预见性维护 predictive maintenance
预测性维护{维修}又称预知性预见性维护

预测性维护{维修}又称预知性预见性维护预测性维护(又称预知性预见性维护)预测性维护,也被称为预知性预见性维护,是一种基于数据和分析的维护策略,旨在提前识别和解决潜在的设备故障和问题,从而最大程度地减少停机时间和维护成本。
预测性维护通过监测设备的运行状态和性能参数,使用数据分析和模型预测技术,以及使用先进的传感器和监测设备等手段,帮助企业实现高效、可靠和可持续的设备维护管理。
一、预测性维护的意义预测性维护在现代工业和设备运营中具有重要的意义。
首先,它能够提高设备的可用性和可靠性。
传统的定期维护往往是基于时间或使用寿命来安排的,这种维护方式无法准确预测设备的真实状态和故障潜在风险,并且容易导致设备停机时间过长。
而预测性维护借助先进的传感器和监测设备,可以实时监测设备的运行状态和性能指标,及时发现设备问题,并针对性地进行维护和修复,从而提高设备的可用性和可靠性。
其次,预测性维护可以降低维护成本和维护工作量。
通过实时监测设备的运行状态,我们可以提前发现设备存在的问题并及时采取措施。
这样,就可以避免因设备故障而导致的停机和维修时间,减少维修成本和工作量。
另外,预测性维护还可以帮助企业有效规划维护资源,提高维护效率和维护质量,降低额外的维护费用。
最后,预测性维护有助于延长设备的使用寿命。
通过持续监测设备的运行状况和性能指标,我们可以提前发现设备存在的问题并及时修复,减少不必要的损伤和磨损。
这样,设备的寿命得以延长,减少了设备更换和更新的频率,进一步降低了成本和资源的浪费。
二、预测性维护的实施步骤实施预测性维护需要进行以下步骤:1. 设立监测系统:在设备上安装传感器和监测设备,实时监测设备的运行状态和性能参数。
监测数据可以包括温度、压力、振动、电流等信息。
同时,还需要建立数据采集和存储的系统,确保数据的完整和准确性。
2. 数据分析和建模:利用数据分析和数据建模技术,对监测数据进行处理和分析。
通过建立预测模型和故障诊断模型,可以准确评估设备的运行状况和故障潜在风险。
设备管理中的预测性维护技术研究与应用

设备管理中的预测性维护技术研究与应用预测性维护技术(Predictive Maintenance,PdM)是一种结合数据分析和智能技术的设备管理方法,通过对设备的实时监测和数据分析,可以提前预测设备故障,并采取相应的维修措施,从而避免设备停机和生产线的中断。
预测性维护技术在制造业、电力行业、航空航天等领域被广泛应用,并取得了显著的成果。
随着传感器技术的进步和物联网的兴起,设备监测的数据量和精度大大增加,预测性维护技术也得以快速发展。
首先,通过传感器和物联网技术,设备状态数据可以实时采集并传输到数据中心,对设备的运行状况进行监测。
其次,通过数据分析和机器学习算法,可以对设备进行故障诊断和预测,提前发现设备故障的迹象,避免设备停机,提高生产效率。
最后,预测性维护技术还可以根据设备的运行数据和维修历史,进行优化维修计划,提高维修效率和设备可靠性。
预测性维护技术在制造业中的应用已经取得了卓越的成果。
例如,利用预测性维护技术可以预测设备的剩余寿命,及时进行维修或更换关键部件,避免设备故障造成的生产停机损失。
同时,通过分析设备的运行数据和维修历史,可以建立设备维护的最佳实践,提高维修过程的效率和质量。
此外,预测性维护技术还可以帮助企业优化生产计划,提高生产效率和产品质量。
在电力行业中,预测性维护技术可以用于电力设备的监测和管理。
通过实时监测电网设备的运行状态和电力传输参数,可以提前发现电力设备的故障和安全隐患。
例如,通过对变压器的温度、振动和电流等参数进行监测和分析,可以预测变压器的故障风险,及时进行维修或更换,避免变压器事故造成的电力中断和损失。
此外,预测性维护技术还可以根据电力设备的负荷情况和运行数据,优化电力系统的运行计划,提高电力系统的可靠性和能源利用效率。
在航空航天领域,预测性维护技术可以用于飞机和航天器的维护管理。
通过实时监测飞机和航天器的运行状态和关键参数,可以预测飞行器的故障风险,及时进行维修和保养,保障航空安全。
浅谈西门子仪表的预测性维护

浅谈西门子仪表的预测性维护设备维护的模式设备维护一般有三种模式:事后维护、预防性维护和预测性维护。
事后维护,也有人称之为“补救性维护”、“故障后维护”、“运转至出现故障管理”,顾名思义也就是说设备出现故障时对它进行维修。
这是种最初级、最简单也是目前在国内被用户采用最多的维护运行手段。
确切地说,这是一种“无维护”管理方法。
它也是最为昂贵的维护管理方法,分析表明,在反应性或事后维护模式下进行维修的成本是有计划或预防性维护模式下进行的相同维护的成本的3倍。
预防性维护(Preventive Maintenance)和预测性维护(Predictive Maintenance)都属于事先维护。
一般地讲,预防性维护可以分为三种类型:基于时间的维护计划、基于性能的维护计划和基于条件的维护计划。
这种方法的问题是,运转模式以及与系统或装置相关的变量会直接影响机器的正常工作寿命。
同时,也有大量事实表明,频繁拆卸和停车维修,即导致产量降低,维修费用增加,而且也大大降低了设备的实际使用年限。
预测性维护(PM)也被称之为预知性维护或策略性维护。
预测性维护集设备状态监测、故障诊断、故障(状态)预测、维护决策支持和维护活动于一体,是近年来新兴的一种先进维护方式。
预测性维护实际上是一种运转状况驱动的预防性维护程序。
预测性维护不依赖于工业或工厂内平均寿命统计数据(即平均无故障时间)来计划安排维护活动,而是对运转状况、效率、热量分布和其他指标进行直接监视,以确定实际的平均无故障时间或将危害到工厂或设施内所有关键系统装置运转的效率损失。
和预防性维护相比,预测性维护具有明显的优势:1、克服预防性维护的盲目性,具有很强的针对性。
根据状态的不同采取不同的处理方法,降低运行检修费用。
2、减少停运(总维护)时间,提高设备可靠性和可用系数,延长设备使用寿命,更好地贯彻“安全第一,预防为主”的方针。
3、减少维护工作量,降低劳动强度,有利于减员增效,提高经济效益。
设备预测性维护技术的研究及应用案例分析

设备预测性维护技术的研究及应用案例分析今天,我们生活在一个充满技术的时代,各种智能设备在我们的生活中扮演着越来越重要的角色。
从人类发展史来看,技术的提高和发展是人类文明进步的基础。
在这样的背景下,设备预测性维护技术成为了研究的热点。
在本文中,我们将探究设备预测性维护技术的研究以及应用案例分析。
一、设备预测性维护技术的概念设备预测性维护技术(Predictive Maintenance)是通过对设备采集的数据进行分析,来预测设备可能出现的故障和问题,并在故障发生前进行预先的维护和保养。
这种技术可以通过对设备的振动、温度、压力等各种反馈数据进行分析和处理,来判断设备是否处于正常状态,并预测可能出现的故障,并通过提前维护,降低了设备故障率,提高了设备的稳定性和可靠性。
二、设备预测性维护技术的研究1.数据采集与分析设备预测性维护技术的基础是数据采集和分析。
首先需要收集大量设备振动、温度、压力等反馈数据,将这些数据传输到系统中进行处理和分析。
在系统中,需要进行数据清洗、数据挖掘和建模等操作,从中提取出有用的信息,进行分析和预测。
2.模型的建立在设备预测性维护技术中,模型的建立是一个必不可少的步骤。
通过对数据的分析和处理,可以建立出一种模型,通过这种模型来预测设备之后可能出现的故障和问题。
模型的建立需要考虑多种因素,包括设备的运行环境、设备的维护历史、设备的设计参数等等,这些因素将决定模型的可靠性和精度。
3.技术应用在设备预测性维护技术的研究中,应用是一个至关重要的环节。
技术应用需要考虑设备预测性维护技术的可行性和应用范围,需要对设备的运行状态进行实时监控和采集数据,以便及时进行预测和维护。
三、设备预测性维护技术的应用案例分析设备预测性维护技术是一个相对成熟的技术,已经得到广泛的应用。
下面我们来分析几个实际应用案例,包括电力、工业和交通领域。
1.电力领域电力行业是一个对设备可靠性要求非常高的行业。
电站的故障和事故不仅会影响电力供应,还会威胁社会的安全和稳定。
设备预测性维护保养指导书

设备预测性维护保养指导书一、工具电工万用表、百分表、等高尺、水平尺等常用测量工具。
二.术语2.1. EM 应急维修---- Emergency Maintenance 设备故障引起的停机维修2.2. PD 一般维护---- Predictive Maintenance 点检巡检、预测性维护中发现缺陷安排的维护2.3. PM 预防性维护---Preventive Maintenance包括周期性维护和预测性维护2.2. EV 事故报告---Event Report 发生设备事故后的调查报告2.5.一般设备---该设备发生故障后或停机修理时,对产品的生产、质量和交货期均无直接影响2.6.主要设备---该设备发生故障后或停机修理时,对产品的生产有影响,但不影响产品的质量和交货期2.7.重要设备---该设备发生故障后或停机修理时,对产品的生产、质量和交货期有直接影响2.8.预测性维护---利用检测技术对设备的状态或性能进行监测,掌握特性参数的劣化规律,预测劣化趋势,以实现故障发生前有计划的适当维修措施。
三、实施步骤1、确定参数预测性维修的第一步是确定设备或设备系统的状态监测参数,参数确定可用测量工具或人们可以直接目测。
如,电器设备的电流、电压,压力机油温、电流、压力,旋转设备的转速、振动等。
(参数确定之后还要确定参数的极限范围,用来作为监测的判断标准。
这些参数及其标准在设备技术说明书上有相关说明。
确定了参数之后要对其进行过程检测、监测,这种检测、监测可以是周期性的(如每周、每月等),也可以是非周期性(如在线随机监测)的。
当参数的测量值超出了工程标准极限范围时就要作进一步的分析诊断。
1.1、询问法询问操作人员使用情况,使用中有何异常声响或声光报警信号?有无烟气或异味,控制系统操作是否正常,操作程序有无变动,在操作时是否有特殊困难或异常等。
1.2、听诊法设备正常运转时,伴随发生的声响总是具有一定的音律和节奏。
预测性维修概述
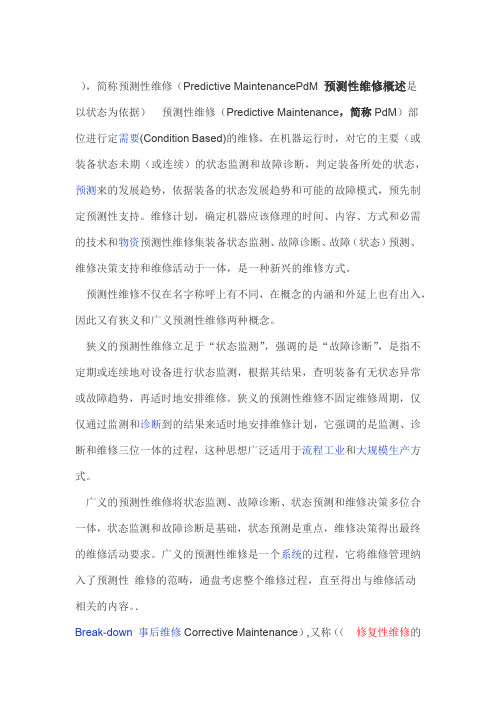
),简称预测性维修(Predictive MaintenancePdM预测性维修概述是以状态为依据)预测性维修(Predictive Maintenance,简称PdM)部位进行定需要(Condition Based)的维修,在机器运行时,对它的主要(或装备状态未期(或连续)的状态监测和故障诊断,判定装备所处的状态,预测来的发展趋势,依据装备的状态发展趋势和可能的故障模式,预先制定预测性支持。
维修计划,确定机器应该修理的时间、内容、方式和必需的技术和物资预测性维修集装备状态监测、故障诊断、故障(状态)预测、维修决策支持和维修活动于一体,是一种新兴的维修方式。
预测性维修不仅在名字称呼上有不同,在概念的内涵和外延上也有出入,因此又有狭义和广义预测性维修两种概念。
狭义的预测性维修立足于“状态监测”,强调的是“故障诊断”,是指不定期或连续地对设备进行状态监测,根据其结果,查明装备有无状态异常或故障趋势,再适时地安排维修。
狭义的预测性维修不固定维修周期,仅仅通过监测和诊断到的结果来适时地安排维修计划,它强调的是监测、诊断和维修三位一体的过程,这种思想广泛适用于流程工业和大规模生产方式。
广义的预测性维修将状态监测、故障诊断、状态预测和维修决策多位合一体,状态监测和故障诊断是基础,状态预测是重点,维修决策得出最终的维修活动要求。
广义的预测性维修是一个系统的过程,它将维修管理纳入了预测性维修的范畴,通盘考虑整个维修过程,直至得出与维修活动相关的内容。
.Break-down 事后维修Corrective Maintenance),又称((修复性维修的方式,它是以设备是否完”Failure Based,是)“有故障才维修(Maintenance)好或是否能用为依据的维修,只在设备部分或全部故障后再恢复其原始状态,也就是用坏后再修理,属于非计划性维修。
)又称定时维修,是以时间为依据(Preventive Maintenance预防性维修和经验,按规定的时间间隔进行停机检的维修,它根据生产计划(Time Based)查、解体、更换零部件,以预防损坏、继发性毁坏及生产损失。
设备的预防性和预测性维护

②对于设备的绩效(OEE、MTBF、MTTR等)进行监控。
例:如果MTBF越来越短,MTTR越来越长,其实就代表着该设备的状态是处于“劣化”的情况, 这时需要提前采取一些措施。原来制定的预防性维护计划是1次/半年对它进行一次维护保养或周期 性检修,这时它的状态不好,就要考虑把它缩短为1个月就要进行周期性检修或预防性维护,这个 就属于预测性维护的范畴。
生产车间设备的 预防性和预测性维护
I AT F 1 6 9 4 9 : 2 0 1 6 对 设 备 管 理 提 出 了 明 确 的 要 求 :
8.5.1.5 全面生产维护 组织应制定、实施并保持一个形成文件的全面生产维护系统。 f) 形成文件的维护目标,例如:OEE(全局设备效率)、MTBF(平均故障间隔时间)和MTTR (平均维修时间),以及预防性维护符合性指标。维护目标的绩效应作为管理评审的输入(见 ISO9001 第9.3条) g) 维护计划和目标以及形成文件的措施计划的定期评审,以在未达到目标时采取纠正措施; h) 对预防性维护方法的使用; i) 对预测性维护方法的使用,如适用; j) 周期性检修。
同时预防性维护是制造过程设计的一项输出【8.3.5.2 制造过程设计输出 h)维护计划和说明】,在 做预防性维护的时候有两个非常重要的输入,一个输入是设备的使用说明书,说明书会告诉我们什 么时候要更换润滑油,什么时候要对一些易损件进行更换。另外一个重要的输入是PFMEA或设备 FMEA,但FMEA在工厂的运用基本上就是纸上谈兵,像一些关键或核心设备、工装夹具、易损部 位等,很多时候是要基于FMEA来进行识别。
预防性维护(Preventive maintenance):
预防性维护:为了消除设备失效和非计划生产中断的原因而策划的定期活动(基于时间的周期性检 验和检修)。它是制造过程设计的一项输出。
预防性维护和预见性维护区别(模版)

预防性维护和预见性维护区别(模版)第一篇:预防性维护和预见性维护区别(模版)预防性维护和预见性维护区别组织应识别关键过程设备为机器/设备的维护提供资源并建立有效的、有计划性的全面预防性维护系统这个系统包括---有计划的维护活动---设备、工装和量具的包装和防护---可得到关键生产设备的零配件---将维护目标形成文件并予以评价和改进。
组织应使用预见性维护的方法以持续改进生产设备的有效性和效率。
我个人理解1预防性维护好比汽车周期性保养3000km换机油到维修站检查20000km再来一次对于设备的每天有日常的保养可说成一级保养一般由设备操作人员进行。
每间隔500小时要进行一次二级保养一般有操作人员和工程部门共同完成每2000小时大修一次三级保养一般由工程部门和设备厂家共同完成。
当然具体的运行时间定多少要看具体情况了。
说简单点预防性维护就是按计划做一些管理维护当然不同级别保养内容可能有差异的哦。
2预见性维护好比早上起来发动车子发现转弯有点不顺畅或者轮胎有点滑我们感觉好象要出什么事情马上去维修站不是计划内的只是从一些问题发现症状预计会发生。
说到具体设备比如设备异常噪音、气味、运转异常、不顺畅或SPC控制图一段时期内异常那么马上应该启动预见性维护程序了。
第二篇:设备预见性维护管理设备预见性维护管理1范围本标准规定了设备预见性维护的管理职责、管理要求和工作程序。
本标准适用于本企业范围内设备预见性维护管理。
规范性引用文件下列标准所包含的条文,通过在本标准的引用而构成本标准的条文,在标准出版时所有版本均为有效,所有标准都会被修订,使用本标准的各方应探讨,使用下列标准最新版本的可能性。
术语和定义3.1 设备预见性维护:通过对设备运行状态及故障的技术分析,找出其具有规律性的东西,采用科学有效的对策措施,对设备可能发生的(特别是重复发生的)、潜在的故障和隐患提前做好准备。
4 职责4.1设备是企业生产的物资技术基础,影响着整个企业的正常运转。
预防性维护系列03-预测性维护
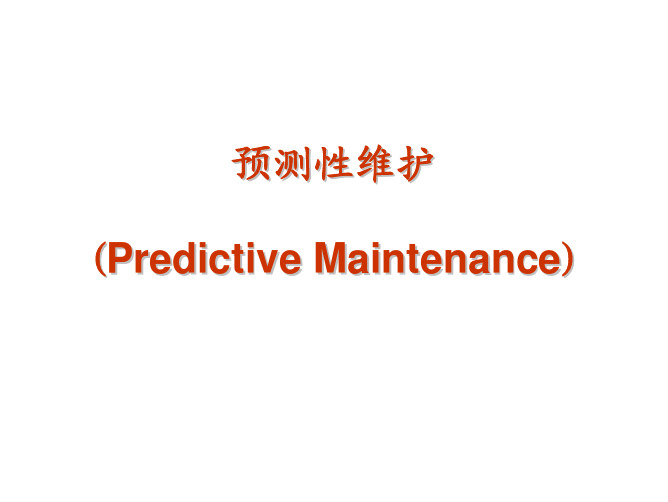
• 最重要的是:应先从改善设备,进而改变 人员观念,来创造设备的最佳条件。
如何开展预测性维护 • 进行预测性维护时要考虑的问题:
- 对象设备是哪一台? - 患处何在?
• 设备诊断选定的重点
故障发生对于生产将产生重大影响 经常发生突发性故障 普通的点检整理,无法预防故障 故障与故障之间的间隔比较长 因劣化引起的故障 劣化的进行比较慢
诊断技术开发案例3
滑架(Carriage)行走时的松动诊断
前进端 前进 附日常产 品搬送用 的支架 附加使支 架垂直、 水平方向 的感应器 否定器 设备诊断外观图 原位置 后退 滑架 上升
下降 波形记录纸
hicoder
掌握劣化模式(和时间同时产生什么变化?) 凸轮从动件(cam follower)磨耗或调整不良、导杆(guide rod)发生磨损时, 以及当滑架(carriage)行走时,松动会加大。
预测性维护与设备诊断 设备诊断技术不仅是故障检测技术, 而且也是施行预测性维护的技术。
状 态 设 备 正常期
依据简易诊断的趋势管理
症候 期 精密诊断
故障
检测极限
机能极限
的 判 定
换 时 间
最 佳 更 时间
图1 劣化模式与诊断的概念
预测性维护与设备诊断
监控机器/设备/系统的健康状况以消除重大故障/停机. 选择一个对设备的健康状况最有代表性的参数 选择一种参数测定的方法 周期性地监测参数 - 判定关键程度 - 预测可能的故障停机发生 关键性的-SOS维修-加强维护监控 开展质量维护并恢复监控 -预测可能的故障停机发生
培训
技术人员
•机械密封 •精密平衡 •静态平衡 •工具和用具的改进使用 •基本的振动分析
主管和行政人员
预测性维护{维修}又称:预知性、预见性维护{维修})

预测性维护{维修}⼜称:预知性、预见性维护{维修})预测性维护{维修}(Predictive Maintenance,简称PdM)(⼜称:预知性、预见性维护{维修})是以状态为依据(Condition Based)的维护,在机器运⾏时,对它的主要(或需要)部位进⾏定期(或连续)的状态监测和故障诊断,判定装备所处的状态,预测装备状态未来的发展趋势,依据装备的状态发展趋势和可能的故障模式,预先制定预测性维护计划,确定机器应该修理的时间、内容、⽅式和必需的技术和物资⽀持。
预测性维护集装备状态监测、故障诊断、故障(状态)预测、维护决策⽀持和维护活动于⼀体,是⼀种新兴的维护⽅式。
预测性维护不仅在名字称呼上有不同,在概念的内涵和外延上也有出⼊,因此⼜有狭义和⼴义预测性维护两种概念。
狭义的预测性维护⽴⾜于“状态监测”,强调的是“故障诊断”,是指不定期或连续地对设备进⾏状态监测,根据其结果,查明装备有⽆状态异常或故障趋势,再适时地安排维护。
狭义的预测性维护不固定维护周期,仅仅通过监测和诊断到的结果来适时地安排维护计划,它强调的是监测、诊断和维护三位⼀体的过程,这种思想⼴泛适⽤于流程⼯业和⼤规模⽣产⽅式。
⼴义的预测性维护将状态监测、故障诊断、状态预测和维护决策多位合⼀体,状态监测和故障诊断是基础,状态预测是重点,维护决策得出最终的维护活动要求。
⼴义的预测性维护是⼀个系统的过程,它将维护管理纳⼊了预测性维护的范畴,通盘考虑整个维护过程,直⾄得出与维护活动相关的内容。
修复性维护(Corrective Maintenance),⼜称事后维护(Break-down Maintenance),是“有故障才维护(Failure Based)”的⽅式,它是以设备是否完好或是否能⽤为依据的维护,只在设备部分或全部故障后再恢复其原始状态,也就是⽤坏后再修理,属于⾮计划性维护。
预防性维护(Preventive Maintenance)⼜称定时维护,是以时间为依据(Time Based)的维护,它根据⽣产计划和经验,按规定的时间间隔进⾏停机检查、解体、更换零部件,以预防损坏、继发性毁坏及⽣产损失。
[VIP专享]预防性维护与预见性维护区别(非常实用)
![[VIP专享]预防性维护与预见性维护区别(非常实用)](https://img.taocdn.com/s3/m/a3bce053de80d4d8d05a4f38.png)
预防性维护与预见性维护区别(非常实用)汽车体系第一步:先看一下TS标准中的描述7.5.1.4 预防性和预见性维护组织应识别关键过程设备,为机器/设备的维护提供资源,并建立有效的、有计划的全面预防性维护系统。
这个系统至少应包括:— 有计划的维护活动;— 设备、工装和量具的包装和防护;— 可得到关键生产设备的零配件;— 将维护目标形成文件并予以评价和改进。
组织应使用预见性维护方法,以持续改进生产设备的有效性和效率。
第二步:TS标准中的定义3.1.7预见性维护predictive maintenance基于针对过程数据,通过预测可能的失效模式以避免维护性问题的活动。
3.1.8预防性维护preventive maintenance为消除设备失效和生产的计划外中断的原因而策划的措施,作为制造过程设计的一项输出。
第三步:现实问题预防性维护是指有计划的定期设备维护和零配件更换,通常包括保养维护、定期使用检查、定期功能检测、定期拆修、定时更换等几种类型;预见性维护是通过运用各种手段和人的感觉进行数据和信号的采集、分析和判断设备的劣化趋势、故障部位、原因并预测变化发展、提出防范措施,防止和控制可能的故障出现。
预防性及预见性维护要求点检表(ISO/TS16949:2009要求)定义/说明/要求/目的:设备维护是指:为了降低设备失效或功能退化的概率,按预定的时间间隔或规定的标准进行的维护;主要是通过系统性的维护工作消除设备存在的故障征兆,使设备继续保持既定的功能。
关键过程是指:对形成产品质量起决定作用的过程。
预见性维护是指:基于针对过程数据,通过预测可能的失效模式以避免维护性问题的活动。
预防性维护是指:为消除设备失效和生产的计划外中断的原因而策划的措施,作为制造过程设计的一项输出。
组织应识别关键过程设备,为机器/设备的维护提供资源,并建立有效的、有计划的全面预防性维护系统。
预防性维护的目的就是为生产提供稳定的设备。
检查表:编号检查内容1必须识别出关键设备。
预防性维护与预见性维护区别(非常实用)

预防性维护与预见性维护区别(非常实用)汽车体系第一步:先看一下TS标准中的描述7.5.1.4 预防性和预见性维护组织应识别关键过程设备,为机器/设备的维护提供资源,并建立有效的、有计划的全面预防性维护系统。
这个系统至少应包括:— 有计划的维护活动;— 设备、工装和量具的包装和防护;— 可得到关键生产设备的零配件;— 将维护目标形成文件并予以评价和改进。
组织应使用预见性维护方法,以持续改进生产设备的有效性和效率。
第二步:TS标准中的定义3.1.7预见性维护predictive maintenance基于针对过程数据,通过预测可能的失效模式以避免维护性问题的活动。
3.1.8预防性维护preventive maintenance为消除设备失效和生产的计划外中断的原因而策划的措施,作为制造过程设计的一项输出。
第三步:现实问题预防性维护是指有计划的定期设备维护和零配件更换,通常包括保养维护、定期使用检查、定期功能检测、定期拆修、定时更换等几种类型;预见性维护是通过运用各种手段和人的感觉进行数据和信号的采集、分析和判断设备的劣化趋势、故障部位、原因并预测变化发展、提出防范措施,防止和控制可能的故障出现。
预防性及预见性维护要求点检表(ISO/TS16949:2009要求)定义/说明/要求/目的:设备维护是指:为了降低设备失效或功能退化的概率,按预定的时间间隔或规定的标准进行的维护;主要是通过系统性的维护工作消除设备存在的故障征兆,使设备继续保持既定的功能。
关键过程是指:对形成产品质量起决定作用的过程。
预见性维护是指:基于针对过程数据,通过预测可能的失效模式以避免维护性问题的活动。
预防性维护是指:为消除设备失效和生产的计划外中断的原因而策划的措施,作为制造过程设计的一项输出。
组织应识别关键过程设备,为机器/设备的维护提供资源,并建立有效的、有计划的全面预防性维护系统。
预防性维护的目的就是为生产提供稳定的设备。
检查表:编号检查内容1必须识别出关键设备。
控制阀细节分析之10_控制阀预测性维护
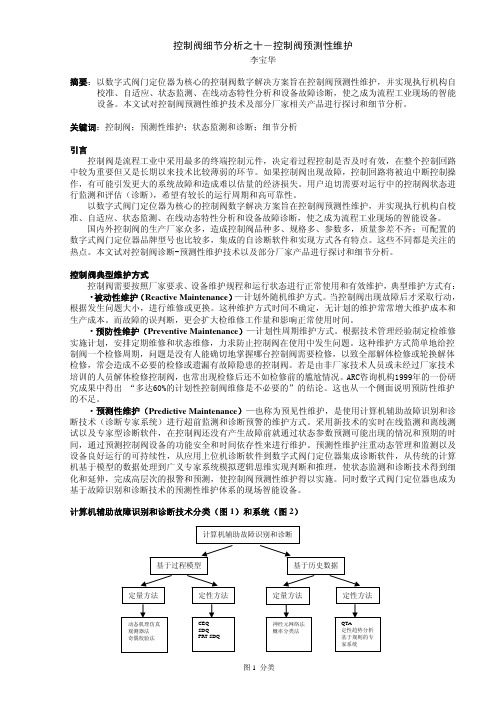
控制阀细节分析之十-控制阀预测性维护李宝华摘要:以数字式阀门定位器为核心的控制阀数字解决方案旨在控制阀预测性维护,并实现执行机构自校准、自适应、状态监测、在线动态特性分析和设备故障诊断,使之成为流程工业现场的智能设备。
本文试对控制阀预测性维护技术及部分厂家相关产品进行探讨和细节分析。
关键词:控制阀;预测性维护;状态监测和诊断;细节分析引言控制阀是流程工业中采用最多的终端控制元件,决定着过程控制是否及时有效,在整个控制回路中较为重要但又是长期以来技术比较薄弱的环节。
如果控制阀出现故障,控制回路将被迫中断控制操作,有可能引发更大的系统故障和造成难以估量的经济损失。
用户迫切需要对运行中的控制阀状态进行监测和评估(诊断),希望有较长的运行周期和高可靠性。
以数字式阀门定位器为核心的控制阀数字解决方案旨在控制阀预测性维护,并实现执行机构自校准、自适应、状态监测、在线动态特性分析和设备故障诊断,使之成为流程工业现场的智能设备。
国内外控制阀的生产厂家众多,造成控制阀品种多、规格多、参数多,质量参差不齐;可配置的数字式阀门定位器品牌型号也比较多,集成的自诊断软件和实现方式各有特点。
这些不同都是关注的热点。
本文试对控制阀诊断-预测性维护技术以及部分厂家产品进行探讨和细节分析。
控制阀典型维护方式控制阀需要按照厂家要求、设备维护规程和运行状态进行正常使用和有效维护,典型维护方式有:·被动性维护(Reactive Maintenance)—计划外随机维护方式。
当控制阀出现故障后才采取行动,根据发生问题大小,进行维修或更换。
这种维护方式时间不确定,无计划的维护常常增大维护成本和生产成本。
而故障的误判断,更会扩大检维修工作量和影响正常使用时间。
·预防性维护(Preventive Maintenance)—计划性周期维护方式。
根据技术管理经验制定检维修实施计划,安排定期维修和状态维修,力求防止控制阀在使用中发生问题。
预防性维护与预见性维护区别

一.设备点检、维护保养的区别是什么?设备点检的目的是为了发现设备异常或隐患,维护(保养)是为了保持设备规定状态所做的工作。
打个比方,你就容易理解了。
定期去牙科检查牙齿或自己不定期检查牙齿(蛀牙、颜色、刷痕磨损等),是点检;自己每天刷牙漱口是维护保养。
另外,根据《设备管理定义和术语》PMS/T 3 的解释,有助于你理解。
3.8 点检checking利用人体的感官(视、听、触、嗅、味)或借助工具、检测设备、仪器等,按照标准(定点、定标、定期、定法、定人“五定”)对设备进行检查或监测,发现设备劣化信息、故障隐患,分析原因并采取改善对策,利用维修窗口进行预防性维修,将设备隐患消灭在萌芽状态的一种管理方法。
注:点检是一种及时掌握设备运行状态,指导设备状态维修的一种科学的管理方法。
3.9 维护servicing为使设备保持规定状态(性能)所需采取的措施。
注:调整、紧固、清扫、润滑“八字”工作方针,是日常维护保养的重要基础工作内容。
3.10 设备维修equipment repair指设备技术状态劣化或发生故障后,为恢复其功能而进行的技术活动。
注1:设备维修,包括各类计划修理和计划外的故障修理及事故修理。
注2:维修模式:通常指一种模式或多种模式的组合,如:定期更换、预防维修、状态维修、事后维修、质量维修、绿色维修、组合维修等。
预防性维护与预见性维护区别汽车体系第一步:先看一下IATF16949标准中的描述7.5.1.4 预防性和预见性维护组织应识别关键过程设备,为机器/设备的维护提供资源,并建立有效的、有计划的全面预防性维护系统。
这个系统至少应包括:—有计划的维护活动;—设备、工装和量具的包装和防护;—可得到关键生产设备的零配件;—将维护目标形成文件并予以评价和改进。
组织应使用预见性维护方法,以持续改进生产设备的有效性和效率。
第二步:IATF16949标准中的定义3.1.7预见性维护predictive maintenance基于针对过程数据,通过预测可能的失效模式以避免维护性问题的活动。
预防性维护系列03-预测性维护
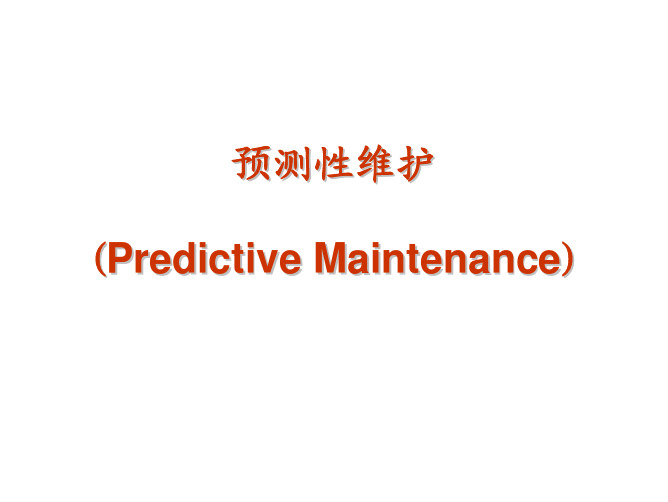
6 ˊDIY诊断仪器的开发 7 警戒值的决定与效果确认 8 依据保养月历实践计划性维护 10 操作人员施行简易的诊断教育 实现最低维护成本 9 为求落实而须实施的各种措施
预测性维护的实施步骤
(1)重大故障的解析
分析过去几年来发生的重大故障资料,选出需要进行预测性维护的 对象设备,并依据前述设备重要程度加以评估。
(10)对操作人员施以简易诊断的教育
为了让操作人员也能担任预测性维护的工作,可依自主维护的水准 程度,对操作人员施以简易诊断的教育与训练。
案例分析
状况监控的本质特征 系统 仪器及应用 培训和技能的提升
系统
LLF技术 - 检查图表/ 路线图 轴承状况监控 振动监控 润滑油状况监控 腐蚀监控 温度图 工艺条件监控
设备诊断技术 设备诊断的原理即寻找异常的原因,预测设 备故障的潜在时期。
点检指令 简易诊断 依计测值的趋势管理 诊断指令 精密诊断 依诊断决定复原时期 行动 再 点 检
设备诊断的机制
如何开展预测性维护
• 预测性维护的前提条件
(1)因自主保养、个别改善的推动,使得设备强制 劣化的现象消失,而只剩下自然劣化的状态。 (2)突发性故障减少,维护人员也学习到设备诊断 技术,这样便有了实践预防性维护的机会(机器、 时间等)。
设备诊断技术的开发
分四个步骤来进行:
(1)
锁定诊断部位 其设备的部位、 零件具有何种劣 化特性? 能否以物理量的 变化掌握其劣化 特性? 有无测定其变化 (劣化)的技 术?
•根据过去重大故障,来决定特
定部位
•是否随着时间经过有逐渐劣化
(2)
的现象?
•参数(物理量)为何? •如果振动的话,是偏移?是速
Байду номын сангаас训
【科普】预防性维护与预测性维护

【科普】预防性维护与预测性维护缘起预防性维护与预见性维护1、汽车行业质量管理体系 IATF16949:2016标准3.1.7 预见性维护 predictive maintenance 基于过程数据,通过预测可能的失效模式以避免维护性问题的活动。
3.1.8 预防性维护 prevention maintenance 为消除设备失效和生产的计划外中断的原因而策划的措施,作为制造过程设计的一项输出。
2、数据中心行业实践基本延用汽车行业的定义。
预防性维护:比较常见,也为国内大多数运维及相关人员所熟知。
通常由各零部件、设备、系统的厂家提出相关的固定周期的计划性维护。
部分优先运维团队,也根据自身实际运维经验进行了一些完善和修订。
其特点:一、固定周期,通常一次性制定全年甚至是多年的计划;二、通常仅以设备进行分类,较为优秀者通常会根据项目所在地区,维护团队实力,客户性质,等项目特点而进行适当调整;三、但往往与设备实际运行状态和数据无关。
针对的是一类产品、系统。
而非根据实际设备/产品实际运行状态/性能而特异定制的以制定项目中的指定产品为准的维护。
预见性维护:由于数据中心行业蓬勃发展,行业近年来广受关注,受益于技术进步,预见性维护近来备受重视。
预见性维护是以运行状态(性能)为依据的维修与维护,在设备/系统运行时,对它的主要(或需要)部位进行定期(或连续)的状态监测和故障诊断,判定设备/系统所处的状态,预测设备/系统状态未来的发展趋势,依据设备/系统的状态发展趋势和可能的故障模式,预先制定预测性维护计划,确定设备/系统应该保养/修理的时间、内容、方式和必需的技术和物资支持。
预测性维修集状态监测、故障诊断、故障(状态)预测、维修决策支持和维修活动于一体,结合大数据分析将成为数据中心行业的一种新兴的维护方式。
(早在1999年既已成为汽车行业标准维修方式)广义的预见性维护包含预防性维护,狭义的预见性维护一般排除了常规预防性维护。
预测性维护技术在工业领域中的应用

预测性维护技术在工业领域中的应用预测性维护技术(Predictive Maintenance)是一种可以预测机器或设备故障并进行预防性维护的技术。
这项技术通过结合航空天气气象学、数据分析、机器学习和物联网等新技术,提高了维护效率,减少了生产成本,降低了风险,为生产企业带来了新的机遇。
在过去,许多企业都采用“应急维护”策略来维护其机器和设备,这种策略通常是在机器或设备故障后再进行维护,导致了大量不必要的停机时间,无法发现潜在的故障,影响着生产线的正常运行。
而现在,预测性维护技术的出现,可以帮助企业更准确的预测和规避故障,从而避免生产线的中断和生产损失。
具体来说,预测性维护技术通过下面几个步骤来实现机器和设备的故障预测:第一步,收集数据。
机器和设备的运行数据以及环境数据被收集和存储。
这些数据包括温度、压力、振动、电流等。
第二步,数据分析。
通过数据分析,可以找出潜在的故障和偏移。
通过算法,计算机可以检测到故障的风险因素,以及提前预测故障的发生时间。
第三步,故障预测。
根据数据的预测结果,系统会生成预测性维护建议,以便将其传达给工作人员。
这样,他们就可以在机器或设备发生故障之前进行必要的维护工作。
第四步,在需要的时候采取行动。
当造成故障的风险足够高时,预测性维护系统向操作人员发出警告,并建议对机器或设备进行必要的维护。
这种方法可以避免突然故障,延长机械的寿命,确保工作的连续性。
自从预测性维护技术出现以来,它已经在很多领域得到了应用,特别是在制造业和工业领域。
许多汽车、航空、能源、医疗等都已经采用了这种技术。
例如,飞机发动机需要长时间的维护和检修,预测性维护技术可以通过监测发动机性能数据,并随时预测可能出现的故障并提前预防。
另外,预测性维护技术在石油和天然气行业中也非常受欢迎。
许多石油和天然气生产设备都需要24小时不间断运转,因此故障对生产的影响非常大。
通过使用预测性维护技术,可以在机器出现故障之前通过数据分析方法,预测可能出现的故障,从而保证设备的正常运行。
计划性维修的12种类型

计划性维修的12种类型英文回答:There are 12 types of planned maintenance that are commonly carried out in various industries. These types of maintenance are essential to ensure the smooth operation of equipment and facilities, as well as to prevent unexpected breakdowns and costly repairs. Let me explain each type of maintenance and provide some examples.1. Preventive Maintenance: This type of maintenance involves regularly scheduled inspections, cleaning, and servicing of equipment to prevent potential issues. For example, changing the oil and filters in a car every 5,000 miles is a form of preventive maintenance.2. Predictive Maintenance: This maintenance strategy uses data and analytics to predict when equipment failure is likely to occur. By monitoring parameters such as temperature, vibration, and pressure, maintenance can bescheduled before a breakdown happens. For instance, using sensors to monitor the temperature of a motor and scheduling maintenance when it exceeds a certain threshold.3. Corrective Maintenance: This type of maintenance is performed after a failure or breakdown has occurred. It involves repairing or replacing faulty components to restore the equipment's functionality. For example, replacing a blown fuse in an electrical circuit.4. Routine Maintenance: This maintenance involves regular tasks that are performed on a daily or weekly basis to keep equipment in good working condition. It includes activities such as cleaning, lubricating, and adjusting equipment. An example would be cleaning and lubricating the blades of a lawnmower after each use.5. Condition-based Maintenance: This type of maintenance relies on monitoring the condition of equipment to determine when maintenance is required. It involves using techniques such as vibration analysis, oil analysis, and thermography to assess the health of equipment. Forinstance, using thermography to detect hotspots in an electrical panel and scheduling maintenance to prevent overheating.6. Planned Maintenance: This maintenance is scheduled in advance based on factors such as equipment usage, manufacturer recommendations, and historical data. It ensures that maintenance tasks are carried out at regular intervals to prevent unexpected failures. An example would be scheduling a quarterly inspection of a manufacturing machine.7. Breakdown Maintenance: Also known as reactive maintenance, this type of maintenance is performed in response to a sudden equipment failure. It aims to quickly repair the equipment and minimize downtime. For example, calling a plumber to fix a burst pipe in a restaurant.8. Shutdown Maintenance: This maintenance involves shutting down a production line or facility to perform extensive maintenance tasks that cannot be done while the equipment is running. It often includes tasks such as majorequipment overhauls or replacement of critical components. An example would be shutting down an oil refinery toreplace a large-scale processing unit.9. Emergency Maintenance: This type of maintenance is performed in urgent situations that require immediate attention to prevent safety hazards or further damage. It often involves temporary repairs to restore functionality until a permanent solution can be implemented. For instance, patching a leaking roof during a heavy rainstorm.10. Overhaul Maintenance: This maintenance involves a complete disassembly, inspection, repair, and reassembly of equipment. It is typically done at specified intervals or when the equipment reaches a certain operating hour threshold. An example would be overhauling an aircraft engine after a certain number of flight hours.11. Planned Replacement: This type of maintenance involves replacing equipment or components at predetermined intervals to avoid unexpected failures. It is based on factors such as equipment lifespan, manufacturerrecommendations, and maintenance history. For example, replacing the tires on a car every 50,000 miles.12. Reliability-centered Maintenance: This maintenance strategy focuses on identifying and addressing the most critical failure modes that can lead to equipment breakdowns. It involves analyzing failure data,prioritizing maintenance tasks, and implementing proactive measures to improve reliability. An example would be conducting a failure mode and effects analysis (FMEA) to identify potential failure modes in a manufacturing process and implementing preventive measures.中文回答:计划性维修有12种常见类型,广泛应用于各行各业。
如何执行预防性维修维护与预见性维修维护
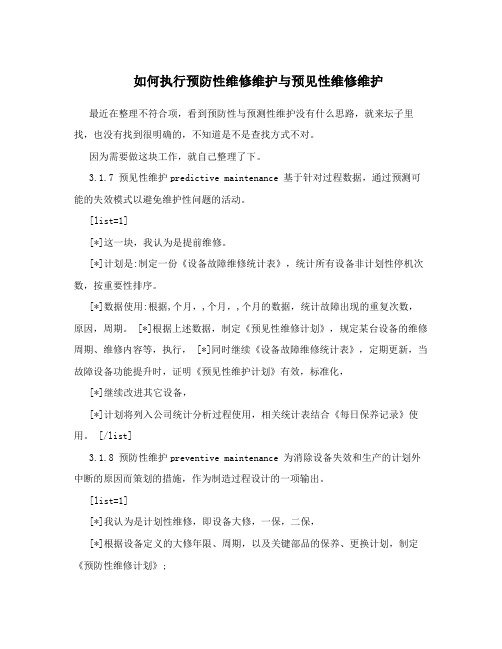
如何执行预防性维修维护与预见性维修维护最近在整理不符合项,看到预防性与预测性维护没有什么思路,就来坛子里找,也没有找到很明确的,不知道是不是查找方式不对。
因为需要做这块工作,就自己整理了下。
3.1.7 预见性维护predictive maintenance 基于针对过程数据,通过预测可能的失效模式以避免维护性问题的活动。
[list=1][*]这一块,我认为是提前维修。
[*]计划是:制定一份《设备故障维修统计表》,统计所有设备非计划性停机次数,按重要性排序。
[*]数据使用:根据,个月,,个月,,个月的数据,统计故障出现的重复次数,原因,周期。
[*]根据上述数据,制定《预见性维修计划》,规定某台设备的维修周期、维修内容等,执行, [*]同时继续《设备故障维修统计表》,定期更新,当故障设备功能提升时,证明《预见性维护计划》有效,标准化,[*]继续改进其它设备,[*]计划将列入公司统计分析过程使用,相关统计表结合《每日保养记录》使用。
[/list]3.1.8 预防性维护preventive maintenance 为消除设备失效和生产的计划外中断的原因而策划的措施,作为制造过程设计的一项输出。
[list=1][*]我认为是计划性维修,即设备大修,一保,二保,[*]根据设备定义的大修年限、周期,以及关键部品的保养、更换计划,制定《预防性维修计划》;[*]定期执行维修保养;[*]为了避免《预防性维修计划》与《预见性维修计划》的冲突,两者中发生冲突的内容及时修订;如《预防性维修计划》里要求,个月换转子,但是《预见性维修计划》要求70天更换,则取消《预防性维修计划》里要求;[*]以年度为基础,更新《预防性维修计划》。
[/list]因系自学,错误时请指正。
- 1、下载文档前请自行甄别文档内容的完整性,平台不提供额外的编辑、内容补充、找答案等附加服务。
- 2、"仅部分预览"的文档,不可在线预览部分如存在完整性等问题,可反馈申请退款(可完整预览的文档不适用该条件!)。
- 3、如文档侵犯您的权益,请联系客服反馈,我们会尽快为您处理(人工客服工作时间:9:00-18:30)。
预防性维护与预见性维护
汽车体系
7.5.1.4 预防性和预见性维护
组织应识别关键过程设备,为机器/设备的维护提供资源,并建立有效的、有计划的全面预防性维护系统。
这个系统至少应包括:
--有计划的维护活动;
--设备、工装和量具的包装和防护;
--可得到关键生产设备的零配件;
-将维护的目标形成文件并予以评价和改进。
组织应使用预见性维护方法,以持续改进生产设备的有效性和效率。
第二步:TS标准中定义
3.1.7
预见性维护predictive maintenance
基于针对过程数据,通过预测可能的失效模式以避免维护性问题的活动。
3.1.8
预防性维护preventive maintenance
为消除设备失效和生产的计划外中断的原因而策划的措施,作为制造过程设计的一项输出。
第三步:现实问题
预防性维护是指有计划的定期设备维护和零配件更换,通常包括保养维护、定期使用检查、定期功能检测、定期拆修、定时更换等到几种
类型;
预见性预护是通过运用各种手段和人的感觉进行数据和信号的采集、分析和判断设备的劣化趋势、故障部位、原因并预测变化发展、提出防范措施,防止和控制可能的故障出现。