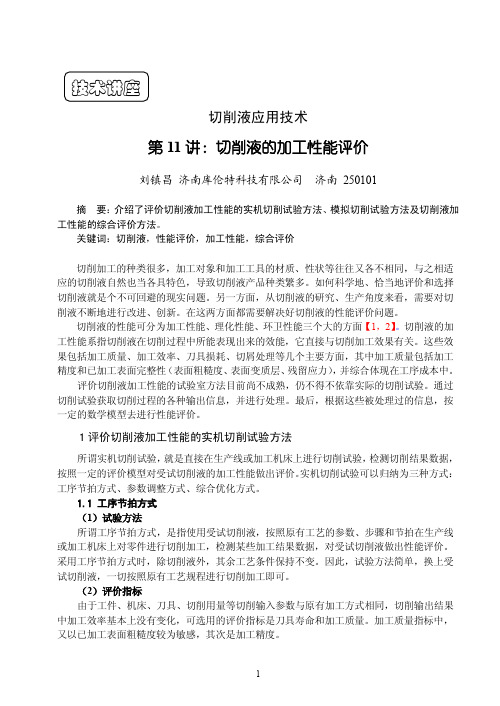
技术讲座切削液应用技术第11讲:切削液的加工性能评价刘镇昌济南库伦特科技有限公司济南250101摘要:介绍了评价切削液加工性能的实机切削试验方法、模拟切削试验方法及切削液加工性能的综合评价方法。
关键词:切削液,性能评价,加工性能,综合评价切削加工的种类很多,加工对象和加工工具的材质、性状等往往又各不相同,与之相适应的切削液自然也当各具特色,导致切削液产品种类繁多。
如何科学地、恰当地评价和选择切削液就是个不可回避的现实问题。
另一方面,从切削液的研究、生产角度来看,需要对切削液不断地进行改进、创新。
在这两方面都需要解决好切削液的性能评价问题。
切削液的性能可分为加工性能、理化性能、环卫性能三个大的方面【1,2】。
切削液的加工性能系指切削液在切削过程中所能表现出来的效能,它直接与切削加工效果有关。
这些效果包括加工质量、加工效率、刀具损耗、切屑处理等几个主要方面,其中加工质量包括加工精度和已加工表面完整性(表面粗糙度、表面变质层、残留应力),并综合体现在工序成本中。
评价切削液加工性能的试验室方法目前尚不成熟,仍不得不依靠实际的切削试验。
通过切削试验获取切削过程的各种输出信息,并进行处理。
最后,根据这些被处理过的信息,按一定的数学模型去进行性能评价。
1评价切削液加工性能的实机切削试验方法所谓实机切削试验,就是直接在生产线或加工机床上进行切削试验,检测切削结果数据,按照一定的评价模型对受试切削液的加工性能做出评价。
实机切削试验可以归纳为三种方式:工序节拍方式、参数调整方式、综合优化方式。
1.1 工序节拍方式(1)试验方法所谓工序节拍方式,是指使用受试切削液,按照原有工艺的参数、步骤和节拍在生产线或加工机床上对零件进行切削加工,检测某些加工结果数据,对受试切削液做出性能评价。
采用工序节拍方式时,除切削液外,其余工艺条件保持不变。
因此,试验方法简单,换上受试切削液,一切按照原有工艺规程进行切削加工即可。
(2)评价指标由于工件、机床、刀具、切削用量等切削输入参数与原有加工方式相同,切削输出结果中加工效率基本上没有变化,可选用的评价指标是刀具寿命和加工质量。
水性切削液的基本检测方法
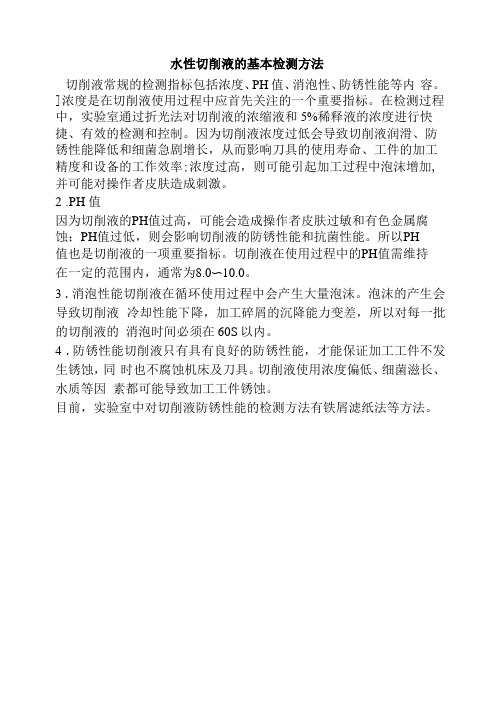
水性切削液的基本检测方法
切削液常规的检测指标包括浓度、PH值、消泡性、防锈性能等内容。
]浓度是在切削液使用过程中应首先关注的一个重要指标。
在检测过程中,实验室通过折光法对切削液的浓缩液和5%稀释液的浓度进行快捷、有效的检测和控制。
因为切削液浓度过低会导致切削液润滑、防锈性能降低和细菌急剧增长,从而影响刀具的使用寿命、工件的加工精度和设备的工作效率;浓度过高,则可能引起加工过程中泡沫增加, 并可能对操作者皮肤造成刺激。
2.PH 值
因为切削液的PH值过高,可能会造成操作者皮肤过敏和有色金属腐蚀;PH值过低,则会影响切削液的防锈性能和抗菌性能。
所以PH
值也是切削液的一项重要指标。
切削液在使用过程中的PH值需维持
在一定的范围内,通常为8.0〜10.0。
3.消泡性能切削液在循环使用过程中会产生大量泡沫。
泡沫的产生会导致切削液冷却性能下降,加工碎屑的沉降能力变差,所以对每一批的切削液的消泡时间必须在60S以内。
4.防锈性能切削液只有具有良好的防锈性能,才能保证加工工件不发生锈蚀,同时也不腐蚀机床及刀具。
切削液使用浓度偏低、细菌滋长、水质等因素都可能导致加工工件锈蚀。
目前,实验室中对切削液防锈性能的检测方法有铁屑滤纸法等方法。
切削液浓度测量方法

切削液浓度测量方法
切削液浓度测量方法
切削液浓度直接影响到加工质量和设备寿命,因此测量切削液浓度非常重要。
目前常用的测量方法有密度法、折射法、电导率法和红外光谱法等。
密度法是将样品与纯水混合后测量混合溶液的密度,计算出样品的浓度。
这种方法的优点是测量简单,准确度高,但需要使用密度计和天平等仪器,并且样品需要进行稀释,不能直接测量。
折射法是通过样品的折射率来计算出样品的浓度,需要使用折射仪进行测量。
这种方法准确度较高,且不需要样品稀释,但需要仪器较为复杂且价格昂贵。
电导率法是利用切削液浓度与电导率成反比的特性进行测量。
需要使用电导计进行测量,该方法测量简便,准确度较高,但受到杂质的影响较大。
红外光谱法是通过分析样品的红外光谱来计算出样品的浓度。
这种方法不需要进行样品稀释,且测量准确度高。
但需要使用红外光谱仪,
仪器价格昂贵。
综合考虑以上几种方法的优缺点,选择测量方法主要受到实际情况的限制。
在实际的工业应用中,大多数情况下采用的是电导率法或折射法,因为这两种方法的测量结果比较稳定,准确度高,而且测量仪器较为简便,价格相对较低。
需要注意的是,无论采用哪种方法进行测量,都需要对仪器进行校准以保证测量结果的准确性。
并且,在测量切削液浓度时,应注意选择适当的样品量和稀释倍数,避免误差的产生。
总之,切削液浓度的测量方法是工业加工中必不可少的环节,需要根据实际情况选择合适的方法进行测量,同时注意仪器的校准及测量误差的避免,以保证加工质量和设备寿命。
[超实用] 判断切削液性能和质量差异的简单方法
![[超实用] 判断切削液性能和质量差异的简单方法](https://img.taocdn.com/s3/m/247af489cc22bcd126ff0c93.png)
机械工厂如何简单判断不同切削液的性能和质量差异可按如下方法在工厂内对不同的切削液产品的主要性能指标进行简单可行的比较:1、润滑性能在相同设备、同样刀具并加工同样工件的情况下,比较刀具寿命(单把刀可加工的零件数或者切削距离)以及加工质量(表面光洁度)。
刀具寿命越长、加工表面光洁度越好,则切削液润滑性能越优秀。
润滑性能是切削液非常重要的指标。
直接影响加工质量和成本。
但是无法直观判断,因为你无法获知切削液的配方及其有效润滑成分的多少。
2、稳定性取原液适量放置在透明容器中静置24小时,观察原液是否有分层和杂质,是否均匀;取原液适量用自来水配制成5%稀释液在透明容器中静置15分钟,观察稀释液是否均匀,是否有分层和杂质。
上述两项有任何一项出现分层、杂质及不均匀现象。
即可判定切削液稳定性较差。
3、泡沫性能配置5%浓度稀释液并放置在透明的试剂瓶中,盖好盖子。
然后用正常力量上下摇动试剂瓶15秒钟然后静置在桌面上开始计时并观察:瓶中产生的泡沫如能在15秒内消失,则泡沫性能合格。
消失速度越快越好。
4、防锈性能及防腐蚀性能配置5%浓度稀释液适量,选取尺寸适中的所加工零件(有经过切削加工的加工面)在切削液中浸泡适当时间(半小时到数小时。
根据零件加工时间长短)后取出在空气中静置观察:多长时间以后零件出现锈蚀或者腐蚀。
基本的要求是3-5天。
时间越长,自然防锈防腐能力越长。
特别说明,对此性能用这种方法只能初略判断。
对一些特殊的材料(比如航空铝合金),往往需要严格的实验室验证。
5、抗菌能力配置5%浓度稀释液适量并在容器中静置,定期嗅闻切削液味的变化。
越早变味发臭的切削液,其抗菌能力越差。
这一项直接关系到切削液的使用寿命。
大部分产品的抑制细菌原理是靠产品配方中的杀菌剂,唯有极少量的产品(如巴索的Blasocut系列)使用先进的生物抑菌方式,有效解决了杀菌剂对皮肤的潜在危害问题。
6、抗杂油能力配置5%浓度稀释液适量并在透明容器中静置,然后在切削液中滴入适量液压油或导轨油。
切削油质量检测的方法
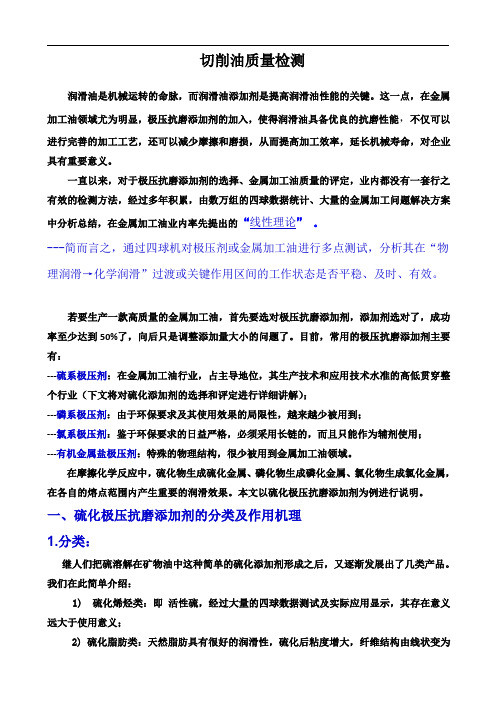
切削油质量检测润滑油是机械运转的命脉,而润滑油添加剂是提高润滑油性能的关键。
这一点,在金属加工油领域尤为明显,极压抗磨添加剂的加入,使得润滑油具备优良的抗磨性能,不仅可以进行完善的加工工艺,还可以减少摩擦和磨损,从而提高加工效率,延长机械寿命,对企业具有重要意义。
一直以来,对于极压抗磨添加剂的选择、金属加工油质量的评定,业内都没有一套行之有效的检测方法,经过多年积累,由数万组的四球数据统计、大量的金属加工问题解决方案中分析总结,在金属加工油业内率先提出的“线性理论”。
---简而言之,通过四球机对极压剂或金属加工油进行多点测试,分析其在“物理润滑→化学润滑”过渡或关键作用区间的工作状态是否平稳、及时、有效。
若要生产一款高质量的金属加工油,首先要选对极压抗磨添加剂,添加剂选对了,成功率至少达到50%了,向后只是调整添加量大小的问题了。
目前,常用的极压抗磨添加剂主要有:---硫系极压剂:在金属加工油行业,占主导地位,其生产技术和应用技术水准的高低贯穿整个行业(下文将对硫化添加剂的选择和评定进行详细讲解);---磷系极压剂:由于环保要求及其使用效果的局限性,越来越少被用到;---氯系极压剂:鉴于环保要求的日益严格,必须采用长链的,而且只能作为辅剂使用;---有机金属盐极压剂:特殊的物理结构,很少被用到金属加工油领域。
在摩擦化学反应中,硫化物生成硫化金属、磷化物生成磷化金属、氯化物生成氯化金属,在各自的熔点范围内产生重要的润滑效果。
本文以硫化极压抗磨添加剂为例进行说明。
一、硫化极压抗磨添加剂的分类及作用机理1.分类:继人们把硫溶解在矿物油中这种简单的硫化添加剂形成之后,又逐渐发展出了几类产品。
我们在此简单介绍:1)硫化烯烃类:即活性硫,经过大量的四球数据测试及实际应用显示,其存在意义远大于使用意义;2)硫化脂肪类:天然脂肪具有很好的润滑性,硫化后粘度增大,纤维结构由线状变为网状,抗磨性显著提高;常见的有传统硫化工艺生产的深色硫化棉籽油(T404、T405、T405A)、现代工艺生产的浅色低味硫化猪油;3)硫化脂肪酸酯类:多采用现代工艺硫化,把天然油脂酯化后,油溶性得以保留,硫含量得到提高后,极压抗磨性均有提高,具有非常好的应用前景。
绿色切削液模糊综合评价
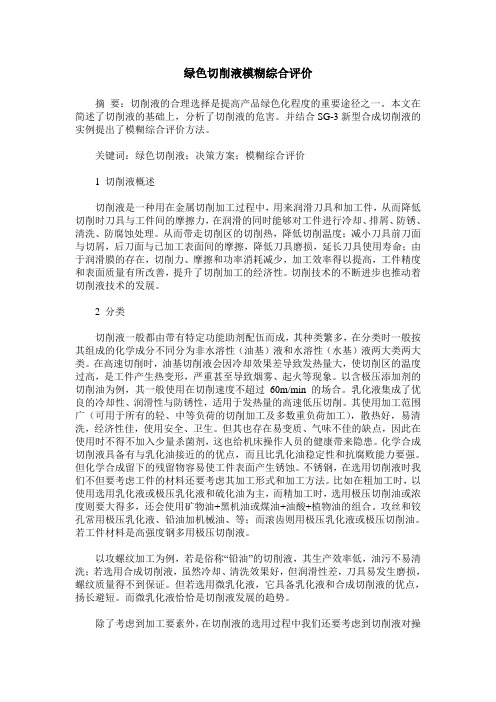
绿色切削液模糊综合评价摘要:切削液的合理选择是提高产品绿色化程度的重要途径之一。
本文在简述了切削液的基础上,分析了切削液的危害。
并结合SG-3新型合成切削液的实例提出了模糊综合评价方法。
关键词:绿色切削液;决策方案;模糊综合评价1 切削液概述切削液是一种用在金属切削加工过程中,用来润滑刀具和加工件,从而降低切削时刀具与工件间的摩擦力,在润滑的同时能够对工件进行冷却、排屑、防锈、清洗、防腐蚀处理。
从而带走切削区的切削热,降低切削温度;减小刀具前刀面与切屑,后刀面与已加工表面间的摩擦,降低刀具磨损,延长刀具使用寿命;由于润滑膜的存在,切削力、摩擦和功率消耗减少,加工效率得以提高,工件精度和表面质量有所改善,提升了切削加工的经济性。
切削技术的不断进步也推动着切削液技术的发展。
2 分类切削液一般都由带有特定功能助剂配伍而成,其种类繁多,在分类时一般按其组成的化学成分不同分为非水溶性(油基)液和水溶性(水基)液两大类两大类。
在高速切削时,油基切削液会因冷却效果差导致发热量大,使切削区的温度过高,是工件产生热变形,严重甚至导致烟雾、起火等现象。
以含极压添加剂的切削油为例,其一般使用在切削速度不超过60m/min的场合。
乳化液集成了优良的冷却性、润滑性与防锈性,适用于发热量的高速低压切削。
其使用加工范围广(可用于所有的轻、中等负荷的切削加工及多数重负荷加工),散热好,易清洗,经济性佳,使用安全、卫生。
但其也存在易变质、气味不佳的缺点,因此在使用时不得不加入少量杀菌剂,这也给机床操作人员的健康带来隐患。
化学合成切削液具备有与乳化油接近的的优点,而且比乳化油稳定性和抗腐败能力要强。
但化学合成留下的残留物容易使工件表面产生锈蚀。
不锈钢,在选用切削液时我们不但要考虑工件的材料还要考虑其加工形式和加工方法。
比如在粗加工时,以使用选用乳化液或极压乳化液和硫化油为主,而精加工时,选用极压切削油或浓度则要大得多,还会使用矿物油+黑机油或煤油+油酸+植物油的组合。
切削加工过程中切削液的加工性能研究

切削加工过程中切削液的加工性能研究摘要:切削液的加工性能是指切削液在切削加工过程中所表现出来的效能,它与切削加工效果直接相关。
这些效果包括加工质量、机床功率消耗、加工效率、切屑处理等几个方面。
本文对切削加工过程中切削液的加工性能进行研究。
摘要:切削加工;切削液;加工性能切削液的应用领域非常广泛,可以说,凡是有机械加工的地方都或多或少的使用切削液。
随着电子技术的高速发展,切削液已不再局限于金属材料的加工,如电视机的显像管、计算机的显示器等主要设备的生产、半导体单晶体工件切割等都需要切削液。
1.切削液的性能与作用1.1切削液的第一性能人们使用切削液的主要口的是希望起到润滑、冷却、清洗三方面作用。
一般称之为切削液的第一性能。
A.切削液的润滑作用切削液的润滑作用是指其减少前刀面与切屑、后刀面与已加工表面的摩擦,以防止刀具与切屑、工件间的粘着,所以良好的润滑可以减少功率消耗、刀具磨损和获得良好的表而光洁度。
B.冷却作用在切削过程中产生的热量使工件、刀具温度升高。
过高的温度可降低刀具的强度和硬度而使刀具寿命缩短,而且因热变形会影响工件的尺寸精度,同时也给工件的及时检测及拆卸带来不便,因此切削加工时必须进行有效的冷却。
切削液通过减小摩擦和带走热量可以有效地降低切削温度。
因切削过程的热量主要是塑性变形产生的,故降低温度主要靠冷却,不是靠减少摩擦。
切削液的冷却性能与其导热系数、比热、汽化潜热、粘度等因素有关。
水的比热较油约大一倍,汽化温度低,汽化潜热大,粘度小,因此其冷却性能比油好。
对油基切削液来说,粘度越小其流动性也越好,越容易将热量带走,所以冷却效果也越好。
C.清洗作用金属加工产生的细小切屑、粉末等会互相粘结或附着在机床、刀具(砂轮)、工件上。
清洗性能就是指切削液防止这些细颗粒粘结和利用液流的机械冲洗作用将其冲走的能力。
清洗性能与切削液的渗透性和粘度有密切关系,为了提高切削液的清洗性经常采用粘度较小的油或向水基切削液中加入较多的表面活性剂。
数控机床切削液的质量检测与评估方法
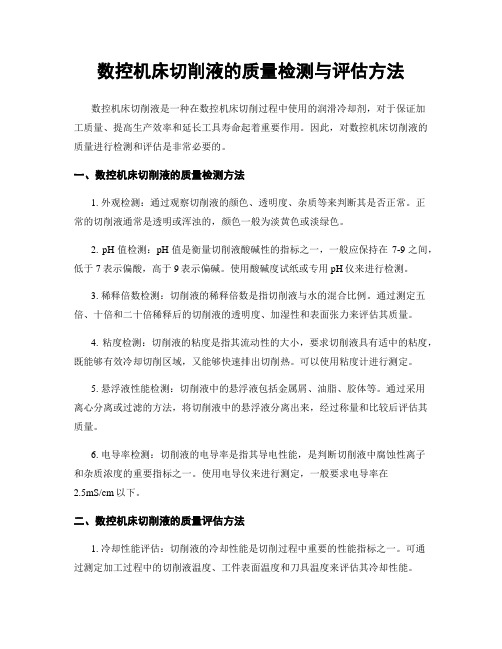
数控机床切削液的质量检测与评估方法数控机床切削液是一种在数控机床切削过程中使用的润滑冷却剂,对于保证加工质量、提高生产效率和延长工具寿命起着重要作用。
因此,对数控机床切削液的质量进行检测和评估是非常必要的。
一、数控机床切削液的质量检测方法1. 外观检测:通过观察切削液的颜色、透明度、杂质等来判断其是否正常。
正常的切削液通常是透明或浑浊的,颜色一般为淡黄色或淡绿色。
2. pH值检测:pH值是衡量切削液酸碱性的指标之一,一般应保持在7-9之间,低于7表示偏酸,高于9表示偏碱。
使用酸碱度试纸或专用pH仪来进行检测。
3. 稀释倍数检测:切削液的稀释倍数是指切削液与水的混合比例。
通过测定五倍、十倍和二十倍稀释后的切削液的透明度、加湿性和表面张力来评估其质量。
4. 粘度检测:切削液的粘度是指其流动性的大小,要求切削液具有适中的粘度,既能够有效冷却切削区域,又能够快速排出切削热。
可以使用粘度计进行测定。
5. 悬浮液性能检测:切削液中的悬浮液包括金属屑、油脂、胶体等。
通过采用离心分离或过滤的方法,将切削液中的悬浮液分离出来,经过称量和比较后评估其质量。
6. 电导率检测:切削液的电导率是指其导电性能,是判断切削液中腐蚀性离子和杂质浓度的重要指标之一。
使用电导仪来进行测定,一般要求电导率在2.5mS/cm以下。
二、数控机床切削液的质量评估方法1. 冷却性能评估:切削液的冷却性能是切削过程中重要的性能指标之一。
可通过测定加工过程中的切削液温度、工件表面温度和刀具温度来评估其冷却性能。
2. 润滑性能评估:切削液的润滑性能对机床切削过程中的摩擦和磨损起着重要作用。
可以通过测定摩擦系数和刀具磨损量来评估其润滑性能。
3. 抗菌性能评估:切削液中的细菌和真菌对切削液的质量和稳定性有一定的影响。
通过采用平皿计数法或培养法来评估切削液中的微生物数量,了解切削液的抗菌性能。
4. 稳定性评估:切削液的稳定性是指在切削过程中,切削液能够稳定地提供冷却和润滑功能。
机械加工切削液的性能研究
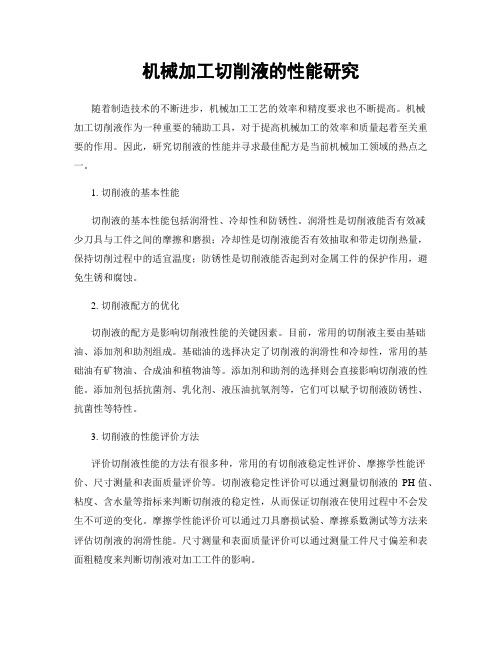
机械加工切削液的性能研究随着制造技术的不断进步,机械加工工艺的效率和精度要求也不断提高。
机械加工切削液作为一种重要的辅助工具,对于提高机械加工的效率和质量起着至关重要的作用。
因此,研究切削液的性能并寻求最佳配方是当前机械加工领域的热点之一。
1. 切削液的基本性能切削液的基本性能包括润滑性、冷却性和防锈性。
润滑性是切削液能否有效减少刀具与工件之间的摩擦和磨损;冷却性是切削液能否有效抽取和带走切削热量,保持切削过程中的适宜温度;防锈性是切削液能否起到对金属工件的保护作用,避免生锈和腐蚀。
2. 切削液配方的优化切削液的配方是影响切削液性能的关键因素。
目前,常用的切削液主要由基础油、添加剂和助剂组成。
基础油的选择决定了切削液的润滑性和冷却性,常用的基础油有矿物油、合成油和植物油等。
添加剂和助剂的选择则会直接影响切削液的性能。
添加剂包括抗菌剂、乳化剂、液压油抗氧剂等,它们可以赋予切削液防锈性、抗菌性等特性。
3. 切削液的性能评价方法评价切削液性能的方法有很多种,常用的有切削液稳定性评价、摩擦学性能评价、尺寸测量和表面质量评价等。
切削液稳定性评价可以通过测量切削液的PH值、粘度、含水量等指标来判断切削液的稳定性,从而保证切削液在使用过程中不会发生不可逆的变化。
摩擦学性能评价可以通过刀具磨损试验、摩擦系数测试等方法来评估切削液的润滑性能。
尺寸测量和表面质量评价可以通过测量工件尺寸偏差和表面粗糙度来判断切削液对加工工件的影响。
4. 切削液的优化应用和发展趋势随着机械加工技术的不断发展,对切削液的要求也在不断提高。
优化应用切削液可以提高切削效率、延长刀具寿命,减少机械加工过程中的磨损和能耗。
未来,随着环保要求的提高,切削液的绿色化和可再生性将成为发展的重点。
研发环保型的切削液,例如水基切削液和微量切削液已成为研究的热点。
总结:机械加工切削液的性能研究是一个综合性课题,涉及材料学、化学、机械学等多个学科的知识。
优化切削液配方和研究切削液的性能对于提高机械加工的效率和质量具有重要意义。
切削液ph值测量方法
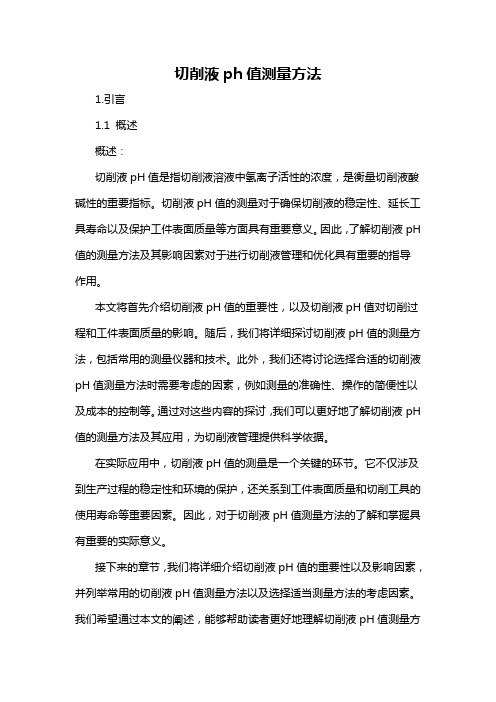
切削液ph值测量方法1.引言1.1 概述概述:切削液pH值是指切削液溶液中氢离子活性的浓度,是衡量切削液酸碱性的重要指标。
切削液pH值的测量对于确保切削液的稳定性、延长工具寿命以及保护工件表面质量等方面具有重要意义。
因此,了解切削液pH 值的测量方法及其影响因素对于进行切削液管理和优化具有重要的指导作用。
本文将首先介绍切削液pH值的重要性,以及切削液pH值对切削过程和工件表面质量的影响。
随后,我们将详细探讨切削液pH值的测量方法,包括常用的测量仪器和技术。
此外,我们还将讨论选择合适的切削液pH值测量方法时需要考虑的因素,例如测量的准确性、操作的简便性以及成本的控制等。
通过对这些内容的探讨,我们可以更好地了解切削液pH 值的测量方法及其应用,为切削液管理提供科学依据。
在实际应用中,切削液pH值的测量是一个关键的环节。
它不仅涉及到生产过程的稳定性和环境的保护,还关系到工件表面质量和切削工具的使用寿命等重要因素。
因此,对于切削液pH值测量方法的了解和掌握具有重要的实际意义。
接下来的章节,我们将详细介绍切削液pH值的重要性以及影响因素,并列举常用的切削液pH值测量方法以及选择适当测量方法的考虑因素。
我们希望通过本文的阐述,能够帮助读者更好地理解切削液pH值测量方法的原理和应用,为切削液管理提供科学的参考依据。
文章结构部分的内容应包括对整篇文章的组织和内容进行概括性介绍。
下面是1.2文章结构部分的内容示例:文章结构:本文主要分为引言、正文和结论三个部分。
引言部分首先概述了切削液pH值的测量方法的重要性和影响因素,并明确了本文的目的。
正文部分分为两个小节,分别介绍了切削液pH值的重要性和影响因素。
在重要性部分,将从提高切削液质量、提升生产效率和延长工具寿命等角度探讨切削液pH值的重要性。
在影响因素部分,将列举切削液成分、工艺参数和环境等因素对pH值的影响进行详细阐述。
结论部分首先介绍了常用的切削液pH值测量方法,包括酸碱指示纸、电子pH计和离子选择性电极等,然后进一步讨论了选择合适的切削液pH值测量方法时需要考虑的因素,包括准确性、便捷性和成本等。
切削液的质量检测4个要点

切削液的质量检测4个要点1、脂肪含量脂肪是切削液中的油性添加剂,是划分切削液类别的一个重要指标。
脂肪在切削液中可起到降低摩擦系数、减少刀具磨损的作用(对防止后刀面的磨损尤为有效)。
加有较多脂肪的切削液特别适合于有色金属加工以及切削量不大但产品精度及光洁度要求高的场合(如精车丝杠)。
一般可用皂化值来大致判定其脂肪含量。
切削油中脂肪含量过高或其质量控制不当,容易在机器上形成粘性物质造成机件运动不灵活,严重时会变成漆膜即所谓“穿黄袍”。
2、氯含量切削液中氯主要来自含氯的极压剂。
氯需要在较高含量(大于1%)时,方可显现出有效的极压作用。
如果氯含量不足1%,可以认为它不是为了提高润滑性。
一般含氯极压切削油其氯含量都在4%以上,最高时可达30%~40%。
但出于职业卫生及环保方面的考虑,有些国家已对切削油中氯的最高含量做了规定,如日本的JIS规定氯含量不得超过15%。
氯对不锈钢的加工以及在拉拔成型加工中都非常有效。
其缺点是不够稳定,遇水或温度过高时会分解产生HCl引起腐蚀、生锈。
3、硫含量切削油中硫来自两个方面。
一个是加入的含硫极压剂,另一个是来自其他没有极压作用的含硫化合物,如基础油中原有的天然硫化物以及防锈剂、抗氧剂等。
有效的硫只需很低含量(0.1%)即可产生明显的极压效果。
含硫极压剂对抑制积屑瘤特别有效,但可惜现在还没有简单的方法能分别测出有极压性的硫和没有极压性的硫。
所以很难仅仅依据其硫含量(特别是硫含量不高时)判断其极压性如何。
不过现在多数切削液制造厂家在其产品说明书中都标明加入的极压剂硫含量。
4、铜片腐蚀测定的方法是铜片法。
腐蚀活性的大小用级数表示,1~2级为低活性或非活性,3~4级为高活性。
级数越大,腐蚀活性越强。
铜对硫很敏感,用此法可以判断切削油中有没有含硫极压剂和极压剂的活性大小(注意:此法不能判断含硫剂的多少)。
此项目也是划分切削油类别的一个重要指标。
本文来自。
切削液的性能评定

切削液的性能评定要选择一个标准来判定切削液性能优劣是较困难的,而根据这个标准建立一个评价切削液效率的试验过程同样是一件难事。
这个问题从实验室转移到车间中会更复杂,但也可通过下述方法对切削液的性能作出评价。
刀具寿命评定采用刀具寿命评价切削液性能时,存在的主要问题是试验结果与工厂所测数据间的相关性常常很差。
因为对直刃刀具有效的切削液对成型刃刀具并不一定同样有效,反之亦然。
此外,切屑厚度对切削液的适应性也有影响。
若在同一特定加工条件下对几种切削液进行评价则要容易得多,因为通过测定刀具锐利度的变化值可得到刀具的平均寿命。
此评定即便简化了过程,但试验费用却很昂贵。
表面光洁度试验面光洁度试验不如刀具寿命试验复杂,可采用一根试验长棒,用同一刀具进行切削加工,通过表面粗糙度测量仪获得试验数据来评价切削液的性能优劣。
此评定试验,切削类型是很重要的。
如在平面铣削中,光洁的表面是由第二切削刃形成的,而在外圆铣削中,则是由主切削刃(轴向平行)形成新生面。
因而由一种加工方法获得的数据不能用于另一种加工的评定。
冷却性能评定采用某些专业技术测量切削液在实际加工中的冷却能力可判定其效率。
由于刀-屑界面的温度与刀具寿命有很好的相关性,因而刀具工作热电偶是一项非常有用的技术。
但其不足之处是不能区分温度降低是由于切削液的热传递还是由于加工中所产生热量少所致。
润滑效率评定切削液润滑效率的测定需采用一台机床刀具测力计。
在切削加工试验中,切削液的润滑作用降低了进刀力和切削力。
通过测定力的变化可计算切削液的润精效率。
切削力随进刀量的增加而增加,随切削液润滑效率的提高而降低。
若对刀具施加恒定的进刀力,则切削液的润滑效率越高,进刀量越大。
这套试验评定装置对刀屑之间的摩擦变化十分灵敏,但需一台设备以保证施加在切屑刀具上的进刀力恒定。
生理影响评价生理影响评价可通过操作人员来进行,如采用类似于过敏试验的医学研究技术进行皮肤刺激反应等。
操作人员的不同生理反应会影响到他对切削液的评价。
金属切削液的环境行为分析与评价
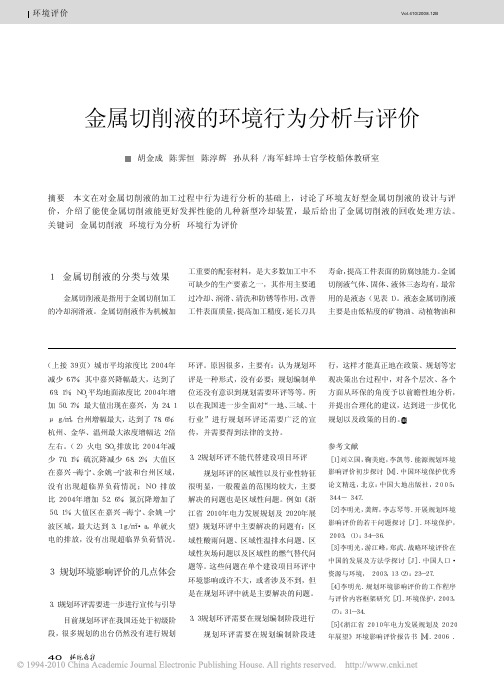
环境评价Vol.410/2008.12B40[1]刘立国,鞠美庭,李凯等.能源规划环境影响评价初步探讨[M].中国环境保护优秀论文精选,北京:中国大地出版社,2005:344-347.[2]李明光,龚辉,李志琴等.开展规划环境影响评价的若干问题探讨[J].环境保护,2003,(1):34-36.[3]李明光,游江峰,郑武.战略环境评价在中国的发展及方法学探讨[J].中国人口・资源与环境, 2003,13(2):23-27.[4]李明光.规划环境影响评价的工作程序与评价内容框架研究[J].环境保护,2003,(7):31-34.[5]《浙江省2010年电力发展规划及2020年展望》环境影响评价报告书[M].2006 .工重要的配套材料,是大多数加工中不可缺少的生产要素之一,其作用主要通过冷却、润滑、清洗和防锈等作用,改善工件表面质量,提高加工精度,延长刀具寿命,提高工件表面的防腐蚀能力。
金属切削液气体、固体、液体三态均有,最常用的是液态(见表1)。
液态金属切削液主要是由低粘度的矿物油、动植物油和EN V IRONMEN TAL A S SE SS M E N TVol.410/2008.12B41ÆäËû»¯ºÏÎï×é³É£¬ËùÒÔ½ðÊôÇÐÏ÷Òº¸»º¬Áò¡¢ÂÈ¡¢Áס¢ÃÌ¡¢¹è¼°°±Ö¬ËáµÈÎï¡£Ëæ×ŶԽðÊôÇÐÏ÷ÖÊÁ¿ÒªÇóµÄÌá¸ß£¬ÇÐÏ÷ÒºµÄ³É·ÖÔ½À´Ô½¸´ÔÓ£¬Ò²Ô½À´Ô½×¨Óû¯¡£ÇÐÏ÷ÒºÓÉÓÚÆäÖØÒª×÷Óã¬ÔÚ»úе¼Ó¹¤Öеõ½Á˹㷺ӦÓ㬵«Ëæ×Ź«ÖÚ»·¾³ÒâʶµÄÔöÇ¿¼°»·±£·¨ÂÉ·¨¹æÔ½À´Ô½ÑϸñµÄÒªÇó£¬ÇÐÏ÷ÒºµÄ¸ºÃæÐ§Ó¦Óú¼ÓÃ÷ÏÔ¡£Ö÷Òª±íÏÖÔÚÒÔϼ¸¸ö·½Ã棺¢Ù¼Ó¹¤¹ý³ÌÖвúÉúµÄ¸ßÎÂʹÇÐÏ÷ÒºÐγÉÎí×´»Ó·¢£¬ÇÐÏ÷ÒºÖеÄÌí¼Ó¼Á¼Ó£¨Áò¡¢Âȵȣ©ÓÐËð²Ù×÷Õß½¡¿µ²¢Ó°Ïì¼Ó¹¤ÖÊÁ¿£»¢ÚijЩÇÐÏ÷Òº¼°Õ³´ø¸ÃÇÐÏ÷ÒºµÄÇÐм±ØÐë×÷ΪÓж¾ÎïÖÊ´¦Àí£¬¼ÈÎÛȾ»·¾³£¬´¦Àí·ÑÓÃÓֺܸߣ»¢ÛÇÐÏ÷ÒºµÄÉøÂ©¡¢Òç³öÓ°Ï찲ȫÉú²ú£»¢ÜÓùýµÄÇÐÏ÷Òºº¬ÓдóÁ¿º¬ÓÍ·ÏÎÅÅ·Å»áÎÛȾ»·¾³£»¢ÝÇÐÏ÷ÒºµÄ´¦Àí¡¢Ñ-»·¡¢±ÃÎüºÍ¹ýÂËʹ¼Ó¹¤ÏµÍ³¸´ÔÓ£¬Ôö¼ÓÁË»úеÉ豸³É±¾£»¢ÞÇÐÏ÷ÒºµÄʹÓÃÓÐʱ¶Ôµ¶¾ß»á´øÀ´²»Á¼µÄÓ°Ï죬±ÈÈçµ¼Öµ¶¾ßÈÈÁÑ£¬Ôö´óµ¶¾ßÊÜÁ¦£¬½µµÍÊÙÃü£»¢ßĿǰÇÐÏ÷ÒºÖÖÀà·±¶à£¬¹ÜÀí²»±ã£¬Ñ¡ÓÃ¶àÆ¾¾-Ñ飬ȱ·¦¿ÆÑ§µÄ·½·¨¡£2 金属切削液的环境行为分析防止公害、环境污染及劳动灾害,以确保安全和健康的问题已经引起全球、全社会极大地关注,相应制定了许多国际性或国家级的有关法律法规。
机床切削液的理化性能与评价方法概述
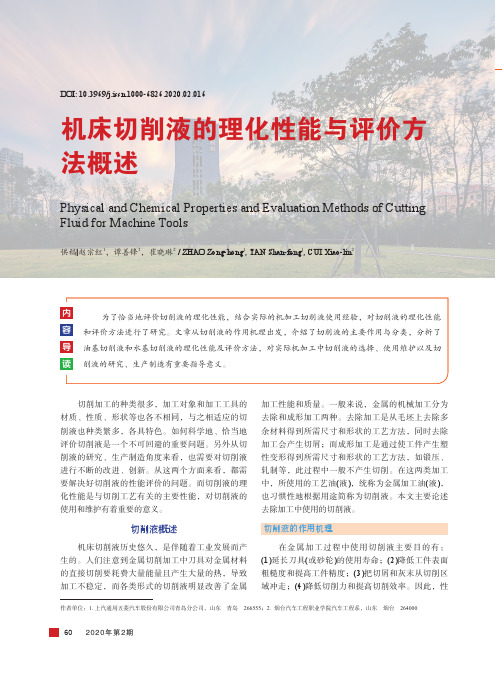
机床切削液的理化性能与评价方法概述Physical and Chemical Properties and Evaluation Methods of Cutting Fluid for Machine Tools供稿|赵宗红1,谭善锋1,崔晓琳2 / ZHAO Zong-hong1, TAN Shan-feng1, CUI Xiao-lin2DOI: 10.3969/j.issn.1000-6826.2020.02.016切削加工的种类很多,加工对象和加工工具的材质、性质、形状等也各不相同,与之相适应的切削液也种类繁多,各具特色。
如何科学地、恰当地评价切削液是一个不可回避的重要问题。
另外从切削液的研究、生产制造角度来看,也需要对切削液进行不断的改进、创新。
从这两个方面来看,都需要解决好切削液的性能评价的问题。
而切削液的理化性能是与切削工艺有关的主要性能,对切削液的使用和维护有着重要的意义。
切削液概述机床切削液历史悠久,是伴随着工业发展而产生的。
人们注意到金属切削加工中刀具对金属材料的直接切削要耗费大量能量且产生大量的热,导致加工不稳定,而各类形式的切削液明显改善了金属加工性能和质量。
一般来说,金属的机械加工分为去除和成形加工两种。
去除加工是从毛坯上去除多余材料得到所需尺寸和形状的工艺方法,同时去除加工会产生切屑;而成形加工是通过使工件产生塑性变形得到所需尺寸和形状的工艺方法,如锻压、轧制等,此过程中一般不产生切削。
在这两类加工中,所使用的工艺油(液),统称为金属加工油(液),也习惯性地根据用途简称为切削液。
本文主要论述去除加工中使用的切削液。
切削液的作用机理在金属加工过程中使用切削液主要目的有:(1)延长刀具(或砂轮)的使用寿命;(2)降低工件表面粗糙度和提高工件精度;(3)把切屑和灰末从切削区域冲走;(4)降低切削力和提高切削效率。
因此,性作者单位:1. 上汽通用五菱汽车股份有限公司青岛分公司,山东青岛 266555;2. 烟台汽车工程职业学院汽车工程系,山东烟台 264000工艺与装备Apparatus and Equipments金属加工能良好的切削液必须具有润滑、冷却、清洗和防锈等作用。
机械制造过程中切削液润滑剂性能测试与优化
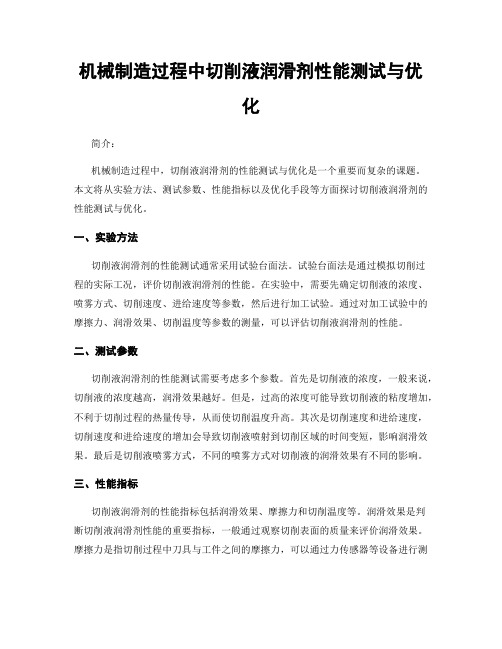
机械制造过程中切削液润滑剂性能测试与优化简介:机械制造过程中,切削液润滑剂的性能测试与优化是一个重要而复杂的课题。
本文将从实验方法、测试参数、性能指标以及优化手段等方面探讨切削液润滑剂的性能测试与优化。
一、实验方法切削液润滑剂的性能测试通常采用试验台面法。
试验台面法是通过模拟切削过程的实际工况,评价切削液润滑剂的性能。
在实验中,需要先确定切削液的浓度、喷雾方式、切削速度、进给速度等参数,然后进行加工试验。
通过对加工试验中的摩擦力、润滑效果、切削温度等参数的测量,可以评估切削液润滑剂的性能。
二、测试参数切削液润滑剂的性能测试需要考虑多个参数。
首先是切削液的浓度,一般来说,切削液的浓度越高,润滑效果越好。
但是,过高的浓度可能导致切削液的粘度增加,不利于切削过程的热量传导,从而使切削温度升高。
其次是切削速度和进给速度,切削速度和进给速度的增加会导致切削液喷射到切削区域的时间变短,影响润滑效果。
最后是切削液喷雾方式,不同的喷雾方式对切削液的润滑效果有不同的影响。
三、性能指标切削液润滑剂的性能指标包括润滑效果、摩擦力和切削温度等。
润滑效果是判断切削液润滑剂性能的重要指标,一般通过观察切削表面的质量来评价润滑效果。
摩擦力是指切削过程中刀具与工件之间的摩擦力,可以通过力传感器等设备进行测量。
切削温度是切削过程中产生的热量,过高的切削温度会导致刀具退火、变形,从而降低加工质量。
四、优化手段为了提高切削液润滑剂的性能,可以采取以下优化手段。
首先是优化切削液的配方,根据工件的材料和加工要求,选择合适的添加剂,以增强切削液的抗热性、防锈性和润滑性。
其次是优化切削液的供给方式,如调整喷雾方式和润滑剂的浓度,以提高润滑效果。
此外,还可以采取节能减排措施,如优化切削参数,减小切削力、切削温度和损耗,从而降低能耗和环境影响。
结论:切削液润滑剂的性能测试与优化是机械制造过程中的重要问题。
通过实验方法、测试参数、性能指标和优化手段等方面的研究,可以不断提高切削液润滑剂的性能,提高加工质量和效率。
磨削液性能评价试验方法研究
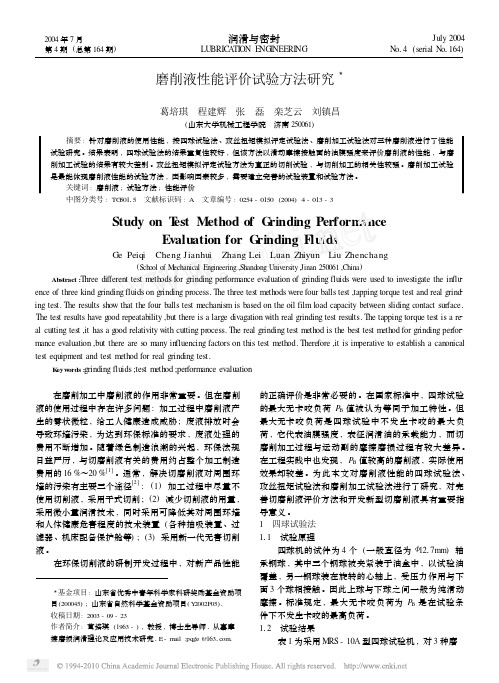
盘 ,扭矩盘与扭矩传感器联接 ,测定攻丝扭矩 。 212 试验结果
本文采用 MRG - 005 型金属加工液攻丝扭矩模拟 评定试验机 ,对上述三种不同磨削液按标准试验方法 进行了试验研究 ,试验结果如表 2 所示 。本试验是按 攻丝切削加工 ,主轴转速为 243r/ min ,数据采集系统的 启动扭矩为 015N·m ,螺母试件材料为 20Cr ,丝锥为关 中产 4 # 。
关键词 : 磨削液 ; 试验方法 ; 性能评价 中图分类号 : TG50115 文献标识码 : A 文章编号 : 0254 - 0150 (2004) 4 - 013 - 3
Study on Test Method of Grinding Performance
Evaluation for Grinding Fluids
15
但与磨削加工试验的结果却有较大差别 。在磨削加工 试验中 , HB - 1 磨削液在磨削力 、表面粗糙度方面表 现的都较好 。
攻丝扭矩 模 拟 评 定 试 验 方 法 比 四 球 试 验 方 法 要 复杂一些 。为了消除不同丝锥的影响 , 需首先使用标 准液校验丝锥 , 选出一批性能非常相近的丝锥 , 并视 其为同一丝锥 , 然后对不同磨削液进行攻丝试验 。因 这种试验方法为真正的切削试验 , 若磨削液性能较 差 , 丝锥的切削刃上很快即产生积屑瘤 , 这对试验结 果的影响较大 , 因此需严格控制试验条件 , 否则试验 结果的重复性就不可能很好 。而且该试验方法是以攻 丝加工为对象 , 没有考虑具体的加工工艺要求 , 在评 价磨削液性能时存在一定偏差 。在试验结果上 , 虽与 四球试验的 PB 值在趋势上一致 , 但在数值量差上二 者还是有区别的 。
触面的油膜承载强度来评价磨削液的性能 , 而滑动摩
如何辨别切削液的质量

1、注意生产日期:切削液的出厂日期不宜过长,一般应选择保存期不超过一年,保存期在一年以上的切削液应经检验合格后方可使用。
2、看外观:不同类型的切削液有不同的颜色,但无论是什么颜色的都应是黏稠均一。
如果颜色深浅不一或表皮硬化,表层出现较多的浮油或稠度明显变小,或由于混入水分而使其表面乳化变白等,这些现象均表明切削液已变质,不可使用。
3、闻气味:如果打开包装时闻到明显的酸味、臭味,表明切削液已变质,不可使用。
4、手捻:用手捻不含填充剂的切削液时,手感光滑,没有硌手感;否则,则可能是稠化剂
分散不均匀或混入杂质,这种不可使用,但含填充剂粉末的切削液略有硌手感。
5、用火烧:用铁丝挑起一块切削液,然后用打火机烧,如果切削液软化滴落,表明是滴点
过低的劣质切削液,不可使用。
需要说明的是,用这种方法只能鉴别滴点过低的劣质切削液,因打火机火焰的温度不超过120~130℃,而大多数切削液的滴点都超过了这个温度,用打火
机烧都不会滴落。
6、在阳光下晒:取一块切削液放在杯中在阳光下晒一两天,如果脂体变化大,出现分油或变色,表明脂的性能不稳定。
金属切削液的各种检测

泡沫的检测
实验条件:5%溶液,常温,振荡30次
润滑性能——四球摩擦机
腐蚀性检测
Blank
Blank
Like Product
Like Product
PE 533
PE 533
PE 1198LA
DI-Water
Tap-Water
DI-Water
Tap-Water
DI-Water
Tap-Water
DI-Water
金属切削液各种检测
陆由东
2012-12-10
切削液的各种检测和比较
1、折光值——糖量仪(折光仪)
pH值的测定
防锈性能的检测
实验过程:把打磨好的试片浸泡5%的稀释液,1分钟后取出悬挂于恒温 恒湿
箱中(35℃,90±2%rh ),2小时取出观察结果。
细菌含量的检测
亚硝酸盐的检测
水质检测
切削液在硬水中析皂
实验条件:打磨后的铜或者铝片,5%溶液,60℃水浴,浸
泡8小时以上,观察试片的变色情况。
PE 1198LA Tap-Water
高低温稳定性
Good Luck !
谢谢!
- 1、下载文档前请自行甄别文档内容的完整性,平台不提供额外的编辑、内容补充、找答案等附加服务。
- 2、"仅部分预览"的文档,不可在线预览部分如存在完整性等问题,可反馈申请退款(可完整预览的文档不适用该条件!)。
- 3、如文档侵犯您的权益,请联系客服反馈,我们会尽快为您处理(人工客服工作时间:9:00-18:30)。
切削液性能的评定方法
过去对切削液润滑性能的评定,一般采用四球机测定最大无卡咬负荷(PB 值)。
近年来已逐渐采用切削机床进行切削试验来评定切削液的使用性能。
这种方法是在工件、刀具、切削条件、供液法等全部保持在相同的条件下,仅改变切削液,根据不同的切削液所测定的刀具寿命、加工试件表面粗糙度、尺寸精度、切削力、攻螺纹扭矩等切削特征值来判断切削液的优劣。
评定切削液的条件和主要参数
1)加工方法(车削、铣削、钻削、攻螺纹)。
2)工件(材料、硬度、热处理状态、形状)。
3)刀具(种类、材料、形状、表面处理、生产厂)。
4)机床(制造厂商、种类、型号、刚度)。
5)同剂条件(切削速度、进给量、切削深度)。
6)供液方式及供液量。
7)切润液(种类、稀释率)
评定切削液性能的项目
1)刀具寿命(刀具磨损量、加工零件数)。
2)加工试件表面粗糙度。
3)精度(尺寸精度、圆度、圆柱度、扩大量等)。
4)切削力、攻螺纹扭矩、
5)切削温度。
6)其他(刀-屑接触长度、切屑厚度等)。
评定磨削液的条件和参数
1)加工方法(平面磨床、外圆磨床、内圆磨床)
2)适用机床(制造厂商、磨料种类、粒度、硬度、组织、结合剂、形状及尺寸)。
3)工件(材料、硬度、热处理状态、形状)
4)砂轮(制造厂商、磨料种类、粒度、硬度、组织、结合剂、形状及尺寸)。
5)磨削条件(磨削速度、进给量、磨削深度)。
6)修整条件(修整器种类、修整速度、修整深度、修整进给量、修整数)。
7)供液方式及供液量。
8)磨削液(种类、稀释倍数)。
评定磨削液性能的项目
1)砂轮寿命(砂轮磨损量、砂轮的磨损状态等)。
2)磨削力。
3)试件表面粗糙度及尺寸精度。
4)工件表面状态(磨削烧伤、磨削裂纹、加工变质层、残余应力)。
5)磨削温度。
6)磨削比。
磨削比的计算如下:
磨削比=工件磨除量/砂轮磨损量
砂轮磨损量=砂轮半径减少量x砂轮直径xπx工件宽度
工件磨除量=(磨前工件高度-磨后工件高度)x 工件长度x工件宽度。