QSB标准化操作(ppt文档)
合集下载
QSB 2009 (Chinese Version) 标准化的操作员培训

装配区
发运/收货 其它支持职能
3
职责:
• 负责人: 生产经理 • 针对各种异常状况的应急计划
Quality Systems Basics rev March 2009
Global Purchasing and Supply Chain
FR
PS
NCP
VS
WPO
SWI (SOS)
OI(JES)
SOT(JIT)
• 第四步:跟踪
• •
• • • • • •
验证受训员工的工作能力 (在节拍时间TT内符合质量标准) 让受训员工展示对以下方面的理解和能力: 安全要求 标准化操作 质量要求 培训师完成质量检验 如适用,每个工作最少完成15件 让受训员工独立进行操作 告诉受训员工向谁寻求帮助 (例如主管,问题解决者,过程控制经 理,质量代表或专员等) 制定检查频次 鼓励员工提问 如果需要,提供任何附加的培训
阅读 听词语 被动的 看图片 观看电影 观看示范
我们参与的程度
口头的接收
视觉接收
•通过说能记住70%
讨论或演讲
接受和参与
主动的
•通过说和做能记住90%
做示范或模拟 做
Quality Systems Basics rev March 2009
FR
PS
NCP
VS
WPO
SWI (SOS)
OI(JES)
SOT(JIT)
OPERATIONS
Operator 1 Work Instructions - Min. 16 Hrs. Operator 3 Work Instructions - Min. 16 Hrs. Packaging Requirements (Regular / Service)
QSB-01快速响应(ppt文档)
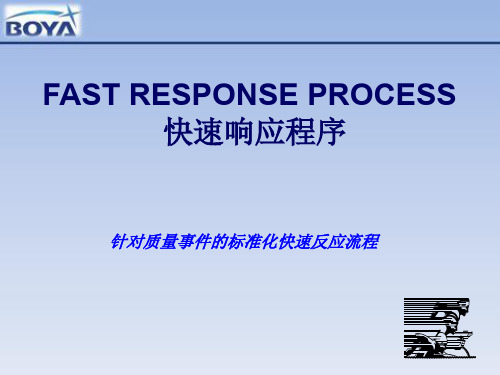
FAST RESPONSE PROCESS 快速响应程序
针对质量事件的标准化快速反应流程
QSB模块
重大质量事件沟通管理
快
不
岗
标
标
风
防
分
污
供
合
准准
染
应
速 格品问 位题 化解 化的决 险
错
层
物
链
响
验
操
操
降
验
审
控
作
控
管
应
制
证
作
员
低
证
核
制
理
经 验 教 培训训
快速响应
• 快速响应是一个系统,用于:
- 对重大的外部/内部质量问题的反应进行标准化 - 通过每天的会议增强沟通和问题解决 - 对重要的信息实现目视化管理
快速响应
为了准备快速响应会议,每天开始,质量人员必须确 定在最近24小时内发生的重大质量问题,包括
- 验证岗位*发现的问题 - 过程分层审核*中发现的问 题 - 停线问题 - 其他的内部质量问题(出货 审核, 产品遏制行动等) 一次下线合格率数据(FTQ, First Time Quality)
快速响应
应该按照快速响应跟踪板上的时间表向管理层汇报
快速响应跟踪板应该作为目视化管理的一部分在会议室进 行张贴
快速响应跟踪板 (例)
未关闭的PRR 列表 11 x 17
白板两面的结构: 2) 4’ x 8’ x ¾” 木板.
2) 48” 图表区 2) 4’ x 8’ x ¼” 有机玻璃
快速反应会议签到表 8 ½ x 11
列出所有导致问题发生的事情,使用系统性的 方法来识别和验证其中的根本原因Root cause
针对质量事件的标准化快速反应流程
QSB模块
重大质量事件沟通管理
快
不
岗
标
标
风
防
分
污
供
合
准准
染
应
速 格品问 位题 化解 化的决 险
错
层
物
链
响
验
操
操
降
验
审
控
作
控
管
应
制
证
作
员
低
证
核
制
理
经 验 教 培训训
快速响应
• 快速响应是一个系统,用于:
- 对重大的外部/内部质量问题的反应进行标准化 - 通过每天的会议增强沟通和问题解决 - 对重要的信息实现目视化管理
快速响应
为了准备快速响应会议,每天开始,质量人员必须确 定在最近24小时内发生的重大质量问题,包括
- 验证岗位*发现的问题 - 过程分层审核*中发现的问 题 - 停线问题 - 其他的内部质量问题(出货 审核, 产品遏制行动等) 一次下线合格率数据(FTQ, First Time Quality)
快速响应
应该按照快速响应跟踪板上的时间表向管理层汇报
快速响应跟踪板应该作为目视化管理的一部分在会议室进 行张贴
快速响应跟踪板 (例)
未关闭的PRR 列表 11 x 17
白板两面的结构: 2) 4’ x 8’ x ¾” 木板.
2) 48” 图表区 2) 4’ x 8’ x ¼” 有机玻璃
快速反应会议签到表 8 ½ x 11
列出所有导致问题发生的事情,使用系统性的 方法来识别和验证其中的根本原因Root cause
WinQSB的基本操作 ppt课件
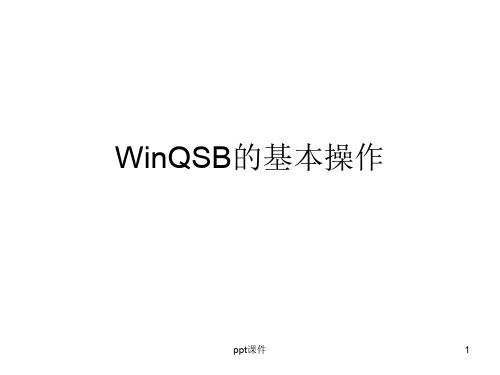
制
产量、需求量、存储费用、生产费用等
复杂的整体综合生产计划的编制方法,
将问题归结到求解线性规划模型或运输
模型
DA
决策分析 确定型与风险型决策、贝叶斯决策。决
策树、二人零和对策。蒙特卡罗模拟
DP
动态规划 最短路问题、背包问题、生产与存储
FLL
设备场地布 设备场地设计、功能布局、线路均衡布
局
局
FC
预测与线性 简单平均、移动平均、加权移动平均、
求解线性约束、目标函数是 二次型的一种非线性规划问 题,变量可以取整数
各种排队模型的求解与性能 分析、15种分布模型、灵敏 度分析、服务能力分析、成 本分析
未知到达和服务时间分布、 一般排队系统模拟计算
建立各种质量控制图质量分 析
ppt课件
6
二、How to install
• WinQSB的安装比较简单。
WinQSB的基本操作
ppt课件
1
CONTENT
• 一、Introduction to WinQSB • 二、How to install • 三、Using LP-ILP
ppt课件
2
一、Introduce to WinQSB
• QSB是Quantitative Systems for Business的缩写, WinQSB是QSB的Windows版本,可以在Windows2000 /XP平 台下运行。
19 Quality Control Charts
NLP 非线性规划
PERT- 网络计划 CPM
QP
二次规划
QA
排队分析
QSS 排队系统模 拟
QCC 质量管理控 制图
有(无)条件约束、目标函 数或约束条件非线性,目标 函数与约束条件都非线性等 规划的求解与分析
QSB_sample

W.E. Deming,
Ningbo Cable QSB Workshop
1992/07/15
12
S-1: 整理 – 区分必需和非必需品,移走非必需品。
关注物品: 设备、工具、库存、个人物品
改善前
Ningbo Cable QSB Workshop
改善后
13
S-2: 整顿
– 物有其所,物在其位
改善前
7
通过标识将产品的各种质量状态明了地标识出来
宁波华骏机械有限公司 标题 不合格标识管理办法
文件编号 版本 页次 HJ-WI-QM09-2007 A/0 第1 页 共2页
宁波华骏机械有限公司 标题 不合格标识管理办法
一、生产现场使用
1、装配线全检员和作业员工发现不良,在缺陷部位贴红色(报废品)或黄色(返工/返修等)色带 黄色色带 红色色带
问题解决和沟通
Ningbo Cable QSB Workshop
2
标准化的现场会议是有效沟通的途径和快速解决问题的方法
Ningbo Cable QSB Workshop
3
快速反应跟踪板上的信息使人一目了然看到各种问题的现行状态
Ningbo Cable QSB Workshop
EXIT CRITERIA STATUS KEY R Required but not initiated Y Initiated but not com plete G Com plete N/A Not Applicable
.
合格标识 检验员: 日 期:
. .
. . .
不合格品标识卡
. .
检验员: 日期:
HJ/QP/7.5.3/0706/05
A/0
Ningbo Cable QSB Workshop
1992/07/15
12
S-1: 整理 – 区分必需和非必需品,移走非必需品。
关注物品: 设备、工具、库存、个人物品
改善前
Ningbo Cable QSB Workshop
改善后
13
S-2: 整顿
– 物有其所,物在其位
改善前
7
通过标识将产品的各种质量状态明了地标识出来
宁波华骏机械有限公司 标题 不合格标识管理办法
文件编号 版本 页次 HJ-WI-QM09-2007 A/0 第1 页 共2页
宁波华骏机械有限公司 标题 不合格标识管理办法
一、生产现场使用
1、装配线全检员和作业员工发现不良,在缺陷部位贴红色(报废品)或黄色(返工/返修等)色带 黄色色带 红色色带
问题解决和沟通
Ningbo Cable QSB Workshop
2
标准化的现场会议是有效沟通的途径和快速解决问题的方法
Ningbo Cable QSB Workshop
3
快速反应跟踪板上的信息使人一目了然看到各种问题的现行状态
Ningbo Cable QSB Workshop
EXIT CRITERIA STATUS KEY R Required but not initiated Y Initiated but not com plete G Com plete N/A Not Applicable
.
合格标识 检验员: 日 期:
. .
. . .
不合格品标识卡
. .
检验员: 日期:
HJ/QP/7.5.3/0706/05
A/0
QSB基础培训课件

在快速反应会议时,管理层必须:
- 如果问题还没有负责人,则指定一个负责人。 - 审核相应的文件。 - 如果问题没有关闭,指定下次汇报时间。
负责人必须确保能按时完成所有退出标准所要求的项目,将问题解决。
10
快速响应
快 速 反 应: 报 告 模 式
11
快速响应
• 在开会之前,问题的负责人必须将新发生的问题添加到快速反应跟踪 板中(如果是供应商的问题,写明其负责人的联系方式).
12
快速响应 • 负责人汇报必须包括问题解决报告PPSR中的更新:
- 问题定义,遏制阶段 - 根本原因分析(5-Why) - 短期/长期纠正措施 - 验证和经验教训 • 负责人必须负责保证所有的问题解决和退出项目能按时完成。
- 更新快速反应跟踪板中相关项目的状态。 - 将有关的更新文件及时发给团队成员或关键的联系人。
3、提交部门遏制措施返工单确保初始的各部门返工区域得到检查。
4、对于跨部门的遏制措施,返工单应该发布到涉及到可疑零件的每个部门 以保证断点有效。
15
不合格品控制
5、对于产品遏制措施,所有产品的包装箱标示要相应地和过程匹配(断点 后用绿色标签,可疑和不合格品用黄色和红色标签)。 6、对于产品遏制措施,断点的持续性应该由区域工程师或其指派人验证。 7、从正常生产线隔离的产品重新返回生产线时,应该从隔离点或之前工序 进入,以保证对该零件进行所有的控制措施/试验。 8、制造区域应该清楚的定义返工、返修、遏制区产品的流程/授权。 9、对于产品遏制措施,管理层应该在遏制措施完成的基础上评审其结果。
PLT002
黄色标签用于需要返工,需要 重新检查或可疑的产品/料箱 标签必须显示最后的工位,以 保证重新导入生产时回到正确 工位。
- 如果问题还没有负责人,则指定一个负责人。 - 审核相应的文件。 - 如果问题没有关闭,指定下次汇报时间。
负责人必须确保能按时完成所有退出标准所要求的项目,将问题解决。
10
快速响应
快 速 反 应: 报 告 模 式
11
快速响应
• 在开会之前,问题的负责人必须将新发生的问题添加到快速反应跟踪 板中(如果是供应商的问题,写明其负责人的联系方式).
12
快速响应 • 负责人汇报必须包括问题解决报告PPSR中的更新:
- 问题定义,遏制阶段 - 根本原因分析(5-Why) - 短期/长期纠正措施 - 验证和经验教训 • 负责人必须负责保证所有的问题解决和退出项目能按时完成。
- 更新快速反应跟踪板中相关项目的状态。 - 将有关的更新文件及时发给团队成员或关键的联系人。
3、提交部门遏制措施返工单确保初始的各部门返工区域得到检查。
4、对于跨部门的遏制措施,返工单应该发布到涉及到可疑零件的每个部门 以保证断点有效。
15
不合格品控制
5、对于产品遏制措施,所有产品的包装箱标示要相应地和过程匹配(断点 后用绿色标签,可疑和不合格品用黄色和红色标签)。 6、对于产品遏制措施,断点的持续性应该由区域工程师或其指派人验证。 7、从正常生产线隔离的产品重新返回生产线时,应该从隔离点或之前工序 进入,以保证对该零件进行所有的控制措施/试验。 8、制造区域应该清楚的定义返工、返修、遏制区产品的流程/授权。 9、对于产品遏制措施,管理层应该在遏制措施完成的基础上评审其结果。
PLT002
黄色标签用于需要返工,需要 重新检查或可疑的产品/料箱 标签必须显示最后的工位,以 保证重新导入生产时回到正确 工位。
QSB标准化操作

QSB Workshop REV.10
Time
60” 50”
节拍时间CYCLE TIME
Takt Time 60” 实际Actual Takt Time 56”
生产节拍Cycle Time 52”
40”
定义Definition:
一个团队完成所有工作
30”
所需实际时间The actual time it takes a
QSB WORKSQHSOBPWREOVR.K0S9H13O0P4REV. 062705 15
15
QSB Workshop REV.10
通
用 客户要求-需求
总 392 辆车/每班
装 实际生产汽车可用时间
厂 480 分钟-休息&用餐
l
=435分钟可用于生产汽车
客 TT=435分钟/392辆×60秒
户 =66.5秒 如果没有系统性时间损失,66.5秒生产
工作流WORK FLOW
在布局图上适当的位置标图标Place symbols on the layout as appropriate:
– 安全Safety
如工作要素表As Indicated on Job Element Sheet
– 质量检验100%测量/测试
Quality Check100% Gauging /
2
QSB Workshop REV.10
标准化工作中的分工
组员
小组成员在标准化操作中的角色
Team Leader Group Leader
• 参与标准化工作的制定,并提供意见 • 对标准化工作提供改进意见 • 向组长反馈标准化执行情况 • 将标准化作为问题解决和培训的基础 • 执行标准化操作
Time
60” 50”
节拍时间CYCLE TIME
Takt Time 60” 实际Actual Takt Time 56”
生产节拍Cycle Time 52”
40”
定义Definition:
一个团队完成所有工作
30”
所需实际时间The actual time it takes a
QSB WORKSQHSOBPWREOVR.K0S9H13O0P4REV. 062705 15
15
QSB Workshop REV.10
通
用 客户要求-需求
总 392 辆车/每班
装 实际生产汽车可用时间
厂 480 分钟-休息&用餐
l
=435分钟可用于生产汽车
客 TT=435分钟/392辆×60秒
户 =66.5秒 如果没有系统性时间损失,66.5秒生产
工作流WORK FLOW
在布局图上适当的位置标图标Place symbols on the layout as appropriate:
– 安全Safety
如工作要素表As Indicated on Job Element Sheet
– 质量检验100%测量/测试
Quality Check100% Gauging /
2
QSB Workshop REV.10
标准化工作中的分工
组员
小组成员在标准化操作中的角色
Team Leader Group Leader
• 参与标准化工作的制定,并提供意见 • 对标准化工作提供改进意见 • 向组长反馈标准化执行情况 • 将标准化作为问题解决和培训的基础 • 执行标准化操作
通用QSB质量系统基础学习资料ppt课件

Yes No
2 Correct Tools / Fixtures / Error Proofing?
3 Correct Parts?
4 Parts in spec?
Countermeasure ______________________________________ _____________________________________________________ _____________________________________________________
Quality Systems Basics
质量体系基础
This presentation was developed by General Motors Corporation Worldwide Purchasing. All rights reserved. No part of this material may be reproduced in any form, or by any method, for any purpose, without written permission of General Motors Worldwide Purchasing.
Correct Part?
Quality Sys / SQ / Supplier
4
Parts Quality?
2 – 工具是否正确
(例)
以下原因是否会导致问题的发生?
• (所有班次)是否使用正确的工具和夹具? • 工具是否按照规定要求设定? • 工具是否经过校验? • 不同的班次是否使用相同的工具? • 工具是否磨损? • 工具和夹具是否具有防护装置以防损坏? • 工位是否有防错装置? • 工具或防错装置是否有效? • 工位布局是否有利于操作员操作? • 预防性维护是否按时完成? (检查记录) • 工具的功能是否正确?
GQS02-QSB中文版-标准化作业
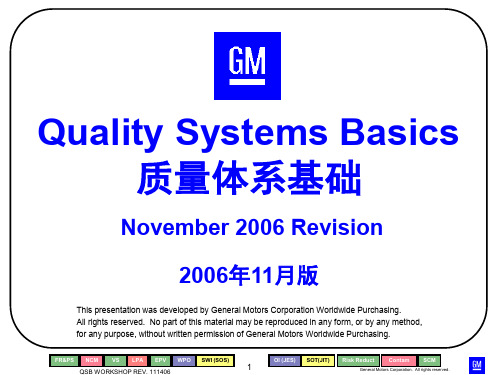
– 超负荷 Overburden (MURI)
– 不均衡 Unevenness (MURA)
正是这三个敌人阻止我们到达目标!我们的主要目的就是通过持续改 进来消灭这三个敌人!
FR&PS NCM VS LPA EPV WPO SWI (SOS)
QSB WORKSHOP REV. 111406
9
OI (JES) SOT(JIT)
QSB WORKSHOP REV. 111406
14
OI (JES) SOT(JIT)
Risk Reduct
Contam
SCM
General Motors Corporation. All rights reserved.
PC
I
O
TYPES
OF
WASTE
W
M
M
库存
定 义: 所有多余的东西,
会占用空间、产生报废、影响 安全,导致动作的浪费和物料 移动的浪费。
QSB WORKSHOP REV. 111406
11
OI (JES) SOT(JIT)
Risk Reduct
Contam
SCM
General Motors Corporation. All rights reserved.
PC
I
O
TYPES
OF
WASTE
W
M
M
动作
定 义: 不会增加产品价值的
,不必要的人员或机器的动作。
在完成工作过程中,所有不必要的步骤都是浪费。包括等待,重新整理 物料,寻找物品,不必要的走动等。
FR&PS NCM VS LPA EPV WPO SWI (SOS)
QSB WORKSHOP REV. 111406
– 不均衡 Unevenness (MURA)
正是这三个敌人阻止我们到达目标!我们的主要目的就是通过持续改 进来消灭这三个敌人!
FR&PS NCM VS LPA EPV WPO SWI (SOS)
QSB WORKSHOP REV. 111406
9
OI (JES) SOT(JIT)
QSB WORKSHOP REV. 111406
14
OI (JES) SOT(JIT)
Risk Reduct
Contam
SCM
General Motors Corporation. All rights reserved.
PC
I
O
TYPES
OF
WASTE
W
M
M
库存
定 义: 所有多余的东西,
会占用空间、产生报废、影响 安全,导致动作的浪费和物料 移动的浪费。
QSB WORKSHOP REV. 111406
11
OI (JES) SOT(JIT)
Risk Reduct
Contam
SCM
General Motors Corporation. All rights reserved.
PC
I
O
TYPES
OF
WASTE
W
M
M
动作
定 义: 不会增加产品价值的
,不必要的人员或机器的动作。
在完成工作过程中,所有不必要的步骤都是浪费。包括等待,重新整理 物料,寻找物品,不必要的走动等。
FR&PS NCM VS LPA EPV WPO SWI (SOS)
QSB WORKSHOP REV. 111406
qf-qsb-04_qsb_标准化作业(sos-jes)流程

责任工程 师
1,每月统计、分析、总结有关标准化作业开发和维 护的流程有效性和经验总结。
2,过程绩效可能是:标准化作业一次审批会签通过 率等。
责 任 工 程 1、记录包括:【部门作业指导书目录】、【系统文
师
件评审及行动计划验证记录】、【标准化作业指
导书 SOS/JES】等
6.记录
部门作业指导书目录,QF-QSB-0401 系统文件评审及行动计划验证记录,QF-QSB-0402
要素时间和作业员移动轨迹、目视化。按照工序流程图,每一工序必须开发 SOS,并张贴在工 作现场的工序附近,易于作业员清晰看到。
3.3 JES:工作要素指导书,其“3+1”指的是:主要作业步骤、作业要点及其原因、目视化。 它是 SOS 的补充,往往是针对复杂的、关键的主要作业要素进行的详细阐述。
4.职责 (见流程图)
某天,我问起他们公司的快递员,小伙子说老板去上海了,在上海开了家新公司。我很杞人忧天地问 他:“那上海的市场不激烈吗?新快递怎么驻足啊!”小伙子嘿嘿一笑说:“我们老板肯定有办法呗!他都过 去好几个月了,据说干得很不错呢!”“那老婆孩子呢?孩子不是刚生还很小吗?”“过去了,一起去上海了!”
那个瞬间,我回头看了一眼办公室里坐着的各种愁眉苦脸的同事,并且举起手机黑屏幕照了一下我自 己的脸,一股“人生已经如此的艰难,有些事情就不要拆穿”的气息冉冉升起。并不是说都跳槽出去开公司才 厉害,在公司瞪着眼睛看屏幕就是没发展,我是想说,只有勇气才能让自己作出改变。
我们每个人都觉得自己越活越内向,越来越自闭,越长大越孤单,以至于滋生了“换个新环境,我这种 性格估计也不会跟其他人相处融洽,所以还是待着忍忍凑合过算了”的思想感情。与其说自己自闭,其实就 是懒,不想突破自己好不容易建立起来的安全区域。于是大家都活在了对别人的羡慕嫉妒恨与吐槽抱怨生 活不得志中,搞得刚毕业的学生都活得跟 30 岁一样。
QSB+ 标准化作业 模块推广.pptx

3)注塑车间安全生产操作规程 SCD-ZS-014
差距分析 车间安全检查表没有文件编号
措施
1)完善车间安全检查表,编号纳 入程序文件 2)按文件归档进行
定期安全检查
条款负责人 赵建光
2) 工 位 的 布 局 和 设 计 考 虑 到 安 全 因 素 , 以 避 免 潜 在 SW1
的安全风险
耿彦卿
明确车间LAYOUT
要求简述
工作环境安全
是否存在差 距
主要差距总结
是
存在安全隐患
SW2
工作环境整洁
是
车间5S活动开展 不到位
作业指导文件太简单,和标准要求差
SW3
标准化作业指导书
是
距较大。
SW4
生产启动的流程
是
设备工装使用作业文件不明确
SW5
样件管理
SW6
检验计量设备的
测量系统能力
是
生产用的封样没有建立台账
是
没有测试设备的MSA
二、修订了工装设备点检表和点检作业指导书(共30份)
Do
Slide 27
模块实施内容及输出---封样件、测量系统计量器具管理
封样件
u生产线需要使用样件校验的防错设备:共3套,所需样件:合格样件和不合格样件。
u建立了《封样件管理办法》。
Check
测量系统及计量器具
u建立了《计量器具管理规定》;《监视和测量控制程序》。
u有2016年计量器具校准计划
Do
u有测量设备的重复性再现性分析。
Slide 28
模块实施内容及输出
名称 1、5S管理规范 2、QSB+宣传看板 3、标准化作业 4、生产启动作业(刘工) 5、修订后的《生产装备控制程序》 6、计量器具管理规定 7、监视和测量控制程序 8、MSA分析
差距分析 车间安全检查表没有文件编号
措施
1)完善车间安全检查表,编号纳 入程序文件 2)按文件归档进行
定期安全检查
条款负责人 赵建光
2) 工 位 的 布 局 和 设 计 考 虑 到 安 全 因 素 , 以 避 免 潜 在 SW1
的安全风险
耿彦卿
明确车间LAYOUT
要求简述
工作环境安全
是否存在差 距
主要差距总结
是
存在安全隐患
SW2
工作环境整洁
是
车间5S活动开展 不到位
作业指导文件太简单,和标准要求差
SW3
标准化作业指导书
是
距较大。
SW4
生产启动的流程
是
设备工装使用作业文件不明确
SW5
样件管理
SW6
检验计量设备的
测量系统能力
是
生产用的封样没有建立台账
是
没有测试设备的MSA
二、修订了工装设备点检表和点检作业指导书(共30份)
Do
Slide 27
模块实施内容及输出---封样件、测量系统计量器具管理
封样件
u生产线需要使用样件校验的防错设备:共3套,所需样件:合格样件和不合格样件。
u建立了《封样件管理办法》。
Check
测量系统及计量器具
u建立了《计量器具管理规定》;《监视和测量控制程序》。
u有2016年计量器具校准计划
Do
u有测量设备的重复性再现性分析。
Slide 28
模块实施内容及输出
名称 1、5S管理规范 2、QSB+宣传看板 3、标准化作业 4、生产启动作业(刘工) 5、修订后的《生产装备控制程序》 6、计量器具管理规定 7、监视和测量控制程序 8、MSA分析
标准化操作ppt课件
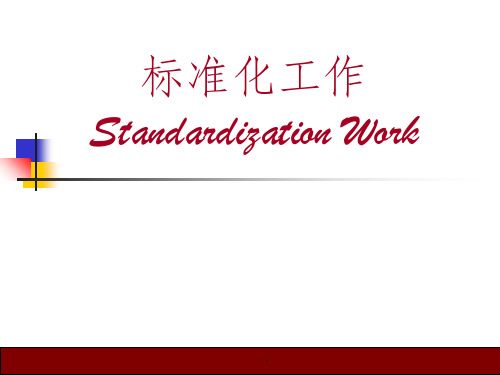
▪ TAKT Time:依据顾客需求为某一零件或总成 生产所应花的时间 ▪ Observed Cycle Time,OCT:操作者实际的 节拍时间
.
节拍时间(TAKT Time)
TAKT Time=
每班或每天的实际操作时间/每班或每天的客户需求量
例:每天一班实际操作时间是7小时10分钟 顾客要求一天600件产品
自动运送 -------------
--
80
1 ´ 00´´ 655
20
30´´
549
20
30´´
606
20
30´´
643
1,000 1,000
7 ´ 00´´ 820 7 ´ 00´´
500 5 ´ 00´´ 1947
.
能力表的编制说明
用秒表测定零部 件的完成时间
1. 工位顺序
2. 工序名称
3. 使用的机床编号
.
标准化工作的目标
通过有效率的劳动提高生产率 1. 通过热心的劳动实现较高的生产率 2. 实现与适时生产有关的各工序间的同步化(生产线平衡)
,为此,必须将“生产节拍”很好地贯穿到标准作业中去 3. 把在制品“标准在库量”限定在必要的最小数量
.
标准化工作的好处
1. 避免无效的动作,消除浪费,降低成本 2. 改善质量 3. 确保安全 4. 为持续改进提供基础 5. 使新人员的培训更为容易 6. 提供可视化管理控制
标准作 业顺序
TAKT Time
Work
Customer Cycle Time Sequence
.
标准 持有量
Standard Stock
确定标准作业的五个程序
❖ 确定周期时间 ❖ 确定一个单位产品的完成时间 ❖ 确定标准作业顺序 ❖ 确定在制品的标准持有量 ❖ 编制标准作业单
.
节拍时间(TAKT Time)
TAKT Time=
每班或每天的实际操作时间/每班或每天的客户需求量
例:每天一班实际操作时间是7小时10分钟 顾客要求一天600件产品
自动运送 -------------
--
80
1 ´ 00´´ 655
20
30´´
549
20
30´´
606
20
30´´
643
1,000 1,000
7 ´ 00´´ 820 7 ´ 00´´
500 5 ´ 00´´ 1947
.
能力表的编制说明
用秒表测定零部 件的完成时间
1. 工位顺序
2. 工序名称
3. 使用的机床编号
.
标准化工作的目标
通过有效率的劳动提高生产率 1. 通过热心的劳动实现较高的生产率 2. 实现与适时生产有关的各工序间的同步化(生产线平衡)
,为此,必须将“生产节拍”很好地贯穿到标准作业中去 3. 把在制品“标准在库量”限定在必要的最小数量
.
标准化工作的好处
1. 避免无效的动作,消除浪费,降低成本 2. 改善质量 3. 确保安全 4. 为持续改进提供基础 5. 使新人员的培训更为容易 6. 提供可视化管理控制
标准作 业顺序
TAKT Time
Work
Customer Cycle Time Sequence
.
标准 持有量
Standard Stock
确定标准作业的五个程序
❖ 确定周期时间 ❖ 确定一个单位产品的完成时间 ❖ 确定标准作业顺序 ❖ 确定在制品的标准持有量 ❖ 编制标准作业单
标准化操作-070816

7种浪费
超负荷
不均衡
SDE Module 2007.08
SGM Confidential
6
七种浪费
QSB-标准化操作
表 现: 使用额 外的资源进行返工 返修;企业处于被 动的状态.
主要原因: 缺乏培 训;工具不足;过 量库存等。
Processing Correction 过度加工 纠正
Inventory 库存
Waiting 等待
7种 浪费
OverProduction 过量生产
Motion 多余动作
Material
Movement 物料移动
定 义:需要额外
动作、额外加工 、额外库存和等 待的返工工作。 所有的修理工作 都是消除浪费的 机会。
SDE Module 2007.08
SGM Confidential
QSB-标准化操作
Standardized Operation 标准化操作
2007.8.16
安全、干净、有序、合理
SDE Module 2007.08
SGM Confidential
1
QSB模块
QSB-标准化操作
快
不
岗
标
标
风
防
分
污
供
合
准准
染
应
速
格
位
化
化
险
错
层
物
链
品
的
响
验
操
操
降
验
审
控
作
控
管
应
制
证
作
员
主要原因: 操作场地 布局不合理;没有很 好地制定或执行标准 化操作。
超负荷
不均衡
SDE Module 2007.08
SGM Confidential
6
七种浪费
QSB-标准化操作
表 现: 使用额 外的资源进行返工 返修;企业处于被 动的状态.
主要原因: 缺乏培 训;工具不足;过 量库存等。
Processing Correction 过度加工 纠正
Inventory 库存
Waiting 等待
7种 浪费
OverProduction 过量生产
Motion 多余动作
Material
Movement 物料移动
定 义:需要额外
动作、额外加工 、额外库存和等 待的返工工作。 所有的修理工作 都是消除浪费的 机会。
SDE Module 2007.08
SGM Confidential
QSB-标准化操作
Standardized Operation 标准化操作
2007.8.16
安全、干净、有序、合理
SDE Module 2007.08
SGM Confidential
1
QSB模块
QSB-标准化操作
快
不
岗
标
标
风
防
分
污
供
合
准准
染
应
速
格
位
化
化
险
错
层
物
链
品
的
响
验
操
操
降
验
审
控
作
控
管
应
制
证
作
员
主要原因: 操作场地 布局不合理;没有很 好地制定或执行标准 化操作。
- 1、下载文档前请自行甄别文档内容的完整性,平台不提供额外的编辑、内容补充、找答案等附加服务。
- 2、"仅部分预览"的文档,不可在线预览部分如存在完整性等问题,可反馈申请退款(可完整预览的文档不适用该条件!)。
- 3、如文档侵犯您的权益,请联系客服反馈,我们会尽快为您处理(人工客服工作时间:9:00-18:30)。
Operations, Engineering, Safety
包括支持人员在内的每个员工的主要职责是全力支持生产线员工工作。
QSB WORKSQHSOBPWREOVR.K0S9H13O0P4REV. 062705 3
3
QSB Workshop REV.10
标准化操作
标准化操作为以下的目标提供基础:
FROM:___________________________ TO: _____________________________
ELEMENT TIME
HAND WORK MACHINE WALK
QUANTITY PER SHIFT:______________
SHIFT:________
STANDARD INPROCESS STOCK
Time 90” 70” 50” 30” 10”
将梯子放回指定位置 安上灯罩并拧紧 拧紧新灯泡 拿新灯泡并去掉塑料包装
去掉旧灯泡并放在梯子上
去掉灯罩 将梯子放在需换灯泡的位置
Operator
QSB WORKSQHSOBPWREOVR.K0S9H13O0P4REV. 062705 10
10
Element 7 Element 6 Element 5 Element 4
QUALITY
Q CHECK
CUSTOMER CYCLE TIME:________________
OPERATOR CYCLE TIME:_______________
CRITICAL
C
OPERATION
SAFETY
标准化操作指导书应包括: - 作业要素 - 要素时间 - 操作顺序 - 标准在制品 - 操作周期 - 顾客要求的和实际的产品周期
2
QSB Workshop REV.10
标准化工作中的分工
组员
小组成员在标准化操作中的角色
Team Leader Group Leader
• 参与标准化工作的制定,并提供意见 • 对标准化工作提供改进意见 • 向组长反馈标准化执行情况 • 将标准化作为问题解决和培训的基础 • 执行标准化操作
Quality, Maintenance, Material
标准化操作
没有标准化操作
定义:标准化操作是由 相关的功能部门共同 编制、执行并定期更 新的文件,该文件指 导某工作按一定的次 序重复执行。
有标准化操作
目的:为持续改进奠定 基础。同时,通过员工 参与实现安全、质量的 更高的目标并提高生产 率。
QSB WORKSQHSOBPWREOVR.K0S9H13O0P4REV. 062705 1
Element 3 Element 2 Element 1
QSB Workshop REV.10
建立作业要素的关键
需要考虑的因素:
– 操作的位置 – 操作步骤的分解 – 完成要素所需时间 – 走动不是工作要素,通常不列在工作要素表中 – 一般来讲,任何操作的每一个工作要素都应该是“
看随工单,取零件” – 不要自动使用在工程操作指导中描述的分组。而要
•培训新员工 •操作改进分析 •分层审核 •问题分析、解决
标准化操作指导书的优势 :
• 总结现有的最好的操作方法 • 良好的目视化工具 • 是解决问题的基础 • 使过程中的浪费一目了然 • 培训新员工的教材
定义:
•小组成员一致同意并执行的 、记录操作顺序的文件,以 达到增加安全性,提高产品 质量和生产率。
1
QSB Workshop REV.10
标准化操作
标准化操适作用于重复操作的工序。
生产
返修
物料运输
不同的供应商可能对标准化操作使用不同的名称:操作指导书,作 业指导书,工艺守则、作业指导规范,PAD文件,等。
QSB WORKSQHSOBPWREOVR.K0S9H13O0P4REV. 062705 2
(例)
QSB WORKSQHSOBPWREOVR.K0S9H13O0P4REV. 062705 5
5
QSB Workshop REV.10
标准化工作的执行
多功能小组应确认并列出所有需标准化的操作.
需标准化的优先次序: - 客户关注的质量问题 - 评估已编制的操作顺序及操作方法?? - 离线返修 - 高 RPN 风险项目 - 员工流动频率高的工位
TOTAL
QSB WORKSQHSOBPWREOVR.K0S9H13O0P4REV. 062705 8
8
WORKSTATION AREA DRAWN TO SCALE
QSB Workshop REV.10
作业要素定义
作业要素是对生产成品的一系列动作的有 逻辑的组合
作业要素是标准操作指导书的基本组成部 分。它将操作分解成利于管理的动作,有 利于对操作的培训。
•确保操作员执行同一工作及程序的一致性 •高效的生产顺序 •减少过程变差 •减少浪费、解决问题、增强质量控制 •识别增值工作 •持续改进 •建立一个精益的组织
•检查操作员对操作标准的执行情况(分层审核)
QSB WORKSQHSOBPWREOVR.K0S9H13O0P4REV. 062705 4
4
QSB Workshop REV.10
•标准化操作应由多功能小组制定 •相关的或新员工应接受标准作业的培训(标准操作培训*). •多功能小组应不断改进和提高标准作业指导书
QSB WORKSQHSOBPWREOVR.K0S9H13O0P4REV. 062705 6
6
QSB Workshop REV.10
标准化操作指导书 (SOS)
标准化操作指导书将用于:
•是以操作员为主导,按一定 的顺序组织操作,且有很强 的重复性。
QSB WORKSQHSOBPWREOVR.K0S9H13O0P4REV. 062705 7
7
Hale Waihona Puke QSB Workshop REV.10
OPERATION:
STEP NO.
WORK ELEMENT
标准化操作指导书
(例)
Standard Operation Sheet (SOS)
操作顺序 各相关部门都认可的操作顺 序,有利于提高安全、质量 和生产率
为什么?
QSB WORKSQHSOBPWREOVR.K0S9H13O0P4REV. 062705 9
9
QSB Workshop REV.10
作业要素
任何操作均可分解成工作要素…
(例)
Changing a light bulb换灯泡