压铸世界·2009年第04期
各类压铸缺陷及其原因解析
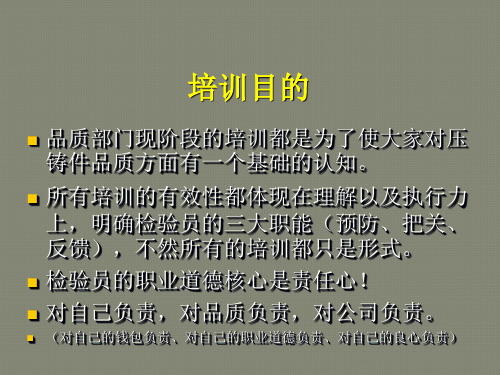
复杂 检验手段:目测
积碳:
特征:涂料经过高温形 成的氧化物粘附在模具 上,铸件表面发白且粗 糙的表面。
原因:
1.涂料喷涂过多 2.涂料过浓 3.模温偏低 4.未及时抛光去除 检验手段:喷漆、目测
粘模:
特征:铸件出现因模具上粘 附多余材料而形成的合金未 能填充现象
原因:
1.多余材料粘附在模具上 2.模具表面粗糙 3.模温太高 4.拔模斜度小 5.浇注速度快、填充模式不
正确
检验手段:目测、去毛刺观 察
拉伤:
特征:由于金属粘附在 模具表面出现的铸件表 面拉伤痕迹
原因:
1.拔模斜度小 2.铸件顶出偏斜 3.模具表面粗糙 4.涂料喷涂不到位 5.合金粘附模具表面 检验手段:目测、喷漆
培训目的
品质部门现阶段的培训都是为了使大家对压 铸件品质方面有一个基础的认知。
所有培训的有效性都体现在理解以及执行力 上,明确检验员的三大职能(预防、把关、 反馈),不然所有的培训都只是形式。
检验员的职业道德核心是责任心! 对自己负责,对品质负责,对公司负责。
(对自己的钱包负责、对自己的职业道德负责、对自己的良心负责)
4.模具温度较低 检验手段:抛光
麻面:
特征:表面细小麻点分布 区域
原因:
1.模温太低、料温太低 2.填充金属分散成密集
滴液,高速撞击型壁
3.内浇口厚度偏小 检验手段:目测、喷漆
冲刷:
特征:浇口附近出现的较大 面积凸起物
原因: 1.模具刚性不够 2.模具老化 3.浇注速度过高 4.料温过高、预热不够 5.未定期热处理 检验手段:目测、打磨后观察
压铸的过程及原理介绍

压铸的过程及原理介绍压铸的过程及原理介绍∙浅谈压力铸造特点及优势∙发布时间:2021-10-21 15:32:27 来源:互联网文字【大中小】浏览人数:226 【收藏】∙内容摘要: 压力铸造(简称压铸) 是在压铸机的压室内,浇入液态或半液态的金属或合金,使它在高压和高速下充填型腔,并且在高压下成型和结晶而获得铸件的一种铸造方法。
1. 压铸定义及特点压力铸造(简称压铸) 是在压铸机的压室内,浇入液态或半液态的金属或合金,使它在高压和高速下充填型腔,并且在高压下成型和结晶而获得铸件的一种铸造方法。
由于金属液受到很高比压的作用,因而流速很高,充型时间极短。
高压力和高速度是压铸时液体金属充填成型过程的两大特点,也是压铸与其他铸造方法最根本区别之所在。
比如压射比压在几兆帕至几十兆帕范围内,甚至高达500MPa; 充填速度为0.5—120m/s,充型时间很短,一般为0.01-0.2s ,最短只有干分之几秒。
2. 压铸的优缺点1) 产品质量好。
由于压铸型导热快,金属冷却迅速,同时在压力下结晶,铸件具有细的晶粒组织,表面坚实,提高了铸件的强度和硬度,此外铸件尺寸稳定,互换性好,可生产出薄壁复杂零件;2) 生产率高,压铸模使用次数多;3) 经济效益良好。
压铸件的加工余量小,一般只需精加工和铰孔便可使用,从而节省了大量的原材料、加工设备及工时。
1) 压铸型结构复杂,制造费用高,准备周期长,所以,只适用于定型产品的大量生产;2) 压铸速度高,型腔中的气体很难完全排出,加之金属型在型中凝固快,实际上不可能补缩,致使铸件容易产生细小的气孔和缩松,铸件壁越厚,这种缺陷越严重,因此,压铸一般只适合于壁厚在6mm 以下的铸件;3) 压铸件的塑性低,不宜在冲击载荷及有震动的情况下工作;4) 另外,高熔点合金压铸时,铸型寿命低,影响压铸生产的扩大应用。
综上所述,压力铸造适用于有色合金,小型、薄壁、复杂铸件的生产,考虑到压铸其它技术上的优点,铸件需要量为2000-3000件时,即可考虑采用压铸。
2009年全球铸件生产统计报告——全球铸件市场在2009年经历严重动荡,总产量相比2008年跌幅14%

20 0 8年 铸 件 产 量 持 续 增 长 的 国 家 中 ,从 20 0 8年 到 20 0 9年 同期 所 有 位列 前 十名 的 围家 中铸 件 产 量减 少
最多 的 国家之 ~ , 幅率 达 到 3 .%。印度 是这 1 跌 1 5 0个
国家 中铸件 产量 增长 速度最 快 的 国家 , 幅达 9 增 %。位 列前 茅 的这 十 个 国家 共 生 产 约 74 . 076 4万 t 件 , 铸 占
全球 铸件总 产量 的 8 %。 8 在全球 铸件 产量 排 行榜 上 ,0 9年 美 国 已经 是连 20 续 第 四个年头 减产 。 同时 , 也是 印度第 一次 铸件产 量 这
除少数 几个 国家外 , 全球 铸 造 行 业 铸 件 产 量 在
2 0 都有不 同程度下 降 , 些 国家 表现 得尤 为 明显 。 0 9年 某
的数 据对 比。 中灰 铁件 的产量 依 旧位列 第一位 , 到 其 达
后 于 印度 和 日本 , 20 其 铸件生 产 企业 又减 少 了 在 09年
3 0家 。 0
3 1 万 t占铸件 总产 量 的 4 %。 19 86 , 7 从 9 9年至今 , 比 相
较有 3. 96 %增 长 的球 铁件 ,0 5 %涨 幅 的铸 钢件 , 以及 产
进 行 了七年来 的首 次更 新 。
捷 克 共 和 国 :0 9年捷 克 铸 件 产 量 从 5 .8万 t 20 3 6 下降 到 2.9万 t 70 ,降 幅 4 .%。铸件 生 产 率从 2 8t 95 64/
工 厂降 为 1 0 t 5 5/ T厂 从 2 0 开始 ,欧洲 铸件 总 产量 下 降 3 . 北 0 8年 1 %。 5 美铸件减产 2. 8 %。亚7J 部和最南部地区的铸件生 5 7 I ,; , 1 1
压铸的原理特点及应用

压铸的原理特点及应用一、原理•压铸是一种常用的金属成形工艺,通过将熔化金属注入压力室,利用高压将金属充填到模具腔内,经过冷却固化后,得到所需形状的铸件。
•压铸主要基于物质流体力学原理,实现了金属在短时间内快速凝固,能够制造出精度高、表面光洁的铸件。
二、特点1.高产量和高精度:压铸采用模具进行生产,可以实现长时间连续生产,保证产量和质量的稳定。
并且压铸工艺具有较高的尺寸精度和表面光洁度,适用于制造复杂形状和精度要求高的铸件。
2.材料适应性强:压铸可以应用于多种金属材料和合金,包括铝合金、锌合金、镁合金等,可以满足不同行业的需求。
3.内部缺陷少:压铸工艺中金属熔液在高压下充填模腔,填充过程较快,可以有效减少气体和杂质的残留,从而减少内部缺陷,提高铸件的强度和耐腐蚀性能。
4.节约材料和能源:由于压铸采用精确的模具和高压填充,可以最大限度地减少材料的浪费,提高材料利用率。
同时,由于快速凝固,也节约了能源。
三、应用1.汽车工业:汽车行业对高精度、高强度的零部件需求多,压铸工艺可以满足这些需求,如汽车发动机缸体、曲轴箱、变速器壳等。
2.家电工业:压铸工艺广泛应用于家电工业,如电视机壳、冰箱门、洗衣机滚筒等,能够满足外观要求、减轻重量,并提升产品的质感。
3.电子工业:压铸工艺适用于制造电子设备的外壳,如手机壳、计算机外壳等,同时还可以提供电磁屏蔽、散热等功能。
4.航空航天:航空航天领域对零部件质量和性能要求极高,压铸能够制造轻量化、高强度的零部件,如飞机发动机部件、导弹外壳等。
5.其他领域:压铸还广泛应用于军事、医疗、通讯等领域,满足各种精密铸件的需求。
四、结论压铸工艺以其高产量、高精度和材料适应性强等特点,在各个工业领域有着广泛的应用。
随着科技的发展和工艺的不断改进,压铸技术将会进一步提高铸件质量和生产效率,为各行业的发展做出更大的贡献。
压铸基本概念教学课件
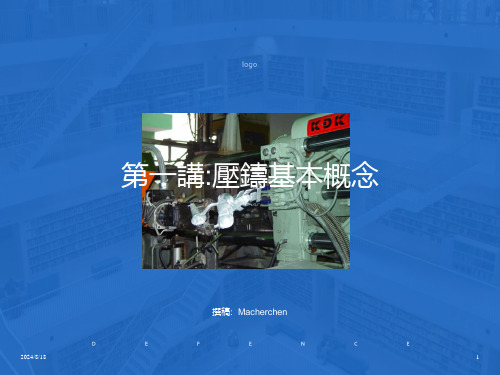
壁厚
四.成型工藝
*
鋅合金: 0.3MM (最小) 鋁﹕0.5MM
最大壁厚與最小壁厚之比不要大于3﹕1(應設計壁厚均勻﹐保証足夠強度與剛度的前提)
最小孔徑: 0.7MM 螺紋螺距﹕0.75MM
*
四.成型工藝
*
加強肋﹕大于或等于2.5MM﹐會降低抗拉強度﹐易產生氣孔﹐縮孔。 設計原則﹕1﹐受力大﹐減小壁厚﹐改善強度. 2﹐對稱布置﹐壁厚均勻﹐避免縮孔氣孔. 3﹐與料流方向一致﹐避免亂流. 4﹐避免在肋上設置任何零部件.
*
熱室壓鑄鋅合金中的合金元素
五.壓鑄合金及其性能
*
03
嚴格控制壓鑄溫度,避免攪拌
02
熱室壓鑄用鋅合金必須是以特高純度鋅為基礎,加入特高純度鋁,鎂和銅
01
---結論
04
水口料重熔時,一定要嚴格控制重熔溫度以避免鋁和鎂的損耗
*
六.壓鑄工藝
時間t
影響金屬液充填成型的因素很多﹐主要有﹕壓射壓力﹐壓射速度﹐充填時間﹐壓鑄模溫。 (一)壓射壓力的概念 定義1﹕壓射力指壓射沖頭作用于金屬液面上的力。 (這個力在壓鑄過程中不是恆定不變的,它大小隨不同的壓鑄階段變化而改變.) 壓射液壓缸 壓射沖頭 壓室熔液 模具型腔 t1:F1為克服磨擦力(壓室中) t2:開始進入型腔﹐因澆口急減﹐阻力 增大﹐F2>F1,達到高速充填 t3:(快速增壓階段)快速充填直止充滿 型腔最大值F3為壓射壓力 t4:F4靜壓力﹐對鑄件壓實 (壓射力與時間關係曲線見右圖)
*
熱室壓鑄鋅合金中的合金元素
五.壓鑄合金及其性能
*
---合金元素-銅
01
銅的加入可
02
增加合金的強度
03
提高合金的硬度
压铸操作工艺培训讲义(连载四)

压铸操作工艺培训讲义(连载四)五、国内外压铸铝合金1、国标牌号标注方法在国标中压铸铝合金的代号是用字母“YL”和其后的数字表示,“Y”及“L”分别为“压”、“铝”两字汉语拼音的第一个字母。
2、国内外主要压铸铝合金化学成分和力学性能如下表:压铸铝合金国家标准:压铸铝合金日本标准:压铸铝合金欧盟标准:压铸铝合金美国标准:3、合金中各元素的主要作用4、各元素对合金的影响①铝合金中硅的作用有两点,第一是增加流动性,但这点主要是对重力铸造等很低压强下的充填而言。
检测与实践都表明,不加硅的铝合金和加了硅的合金在超过1MPa的充型压强下,充型性能差异不大,而现在压铸生产中压射充型压强均达到30MPa以上,即使流动性最差的合金、如变形铝合金及变形镁合金,都不存在充型不足的困难。
第二点,也是铝合金中硅作用的最重要的一点,也是大家最容易忽略的一点。
硅的作用是减少“液-固”相的相变体积收缩率。
特别是高硅铝合金,当硅含量达到20%左右时如B390,ADC14铝合金,相变体积可以保持不变。
由于铝合金压铸属于单方向的高压强充型铸造,不具备有反向补缩作用。
正是这个原因压铸行业才特意配制相变收缩率比较低,含硅量高的铝合金牌号。
②硅含量的降低,压铸件毛坯在同样的压铸条件下,缩孔、疏松现象严重,合格率明显降低。
主要原因是硅含量的降低导致铝合金体积收缩率较大。
③硅及铜含量的降低,产品的机械强度降低,热裂倾向增加。
合金的延伸率增强,变得更软。
顶出时易变形甚至开裂。
一方面通过Mg和Mn 含量的配比提高机械强度,并在压铸工艺参数设定时,调整冷却时间、顶出速度及顶出力及脱模剂的喷涂,解决产品顶出时的变形及开裂的缺陷。
④元素Mn的作用,锰能阻止铝合金的再结晶过程,提高再结晶温度并能显著细化结晶晶粒。
再结晶的细化,主要是通过MnAl6化合物弥散质点对再结晶粒长大起阻碍作用。
过多的MnAl6能溶解杂质铁形成(Fe,Mn)Al6减少铁的有害影响。
故锰的含量也不能太高,控制在0.30-0.40%范围内。
压铸常识知识点范文
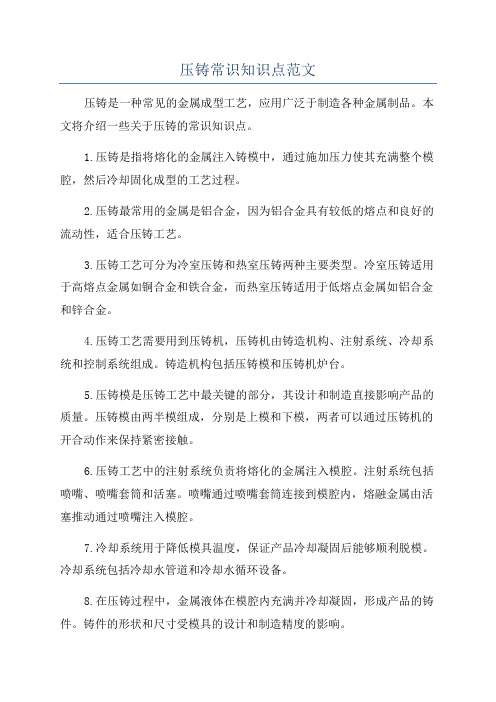
压铸常识知识点范文压铸是一种常见的金属成型工艺,应用广泛于制造各种金属制品。
本文将介绍一些关于压铸的常识知识点。
1.压铸是指将熔化的金属注入铸模中,通过施加压力使其充满整个模腔,然后冷却固化成型的工艺过程。
2.压铸最常用的金属是铝合金,因为铝合金具有较低的熔点和良好的流动性,适合压铸工艺。
3.压铸工艺可分为冷室压铸和热室压铸两种主要类型。
冷室压铸适用于高熔点金属如铜合金和铁合金,而热室压铸适用于低熔点金属如铝合金和锌合金。
4.压铸工艺需要用到压铸机,压铸机由铸造机构、注射系统、冷却系统和控制系统组成。
铸造机构包括压铸模和压铸机炉台。
5.压铸模是压铸工艺中最关键的部分,其设计和制造直接影响产品的质量。
压铸模由两半模组成,分别是上模和下模,两者可以通过压铸机的开合动作来保持紧密接触。
6.压铸工艺中的注射系统负责将熔化的金属注入模腔。
注射系统包括喷嘴、喷嘴套筒和活塞。
喷嘴通过喷嘴套筒连接到模腔内,熔融金属由活塞推动通过喷嘴注入模腔。
7.冷却系统用于降低模具温度,保证产品冷却凝固后能够顺利脱模。
冷却系统包括冷却水管道和冷却水循环设备。
8.在压铸过程中,金属液体在模腔内充满并冷却凝固,形成产品的铸件。
铸件的形状和尺寸受模具的设计和制造精度的影响。
9.压铸工艺可以实现高产量和高精度的制造。
通过合理调整压力和温度等工艺参数,可以获得不同材料和形状的铸件。
10.压铸工艺常用于制造汽车零件、家电产品、工业设备和通信设备等各种金属制品。
压铸工艺具有成本低、质量稳定、生产效率高的优势。
总之,压铸是一种重要的金属成型工艺,具有广泛的应用前景。
了解压铸工艺的基本知识,有助于正确选择和应用该工艺,提高产品的质量和生产效率。
2009中外压铸技术交流会在苏州召开
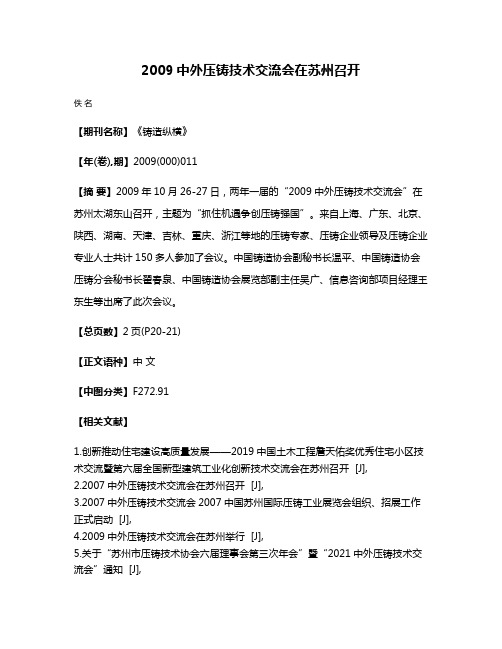
2009中外压铸技术交流会在苏州召开
佚名
【期刊名称】《铸造纵横》
【年(卷),期】2009(000)011
【摘要】2009年10月26-27日,两年一届的“2009中外压铸技术交流会”在苏州太湖东山召开,主题为“抓住机遇争创压铸强国”。
来自上海、广东、北京、陕西、湖南、天津、吉林、重庆、浙江等地的压铸专家、压铸企业领导及压铸企业专业人士共计150多人参加了会议。
中国铸造协会副秘书长温平、中国铸造协会压铸分会秘书长翟春泉、中国铸造协会展览部副主任吴广、信息咨询部项目经理王东生等出席了此次会议。
【总页数】2页(P20-21)
【正文语种】中文
【中图分类】F272.91
【相关文献】
1.创新推动住宅建设高质量发展——2019中国土木工程詹天佑奖优秀住宅小区技术交流暨第六届全国新型建筑工业化创新技术交流会在苏州召开 [J],
2.2007中外压铸技术交流会在苏州召开 [J],
3.2007中外压铸技术交流会2007中国苏州国际压铸工业展览会组织、招展工作正式启动 [J],
4.2009中外压铸技术交流会在苏州举行 [J],
5.关于“苏州市压铸技术协会六届理事会第三次年会”暨“2021中外压铸技术交流会”通知 [J],
因版权原因,仅展示原文概要,查看原文内容请购买。
压铸世界·2010年第02期
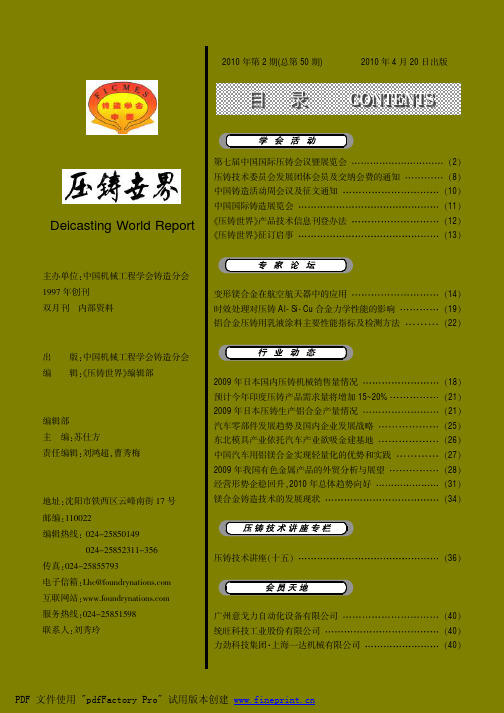
Deicasting World Report 主办单位:中国机械工程学会铸造分会1997年创刊双月刊内部资料出版:中国机械工程学会铸造分会编辑:《压铸世界》编辑部编辑部主编:苏仕方责任编辑:刘鸿超,曹秀梅地址:沈阳市铁西区云峰南街17号邮编:110022编辑热线:024-********024-********-356传真:024-********电子信箱:Lhc@互联网站:服务热线:024-********联系人:刘秀玲2010年第2期(总第50期)2010年4月20日出版第七届中国国际压铸会议暨展览会(2)压铸技术委员会发展团体会员及交纳会费的通知(8)中国铸造活动周会议及征文通知(10)中国国际铸造展览会(11)《压铸世界》产品技术信息刊登办法(12)《压铸世界》征订启事(13)变形镁合金在航空航天器中的应用(14)时效处理对压铸Al-Si-Cu 合金力学性能的影响(19)铝合金压铸用乳液涂料主要性能指标及检测方法(22)2009年日本国内压铸机械销售量情况(18)预计今年印度压铸产品需求量将增加15~20%(21)2009年日本压铸生产铝合金产量情况(21)汽车零部件发展趋势及国内企业发展战略(25)东北模具产业依托汽车产业欲吸金建基地(26)中国汽车用铝镁合金实现轻量化的优势和实践(27)2009年我国有色金属产品的外贸分析与展望(28)经营形势企稳回升,2010年总体趋势向好(31)镁合金铸造技术的发展现状(34)压铸技术讲座(十五)(36)广州意戈力自动化设备有限公司(40)统旺科技工业股份有限公司(40)力劲科技集团·上海一达机械有限公司(40)PDF 文件使用 "pdfFactory Pro" 试用版本创建 1820222628303234363840。
AE44镁合金油底壳压铸件本体组织与性能分析

··汽车发动机油底壳是汽车上重要的安全部件之一,对其各项力学性能尤其是抗拉强度有着明确的要求。
目前,油底壳压铸件大部分采用铝合金材料[1],而汽车轻量化的趋势使得我们需要寻找一种更轻的材料,镁合金因其自身的特点而在这方面得到应用。
近年来,对于镁合金材料的研究很多,但对于镁合金压铸件本体的研究却鲜见报道。
本试验以汽车油底壳镁合金材料AE44为例,结合其铸造及加工性能,分析AE44镁合金油底壳压铸件本体组织与性能,并对其工艺的改良提出建议。
合金的铸造性能是保证铸件质量的重要因素,铸造性能主要有流动性、收缩性、偏析倾向等,直接影响其加工性能。
流动性是指液态金属充满铸型的能力,流动性受很多因素的影响,其中最主要的是化学成分和浇注温度的影响。
收缩性是指铸件从浇铸温度至室温的冷却过程中,其体积和线尺寸减小的现象[2]。
偏析倾向是指铸件凝固过程中有产生组织不均匀的趋势,倾向性越强,出现偏析的几率就越大。
1试验材料与设备试验材料为Mg-40%RE 合金、AM50、纯镁,通过这三种材料的配比得到本油底壳所需材料。
油底壳本体在力劲DCC1600M 冷室压铸机上制得。
油底壳长约450mm ,宽端宽约325mm ,窄端宽约170mm ,高约170mm ,壁厚为8~13mm 。
显微组织观察试样及力学拉伸试样由线切割在本体上取得,拉伸试样采用矩形ⅠⅠⅠⅠⅠⅠⅠⅠⅠⅠⅠⅠ压铸董泰山,龙思远,廖慧敏,刘勇(重庆大学材料科学与工程学院,重庆400030)摘要:通过材料的替代研究,得到了AE44镁合金油底壳压铸件。
模拟结果显示该合金的充型能力和凝固顺序等铸造性能都满足此油底壳的工艺条件。
利用OM 、SEM 、XRD 对本体组织和物相分析,结果表明:本体组织主要由α-Mg 基体和沿晶界分布的Mg-RE 化合物组成,这些化合物主要为Al 11RE 3、Al 2RE 、Al 2.12RE 0.88。
Al 11RE 3和Al 2.12RE 0.88稀土相的存在,对材料性能的提高起到很大的作用。
汽车压铸及铸造铝合金_李平

Key words: die casting aluminum alloy; casting aluminum alloy; low pressure casting;
metal mold casting; Cosworth process
铝合金具有一系列的优异 性能与高 效 的 节 能 环 保效果, 在汽车与摩托车中的应用 越 来 越多, 在用材 结构中占的比例也逐年有所上升。 减轻 车的 自身质 量是扩大其 应用的 主要途径之一, 为 了 大幅 度 减轻
3
2011 ,Vol. 39 ,№12 1993 年 下 降 到 81. 9% , 2003 年 减 少 到 为 88. 4% , 79. 1% , 以 后 至 2008 年 几乎 保 持 不 变, 再 后, 下降 幅 度会稍微大一点。 2000 ~ 2008 年美国铸造铝合金的发货量 见表 4, 而图 2 示 出美国 2008 年发货的各种铝铸件的比 例。由这些数据可 见, 在美国铝合金压铸件 占 的比 约 低 25 个百 分点 以上, 但还是 例比日本的低 得 多, 呈上升趋势, 新 世纪后 几 年的比例 就 比 开 头几 年的 高一些。 2000 ~ 2008 年 北 美 ( 美国与 加 拿 大 ) 铝工 业 向 汽车工业的发货量见表 5 。
压铸件及铸件产量 Tab. 1 Output of die casting and casting aluminum alloys used for Japanese automobile from 2003 to 2008
年度 2003 2004 2005 2006 2007 2008 总计 铸件 / kt 384. 167 364. 738 381. 411 397. 322 399. 741 381. 675 2 309. 054 压铸件 / kt 733. 746 817. 033 897. 501 950. 417 957. 658 940. 611 5 296. 966 总计 / kt 1 117. 913 1 181. 771 1 278. 912 1 357. 399 1 357. 399 1 322. 286 7 606. 020 压铸件占比例 / % 65. 7 69. 2 70. 2 70. 6 70. 6 71. 2 69. 6
中国压铸行业发展历程及现状

中国压铸行业发展历程及现状孙猛力劲力劲科技科技科技集团集团集团有限公司有限公司杨达康 李培杰清华大学机械工程系摘要摘要::本文从压铸机的生产、压铸产品、压铸模、压铸单元等方面介绍了我国压铸业的发展历程与现状,反映了我国正逐步从压铸大国迈向压铸强国的现状及趋势。
同时梳理了压铸机关键技术的发展脉络及里程碑事件,并对压铸机行业的发展进行了展望。
关键词关键词::压铸 压铸机 中国压铸行业前言压力铸造技术是金属加工工艺中发展较快的一种铸造方法,液态金属在高速高压作用下射入紧锁的模具型腔内,并在保压条件下结晶凝固,形成半成品或成品。
压铸作为一种高效率、少切屑的先进精密成型技术,随着19世纪20年代世界印刷工业的发展,起源于活字制造,至今不到200年。
它与传统铸造技术相比,是一种年轻的铸造技术分支,目前已应用到各行各业中。
一、我国我国压铸机生产厂家的变迁压铸机生产厂家的变迁我国的应用压铸技术以20世纪40年代中后期作为起点。
1949年前,我国仅少数几家工厂有少量进口压铸机并生产锌合金铸件。
机型主要为小型压铸机,冷压室热压室均有。
1947年,中国第一家压铸专业厂在上海弄堂里诞生。
20世纪50年代,航空、仪器仪表、汽车等工业发展迅速,促进了中国压铸业的兴起。
50到60年代,以南京为中心,许多科研工作者在压铸行业的发展中作出了卓有成效的工作。
20世纪60年代中期,上海及南京一带的压铸生产厂家在技术上有了较快发展,可生产精密、薄壁、小孔、螺丝、齿轮、花纹及镶件组合结构等复杂的压铸件。
真空压铸除南京外,在上海也开始用于生产。
此时压铸技术的水平有了提高,上海、南京、沈阳等一些地方已开始研究充氧压铸。
60年代,为适应国内压铸件生产,上海压铸机厂成为国内第一家压铸机专业生产厂,不久,压铸机的生产厂家不断涌现,相继有隆华、灌南、阜新等一批专业生产压铸机的骨干企业。
多年来,这些压铸机厂生产了大量的国产压铸机。
在大型压铸机方面,阜新压铸机厂曾生产了锁模力为28000kN 的大型压铸机,当时填补了国内的空白,但因为技术及配套设施所限,没有进行批量生产。
0945561234 张磊 压力铸造的发展状况与展望汇总
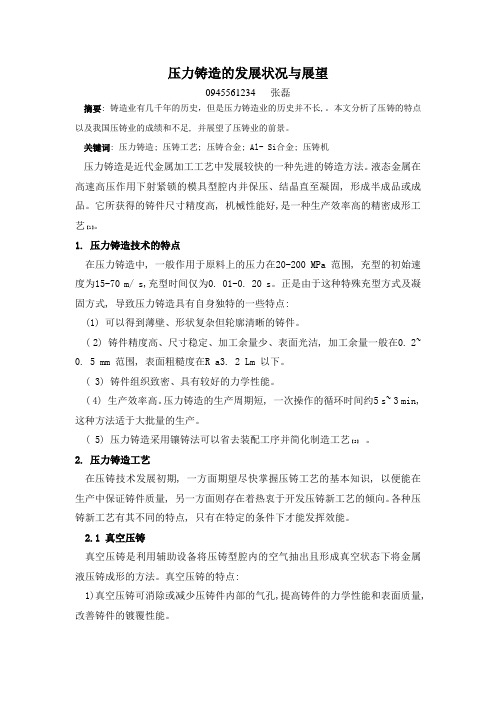
压力铸造的发展状况与展望0945561234 张磊摘要: 铸造业有几千年的历史,但是压力铸造业的历史并不长,。
本文分析了压铸的特点以及我国压铸业的成绩和不足, 并展望了压铸业的前景。
关键词: 压力铸造; 压铸工艺; 压铸合金; Al- Si合金; 压铸机压力铸造是近代金属加工工艺中发展较快的一种先进的铸造方法。
液态金属在高速高压作用下射紧锁的模具型腔内并保压、结晶直至凝固, 形成半成品或成品。
它所获得的铸件尺寸精度高, 机械性能好,是一种生产效率高的精密成形工艺【1】。
1. 压力铸造技术的特点在压力铸造中, 一般作用于原料上的压力在20-200 MPa 范围, 充型的初始速度为15-70 m/ s,充型时间仅为0. 01-0. 20 s。
正是由于这种特殊充型方式及凝固方式, 导致压力铸造具有自身独特的一些特点:(1) 可以得到薄壁、形状复杂但轮廓清晰的铸件。
( 2) 铸件精度高、尺寸稳定、加工余量少、表面光洁, 加工余量一般在0. 2~ 0. 5 mm 范围, 表面粗糙度在R a3. 2 Lm 以下。
( 3) 铸件组织致密、具有较好的力学性能。
( 4) 生产效率高。
压力铸造的生产周期短, 一次操作的循环时间约5 s~ 3 min, 这种方法适于大批量的生产。
( 5) 压力铸造采用镶铸法可以省去装配工序并简化制造工艺【2】。
2. 压力铸造工艺在压铸技术发展初期, 一方面期望尽快掌握压铸工艺的基本知识, 以便能在生产中保证铸件质量, 另一方面则存在着热衷于开发压铸新工艺的倾向。
各种压铸新工艺有其不同的特点, 只有在特定的条件下才能发挥效能。
2.1 真空压铸真空压铸是利用辅助设备将压铸型腔内的空气抽出且形成真空状态下将金属液压铸成形的方法。
真空压铸的特点:1)真空压铸可消除或减少压铸件内部的气孔,提高铸件的力学性能和表面质量, 改善铸件的镀覆性能。
2)真空压铸时大大地减少了型腔的反压力。
可使用较低的比压及铸造性能较差的合金, 甚至可用小机器压铸较大和较薄的铸件。
压铸机的历史

横合模、縦射出圧鋳、水圧式的開発、鋳造圧力210~700kg/cm 小型機) 横合模、縦射出圧鋳、水圧式的開発、鋳造圧力210~700kg/cm2 (小型機) 210 立式圧鋳的開発 横式圧鋳液圧式的開発 低速、高速、 低速、高速、増圧三段速射出圧鋳 国産圧鋳機械液圧式的製作 正式的圧鋳生産 大型圧鋳機的生産 镁合金加料的开发 射出監測装置開発 射出、合模控制装置(SEMU・LMU)開発 射出、合模控制装置(SEMU・LMU)開発 (SEMU 電脳監測装置開発 TOSCAST控制装置開発 TOSCAST控制装置開発 超高速射出圧鋳機的開発 (空射出速度10m/S) 空射出速度10m/S) 10 DEC150MT DEC150MT 150 P-2 P-2 200C 1号機 200C
電動合模、 電動合模、超高速射出圧鋳機的開発
冷室圧鋳機 (手動式) 手動式)
熱室圧鋳機 (手動式) 手動式)
P-3 P-3
冷室圧鋳機 (手動式) 手動式)
立式冷室圧鋳機 (水圧式) 水圧式)
P-4 P-4
東芝機械従1953年製作第一台圧鋳機以来、 東芝機械従1953年製作第一台圧鋳機以来、 1953年製作第一台圧鋳機以来 累計生産台数是一万台。 累計生産台数是一万台。
氧气
氧气瓶
氧气
P-21 P-21
半固态压铸法(液延压铸法) ④ 半固态压铸法(液延压铸法)
将固体和液体共存的状态的合金进行压铸的方法。 将固体和液体共存的状态的合金进行压铸的方法。从液体到固液共存状态时称为半 固态压铸法(レオキャスト法)。 收缩孔的发生率降低,延长模具寿命,结晶粒子大 (レオキャスト法 小均一是其特征,并能得到质量稳定的压铸产品。液延压铸法。
① 压铸的一般知识
压铸原理及理论
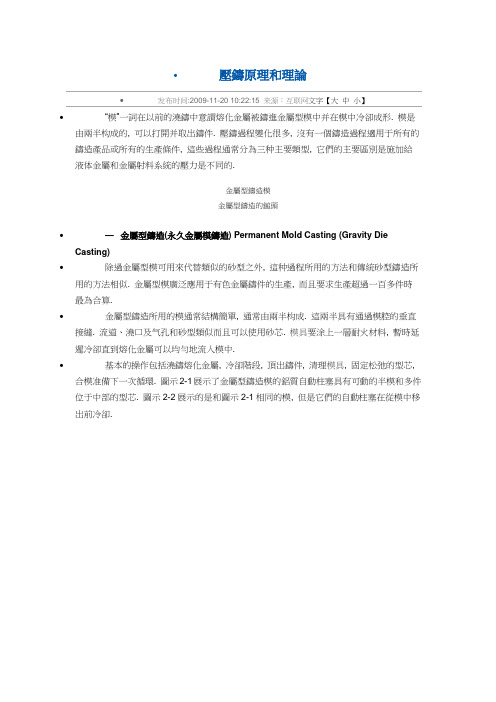
∙壓鑄原理和理論∙发布时间:2009-11-20 10:22:15 来源:互联网文字【大中小】∙“模”一詞在以前的澆鑄中意謂熔化金屬被鑄進金屬型模中并在模中冷卻成形. 模是由兩半构成的, 可以打開并取出鑄件. 壓鑄過程變化很多, 沒有一個鑄造過程適用于所有的鑄造產品或所有的生產條件, 這些過程通常分為三种主要類型, 它們的主要區別是施加給液体金屬和金屬射料系統的壓力是不同的.金屬型鑄造模金屬型鑄造的鎚頭∙—金屬型鑄造(永久金屬模鑄造) Permanent Mold Casting (Gravity Die Casting)∙除過金屬型模可用來代替類似的砂型之外, 這种過程所用的方法和傳統砂型鑄造所用的方法相似. 金屬型模廣泛應用于有色金屬鑄件的生產, 而且要求生產超過一百多件時最為合算.∙金屬型鑄造所用的模通常結構簡單, 通常由兩半构成. 這兩半具有通過模腔的垂直接縫. 流道、澆口及气孔和砂型類似而且可以使用砂芯. 模具要涂上一層耐火材料, 暫時延遲冷卻直到熔化金屬可以均勻地流入模中.∙基本的操作包括澆鑄熔化金屬, 冷卻階段, 頂出鑄件, 清理模具, 固定松弛的型芯, 合模准備下一次循環. 圖示2-1展示了金屬型鑄造模的鋁質自動柱塞具有可動的半模和多件位于中部的型芯. 圖示2-2展示的是和圖示2-1相同的模, 但是它們的自動柱塞在從模中移出前冷卻.∙∙—金屬型鑄造的优點(Advantages of Permanent Mold Casting )∙這种鑄造過程的主要優點是經濟和优良鑄造品質. 生產率通常比砂型鑄造高。
這种鑄造鑄出的鑄件比砂型鑄造鑄出的鑄件具有更細的晶粒結構和更好的強度特征. 而且, 鑄件可以設計成具有更薄的件壁. 另外, 鑄造表面比砂型鑄造件的表面更光滑, 而且由于可以保持更為緊密的尺寸公差, 因此很少要求机加工. 金屬型鑄件的孔隙率小于砂型鑄件, 因而具有优越的氣密性, 金屬型模的壽命通常是50000到70000啤之間.∙—金屬型鑄造的缺點(Disadvantages of Permanent Mold Casting )∙這种鑄造過程由于工模成本高、生產期短而不經濟合算. 這种鑄造過程要進行大批量的生產既慢且成本昂貴. 高壓壓鑄過程可以更好地滿足大批量生產的要求, 當要求不同尋常的可靠性和高机械特征時, 金屬型鑄造件就不會滿足零件的要求了.∙—低壓壓鑄(Low Pressure Die Casting )∙要想使熔化金屬進入模中的工藝自動化, 就要開發出一種技朮代替人工操作熱金屬。
第六章压力铸造

铸造工艺与压力铸造
20世纪60年代至70年代是压铸工艺与设备逐步完善的时 20世纪60年代至70年代是压铸工艺与设备逐步完善的时 期。而70年代到现在,则是电子技术和计算机技术加速用 期。而70年代到现在,则是电子技术和计算机技术加速用 于压铸工艺与设备的大发展阶段。数控压铸机、计算机控 制压铸柔性单元及系统(压铸FMC及FMS)和压铸工艺与设 制压铸柔性单元及系统(压铸FMC及FMS)和压铸工艺与设 备计算机辅助设计(CAD)的出现,标志着压铸生产开始从 备计算机辅助设计(CAD)的出现,标志着压铸生产开始从 经验操作转变到科学控制新阶段,从而使压铸件的质量、 自动化程度及劳动生产率都得到极大的提高。 各种常用铸造方法适用范围及技术经济指标见表1.1。 各种常用铸造方法适用范围及技术经济指标见表1.1。
(2) 卧式冷压室压铸机的基本原理。压室与压射机构处于 水平位置,压铸过程如图1.4所示。压铸过程中,金属液 水平位置,压铸过程如图1.4所示。压铸过程中,金属液 从加料口浇入压室,压射冲头向前运动,推动金属液使之 经浇道充填模具型腔。金属液在压力下冷却凝固,然后开 模,取出带着浇注系统和余料的压铸件,完成一个压铸循 环。 (3) 全立式冷压室压铸机的基本原理。全立式冷压室压铸 机的合模机构和压射机构垂直布置。它又分上压式和下压 式两种。上压式压铸原理如图1.5(a)所示。压铸过程是先 式两种。上压式压铸原理如图1.5(a)所示。压铸过程是先 加料后合模,然后压射冲头由下向上运动将金属液通过浇 注系统压入型腔。下压式压铸原理如图1.5(b)所示。合模 注系统压入型腔。下压式压铸原理如图1.5(b)所示。合模 后,将金属液浇入压室中,依靠下冲头底部弹簧弹力,由 下冲头托住金属液,防止其在重力的作用下流入型腔。当 上冲头下压时,通过金属液推动下冲头,下冲头下降,让 出浇道,金属液在上冲头的压力作用下充填型腔。
压铸技术资料

压铸复习资料第一章绪论第一节概论压力铸造是近代金属加工工艺中发展较快的一种少无切削的特种铸造方法。
最原始的压铸机于1856年问世,迄今已有近150年历史,从最早的手工压铸,到现在的全自动化计算机控制压铸,从最早的冷室压铸方法到现在的镁合金hot runner 法,现代压铸已渗透到现代制造业的各个行业。
熔融金属是在高压、高速下充填铸型。
并在高压下结晶凝固形成铸件。
高压、高速是压力铸造的主要特征。
由于它具有生产效率高,工序简单。
铸件公差等级较高(常用锌合金为IT10-13,铝合金为IT11-13),表面粗糙度好(锌合金为Ra1.6-3.2,铝合金Ra3.2-6.3),机械强度大,可以省去大量的机械加工工序和设备,节约原材料等优点,现已成为世界铸造业中一个重要组成部分。
锌合金压铸开始于1890年,铝合金压铸开始于1910年,铜合金压铸开始于1911年,镁合金压铸开始于1925年。
第二节压力铸造的基本理论一、典型的填充理论国外在30年代初期已有一些著名专家对压铸过程中金属的流转作了系统的试验研究,比较公认的有三种。
1.喷射填充理论(第一种填充理论)。
它是由德国人学者L.Ffommel于1932年根据流体力学的定律,以理想流体为基础通过实验得出,在速度、压力均保持不变的前提下,金属液进入内浇口,冲击到正对面型壁处——冲击阶段,经撞击后,金属聚集呈涡流状态,向着内浇口一端反向填充——涡流阶段。
最终填充成形。
2.全壁厚填充理论(第二种填充理论)这种理论认为:金属液通过内浇口进入型腔后,即扩张到型壁,然后沿着整个型腔截面向前填充,直到整个型腔充满为止。
3.三阶段填充理论(第三种填充理论)第一阶段:液态金属射入型腔后,沿着型腔各方向扩展,在正常的传热条件下,与型腔壁面相接触的部位形成一层凝固层,亦即铸件的表面层。
第二阶段:铸件表面成壳后,型腔继续受到液体金属的填充,凝固层逐渐增厚,此时合金的粘度亦增,而处于中心部位的液体金属,在第二阶段结束时,尚处于液态,除了继续得到液体金属的补充外,仍可承受来自压室的压射压力。
低压铸造法的历史

低压铸造法的雏形可以追溯到本世纪初。
适用于铝合金是1917年在法国,1924年在德国提出的申请,但并没有形成大规模的工业生产。
为商业的目的而开始生产是在二战以后的1945年,由英国的路易斯先生创立了阿鲁马斯库公司,开始生产雨水管道、啤酒容器等。
在那以后的五十年代里,奥地利和德国开始生产气缸头。
1958年美国的泽讷拉路默它斯在小型汽车的发动机零件上(气缸头、箱体、齿轮箱)大量运用了铝合金铸件,并采用了低压铸造法。
这件事对至今仍广泛采用的低压铸造法而言是不可或缺的推动,特别是在全世界的汽车工业界引起了极大的反响。
低压铸造法被介绍进我国是1957年左右,但真正引起业界的注意,开始进行各种研究、引进设备是从1960年左右开始的。
但是这种打破了以往常识的划时代的工艺方法,几乎没有冒口,与已经作为一种“技术”确立起来的重力金型铸造的技术相比具有完全不同的难度,因此业界的反应比较冷淡。
在这种状况下,1961年的轻型汽车用空冷气缸头的生产成为低压铸造法在我国实用化的开端。
以后的发展非常迅速,在克服了多个技术难题后,利用低压铸造法所具有的材料利用率高、容易实现注汤自动化等优点,以汽车部件为中心,逐步确立了轻合金铸件的主要铸造法的牢固地位。
目前在铝合金铸件的生产量中,低压铸造品已占了大约50%,并以其巨大的生产量和优良的品质而著称于世。
产品扩大到汽车相关部件,如气缸头、气缸体、刹车鼓、离合器罩、轮毂、进气岐管等。
特别是1970年以后大量应用在轮毂上,并且随着近年来的汽车轻量化和提高性能等要求,在以往从未有过的复杂内部品质和机械性质的严格要求下,气缸头、气缸体上的使用也逐渐增加。
基本原理及工艺过程基本原理如图5.1所示,在密闭的保持炉的熔汤表面上施加0.01~0.05Mpa的空气压力或惰性气体压力,熔汤通过浸放在熔汤里的给汤管上升,被顶入充填进连接着的炉子上方的模具内。
因此熔汤是从型腔的下部慢慢开始充填,保持一段时间的压力后凝固。
- 1、下载文档前请自行甄别文档内容的完整性,平台不提供额外的编辑、内容补充、找答案等附加服务。
- 2、"仅部分预览"的文档,不可在线预览部分如存在完整性等问题,可反馈申请退款(可完整预览的文档不适用该条件!)。
- 3、如文档侵犯您的权益,请联系客服反馈,我们会尽快为您处理(人工客服工作时间:9:00-18:30)。
Deicasting World Report
主办单位:中国机械工程学会铸造分会
1997年创刊双月刊内部资料
出
版:中国机械工程学会铸造分会编辑:《压铸世界》编辑部编辑委员会
主
任:唐玉林委员:苏仕方,刘鸿超编辑部主编:苏仕方责任编辑:刘鸿超,曹秀梅地址:沈阳市铁西区云峰南街17号邮编:110022
编辑热线:024-********
024-********-356传真:024-********电子信箱:Lhc@
互联网站:
服务热线:024-********
联系人:刘秀玲2009年第4期(总第46期)2009年8月25日出版
第七届中国国际压铸会议暨展览会展位预定办法(2)2009中国铸造活动周邀请函(3)第69届世界铸造会议穴WFC2010雪征文通知穴8雪2009年《压铸世界》产品技术信息刊登办法穴9雪《压铸世界》征订启事(10)关于全国铸造学会压铸委员会发展团体会员及交纳二OO 九年会费的通知穴11雪第十一届(2008年度)“福士科”杯中国机械工程学会铸造专业优秀论文评选活动结束(13)中国机械工程学会铸造分会环境保护及安全技术委员会八届二次会议在银川召开(13)半固态金属浆料制备技术的研究进展(一)(14)北美压铸学会(NADCA )发布2010年研发战略和发展路线(18)打破瓶颈中国模具企业亟需提高创新能力(20)浅析进口铝对我国市场的影响(22)英国研制出铝熔炉铝水测量新技术(24)
过去10年镁合金压铸件在汽车上的用量增加了15%(19)2009年1~3月中国共出口金属镁3.9万吨(23)欧盟拟对华铝合金轮毂发起反倾销调查
(25)全球5月原铝日均产出量为6.3万吨(26)我国压铸模具现状与发展前景(27)日本开发高强度镁合金(29)深入透析我国模具产业市场聚集地(30)俄罗斯铝业发展势头强劲(32)世界主要镁资源储藏和生产(33)澳镁工业新技术一瞥
(34)全球1~4月精炼锌市场供应过剩(38)压铸技术讲座(十一)(35)东莞市祥威机械有限公司招聘启事(39)
济南慧成铸造有限公司
(40)福士科铸造材料(中国)有限公司
(40)
热烈欢迎参与亚洲最大的高压铸造、低压铸造、挤压铸造、半固态加工、金属型铸造业盛会
第69届世界铸造会议(WFC2010)征文通知
2010年10月16-20日中国杭州
会议主题:绿色铸造
18
20
22
26
28
30
32
34
36
38
40。